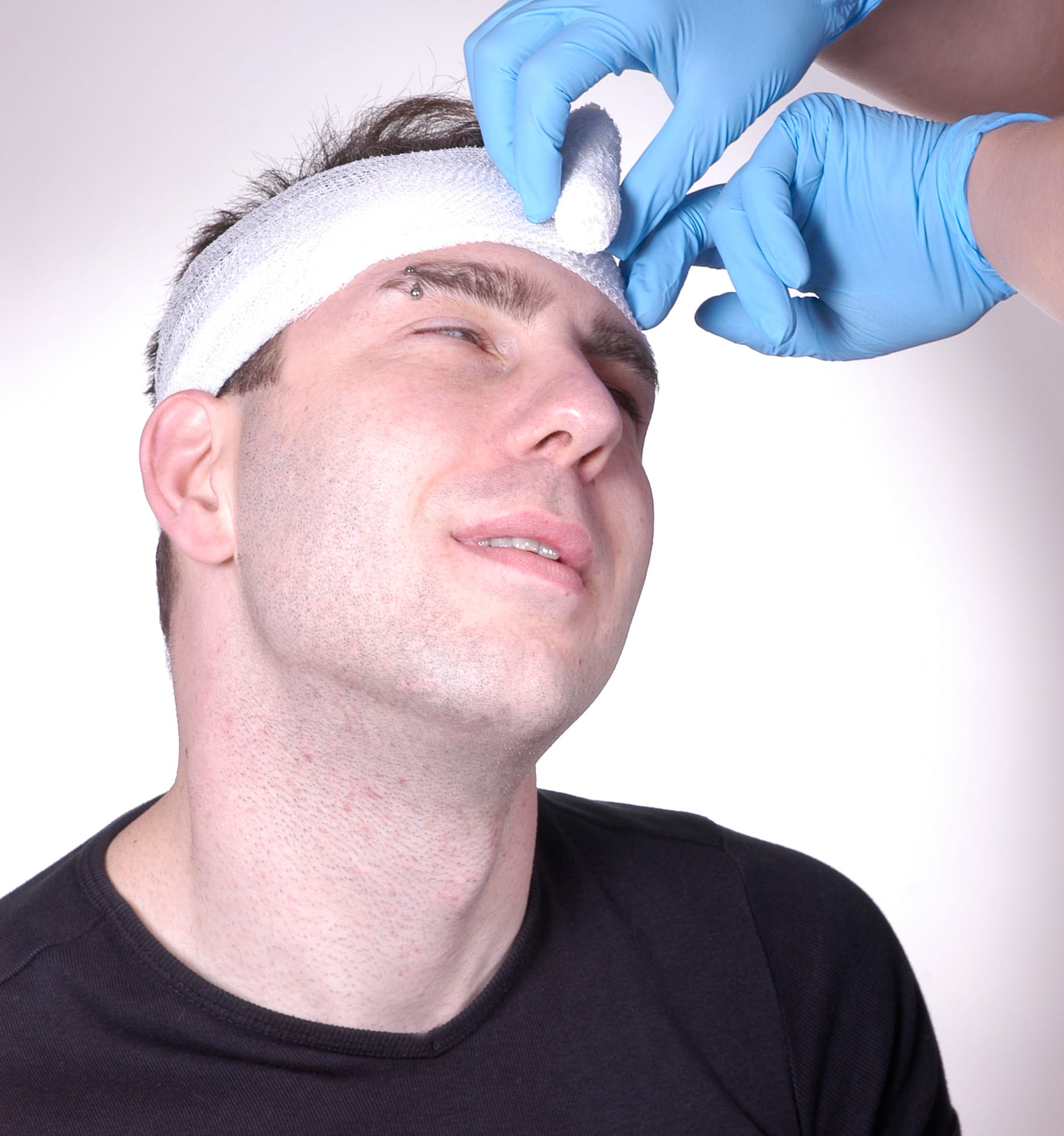
When sailing deeper than a beam reach, sailors are faced with the ever-present danger of an accidental gybe, particularly as the boat is pushed around by a following sea.
If the wind gets behind the sail, (caught aback) an unrestrained boom will swing rapidly across the boat, potentially resulting in catastrophic injuries or damage.
The purpose of a boom preventer is to oppose the quickly reversing wind forces and restrain the boom in the event of a gybe.
The Maryland School of Sailing & Seamanship taught me to set a boom preventer whenever the apparent wind is on or abaft the beam. This is sound advice from a well-respected school.
To support that excellent recommendation, in this two-part article I will:
- Part 1:
- Explain the forces that influence the design and rigging of an effective preventer.
- Highlight the risks of using elastic rope such as nylon or polyester (Dacron) as a preventer.
- Part 2:
- Provide a simplified methodology for estimating preventer tension, which we can then use to size the preventer line and associated hardware.
Use The Worst Case
Evaluating the wind forces on a sail is a complex matter of aerodynamics, but this problem can be simplified for the purpose of designing a proper boom preventer by concentrating on the worst possible case:
If the boom is restrained by a preventer after being caught aback after an unintended gybe, then it is reasonable to expect that the backed mainsail will, or at least could, turn the boat to a position where the mainsail is perpendicular to the wind in a fully stalled condition as shown below1.
