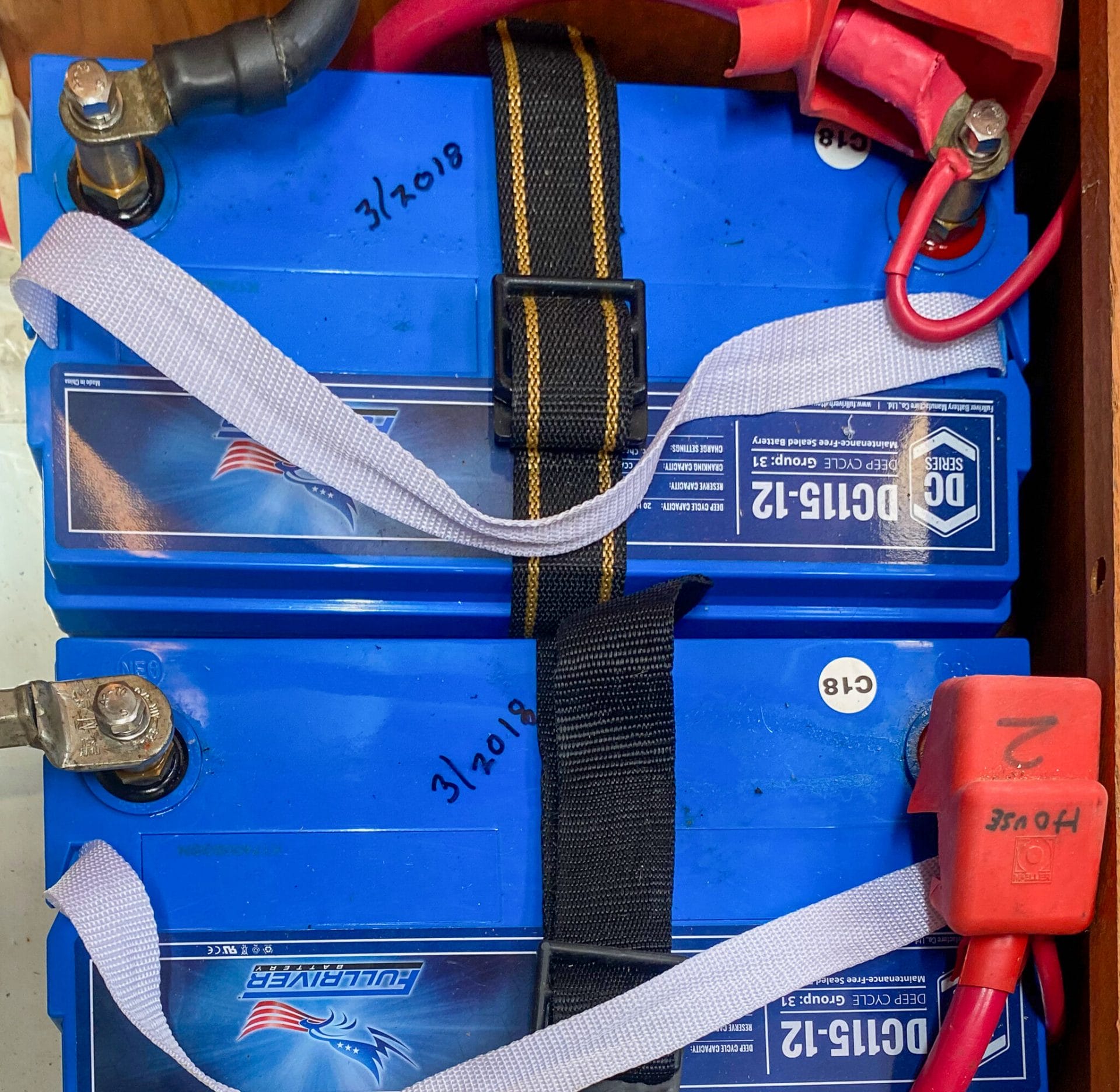
Not Fused
Before we dig into how to upgrade our boat’s DC electrical system, we need to check for potential boat-burners.
Two thoughts on that:
- I’m pretty sure that fires started by 12- and 24-volt battery-supplied systems are a common cause of boat losses.
