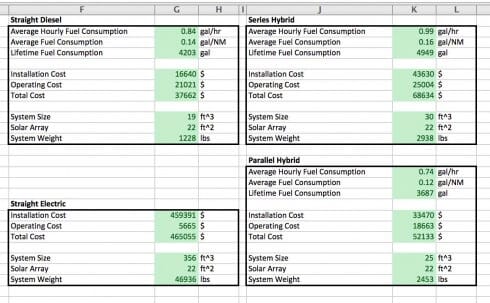
I have always believed that one of the most important things you can do in sailing, as well as life, is do some basic arithmetic before you make a decision. That would seem to be self evident, but it’s amazing how many of us (I have made this mistake too) rush into things just because they are cool and/or the latest fashion without subjecting them to a bit of arithmetic rigour.
I guess the classic error in this regard is whipping out a credit card and buying something without doing the simple arithmetic to figure out how long it will take to pay down the card or how much interest we will incur while doing so. In the same vein, investing large amounts of money in electric or diesel-electric drive options without doing the maths first can be expensive, as well as extremely time consuming and disheartening.
Ran my boat numbers through the model and no surprises. The output data passed my test of reasonableness.
The Series would cost me plus $1800 a year and the Parallel plus $600 over 20 years — doable. But I can’t find a reason to triple the complexity of my power plant (Diesel + Electric + Interfaces), aggravate my search for quality maintainers, and render resale very, very problematic.
I would really like to see the people pursuing this succeed in a manner which makes this a supportable concept from the maintenance and logistics standpoint as well as an energy conversion one. But as a thermodynamics instructor and a former aircraft maintainer, I would say it will be a while.
A quick remark concerning diesel-fuel-to-propeller math in the pure-diesel and series-hybrid cases. I noticed that shaft-power-at-cruise figures were 13,15hp fore pure-diesel and 12.89hp for series-hybrid without too much explanations for those figures.
-Pure-diesel solution uses 270g diesel fuel per KWh, does not generate any diesel-based house electricity and has an expected life of 5000 hours (perhaps 20 years with 250 hours par year…). In that case diesel fuel consumption over equipment expected life should be 4202,96 gal. I didn’t see gearbox efficiency in the datas, so I guess that the 13,15 shaft-power hp are engine power and not really shaft- power, and that you took about 98% for gearbox efficiency, which means that shaft power is the same 12.89hp with both solutions.
-Series-hybrid solution uses an electric motor with 86,71% efficiency, a controller with 98% efficiency a generator with 82,15% efficiency, and generator’s diesel uses only 240 g. diesel fuel per KWh. Grand-total for global transmission efficiency is 69,80% (86,71% * 98% * 82,15% ), but, accounting for a better diesel-engine thermal efficiency (240 g. instead of 270 g., which makes a 11% improvement probably due to reduced running hours at higher loads, the batteries being used as buffers between engine & propeller…), you get about 77,47% relative efficiency of series-hybrid vs. pure-diesel solution (69,80% * 111%)(in fact counting pure-diesel 98% gearbox efficiency hybrid relative efficiency should be 79,02%…). So diesel consumption should be about 21% more (100 – 79,02…), which means 5085,58 gal. (4202,96 * 1,21). You got slightly less (4948,76 gal.), because you considered that batteries will provide on average 0,52 KW of propulsion (green ?..) energy when motoring.
First I am a bit surprised by your efficiency figures for electric motors, controllers and generators. UQM Powerphase systems, which are moderns, but not experimental-grade electric motors, controllers & generator have figures of 92% for motor + controller and also 92% for the generator (and its controller…), which makes an grand total of 84.84% instead of 69,80%. Adding your figures of 11% diesel-engine thermal-efficiency improvement (because of higher loads for shorter times…), 2% for the pure-diesel mechanical-gearbox (not used here…) and 2,7% to account for green or shore energy ending-up in propulsion, we get about 100,54% relative diesel efficiency of series-hybrid vs. pure diesel. This won’t pay for 20659.17$ of batteries but do you need that much batteries, in fact many series-hybrid have been built without batteries. Plus, UQM PowerPhase125 motor + controller or generator + controller are about 1500$ per unit, volume prices. Makes a total of #3000$, looks to be a far cry from your #14000$ quotation.
Then I don’t know were those values of 13,15hp & 12.89hp at propeller shaft come from. As pure-diesel gearbox efficiency is not mentioned I understand that you probably took the same 13,15hp at propeller shaft for cruising in both case. Point is that the main advantage of diesel-electric transmission is to be able to fulfill requirements (here enough bollard-pull at zero speed to be able to get out of a quite bad stormy and windy situation…), with much less compromise than a fixed speed gearbox. So in our case, the efficiency of the propeller that will be able to reach the required bollard-pull value with a continuously variable transmission will in most case have a much better efficiency in cruising conditions with the same transmission (typically twice better…). So relative efficiency is not 100,54% but more in the vicinity of 201,08% which means a 10021,45$ diesel-fuel saving over equipment life.
Then do we need propulsion batteries in the case of serial-hybrids ?. Batteries can give plugin, or alternate energies, capabilities, an can also help with thermal diesel efficiency and diesel engine life-time, because they can be used to run diesel engine nearer from their efficiency optimum by storing excess energy and shutting down the engine at slow-speed (using stored energy instead). Those functionalities have a cost, and it is not very difficult to conclude in each and every use case, and to add batteries, and the number of batteries, that make sense for each user.
Last, I never said that, in the world as it is, everybody should rush installing series-hybrids in every boat. I said that considering the technics and the costs we can get nowadays, it looks quite reasonable at least on paper, and I guess that we are on a trend, not a fad, so the guys who have somewhat deeper pockets or somewhat better technical knowledges could or should not hesitate much more (“early adopters”…). For the other guys (most of us…), it might take some time before the recreational equipment industry considers it is a safe ground for you (and for them…).
Laurent
PS. in my opinion parallel-hybrid and pure-electric concern mainly, or only, comfort of use and for pure-electric, only day-sailers.
Hi Laurent,
I will try to answer your questions, hopefully I succeed.
There is a gearbox efficiency in the model. The model is broken into assumptions and inputs and this falls under assumptions so it doesn’t jump out at you as quickly but you can change it if you want. You are correct that this efficiency accounts for the difference in engine/generator shaft power. In some installations, there should be an efficiency number on the electric drive as well but most of those installations can achieve high enough efficiencies that they were deemed to be negligible. You are also correct in the end of your first statement about the little boost from the batteries. To make the model “fair”, all of the configurations end up at the fuel dock/charging station with depleted batteries. In practice, this could be difficult for some people to achieve but it gives the hybrids the best shot as a really skilled user could achieve this.
Regarding motor selection, the model provides inputs so that you can play with a few different motors. The motor that is in there right now is the motor used with the Beta hybrids and this was chosen as it is actually a configuration that someone can buy off the shelf right now. It is not the most efficient motor available as you point out but I would guess that it is one of the most commonly used motors in boats. Many people use Elco motors in marine installations and a bit of efficiency data is available for them but they do not appear to have a plot publicly available. To change the motor input, go to the motor efficiency tab and change the numbers in the left most matrix. For motors or anything else, if you are aware of options that are much more appealing than the ones included with the model, I would love to hear about it. You would just need to post efficiency numbers, size, weight and cost.
Regarding prices, these are single unit prices. For something like the Adventure 40, I hope that prices would be a lot lower. The prices in the model could be said to reflect the price of a single repower not a new production run where prices are normally more secret.
For propellers, you are welcome to put in any propeller curve you want in that tab. There is a graph that has several in there that you can pull data from. If you have data for a much larger propeller as electric propulsion proponents often suggest, you could certainly put that in there. If you manage to put in a propeller with such a high midrange efficiency that you don’t have enough torque, the model will not return values. This is very unlikely unless you choose a maximum speed that is far below hull speed so that you get onto the more linear part of the hull drag curve. It is my opinion that propeller selection is one of the largest areas for improvement in current propulsion selection.
If you don’t want batteries in the series hybrid (or parallel) part of the model, simply set the time at full power to near zero. These batteries are for peaking application so if you don’t do any peaking, they won’t need to exist. There is a limit to make sure that you don’t end up with less batteries for the hybrids than the straight diesel as that would not be fair.
Sorry for being long-winded, I hope that answered your questions.
Eric
Hi Laurent,
I think that I might have said something slightly misleading in my last comment and wanted to clear it up. While it is true that you can eliminate the batteries for a series hybrid by setting the time a max speed to near zero, that is probably not the best way to do it as that messes with your use assumptions which you shouldn’t do. A better way to do this would be to turn up the “% Series Hybrid Overrate for Cruise”. This was actually specifically intended to let you do what you want to do. 100% rating (0 overrate) means the generation system is matched to supply the full power of the motor at cruise with the engine at WOT at the chosen RPM. If you overrate it, you get a bigger generation system and need less batteries to deal with your peaking requirements. Once you increase this generation system so that it can output the amount of power used by the motor at max speed, the model will not require any batteries to meet your propulsion requirements. This “knob” also lets you play around with finding the most efficient point in the fuel map for the engine.
Eric
I think that the main question to be answered is: “might a sailboat hybrid aux. propulsion system pay for itself in saved diesel-fuel, considering different technologies and different use-case ?”.
The mainstream solution we are trying to beat is 2014 sailboat aux. diesel + mechanical gearbox with same technology level than the diesel-engines used in the hybrid systems we try to evaluate.
I think the documents you can find on Hybrid Marine site give a good approach of the problem. For instance their paper about “Propulsion methods for a 32′ auxiliary yacht”. In that paper they compare a classic “pure-diesel” system, a diesel-electric transmission (without propulsion battery), a serial-hybrid and a parallel hybrid with, as I understand it, the same diesel engine and the same propeller in those 4 cases.
They conclude (see fig. 5…) that :
– the diesel-electric efficiency is about 10% below pure-diesel in all cases (3 to 6.5 knots)
– the series-hybrid is about 60% more efficient than the pure-diesel at 3 knots and 10% less efficient at 6.5 knots
– the parallel-hybrid is about 60% more efficient than the pure-diesel at 3 knots and as efficient at 6.5 knots.
In this example, they didn’t try any “overrate”, that is, it looks like they used the same diesel-engine in the 4 cases, and this engine is powerful enough to generate all the electricity needed by the electric motor even at max. speed. I have no objection against overrating, but, if the intent is to evaluate the fuel-efficiency of different solutions in different use-case, I think that overrating makes things more difficult to understand without improving the fuel-efficiency of the solution. I understand that overrating might improve efficiency because it should increase diesel engine average load, but, you can get the same result through engine-cycling in way that is easier to understand and to simulate. I don’t mean overrating might not be part of a fully optimized solution, but I think it should not be part of a debate about the capabilities of sailboat hybrid aux. propulsion systems to pay for themselves, because it can not help to understand this point and it adds unneeded complexities.
