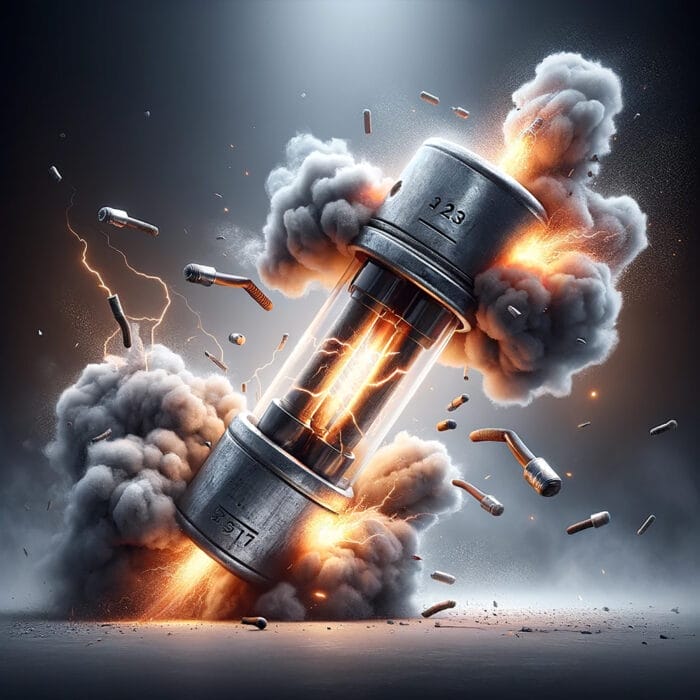
I don’t know about anyone else but I’m getting bored with lithium batteries…but that highlights one of the biggest pitfalls awaiting a cruiser planning to install them:
There is so much to know that it’s tempting to pull out the credit card before completing the planning process properly.
I freely admit I have done exactly that with other projects but it never goes as well as when I grit my teeth, finish the research and then complete the plan, all before spending the first dollar.
So let’s soldier on. At least this one is a relatively short read.
Fusing Fundamentals
With that blather out of the way, let’s quickly cover the fundamentals of fusing.
Well, I started reading this article feeling all smug about my installation and the fact all batteries on my boat are fused within 7 inches, but as usual John quickly shattered this illusion with the AIC requirement. I think the fuses I have are MEGA fuses; looks like I’ll have to upgrade to class T. At least they’re on sale at Binnacle right now!
Hi Emile,
Good call, and don’t feel bad, half way though writing the above I realized that I too needed to fix something. In my case I had installed one fuse of my house bank made up of two AGM group 31 in parallel. Probably perfectly compliant, but certainly not best practice in that if one of the two batteries failed to short there would be no fuse to blow. I too will be ordering from the Binnacle!
Hi Mal,
I can’t really see any relationship between internal and external BMS and over current protection (fusing). As I say in the article the whole idea of the fuse is to protect when all else fails. Keep in mind that an external BMS is not actually passing any current but rather controlling relays so it does not need to be protected itself, other than maybe a fuse on it’s own electronics, and the relays are protected by the fuse on the battery, just as the wire to the busses is.
And yes, you are right that with an external BMS managing several batteries you can’t charge them individually at least without removing the others, but why would that be a problem?
On the other hand with an internal BMS it is passing current using MOSFETs that tend to fail to short, so the more I think about it, the more I think that, on balance, an external BMS is safer.
Hi Mal,
Ah, I see what you mean. So yes, it might be true that an internal BMS would shut the battery down if a tool was dropped across the terminals. But I would not bet on it because internal BMSs use MOSFETs to switch which tend to fail shorted. In many ways the best solution is an internal fuse like Epoch put in their new 460Ah battery. But then again, I’m nervous about a battery that big with only one fuse and also wonder about the dangers of that fuse lowing up inside the battery and starting something bad. Also, the presence of that fuse tells us that Epoch don’t believe the BMS would work to interrupt a short.