- I would also bet that more fires are started by 12- and 24-volt systems than by shore power 120- or 240-volt systems.
No, I don’t have accurate statistics on this, and I’m guessing that, as is typical around recreational boating, no one does due to poor or non-existent reporting requirements. But using poor reporting as an excuse for inaction would be stupid…err…unwise. (If you know of useful stats on this, please leave a comment.)
What do I base this on?
The current (amps) in even a single small 12-volt lead-acid battery can turn any conductor with low resistance (think a length of wire) red hot, thereby starting a fire.
And the amount of dangerous amps lurking in the huge battery banks we see on modern cruising boats is positively mind blowing.
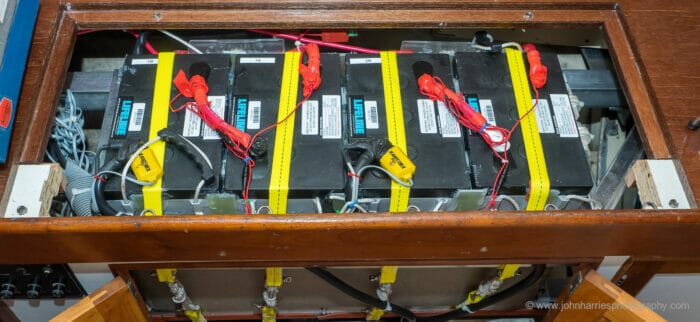
Wait, it gets worse. On many boats, even ones built comparatively recently, like our new-to-us J/109 (2004), the only over-current (short-circuit) protection is on a breaker/fuse panel, leaving the high-current conductors connecting batteries and alternators completely unprotected.
Contrast that to the shore power system that typically carries ten to twenty times less current (amps) and is pretty much always properly protected against a short-circuit-started fire by fuses and/or breakers.
(Shore power systems kill people, but that’s another article.)
Hi, here’s some stats that I had run into. Nigel Calder had these 2009-2013 BoatUS stats on his new website, that indicate ~55% of fires start from electrics, and roughly third from DC side.
https://boathowto.com/electrics/fuses-circuit-breakers-on-boats/
Then, here’s more recent 2015-2019 statistics on BoatUS article:
https://www.boatus.com/expert-advice/expert-advice-archive/2021/february/analyzing-onboard-fire-claims
Again, roughly third from DC.
Cheers, PF
Hi Petri,
Thanks for finding that. Looks like the percentage of DC caused fires when measured against AC is even worse than I thought with Nigel saying:
And boat US saying that DC fires are over three times more prevalent than AC fires
Hi John,
I came across this in my notes for some past writing, perhaps from the same source:
Boat Fires
1. 26% start off the boat
2. 20% due engine electric
3. 15% other DC elec
4. 12% AC elec
5. 9% eng
6. 8% batteries
Hi Dick,
The source that Petri found (Boating US) says it’s much worse than that, but a lot of this will depend on sampling method, so is far from definitive but all agree that DC shorts are a big cause of fires, so I think that’s what matters.
I want to add that it doesn’t suffice to add breakers, especially for switchable/resettable breakers. These should be from a reputable manufacturer, e.g. BlueSea Systems, and not some cheap breakers built in ~somewhere~ 😉
For my two house circuits I had purchased two cheap 50A resettable breakers. Then I made an error in the cabling, producing a direct short circuit, which I initially didn’t notice, however when flipping the battery main switch the aft cabin (where the breakers are located) quickly filled with smoke. The affected breaker did not open but instead started to boil, and more or less welded its internal contacts, making things worse…
See attached images
Hi Ernest,
Wow, that’s a scary story.
A question for you. What size fuse or breaker is between the breakers that failed and the batteries? The reason I ask is that if that fuse is a big one, then it might be that the dead short current exceeded the breaker’s interrupt current limit without blowing the up stream fuse. And a follow up, do these breakers have an interrupt current limit printed on them. Might be called Amper Interrupt Capacity or AIC.
I’m asking all these questions because your comment made me realize that I should have added a section to the above explaining the difference between trip current and maximum interrupt current and why it matter. Definitely need to fix that.
