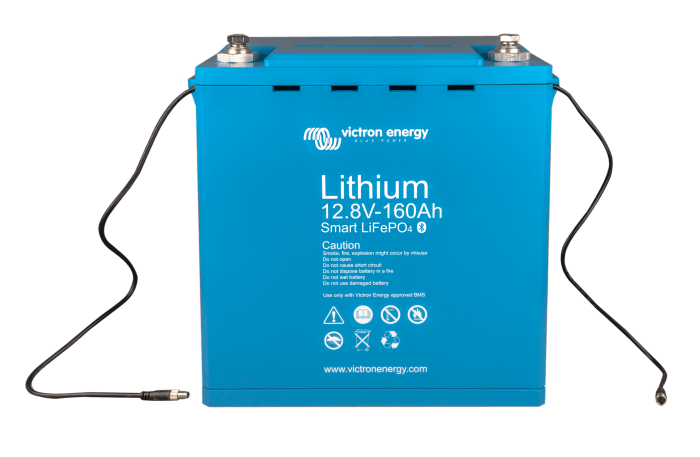
The summer before last we were stuck close to Base Camp, due to a health issue I was dealing with, and so it seemed like a good time to replace our aging—six years and many hundreds of deep cycles—house battery bank.
Not only was one of the batteries down to 50% of its original capacity, but our house bank was small by modern standards, so we wanted to upgrade to 800 amp hours at 12 volts. (More on how we determined our desired capacity for the new bank.)
Our first task was to decide what type of battery to buy. The options I looked at were:
- Lithium
- Lead acid:
- Carbon foam
- Liquid filled
- Gel
- AGM
A quick aside: Many people use “lead acid” to mean liquid filled but, in fact, all of the commonly available battery types, other than lithium, use lead acid chemistry. The differences are in the physical way the batteries are constructed.
Back to our selection process, what I learned about each battery type, and why we eliminated three of the four to arrive at our final choice (to be revealed in Part 2).
Let’s start with the sexy exciting one…yup, lithium.
Must say that cost is higher for litium, on your side of the atlantic, then it is on our side.
i have a friend ho has 1000amp Winston batts. and lives in the boat, he does it al electric. cooks +++ and afther 3 years (incl trip to Carib) the batts are at 103% from new, tested on a load test. not bad.
i will go Litium when my 4 years old leads/Trojans start going bad. but they are still doing very well.
over on this side we get 100amps Litium w/BMS and BlueT. for around 7000nkr. (and that is with 25% VAT)
And there are many that runns them and not upgrading there Altenator. just a good heat sensor on it. and have not heard of breakdown yet. there is solar panels, and some motor running when sun is not there.
Hi Geir ove,
Note that I said that my costs were made higher by selecting a main stream vendor, in this case Victron. I totally get, as I stated in the article, that lithium batteries can be sourced much cheaper.
But note that I said 400 amps hours, so even at 1000 nkr that would be close to US$4000. The Victrons would be about US$5500 for the same 400 amp/hr, so not that much difference and I think worth it for Victron quality and sourcing the entire system from one reputable vendor.
As to upgrading the alternator, I never stated that was necessary, what I wrote was that my chargers would need replacement, which is true since they don’t have a lithium program or any way for the BMS to shut them down when the batteries are full. This will be the case with most cruising boats unless the charger (s) were bought relatively recently.
Also, when you go lithium, don’t underestimate how fragile they are. I would suggest you read RC Colin’s article (see link in further reading) about just that and how many he has seen wrecked by a poor system design.
Not saying you should not go lithium, just make sure you really read up first.
Good to hear about the Trojans, I have long been a fan. More in the next chapter.
John,
I hope this series includes a consideration of Ni-Fe Edison batteries. Here are the positives:
1. A guaranteed life of at least 10,000 cycles; properly maintained their life is essentially indefinite.
2. Hit them with an 80% DoD on a daily basis with no loss of cycle life. This is a huge advantage over FLA’s and even Lithiums, both of which suffer if taken below 50% on a daily basis.
3. No complex BMS system needed; you cannot damage them with over or undercharge, storage at PSoC, and they have a remarkably wide operating temperature range. Nor is there any chance of thermal runaway.
4. A high-ish internal resistance means they are electrically safe, a short circuit will result in a self-limited current and excess gassing, without any of the extreme kAmps of fault current that Lithiums and Lead Acids can pump out.
5. They’re considered environmentally benign.
The downsides are:
1. High initial purchase price. A 12volt 500AH battery will cost around U$5000. (But remember no expensive BMS and very simple wiring will offset this, and their total cost per kWhr delivered over their entire life is by far the lowest of any battery. )
2. Their high internal resistance comes at the cost of limiting operating current to about C/5. ie a 500AH battery will work best at less than 100 Amps. This limits their ability to be charged quickly via a genset or engine. It makes them best suited to solar/renewable installs.
3. They are a flooded battery and there is no sealed option. If you routinely fully or over-charge they will out-gas and the electrolyte will need to be topped-up with distilled water every few months. (Although it would seem you can minimise this if you don’t charge past roughly 15% DoD.)
4. Disconnected Ni-Fe’s will self-discharge at about 1% per day. (Some people report a lot less and it’s not an issue for anything with solar charging.)
5. The Charge Efficiency in the top 20% SoC isn’t very good; overall most people allow for an average total ‘rule of thumb’ CE of about 80%. This isn’t as good as Lithiums, but because this figure is very stable of their lifetime, its actually better than most Lead Acids whose CE drops quite quickly with age.
6. Their terminal voltage varies quite a lot depending on SoC. A nominal 12v battery will be about 15.5 volts at 100% SoC and 9 volts a 0%. Not inverters will fully utilise this range. The upside is that SoC is a very simple function of voltage; no fancy Coulomb meters required.
7. In an enclosed space you WILL need to provide venting to deal with hydrogen out-gassing. Fortunately this gas wants to escape upwards so it’s easy to deal with.
8. Their specific energy on a volume and mass basis is similar to lead acid. A 12v 500AH battery will weigh about 260 kg or so. (In my case this is balanced by the similar weight of auxiliary gear I can remove from the same location, but it rules them out for most catamaran installs I’d imagine.)
In my case I have an ancient diesel genset to remove that will free up the perfect space to install Ni-Fe’s. Our true cutter rig balances nicely on both a Fleming wind-vane or an old AutoHelm, and we don’t have a freezer, so with care our total power consumption can likely be balanced with solar/wind/hydro. So I’m fortunate the Ni-Fe stars align for me; it accept won’t for everyone. What really appeals is the robustness of NiFe’s. While I have zero offshore experience, one thing I’m certain of, is that I really don’t want to be messing with complex technical problems on top of all the other usual challenges of good seamanship and fatigue to deal with when I do get there. Ni-Fe’s are generally way more tolerant of mistakes, abuse and idiots than any other available chemistry I know about, and that’s their biggest tick in my box.
(I ruled out the very promising Firefly Carbon Foam batteries simply because you can’t obtain them here in Australia. As you said in your podcast with Andy and Mia, the technology really needs to be licensed to see some real market leverage.)
Correction to above: messed up my currency conversion. The purchase price above should be under U$3500 based on this Australian suppliers prices:
http://www.ironcorebatteries.com.au/page2.php
Hi Philip,
Thanks very much for a very well balanced analysis. I did not include them in this series, and after your comment, I don’t think I need to!
Seriously, I just have not had enough exposure to them to add anything to what you wrote.
I guess for most of us your points 2,4 and 7 make them not really a good option. That said, I did a bit of reading and I’m 100% with you on liking their fundamental robustness. As you point out, a high internal resistance, while in some ways a downside, provides a lot of safety in a lot of different ways.
Hi Philip,
your post got me curious and I did some read-up on Ni-Fe batteries when I stumbled across this article:
https://www.rpc.com.au/blogs/news/disadvantages-of-nickel-iron-batteries?_pos=1&_sid=9f239c883&_ss=r
Most if not all issues mentioned here would keep me far away from considering them for a boat installation, offshore or coastal.
Ernest,
I think I covered off all of the issues mentioned in this link in my appraisal above … no question Ni-Fe batteries do come with some specific downsides that must be understood. But addressing each issue mentioned in that link, it’s helpful to be aware of what more could be said:
1. Ni-Fe total new installed cost is somewhere between good AGM’s and Lithiums overall. Certainly not out of the ball park. But when considered on a total cycle cost over a 20+ year lifetime Ni-Fe’s have by far the lowest cost of ANY battery chemistry.
2. Charge Efficiency (CE) overall from empty to fully charged is about 80%. But it’s only the top 20% of the charge where the CE is poor. This suggests two ways to mitigate the issue, one is simply not to fully charge on a daily basis, and the other is to add another 20 % of solar panel.
3. Self discharge is higher than many other chemistries, but insignificant if you have solar/wind available to float charge. It just doesn’t matter.
4. Ventilation is an important issue, but the good new is that hydrogen is an extremely light and diffusive gas. It’s difficult to contain and WANTS to escape. Just about any simple venting scheme will work. Moreover gassing will really only be an issue if you are over-charging. Simply limit the charge voltage to about 1.55 volts/cell and hydrogen production will be minimal.
5. At say 80% DoD a nominal 12v battery will be down close to 9.5 volts. Some inverters may cut out before this, pre-maturely limiting how deeply you can discharge. This means they may not be a drop-in replacement for LA’s on an existing boat, but I do know that Victron and Schneider (any probably others) do have inverters that will operate with this wide input voltage range. Specify correctly and it’s a non-issue.
