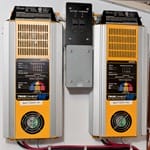
This article is primarily for those with lead acid batteries. If you have lithium batteries, your charging needs are different, so start reading at this chapter.
Charging lead acid batteries properly is complicated by the fact that most battery chargers are, despite the claims made for them, not capable of charging any battery properly (lithium too). Or at least not without a lot of user intervention.
Fully Charged
First let’s revisit: lead acid batteries are only fully charged only when the current (amperage) that the battery is absorbing at the acceptance voltage (typically about 14.4 volts) reaches 0.5% to 1% of the battery’s total capacity.
In other words, a typical 8D battery is fully charged when the charge current drops below about 1.25Â to 2.5 amps.
A Dirty Little Secret
But the dirty little secret of most AC chargers is that, while they can monitor how many amps they are supplying at their output, if we are using any of those amps for anything other than charging (as we almost certainly will be on a cruising liveaboard sailboat) the charger has no way to know what part of its output current the battery is getting and what part is powering loads (say lights).
Therefore, there is no way for the charger to detect when the battery is fully charged, despite the claims in the manual.
Overcharge Danger
So if we have any appreciable loads on while charging, many chargers will stay at the acceptance voltage (about 14.4 volts) long after the battery is fully charged, instead of dropping to the correct float charge rate (about 13.5 volts).
That’s right, most marine battery chargers will overcharge our batteries if there are other appreciable loads on.
The good news is that lead acid batteries (unlike lithium) are quite tolerant of being held at acceptance after reaching full charge.
That said, we are pretty sure that the early demise of one set of our AGM batteries was because we, when working on the boat while she was hauled and on shorepower over a cold winter, left the Espar diesel heater on for weeks. This meant that the batteries were being overcharged whenever the heater ran—probably hundreds of hours over that winter.
I’ve continued my practice of lead/lagging my two house banks even though plugged into the boatyard. I have the same chargers as you and recently completed conditioning of all four banks that have these dedicated chargers. I experienced some of the same frustrating revelations as you. I can isolate my loads and condition banks while the batteries are at rest so it wasn’t quite as challenging as you write. Justin instructs us to condition at 15.5 volts (room temp) for eight hours. The chargers as you know cycle off at six hours so one must set the alarm and re-introduce the cycle for two more hours. Also my chargers must be programmed at 15.7 volts because three of the four held that voltage for the cycle even though the battery temperatures varied ten degrees (F) or so. My battery temperature didn’t rise appreciably so the pre-programmed conditioning voltage was a non issue. One charger refused to enter conditioning mode even when fooled (flooded batt pos), actually it adopted the mode but refused to come above 13.7VDC. I replaced the charger with the spare and all is well again. I agree with your idea that this is an expensive process when away from the dock. I can expect the generator to run 16 hrs or more for this monthly exercise for each house bank. I do not count amps as you know but rather rely on voltage to determine battery condition. I think the amp counting is too complicated and subject to error and it’s one more thing for this old man to manage.
I look forward to your research on alternator charging as this may be my Achilles heel here on Sea Return. We do not use a three step regulator and charge every battery through a Mastervolt battery isolator, hitting all with as much as 14.2 vdc. For the house bank we keep the switch on all while alternator charging because we charge through the switch for the combined house bank. Not all the banks are under load so we may be heating some more than we should but everything stays topped up while underway. With the new engine install we plan to place two 90A alternators on the engine feeding that same Mastervolt battery combiner simultaneously. This deviates from my long time practice of avoiding belt drives but David (ace machinist at Billings) will engineer the two dual belt drives which should be a durable work of art. I also believe in not combining components in a single case so that will begin to explain the two sine wave, one square wave, inverters and four Statpower and one Newmar charger. Good luck with your continued research, we should all benefit in the end.
Great comment, thanks again for sharing your experience.
We elected to use a single larger alternator and carry a spare to keep the clutter on the engine down.
The single alternator charges all the batteries through an automated solenoid that gangs them all together once the voltage is over 13.5. This always worked well on the old engine.
I would still recommend a digital amp meter to measure the amount of charge going into the batteries as the voltage will come up to 14.4 long before the batteries are fully charged. While our meter does count amps but, as you say, not terribly accurately, the big payoff is that it accurately measures the actual amount going into the battery.
I guess I may have missed something in your battery discussion. I have two smaller Rolls. I use an inexpensive Sears 110 charger. It tells me what the outgoing current is. Couldn’t you isolate one battery at a time to charge and use the others to run the ship until that one was fully charged then switch to the next…?