And yes, I agree that the Lynx distributor is total inadequate for battery fusing. Not only are the fuses inadequate it would be impossible to comply with the 7″ rule using it.
Hi John,
This is a very important topic that most skip. Thanks for discussing it properly. Many think the average sailor doesn’t need to worry about this. WRONG! Working with lithium has convinced me it’s an even bigger problem than it looks like when discussed without the scary words and smell of sulphur it might deserve. 🙂
Some rough calculations. Say we want to have a small to medium lithium bank for our moderately sized average power consuming long distance cruising sailboat. Often 400 Ah @ 12V. Such a bank will give a similar comfort level as a good 800 Ah LA bank, which is not excessive for this use case, of course.
Then we look at the data sheets from the cell manufacturers. We must look at cell level, not pack. NEVER look at info from assembly brands: All brands on the market, except from the limited number of Chinese cell factories, which NEVER sell cells or batteries directly.
Those data sheets vary some, even for similar chemistry cells, but typically they say max discharge rate is around 10C. Ten times the Ah rating. That’s what they can support for a significant duration, like several minutes, without damage to the cells.
The maximum momentary short circuit current is hard to quantify, and I haven’t seen any reliable numbers, but it’s definitely many times as much. My assumption is more than 10 times as much, amounting to 100C for some seconds.
On our 400 Ah bank, this gives us an ability to supply 4000 Amp continuously for several minutes and perhaps exceed 40 000 Amp for a few seconds. We’re into lightning territory. We have all witnessed enough of that to not want it happening inside our boat…
+40 000 Amp is way over the AIC (Amp Interrupt Ability) of even Class-T fuses. So thinking about lower rated fuses is flat out ridiculous. But is even Class-T not sufficient then? I don’t really know, but I do think they’re doing a plenty good job for our 400 Ah example. Firstly , I’ve never heard about one failing its job. The proof is in the pudding.
Also, my potentially flawed understanding is that if the fuse gets a massive blast of current, it will fail so fast that the current hasn’t yet reached its potential max. The current comes from a chemical reaction in the cells. Even though it’s very fast, it’s not immediate. The fuse tripping means that the impulse to increase power is stopped before the Amps surpass the Class-T fuse interrupt ability. Please correct me if I’m wrong about this.
As John mentions and I agree with, we shouldn’t feel confident about Class-T fuses for really big propulsion banks. For LA, that’s what we use, but for several thousand Ah lithium I don’t like it. I still see it being used and I haven’t looked for alternatives, as that is not my job or area of competence, but as mentioned I’ve also never heard of one failing, even there. I also don’t know, but my guess is that actual AIC might be a lot higher than the rated value, and that the failure modality is better than for any other normal fuse type I know. There’s no way it can create a better connection after any mode of failing. The other mentioned fuse types fail on this too.
Anyway, my point is that this is a really important topic, which is also easy and relatively cheap to do right. A proper sunshine story, with some thunder in the background, for motivation. 😀
Hi Stein,
Good points, particularly that it’s important to think of the cell level.
I do need to point out for others that assuming we fuse each battery independently in your theoretical 400 Ah bank, and assuming multiple batteries in parallel in the bank, the max current will be split between the fuses in parallel and so probably not exceed the AIC. That said, we are now seeing some huge single batteries, so your point is still valid.
As to the time to ramp up to max current, I just don’t know. Good news if it works in such a way that the fuse will reach its rating well before its AIC, but without certainty on the theory, we just have to make our errors on the safe side, as you say.
As to why max short circuit current is not published for lithium, I did some research and now have a theory, which I will publish as a tip.
HiJohn,
I saw a video somewhere where the short circuit current of some small cylindrical cells was tested. One single cell at a time. The capacity per cell was said to be around 2 Ah. The chemistry was not LFP, probably rather LMn or such, as these were taken out of appliances. One from a battery drill. The other cells reached around 50-60 Amps. The drill cell tripped his meter, which had a 600 Amp limit.