6. Size and weight are similar to Lead Acid. At 12 v 500 AH battery (that will deliver 400AH of usable capacity on a daily basis for decades) will weigh around 260kg. Sure Lithiums are brilliant by comparison, but it’s not unreasonable either. (In my case they’ll fit right into the space where I’ll be removing about 200kg of auxiliary engine and equipment.)
7. Maintenance is certainly not weekly. You’d have to be heavily overcharging almost continuously to need that much refilling. Most users report that at most they need to check once every few months or so, many much less. All you are doing is looking at an easily seen level through a translucent case and adding some distilled water. Overall maintenance doesn’t seem any more onerous than standard FLA’s and many people live quite happily with them. (And I’m only interested in a 12 volt, 10 cell installation, not 40.)
8. Yes the electrolyte should be replaced at most about every 7 – 10 years. All that is happening is the KaOH slowly reacts with CO2 from the air and forms insoluble carbonates which you can see as a visible deposit on the bottom of the cell. The upside is that now you have a virtually new battery that will last another 10 years or more! Rinse and repeat … hand them onto to your grandchildren.
Here is a video that discusses large fixed Ni-Fe/solar installs in some technical depth. It’s commercial but as a professional engineer who has used Schneider equipment in many projects, I read it as a reliable source. A good comparison table is at the 28 minute mark: https://youtu.be/eGZ9-bp4uZM?t=1687
NiFe batteries are a niche solution. They’re going to best suit offshore mono’s looking to replace an auxilary genset with renewables in a super-robust, long-life dependable system.
To achieve 12v/400 AH of usable storage with Lead Acids will mean installing 1200 AH of battery also weighing close to 300kg. With daily cycling between 80% and 50% DoD you’d be doing well if they lasted 5 years if you treated them well. 3 years with the usual yotti treatment. And they come with a whole bunch of well-known charging and maintenance issues.
And I don’t need to repeat John’s analysis of Lithium’s. Neither of these common solutions is without issues. Nor are Ni-Fe’s fault free. The whole point though is that understanding each type’s strengths and weaknesses, and understanding how these fit with YOUR individual boat and YOUR sailing needs is what this excellent series is about.
Philip
Hi Philip,
Another balanced analysis, thank you. I particularly like your last sentence. That’s really the whole point.
Technology assessment: Bleeding edge or best fit for the job?
We were building a cost-is-no object 116′ motorsailor for an Owner who loved to create problems and then observe how people solved them. So he comes to me saying “Richard, I’m having a terrible problem deciding what battery arrangement to use. I want you to research the field and produce a recommendation for me the next time I visit. ”
Now I’m smart enough to know that my hydraulic theory of electricity won’t be sufficient for this task (LOL) so I bought beers for several friends who design factory trawlers for the Gulf of Alaska and tourist submarines for Hawaii. They strongly favored 2V conventional deep cycle lead acid submarine batteries in series. (somewhat similar to Steve Dashew’s approach) When I did an analysis of this concept I found that I could package them between the ring frames below the sole and achieve a higher power density than the AGM batteries that were the state of the art for that era, still keep each unit within a manageable weight range and drastically improve the storage utility of the “garage”.
So I walk into the meeting with the Owner and discovered that the other participants were the President of Sparkman & Stephens and a senior electrical engineer from MIT that the Owner had paid $75,000 to produce a study of the state of the art in batteries for our project. Of course you know what happened! I will say that the MIT/Victron design with individual heat sensors and controllers on each battery racked along the hull sides worked just fine for the 4 years before I lost track of it.
An Owner with that much money to burn can afford the risks and costs of a custom install like that; but the next person to own the boat may not be so fortunate. If there is one thing a lifetime of heavy engineering has taught me is that robust and slow to degrade solutions are always the best life-cycle value for most scenarios, most of the time.
Innovation has it’s place (and I’m always a sucker for it), but complex, fragile innovation does not belong offshore.
Hi Philipe,
“robust and slow to degrade solutions” Kind of the opposite of a runaway Lithium battery!” LOL.
I would note that a power failure on a lee shore in Antarctica with a complex automated yacht is equally serious regardless of whether money is of no object to the Owner—.
Hi Richard,
A fun story, although not for you at the time, thanks for sharing it. And I agree, there’s a lot to like about plain old liquid filled. More on that in the next chapter.
I’m surprised you considered that your whole charging system would have to be changed. Lithium batteries are being quite commonly used in motorbikes these days as a simple replacement for lead acid, apparently without problems other than the need to “wake them up” by switching on lights before cranking the engine.
Could it be you’re overthinking this?
No, he’s not. I’m a boat yard electrical technician, and I just had my first service experience with lithium batteries. Here’s the story:
A customer brings his nearly new Alieron 40 to us for storage on the hill during hurricane season. The vessel has 48 volt electric propulsion, two large lithium battery banks capable of powering the motor for about one hour ($20,000 worth), a 48V diesel generator, a Victron changer/inverter, and a battery management system.
Whilst the boat is in the hard, we have a power failure that lasts multiple days and the inverter/charger is in the default invert mode, so it inverts until the batteries are deeply discharged. Why the bms didn’t shut the system down when the batteries got low, I don’t know.
With the batteries deeply discharged, the bms won’t allow the inverter/charger to connect to the batteries, so consulting with the guy who designed the system, I charge each individual 12V battery with a specially designed rescue charger that puts out about 280 milliamps in rescue mode. The hitch is that this smart charger will only stay in rescue mode for three hours before needing to be reset.
To make a long story a little shorter, it took me three weeks to get the batteries up to the point where the bms would allow the charger to operate, and it finished the charge cycle in a few hours.
Anywho, to echo John’s point, you don’t want to have such a delicate system on an offshore cruising vessel. Just imagine what could happen if that system went off line during heavy weather. Yow.
That’s my two cents.
Hi Scott,
Thanks for that real world information, the best kind.
Added to your experience, assuming that the BMS did fail, to at least some extent, which makes sense from your description, I’m guessing that the batteries were also damaged by the incident and will probably fail much sooner than they would have otherwise.
Another tale from the bleeding edge of design engineering—.
I was asked to work with an engineer from a Paul Allen company called Advanced Lithium to design and fabricate the battery containment module for the Fisker EV. (the design that the Muskrat stole and evolved into the Tesla Model S)
Upon viewing the AL operating prototype my immediate reaction was “this is nutz” . Their battery design consisted of thousands of laptop batteries in series, each with its individual controller. So far so good– a copy of Tesla’s early battery except that the AL design had the batteries air gapped instead of liquid cooled, and thus was 100% dependent upon flawless operation of every single controller. Needless to say, Advanced Lithium’s cash burn soon rose to a million $ per day as they learned to never test a battery in anything but a fireproof and explosion proof room. Something that even my hydraulic theory of electricity could predict!
Hi Scott,
Thanks for the example – although I’m not sure it demonstrates that lithium (phosphate?) batteries are delicate. It suggests the BMS did shut the batteries down but at a minimal level. Or it didn’t shut them down and yet the batteries recovered even after being put in a condition they should NEVER EVER reach. In which case the battery system designer should have a red face and probably a warranty claim by the owner for probable loss of lifetime cycles.
As I understand it (from reading a manual), below 20% charge the lithium phosphate batteries undergo a chemical change that can at best damage them often irreversibly, or at worst make them unstable. To combat this, most battery management systems (integrated in the battery in the case of reputable products) will shut down the battery at the 20% charge level as a factory setting and will not allow re-charge until it is checked by a technician to ensure it is safe to do so.
So as normal practice, the system SHOULD be set-up so each battery separately alarms at around 30% charge remaining, and shuts itself off at about 25% capacity remaining. This will be a setting in the battery management system (for MasterVolt anyway). Then, when the power comes on again the battery(ies) will simply re-charge if any isolating switch (if fitted) is turned back on, because they haven’t reached the minimum threshold.
That the system you encountered locks the user/charger out may demonstrate an entirely sensible precaution – an installer / user inexperienced enough to not have set the cut-out above the minimum 20% (save the ship) level, is probably also inexperienced enough to override the 20% cut-off and endanger the battery and / or their boat.
But it may also illustrate (and go against John’s recommendation for single source) how cobbled together lithium battery systems from multiple suppliers can and possibly did go wrong, and even be dangerous.
Rob
Hi Rob,
Yes, as I understand it, that’s exactly how battery mangement systems are meant to work, so you may be right that in this case this one did, but the interlocks needed to be overcome.
Either way, as you say, this is exactly the sort of issue that, if I was going lithium, make me wish to source the entire system from one vendor like Victron. For example, the Victron system BMS would have shut down the inverter before the batteries were even close to depleted.
Hi Jim,
No, I’m not over thinking this. I spent hours and hours reading up on lithium batteries and the required control circuitry to protect them. The replacement lithium battery for your motorbike may look like a simple battery, but in reality it includes much of the circuitry and interlocks that I describe above within the battery unit. Also a motorbike is a much simpler, and very different, usage case than a voyaging sailboat since the engine is running pretty much all the time when the battery is being used.
Another way to look at the same thing is that lithium batteries are used in pretty much every cell phone, but that does not make them simple. In fact the circuitry that controls and protects the battery in say an iPhone is fantastically complicated. We just don’t see those complications…that is until things don’t work well, as Samsung found out a couple of years ago.