I like Hybrid Marine approach, but I think their study is a bit flawed, mostly because diesel-electric transmission and serial-hybrid should not use the same propeller than pure-diesel and because it looks like they evaluated only fairly mature electric components instead of reasonably modern ones (electric high-efficiency from the 1960′ vs. electric high-efficiency from the 2000’…).
Hi Laurent,
I agree that the approach shown in the Hybrid Marine study is a reasonable one. To me, the most important conclusion that they came to was that above ~4.5 knots (the exact speed is a little unclear, under the description they mention 4.25 for the parallel), the best system from an efficiency standpoint was a regular diesel. The parallel had equal efficiency but the motor was sitting idle so it was effectively a straight diesel. As we have discussed in the comments to previous posts, it really comes down to how you use the boat. On a 32′ boat as they used with a hull speed of around 7-7.5 knots (I don’t see a mention of the actual boat or LWL?), I can’t imagine motoring along at below 4.5 knots for any length of time. However, some people might really enjoy this type of motoring or they might really want to save the fuel and still have the ability to motor at high speeds.
In all of these studies, arguments can be made that either a diesel or hybrid system was not optimized. It seems that one area where you feel serial hybrids should be optimized further is the propeller. I assume that you want to go to a larger diameter propeller with a lower slip ratio. When comparing torque curves, modern common rail diesels and AC motors actually have very similarly shaped torque curves, DC motors are obviously very different but I don’t think that those are what we are interested in. You could potentially run a larger drive motor (higher cost, slightly lower efficiency at cruise) than generator to allow you to get more torque (and less speed) in bollard pull situations although this is not how the systems I have seen are designed so they are really not different than a diesel. From a practical standpoint, many boats simply don’t have the room to swing a larger prop and maintain the tip clearance required for efficiency. I am not a designer so I can’t answer the question as to whether it would be reasonable to design for this in new boats. For people who like fixed props, a larger diameter one would really have a lot of drag associated with it so I think you could only consider it with a feathering or folding one.
Eric
Hi Eric.
I like Hybrid Marine approach of the problem and I also like their product offering, because I think they are nice pieces of engineering and probably quite appropriate for some use-cases.
This said, I also understand that their study is part of the marketing literature they published on their server and I suspect they went not very far discussing the issues where their products were at a disadvantage.
The first obvious shortfall I noticed in this study concern the electric motor/generator/controller technology they presented. High efficiency electric motors etc. have done huge progress in the last 50 years, and you still find electrical motors etc. dating from the 1960′, and sold in the 60′ as “high efficiency components” still sold today with that kind of arguments, while today’s “high efficiency” should relate to component with significantly lower losses (#92% efficiency instead of #85%, which means losses reduced by #50%…). I understand that their products use 1960′ criteria for high efficiency and that they also used the same level of efficiency for the electric-transmission and series-hybrid solutions they discussed, which is not quite fair in my opinion.
The second shortfall is that the main “raison d’être” of electric transmission and serie-hybrids as I see it, is to be able to take advantage of the corresponding continuously variable transmission, and to use larger propellers with carefully calculated characteristics to offer a very good propeller efficiency at motor-cruising speed and to fulfill all the constrains. I understand that they used the same propeller in all 4 cases, which I consider a serious flaw.
I don’ t think that the existing space for the propeller in existing sailboats should be a game-stopper. If, after system-optimization including careful propeller calculus, we find-out that this kind of problem does happen, it might only mean that sailboats hulls might need to be redesigned to be able to take full advantages of hybrid aux. propulsion systems. I think that current condominium-inspired sailboats are losing their marketing appeal, and I doubt that a return to 1960′ style sailboats might be a lasting solution for that problem. “Reduced environmental impact” equipments are fashionable and should remain so in the future, so I don’t think that a sailboat that would include some unusual architectural feature to obtain that kind of reduced environmental impact, should be very hard to sell.
Laurent
I didn’t try altering your spreadsheet model, because I think that spreadsheet technicalities should be addressed only after more basic questions of equipments efficiency and general logics of hybrid propulsion design have been fully understood and explained in plain english.
Considering electric motors efficiency weight, cost etc…. You must understand that “high efficiency” industrial motors are typical factory-equipment motors improved to obtain a somewhat better efficiency than usual, but “usual efficiency” in industrial electric-motors is low or very low by current standards. Corresponding designs date from the 1950′, or sometimes the 1930′, and users were most concerned by reliability and life-expectancy, not by energy-efficiency. So basic industrial motor efficiency is typically around 75%, and “high efficiency” industrial motors efficiency is around 85%. Today ‘s good volume-produced electrical cars’ or buses motors are at 92% or better, which makes 1960′ “high efficiency” industrial-motors something of a joke.
Concerning Beta hybrids, I understand that, today, you have 3 kind of electrical equipment manufacturers :
– 1) very mature ones (technology from the 1930′ or 1950’…) who sell very sturdy reasonably priced motors & generator with motor-efficiency around 75 or 80%
– 2) “high-efficiency” standard industrial equipment manufacturers (technology from the 1960′ or 1970′), who sell more expensive equipment with same standard flanges etc. than preceding and motor-efficiency around 85%
– 3) specialized manufacturers : who sell much more advanced equipments (technology from the 2000′) generally with non-standard flanges, ratings etc., mostly intended for electric cars, buses, trucks etc.. , with efficiency in the 90-94% range. The good new is that those manufacturers have been reaching volume production levels lately, and that sticker price of their equipments is much lower than 10 years ago.
4) as a side remark, some specialized real-high-efficiency motors (more than 92% efficiency…) have been on the market for 20 years or more for diesel-electric passenger-vessels transmissions but those motors are very specialized and…….very large (Converteam corp…).
Beta-Marine Elco motors belong obviously to category number 2 (“high efficiency industrial”), which is a reasonable choice if you consider that Beta-Marine purpose was to allow slow-speed for a limited time without diesel-engine noise and smoke, for a better user experience, and not really energy saving for itself. Point is that if you have an electric motor + a generator 86%^2 makes 74% and 92%^2 makes 84,6%, which is a big difference (losses reduced by 69%….).
As for the appropriate electric-motors and generators, I understand that UQM corp. is probably today the only manufacturer currently engaged in a pure-player volume strategy for type-3 electric motors and generators manufacturing in the 45 KW range, so the UQM PowerPhase125 motor/generator looks like a very good choice today. I guess that we will see many other similar offerings in a near future.
For propellers, I think you missed the main issue about series-hybrid vs. pure-diesel in our case, which is that pure-diesel have fixed-ratio transmissions while series-hybrid have continuously variable transmissions, and, concerning aux. propulsion of sailing boat, the first requirement is, and has always been, to be able to start moving the boat in a demanding wind a sea condition, for instance, lifting an anchor in a gale. Because of that you need a bollard-pull (that is a pulling-force at zero speed..) that is superior to the force that will be exerted by wind and sea on your fully rigged sailboat in those conditions. So, in the case of sailboats, you must chose propellers and gearbox ratios that will give this kind of bollard-pull with limited engine power, which is a big constrain. The same propeller and gear ratio are generally a very poor choice when motor-cruising or motor-sailing because they are very far from the optimum propeller and ratio you should use for those conditions only. With the continuously-adaptable gear ratio you get from a series-hybrid, you need much less of a compromise for bollard-pull constrains (because you can increase the gear ratio at zero speed as much as needed) and you will have a much better usage of this less compromised propeller when motor-cruising, because you can lower gear ratio at will. I guess that, with both benefits you should get a propeller-plus-gearbox-system twice as efficient when motor-cruising with series-hybrid vs. pure-diesel. This point is mainly due to the high wind and sea resistance, plus limited aux. power of sailing boats. With lower wind resistance and higher specific power, like recent Dashew motor-boats, the corresponding advantage should be lower.
Considering batteries, I think that once series-hybrid motor, generator, diesel-engine & propeller configuration have been optimized without any battery in the system, it is no difficult to make a detailed spreadsheet to simulate the possible advantages of adding batteries for pluggin-capabilities, diesel-motor thermal-efficiency improvements (using cycle at optimum load instead of continuous sub-optimal loads) & green energy usage for propulsion. I guess that “some” batteries will prove worthwhile in most, if not every case, but I think we can set aside the battery issue when deciding about series-hybrids. Batteries, when (and perhaps if…) added can only improve figures, not degrade them.
Laurent
Hi Laurent,
All very interesting, although I have to confess that I did not understand all of it (my failure not yours). However I think that we are veering off into the esoteric here in ways that really add little to the goal, which is to help people make an informed choice based on gear that is readily available off the shelf today at a capital cost that makes some kind of sense.
I also think that those that are keen on hybrid options need to be very careful not to start from that goal and then only look at ways to make it happen. That was the trap the HyMar project fell into.
The point being that arguing about tweaks to a hybrid system that would theoretically make it more desirable is pretty pointless if one does not make the same tweaks to a straight diesel system which is the baseline. For example the diesel system can be made much more efficient than Eric’s models shows it to be by using a common rail computerized engine and/or a variable pitch prop, either manual or automatic (Brunson), which also solves the bollard pull issue.
The bottom line is that HyMar dropped several million Euros trying to make hybrid systems save fuel and failed. I quote from their site:
“After many months of gathering data under different conditions and with a wide range of propellers, it is evident that, when loaded correctly, a diesel engine will always be more fuel efficient than a hybrid.”
Given that, and since Eric’s model is based on the HyMar research, whether or not hybrids make sense depends exclusively on usage profile and Eric’s model does a great job of allowing the non-technical to understand that and explore the options. Let’s not obscure that in a fog of esoteric discussion.
Point is that Hymar research team studied a few hybrid or pure-electric #”off the shelf” products obviously not made for high efficiency, but only for added user comfort in some situation (less noise, fumes etc…) and needed about 50 pages to conclude that those systems were not made for high efficiency.
Looks like established recreational equipment manufacturers and distributors were asked if they should/could/would give parts of their market to newcomers and “demonstrated” that they would not.
