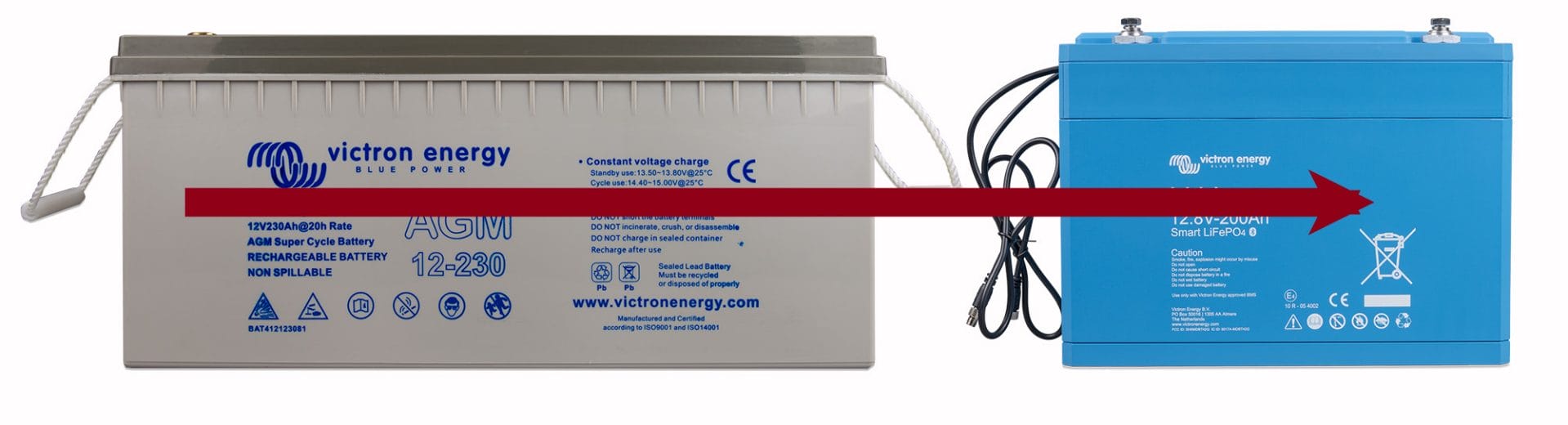
Many cruisers have already made the jump to lithium batteries, some with good results and some not, and I have already written about how to make that decision in a rational way while filtering out the screaming from the fanboys on one side and the naysayers on the other, so we don’t need to go there again.
And we also have a complete lithium buyers guide starting here.
But what if we have made the decision to stick with lead acid while we wait for lithium to get more reliable, easier to install and maintain, and less expensive? Pretty much always happens with comparatively new technology.
This is particularly worth thinking about since, although I’m neither a lithium fanboy nor a hater—I have come within a whisker of selecting lithium twice—there is little question in my mind that lithium will indeed become a no-brainer for most cruisers some time in the next five to ten years.
That is, if some other technology does not come along that renders lead and lithium obsolete, always a possibility, but my guess would be not a high probability one, at least not in that time frame.
So that begs the question: Can we future proof our boat electrical system for lithium?
That’s a hard no:
I have spent much of my life in high technology, and while salespeople love to babble on about how future proof their product is, that’s pretty much always rubbish.
Predicting the future direction of technology at the level of detail required to truly future proof anything is near-impossible, so best not to waste time worrying about it¹.
That said, if we are contemplating improvement to, or replacement of, a component in our lead-acid system anyway, it is worth thinking about how to do that in a way that has a probability of being lithium friendly.
Here are some ways to do just that:
¹Eric Klem started an excellent thread on just this in the comments to an earlier article.
Hi John,
In 2016, we had recently converted to a MasterVolt LiFePo4 bank, creating a new dry and cool electrical locker in a large void space under a quarter berth, removing two big and old AGMs from in front of our engine and two more from a lazarette – not the places for mounting Lithium batteries. We also replaced much of the wiring and switching.
