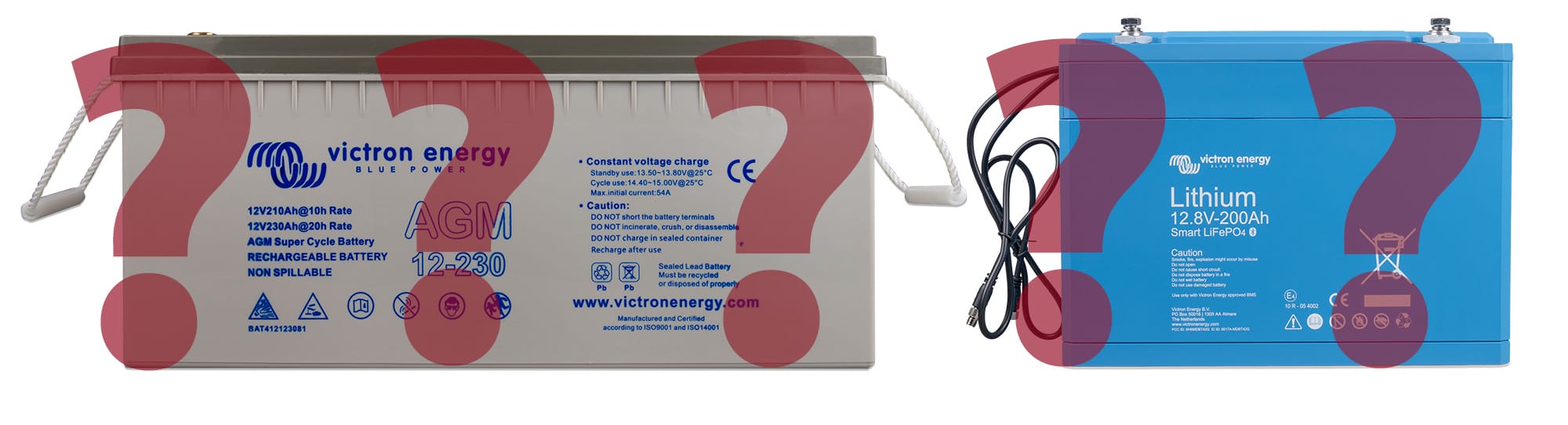
Most of us cruisers have probably either made the transition to lithium batteries, or are wondering whether we should. And, at first glance, what with all the claims and counterclaims made by each side of the debate, this seems like a horribly complex decision.
The lithium fan-boys, often in the grips of confirmation bias, scream “no brainer”, while the reactionary lead-acid stick-in-the-muds yell “unreliable and will probably burn your boat”.
Both positions are wrong.
But, not to worry, the decision becomes easy as soon as we cut through the claims to an understanding of the fundamental difference between the two chemistries.
And, further, once we have that fundamental locked into our heads, it becomes easy to select the right system for us and our boat.
What’s that fundamental?
Lithium batteries store about four times as much usable energy for a given weight and volume as lead-acid batteries do.
Yes, I know, four times seems high given that a good-quality lithium battery weighs about 40% of a lead-acid battery, but the difference is that lithiums can be consistently cycled through about 80 percent of their range and lead-acid about half that.
Lead-acid salespeople claim 50%, but 40% is more realistic in typical yacht use due to tail off in charge current, making full charge every cycle unlikely, although solar does help with that.
And, yes, the savings in weight of lithium tends to be more than the savings in volume.
So let’s just stipulate (as the lawyers say) that four times is a rough approximation. Don’t worry about it…for our purposes it will do. Remember, this article is about a simple way to decide which batteries to buy, not an challenge to get into a mind-numbing debate about every detail.
If you are a lithium-lover and want to use five, or a lead-luster who wants to use three for the factor, that’s just fine with me; besides, it will make little difference to the final logical outcome.
OK, so now we know this basic difference between the two battery types, the decision comes down to two questions each of us need to answer for ourselves:
- Is having either the same capacity at one-quarter the weight and volume, or four times the capacity at the same weight and volume (or a mix of the two variables in between), worth the cost of changing to lithium?
- If the answer to question one is yes, then the next question is, are we willing to take on the complications and hassles of installing a seamanlike lithium-battery system?
Wasn’t that nice and simple?
But wait. What about defining costs (question 1) and complications (question 2) in a world of fan-boys and salespeople from both sides screaming at the top of their lungs stuff like:
- Lithium reaches full charge much more quickly than lead.
- Lithium will last twice, five, ten times longer—the number claimed will vary with the speaker’s ability to tell a whopper without blushing.
- Lithium will burn your boat.
- Lithium is safer than lead.
- Lithium is far less reliable than lead.
- Lead batteries die in less than a year with typical cruiser use.
- Lithium is so expensive that it never makes any sense.
- Lithium is actually cheaper than lead because it lasts twice, five, ten times longer.
As so often in these kinds of arguments, all of the above claims contain some truth, but most are more wrong than right and even the few that are right, are secondary to our decision.
Getting To Truth
The good news is that with a bit of logic getting to the truth is easy. Let’s do that.
Claim: Lithium reaches full charge much more quickly than lead.
This one is absolutely true because the charge rate of lead acid batteries tails off very quickly once they are about 70% full and lithium does not.
But all that means is we will only be able to use about 40%1 of a lead acid battery bank’s rated capacity…which we already allowed for (grey box above), and used to calculate the relative energy density of each chemistry.
Therefore lithium fan boys who keep pointing this out and crow about higher energy density are double dipping—a complete logic fail.
The same applies to pointing out that the last 50% of lead acid battery capacity can’t be used, as against about the last 20% for a lithium battery. We already accounted for that. It’s a contributor to higher energy density, not another advantage for lithium.
Claim: Lithium lasts longer than lead
Let’s check with Victron who make several kinds of batteries of both chemistries, and then add in our own experience:
- Lithium 80% discharge: 3000 cycles
- AGM Super Cycle battery 40% discharge: 1000 cycles
- Gel long life 50% discharge: 2500 cycles¹
- LifeLine AGM manual 50% discharge: 1000 cycles
- LifeLine AGM real-world experience on McCurdy and Rhodes 56 (no solar and brutal usage) 50% discharge: ~1500 cycles (see Further Reading for details)
So where does the truth lie? Assuming that both types of batteries are well taken care of, let’s call it three times as long for lithium, although based on our own experience that is being kind to lithium, not that it matters for our purposes.
Note that I’m assuming high-quality lithium cells from a reputable manufacturer and that they are treated absolutely perfectly for their entire lifetime—one BMS failure or wiring mistake can total a whole battery or even the whole bank.
Also be aware that, as I understand it, even reputable manufacturers sell cells that don’t meet the standards of mainstream companies (like Victron, Mastervolt, and Lithionics) into the secondary market, so the claims you often hear that “the cells I got from no-name-lithium are just the same as those used by Victron” is likely not true.
To mangle a quote from George Orwell’s Animal Farm, “all lithium cells from a given manufacturer are equal, but some are more equal than others”.
¹The claimed cycle life for gels is interesting.
Claim: Lithium will burn your boat
This one’s easy. Assuming we are using Lithium-Ion-Phosphate batteries from a reputable source, properly installed, this is crap. Heck, ABYC just went through the exercise of actually trying to get a lithium battery to thermal runaway without success.
As far as I’m concerned, this one’s a deader.
That said, if we buy no-name cells off eBay, without safe containment, and then cobble together a bank using the instructions from some wan….err…presenter on YouTube, without a full understanding of what we are doing, all bets are off.
Claim: Lithium is safer than lead
The argument is that lithium cells are individually controlled by a BMS and therefore will be isolated if something goes wrong.
But the problem is that said argument assumes that BMSs never fail, clearly rubbish, particularly given how complicated they are.
And all that complex wiring in a lithium system, or even inside a “drop-in” lithium battery, can be a cause of a fire in and of itself. This is particularly true of the sketchy cheap internal BMS batteries available directly from the far east—see Further Reading.
Also, lithium batteries enter thermal runaway at a lower temperature than lead acid, and if they do catch fire are harder to put out and produce more toxic fumes.
Anyway, the bottom line on both this claim and the one just above is that assuming good-quality batteries of either chemistry fires are generally the result of poor system design or installation not battery chemistry, so let’s move on.
Claim: Lithium is far less reliable than lead
This one is fundamentally true in that lithium systems are far, far more complicated than lead and more complication pretty much always equals less reliability, particularly at sea.
Also, lithiums can be totalled by just one charge or discharge mistake, whereas good-quality lead-acid batteries are fantastically tolerant of screw ups.
That said, if we use equipment from reputable vendors, and install the right backup and monitoring systems, this is now a manageable issue that should not deter anyone from installing a lithium system that makes sense for them and their boat when measured against the above fundamental: much higher energy density.
Claim: Lead acid batteries die in less than a year on a cruising boat
True, if we don’t charge them properly and leave them in a partial state of charge for weeks or months.
But that problem was fixed 15 years ago (by this Online Book) and now that we have efficient and cost-effective solar panels, even with a small array (properly managed) it’s a very easily solved problem.
Bottom line, if we get less than 1000 cycles out of good-quality lead-acid batteries, we need to go look at our installation and charging practices, not blame the chemistry.
Or, to put it another way, changing to lithium to fix a faulty lead-acid system that would have, when fixed, met our needs, is a giant logic fail.
Claim: Lithium is so much more expensive than lead that it never makes sense
Rubbish. There are a whole bunch of scenarios where lithium makes perfect sense, even if it costs much more than lead. Saving weight and volume is a huge benefit, particularly on smaller and/or lighter boats.
And every year, as lithium systems get better, more reliable, and less expensive (in inflation-adjusted terms) there are more and more scenarios where lithium makes sense.
Claim: Lithium is cheaper than lead because it lasts so much longer
Not true, at least at the moment.
This is an assertion that lithium fan-boys love to support by comparing above-mentioned no-name cells to quality AGMs and/or conveniently forgetting all the expensive surrounding equipment required to build a seamanlike lithium battery system.
And lead-acid lovers can be just as biased by comparing a primitive system based on no-name golf-cart batteries from Costco², charged by the shitty OEM alternator that came with their engine, with an all-singing, all-dancing seamanlike lithium system.
What’s the reality? At the time of writing, a good, although very rough, rule of thumb would be that a seamanlike lithium system will cost four times what an equivalent usable-capacity lead-acid system will.
Three-quarters of that added capital cost is the price difference in the batteries, including BMS(s), and the remaining quarter is the cost of the added equipment to build a reliable and fault-tolerant lithium system that is not required for lead.
However, the per-cycle cost over the life of the lithium batteries will be only about twice as expensive as an equivalent lead-acid system. The difference between this factor and the one in the paragraph above being that the lead-acid batteries will be replaced two to three times as often as the lithium.
²I’m not suggesting that golf-cart batteries from Costco are always a bad idea, just that for the purposes of this article we need to compare apples to apples. In fact, golf-cart batteries can be a great option for the right usage profile.
Conclusion
We have come full circle.
To make the choice between lead-acid and lithium, all each of us needs to do is shut out all the screaming and yelling and answer the two questions at the top of the article for ourselves.
One more time:
The decision comes down to cost as against energy density, and willingness to take on the complications of a seamanlike lithium installation.
It really is that simple. Everything else is just noise.
Our Technical Comfort Level
That said, there is one other issue that we should all think about before pulling the trigger on lithium:
Designing, building, troubleshooting, and maintaining a reliable, seamanlike, regulatory compliant, and insurable lithium system is a complex project (see our buyer’s guide coming next in this Online Book.) that only boat owners with a good technical understanding will be able to DIY.
Others should make sure they have a really good technician lined up to do the installation, not Bubba at the boatyard, and also think deeply about what they will do if the system fails far from said technician—our suggested backup system can help with that, see Further Reading.
Further Reading
- A seamanlike lithium-battery system defined
- And why it matters
- Battery separation best practices
- Lead-acid batteries with short lives, and how to fix that
- Some very disturbing facts about cheap internal BMS batteries from the far east³
³Rod starts this otherwise excellent article with a rant claiming that lead-acid batteries typically last just 150 deep cycles. And he is kinda-right given that he is quoting a survey of cruisers who had clearly not followed the recommendations in this Online Book. And, as I write above, with the advent of reasonably priced solar this is an even easier problem to solve. So ignore that first part, it does not apply to smart AAC members.
Comments
If you have any questions, please leave a comment.
- The reason it’s 40% not 30% is because most all cruisers will have at least some solar, which can take over charging during the tail off phase. In fact with smart usage the usable capacity of a lead acid bank can be as high as 50%. ↩︎
I am not in a position to criticise what you suggest as my electrical energy upgrade is only just starting. I would like to thank you for bringing a bit of clarity to the decision process. I am very much a late adopter of technology, not because I am a luddite, but rather I want to benefit from technology maturing and associated price drops. So, in the market for changing out old dual alternators, to a single alternator, split charging via diodes to something else, regulators, AtoB, BtoB and nearing end of life T105s et cetera, I am beginning to consider lithium. Two primary reasons: my current set up will be removed entirely, so blank canvas and I would like the space that the current bank takes up to be freed up for something else. However, if I answer your questions as noted: 1) Yes, 2) No. Hence for me, I will be upgrading system for lead acid this time round. I would of course want to make sure that the new equipment is at least lithium charging capable at some future point.
