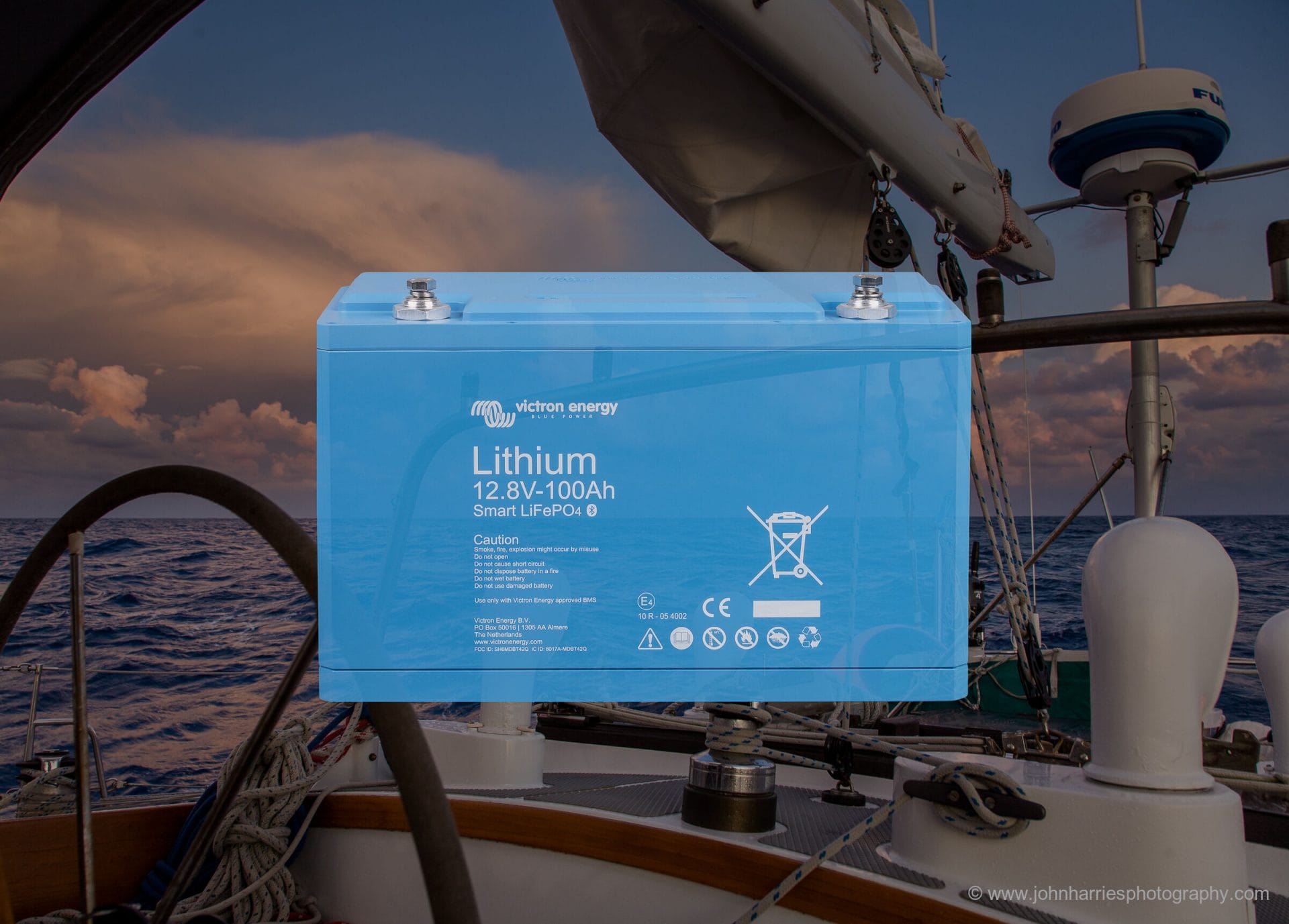
The electrical system on an offshore voyaging boat must:
- Have no potential for a sudden blackout of electrical power (load dump).
- Require little human supervision for reliable operation.
- Place no added stress on the skipper and crew, particularly when the chips are already down.
- Be fault tolerant: will keep supplying power even after a hardware or software failure.
If those requirements don’t make sense to you, please read, or reread this article.
Now that we have the requirements defined, it becomes clear that, due to intrinsic fragility and level of complication, no lithium-based system available today can satisfy all of the above requirements without a backup system.
The good news is that there is a simple and relatively inexpensive solution to the problem:
The Requirements
To make a lithium-based system truly ocean ready, it must have a backup that:
- Is simple and easy to understand.
- Will take over critical loads instantly with not even a millisecond blackout. (Read or reread this article if that did not make sense.)
- Does not rely on complex hardware and software for operation.
- Allows the skipper and crew to keep operating the boat safely for several hours after a main system failure until there is a good time, without a lot of other stuff going on, to investigate the problem.
- Will supply critical loads for several hours while the main system is being fixed.
- Will get us home if the main system can’t be fixed at sea or in a remote place.
The above list of requirements makes it obvious that the backup should be based on good-old simple and tried-and-proven lead-acid batteries.
It makes no sense to back up a complicated lithium system with another complicated lithium system, when we can design a better backup for less money using a lead-acid battery.
Let’s dig in to how to do that:
Hello John,
How would you deal with the temp and voltage sensor wiring from the alternator regulator?
Regards,
Jim
Hi James,
Good question. If we followed the normal, but generally wrong, directive to connect the voltage sense wire at the battery positive we would have a problem, but if we follow the standard AAC policy, that I have verified with Al at Wakespeed, and connect the voltage sense wire at the first point from the alternator where there is a switch or fuse, we are all good: https://www.morganscloud.com/2022/03/19/8-checks-to-stop-our-dc-electrical-system-from-burning-our-boat/ (Number 5).
As to the temperature sensor, one of the reasons that I suggested LifeLine batteries is they are very robust and will put up with higher than optimal charging voltages for a surprisingly long time, therefore it probably does not matter for a comparatively short get home passage. That said, if the passage was going to be weeks with a bunch of alternator charging cycles, it would be a good idea to move the temp sensor over to the backup bank.
Hi John and James,
I know this is a bit late to comment about a detail, but anyway:
Since in this case the alternator and chargers are set to feed the lithium bank, the temp sensor is not active. Lithium batteries should not have a temperature compensated charge adjustment, like lead acid should. If in freezing temps they shouldn’t be charged at all, and if too hot they should be cooled, but the voltages shouldn’t change.
The Lifeline batteries and most other LA batteries can live fine a long time without temperature compensation, but we can actually leave the temp sensor by the LA backup battery, where it will be inactive, until we change the settings of the charging sources.
Apart from the temp compensation, different charge voltage and curve might be a bigger problem for the LA, depending on the lithium setup, but probably not enough to be a concern, if we just let it be for a limited time.
One benefit of many of the chargers and regulators recommended in the series, like Victron of the “smart” variation, is that their settings can very easily be changed to what is needed. Often a bluetooth connection with a phone app will do it within seconds. Really nothing intimidating. The detail settings can be found in the data sheet of the batteries, if you want it perfect. Using the default settings in the app is also totally fine, at least temporarily.
Hi Stein,
Good point that the temperature sensors can simply be left on the lead acid side. And as you say, changing charge profiles is easy these days.
A few questions:
Is the DC:DC charger not now a single point of failure with no easy backup?
In this set up would you have a split 12V panel. Critical and other?
Although on smaller boats with smaller loads maybe a DC:DC charger can cope with everything, just turn off what you don’t want in case of lithium bank failure.
Before switching the switch so all charging sources go to the backup bank it seems there would be some fiddling with controllers to change the charge profile of all the charging sources to suit the backup bank. In my experience this varies from a bluetooth app connection, a laptop and a specialist lead or some configuration of din switches on older equipment.
Also I would have added bilge pump to critical loads, unless you are assuming just using a manual pump.
Hi Dan,
Sure, if the DC:DC charger dies we have no back up system, at least in systems with only one (bigger boats will likely need two). But if the the DC:DC charger dies in normal operation, it would be pretty easy to move the critical loads buss to the lithium bank. At that point it would be very bad luck to have the DC-DC charger die, followed by a complete unfixable shut down of the lithium system.
To me this would be an acceptable level of backup, in that we can’t backup against every eventuality, but those who disagree can just have a spare DC/DC charger, they are not that expensive.
Yes, we will need to split the breaker panel, one part for critical loads and one for other loads. On most panels this could be easily done by just hack sawing through the copper plate positive common buss. In other cases a small separate panel will be more elegant. All pretty trivial stuff in comparison to the complications of installing a full on lithium system.
As to changing the charge profile, that would be ideal, and worth doing to get more efficient and complete charging if the get home period after the lithium fail is going to be long. If not long, given how robust LifeLine batteries are, I would not bother unless there was a very large difference in charging profiles. In most cases lithium batteries have lower charge voltages than lead acid, so not a problem at all, other than a bit of under charging. For example Victron lithiums want 14.2 and LifeLine AGM 14.4.
As to a bilge pump, sure, that’s good idea.
Thank you for your answers.
John, Dan,
Thanks, this is all super helpful! On specific use case question: if you connect bilge pumps, high water alarms, etc., to the backup bank, how would you think about this when at anchor / moored without shore-power and the boat unattended? Do you worry about the main lithium bank failing in such a circumstance and thus there is a risk that the bilge pump, etc., could run the backup bank down more quickly than the larger house bank? Admittedly this is layering on bad scenarios, but does feel like a reasonable concern if your boat is unattended for reasonable periods of time.
Thanks!
Alex
The best answer to that kind of problem is a remote monitoring system. We have had one for years, which reminds me I should write a chapter on that.
Makes sense, thanks!
Looking forward to that read John as its something I need to tackle.
On the bilge pump side, what about separating them by bank? I have two DC ones in my main sump, a 750gph lowest which handles routine drips and is on the start battery. A 4000GPH heavy duty on house bank. The thought here is that I don’t want my serious pump cycling routinely or plugging with crud. In the event of taking on serious amounts of water, I don’t want to rely on the small battery. As a side note on this, for boats often left unattended at the dock a lot of sinkings seem to occur due to low battery/charger failure etc after long periods relying on the pump without anyone nearby noticing. In the last few years I’ve caught two. One I’d asked their slipmate if they noticed the pumps running often and now stopped. They had concluded it has resolved itself when the reality was the batteries were underwater. To that end I have a 120v sump pump hardwired as well. Oil bath motor, stainless impeller able to handle debris, dead reliable and superior float system(though not useful when water levels are below 6″) and dedicated 1-1/8″ discharge. Should it ever get a phone call very quickly because the water discharge shoots about 6′ onto the main dock, a call made out of annoyance if nothing else. Costs less than a 1500 plastic 12v.
Hi Star,
Sure all that works. That said, I still like a monitoring system that tells me remotely if the bilge pump is running and how often. That way I will generally catch a problem before it’s a big one, particularly since I always try and get my boats to the point that the bilge pump never runs in normal operation.
Greetings John,
After following all of your articles on lithium batteries plus all the excellent comments by you knowledgeable members this article presents the design I was pretty sure you were heading toward.
I have a couple of questions though. Please be gentle in your reply as I am, admittedly, an electrical novice.
Question One: Would it make sense to make the lithium bank a 24 volt bank and use a 24-to-12 volt DC-DC charger so that there would almost always be high enough voltage to equalize the lead batteries when necessary?
Question Two: Is there a difference between a DC-DC charger and an DC-DC inverter? Apologies if I missed that distinction along the way. I ask because I was thinking it would be nice to have and inverter to both charge the critical systems battery bank and provide 12 volts for other non-critical systems from the lithium bank through the inverter.
I also like the idea of a 24 volt (or even 48 volt) lithium charge bank to, potentially use lighter wire for things like a windlass, watermaker, et cetera…
As always, thanks for all you do!
Kurt
Hi Kurt,
Question one: No, the backup bank needs to be the same voltage as the main bank, otherwise we would not be able to charge the backup bank after a total main system failure.
However, not to worry, DC/DC chargers have “boost” capability so a battery at a lower voltage, say 11.5 volts, can still charge another battery on the output of the DC/DC charger at a higher voltage, say 14.4 volts. with the Victron units this is all easly programmed using a phone.
Question two: There is no such thing, at least as far as I know, as a DC/DC inverter. An inverter is a device that has a DC input (12, 24 or 48 volt) and AC output, generally high voltage output to power household type appliances.
The whole issue of 12, 24, or 48 volt is a whole separate issue that I have written extensively on: https://www.morganscloud.com/2020/12/10/should-your-boats-dc-electrical-system-be-12-or-24-volt-part-1/
Worth reading because just assuming that higher is better can get us into a lot of expense and complication that might not be necessary.
Got it, thanks for the clarifications!
Hi John – on the question one, could I use a double alternator setup. One at 24v for lithium and another at 12v for the lead acid? (I already have two alternators on the engine), or would charging both battery banks at the same time from the engine potentially cause issues? If not then I would only need to switch the solar input and reprogram the MPPT in the event of a lithium failure.
My background is that I would like to go electric cooking, but understand I really need 24v for this, plus extra battery capacity so hence lithium. However I like the idea to keep a lead acid backup bank so wondering if I can keep this on 12V. Our watermaker, electric winches and windlasses all run off 12v so I would still need a reasonable size backup pack and enough DC-DC conversion to keep it full. In this case I would probably only use the 24v system to run the inverter, and keep the rest of the boat 12v. Finally we have an old breeze wind generator so could leave that connected to the 12v lead acid rather than having to update it to 24v lithium.
Thanks and appreciate all the articles.
Hi Matthew,
Sure two alternators will work, albeit with a ton of complications. That said I’m not a fan because of the clutter and possible bracket and crank shaft loading issues, particularly once you go over to lithium.
Remember the engine is a mission critical system so we don’t want to compromise it in any way, particularly for what I regard as an “upgrade” (electric cooking) that is very rarely worth the added complications and expense, and is not green.
More on my thinking on alternators: https://www.morganscloud.com/2013/11/06/10-tips-to-buy-and-install-a-liveaboards-alternator/
More on electric cooking: https://www.morganscloud.com/2021/01/04/cooking-options-for-live-aboard-voyagers-part-1-electric/
Hi Matthew,
I must agree with John here. If the main reason to get a 24V system and lithium batteries is electric cooking, I would certainly not do it. It becomes a very expensive way of cooking.