This isn’t solid evidence of anything, but still interesting. A 2 Amp cell providing a 600 Amp jolt (if that was indeed what happened) is 300C. Meaning a 400 Amp bank could give a + 120 000 Amp jolt. This is just speculation, but I do think it’s representative of what we should expect might be possible. LFP has a higher current capacity, both in and out, than most other normal lithium chemistries.
As an aside, this topic illustrates how the “cold cranking capacity” of such cells is astronomical. The reason people think lithium can’t crank an engine dramatically better than any LA is that they have been served the “facts” by drop-in swindlers selling garbage electronics in boxes.
Editorial Comment – Under AIC, line 5, I believe “failing to short: should be “failing to open”. Observation from a retired electrical engineer.
Hi Garry,
Thanks for checking these things, but in this case “failing to short” is correct in that context. Note that the sentence makes it clear with the words “pretty stupid” that I’m warning of undesirable behaviour. And of course a fuse or breaker failing to short circuit, rather than failing to open and breaking the circuit is about as undesirable as it gets.
Hi Gary,
“Failing to short” is the correct wording, indicating the problematic nature of this issue. Fuses fail to break the current, they fail into a closed short circuited position, allowing current to keep passing. Or in the case of lithium, they just may lack the gap necessary. The current can jump it and close the circuit without physical connection.
“Open” and “closed” are a bit counterintuitive with circuits.
“Failing to short” is slightly odd wording. One would normally say “fail shorted” or “fail closed” for a device that conducts current after failure.
Hi Matt,
Good suggestions, I will change it.
Sorry – you’ve still got it wrong. Correct fuse operation is to open under fault conditions. A failure of that operation is a failure to open!
Hi Gary,
I think we all agree and just talk past each other. The “failing to short” wording is not about how a fuse “pops” and opens a circuit, which is what it’s meant to do. It’s a way it can fail to perform its job.
If it gets overloaded and it doesn’t open the circuit, but rather has a meltdown or other failure, resulting in it keeping the circuit closed. It failed into a situation of a short circuit. In short, “failed to short”. I agree that the wording easily lends itself to misinterpretations. I’ve just gotten used to it. Perhaps we should look for better wording?
Hi Gary,
Ah, I see what you mean. That said, I think “failure to open” might be confusing too. So I think I will use one of Matt’s suggestions going forward. Thanks for the heads up.
Hi Mal and John,
The Victron Lynx Smart BMS does have a contactor inside that also works as a system fuse and a remote controlled main switch. The standard rating of it is 500 Amp. Others can be ordered. I have no idea what its AIC is, but considering that it’s Victron and made specifically for their own lithium batteries, I assume it’s good, but that could be wrong.
Beware though, a Victron BMS will only work with Victron batteries. (They have gotten dramatically cheaper lately.) It depends on circuits inside the box to monitor and maintain the cells. I assume one could copy those electronics for a DIY setting, to use the cool BMS and the other nice Lynx gadgets, but I doubt if it’s worth the hassle.
I also see no point in preparing the system for charging separate parts of a single battery bank separately, unless it’s for real top balancing of single cells, which may occasionally be a good idea for some DIY setups. The external BMS in Victron systems does the same inside the boxes as an internal BMS, but does that job better. Better components, better design, better cooling, less need for cooling due to the better design, and so on.
Hi Stein,
I need to disagree on that. A contactor is not a fuse or over current protection device. Yes, a contactor can break current in an over current situation when everything works as designed but it is not in any way a substitute for a fuse. That’s my point under “Relying on the BMS”.
To stretch this a bit to make a point, thinking that the contactor in conjunction with the master switch is in any way a fuse is like saying that the switch on the wall in your house that turns the lights off and on is a fuse.
I know you understand this, but when dealing with something this potentially dangerous we need to be really careful about our language lest we give someone with less experience the wrong idea.