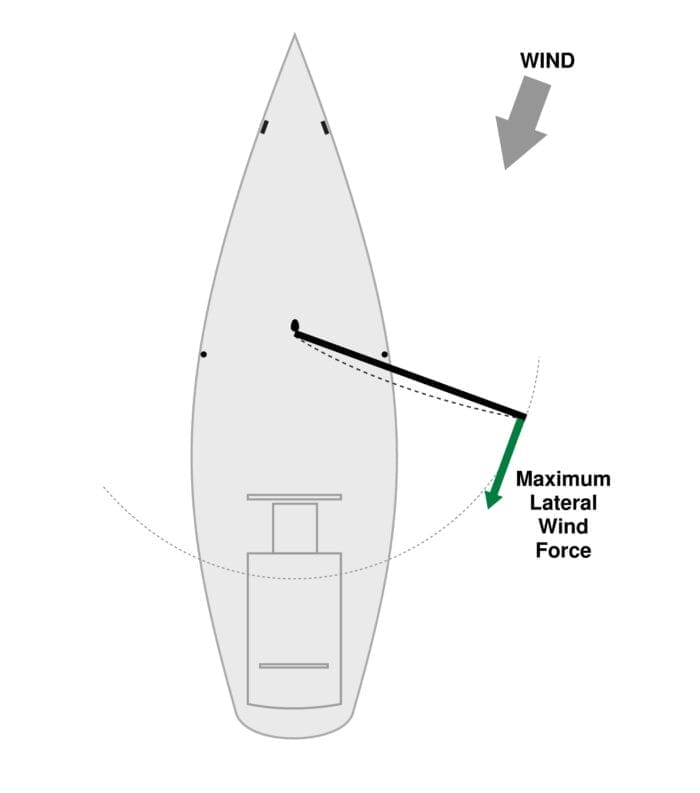
So we will design the preventer system to withstand this maximum lateral load using a simple drag equation.
Very useful analysis, thank you. It gives support to John’s and others’ preventer advice. This helps explain why my rigger wants the preventers he made for me be fabricated from low stretch line and be tightened on a winch in the cockpit. A slack preventer will allow boom acceleration.
I agree completely. Slack in the preventer is undesirable because it allows the boom to build momentum which creates an impact when the slack is taken-up by boom swing. This impact is made worse by a high modulus (low stretch) preventer. The low-stretch preventer is needed to limit the boom swing, but it is important to pretension this configuration to avoid any impact due to slack.
At some point, some component will break. What component do we want to break first?
In this case, I would not recommend designing in a weak-link. All of the standing and running rigging components should be specified based on the maximum righting moment of the boat, i.e. none of it should break under wind forces alone, even in a total knock-down. The sail should get torn to shreds and the boat be 90° on its ear before any standing or running rigging is at risk of failing.
To that I would add a load case for hydrodynamic drag in a realistic “boom end dips in wave” scenario, which will require some guesswork, but would give some idea of the loads the preventer could be subject to during an uncontrolled broach.
Weak-links are useful when you know that a system is likely to be overloaded and must fail in a graceful, repairable manner. I don’t think that’s the case here; if it does break, even at a designed weak-link, the consequences are catastrophic. We can and should specify this stuff to not break under any realistic load….. it’s more like an airplane’s “wings stay on” bolts than like a snowblower’s “auger stays pinned to shaft” bolts.
I’m interested in other opinions on this scenario. Scenario = Santa Cruz 52, a fast cruiser, broad reaching, surfing at 15 knots on the wave descent. A knock down occurs, resulting in the end of the boom in the water. The mainsail is full length battens, high modulus, built tough for cruising. My guess is that the loads on the preventer system are now more than 10x higher than the loads being discussed for the “normal scenario” for the preventer. Seems a bit like dropping a large parachute drogue in the water at 15 knots. If it bites, the loads will be enormous. My guess is that I’m better off in the knock down scenario with the preventer system having a weak link that gives up. Further thoughts anybody?
Hi Glenn,
I can help with this one based on a conversation I had with Stan Honey. The upshot was that when driving their Cal 40 really hard Stan and Sally did not rig a preventer at all. Stan’s reasoning is that with that much sail up in that much wind it is possible, or even likely, that an unintentional jibe would end in a death roll and in that case the main being held by a preventer would result in the boat being pinned on her side with the boom pointing at the sky, very nasty.
Of course you are thinking about the opposite situation with a knock down but I think the same logic may apply: this is a case where no preventer at all may be the best call. My thinking is that since water is 700 times denser than air, the loads in a full broach when the boom really digs in are going to break any preventer and maybe a lot of other stuff like the boom, gooseneck and vang, so it may be better not to use one at all. That way the boom will just swing inboard when it digs in and no harm done—seen that many times in the bad old days of IOR boats which tended to wipe out regularly.
Of course the other idea is a known weak link, but Eric Klem has written before about the practical difficulties of designing something that will break when you want it to, and not when you don’t.
That’s not to say that a weak link is a bad idea, just that I would lean toward no preventer at all when driving that hard. That said, I could be wrong, so best to check with the crews that drive their boats hard in the Trans-pac for what SOP is.