Hi John,
directly behind the house battery positive terminal there is a 500A Mega fuse. A 70mm2 cable goes to a T-Bone and then to the 1-2-both master switch.
The circuit with the failed breaker originated at the master switch with 16mm2, approx. 15cm (~6″) to the failed breaker, then continuing with 15mm2 for cm (~7″) to a bus bar, from there 25mm2 approx.7m to the switch panel at the nav station.
The wiring fault occurred at the said bus bar where I connected a preexisting red-coded cable which I believed would power the front cabin, but actually was connected somewhere to neg.ground… I know, I should have used my multimeter before.
The breakers have no additional AIC or similar, only printed “50A” on them. As I do not want to advertise them here I’m sending you the product link by mail.
Since the failure I exchanged both of the cheap no-names with this model of BlueSea Systems, having an ACI of 5000A @12V: https://www.amazon.de/gp/product/B000MMH20W
Hi Ernest,
Thanks, and for the link to the breakers that you sent by email. I think we can state a new rule here “Ernest’s Law: never use a breaker or fuse that does not have ACI clearly specified by the vendor.” I have to say that I really would never have thought of that either, but now you brought it to my attention, clearly I should have made more of the ACI in the post above. I will fix that, thank you!
One other thought. Why such a big fuse on the battery? 70mm2 is equivalent to 2/0 and by my calculations the fuse should be half that? http://assets.bluesea.com/files/resources/reference/20010.pdf
Even with 4/0 cable the fuse is only 300 amps.
John, you’re absolutely right – I once (mis)calculated and never challenged – will change these fuses when I get back to the boat.
As to the BlueSea PDF, 2/0 inside the engine room would allow for 300A, which should be sufficient for even the starter circuit (28hp Hatz Diesel).
Thank you for the heads up!
I’ve seen that kind of breaker before. I’d bet a beer that you will find no CSA, UL, ETL, TUV, or other recognized certification marks on its case, and that if there is a brand name, it’ll be something that nobody’s ever heard of.
The common abbreviation is AIC, ampere interrupt capacity. As an aside, class T fuses should be used with any primary battery bank supply wiring, they have an AIC of 20k amps, compared to ANL’s which are commonly and incorrectly used, and cheaper, which have an AIC of 6000 amps, which is easily exceeded by two 8D batteries’ fault current.
Hi Steve,
I agree that class T is the way to go on big banks. That said, they take a lot of room. So on, for example, my J/109 I’m using space saving fuses from BlueSea. The AIC is 10,000 amps which is 10 times the CCA of the bank, so should be fine: https://www.bluesea.com/products/5190/MRBF_Terminal_Fuse_-_300A
I like the MRBFs in 12 volt applications, where they have the necessary AIC, they have made life much simpler in many installations. For 24 volts the AIC is lower. On that subject, the 24 volt discussion is an important one, to many builders, IMO, cling to 12 volt where 24 makes much more sense. Any vessel over about 35 feet benefits from a 24 volt system. When I built 36 foot lobster yachts, I calculated we saved about 1000 lbs. in wire weight by switching to 24 volt.
Hi Steve,
Good to hear on the MRBF fuses. I put mine in yesterday and it’s hard to see how I could have fitted anything else in to the very small area available on our J/109. That said I will punch up that this is only for small banks when I write about it, thanks.
I have always liked 24 volt too, and after a day spent wrestling 2/0 cable and lugs I like the idea even more!
For others: I look at the decision in this two parter: https://www.morganscloud.com/2020/12/10/should-your-boats-dc-electrical-system-be-12-or-24-volt-part-1/
Just a quick comment. When I used to work as an electrician, we had to do calculations to avoid this exact problem in case of a high load or a short far out on a wire, that they break fast enough for the cable to not exceed a specified temperature, to balance between the different fuses/breakers so that the correct fuse/breaker would trip and that the whole spectrum was covered, and that they have the breaking-power of the current that can be generated.
These are Norwegian requirements (which are somewhat special since we use high power heaters that can overload a wire without the current tripping the fuse/breaker), but I would assume there are similar stuff in English. Sadly I don’t have a link, as it’s all in Norwegian and in paper.