Hi John,
I agree with every word you say. I was too quick and didn’t notice it. If I was a fuse, that would be me failing to short. 🙂
When i built my Victron 4 x 200 ah system i immediatly posted on the Victron forum if they support MRBF or if we need to install class T. Nobody answered and from a company that must have hundreds of engineer it scared me not to have a very important answer to that problem. I ended up installing MRBF on each battery but after many thoughts i will also add a class T fuse on every negative side of each battery (negative is where the electron get off) without removing the MRBF on the positive pole because for me its a kind of safety not to have direct exposed positive battery pole. And i will add a class T for the global Lithium wire that goes to the battery switch for distribution also. Thanks !
Depending on the rating of your MRBF I think you might be OK.
A class T might be safer, but you give away the potential to mount on the battery stud. Maybe do both?
A class T is much faster, so you do limit the amount of energy available to the system in a short. (MRBF<200ms @ 600% rating vs 10ms @600%)
See this article on discharge current into a short circuit.
Microsoft Word – 13_PE_05_17_67-73_lebkowski
It looks like discharge current is less than 10C in a short for 160AH LiFePO4.
That being said there is not a great amount of good data on current in to shorts.
I did a bunch of research yesterday trying to find good data.
I did find this frighting post for those thinking about 48v batteries. When you have a short with a class T fuse, if you have one bad connection…
https://diysolarforum.com/threads/short-circuited-my-48v-120ah-build-im-fine.17257/post-197941
Hi Tim,
I too did a bunch of research for this article, but I did not find those resources, so thanks for bringing them up. I will spend some more time with them, as soon as I get a moment.
Anyway, as you say, the issue with MRBF is the “might” in all of this, so given that we have Class T fuses and that they are, as far as I can see, intrinsically less likely to fail shorted I’m still comfortable with saying that MRBF should not be used on lithium or large lead acid batteries.
Hi Andre,
The Victron forums seem to be pretty active most of the time, so no answer is surprising. The answers mostly don’t come from Victron employees, but from other users. There are channels to contact Victron officially, but it’s via dealers. They do not at all interact with end users, unless it’s some market stunt. Having millions and millions of customers means they need filtering.
I work with this stuff but I’m no electrical engineer. The following is opinions, not facts. FWIW:
Normally fuses are on the positive, while a shunt is on the negative. Both should work also if that was reversed. It doesn’t really matter which directions the electrons move. As long as there is a circuit, some level of connection between the positive and negative of a battery, power will flow. We don’t need to know which direction. It took many years before anyone knew. It still worked.
There are situations where both positive and negative are fused, (apparently often in metal boats?), but I don’t know enough and I’m even a bit in doubt of its usefulness. I don’t see how it differs from two fuses after each other on the same side. If only the battery is between them, what is really different? If the connection is broken, anywhere in the circuit, all stops.
Having two equal fuses in line will not noticeably add safety, unless we don’t trust the fuses to blow when needed. However, the second one does add complexity, noticeable resistance and voltage drop.
How I’d prefer to do it is Class-T fuse(s) as close as possible to the battery + terminal, directly followed by a bus bar with other smaller fuse types to each main circuit, in or out, some of which going to the control panel with yet smaller fuses. The wires after each fuse level reflecting the smaller fuse. For the minus side I prefer to use gradually branched system, where an oversized cable go to each area and spreads out there, take in all minus from that area. No point in knowing what it came from. It just needs a connection to battery -.
To link this to how I understand your description, I would remove the MRBF fuses and replace them with Class-T. That’s enough for main fuses. When you split up into smaller cables, you need smaller fuses at their start, of course.
I cover any + connection rigorously. I do that with the – side too, for redundant safety, but if all + is insulated safely, no short circuits can happen.
Hi Stein, i am a official Victron dealer registered as AL2M Marine and i can’t have the direct support you are talking of. Maybe if i was selling for a million per year i would. I rely on the forum which is unequal as of support. Sometime you are lucky.
I currently have one 200A MRBF on each positive post of a lithium battery.