If you still wanted it, perhaps for other high amp uses too, I might look at going for a 48V bank and charge the 12V system via a Victron battery to battery charger. Thus, only one alternator. If the main purpose of the battery is to run an inverter to drive AC applications, 48V is very much better. I still would question the wisdom of such an endeavour, but it depends on so many different topics specific to your boat that I just don’t know.
FWIW, on our cat we now have a cooktop with 2 induction elements and 2 propane elements. Loving it! We pretty much always use the electric cooking, but would never want to have only that. We monitor battery levels religiously. We have 3,2 kW solar, space for more with no arch, no generator and never run engines for charging only. This is in Northern Europe…
This may work on some cats, with an aware crew. I really don’t think it’s smart to plan large electric consumption on a mono with its very limited space for solar. That creates a boat mostly running an engine of some kind. Not nice to live in, or next to.
Hi Stein,
I agree that 48 volts might be the way to go here because of the efficiencies, but that would also leave Matthew with a bunch of single points of failure with high consequence so I think it would only be a good plan if he were willing to spend heavily on spares, including a spare alternator. Of course I believe in spare alternators anyway but 48 volts ones tend to more expensive and he would also need to manage the poor fault tolerance of such a system. All doable, but a good deal of work and expense. https://www.morganscloud.com/2017/01/28/three-tips-to-make-your-cruising-boat-more-reliable/
All that said, I think you are right that if he goes electric cooking 48 volts might be the best bet.
I like it. By sheer coincidence I have helped a good friend locally (who is a much better sailor than me) to build something very similar. The motivation was slightly different in that he already had two large and physically separate lead acid banks, and one of them was new and perfectly good. So why toss it out?
Still this is very similar to what we ended up with, with just a few legacy load wiring differences that we haven’t bothered to change. Too much work not enough gain.
Hi Philip,
Good to hear that we came to the same conclusion independently, generally a comfort that we are on the right track.
Hi John
I guess that it’s not included in your diagram for clarity but would the AGM start battery be charged from or to the emergency battery (via a VSR/ACR?) ie priority to start or emergency battery?
Hi David,
That’s a good point that I had not given a lot of thought to, but now you bring it up (thank you) I think that the best bet for charging the engine start would be another DC/DC charger fed from the lithium bank with another 2 pole switch allowing the input to the DC/DC charger to be moved to backup bank if the lithium bank fails. This has the nice side effect of providing a backup DC/DC charger.
Hi John
Is this where my 2nd smaller -60A- alternator finally makes sense! What if I dedicate it to charging the two LA batteries? Saving on the DC/DC chargers. Elegant!
No I didn’t think that I’d convince you.
Hi David
Sure, that would work. The only thing is if that alternator is the one that came with the engine it will need to be converted to to use an external regulator, otherwise the standard bad charging profile of the internal regulator will wreck the backup bank. The other issue us that in a case where the main lithium system is down, most boats will need a bigger alternator, so still good to have the switch to move the charge buss.
All that said, the fundamental problem remains, the alternators generally supplied with engines are not intended for continues duty charging, so tend to burn out sooner rather than later.
I know lithium is all the rage with sailors at the moment. It seems like the drop in salespeople are handing out free batteries to the “influencers” and offering incorrect and often unsafe “systems” to them.
I’ve been following your articles on this subject and it just gets more clear and more clear that a true seaman like lithium system becomes very complicated and expensive.
Unless you have an all electric galley, I’m just not seeing a large benefit. Air conditioning on lithium is something I hear about a lot but the boats that I know that do it, end up running a generator to recharge all that used energy anyway.
If the amount of effort that you are showing is required for a lithium install was spent on designing and installing a lead acid based system, I imagine a much more robust, safe, and fault tolerant system would be the result.
I’m the opposite of a Luddite and I’ve spent considerable time investigating the design and install of a lithium system for us. In the end, we keep concluding that (for us) the expense and complication of doing it right far outweighs any benefits.
This opinion is based on having enough solar, wind, and hydro to get a full charge and supply large house loads everyday. We also get a large amount of charging at the push of a generator button.
I would like the weight savings though!
Hi Ray,
Good analysis and very hard to argue with.
You are right, many of the claims made for electric cooking and aircon off batteries are pretengineering at best. Often the claims are made by those who have spent a bundle for something that does not actually work well, and are then trying to makes themselves feel better about it. And there is pretty much always a generator lurking in the background.
As you say, the key benefit of lithium is weight saving.
This goes against your simpler is better principle. Go with Firefly batteries and you get 90 percent of the benefits and none of the complexity. A very experienced racer I know just burned his boat to the waterline when his lithium regulator shorted and started a fire while he was aboard.
Firefly carbon-foam batteries are great, and I do recommend them for a lot of applications now, but “90 percent of the benefits” sounds like hyperbole. They have a nice charge acceptance curve, good cycle life, and are resilient against occasional deep discharges and other abuse. But they are much heavier than LiFePO4 for the same usable capacity, and the service life suffers significant degradation if they are cycled deeper than conventional lead-acid types.
See https://www.morganscloud.com/2020/12/04/firefly-carbon-foam-batteries-are-great-but-read-the-fine-print/
I’m not sure the FF batteries are still being made. https://www.fireflyenergy.com goes nowhere now.
Hi Ray,
I heard that too. A great pity in my view.
Hi Gino,
You misunderstand me and are putting words I never wrote in my mouth. No where in the article above am I advocating for lithium batteries and further I have never done so, although I do try to be even handed about the benefits. I also have written a lot about the dangers of lithium. I suggest having a look through the further reading list at the bottom of the article.
I have also advocated for Firefly batteries: https://www.morganscloud.com/2018/05/11/battery-options-part-2-lead-acid/
That said, be aware that I’m currently hearing disturbing news, from reliable sources, of reliability problems with Firefly batteries.
Hi John,
As someone who is considering installing Firefly batteries, I would love it if you could expand on your Firefly comments. Are the problems with their construction, the technology, both, or something else?
Also, FWIW, as of 07/07/22 the Firefly website seems to be completely operational.
Hi Sam,
As I understand it the problems have been with manufacturing QC and honouring the warranty, not the underlying technology, to the point that Ocean Planet have stopped selling them.
That said, I hope they set this sorted out since I think that they are the best bet for many cruisers.
I was all set to buy them for the J/109, but decided against it based on input from Bruce at OP.
Hi John,
Did you end up doing any research on the Lead Crystal batteries from Betta Batteries ?
Hi Paul,
No, I have not. The problem is that there is really no valid way to research that kind of thing, other than buying them myself and using them for a couple of years of cruising, at least. Otherwise with relatively new tech like that I’m dependant on claims of the manufacture and the early innovators who have adopted it, neither of which tend to be reliable since they will obviously tend to play down any drawbacks.
The result is that anything I did would tend to veer into breathless-fan-boy territory, and we get quite enough of that from other sources!
This is one of the many reasons that I suggest that those of us who really want to get out there adopt a wait and see approach on tech that has not yet been widely adopted: https://www.morganscloud.com/2013/10/25/want-to-get-out-cruising-dont-be-a-pioneer/
I guess I’ll be the odd duck out, and state that I am not enthused by this proposed solution, which I regard as an over-engineered lead-acid system.
While I agree it is difficult, if not near impossible, to implement a fool-proof system, why is that the goal? We are surrounded by systems that are not fool proof, and never will be.
The articles here, related to lithium batteries, and their associated comments, display the general concerns and lack of trust that comes from not understanding a concept.
There’s a discussion on Cruisersforum.com around this same subject, started 11 years ago, where Rod Collins, who understands more than most, was a frequent contributor. That discussion is more than 7,500 posts, and will take days to read through. Another engineer who’s contributed much on that site is Eric Bretscher. Eric has a number of excellent, albeit very in-depth, articles on his own website nordkyndesign.com.
I would suggest those who don’t yet fully understand the concept and ideas these two, and especially Eric, have outlined in their writings, over the last several years, stay away from lithium technology for now. Eric makes a strong argument for why only a completely custom-built system will be able to fully protect and maintain a lithium ion battery, and that while vendors are selling components that don’t have the ability to be fully integrated into such a system, we’ll be stuck with a half-assed system, likely to cause problems.
As a background, I am an electrical/electronics/computer tinkerer, with three related university degrees, and a long career behind me. While I’ve designed and implemented custom electronics to handle my boat’s LiFePO4 setup, I’m comfortable enough with this battery chemistry that I have no concerns for the entire control system failing, and having to revert to manually controlling the charging, which I did for the first few years.
I definitely agree that anyone who isn’t willing and able to fully understand all aspects of lithium system design should not try to implement one.
Frankly, the amount of time and effort involved in reviewing all those reports and coming up with a genuinely well-engineered design for a specific purpose is, after cost, the second biggest barrier to adopting lithium technology for my own purposes. If someone’s paying me to do it, sure. But if I had a spare man-month to dedicate to a personal project, this one would be pretty far down the list.
As to whether John’s proposed solution is “an over-engineered lead-acid system”, I would disagree with that assessment. Rather, I would describe it as a system in which the main bank and main bus are a properly-engineered LiFePO4 design, and then a small number of critical loads are placed behind uninterruptible power supplies.
The double- or full-conversion UPS architecture (where AC or DC source power is always run though an isolated converter to provide DC at the UPS’s battery, and the loads either run directly from that DC battery or are powered 100% of the time by pure-sine inverters drawing from it) has been standard practice in data centres and other critical high-uptime infrastructure for many years.
(This is distinct from cheaper UPS topologies in which main power is passed directly through to the load, except during a fault, at which point a transfer relay switches the loads to backup power. In the article, John rejected this approach as being too dependent on the BMS controls, and I agree.)
In its DC form, double / full conversion UPS is an appropriate solution here as well. The only change John has made to the basic well-proven architecture is to add a transfer switch for the charging buss, thus allowing easy manual change-over if the main system must be shut down for extended maintenance.
Hi Matt,
The UPS is a great analogy, thanks!
Hi Frode,
To answer your question, I explain why I’m proposing this backup solution here: https://www.morganscloud.com/2022/06/19/8-tips-to-select-seamanlike-gear/ In short and in my opinion, going offshore regularly requires a higher level of fault tolerance than even the best engineered lithium battery systems can provide today. This system fixes that.
And I do agree that those without good understanding of technology should not install lithium. In fact I have been saying that for four years: https://www.morganscloud.com/2018/05/05/battery-options-part-1-lithium/
But in the real world many cruisers without that understanding have installed lithium systems, and many of those systems are fundamentally flawed—drop in batteries that can’t communicate being but one example—so this solution is particularly valuable now.
This is very close to what we are implementing with one exception due to being an all electric boat.
If the Lithium bank is used for an electric motor then it almost certainly won’t be 12 volt. Ours is 48 volt (although the motor also supports 96 volt which we feel adds considerable danger so haven’t gone there).
If you are using a lot of mains electric so that you are looking at say 2000 watts or more from your inverter then 12 volt becomes very tricky due to the high current. So a battery bank at a higher voltage becomes a good idea. For us switching to 48V allowed us to have 5,000 watts and also gained us features from the Victron Multiplus 2 which gives faster mains charging, the ability to use the solar to reduce the cost of shorepower and more.
In the normal way of things this isn’t a problem. we have a 48V to 12V Dc-DC converter.
However, our solar needs a 48V MPPT controller to charge the main bank. While our MPPT can support 12V I don’t think it is auto-sensing so not as simple as a 2 way switch. However, the DC to DC converter can take the MPPT output and use that as it’s supply so I think that it will work without the switch (assuming that if they fail you use your switches to disconnect the Lithium batteries). Obviously putting the solar through the DC-DC converter does have an efficiency cost.
Obviously you also should have either 2 DC-DC converters for redundancy.
Also we have 2 separate 48 volt lithium banks for redundancy (independent switches and fuses).
Hi Dave,
The system I describe in the article is not intended for electric drive boats which are a special use case.
However, it has been super helpful for us. I think the dc-dc converters can make it work well for us.
Hi Dave,
Glad it was useful, I just wanted to make clear to others that I had really not thought about electric drive boats when I was writing the above.
I guess the key problem for electric drive boats is that the standby bank needs to be of the same voltage as the main bank so it can be charged from the main banks charge buss if the main bank dies completely. Not a problem with 12, or even 24, but going to make the standby bank kind of big for 48 volts. And then, of course, the standby bank is not going to have the power to provide much drive, so that’s a whole ‘nother thing to think about.
Hi John,
A battery bank for electric propulsion is far from the topic here, of course, but it might still be useful for perspective. As I work with fully electric boats (tourist boats on the Amsterdam canals) that are running something like 14 hours per day, every day, and some of them used to have diesel engines, I I’ve gathered some observations.
The main lesson is that the reliability of batteries, and the complete electric drive systems, are on another planet compared to any diesel driven system. The latter needs literally hundreds of times as many hours of maintenance and fail in traffic about four times a year, always at the worst times. These fails are usually caused by the many different skippers being incompetent or careless, or some miss in maintenance, but the same treatment is given to our electric drive battery banks and drive systems. They need close to zero maintenance and just never fail. Our current 42 boats, from about 20 to 200 passengers, use only lead acid flooded 2V full traction cells, so it’s old tech. The battery banks do have electronic control systems, however, and the cells typically last 5 years of extremely heavy use. The diesel engines last not much longer…. The vastly improved economy and reliability of electric drive systems make them a no brainer here. The lost diesel noise and stink help too… Already now there are almost zero diesel engines left on the hundreds of local commercial vessels.
We, myself definitely included, tend to focus on the item we’re thinking about, while missing the context. While having fail proof systems should always be the goal, of course, it might be useful to look at it in the above context. We accept that our diesel engine is a very fragile animal, known to fail mostly in the worst situations, usually due to fuel contamination. It’s totally possible to dramatically improve that lousy reliability, but it demands knowledge and militantly rigid routines. We accept the demands, often knowing we’re not gonna satisfy them well enough…
Our battery banks, no matter what type, can indeed run empty, or fail in other ways, which does give us that uneasy feeling, so we’ll put lots of attention and money into it. However, the fact remains that our battery banks are probably the most easy going and reliable technical items on the boat. The electric system they’re running, on the other hand, is often/usually a whole another can of worms!
I’m a tech nerd type of guy and a lithium fan boy. Still, when people ask me about how to go to lithium, I always insist on first discussing WHY they want to do it. It’s almost always based on the emotional reaction mentioned above. Uncertainty, not actual need. Having the shiny new latest tech is also at least as important. The vast majority of boats should just not install lithium yet. It will not give any noticeable benefits, just costs and complexity, meaning vulnerability, especially since the majority of available consumer products are not good. Boats that depend on solar etc most of the time, will definitely gain a lot of extra available power by getting lithium. In the region of double, if the lithium bank is 60% of the Ah of the lead bank. Others won’t.