Hi Arne,
Good point, ABYC has similar requirements and tables and the App from Blue Sea takes it up a notch for DC systems by adding the cold crank amps of the battery bank into the calculations and then using that to calculate interrupt capability, with, I suspect, a large safety margin.
Well-done and an important subject, especially the over-current protection aspect. Lack of OCP, or improper placement of OCP, is the number one electrical issue I identify in vessel inspections I conduct. I can find it on virtually every vessel, it’s the thing that keeps me up at night more than any other onboard short-coming (pun intended). I too worry about DC fires, and AC electrocution.
You are understating the severity of the amperage supplied by a short from batteries. The fault current supplied by a battery can be 4-5 times its CCA.
I may be mistaken, however, the small gauge red wire shown in the third photo looks like it is much longer than 7″ before it is fused. Also, if it’s smaller than AWG 16, it is in violation of ABYC Standards.
If ABYC compliance is the goal, alternators actually need OCP at their output, as well as at their connection to the batteries if…
ABYC E-11.10.1.1.1 #4. Overcurrent protection is not required in conductors from self-limiting alternators with integral regulators if the conductor is less than 40 in (102 cm), is connected to a source of power other than the battery, and is contained throughout its entire distance in a sheath or enclosure.
#5. Overcurrent protection is not required at an alternator if the ampacity of the conductor is equal to or greater than the rated output of the alternator.
Essentially, this means after-market alternators with external regulators whose output cable leaves the engine, require OCP at the alternator.
A common issue, and ABYC violation I encounter all too often, is starter positive cables making contact with the engine (if they are fused, as you recommend, it’s less of an issue but still a concern, I never rely 100% on a fuse). The positive starter cable should leave the starter and not make contact with any part of the engine, brackets, transmission or motor mounts.
Balmar does call for the voltage sense to be placed at the alternator output stud. This is safer, but offers less accuracy.
Re. #6, this issue can be avoided by placing the regulator near the batteries rather than near the alternator. Voltage drop from the regulator to the alternator is a non-issue as it is compensated for, while voltage drop from the regulator to batteries is an issue, for which there is no compensation, at least not automatically.
I deal with so many OCP violations, with boat owners and builders alike, I wrote this article on the subject, to try to educate them and save myself some typing time when writing reports. https://stevedmarineconsulting.com/over-current-protection/
Again, you’ve covered a critically important subject that will likely prevent fires.
Hi Steve,
Great comment as always and brings up several interesting points. Here’s my thoughts on that:
True, but that number (maximum short circuit current) is highly battery specific and very difficult to get from the manufactures and given that CCA is generally used to calculate the fuse’s maximum interrupt capability by apps like the excellent BlueSea circuit wizard, I elected to keep things simple and used CCA which is readily available. Later I will talk for about interrupt capability and particularly lithium and bring out the huge safety margin we need.
True on both counts. In my defence that’s the way the battery sense leads came from Victron who are a European company and therefore don’t always comply with ABYC. By the way, I think the 16 AWG minimum is out of date in the age of very low current solid state devices, at least as long as everything is fused to protect smaller sizes. (I’m used AWG 18 to wire a bunch of very low current stuff, in compliance with the manuals) Definitely suggest ABYC revisit this.
I nearly wrote that, but after a lot of thought decided that fusing at both ends has more downsides than upsides since it gets us into my #6 problem. While it’s certainly possible to have a problem from not fusing at both ends I think it’s unlikely enough that the dangers of an out of control alternator due to sense wire separation are worse. My thinking is that most any alternator shorted to ground in such a way that the fuse close at the battery end of the fuse cable does not blow (very unlikely) will quickly blow the diodes and or coils and so self fuse. Also, this will only happen when the engine is running and people are around to deal with it. All that said I agree that fusing both ends is debatable (particularly with very large alternators) with pluses and minuses on both sides. I will bring that out in later articles.
If so, they must of changed their instructions since all the Balmars I have installed over the years (at least 4) called for the sense wire at the battery positive post—that’s how I learned about the problem the hard way! I’m guessing they made the change because they were too lazy to make the changes to the manual to really explain the issue properly. Anyway, I don’t recommend using their regulators at all, since we now have the much better options from Wakespeed.
