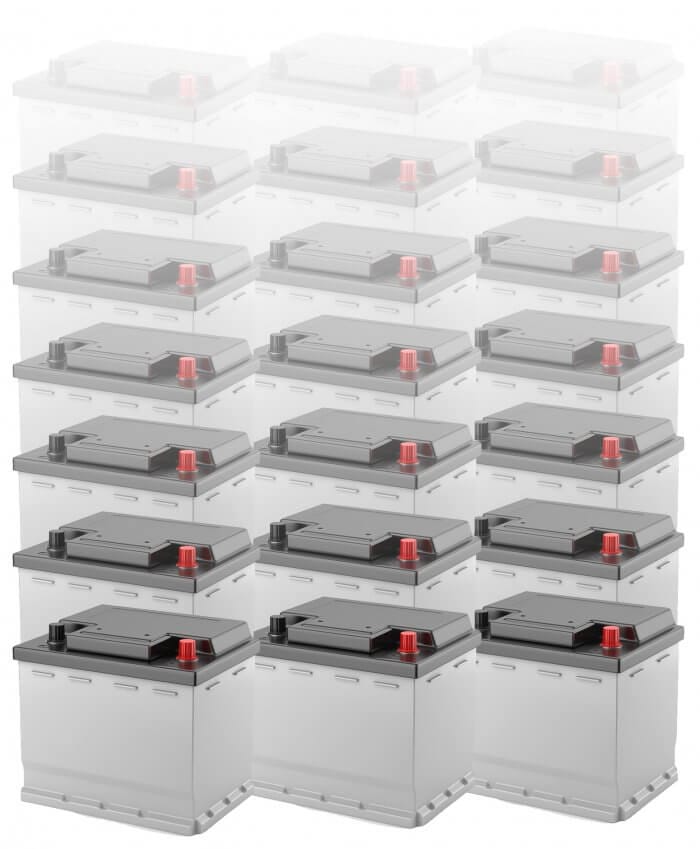
In Part 1 and Part 2, we took a deep and considered dive into analyzing the electrical loads on our boats and thinking about ways to reduce said loads through smart systems thinking.
(If you have not read those articles, please do so now, otherwise this one will make no sense to you.)
In this chapter we get the payoff for all that hard work: How to calculate optimal battery bank size or, alternatively, how to live with the bank we have. And I have built a spreadsheet to make the whole process easier.
Note: To help things simple, I have assumed 12 volts, but if you have a 24 Volt system just divide by two.
Let’s dig in:
Lot of interesting information there. I like it. But I think you made a mistake here:
Wind: zero when at anchor and say 10 Ah/day sailing in lightish air downwind.
Solar: Assuming a reasonable sized array without much shading on a sailboat, but worst case conditions, 20 Ah/day.
Wind generators: given the poor reliability track record of these units, I would not take them into account at all—if it dies at sea, we will need the same battery bank size that we would without one. If it works, cool.
I would consider wind and wind generators as the same. Was the first one water generators?
Woops. Thanks for catching that, I will fix it.
I used a Watt & Sea hydrogenerator to provide my power on a race / trip to and from Hawaii and it worked great. Underway it more than handled our electric needs for that 13 day trip. However one issue with 100% renewables is that you need another way to heat domestic water since the engine heat isn’t available. We ended up running the engine for a short time each day just to make hot water.
Hi Paul,
Glad to hear there is someone else out there who is too wimpy to shower in cold water, other than me. 🙂
Running the engine a short time once/day on an ocean passage is good practice to detect
problems.
As Captain Ron said. “If anything is going to happen, it’s going to happen out there”
This is a handy spreadsheet, and, unsurprisingly, I do not question your figures. We have one of those big banks, plus four panels in an arch over the stern and a yet-to-be-installed wind generator. But the “fast boat” thing was never going to happen with a full keeled steel motorsailer as we have, so having a circa 1100Ah bank directly beneath the center of effort (basically three metres under the gooseneck) is part of the internal ballasting and plays a role batteries usually do not. We’ve chosen small generators (a pair of Honda 2200s) as “tertiary” charge sources and ways to run standard power tools without resorting to the “lossy” inverter process. And I’m going to very likely get a Mark Grasser externally regulated alternator to make amps while motoring, as that’s unavoidable and I may as well make water then, too. And hot water, then, too! That said, our projected energy budget is lower than most, because we don’t have the appliances some cruisers sport.