What surprises me most in that kind of “research” is that I understand it has been paid with my taxes 🙁
+ a diesel-electric transmission based upon UQM PowerPhase125 motors/generator, some batteries and a controller able to deliver a specified power on the propeller-shaft, adapting torque and rpms as needed, is a very straight and simple adaptation of modern serial-hybrid delivery trucks off-the-shelf technologies. There is no tweak in that system apart from the good efficiency of standard UQM components and perhaps a really optimized propeller calculus using a very basic fixed pitch propeller.
Controllable pitch propellers for sailboat aux. propulsion is very common in the 30m.+ boat and nearly non-existent in the field for sailboats less than 60′ in length. I understand that corresponding providers had ample opportunities to develop and demonstrate their offerings for those boats and did not succeed. I don’t think that none of them was both a good technician and a good salesman, so I understand that this solution was probably not that good for those boats (manufacturing costs, maintenance issues ?….).
well, I just wrote a nice long comment asking if John or someone could plug in the Wylo II system into the attached SS and display a comparison study since I lack the skills to do so. But then the spam protection, which has two numbers, one in text and one in cardinal, does not accept a text reply, meaning that the entire comment was lost!
How does the parallel hybrid work?
During low to mid power cruising (around 2/3 of maximum hull speed) the electric motor can drive the vessel using the energy stored in the battery bank. When the batteries are depleted then the main engine is started to drive the vessel. At this time the electric motor automatically becomes a generator and recharges the batteries. The extra shaft load seen by the engine during this combined propulsion and charging period causes the engine to operate with higher efficiency. Once the batteries are recharged you can then switch back to electric drive. Alternatively you can keep the energy in your batteries to silently drive high power appliances when anchored at the end of the day.
When sailing, the propeller can be allowed to freewheel. The motor/generator will then rotate and regenerate electricity to charge your batteries. This charging process does add some drag to the vessel and so in light airs regeneration can be reduced or disabled via the control panel.
If you need to punch into heavy seas or motor against the tide then the full power of the diesel engine can be used to drive the vessel. Equally in calmer conditions you can slip your lines and motor in complete silence under electric drive, later in the day, perhaps after some regenerative sailing, you can return in the same way. In the evening you can use power stored in the battery bank to silently run standard domestic appliances.
How fast can I go using the electric motor?
The Hybrid is intended for low-medium power requirements – for slipping in and out of harbour silently and with the great control offered by the high torque and instant response of the electric drive – and will deliver up to about 2/3 of hull speed in calm conditions, about 5 knots for Wylo 35.5.
How far can I go on my batteries?
This depends on boat size, the size of the battery bank and how fast you want to go. The standard Wylo 35.5 installation will give 2-3 hours use at 4-5 knots. Increasing the size of the battery bank will increase these figures.”
Seems to me the folks making the Wylo II have put together a pretty good design with similar goals to the Adventure 40. Personally I like their presentation because it appears that
a) for most short-term uses the electric motor will do find – entering and leaving marinas etc. and
b) each is back-up for the other, which is also good
c) I just like electric motors mainly because I have never liked, nor understood, combustion engines.
(I am copying this second, less well composed version!)
Hi CaperAsh,
That is a good question and the answer is that the model does not directly address the usage profile that is described in your comment. The parallel hybrid system chosen for the model is what I call a peaking system and is the most efficient way to use a parallel system that I am aware of. The advantage is that you can run a much smaller diesel engine for normal cruise which is more efficient (reflected in the better fuel consumption numbers the model should give you when compared to diesel). However, this only works when short burst of peaking are required as batteries have comparatively poor energy density so the system gets impractical if long periods of peaking are required.
The Wylo II system’s advantages to me are in noise reduction, fast house bank charging and very low speed maneuvering all of which the model does not address. From an efficiency standpoint, it will be lower than a straight diesel for most applications (exceptions being extremely high house loads or very low propulsion loads). The reason for this is that each time you convert energy, you loose some to heat so taking the diesel shaft energy and converting it into chemical energy (batteries) and back lowers your overall efficiency. As they state, the diesel efficiency goes up from the higher load but the important thing is that the incremental efficiency is below 100% so you can’t make up for the lost efficiency in the energy conversions. In fact, you would be better off leaving your batteries at whatever state they are and simply running the diesel when at a steady cruising speed.
If you want to model this yourself, you can do it as an energy problem and draw out a diagram of each step in the process and assign efficiencies. I am happy to give more detail on how to do this if you would like.
Eric
Hi CaperAsh
Sorry about the spam protection problem. I am currently working on another alternative that will allow us to remove it. It may be a month or so, but I’m committed to making commenting as easy as it possibly can be.
Just so you know, if the spam protection gets you again, you can save your comment by hitting your browser’s back button.
No big deal, J. I just wanted to let you know in case others were having similar issue. (I did do the back button but the previous post was etherized.)
That spreadsheet is impressive..
I am really thrilled to be studying this spreadsheet, not only for the numbers and what they may mean, but also for the example it sets in doing thorough planning. Thanks to all involved!
I’m afraid that a lot of this discussion has gone way over my head!
I loved the “idea” of a parallel hybrid engine installation, like the Hybrid Marine based on the Beta engines.
My limited voyaging experience has taught me that you can never have enough battery power. Lying at anchor for a few days at an exotic out of the way spot is bliss without engine or generator noise but if you want the battery power you have to suffer every so often.
Running the main engine to recharge the domestic batteries is generally inefficient and bad for the engine as it is not loaded sufficiently. Having a dedicated generator is another expense, another engine to look after and a load more space used up.
However, a charging system that fully loads the yacht’s engine and charges the battery bank quickly appeals to me – especially if it can provide silent and precise propulsion for entering and leaving anchorages/docks.
I realize that we all want something simple so I guess what I’m saying is I will want an engine optimized for my Adventure 40 as a propulsion unit but when all or some of its power is not required for propulsion I would want to be able to direct that as efficiently as possible into the domestic battery bank such that the engine remains suitably loaded and running efficiently. I also like the idea of the idling prop charging the batteries when sailing fast but stopped/disconnected when the additional drag isn’t wanted. Electric propulsion is way down the list of “wants” but if it comes in the package I’ll have it.
I’m really not sure if the discussion has addressed this question and these priorities. Please enlighten me – It’s beyond me to work it out for myself!
Hi Ian,
I think it is simpler and easier to understand if we separate the whole drive option debate from the issue of having enough power to satisfy electricity wants at anchor. And in fact the two are completely different issues. No hybrid drive system solves the problem of having enough power at anchor unless you have a truly huge battery bank. And if you have a truly huge battery bank, well, you don’t have a power problem at anchor.
In fact adding a hybrid system could easily make the electricity at anchor problem worse, not better, since said hybrid system will take up space and add weight that could be used for batteries. (Never mind using up funds that could be spent on batteries, solar panels and water generators.)
Either way, Eric’s model shows pretty clearly that a boat like the Adventure 40 being used for a typical voyaging profile would not benefit from hybrid drive, and in fact would be a poorer boat for it due to the added expense and the hit on hull volume.
So what to do? The first thing is to keep in mind that the very ethos of the A40 is simplicity and minimalism, so the start point is to minimize power requirements. After that, probably the best bet is solar and we will be providing an arch for that. Using both those approaches hand in hand will mean that a careful owner will almost never need to run the engine to charge.
Hi Ian,
Here is my take on this. First, I agree completely that one of the absolute most annoying things is to have to run the engine for battery charging while at anchor. On our own boat, we have gotten the loads low enough which combined with alternative generation means that we have only done this maybe five times but on many other boats that I have been on, I feel like I am constantly running the engine on the hook.
I would first attack your problem from the usage standpoint and not the generation or storage ones. The important thing to do here is to figure out what the usage of different items are and tackle the big ones that are cost effective (I am comparing to the cost of significantly more batteries, wind, solar, bigger alternator, hybrid, or whatever else the alternative might be). Many boats that I have sailed on have had almost their entire house load come from a poorly insulated refrigeration system which is not a hard fix if you don’t mind giving up some room inside. Also, it seems like LED lights have matured to the point where they make sense in many applications especially the anchor light which runs a lot. We don’t do a lot of computer work onboard but looking at the ratings for the power adapters and hearing from others who do it, this is probably a large draw as well.
Now, onto actually answering your question which concerns the generation side. A hybrid (series or parallel) has the ability to generate power. Be careful with parallel as the systems where the motor is connected to the propeller shaft require that the shaft be spinning to do this and that is probably not something you want to do in an anchorage but luckily, many systems have them attached before the transmission. From a strictly energy standpoint, the generator in the hybrid system is like a giant alternator in this use (for example, 10kW at 12V is over 800A). The question then becomes how much power can the batteries accept and this depends on your battery bank. Not knowing what your battery bank is, my suspicion is that a hybrid could charge it more quickly at first and as the state of charge went up, it would become equal to using an alternator. One quick and dirty way of figuring out how big the difference would be is to watch your charging current with your current system and see how quickly it takes for it to start to drop off as once it starts dropping off, there would be no advantage of a more powerful system. Keep in mind, for what you are asking a much larger alternator would work as well.
There are a few practical concerns to keep in mind in all of this. The battery bank voltage for an electric propulsion system is typically much higher than 12V, the electric cars that I have built have been between 120V and 156V which are not very high in that world and I don’t know of any systems below 48V. This isn’t a deal breaker but you need a way to make the two voltages work together like a DC to DC converter. One nice thing is that electric motors in hybrid systems are usually much more efficient than alternators (double the efficiency is not unheard of) so if you do have large house loads, this can make a difference. The article by Matt that John linked to discusses hybrid efficiency at high house loads.
I hope this helps.
Eric
Hi Eric and Ian,
We address a lot of address a lot of these issues in our Battery Installation and Maintenance Online Book.
The short version is that when we took a complete fresh look at out system we discovered that many of the default settings that our charging gear came from the factory with were horribly inefficient, even though we had the then latest in supposedly efficient charging technology.
And I would venture to guess that a good 75% of the boats out there are in the same state.
Also, the number one problem on the typical cruising sailboat is not how big your charging sources are, but rather the amount that the batteries will accept, particularly when they are 75% to 100% full.
The bottom line is that you can do a huge amount to solve these problems at very little cost by simply optimizing the system you already have.
Also, the new more efficient solar panels can help a lot since they can take care of that difficult 75% to 100% part of the battery charge curve. We have a lot more information about solar in Colin’s chapters in the Electrical Systems For Cruising Boats online book.
Hi All,
I need to make clear that this post is about Eric’s model that makes it possible for non-engineers to evaluate 4 different drive options.
We have already debated the benefits or not of these system to death and I really don’t want to go there all over again.
The bottom line is that what governs whether or not a given drive option makes sense is usage profile and that’s what this post is about.