Or to put it another way, just because something is commonly available, that does not make it simple.
Dear John
Please accept my apologies if this suggestion has already been covered:
I think I may have found a lithium battery that would be useful on a boat. At least on a reasonably small boat. It is a 10,000 mAh car jump start battery I bought from Amazon at Christmas for £40. It started the 1.6 litre diesel in my car with ease and with plenty of juice left over. It claims to be able to start a 2 litre diesel and I have no reason to doubt it.
A further use for it is as a power bank for iPads and such like should the electrical systems on board completely crash. It has a USB take off and also doubles as a torch. Higher capacity alternatives may be available.
By the time you come to replace your current batteries maybe lithium battery technology will have advanced far enough to be both safe and economical enough to suit our needs.
Best.
Mark
S/V Tumbler (as of 3 weeks ago)
Hi Mark,
While that’s interesting, and demonstrates a fundamental characteristic of lithium batteries—very low internal resistance, resulting in very high peak amps capability, I can’t see them as a viable alternative. 10,000mAh is only 10 amp/hours, so even with a small boat only requiring say 200 amp/hours in the house bank that would take 20 of these in parallel. Can you imagine the wiring! Also, paralleling that many batteries has fundamental difficulties and dangers.
And finally, these car starters are not just batteries, they also contain much of the control and management circuitry that I describe in the post above, but said circuitry will be optimized for very different use (car starting) and not intended to be paralleled with other modules.
I too have one of those lithium-based portable jumpstarters; they are indeed handy! However, folks should be aware the instructions for its use require a lead-acid battery in the circuit. I tested – the device by itself was not able to start the engine with the starter battery disconnected. Even with the jumpstarter’s safety mechanism disengaged, it would not crank my 3-cylinder diesel AT ALL. But in conjunction with a very depleted lead-acid starter battery, which on its own could not crank the engine, the jumpstarter worked great. In summary: not very useful as a general or stand-alone battery, put perfect for its stated purpose.
Chuck
Hope you include firefly carbon foam. Currently have lifeline agms but when they go thinking of the carbon foam as the replacement. Think it’s safe and a simple drop in. Don’t even need to change programs from wind/solar/invertor/ alternator. Also they are a bit lighter.
Hi Lee,
Yup, a big part of chapter 2 is devoted to carbon foam.
Hi John, now this content is worth the price of admission. Timely for me as the 16-8D Lifelines aboard here will have given five years service this August. The 8 batteries in the house bank in particular are just beginning to show their age with some capacity drop. You will save me lots of research. I had begun my homework with the Lithiums and came to a very quick decision; not yet for me! Weight here isn’t a factor as you know (aside from getting them in their boxes from the crane hook). I look forward to the next chapter. Bob T.
Hi Bob,
Good to hear from you, as always. I’m pretty sure the next chapter will give you everything you need to make a call on replacement, but if not, don’t hesitate to ask for a fill in the comments.
My battery bank is ~450 A. And after we change all lights to LED AND installed new fridge (new isolation+new fridge unit) it is full sufficient. My point is that reducing the demand is by far better and cheaper than increasing the generation/storage capacity. Sorry for repeating the old news but as much as I like new “stuff” installing any new technology onboard is asking for another “bleeding edge”…in addition to the bleeding toes ! Thank you Hershoff-designed cleats?
Hi Marek,
I totally agree, conservation and simplicity are a powerful combination, particularly for those who want to go sailing rather than mess with complex technology.
John,
Another consideration that helped me not choose lithium batteries [for now] is I have read [but not looked into the details] lithium batteries must be above freezing temperature to safely accept a charge.
My present house bank is against the hull, and maintains a temperature not much above raw water temp. I could envision having to run a radiant heating loop inside the [not yet insulated] battery compartment as another lithium bank requirement/enhancement- at least in higher latitudes.
Thanks for the well researched details.
Cheers! Bill
Hi Bill,
You are right. For most lithium batteries, you can’t charge them at temperatures under about 0C. That said, unless you were planning to winter over in the high latitudes I think just a bit of insulation between the hull and the batteries should do the trick since even on the East Coast of Greenland, I have rarely seen water temps below about +1C in summer, even with a lot of ice around.
But isn’t this a problem for unoccupied boats? The cabin temperature of my boat frequently drops below freezing in the winter, and that is in the water in Maryland.
Or does it reset and charge again when the temperature rises?
Hi Drew,
Yes, could be a problem since, with the Victron lithium batteries, for example, they must not be charged at less than +5C or discharged at less than -20C. I think the latter is not a big problem where you are, but the former could easily be since if you did inadvertently charge at less than +5 the batteries could be damaged. To me, this disqualifies lithium in a case like yours.
I wonder what accounts for the price discrepancy between Victron’s batteries (12.8 V/200 Ah LiFePO4 at $2,730.20) vs CALB (12.8V/180 Ah LiFePO4 at $259 from EVWest)?
Hi Rolly,
Interesting question.
I really don’t know, but a few fairly well informed guesses:
I also note that the system that Bruce Schwab at Ocean Planet is selling for marine use prices out at the same level as Victron, so that kind of confirms to me that while it might be possible to build a system for much less with these cheap batteries, I for one would not being going to sea with it since I don’t wish to be suddenly shipmates with a “thermal excursion” as battery engineers call a lithium battery self-sustaining fire. One thing to put these in a car, where if it goes wrong we can pull over and get out, quite another in an offshore boat.
And finally, note that a 195 amp hour battery from the same guys is actually more than the Victron: http://www.electriccarpartscompany.com/12V-195Ah-Engine-Start-Battery
The Victron batteries may even have these cells inside. Essentially what is missing is the attached BMS and configuration.
A few people have been experimenting with the type of bulk cells sold by EVWest — not simple at and certainly nowhere near the kind of plug-and-play ease that Victron provides (and is without any kind of warranty or supplier liability).
But yes, there is a huge price difference. Prices will come down. At the moment Victron and Mastervolt are the only players in a small market. This won’t last long.
Hi Stefan,
I hope your right on price, but given that much of the added cost for full systems is, I think, fire containment and control circuitry, which seems to absent from the less expensive options, I’m not sure how quickly the price will fall. The other issue is that companies that sell full solutions like Victron and Master Volt have big due diligence and liability costs, which will probably not drop much.
Bare lithium cells are dirt cheap. Bought in small bulk quantities, the common 18650 cell in lithium-cobalt-oxide chemistry is around two dollars a cell, or $180 – $220 USD per kilowatt hour, now. Complete packs for electric cars, in vertically-integrated production, just dropped below $210/kWh a few months ago.
In John’s reference 400 Ah @ 12 V (4.8 kWh) pack, that’s roughly $860 – $1060 for the cells. Hardly a king’s ransom.
The expensive part is everything that goes along with them. Containment. BMS. Cabling. Charge controllers. DC/DC converters for the chartplotter, radar, VHF, and a few dozen other loads. Design effort. Installation labour. Fat markups on all the above due to it being a new technology with relatively little price competition between vendors.
In John’s example, the wholesale cost of the lithium cells themselves was just 20% of the retail cost of the battery modules, and 10% of the cost of the whole installation.
Bringing that price down will require next-generation marine Li-ion systems, in which the major manufacturers learn a lot of lessons from their current products and optimize their designs and manufacturing processes accordingly. I said, four years ago, that it’d be about five years before we saw the necessary expertise and economies of scale for plug-and-play marine Li-ion systems to start becoming viable. I think that timeline is still about right.
Hi Matt,
Thanks for coming up on that. All makes sense to me. One thing I do wonder about is if the benefits of carbon foam may make lithium a special use product for a long time to come. More on that in the next chapter.
Thinking of the next chapter… Right after I replaced our house bank in 2014 with Trojan T105 golf cart batteries, Trojan announced their ‘Smart Carbon’ technology.
It is purported to improve the useful lifespan of battery banks subjected to ongoing PSOC situations.
http://www.trojanbattery.com/new-products/smart-carbon/
I have been keeping an eye out for reviews, but find none. I mention it here in case it is of interest.
Cheers! Bill
Hi Bill,
That’s interesting and the first I had heard of them. That said, even Trojan is only claiming a 15% life cycle increase for them in applications where they are often not fully charged. So defiantly a step in the right direction, but probably not a break through.
John,
While I have no doubt you are educated, you are perhaps too educated? LiFePO4 is not nearly as “fragile” a you claim, not nearly as expensive, nor as complicated. I have 800Ah of LiFePO4 in service now for over a year not even a hick-up. I paid, all in, batteries, chargers, controller about $3000. I have used my existing buss distribution system with a few tweaks. The engine battery is a standard lead acid, and the alternator can be used on the Life bank if I needed, but my 480W solar tops it all off everyday so have never had to. Simply have to monitor the process.
If you want a fool proof, no knowledge or skill required, then lead acid is the way for you. If you want an icemaker, and lots of spare dc power the cost per amp hour is way better for LiFePO4.
You either over thought the issue or did not talk to someone who has actually done the work and is using a system… not sure I did not read you whole article just skipped to the results.
Hi Shane,
Glad to hear they are working out for you. As I said in the article, there are cheaper and simpler ways to do lithium batteries but my position—based on substantial research including reading accounts from people who have done many of these (see further reading)—said cheaper ways are not safe enough or failsafe enough for most of us to use offshore. You obviously feel differently, and that’s fine, but please don’t denigrate my substantial research and valid opinion particularly if you can’t be bothered to read all of what I wrote.