Technically speaking if a surge of electron will start to flow it will be from the Negative to the Positive. So by adding T Fuse on the negative i bet they will trigger before the MRBF on the positive 🙂 Much more because they have a faster reaction time. I could build a setup and try it but i won’t short my battery for fun but it would have been so easy for Victron or Blue Sea to do the test and post it on Youtube to educate every one. By the way when you weld with a negative electrode vs a positive electrode the difference is quite visible !
I will talk to my surveyor who’s also a marine electrician to have is view on this. Thanks John and Stein !
Hi Andre,
Sounds like a good upgrade to me. That said, I don’t think it matters where the electrons get off, the key to fusing is to break the circuit, so while it’s unorthodox I think fusing the negative as well should work. That said, it’s a bit idiosyncratic and might cause you problems with a surveyor, so it might be even better to add the Class T to the positive. In my experience, most surveyors are horribly ignorant about electricity when faced with anything different will mark it as non-compliant.
Hi John,
I am glad that you are bringing attention to the AIC rating, it doesn’t get enough consideration. I witnessed a nearly fatal battery thermal runaway in 2002 or so that while not quite related to this fusing topic of protecting wires really helped drive home the importance of AIC to me. This was an experimental electric car using “laptop batteries” as lithium batteries were referred to at the time, I don’t remember the exact chemistry. I also don’t know the pack size but just based on what these experimental cars typically ran, I would guess something like 20-30kWh and most were in the 120-180VDC range. Rules required that packs were fused and had a disconnect (contactor) every 50V or so so most packs had quite a few internal fuses. What happened was that someone working inside the pack dropped a wrench across the most positive and negative terminals which bypassed the main fuses but still had several internal fuses that could have opened the circuit. I was sleeping a few hundred feet away and was immediately awake and saw everything start to rapidly deteriorate. Afterwards there was a lot of discussion around how the team was using regular uninsulated metal wrenches which was highly unsafe but almost no talk of why the fuses didn’t protect anything and why the disconnects were closed. A few of us have hypothesized that the fuses failed closed and allowed current to flow for long enough to allow the thermal runaway. There were a couple different pieces of evidence that all suggested that very high current flowed for a while and I am skeptical that a thermal runway would have started if the fuses had blown quickly. The actual evidence is no longer available and I am relying on memory only but it was quite an experience. I actually ran into a marine electrician this summer who had been on another team at the same competition and when I made a joke about how many lithium installs he probably did, he stated that the fire had scared him enough that he wouldn’t do any lithium installs until the industry matured.
I see actual AIC events as a bit of a probability thing but not one you treat that way in design. Most shorts are not perfect no resistance ones but I am not going to play that probability game and try to rely on resistance to keep the current down. I have found a few different examples of bad starter cable chafe against an engine and shorts don’t get much worse than that although thankfully I have always spotted them early enough. One thing that scares me is how you see things like bilge pumps going direct to the battery with only an AGC fuse in between which has a really low AIC rating.
Eric
Hi Eric,
That’s a sobering story indeed and highlights a danger I have written about before: even if we have Class T fuses within 7″ dropping a tool across the terminals can be spectacularly bad. Many think that MRBF fuses solve this issue, but in some ways they make it worse because it’s difficult to properly insulate the whole mount. They come with a silly little plastic cap, which is useless and a fig leaf at best. I resorted to a lot of self amalgamating tape on the J/109, which kind of works, but it’s far from ideal.
And I agree that how much current will actually flow dependant on how the short occurs and that many (probably most) the current will be less than the battery can theoretically supply, but, as you say, we can’t design for that.
I only have 2x100Ah lithium batteries but even at that level the fusing problem is bugging me.
I want to fuse at 1C, that’s what my user manual says is the max safest load and the smallest class T fuses by blue sea are 110A. With the response curve, I think even 1C is generous.
The Lynx fusing situation is actively ignored on every Victron forums I’ve seen. The only responses were about shaming the questioner as paranoid and pushing the Lynx cool-aid
Hi Mathieu,
I think separate Class-T for each should be fine, the difference is just 10 amps, that is as long as the cables are heavy enough that they will be protected by a 110 Amp fuse and if not they should be changed anyway.