Bottom line on this is that Kurt is writing about solutions that work for conservatively sailed family cruisers, but when we get into high performance semi-planing boats like the SC-52 (love the boat) we must think differently and accept that there is intrinsically more risk in driving the boat that hard and that a higher skill level is required to remain safe.
Thanks John! Your site is an amazing resource! Wonder if your article should mention the the scope of the “design brief”. My cruising boat is 17 meters and a similar genre to the SC-52. Even when sailing the boat “conservatively”, broad reaching at roughly hull speed, reefed, no code-0, 22 kts true, once a night on passages we might see an outlier wave of maybe 4 meters, and she’ll quickly get into surfing the descent at 15+. I like the idea of the preventer. But not the idea of turning the boom+sail into a drogue. Nor the “pinned on her side” scenario that I had not thought of. I’ll go with Stan Honey’s model.
Hi Glenn,
Thanks for the kind words.
That said, I think I’m going to reverse myself. Assuming you are sailing the boat conservatively, which clearly you are, you will be reefed, and any sailmaker worth a damn will have rocked the reef clews to move the boom end up with each reef for just this reason, making a boom dip of any depth unlikely, I think?
Also, when reefed even if you do dip, the area will be less although the bunt will have some effect.
Given that, on your boat (she sounds cool) I think a preventer may be situation dependent. So if I was skipper I might mandate that in cases where the autopilot is steering the boat should be well reefed (she is easily driven so you will still make good numbers) and a preventer rigged.
But if driving her hard and hand steering with a full crew then not.
That said, I should make clear that I have never even been on a SC-52 or a boat like her, so I’m just brainstorming in the hope it will be useful. One thing I do know for sure from our M&R 56 years: when sailing big boats short handed we have to be far more conservative than on say a 40 foot boat.
I’m certainly not defending boom brakes and I might be being thick, but as they’re designed to slow down rather than prevent a gybe I’d appreciate comment as to why this factor was disregarded in the energy calculations.
Many thanks to Kurt for such an educational, fact-based and interesting analysis.
I have the same thought and question as Iain.
I have not used a boom brake, but I understand that the user must experiment with adjusting the device to provide the right amount of friction to sufficiently slow but not arrest the boom. Perhaps that is unachievable if adjusting in lighter wind and applying in heavy wind.
I guess that with too much friction, the boom arrests or nearly so causing breakage and a rapid sweep of the cockpit; with too little friction, the boom rapidly sweeps the cockpit.
Perhaps they are suitable for intentionally gybing smaller boats.
Hi Iain and Michael,
Michael hits the nail on the head. The reason I spiked the old boom brake article is that if you read accounts of using them, or watch videos, we can see that actually getting the tension right is very difficult and requires continues adjustment, so if the tension is too high the forces will become colossal because of the multipliers that Kurt explains above.
And if the tension is too low, the boom will smash across.
The other big problem I have with them is that once people install them they tend to stop using a proper preventer, which is a huge mistake.
Michael, John – many thanks and much appreciated.
I agree with what John states above. You have to get the brake tension correct to make sure you get the desired amount of braking. Unfortunately, the amount of braking is dependent upon the wind speed and so there is no good way to know if the brake is set properly at any given time.
I would like to go a bit further, because this question has come up before. When set properly, the brake should allow the boom to swing across slowly. This makes the analysis a bit more difficult, because it becomes a dynamic problem instead of a static problem. However, the short answer is that if the brake is doing its proper job and severely limiting the boom speed (and acceleration), then the forces (and bending) imposed by the brake are only slightly reduced from those in the static condition described in the article. In other words, the boom brake imposes large undesirable forces and bending even when the boom swings across in a semi-controlled fashion.
Getting a bit more technical, if you go to basic physics, you may recall that Force=mass*acceleration (F=ma), where force is the “net” force on an object. In one extreme, where there is no preventer or brake, the un-restricted force of the sail on the boom will rapidly accelerate the boom and cause it to swing across uncontrolled. At the other extreme, if a preventer or brake is applied to fully counter the force of the sail, the “net” force is zero and there is no acceleration (no movement of the boom). This is the static condition described in the article. In the case of the boom brake, the acceleration is very small (nearly zero), so the “net” force is also very small, which means the forces applied by the brake are nearly equal to the wind force and the situation is nearly equal to that of the completely static condition.
Again, the bottom line is that, when set properly, the boom brake will impose amplified forces resulting in undesirable bending and goose-neck reaction forces.
Sorry for the long explanation, but hopefully this makes sense.
Hi Kurt,
Thanks for the fill on that. That was my gut feeling, but once again I don’t have the chops to say it for sure.
intuitively, I was having a very hard time believing that a boom brake could not work without excessive loads since the boom is not allowed to build a huge momentum – provided that the need for perfect adjustment could be solved.
What I failed to realize was the simple math that if ’a’ has to be very small, the countering ’F’ has to be practically speaking the same as the wind force, i.e. huge in a gybe.
Your comment goes to show that very simple highschool physics with a pinch of logic trumps intuition every time.
You really managed to put it very clearly: a boom brake that works is almost as bad an idea as one that doesn’t!