Firstly there’s a bit of confusion on this board about lithium and LiFePO4, with safety misconceptions based on a different, outdated technology. LiFePO4 batteries are not the types found in laptops or exploding Samsung phones.
In addition, the price comparison needs to be put on a level playing field: also factoring in lifespan and usable capacity. The price difference shrinks massively when the comparison is fair.
As for safety issues, I’d also look at the fact that the capacity and power improvements from LiFePO4 can open up huge safety gains such as the elimination of on-board gas stoves and LPG bottles.
For complexity, a good, safe LiFePO4 install is no more complex than a good, safe lead acid install. It just has it’s own peculiarities and considerations.
However I take the point about not being bleeding edge, and I agree with the sentiment that Lithium is just a bit too new to try. This is not necessarily logical, but it doesn’t mean it’s wrong. After all, modern diesel engines are horribly complex and have huge numbers of failure points, but we’ve got used to proving the kind of TLC that keeps them broadly reliable.
Still, I think this will change and battery prices will plummet in the next 5 years, with the technology maturing rapidly. At the moment Mastervolt and Victron are the only real off-the-shelf players in town, as far as I know, and when this changes (which it will), than lead acid will be seen for what it really is: poisonous, inefficient and outdated.
I think we’re at a turning point right now. The technology is advancing fast and will become the norm for may people within a few years. I would even predict that lead acid will be hard to find in the shops in most developed countries in about 10 years from now.
As someone who installed a large lead-acid bank recently, I faced the same decision-making tree. Excellent in potentia as lithium is, once you’re in, you’re in for table stakes with the sort of tech I feel only makes sense on a large boat with a large budget. A big lead-acid bank such as ours is part of the internal ballasting and is easily replaced most of the places in the world we plan on going. Flexibility in charging sources and being parsimonious with amp draws covers the rest. But were I doing ocean racing, or planned on being closer to shore, I would consider the lithium option. Poisonous, inefficient and outdated could also be said about the internal combustion engine, yet here we are.
Hi Stefan,
I’m well aware that LiFePO4 and phone batteries are different and the former far safer. In fact we have an entire article from Matt, who has built lithium batteries from single cells (for cars) and is a professional engineers. See further reading.
I will deal with cost per cycle in the next chapter, but having done the analysis I can say that the idea that lithium, at least a full fail safe system from a reputable manufacture, is even close to the per cycle cost for example liquid filled, while often repeated, is simply not so. In fact the cost is several times higher for lithium, even taking into account that the bank can be half the size.
Also, I have to disagree with you when you say that a lithium system is no more complex than a lead acid system. Just one example of added complexity is that if we want proper fail safes to protect ourselves and the batteries, with lithium we need to separate buss bars and voltage sense relays to controls each. And further, ever cell of a lithium battery needs managing at all times by a battery management system. No such system is required for a lead acid battery.
Hi John,
I hope our thinking and experience to date provides a helpful counter-point to your decision making process on lithium batteries. I can only speak with any knowledge about lithium ion phosphate battery technology and I should add we are not intending to voyage to high latitudes, or planning extended multi-year cruises.
I mostly agree with your points on lithium, but differ in thinking on who could/should undertake a lithium install and why. Three years ago we were faced with a complete re-power to go offshore in 2017 to the SW Pacific for 6 months cruise. Our batteries were end of life, the seawater-cooled generator (no heat exchanger) needed junking, the charger was old and rusty being installed in a damp lazarette, we had no inverter and the original alternator was entirely inadequate (60amp). Finally, two of our AGM batteries were installed in the same lazarette, and in the wrong place for that weight (140kg) on most boats, but especially ours. Strangely, our power decision was largely made by a decision to not replace our generator and by the choice of replacement alternator. Volvo supply a retro-fit kit for our engine specifically for the MasterVolt (MV) alternator, with a purpose made / tested mounting and a serpentine belt system. Having read your excellent article on retro-fitting a cruisers’ alternator, I liked that we could fix our charging system without compromising our main propulsion.
So having made this call, we decided on a single vendor (MasterVolt) solution which 100% aligns with your thinking on lithium John, but we went further with new: MV 130 amp alternator with MV controller, MV charger/inverter, MV solar controller (+ panels), MV battery management and electrical management and 3 x 180 amp MV lithium phosphate batteries. This trebled our effective battery capacity for about a third of the weight (none in the stern).
The benefits (apart from weight and space):
In our 6 month cruise to the Pacific we managed a horribly inefficient fridge and freezer (often consuming over 20 amps between them running for long periods), a water-maker, plus an electrically powered auto-pilot and the usual electronics, with 4 flexible solar panels (600W total). SW Pacific Island cruising is in our southern winter, so we only experienced about 1/2 our normal summer solar gain. In all we ran the main engine for 360 hrs, of which about 30hrs was at anchor solely to charge our batteries. This is entirely attributable to your second lithium benefit: “Will take the FULL output of all charging sources until fully charged, instead of the charge rate tailing off for the last 20% or so”. These batteries are simply amazing – they take the full available charge from the alternator and solar, right to the 100% charge level.
So how about overcoming the challenges you mention:
1) We used one manufacturer MasterVolt and a highly skilled supplier/installer/service agent here in NZ (Enertec). I didn’t install myself, but I did ask dumb questions like “what happens when the power goes off”, and emphasised a need for redundancy and resiliency in the design.
2) Despite being one of the best Marine Electrical specialist companies in NZ, Enertec organised a MasterVolt technician to do the final system integration and testing remotely. This is specialist work in their view, not a DIY scenario unless you’re experienced with computer systems and electrical work.
3) We bought 3 smaller 180 amp/hr batteries installed with their own isolating switches, though we could have bought just one larger lithium phosphate battery at a big cost saving (about 30%). If any power or battery issue (like heat) is detected by the battery management system, it will trip the individual battery isolator. We can lose two of our three batteries in this way and still have as much effective electrical storage as we had with our old AGMs combined.
3) Our new battery locker is designed to keep the battery and electrical system units well ventilated and elevated/insulated above the hull. Every 3 months we replace the dehumidifying agent in a little plastic tub (the disposable type designed for wardrobes). The locker is exceptionally clean and dry, and we have a little climate monitor with temperature and humidity sensor. In all respects we try and keep this space like the computer room it is.
4) The correct extinguisher class for lithium phosphate batteries is a standard dry powder unit. We have an extinguisher right outside the berth, a set of fireproof gauntlets, fire-resistant boiler-suit, charcoal breathing mask and flash hood ready for emergencies (not just for the batteries). I am under no illusion about how difficult removing a combusting battery would be, but we are as prepared as can be. I believe lithium phosphate is no more risky than other battery technologies if they are kept in the right environment and managed properly. Think of the millions of lithium batteries out there every day kept in far worse conditions than our pampered batteries, that do not catch fire. Batteries in tiny fragile devices that have been sat on, bent, dropped from a great height, even dropped down the loo or been swimming in the sea – in fact it is amazing when you hear some of the stories (my son is in the mobile operator business) that there aren’t way more mobile fires reported.
5) Each battery is factory programmed to shut down at 20% charge, so the MasterVolt technician set our batteries to individually alarm at 30% charge and isolate-out at 25%. Then we tested it in real-time to ensure it worked by shutting off the charger. This means that if we have a power problem (as Scott described above) and one or more batteries shut-down, the battery(s) resume charging as normal when power is restored, without any special intervention (except to manually switch the isolator(s) back on).
Expense:
1) Because we saved by not replacing the generator, we were up already on $$ for the project as a whole. But I expect the batteries to easily break-even with lead-acid technology over 10 years, even without the generator saving.
What about serviceability:
1) When storing the boat for longer than two months we run them down to around 50%. Lithium phosphate batteries prefer to be kept at mid-charge level if not active.
2) Our engine battery is a high capacity conventional lead acid type and is deliberately separate from the house bank and a different technology. The only common part on the line side is charging from the alternator and shore power. If the worst happens and we lose all three lithium batteries with the batteries isolated, we can parallel switch the load over to the engine battery and keep that alive with our main engine, turning off non-vital electrics. We also carry LED emergency nav lights, battery powered back-up hand-held GPS, a “pocket” lithium power-pack for emergency comms re-charging and an engine “jump start” battery pack.
Finally John, I am no electrical expert nor want to be. But with our electrical / battery management system we have great visibility and control over our battery bank and all the other electrical sub-systems. MasterVolt lithium phosphate batteries and management systems have powered the last two Volvo editions to my knowledge, in far worse conditions than we could ever imagine – and that speaks volumes to me.
Yes, the clever folks buying their batteries direct from China, integrating their own battery banks and hooking up to third party management systems are saving serious $$ upfront (50% at least). But in my view, unless they are engineering and system testing as much as a MasterVolt or Victron, they are taking short-cuts. Now that’s something to be worried about.
Rob
Hi Rob,
Sounds like you did the job just right and are getting great results. I really don’t disagree with any of your analysis, except possibly “as safe as any other battery”. The key point there is that although, as you say, there are millions of lithium batteries that never cause issues, we should never forget that all lithium batteries use a combination of chemicals that are capable of self-sustaining combustion, which is not the case with lead acid. The very fact that much of the cost of reputable lithium batteries is in the containment system tells us something.
I also need to point out that, given your statement ” I am no electrical expert nor want to be” if the system had failed on your cruise you probably would not have had the knowledge to fix it, and probably not the parts either. Whereas a simple lead acid system can be fixed by anyone with, common sense, a meter and Nigel Caldar’s book, using parts that are readily available most anywhere.