PS
The future of electric drive systems is much higher voltages, probably in the region 500 to 1 000 Volts. That gives some important advantages, like less heat and way more power, from tiny, light and cheap motors, (think 100 Hp from the size of a 6 dinner plate stack,) but also plenty of issues to solve when that time comes, quite soon…
One of the few unambiguous, must-be-lithium cases that I can think of is for trailerable electric boats. In that case, you simply cannot get enough energy density to achieve usable range, while staying within practical and legal weight limits, from any other chemistry.
For the cruising sailboat / cruising powerboat case, and for short-range all-electric boats that are not bound by a legal maximum weight, I agree that lithium batteries of any kind are, for the moment, still a hobbyist / tech nerd thing rather than a compelling, obviously beneficial choice.
The road-going EV industry is settling on 400 V, 600 V, and 800 V as common nominal maximum bus voltages (in practice, there’s about a 25% swing in voltage below the nominal maximum as the load conditions and state of charge vary). As our industry is not large enough to spend billions of dollars on R&D and factory tooling, we will almost inevitably end up piggybacking on the car industry’s work, and I would expect future electric boats to increasingly use off-the-shelf high-voltage parts pulled from the parts bins of BMW (as Torqeedo already does), Ford, GM Ultium, etc., which will work well, but which is — for the moment, and possibly forever — more the domain of electrical engineers and technologists than of DIYers. GM Ultium in particular, being highly modular and designed for versatility and easy reconfiguration, may well become a significant player in this space.
Hi Stein,
I really don’t want to go down the electric drive rabbit hole on this article. Said discussion tends to turn into a huge time sink and we have already done it to death on several other articles: https://www.morganscloud.com/2021/03/22/when-electric-drive-works-for-a-cruising-sailboat/
I do agree that many people go with lithium who would probably be better off without.
John,
I am familiar with Eric B.’s and Rod Collins’s work, and this article of yours is the most succinct and useful article I have read on the subject. Thank you, and I will re-read this a number of times.
Regards, KL
Hi Kit,
Thanks very much, putting my stuff with those two is high praise indeed and much appreciated.
I have a pet theory I’m working on that will (hopefully) be a game changer for using Lifepo4 for house loads on boats. I’m going to build a bench test unit later this month, try to wreck it every way I can think of, if it doesn’t work I’ll build a new one and replace my start with that. There is a newer chemistry called LTO, apparently very safe, mostly used as motive batteries in busses in Japan it seems. The magic is in the voltage of the cells, no BMS needed I believe. Cycle life is reportedly around 100, 000 cycles. By running one more cell in series, you lose a bit of capacity, but have a high voltage cut off way above anything the alternator should reach allowing for graceful taper and shutdown just like lead acid, then a simple (and cheap to carry spares) VSR to stop excessively low voltage from being an issue. Temperature insensitive, (-30-+100)massive power delivery for the AH, 8C draw and massive charge rate is acceptable, so a single set of cells will give better starting on my 3 cyl Yanmar than the current lead acid, and if charging with a portable generator or shore power, even a single set of cells can handle 100A of charging no problem, the buses in Japan apparently typically charge for minutes not hours at huge rates.
If a salesman is telling you that lithium titanate cells will last 100,000 cycles, you should be very suspicious. 3,000 to 10,000 cycles is typical of that chemistry and some can reach 15,000 in gentle service. And that is *with* a good auto-balancing BMS; they will not reach anywhere near that cycle life if they are not balanced regularly.
LTO is used for buses etc. because the high specific surface area of the lithium-titanate nanocrystals on the anode enables very high charge acceptance rates, which allow a bus to add meaningful range from a 5 minute plug-in at the transfer hub. It has lower efficiency and lower energy density than other lithium battery formulations.
I have built my own LTO bank and learned a fair bit along the way. I agree that 100,000 cycles for LTO is too high. On the other hand 3,000 may be on the low side. Yinlong, who are the main vendor people source LTO cells from, claim 30,000 – which seems plausible given they are an established and credible manufacturer at scale. And as you say their target market is buses which encounter very fast and deep cycle rates (maybe 5 – 20 per day). I would expect this is a reasonable number based on real world experience.
The main reason why they achieve this outstandingly high number is that LTOs generate no physical strain inside the cell while cycling, which eliminates the main mechanism of cycle failure all other lithium chemistries are are vulnerable to.
In this light I would be comfortable with conservatively claiming 10,000 deep cycles – which is going to be way longer than most owners usage profile.
There is some debate around their efficiency – but much of it is based on a faulty misinterpretation of the difference between coulomb efficiency (which is exceedingly high) and round trip energy efficiency which is only slightly less than most other lithium cells. The difference is insignificant. (I have done the measurements on this and satisfied myself on this point.)
Hi Mal,
I took a look, but given that he is advocating for paralleling batteries of very different chemistries, charge profiles and internal resistance I would recommend staying away from his ideas, particularly since in many cases he is bending the facts to make his case and is also advocating for something that is intrinsically dangerous. (He does mention the dangers, but glosses over them in a scary way.)
I do agree with him that current measuring charge controllers are the way to go, but his claims to being the only one to figure this out are wrong as others have done exactly that in far better ways than he is proposing: https://www.morganscloud.com/2022/01/30/wakespeed-ws500-best-alternator-regulator-for-lead-acid¹-and-lithium-batteries/
That said, if he comes up with a good low cost current measuring solar controller, that might have value, although I think I’m right in saying that companies such as Victron already do this with current measuring BMS that then communicate with all charging devices, albeit at a price.
To me his presentations demonstrate the big danger of YouTube: someone who has great presentation skills can evangelize well for ideas that are fundamentally flawed. To me a sign of this behaviour is when the presenter consistently claims to know better than the companies that make the gear and when they are very light on specifics, such as bank size, weight, etc.
Hi Mal,
I don’t have any wisdom on this. The problem is that most of these “breakthrough technologies” fall by the wayside once subjected to the real world offshore.
Don’t get me wrong, I have no doubt that we will see huge and practical breakthroughs in battery tech for use on boats in the next few years, but in my view there is pretty much no way to determine which claims are valid and which are not, so I don’t try. Or, to put it another way, I would rather be sailing on a boat with gear that I know works and does not have some lurking unintended consequence that will ruin any of my time on the boat and more importantly, limited time on the planet.
More on this thinking here: https://www.morganscloud.com/2013/10/25/want-to-get-out-cruising-dont-be-a-pioneer/
All that said, some other people derive pleasure and satisfaction from investigated and maybe even experimenting with the latest tech, but that’s a hobby in and of itself and not mine: https://www.morganscloud.com/2016/01/08/marine-electronics-system-recommendations/
Hi Mal,
I have no previous knowledge about the EcoUlt batteries, but being a nerd 🙂 who also works with electric boats, I got curious and googled a bit. I only looked at it superficially, so I might have missed important points, but my impression is that this is not suitable.
The tech is apparently a combo of a “new type” of flooded lead acid cells and supercapacitors, using the same electrolyte. The supercapacitors would then help with some of the weaknesses of lead acid cells. The claim is that the combo can live well with partial state of charge for long periods of time, which is important for an efficient house bank in a boat. However, these are 48 volt banks only, they need some electronics, similar to a lithium BMS, and they are quite large, meant mainly for solar in houses.
This short Wikipedia article, states that the company “has ceased operations”: https://en.m.wikipedia.org/wiki/Ecoult
There was a big recall issue, which might be the reason. The tech might still be good stuff. I don’t know.
Hi Stein,
Thanks for researching that, makes sense to me. It seems that a lot of the solutions being used in off grid situations on land are not useful on boats because of weight and volume. To me the biggest benefit of lithium is the size and weight of the bank, so I would not consider any sort of high tech bank that compromised that benefit. My thinking is that if it’s going to be heavy and take up a lot of space, it might as well be good old simple and reliable lead-acid. But then I’m like you: a weight obsessed guy with a racing background.
I think you should add an alarm on your vital loads that will scream if the normal load buss drops to zero.
Hi Mathieu,
Good point. That said, battery monitoring with alarms should be part of the main system on any cruising boat, so I’m not sure I need to add it to this article given I have already written extensively about it in other chapters: https://www.morganscloud.com/2018/08/13/battery-monitors-part-1-which-type-is-right-for-you/
Hi John,
I have been planning a battery capacity upgrade, so great timing for me to seemingly affirm my soon to be done approach.
My preference would actually be to expand my existing flooded 2x 240ah 6v bank, but space on our 33ft yacht precludes that. Instead to increase capacity, I will add a 125ah drop in lithium, and reroute my small fridge freezer load( 50-70ah daily)to that added battery via a 1-2/off switch, meaning I can divert that load back to the original house bank if needed. Charging the lithium would be thru a DC-DC charger, or two if need be, with solar input into the house bank and occasional motoring keeping the lithium reasonably full, with no PSOC issues if not fully recharged.
Hopefully this provides an effective use of Lithium, with minimal upgrade costs, and whilst not fully utilising the technology, and possibly lacking a little in efficiency, a reasonable compromise?
Whilst it is a second battery to monitor, it should take care of the majority of my house load, effectively doubling it, and alleviate BMS drop out concerns, as between a SOC alarm, a Bluetooth internal BMS alarm, and my beer getting warm I should be able to divert the fridge freezer load back if need be,
Planning also on a relay activated by the main house bank switch to ensure the fridge freezer load gets turned off when laying up the boat, possibly along with the dc to dc input. Another option is to also divert a portion of solar via seperate MPPT regulator to the lithium bank directly.
I guess in many ways this is a much simplified version of your proposal, but hopefully worth mentioning.
Cheers,
Steve
Hi Stephen,
Interesting and possibly a good use for “drop in” batteries, although if it were me, I would still look at the relative cost of a lithium battery with an external BMS that can communicate and not just default to “drop in” because it seems easier. After all, you might find that you love lithium and wish to go 100% that way when the lead reaches end of life, so then being stuck with non-communicating “drop ins” might be a drag.
John,
Forgive me for jumping ahead of myself. I’ve just joined you on high recommendation from some folks at the Cruising Association. …so I haven’t yet read all your content on this subject, but looking forward to it.
Do you know if Johan on RAN Sailing, YouTube designed his system around your concepts?
Our windlass and bow thruster are currently run off the 420Ah ‘lead’ house bank, in the stern through big cables that run the length of the boat. Could we put lead batteries in the bow for the windlass and bow thruster and use them as backup if the LFP goes down? How would the circuit work in your recommended configuration?
This seems like a low risk option as offshore those are two components you’re not likely to be using.
Hi Andrew,
I don’t know if Johan is basing his stuff on us. Assuming that he is doing the same thing (I have not watched) then he might have come up with it independently, it’s not rocket science. In fact I would argue that as soon as we come at this in a seamanlike way the above solution becomes obvious.
As to using the bow lead acid batteries as backup, I guess it might work, but it would get you into a lot of long cable runs and would also subject the sensitive mission critical stuff to spikes and brownouts when the bow thruster and windlass were being used, so not optimal for the same reasons that using the starter battery is not a good way to go.
Thanks, Johan probably got his advice from Batterybalance.com in Sweden. They look like they do an interesting external BMS kit.
I was only thinking the bow installed lead backup idea would work because the high current power feeders are already run the length of the boat. I’d like to avoid running smaller charging cables the length of the boat. The challenge is working out how to use the single pair of large cables to charge the batteries from the back of the boat and then switching to feeding when required.
Hello John,
I have been using the Victron DC to DC 30 amp charger without any issues for the past year. Great product!
I am doing coastal cruising so I wanted to experiment with a rather low cost lithium system to see how it works.
My system: New Beta 35 (awesome engine and good choice for the Adventure 40) 120 amp alternator upgrade with brush box connected to a Balmar charge controller (I now know the limitations with the Balmar vs. WS500)
Start battery – basic 12 volt flooded
House battery 300 Amp hour (Ampertime from Amazon)
Alternator charges the 12 volt flooded and is regulated by the Balmar charge controller. Victron DC to DC 30 amp charger senses when the ignition is on and alternator is charging – sends 30 amps to the lihium
Since I have a very heavy cruiser (Downeast 32) I tend to motor often benefiting from the charge. I will add another 30 amp DC to DC charger to double the charge capacity.
So far, this has worked out extremely well for the last year. I find my house bank never gets below 85% (measured with an Ipad and using the Victron shunt)
I have no way of starting the engine if the lead acid fails other than jumper cables.
Let me know what you think.
Hi Dan,
Sounds like a good system as long as your usage profile involves a lot of motoring. For other usage profiles involving more sailing or a lot of time at anchor, charging the lithium through a DC/DC charger gives up one of the biggest benefits of lithium: its ability to lap up all the amps the alternator can supply (within reason), all the way up to full charge. For example I’m guessing your bank would happily charge at ~150 amps so you would need five DC/DC chargers to equal that.
Thanks John. Sounds like my systems is good other than sending more amps to the lithium. Two possible solutions – charge the lithium regulated by the WS500 and charge the flooded cell with the DC to DC charger. Or, wait for Victron to produce larger DC to DC chargers!
Sterling Power makes a 60 amp DC to DC charger, and possibly a 120 amp. https://www.sterling-power-usa.com/SterlingPower12volt-12volt-60ampbatterytobatterycharger.aspx
Hello john,
I just bought a multihull and I’m immerse in some works, so I have to take some decisions about the battery bank.
I read the system that you propose in this article and seems a good compromise to use lithium battery in a safely way.
But from the point of view of this implementation is a bit complex to divide the charges into critical (connected to the lead bank) and the rest.
I’m wondering what would be the inconveniences (in your lead/lithium series system) to connect all the charges (critical and others) only to the lead bank?
Regards
Carles
Hi Charles,
You often hear of people advocating for attaching all chargers to the lead acid bank, usually the engine bank, and then charging the lithium through DC/DC chargers and this does have some advantages, but to me it makes no sense since one of the biggest reasons for installing lithium is how fast it takes a charge. Anyway, to me charging should always be attached to the house bank, regardless of battery chemistry. More on that coming soon.
As to complications. In my design the all charge sources are on the charge buss and said buss is normally connected to the main bank and only moved to the backup bank if there is a major failure of the main bank, I don’t really see any complications here. Am I missing something?
I guess inverter/chargers could be seen as a complication, but the answer is to lock them out and just not use them when the charge buss has been switched to the backup bank. Pulling the fuses on inverter chargers is a simple way to do that.