Disagree with you on this on this one. The sense wire, on a good regulator that has a separate power wire, only carries milliamps (maybe microamps) since it’s not powering the regulator, therefore distance to the battery or length of the sense wire (within reason) has no effect on the issue.
The voltage drop I’m writing about here is that from the battery post to whatever point the sense wire is attached, for example the load side of a 1-2-both switch or the fuse protecting the alternator feed wire at where it connects to the main positive buss bar. Here the voltage drop can be significant since the entire output of the alternator is being carried, and often the cables are too small or there are too many poorly executed contacts or fuses in the chain.
I have actually tested/measured this voltage drop, on a larger vessel it can be significant, which in this scenario can be as little as a tenth or two of a volt. If the sense wire is run directly to the battery, my preference the highest accuracy is achieved, and it avoids the voltage drop issue you describe, and locating the regulator near the battery makes that run short, more reliable and easy to protect.
Hi Steve,
That’s interesting. My guess is that having said drop is regulator specific, and happens where they are using the same wire to power the regulator. Could be a poor contact too.
But in the case of say a Wakespeed, or the Balmars with separate sense wires, that wire is just being used as the input to an analog to digital conversion IC, so the load will be so small (milliamps) that even with #16 wire and say 40 feet the drop would be negligible.
In fact I just calculated that and even assuming the sense wire load is 0.1 amps (almost certainly way higher than it is) the voltage drop over 40 feet of wire is just 8 millivolts. Not enough to change anything.
As to putting the sense wire on the battery, Al, who designed the Wakespeed, specifically, and a length (bad pun), warned me against that because of the run away alternator problem. And I have seen exactly this problem, (see article above) on my own boat with a Balmar regulator.
I am puzzled by the statement: “#5. Overcurrent protection is not required at an alternator if the ampacity of the conductor is equal to or greater than the rated output of the alternator.”. From what context is this taken? The “conductor” referred to cannot be the voltage sense wire, so that leaves the wire from alternator to battery/buss. I must be missing or misreading something.
Hi Andrew,
I would have to check ABYC to be sure, but I’m near-certain that this refers to main feed from the alternator, so that would seem to support my contention that only one fuse is required at the battery end. I will dig deeper into this as we go forward.
It does refer to the main output wire. Indeed, if only one fuse is used, at the battery end, the short circuit remains, pumping current into the block for instance, without overheating the wire, the alternator simply sees it as a load. If you are OK with that, I’m not, then only one fuse is required. Interestingly, Caterpillar uses a CB on the output of most of their alternators even though they are internally regulated and the output goes from the alternator to the starter, a short, harnessed run.
Hi Steve,
That’s a good way to explain it. That said, for that to happen the wire would also need to be disconnected from the fuse at the positive bus end, which I think is unlikely given that there is no vibration that end. And further the operator would need to not notice that the charging rate had dropped to zero and also they would get a low voltage alarm on most engine panels.
Given all that, I would prefer to take that risk, that I regard as very low and have never seen happen, rather than the risk of sense wire separation and alternator voltage run away that I have seen happen, and have been specifically warned against by the designer of the regulator I recommend.
Hi Again Andrew,
Of course this presupposes that said main output conductor was properly upsized to the right ampacity if and when a stock alternator is replaced with a larger one.
I’d like to add a comment on the importance of checking any existing cables already fitted. A friend upgraded his shore power charger from 30 amps to 120 amps and asked the yard to fit it whilst he was away. Before he returned after the winter break he asked them to turn it on – and his boat caught fire. They hadn’t upgraded the cable to carry the extra current.
Hi Matt,
Good to hear from you. And yes, your story makes a very good point. I guess said yard must have also upgraded the breaker so it would not trip with the larger charger and still not upgraded the wiring to take the added load. If I was your friend’s insurance underwriter I would be lawyering up with a view to recovering the claim from the boat yard’s liability insurer.
Possibly avoided by prefacing any (electrical in this case but applicable to many areas) work requests with, “And all work must comply with ABYC Standards and manufacturer installation instructions” and conforming the yard is a member and preferably has certified staff on hand. That is a rookie error of epic proportions. Was the boat a total loss?
