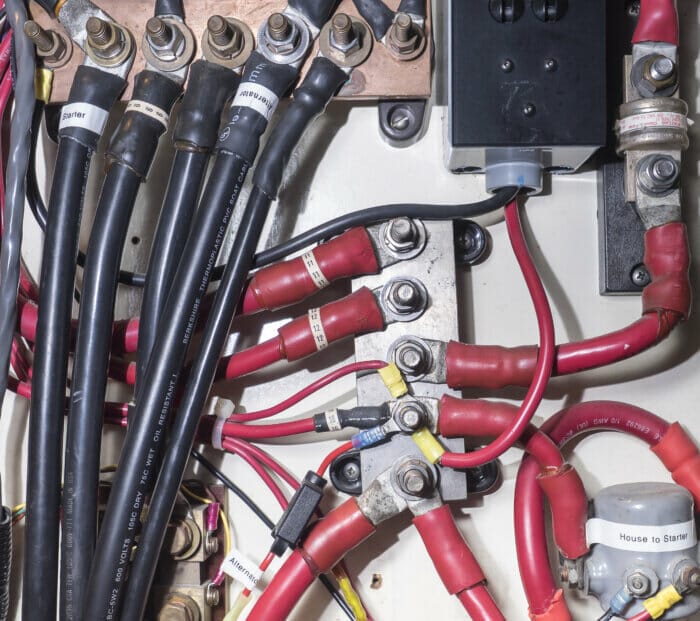
In earlier chapters we have already figured out how much battery capacity we need, now we need to look at the optimal voltage for our needs: 12, 24, or even 48.
We should do this analysis before we consider adding any of the high-current (amperage)-drawing devices that are becoming common today:
- Electric in-mast or in-boom roller furling
- Bow and stern thrusters
- Electric winches
- Electric cooking
- And on it goes
You will notice that I did not list electric windlasses. The reason is they will almost always be used when the engine is on and the alternator charging, so even a big one is practical on 12-volt boats. That said, 24-volt boat voltage makes windlass installation easier—more in Part 2.
And I left air conditioning off because anyone who thinks they can appreciably cool a boat and keep it that way for long powered by the batteries should move to Canada for two reasons:
- It’s cooler
- That stuff you are smoking is legal
The Theory
Now that we know why we need to look at the base DC voltage of our boats, let’s dig into a little theory so we understand why higher boat system voltages are required for high loads, and further, to give us a basis to calculate the crossover between 12 and 24-volt systems.
Yeah, I know, theory is boring. Stop your whining. You know from past bitter experience that I’m going to subject you to this before I get to the fun stuff, so grab a Red Bull so you don’t nod off, and let’s do it.
The Theory
The power consumed by a device to do work—spin a motor, heat the tea, light a light, whatever—is measured in watts.
For example, a single induction ring turned full up consumes 1500 watts or 1.5 kW regardless of voltage.
At 120 volts (AC mains current in North America) there will be 12.5 amps passing through the wires feeding the ring. How do I know that?
watts=volts x amps
therefore: amps=watts / volts
Or in this case: 12.5 = 1500 / 120
In the case of our induction ring at AC mains voltages, 12.5 amps can be passed along quite a small wire—as is typical for plug-in portable household appliances—that is inexpensive, flexible, and generally not a problem.
But on most boats we are saddled with 12 volts. So now we plug our induction ring into an inverter and the math changes:
1500 watts / 12 volts = 125 amps!
Actually, it’s worse than that because inverters have inefficiencies of at least 5%, and many are more inefficient than that. So let’s say 10%, so our 125 amps becomes about 140 amps.
Required Wire Size
We can calculate the wire size required to pass that many amps thusly:
- Decide how much voltage drop over the length of the cable between the batteries and inverter—both conductors (negative and positive) added together—we will accept.
- A good standard for applications like this is 3%.
- Use ohms law to calculate the resistance that will yield that voltage drop from one end to the other of the wire.
- Divide that by the number of meters of wire.
- Look up what cable size has that resistance per meter—known as resistivity—or slightly less, and that’s the cable we need.
Was that snoring I heard? Suck up that Red Bull.
The Easy Way
OK, because I’m a really nice guy I will let you in on a secret:
I’ve generally used 1.5 kW as the threshold for saying “yeah, you really need to go to 24 V”. 2 kW, intermittently, might be OK at 12 V, but beyond that you’re just asking for trouble. It’s not just the wiring, it’s everything else; inverters, motors, etc. are much harder to make efficient and reliable at very high currents and low voltages.
Any more than 100 amps on a single wire – at any voltage – is getting into the kind of serious territory where deviations from perfect installation, or degradation / corrosion over time, become significant problems in very short order.
I am totally OK with recommending, and using, 12 V systems as long as the total concurrent load is below 1.5 kW, maybe 2 kW tops, and no single device except the engine starter ever draws more than 100 A. (A thousand-watt windlass would normally draw 80 A and have a 100 A breaker.) Beyond that, you really need to pick a system architecture that fits what you’re trying to do.