These measures work to the strengths, such as they are, of the boat we have, which will let us cross oceans at five, instead of seven, knots. So we’ll need a drogue, too, because we can’t outrun weather so well. The logic for an oceangoing catamaran or a “fast” mono with shallow bilges would be necessarily quite different when it comes to positioning and keeping charged big boxes of acid-covered lead. Your spreadsheet is very useful in helping to focus those concerns, even if it leads some to rethink refrigeration and the value of a wind vane!
Hi Marc,
Glad the spreadsheet is working for you.
Anything that helps sailors to think critically about what’s important to have on their boats is worthwhile. Perhaps an extra comment would be that the loads bigger alternators draw from a running diesel may drive a lot of other decisions. When we went from a 52 to a 60 HP diesel, I always planned to use that margin to spin a bigger alternator, which was feasible thanks to the acceptance of a larger bank and heavier cabling. A very rough estimate is that 200 amps @ say, 14.4 VDC “costs” five HP, although I forget the actual method of calculation and am going off a Beta Marine tech’s recall. While nothing one bolts to the engine is trivial, that’s acceptable to someone in a motorsailer, and maybe less so to someone with a smaller diesel and a lighter hull.
Hi Mark,
A good rule of thumb on an alternator is that they are 50% efficient. Taking that, 14.4V*1A=14.4W=.02hp. Including the efficiency gets you .02hp/0.5= .04hp/amp of alternator output. So a 90 amp alternator output would take about 4hp to run when flat out.
When it comes sizing the system, it gets a bit trickier. The recommended sizing seems to be to take your shaft power at full speed and add your accessory power and get the engine requirement. But how often do you motor at full power with your alternator at full output? If we sized for normal usage, most cruising boats have large enough engines and they are matched to the boat such that there is >5hp available for an alternator at cruising rpm. The problem with this is what do you do when you do need full rpm and your batteries are low enough that you will bulk charge as you won’t be able to reach full rpm due to being power limited. The clever solution to this is to have the system back off on alternator power when you get to really high rpm or even better high load and I have heard of a few people who have put in a manual switch for doing this but I don’t know of any system that does it right out of the box. Even this is a simplification as for boats with good sized props that really bite, your load varies not just with engine speed but with boat speed. The best would be a regulator that depowers the alternator at high commanded engine load and a variable ratio transmission but I don’t know of any cruising boats doing that. Of course, we need to keep it all in perspective and if you look at a fuel island plot for a diesel engine, the efficiency doesn’t vary that much in the normal operating range so while there is some to gain, it is much less than most people would expect.
Eric
Hi Marc & Eric,
I installed a field wire disconnect back-when for two reasons: we had a big alternator and only an adequately sized engine and I worried about the amount of hp that might not be available to me in a fire drill of some sort if the batteries were low. Luckily, this was never necessary.
The other reason (used a lot) was that the PO had put on a microwave, which actually has proved very useful and has earned its place. However, when motoring and wishing to use the microwave, I worried that the inverter draw off the batteries would make for a shock load on the alternator and, more important, a shock load on the belt that might cause a problem. So, we would take the alternator off line (a field wire disconnect switch) while using the microwave under way by power, use the invertor to run the microwave off the batteries and then bring the alternator back on line which was done with a soft ramped-up charge curve.
Worked a charm.
My best, Dick Stevenson , s/v Alchemy
Hi Dick,
Interesting. I have though once or twice about a switch to shut the alternator down, although I have never got around to it. A question: Did you install the switch in the field wire from the regulator to the alternator, or in the wire that powers the regulator? I’m guessing the latter since you say that the alternator “ramped up” after being switched back on.
Hi Eric,
Thanks for the efficiency numbers on alternators. Very useful for my in progress article on Nigel Calder’s new machine.
Hi John,
Just to be clear, that rule of thumb includes the losses of a v-belt and is on the conservative side. At low power levels, the efficiency can be a lot lower as the parasitics never go to 0 but things are sized around full output so the rule of thumb is a decent guide there. I hope that Calder’s system is far more efficient than 50% given its power levels. A synchronous belt should be capable of >95% efficiency and a decent generator >85% meaning I would think it should be >80% efficient if they put the effort in.