Hi Alastair,
I think your position and approach makes a lot of sense. We are still in the early days of lithium systems on boats, and they will get a lot better and less expensive going forward.
I wrote about why this kind of approach makes sense generally here: https://www.morganscloud.com/2013/10/25/want-to-get-out-cruising-dont-be-a-pioneer/
Your comment has also got me thinking again about an article on how to build or modify a lead-acid system to make it as lithium ready as possible.
John, I don’t know where you find the time! However, an article on “build or modify a lead-acid system” so that it is lithium ready, would be appreciated by many I am sure.
Hi Alastair,
Will do, I have to find the time anyway as I will be advising on the A40 electrical system design and we want to, as much as is financially sensible, make it lithium ready although lead acid will be standard—two birds with one stone.
I have been the slave of Lead-Acid battery for 40 years. Started my life as a mechanic responsible for truck maintenance, burnt alternator and dead batteries. On my current exploration boat, i had 8 Crown CR-235 from 2008 to 2015 then i bought another set in 2015 that i just discarded (from July 2015 to December 2022 = about 2000 cycles. The secret for golf cart battery longevity is 1) watering, watering watering and 2) daily charge after night discharge. Water consumption has been around 1 liter per battery per month under daily 50 % discharge in a liveaboard situation in the Caribbean.
I switched the 8 CR-235 to 4 Victron 200 AH Smart Lithium in December 2022 and i think the most important point to the analysis is that Lithium stop the dependency to the daily charge. Which mean that it open the door to transient charge/discharge scenario like solar (a cloud passes and no charge while there is still a DC load that discharge), induction oven and other transient use.
this has completely changed my life, much more than the weight savings or the added capacity.
The Lithium system has been made ABYC TE13 compliant by careful engineering of the BMS interaction with all charging and load component has well has the monitoring system.
(on the picture, hard to believe that these are equivalent)
Hi Andre,
I see your point, but I don’t think it changes the fundamental in my article above in that the added capacity of lithium for a given weight and space is what has enabled you to charge less often.
But you could have simple made your lead-acid battery larger and got the same effect. Of course that would have been impractical for weight and size, so we have come a full circle.
We are both saying the same thing, although slightly differently.
Example of a seamanlike load-dump (blackout) proof lithium system with proper backup, designed for full-time offshore voyaging,
There is a starting set of 2 Victron AGM battery (2) and 4 Smart Lithium Victron battery in two separate bank each with its own BMS. The Balmar 250 Amp alternator feed the AGM with a charge profile set at 14.2 volts. At that voltage the AGM are happy and its the recommended absorbtion voltage for the Victron Lithiums. The Alternator is also connectd to the ALTERNATOR STUD on the Victron Smart BMS 12 200. The Smart BMS 12 200 has integrated switches and mosfet transistor to separate and interconnect based on voltage rules, the Lithiums, the alternator and the DC loads.
The system on our boat is completely redundant, all DC loads including engine start can either be run from the AGM, from Lithium bank 1 or Lithium bank 2.
The system has been designed to meet ABYC TE13 and be highly redundant.
Hi Andrea,
Looks like a nice system, but don’t you have to switch over to AGM in the event of a load dump? Or am I missing something?
I prefer a system where critical loads like autopilot are not interrupted even for a second (think crash jibe) by a load dump and therefore advocate for a serial backup system.
More here, and here:
https://www.morganscloud.com/2022/04/25/why-lithium-battery-load-dumps-matter/
https://www.morganscloud.com/2022/07/03/building-a-seamanlike-lithium-battery-system/
John this is the feature of the Victron Smart BMS 12-200. It receive the alternator through a dedicated stud, which get triggered at 13V and disconnect at 14.4. The DC system is on another stud which is not deactivated unless an internal problem in a lithium battery. Since the alternator is also connected to the AGM there is no dump load. The alternator stud also serve as a programmable shunt so to limit the amperage output of the alternator. I have two separate system so having both disconnecting at the same time would be very low probability and in any case there is still 200 Ah of AGM.
Hi Andrea,
Thanks for the fill on that, but that only takes care of a blackout from alternator overcharging, and also relies on quite complex tech, so I still prefer a serial lead-acid backup for critical loads like the autopilot
Hello John i don’t want to argue but the system is fault tolerant with two separate set of lithium batteries each governed by its own BMS. Since the BMS take care of all external events, what remains are internal events (cell out of balance, temperature, low SOC). Both set are connected to the same DC wire that provide all current to the main panel including the autopilot. They are thus governed by Ohm law. If one set of battery goes down by an internal event, then the other set is still there and no DC shutdown occurs.
I agree with you that a backup is needed. I’ve put an excerpt of the TE13 that say so. But the backup can be another Lithium set…
Hi Andre,
I agree, your system is very good, and probably in your hands, very fault tolerant. But for less technical people I still recommend a serial backup set as detailed here since it relies on less complex tech:https://www.morganscloud.com/2022/07/03/building-a-seamanlike-lithium-battery-system/
And yes, I’m aware that the standard allows for a parallel lithium backup, but I have it on good authority that was put in there to appease the lithium battery representatives on the standards committee not because it is an intrinsically good idea. We must never forget that at least in NA standards are the result of negotiations between industry players all with an axe to grind. As I have written before TE13 (now E13) is better than nothing, but not much.
Diffferent strokes and all that, but I’m going with something similar, as much as I like Lifepo4, and firmly believe my next round the lead acid will be replaced with an LTO battery, but I need to do a bunch of testing first. I don’t trust the lithium on it’s own exactly, doubly so since I’ll be rolling my own for cost reasons. Lead acid (AGM, MagnaCharge, has higher reserve AH, and same CCA as the victron equivalent, better warranty and 1/2 the price at retail vs my cost with victron) engine start, one isolated bilge pump mounted higher in the bilge. In use, each battery bank will be charged by any charging source, but the lead acid will see me through surprises. It worked out to be no real difference in price to put it all together using a Lynx set from Victron vs buying fuses individually. Similar to the above BMS, but I’m doing it using a ML-ACR with remote switch for over-ride. Alt will always be direct to the lead acid, but the manual switch can be used to start off the lithium. To solve my back and forth on nav lights, VHF/plotter etc, I am reversing a set of 3 way toggle switches; 2 in one out. So by default my start sequence will look like this: over-ride ACR with remote switch, start. Nav light etc switches in Pos 1 means everything is off lithium. If it goes down for whatever reason, toggling the switches to Pos 2 means my AGM will keep critical systems going. It does require a bit more manual interaction, but to me gives the best combination of reliability and minimizing extra thinking bits. I have a funny story about chasing a GFI in a Nordhaven recently. Ended up they rail mounted them behind the panels requiring tools to access. All was well until the thinking bits reached a different conclusion than anticipated.
Weight savings & the number of cycles on the life of the battery are only part of the appeal of a Lithium house bank.
Much better charging efficiency means the generator runs can be significantly shorter (huge benefit IMO) and the solar charging is more efficient. Maintaining a constant voltage well above 12V (even when under higher loads like running a microwave to warm up leftovers) is also appealing as some instruments and devices (eg Wallas heater) are more sensitive to low voltage states.
My 660 Amp-hour Firefly House bank will drift pretty close to 12.1V by the time I’m at a ~ 300 A-h deficit & there is no way we are warming up leftovers when we are anything but close to a full charge.
The Fireflies are still working well enough but my next house bank will almost certainly be LiPO4.
-evan
Hi Evan,
Good points, but I would still argue that the fundamental is the weight and size benefit of lithium.
For example there is no reason you could not increase generator efficiency with lead acids just by making the bank bigger, and in fact there are AGMs (LifeLine) that have higher acceptance current specifications than most lithiums.
I also can’t see why solar is more efficient? I’m guessing that what you mean is lithiums have no tail off current at higher charge level, which is of course correct, but I take that into account above by only using 40% for the effective capacity of lead acid, not 50%.
Bottom line, I think we are saying the same thing in a different way:
Lithium batteries allow us to have more capacity in the same space.
I’m also surprised your inverter won’t power the microwave when the bank is anything other than full. In my testing of induction I did not get inverter shutdowns until the AGM bank was well below 50%. Maybe worth having a look at the inverter or posibly the cabling between it and the battery.
In this post you can see my inverter happily suppling nearly 2kW to an induction ring with the input voltage at 11.
https://www.morganscloud.com/2020/10/25/induction-cooking-for-boats-part-1-is-it-practical/
Hi John,
I should have been clearer in my description. My inverter keeps going but the house bank voltage drops off from say 12.4V to 11.9V after a minute or som of microwave use. It’s winter and the heater is running and I don’t want the voltage to drop less than 12.0V
As I understand it, a LiPO4 house bank would not do this.
Also, AGM’s like to be brought up to a full state of charge frequently, so that last 10% of charging is important for AGM battery health whereas the Lithium bank, or the Fireflies too for that matter, are happy to be in a partial SOC and do not need that extra hour or so of generator run.
Hi Evan,
I hear you on the heater problem. Good point, our Espar was voltage sensitive too. One way to solve that, that I thought about, but never implemented, would be to run the Espar (or similar) from a DC/DC power supply.
Sorry, I don’t want to be pedantic, but equally I’m trying to make sure that people don’t migrate to lithium because of a problem with lead acid that’s solved. For example there is no need to run the generator for extra time to bring AGM’s up to a 100%. First full charge only needs to be done about once a week and second even a small solar array can get rid of the problem completely. As I say in the article, it’s a solved problem.
Don’t get me wrong, I’m not trying to talk anyone out of lithium, just trying to simplify the decision to what really matters: weight and size for a given capacity.
Not to put too fine a point on it, but my experience this past weekend underscores an issue I would think a LiPO4 house bank could solve: Rapid charging.
My wife & I just did an overnight trip to one of our favorite anchorages ~ 2 hours away from where we keep the boat. ( I have switched to a bulk charging / no float regimen for our 660A/h Firefly house bank when on shore power so can get to the boat with it less than fully charged.) On arrival we were still down ~120 A/h from a full SOC despite a 2 hour run on a 120A alternator. I ran the generator for an hour around supper. After our overnight stay with the heater running & a few extravagances (think Starlink & streaming a movie) we were down to -335 A/h in the morning
After raising anchor & heading home, I had the generator running, feeding 2 battery chargers & with the engine alternator working well (it was a foggy morning so no help from the solar panels), we were pushing 210 Amps into the bank. An hour later this was down to 95 Amps at 13.74V.
By the time we arrived home, we were still only at 90% SOC and pushing ~70 amps into the bank.
This doesn’t matter much in this scenario as we returned to port to plug into shore power; but I would like the house bank to accept everything we can throw at it in as short a time as is practical. If we had been moving to a new anchorage we would still be starting the winter afternoon/evening in a deficit.
My understanding is that a LiPO4 bank would have maintained this ~ 200A+ acceptance and be nicely full in an hour and a half. (Other sources & Andre’s comment seems to support this expectation.) This would be a very compelling reason to consider LiPO4 over lead acid.
– evan
Hi Evan,
Well, fundamentally a 660 A-h battery bank is way too small for a boat that’s going to burn through ~300 A-h in less than 24 hours, that’s the fundamental problem here, not chemistry type, or charging speed.
Remember we must think in effective capacity and lead acid effective capacity is ~40%. So in your case your effective capacity is only 264 A/h, so no wonder you are frustrated if you are going through > 300 A-h in an evening and overnight.
If you were to continue with lead acid you would want a (guess here because I don’t have all the details) a 1200 A/h bank (effective 480 A-h) probably closer to 1500.
So the first thing to do is accurately figure out what your battery bank size should be. We have a post and spreadsheet to help with that: https://www.morganscloud.com/2019/01/23/cruising-boat-electrical-system-design-part-3-specifying-optimal-battery-bank-size/
Then once you have that figured out, it still comes down to the two questions in the above Chapter. Given your usage I would guess that you are right lithium will be the only way to achieve the effective bank size you need at a weight and size you can live with, but it’s as well to come at this in a systematic way, all the same.
Of course the other option is to look at your loads. Just as a bench mark, on our McCurdy and Rhodes 56 we were about half that usage and had an 800 A/h lead acid battery which served us well, often going 2 days without the need to charge—we did have a holding plate fridge which makes a difference.
Also keep in mind that lithium batteries have charge acceptance limits too, they don’t take “everything you can throw at them” so the ratio of charging source output to bank size is important. Again, the spreadsheet can help with that.
Hope that helps.