Thank you 🙂
While I understand the physics described, I have used a boom brake with good results for coastal single-handed sailing in winds less than 25 knots on a 20000 boat, and have found them to be beneficial. I’m not sure why this site is now taking a hard line on them because in my view, if used properly and within limits, they offer safety and maneuverability benefits. Shouldn’t there be some consideration to the shock loads on mainsheet systems (especially traveler cars) from an uncontrolled jibe? They can be rather jarring even in 15 knots of wind. If jibing in a seaway, the boom brake allows for a bit less centering of the mainsheet so that when the boom does come around, there is far less force rounding the boat into the wind or causing an overcorrection of the helm. Without question, if the boat jibes unexpectedly, it gives anyone in way of the boom that extra split second to duck. The brake and the preventer are two separate systems and should be treated as such. If I’m coastal cruising short-handed in relatively benign conditions, I think the brake adds some added level of safety without undue compromise to gear.
Hi Jesse,
Yes, it’s a tricky issue so I think I will do a short tip on why I decided to recommend against boom brakes.
OK. I hope you will offer some anecdotal evidence of why boom brakes are no longer recommended. Everything I’ve seen so far is based on empiricism. I certainly cannot be the only person on this site that uses one successfully.
Hi Jesse,
I disagree, everything we have backing our decision is the exact opposite of empiricism: logical and rigorous engineering analysis. Looks like it might turn into an chapter rather than a tip.
Great presentation – I look forward to the next parts!
What do folks think about tying off the preventer at the bow, instead of running aft, in order to reduce both stretch and load on whatever turns it. Can’t get it as tight but with maybe 1/3 the length you can’t stretch as much and not pre-loading it. Also limits adjustment speed and ability to come into the wind. But from a load standpoint seems better.
That makes some sense from a loads & forces standpoint. But how would you manage it without sending someone all the way up to the bow every time it needs adjustment?
I’d argue that being able to ease or tension the preventer from the same location where you’re easing or tensioning the mainsheet and/or traveler is quite important, in situations where you need the preventer. It’s not terribly difficult to make the line, and the block on the bow toerail, strong enough.
I agree with Matt here. It is important to be able to maintain control of the preventer before and after a gybe. With the preventer secured at the bow, if a gybe occurs you may be forced to gybe back over in order to release the preventer. At the very least, you will need to send crew to the bow to contend with the situation. I don’t believe you want to be backed into this corner in a post-gybe situation. Keep in mind that the preventer will potentially be under a tremendous load and so it may be difficult to manage post gybe. Securing the preventer to winch or through a winch will give a much higher degree of control than a simple cleat.
I guess I should read up on the subject, but I’ve been thinking of preventers as a tool for longer periods between maneuvers, when crew isn’t paying as much attention. And downwind I don’t exactly play the sheet by any means. But for sure they’d get used more/at all if led aft.
We rig the preventer whenever the apparent wind is going to be within ±45° of dead astern, for more than five to ten minutes, in winds greater than force 2. Maybe if we were in an area where wind was more consistent, we’d be a bit more lax about it…. but, around here, gusts are really shifty and it’s all too easy to get caught in “ahh, nice starboard-tack broad reach, boat’s doing 6 knots in 9 knots true, tracking perfectly, WHY THE F…. DID WE JUST GYBE!”
Hi Michael,
Securing preventers at the bow is common on large vessels but I wouldn’t do it on a cruising yacht. Some key differences are:
Thanks to high modulus lines, I just don’t see the need to do this, if we were stuck with nylon I may have a different view.
The other trick that many of the traditional large vessels use is to use a multipart tackle going from the end of the boom to a fixed pendant coming from the bow with the the standing part of the purchase led back along the boom. This was basically a workaround for not having high tech blocks, line or winches and it works okay for that. The issue is that the tackle portion is often in the 100+lbs neighborhood and getting the whole thing hooked up is tricky and time consuming. Similarly, I feel that this is obsolete due to modern gear. If you ever see a large traditional vessel with a 5 or 6:1 tackle pulled tight along the underside of the boom for no apparent reason, you are seeing a preventer in the stored state.
Eric
I find that when i rig a preventer to bow the first thing it will take out as the load comes on is the lifelines, before it would get anywhere near the shrouds.
I look forward to seeing what the loads are in the next article. I have been rigging with polyester. Probably undersized (but only 35′ boat).
Maybe with less line stretch the preventer would be kept off the lifelines. Although this gets hard to achieve when the boom isn’t fully out.
Hopefully john can address this in his rigging article.
We do also have a very basic boom break. It doesn’t do much as a preventer but does help slow everything down in an intentional gybe and helps stabilise the boom position in light wind wavey conditions. (Not necessarily off the wind, or just while rigging the preventer).
Lifelines definitely pose a challenge and it seems the lead from the boom to the bow is very boat dependent. Some boats are able to go over the lifelines where others have to go under. In some cases, the lead has to be changed from over to under depending on the boom position. This creates some unfortunate and unavoidable hassles but it is necessary to establish an initial fair lead so that the preventer can be properly pre-tensioned without the potential for chafe.