Then I read one of your first articles on the comparison between lithium and other battery technologies. You made the excellent point that cruising off grid, one important benefit of lead acid if faced with total battery/system failure, is the ability to go ashore almost anywhere populated on the globe and buy a couple of replacement truck batteries. Not possible with lithium.
Since we cruise to the Pacific Islands and would need to await our return to NZ to fix any lithium system failure, this made me think how to replicate your lead acid redundancy. So we ran new cables back from the main buses into the engine space, isolated with electrical tape and then heat shrink. We left the tie-down mounts in place in front of the engine, the space empty, with spare truck style tie-down straps ready.
To convert back to lead acid, all we have to do is isolate our three lithium batteries using their manual isolators, and cable up the two new truck batteries. The simple original BEP battery monitor which currently monitors just our lead acid start battery, will also show the new house battery state without change.
So perhaps consider a P9 – when renewing your electrical setup, plan for the far more demanding environmental needs of lithium batteries, not lead acid.
And P10 – plan for redundancy, to revert back to lead acid if you ever need to.
Sometimes the simplest, most obvious solutions are the most ingenious!
Hi Rob,
That’s a good point, but given that we probably won’t know the sizing of the lithium batteries we will eventually buy it’s a bit problematic to know where to put them. I guess, if we were building new boxes for lead acid it might make sense to think about lithium, but here again it’s going depend on whether we eventually decide to physically downsize the lithium bank or stay the same size and get more capacity, or something in-between. And then there’s the variable of possible increased energy density or changed environmental requirements of future lithium batteries.
I also would not worry about the redundancy thing now, because I think there will be even more unknowables around that going forward. For example, my guess is that within 5 to 10 years we will see reliable enough lithium systems, with built in redundancy, to render lead acid backup obsolete, except maybe the system we advocate for here, and maybe not even that: https://www.morganscloud.com/2022/07/03/building-a-seamanlike-lithium-battery-system/
All that said, the changes you made to battery placement on your boat make a lot of sense, regardless of chemistry, and are clearly big improvements, so that’s the guide line I would take from your experience and choices.
Hi Rob,
FYI, I installed my own Lithium battery right where the old one was, which is in the engine room. I’ve been monitoring the temperature while motoring as obviously I was worried about over-heating, but the highest I’ve seen is 38°C after ~24 hours of continuous motoring (my max range anyway). From what I’ve seen, electric cars routinely heat their battery packs to ~40°C to improve performance (especially when charging), so I think this is not an issue at all.
In fact, looking at the datasheets, my old AGM didn’t give ranges but the “capacity-temperature” chart topped at 40°C, while the specs for my new Lithium say the charging can go up to 55°C and discharging to 60°C.
So yeah, I think lithiums don’t have especially onerous environmental requirements, except cold-weather charging. And even then, if it’s so cold you can’t charge, you’re probably stuck in ice.
Hi Emile,
Interesting observations, thank you. The highest temperature we have observed on our batteries is 30 degrees in Fiji (also sea water temperature). Our marine electrician had us place a large vent in the forward (cabin) end of the locker to provide some air flow, and we left provision to put in a couple of computer style ducted fans if needed – but haven’t so far. He also recommended charging below 35 degrees Celsius which could equate to an internal battery temperature of 70 C. At 40 C under hard-charging you could be close to 80 C internal battery temperature, and getting close to your battery limitations?
The bigger environmental concern for me is maintaining low humidity and minimising the salt / oil vapour in the air, something that would be difficult to achieve in the engine bay, especially when you have a water leaks that are not uncommon events, like a recent SW leak we had that we eventually traced to the rear seal on our raw water pump. Or as happened recently, the cylinder head pressure relief valve blocked and we had oil spurting from the dipstick around the engine bay.
Our batteries have both an internal and external BMS with integrated electronics and ethernet style connections for communications. In the locker, we also have the battery isolators, and 2x controllers for solar panels, alternator, shore power unit and the inverter. We treat this space more like a computer server room than a battery locker, and the batteries more like microcomputers with over specified battery backup capacity!