And I agree that while I like Victron products a lot, the Lynx distributor is a mistake. The bottom line is that the AIC is woefully inadequate, but that never did stop fan-boys on forums from behaving badly. Good on you for seeing past that.
Hi Mathieu and John,
I’m a Victron fanboy, no doubt, but that’s only because they have a lot of very good products, often the best there is. The Victron Lynx system is absolutely one of those. The comments made here completely miss the target.
The Lynx system does not use Class-T fuses. Correct. It uses Mega fuses. Those are not suited for fusing a battery bank. Again correct, of course, but so what? A book isn’t suitable for washing a floor. The Lynx system is not at all made for that function. A separate main battery fuse must be placed between the battery and the Lynx system. This is totally clear in all documentation.
The “Lynx distributor” is the one with fuses. As its name indicates. It’s the starting point of the main distribution cables. It’s also used for fusing inputs to the batteries, like solar regulators. It can never be used to connect batteries.
The Lynx unit that can be used for connecting different batteries or cells etc looks (almost) the same on the outside, but has no fuses. It’s a pure bus bar unit, only for connections, and is called the “Lynx Power in”. Maybe the external similarity between these two fundamentally different units is the cause of this confusion?
Of course it’s possible for incompetent customers to use the Lynx distributor for connecting batteries, but such a user may also connect the whole boat system without a single fuse. We can’t judge a product from how it can be misused.
On the other hand, I think it would be very nice if Victron also made a unit of similar type that integrated a Class-T main fuse and perhaps even one meant for Class-T fused connections between batteries.
I doubt if they will make this, as there are fully good alternatives on the market, while the general awareness on AIC and Class-T fuses is low, so the sales volume might not be sufficient.
Stein why do you say the Lynx Distributor shouldn’t be used to connect batteries? What do you see as the down side to having fuses at both ends of parallel battery cables? I’ve actually had this design recommended to me by a Victron system designer since if one individual battery fuse blows it could
create an overcurrent situation in the other battery cables with fuses at the battery end of the cables.
Hi Jim,
The reason is that the Mega fuses are not suited for that task, due to their way too low AIC, Amp Interrupt Capacity. As long as there is a main fuse for all the batteries that can handle anything the total pack can deliver, this system with Lynx can be used, as the fuses aren’t necessarily needed, but I’d do it differently. Making it work well is more important than making it look good.
The Distributor can’t use the physically larger Class-T fuses, which are suited. Class-T fuses of decent quality are also dramatically more expensive, which is probably why they’re not more used.
My guess is that the “Victron system designer” didn’t work for Victron and that his credentials were no better than mine, which is: Zero! 🙂 That means my claims are only worth that much… I still work with big battery banks, but the marine business has a mostly useless qualification system and loads of big claims with no substance. “I could get some exams, but why should I?”
By the way, I love your tip about using a split see through hose and zipties for insulating battery terminals etc. So simple and good it annoys me I didn’t think of it. I have at least one spot on my boat that needed that tip.
Hi Stein,
Looks like they are: https://www.marinediagnosticservices.com/product-page/lynx-class-t-distributor-m10
And given that it has just two fuses in it, it might be just possible to mount it to honour the 7″ rule.
Hi Mal,
Yes, isn’t that great. Selling the old units for battery fusing was a blot on an otherwise good company.
That said, I still like the Blue Sea class T mount better because it will be easier to honour the 7″ rule using it.
I’m also a Victron customer and I like a lot of what they do. Perhaps I also have a part of bad faith in my original comment.
If you want to talk about the doc, it says to use a lynx power-in or “fused lithium batteries”. And the nice connection diagram that comes with those recommendation does a great job of omitting the fuse. They also say that you can connect 4 batteries to the power-in but it only has 2 class Ts. That’s also ignoring the near impossible geometry of connecting two, let alone 4 batteries with 7 inch cables to the power-in.