Sure there is! Beyond 4/0 you can get European / Asian wire measured in mm^2 or American wire measured in circular mils (kcmil). 450 amps wants 700 kcmil wire, which is a hair under an inch thick, weighs two and a half pounds per foot, and is cut & crimped by a special version of the fireman’s “Jaws of Life” tool. It needs half-inch bolts torqued as tight as car wheel lugs, and the electrical arc formed at any imperfect connection is stronger than the one used to weld freighter hull plates together. Fun!
Hi Matt,
Love your last paragraph, really puts it in perspective. If we all decide to do that I’m thinking it’s time for a substantial investment allocation to copper futures.
And I agree that 1.5 kW is a good place to start thinking about 24 volts.
There were three reasons I put a 40 amp charger and two Group 27 batteries in my forepeak workshop for my 1500W Lofrans windlass, the draw of which is “on your bubble” for current all by itself. 1) I didn’t want to run heavy cabling to and from the main bank and put a hole in the collision bulkhead; by keeping the runs as short as they are, I can use 2 ga. on a round trip of under four metres; 2) I didn’t want to affect the rest of the DC system running the windlass, even with the engine running; 3) I wanted two fully charged batteries I could use in a pinch if my main bank went south. This is clearly not a popular course to take, but keeping those two batteries charged, either through inversion on a sunny day, shore power or running a Honda generator on deck is straightforward and the batteries have a lot of reserve to haul or lower chain and SPADE effectively.
And there was me thinking perhaps ruin multiple wires in parallel.
Yup. Even with a minimalist electric cooking setup, it was obvious to me that 12v was never going to cut mustard. The 1.5kw or about 120 amps sustained in any one conductor rule of thumb is a good one.
Hence I’ve gone completely down the 24v route on a very mid-sized boat and not regretted it for an instant. I haven’t found any modern equipment that I wanted which didn’t either support a wide 10 – 30vDC input range, or had a 24vDC option.
The other cool thing I found was that my conductor sizes for most loads are now around 4mm or less, which means you can start using multicore cable in lots of places. This tidies up the install quite a lot.
Like Nancy Reagan, just say no (to 12V).
Hi Kit,
It’s not that simple (is it ever) more coming in part 2.
There’s also an option of going to 48V system. I hear automotive industry is moving to 48V system voltage. That means there will be an abundance of 48V accessories any day now. Victron also makes a 48V inverter.
That said, it’s really early adopter territory with all that entails.
Hi Alex,
I cover 48 volts in Part 2.
Question: why include the thrusters? Aren’t they, like the windlass, only run along with the engine?
Hi Michael,
That’s true, but most thrusters have power draw that is much higher that a windlass. Think two to four times higher. Given that while the engine alternator will help a bit, the voltage drop to the thruster from the alternator at 12 volts wipes out most of the benefit.
Even a small 12 V thruster, like a Lewmar TT140, draws 150 to 180 amps and needs at least 2/0 cabling. One suitable for a 45′ cruiser – say, a Lewmar TT185 – can be over 400 amps at 12 V, with perhaps a hundred and fifty pounds of wire going to the bow and back.
At that kind of current, the little bit of help you get from the engine’s alternator doesn’t really matter. You have to size the cabling, fuses, etc. for hundreds of amps, and you have to size the battery bank so that the voltage drop from turning the thruster on doesn’t put all your electronics into “undervolt – reboot” state even with the engine running.
A 12 volt windlass, at least under about 1200 watts or so, is at or near the 100 amp mark. Its cabling must be sized and fused for that, but with a 40 to 80 amp alternator turning, it’s much less likely to have the “flipping this switch drops the main bus voltage so low that everything else shuts down” problem.
Anyone make a bow thruster powered by a small petrol engine? Getting 400A (or even 200A) all the way from the batteries to the bow sounds heavy and risky.
PD,
Yes, for me it was called my inflatable powered by my outboard and used as a yawl boat. Amazing how effective it was at pushing (or pulling) the bow around.
I was pleased not to have gone swimming handling the dinghy, the engine and the line to the bow: it was competition for a Charlie Chaplin scene.
My best, Dick Stevenson, s/v Alchemy
It”d be great fun for a single-hander 😉
Hi PD,
Yikes, adding petrol? No thruster is worth that. Why not just go without?
We have a whole book on how to handle your boat without a thruster: https://www.morganscloud.com/category/docking-tying-up/online-book-docking/
Phyllis and I have been handling our boat (56-feet) for nearly 30 years without any big problems and without a thruster.
I have also single handed quite a bit without problems.
When we got our first single-screw inboard, I was worried about how hairy things might get around the docks without a thruster, after three decades of usually having vectored thrust.
The e-book John linked above, plus a few hours of touch-and-go on an empty dock, solved that. Now, I’ll choose a 16,000 lb boat with a single inboard and a “magic springline” over a 600 lb boat with vectored thrust and no springline, easy.
Hi Matt,
Yes, the change from vectored thrust to inboards is a big one, no more swinging the outboard at the last moment and bringing the stern in with a burst of reverse. That said, particularly with sailboats, being able to still steer in neutral is great. The configuration I find most challenging is single screw motorboats with small rudders. On the other hand, once I got the hang of it, twin screw motorboats are a treat, and the easiest of all is a power cat with outboards, again, once I got the hang of it.