So, in summary, I guess it comes down to the trade off between complexity and repairability, and the undeniable benefits of lithium and each of us must decide how to balance that.
Hi John, I thought you and others might be interested in a modification we have made to our electrical system as a result of reading both part 1&2 articles and specifically your comments about lithium based systems being less maintainable. Indeed, it made me consider your point about your “back-up stop”, being to hike up the road and buy a truck battery to slot straight in.
So anticipating our worst case, where our Master Volt lithium battery management system shuts down and we can’t diagnose or fix it, we have pre-wired battery cables to their appropriate house electrical bus, suitably secured and isolated. Now we can source any “truck” battery ashore, isolate the lithium batteries using their isolating switches and connect up the battery cables to run as a conventionally powered vessel with separate house and engine bank until our return to NZ. The charging and load side functions remain completely as before. We have the old battery management panel and screen still wired in, and even have a nice spot in the engine bay left over from replacing the old batteries!
I know this still isn’t a purist’s solution, but it adds a further level of pre-prepared resiliency for us – electrically challenged as I am. As ever John your valuable comments provide a “check-in” for our thinking and systems. Thanks.
Rob
Hi Rob,
I think that makes a huge amount of sense. My thinking has always been to minimize the number or potential failures that can ruin a cruise, and this seems like a very good way to do just that.
Hi again, Rob,
I should add to my comment above that I’m not in any way suggesting that you made the wrong call on lithium. My only purpose in the comment was to make sure others clearly understand the tradeoffs you have made.
In the “Volvo Ocean Race Independent Report into the Stranding of Vestas Wind”
it says “The Lithium Ferrophosphate (LFP) batteries were beginning to smoke due to their immersion in salt water and the extraordinary likelihood of a fire became a possibility.”
At the time following that accident I also read somewhere else that the crew removed the batteries from the boat because of the fire risk and deposited them on the beach.
My takeaway from this is that you really don’t want to submerge your lithium batteries in sea water.
When I read that story, I remembered one of the incidents in my boating career that I am least proud of but from which I learned a lot.
We wanted to move the boat the short distance of 12nm from Lisbon’s central Doca Alcantara to Cascais because I was to leave the boat for a week on business back in Germany. The weather forecast wasn’t good but I figured “It’s only 12 miles. How bad can it get?” We waited until the last minute because (of all things) I spent 2 hours in town finding a topup for our mobile data card. When I got back to the boat it was dusk. We called the harbormaster asking for the pedestrian walkway to be swung open. He said they don’t open on request but on the full hour and they are open now. We had 2 minutes. After we left in a big rush, we moved down the Rio Tejo in full ebbing tide. At the mouth, which is fully open to the Atlantic swell and which has lots of bars and shallows, we were met with 25 to 30 knots true closehauled. In the extremely confused seas and wind-against-tide, we had seas breaking over the foredeck and water coming rushing along the side decks several times a minute.
When we approached the Cascais harbor entrance, I felt the boat behave decidedly weird. When we docked at the reception berth, we noticed that we (my wife and I still have not settled if it was her or me) left the sail locker hatch partially open due to the fact that in the rush to leave we had not put all the fenders away. The sail locker was filled to the top with about a ton of sea water. Some of it, though not very much, had entered the inside cabin.
The bow thruster battery was submerged under 3 feet of sea water.
As you will agree, there are many things to be learned from this. In the context of this post, let’s just focus on “it can happen quite easily that your battery is submerged in sea water”. And it doesn’t even have to mean a lot of damage. The bow thruster motor had to come out and be cleaned and we had to lift the boat quickly to change the oil in the bow thruster gearbox. The rest was just a big cleanup, mostly done by my wife as I was away.
The bow thruster battery, a normal Victron AGM of 100AH, then 5 years old, was none the worse for spending one hour under water (other than lost tinning on the poles) and is still going strong today at 10 years old. It still drives the bow thruster at full power, taking 350A, for the full time until the overheat protection of the thruster motor kicks in.
You may say that I wouldn’t use a lithium battery for a bow thruster. OK, but then I would have to have separate charging sources/regulators for each type of battery for my three banks for (a) shore charger, (b) engine high output alternator, (c) DC 12V diesel generator and (d) solar.
I installed the full set of batteries (1 start, 6 house and 1 bow, all identical 12V 100AH Victron AGM) at the same time in ca. 2008. I must have been using them very mildly. The two deepest discharges, according to the “Ah consumed” number output by the Victron battery manager, were 100Ah (at sea Azores – England) and 117Ah (I used the power washer to wash the deck, hit the AC cable and plug with the water jet and didn’t notice the residual current breaker trip as the inverter was taking over immediately – that wiring fault is now corrected).
So my second point against lithium batteries is: If my plain, robust and economical AGM batteries are in excellent working order after 10 years, then what problem would I try to solve with lithium? Calculating the price difference, they would have to last for 30+ years. Is that in any way likely?
Hi Henning,
I always learn so much from your comments for many reasons, but one of the most important and appreciated is your willingness to discuss and learn from your mistakes. I try to do the same, but it’s always a struggle to recognize and confess to my mistakes, so I doubly appreciate your fine example of a talent that is at the core of good seamanship.
And you story particularly resonates today because I’m sitting the emergency room waiting to have a bit of a nasty scrape looked at that resulted from me being in too much of a hurry and not securing the boat properly before trying to get ashore—hurry is a dangerous thing!
As to the details, thanks for pointing out the immersion risk, and having just done the numbers for the next chapter, you are right on the cost issue.
Hi John,
I enjoy watching the latest in battery tech and have been following the different lithium chemistry options and have come to the same conclusion as you for basically the same reason. While I could convert our boat, I just can’t see a compelling reason to do it as our current system in no way limits us and it is installed and paid for.
One other thought is that there is a lot of R&D going into batteries right now and I suspect that the current crop of chemistries available will likely not be the desired ones in 10 years time at least for cars and maybe for boat house banks too. That then brings into question the issue of product support and potentially needing to replace more than just batteries when they wear out. I am open to new technologies but will wait for something to become commercially stable as well as fulfilling all other requirements.
Eric
Hi Eric,
Now that’s a point I had not really thought about, and should have. Spending close to 10K, as I would have had to, only to be told in say three to five years that no parts were available for the system would be really upsetting
Hi John
I just replaced the batteries on Rajah Laut. After much research and debating we ended up with Lifeline Golf cart AGM’s again. They main reason was lack of familiarity with the Lithium technology. The need to reprogram solar controller, inverter/chargers was also a big factor. Where we travel and plan to sail in the future might necessitate a quick change and reversal back to an older technology which would require another re-programming in a hurry.
This Spring we are land based while I convert a Sprinter cargo van into a RV. I took a different approach since I had an empty slate. For this project I went with just one main stream vendor- Victron including a 300ah lithium battery. Wow what a leap of faith but the thought is that on land I can live with and survive without AC/DC for a day or two which I am not willing to contemplate while at Sea.
One last observation after shelling out considerably for the big lithium, while it was being loaded into the truck I noticed the label on the side of the crate, Made in China, by Winston Battery Company. So I paid probably 3x the cost for Victron’s label, testing, verification and hopefully warranty versus finding my way with a cobbled together system of my own. Time will tell if I made a big mistake. Keeping my fingers crossed.
Enjoy your Summer
Hi Victor, Thank you for being a brave pioneer and trying Li-ion! I will have to make a choice soon myself. Looking at the diagram, I see there’s a relay between the alternator and the batteries. Presumably that’s for over voltage or over temperature protection of the batteries, however if there’s an over voltage condition while the alternator is engaged, and the relay is opened, won’t that damage the alternator’s diodes? I’m surprised that there isn’t an alternator field disconnect in the diagram.
Chuck
Hi Chuck
The alternator has its own regulator, not sure whether internal or external. Apparently this system has been installed on many MB Sprinters. Some people install a separate alternator but at 220 amps not sure I would need a second one.
This battery itself has a BMS. In addition there is an external BMS which in concert with the Battery Protection units monitors and controls the charging of the Li-ion battery. We will be adding 400 watts of solar panels to keep the battery topped off while stationary.
This does not really address your question but I have not heard of this being an issue until you mentioned it.
Hi Chuck,
You are right, that will take out the diodes. There are solutions to this problem but they add complexity. On boats one of the solutions is to automatically connect the starter battery, which is lead-acid, to the alternator a fraction of a second before disconnecting the lithium bank.
It’s just this kind of added complication that made me decide that lithium was not a good idea, at least for boats. Just too much to go wrong.
Hi John,
I’m surprised you don’t mention the new type of self contained Lithium batteries where the BMS is built into each battery, for drop-in replacement of lead acid batteries incl. G31 types, 12V 100Ah. So no need to add all the complex BMS and relay stuff normally required.
In Norway where I live there is a local dedicated supplier of pretty much the same thing, locally branded as Makspower (they are all from China and offered on Alibaba). I know that many are super sceptical to this sort of thing, but fact is they work exactly as advertised, and Makspower is enjoying great success locally. My son swapped out three lead acids one by one with these three years ago in my old 42ft sailboat that he has taken over, and I helped him upgrade the charging by replacing the alternator with a Balmar hairpin wound 130A unit with serpentine belt and MC612 regulator. He has now sailed 14000nm with this, incl. crossed the Atlantic twice to and from the Caribbean, and is very happy, a completely different world than the traditional setup that was before. I have also a friend with a 50 footer who did a similar upgrade two years ago, also extremely pleased.