So here’s another question or two on #5. This is timely for me since I am upgrading my battery side DC wiring after burning out a 120 amp alternator. The Amptech alternator is on a Westerbeke 35B engine with a serpentine belt and is regulated with a Balmar ARS-5. I believe the cause of the alternator failure was either too much heat (I have now installed a heat sensor on the rebuilt unit,) or a bad connection on the alternator field terminal.
In the upgraded wiring, the current path from the alternator hits the first fuse at the always-on positive bus with the next fuse on the house battery bank positive terminal. The Balmar ARS series has a single power input/sensing voltage wire. If I connect that wire on the alternator side of the positive bus fuse, then I am missing the voltage drop between the positive bus and the battery bank. (Do I also risk losing power to the regulator if the alternator fuse blows?) If I connect the power/sense wire to the battery bank fuse, then I could have the aforementioned separation problem. Seems a conundrum.
Seth Winnick
S/V Nomad
(Sabre 38 Mk I)
Hi Seth,
The base problem here is the ARS-5 which is a very primitive regulator. Bottom line, using the one wire for power and sense is a fundamentally bad design, so that’s the problem to fix by replacing the regulator, preferably with a Wakespeed.
The longer battery life and shorter engine charge times will more than pay for junking the ARS-5 and buying a WS500
More here: https://www.morganscloud.com/2020/07/04/stupid-alternator-regulators-get-smarter-finally/
https://www.morganscloud.com/2010/08/02/agm-battery-test-part-1/
One you do that, then, as long as you make sure that there is no excessive voltage drop as detailed in #6 all will be good.
This post offers to serve as a lesson to other readers who may be as electrically numpty as me.
In contrast to the many who know what they’re talking about here, I’m an ‘electrical dyslexic’ – but I’ll bet I’m far from alone in the cruising community. My eyes tended to glaze over in any discussions about power onboard; there was always a marine electrician who’d handle that black art for me.
Until one day I smelled burning at sea.
I simply could not imagine the hazards around even professionally-installed low-voltage gear such as my AIS. With the instruments on but under sail I was astounded to see acrid smoke and molten plastic dripping from the back of the AIS straight on top of a folded genoa beneath the unit. I was single-handed well offshore at the time and had I been elsewhere but in the cockpit and able to react quickly the results might have been much worse than an early trip to the sailmaker. The picture doesn’t really reflect the volume of smoke or smell but it illustrates the point.
Despite now knowing my Ohm’s Law and able to infer the likely consequences, this has not cured my electrical dyslexia. However, I am much, much more aware and have regular and thorough electrical checks by someone I trust, with me following assiduously in the hope of something actually sinking in. I still can’t pretend to know what I’m talking about, but at least I’m very aware of a shortfall in my knowledge and I mitigate accordingly.
Hi Iain,
Yikes, that is a scary one and sounds like something totally internal to the AIS, so hard to avoid. That said, probably worth checking the AIS manual for the correct fuse size and making sure that’s installed in the power feed.
I found that the “professionals” who installed the AIS on our new-to-us J/109, a couple of years before we bought her, had just piggy backed the power for it onto a 15 amp breaker without fusing it, so we could easily have had the same kind of flare up.
Anyway, your point that we need to watch and learn when anyone one is working on our boat is well made and taken.
Well, you have certainly worried me. But that may be because I have a hard time understanding this all. Not your fault. But let me try: My batteries are all fused at the big positive wires. But the Balmar regulator (I know, I should get a Wakespeed, but other projects have intervened) has both a sense wire and a temperature wire attached directly to the battery accepting the charge. (All batteries are combined when charging.) I can’t remember if Balmar told me to fuse the small sense and temp wires. If so, I am ok there. If not, I understand you to say these wires need to be fused on their way back to the regulator. Similarly, any smaller wire attached to the batteries (or positive bussbar) and going anywhere should be fused or have a breaker sufficiently sized to carry the normal load, but small enough to blow if the small wire might get dislodged or damaged. Am I correct on that? And does that fuse/breaker need to be right next to the battery? Or can it be a couple of feet away? And, you have convinced me, I will join ABYC as a “boat owner.” I have an ABYC electrician coming down soon to install the big shore power ELCI. Hope he knows the rules. Scary to learn that those we rely on may often be ignorant. As you say, self-reliance may be advisable . . . until it isn’t.