Thanks John,
I don’t wish to hijack this discussion any more than I have already; but, as a case study, it may be useful for this question of why go LiPO4 when good old lead acid may be good enough…
This past weekend was an anomaly in that we left the dock with a significant SOC deficit but if we had been at anchor for a couple of days, the daily charge requirement in winter would still be in the 300+ range. (Your comments will prompt me to do an another inventory on my loads again but I do not see much that I can cut out of the load side of the equation. We have all LED lighting and I have, in the past looked hard in vain for any parasitic loads.)
Summertime is not so much of a problem as we have 550W of solar and long days to maximize power delivery.
In wintertime though, at anchor with a NMEA 2000 network with redundant GPS’, wind instruments, a fridge and a freezer, & a diesel heater running 24/7 along with the inverter supplying power to a laptop (with requisite anchor alarm) and a few other assorted devices we average 13-15 amps draw per hour. We just added a new Starlink which looks to be drawing another 2 – 4 amps when it is on, potentially bringing us even closer to a rather horrifying 18-20A per hour. In winter, the solar panels don’t add much to the charging input so, yes, with potentially 360 A/h per day at anchor, my house bank is probably too small.
Nevertheless, adding more lead acid storage to get to 1200 A/h (even if I could find more Fireflies and find the space for them) would not address the problem of the prolonged daily charging cycle to replace ~350 A/h with the tapering charge profile of the lead acid batteries limiting the efficiency. With a 9.5 KW generator and a Magnum 2800W charger, and a 40Amp Xantrex auxiliary charger,(+ 120A alternator) I don’t really think that I need more charging capacity, I just need the bank to be more efficient at accepting the offered charging current. I really do not want 4 hours of generator time per day to get back to 100% SOC.
Thus; LiPO4 makes the most sense for the next house bank.
Hi Evan,
You seem to be tech savvy enough to make good choices already. You’re probably right that lithium is the best solution for you. Since you wish to use the fast charge properties, you need to be careful with which lithium setup you chose. Most drop-in batteries (12V battery box with BMS inside) are limited on current capacity. They’re usually better than similar size AGM, but not by as much as many think. To exploit the insane current capacity of the raw cells, you need either a very serious integrated battery, no drop-in, or better; separate 3,2V cells with external good BMS etc.
I’d also suspect that you can find ways of reducing consumption. I notice that you run a laptop via an inverter. Perhaps also phone chargers etc? That will, according to Rod Collins and several others, make your items consume at least twice as much as it would if you turned off the inverter and ran them via a DC converter straight from 12V. Your laptop is probably running on 19V DC. All that back and forth transformation, DC to AC, low voltage to high voltage, high voltage back to low voltage, AC back to DC, makes more trouble than the stated efficiency numbers from the inverter maker indicate. An inverter on a boat should close to always be off.
Hi Stein,
I agree on the use reduction suggestions, thank you.
However I can’t agree with the blanket statement that lithiums can take a higher charge current than AGMs. In fact AGMs from Lifeline can take far more charge and charge inrush current (up to five times capacity) than even high quality lithiums from Victron, and a great deal more than “drop in” lithiums with an internal BMS.
Sources:
https://www.victronenergy.com/upload/documents/Datasheet-12,8-&-25,6-Volt-lithium-iron-phosphate-batteries-Smart-EN.pdf
https://lifelinebatteries.com/wp-content/uploads/2015/12/6-0101F-Lifeline-Technical-Manual-Final-5-06-19.pdf
https://www.solar-electric.com/lib/wind-sun/Battle_Born_Manual.pdf
Thank you Stein.
Your suggestion to turn off the inverter is a very good one, as the obligatory basal draw from the Inverter unit is quite significant. The primary reason to keep it going was to feed the laptop but as you suggest, a simple 12V to 19V step-up converter for the laptop and converting the phone chargers to DC USB outlets should decrease the need for the inverter to be on for the majority of the time.
-evan
Thank you Stein.
Your comments are very helpful and have prompted me to make some changes.
I’ve done a little more inventory as to my power usage. My Magnum Inverter is drawing close to 3 amps at idle. (~70 A/h per day).
I have been using the inverter to power the navigational laptop and various AC chargers to phones, iPad, flashlights etc. thinking I need these on at all times. It makes much more sense to get these off AC and onto DC power sources in order to allow me to turn off the inverter (except when needed for brief usage of a few AC-only appliances).
I bought a DC-DC converter to power the laptop. That works well.
All smaller devices can be charged through DC USB outlets
The Starlink does not run 24/7 but when it is on, it has a significant impact on my power usage. I have the parts on order to convert the Starlink to DC power which should reduce its power requirements from ~ 55-60W to 30-35W. (With no need for the inverter and this reduction in power draw, the Starlink related loads should go from 6-7A down to ~ 2-3A.)
Anyways, I appreciate your thoughtful comments (and John’s comments) to nudge me to look at the house loads a little more closely.
-evan
Hi Evan,
While I agree with your end conclusion, assuming you can’t cut consumption, I still don’t agree that the problem is charge efficiency. If your bank was lead acid and big enough it would take everything your alternator and generator put together could produce from about 50% to 80% charge and only tail off slightly to 90%, and there would be no need to keep charging for the last 10% except for once a week or so which the solar or shore power could accomplish with a bit of management. So, for example, if you had 1200 A-h of batteries 40% is 480 A-h that could be charged at about 200% of your current available charging capacity, which would be fine.
Also, from a systems architecture point of view your alternator is too small. With that kind of usage at least 200 Amps would be better and 250 better yet. Again the spreadsheet I recommended will help with that.
In addition given that you have a 9.5 Kw generator and assuming you are going to up the bank size to one capable of supporting your usage I would suggest that you will also want to consider adding more charger capacity, probably a lot more. I have a case study on that here: https://www.morganscloud.com/2018/06/29/reducing-ac-generator-run-time/
The point being that just throwing money at lithium is not going to fix this, rather you need to look at the whole system.
One other thought. I’m guessing your current issues are made worse by your batteries being sulphated, which cuts charge efficiency a lot, so worth running a conditioning cycle on them as per the Firefly manual. The reason I say that is you mentioned that when you left the marina you were already down a lot so I’m guessing you have loads on when the boat is not being used and since you are not leaving the chargers on the batteries are spending a lot of their lives in a partial state of charge. By the way, this is another good reason to go to lithium since they don’t have a problem with this usage.
Hi again John,
Your advice and comments are appreciated.
Although leaving an anchorage in the morning with a charge deficit of 180 A/h is not uncommon, it might seem a little odd when the boat was docked and on shore power.
A little background explanation is in order:
I was noticing that when using the boat after being on shore power for a while, the house bank would drop its voltage rather quickly with only a modest draw; but this would improve after even one or two discharge /recharge cycles. I had been using the typical float charge when on shore power at our home dock.
This has begged me for quite a while but I was unaware that Firefly had modified their manual to be more specific. As per the revised Firefly manual, it is recommended against having the Fireflies left in a float 100% SOC and using a different charging scheme for their “storage state”. I recently switched to their recommended Constant Current / Constant Voltage charging regimen for the FF house bank. The Magnum charger will start charging when the house bank voltage hits a programmed number (12.1V) and charge for a specified duration (10 hrs) or until the charging current hits < a set current (5A). (I have the Lifeline start battery isolated on a separate charger circuit with a typical Lead acid float profile.). The fridge, freezer, heat pump etc. are all on AC. Virtually all DC loads are off except for my aging Raymarine autopilot which does not take kindly to being turned off and on and the NMEA 2000 network. (The total DC load is trivial when at the dock.)
This new regimen seems to be working in that the FF bank maintains its voltage better under load when first out but it also means that if I get to the boat at a point when it is at a nadir in the cycle, it may have a SOC deficit when we leave the dock. This is why we started our overnight trip at a deficit.
I may need to change the parameters to a higher trigger point for starting a recharge cycle but will not likely go back to the typical float regimen.
(I do need to do a deep discharge to ~10.5V with an aggressive recharge cycle as per the manual (equivalent to an equalization routine) but I need a chance to do that over a few days with all instruments and sensitive electronics turned off.
Anyways, I hope that fills in the blanks a bit.
-evan
Hi Evan,
Thanks for the fill.
Another area I would look at is the way small loads add up. For example leaving the NMEA 2000 network on for 24 hours while at anchor could easily add 50 Ah to your usage. 2 amps is not unusual for a NMEA 2000 network, mine is 2.2 amps, although that does depend on the number of devices that are powered by the network itself.
So turning that off could save nearly 15% of your daily at anchor use. Add that to the savings Stein suggests and I think you might be able to save 100 Ah a day, which would go a long way to solving your problem.
I say this because I have noticed in recent years when anchored with other cruising boats the glow coming from cockpits of instrumentation and plotters left on all night, definitely a new trend.
Hi again John.
When at anchor, I use my laptop to run Coastal Explorer and to maintain a continuous anchor alarm. I also appreciate knowing the outside temperature, wind speed data, AIS info etc. so feel pretty committed to keeping my NMEA 2000 instruments up and running.
As I’ve posted above, I think I may have found some other power savings and with your suggestion of using DC-DC converters to mitigate some of the negative effects of lower voltages on voltage sensitive devices, I think I may have a workable solution to my situation.
I will look to adding another 40-50 Amps of charging.
I hope you don’t mind all my comments on this thread; but, perhaps others might find it useful in considering similar issues with their own systems?
-evan
I have been doing a lot of thinking about the many issues discussed here. A number of good suggestions have been made and I am seeing a number of ways that I might carry on with my FireFly house bank for a few more years.
Your suggestion of using a DC-DC converter to power the Wallas heater with a controlled, more favourable, voltage makes very good sense. I think I will try that, as on paper, it is probably the most voltage sensitive device on the DC side of the system. (I have yet to have it cut out or quit at even 12.0V but in the written specs, it wants a minimum of 12.6V for startup and operation.)
It might also make sense to have a DC-DC converter to provide more consistent voltages for the more sensitive instruments and NMEA 2000 network?
With these devices protected against lower voltages, I could be less concerned when the house bank voltage drops a little below 12.0V…
Hi Evan,
I would not worry about a DC-DC converter for the electronics. Most are quite happy down even as far as 11 volts or so, or at least that’s been my experience.
This discussion has been quite useful to me. Thank you.
I’ve been wrestling with this question of replacing my Lead acid (Carbon Foam) house bank vs LiPO4 for my boat for a while now.
One major factor that prompted me to consider LiPO4 was that I was under the impression that I should never allow the house bank voltage to drop below 12.0V.
In hindsight, I am not sure where I got that idea. I was under the impression that my Wallas Heater and the NMEA 2000 network and its associated devices would not tolerate voltages lower than 12.0V
Like so many things, it doesn’t hurt to review the documentation.
The official documentation for the Wallas heater is rather sparse but states that it does not like to be started at a voltage below 12.6V; but it has never stalled in its startup cycle even at voltages as low as 12.3V. As it turns out, it will apparently tolerate operating voltages as low as 11.0V…
Your comment that NMEA 2000 networks and and instruments should be tolerant of voltages well below 12.0V prompted me to look into this and indeed 9.0V is listed as the minimum for the NMEA 2000 network. I would not a want to be anywhere near that but it suggests that dropping into the 11.8 – 11.9V range would not cause any grief.
So, if we can allow the system to drop into the 11.9V range I would have at least another 1/2 to full day of usage in dark winter days on the hook and the need to consider a LiPO4 upgrade decreases significantly.
The slower charging is a nuisance in that the generator runs in winter stretch into 2 – 3 hours a day but we have a very quiet and fuel efficient generator that really deserves to be run regularly anyway.
I have also been prompted by this discussion to look to reducing the demand side of the equation. I have have made changes that allow me to turn off the inverter. I’ve converted the navigation laptop, all phone chargers, Starlink and assorted other devices to DC power. Doing this, it looks like I can reduce my average power requirements by around 5A or so or ~ 120 Ah / day: Not insignificant.
Anyways, I appreciate the useful information and guidance here.
Thank you.
-evan
Hi Evan,
Glad things are coming together for you.
Yes, voltage is not a good way to access the state of charge of a battery under load since it varies a lot with said load regardless of state of charge. I explain why in this chapter: https://www.morganscloud.com/2016/05/24/one-simple-law-that-makes-electrical-systems-easy-to-understand/
Voltage only works to determine state of charge if the battery is completely isolated from all loads and even then only after it has been left unloaded for about an hour.
This is why we need to rely on battery monitors: https://www.morganscloud.com/2018/08/13/battery-monitors-part-1-which-type-is-right-for-you/
Hi John,
Yes. I totally understand why voltage is a poor indicator of a battery bank’s SOC.
(I have a Victron Shunt and monitor the SOC pretty religiously through Bluetooth. )
My point above was, that despite the state of charge, I was loath to let my system drop below 12.0V fearing damage to the more sensitive DC instruments and devices in the system.
Having looked at this arbitrary threshold more closely though, it looks like there is no reason to not make something like 11.7V or even11.5V the new limit to how low I can go. It does not appear to be a risk to the instruments or even the supposedly voltage sensitive heater.