So before commenting here on said benefits or not, please read the original post (membership required).
Comments that ignore this request will be moved from this post to the original one.
Hi All,
In rereading my above comment I realize that it’s a bit harsh, my apologies. My intent was not to stifle debate, but only to make sure that we didn’t end up revisiting things that have already been well covered and debated on Eric and I’s first post on the subject.
Comments like Ian’s above that deal with usage profile issues add a lot more to the conversion, over and above what we have already covered, and I welcome them.
Having done a lot of modeling in my years, I know how quickly these discussions can get to angels and dancing room on pin-heads. It’s a slippery slope. I try to stay of those slopes these days.
The longer I looked at the numbers, though, the more I should have looked at all the sheets even though the treatment diesel was my only interest. What I kept coming back to was the weight and cube of of diesel only system and fuel consumed.
It appears to me that the “Battery used in Calculations” is a bit light for current practice in cruising boats. When I substituted the Lifeline numbers, they returned a system weight more in keeping with my propulsion and charging plant (sans genset).
Which brings me to another point. I would suggest a sheet for gensets. Charging batteries at anchor with the main engine is certainly common practice, but it isn’t efficient nor is it particularly good for the engine. I would take a couple of years life off an engine for this in the model, or at least increase the maintenance cost. Yes, the genset has an acquisition and maintenance cost, but it burns 1/3 the fuel the main engine does during battery charging and operates at a life prolonging load and temperature.
Finally, and again just looking at the diesel implications, I could not resolve the comment about battery discharge in the Assumptions with the input field for that value. We begin shutting things off when we have discharged the bank by 20% (130AH), so the “batteries are always discharged at the end of the time away from shore power” is puzzling and scary.
Hi Chris,
The battery numbers were interesting when I looked them up. The Trojan T105’s which are the battery in the model at the start have very favorable ratings which is interesting and somewhat surprising to me. The real shock was the lithium ion batteries that are included in the spreadsheet. Their energy density by volume is not nearly as high as I expected and by mass it is lower than I expected as well although it is better than the other technologies. I know some batteries have significant unused space in the case and maybe this is what is going on or maybe it is the safety features? If you or Matt or anyone else knows, I would be interested to hear. The intention was that people looking to dig deeper would go in and change things in the sheets with multiple options, particularly batteries and motors so I am glad to see that you have done this as it can have a big effect.
That is an interesting thought about adding a genset, I will have to think about it some. I suppose you could have an input for how often and for how long the person wants to charge and that would give you your generator sizing. For people who put a premium on space, it would be an interesting trade off with batteries and fuel.
I am afraid that the wording on the batteries discharging may not be clear. By fully discharged, I mean that the batteries are discharged to whatever level you allow in the assumptions not fully discharged in the sense that you have taken them to 0% state of charge which as you state is not reasonable at all. If you only allow 20% discharge, then they will only be discharged to this amount when you plug into shore power. When comparing different systems, it is difficult to do it fairly so this was an attempt to do that as this can be a very important feature for hybrids and electrics and ignoring this would unfairly penalize them. If there is a consensus that this is not a fair assumption, it would not be difficult to modify the model.
Eric
Eric, thank you. I know how difficult this can be.
As to the genset. It is 4.2 kw, takes up the volume of 2+ batteries and weighs in at 170 lbs (call it 200 with sound enclosure and plumbing). It uses the charge controller for the charger and so charges the batteries in pretty much the same amount of time ~3hrs. Fuel consumption is on the order of .33-.4 gph depending on the depth of charge at charging start.
I will ask my battery guru, but I suspect the weight issue is just the difference between Li and Pb. Chris
I think you are addressing 3 or 4 different questions in the same spreadsheet, which might be a bit confusing and/or not very practical:
– 1) Hybrid propulsion impact on diesel consumption, and possible amortization of its equipment costs through diesel-fuel saving.
– 2) House electricity generation with classic diesel alternator, dedicated genset (classic or custom) or hybrid-propulsion system
– 3) Optimisation of batteries configurations in different cases, including technology choice & battery bank size
– 4) Use of hybrid propulsion system for other purposes than possible diesel-fuel savings (mainly improved user-comfort while navigating…) and corresponding costs.
– For question 1, I think the issue is quite different between series-hybrids and paralell-hybrids. Paralell-hybrid can be more efficient than pure-diesel when used under 4 knots and when cycling the diesel engine with batteries used as a buffer (see http://www.hybrid-marine.co.uk). Series-hybrid can be more efficient in that case & also at classic motor-cruising speed if real decent high-efficiency motors and generator are used (UQM….), so I guess that an accurate spreadsheet should precise motor-cruising hours at low-speed and expected efficiency gain because of diesel-cycling. Plus, you don’t need much propulsion battery to cycle diesel-motor at low speed in order to stay in diesel-engine efficient workload conditions. I guess that the equivalent of 2 hours worth of diesel power output should be quite enough. Additional batteries should be evaluated later as part of question 3, perhaps with another spreadsheet.
– For question 2, in Europe a big argument for genset is that they generally use untaxed diesel contrarily to main engine alternators or hybrid systems with house electricity generation as a byproduct. I think this point should be part of the corresponding spreadsheet.
– For question 3 : Battery life is generally shorter, or much shorter, than 20 years (life expectancy used in the model…) , so I think that the question of optimizing battery bank size should be studied each time some batteries need replacement and that battery size should evolve during main equipment life-time according to sailboat usage and to battery cost, which will most probably evolve in 20 years. I guess this point can be explored to some depth with a dedicated spreadsheet. At launch time, it might be a good practice to build battery-racks distinctly larger than the optimized battery size at this date.
– For question 4 : hybrid propulsion systems might be interesting for added sailing comfort (less diesel noise & fumes…), even if no more efficient and more expensive than pure-diesels. In that case you will need to buy more equipment (generator/motor + additional batteries) in order to have a better comfort and the capability to use more house-electricity. I think this is not the same issue than point 1, and that corresponding price-tag can not be below 3.000 to 5.000$, which might not be excessive for quite a few customer, but I don’t think that the A40 project, for instance, can indulge 5.000$+ on a comfort-only issue.
Hi Laurent,
I just want to correct one thing which is that the battery life in the model is different than the system life. If you look at the inputs in yellow, you will find one input is battery life. Originally, the model predicted battery life based on some cycling assumptions but the number of years that it was predicting were far higher than the life of most battery systems that I know of. The numbers that come in the model are 20 years for the system and 5 years for the batteries but these should not be considered the “correct” numbers. For that matter, as the instructions state, the initial numbers in the model are only one potential solution and they are in no way optimized at all. This comment even stretches to the other sheets such as “Batteries” and “Motor Efficiency” which have different options included in them and the user’s preferences will dictate which to use (for example, some users may refuse to use unsealed lead acid batteries for fear of the consequences in a knockdown). As a general comment not directed at you, to really get something from the model, each user needs to change all of the inputs and potentially the assumption cells as each one potentially can have large effects on the outcome.
Regarding looking at detailed analysis of battery charging, the best way to handle this would be a simple dynamic model that tracked state of charge. This model was intentionally not a dynamic model as the significant additional difficulty in using a dynamic model was seen to outweigh the small increase in functionality for the target audience. Given how low house loads are in relation to propulsion loads, the difference is very small unless you spend a lot of time charging whiled moored. If I were out to really optimize a system in an application with a lot of transients, I would absolutely build a static model like this first to get in the ballpark and then build a dynamic one. Another way to say all of this is that this static model ignores when things happen which can be important in applications like charging.
I had not realized that there was a fuel tax difference between the main engine and a genset in Europe, that is interesting. I assume that this would require separate fuel tanks as well.
Eric
1)- In Europe we have 2 kind of diesel-fuels:
– “white” taxed one, uncolored fuel, which pays full taxes. This is the kind of fuel you pour into diesel-car’s tanks or yachts’ propulsion-engines tanks. It’s current price is about 1.35€/l.
– “red” detaxed diesel-fuel, colored with red pigments, which pays only limited taxes. This is the kind of fuel you use in houses’ diesel-stoves, in agricultural tractors and in professional fishing-boat’s tanks. It’s current price is about 0.95€/l.
When in EU waters, yachts (even non-EU yachts…) must use only “white” diesel-fuel for their propulsion engines , but if you have a diesel stove in a yacht nothing prevents you from using the kind of diesel-fuel you may use in any house diesel-stove, that is the “red” one, but you will need to have separate “white” and “red” diesel tanks and the custom service may inspect your yacht to make sure that your red diesel tank can not be used to feed the propulsion engine. For tax purposes, yachts’ gensets are considered similar to stove, not to propulsion engines, so you may also use red fuel for them with the same remarks about fuel tanks.
2)- Considering batteries: I understand that as part of question 1 (possible fuel savings in case of hybrid propulsion…), you should develop the “diesel-engine-cycling at efficient workload instead of longer inefficient diesel workload” issue to find out corresponding costs and benefits depending how-much low-speed motoring is expected. As part of corresponding configuration, you will need enough propulsion batteries to store 2 hours worth of diesel efficient-workload output (minus the energy used by the propeller during those 2 hours…), those batteries may be considered as the “basic set” nearly certainly needed or justified in that kind of systems.
Then you should have a discussion about the technology of those batteries (lead-acid, lead-gel, lithium…) including amortization costs considering expected life of those batteries (including aging and max. number of cycles…). This should be part of the main issue, which should be to find-out if sailboat hybrid aux.-propulsion can pay for itself, with what technologies and in what use-cases.
As an add-on, it might be interesting to evaluate additional batteries, ,with what technology, how-many at what cost and with what kind of advantages. But, I guess that batteries pack much larger than equivalent of 2 hours of efficient diesel output might not have a very good value/cost ratio unless shore power makes a significant part of inputs.
Thank you for this information in almost non-enginerese! I was trying to do research on exactly this theme for my project, which will be a gaff rigged 26 footer. My plans were to have sizeable house banks, a (quiet) 4Kw generator, and a slow-revving (probably permanent magnet) reversible electric motor. The boat will be used for coastwise cruising, lagoon exploration, but with open water capabilities.
For someone that can manage to change a light bulb on goo days you brought the possibility closer. Now to find time to study this! Thumb suck is that the genset will run at optimum power, so best fuel efficiency. Engine will be used for manoeuvring (not many marinas where I intend cruising) and for slow motor-sailing. Also enough electric capacity for household use, CPAP achine, radio’s, computers to allow translation-editing work to continue en route.
Thanks again, also for the discussions!