Hi Terence,
The Balmar sense wire should definitely be fused, and to be ABYC compliant, that fuse should be within 7″ of the battery terminal.
I have never seen a temperature sensor fused, and in theory there is no need for it because there is no electrical connection to the battery.
And in all cases the fuse should be as close as possible to the battery end or the point where the wire it’s protecting connects to a larger wire, for example the positive bus bar. Again, ABYC demands <7″.
Sounds like you are really thinking about this and taking on the task of making sure it’s done right, which is the main thing.
Hi all,
In a recent issue of Professional Boatbuilder, Jonathan Klopman (Marine Surveyor), comments on the state of lithium batteries on boats. His particular expertise is accident reconstruction and failure analysis.
Of particular interest in the article was his description of the suggestions generated by ABYC’s technical information report which (as I understand it) is a precursor report prior to ABYC developing and publishing their standards for a Lithium install.
I am loath to c&p copywrite material but “Loose Cannon”, with permission of the author, has re-printed the article and it can be found at https://loosecannon.substack.com/p/youre-not-qualified-to-have-li-batteries?s=w&utm_medium=web.
The article also has some compiled fire statistics.
My best, Dick Stevenson, s/v Alchemy
Don’t know if this in on-topic, but here goes: A few years ago O bought a Sterling Power alternator open circuit protector from Rod Collins at Compass Marine. I never installed it, however. I was about to wire it in, but thought I should ask you, John, before I do. Yes or no? Thanks.
Hi Terence,
Sure, since you have it, I would go ahead and install it. Can’t do any harm, and could do a lot of good. Just make sure you ignore Sterling’s instructions to put the connection under the alternator feed cable lug. The higher current connection should always be on the bottom, and that’s also required by ABYC.
what happened to the 2 minute edit feature?
Hi Terence,
You can still edit your comments, and now for 15 minutes, just hover over the little cog wheel on the bottom right corner of your comment. See this graphic for other features of our comment system: https://www.morganscloud.com/2013/11/10/aac-comment-guide-lines/
I’m down a rabbit hole on circuit breakers and trying to understand the difference between UL489 and UL1077. The way I’m reading it, all of the Blue Sea electrical panels are built incorrectly. They only have UL1077 devices for both the main and branch breakers. However, UL1077 is not rated for standalone circuit protection, it’s only meant for protection downstream of a UL489 branch circuit protection device. It’s also only meant to protect a single device, not for example a series of outlets. Am I reading this right, or does ABYC provide different guidance? Maybe it’s a topic you’d like to tackle?
Hi Stephen,
I really don’t know. That said, I have never heard of actual issues with BlueSea panels so that’s probably not a research project I would take on given that I have my hands well and truly full with issues where I know there are problems that need light shone on them.
Anyone else have any insights or has anyone had problems with Blue Sea panels?
Re: which end to fuse? As the article indicates, one scenario for shorting the alternator wire is vibration causing the wire to fall off the alternator terminal. Since the shorted battery current is more than the alternator’s output, a fuse at the main positive buss (which I have never had before) makes the most sense. I am implementing the improved fusing that seems so obviously necessary now that I have read this article (thank you, John), but I am thinking about the chafe/shorting that could theoretically happen anywhere along the wire, while the alternator is putting out current. The compact terminal fuses designed for battery posts are very convenient to install and very affordable. It seems tempting to install one on the alternator stud in addition to fusing at the buss. This adds two bolted connections at the alternator instead of just one, so doubles the vibration risk, I guess. It will also more than doubles the resistance present. I am not sure that those are compelling reasons not to add the fuse, but I feel there must be a reason not to, or it would have been alluded to somewhere. I am wondering iof the answer might be that the alternator will fail in the case of a mid-run short just as safely as it would fail in the case of opening a fuse on its output while running. I am not sure about that. Any comments would be appreciated.
HI Andrew,
I have thought about that quite a bit and would not add a second fuse because of the danger of said fuse or it’s mount failing resulting in the sense wire being separated from the output, which can fry every piece of electrical gear on the boat and the alternator. The key point here is that the alternator is a current limited device the fuse must go, as you point out, at the battery end, since the battery has a huge potential dead short output capability.