(I appreciate that deeper discharges shorten the overall lifespan of carbon foam batteries but these Fireflies seem to perform better with occasional deeper discharges.)
This might be a good question for another post:
How low is too low for house bank voltage?
Hi Evan,
That’s not an answerable question as long as the battery is under load, so not worth an article. And if the battery is not under load, there are plenty of tables online that relate state of charge to at rest voltage, but I don’t use them much because it’s just not that useful on a boat.
Indeed Victron recommend to put charge efficiency at 99% for their Smart Lithium. I notice since my installation that the battery charge faster because of this increase efficiency. Its notable.
Dear John et al
My current batteries are failing, all together and all at once. They need replacing. So I read all these articles with urgent interest.
The seductive allure of lithium is obvious but the need to apply backup systems and three types of batteries combined with a complicated array of control systems ? Aargh! I just want some new batteries so I can go sailing.
All these discussions must be catnip to those who imbibed Ohms law with their mother’s milk and who delight in these matters but to those of us who were too thick to pass their advanced mathematics exams they are excoriatingly and opaquely irritating. I hesitate to say tedious for they do matter. But my eyes cloud over and I am filled with a deep sense of ennui.
Warren Buffet advises investors, and here I paraphrase, that if you don’t understand what the company does don’t invest in it.
So I deduce from all this that if I invest in a unitary bank of Victron super cycle AGM batteries and the requisite Victron gizmos to control it I will get at minimum 3 years non stop usage and probably more. Realistically, including void periods when life and fate prevents me from going sailing, I will get five years. (As long as I don’t do something deeply stupid but then the same caveat would apply to any batteries.). By which time I will be 73. If I’m still fit then I will thank my lucky stars and then look again at lithium. Maybe by then it will be cheaper and simpler to operate. Planning ten years ahead at my time of life might be seen by the gods as presumptuous.
As for the weight and space saving that comes with lithium its a nice idea but I’m a single hander in a 40 footer and the the battery compartments are already conveniently located near the engine and the middle of the boat and there is adequate storage space elsewhere. (I’m a bit of a weight watching fascist as regards the storing of the boat.) I have an adequate solar array so charging isn’t a major issue. And from what I read the new AGM batteries offer the option of deeper discharge than the previous generation so I may well already be getting more bang for my buck.
Mark its not that complicated, manufacturers like Victron have scientist and a lot of knowlege more than us sailor so they have product that support the ABYC TE13 requirement and enable mixing AGM and Lithium safely BECAUSE they are clever and they designed the AGM to have the same charge profile as the Lithium. I wish i could help you.
Hi Andre,
As a fellow nerd, but one who spent decades in high tech user support, and kinda still am doing that, is that the great blind spot of nerds is inability to see that what is simple to them, is not simple to non nerds.
Hi Mark,
I think that’s a very sensible analysis and given that you have a good solar bank my guess is that three years is very conservative. My guess is your new lead-acid bank will go at least five years of full time use and I would also guess that by that time there will be a less expensive and easier to install lithium option. In fact I have insider information that there’s a company working on just that in a full turn key system.
Will Adventure 40 have lithium or Acid?
or better to ask, which one you think it should have.
Thanks
Hi Ignat,
In keeping with A40 core principles the boat will come with lead acid batteries as standard.
That said, again in keeping with core principles, we are planning to design the system to make it as easy as possible for an owner to upgrade to lithium.
A40 core principles: https://www.morganscloud.com/2014/08/31/twenty-adventure-40-core-principles/
thank you and I think that’s the shortest answer to the question posed in this article 🙂
I have two Lifeline 8D, 255 amp AGMs on my coastal used boat. They lasted 6 years before being killed by negligence of Marina staff. Given my usage they could have lasted another 3 years. I have been reimbursed for replacement costs. Lithium then became lustium. I thought why not with such a head start on the cost? Well, once you find out that you need to replace your 9 year old magnum Charger/inverter and it’s controller and a new regulater to replace the old Balmar 612 and maybe some type of isolator and a new Victron shunt and other miscellany and pay a true professional to install it and set it up you realize that the gain isn’t worth the cost. Not for 5-7 day cruises. If I were going on a long term cruise then I would switch. So, for me it’s about how one uses his boat and is there a break even point when your a 75 yr old sailor. I am now recovered from Lustium.
Hi Mike,
A very sensible analysis, thank you. I came to the same conclusion for the same sort of usage on out J/109.
One thing I have noticed is that as I age (71) I get better at figuring out what really matters. I guess having a shorter amount of what a friend calls “quality time remaining” focuses us. I also fervently wish I had back all the time I wasted on non essentials when I was younger.
Love the Lustium term
Hi John,
As you know, I can be counted on the side of the lithium fanboys, and I’m definitely on the nerd side of it. I’m happy to report that I agree with every word in this article. Of course one can dig into loads of detail with specific systems, but the point here was to make it simple so that people can see the main points. Applause for that!
I also like to say that if your lead acid batteries do the job well now, why pay 4 times the price for the same job? Why buy a Ferrari if you will never drive faster than 100 km/h / 60 mph? If we regularly spend extended periods with solar etc as our main charging source, lithium is a life changer. Same if we regularly use a lot of power. If we either plug into a dock most nights or use our engine most days when we’re cruising, lead acid is totally able to do the job. We won’t notice any reason for paying a lot more.
One detail, that doesn’t diminish anything of the above evaluation: The point mentioned by Evan about improved solar charging is something I’ve also noticed on several boats that have gotten lithium and kept the solar setup unchanged. According to the battery monitor, the Watt hours gathered per day goes to very roughly double what it was. Changing from lead to lithium sort of makes the solar panels “twice as big”. I can’t give a complete explanation for it. It’s just an approximate observation. My guess is that several factors are relevant.
Probably the most important factor is that lithium will always receive all the charge current it is given and store it in the cells with about 98% efficiency, even when close to fully charged. Lead acid can also be quite efficient at low to mid charge levels, above 90% efficient, but as the charge level rises and the resistance increases, charge efficiency drops fast. Closer to full, the current acceptance also wastes much charge power, especially from a big array. This happens well before 90% full, where most boats tend to hover a lot in the day time.
But again: This solar thing is a detail that is nice to know, while the simple main issues relevant for making a choice are the ones discussed in the article. Letting our love for the lates tech take us for a ride can often (but not always) be expensive and give little benefit.
Hi Stein,
I understand charge tail off on lead acid batteries better than most, and base on that I’m very uncomfortable with dramatic claims like you will get double the daily charge out of the same solar bank by connecting it to lithium. Sure that would be true if one were cycling the bank between say 80% and 100% on a daily basis, but that would just mean that the system design was very poor with too much solar in relation to battery bank size, a huge waste of money, weight and windage.
With the right design the difference will be more on the order of 10% to 20% and very large amount of money, weight and windage can be saved when we get away from the “I want the biggest battery bank and solar array in the marina to impress everyone” and apply logic and good system design.
Anyway, we have am article coming that will help people really parse that issue for their own usage profile.
Hi Stein,
Your comment on the picture of Rob’s lithium install reminded me of this comment. I didn’t respond when you made it as I didn’t want to front-run the article on battery and solar sizing but I think a major contributor to people reporting more solar output with lithium is likely that they installed more battery capacity and are more willing to be at lower SOC. It could also be that people increase their usage when they increase their capacity. With a small battery bank, on the cloudy days you get forced to run another charge source like an engine or generator to not drop to too low of an SOC and that energy is now not solar energy. On the sunny days, you are more likely to get into absorption or float so no useful solar then. For max solar efficiency, we would have a giant battery that would never drop below minimum SOC and never get into absorption.
There is a straight up charging efficiency too but it isn’t nearly as big as the difference claims some are making.
Eric
Hi John,
I think this is a very good way to look at it. I started to think about the advantage of faster charge acceptance rates as I was reading but your earlier comment is right, this is actually a bank sizing question. There is some truth to charge efficiency differences but it isn’t a large difference until you get to high states of charge with big charging sources on lead acid which is poor system design anyways.
In my case, I would love to save the weight but I don’t think it would make huge performance differences for us and I am sure I could get bigger gains by spending the money on other things like fancier sails. Ignoring the money issue, I want to wait until lithium becomes more widely adopted and things like insurance requirements, availability of components, etc. becomes a lot more stable. I certainly think it is possible to build a good lithium system these days if you have the right technical knowledge but going back to your questions, I am not willing to put in the effort yet.
Future proofing systems is a very interesting topic. I can say that professionally I have learned to completely ignore it unless someone really can give you hard interface requirements for something that is close to completion of development. Everything else just ends up being a huge distraction and you end up compromising your design for all sorts of hypotheticals that usually end up not actually being compatible when that thing ends up eventually being developed. Unfortunately, future proofing is one of those things that sounds good in a white board discussion and it is a buzzword in marketing so it eats a lot of time for almost no value. That being said, if I were replacing something like our alternator external regulator right now, I would try to get one that has the most controllability but I wouldn’t spend significantly more money or effort to do it. I expect to replace our GC2’s in probably 2 years with another set and when they die it will be 10-12 years from now probably. Whether LFP is the prevailing chemistry at that point (solid state?), whether a company like Wakespeed is still in business to keep updating their interface with BMS’s, etc. are all questions that have answers that are significantly lower than 100%. This doesn’t make something like the Wakespeed a bad product but I would buy it because it was the right product for now as opposed to a hypothetical future. Maybe I am pessimistic but I usually find that I end up having to replace entire systems as a unit and upgrading to a fundamentally different thing like lithium is not possible to do piecemeal.
Eric
Hi Eric,
Good points, but I think there’s still room for making it easier for those who will install lithium in the near future, as several A40 owners might do in the first year of ownership. It’s far easier to predict what can make their life easier the first year or two after purchase, while also fitting lead acid.
Choosing the right chargers is one example. This model from Victron https://www.victronenergy.com/chargers/phoenix-smart-ip43-charger is completely programmable via an app, gives 50 Amp at 12V, (25 Amp with the 24V version) can be parallelled with another of the same for more power, is water resistant, has no fan. Most modern boats go for inverter chargers, but most smart cruisers have no need for AC when unplugged. Owners can then add the inverter they wish. A pure charger seems like the right standard solution. Great for lead acid and perfect for any other battery chemistry I know of now.
Another thing that could be future proofed is to go for fuse systems that have large gaps when in the open positions, to prevent the arcing lithium is capable of. There are probably many more issues, but I’d assume one would stick to modifications that don’t add noticeably to cost and complexity, and that might also enhance the system quality for a lead acid system.
Hi Stein,
I agree on the A40, particularly since I think that many owners will immediately go to lithium when they get the boat. In my view that’s would be a big mistake (I would go sailing) but that does not mean we should not allow for it as much as we can, like, as you say, using the right fuse holders.
As to chargers, good point, but the A40 won’t come with a charger as standard, and not even shore power if I have my way, although that will be easy to install to support the buyers preferred voltage.
All of this fits in the A40 core principles: https://www.morganscloud.com/2014/08/31/twenty-adventure-40-core-principles/
Hi John,
I think the no charger and no shore power installation might be a good call. I’ve never bought a new cruiser, so maybe this doesn’t count, but with any new to me boat I’ve invariably replaced everything related to shore power, including the charger. The consequences of faults are too big to accept anything but perfect. I think I’d do it on any new boat too. My definitions are probably not universal, to say the least, so avoiding discussions with people like me is smart. 😀
By the way, the mentioned charger does take any shore power voltage and frequency you feed it and makes out of it exactly what you told it to feed the batteries, and how you told it to do it. Pretty neat stuff, but since it’s such an easy thing to install, I se no reason why the builder should do it.
Hi Stein,
I think you are totally right that there should be no shore power as standard. As you say, there are chargers that are universal, but that does not solve the problems for the builder since there are so many other differences between European and North American systems. The plugs are just the start of it, since the safety standards are also quite different.
The only way I can see to do a universal system would include an isolation transformer and all kinds of other complications. Think adding at least Euro 5000 to the price (wild guess) and then, as you say, half of the buyers would want to argue about the decisions made.
A40 Comment: Possible Owner upgrades and improvements.
Is there is a large protected surface for mounting necessary electrical equipment and cables? Preferably behind some large cabinet doors.
Is there a large well ventilated battery box or cabinet inside and not part of the engine area?
Is there relatively easy access to run cables for solar and to and from the engine area? Where is it?
Having a small boat without these features I am very aware of the need.
Thanks for the good discussion.
Hi Fredric,
Have a read through of the early articles on the A40.
Most all of your mechanical and electrical questions are answered there, although final details will come later in the engineering phase of the design: https://www.morganscloud.com/category/boat-design-selection/adventure-40/
Hi Frederic,
See my previous comment about having a read through, but here’s the spoiler…yes.