Eric
Hi Eric,
Thanks again, that really helps.
Hi Dick,
Interesting, thanks for the report. I have contemplated doing that but never have. Even for people who have not “overpropped” and simply tune the pitch so that they can get full rpm in flat water with the alternator putting out, this might be a way to deal with the issues of prop loading related to weather. That said, not many boats that I have been on can really put down all their power anyways.
Eric
Thank you, Eric, for those numbers and the formula. And Dick, the “disconnect switch” is a simple, very good idea I’ve heard of before; such a thing could even be at the helm for when you absolutely have to have every HP available for thrust. I would not motor at full power customarily otherwise; I would motor at the 75-80% point for best fuel efficiency. In fact, I’m flattening my Variprop’s pitch this winter because I want to get more RPM out of my wide-open throttle…at least in forward. I’m quite pleased with the rather torquey reverse. I also wish to have enough flexibility to equalize under power, which I would only attempt during pretty calm-state, daylight motoring for obvious reasons, as I would effectively go to handheld instrumentation for a few hours. So, no equalization runs in a TSS.
As is axiomatic, everything a trade-off and I have designed my setup to operate (ideally) within a fairly narrow (70%-100%) band of battery discharge well above the 50% SOC on which a lot of charging regimens are premised. Whether panels, wind gen and alternator can restore what we draw down is another question, but we are going to try hard to be sensible and ever so slightly Amish in our use of electricity aboard. Now, to order that hand-powered coffee grinder…
Hi John,
For users who have kept their loads down, I think that the time where renewables get really interesting is when you have a battery bank and solar system that are well enough balanced in size to get you where it is not a day between recharges but multiple days. The key to the battery capacity is that if you have a low output day or 2, it needs to be able to get you through with minimal renewable input. If you can slowly step down your charge over a few days but stay within an acceptable range, then you will likely get to a stretch of better weather or need to motor anyways which will bring you back up towards the upper end of the charge range. If you look at the extremes with renewable only generation, a very large battery bank and renewable that can just hit your average consumption works as does a battery just large enough to get you through a night and renewables that are enough to get you back up to charge each day in any weather works also. Of course, you ideally want to be in between these 2 extremes and to really figure that out, you need a basic time-stepping analytical model and some basic climate data which is beyond the scope of this post. I quickly put together one of those models when figuring out the backup battery bank for my parent’s solar system many years ago as they can have long outages where they are located. At one point I looked at it for our boat and decided that our batteries were actually pretty big and our solar pretty small so if we ever need more power, more solar will be the answer for us but for the time being, our modest solar works quite well thanks to the large battery bank.
For people unable to get to the consumption, storage and generation levels for a mainly renewable boat, timing is key and I still think that renewables have a place. With solar, running the generator first thing before the solar starts putting out is really interesting as it lets you use more of your battery capacity and keeps generator run times short an efficient. And for weekenders, solar is really compelling on boats that live on moorings as you can leave the boat not at full charge without wrecking the batteries and come back the next weekend to a full charge all with a pretty modest panel size.
Eric
Thank you for this comment, Eric. It introduces a very valuable angle into John’s reiteration of “be realistic”. Readers can include in their own assessments the consideration of whether they can realistically accept sub-complete charging and make the rest up a bit later in scenarios similar to those you’ve described.
As always there is quite a bit of good, enlightening and informative material. After looking at several years of fixed solar panels on top of our house I have used the formulae for sizing 75% output for 5 hours a day. This takes into account thermal losses due to the panels getting warm. This square wave fits nicely around the curve showing our daily usage. For a 12V 100W solar panel system this means there will be 75W for 5 hours. Converting 75W for 5 hours into AH, 75/12 = 6.25A, 6.25A for 5h = 31.25Ah. Each solar charging cycle you must supply the needs plus replenish the batteries usage from the night before. Assuming a 12 hr day and 12 hr night and a 10% inefficiency, loss, means I only have 1/2 of 28Ah available for usage and 1/2 of 28Ah for charging. This shows how little solar panels actually resupply during a good day. Things deteriorate quickly when the days are very dark or cloudy.
Hi Mike,
Great information, thank you…and realistic too. 🙂
Mike,
Just want to confirm your numbers.