Hello John,
I’m sorry but I was confused with the terms. I mean loads when I writed charges.
So my question is if it would be any inconveniences (in the system with lead bank charged with a DC/DC charger from lithium bank) to connect all the loads (critical and others) only to the lead bank?
I hope that now my question have more sense.
BTW, if we put the charges from the alternators only to the lithium bank , and there is a problem with the BMS and he cut the charging, how many time would pass until the alternator become damaged?
Would be more convenient to install a separator for the alternator charge connected to both, lead and lithium bank?
Regards
Carles
Hi Carles,
Sure, you could connect all loads to the backup bank, but I can’t see any advantage in doing that, and the disadvantage is you would need larger and/or more DC/DC chargers to keep up with demand.
The whole issue of alternator damage is a complex one, and beyond the scope of this article, more on that here: https://www.morganscloud.com/2022/01/30/wakespeed-ws500-best-alternator-regulator-for-lead-acid¹-and-lithium-batteries/
I will also write more about the subject in coming articles over the next few months.
Hi Carles,
You ask how long it takes to damage the alternator if the BMS cuts the connection. The answer is: Within a fraction of a second. Immediately. It’s a voltage spike that can get to far more than double of what your system is meant for. This can destroy much more than the alternator. It’s not 100% certain that it will result in serious damage, but it’s the most likely.
It’s essential to design the system so this cannot happen. A lot of boats fail this demand.
Following on from Stein’s comment;
John, is it your assumption that the dc/dc charger will be able to absorb the voltage spike in case if bms shut-down? What if the AGM battery already is at 100% charge?
Any more thoughts on carbon/lead batteries as an alternative to Li? Apparently durable, but can only accept charge of 30% of battery capacity (like you pointed out a while ago)
Browing the BMS from https://batterybalance.com/x2-bms-12-24/ and think it may be worth investing some time, as the at first glance seem to address many of the issues you raise.
Lastly thanks for another great and clear thinking article on a complicated subject.
Hi Petter,
Thanks for the kind words on the article.
No, a DC/DC charger is probably not going to absorb the spike. Also, whether or not a lead acid battery is at full charge does not effect its ability to absorb an alternator spike.
As I write above, this article is not about dealing with alternator spikes caused by BMS shutdowns. That’s a completely different subjects and too complex to get into in a comment here.
That said, the right way to deal with alternator shutdown spikes is not to rely on some kluge of lead acid batteries in parallel, but to have a BMS that communicates it’s intent to the alternator regulator before shutting down: https://www.morganscloud.com/2022/01/30/wakespeed-ws500-best-alternator-regulator-for-lead-acid¹-and-lithium-batteries/ (Scroll down to, and start reading at, “Lithium and The Wakespeed WS 500”.)
So it would seem that a way around this problem would be to run 2 x LiFePo4 battery banks that are separate batteries but connected to the same Buss bar setup – say an A and B bank. If each battery has its own BMS with associated switching/fusing then if the BMS shuts down, say, bank A then bank B is still up and running and accepting charge. Which is not to say to not use a wakespeed 500 unit – rather a layered defence against this problem. Thoughts ?
Hi Mark,
That’s not he best answer, given that there are things that can shut down both banks.
More on the best answers, here: https://www.morganscloud.com/2022/01/30/wakespeed-ws500-best-alternator-regulator-for-lead-acid%c2%b9-and-lithium-batteries/
And please add further discussion of this issue to that article so we are in the relevant place to discuss an important issue.
Hi Mark,
Now I think about it, that’s not only not the best answer, it’s unlikely to work at all: Since the two banks are connected together in parallel they will reach an overcharge condition at about the same time, so first one will kick out, and then the other will get the full output of the alternator and immediately kick out too. Instant blackout (assuming single buss), and fried alternator diodes too.
>> it makes no sense since one of the biggest reasons for installing lithium is how fast it takes a charge. <<
Have you seen the Sterling B2B chargers – these work on this principle: alternator to starter batter and B2B to Lithium.
BUT – the charger manipulates the voltage to trick the alternator to output high amps for fast charging the Lithium. The clever bit is that it does this without over charging the starter battery.
This is the system I have – and it works very well. No risk of an alternator load dump for example.
My system can charge the Lithium at over 100 Amps without over charging the starter battery, though I usually max it at 60amps for the sake of alternator life.
Best of all, it is incredibly simple to install – and protects the lithium from alternator voltage spikes.
And a fraction of the cost of your system!
Hi Richard,
Yes, I have seen the Sterling units and while I agree they are less expensive, they are not equivalent.
In fact your comment kind of makes my point, at least in my eyes, in that I would be pretty disappointed to go to all the expense and aggravation of lithium and then only be able to charge it at 60 amps at 12 volts or 35 amps at 24.
If it were me going lithium I would be going 24 volt and want a filthy great continues duty large case alternator controlled by a WS 5000 so that it could charge the lithiums at at least 3.5 KW or 150 amps at 24 volts rather than .75 KW (60 amps at 12 Volts). To me that’s half the point of lithiums.
Even with a lead acid bank the minimum alternator charging capacity for a live aboard cruising boat, in my view, is 2 KW—the amount we always had on our boat.
The Sterling unit was primarily designed to get more out of standard OEM alternators on Yanmar and particularly Volvo engines where at one time changing the alternator voided the warranty—the reason Boreal used/uses the Stirling unit—but the problem with that is these OEM alternators are not designed for continues duty and so will fail comparatively quickly compared to a continues duty alternator.
More here on alternators: https://www.morganscloud.com/2013/11/06/10-tips-to-buy-and-install-a-liveaboards-alternator/
Hi Again Richard,
I should add to my comment that I’m not saying your system is a bad one. These things depend entirely on usage profile, so it may indeed be the best and most cost effective solution for you. Also, I would be the first to say that the Sterling B2B is a cleaver unit that solves a problem in a very inexpensive way, but like all things its best to be aware of the drawbacks and limitations.
My setup is bascially as you describe, but 48v/12v. I use the same MPPT for the DCDC as is for the solar panels, giving common spares.
Only thing I have found with mine, is I need an alarm if the DCDC is out / switched off. The BMV712 is not really ideal for this.
My one 12v agm does critical instruments, winches, windlass and 2 x engine start.
Very simple Onewire alternator is backup charging.
Solar can be reconfigured if really needed. 48v pack could be reconfigured to 12v if way offshore and MPPT’s adjusted to suit.
Lithium jump starter pack is charged every 3mths for the emergency engine start.
The only gap I have is the battery is not big enough for full overnight autopilot. I would need to run an engine. I need to give that a little more thought. Running an engine is not a big deal in the event of major electrical failure.
Hi Paul,
Sounds well thought out although I wonder why you went 48 volt given that it does not supply your high current loads like winches and windlass. Would 24 volt work better? Of course that would mean changing the motors on the high loads.
Some months ago I had a similar thought and asked a battery-geek friend about it. His response was “Yup. Could work well. I’ll give it some thought, but you will want to charge the lead side and use the dc-dc to charge the lithium. I’ll get back to you”. He’s been traveling since then and I’m still waiting to hear the logic there, but it’s an interesting response.
Hi Ashely,
You hear that a lot, but to me it makes no sense. One of the biggest benefits of lithium is it’s ability to take a lot of charge current right up to fully charge, so why would we want to bottle neck that with DC-DC chargers?
Totally agree with that – Lithium can take a high charge current – want to get as much juice into the bank while the engine is consuming diesel. Depends on the batteries, but most LiFePo4 cells can take a .5c charge current happily, better cells can take 1C and if you went to Headways (brand of cell) some can take 4+C !. Its one of the big advantages of lithium – charge them quickly, the next being if you dont charge them to the top, no problems at all. Pb needs to get back to 100% and the absorption stage takes…..way too long
Personally I like LTO’s. They are not that much more energy dense then Pb – but in an 11 ton cruising boat (eg, mine) I am not sure the weight issue is an issue. However getting GENUINE new Yinlong cells is not easy or cheap. But I think LTO makes the best sense of all Lithium’s – you can discharge an LTO cell to ZERO and it will charge right back up with no damage other then some loss of cycles – it is said a total discharge to ZERO knocks the cycle life down to around 6-8000 cycles. I think this is hugely important. Knowing I can safely go to ZERO if I need to for some reason and then the cells in the battery charge right back up with no real damage. Its almost like an insurance policy on the batteries. I have lost expensive Victron AGM’s through them being discharge too low and then the people who should have charged them back up – simply didn’t ! = result was ruined bank. With LTO that is a thing of the past. It seems like a very valuable good to have trait in a battery bank that is relied upon heavily.
Hi Mark,
LTO do sound good. That said, I would not install a bank built from tech that is that far outside of normal usage on boats. Might be fine, but there might also be unknown, unknowns, in the words of Rumsfeld. More on that here: https://www.morganscloud.com/2016/11/22/the-unknown-unknowns/
The other issue could be insurance since underwriters are notoriously conservative about new-to-them technology even if it’s well proven in other usages.
I also wonder about if LTO is so great, why are none of the established marine battery vendors offering it? Might not be significant, but could be, and no way to know for sure.
So, personally, I like to go sailing while others experiment with this stuff: https://www.morganscloud.com/2013/10/25/want-to-get-out-cruising-dont-be-a-pioneer/
Hi John,
Being a nerd, I can’t resist a comment.
As a summary, LTO (Lithium Titanate) is just not a good alternative for boats and probably will not become a good alternative in the future either. The only smart alternatives right now are some type of lead acid (LA) or some configuration of LiFePo4 cells (LFP).
The LTO chemistry has some very cool properties, like extremely long usage life, (some claim more than 20 000 cycles above 80% capacity), the ability to take super high charge currents, (a 100Ah battery could take 400 Amps without a sweat), extremely stable chemistry that will not burn no matter what you do to them. Arguably the safest chemical battery type available, no matter what tech.
However, LTO also has some not so cool properties. The energy density, both weight and volume, both nominal and real, is not much better than lead acid, thus about one third the real values of good LFP (LiFePo4). If going for fancier battery banks, better energy density is an absolute must.
LFP cells have an extremely flat Voltage curve. From charging, often at 13,8, to empty, 12,8 V, is just 1 Volt difference. That is enhanced by the ability to keep the Voltage pretty well even under heavy load. This is a big advantage! Lead acid will in normal use go from 14,4V charging, down to about 12,0 V, plus the drop under load, which can easily be down to 11, or sometimes far more. That’s well over 3 Volt difference. The electronics really hate those low Voltages, but it still works.
LTO cells are even worse. They change Voltage so much over the span from full to empty that we’d need electronics to stabilise it. It cannot be used directly, which is a vulnerability in itself. Also, each cell has a lower base Voltage, so we need more cells for a given bank. Adding all this up, plus that the production volume is way smaller, a complete LTO bank ends up at least twice as expensive as a top quality LFP bank.
There’s just no point in paying more than double for a big and heavy bank that is even safer than what is already very safe (LFP and LA), can tolerate charge speeds we will never be able to provide, (even decent sized LFP challenges our ability to reach the limit) and might be still working when our grand children dies. In about ten years they will be severely outdated, so our grandchildren will not be thankful. LTO is just not a smart choice.
Hi Stein,
As you say good and not so good traits about LTO cells.
LTO chemistry = Li2TiO3
The LTO cells are 2.3v nominal so it takes 22 cells to make a 48v battery. LiFePo4 are 3.2v nominal, so take 16 cells to make a 48v battery.
The biggest downside is that, as you say (and as I eluded to at the beginning of my post) is the LTO cells are only a little ahead of Pb in energy density, so they are only a little lighter then Pb and take up the same amount of room. So there is that. However is this really a problem on a heavy cruising boat?
Four BIG positives about LTO cells…
1/ Safest chemistry of all Lithium’s – some like that. LTO is completely free of carbon, thus they avoid thermal runaway or overheating which is a main cause of fires in energy storage systems. LTO is without the risk of fires or explosions. This video https://www.youtube.com/watch?v=Qzt9RZ0FQyM&t=212s is a real eye opener ! Note those gases that are expelled – that alone can be fatal in an enclosed area.
2/ The recharge efficiency is approx 98% – better then any other battery chemistry. (98% of what you generate goes into the battery – Pb is about 70 – 75% – UP TO ABSORPTION stage – then it drops off to about 50% efficient for the next 4 -6 hours in order to get the Pb batteries back to that VERY important 100% SOC). It can be important on a boat in a remote area that everything you can generate goes into the battery and is not wasted with inefficiencies – meaning that limited fuel supply can get more of that fuel converted to electrical charge with LTO. This may be very important to some.
3/ They charge incredibly FAST – they can be recharged to full in 6 to 10 mins – IF you can generate enough current to charge them that fast. Depends on how big your LTO bank is. But in general we cant charge them that fast on our boats – possibly when docked? But at least you cant hurt your battery bank by whatever you are outputting on your boat. They will take everything you can throw at them and then some. A 1C charge rate is very very kind to these batteries which extends thier cycle life considerably. I wouldnt want to go any higher then a 1C charge rate on LiFePo4 because it would reduce the number of charge cycles.
4/ They can be discharged to FLAT – ZERO v and then be recharged right back up to full with no damage to the cells. The cells will lose some charge cycles but its estimated that after a ZERO discharge event the cells still have in the region of 6-8000 cycles left. That’s a lot of life left in my battery bank when I had to run it down to ZERO v for some reason – and I can think of a few reasons why I might have to discharge to ZERO at times. Nice to have a battery that is not ruined by this and recharges and carries on – another 6000 times.
5/ (Bonus BIG Positive) – they can be recharged in freezing conditions – I cant remember now if its up to -20 or -30c but its way way more then any other battery can be recharged at – might be important for boats cruising the Artic/Antarctic regions or even Canada or the Scandinavian countries? LiFePo4 can be dangerous to recharge at below 0c.
As for your point about LTO changing voltage to a degree that we would need electronics to stablize them – I dont understand this point. A fully charged LTO cell is around 2.5v, a fully discharged cell is around 1.5v. With LiFePo4 a fully charged cell is around 3.65v and a fully discharged cell is around 2.5v. With any cell chemistry we dont go to the charge/discharge knees – we rely on a BMS to control that for us, but with LTO even if you do over charge a cell it is not going to explode or burn and if you go over the steep discharge knee to 1.5v you are not going to kill your LTO cell. The opposite is true with LiFePo4 – take this cell down to 2.5v and its almost lost. Just a little more discharge and you can throw it away. Overcharge an LiFePo4 cell and it will bulge and eventually catch on fire.