On top of that, lynx only monitors the distribution fuses. I don’t know about you but I’ll notice systems going dead when the outbound fuse blows. On the other hand, it could take a while before I notice that one out of N batteries is out and I’m running on reduced capacity.
Bottom line, the Lynx system is beautiful, *expensive* piece of kit but to me it’s a solution that’s looking for a problem.
Hi Mathieu,
I agree that the Lynx system is often not the right solution. However, it does make it easy to start a tidy and protected system that saves wall space. Sometimes it’s also about equal in cost to separate bus bars of similar quality. A larger number of separate parts are needed then.
It’s very easy to use the Power in module with fuses too. Just buy the fuses and 8 suitable bolts. 8mm if I remember correctly. Hex head. Everything else is the same. Saves some money by skipping the electronics and LEDs.
For connecting batteries I’d use other simpler methods. The blown fuse indicators on the Distributor are overly fancy for my taste. I’d prefer to rig a little LED at the panel for that. No electronics needed.
For watching individual batteries joined up, I think I’d want a Voltage meter for each battery? Perhaps with an alarm? Kind of a primitive BMS. For connected drop-in lithium batteries, I’d probably want something more advanced. I’ve never done that.
We only use separate cells connected directly to each other and a BMS watching each parallel 3,2V string. No need to watch each cell. If one goes off, the BMS can tell, from the string average changing a bit related to the other strings. Very reliable.
Thanks for the clarification Stein that makes perfect sense regarding the fuse selection in the Lynx Distributor. The stacked configuration of the Lynx is attractive for space savings but certainly not worth it at the expense of proper OCP.
Hi Stein,
You make a logical case, but unfortunately it’s not true to say that Victron don’t try to sell the Lynx distributor as a battery fusing solution. Please see this schematic from Victron where the Lynx distributor is used for just that on a suggested set up for a catamaran: https://www.victronenergy.com/upload/documents/Manual-&-Drawing-Catamaran-setup-Quattro-5kVA-230VAC-24V-Extra-Alternators-&-WS500.pdf
Also, note that you, yourself, suggested the Lynx distributor for battery fusing some years ago. And note that in my answering comment I did not pick up on the problem with the fuse either: https://www.morganscloud.com/2021/12/05/protecting-our-boats-underwater-metals-from-corrosion/#comment-301019
If MEGA fuses are so poor, why is it that Victron uses them in their key distribution units (e.g. the Lynx distributor?) The issue with AIC is going to be present regardless of marine environment or otherwise, and Victron specifically supply this kit for really large systems.
Surely the people at Victron had a long discussion when deciding to use MEGA fuses as their primary fuse architecture.
Hi Stuart,
I have no idea. But the fact that is that the AIC on those fuses is just 2000 amps not enough to safely fuse even a small lead acid battery, never mind lithium: https://lifelinebatteries.com/wp-content/uploads/2015/12/Internal_Resistance_and_Short_Circut_Current_of_Lifeline_Batteries.pdf
The other problem with the Lynx is that when using it for battery fusing there is no practical way to honour the 7 inch rule.
Bottom line, the Lynx distributer is both dangerous for battery fusing and non compliant with ABYC and almost certainly CE (I don’t have a copy of that code) so if a fire were to occur on a boat with one the insurance company could easily refuse the claim even if the Lynx was not the cause: https://www.morganscloud.com/jhhtips/insurance-claim-denied/
How did this happen with an otherwise good company? I have no idea, but in some 50 years in this game I have seen many dangerous products sold for years. I think what happens is that even though the problem is obvious and undeniable the very human reaction is to circle the wagons and go into denial. We humans are not good at admitting we are wrong.
Another good example is the dangerous tethers that Spinlock, another good company, sold for years after one had contributed to the death of a crew on a Clipper boat: https://www.morganscloud.com/2018/04/08/time-to-stop-using-and-selling-tethers-with-gibb-style-hooks/
Hi Stuart and John,
See comment on this topic just above here. In short, Victron Lynx cannot be used as a battery main fuse. It’s not made for that. The unit with fuses is called the “Lynx Distributor”. The name says it all… Mega fuses are totally fine for that function.