Yes, you could do as you suggest on the batteries, but you would be constantly cycling the batteries while on shorepower and using up battery lifetime in so doing.
With our system, detailed above, we bring all the batteries up to fully charged as soon as we plug in, and then switch one of our three chargers to float at 13.5 volts and turn the other two off. This keeps all the batteries fully charged without overcharging and gassing off electrolyte, which is a finite resource in an AGM battery.
We are getting ready to go to the Arctic with a 24v only boat and would suggest keeping batteries warm with a diesel heating system. How say?
We have never had a problem with low battery capacity due to cold. But then, generally, we don’t let the temp in the boat go below 50F (10C), more for the sake of the crew than the batteries!
However, you do want to make sure that all your charging systems are automatically temperature compensated since when the batteries are cold you need to use a higher voltage to properly charge them.
GPL-L16T Marine Battery, I plan on using 2 of these 6volt bats on my 38 year old 20′ Ensenada. I was wanting to know what is the best way to charge these bats as a 12 v system or isolate and charge as 6 v.
These are 400 amp/hr bats each. Will the system be 800 amp when seried to have my 12 volts? Also, I only have room for one solar panel, I’m thinking 235 watts. What kind of charge controller will have a 3 step charge control for AGM batteries?
Hi Rick,
To answer your questions:
1). It will be best to install the batteries and charge them in series at 12 volts.
2). The bank will be 400 amp hours at 12 volts.
3). See Colin’s chapters on renewable energy in our Online Book Electrical Systems For Cruising Boats for info on charging solar cells.
I’ve installed a new Mastervolt based system on our new boat. This has the advantage that it ties all chargers, inverters, shunts, etc., together with (optional) remote control panel(s). The trick here is that you can tell the charger to interface with the shunt so that it knows how much charge actually goes into the battery.
Yes we looked at Mastervolt. As you say, good equipment. The problem is that their 115 volt chargers top out at 50 amps, so we would need three of them—ouch!
We still think that the world needs a really good three stage charger that can output a total of say 150 amps at 12 volts, senses charge current from a shunt and does not include an inverter.
Just to add a good source, I have a Magnum charger/inverter, an optional shunt for monitoring the battery is available, ME-BMK. I don’t have it yet but will be looking into it more. If I understand this discussion right; putting the shunt in at the battery (before any loads) the charger will have accurate data for controlling the charging cycle.
Thanks for the pointer. I have heard good things about the Magnum and you are right, putting the shunt in should allow the charger to properly sense when the batteries reach full charge.
My problem with the Magnum is that they only make inverter/chargers and I think that this is just putting too many eggs in one basket. I really prefer to see the inverter and charger(s) as two separate units. See this chapter for why.
Can anyone please advise on which manufacturer(s) have a unit with a separate sensor wire? Pricey models from Blue Sea, Chargemaster, etc. seem to have no such provisions.
Same question regarding multiple temperature sensors. From what I can glean, those that have sensors have but one, even if the charger has 3 independent legs.
Hi Jon,
Good question. The best way to deal with this issue is to install two smaller chargers, one wired to each bank. This solves the issues you bring up and also gives backup and flexibility when equalizing: https://www.morganscloud.com/2010/10/05/equalizing-batteries-the-reality/
That said, I think Victron may have a unit with separate sensor wires, although I have not investigated in detail.
Hi John,
What could be the best 12v. battery charger avalaible? I’m refitting my sailboat with 2 indĂ©pendent house banks like Morgan’s Cloud 2 X 8D AGM Lifeline in each bank. I want it big, adjustable. I already have a Xantrex 40 who i’ll use for starting and windlass batteries bank 2 X 31 AGM Lifeline. Batteries still to come.
I also have 340 watt of solar panels and a wind turbine.
If something to change, just tell me please.
Hi Guy,
I have no personal experience with them, but if I were buying a new charger, I would put Victron at the top of the list. Steve Dashew is a huge fan of their products and he does not suffer junk. Also, we are now using Victron battery monitors and I’m very impressed with the attention to detail and overall engineering of the product. After and admittedly cursory look, I like this one: https://www.victronenergy.com/chargers/centaur-charger-12v-24v
That said, I could not find if it had a separate voltage sense connection, so I would check for that.
As to batteries, we no longer use 8D batteries, but have switched to 4 six volt batteries, two in each bank, and are very happy with the arrangement—reminds me I need to write an article on that.