So I dont get why you think LTO voltages are a problem – they are in the same voltage swing as LiFePo4 – about 1v from full to empty. If you have any reference to this I would love the url to study this point as I have NEVER ever heard of this problem you outline for LTO – doesn’t mean its not true – just means I have never heard about it up till now, so am interested to dig deeper into this phenonium
Thank you for this excellent article. It’s one of the best pieces I’ve read on the topic. More people need to hear your core message about system failsafe robustness.
Here is the States, the ABYC’s newly published standard on lithium batteries doesn’t do enough to raise the bar on system safety and reliability. Specifically, it doesn’t address a number of important points, all of which you touch on in your article:
Hi Earl,
Thank for the kind words, and I totally agree about ABYC’s new standard and your list: https://www.morganscloud.com/jhhtips/abyc-publishes-lithium-battery-standard/
I guess we only need to look at the number of industry insiders on the ABYC committee with an axe to grind to understand why those committee members who wanted more stringent standards, were not heard. Having talked to a couple of ABYC committee members over the years I’m deeply aware that any idea of impartiality is a myth. Still it’s a start and a great deal better than nothing.
Some of these desired points are mutually exclusive with regard to the purpose of the BMS to protect the LFP.
ABYC does require that there be a visual and audible alarm in advance of shutdown of the LFP.
As I understand it, ABYC requires that the shutdown isolate the LFP completely, at which point the boat will be left dark unless primary and essential loads feed from a different battery.
Also ABYC regulations do not allow paralleling different types of batteries. In any case, paralleling LFP and FLA is a poor solution to potential drop-in LFP Battery disconnects which damage charging Alternators and equipment.
For our small boat we have designed, with the help of 3 other sailors, a BMS/LFP system with a single switch that allows us to feed the DC Panel from the SLA battery in an emergency, rather than groping for jumper cables and pulling fuses.
I chose to do this rather than separate our small DC Panel, into essential and non-essential loads, as I can simply turn off the Refrigerator and Autopilot at the panel.
I think it is better to follow ABYC requirements and adapt, otherwise these systems will become horrendously complicated and difficult to fix.
We need to develop some standard wiring diagrams which meet all the requirements which provides sound guidance to boat owners. I actually think ABYC should have some examples of systems that comply.
Hi Rick,
I agree on ABYC compliance, but if you look at the chapter above you can see the the solution I propose is also ABYC compliant and does not parallel lead acid and lithium. The other advantage is that in the case of a BMS load dump there is no need to change any switches and no interruption of essential loads, not even a second, which I think important, at least in an offshore boat. I explain my thinking on that last point here: https://www.morganscloud.com/2022/04/25/why-lithium-battery-load-dumps-matter/
I agree with you that separating the essential and non-essential loads is a better solution and will probably be looking at that alternative again, since it will basically require that I remove the refrigeration and just a few other circuits to a non-essential bus powered by the LFP, since it is a smaller boat. The problem is I already have a good reasonably new DC Panel and switching off those circuits is quite easy.
Also I do like the continuous operation of essential loads.
On our boat, I think I would like to keep the SLA to just 70ah-100ah and I would have to increase the size of the DC-DC charger and change the wiring a bit.
I am still trying to figure out where to put it all, and for the time being I am going to push development of the current design as far as I can to learn more.
Thanks.
Hi Rick,
Sounds good to me.
HI John
Having had FLAs batteries fail I do feel that this sets a higher bar for LifePO4 and hence seems a little prejudiced.
Should your design not be applied to any house bank irrespective of chemistry as all do fail?
Disclosure: I have built a LifePo4 bank. It include monitoring, alarms and integration with Viltron charge sources (MPPT/B2B).
I have had FLAs fail due to cell short circuits resulting in lots of heat and dangerous presumed Hydrogen/Hydrogen Sulphide gassing. One left me with no house bank power whilst sailing which also due to legacy wiring meant I lost VHF and auto Bilge pump. Ie the exact issues you want to avoid.
Although I might be burnt at the stake, I have kept my 1-2-Both Switch but relabelled it as an Emergency combiner. I appreciate this will overheat / burnt out the Alternator if I take no other action, but would allow me to start the engine if the start battery had a low voltage/charge issue.
I have also rewired my loads and banks. I included individual battery switches with fuses so that in the event of a similar event as to the past I can isolate an issue and not lose VHF/Bilge Pumps.
On reflection one issue in my design would suffer from is if the start battery short circuits I would have an issue running the (dum) alternator as it connects to that battery. I think your design might the same issue, but that is a different problem.
Your approach does give food for thought of how to mitigate bank failures so is very much worth while. I might review my design with a list of possible failure modes and their mitigation as I may have some gaps.
Hi Greg,
While I agree that lead acid batteries can fail too—although it has never happened to me in over 40 years of use—I don’t agree that they should be treated the same way at lithium. The difference is lithium can suddenly shut down due to under of over charge, not the case with lead acid. More here:https://www.morganscloud.com/2022/04/25/why-lithium-battery-load-dumps-matter/
Given that, and the fact that lead acid battery banks can be combined safely (with a few exceptions I cover in https://www.morganscloud.com/2022/08/15/how-hard-can-we-charge-our-lead-acid-batteries/) in my view the best backup system for lead acid is the variant I describe here: https://www.morganscloud.com/2022/08/10/choosing-installing-battery-switches/
Further I strongly recommend that you remove the combining function from your system since suddenly connecting a lithium battery to a flat lead-acid one is potentially dangerous and could easily burn out the BMS on the lithium side and possibly even cause an explosion if the BMS does not shut down fast enough and allows a huge current flow from the lithium to lead side. And even if none of that happens, if the lead acid is flat enough not to start the engine, it’s quite likely that the BMS current limit will be exceeded the minute you combine, so the lithium will shut down and not assist in starting the engine anyway.
Hi John
Thanks for the reply.
I understand the concerns around high voltage (or charge) disconnect from LifePO4. Especially drop ins. I believe I have mitigated that in the following ways;
In reference to the dangers of combining a charger LifePO4 bank with a depleted Pb one there are a few things I need to make clear about my setup;
Hi Greg,
Looks like you have taken a lot of good precautions in your design.
That said, I stick by my recommendations above for a bunch of reasons.
For example while the BMS may measure 150 Amps draw from the starter motor, that’s wrong. Only good clamp on peak meters can measure inrush current on starter motors, typically 1000 amps or more, since the duration is typicaly only 300 ms.
Even the starter motor on the tiny yanmar in my J/109 peaks out at 600 amps inrush, according to the manual.
Subjecting sensitive electronics like a BMS to those kinds of loads and spikes is never a good idea and even 600 amps is well over the 50% of capacity max current rule of thumb for most lithium battery banks.
I also still recommend a critical load backup lead battery for all lithium systems that will be used offshore, regardless of how well designed the system is.
I have a simple question as someone who has been in a lot of hazard and operation analysis reviews. Whats the failure rate of lithium iron phosphate batteries vs lead acid?
Hi Cory,
I agree it would be interesting to know, but I can’t see any way that accurate unbiased numbers would ever be compiled. Also a lot depends on usage profile, quality of the battery (both types), quality of the BMS, quality of the installation, and on it goes.
Agreed. While I don’t know either, I struggle with some comments about failure of devices where we don’t know how often they fail and so we have a whole store of backups onboard, yet the failure rate might be 1 in a million and that will simply never justify a backup when something else on boat might fail 1 in 1000, or 100. Also we often don’t take into account double jeopardy where 2 things must fail in parallel to be catastrophic, but it scares us, so we back up the backup when the failure simply has almost no chance of happening .
Hi Cory,
I expect that there are actual numbers somewhere, but I don’t have them. However, as I see it, it’s not a straightforward issue. For one, there are different takes on what constitutes “failure”:
1. The battery has permanently lost its usefulness as a battery. Destroyed. Theoretically, lithium is several times better than lead at this one, but given the abundance of drop-in batteries and incorrect system adaption, reality is most likely that lithium dies far too early more often than lead acid.
2. The battery fails to give power when needed. Either because it’s empty or because it was for some reason disconnected. The lithium chemistry has a far better resilience to heavy use and keeps giving good Voltage and Amps until really deeply discharged. Still, the mentioned prevalence of questionable drop-in batteries and poor system design means that BMS shutoff (overcharge, over current, under voltage, over temperature, etc) probably happens at least (!) twice as often as lead acid goes empty.
My conclusion of this is that lead acid batteries have a dramatically better failure rate than the lithium batteries we currently see on boats. Being a lithium fan boy, I would strongly claim that this is the fault of the market operators only, not at all the chemistry, which arguably is far more reliable than the lead acid chemistry. However, as mentioned here, and as elaborated in several articles on this site: Reliable cell chemistry doesn’t necessarily lead to a reliable system. To get that, we need a really good system design. With that, my opinion is that lithium can be made superior to any lead based battery, also on any definition of “failure rate”.
FWIW, a traditional method of estimating failure rate, or its inverse, the mean time between failures (MTBF), is given in MIL-HDBK-217. Generally, with that type of method, a comparison of the MTBF of similar electronic assemblies, for example, the electronics associated with Pb-acid and Li-ion battery systems, the MTBF is the inverse sum of the component failure rates. This means that typically a system with more components will have a shorter MTBF, and thus a higher failure rate than a system with fewer components. Assuming a BMS is more complicated than the Pb-acid charge regulator suggests that the Li-ion system will have a higher failure rate than a Pb-acid one. Of course this may be mitigated or exacerbated by the pros and cons of the battery chemistries, which MIL-HDBK-217 and similar processes don’t usually consider. But the bottom line is that a Li-ion battery system starts out with a failure-rate handicap compared to a Pb-acid system because Li-ion requires a more complicated electronic system (more components) to operate.
agreed, well said. I believe i am preaching to the choir. With that said, and wanting to avoid a pissing contest, I believe if you are going to condemn the BMS, you have to include all the components in Johns system, including the not only the BMS, but the alternator, chargers, DC-DC, panels, terminations, regulators, mechanical switches, even instruments etc. Someone even mentioned a UPS…..I would guess that 1 BMS of a bank shutting down receiving charge is the least of the worries in the system??
Hello John,
thanks for the article. I using a similar setup since some years although not the same. In short I would say my setup has one disadvantage and 4 advantages. Although I don’t say that the 4 advantages are more weight. Everyone has to answer that for himself. So in short:
I charge Led Acid Batteries with the alternator and use then a DC DC charger to load Lithium batteries. That gives me 100A from a 57HP standard alternator. You get this high ampers only with a DC DC charger. The setup you propose needs either an upgraded Alternator or leads to low energy charging and is anyhow not good for the lithium battery as standard alternators don’t care about Lithium load profiles.
Solar is directly connected to the Lithium house bank.
In case of the Lithium would fail (which never happened in years with full time sailing, but I agree that it could happen), I can switch the starter batteries to use for as house batteries.
I need to do that manually, which means it is not immediately fail over save like yours, but it can be done in 30 seconds, which for my assessment sounds be not perfect, but good enough.
While crossing the atlantic with the ARC I also have to say that from 30 boats 6 had severe issues with their led acid batteries. It didn’t failed totally but the batteries where so beaten down and bad that they had serious issues at night.
For sure that could have been solved before the travel, but next to the correct statement “Lithium Battery setup needs to be carefully designed” it should also be said that “In practical life Led Acid batteries are often run down cause serious issues for many sailors at night”.
Hi Karsten,
Obviously you are happy with your solution, and that’s the main thing.
That said, that’s not the way I would do it, or recommend to others. My thinking is that it is vital that the backup system totally prevents blackouts.
Here’s why: https://www.morganscloud.com/2022/04/25/why-lithium-battery-load-dumps-matter/
I also don’t like backup systems that share the engine start batteries with sensitive electronic gear, see my reasoning in the article above.
Also, my thinking is that all offshore cruising boats will be much better served by changing to a continues duty alternator that is externally regulated and measures amps with the correct profile for the house bank, and that goes double for lithium battery systems:
https://www.morganscloud.com/2013/11/06/10-tips-to-buy-and-install-a-liveaboards-alternator/
https://www.morganscloud.com/2020/07/04/stupid-alternator-regulators-get-smarter-finally/
As to inadequate lead acid systems offshore. Sure, that’s has long been a big problem, but it’s a function of poor system design and installation, not fundamental to lead-acid batteries: https://www.morganscloud.com/2022/03/04/a-simple-efficient-and-inexpensive¹-12-volt-electrical-system/
Using John’s “Seaman Like Lithium Battery” suggestion we (svsagres, wholybee, Goboatingnow and rgleason – 4 sailors who have been involved with Lithium Batteries for awhile) have collaborated and developed a basic diagram for “Small Boat BMS/LFP with Backup” see Post #325 on DIYsolarforum.com which uses a “1-Off-2 Switch” and small automotive relay to provide the functions needed while complying with ABYC. Please note that the “Off” position is “Normal LFP”.
If you have constructive suggestions, please comment.
Hi Frederick,
I tried to take a look, but it won’t let me download the diagram without logging on. You could upload it as an image attached to a comment here, if that works.
Ok John, I can certainly do that. The thread does have details and discussion about the iterative development, which provides the reasons for the choices made, although it is a bit long winded, but the forum is quite worthwhile.
I would be very interested in your thoughts.
Rick
Hi Rick,
I took a look at the design, and it seems fundamentally good, but I don’t have the band width to get into a full analysis or participate in a detailed discussion on the forum, without neglecting my job here at AAC, so I may have missed a problem.
One thing I think I noticed is that the essential loads backup lead acid battery and the started are one in the same, which I generally don’t like. But then I note you are using a DC/DC power supply in there, which is innovative, although it does add another point of failure, particularly since the input will be subjected to brown outs and spikes from the starter motor inrush.
I also noted that you are using a 100 amp fuse on the engine starter, which is probably too small, unless the engine is tiny. I like to see 2/0 cable to the started and a 250 amp fuse, generally. And if memory serves RC Collins agrees.
Anyway, good on you for really thinking this stuff out and using good kit, rather than just jumping in with junk and little understanding, as so many are doing.
It’s also a great illustration of how complex doing a seamanlike lithium battery system right is. Others take note!
Thank you John.
I’ve tried to keep the separation of essential loads really simple and handled manually from the DC Panel simply by switching off the device. The major ones that I would switch off is Refrigeration and Autopilot, and since that leaves mostly essential loads like Nav, Nav Lights, etc the loads get managed. Larger boats would want a more sophisticated arrangement.