The saddest thing I see is a twin screw power boat with bow and sometimes even stern thrusters.
I actually think any cruising boat should consider going to a 24 V system. It’s just better, and more future proof. The following isn’t directly relevant, some of it is even definitely off topic, but might give perspective:
My work is with electric tourist boats in Amsterdam. The smallest ones have nominally 10 kiloWatt motors, in reality about 8 kW / 11 Hp. (Far more powerful than it sounds.) They’re just at the limit of what’s possible on their 48 Volt battery banks. Our bigger boats have 20 kW motors, about 27 Hp and need 96 Volt banks. Lower voltage makes the systems ridiculously big. Higher voltage actually also saves a significant amount of money in smaller cables, chargers, etc.
In the not too far future, most boats will have electric motors. Our 48 V and 96 V motors are quite big and heavy (not compared to a diesel, of course). The 20 kW motors weigh about 50 kilos and are a cylinder with about 25 cm diameter and 35 cm length. (1 foot is 30,48 cm.)
Next generation electric motors are already available. I’ve seen one first hand. It was the same about 25 cm diameter, less than a foot, but only 10 cm long/thick, and it delivered a continuous power of 80 kW / 107 Hp with instant insane torque. So, all that power in the form factor of a small stack of dinner plates. However, this comes with one caveat: It needs at least 700 Volt.
We won’t see battery banks anywhere near 700 Volt anytime soon. That will come from inverters etc. Also, we won’t be able to store such amounts of power in our batteries anytime soon. No point having a motor we can use for five minutes. Watts are the same, no matter what voltage delivers it. The point of mentioning this is to illustrate the “magic” of higher voltages. There’s no doubt that we’re moving towards generally much higher voltages for all high power applications.
I think the normal house bank of near future cruisers will be 48 Volt and that it’ll be the only battery on the boat, perhaps with the addition of a small emergency backup battery that has no other jobs. It just rests at a safe storage charge, and can be quickly connected to only the critical circuits when the main is disconnected. A much simpler, more efficient and reliable system.
As I’m already way off topic in this praising the higher voltage and electric motors rant:
Electric motors (of a good design) have no oil, no gears, no nothing. The motors just don’t need service and are incredibly reliable. Some of our 20 kW motors have passed 30 000 hours running time, and are still like new. Only service has been exchange the coolant fluid every second year. The 2 axle bearings have been exchanged once on 3 of them. That’s the only wear parts. And then there is the “fuel” price of about one tenth of diesel. For us, diesel is totally out of the question.
This will be reality for cruisers too, sooner than we may expect. Some places regulations will speed it up, like here in Amsterdam, but mostly the transition will come because boaters like the improvement. Here many are already rebuilding even boats that have no regulatory motivation.
Hi Stein,
I really don’t want to go down the electric drive rabbit hole yet again on this post. We have already done that to death and the key point is that whether or not it’s practical is usage profile. For your usage where you can plug the boat in every night, absolutely. For long distance cruisers it depends on profile. Thinking about a post on that so let’s leave the subject for that time. Thanks
Hi John, been awhile since I have commented. This topic is timely as I watch boaters burning up their electric systems trying to add creature comforts to improper boat grids. I am old enough now to have experienced this coming full circle. Back in the 50’s and 60’s we were all 32vdc. Why, because locomotives and trains were. Bulbs, DC motors, and generators were readily available. A basic system used four 8v 8D batteries. When one needed 12v to power a radio or other 12v appliance you simply tapped after the second cell on the second battery. Even back then a 12v automotive starter wouldn’t start a Diesel engine. After the 60’s there was an explosion in Automotive accessories and wide use of alternators for battery charging. Diesels became smaller and lighter. 12v systems became the norm with lighter, less expensive components. Converting a 12v boat to 24vdc will prove much more difficult than coming down from 32v but needed and well worth doing.
Hi Bob,
Great to have you back! And thanks for the fill on 32 volts. I wondered why the App I linked to had that option, now I know. In many ways it’s a pity we did not stick with it.
I was also wondering why Electrodyne had 32 volt alternators – now I know.
We have electric cooking on our boat.
Three 800 watt induction burners and a 1400 watt electric oven. Cooktops are made by Pantin. Oven is Unox Roberta.
12v system 3200 watt inverter 720 watts of solar 600 amp hours of LifePo4 batteries .
24 amp hrs used to boil pasta for 4
20 amp hrs for the sauce.
Once everything is cooking i turn the cooktops down to maintain temps .
This is the hardest use we do for the cooktop .
The oven takes 12 amp hrs to preheat and holds 325 degrees for around 25 amp hours for an hour at this temperature. The oven is very well insulated and commercial grade.
Yes I have shares in a copper mine all the cabling is over sized . The Inverter is 4 foot away from the bank with 4/0 cabling .