I have just done my first equalization of my house bank (1,185 Ah over six L-16s) using my new Victron 3000Va 12 V charger/inverter. I have been very impressed with the engineering, although I was told, and the manual supports this, that it was “designed for engineers by engineers”. There are many ways to configure the unit, only some of which are through either the panel or the excellent computer interface, which takes a little getting used to and relies on the creation of custom profiles depending on one’s battery type, bank size and ideal charging voltages. Further tweaking can be done with DIP switches and other old-school methods. The unit is lighter and significantly quieter than the Xantrex unit it replaced (it was also physically smaller and cheaper) and I am to date very pleased with it and will integrate my solar and wind charging sources with it after launch this spring. Most cruisers in most situation can use the unit out of the box, but if you wish to gang more than one together or integrate it with a generator, those options are very available. This may be informative: https://alchemy2009.blogspot.ca/2018/02/equalization-right.html
Hi Guy,
Further to my last. I couldn’t find any mention of an equalization cycle on the Centaur, so you would want to check for that too, before buying.
On my Victron charger, the equalization variables are manually set as per battery type and manufacturer’s specs. The makers of the Victron units seem the opposite of “set and forget” in that they expect you to already know a fair bit about battery chemistry, charge profiles and how to test your own banks via S.G. and voltage readings. That was part of the appeal to us, actually, but it’s also not for the casual weekend boater, I would think. But I don’t think many of those are reading this.
Battery Storage:
We are about to leave our boat on the hard for 3-4 months to avoid the summer heat and windy weather on NC. Do you have suggestions for how to handle AGM battery storage? We have one 105 AH (1000 MCA, 800 CCA) as a starter and two 198 AM (1420 MCA, 380 RC) for house batteries. Should we put a trickle charger on each of them (3 in total)? If not, what would you recommend?
Hi Sarah,
just fully charge them and then disconnect them from all loads and they will be fine. We have left AGMs for over a year in this way, including through a summer, without any issues. You definitely don’t want to leave them on trickle charge.
In a number of places (article and comments) reference is made to measuring actual amps into a battery to assess the 0.5% criteria for determining full charge. For this assessment, I installed an ammeter/shunt between the negative terminal and engine ground. This measures battery charging current, net of any house loads, and gives a clear picture of the actual charge current on a single, simple meter at the panel. The shunt needs to be sized conservatively to handle currents which can be higher than the alternator’s maximum output. Since several posts speak of a shunt on positive side, I am just wondering if anyone see a problem with my set up?
Hi Areddon,
In theory, it really doesn’t matter if the shunt is in the positive or negative side, as long as it measures the charge current (amps) going into the battery. The point being that the amps are the same at any point in a circuit, unless there is a load in parallel with the shunt. Generally it is easiest and best to place the shunt in the cable to the negative side of the bank making sure that there are no loads connected between the battery side of the shunt and the negative terminal(s) of the bank.
Out of curiosity, where did you find an article suggesting that the shunt should be in the positive side?
All that said, to accurately determine when your battery is charged, you also need to know the voltage, amps alone are not enough. See #11 :https://www.morganscloud.com/2011/02/10/eleven-steps-to-better-battery-life/
So given that we would need two meters (volt and amp) I guess I favour a purpose built battery monitor, particularly since they are now so inexpensive and do other cool stuff. Three chapters on that starting here: https://www.morganscloud.com/2018/08/13/battery-monitors-part-1-which-type-is-right-for-you/
John: Thanks for quick response. I understand that one needs to measure current and voltage too.
To answer your inquiry, I took the following to suggest positive side for shunt: “The best solution is to install a charger that has a method to measure actual amps going into the battery. This requires a shunt on the battery input. Unfortunately these are pretty much non-existent. (If you find one, please leave a comment.)”. I tend to think of positive as where electrons going “in”, but I know that is a fiction.
I am glad to hear that negative side is OK since a positive side shunt measures charging current plus house loads whereas the negative side shunt only sees charging current, net of the house loads. When I see 1.25 amps on the negative side at acceptance voltage I am pretty confident that I am at 100%.
Thanks again. This is a great series which totally changed by battery care for the better!
Hi Areddon,
Ah, the old “which way do the electrons flow” discussion. Don’t worry about that, it’s really not relevant for what we are doing here. The key point to understand is that the same number of amps are flowing anywhere in a circuit, therefore a shunt will read correctly (amps going into the batteries) regardless of which lead it is installed in, as long as no loads or charging sources are connected between the shunt and the battery.