I have two DampRid containers in the space, which I monitor and replace about once a quarter. So it is dry in this locker with no sign of corrosion anywhere after seven years.
A last consideration is we have been able to mount the batteries and electronics above the cabin floor level, just under bunk height. In a flooding event, we buy some vital time with electrical power. In our engine bay, the old AGM batteries needed to be low down at sump level, to enable engine access to things like our SW pump.
Hi Rob,
Good point about the effect of hard charging on temperature.
You also make a good point about the engine compartment generally not being electrical equipment friendly.
One thing I’m confused about, you say that your batteries have both internal and external BMS, but I can’t see how that could work. Are you sure that it’s not an external BMS that talks to some cell monitoring circuitry within the the battery. That’s the way Victron works it, and I think that’s more likely what’s happening on your system too, but I could be missing something?
Could you link me to the spec on the batteries and BMS you are using so I can understand this better.
Anyway, I think your comment illustrates a benefit for lithium that I had not thought of before: the much smaller size and weight of lithium for a given capacity will often allow the bank to be moved to a much better place than the lead-acid batteries were originally installed in by the boat builder.
Could you email me a pic of your battery space, please? I would like to use it to make this point in a tip, or maybe even article.
Hi John,
My understanding is each MasterVolt battery (we have three) has an integrated BMS function that communicates over the MasterBus to the Masterview management and monitoring system. If the batteries lose their connectivity, they can still operate electrically, AND isolate themselves independently in a fault scenario by triggering their individual safety relay. Sorry, I don’t have a more detailed understanding to share. Spec here for the current product (ours is slightly earlier version):
https://www.mastervolt.com/products/li-ion/mli-ultra-12-2750/
Will email photo separately.
A last thought is that Maritime NZ (and Australian counterpart) are currently revising the electrical standards for vessels under 12m and over 12m in length, which will include changes to physical housing with special requirements for lithium batteries. I very much doubt that our engine bay environment would meet this new standard, without major modification, and so become non-compliant for insurance purposes. I was alerted to this by the marine electricians who installed our MV LiFePo4 system. Replacing our engine start battery recently in the engine bay with a high capacity AGM, it was installed in a new acid proof box with integral cover, to meet this new incoming standard.
Hi Rob,
Thanks for the fill on that.
I took a look and the only BMS is in the battery, and as far as I can see there is no external BMS, as such, but rather a master control and monitoring system.
Looks to me like a good way to do things by giving each battery some independence from the other batteries but still have full communications with charging sources.
Bottom, line, the point that gets missed so often is that it’s not important whether the BMS is internal or external, what matters is that it can communicate with charging sources and there is good external monitoring as well as BMS redundancy. For example some vendors can support two or more external BMSs and achieve the same functionality and redundancy that way.
Thanks John,
I tend to think of the system as a distributed management system. I can monitor the batteries using the Masterview display, and by connecting a PC to the management bus with the MV app, change the set-up parameters, bring the batteries back on line if they have shut down and more.
If I connect a PC to the internet using mobile data (or say StarLink), our MV dealer or MV themselves can access the system and diagnose issues with any MV device connected to the MasterBus, especially the lithium batteries.
Hi Emile,
Can you get away with batteries in the engine space? I think yes, and clearly you have done your home work on this, so that’s good.
That said, I for one would not be comfortable with a lithium bank subjected to temperatures that high. Particularly since when the engine is running they will also be being charged by the largest source on most boats. Point being that you may be getting away with this because you are charging them at very low current through a DC/DC charger but anyone taking advantage of a large alternator connected directly to the house bank could have a different result as the batteries heat from charging.
Bottom line, I don’t feel that batteries of any chemistry in the engine space are best practice, and I think that’s even more true for lithium.
See Rob’s comment for the way a professional installer insisted on moving his batteries out of the engine space.
Of all the articles on this topic, this one is the most pragmatic and widely applicable of the lot. I have found myself in several conversations with sailors a lot more competent than myself, but struggling a little with the complexities of this topic.