Would never go back to propane
Hi John,
If you are willing to cook that little I guess it will work but unless you have a generator usage must be more limited than most of us would be willing to put up with.
Yes I have a generator , sort of . It’s used for charging the batteries and making water only , it’s a dc setup .
We are heading for the tropics as soon as this pandemic is under control and we can all travel again . So cold things will be the order of the day . Even so the electric setup works for us and we gained a locker we’re the propane tanks were . I honestly never thought of going electric until I saw S/V Delos doing it and having great results .
Regards John
Hi John,
What kind of generator do you have?
Thanks, Dick Stevenson, s/v Alchemy
Hi Dick
I designed and built my own DC generator based on a Kohler 8KW generator that was wired up wrong and fried the electrical side of the unit. I acquired the engine, a 15 hp 3 cylinder yanmar with the governor which enables to unit to run steady at 1800 rpm just like a generator , from that i coupled a Eco-Tech alternator directly to the crank shaft , no belts and no side loads. The alternator makes 225 amps when hot at 1800 rpm . Above that I mounted a HydraCell D10 high pressure water pump pump to drive the water maker , these are ideal pumps for that purpose , they can run dry and the oil end is complete separated from the wet end, unlike the usual piston pumps that introduce small amounts of oil into the water as it passes through . No good for the membranes. Produces 40 gallons an hour . But they are not cheap. .
The solutions are there but you have to do your research and source top quality parts for the least amount of compromises in any design .
Regards John.
O yes , after reading your next response , yes I think I have invested well over 30000$ in this system with the water maker and cabling/switching/solar. So it is a significant investment to get it right . Our boat is 45 feet And able to accommodate all the gear .
John
Hi John,
Thanks for being clear on the realities. Both refreshing, and distressingly rare.
OMG, John, this is sooo timely for me! We’re re-kitting our recently purchased 36′ steel expedition sailboat. Our galley is half ripped out and I need to replace our house battery bank. Work is on hold, however, while I discuss (read argue) with my 1st Mate/chef about her desire to convert the galley from from Propane to all-electric. I’ve been crunching numbers to reach a consensus on if/how this can be made feasible with our boat and budget.
Yesterday we cooked a typical “quick” meal (at our terra firma home base) on an Instant Pot and boiled 4 cups of water on an induction plate, using a Kill-A-Watt meter to keep the score. The Instant Pot used 0.13 kWh. The plate consumed 0.11 kWh. So, 0.24 kWh = 240 Wh x 1.05 (efficiency losses) = 252 Wh/12V = 21 Ah of battery capacity. 3 “quick” hot meals per day (is that being extravagant?) = 63 Ah. We gulped when we realized that this amounts to 15% of our 420Ah of battery capacity on our four Group 31 Lead Acid AGMs. That only leaves another 63Ah of capacity for all other loads before we bring the battery bank down to their safe limit of 70% DOD. In our current set-up, the fridge, watermaker, lighting, fans and electronics already draw so much energy that we have issues on some days, even with 350W of solar and a wind turbine. Adding even these conservative galley loads seems pretty daunting and that’s just considering the battery capacity. The impact on the boat’s cable sizes and risk of blowing fuses /starting fires adds another worrisome wrinkle.
A switch to 24VDC architecture certainly is attractive at first glance. I’m sure the devil is in the details, however, and you’re great at rooting out devils. For example, what’s the most reliable and cost effective way to connect the boat’s existing 12VDC devices into a 24VDC architecture? Ooops, I’m front running!
Please don’t wait too long to publish Part 2. The winter solstice is just ten days away and Spring seems to be just around the corner. No, I’m not a glass-half-full kinda guy. I’m just so full of projects right now i.e. building a new rudder, stripping and re-coating the hull’s bottom, new through-hulls, new holding tank, new battery bank location and restraints, as well as aforementioned galley, that time is flying by!
Hi Robert,
Good on you for doing realistic analysis before jumping in to electric cooking. The bottom line is a battery bank that small is not going to support electric cooking and changing voltage will not fix that. Changing to 24 volts only reduces required wire sizes, it does not add battery capacity, although it is required for realistic electric cooking.
As I have said in earlier posts, the only way you could get a bank to support realistic electric cooking on a boat that size is lithium and you would also need a generator since solar and wind will never cover it. See the previous posts for the math supporting this.
Also note that if you plan to live aboard, unless you are food agnostic (some people are) you will do far more cooking than your experiments. Think at least three to four times more.
Bottom line, this is simply not going to work on your boat unless you spend at least US$30,000 on doing it right and even then it makes no sense, or at least not to me.
A number of years ago I was involved in building a series of 26 foot lobster yachts. At my insistence, we decided to switch from 12 to 24 volts during the construction process. We estimated the wire weight savings at about 1,000 lbs…
Needless to say I’m a huge proponent of 24 volt systems with the vessel length threshold, for me, at about 35 feet.
Hi Steve,
I understand it’s an easy decision for a new build. What about existing boats with a 12V system? Under what circumstances would you feel a conversion to 24V was justified?
With rare exceptions, I would not envision conversion as practical or cost effective.