Hi Stein,
See my comment that Victron are specifically selling the Lynx distributor for fusing batteries.
Sounds like Victron is coming out with a Lynx Class T Power In module to address this.
https://www.victronenergy.com/upload/documents/Lynx_Class-T_Power_In/165891-Lynx_Class-T_Power_In-pdf-en.pdf
Great article John. I think I brought the AIC issue and Class T fuses to your attention some years back in another battery related thread – but I’m delighted to see how you have expanded on this so comprehensively.
As someone with a strong lifelong industrial electrical background I fully concur with your conclusions.
The only thing I would add is the observation that the battery’s potential short-circuit current is going to moderated in most realistic scenarios by the added resistance of the battery cables distance from the terminals to the point of the short-circuit. For most installations – IF the first meter or so of the cable runs are well protected – it’s extremely unlikely the short will occur so close to the battery that the full multi -kA current will flow.
Many experienced designers have rule of thumb that says anything more than about 200A in any given conductor should give pause to re-think what you are doing. If this rule is observed the cables are going to be small enough to be contributing some useful current limiting resistance over the first few meters.
Of course this does not detract from any of your core points – but it does suggest that at the 20kA AIC of Class T fuses levels – the battery cables are likely to be giving some extra safety margin in the design. Even if by the book it’s not strictly accounted for.
HI Philip,
Yes, I agree that the chances of the full current that the battery can theoretical supply actually flowing in a short circuit is slim. Eric made the same point earlier in the thread. That said, as both you and Eric point out, it’s prudent design to fuse for the worst case scenario, not the most likely. As to cable runs being “well protected” I think that’s more problematic. Sure, if they really were properly protected, but the reality in the field that I see all the time on AC cables is a bit of split wrap and call it good, clearly not adequate. I don’t think I have ever seem wiring on a boat with real protection that would withstand long periods of chafe. Any ideas how that could be done relatively easily, particularly in a retrofit situation, with off the shelf available products?
https://www.mcmaster.com/products/chafe-guards/
Every installation will have it’s own considerations – but this is a good overview of the options. Industrial spiral wrap performs very well – and while expensive we don’t need a lot of it.
Hi I enjoyed reading your lithium articles and Halifax harbour. We enjoyed NS on our way back to Scotland after the ARC on to Newfoundland and the Viking route. We have a Malo 42. Separate 12 and 24 v alternators. Currently lead acid 430 Ah 24v service bank. So we can’t use the starter battery as the buffer I don’t think?
Recent article in PBO on lithium also. Tempted to stay with LA with our set up having two alternators?
Jon
Hi Jon,
As a general rule I don’t like using engine banks as “buffer banks”. More here on a better way to backup lithium: https://www.morganscloud.com/2022/07/03/building-a-seamanlike-lithium-battery-system/
I am having a hard time visualizing how you both meet the 7″ rule for a class T from each battery terminal, and also meet the best practice of equal cable lengths from all battery terminals to the main bus. Anyone have some links to example designs in practice?
Actually, I finally found a post from an installer in Florida providing a way to do this. What they are doing is running a piece of bent short copper bar from the battery terminal to one leg of the Class T for each battery. Everything is insulated and it sits on top of the battery. Then equal lengths of wire are run to a common bus, in this case a Victron Lynx distributor.
Hi Tom,
Each battery, or at least each series string of batteries should have a separate class T fuse. The reason is that if one battery in parallel with others shorts out with no fuse in the line there is a very good chance of a fire or even explosion. See above article for more.
So I strongly recommend against paralleling the batteries before the Class T and would further recommend against listening to anyone who would advocate for that.
So once we have a Class T for each battery (or series string) it’s comparatively easy to have the same length cables running from said fuses to common negative and positive buss bars.