That said, for practical installation reasons, as well as the way battery monitors are powered, it is standard practice to install shunts in the negative side.
Hi John, it exists, we have a mastervolt system. Both the AC charger and alternator regulator know what’s going on via the mastervolt shunt, which shares info via masterbus. All units have as well temp info about the battery. And the regulator as well has a temp sensor on the alternator. We use a mastervolt alternator instead of the standard alternator.
Hi Johannes,
That’s good to know. That said, are you 100% sure that the regulator is actually measuring net amps going into the battery and then acting on that to reduce voltage to float when said amps reach 1 to .5% of capacity? The point being that as I say in the post, many systems have a shunt, but the only ones I know of that actually use said shunt properly are the old Link 2000 and one from Ample Power, and both are no longer available.
Can you tell me the model numbers of your gear and, better still, link to an online manual, so I can investigate further with the view of featuring them in a post?
Re-reading these articles as I am in the market for a new AC charger for my 420Ah 12v house bank.
Victron Energy Phoenix Smart IP43 Charger is an interesting option in that it seems to provide an option to control Absorption Phase duration based on return amps measured at a shunt. ie. actually measuring what is going into the batteries
The Victron term for this is ‘current sense’ and is described as follows in the manual;
“Current Sense uses battery current data that is measured by the battery monitor shunt (requires a BMV or SmartShunt) and
provides it to the charger, the charger then references this current data (as opposed to the charger output current) for the tail
current setting.
The tail current setting references the diminishing level of charge current (typical at the end of a full charge cycle) in relation to the
trigger threshold to determine when the battery is fully charged and consequently when the absorption stage can be ended (prior
to the absorption stage time limit being reached). The use of tail current to end absorption stage is a highly effective and common
method used to properly charge lead acid based batteries.
In order to end the absorption phase at the correct point, it is important that the true current flow into the battery is referenced
in relation to the tail current threshold, rather than the charger output current which may be significantly higher; if any loads
are powered while charging a portion of the charger output current will be flowing directly to the loads, making the tail current
condition more difficult or impossible to meet without current sense.”
Assuming I have understood this correctly, it should alleviate problems faced by charger determining when battery are fully charged whilst fridge, heaters, water pumps etc. are loading the system during the charge cycle.
Would be good to know if anyone has had any experience (good or bad) with this particular charger?
H Nick,
I have a smaller Victron charger without that feature, so no direct experience. That said, the quote above is exactly what is required and the same as alternator regulator I do have first hand experience with. So I would say this solves the problem detailed in the article above and should be a good solution.
Hi Nick,
Over 2 years old post, but for the records: Your understanding is correct.
The Phoenix IP43 is small but great. 🙂 Fairly moisture resistant and also flex volt, so it can be plugged directly into 240V or 120V shore power. It automatically does the transition, so it does part of the job of an isolation transformer.
(Just a thought: If all onboard AC network is from the inverter, only the chargers straight from the shore power, and the system is designed correctly, it may be able to fully replace an isolation transformer. However, I’m no EE, so this claim must be confirmed by someone more competent than me.)
The weak sides of this charger is that it’s relatively expensive for its power, and that it has no fan. The latter is nice and might be no problem, but if in a place with limited ventilation, or generally too high temperature, it will fail. That can be fixed by using an external fan run by a thermostat.
Victron has another significantly cheaper charger of similar size that has a fan, the Blue Smart IP22, but is less water resistant and has no flex Voltage. I also have one of those. If not moving between different Voltages, I think this is a better choice. Victron has many other chargers, of course, both bigger and smaller. (I agree with John that a combined charger and inverter is a bad idea. It works, of course, but has disadvantages for control and reliability that for me means a 100% no go.
Most of (perhaps all?) Victron chargers can operate as described in your text. They use a Victron communication cable in a daisy chain to share info between different units in the system, including solar regulators. The “smart” versions of the units can also do the same via Bluetooth. Linked units will by default use the best info available. If a a smart shunt or BMV monitor is added at the battery, all units will by default take battery data from that unit, not their own measurements.
I love the Bluetooth ability because it’s so easy to address each unit, to know what’s going on, if all is ok, to make software updates and adjust settings. However, I think it’s smart to use the cable connection to get max reliability. After setup, Bluetooth can be disabled, to stop hackers. I see no ned for that. My boat isn’t Pentagon… Just change the passwords from the factory standard. Many don’t…