Most real world boats were built for 12v lead acid based systems, yet the hugely improved performance of lithium is undeniable. Given increasing expectations it is inevitable the upgrade/conversion question will arise. The gold plated approach which is to rip and fully replace with a new (and logically a shift to 24v system voltage) is not an accessible option for most – instead most will be served best by an incremental approach as you outline above.
Correct cable sizing and fusing is rightly the first priority. Far too many existing marine installs have been unsafely modified and extended over time that the forgiving nature of lead acid allows you to get away with. The same wiring with lithium becomes a death trap.
Fast acting Class-T fusing will feel like an overkill for many – but frankly the cost of these items is a fraction of your annual insurance bill. Most people have no idea of what happens when 20kA or more of fault current blasts through a wiring system, the physical violence is shocking. Search for “arc flash fault” videos for some diverting action.
This article is a very useful summation of a lot of other prior material published here, and I will be pointing others to it.
Hi Philip,
Thanks for the kind words, and some very good point too, particularly the importance of Class-T fuses and how dramatic a fuse failure could be.
Class T are 20 000 A. MRBF are 10 000 A. Given the ABYC 7 inch rule, MRBF fuse should be on every positive pole of a Lithium battery. Since there exist MRBF terminal connector its feasible.
http://assets.bluesea.com/files/resources/reference/Quick_Guide_to_Blue_Sea_Systems_Fuses_and_Fuse_Holders.pdf
It is not in all installation that Class T fuse can be the primary fuse for each lithium battery.
Once the battery cable has been protected with the MRBF, Class T fuses can be installed on the parallel link (after the battery have been combined ) downstream. Then you are ABYC compliant.
Yes I understand the point you are making – mounting a Class T fuse within 7 inches of at least one terminal is not always easy to physically achieve. Which begs the question of why 7 inches? If anyone knows for certain I would be interested to know.
I am guessing that this length is short enough to be unlikely to physically reach across the terminals of a typical lead acid battery. If this is the rationale then yes it makes sense to place a MRBF fuse on both the positive and negative poles. Especially as lithium batteries may well have different dimensions and the 7 inch rule might not work so well. But the problem with these relatively slow blowing fuses is they do allow for a lot of energy to pass through under a fault condition and this is what causes the damage.
Therefore you say – it then makes good sense to then place a single fast acting Class T fuse in the positive line – at the point where all the sources and sinks are combined. On my benchtop have sent a 400A Class T fuse to that big fuse-box in the sky and it was remarkable how little fuss was involved. A short crack sound and then nothing, no smoke no damage anywhere – and this was with at least 25kA of fault current available at 24v from a LTO bank with an internal resistance of under 1 milliohm!
I quite like your suggestion and I may well adopt it – it achieves the best of both worlds; useful protection of the high ampacity battery compartment cables, and high speed discrimination, low energy fault clearance to protect the far more vulnerable wiring and equipment throughout the vessel.
I would be curious to know if anyone can spot an issue with this.
Hi Philip,
Good point on the quick blow speed on a T fuse, another benefit.
Given that, and after some thought, I’m still liking a T fuse on each battery positive.
I know this can be a PITA but on the other hand we are, as you pointed out earlier, dealing with crazy amounts of current.
To be clear – are we talking about a T fuse per *BATTERY* positive or per cell positive that goes to make up that battery?
I think fusing the positive of each cell is the most secure way forward, followed by a class T at the main *BATTERY* positive.
With Lithium a cell can have an internal short and cause havoc. So how do we effectively address those concerns?
Hi Mark,
Yes, T-Fuse for each battery.
The safety of cells within a lithium battery is managed by the BMS. This is one of the many reasons I don’t recommend building our own batteries from individual cells.
Rather I think it’s better to buy from an established vendor like Victron who will have thought about all this and designed the battery itself in concert with the BMS to be as safe as they can since they don’t want to get taken to court and/or have their reputation ruined.
For example, Victron have added circuitry in their batteries that works with the an external BMS to increase safety: https://www.victronenergy.com/upload/documents/Datasheet-12,8-&-25,6-Volt-lithium-iron-phosphate-batteries-Smart-EN.pdf
Also a battery from the likes of Victron will have full and compliant containment, which would be difficult to do DIY, and even if we could, how would we prove our home brewed containment was compliant?