I also charge the SLA battery with a DC-DC charger (fed from the LFA batteries normally) from a breaker on the DC Panel, because I want to be able to easily switch it off when we have Manually disconnected the BMS/LFP and turned the 1-Off-2 Switch to SLA Emergency Feed to power the DC Panel. Actually I don’t see how the DC-DC charger “input will be subjected to brown outs and spikes from the starter motor inrush”?
Thanks I will check the 100a fuse and the cable. I have a 3YM30 Yanmar which starts quite readily.
Thanks again.
Rick
Hi Rick,
As far as I can see the panel is fed by a DC/DC power supply off the lead acid bank, and that’s the one I was referring to, not the one that charges the lead acid. But, as I say, I only had a few moments to trace it out, so may have made a mistake.
I too have a small three cylinder yanmar. Check your service manual for the graph of starter draw, it’s a lot, particularly inrush.
PS:
The objectives have been:
1. Simple and reliable BMS/LFP installation for a small boat without much area available for equipment.
2. Compliance with ABYC requirements.
3. Integration of External Regulator and BMS operation with canbus to protect LFP and Alternator.
4. Excellent monitering and control and integration with the BMS.
5. Integrated SLA Emergency Backup which isolates the LFP via a single switch.
John is correct about the starter wiring. “3YM30 Starter 64a min with Max load current 250a and 400CCA load minimum” So the Starter needs 0/2 awg with 250a fuse at the SLA battery 250a.
The dashed red SLA Emergency Feed to the DC Panel and Chargers was fused 100a and sized for emergency condition DC Panel loads.
I now realize now that we have the Alternator also recharging the SLA when the 1-Off-2 switch is on the SLA Emergency position.
The Wakespeed under these emergency conditions (with the BMS dark and unpowered) will just output 13.8 volts. Is it really necessary to increase this wire to 2/0?
Additionally we plan to depower the Alternator to 100-120a in all modes but with the switch in Off “Normal BMS/LFP” mode we have sized the alternator wires for full 160a.
Thanks John for catching this.
Incidentally, in SLA Emergency Mode with no LFP any brownouts and spikes when starting the engine, can be solved by shutdown of all equipment for a brief period, if this is thought to be a problem. At sea, this is definitely a consideration.
Hi Rick,
I think, on balance, I still prefer a separate critical load lead-acid battery, as detailed in the chapter above, particularly given that for most of us a small one will do, say group 31. I also prefer the critical load switch panel to be separate, otherwise, as I read it, the lithium and lead-acid are connected in parallel through the panel, which I don’t like, even though it’s fused. As to wiring from the alternator, that only needs to be sized to the max of the alternator as long as it is also fused at source:
This chapter fully explains fusing, and that particularly, although ABYC is still the standard: https://www.morganscloud.com/2022/03/19/8-checks-to-stop-our-dc-electrical-system-from-burning-our-boat/
Hi Rick,
Took another look and realized I was confused and thought that the line coming from the panel to the DC/DC was feeding the panel, rather than the other way around. Hence my comment about parrelling the banks, which was wrong.
I now understand better what the switch does and how that works to switch to the LA bank.
That said, I would still come at this with the design in the article above that does not require human intervention to bring the critical loads back on line and would make the critical loads bank separate from engine start. Of course that requires a separate critical loads panel, or modifying the existing panel.
All that said, the key point here is that you guys are really thinking this out, rather than just diving in, as so many do.
Our current DC Panel is relatively new, but separating the non-essential loads would be easy (Refrigeration) and putting just that on LFP and increasing the size of the DC-DC and adding another battery start to press existing limited space. However the advantages would be great.
In the current configuration none of the 3 Switch positions parallel the LFP & SLA batteries:
However it has been recently raised point: ABYC “13.7.7 No electrical connections should be made directly to a lithium ion battery that would bypass a BMS or the protection relays.”
LFP Override does bypass the BMS and Protection relays. In the event of an LVD we will need to recharge the LFP and this is the only way to do that, other than carrying around jumper cables and connecting them under duress.
I believe that the same diagnostics and need to charge LFP after and LVD shutdown would also occur, even with the Seamanlike Diagram. This has caused a conundrum in my development of the diagram. What does ABYC really want?
I happen to think that a LFP override is better than trying to wield a set of jumper cables on the high seas, and ABYC apparently does not. I happen to think that context and practicality are more important. Quite obviously, this switch will not be where everyone can get to it, but I don’t know what to do about this problem.
PS: I will post a revised diagram soon.
Updated Diagram.
Hi Rick,
I can’t see why my design above requires bypassing the BMS controls. Surely it’s just a case of putting the BMS controlled over charge relay in the line between the 1-2-both switch and the lithium battery? Anyway, I agree that it is unacceptable to bypass the BMS, ABYC or not.
How would I recover the battery After an LVD (low voltage disconnect) or HVD (high voltage disconnect)?
Without being able to bypass the BMS?
What happens with your design?
In your diagram above, I think you need an interlock and small relay using the Orion Tr on/off terminals to automatically turn off the Orion when you switch batteries, similar to what our diagram shows.
Hi Rick,
Recovery of the BMS is beyond the scope of what this article is about. My intent here is not to provide a full on design with every detail covered, way too many variables for that, but rather to illustrate the concept. You maybe right about the need for switching the Orion, but digging into that is beyond what I can do in the comments.
Bottom line, anyone who is actually going to take on a lithium installation needs to be capable of figuring out these details themselves, or should hire someone who can.
John, I understand your points. I am digging into it. It is a REC BMS we are using in this diagram because it integrates with the Wakespeed WS500 and Victron CerboGX so nicely.
Here is a little further information about ABYC since these so called “standards” do not exist in the public realm and a friend has clued me into one of the statements. Regarding my diagram and the 1-Off-2 Switch diagrammed there:
“OFF LFP Normal” complies with ABYC 13.7.7 and does not bypass the relay.
LFP/BMS Bypass Override for LVD & HVD Recovery is a manual override “on extremis” and allowed by:
“ABYC13.5.3 Consideration should be given to providing alternative power for critical systems (e.g., engine starting, navigation lights, etc) if a BMS shuts down the battery.”
For example, in the unlikely event LVD occurs I don’t want to be using a jumper cable at sea alone on a dark night to recovery charge with the Alternator after an LVD. A similar situation applies to HVD.
The switch will not be readily accessible to most users, but will be in the engine compartment. It may require a key.
Your diagram and use of the SLA Battery for essential loads solves several problems, but I believe you will need to solve the same problem after BMS shutdowns.
However this boat is small enough so the only thing that would be moved to the LFP would be refrigeration, which really doesn’t use LFP to its full potential, and requires a larger DC-DC charger for the additional essential SLA loads. Given the choices think I would prefer to have an accesible but hidden switch to change to SLA Emergency Battery quickly. It is a different situation.
I will stop bugging you about this, as this is conceptual, but not really on topic. Thanks for your interest.
Rick
Hi Rick,
If you are going to carry on with this, I strongly suggest you join ABYC so you can read the standards, flawed as some of them are. The cost of their non industry membership is trivial in comparison to the cost of the lithium system you are planning.
Sorry, but I am an Architect and don’t have that kind of money to spend.
This is a trial on paper. I am going to see where it goes. Also I have the benefit of an EE who is reviewing the diagrams and has been there all along the way.
Hi Frederick,
I don’t know the specifics of the Orion BMS, but I also think it’s unacceptable if it needs to be bypassed in case of a LVD (Low Voltage Disconnect). Are you certain that this is actually the case? Doesn’t it differentiate between LVD and HVD? If not, wouldn’t it just reconnect the cells when it sensed that a charge source is present? I know some BMS do that. Orion is a well known brand, so I’d assume they’re aware of these issues? None of this is difficult.
My main issue is: I’d absolutely not accept that a BMS disconnects both incoming charge and outgoing consumption simultaneously. In my opinion, it’s only allowed to disconnect from the actual problem. The Voltage is either too low or too high. It can’t possibly be both. If the one situation is detected, the opposite one urgently needs to get active, not disconnected!
Same with Amps and temperature. Having only one possible reaction, no matter what the problem might be, is an unacceptable behaviour. This is one of several reasons I dislike most “drop-in batteries” so much. It’s also possible to build a less moronic drop-in, but that’s just not normally the case. They’re usually made to rip off customers, not to be good products.
Well actually, I believe ABYC requires that . on failure the LFP be disconnected completely, after an advance visual and audible alarm.
Initially I drew a dual bus arrangement thinking that chargers could be shutdown on HVD and DC Loads could be shutdown on LVD. The REC BMS has relay circuits for both Charger and Dis-chargers, but I was advised that both buses must be shut down to comply with ABYC, so I have redrawn and tried to simplify accordingly.
We will just not use the discharge relay circuit on REC BMS.
REC BMS is a very reliable and good BMS, it is just ABYC “standard” that is in the way here.
Hi Frederick,
REC BMSes I know a bit more about, and yes, they are indeed intended to operate the charge bus shutoff separately and independently from the load bus shutoff, which is the only acceptable option.
I don’t know the ABYC recommendations more than what I gather here and there, but if they do indeed require that both are by default disconnected simultaneously if anything is triggered, I will have to conclude that their recommendation is incompetent and must be disregarded.
I know for a fact that several of the members of the relevant ABYC committee are extremely competent, like RC Collins. However, there are also members with a commercial interest, like vendors of drop-in batteries. They would perhaps be motivated to push for recommendations that don’t discredit their own less able products.
I really don’t know if this is indeed an ABYC recommendation. If it is, it promotes a setup that, in addition to being a practicality nuisance, can become quite dangerous. It creates totally unnecessary risks of sudden blackout, similar to what we risk with the deaf and blind drop-in batteries. Unacceptable. Such a recommendation must absolutely NOT be followed.
I do not have access to ABYC however I have been working with some EE with access. I expect that this is an evolving standard, and eventually I may be revising the diagram to a dual bus.
You wrote:
“I will have to conclude that their recommendation is incompetent and must be disregarded.”
I don’t think you should conclude that!
SK-1 update
SK-2 update
Hi Rick and Stein,
I’m with Stein on this one. I would definitely want to two busses independently controlled and I would not install a BMS that had to be shorted out to reset after a dump. I have not done detailed research into BMSs but I would bet large sums that the good BMSs from companies like Victron and Lithionics have a better way to reset.
And if I’m wrong about that, then it makes my backup design detailed above that much more necessary since it will keep everything going, including charging the lead-acid backup, for as long as it takes to get the lithium back on line.
John,
I did not say I was against having a dual bus! You have misrepresented what I wrote. ABYC requires that the LFP be shutdown on a problem.
As far as restarting a failed BMS/LFP, which is hopefully a rare event, I will let you find out.
The type of BMS you are asking for is rare, please let us know when you find it.
Rick
Hi Rick,
I’m not at all sure that ABYC requires a total shutdown, rather than single buss disconnect, but I will check. That said, if it does, I would agree with Stein on why that might be, and therefore discount it.
It will also be interesting to check on waking up a BMS after a shutdown. I hear you that a lot of the less expensive ones require this, but I will be surprised if a company like Victron would put something out there that requires a dangerous activity like shorting a BMS out to reset it…but then I have been surprised before.
I am going to check with REC BMS about it’s operation after a failure and if there actually is a setting to shut down the charge relay in all failure events, since they also support a discharge relay.
I will also ask REC about that part of ABYC requiring a total shutdown.
Hi Rick,
Just to be clear, I did not misrepresent you, although I could easily have misunderstood you. Misrepresent implies malicious intent, which is not the case. Please keep in mind that I don’t have hours to put into this, since so doing would take away from other writing projects, so it’s perfectly possible that I would misunderstand something. You will also note that all of my comments have been about what I prefer and would do, rather than denigrating your design. This is in keeping with our comment guidelines: https://www.morganscloud.com/2013/11/10/aac-comment-guide-lines/
Sorry, perhaps misinterpret is a better word to use?
Hi Rick,
That works.
I wish ABYC E-13 was public, as I spent some time this afternoon trying to collect what I knew about its “standards” which is here.
“The key point both under ABYC and ISO is the presence of a BMS , a complete disconnection of the Battery from both loads and charge sources , and advance warning of such an action.”
So dual bus is acceptable, but ABYC still requires complete disconnection of the Battery from both loads and charge sources upon a failure, as I understand it.
I note that Bruce Schwab, who prefers dual bus configurations, hopes that ABYC will evolve to support separate shutdown of the charge bus and discharge bus.
Hi Rick,
I’m sure he does, me too!
Just read the standard and you are right:
13.7.2.1A BMS shall respond to any conditions outside the SOE by activating the output disconnect device.
My guess is that this is probably the result of poor drafting, rather than intended. The problem, of course, is the word output.
Just another way in which ABYC E13 is, in my view, deeply flawed.
All the said, if it were me I would consider installing an all Victron or Lithionics system with duel busses and then hide behind:
13.6.1.2 No electrical connections shall be made directly to a battery that would bypass a BMS or any battery protection circuits. EXCEPTION: Connections made specifically per the battery manufacturer’s instructions.
(As I remember Victron manuals for their higher end BMSs show duel busses, so I would file that and feel comfortable.
Anyway, I’m 100% with Stein on this, in my view, compelling the BMS to dump the loads just because of an overcharge does not increase safety, it decreases it since load dumps are dangerous in and of themselves and overcharge is the most likely scenario to cause a disconnect.
I actually agree, but am trying to keep it really simple and follow ABYC requirements. REC BMS Active supports dual bus and several additional relays and integrates well with WS500 and CerboGX via VE.CAN and Canbus. So what would it cost for dual bus? Another relay?
Although it increases cost somewhat there are many advantages to a dual bus that works as one would expect,
A. Disconnecting the charge bus on HVE , B. Disconnecting the discharge or load bus on LVE.
The lights won’t go out on “A” as the loads reduce the battery SOC, and the alternator and chargers remain connected to recharge the LFP.
Also I am planning a rather small LFP 240-300ah, not having the additional small load of the NO relay does help, although our 100w solar would help, when we aren’t on board and on the mooring.
Thank you for checking.
Best
Rick
John,
I know you are tired of wiring and electrical, but I thought I would pass on several comments about your diagram which may be worthy of consideration (from someone I respect). Just intended to help improve your diagram. I appreciate your comments on mine.
Since the assumption is the bms in integral in the battery. There’s
(A) no manual emergency override of the bms. Personally I would want that.
(B) if you add an external bms and its cutoff you are back to your original two manual switch option and and you have the issue that you can now inadvertently parallel the batteries.
(c) no means of charging the SLA.