On a 35′ boat, polyester might provide sufficient strength but will have a fairly pronounced boom swing during a gybe due to the relatively high elasticity of the line. This boom swing will likely result in interference between the lifelines and the preventer during a gybe as you suggest above. Switching to a properly sized, high modulus preventer will typically limit the boom swing to about 2 or 3 degrees or less, which should eliminate or minimize the lifeline interference given a fair-lead to start with.
I think you are right that eliminating stretch will reduce the interference with the lifelines with fair lead to start.
I had hoped for a magic solution i hadn’t thought of to avoiding adjusting the lead of the preventer around the lifelines as the boom is sheeted in. I could use the reaching strut suggestion by pete below but i think that would be more work for us and i don’t have a running strut.
Same setup here. We use a very simple preventer that is essentially nothing more than a stainless steel triangle about 300mm on each side, with rings about 50mm in diameter on each apex. The top one clips to the boom just forward of the mainsheet, and the lower two have the preventer line run through them and twisted around the lower arm two or three times. This line is terminated midships, not at the bow as a preventer is.
Extensive use has shown this setup quite insensitive to tension as long as it’s not entirely slack. Like you I only use it to take the energy out of intentional gybes. Once the preventer is on, I might slacken off the brake line altogether as the leeward part of it is a nuisance to step over if it’s still tight.
The important point is this brake only comes into play once the boom has swung inboard past the point where the brake like is terminated. So it’s only exerting forces pretty much when the boom is within about 30deg of midway.
Unintentional gybes are a different creature altogether as you want as little movement as possible and the angles involved are quite different. A boom brake should play little to no role in this scenario.
Which is why I’m happy with having both – each serving different use cases.
I have been using precisely the system advocated by Kurt (and John Kretschmer) in his excellent article for some years and my set up is to use a length of low stretch line (our previous Spectra main halyard) down either side of the boom with eyes spliced into each end of both lines, from the end of the boom to near the gooseneck. That provides the aft end of the preventer line. When not in use, there are bungees on the gooseneck end of the lines to secure it to a mast or boom winch or cleat.
The forward end is a similar line run from the cockpit along the deck to a block on a padeye just aft of the pulpit and back outside the shrouds and connected to the aft preventer line via a snap shackle attached to the for’ard line. It is tensioned either to a winch if I have one spare (usually the case) but if not it is made fast to a large horn cleat on the outside of the cockpit coaming with the main eased too far (ie right onto the shrouds). Tension is the applied using the mainsheet to trim the boom and main away from the shrouds again. We have found that the horn cleat provides sufficient resistance for us to ease the main across in a controlled manner in the case of un involuntary gybe on our 47 footer with 475 sq ft’ mainsail. However, where we can, we do use a winch.
The for’ard end, like its aft counterpart, is also permanently rigged on both sides and the windward one doubles as the foreguy for the whisker pole when poling the headsail. When not in use they are simply clipped to the shrouds where they can be easily reached.
This is on a cruising yacht sailed only two-up and it works for us. Full racing crews would no doubt have a different way of doing it.
John H. has other great articles about the use of the boom pennant that you describe above. I believe this is a great set-up that facilitates the preventer attachment in a safe and controlled fashion.
I would be interested to hear more about how your system performed in any planned or unplanned gybes and under what sort of wind/sea conditions.
It has worked very well in both although we’ve done way more planned gybes to test it than unplanned. I changed to the Spectra line after a JK Captains Hour when this was discussed, maybe a year ago and was immediately impressed that it didn’t bear sideways on the shrouds.
We rarely have unplanned gybes because we generally reef the main earlier and try to make sure we have the driving power concentrated forward by having more headsail in the sail plan than main. That said we have had unplanned gybes caused by auto pilot issues in 30 knots plus with double reefed main and the boom remained rock solid. In both cases the poled headsail also backed and the boat was able to be hand steered back onto the original tack.
I think my sail plan in such conditions is pretty much always going to involve more headsail than main (indeed, often no main) so I think the issue of steering back against the gybe pretty much resolves itself.
Hi Kurt,
Great explanation of the problems of geometry and stretch that face us with preventers. And I agree with you, lets keep this a static problem as much as possible so no slack and very little stretch is best. While one could run a nylon preventer that was highly preloaded assuming your sheet was stiff so that it would never see more load than that preload, I don’t want to be cranking on that much preload at least on my boat as it causes plenty of other issues such as higher loads elsewhere.
One use mistake I have run into a lot is where the main is trimmed with too much twist. The issue is that this pulls the boom into centerline a lot more than it should be to prevent luffing making the geometry quite bad. Also, the boom tends to have a lot of vertical movement as you go through the waves and the temptation is to have the preventer only be tight when it is high which means there is more slack than desirable. So I guess the point is to use your vang and control twist.