And even if we are smart enough to build a battery from individual cells that’s as safe as those from Victron, so doing is unlikely to make our insurance company happy, particularly if there is a fire.
All that said, when cells, (or batteries) are in series, as they are within a battery, the results of a short in a single cell, are a lot less of a problem than they are when batteries are in parallel. A read of our ohms law chapter and the next explains why: https://www.morganscloud.com/2016/05/24/one-simple-law-that-makes-electrical-systems-easy-to-understand/
Hi Andre,
Whether or not MRBF will be compliant and safe depends on the max short circuit current that the battery can produce. The problem with that is that battery manufactures are coy about that, so for big batteries I still think that Class-T is correct.
To support that I checked and a lifeline GPL-L18 (the ones I installed on our M&R 56) can produce short circuit amps of 9430 with a possible variance of 35% so possibly well above the capabilities of a MRBF fuse, and that’s lead acid.
So given that lithium batteries have much lower internal resistance than lead acid, I suspect there are many single lithium batteries out there than can produce more than a MRBF can handle, and therefore I would stick with the class T recommendation, unless we can actually verify with the manufacturer that the battery is not capable of producing more than 10,000 amps.
And that may be difficult. For example, I was not able to find that information for Victron lithium batteries.
So given that getting this wrong is a potential boat burner, I would stick with class T, inconvenient though that is.
why is this if it blows at 10,00? Because it doesn’t blow fast enough?
Hi Roger,
As I say in the article above, the great danger with a fuse that has a lower Ampere Interrupt Capacity (AIC) than the current the connected battery can supply is that instead of failing to open circuit when it’s rating is exceeded, in fails to closed circuit (welds together). In this case everything attached to the battery can go white hot and the battery itself may burst into flame or explode. This is a boat-losing modality none of us want to risk. Also, if it turns out that the AIC was lower than it should have been on the fuse, it’s likely the insurance company will deny the claim.
This is why I recommend Class-T for all but the smallest lead acid systems, and all lithium. The added advantage of Class-T, is, as you say, they blow more quickly, so damage to other gear, and the battery, is reduced in the event of a short somewhere in the system.
This debate reminds me that I need to write a chapter on AIC and why it matters so much.
thanks, good to know, yes an article would be helpful for us electrically illiterate
Hello John,
A very good resumé. I also love the comments so far. With my experience of designing and installing energy systems on boats i could suggest:
A) Identify everything that can put a charge, solar, alternator, fuel cell, windvane, water turbine and for each of these check if the charging profile is adaptable to Lithium. Most windvane are not programmable… Many charging source not coordinated can work against each other. Clean that up while you are on Lead Acid. With Lithium it is of prime importance that you don’t create a high voltage event because a charging source went south.
B) Choose your manufacturer against the philosophy they have toward the BMS. For example Victron has a BMS with a dedicated alternator port, so that old non programmable alternator can still be used safely and contribute somewhat to the charging process – although not completely efficient.
C) In the same vein as B, insure that all compatible charge controllers have access to the voltage of the target battery correctly. It means sometime to rewire the alternator so that the S (sense terminal) is not on the starting battery.
D) Invest in solar because with Lithium its worth it. Previously with lead acid you had to charge the battery early and we all know the sun shine more at noon. Now with Lithium you are not bound to the charge/discharge that occurs when a cloud obscure the sun.
E) Install measuring shunt as several key places so that you can check where is the current going, and from where is it coming. Very important unless you are an octopus with multiples Fluke clamp on amperemeters.
F) Separate your current house banks in pair A and B that can be isolated from one another. Very useful later.
G) If you have bought a boat recently or are not so sure about the electrical system, have someone knowledgeable come aboard and inspect it, recommend conformity upgrade and draw you a high level view of your system. And why not a transition plan toward lithium in several stages if required. Worst come to worst, it could be valuable to say to a insurance underwriter in the context of a claim, that you have not improvised becoming an industry professional.