Two late questions. My Balmar regulator has a sense wire connected directly to the battery that first receives the charge from the alternator. (Combiners connect the other batteries at 12.75 volts or thereabouts.) Balmar includes a 1 amp fuse in the sense wire. Do I understand you to say that if that fuse blows for some reason, all hell will break loose? Second question: The positive post of all three of my battery banks are protected by MRBF fuses. I take it that is satisfactory as long as the fuses are sufficient to protect the wires in case of a dead short. The few smaller wires connected to the batteries are all separately fused next to the batteries. (Yes, I know, I intended to get a Wakespeed, but I ran out of time and money this year.) Thanks, as always.
Hi Terence,
No, if the fuse in the sense wire blows, the alternator will simply stop charging. Or at least that’s the case with the Wakespeed and I’m pretty sure the same applies to the Balmar. #5 (above) applies in cases where the main charging cable from the alternator can be disconnected from the battery with the sense wire attached, say in the case of a 1-2-both switch.
As to MRBF fuses the key here is can the battery (in a dead short) supply more current than the fuse can interrupt? That limit can be found here: https://www.bluesea.com/products/5189/MRBF_Terminal_Fuse_-_250A
If so the MRBF should be replaced with a class-T
On a practical bases that means that small lead acid batteries (think Group 31) can use MRBF but all lithium batteries and large lead acid should use class-T.
Re:#5 Alternator sense wire. Thank you for raising this important issue. Attaching the wire on the alternator ( one of several suggestions in the Balmar installation manuals (mc-614 and earlier ?) , which would ensure this issue cant happen,but sacrificing accuracy. So if one has the ability to switch alternator output to a different bank , perhaps in an emergency, what suggestions do you have to ensure the sense wire “follows the alternator output”
Hi Craig,
Good question. I have been thinking about that in relation to our recommended lithium backup after a similar point was raised: https://www.morganscloud.com/2024/03/06/lithium-batteries-buyers-guide-part-3-current-amps-requirements-and-optimal-voltage/#comment-310190
But the problem is the shunt, and then only with really smart controllers like the WS 500 that have them, not the sense wire, which should always be on the alternator side of anything that can break the circuit to the battery: switch to change banks, fuse, whatever as specified above in point #5.
And that should not result in much accuracy drop because the switch can be close to the batteries so the voltage drop will be small.
And although the shunt would remain on the lithium side when switching the charge buss to the backup bank, the lithium side would be down and so no charge current would be flowing through the shunt, so the Wakespeed would just assume the lithium battery was fully charged and drop to float mode so the lead acid would not be charging much. At that point we can just switch over the backup alternator controller with a two pole switch in the power line to each controller so only one can be active at a time. Standard practice with a backup alternator controller.
I plan to update our recommended backup bank article with this, unless anyone can see a flaw in it?
Hi John,
Craig’s comment got me reading your point 5 again and I found it more than a little alarming that you saw 22V with a disconnected sense wire. Do you mind sharing what alternator regulator that happened with? If I have the same one, I may need to think harder about how to protect against that failure modality.
The reason that I ask is that it seems like really poor risk management was done on the design of that unit. If doing something like design failure modes and effects analysis, some of the first lines I would expect to see would be what happens if each I/O becomes disconnected or shorted to something. You would then find that a disconnected sense wire would result in dangerously high voltages that could not only harm electronics but cause some real exciting stuff to happen in the battery compartment. But this also shouldn’t be that hard to mitigate against in design. The whole point of a sense wire is to deal with voltage drop so you could limit the regulator to a maximum mismatch of something like 1.5V or just set the max alternator voltage to 1.5V above commanded and that should take into account even poor wiring practice. I think that all the regulators I have used have always had a direct connection to the alternator positive terminal for powering the regulator so you are already electrically connected to do this and it becomes a firmware implementation only in all likelihood.
Eric
Hi Eric,
It was a Balmar “smart” regulator, if memory serves a MC-618. And yes, now you say it, I think you are right, it’s crazy that these regulators do not have any fail safe programming in them, particularly since the method you suggest should be fairly easy to implement.
Next time I’m chatting to Al at Wakespeed I will ask him whether he has done anything in that way, and if not, why not.