Your example of the nylon preventer does a great job of illustrating a potential bad situation. That amount of side load on the shrouds is also really scary as they tend to be quite stiff so the increase in shroud tension is a lot more than that. This got me thinking about what the correct thing to do after you jibe onto a preventer is. Some people will jibe back but that isn’t always possible or desirable. The other thing to do is to ease the preventer across which does put it on the shrouds sooner or later. I guess the question is whether the boat could be in a position to have close to max force on the sail while easy the preventer with it across the shrouds, I am not sure. If you have any thoughts on this it would be appreciated, I will have to think on it more. For what it’s worth, on some traditional boats it is actually a common practice to jibe onto the preventer then ease to centerline where the sheet will have been hauled in tight and can be used to ease from there with the reason being that the forces on the sheet are high enough that they can’t haul it in to jibe by centering the boom first.
Eric
You are correct that the nylon and polyester preventer lines do benefit substantially from much higher preload, but I don’t find that to be the case with high modulus preventer lines. My modeling indicates that with high modulus lines, a small amount of preload is good and necessary, but higher preloads don’t add much additional benefit.
You raise a good point about easing the preventer post-gybe to bring the boom across on the new gybe and how it will undoubtedly interact and apply side-loads to the shrouds during this process. You are correct and unfortunately, I don’t have a good answer for this problem as my focus has been on trying to ensure the preventer system survives the gybe itself.
If the decision is made to stay on the new gybe, then this should probably be done quickly, but in a controlled fashion to minimize the time that the preventer is in contact with the shrouds. Post gybe, I would recommend that the first step should be to take-up any new slack on the mainsheet to prevent the potential for slamming in the event that the boat gybes back to the original course (intentionally or otherwise). If the boom is to be eased to the new post-gybe course, then the mainsheet should be taken-up simultaneously with the easing of the preventer so that the boom is under full control in both directions during the process. These are fairly obvious points that don’t really address your concerns about the interaction with the shroud, but I felt they were still worth mentioning.
If the gybe actually occurs at design conditions (more to follow on those assumptions and the anticipated loads), the results will likely be fairly severe from a boat handling standpoint as John described in a previous comment. Control of the boat may be partially out of our hands initially. Taking up the slack in the mainsheet/preventer system would be the first priority in my mind to avert further potential for failures due to slamming. After that, I feel the next steps will be very situational dependent. Easing the preventer and boom to the new course does introduce a concern with the shroud loading. I would be interested in hearing the thoughts of others on this subject/concern. There may be other discussion threads on this site regarding this subject that I am not aware of.
Hi Kurt,
Thanks for the thoughts. On the shroud load, I assume the 1300lb load you give will be tied to the example you are going to give in the later parts as I am not sure what size mainsail and boat that is relative to unless I missed it. Using that, we can probably make some basic estimations on how high up the shroud the preventer is hitting and what the span between deck and spreader is. The hard part is getting the deflection of the shroud, technically you should know the stiffness of the whole rig (and some of the boat maybe) but if you just took the stiffness of that wire section you could solve for deflection and tension together and probably be slightly conservative but close enough to tell you whether you needed to watch for issues here.
If that tension is lower than the normal sailing tension, then it is likely a non-issue as I think you can assume that the leeward shrouds are slack enough that you are just providing a slight bend in the windward shroud but that the load remains constant as you haven’t changed the geometry significantly or applied extra tension to the leeward side (obviously not quite true with a tensioned rig but probably not too far off). However, if the tension you find is higher, then you are increasing overall tension in the shroud. The shrouds that I have run the numbers on usually have a safety factor on the order of 3 so there is some margin but once you start eating into this, you need your numbers to be more precise than the method I just outlined.
At least I have never heard of a failure due to this but it would be interesting to see rough numbers.
Agreed on the preload relative to the modulus, that is the behavior I would expect.
Eric
Thanks Eric,
The example in the article is actually a Kaufman 47, which you may know.
I actually started down a path to tackle the problem of side-loading on the rig. My original concern I believe was similar to your initial reaction. Specifically, anytime you side load a highly tensioned cable, the tension increases dramatically. This is the classic clothes-line example. As I got into the problem, I quickly realized that it gets complicated in a hurry, but I also began to recognize that we don’t have two perfectly rigid end conditions. As you point out, there is give in the opposite side cables of the rig system and a certain degree of flexibility in the entire rig. The other factor that you touch on is that the preventer contact point is fairly low and close to the rigid deck connection making the system a more resistant to the side-loading. When I made these two realizations, I decided to worry less about this particular aspect of the problem and move on to the more manageable concerns. I believe there is still some reason for concern, but not to the degree I initially thought. More study is probably warranted, but it gets into a degree of fundamental engineering that I’m a bit too rusty on. I kind of wonder if it isn’t something that the spar manufacturers couldn’t potentially help with (e.g. Seldon).
Hi Kurt,
I took a crack at the numbers using the method described and the info I could find on the Kaufman 47. Using relatively conservative assumptions, I got a shroud tension of ~4900lbs which for a wire of 16000+lbs breaking strength puts it right around the max tension due to righting arm. There were quite a few assumptions in here but I generally made them on the conservative side and I doubt that the real load is more than +30% greater. You are correct that one of the most important points is that the preventer bears close to one of the shroud constraints (I hope that vang is on).
To me this suggests that while the load is high, this rig should have enough give that it should probably be a survivable event although it may be one of the highest loads that shroud sees. It is certainly possible to imagine a rig where the numbers work out worse than this such as a preventer not at the boom end, high boom, single spreader, etc. Since we are dealing with all worst case numbers it is probably fine on other boats as well but some care definitely needs to be taken, if you shock load something it could be bad.