I would gladly have chosen this also when I built my 53ft one-off boat Cheetah had I known about them in time. My Lithium battery setup is working great though (Genasun bought from Bruce Schwab, I considered Victron and Mastervolt which would have been a lot easier to source here in Europe, but I couldn’t get enough documentation on the BMS stuff to fully understand it), but as you point out in your post, the complexity of the installation makes it not well suited for a refit. Also, regarding your other concern that Lithium batteries suffer from fragilty and serviceability, I had the same concern so I designed in fault tolerance allowing my AGM stern thruster batteries to take over everything for a short period by means of a simple switch (they would not be able to take advantage of my main charge source though, but would take me to safety).
BTW You may take interest in hearing that I do not have a separate bow thruster battery bank up front. Instead my Genasun house bank powers everything up front as well, that is, a powerful bow thruster, windlass and electric headsail furler. The interesting bit is that in this situation the issue of voltage drop to heavy consumers such as these becomes reversed. As opposed to wanting a closely located battery bank to avoid many volts of cable drop that would come on top of the high load drop of lead acid batteries, I now benefit from such a cable drop from my Genasun bank to avoid too high a voltage on my bow thruster etc. Point is that bow thrusters are designed for around 21V operating voltage (24V nominal minus inevitable load drop of lead acid batteries), while Lithium batteries keeps a good 25V plus even at the very high amp loads of a thruster (appr. 300A in my case). This would overpower the gears in the thruster according to the manufacturer (Sleipner SidePower). I have even designed in a relay on my charger circuit to cut charging (which is at 28.4V) from my two big Prestolite 24V 140A alternators on the main engine when the thrusters are engaged, again to keep the loaded voltage up front well below 24V.
An overview of my electric system is posted on my boat web site,
http://sy-cheetah.no/technical.html
Of course as you can deduct from all of this, I belong in the category you call “techie owner” (yes, I have a degree in electronics/computer hardware). So my system is maybe not for everyone, but the drop-in types as described are as easy to install as any lead acid so they definitely are! Although to get full benefit from them, an upgrade of the charging scheme is highly recommended.
Thomas
Hi Thomas,
See my comment to Philippe on built in BMS. https://www.morganscloud.com/2014/01/26/lithium-ion-batteries/comment-page-1/#comment-267083
Bottom line I don’t think that building the BMS in really changes much. Each cell in say the Victron is individually managed too so whether the BMS is inside or outside the case is just packaging.
Also, the big issue not felt with by all of the lower cost options I have looked at is fire containment.
That said, as I said in the post, I see no reason that Lithium can not be used well and safely by a techie owner, but that does not make it generally a good idea that I can generally recommend, particularly with products where I’m not convinced of fire containment.
Bottom line, I trust that a company like Victron operating in a highly regulated European country will have done their upmost to make a safe system, others not so much.
Hi John,
In case it hasn’t already been mentioned, Trojan Battery just announced a lithium drop-in replacement for lead acid batteries. https://www.trojanbattery.com/
Cheers! Bill
Hi Bill,
That’s certainly interesting, but having just read through the manual, I can’t see that these batteries change many of the issues that I highlight above. For example, most boats will still need to change out their chargers and voltage regulators and plan for what happens when the batteries suddenly trip out from being under or over charged. Or to look at it another way, I just can’t see why putting the battery management system inside each battery, rather than outside connected by cables, as say Victron does, changes anything significant. Both battery managers do the same job, so, to me at least, inside or outside is just packaging.
In fact the Victron system (and others I’m sure) have an advantage over these because their BMA can tell their chargers to shut down before the battery disconnects itself. And I’m pretty sure that it’s only a matter of time before a vendor comes up with an alternator regulator that can be controlled by the BAM in the same way chargers are, which would, I think, be a much more important advance for lithium based systems.
The point being that these are not “drop in replacements” since the surrounding system will need to be significantly modified.
Hi there,
I watch the video from the cruising project SV Delos on youtube
https://www.youtube.com/watch?v=GvDCLtN22jY
which totally convinced me that lithium batteries was the perfect solution. Now, obviously the information on this site telling me that it is not that simple.
One of the reasons I found the Delos setup very interesting is that they have no more dangerous propane system onboard. I understand that all cruisers always having difficulties to get propane as the systems are different in each country. To go electric in the galley sounds like a major benefit – this has not been mentioned here on this site. Combined with solar cells the degree of independence of getting fuel and gas has been reduced.
According to Brian from Delos the change from lead to lithium was not that comprehensive and his cost calculation was in favour of going lithium as well. Maybe I have missed something?
The system is all American design and fabricated (My understanding is that no components are from China.)
I would love to hear your expertise comments on the Delos project.
Thank you, Regards, Niels
Hi Niels,
I’m a bit snowed under right now, but will try and take time to view the video at some point.
And yes, I agree that getting rid of propane is a fine idea. The problem is that to actually do all your cooking on electricity requires a huge battery bank and the charging sources to recharge it. There is no way solar will be able to come even close. Just boiling a kettle for tea or coffee once will use about half the power (about 20 Ah at 12 volts) that a typical solar array can produce in a whole day. (This can be improved on a bit with induction, but not that much.) So if you go this way, you will need a generator too, or Nigel’s Integrel machine. Either way, think US$50,000 and up for a full system capable of handling all your cooking needs with electricity.
Details of why it will cost that much here: https://www.morganscloud.com/2019/02/18/nigel-calders-generator-replacement-machine-part-2-is-it-really-better-than-a-generator/
Hi Again Niels,
I had a chance to watch the video last night. Certainly well done, interesting and informative, but confirms what I wrote yesterday: generator definitely required. You will note he mentions their generator several times and also the draw shown on the meter when they use the microwave and cook top confirm that. Also his lithium bank is not complete as shown (no isolation relays for one) and he is confused about how to limit disconnection voltage spikes. And finally, there is no mention of cost. This last omission drives me nuts. What’s the point in talking about a system without discussing cost and value for money? My guess on that stands at about $US50,000 to do the whole thing right including either a small generator or Integrel.
Hello.
I just came across this thread. Great information. Just a quick note about 2021 prices, here is the same setup delos has now for only 8k 😅
https://battlebornbatteries.com/marine-systems/
Hi Matt,
Only 8K is about the same as I priced it in 2018, albeit for a bigger bank but no cost of rewiring, so not a lot of change there. At least BattleBorn have finally admitted that “drop in” is BS and most boats will be replacing most or probably all of their surrounding system when they go lithium. Given that I don’t see a lot of point in batteries like the BattleBorn with internal BMS. Better to go with an external BMS. I still like Victron for their honest no BS system approach to lithium. And if we go with a full Victron system I think it will be a lot less likely that our insurance company will tell us to take a hike, although I would still clear it with them first.
As to Delos’s experience as a data point, just remember that they don’t pay for this stuff, it’s all free, or close to it.
Hi Matt,
Just took another look at the BattleBorn kit and noted that they are including a Sterling alternator surge protector. That’s deeply half assed way to deal with overcharge cut off events and the same way they were doing it two years ago when I questioned them at the boat show. It’s easy to be cheap when not doing things correctly.
I am sure i have read it on the site, but what is the right way to do cut off events? Its hard to parse the best way, Which article should i read?
Hi Matt,
The best solution is if the BMS tells the alternator regulator to stop charging prior to an over charge shutdown. There are other ways too. Also, to avoid a dark ship event there should be separate charge and supply busses. Another good option is fail safe relays that transfer the charging buss to a lead acid start battery. Bottom line, doing lithium right is complicated. See further reading in the article above.
Back when I was a young man and a volunteer fireman I saw what happened when a 12v lead acid battery was overcharged. The electrolyte started to boil off as a short developed in one of the fully charged cells which began to further increase the boiling off of the sulphuric acid. This is a runaway event, a battery powered China Syndrome and impossible to stop. H2SO4 fumes will ruin your day. Before very long the electrolyte was completely dry and the cells began to discharge internally and the plastic battery case began to burn and the car was quickly fully enveloped in flames. Of course you could not get near the car as the fumes would kill you.
All this happened in about 10-15 minutes. This event was caused by a faulty voltage regulator. This was also not uncommon.
Today when a voltage regulator fails the circuit is opened and current stops flowing; that is technology. The likelihood of an overcharging event in a lithium battery is arguably the same odds as with a lead acid battery. However technology has given us highly reliable Battery Management Systems not only for Lithium LiFePO4 but also Lead Acid.
A good BMS system will not charge to 100% and 100% is a pretty tough number to hit if say an autopilot is in use or any of the other electronic devices on board.
However the simplest solution is to disconnect charging at 90-95% if you leave the boat or are running quiet. 100% is simply not necessary if you have a diesel engine or generator.
The biggest flaw of lithium then becomes not deep enough for starting batteries. And that is resolved by using 2 batteries for the engine starter. That way you isolate your starting batteries from your house bank.
However when one spends in excess of EU600,000 for a capable expedition yacht quibling over a few thousand Euro for a proper power bank seems somehow cheap.
LiFePO4 battery technology is fully mature just as mature as say using a roller furling jib. I seem to recollect a time when true passage making yachts would have hanked on head sails as on they were 100% reliable! Hmmm…. attitudes seem to have changed there just a tad.