Hi Rick,
We are back at trying to judge a block diagram drawn to illustrate a single concept as a schematic. The two are different and my diagram is the former. For example, no where does it say that the BMS is integral to the battery. In fact I’m on record over and over again advocating against that.
And the other issues you friend brings up can all be dealt with without compromising the the point that the diagram was meant to illustrate.
Let’s move on from this misconception about what my diagrams are, please, particularly since they are all clearly marked as not being schematics.
Agreed, I run into the same problems. I had “Draft” on it, but took that off. Perhaps I should put “Conceptual” because it is being revised often.
Here is the most recent version dated 10-04-2022. I think it is 99% there but is is labeled “Conceptual”
Here is the second sheet SK-2
Please note that the use of a 3 way switch in the diagram above, has a very different use than what John is referring to above. See the description please.
Hi John
I’m looking to upgrade my drop in
lithium setup. After discussing options with friends and reading your articles,I,m leaning towards the Pylontech RT12100G31.
Do you have any thoughts on these batteries?
Thanks & regards Murray
Hi Murray,
I don’t have any experience with that battery, so don’t have an opinion on it, but generally I recommend buying a system from the likes of Victron, Mastervolt, or Lithionics including both batteries and BMS. That way if there are any issues you only have to deal with one company, and they can’t wiggle off the hook by blaming another manufacturer.
It looks like that Drop in LFP has a CANbus and external communication and may support a signal for advance disconnect of the alternator via a set of contacts.
“Communication CAN, RS485, BlueTooth, Dry Contact enable data transmission to meet the needs of different usage scenarios.”
They also mention compatibility with chargers and generators. It is worthwhile checking if the Wakespeed WS500 is compatible and operates properly with this BMS and what the settings are.
Since it is IP67 and compatible with the CerboGX it is very likely a reasonable choice that works with Wakespeed WS500, but check. Also don’t locate it in hot/warm areas like alongside the engine compartment as that will degrade the LFP.
Hi Frederick,
Thanks for researching that, and the fill.
Thanks.
Later I found it does not have adequate charging capacity for a good sized alternator, perhaps ok for solar charging.
John
I have a Victron LI system and am installing separate AGMs forward to run the bow thruster and windless, does it make any sense to use those AGMs as backup? Or is that too complicated.
Thanks
Hi Leo,
That’s an interesting thought, but probably not the best way for the same reason that I don’t recommend using the starter battery: surges and brown outs from the very heavy motors in the windlass, and particularly the bow thruster, that are not good for the sensitive electronics that would be on the essentials panel.
Hi Leo and John,
I agree with John, but perhaps the option is still viable. Starting the engine is an essential safety function. That makes the start battery not suitable as a backup battery. On the other hand, in a situation when we need a backup battery to run essential systems, I would see zero problem if the windlass and the bow thruster could not be used.
That means this battery bank could be a good backup battery, as long as we can make sure the two items cannot accidentally be used while that battery is in use as emergency backup. A bistable relay per unit, triggered when the emergency circuit has power, and reconnecting when the normal power system is powered, would do the job automatically.
The relays can be small and cheap low power versions, as they only need to disconnect the control power, not the high power cables. The relays would not consume any power in either position, and would also not cause voltage drop or power loss, except for a theoretical minute amount in the control circuits just when a signal is passed.
The relays and cables needed should have a combined cost of perhaps 20 Euro / Dollar and install should be doable in minutes. We all know what that means…. 😀 We have no bow battery, so I haven’t done this. Also, I’m no electrical engineer. There might be issues I haven’t thought about….?
Hi Stein
That’s a great idea, thanks. Might indeed make this viable.
Hi John,
I hope this is the right place for this comment regarding an example of a sailing boat experiencing “a complete blackout” mid-ocean due to battery failure, and then a fire that forced immediate abandonment. I’ll stick my neck out and speculate that the fire aboard Fabrice Amedeo’s IMOCA 60 Nexans – Art et Fenêtres during the Route du Rhom, that eventually forced Amedeo to escape on a liferaft, was due to Li-ion battery failure and delayed thermal run away. A lead-acid backup system may’ve helped, but I don’t see how anything short of jettisoning the smoking batteries between their reactions to the ballast water that flooded the cabin could’ve prevented the need to abandon the boat. It’d be informative to know more about the electrical system and battery type on Nexans; perhaps they were exotic batteries that are unlikely to be on a cruising boat. His description of an “explosion” suggests that the batteries were not Li-iron-phosphate (LFP) but that’s a guess.
Here are excerpts from Amedeo’s account of the disaster and his harrowing escape:
“Sunday morning: everything is fine on board and I’m having a great race. The boat is flying hard in the squalls and the sea is heavy. Suddenly, I realise that my ballast has exploded on a wave and that I have several hundred litres of water in the boat. I stop to be safe and start to empty everything.
“At that moment, the batteries are immediately affected by the water and failed and I had a complete blackout on board. I have no more electricity: no more autopilot, no more computer, no more electronics. I decide, in consultation with my team, to proceed cautiously towards Cascais.
“Sunday afternoon: big smoke on board the boat. I use the extinguisher, I put on my TPS (survival suit). I alert the race direction who asks a competitor in IMOCA to divert to assist me if necessary. The smoke eventually stops. I decide to resume my passage to Cascais….
“Again 2h30 of siesta then 7 hours on the helm. Shortly after 1230 pm more new smoke on board. Followed by an explosion. I grope my way back into the cabin and manage to retrieve my TPS. My Grab bag (survival bag) had remained in the cockpit. I’m going back to get my wedding ring. I hit the fire extinguisher but nothing happens. The smoke is not white like yesterday but yellow. The cockpit warps and yellows. Seawater spray sounds like the sound of water hitting a saucepan. I understand that I will have to evacuate. I warn my team of a possible evacuation.
“When I hang up, I am then at the back of the boat ready to trigger my survival: a torrent of flame comes out of the cabin and the coachroof. I am caught in the middle of the flames. I can’t even open my eyes. I manage to push the life raft into the water and jump….
Steve
Hi Steve,
I’ve also been interested in getting more info about the details of this event. Since I have no more than you also found, I can only speculate, but FWIW my thoughts on it:
– The battery problem most likely was the result of water shorting out a major circuit, not the battery bank itself. Modern lithium cells can give enormous currents, able to sustain an arc over a considerable distance, once it’s been started. Like a small lightening, or a welding arc. That means no actual touch between conducting materials is needed. Huge current creates it’s own plasma to conduct it.
Digression 1: That’s why we need different types of fuses, with bigger gaps, for really powerful battery banks. And water protection.
Digression 2: The enormous current capacity means that lithium cells are waaaay better at starting engines than any type of lead battery. The cheapo electronics in drop-in batteries can’t handle that current. The cells can. That’s the origin of the misinformation that lithium isn’t good for starting. A correctly designed lithium battery, separate cells and external BMS etc, can start any engine and run any thruster or windlass, simultaneously, while yawning. 🙂
– Such a short circuit starts massive currents that can overload both the cables and the cells or control systems, causing power loss and smoke from overheating.
– The word “explosion” makes me think this was probably not LiFePo4 / LFP cells but more likely Lithium Manganese or such, like in phones and laptops. They have significantly more energy stored in less space and weight, but are also far more sensitive to damages. They may in some cases enter a thermal runaway from as low as 90 Celsius. LFP cells need perhaps 250 C, usually more, to start that, but subjected to a dead short will also create (very) poisonous smoke and will eventually get really hot. Explosions are close to impossible, but lots of water hitting a burning hot battery might seem like an explosion?
– My initial reaction to his response to the problem is that he seems to have not tried to find the short that caused the blackout. He just bailed and wiped up the water he could see and then hoped the electric problem was stabilised. Probably not a complete description, of course. However, if it’s relatively correct, this is really poor crisis handling. The sailor needs to know how such a system is built, how to interpret each element and how to act in different scenarios. Missing this ability on a cruiser is not good, but understandable. On a professional long distance solo extreme racing boat like this, it’s unacceptable.
On the 20/20 rear vision besserwisser side of things, where I’m highly skilled. 🙂 What would I have wished to have (different?) if I was in that boat?
– Knowing that it’s a very wet boat, I’d have wished for a completely sealed electric system. Where any part can be flooded without issues.
– Especially if going for a more sensitive battery type, I’d wish for a fire retarding case, an easy option for quick disconnect, and if not enough, a quick procedure to dump the cell case. These batteries are extremely light for their capacity, so hand power is definitely enough, as long as the person is protected from the heat and smoke.
– A small simple emergency battery and a prepared system to limp home.
Hi Stein,
I agree with everything you say—my guess is a short too—except that lithium batteries are appropriate for starting engines. Check the specs, but I think you will find that few BMSs and few lithium batteries can handle the inrush spike from even a modest diesel engine starter motor. For example the max inrush on the starter motor on my sewing machine sized 30 hp yanmar is an eye popping 600 amps! That’s more than the max on all but the largest of Victron’s lithium batteries, and this is a tiny engine. Now admittedly Victron rate for continues discharge current, but even so I can’t see that it would be a good idea to exceed that every time we start the engine, even as a short duration spike.
I could be wrong, but I think if you call Victron, they will caution you not to use lithium batteries for starter loads on diesel engines.
And anyway, why do that when lead acid do such a great job for starting engines and are way cheaper?
Hi John,
I forgot to answer the start inrush current comment:
Victrons lithium batteries have Winston prismatic cells inside the box. Arguably the best cells on the market. Often there’s also some electronics, depending on the configuration, but usually no internal BMS. The limits on current capacity given by Victron comes from wanting to be conservative to avoid complaints, but even more from the electronics, definitely not the cells. Victron can also supply batteries that don’t limit the cells. This is done by not running the current through the electronics at all, just measuring it and using big relays etc to control it. Also keeping the cells inside a box reduces the cooling ability, which is needed if we want to push the cells to their max, which we normally shouldn’t, of course.
Thunder Sky Winston 200 Ah 3,2V cell:
4 cells like this one will give us a nominal 200 Ah 12V bank. It has a ca 220 Ah actual capacity and mostly operates just above 13V. 12,8 can be considered “empty”. Such a bank will be equivalent in available stored energy to a lead acid bank of 350-600 Ah, depending on what parameter we look at.
The data sheet gives optimal discharge current 0,5C, where “C” is cell Capacity. 200 Ah x 0,5 = 100 Amp. That’s a discharge it can run from full to empty without any consequence whatsoever and with very little Voltage sag most of the way. No similar size lead acid battery can handle even a quarter of that.
Next we can look at maximum discharge current, which is what the cell can deliver continuously for 15 minutes. That’s 3C, which is 600 Amp. That means the 200 Ah bank can handle the momentary inrush current you mention for 15 minutes, nonstop. Again, in a different solar system than any lead acid battery.
Next we can look at the max peak discharge current, which the cell can deliver max 5 seconds for each 1 minute. 10C, which is 2000 Amp. Iv’e seen another sheet mentioning an actual inrush capacity, half a second, of up to 5000 Amp. (Would need some impressive cables!) All this is without causing any damage to the cell. Way higher Amps have been demonstrated. That means the mentioned 4 cell, 12V, 200 Ah, 32 kilo/60 pound bank can start pretty much any motor on any cruising boat, approaching superyacht sizes.
If anyone would like to go really extreme on Amps, both in and out, LTO, Lithium Titanate cells, have current capacities that blow the above discussed LFP, LiFePo4, Lithium Ferro Phosphate, cells off the water, are even far more safe, and will last for decades. However, they have other disadvantages that make LFP still easily the best choice among lithium chemistries for boat use.
Side note:
As we have the data sheet, it’s worth noticing that this 200 Ah cell has an optimum charge current of 0,5 C / 100 Amps, and a max of 3C / 600 Amps, which means if we have the power available, we can take it from totally empty to 100% full in 2 hours or in extreme cases in 20 minutes. The charging is mostly (or only) “bulk stage”, full speed, no slow saturation charge needed. Also, sulphatation doesn’t exist. They prefer partial charge use, exactly as we do in boats.
Conclusion:
LFP cells are way ahead of any lead acid cells when it comes to starting anything, and current capacity in general. A boat with a LFP bank will not be current limited by the cells, but often is by a poorly designed setup of the electronics controlling the system. Drop-in batteries are the worst in this respect. Most discrete systems, DIY or not, have zero such issues. The electronics don’t carry the current. They measure it, and use big relays etc to control it. In real life, normal cruising boats have no need for the max Amps of LFP cells.
On the contrary, their immense power capacity constitutes a danger in itself. If there is a short somewhere, the circuit should be broken by the fuse. However, most fuses used on boats have too small air gaps when breaking to off position. If the short is big, the huge Amp capacity of lithium can bridge the fuse gap with an arc as it opens. A small continuous lightening. The same as having no fuse, plus in seconds you now also have a red hot fuse you can’t trip. Not good!
It’s not difficult to solve this problem, but it has to be dealt with. Lithium needs to be treated as a part of the whole boat electric system. Every single object in the system must be evaluated for suitability. Normally going to lithium should mean a total rebuild of everything connected. Drop-in battery sellers are trying to tell us we don’t need that. They’re right in a way, but at which costs?
Hi Stein,
I think we are getting a long way into the weeds here. To me the bottom line is simple.
If a reputable lithium battery vendor tells a customer that their entire system is capable of starting a given engine, then fine, do that if you really want to.
If not, use lead acid.
Anyway, we should always have a separate start battery, so unless we are incredibly weight sensitive, lead acid is just more cost effective, and probably more robust, in that function.
Point being that even cheap consumer lead acids as starter batteries last a very long time because they are not left in partial state of charge, so I see no reason to add the complications and expense of lithium start batteries, particularly if the vendor does not sanction that use.
Hi John,
I agree that I’m risking weed in the propeller here. 🙂 Just have to answer your point about vendor support:
Winston is a very reputable brand, much bigger than the high end market leaders Victron, Mastervolt and Lithionics combined, who all use Winston cells in their best solutions. There are several reputable large volume resellers of separate Winston cells. The main one in Europe is where I found the spec sheet discussed above, which clearly says that starting an engine is a walk in the park. We can all buy Winston cells and suitable systems from them and various other big reliable suppliers who will stand behind this claim. It’s not experimental, and DIY isn’t necessary anymore.
The whole point of this and the above is that I felt it necessary to correct the statement that lithium battery systems are not able to start engines. Even though it’s just not true, it’s been said so often everywhere that it’s become a “fact”. It originates from most “drop-in” lithium batteries. The vast majority of those do have a low max current, and other issues. The reason, however, is not related to the word lithium. 100% comes from shortcuts in the pack design and electronics. They also mostly use far inferior cells.