And my previous post should have said “A number of years ago I was involved in building a series of 36 foot lobster yachts.”
If it’s a total refit – i.e. you are ripping out & replacing most of the existing equipment, installing new batteries, etc. – on a boat with the pedigree and value to justify this level of work and investment, then I think switching from 12 V to 24 v is worth considering.
For anything shy of that, you are looking at a lot of work, a lot of old used gear to re-sell for pennies on the dollar, and a lot of expensive new gear to install. I’d say either learn to live within the limitations of what you have, and not try to graft on more electrical loads than the 12 V system was designed to handle….. or sell that yacht and buy a different one whose electrical architecture is better suited to your demands.
Hi All,
We are starting to front run the next post. Let’s keep all of our thoughts on 24 volts for my post on just that. That way everyone’s wisdom will be where it will do the most good and help people for years to come. Hum, that last sentence sounds so familiar, I wonder why.
Interesting induction hob Ecoheat Smarttouch (Australian) has 500,1000 ,1500 and 1800W settings
I have two installations that might be of interest here. The first is 24v and we use a DC to DC power supply to provide 12v where required. This is very efficient and could easily be used to provide 12v on a yacht for all the relatively low power requirements eg lighting and instruments. On the down side I have had problems with keeping lead acid batteries in series balanced on a 24v system.
The second is a larger partial off grid application using a BMW i3 battery bank in units of 48v with all Victron equipment for solar charging and inverter. Bearing in mind that our max output is 10kW we still have 75mm2 cables connecting the inverter and its only a 4m run.
What about inverting all large loads to AC eg cooker,windlass, thruster etc. Cables can be 1/10 or even 1/20 the size (for Europeans) then. But can you get thrusters and windlass in AC?
Amps are the real deal breaker with cable sizes – I think I saw that copper prices had reached a record high the other day.
Hi Tim,
Interesting idea, but I have not heard of yacht sized bow thrusters etc that run off AC. Also, to me at least, such a solution would be more complicated than I would want to see on an offshore boat.
And we will be covering DC-DC converters and 48 volts in part 2 so it would be good to have the benefit of your experience then.
At the risk of front-running a future instalment:
You’ll have a hard time finding off-the-shelf thrusters, windlasses, etc. in yacht sizes wired for single-phase 120 V or 240 V AC. The way you’d do that is to buy the complete mechanical bits, without motor, from the marine hardware maker, and then buy an AC motor with the same mounting flange, plus a controller, separately from an industrial automation supplier. You’ll find a pretty firm ceiling at 2 hp for single-phase AC motors, beyond which almost everything is 3-phase. At that point, your main bus may as well all be 3ph AC and your systems engineering becomes much more like that of a small ship than a yacht. I would hazard a rough guess that the crossover point for an all 120/240 V 1ph approach to make sense is somewhere around 6 – 8 kW of concurrent loads, i.e. a factor of four higher than the point where we want to switch from a 12 V to a 24 V main bus, and doubling that again is sufficient justification for going to 120/208 V 3ph.
Hi Matt,
Not front running at all. I’m not even going there. As you say, that’s ship stuff. Actually, from what I have seen, when 24 volts won’t do the job hydraulics is the way to go. That’s what we had on the mega yacht I did a guide job to Greenland on some years ago and that’s how fishing boats handle really heavy motor loads.
You can do a lot with hydraulics – there is tremendous power density there (i.e. stuff is small for its strength), the technology’s been perfected over many decades of hard commercial service, and cooling is naturally combined with power delivery.
That said, I’m seeing evidence of a push away from hydraulics in favour of 3-phase AC, now that 3-phase variable frequency drives are very good and relatively cheap. Hydraulic maintenance can get to be a real handful when you start trundling 55-gallon drums of oil around the dock and have to mop spills out of the bilge.
Hi Mal,
Most all the yachts over about 60 feet I have seen are hydraulic and many in the 50 to 60 foot range. My answer to all that? If you can’t handle the boat without getting this complex, buy a smaller boat.
What powers the hydraulics, an electric motor? Or are we talking about a main engine power take off?
We have a hydraulic takeoff from the gearbox because we have a hydraulic windlass and bowthruster. These work so much better than the electric versions. More power, use it as long as you like without thermal trips or burning things out and much more reliable. Of course we are limited to things that you use with the engine running though, so no hydraulic winch’s or reefing systems, but that suits us, prefer to do that by hand.
Hi PD,
Most yachts that rely on hydraulics have a PTO on the main engine, often one on the generator, as well as an electric motor (usually 24 volt) driving a hydraulic pump. The result is a very complex system that I certainly don’t recommend. A friend of mine just had a fire in his hydraulic control circuitry and that after spending a bundle replacing it all.
Much better to just not have the gear that requires all this.
My 1200W windlass seems happy running on 12V LFP, Why must the engine be running?
Hi David,
Yes, we often run our windlass without the engine running too. It all depends on battery bank size, state of charge, as well as cable gauge and distance of the run. My reason for putting that in was to explain why a windlass is less of a problem than say an electric winch, but that does not mean that the engine must be running on every boat when the windlass is in use.