Today was a good day for solar here on Martinique. My 640 W solar produced 190 Ah.
Yesterday we had a day with many showers. Still I got out 150 Ah. The panels are fitted horisontal and there will be some shadows occasionally. I’m actually very pleased with the result as that means I only have to run the engine one hour every second day to charge, make water and generate hot water.
Roland,
Your numbers fall within expectations. Assuming you have a 12V system, 75% of 640W = 480W, 480W / 12V = 40A, 190 Ah / 40A = 4.75 hrs. My formulae is for sizing how big a solar array does one need. The other item in the equation is what is your load is in the day and at night. With 190Ah you should be able to replenish your night time usage if you have an average hourly load around 5 Amps. Anything more will require some other method to top off the batteries periodically. ( Assuming 12 hours of daylight and 12 hours of night).
Hi Roland,
Wow, that’s a lot or panel area. Where do you have the panels installed, and how do you manage shading?
John,
By today’s standard 640W is not that much. Many boats I see have 900-1000W. I would say 90 % of the boats in the Caribbean are equipped with an arch in order to increase panel area.
We have 2 x 100W on the lifelines,
240W on the Hardtop and finally 200W on the Bimini. Shading is not a problem when on anchor. Under sail shading can be an issue as I can not bring out the boom as I want. But normally I have ay least 400W not shaded when under sail.
Hi Roland,
Thanks for the fill. I can certainly see the utility of an arch, as long as it’s built strong enough, but I do worry a lot about this trend to attach panels to lifelines, unless they will be removed before going to sea. It would not take much of a wave offshore to trash the stanchions and even tear a base out of the deck if it hit a panel. And I’m also seeing a lot of boats where the ability to properly handle the mainsail, or even reef efficiently, has been badly compromised by the presence of panels. Also Bimini tops that can’t be taken down because of the presence of panels can be a worry.
Not saying you are in this situation, but I think it’s important to prioritize seamanlike boat handling way ahead of solar panels. The other thought is that just because 90% of boats are doing something, that has little to do with whether or not it’s a safe and seamanlike idea. I would say that 90% of cruising boats are not set up to be safe offshore.
More here: https://www.morganscloud.com/2011/02/25/clear-the-decks-for-action/
and here: https://www.morganscloud.com/2018/07/15/10-things-that-are-common-on-offshore-cruising-boats-but-shouldnt-be/
Hi Roland,
I share John’s concern about items attached to lifelines: solar panels are a big concern, but I extend my concern to jerry cans, kayaks and the like. John has expressed one element of concern well, but a seldom considered concern is the stress on the stanchion bases/bolts/backing plates which were not designed with tolerating repeated sharp loads of this kind. Think, if you will, of the loads going to wind in a breeze heeled over 20 degrees that the weight of solar panels puts on the stanchion bases with each “slamming” into a wave, especially if there is some water flying around (or exchange solar panels for full jerry cans etc.). If you hear of stanchion bases leaking (and I have come across this 2 times, at least), there is always the chance that the lifeline stanchions were actually stressed saving a life, but it is far more likely that were items attached that caused multiple thousands of small shock loads on the stanchion bases till they loosened enough to start to leak. And, if lucky, the leak did not migrate into a balsa core.
My best, Dick Stevenson, s/v Alchemy
Great stuff!
Nigel’s magic machine? Looking forward to that article. My thoughts so far:
– 9kW is a huge amount – requires large bank to take advantage of it (his standard is 10kWhr which is equivalent to ~800Ah at 12VDC). That’s probably not big enough to need/take advantage of 9Kw of charging, unless you can time a lot of heavy loads to run when engine is on? Probably needs the next step up, ie 20kWhr (ie 1600Ah)! That’s a lot of lead. Considering this system “the answer” in isolation would probably be a mistake, since it ignores all those neat little gains from bits of renewable here and there, to keep the bank size down. As you nicely explain above.
– Main engine for all energy? Hmm. Main engines are usually noisy when run alone (even if the lightly loaded problem is “somewhat” solved). Might work really well for your average “Med-style-cruiser” when motoring on/off anchor/marina and to next bay each day (due to lack of wind or motivation). But for longer passage-making-live-aboard types?