Hi Stein,
I wasn’t thinking specifically about the A40 when writing my comment but if I were the one making the decisions, I would still generally apply it. In line with John’s comment, I would try to set things up per best practices with the right fuses, bus separation, etc. but I don’t see that as chemistry specific. What I wouldn’t do is try to select fancy components such as chargers, alternator regulators, etc. with too much emphasis on lithium. I do think a significant portion of buyers will go out and immediately switch to lithium so in many ways this isn’t even future proofing, it is now proofing. But I would certainly not drive up the base cost measurably or create a situation where you could drop in a lithium bank with doing nothing else because invariably the consumers won’t even agree with what has been done as is shown by endless debates on the right way to set it up, this is not a mature implementation yet. Back to future proofing, I think the best you can count on is to make the system upgradable now but if someone switches to the latest in battery tech in 15 years, they will likely require more than new batteries. Heck, many of the electronics don’t last that long anyways.
Eric
Hi Eric,
That makes perfect sense to me. The good news is that no fancy stuff will be supplied standard with the A40 so it won’t be the builder’s problem and owners can do whatever they like. As you know, this is a lot of the reason we think we can deliver a quality boat at an unprecedented price. And it’s not just the savings in fancy gear not bought, but also the huge time and resource savings from not getting into all those complications and ambiguity, not to speak of long arguments with every potential buyer about every piece of standard kit.
Hi Eric,
Good point on the fallacy of future proofing, particularly for more than a couple of years out. As someone with a long career in computers, first hardware, then software, I could not agree more. I can’t count the number of times I have rolled my eyes at some salesman claiming their product is “future proof”.
I’m more thinking of fundamental stuff we can do that’s easy and not expensive, like separating the charge and discharge buss bars and using T fuses that can withstand a dead short of a lithium battery without welding closed.
Hi again Eric,
Great to have your confirmation of the basic methodology of the article, particularly since it fits in with your personal experience. Thank you.
My comment will seem off topic but its not. Read on. I just read the story of that french crew who was attacked by Orcas west of Portugal. After multiple attacks by a groupe of whales, the rudder post was torn out from the bottom of the hull and the boat finally sank. Why I’m bringing that story here is because when reading it, (“Voiles et voiliers” february 2023), the skipper explained he was using his main VHF instead of the handheld, because the transmission was much better. Also, in addition to the manual pump, he turned on all electrical pumps (bilge, shower). The most interesting words he said was that he was surprised that the batteries were still working under 3 feet of sea water.
Which is the point of this comment. Would Lithium batteries, with their sophisticated electronics, would still work under 3 or 6 feet of sea water? For how long? As we can imagine, it could be crucial to keep working batteries under any kind of emergency where the batteries might be submerged.
Battery can work under water for some time and its documented in many boating forums. But i wouldn’t expect this to work for hours…mainly a few minutes. Any battery under sea water is shorted and start producing oxygen and hydrogen through electrolysis. Lithium battery electronic will go crazy with sea water and i would much more confident that AGM or Lead Acid would operate underwater than Lithiums.
Hi Pierre,
The Lithium cells themselves are totally sealed, unlike any type of lead acid battery. That means the cells, where the chemical action happens, will not be influenced by immersion. Most of the lithium batteries on cruisers are some type of drop-in battery. They normally use a non sealed box with open electronics. That will go just as you expect. The battery will certainly fail pretty immediately when the box is flooded.
However, there are versions that are fully sealed. They will work at least as long as lead acid batteries. Either way, I assume it won’t be too long. When both battery poles are immersed in salt water, quite a lot of current should flow between the poles, which should empty the battery. This is just my assumption. Perhaps somebody here has some numbers?
It should be theoretically possible to make a completely protected system, where also the poles and all electronics are sealed, but I doubt if it will be worth the effort.
Hi Pierre,
My guess would be pretty much the same as Andrea’s thoughts.
To sum it up, if the lithium battery’s BMS is not water proof, it would fail very soon after the battery is submerged.
I’ve seen a guy who has setup his electrical system such as the critical instruments (GPS, VHF, etc) are powered by a small 12 volts lead acid battery (a motorcycle battery I tink) which is placed very high in the boat. So in the case of a serious and prolonged water ingres, these critical devices would still work even if the main house batteries are submerged and discharged. This would be an interesting backup plan, both for a lithium bank and a lead acid bank.
Hi Pierre,
I agree that backing up that way is a good idea, that said, for different reasons: https://www.morganscloud.com/2022/07/03/building-a-seamanlike-lithium-battery-system/
One point on installing separate charger and inverter versus combined.
I’ve installed Victron 12v 50A smart charger because it can work anywhere- it accepts 100V and 220V, while MultiPlus inverter/charger you need to buy for specific voltage.
Great distillation John. We have the MCA surveyor coming Monday to do the full commercial inspection on FALKEN, and a big part of it is the electrical system. The MCA don’t yet have a commercial standard for house lithium batteries, so we, along with Bruce at OPE, have had to provide a compelling case as to why they are safe. It’s been an interesting process.
The new system is fully operational now!
Hi Andy,
Great to hear you have it all done and with Bruce and Nigel in the process I’m sure it’s a good system. Interesting about MCA not having a standard yet. When they do, I hope the do a better job of it than ABYC E13.
What about the restriction on charging below freezing? My understanding is that most (all?) BMSs block charging below 0C. That has been the non-starter for me on both my last and current boat. Because they are multihulls and the batteries are in the bridge deck, they absolutely go well below freezing for days or weeks at a time, even if I am on the boat. Heating (like Tesla) makes no sense, I do need a sump pump, and I don’t completely trust shore power not to fail for either local or ice storm reasons. I use solar for winter battery maintenance. I could figure out a lead work around, but that’s one more thing. And even if I did, they would not be useable for winter cruising. Perhaps mostly a multihull thing, though a shame, since we have the greatest motivations to save weight. We’re seeing a lot of lithium on new multihulls, but if you ask the builders about sub-freezing operation, you get blank stares.
I should have mentioned that storage below freezing on the hard is not a problem, as long as the charging sources are disconnected. Battery bank locations in the bilge generally do not freeze if the boat is in the water, although this depends on the specifics (how deep in the bilge, remembering that getting batteries wet is bad). Obviously, not that many people expereince conditions where both the bank is below freezing and they have need to charge it.
Hi Drew,
The “do not charge below freezing” is a real LFP chemistry issue, but it’s also partly a lead acid issue. The reason the BMS cuts charging is that the cells actually do get damaged by it. They can be charged at far below freezing, but then at very low current. Winston use a variation of chemistry with Yttrium to get LiFeYPo4, and they claim normal charging down to minus 5 C and at reduced rates down to minus 20 C (minus 4 F). They can probably go slightly further than the other makers, and I can’t dispute those numbers with any facts, but I’d be very careful with pushing those limits. Crossing the line apparently doesn’t cause sudden death, as some other actions can, but does cause much accelerated ageing.
In remote locations in Norway most lit sea lead markers have solar cells and lithium batteries. They’re expected to tolerate a bit of charging even at below 20 C minus (- 4 F) and still last many years, so it can be done.
We also have a cat and the batteries are also in the bridge deck, but in the salon sofa, where it does get chilly on really cold days, but never close to freezing. Our home harbour is Amsterdam and we live on our boat so we heat it, of course. If you need your batteries to give power during the winter, thus need charge, and also don’t keep the boat heated, I’m assuming that the amount of power needed is very limited? A seriously low charge Amperage might do the job? I don’t know. If you do want lithium for the house bank, you could disconnect it in the winter and let the backup lead acid backup battery do the job as house bank?
So LFP cells are not happy with proper charging below freezing. Are lead acid batteries better? Yes…, and no. They do not charge well below plus 15 degrees C (60 F) and the further below the harder it gets. At below freezing, they give minimal power out, and take even less. Also they must absolutely not be discharged significantly, as the previous mens it’s hard to reverse and the battery fluid in a low charged LA battery is closer to water than acid. Water will freeze and destroy the battery. A decent charge current will heat lead cells and (lithium cells too, if you really push power), but neither are straightforward tasks.
I have no better solution than, if we use our boar in really cold places, we should keep the batteries in or close to the heated areas. If we store our boat, when not in use, in proper cold, we probably need to have either:
– No power consumption at all, and batteries disconnected, or
– Very low consumption and very slow charging, or
– Somehow keep the batteries slightly warmer than the ambient temp.
All three strategies can be done with any battery chemistry, even though:
– Lithium drop-in batteries often will self drain from the BMS and electronics inside the box, that can’t be disconnected, so they need a charge now and then.
– Lead Acid prefer to be kept charging at a low maintenance voltage, like 13,4V. Charge at least once a month, preferably when the weather is non freezing.
– Separate lithium cells can be stored for years without charging, especially in a cold or freezing environment, as long as they are completely disconnected from everything, also free from the battery monitor, BMS etc. The cells alone have extremely low self discharge.
Hi Stein,
Sounds like a good analysis on Lithiums, although I have no experience with that.
On lead acid I have extensive experience both living aboard and storing a boat, but working on her, in cold places down to about -20c and have never had any problems or needed to treat the batteries in any specific way other than using a charger with temperature probes on the battery to increase the acceptance voltage as the temperature decreases. I have also not needed to charge once a month since when it gets cold self discharge goes to pretty much zero. (I used to worry about the supposed self discharge problem, but Eric Klem and Rod Collins corrected me on that.)
All that said, I don’t have any experience at temperatures below -20, where there may be more issues.
For those interested lifeline has good information on all of this. For example when fully charged one of their batteries will not freeze until -70C! And when at 50% charge at -25%C” https://lifelinebatteries.com/wp-content/uploads/2015/12/6-0101F-Lifeline-Technical-Manual-Final-5-06-19.pdf
They also have good graphs showing charge voltage and capacity by temperature.
The big thing to think about is that capacity drops with temperature, as Stein says, but this is not a problem as long as we have shore power available. If cruising off shore power, then it will, again as Stein says, be important to have the batteries in a location where they will be kept at least somewhat warm by the accommodation heating, 12C is plenty.
We cruised extensively in areas with water temperatures around 0C and air temps not a lot warmer and had no problems with lead acid.
Hi Stein, i live in Quebec and have stored my boat in winter with Lead Acid battery inside the boat, connected for 31 years. As you know we have temperature in the -20C for long period and winter is officially from December to March. No load and all battery disconnected i got 7 years of service on my first set of flooded lead acid battery and 8 years of service on the previous set. Now i have switched to Lithium and i’m quite concerned about what will happen next winter. I may bring the battery back home for the winter season…
Hi Andre,
I share your question mark about the new lithiums. The answer depends on what type and configuration they are. I’m certain that you can find a good routine for how to handle them in the winter.
I just wanted to hang on to your mention of flooded lead acid traction batteries, which are very competitive to any other battery type! They typically live 2-4 times as long as any AGM and can take far more abuse without dramatic issues. On raw data, they’re easily the strongest contender to lithium. The weaknesses (compared to consumeer adapted AGM batteries) is that they regularly need to be checked and refilled with distilled water, and that they emit a bit of explosive hydrogen gas when charging. That’s no exaggeration.
I was nearby when one big 48V bank exploded. An open boat, but a huge bang and much damage. Nobody hurt, except for acid burns and beeping ears for some days. (Not me). Caused by a tiny spark in a relay (we think). All those were removed.
Just to illustrate what this type of battery is capable of, I’ll mention (as I’ve done before in other contexts) that I work with electric tourist boats in Amsterdam. Skipper + tech supervision. Almost all of the boats have 2V FLA cells in 48V to 96V banks. The type you find in fork lifts and golf carts. The company I mostly work for now (Flagship) has 43 boats (at the moment), up to 20 meters (65 feet), 120 passengers and 40 metric tonnes. They run 8 to 15 hours nonstop every day the whole year and charge in the night only. The bank lasts typically 5 years of this heavy use. Flooded Lead Acid traction batteries are impressive stuff, but no set and forget.
A small number of the smaller boats here (other companies) have moved to lithium, but that’s not mainly to save weight and space but to get much faster charging. The night often gets a bit too short for the lead charge cycle, even at high current. The bigger boats charge at 96Volt 140 Amps, which is the same as 12Volt 1120 Amp… When all the boats come in and plug the chargers late in the evening, that harbour has a serious power draw! Try that at any normal marina… 😀
(We use several industrial 3-phase 240V = 360V supply lines). The current tapers off after some hours, so the batteries take too long to fill completely.
My main point is, there are very good alternatives to AGM and lithium. AGM might have the weakest performance of them all, especially their durability, to make the vendors happy, but it is indeed very easy to use…
Hi Andrea,
Hum, I can see how that would be an issue. I think the way I would come at this would be to use the backup system we recommend here: https://www.morganscloud.com/2022/07/03/building-a-seamanlike-lithium-battery-system/
Then in winter just switch over to “get home” mode, which isolates the lithiums from all loads and charge sources (see system block diagram).