This kind of makes sense if you compare it to a jib which applies a distributed load all along the headstay. A boat like this will have 2000+ lbs on the jib sheet so the headstay is reacting more load than this although it is also usually a size larger.
I agree with your assessment that there are other more critical areas to focus attention on.
Eric
Hi Eric,
That’s great, after I learned about the load multiplier on tight wires (jacklines) I have wondered if a preventer bearing hard on a shroud could bring the mast down. Great to hear that’s unlikely.
Thanks for looking at this Eric. It’s reassuring to have more thought on it. Your Jib load on the forestay is an interesting analogy that hadn’t occurred to me.
There is something I like to do that I don’t hear talked about much. Maybe because it’s a daft idea, I dunno… I often use the reaching strut, rotated upside down (so the little finger at the outboard end is on top, rather than on the bottom as it would be when used with a guy). The strut is useful when the boom isn’t too far out, it can help to increase the angle of the preventer from the end of the boom but more importantly it protects the shrouds in the event of a gybe, which is something that scares me. The load is transferred to the mast instead of the shrouds which seems preferable to me. With the boom out further the strut becomes too short so needs to be removed but at that point the shrouds are less vulnerable providing there is enough tension in the preventer.
Using the reaching strut (aka jockey pole) is a very interesting idea that I like the sound of.
This is definitely an interesting idea. It certainly improves the geometry of the preventer, which should reduce the loads and it sounds like it gets you off the shrouds. It does add some additional complication, but it sounds like you’ve worked out a system for it. If the turning angle of the line at the end of the pole is not too severe, then the compressive loads shouldn’t be too bad. You should be able to run the numbers on that scenario after the upcoming Part II of the article. We can circle back then if you remind me.
We use a similar system as Mr. Browning describes in his comment above, with variations. Instead of a stainless snap shackle we use a soft shackle to join the eye splices on the boom-end-attached section of the preventer to the permanently run forward line (which returns to the cockpit). The forward section turns through a low friction eye on the toerail about halfway between midships and the pulpit. Because we have an ‘aft intermediate’ shroud rather than runners we cannot ease the main boom as far out as some boats. Thus, the best angle at maximum boom that we can create is with the turning point as indicated. If it’s taken all the way to the bow the angle decreases slightly. We use 1/2″ StatSet XLS line.
This system of two parts is very fast and easy to set it up, which means we use it very frequently. In use, we keep the preventer tensioned through a clutch on the side deck and it usually also lives on the secondary winch. This preventer has proven itself a couple of times at sea when the autopilot has taken an unexpected nap. And once when I lost spatial orientation in the pitch black of a squall as I tried to run off. Oops.
The key to any safety device is to use it every time.The pre-rigged components of this preventer make this convenient.
Brian on Helacious (Dix43) , currently west Sweden.
Completely agree about using it frequently, if it is simple and easy to deploy. Which is part of why I use snap shackles, although that has more to do with its alternative use as whisker pole fore-guy. Prior to using them, I simply tied the fore and aft sections together using a fishermens bend, but my crew (aka wife) is not as proficient with knots as me 🙂 and I wanted it to be simple for her to deploy as well.
This sounds like a good system. The StaSet XLS is pretty rigid but not quite as good as the dyneema lines. Depending on the boat size, the StaSet may be allowing too much boom swing. We can check it after the release of Part II. It would also be good to verify the turning hardware at the low friction eye on the bow at the same time. I’m glad you had it rigged during your gybes. Do you recall how much boom swing you experienced during those gybe situations?
Kurt, I don’t recall boom swing being obvious or alarming, but of course I wasn’t paying attention when the AP glitched. In the other case, I was preoccupied!
I think we were about a week into the 12 day passage. What happened wasn’t a “worst case”. We were beam reaching on a Po tack when a squall approached around 0100. These Atlantic squalls tended to be quick and not too fierce. Wind in the squall was in the F7 (30’s range). I decided to disengage the AP and steer the boat more downwind to reduce the apparent wind. I’d like to blame the wind and seas for the problem, but I simply oversteered, failed to ease the main out and the wind got behind the sail.
I had taken note of the new compass heading I wanted to achieve,about 30˚ off course, but as I began my turn the boat was rolling so much that the compass was unreadable. On the MFD, the radar screen was set for Heading up, but the chart was on north up and we were heading south, so they were opposite. This added to my confusion. It was absolutely black outside. In seconds we were sailing by the lee, with the genoa backed as well. I eased everything and we basically stopped in irons. The squall blew past. I started the engine, turned us back on course and whistled into the dark. In the quarter berth below, Helen never even woke. Her comment when she relieved my watch was, “I heard the engine start-did the wind die?”
Thanks for describing the event and analyzing your disorientation. Clearly, you learned a lot. Now, I have as well.
This information is fantastic and I look forward to the upcoming parts. I would like to petition this (Part 1) article be made free so this important information can be shared in the hundred of threads elsewhere about this topic. Business wise I would think you’ll gain subscribers interested in the subsequent parts. Thanks!