And my last comment is about the complex battery monitoring and control systems. You are totally right that the attention should not be given to that. The focus has you layed it and also from the comment of others is on safety and preparation. On all my customer installations I suggest a Cerbo and a VRM account so that I can remote monitor the customer installation and set my own set of alarms rules. The cost is less than 3 % of the total energy upgrade cost. for the people i have worked with, its invaluable visual tool in their understanding of their new system (especially the woman aboard who prefer a visual graphical interface than a bunch of numbers on dials)
My humble 2 cents
Hi Andrea,
Lots of good points, but it seems to me your list is more for someone who is in the process of converting to lithium, or will do so in the very near future, say less than a year, rather than someone who might convert in say five years, when much may have changed, which was my target for the article above.
Hi John,
I recently switched to Lithium, but I wouldn’t consider my installation “finished” by any means. I wasn’t really planning on switching as I was in the middle of cruising towards the Bahamas, but I had to face the fact that my AGM house battery was shot so I looked for a replacement.
As soon as I started shopping for batteries, one thing became apparent: Lithium batteries are now only ~50% more expensive than AGMs now. So I made the switch; only for the house battery now. The charging sources I had that could be switched to lithium were connected to the lithium battery (only solar for now). The rest was connected to the start battery, and I added a DC-DC from the start battery to the house battery.
The plan is to evolve that installation and move the alternator to the lithium battery (I have a Balmar regulator) as soon as I can get one of these Sterling protection devices.
Anyway my point is this: while my lithium setup isn’t ideal, it’s still delivered lithium’s main benefit in my view, which is that it’ll happily take partial charges all the time. I no longer have to worry about my battery except looking at the percent-value on my BMV. High charging current is another benefit that I’m yet to take advantage of, but it wasn’t that important to me.
Hi Emile,
I think that kind of phased approach, while not ideal, is probably OK when coastal cruising, as I think you are, but I would strongly caution those who are heading offshore against any lithium battery installation that is not fully finished and seamanlike: https://www.morganscloud.com/2022/07/03/building-a-seamanlike-lithium-battery-system/
I would also not totally rely on a sterling alternator surge protector, particularly since there are many other far more serious potential problems from a load dump than blown diodes on an alternator: https://www.morganscloud.com/2022/04/25/why-lithium-battery-load-dumps-matter/ It’s also not clear that these surge protectors from Sterling or Balmar will withstand multiple load dumps (source: phone chat with Rod Collins).
Also, my analysis done only a couple of months ago showed that when we compare like for like and take into account the costs of a fully functional and load dump safe lithium system is about four times more expensive than lead-acid on a capital basis and twice on a per cycle basis:https://www.morganscloud.com/2023/01/10/a-simple-way-to-decide-between-lithium-or-lead-batteries-for-a-cruising-boat/
Of course that’s dependent on a lot of factors and how we calculate, but I think it’s still a good rule of thumb.
Sorry, I know the above sounds argumentative, but I think it’s important that others are aware of all the issues before taking the step of going to lithium.
Hi John,
Probably no surprise but I think your suggestions are very reasonable. This is a case of where there are a few basic things you can do from a best practices standpoint but trying to buy the exact right box that does everything is a fools errand until you put the entire system together which is the time to do it.
And to your comment above, I think an article on AIC would be great, it is definitely an important topic that seems to get very little thought. With the size of some of the battery banks these days, I think a lot of people are not protected in the way that they think as even a class T can’t handle the potential current from that big of a bank and the batteries need to be separated with multiple fuses instead of all in parallel with a single fuse.
Eric
Hi John and all,
I looked but may have missed a comment on this: would lithium batteries on a boat need to have inside warm storage in northern below freezing locations. Would they survive just sitting for 4-6 months of below freezing temps when charging is not possible or would they need to be removed from the boat and brought inside?
Thanks, Dick Stevenson, s/v Alchemy
Hi Dick,
That’s a big subject. I have some ideas and have thought about an article.