A bit off topic here but fits to windlass+engine – a lot of production boats I know (most notable from a respected french cat builder) have their windlass wired in a way it would only turn when the engine is running. An absolute no-go if you ask me…
Hi Ernest,
Seriously? I agree a total no go and a disturbing indication of misunderstanding of cruising reality on the part of the builder.
I know for a fact that this is not a new trend. Our boat has been produced in late 70s – early 80s and the builder wired it exactly like that. I guess their only excuse is they were targeting charter market, not cruisers
Hi Alex,
That just makes it worse!
I couldn’t agree more. My French 46′ had this system and I fitted an override switch so the windlass could be operated without the engine running when required. The electrics are all 12v except for the bowthruster which is 24v with its batteries 4′ away.
Abuse the planet???
Hi Sven,
See https://www.morganscloud.com/2020/11/03/efficient-generator-based-electrical-systems-for-yachts/
See also: https://www.morganscloud.com/2020/09/16/hurricanes-what-the-blazes-and-taking-a-few-days-off/
What has this got to do with the planet?
Hi Sven,
Did you read the link to efficient generator article? The point is that by using a generator in that way you can save a huge amount of carbon and fuel when measured against starting the generator every time you need AC power, or worse still leaving it running in case you do. All explained in the linked article.
Still don’t see the connection to the planet.
Hi Sven,
Surely if we use much less fuel and create much less carbon than normal practice that’s good for the planet. Just like hybrid cars: not zero carbon, but way better than normal practice. Or for that matter electric cars that while zero carbon in and of themselves use a percentage of electricity that, depending on where you are, was generated by burning hydrocarbons. Perfect? No. Better? Yes.
OK You think carbon i harmful to the planet?
Hi Sven,
I don’t know where you are going with this, but I can’t see it going to a good place. Let’s leave it there shall we.
My wishlist for part 2 or 3 would be to cover Integrel Lite with 48V LiMnC-natteries. I recall the discussion around original Integrel when discussing generators, but I find their approach much more palatable when looking to save on copper with electric cooking. I.e. when assuming a small boat with high electricity usage.
I haven’t been following the market too closely, but it seems 48V accessories like bow thrusters and solar controllers are becoming more common by the minute. With the need for balancing, 48V Lithium with integrated BMS seems like the first reasonable upgrade from 12V. And hardly overkill for the 2kW ballpark?
While all good and admittedly really interesting and educational the feeling creeps up that the “attainable” from the sites title gets forgotten somehow.
How would “attainable” cruising fit together with complex and expensive 48V systems, hydraulic mainsail reefing and other expensive gear that gets discussed?
Sorry for the rant, though.
Hi Ernest,
Not by me. Take a look through my recent articles and comments and count the number of times I have cautioned people to keep stuff simple. And one of the primary reasons I write articles like the one on induction cooking and then follow up with ones like the above is to explain how things can get complicated fast when we add gear without really thinking about the consequences.
Hi Mikko,
I tool a quick look at Integrel Lite. My hope was that they had brought out a simpler 12 and/or 24 volt system using their controller and alternator. Sadly not the case. Integrel Lite is just a bit smaller version of Integral but it still, although very cool technology, has all of the issues I explain in my review: https://www.morganscloud.com/category/electrical/integril-review/
Hi Mikko,
I agree with what has been said by others, that your suggestions seem to point towards expensive and complicated, given that it’s still very far from easy to find 48V appliances for boats. I mentioned our commercial electric drive boats far above. They have high voltages banks for their propulsion, but all other consumers on the boats are 12V or 24V (thrusters). The reason being that it’s far easier and cheaper, even when 48 V is already available.
As a side comment, be very critical to integrated lithium batteries, so called drop-in batteries, with BMS and connections inside a normal looking 12V battery box. Reasonably decent versions do exist, but are very rare and expensive. The standard issue of this layout is very very poor. The alternative is separate prismatic cells with separate BMS etc, which way more powerful and durable (think 2-4 times) while simultaneously being cheaper and, in real life, not harder to install.
For big DC loads like big inverters and windlasses, etc. 24 VDC makes complete sense. For smaller loads like entertainment systems, DC lighting, small water pumps, bilge pumps etc.. 12 VDC is much cheaper and more readily available at least in the in the US.
To power those DC loads use a split 12/24 battery bank and a Vanner Equalizer to keep both banks halves equally charged…. this is the same method transit busses have used for years.
You pull the 12 volt loads off the 1st half of the 24 volt bank. The 24 volt loads are suppled by the full bank. The Vanner Equalizer keeps the amp hours in and out of each half the same.
If you’re going to put as much electrical gear on a sailboat as power boats had not that many years ago….. approach it like a power boat. Wire it for VAC and supply your water makers, air conditioners, etc. from an inverter(s)….. or a Northern Lights generator.
Larger Sine Wave inverters are very inefficient at low loads…. idle draw is often around 3 amps @ 12VDC. For some appliances, like microwaves that have digital clocks that are a nuisance to reset, a smaller more efficient modified sine wave inverter is an option to power them… you can leave it on without the big parasitic draw….. save the big inverter for when you need it.