The short observation is you trust your life to technology and not just a well found hull. You depend upon GPS to keep you off the rocks, AIS to keep you from being run down, autopilot to helm the yacht so you can sleep and you also depend on 40kg of steel to hold you to the bottom. As I said before lithium batteries and Battery Management Systems are a very mature technology in no small part thanks to Elon Musk and Tesla EV’s. EV systems basically have to be idiot proof.
You are right though about Victron they are the gold standard and in the US Battleborn seems to be the go-to lithium battery.
The problem with a LiFePO4 bank is it is not a cheap solution but it is highly effective and efficient. At 29 pounds a battery it’s a no-brainer. Perhaps when Tesla builds a Marine Powerwall the price might come down except Musk just can not manufacture enough of those.
One also has to consider what else a LiFePO4 bank can do for improving the safety and quality of life aboard. Getting rid of any sort of cooking gas and having an all electric galley can only be accomplished with practicality only with a Lithium bank. Getting propane off the boat and cooking with an induction cooker is in my opinion a preferred solution. Using lead-acid is impractical.
Hi Robert,
I agree with a lot of what you say, however I’m not at all sure about lithium being mature. For example I had a conversation with the folks at Battleborn and they gave me some simply bad answers about how to set up a safe and effective lithium battery bank. For example they said that all you had to do to cope with a BMS suddenly kicking out from 100% charge was install a simple spike suppressor on the alternator. A very bad idea since that will not protect the rest of the system particularly the electronics. That’s just one example.
So, as I say in the post above, I agree that lithium can be great, but it must be done right and there are a lot of “solutions” out there that are anything but. Also, the cost of a really done right lithium system that will have the capacity to say supply a induction cook top is still very high. A buddy just dropped over $25,000 on one! Also, there is no induction oven, so for anyone who wants an oven, propane is still required. And if you cook on electricity you still have to charge that big lithium bank, so that means a generator, renewables are not going to cut it.
Seems like lithium might make sense if you are to start from scratch, or do a complete electrical system overhaul.
If it happens to be relevant to also refit the engine, it just might start making sense to consider combining the two projects: new powerline and lithium – with getting rid of that other archaic, inefficient source of pollution: the diesel engine.
https://oceanvolt.com/testimonials/arcona-380-z/
Obviously, these types of systems are far from proven in the long run in long distance sailing as of yet, but the development seems intriguing. I had the opportunity to test sail the 380Z a few years back, and I must say the the ease of handling (torque!), huge acceleration, complete silence of the engine, and the ability to run it overnight (ok, at 5 knots only, but still), galley with an induction stove (no propane), the ease of maintenance (lubricating the saildrive – zero other engine maint), no smelly diesel fuel to mess with, ease of winterizing (turn off the key) were all attributes of a system that I can’t wait to become mainstream.
The boat has integrated solar panels all over the deck, mast, and boom installed so cleverly that they seemed to not create clutter, and the best part was the sails with soft panels laminated into the fabric. Sure, no idea yet how long these last out in the field.
Also the saildrive is acting as a hydro generator while sailing.
In terms of cost: the system was around 15k Eur (around USD 18k) more expensive than the same boat with diesel & lead acid – not all that bad for a 200k boat.
In terms of weight (and this is the really interesting part): just about the same. How come? Well, the space for the diesel fuel tank was filled with lithium batteries, which of course are heavier than diesel fuel, but that was offset by substituting the very heavy diesel engine for a far lighter electric motor.
While this is certainly not mature enough a solution for the average blue water sailor, for coastal sailing it is becoming a real option. The company that created the tech for the Arcona (called Oceanvolt) has done an impressive number of retrofits to older boats already, despite still being what one might call a mature startup.
Maybe in 15 years, this (lithium, solar, electric motors) is the mainstream(?).
Hi Vesa,
Yes, interesting times. That said, for most usage profiles the barriers of fundamental physics are substantial. We have analyzed that in detail: https://www.morganscloud.com/2013/04/23/electric-or-diesel-electric-drives-for-voyaging-boats/
https://www.morganscloud.com/2014/04/13/real-numbers-for-electric-and-diesel-electric-drives/
Also, here are some thoughts on saildrives:
https://www.morganscloud.com/2019/07/03/why-are-saildrives-even-a-thing/
Hi John,
thanks for the links. Seems I still have a lot of ground to cover with past articles on AAC 🙂
The saildrive bit was all news to me, thanks for pointing that out.
Granted, hybrids make pretty much no sense at all on yachts.
I do, however, maintain that the approach taken on the Arcona does actually overcome quite a few of the (very justified per se) reservations provided in the articles.
First, there is no compounded energy conversions – just solar stored in lithium, driving an electrical motor. Adding a genset would ruin the whole deal, as happens with hybrids.
Second, the weight & space issues has, as I wrote, been solved quite nicely (lithium & no diesel engine or tank). If memory serves me right, the Arcona had like 10 regular size batteries installed in a space under one settee (that seats 3 people) where the fuel tank wold normally be. If you were not told that the boat has no diesel engine nor tank but a substantial battery bank, you would not have noticed anything until the engine “started”. Actually, the sales rep told me that they were still trying to figure out what to do with all the empty space left over in the engine room designed for the diesel engine, as the electrical motor was like 1/10 of it’s size.
Third – and this I think is the key point – the solar panel area. The only place on an average boat with loads of non-shaded area to spare are the sails. I mean, think about having, say, 50% of your sail area covered with solar panel!
I really don’t think you would have to worry about lack of charging. In fact, I would love to get such sails regardless of the engine & battery type in use.
Of course, it does remain to be seen if the material survives the test of time offshore – and naturally this would not work too well in higher latitudes outside of the summer months.
Then again, who would be sailing at 60 deg North in late October anyways (except me of course 🙂 )
Am I missing something? I installed a 540 A-hr LiFePO4 installation modeled on Stan Honey’s 4 years ago. Instead of disconnecting the alternator output I have the high voltage cutoff simply remove power from the Balmar alternator charge controller, more or less just like turning the key on a running diesel off. That should be the same as doing a field disconnect.
https://www.bluesea.com/resources/91
I decided to go LiFePO4 because of Rod Collins’ write up. They do require a change in thinking due to different failure modes. While I do agree it’s not for everyone (yet), they’ve been good for us. The Balmar SG200 with the latest firmware update has made a big difference.
Hi James,
No, not missing anything, that’s a perfectly good alternative as long as it happens before the BMS cuts the power to everything, and/or you have separate charge and load busses with control relays connected to the BMS.
And I totally agree with your assessment.
For others: James’s solution is a good one but it’s not a panacea. For example if a solar panel or wind keeps charging and the system is not set up right, the BMS will cut power to everything suddenly which could have very nasty repercussions at sea, for example the autopilot shuts down in big breeze.
Given that James took his information from Stan and Rod I’m guessing he has that sorted too but getting this right is not trivial and definitely not “drop in”.
I’m now into my fourth year of a leading brand LFP installation. The ancillary equipment, (BMS and disconnect relays have not given any trouble and as should be expected in a properly configured installation the BMS has not once activated the disconnect relays, they are there for the unexpected and if they did fail to operate then I would get an alarm from the monitoring system and could quickly and easily take over control of the battery charge/discharge manually. The point to mentioning all the above is I don’t believe the risk of possible damage done to an LFP battery by overcharging or over-discharging to be any more significant than, say, running an engine low on oil.
As to the cost, although lower now than when I did it is still high. However it is probably not as high as, for example, fitting a generator which many cruisers would be happy to do. The benefits of LFP batteries far outstrip the benefits of a generator although the latter is a great complement to the former.
Sitting in the beautiful anchorages drinking cocktails in various parts of the world conversation rarely doesn’t touch on batteries or charging, much to the distaste of some of the wives! Once you have an LFP installation you never think about energy or state of charge again, it’s there and you just use it; in abundance.
For me it’s a must-have on any long term cruising boat.
Hi Timothy,
Sounds good, and I agree if the installation is done right there should not be problems with lithium, but that’s a big if. There are now a bunch of salesman running around telling people they can just drop lithium in in place of lead acid and all will be good, and that’s BS. There are also a bunch of DIY solutions out there that scare the hell out of me. For example, many of they use cells without proper containment.
There is also always the possibility of a BMS failure, which will probably destroy the bank. So I think its still fair to say that lithium is more fragile that lead acid, particularly liquid filled which will put up with a ton of abuse before failing.
The other thing I can’t see is that installing lithium replaces a generator although I hear it said all the time. Sure with lithium you can have a bigger bank for a given size and weight, but eventually that bank will need charging no matter the chemistry. So the generator, or not, decision is all about usage patterns including overall consumption and desired quiet time between charges and whether or not we motor a lot and how often, as well as how much renewables we have, and very little to do with battery chemistry.
We have a spreadsheet to calculate that and other chapters that explore whether or not a generator is required in our online book. Bottom line it’s far from simple and requires analysis for each boat.
BMS’s are generally fail-safe, needing to be working to keep the relays closed so I don’t see their potential failure being a high risk. I do have top shelf equipment from a leading European manufacturer which adds confidence.
Battery bank size of LFP will generally be significantly less than more conventional batteries that are being replaced, it’s often hard to get the message across that energy doesn’t come from batteries, it merely passes through them. In our case we run a fully equipped 42’ cruising yacht with a single 300Ah lithium battery. My rationale for the sizing is that for the majority of the time we want to wake up to a battery that is around 50% S.O.C.