But the short answer is as long as they are not used at low temperatures most brands will be OK. Probably the safest thing to do is disconnect them. Also check the manufacture max cold while in storage spec.
I recommend reading the 4 articles on lithium batteries on this website:
https://nordkyndesign.com/electrical-design-for-a-marine-lithium-battery-bank/
Hi Olivier,
I agree, a very good resource. I’m in agreement with pretty much everything there and particularly like his explanation of the importance of using current accepted by the cells (amps) as a charge cut off parameter, not just voltage. He also has a very good explanation of why there must always be a battery in the system when change sources are active.
That said, I think his articles are, as he says himself, a bit difficult to understand without formal electrical training so my hope is that the buyers guide I have embarked on will bridge a bit of that gap.
Hello John, I’m a novice (to the group and Lithium knowledge level) . I have a question regarding Point #2 – separate load and charge busbars. Can you elaborate on how having separate charge and load busbars benefits a Lithium system. In the chapter on BMS, you speak of multiple relays to shut down individual charging DEVICES but I’m unsure how having these separate busbars makes a difference.
Hi Craig,
Here you go, all is explained: https://www.morganscloud.com/2024/01/29/lithium-batteries-buyers-guide-part-1-bms-requirements/
The point being that if the shut down of charging sources does not work for some reason a BMS with one bus has no choice but to cut off everything including loads, so lights out. A BMS with two busses can just cut off the charge bus, way less of a problem than a full blackout.
A neophyte question: how to determine what amp fuse should be used with the T type fuse on each of the 100ah lithiums I’m installing. Wire size is 12mm or 0000 gauge between terminals that are a few feet from each other. The ampacity of 0000 is approx 300 amps, so a 250 amp fuse?
Also, I’m trying to visualize the installation to keep within 7″. I’ll look for some pics but interested in input
Okay, I see that BlueSea makes a Class T fuse that will literally fit on the battery terminal up to 300ah.
Hi Tom,
That’s not a class T fuse and those fuses that fit on the battery terminal should not be used for lithium: https://www.morganscloud.com/2024/03/21/lithium-battery-buyers-guide-part-4-fusing/
I’d edit my comments or delete but not seeing a way to do that. So apologies for all the posts. It looks like 300 slow blow amp fuse would be the way to go to avoid nuisance trips. And I guess make sure to have spare big fuses!? This page helped answer some of my questions on sizing, rush current, etc. https://marinehowto.com/battery-banks-over-current-protection/
Looks like you can only edit your own comment momentarily. I did find this excellent article that answers most of my questions, but I’d like to confirm the guidance for the fuse rating to use after selecting the Class T fuse type. So, for my 300ah lithium house bank, with 0000 gauge wire, 11.6mm, I think I’m hearing use a 250 amp fuse, not a 300 amp fuse. And I’m hearing I likely won’t have a nuisance trip if I have to use the house bank in a pinch to start my Yanmar 3GM 27 HP or my relatively small Lewmar windlass on my 6.5 ton 35′ boat. I think I’m also hearing don’t use a Class T terminal mount. And TIA!: https://www.morganscloud.com/2024/03/21/lithium-battery-buyers-guide-part-4-fusing/#:~:text=Choose%20a%20fuse%20rating%20that's,fuses%20from%20a%20reputable%20vendor.
Hi Tom,
More on engine battery fusing here: https://www.morganscloud.com/2022/03/19/8-checks-to-stop-our-dc-electrical-system-from-burning-our-boat/
That chapter included a link to a fuse size calculator app.
Hi Tom,
This is a complex subject, so I suggest that before doing anything on you own boat, you at least scan through this entire Online Book, which contains the answers to all your questions so far, and probably most of your future ones: https://www.morganscloud.com/category/electrical/online-book-electrical-systems/
Also, don’t forget the search function on the menu at the top of the screen.
Hi Tom,
Yes, for security reasons you an only edit or delete a comment for 15 minutes after posting it.
Hi Tom,
More on lithium battery fusing here: https://www.morganscloud.com/2024/03/21/lithium-battery-buyers-guide-part-4-fusing/