Problem solved since, for example, the lithium batteries from Victron are good down to -45 c as long as they are not being used in any way. To be super safe you could pull the main buss fuses on the lithium side in case the “get home” switch was inadvertently which would also disconnect the DC/DC charger on the lithium side—all the work of 5 minutes.
Hi Drew,
Good point, as you and Stein say, this is a manageable problem, but on the other hand it does add significant complications when compared to lead-acid, so, in my view it comes under question 2: are we willing to take on the complications of lithium in exchange for the weight benefits.
One parting thought, slightly off topic. I like to post a voltage/temperature chart next to the panel as a reminder of where they are on the curve, both charging and discharging. This means little to the typical summer-only cruiser, who sees only a small temperature range, but it helps me. The other thing I have to remember is that solar becomes much less with shorter days and low sun angle, which is kind of why it’s winter. Small wonder solar is less talked about in the UK and northern climes.
Hi Drew,
Although I never did that in my cold water sailing years, it sounds like a very good idea. Awareness of issues is half the battle to reliability, I think.
Wow learned a lot here, I”m not that clued up yet, on all things battery and charging.
But I took simple laymen commonsensical
approach, I thought.
I Figure out what my usage would be and tripped it.worst case.
Then figured out what solar I need to put back in 5hrs a doubled it. +120amp alt, small but good in gray days to top up..
Then figured what storage I would need and tripled it. So I did not have to go below 30 40% draw down in 24hrs for my daily use.Have cut offs to shutdown unused system banks at anchor.
I cycled those AGM battery’s for 7 years, never plug-in to shore
Well I did, plugin ever 3 months to desulfate with a good q 8 stage charger.
So for me, AGM are very affordable. and easy install and management, cheaper components Plus AGM are recyclable apparently Lithium are not, so feels better to use them.and simple ….
Plus, I dont have microwave, (still dont trust them) I just have fridge freezer, phone laptops,cameras,nav,radios,pumps Cordless tools the basics stuff,
So keep the system lean as pos… seems to work…
And I understand it, and also I can troubleshoot.fix at sea, well most of the time…For me its one of those cases I dont want to fix what ant broke.
Hi Michael,
Sounds like, as you say, a good common sense approach, particularly focusing on keeping loads low since that’s the #1 thing that makes everything else easier.
Nicely well balanced article. One thing I think we will see is internal BMS batteries becoming the standard (even Victron have introduced them). Agree there are some low quality products, but if done properly, I think this is a better solution since if one battery does fail, it switches itself off and one or more others wired in parallel can keep going uninterrupted. You still need to be careful with alternator connections but there are good products (DC-DC chargers) to help with that.
I am in process of binning my 3 Victron 130A Gels in favor of 3x 280A Lithiums that are the same size. Expensive, but then little in sailing makes sense financially.
Hi Stuart,
Thanks for the kind words.
That kind of backup can be done with external BMS too. Anyway, I’m agnostic about internal or external, what maters is whether or not the BMS can communicate properly and the best communication is generally CANbus, which most internal BMS can’t do.
For example, as far as I can see, the Victron superpacks have no external communication capability, never mind CANbus.
And this is why that matters: https://www.morganscloud.com/2022/04/25/why-lithium-battery-load-dumps-matter/
I’m also not a fan of using DC/DC chargers between the alternator and house bank since it’s generally inefficient and expensive: https://www.morganscloud.com/2022/09/04/battery-bank-separation-and-cross-charging-best-practices/
Congratulations, J&P, on an incredibly thorough analysis. I may have to read it a few more times before I truly understand. What a treasure you two are to the cruising community.
Hi Doug,
Thanks very much for the kind words, much appreciated.
Hi,
I am on the low side of storage vs demand. I have two lead acid 130ah house batteries that power a fridge, nav array (when on), led lights and a autohelm.
I leave my inverter in which I will change now as I suspected it draws power.
The change over cost and hassle to lithium is not inconsiderable. I want to be able to cruise for weeks maybe months and not be concerned about if the battery has enough charge.
I have a wind gen that pumps out about 15amps, and a single solar panel that does about the same. My concern is the autohelm (octopus/raymarine) and fridge. I’m guessing I am a bit short. So I am thinking of just adding a third battery rather than going li which will give me the storage I need but also cost a bomb – north of $10,000… as opposed to maybe $600.
Thoughts?
Hi Gordon,
Yes, I’m pretty sure that’s too small a bank for your usage. (I have the same on the J/109 and it certainly would not be adequate for your goals.)
Anyway, the best way forward is to properly analyze your usage, not guess, as I would be doing to answer your question. To that end we have a fairly quick and easy way to do just that (three chapters) including a spreadsheet, that will take you less than an hour to read and complete: https://www.morganscloud.com/2019/01/09/cruising-boat-house-electrical-system-design-part-1-loads-and-conservation/
Once you have figured that, have a quick read through the rest of the online book to make sure you have a plan before starting any changes. We don’t want to do a ready, fire, aim, job on this because that can be frustrating and very expensive:
https://www.morganscloud.com/2019/01/09/cruising-boat-house-electrical-system-design-part-1-loads-and-conservation/
Hi Folks,
I thought put in a short note here regarding two things that have come up in the comments; fast recharging, and supporting critical loads.
On many of the system upgrades we do, the house bank (if 12V) is upgraded to 24V, or even 48V (actually 51V if Li). The reason for this is much faster alternator recharging.
The critical and/or general loads can remain 12V (or 24V), and run from a backup battery that is kept fully charged from the house bank, using a B2B charger (or sometimes we use MPPT solar controllers). The size of the backup battery is determined by the loads, and how long you want to run off it in the case of a main battery bank cutoff.
Smooth seas
Bruce
Hi Bruce,
Good point. We have two chapters on the voltage decision, but I forgot to add the faster alternator charging benefit. I will fix that, thanks: https://www.morganscloud.com/2020/12/10/should-your-boats-dc-electrical-system-be-12-or-24-volt-part-1/
This is my first comment here. So on the beginning I would like to say thank you John for that page with tons of interesting articles! English is not my native language so I’m sorry if sometimes I use wrong word.
I use to live aboard for 15 years sailing to remote places. For me LFP was a game changer. I changed from 800Ah (12V) AGM to 700Ah (12v) Winston cells with REC BMS. After two years of using it I can say that I’m lithium fun boy 😉
When I wake up and the batteries are around 50-70% I can boil water on my induction stove. Under 300amps of load the voltage is around 12.6V! Impossible performance with LA batteries. Even if I had a ridiculous 1500Ah. Even @50% SOC I can run my watermaker (160 amps) for more than one hour.
The system now is much more powerful weight 88kg (LA was 260) and taking 3 times less space.
Another benefit is the charging efficiency of LFP is close to 100%. For LA that is around 85%. So with LFP we need to return less energy with the same usage….and so on….Others mentioned other benefits like more efficient solar charging, long time with partial state of charge, faster charging, low voltage drop, flat voltage curve. Big advantage is also no need for equalization and building an electric system around LA weakness.
And what is the price?
Let’s compare Lifeline GPL-4DA AGM Sealed Battery 12V 210Ah with a couple of lithium options.
Let’s assume 40% standard DOD (depth of discharge) for AGM and 80% for LFP.
For example we need around 300Ah usable energy. So we need 4x210Ah=840Ah of AGM, or around 400Ah of LFP. For lifeline the cycle life is 1000, for Winston cells 5000 (manufacturer data), for the rest of LFP 3000.
We should not compare a number of cycles but number of usable Ah during battery life.
So for Lifeline it will be 840Ah x 40% x 1000 cycles = 336 000 Ah
For Winston DIY: 400Ah x 80% x 5000 cycles = 1 600 000 Ah
The price for Lifelite is 4×700$ = 2800$
For Winston is 1600$ – price from reputable Sky Power. To make the battery work you need BMS, contactors and other gadgets – so add 1000$ (REC MBS with 2 contactors). When you change batteries in the future BMS and contactors remains the same. But ok. 1600$+1000$ = 2600$
So what is the price for one usable Ah?
Lifeline – 2800$/336000Ah=0,0083$
Winston – 2600$/1600000Ah=0,0016$
That means that ONE usable Ah with Lifeline AGM is more than FIVE times more expensive than a DIY pack built from raw Winston cells. And Winston cells are one of the best on the market.
But ok. Not everyone is able to assemble and use DIY pack. So what about Victron?
The price for 2x Victron LFP Smart 200ah is 4000$. Plus 1000$ for BMS(one time In the lifetime) and we have 5000$
400Ah x 80% x 3000 cycles = 960 000 Ah
5000$/960 000 Ah = 0,0052$, 1,6 times less expensive than AGM
The route with Battleborn is 2,2 times less expensive. Ok. Drop-ins are not very good for yachts but for the same money and for redundancy you can have two Battleborn banks.
What about the state of art., and one of the most expensive LFP – Lithionics @ Ocean Planet Energy?
They don’t have 400Ah.
Price for 320Ah is 4600$+2200$(BMS) = 6800$
320Ah x 80% x 3000 = 768 000 Ah; 6800$/768 000 Ah = 0,0089$ for one Ah, 6% more than AGM
Price for 555Ah is 7200$ + 2200$(BMS) = 9400$
550Ah x 80% x 3000 = 1 332 000Ah; 9400$/1 332 000Ah = 0,0070$ – 16% cheaper than AGM!
If someone sees a mistake in my calculations, please correct me. Summary on the picture below.
LiFePO4 batteries are not only better but also cheaper (much cheaper with a DIY pack). I think that for people that live onboard, that is a complete game changer. I have never heard that someone installed LFP and went back to AGM. For me, there is no way back.
Let the (electric) force be with you
Michal
Hi Michael,
You make some good points, all of which I also talk about in my analysis of lead against lithium above and in other parts of the book.
As to pricing, I’m not going to get into a debate on that since I’m comfortable with my conclusions on the post above. The point being that pricing battery systems is a bit like statistics: the numbers can be moved around to support whatever each person has already decided is best and this is very easy to do when we get into cycle costs.
There is also the matter of making a lithium system truly reliable and seamanlike, which adds cost and complication: https://www.morganscloud.com/2022/07/03/building-a-seamanlike-lithium-battery-system/
And then there’s the issue of insurance, particularly for DIY systems.
Bottom line, these things are situation and usage dependant so if you have a good solution that’s working well for you, that’s great, but it does not make it right for everyone, or “best”, just best for you.
As to no one going back to lead, I agree. Why on earth would anyone do that after going through the complications and expense of installing lithium. But again, that does not make lithium right for everyone.
Hi Michal,
This is a general comment that has been on my mind for some time but your comment got me thinking about it. One thing that I wonder about in a lot of cost comparisons is how people count cycles. At one extreme, you have the liveaboard cruisers who are on their boat something like 300+ days a year. If they are sized so that they have to use a generator once a day and have no other significant charge sources, then they may get 300 cycles a year. But I think this is pretty rare, most of these people will have solar, wind or hydro and will only use the entire available SOC range relatively occasionally and most of the time will be cycling over a much more limited portion of the range. Even people who are planning to use a generator a lot likely are only getting something like the equivalent of 100-200 full cycles a year. With 5000 rated cycles, that would be 25-50 years for the heaviest users.
Going to the other end of the spectrum, there are plenty of people working full time using their boats for a 2 week cruise a year and then some daysailing. Many of these people seem to be also going lithium from what I see. These people might realistically have more like 10 cycles a year. Even if these people go for max sailing performance with minimal battery and charge twice daily with an engine, they are still in the range of 30 cycles a year which would be 167 years.
I think we need to include an age check in any cycle life claims. Batteries all degrade with time even with no cycling and the amount depends on the specific chemistry and the storage condition. Electrical requirements also change, in 20 years we may all be charging with a different source, using significantly more energy or running a different bus voltage or something else. This all also assumes you don’t have a fault or make a mistake that destroys your whole pack at some point. These days, electronics are generally quite good but still a failure of part of your BMS can make a pack useless for all but the very technically savvy. Finally, how many people actually keep a boat for multiple decades, I think the number is actually quite low. My guess is that very few people will make lead acids last more than 10 years and lithium more than 20 even in ideal conditions so a lot of people may not be cycle limited but age limited. For truly heavy users, cycles is probably a decent measure but even many full time liveaboards and certainly most seasonal cruisers may find that the math is driven differently.
Eric
Hi Eric,
What an interesting comment – I have been pondering the excellent reporting available in our MasterVolt BMS, by interrogating our bank of 3 x 180 A/hr LiFePO batteries, which were installed in February 2016.
For us, that economic decision was easy, our AGMs and old generator were end-of-life, and not replacing the generator paid for our new system, even without considering the maintenance and fuel savings we have since enjoyed.
Since then, the BMS tells me that we have only used ~330 cycles on our battery bank, and I was questioning this being so little after 7 years. We average something like 80 nights per year on board, plus one full-time six month cruise to the SW Pacific.
I was thinking at this rate of cycling, not only will I be dead before replacing the bank, but our kids might be too…!