I have spoken to several captains of big boats that recommend the modern diesel electric solution before the traditional solution. If you look at stadt.no , English version and the guideline there, you can see many improvements in such as less fuel and less noise. Stadt has solved this on big ships, but like John I am skeptical when it comes to small boats. However, that may be close I guess?
Hi Svein,
See my comment in answer to Ian on why it is that certain types of vessels benefit from diesel electric and certain don’t. As I understand it from Matt, the main criteria are whether or not you have high house loads compared to drive loads (cruise ship) or whether or not you need high bollard pull at low speed (tugs). As understand it, if you need neither, then a straight drive slow speed diesel will always burn less fuel on a per mile basis. This is why oil tankers, that need neither, are generally, as far as I know, not diesel electric.
Given that, and since yachts generally have neither requirement, I’m going to guess that we in the small boat community would be better off looking at ways to make the controllable pitch props that Norwegian fisherman have been using for decades more efficient and less expensive and complicated. Seems to me that Brunson are on the right track here, but there is more to be done.
Ok, John, I follow you here. An even better solution is in one of my old boats: A slow turning 4-stroke diesel at 200- 300 RPM, no gear box at all ( a gear box needs a lot of energy) and a big CPP( around a fathom diameter). My 60 years old boat is only 44 ft., 40-45 tons displacement and burns 5 liters pr. hour at 7 knots. The pollution from such an engine is lower than on modern diesels and the energy conversion efficiency better. Modern boats can not match this. It is a bit disappointing that 60 years old technology is better than the modern. I had believed it should be the other way round
1)- Another advantage of diesel-electric transmission is its capability to offer a good efficiency in a wide range of boat speeds. Large tankers are built to go directly from the Persian-Gulf to the US at 12 knots constant speed. Cruise ships often need to adapt their speeds in different legs of their cruises, often leaving a harbor late at night and entering next harbor, or next significant sightseeing location, next morning when passengers take their breakfasts. Distances between harbors being different, it means that some nights, these ship will go at full power (#25 knots), and other nights they will go much slower (12 knots…). With that kind of use-profile diesel-electric transmissions often pay for themselves easily because of fuel savings when using a wide range of speeds.
2)- Sailboats need good or very good bollard pulls, or stated another way, sailboat’s specific auxiliary power is low, or very low, the forces exerted by strong wind and sea on rigging and hull are high, or very high, and sailboats need to be able to beat wind and sea forces in strong or very strong conditions, at least enough to get the boat moving even if speed doesn’t need to be very high in this case (for instance : lifting anchor in a gale…). So, in most cases, propeller and gear ratio cannot be fully optimized for motor-cruising but have to be compromised to be able to pass this kind of bollard-pull requirements.
3) – concerning use-profiles, most sailboats are used with very different aux. power levels for significant times (slow motor-cruising, quick motor-cruising, motor-sailing…), so their use-profile is more similar to cruise-ships’ use-profiles than to large tankers’.
4)- I understand that the larger the genset the more efficient it gets (within some limits…), but I don’t think that propulsion + house-electricity gensets of large diesel-electric cruise-ships are way much more efficient than house-electricity only gensets of large pure-diesel cruise-ships, which are already fairly large pieces of equipment. I understand that cruise-ships house-electricity generation efficiency should be slightly improved with diesel-electrics, but I guess this kind of saving is less significant than point 1 in most cases.
Hi John, Eric and all,
Many thanks for your detailed responses to my post. Please accept my apologies, John, for inadvertently opening up an electrics discussion in your propulsion post – wrist duly slapped! I will read the battery and alternative energy online books.
I’m very happy to concede that a “dual fuel” propulsion system in a sailing cruiser is serious overkill when really looking for a good simple charging/domestic battery system, especially when charging capacity probably isn’t the major problem.
My situation is that voyaging stopped some years ago and the boat was sold but, as my kids grow up, the urge to go to voyaging again increases. Having recently stumbled upon this fantastic website, I have read all about the Adventure 40, the Boreal 44 and all the latest posts. I will be working through the other subject matter over the next few weeks. Please keep up the good work. Your site is an amazing resource and I am very pleased to be a subscriber.
Hi Ian,
No worries on bringing the electrical issues into it. They are perfectly relevant since supplying house power is often touted as one of the benefits of hybrid systems. Unfortunately that only really works economically, when compared to a simple alternator, if the house loads are very high in relation to the drive loads. This is one of the reasons most cruise ships are diesel/electric and most oil tankers are not. Matt does a great job of explaining this on his site on the post we linked to.
The point about “good efficiency over a wider range of boat speeds” has been mentioned a few times.
Cruising boats do not have to be efficient under engine over a wide range of speeds or loads. When they’re motoring for long periods, they’re usually within 20% of their design displacement and within a 2, maybe 3 knot window of comfortable speeds. It’s a narrow enough operating regime that you can optimize a purely mechanical drivetrain to perform very well.
These boats are only operated outside that “standard cruise” condition occasionally and for short periods- half an hour to get out of an anchorage here, an hour of full power to claw off a lee shore there. The powertrain must be capable of doing those tasks, but efficiency is only really important at cruise.
Sometimes a wider range of efficient speeds, and/or a better bollard pull, is called for. In these cases, a controllable-pitch propeller can usually accomplish the same improvement as a D/E hybrid, for less money and taking up much less space.
One case where diesel-electric starts to make sense is if you need the electricity for other things as well. At some point it becomes easier to just have a heap of generating capacity that you can switch to wherever the power is needed. Long range cruising boats, power or sail, usually have non-propulsion loads an order of magnitude below that level.
The other case where I recommend hybrid power is as a mostly independent, auxiliary system for creeping around at low speeds. A river/lake fisherman is the classic example; he’ll carry a 100hp engine to get to the fish and a 1hp electric drive to move around silently once he’s there.
I understand that the “Millenium” series of cruise-ships built by STX-France and now owned by RCC were originally engineered with the assumption that they would sail with “a narrow enough operating regime” where engineer could “optimize…drivetrain to perform very well”. Accordingly they were fitted with combined-turbines (COGAS) plus electric-pods propulsions. Combined-turbines being more efficient than diesels in a narrow power range. House electricity was generated by dedicated large diesel gensets.
The initial choice of electric, instead of mechanical, transmissions was supposed to bring additional savings on hull shape due to the electric pods, and additional functionalities because of those pods (maneuverability, propellers efficiency…).
As a conclusion, RCC lines had to engage into expensive re-motoring of all the units of this class because they found out that more recent cruise-ships with diesel gensets for propulsion made significant fuel savings on typical cruises, considering that real propulsion-engine use-case were significantly different from STX assumptions when those ships were built.
Nowaday those ships have all been refitted with large diesel gensets as additions to COGAS turbines, and corresponding significant fuel savings are due to better fuel efficiency when cruising at half speed, which proves that they do cruise at half speed reasonably often.
I don’t think that those new genset are significantly more efficient than initial house-electricity-dedicated diesel gensets, but I understand that some of the house-electricity genset have been discarded to make room for the new ones, which were mainly intended for propulsion.
Generally speaking, cruise-ships advanced propulsion systems problems have triggered some acrimony between a few shipowners and a few shipyards and some bad press too, so it should not be very surprising to find some strange ideas about corresponding debates in todays litterature….
Hi John, I have some remarks: Laurent thinks that there are no controllable pitch propellers for small boats. In Scandinavia CPP has a long tradition also in small boats. There are many manufacturers of CPP and you can get a lot of systems. They can be operated by a mechanic handle, a small hydraulic pump or by an electric joy stick. The pitch can be adjusted at full speed and some of them can be put in a zero position when sailing by sail only. To your A 40 West Mekan has a system that is relevant, it is not expensive but robust and can go in zero. The seize (diameter) of the propeller is of vital importance to fuel economy. With CPP you can have a large propeller with little pitch and high efficiency and lots of power.
Laurent believes that there is only one type of diesel fuel (with or without color). In fact there are many types all the way from crude oil to car diesel with up to 40% kerosene (paraffin). Most common in shipping is Marine gas oil that is also sold with or without color. MGO price in Europe is 50-60 cent, much cheaper than Laurent says (90 cents). This must also be considered when doing calculations.
It also has a practical side: In remote or cold parts of the world you often may have to choose between MGO or Kerosene-diesel. The problem is that a modern common rail computerized engine will run badly or not at all on this types of diesel. Two large boat builders in Norway had last year a brake down on new diesels of around 35%. The manufacturers says this is because of wrong diesel quality in use. In the A40 I would use a traditional engine. In one boat I have crude oil fuel pumps. They work good on any kind of diesel fuel and are very robust. Each cylinder has one pump that is separately operated, so in case of brake down I can in principle run on one cylinder. This engine consumes 156 grams/HP/hour while the common rail diesel has problems to get below 200. In your A40 I would not have a common rail, but a traditional engine. To install crude oil fuel pumps is probably an overkill in such a boat.
I read above that the loss in a gear box is 2%. My experience indicate that some times it is up to 30% and often 20%. That is way tankers do not use a gear box, but a slow turning engine. There are slow turning small diesels without gear box. But they are heavy. To the A40 I would give the gear box some consideration. Remember also that a stiff an strong fundament of engine and laser alignment of the drive train is an easy way to reduce fuel consumption, noise and mechanical brake downs.
All valid points, Svein. One caveat, though, about gearbox efficiency.
Typically, you lose 1%-2% for each shaft bearing and 2%-5% to the gearbox (including its internal hydraulic pump, if applicable). If you are losing 20% of the power in the gearbox, then the gearbox is seriously defective or damaged.
20% of the power output of a 40 hp auxiliary engine is 6 kW, or 20,000 BTU/h, of heat being dumped into the gearbox. The gearbox housing would be hot enough to fry hamburgers, not to mention its seals and lubricants.
Hi Matt,
I worked a few years for a company doing laser based alignment on rotating shafts. We did this on everything from new super tankers in Korea, to Navy ships, large power plants, oil rigs and also yachts. On professional new ships this were easy, but not on yachts. Yachts often have a lot of vibrations, a bad fundament, soft rubber mountings and a hot gear box. Rubber mountings may increase the vibrations a lot compared to a fixed engine on a strong fundament. The producers of small gearboxes are aware of this and they have given their boxes a good cooling system. It is often tree different cooling systems: A fan on the flywheel to give air cooling, saltwater cooling of the box itself and salt water cooling of the gear oil. A gear box has often a better cooling system then the engine. This way the gear box will not become as hot as you think, but there can be many other serious problems in the drive train. I saw a lot of them: Salt water coming in, leaking gear oil, leaking engine oil etc. Some of the salt water leaks were very serious and nearly sunk the boat. On yachts in a state like this the owner would normally just do the minimum repair, put the engine back in the least bad position with the smallest vibrations. Only one owner ordered a complete reinstallation of the engine and the drivetrain. This yacht became very good. But it is my experience that the typical yacht is often loosing a lot of energy in the gear box and the drivetrain because the installation of the engine is bad.