– 100% proprietary system. If that super special alternator blows when you’re in the Marquesas, you’re hosed! Better carry 2 (expensive?) spares. Same for all the electronics. The “all eggs in one basket” approach makes this even more serious. Because all your storage capacity is now 48V you can’t really use wind/solar/hydro etc? A more balanced approach (incl renewables, engine, genset etc) with standard modular components might make more sense for the “far-flung” conservative cruiser?
– I instinctively dislike the 48V to 12V DC-DC charging step. I see why he’s gone 48V (wire sizes in alternator with I²R heating), but it makes the system more complex again with yet another small 12V bank and those 48=>12V chargers. But could be convinced on this one…?
Anyway, looking forward to your analysis…
Hi Oliver,
Good thoughts, but I’m going to stay out of this until I get the article done. That way everyone’s wisdom will be in one place so it will be most useful for others.
Yup, Thumbs up.
One further thought for the notepad, which I failed to write down (I only touched on it):
– Having all the 48V as your storage creates another issue. In order to keep your bank size down, you always want to run as much as you can while it’s available – in any system.
In a system with a 110/230V genset this creates the issue that some/many of your loads (potentially including high powered ones like big freezer compressors) want 12VDC, so you have to convert all that plentiful power from 110/230 to 12VDC using battery chargers. More high power components which become the bottleneck.
In the Integrel, you have a similar issue, but the additional bottleneck is now the 48VDC => 12DC chargers. His standard spec for that is 600W (not much!), with options to go to 2kW (still not that much!).
The result is that most/all the energy has to go into the 48VDC lead-acid bank only to come back out later. And we all know what that means….
On Lithium – which has the potential to be a disruptive partial solution to some of these issues:
Read all of RC Collins, and spent 2 more full days reading further into the subject. A lithium system is complex to implement well and safely – by boat standards. It doesn’t seem complex to me, but then I am University trained in this subject and have decades of industrial control systems experience – which is what this is. I wouldn’t hesitate to do it myself given how mature it is now and the information which is available. But that’s me. The off the shelf commercial solutions from Victron and Lithionics are no silver bullet, because they are “not a system”, so might as well do it yourself, or pay someone professional to it.
I thank RC Collins for all his efforts and his writing. I also found this series of articles extremely good:
http://nordkyndesign.com/category/marine-engineering/electrical/lithium-battery-systems/
Rc Collins and Eric Bretscher seem to agree on almost everything. I found the Nordkyn Articles better structured, with useful, formally noted references to external research, etc. Lots of technical data including sample high level approaches to the required interlock circuitry (without a detailed wiring diagram which would be a mistake). Perhaps written by an Engineer for an Engineer, and that’s why it spoke to me? Your mileage may vary.
Aside…John: You may have seen already. Nordkyn is experimenting with Ultrasonic antifouling system on his Alu Yacht:
http://nordkyndesign.com/category/marine-engineering/electronics/ultrasonic-antifouling/
Far too early for you to adopt I am sure, but maybe there is hope “for less painting”?
Oliver
Hi Oliver.
While I agree with much of what you say, I disagree about Victron. I took a deep dive into their stuff when I was considering lithium and they do have a full system, at least in my opinion: all the gear we need from one vendor, together with complete instructions on how to put it together and fully supported.
Another key benefit of this approach is that if it all goes wrong there is only one vendor to hold to account.
As to the ultrasonic anti-fouling idea, this stuff has been around for a good 20 years. So far I have yet to hear of a test that shows that it really works. Also, I don’t much like the complication, or the need to drill several holes in the bottom of the boat.
Hi John
To be fair, I didn’t look at Victron in huge detail. I looked at Lithionics, and that seemed far from complete as a system, which is always “custom” to some extent for each boat anyway.
Also, I recalled the effort you went through to get all your “smart (or not) regulators, chargers etc from proper marine brands” to actually do what you wanted with your lead acids. An experience I could completely sympathise with from personal experience. And being the sort of person I am, on this topic because it’s my area, i figured that I would not be happy unless I really understood what each of these black boxes was doing and that it was doing it as well as I could manually. So if I am going to go through that effort, I – and this does not apply to most people – would be far better off using “open modular components” which are programmed, configured and wired into a system which I personally fully understand and therefore trust. If something starts acting weird, I would have a much better chance of being able to detect and fix it early than a black box from a brand who, understandably, does not want to disclose the internal workings of their components.