The key to all this is a large capacity battery bank…. and the charging capacity to go with it. Use the battery manufacturers guidance for “finish rate” (normally 3% to 5% of capacity) and be able to maintain that for the full cycle… figure you’ll put back 15% to 25% more than you’ve taken out.
Instead of the theoretical 4 hour 50% to 100% recharge time…. figure 5 hours.
To maximize engine life, run it at proper temperature, minimize the start-stop cycles (in aircraft that’s called heat cycles), use synthetic lubricants.
Modern “Over the Road” refrigeration generally uses small diesel engine powered compressors…… engine service intervals, oil and filter changes, etc., run between 1000 and 4000 engine hours…. as compared to yacht engines averaging a 200 hour service interval.
Everyone has budgets…. my experience is sailboat batteries are usually destroyed by abuse… infrequently by equipment malfunction, rarely by life cycles.
I would rather replace much cheaper deep cycle lead acid wet cells than any of the more expensive alternatives. The key to this is the batteries being located so they are easily maintained.
As battery technology is rapidly evolving, that will probably change. Right now lead acid is still cheaper and safer.
Overall… remember boat size places physical limits on where you put all this gear. There are a lot of advantages to keeping it simple. But as we get older the more luxuries seem to become necessities.
Hi Dennis,
I agree with a lot of what you say. The exception is building a hybrid 12-24 volt system by tapping off the the 24 volt bank. Sure it can work, but today I prefer a simple 24-12 power supply for the few things that must run on 12 volts, like NMEA 2000 networks, and make everything else 24 volt. Either that or cut back and stay 12 volt.
I also don’t think that transit busses are a model I would follow for boats since the usage profile is so different between the two: the bus alternator will be making power pretty much whenever power is required. A boat goes long periods with no charging.
I agree that liquid filled are often the best bet and still probably the least expensive on a per cycle basis. More here:https://www.morganscloud.com/2018/05/11/battery-options-part-2-lead-acid/
After being introduced to Vanner Equalizers many years ago by a major starter-alternator rebuilder, I’ve set up several yachts with Vanner Equalizers…. and have considered adding one to our boat.
In 15 years experience with Vanner’s, I’ve never seen one fail.
There are other manufacturers that supply DC-DC converters similiar to the Victron you mention. One problem with them that John stated is if they fail, you loose 12 volts.
If a Vanner fails, it is relatively easy to bypass it and pull the needed 12 volts directly off the batteries…. simply move a couple of wires.
Vanner’s are also available in capacities up to 100 amps @ 12 VDC.
The transit bus reference was just to point out their reliability….. they do have different operating conditions. However there is a lot of equipment used in yachts that originally was developed for use in other fields…. High output alternators in particular were not originally developed for yachts.
Remember commercially time is money. Reliability is paramount and should be on the water also.
Regarding Matt L’s comment….. Vanner’s were around when transit buses were powered by 2 cycle Detroit diesels…. the 2 cycle engines are gone, today’s electrical systems on transit buses, large motor homes, long haul trucks are even more demanding…. accordingly the Vanner’s are in even wider use.
There is always more than one way to do things….. I base my opinions on personal experience…. vocationally and avocationally.
A boat needs to be designed for a particular owners, intended use, talents (experience) and budget.
My personal experience includes years of cruising…. and working in the marine industry….. long term both yachts and ships.
To put my opinions in perspective….
I originally paid for my sailing avocation with 30+ years sailing as a marine engineer in the Merchant Marine, including Chief Engineer on 3 ships, both old and new build.
We cruised, and still own, a 54′ steel cutter Nelson-Marek designed for us. Before that, we cruised a gorgeous old 40′ wood boat . The Nelson-Marek started life as a simple 12 VDC boat that over the years has been gradually upgraded to now having reverse cycle air-conditioning.
No disrespect to John, but we prefer warmer climates.
We would still be cruising except my wife’s health changed….. that change lead to me working more in the yacht industry. Sailboats of all sizes up to 125′ and motor yachts up to 185′.
Hi Dennis,
All good points, but I would still prefer not to use, nor would I recommend, a tap off system to produce 12 volts. Just like the simplicity of a 24-12 supply, as well as the added benefit of isolation of sensitive electronics.
I wanted to offer an insight into a real-world scenario working quite well with 12V, as implemented on my catamaran. I’m not bringing this as an argument against 24V, just as an indication that 12V-based systems need not be shunned, with just a modicum of non-traditional thinking.
I’m bypassing the discussion around winches, thrusters, and windlasses, as these have always functioned quite adequately with 12V, and function even better after I changed the location of the battery banks, to be closer to these consumers.
My battery bank consists of 20 180AH CALB LiFePO4 batteries, connected in series and parallell via 1/4″ thick copper bars. This bank is (almost) directly connected to the DC bus, which also consist of 1/4″ copper bar, bulkhead mounted. The “almost” is because of a 1,000 amp fuse between battery positive and bus, and a 500 amp shunt on the negative side (500 because of higher accuracy – shunt can easily handle peak loads of 1,000 amps).