1) – about controlable pitch propellers, I wrote “controllable pitch propellers for sailboat aux. propulsion is very common in the 30m.+ boat and nearly non-existent in the field for sailboats less than 60′ in length….” . I insist it is the case in Europe and in the US as an average. It doesn’t mean that there is no decent offering in that field or that norvegian less than 60′ sailboats might not diverge significantly from european average, but I understand that CPP propellers didn’ caught with those boats and, it looks very dubious that they might make significant progress in that market in the near future. I have no clear explanation for this problem because this kind of solution seems technically appropriate for many use-cases. Perhaps they have acquired a reputation of hard to maintain pieces of equipment, or perhaps they are caught into some market-positioning dead-end (most sailboat owner might be uncomfortable with CPP basic ideas…).
2)- If you are a private sailing yacht owner in France you may/can buy only 2 kind of diesel-fuels, mostly because of regulation, but also sometimes because of practical considerations. One is the standard car-type diesel-fuel you are supposed to pour into modern pure-diesel saiboat tanks (in France we call it the “white diesel”), the other is the standard agricultural tractors or house-diesel-stove diesel-fuel you are supposed to use in agricultural tractors or diesel-stoves (in France we call it the “red diesel” because it is dyed red). Most of the times, they differ only by tax-levels and color. The price for red diesel in France is currently 0.95€/l. If vou are a commercial-cargo owner, you will be able to buy other kinds of fuel-oils (bunker, crude oil etc…) and you might also be allowed to buy fully-detaxed classic diesel-oil (“red” diesel is only partly detaxed…) , but private yacht-owners in France are strictly forbidden from buying at this price, even if foreign-registered…..
3)- I took 98% for gearbox efficiency to use somewhat optimistic figures for pure-diesel solutions in order to be fair when comparing with hybrids. I agree that real figures should be closer from 95% but the UQM electric motor I quoted also needs a fixed mechanical reducer and thrust bearing with about 99% efficiency, so I guess that a difference of 2% in favor of the hybrid solution should be a bit pessimistic for the hybrid, which was my intent.
Hi Svein,
You bring up several interesting points. I am glad to hear that you have a good selection of CPP’s, I wish that we had them here. I have a bit of experience with the old Sabb CPP’s which were pretty cool. One interesting difference is that you seem to be having lots of problems with the new common rail engines whereas they seem to be more reliable here. A diesel mechanic who does a lot of work for the Maine lobsterboats joked to me a while ago that common rail engines were putting him out of business as he was seeing many fewer break downs and almost no large failures requiring rebuilding or repowering.
The actual efficiency of the diesel engine in any of the configurations that we are discussing is important as you point out. The most efficient engines in the world are the slow turning ones in large ships which can have over 50% thermal efficiency. Our small engines are no where near that for several reasons. If you look at the fuel island plot for an engine, you see that at WOT, the most efficient speed is very close to where peak torque is generated. This makes sense as designers try to keep cylinder pressure constant at WOT so you will have the highest torque where you are the most efficient. As you back off on the throttle, the most efficient point decreases in rpm until you get to idle. If we only cared about fuel economy, we would be running all of our engines a lot slower but we would also have less maximum power available so we would need to increase size to do this. I suspect that this is the reason why we don’t see people doing this as it would cost more, take up more space and be heavier and frankly, I don’t think that most people shop based on efficiency. Going to a true low speed diesel is interesting and could be the subject of many long discussions. The model does let you play with this a little bit as you can go into the “Diesel” tab and adjust the “Engine RPM at Max Speed” (it will rescale things so that you use a different part of the fuel island plot but it doesn’t do anything to size or cost as that would require too many assumptions).
Eric
Hi Svein,
I have been unable to get information about such small CP propellors. Hundestadt and SABB both told me they do nothing under 50 or 100 hp. I am sure a few names of suppliers would be welcome.
I am looking at a non-electronic Kubota-type diesel genset, with large house bank and electric motor turning a large propellor, but to find that is not so easy! In the islands the diesel is often contaminated, so modern high-efficiency engines are trouble.
Hi Coen
Try this address: westmekan.com
I bought a West Mekan CPP system some years ago mainly because it was the cheapest one I could get. It worked well many years when fishing in Lofoten. This boat was small, 27 ft, with a light high speed engine of 3600 RPM, 36 HP, gear reduction 1:5 and as big a propeller as possible. My advice: gear reduction can be increased and also propeller diameter. I have tried such boats with a reduction of 1:10 and it is very impressive. However this has a practical side: Most boats are constructed to have a small propeller. Than an advanced CPP system is not worth its price. To exploit a CPP system you need a slow turning and big propeller. And it should be possible to put in a zero position for sail.
Hi Eric, it is interesting to hear your opinion. As you say most people do not shop efficiency, but if you cruise in the arctic you have to think about this. In the arctic summer there is often little wind and long distances. In a small boat fuel economy can than become critical. I also believe that global warming is a serious problem that all of us have to help solving. A yacht with plenty of pollution is no good.
I am a big fan of CPP and find it strange that most sailors do not use it. With CPP and some joy sticks on the boat you get a lot of power and control of it. You really feel in charge of the boat.
The problems with common rail in Norway is interesting. Producers of engines say it is because of the many different diesel fuel qualities. I think they have a point here, but I also think it is because of long range high speed motoring. Too much energy in a small motor can create a over heat problem that leads to brake down. A slow turning diesel will not have such a problem. So the explanation of no problem in Main with such engines can be cultural: Norwegians go long distances at full speed while in Main you do not. With a cruising yacht in the arctic you can become forced to behave like a Norwegian by nature. Full speed ahead for 3 days. In the arctic you have to accept any diesel fuel that is offered and often you do not know what you are getting in your tanks. That’s way I am skeptical to common rail in A40.
The future of small slow turning diesels is dark. I am glad I have one. But still Grenaa is able to produce the fabulous 3 cyl at 165 hp. My neighbor has just got one and it is fantastic. His 49 ft and rather heavy boat makes 8,5 knots at 5 liters. And it will probably do so for the next 50 years even at full speed.
I won’t dispute any of the fine research that has been done here or by the folks at the cited links, I’d just like to point out a few things.
1. Serial hybrid offers the ability to move your generator to a location that would make a standard shaft drive impossible.
2. If you ignore some of the cost it would be possible to have two generators for redundancy.
3. Electric motors are cheap enough that two can be used w/separate controllers for further redundancy.
4. Electric motors can be attached to the shaft with a belt providing the weak point.
5. Even small amounts of current (100-150 Watts) put from your solar/wind to the propeller when sailing in light air can have a noticeable improvement on hull speed.
None of those are, as has been brought up, the right things for the all people or reasons to make things more complicated. I think the most interesting one for thought is number 5, next time you are in light air making about half of hull speed try running the engine in gear at idle and see how much hull speed you can get (obviously not for a long time or anything I know what this will do to the engine, just as an experiment).
Hi Andy,
The redundancy point is an interesting one. My thinking would be that we sailors already have adequate redundancy in the form of the rig. Also a properly installed and maintained diesel engine is amazingly reliable. For example, in my entire voyaging life I have never had a diesel engine fail me in a way that I could not fix at sea.
Also, even if a person did want power plant redundancy it is only fair to point out that for most usage profiles two small diesels would be cheeper, take up less space, and be more efficient than a serial diesel electric system comprised of two generators and two electric motors. And if both engines were fitted with Bruntons props only one could run in low speed cruise situations.
Finally a much better sacrificial drive link than a belt already exists in the form of a Drivesaver.
The point of all of this is that I think that it’s really important when evaluating new technology to rigorously compare against an existing technology base line.
I agree completely with you on the reliability of a simple diesel with a good fuel system and I am not advocating a switch to hybrid in all (or even most) applications, just bringing up some of the things I’ve seen. For instance ReGen Nautic converted a Grand Banks 42 called Watt Power and claims to have tripled her cruising range on the same amount of fuel. The system they used was expensive and complicated with a huge battery bank so it’s not really a comparison to other applications, but it is interesting.
Many trawlers have a backup electric motor that is attached to the shaft with a belt and can be run directly off of the generator as an emergency propulsion device. These boats all have generators anyway so this is actually a cheap add on, but a similar system could be used on any sailboat that has a generator. Something similar might be considered if it was fed from solar in that putting that energy to the shaft could increase speed in light conditions (go ahead and say “that’s not sailing”). I have seen numbers (from people who advocate hybrid so take with a grain of salt) that they have seen that a boat going to weather in light air at 2-3 knots can be sped up to 5 knots with as little as 150 Watts.
Again none of this is meant to be considered in something like the A40, but I do like hearing experienced people giving opinions on things that I have considered/am considering.
Hi Andy,
All good points, and like you I’m very interested in exploring the alternatives. However, the key I think, as I say in the post above, is to do the numbers. That’s why I was so excited when Eric volunteered to create the spreadsheet model because it clearly demonstrates that claims like tripling cruising range on the same amount of fuel by installing diesel electric systems are, with most usage profiles, absolute rubbish. And this clarity that Eric has so kindly provided protects people like me who don’t have engineering training from being taken in by extravagant claims that typically don’t take into account said usage profiles.
For example, it might be possible to triple range on the same amount of fuel on a trawler by having a huge battery bank—think several tons of batteries, as Eric’s model clearly shows—and stopping at a marina every night to charge off shore power. But does that fit your or my usage profile? And even if it does, what about capital cost, space used and the cost of a marina berth with a 50 amp feed every night. What does that do to the numbers? Eric’s model allows the rest of us to explore that.
As to doubling speed with just 150 watts, well let’s do the numbers. Let’s see, 150 Watts is 0.2 of a horse power. Do we really believe that less than a quarter of one horse power is going to give us 2.5 knots of speed increase while sailing? I know my answer to that, and it’s based on a lot of experience motor sailing on a lot of different boats!
And I suspect I know the game being played here: The boat had a large three blade fixed prop that was locked in place. And letting said prop spin and giving it a little push with 150 Watts is going to result in a good jump in speed, which increases apparent wind and that in turn increased speed. But that has little to do with the benefits of electric drive since the same can be accomplished by fitting a feathering or folding prop, and that will work at night too.