But that’s just me. I dislike black boxes.
As a distant further consideration there is price..
===
I agree that ultrasonics have been a dream for a long time. The point here was that he is testing this now, using a different approach – more power, higher frequency – and it’s showing results. Of course the tests are not high sample nor completely scientific, but he is trying hard be structured and neutral in his evaluation, and it looks like there might be something there.
There are no through hulls involved at all as far as I can tell. The piezo electric ultrasonic vibration transducer is mounted hard against the INSIDE of the Alu hull.
You should have a read, when you get a moment…
Oliver
Hi Oliver,
Good to hear that the ultrasonics are a different approach. That said, I think I will stay out of that rabbit hole, at least for the moment. Being disciplined enough not to get distracted by every new cool thing is one of the hardest parts of my job, particularly since my natural proclivities are to do exactly that.
And, one of the things I really like about Victron is that they use modules well, within their system, without over reliance on back boxes (I too am a black box hater). They also do a great job of explaining how their stuff works in the manuals, and are very responsive to questions. All in all, one of the least opaque companies I know of.
Thanks. I’ll have another look at the Victron Li-System.
I agree it’s far too early, to take the ultrasonics seriously. It might be 20years before we know to what extent this can work, as each “test” takes 12-36 months! Might be too late for you..and for me.
But we live in hope of antifouling solutions that actually work, as opposed to enrich paint companies and generally annoy us..
😉
Hi John,
I must admit that at this point, I do not remember the wiring decisions I made well over a decade ago. And my schematics are on the boat.
My MO is to come up with an idea, work out the details to the extent of my abilities and then pass it by one of my go-to gurus for further suggestions before execution.
My first guess would be that I kept it simple, break into the field wire with a toggle switch. But I do believe I remember a soft start, but perhaps that reflects that, even after the use of the microwave, the batteries are still pretty close to fully charged when the field wire is brought on line again.
In April, I will let you know.
My best, Dick
Hi Eric,
I felt my initial engine was under-powered, but I did put on a larger alternator and that worked out fine. Then one night, there was a fire drill of somesort, the batteries were quite low and I wondered how compromised the engine’s power was by the big alternator going full out when I might need power to get out of a predicament: hence the disconnect.
The closest I came to actually activating in need was coming out of Treguier, France, stiff wind in the face against a tide, rocks on either side of the channel, Alchemy going slower and slower as she succumbed to her bluff bows and the increasingly steep walls of waves we were encountering. I realized we were fully charged and taking the alternator off line would make no difference: but I thought about it. (That started a 3 years quest to get more “punch” out of engine/drive train.)
So in the end, my taking the alternator off line has been in the far more hedonistic pursuit of using the microwave.
My best, Dick Stevenson, s/v Alchemy
Dick, what size is your diesel, your bank and your alternator? I’m curious in terms of my own setup, which is a 1185 Ah bank over six L-16s, a Beta Marine 60 and a proposed Mark Grasser alt circa 180-200 A to replace the stock Beta 75 amp one, which does something, but could do a great deal more.
Hi Marc,
Alchemy has a 4yo Yanmar 4jh5e (~~53 hp) with a 150 (maybe 180) amp large-frame Presolite- Leece Neville alternator powered by a serpentine belt on a custom mount. The alt has an external regulator which I have programmed to not ask for more than ~~ 110 amps. My house bank is 6 gel cells nominally producing 95ah each with one starter battery of the same size.
My thinking on this is that alternators which are only asked to work at 2/3rds capacity or so will last for a very very long time. Also, the propulsion engine will often be going long enough that having the initial amperage output maxed out will make little difference in the long run and that less demand is easier on the belt and engine and the large-frame alt runs cooler. Finally, in the event that the genset stops giving me amps, I can always ask the alt regulator to give me full alt output so that I can more efficiently charge at anchor. (That is if I can use the little magnetic wand over the potted regulator successfully.)
I hope that helps: come back with questions.