From your comment, I think what we are experiencing is the benefit of our solar directly supplying the bulk of our load during the day. At night, our current draw reduces dramatically as we aren’t opening the fridge or freezer and the nav systems are off, unless we are on passage.
So the batteries are only experiencing the difference, plus our reduced winter season usage (but increased battery draw) when we have our bimini and flexible PV panels stowed away .
Thank you for demystifying this for me…!
Hi Rob,
That is a great data point. I wonder how your BMS calculates a cycle. With batteries that give a relatively constant amount of energy over their life regardless of DOD, it is pretty easy to divide the total energy used by the usable capacity to get something realistic.
Wouldn’t it be great if you never had to do anything with batteries again.
Eric
Hi Eric,
Sorry, can’t help there – I even had to Google what DOD stood for..! I just checked the manuals for the MV shunt and MasterView display, but no insight there.
As you say the BMS knows the capacity of the bank and our usage. Not sure if it is more sophisticated than that, in monitoring and adjusting the capacity in the calculations as the bank ages. To be fair, the conservative minimum rating of 2000 cycles quoted by MV probably allows for degradation of the battery over time, so it may well do.
Our cycle count usage data point, is flattened and flattered by around 50% on account of me interrogating the MV EasyView BMS monitoring system soon after we bought two MV batteries originally. I noticed our new batteries were 28 months old (elapsed time since first charge is recorded in typical thoroughness) and the dealer hadn’t told me they had been in MV stock for a while.
On questioning, we were sheepishly given a free third 180A battery, to act as redundancy for going offshore, which I had planned for space-wise in the electrical locker, but hadn’t ordered as we didn’t need the capacity. So now we can have two out of our three batteries in fault mode and automatically isolated by the BMS, and still have a perfectly useable house bank.
And our experience to date is the batteries have been very much set and forget (and monitor).
Like Michal I’m a fan, but I suspect for different reasons.
Hi Rob,
That’s an interesting number, and, like you I’m surprised how low it is. Another useful take away from your comment is the benefit of turning stuff off at night. I’m increasingly seeing cockpits lit by the glow of instrumentation all night and I think most people have not thought about what a huge consumption hit that is. Just leaving a NMEA 2000 network on for 24 hours could use 50 Ah at 12 volts. Add in a plotter, AIS and some other odds and ends and we can easy get to double that.
And the other take away is with that much solar and that few cycles, a lead acid bank would be fine too, and last for 20 years, although obviously much heavier and space intensive.
Great point John, we too are “seeing the glow!”
And it’s bad for their displays – Raymarine certainly advises in their operator manuals to turn off and cover up all screens from sunlight when not in use. Our Raymarine cockpit chart plotter mounted in the elements by the helm station is coming up 10 years, and still works and looks like new.
Never given this any thought before, but now you make me wonder if many boaties unused to navigating after dark without instruments, feel if they don’t have their plotter going, they are somehow lost?
I have even been told we are UNSAFE at night for not running our AIS, which is a fair point if we ever had to anchor in a fairway or shipping channel, but that’s certainly not by choice. Personally, I find it counter-productive for small craft to leave the AIS on when anchored – it just creates screen clutter and makes it hard to spot boats that are underway, as we approach an anchorage in the dark – we have a few that we know well and happy to enter.
It might be a helpful post John in your anchoring book, giving some guidance for people in how to create their own situational awareness at dusk, so they feel secure without a chart plotter and instrument bank telling them what they can see with their eyes (and ears) if they know how and have a little confidence to try it.
Perhaps some hints like which bearings will be of no use after dark (or even create confusion). And in remote anchorages on a back night, with no lights, how to pick unlit features ashore that you can find after dark with a powerful torch or searchlight, or will see against a clear skyline. And perhaps when to turn on the instruments and have them running..?
Personally, I enjoy the dusk ritual of getting my situational awareness, choosing my bearings, noting the magnetic compass heading, checking time of moonset/rise. I find it helpful to visualise what things will look like after dark when the wind shifts, or tide turns. And then what is the relative position of other boats around us, and how are they lit so I will be able to figure out if they are moving relative to us.
And I always pop up again before bed, when it’s fully dark, just to lock the situation in my head, if we ever have to get up in a hurry.
Writing this up in the log, then staying out in the cockpit as darkness falls, observing the fading skyline, seeing more lights appearing, listening to the Kawau (NZ shags) arguing over the best perches, these are some of the most magical moments on the water…!
Situational awareness is good but if you want to sleep at anchor, I would argue that an anchor alarm is pretty essential. We always turn on our anchor alarm which uses GPS units serviced by our NMEA 2000 network.
So, we may not have our chart plotter on but my navigation laptop is always on at night with an anchor alarm set. It has saved our bacon more than a few times & quite frankly, when the wind is howling at ‘oh-dark 40’ I want to quickly know how hard & what direction it is blowing and where we are. If we’ve dragged, I want to know without any doubt.
My NMEA 2000 network with an Actisensense Ethernet adapter, Airmar wind instrument, Vesper XB-8000, Furuno 330 GPS & Airmar heading sensor and a thermometer does not draw very much power at all (< 2A ) but provides excellent / invaluable situational awareness.
Around here we get to listen to the cormorants squabbling over their roosting trees. For that we use our old fashioned senses 😉
Hi all,
I am interested in Evans declaring an anchor alarm being essential for sound sleeping and what others do.
In many thousands of nights at anchor, I would guess, I have set an anchor alarm just in the past couple of years and then, just a few times when things were predicted to get boisterous and hard stuff was close-at-hand. I generally sleep very well, but also seem to awaken to an increase in wind or change in the noise and check things out. Situational awareness is from a telltale compass right over my head. If I am facing the same direction I was when I set the anchor, I figure I am good for a gale.I also have several (if possible) shore lights or the like to orient myself if I happen to go on deck.
I am of two minds about becoming better acquainted with anchor alarms. One, will it interfere with the sense I have that I will awaken if something untoward is occurring: too much reliance on the alarm? Or am I in for an uncomfortable surprise when I sleep through an event that the alarm might have warned me about?
I am not a Luddite, but I am wary of electronic stuff creeping insidiously into my life and tend to eschew the seduction of relying on electronics/tech etc. in all its seductive manifestations.
Random thoughts, Dick Stevenson, s/v Alchemy
Hi Dick,
The tell tale over the bunk is a great way to keep an eye on things for zero electrical use. I also commit the bearing to the anchorage entrance to memory before bed.
Hi John and all,
Yes, having a bearing to the anchorage entrance and orienting lights in memory good practice, but I would probably not choose to bail out of an anchorage at night in a fire drill of some sort with just a bearing.
For those who are as slow in new tech as I am: my chart plotter in the cockpit is great, but takes forever to get going which always concerned me if needed quickly. I am not generally an iPad user so it took awhile to realize that our iPad with its nav system is almost instantly on and with a quick fix.
It impresses me what a significant increase in awareness and confidence going from a few bearings in the dark to seeing the boat icon situated just where I thought in the anchorage. Another way of saying this is that, for me, night-time fire drills where the boat needs to be moved can be impressively disorienting: and instruments help.
My best, Dick Stevenson, s/v Alchemy
Hi Dick,
I would agree on the difficulties and dangers of leaving an anchorage at night and am pleased to say I have never had to do it. Still, I like to know which way out is.
I also agree that instruments can help with orientation and that a tablet is an interesting alternative.
That said, tablets have one huge drawback for me in this situation: the process of getting them going in nav mode will totally ruin our night vision.
Given that, what we did on the McCurdy and Rhodes was install a small plotter with integrated GPS antenna that we would leave on all night in night vision mode if it was blowing or the anchorage was at all sketchy. Very low power draw and ready to go at a moments notice. I’m just in the throws of installing the same (on deck) on the J/109, for a whole bunch of reasons, including this one.
Hi John,
I also have never had to bail on an anchorage, but knowing the way out has become something like carrying an umbrella: if I prepare to bail, I will not have to do so.
Yes, agreed about night vision. Our SOP for situations like this is for Ginger to be looking at the iPad while I am at the helm with what situational awareness I can have in the dark and Ginger calling out information from the iPad. This would take a few minutes until the cockpit chart plotter fired up and could be used in its night mode. Even then Ginger would be monitoring the instruments while I drive.
Yours like a good solution, especially for single-handers.
What small plotter is your choice?
My best, Dick
Hi Dick,
I have ended up with a B&G 7″ Zeus3 twice, for this function and others (not primary navigation, which they suck at) but that’s more about compatibility with what I already had aboard than any love of the brand. My usual recommendation for plotters (and radars) is AFF (anything from Furuno). That said, I have not looked at their plotters in detail for some time.
Hi John, Agree about Furuno. I will look. Thanks, Dick
Hi Evan,
I agree on the desirability of anchor alarms, but I have always set up my boats so I only need to leave one unit on to accomplish that. You could do the same with your Vesper XB 8000 by wiring an alarm to it and using the internal GPS antenna, or if that’s too obstructed add a vesper external GPS antenna which does not use NMEA 2000. This is the way we were set up on our old boat, and I have just finished doing the same on the J/109.
There are also other ways to get the same result.
There is no way I can see that leaving a laptop and the network on over 24 hours can use less than 100 Ah at 12 volts. That’s about half of what used to be our total at anchor usage for everything on the McCurdy and Rhodes. So still lots of of low hanging conservation fruit to harvest in your situation, I think.
All that said, I agree that if its really howling (F7 or above) I do tend to leave the wind instruments on so I can check direction with a quick glance—velocity I can estimate quite well from noise in the rigging.
Also, if you have been saved that many times by a drag alarm, it might be a good time to review your anchor gear. We have not dragged once set in over 20 years since we took a long hard look at our anchoring gear and practices: https://www.morganscloud.com/category/anchoring-mooring/online-book-anchoring/
It’s an Interesting suggestion to set things up to allow the the Vesper to run separately from the NMEA 2000 network. (I do have the external GPS unit for the Vesper & it is probably the most reliable GPS of the lot. ) I will look at a more power friendly setup using the Vesper.
As to the necessity or desirability of an anchor alarm? We dragged at least twice with a Rocna 25 kg (roll bar) anchor. One of those occasions was at 0200 after a wind & tide shift that had us coming within 20 feet of a rocky shoreline that would have destroyed the boat. I was very glad to the have set the anchor alarm.
We switched to a SPADE anchor & an all chain rode in 2016. We have never dragged since but I never want to assume that it couldn’t happen…. We are often anchored in lonely places up the BC coast where there are no other boats, no shore lights & unpredictable wind shifts. The anchor alarm is non-negotiable.
Hi Evan,
I agree on the anchor alarm. Even though we have not dragged in over 20 years I like the added security and it helps me sleep better too.
Sounds like you are pretty much all set on the Vesper since you are using the external antenna. So just add the external alarm buzzer and you are good to go, I guess one drawback is that Garmin are not supporting the App (see my tip on this) but I would guess it will still work fine for a couple of years to give you time to research another low current draw solution, see my comment to Dick (and Eric’s solution) for one alternative.
And good to hear you have solved the drag problem. Experiencing that drag modality of the Rocna is enough to make any person a lifelong advocate of drag alarms. Living with a CQR, as I did, will do that too!
Hi All,
I too can’t imagine having the electrical draw of all the electronics going all the time. Our NMEA 2000 network draws around 0.6A (12V) and the chartplotter draws a little under 2A so if we left it running all the time and didn’t have stuff like the VHF going, it would not quite double our electrical usage. We do sometimes run an anchor alarm and for this we keep a small standalone chartplotter at the nav station that draws 0.4A when the screen is relatively dim. This also doubles as our backup to our main unit so we have it wired to a waterproof plug with receptacle at the nav station and on deck and mounting points in both places too.
We have tried other methods that I didn’t like as much. We used to have a small black and white plotter above my head in the bunk but I found it too tempting to look and it couldn’t be seen from anywhere else so if the wind suddenly picked up and I decided to get up, I now was electronics blind for a little while getting something else running. I have also tried a smartphone which I didn’t particularly like and at least when I measured the one I had several years ago, the power draw was no less than the small chartplotter. I had not considered using the AIS unit so I will have to think about whether that makes sense in our case. One thing that I do think is important in many instances is not having to spend a bunch of time booting stuff up if you do have to get moving. Unfortunately, modern MFD’s boot a lot slower than ones from 10 years ago but I still find them much faster than computers although computers are a lot better than they used to be. In our case, we can see the plotter down below reasonably well from on deck so can use that while the on-deck one boots. At least the new radar doesn’t take 3 minutes, that used to feel like forever when the visibility went to nothing and there were likely to be other boats dragging.
Dick’s comment about when to use an anchor alarm is certainly an interesting one. The majority of the time we do not but most New England nights are pretty calm, if there is much wind or any other reason to worry like a bad bottom or reversing current, I set one. With any light at all, I can easily see our jib halyard and how it is deflected in the breeze from in the bunk and it is great at telling me our angle to the wind. Our boat sails at anchor a little so I expect to see some movement but if we were to ever be closer to beam on and staying there, we would know that there was an issue. If there is any actual change in anything, then I get up and check ranges, other boats, etc.