I too suspect that the numbers that are put forth by companies trying to sell their systems are subject to all sorts of trickery as well. Indeed the GB conversion is way out of line with the feasible (100KW generator for example), but it would be interesting to see someone do independent testing.
Just as we can do the math to determine the theoretical hull speed of a design before we put her in the water and still be surprised that our numbers were off, all of the math as to how a hybrid system will perform is theoretical until tested. There are a few interesting owner testimonies on Electroprop’s website, including a Shannon 38 at 18,000# that claims 2 Knots at 400 watts up to 6 knots at 8.5KW with essentially a doubling of power for each knot (almost 4 knots off of a 2KW generator). They also claim that they are going to do a refit on Godspeed (a Steve Dashew aluminum 80 footer).
Usually people are quick to complain about things that don’t work the way they are supposed to, and while I wouldn’t expect a manufacturer of these systems to put this on their website, I find very few complaints online from people who have converted. I also acknowledge that a vast majority of these boats are in the 30 foot range and are primarily day sailors (which unfortunately is more of my current situation, the kitty isn’t quite built up enough yet). It is also perfectly clear that this type of thing will almost surely destroy any resale value of a boat again making it not a good idea for many.
HI Andy,
I would caution against classify numbers provided by an engineer of Eric’s caliber as “just theory”. Sure they could be off by few percent, but they won’t be wrong by enough to make the extravagant claims of diesel electric proponents right.
And, by the way, modern velocity prediction analysis is pretty accurate too.
I think the reason you don’t hear many sad stories about hybrid systems is the very human tendency to ignore facts that indicate that one has been had.
Hi Andy,
You are absolutely right that there are many other factors that have not been addressed. How important these factors are will depend on who will be using the boat. For example, some people don’t mind a noisy engine and just want to get there quickly while others will want as quiet a system as possible with speed not being a big concern.
One of the issues that I have seen come up a lot in debates over propulsion systems is that some people don’t compare similar systems (this is a general comment aimed at no one in particular). For example, you will often see someone thinking about going to a series hybrid system with plans to use a 2 kW Honda portable generator as the power when the system would be replacing a 30 kW diesel, obviously these systems won’t perform the same. For my own preferences, I prefer to think of it as how fast do I want to go and for how long and then figure out what system will meet that need rather than picking components and seeing what they will do.
Boat speed is incredibly important in all of this as you note in a later comment. Going with the numbers from the Hymar report, the Malo 46 only takes ~1 kW to go 3 knots and takes 3kW to go 5 knots in calm water. Note, your propeller is going to only be ~50% efficient so the engine/motor power will be about double these numbers. If you are willing to go a lot slower (there are comments on Electroprop’s website about 3-4 knots being ideal for their system), things can look very different. Electric drive systems do have an advantage for people who want to normally motor slowly but need the ability to really power up for a few minutes as they have better turn down (I have generally referred to this as peaking ability in our discussions). If you do an apples to apples comparison with a system that doesn’t need the peaking power, the hybrid advantage goes away although range for a straight electric will be greatly increased so they look more appealing. It should be said that these comments are for a monohull, multihulls have a somewhat different power curve.
Eric
Eric, John,
I don’t in anyway dispute the math or the engineering that Eric put into the tool and think it’s incredibly valuable. I am used to seeing over powered boats and in that context I think there may be a theoretical difference if usage patterns are adjusted slightly. If the diesel isn’t being pushed then there is some loss of efficiency, and if it’s sized to go beyond hull speed then there is definitely an inefficiency inherent to the system. If a boat has a theoretical hull speed of 6.5 knots, and can get there with 25HP many people wouldn’t feel comfortable without the 40HP (or the 50+ that I’ve seen in a Westsail 32) engine that they have for the ability to power quickly out of a situation.
I completely agree with comments here and elsewhere about a fast passage being a safe passage, as always there are tradeoffs when efficiency rears its head. It also depends a little on cruising grounds and distances to be covered which are much lower in Baja than up north so speed can better be sacrificed for efficiency. Obviously the usage of the vessel, and the maximum power the sailor wants, have a lot to do with what the “best” system is for each user.
If we imagine a serial hybrid system that is capable of powering the vessel to 85% of hull speed on one generator, with “peaking ability” provided either short term from batteries or longer term from a second generator, and given a sailor who is comfortable with this usage, and add a heavy amount of creature comfort desires at anchor, then we get back to the points that have already been discussed.
Thank you both (and everyone else who has contributed) for helping me to work through these thoughts and sorry if it took me having to say things that have already been discussed to help work this out in my head.
Andy
Hi Andy,
Not at all. I have enjoyed and learned from our discussion. Your comment really says it all: it all comes down to usage profile.
By the way, I’m a big proponent of smaller engines in sailboats. And, in fact, have put my money where my mouth is and into the bargain enjoyed substantial fuel savings.
I think that the question of electric aux. propulsion is very different if you use “high efficiency electrical components” as defined in the 1960′ (about 85% efficiency) or “high efficiency components” as should be defined today (about 92% efficiency).
In the first case, when compared with classic diesel engine + gearbox, you can have only marginal efficiency gains in limited cases, like motor-sailing or “peaking power” cases. At normal motor cruise speed, the combined energy loss of a serial-hybrid electric-generator plus electric motor vs. boat gearbox is about 25% (100 – 85%^2 – 3%), which should be about the same value as the average gain you should expect with the variable transmission and a correctly optimized propeller. The global efficiency gain of this system should be limited, but a correctly engineered system should be no less efficient than classic engine + gearbox, with other possible advantages, like silent motoring at low-speed, better house-comfort, or the capability of to use shore-power in short cruises.
In the second case the combined energy loss of a serial-hybrid electric-generator plus electric motor vs. a gearbox is about 12% (100 – 92%^2 – 3%). Depending on the use-cases and the cost of this electrical equipment, this could be a complete game changer.
Unfortunately, the vast majority of solutions you find today on the market belong to category 1, which is a bit surprising because real-modern-high-electrical-efficiency motors & alternators are already manufactured in volume by companies like UQM or Tesla.
Personally, being an electrical engineer by education, I do believe that a prototype 45KW hybrid series with UQM motor + generator a 45KW Kubota or similar + 80KWh of lithium battery should make sense today for me in my boat, but I also understand that I might feel a bit alone when dealing with integration and maintenance of such a system.
Looking at the A40 project, I think that the targeted budget and the project time-schedule are probably a bit too short to consider this kind of solution on a commercial (non-prototype…) basis, but, with slightly more money and more time to spend, it could become a reasonable option.
Laurent,
As it took me a while to come to it as well I think that there are definitely user profiles that would see a benefit but they are only present if one demands the modern definition of “enough power”. Anything that we do when we start with diesel is going to involve burning it so unless we want the heat and the smoke we have lost much of the efficiency already. Once we convert it to rotational energy the question is if it’s more efficient to deliver the exact needed amount of power through a transmission or by converting the energy from rotational to electrical and back to rotational. If the diesel is running at its maximum efficiency as is the case in a generator and in a properly sized aux diesel then it doesn’t seem to be the case. There is a case to be made that creating a larger amount of power through a generator is more efficient but then we have losses in the storage system for the electricity.
I do think that if a large amount of reserve power, sprint power, peaking ability, or whatever we want to call it is desired the hybrid system makes much more sense, as does the system if you are going to be running air conditioning most of the time anyway.
The lightest numbers I can come up with using a Tesla battery pack and Kholer generator of your specs is still over 4,000 pounds and that doesn’t include the motor, controller, charger, etc… I doubt that there is that much weight in the budget for something like the A40, never mind the money.
Andy
The main point about efficiency of sailing yacht series-hypbrid aux. propulsion vs. diesel + gearbox,is due to the poor adaptation of propeller and propeller rpm in classic motor-cruising conditions and to the poor efficiency of diesel engines in same condition.
Propeller & gearbox need to be able to move the boat forward, even if slowly, in very bad sea and wind condition (for instance lifting anchor in a storm…). This implies that same propeller and gearbox will be typically at least #25% less efficient than optimum than if they were fully optimized for motor-cruising.
Diesel engine will typically operate at 1/2 power, which means a thermal efficiency about 5 or 10% less than optimum (at 80% of power). Those figures combine, which means that typical sailboat’s diesel + gearbox will be about #30% worse, when motor cruising, than the optimal (smaller) diesel connected to the optimal gearbox & propeller for that use case. You can’t/shouldn’t actually use that engine and propeller in a sail yacht because it would be dangerous in bad or very bad weather.
Series-hybrid take can take nearly completely care of those 2 problems at a cost of a loss of efficiency due to conversion from mechanical energy to electricity and back to mechanical energy. So the point is not a point of opinion or similar, it is a point of electrical efficiency: can your electric alternator & motor lose less than those #30% you loose with engine + gearbox and still fulfill all constrains (including storm constrains..).
Answer in no if you use 1930′ electric technologies, yes but with limited margins (#5%) if you use 1960′ electric technologies and yes with much better margins (#17%) if you use 2010′ electric technologies.
Those figure concern normal motor-cruising speed. If you consider half-power motor-cruising of motor-sailing, modern serial hybrid technologies can get double diesel+gearbox efficiency or more, because in that case diesel+gearbox propeller efficiency & thermal efficiency are worse, or much worse than the figures I gave.
Considering equipment cost and weight, modern volume-produced electric alternator and motor are neither expensive nor heavy (watch UQM products…). The only possibly heavy and expensive part might be the battery (depending the size…). I think that you will very rarely need more than 2 hours worth of diesel-engine optimal output (80% max.) minus the power normally needed in slow-motoring, let-us say 25% of max output. That makes 55% of max engine power for 2 hours, or for a 45kw engine (big boat…) about 50 kw.h.
50 kw.h. in lead batteries is about 50 * 80 A.h. which is about 1000 kg or about 2000 lbs. (if you use lead batteries, you wont be able to use 100% of their capacity…). Using lithium battery, as I suggested, weight should be less than half that value.
So, hybrid-series make an obvious sense when using real high efficiency electric components (#92% efficiency) and less, or much less sense when using 1960′ criteria high efficiency electric components (#85% efficiency) . But, event in this case, using perhaps a 50kw.h. nominal 25kw.h. really usable, lead battery, I guess you could find some use case where this system could be justified. Guess that in that case the hull should be full-bidged to be able to use battery as keel weight, but anyway, I never argued for 85% efficiency component plus lead batteries system, I argue for 92% efficiency plus lithium. It is a pity that none of the integrated system you find today on the market belong to this category.
Hi Laurent,
Good summary, thanks.