There are many boasts that batteries are at 99% by 11 o clock in the morning but for me that just shows an over-investment in charging capability, (solar).
Continuing to enjoy the content of this site. Thanks. Tim
Hi Timothy,
I agree. Far too many cruisers size their system to have the coolest and biggest battery bank in the marina or end up with silly sized solar arrays.
Also love your point “energy doesn’t come from batteries, it merely passes through them”. If one more person says I installed lithium and so I don’t need a generator I will lose it! Sure in some usage cases a bigger bank might obviate the need for a generator, but the idea of a direct simple link is like saying “I painted my boat green, so I don’t need a generator”.
I think I worded my post poorly. I was in no way advocating that an LFP battery bank is a substitute for a generator, obviously they don’t do the same job. I was trying to illustrate that people are much less resistant to opening their wallets to some items rather than others and if I had neither I would buy LFP before I bought a generator.
I have both and although the New Zealand summer has reduced generator usage to almost nil I would never be without it.
Hi Timothy,
That makes sense. I can certainly see that a larger bank capacity can reduce generator usage. For example, if we have a big alternator and motor every time we leave or enter an anchorage or harbour, the big bank will extend the time we can remain at anchor without running the generator.
That was our logic, along with having an advantageous place to put a large bank in terms of both access and ballasting.
I haven’t been sailing in some years, and I’m looking to get back to it. It’s a little bit shocking to me how much has changed.And Lithium batteries are a prime example of the sort of revolutionary changes that have taken place during my absence from this sport/activity/lifestyle.
But… Lithium batteries? Really? On a *BOAT*? Doesn’t lithium react rather poorly to water? I mean, if your boat should swamp, having it burst into flames, or explode, seems like that could make a bad situation a bit worse. Is there some reason that that isn’t a concern? I mean, no one else has mentioned it, so I *guess* there’s some reason to believe these batteries would not react violently to submersion. I’m not trying to be alarmist, my concern may reflect my ignorance, rather than any actual risk. Does anyone else know?
There are multiple Lithium battery chemistries out there:
https://batteryuniversity.com/learn/article/types_of_lithium_ion
As this article describes, some types are more prone to thermal runaway (catching fire) than others. There are two types that are however very safe; LiFePO4 (Lithium Iron Phosphate) and LTO (Lithium Titanate Oxide) are both perfectly fine to use on a boat; the first being very common and all the commercial vendors selling Lithium banks into the marine market use this type.
LTO’s also have an excellent safety profile, but are more of a niche style favoured by DIY types. (Tests have shown they’re complete immune to catching fire, it’s never happened as far as I know.)
Other factors such as a sound electrical design and correct fusing are more important factors in how safe a lithium installation is. Short answer is like everything on a boat lithium batteries do come with risks and tradeoffs, but catching fire is not really one of them.
Thank you. I had managed to fail to be aware of the different Lithium chemistries until your kind reply. I’m familiar with the Lithium Polymer batteries used in modern electronics and radio controlled aircraft… and those are just, it seemed to me, a terrible idea for a boat. I appreciate the reply. Now, I’ll go try to remedy my ignorance more completely. Be well.
Hi Philip and Karl,
I would agree with Philip. One point though that’s worth thinking about is that even LiFePO4 are, as I understand it, very difficult to put out if they do catch on fire with most normal extinguishing agents not effective.
The other thing to be aware of is that even LiFePO4 requires good containment. What scares the hell out of me is DIY yachties building big banks with no name batteries sourced from Asia that may or may not be properly built and contained.
On the other hand I think LiFePO4 sources from reputable manufactures like Mastervolt and Victron are pretty safe.
Matt has a article here: https://www.morganscloud.com/2014/01/26/lithium-ion-batteries/
Thank you, Mr. Harries, for the reply. Matt’s article does little to reassure me. I’m *so* old, I remember the ’79 Fastnet race, and one of the lessons from that debacle was: big boats don’t sink until the water is about chest deep in the main cabin, so, until the boat leaves you, stay with the boat. (Several liferafts, and crews, were lost, while the abandoned boats were recovered.) I can’t imagine mounting batteries in a box in the cabin higher than chest high. I’ve not seen the results of anyone driving their Tesla Model 3 into a river or the ocean, yet, but I imagine it could be bad.
I understand, too, that submerging lead-acid batteries is unlikely to be good for the batteries, or any thing around the batteries, but I don’t think it’ll create the same kind of emergency one might risk with Lithium batteries.
So… lead-acid, carbon-foam, whatever, still, yeah?
Lithium banks can be a huge improvement, but the changeover must be an informed, engineered choice. Ideally you need to have sufficient technical background and confidence you understand exactly what the install will entail.
Doing because ‘everyone else is’, or ‘it seemed like a good idea at the time’ (and trust me I’ve done a few of those) is not a good idea. This means that for 90% of boats at present, some form of lead acid will remain the default choice … and this is a good thing.
Having said that, as the vendors gain experience, the lithium battery market matures and yachting consumers become more confident, the trend toward lithium will continue to gain momentum. By 2030 lithium could well be the ‘default’ chemistry.
Hi Philip,
A lot of wisdom in that comment!
I have a Victron 400 AH (2-200 AH) Lithium house bank system on my boat with an AGM start battery. I also have a Victron Multiplus 120/300 charger inverter. It was relatively simple to wire and design, I received great help from PKYS on design and questions. This is a very common system for sprinter vans which are proliferating. Also, you are quite off on your costs, the price of my batteries was about 4k, not 5.5k. It was still a sizable investment, but given the weight savings, space savings, and long times between charging I am glad I went this way.
Hi Bryan,
Good to hear it went well for you.
I’m dealing with general analysis and recommendations here. Given that, I don’t consider that you got batteries for 20% less relevant to the overall point or recommendation. It’s just not practical for me to be constantly updating articles to reflect he latest prices, particularly since we have readers all over the world, so prices will always vary. That said, even if lithium was half the cost I quote, this article would still be relevant.
John
loving the great inside of your articles, but reading this I have to say that I see that many points are not really covered which deserve some credit:
I don’t work for any Lithium Battery company, nor I say everything is solved with that. But I think the above points should be mentioned in some way.
Have a great sailing day!
Karsten
Hi Karsten,
Pretty much all your points about how battery systems work are covered at some place in this online book. I just didn’t stack them up to make a case for Lithium batteries as you have. As I say in the post, there’s a lot to like about lithium and I and/or Matt specifically cover charge curve etc, but doing lithium right is both expensive and complicated and I stick by that. Lifetime cost, can, I agree, favour Lithium, but there are a lot of variables that need to go your way to make that happen.
Also lithium can have some unexpected issues. For example we are now hearing from members who have been refused hull insurance because they installed lithium batteries.
Hi John thanks for the detailed information.
I’m curious to learn a little more about the fragility you see around lithium batteries. I get the commission versus omission issue and that makes a lot of sense. However you mention something to the effect of ” if a lithium battery goes bad in a remote place you probably can’t get a replacement and with lead acid at least you could drop in and truck battery”.
Question is even with lithium if they’re toast why can’t I just drop in a truck battery? Obviously I don’t have the amperage but basic systems will still function until I’m able to properly replace things. With the victron components throughout the system, would most things be configurable for lead or lithium?
Cheers
Hi Matt,
Yes, that’s a good point that you could change over to a lead acid, although there maybe battery size issues to deal with. The other issue is that the entire system will have been designed around the higher energy density of lithium so actual functionality maybe a problem.
That said, if one designed the system with an emergency switch to lead acid in mind, I think that might be a very good idea.
“lithium batteries will be totally wrecked by just one over-discharge or over-charge event. “ While this is true it is also true most modern LIPoFe batteries now come with a BMS built in which reduces the chances you will permanently damage your battery. With normal charging or discharging. The BMS May shut down to protect the battery cells leaving you temporarily without power but once the issue that caused the shutdown is fixed and the BMS is rest the battery cells will probably be fine. (Biggest culprits are cheap PWM solar controllers always get a MPPT controller and bad alternator regulators or chargers designed for lead acid batteries) so your assessment that charging may also need updating as well as the expense of the batteries is true also. BUT if one is do a total electrical system update designing it to be LIPOFe compatible from the beginning today is the way to go even if you initially go AGM due to costs at first.
Hi Michael,
I’m aware of the function of a BMS, in fact I write about that extensively later in the article. However said BMS can fail and also there are some events that will still damage lithium batters and/or the BMS, particularly in the case of cheaper BMSs in so called “drop in” batteries, where very often the BMS is not capable of withstanding even a 50 amp inrush.
I have been communicating a lot lately with true experts on these batteries and all three of them have countless horror stories of trashed lithium batteries from a mistake.
Bottom line, nothing changes the fact that lithium batteries are far less tolerant of a mistake than lead acid. For example a AGM from lifeline will repeatedly withstand an inrush of several hundred amps without damage.
Does that make lead acid better? No, just a different set of advantages and disadvantages. But if one is going to spend the bucks for lithium it’s simply unwise to go into it without understanding how fragile they are and how dependent they are, as you say, on good system design.
By the way, I, and most experts, recommend against battery internal BMSs on a cruising boat. And said BMSs will not be compliant with the new ABYC regulations expected in 2022-23 and therefore boats with them will likely be uninsurable. (I need to write more about both these issues).
And yes, I agree that designing, as much as is possible, to accommodate lithium in the future is a very good idea. I will be adding that to the lead acid based system design we will be publishing.