My best, Dick Stevenson, s/v Alchemy
No, thank you, Dick…that’s good info, and I guess you are running a Balmar 614 regulator…that’s the one with the magnetic wand? Are you pleased with it? The idea of restricting alternator output I assume is twofold: to keep it cool and keep it forever. That argues I should perhaps try to get a 200 amp alternator and just run it circa 130-140 amps, which is double the max. output of the stock model, which could become a vacuum-bagged spare. Custom mounts and such are easy for me to do (I want one of those turnbuckle tensioners because I have a generous engine bay. Thanks for the information…once again this site helps me understand my vague ideas!
Hi Marc,
No, not a Balmar, although I have heard good things about the units they are building these last couple of years. It is a Xantrex that has given me good service for 15+ years now. And, yes, those are the reasons for restricting the alternator output.
I am also a bit wary of maxing out the alternator output on the propulsion engine. It strikes me (and I am no engineer), that taking out 3-4xs the amperage that the engine came with and was likely designed for can’t be easy on the bearings/water pump etc. It also strikes me that, for most of us a big alternator will: in a 15 minute run, put out a good % more amperage, but that after you get to 30-45 minutes or so, the difference may not be so great. Yes, it is nice to get a good charge in the time it takes to up anchor and motor out of a harbor into a nice wind and turn your engine off: but just as often you are motoring for a bit.
I would be curious what the amperage output difference is (same rpm, regulator and battery bank) between a 100a alternator and a 150a alternator at 15”, 30”, 45” etc.
In any case, I lean toward de-tuning that area for those reasons.
Given the above, one might suppose that I would just get a smaller alternator and that certainly makes sense, but I am clear that if the propulsion engine alternator ends up being my only source of supplying amps, then I will ask more of the system.
My best, Dick Stevenson
Thanks, Dick, for further explaining your logic. I’m pretty much on the same page, save that I already plan to charge up with the alternator and use solar and wind to stay in the higher reaches, when possible, of the SOC of a big bank. In our case, the bigger alternator would be to also supply juice for watermaking while, so to speak, the sun shines. That would be in the context of a three-hour diesel run at cruise speed a couple of times a week. Once the diesel’s on, I prefer to keep it on and would, within reason, schedule pump-out runs and calm air crossings to facilitate that.
Hi Mark,
I do run the earier model Balmar (612). I´m very pleased with the regulator itself. Even if the programming tool is a little bit finicky. I only use one regulator for my two alternators. One small frame Balmar 110 and one large frame Mastervolt 130A. I take out 150A (hot). I actually thinking about upgrading the large frame to 200A as that would give me full charge when I run the watermaker. With 2000 hours on the existing generators you would think it is time anyhow. When batteries (900Ah) are in bulk and watermaker (38A) is running I could use 200A.
I will also go for two regulators instead of one as it gives more redundency and probably better regulation of the two alternators. My advice is to oversize alternator. If you find it to much you just derate it to what you want. Going the other way is more expensive. Also if/when converting to LiFePo4 you want maximum output.
Hi Roland,
I agree on oversizing and then downrating. And yes, if you are approaching 2000 hr, those alternators are almost certainly on borrowed time: https://www.morganscloud.com/2013/11/06/10-tips-to-buy-and-install-a-liveaboards-alternator/
Thank you for the real numbers of amps. A derated larger alternator makes a lot of sense in terms of wear and temperatures avoided.
Well,
I went with a 1200ah lithium bank and full electrical upgrade with solar, professionally installed. It wasnt cheap…
Posting a link here for people who are interested. http://www.billynewport.com
Great Information, Being an Electrician and retirement in 3months, Heading to Bahama’s in 6. Got 4 new Marine/RV AGM’s but not sure how to split the Batteries up with the Batt switch 1-2-all, Either 2 on each side or 3 for house, 1for start. I though 4 battery’s of the same type would charge equally. Did get the Victron Monitor. and after reading looks like I need another one. Thanks in advance. I’m thinking of 2 on each switch would be more of an equal load and charge.
Hi Paul,
I’m not a fan of putting the engine start on a 1-2-both. If it were me, I would buy another battery for the engine starter and wire it completely separately with only a voltage sense rely for charging. I would then split the house bank into two banks of two with the 1-2-both.
One other point, if the AGM’s are not from LifeLine, you will not be able to equalize them and therefore you are going to need to be very careful about fully charging them after each discharge (solar is the only practical way to do that) otherwise they will only last a year or so before they fail from sulphation: https://www.morganscloud.com/2010/08/02/agm-battery-test-part-1/
John, Thanks for providing the spreadsheet calculator.