One issue, anyone considering Lithium batteries should first read Matt’s excellent article on that technology.
Fascinating discussion. I learnt a lot, but I wonder if we are not staring at absolute efficiency figures, and forgetting that most of the sailing compromises are sub-optimal compromises. Does one really motor at maximum efficiency revs? I am looking at a power plant that would enable me to have minimum continuous power (for my hull that would be about 8hp) and a means of ‘peaking that up, to say 10hp for a short while, off a battery bank. Research so far has not been able to deliver a motor-generator of any useful efficiency. So I an looking at a diesel engine, a generator and an electric motor, Getting a little complicated, then it begins to look better to just have a small diesel. Still, a hybrid should be feasible. I think.
Hi Coen,
You are correct that we can’t look at peak efficiency numbers, we need to look at them at our actual operating point. The model actually directly addresses the case that you describe and it looks at the efficiency at the operating point by using lookup tables instead of just a max or average number. If you want a diesel that runs pretty much flat out at cruise and then an electric motor to boost you above that, you can use the parallel hybrid inputs and set the overrate low (you won’t be able to go to 0% as the power curve of the engine is such that you will have less than max power at the cruise rpm which is necessarily not your max rpm). If you set this cell as low as you can go while the model still works, you will have your engine running full throttle at cruise. The model will then tell you what the system looks like. The reason that the overrate “knob” is there is to allow people to experiment how important the sizing is and what the tradeoffs are in terms of size, weight and cost. If you really want a full understanding, then putting in different motors and batteries will also have large effects.
I hope that this is helpful.
Eric
Hi Eric,
Thank you, I did try the model, and found it very interesting. Now comes my problem: turning that into a system I can put into a boat in say four months. Are there practical motor-generators on the market? An interesting hybrid go-kart I saw ion the net uses a lawn mower motor with centrifugal clutch and a motor car starter as generator and motor when the engine is switched off. Simple, no controllers, everything purchasable off the scrap yard shelf. DC, compatible with the normal battery banks. Most small, commercial generators produce single phase AC. My non-engineering logic prompts me that a single phase AC motor should work in a sort of direct drive option. But are there generators that you could also link, perhaps by belt drive, to the prop shaft? What type of motor? I wrote to a few manufacturers with no replies. Perhaps members could suggest some possibilities?
Hi Coen,
Reducing this to practice takes a very careful study of what is actually commercially available and doing some system level engineering to make sure that it will work properly. On a high level, for a parallel hybrid (assuming we are talking electric and not hydraulic or something like that) which I believe is what you are interested in, you need an engine, a motor/generator, a controller and an accumulator (usually batteries) plus several smaller components such as contactors.
One option is to get a prepacked system from someone like Elco or Electroprop. I would hope that these systems have been well engineered and it will certainly be easier for you to do.
If you want to do it yourself, I would recommend carefully studying what others have done including boats and vehicles. AustinEV has an album that includes a huge number of EV’s so you can see some solutions there but many are pretty low tech. In general, I would look to AC systems rather than DC but the trick is that you really need to get a matched motor and controller with AC. I suppose that you could do a brushed DC system without a controller if you were okay with it being basically full speed (voltage is proportional to rpm with some effects from load) whenever you closed a contact but I would not recommend it. I haven’t built an EV or hybrid for many years but back when I did, we had an enormous spreadsheet of all our options and we always felt like we couldn’t get exactly what we wanted. If you go the DIY route, you have to do some serious engineering to get your system to work right and be safe. For example, whether you direct drive or belt drive will largely be determined by the gearing that you need. It is really the subject for full books rather than here in my opinion. If you look at the Formula Hybrid competition which is a competition of college students designing, building and racing hybrids, the teams have 20-50 people on them who each have huge numbers of hours invested and the cars are still far from optimal or reliable. Sorry that I am not being more helpful but I don’t want to completely fill John’s blog with this.
Eric
John, Matt,
Do you know what the power loss to expect in a propeller pitch controlling device?
Hi Henry,
We have an article coming from Matt on CPPs that explains all.
I know this is not the favorite topic here at AAC. (LOL)
But the technology that is developing around electric drive systems is fascinating. Fifteen years ago I was involved in building a yacht that incorporated a custom designed computer information data collection system linked to a bulky satellite communication system that enabled the owner to monitor the running state of the engines from his office in New York while his boat was in Antarctica. — at a cost of several hundred thousand dollars in design and installation.
Today you can have a much advanced similar system on your laptop for pennies. Rather than speculating about operating efficiency and charge rates of electric motor drive systems as we have been doing on this site, the entire data stream for a number of multi-hull and mono-hull installations sailing worldwide is being monitored and collected in real time.
If your system develops a problem while at anchor in Vanuatu the factory in Finland can troubleshoot and possibly repair your system fault remotely. Try that with a diesel motor!
Follow this link: https://www.facebook.com/SailingAnarchy/videos/vb.155344415374/10156198553415375/?type=3&theater
Hi John and Matt,
Sorry for posting on an old thread.
Thanks for the detailed analysis. I ran across this article when researching diesel-electric drives and it seems to offer a different analysis to what you’ve described here (both the Trybid project and the company which did the analysis seem to have gone under – I don’t think that negates the value of this analysis):
Their analysis assumes a boat that is designed to support the configuration of electric motor, generators and a properly sized prop for electric use, so it cannot necessarily apply to the most common use case of people considering adapting this system to existing boats.
But for people considering a new, possibly semi-custom boat that can be built around the system, I think their analysis offers a compelling argument for what they describe as “diesel-electric”. This system provides direct power from a diesel generator to the electric motor, without going through a battery bank first (with the resultant efficiency losses).
I am far from an expert on these details, but I have a goal of when I eventually buy a boat (when my youngest graduates high-school in 7 years) to have a “one-fuel” boat – no propane for cooking, no gasoline for the dingy motor (all electric) – and plenty of electricity for my “condo-on-the-sea”.
I have time to allow technology to mature, and am willing to pay for my vision if it truly makes sense.
Thanks for your feedback,
Dan
Sorry to be a party-pooper, but the paper you link to is simply a rehash of the old propeller matching argument in favour of serial diesel electric. Proponents have been trotting this one out for years but as yet no one has been able to build an efficient enough rig to overcome the losses in energy conversions.
Also, these guys alway pick the most inefficient case possible to compare to in an effort to make a case—even then they fail. But in fact, if one is really concerned about prop matching over a wide range of speeds (the case they always use) a CPP is far more efficient and probably cheeper too. More here: https://www.morganscloud.com/2016/04/03/controllable-pitch-propellers-cpps/
Even Nigel Calder, who dropped some 3 Million of the EU’s money trying, has now publicly acknowledged that serial hybrid simply does not generate fuel savings for most usage profiles.
If you want a single fuel boat (a sensible goal) and are starting from scratch, I would suggest you focus your efforts on a really good solar array and then look at electric induction cooking. Steve Dashew has gone this route with impressive results. As to no gas for an outboard, that’s a solved problem albeit at a price.
Hi Dan,
I took a look through the link and I have to disagree with their conclusions. Their “modeling” should have started with a proper “fuel island plot” and then used real world boundary conditions. In the end, they claim a 30-50% efficiency increase yet no one has been able to show that in the real world meaning that the modeling is incorrect (for that matter, for most usage profiles, there simply isn’t that much efficiency to be gained without perpetual motion). The major assumptions that I object to are:
-The numbers used for electric efficiency are higher than anything commercially available on the market.
-Comparing numbers for different propellers is not correct. It may take some re-gearing but the diesel can spin that big propeller too if you are willing to live with all the problems of a large prop.
-The numbers for partial loading are really extreme and even if they are right, the following sea example represents a very small percentage of the usage profile.
-No batteries were included which really changes the control algorithm and eliminates a lot of the gains to be had with dynamic controls at low power.
-Cost was assumed to never be an issue. If it isn’t, then what is the point? Is range the most important, if so a properly specified diesel is best. Is carbon footprint more important? You would have to have a pretty big efficiency increase to make up for the extra embodied energy. Efficiency without context means nothing.
What it comes down to for me is that diesel engines are actually pretty good to start with provided that your power will come from diesel. If you go to the fuel island plot, you will find that for the entire normal operating range, the maximum efficiency point is only a few percent higher than your operating point so there isn’t a lot of room for improvement unless you ditch the diesel altogether. Right now, we don’t have a viable alternative to liquid fuels so diesel it is. If you want to get that last little bit of efficiency, a controllable pitch propeller or a multi speed transmission would be best. After all, the author is simply suggesting using the hybrid system as a continuously variable transmission, something which can be done simpler, cheaper and more efficiently with traditional transmission technology.
Eric
Hi Eric,
As always, thanks for the fill on my rather simplistic answer.
John and Eric,
Thanks for the comments. John – my thoughts exactly about the stove – an induction stove seems to be a good solution. And of course, solar, wind and hydo are all options in my mind.
I would like to ask for clarification of a few points both of you made.
John – you said that that “no one has been able to build an efficient enough rig to overcome the losses in energy conversions” in a serial diesel electric. What energy losses occur when the diesel generator is hooked directly to the electric motor (or more likely through a bus of some sort)?
Eric – you said “No batteries were included which really changes the control algorithm and eliminates a lot of the gains to be had with dynamic controls at low power.” – the authors very clearly don’t think going through batteries are a good idea, as those conversions are where all the efficiency losses come from. Why do you state that batteries must be included? I don’t understand the concept of control algorithm’s or the reference of dynamic controls at low power. Can you explain further here?
Finally, you make some good points about considering other factors than total cost. Most people don’t buy based on just one factor. I was wondering if you considered expanding the spreadsheet to consider other factors than cost (i.e. – reliability, performance, service availability, ecology, etc..) to allow someone to compare all of their buy decisions? It would be very important to allow someone to create their own evaluation weighting factors of each criteria (or even sub-criteria) to model the decision that best supports their needs. I’d be glad to help design this if interested as this is where some of my professional background comes from. I also recognize that this particular subject may not need further refinement, but I’d be glad to help.
Finally, for John – I’d be happy to help convert the evaluation criteria you describe in your books about how to buy a boat into a flexible modeler that subscribers can use to put your recommendations into practice.
Dan
Hi Dan,
We have already done this subject to death in two posts (the one above and the one linked to) as well as discussing it in over 160 comments to those posts. You will also find a link in the post above to an excellent analysis of usage profiles that work and those that don’t by Matt Marsh. So you will find the answers to your questions and much more in all of that.
And further Matt and Eric are both professional engineers who have actually built experimental electric vehicles from scratch, so you can be sure you are getting good information.