I have three Victron 1,600 watt inverters, working in parallell, connected to the DC bus via 4″ and 6″ 4/0 cables (custom made on the boat, using TEMCo’s $20 hammer lug crimper). While pulling 5kW (inverters can handle up to 9kW peak load), there is a voltage drop from battery post to inverter of 0.03V (at about 450 amps) – negligible.
This setup is neither expensive nor difficult to pull off. However, having the threaded battery post configuration of these cells is what makes it easy to connect them via a bar.
Also note that instead of going up in cable size, if copper bars won’t do it for you, parallell runs of smaller cables will do the same job (ex: 1×4/0 = 2×1/0 = 8x6AWG).
Great article John – made for outstanding Saturday afternoon reading. If you forget a windless and electric winch in the discussion and just think about induction cooking, you are really talking about sizing the inverter (s) correctly as well and having a battery bank that is either set up for 12/24V or having a genset (or both). Since induction cooktops are running 120V/240V I am fuzzy on the wire gauge relative to the cooking set up since they all require AC. Thanks!
Hi Ryan,
Not sure I understand your question. I do cover the theory of how wire size relates to amps and how that varies as voltage changes in the first part of the above article. Have a reread of that part and then if you still have a question I will see if I can answer it.
Hi – ok in an ideal world I would go 24v, but could the problem also be solved by using two inverters to share the load going to the oven and another powering the induction hob (assuming they have different inputs)? That may be a way to keep the power draw down and keep 12v source feasible? Essentially I have a 12v yacht currently and changing all the windlass, winches and watermaker to 24v is likely infeasible from a cost perspective.
Thanks
Matthew
Hi Matthew,
Sure, two 12 volt inverters can work. But, if it were me I would be taking giant step back and asking myself if all this complication, expense, time and potential reliability problems are actually justified to achieve the marginal (at best) benefits of electric cooking. This one would almost certainly fail my “too hard, didn’t do” test. “Just because I can do something, that does not mean I should”. The other test I always apply is “opportunity cost”: what else could I expend all those resources on for better result. For example, what state are my sails and rigging in? And finally, maybe it would be better just to go sailing, the ultimate opportunity cost question I always ask myself.
Also be aware that cooking on 12 volts will always be marginal. The numbers just don’t work out that well. Is it doable? Yes. Is it elegant? No. And I agree that changing to 24 Volts does not make much sense in your case.
Hi John
Thanks for the quick responses. I appreciate the advice, for me I needed to be able to compare the options in quite some detail, and how they would work for my particular situation and yacht before I can take that step back. I think I am now fairly close so can fully compare how I would remove propane add lithium, expand battery capacity and attempt to go green while sailing (with a watt&sea) or remain lead acid and propane.
I also agree that its important to consider opportunity cost, unfortunately as a single dad I can’t just go sailing at the moment), and in terms of the yacht thankfully we have a lot of the sails and stuff dialled in (having finished 2nd in ARC Europe last year) so have the luxury to consider items such as electric cooking.
Hi Matthew,
Do as you see fit. But one more thought for you. Diving into the details before analyzing the fundamental veracity of basic premise (electric is better than propane for my purposes) is a classic symptom of someone in the grip of confirmation bias. You already know all you need to know to step back: it’s going to be complex, expensive, a huge time sink, and less reliable (way more complex is always less reliable) and harder to fix at sea than a good propane system.
Why do I think that’s what’s going on here? Because I can look back at many times in my life when I have done exactly that and then regretted it. (Let’s not talk about my second marriage.) And I fear there will be more for me in the future, because it’s really hard to recognize the behaviour in ourselves. And of course you have an even worse problem in that electric cooking on boats is promoted by a bunch of ignorant charlatans who care about clicks, not you, or the facts, on YouTube.
Anyway, sorry for the tough love, and of course I could be wrong, but that’s what this smells like to me.
John – firstly I am a fan, i was recommended your site by friends and have already recommended to others. What you do and the approach you take is a great gain to sailors, detailed and specific! However you may wish to remind yourself of your own comment guidelines, “be nice” and Even the slightest indication….way of doing things is…worthless”. Your comment did come across to me that the process I am taking is worthless, now its ok I am strong and not so easily offended, my underlying assumption is you are a good person trying to help me. However, just because you have had experiences of confirmation bias in the past does not mean you can imply I have the same for me based on just a few comments made. Me I am a data driven mathematical brain, I know how my brain works, it needs information, analyses, weights pro’s and cons and then decides. I’m not a big sailing you tube watcher but have friends with lithium and electric cooking doing similar ocean sailing to me and who’s opinion I respect and have suggested its something I consider. Anyway please take the feedback positively, its sent with love and a smile.
Hi Matthew,
Thanks for sharing how you feel about this. I would argue that I never breached our comment guide lines in the discussion since I always made clear that it was my opinion and even made clear that I knew I could be wrong and that my thinking came from my own mistakes. However, in reviewing what I said, I should have put one more “in my opinion” just before “you already know”—always more to learn about all things, including answering comments. Thanks