Can you help me in understanding how you calculated the bank weight by letting me know what the numbers are that make up the equation (the 119*2 and the 400)?
Hi Stephen,
I don’t remember off hand exactly how I derived that equation, but the theory was that I looked up the weight of a typical lead acid battery and divided by the capacity to get weight per amp hour and then multiplied by the required bank size. By all means check my numbers and please report back if I have made an error. I think the times two may have been because I looked up 6 volt batteries.
Hi John Im a new member. Im trying to decide whether to buy a Watt and Sea 300w hydro generator to do the ARC and back. You appear a bit negative about them ? I have a mate who did world arc and didn’t need any engine power and no generator on board. Most of the problems others had were with generators. Are the W & S not the vendee globe choice ?
Hi Jon,
Not at all, just realistic about the issues there have been with them. That said, for that usage I would seriously consider one, but also really think about what I would do if it died on me. Keep in mind that vendee globe boats use the higher end (more expensive model) and also have at least two, and sometimes a spare on top of that.
We have a complete hands on review here: https://www.morganscloud.com/2017/08/04/watt-sea-hydro-generator-review/
Note Andy’s recommendations on when they make sense.
I zeroed the autohelm in anticipation of windvane use. It didn’t make any difference. It seems with the figures provided that bank size is determined by use at anchor.
Hi PD,
That’s sometimes the case that at anchor use will drive bank size. A lot of variables but that can often be driven by how long you want to stay quiet at anchor.
John –
I downloaded V1.1 of Battery Capacity Calculator after studying the relevant articles in your ebook. I follow the logic and calcs is the spreadsheet. So, here’s my observation: for the Required Bank Size (cells B26 and B27 in the spreadsheet), the value appears to be based on values in row 20, rather than taking into account the “Usage between charging cycles” in row 22, which reflects the desired quiet time in row 6. In other words, Required Bank Size does not vary with Desired Quiet Time. I may be missing something, but it seems the bank size must increase as desired quiet time (or, usage between charging cycles) increases. If this is the case, then Required Bank Size should be based on the higher of the two values in cells B22 and C22.
Note: My version of Excel may have screwed things up by being ‘helpful’ with spreadsheet updates…maybe making my observation irrelevant.
I am learning a ton on your site! I am a bit of a minimalist – having a Monsun 31 and big dreams – and so I appreciate especially your real-world advice about essential tools, keeping weight down, and keeping things fundamentally simple and reliable.
Mark
“New listener and first-time caller”
Hi Mark,
Thanks very much for checking that. Clearly I have screwed up somewhere. I’m just off for a few days vacation, but will make a note t o fix that as soon as I get back.
Re the Title of this topic Optimal Battery bank size, very informative reading & comments but I’d like to get back to basics please and gather some confirmation. We have temporary house GEL @ 300a/h, with rated 1000W of solar panel and potential engine charge of 140a off one engine (two available).
Totally agree with ‘general experience’ calculator which gives me the following results:
> Usage between charge cycles: at sea 420a/h, at anchor 255a/h
> Recommended lithium capacity 600a/h
I am at the point of installing a permanent lithium power source. The two best configurations I find from the supplier: 2 x 280a/h or 2 x 400a/h.
My requirement is to provide enough power to systems over say 3 dull/cloudy days without the need to run the engine.
Q.1 What capacity bank would I typically need given judicious use of non-essential loads?
Q. 2 Is it better to have integrated BMS or External for a simple system?
Many thanks:)
Hi Euan,
Sorry, but I don’t do specific system design. Way too many variables for me to do that in the comments, not to speak of the time it would take to question you properly about your needs and then come up with an answer. The whole idea of AAC is to give you the tools and information to make your own best decisions.
One thing I would say, is that I would not design a system for that long a quiet time on cloudy days. To me that’s an edge case and designing for edge cases typically ends with a system that’s bigger, heavier, and more expensive than is optimal.
As to internal or external BMSs, that’s not what matters. I explain in detail here: https://www.morganscloud.com/2024/01/29/lithium-batteries-buyers-guide-part-1-bms-requirements/