Eric
Hi Eric, You remind me: my “alarm” is my line to raise the inboard end of my pole which, at anchor, slaps when the wind gets much above 25kn or so. All efforts to quiet it have so far failed and I do not mind the wake up call. My best, Dick
Hi Eric,
The small stand alone plotter is our preferred solution too, and I totally agree on the dangers of being blinded by electronics, see my answer to Dick.
This is what we’ve found by “going big” with lead-acid batteries. We can stay at high states of charge because our usage patterns rarely dig down deeply before we are back to pumping in amps. “Cycles” is so ill-defined as to be meaningless: if you draw down by boiling water or vacuuming at noon when solar is peaking, is that a cycle? Or pretty much a wash? I draw more deeply on passage, but that is also when we tend to motorsail more in coastal mode, so the big radar and related nav devices don’t really hit the battery bank the way they would if we were just sailing at dark o’clock. It’s too ambiguous a measure.
Hi Michal, John, Eric and Rob,
Good points, and seen from different sides.
There’s no doubt that a good lithium bank treated right will live way longer than any lead acid bank, and that this will influence the lifetime cost a lot. At the same time, we must accept that a quality LiFoPo4/LFP bank on a boat will most likely not die because it has reached its maximum cycle number. Rather, it’s way more probable that it dies from:
1. Over charge or over discharge, resulting in sudden death. (Slow over charge is reportedly the most frequent reason for premature death of LFP.)
2. Age, accelerated by hot environment, constant high charge level and more.
Since lead acid banks are also often mistreated and die far earlier than they should, the difference in expected cycle numbers is probably still fairly realistic, albeit with lower numbers for both. It seems like a realistic guess could be that a good LFP bank lives about three times as many years of similar use as a good AGM bank. (Flooded lead acid banks live at least twice as long as AGM, tolerate far more abuse and are cheaper… Gel also live at least twice as long as AGM, and cost roughly the same, but are not tolerant to abuse.)
In the data sheet above we can notice that Winston has by far the highest number of lifetime Ah. 16 million, while Victron is at about 9 mill and Lithionics in between. This is especially interesting, as the three all use the same Winston cells. The numbers should have been the same. Reading the white papers from Winston will reveal that they tend to name the true achieved limits, while not necessarily emphasising the conditions they are using. Victron on the other hand, tend to report levels that are quite conservative, to avoid complaints. Still, they’re all relating to lab conditions, which are not the same as multi year boat use, especially in that aging doesn’t interfere and that the cycles are quite high draw and done in short order.
Comparing between traditional battery banks and lithium when applied on an existing boat will also give a pretty different cost calculation than mentioned, if the system is done right. Just exchanging the lead acid bank means that’s it. There are no system rebuild costs. Changing over to LFP will imply some significant costs in replacing much of the electric system. The battery bank itself may be far less than half the cost, if the system is done right. (By going drop-in, we can fool ourselves into believing we got it easy…)
As Eric mentions, from cycle life we can calculate perhaps 50 years of service life from our LFP bank. However, that’s not realistic, unless we look at LTO (lithium titanate) cells, which for several reasons is a poor choice. LFP cells can indeed live long, but probably not much more than 20 years of actual use, no matter how they are treated. They do age. “Dendrites” is a key problem. Since the tech hasn’t existed long enough yet, we don’t really know enough, but one bank belonging to Rod Collins of marinehowto.com has some actual numbers. That’s Winston cells and it’s been run extremely hard, for testing purposes. That’s his business. It’s capacity is still higher than its rated capacity and it’s about 14 years old now, past 3000 cycles if I remember correctly. It seems likely that 20 years will not be a problem, but it can also suddenly fail.
Either way, to benefit from the long life expectancy of LFP, we need to push the envelope some. A boat that is normally plugged in at night or runs the engine most days anyway, will probably not notice a benefit from getting LFP, unless the boat regularly has an extremely high power consumption. A boat that regularly has extended periods at anchor or under sail, mostly charging from solar, will certainly notice! We can all crave for the new cool stuff. In this case it’s the wrong choice for the majority of normal boaters. For the group on AAC, it’s perhaps a good choice.
Hi Stein,
I agree on lithium life being about three times lead-acid (in the article above) but that does assume, as you point out, that mistakes are not made with the lithium system.
My experience does not support that liquid filled last twice as long as AGM, although I think it is true that AGM are somewhat more susceptible to sulphating and so need to be managed a bit more carefully, a process that’s way easier now we have more efficient lower cost solar. Properly managed I don’t think there’s a lot of life difference between liquid filled and AGM.
Hi John,
I forgot to specify that I was thinking about liquid filled traction cells. They’re normally in 2 V single cells or semi traction in 6 V batteries. They are far more durable (hand heavier) than standard liquid filled batteries available in normal boat shops.
Hi Eric, Rob and Syein
I was also wondering how BMS counts cycles. I think that for my REC one cycle is when the sum of partial discharges reaches 100%. When I’m on a boat using battery heavy my average on BMS is 11-12 cycles during one month. I have a 700Ah battery bank and my average DOD when I wake up is in range 200-300Ah. Most of the days solars take care of loads and they charge the batteries. So three 30% partial cycles make one cycle for BMS.
12 cycles in one month are less than 150 cycles during one year. So even if that 5000 cycle life is too optimistic and my batteries will last only for 2000 cycles it would be 15 years of full time cruising!
So Stein is right. most probably they will be dead not because of the number of cycles but because of their age, or because I make something stupid 😉
For me switching from AGM was not very expensive. I had already Victron programable solar chargers and Balmar external regulator with temp sensor. I know that wakespeed is better but I didn’t wannt to spend more money and with balmar is still possible to tune all variables right. So except the cells 90% of the cost of switching was BMS, two conntactors and couple of meters of thick cables. The cost of the system can go crazy if you hire someone. Especially in US where labor is extremely expensive.
And of course, I agree that the benefits of lithium are for peole who spend more time off the grid than connected to shore power. More off grid, more benefits. For those who make 10 cycles a year, LFP is waste of time and money.
As I did not see the keyword I was searching for, I will give another viewpoint. 1) I think lithium is wonderful, particularly for lighter cruisers. 2) We are sticking with quality lead-acid, because our boat is steel and we’ve built our battery compartment pretty much directly above the keel tanks and directly below the mainsail’s center of effort.
That’s right, it’s about 330 kilos of “internal ballast”.
This has made our boat actually stiffer in a blow. The six L-16s we’ve had for the last seven years have been babied, rarely if ever below 75% SoC, and watered and equalized on a schedule. The addition this winter of a new wind generator charging source on top of the four solar panels should not charge the range at which the house bank stays charged via the Victron setup, the Outback MPPT and the simple alternator, which is easier to embiggen elsewhere (and to add that slick Wakespeed regulator!) if that becomes necessary or preferable in some foreign harbour.
If I had a light performance cruiser, I would absolutely go lithium, and top-end, too. But in contemplating a circ, getting lithium shipped to exotic repair locales is still problematic, as far as I know, in ways that lead-acid batteries are not (save for the weight of the freight). I would also have a “wall” of lithium for an off-grid house, or, if they exist in five years, some of the next wave of battery chemistries.
I am only switching up our existing house bank because the batteries are long in the tooth, not because they are showing any signs of failing.
So we are in the odd position of liking a big tray of lead under the saloon stairs. If we didn’t have the boat we do, I would hold quite different opinions and am ultimately agnostic on the topic.
I have not read all the comments so this may have been covered but I believe you are dead wrong with your whole hog lithium advice. The hybrid approach is the only practical answer to lithium. You can make the lead acid bank small but you need it for many reasons. You still get the benefit of Lithium and the cost and complexity is well worth it. Boats going all lithium are struggling. Your opinions and advice are usually more thoughtful. This seems more like bias. Best to speak with some people who know about such matters before making bold and incorrect assertions.
Hi Robert,
I’m happy for you, or anyone else, to disagree with me, but watch your tone. There is no reason to couch things in that way, just because you disagree with me: please read our comment guides lines: https://www.morganscloud.com/2013/11/10/aac-comment-guide-lines/
I will delete any further comments couched that way.
That said, if you would like to explain your position clearly and without aggression, I’m happy to listen and discuss it.
Also, to be clear, I don’t recommend going all lithium, so you and I may be closer than you think, but we will never know if we start off on the wrong foot: https://www.morganscloud.com/2022/07/03/building-a-seamanlike-lithium-battery-system/
I recently designed and installed a LifePO4 system in my boat. Absolutely more expensive because of the added equipment necessary for a reliable system but, at least in my case, the economics were better than you have presented here if you consider the longevity and assume you are keeping the boat for at least the life of good lead acid batteries, properly treated. First, the lithium batteries I installed were not appreciably more expensive than the really good AGMs I had. In fact, the prices were nearly equal (about $600 for each of three Kilovault HLX+ 100ah batteries to replace the Odyssey Grp 31 AGMs, one of which I repurposed as my new start battery). And the Kilovaults are UL1973 approved unlike many other top brands (we can argue over the merits of different ULs but Calder says 1973 is what you want). Since I already had “smart” charging equipment in the AGM system, my adds were a DC-DC charger, a T-Class fuse block, separate pos/neg terminal blocks, and larger 2/0 cable. I also threw in a battery isolation switch. There are some hassles to the system, like the need to remove the lithium batteries for storage because of the cold winter temps. I got a fuzzy answer from Kilovault but it seems the best course of action is to remove them in the winter and place in storage mode. I’ll place an old AGM back in the system for lights and bilge pump when I’m aboard on the hard. So, whether I keep this boat for the long haul or replace before the economics of the switch evens out, my view is that I tackled a tough technical problem and learned a lot in the process. This will make the decision and the process of going lithium on my next boat far easier.
Hi Jesse,
Glad to hear the change has worked out well for you.
That said, my pricing assumes a full on offshore system including serial lead acid backup and batteries with a CANbus capable BMS that can directly control the alternator controller and all other charging sources, not “drop ins” so we are comparing apples and oranges here. More here:
https://www.morganscloud.com/2022/04/25/why-lithium-battery-load-dumps-matter/
https://www.morganscloud.com/2022/07/03/building-a-seamanlike-lithium-battery-system/
John, how would you define the difference between a lead-lithium hybrid system (which you say to avoid) and a lithium system with a lead-acid backup for critical systems (which you describe as seamanlike)? I’ve read your article here https://www.morganscloud.com/2022/07/03/building-a-seamanlike-lithium-battery-system/ but I’m still not 100% sure I understand. Is it just the way the system is designed ie in series not parallel? Or is there something else I’m missing?
Hi Jim,
Yes, you have the key point, series, not parallel. In the back-up system I recommend there is no connection between the lead-acid and the lithium, other than the DC/DC charger, and those are pretty much guaranteed to fail to open circuit. The bottom line is that connecting lead-acid and lithium together in any way that’s not totally isolated by a device that will fail to open, is bad practice and potentialy dangerous.
It’s also bad for the batteries since lead and lithium have substantially different charging profiles.
We will get more into this as we go.
Hi John,
First comment for me – thank you for the great resource for this novice sailor in Australia.
In my search for a suitable battery for my 22ft NZ designed trailer sailor (where lithium is very attractive due to weight) I came across the recently released Trojan AES AGM line of batteries. (Not available in Aust. yet)
Boasts a pretty amazing 1200 cycles to 100% DoD in a BCI-06? test
See website link:
Trojan Battery | Trojan AES AGM Batteries
Love to hear your take on these and what the industry experts are saying about them – I can’t find too much out there.
Mentions use of proprietary carbon additive and other technology.
Best regards,
Brett
Hi Brett,
I knew Trojan were working on carbon foam tech but had lost track of what they were doing, so thanks for the link. A very exciting alternative to the complications of lithium. I’m also guessing that their claims are probably accurate since Firefly already proved out this technology before having manufacturing QC problems that made them a poor option.
One thing to keep in mind: you will probably not be able to actually use 100% of the battery capacity because at around 30% charge (guess) the voltage will drop off to the point that some pieces of gear like autopilots and inverters will start shutting down. That said, that will probably not be a big issue on your boat?
Thanks John,
You are right, we have simple needs for bay cruising and the only thing to actively manage is a small efficient fridge which is easy to do. (we’ve been campers all our lives – just moving to a boat now). We certainly wouldn’t run it right down but even 70% DoD gives you lithium like storage and only a 2x weight penalty 16kg vs 31kg (100Ah nominal). I would happily take the 15kg weight penalty for all the other benefits of AGM.
I am going to wait for the Trojan AES AGM to become available in Aust. Lifeline are ridiculously priced here ($920 vs $400 Victron AGM/Gel for 100ah). Hopefully Trojan are more competitive with Victron.
Cheers, Brett.