Bottom line is that we get to about the same conclusions, albeit with varying details on the way there. My point wasn’t to promote lithium start batteries. On most boats that’s a silly idea. I also agree that lithium is quite often not the best answer, even for a house bank on a boat. Lead acid is a better choice for most, unless they regularly spend long periods with solar etc as their main power source, or generally use a lot of power. If either of those, lithium is a must.
Hi Stein,
I agree with most of that, except that those with solar necessarily have to go with lithium. We have a very interesting article coming from an engineer with deep experience in the field showing that solar can work very well with lead-acid and in fact makes lead-acid systems more functional and long lasting. As usual the variable here is usage profile.
Thanks Stein for your thorough description of LFP game changing capabilities. Ideally development and use of LFP/BMS will become “normal” and background, enabling us to sail with greater comfort and safety.
Hi Steve,
Yes, I read that, but I’m not ready to jump to the conclusion of blaming lithium batteries. First off, as you say, we don’t know what lithium chemistry the boat was using. Maybe they were using more volatile lithium batteries than the ones used on cruising boats (Lithium Iron Phosphate) which I think are, when from a reputable manufacturer, pretty much as safe from fire as lead acid—ABYC just spent a huge amount of time trying to get LFP to burn and had no luck. They even set an old test boat on fire with the LFP batteries aboard and got no explosion.
Also, regardless of battery tech, this could have been a bunch of other things including a short to the carbon hull. My friend Stan Honey had exactly this happen to him on a Volvo boat and the results were spectacular, including a lot of toxic smoke, although in the end not fatal to the boat, but a lot of that happy outcome was the result of having Stan there to figure out what happened and fix it.
So, in summary, I don’t think this incident has any bearing on whether or not we have a lead acid backup.
John and Stein,
Your replies are very interesting, thank you. No argument that the batteries were likely not LFP, and that the root cause of the accident may have little to do with cruising boats. Except that: I think the sudden blackout reported supports the case for having a lead-acid battery backup system like what you both have advocated.
What made me speculate that a battery failure was the main culprit, rather than a short, was the several hour delay between the initial blackout and brief smoke emissions, and then later the final catastrophic fire event which forced immediate abandonment. A delay between insult to certain li-ion batteries and eventual thermal run away is a well-known ‘feature’ of Li-ion batteries which is presenting firefighters with new challenges (to put it mildly). In this scenario, the insult may have been the flooding from the burst ballast tank, and/or the mechanical shock that caused the ballast tank to fail.
Anyway, all that said, I agree that there isn’t enough info available yet to make a conclusion with reasonable confidence. Perhaps more details will become public soon. In the meantime, I remain comfortable with my plan to continue to use Lifeline AGMs!
John, what are your thoughts on this product: https://www.bos-ag.com/products/le300/
Although expensive for it’s size you can parallel them for more power and it might be an option for someone who wants to extend the life of their Lead batteries without fully committing to Lithium.
Richard
Hi Richard,
I don’t know enough about this product to give a proper judgement, but it is possible to make a system like they describe and make it do what they claim. However, it does need some electronics and software and relies completely on those never failing. If either does fail, the LA or LFP or both will most likely die quite fast.
My conclusion is, as you probably guessed, that this might give a pretty good boost to the performance of the battery bank, while at the same time increasing its complexity and vulnerability. It also doesn’t properly exploit all the benefits of lithium. If it’s much cheaper than a discrete system with separate 3,2V cells and external electronics, it might be interesting. The cylindrical cells rather than bigger “prismatic” cells indicate low price. BUT: It’s probably not cheaper, no matter how we calculate it, as this is aimed at the DIY retail market.
Hi Richard,
I have been asked about that product several times before, and can certainly see why the idea is so seductive, but I don’t think it’s a good idea on a fundamentals basis. In fact just this question was a lot of the inspiration for the article we published yesterday: https://www.morganscloud.com/2023/01/10/a-simple-way-to-decide-between-lithium-or-lead-batteries-for-a-cruising-boat/
Hi, This is a long comment that I wrote in article form in order to organize my thoughts. I’ve been researching and pondering the LFP vs AGM decision for about a year now and this is what I’ve come up with as a solution for our boat, which we live on full time, cruise extensively (Norway last summer, Newfoundland this summer) and practically never plug in to shorepower. Thanks for any thoughts.
Lithium (LFP) Battery Top Up Charge Source for AGM house Bank
SV Helacious Energy System Primary Components
House Bank: Currently 5 x 116AH Firefly Carbon Foam AGM (580AH Total)
To be replaced with:
5x 12v Victron SuperCycle 170AH AGM, connected 5P=850Ah total capacity
Charge sources:
Victron Multiplus 120A/12v/60 inverter charger primarily powered by 9kw Kubota Beta diesel genset
760w solar panels via 5x Victron Blue Solar 75/15 MPPT controllers
Marine Kinetix Wind generator
150A Balmar Series 6 main engine second alternator, derated to 120A
Additional Available charge sources:
Victron Skylla 70A /12v charger currently running off AC2 Out of the Multiplus
Primary Engine Alternator 80A, currently only charging the Engine Start battery (an Optima Blue top AGM)
How to Keep a large AGM battery bank healthier
The idea is to try to assist the AGM bank to get to100% more often than it would under typical higher latitude cruising conditions. In our experience, we are able to bring our current Firefly carbon foam batteries to 100% about every 3-4 days in the cloudy higher latitudes and only then when we motor for more than about 3 hours. Typically we only run the genset in the morning for an hour or so while making tea and coffee with the electric kettle and may use the induction hotplate to cook breakfast. We might make RO water for 1 to1-1/2 hours, and the electric heating system (a component of the air conditioner but not a reverse cycle) is running, all good loads for the 9kw genset. This will bring the battery bank from an overnight status of 70-80% (depending on the windgen production) up to around 92%. That last 8% , the end of the absorption phase, takes another 3 hours of generator or engine time. We never run the generator that long. We will be picking up our new Victron SuperCycle AGMs next month in Halifax.
LFP Complexity Issues
Why did we not opt for a LiFePo4 battery bank? I have determined that relying solely on a LFP House Bank and its myriad relays and IC circuit controllers for offshore passage making is too risky due to the possibility of a Load Dump (due to over/undervoltage of unbalanced cell) or system shutdown due to equipment failure such as a BMS relay. Helacious really is an electric boat, what with the 2 chartplotters, electric autopilot, satellite system, fridge and freezer, etc. We must safely and reliably feed the beast. A full LFP system is expensive and fragile. One mistake and the smoke can easily escape. When I look at some of the complex LFP system wiring diagrams on, for example, the Victron website, I am amazed at the number of components, failure of any one of which can cause the shutdown of the entire DC electrical system.
AGM Charge Issues
The problem with AGM lead acid batteries is their susceptibility to sulfation due to PSOC operation. The slow Absorption charge curve is the Achilles heel of an FLA bank, especially on a sailboat. High latitude cruising often means light wind and cloudy or foggy conditions, making daily full recharge difficult without extended fossil fuel consumption. Newer AGM chemistries (Firefly Carbon Foam, Victron Super Cycle)can mitigate the sulfation issue, but the slow charge curve for the final 10% of the cycle remains.
High rate of charge is not required for the end of the Absorption phase, time is the key, but this generally means extended low load engine or generator operation, especially in locales where the sun doesn’t shine often.
A Possible Solution
One solution to the Load Dump issue proposed by John on AAC is to have a single AGM battery running the critical systems, with non-critical systems run off a larger LFP bank. The AGM is constantly charged via B2B charger from the LFP bank, with the LFP bank receiving the energy produced by wind, solar, genset and alternator. The system capacity comes from the expensive larger LFP bank, with its attendant complex and expensive BMS and relays. Alternators may be damaged in the event of a load dump, and there is a chance of a voltage spike damaging electronics should the BMS shut down the Charge In relay unexpectedly. There are apparently new devices on the market that may mitigate this potential for alternator damage. Again, more complexity with the risk that their failure could cause cascading damage issues. Installation of a split system like this wold require separating the main DC buses and significant rewiring of the DC the distribution panel. Expensive and complex without redundancy.
Reverse Thinking
Why not flip this idea on its head and have the LFP provide a manually initiated “Top Up” to the AGM bank? Could we use a 200AH (?) LFP with simple built-in BMS (a so-called drop-in LFP) to provide a charge source for topping up the larger AGM bank and providing the electrons for the final stages of the Absorption cycle? A Reserve Tank, if you will.
Most sunny days, in normal use, the AGM bank would get charged fully by the solar, or nearly so. But when needed, such as near dawn on a downwind run in the trades, when the autopilot has been working hard all night and the wind generator isn’t producing much if anything, having the extra 160 available amp hours (200AH x .8 usable) would be highly advantageous. Two separate programmable Sterling Battery to Battery (B2B) Chargers (https://sterling-power.com/collections/battery-to-battery-chargers) would provide the charge sources. The first being between the LFP Top Up bank and charging the AGM House bank. The second charger is between the engine starting battery (and its 80A Engine alternator #1 currently underutilized in its role of merely recharging the start battery) and the LFP bank. According to Sterling their B@B charger can be connected to the start battery but with the initiation voltage set high enough that the charger only operates when the alternator is running. No “smart” regulator is required on this engine alternator.
The existing Victron Skylla 70A/12v charger could also be connected to the LFP charge bus providing LFP charging when the genset is running: the AGM House bank charged by the Multiplus at 120A and the LFP Backup bank charged by the Skylla at 70A. Note: It may be advantageous to install a second Skylla for charging the LFP bank and use the original Skylla in parallel with the Multiplus to charge the large 850AH Super Cycle AGM bank. There is plenty of available AC power from the 9kw genset.
The LFP Top Up Bank would be independent from the AGM house bank. No equipment would be connected to it other than the two Sterling chargers and the Skylla. Thus, if the BMS on the LFP battery were to shut down charging or discharging, there would be no effect, as the B2B chargers are designed for this-they simply go dormant. In effect, they are the buffers in the system. Indeed, I think we could use the BMS high voltage shutdown to end charging at a certain voltage, although I am confident that the B2B charger can be programmed to end absorption and stop charging at a certain voltage set-point as well.
A second inexpensive Victron BMV 702 with shunt could be installed on the LFP DC- cable to monitor the LFP Bank, although it looks like most drop-in LFP batteries now have some sort of BT monitoring built in.
Problems:
One problem with this idea is that the LFP battery only gets charged by either the Engine alternator or the Genset, never by solar or wind. So it would not always be fully charged. Since no damage will occur to a partially charged LFP battery one could treat the situation as if it were a partially filled petrol can-fill it up when you get the opportunity. Use of the LFP battery to top up the AGM bank would be a manually initiated option. I suppose it would be easy enough to dedicate one solar panel and it’s MPPT controller to the LFP battery if determined to be useful. But there is an efficiency loss each time the electrons are moved from one place to another.
I am looking for other potential problems and flaws with my thinking. What am I overlooking? I think LFP batteries are amazing energy storage devices and I want to leverage the technology. I’m just not willing to risk my vessel and potentially my life on them.
Thanks again,
Brian on Helacious
Hi Brian,
It’s an interesting idea, but to be honest, I think you are making this more complex than it needs to be. Yes, AGM’s can sulphate, but that’s quite manageable, even without solar, and easy to manage with solar. On our McCurdy and Rhodes we got 1500 cycles out of lifeline AGMs and that was with no solar and in the high to mid latitudes. And we never ran the generator after charge tailed off. With that much solar, you should have no problems at all keeping AGM’s healthy.
More here: https://www.morganscloud.com/2010/08/02/agm-battery-test-part-1/
So, in my view, either keep it simple with AGM or go lithium with a small backup. More on how to decide: https://www.morganscloud.com/2023/01/10/a-simple-way-to-decide-between-lithium-or-lead-batteries-for-a-cruising-boat/
By the way, Victron Super Cycle are not primarily designed to resist sulphating. That’s their carbon foam option, but the problem with those is low energy density.
Anyway, if you are currently fully charging your AGMs every few days, you really don’t have a problem to fix. That an occasional equalization should give you a >1000 cycle life. If not, it probably means your bank size is too small to match your needs.
Anyway, first thing to do is take a step back determine if your battery bank matches your loads: https://www.morganscloud.com/2019/01/23/cruising-boat-electrical-system-design-part-3-specifying-optimal-battery-bank-size/
Once you have done that you will be in a position to decide if you need a larger bank, and then if so, whether or not that needs to be lithium which depends on how much space you have and how much weight you are willing to carry.
Thanks for the thoughts, John. If available I would replace our current five 4 year-old Firefly AGMs in a heartbeat-with 7 of them. They are definitely not as energy dense. The Firefly specs say 116AH for a G31 footprint and the SuperCycles come in at 170AH for the same footprint and 1 inch taller.(both rated at the 20 hour rate). We definitely run low on energy on overnight downwind passages, especially when the seas are up and the AP is working hard, thus my desire to increase capacity. But, with increased capacity comes a lengthened charge time. I am definitely going with the SuperCycles at this point, they’re already at the chandlers in Halifax. We’ll have a good opportunity to test the new bank this fall and decide whether I need to implement this Top Up project before heading south to the Caribbean in November. It may be that the extra capacity in the AGM house bank is all I need.
In any event, does it seem reasonable to use the available energy from our original 80A Balmar alternator via a B2B charger from the start battery to charge the house bank? Currently all that alternator does is recharge the start battery, which typically has been engaged for 1.2 seconds to start the Beta 60. There is a second Balmar 150 (derated to 120A) dedicated to the house bank. I understand that I can charge the Supercycles at .2C, so paralleling the current 120 amps from the #2 Alternator with a 40A Sterling B2B charger from the #1 might speed things along. This would place the charge rate at approx.160Amax (850Ax.2=170A) The Sterling B2B could always be turned off in the event we were running hard against wind and current and felt the engine was overburdened by load.
It’s a developing idea, based on new product innovations and our own experiences with our usage requirements. My design philosophy: redundancy, reliability, repairability(don’t install it if you can’t repair or replace it yourself);low cost (but not at the expense of quality) and low fossil fuel use. Without, of course, feeling like we are camping out onboard!
All the best from White Bear Bay.
Hi Brian,
Sure adding the charge from the other alternator through a B2B would make sense. Also there is some confusion about the allowed max charge on the super cycles so when you get them check out the specifications stamped on the batteries themselves. In my case that allowed a higher charge rate than the spec sheet seemed to indicate.