Hi Christopher,
Sorry, we can’t do that. This series was a huge amount of work to put together and edit, so it must be paid for. We also pay our contributors about three times what other similar publications do, and that needs covering too. Also be aware that AAC is only just sustainable, there is no fat. More here: https://www.morganscloud.com/why-we-need-your-help/
And we long ago proved with hard data after multiple experiments that the idea that people will join if we give them good information for free just does not work. The hard cold fact is that people join only when the pain of not being able to read really good information that they need gets unbearable. Sad but true.
Not just us, you will note that most-all quality publications have cut back on free content after trying that route.
At the risk of violating Rule Five, I’d like to elaborate on this just a bit:
The vast majority of the journalism world has gone to a low-wage, low-effort, churn-it-out-fast model. Rigour and accuracy are sacrificed in the name of getting stuff written, published, and indexed for advertising network match-up ASAP, and editors are necessarily reluctant to be critical of bad decisions on the part of the advertisers who pay their wages.
AAC is one of a small handful of niche publications where technical rigour, accuracy, and thoroughness are prioritized above all else; clarity of presentation is close behind. Ideally, we try to take a subject that’s worthy of an entire chapter in each of six design textbooks, or that took 14 different skippers 150,000 miles to collaboratively perfect over twenty years, and distill it down to ten or twenty minutes of reading that’s accessible without advanced technical training and makes most readers go “oh, that makes total sense now, I don’t know why I ever thought this subject was hard.”
So you look at an article like Selecting The Right Hull Form and what’s shown in your browser looks just like a nicely polished blog post, but there’s actually about seven hours, spread over three weeks, of planning, writing, preparing diagrams, cross-checking every detail against multiple engineering books, proof-reading, revising, etc. before that even lands in the editor’s lap. The editors here don’t just proofread and approve – they read the whole thing, several times, tweaking it in different ways and pondering how people of different background, English-language skill, and technical knowledge will interpret it. Then the author reviews it *again*. Oh, and there’s lots of overhead to running the site too! Don’t forget the hours that the authors spend in the comments section, clarifying & adding to the article once the members have seen it.
And it’s that way for most of the hundreds of articles on here. The contributors get paid three times more per article than at similar publications because the articles take five or six times longer to research, write, edit, and polish. (Yup… your mental math is right! None of us are getting rich here. We write this stuff because we think our fellow sailors will be safer, happier, and more successful for it, not because we’re making bank on it.)
Put simply, AAC costs money because it’s the only way to ensure full editorial independence (John & Phyllis are beholden to no advertiser or corporate parent) and to ensure that Colin, Eric, Kurt, etc. and I can justify to our families the sheer number of hours that we all put into this.
My goodness, that explains a lot! thanks to all of your for your magnificent efforts on our behalf.
Also, anyone who wants to see what’s hidden behind the paywall but isn’t ready to pay is welcome to use the “10 free chapters” offer https://www.morganscloud.com/get-to-know-us-for-free/
Hi Kurt,
Such a good article – thank you.
A request please for Part 2 around footnote 4. “On boats with mainsheets that attach to the boom substantially forward of the clew, such as those with travellers forward of the dodger, it may be wise to move the preventer attachment point inboard from the clew, perhaps a third of the distance between it and the mainsheet bails, to avoid bending the boom too much when preloading the sheet against the preventer”.
This footnote describes perfectly the setup on our 14.5 m sloop – the multipart mainsheet blocks attach 45% forward from boom end. Complicating things, we have moderately swept back side stays and in-boom furling, meaning our boom is heavier than standard.
Currently we have the preventers running to the end of the boom, on the basis that this will give the best angle at the bow for the preventer AND the boom end is strengthened to take a high load attachment. By bringing the preventer attachment forward as may be suggested, we would worsen the lead angle at the bow. Using your vector modelling approach (in a rather amateurish way), it would appear to increase our preventer load by more than a third -> worse-case scenario.
If you were able to cover such variations to standard in your Part 2 “how-to”, or maybe even in a Part 3, that would be awesome.
Many thanks. Rob
Rob,
The concern with that setup is that booms are (usually) designed to be very strong for axial compression and for bending loads in the vertical plane, but without much consideration given to bending loads in the horizontal plane.
Consider your boom with its forward-attached mainsheet as a beam:
You have the boom pinned in both planes at the gooseneck.
In the vertical plane, there is a downward force on it at the mainsheet and at the vang, and an upward force on it at the clew of the sail. These are trying to bend the boom into a vertical “U”.
In the lateral plane, there are forces on it at the clew and at the mainsheet. These are smaller than the vertical forces. They are trying to bend the boom into a lateral “U”.
Now we add the preventer.
To most efficiently handle the loads of a sail suddenly loaded from the wrong side, the preventer should counter the force applied by the sail on the boom, which is a point load at the clew (carried from sail to boom via the reef pennant or outhaul). Thus, the force from the caught-aback sail goes directly to the preventer without bending the boom, and the boom only has to take axial compression.
However, this means that pre-tensioning the preventer while the wind is from the correct side will ADD the preventer preload to the lateral component of the force applied by the sail at the clew in normal sailing. Thus, it is easy to bend the boom too far into a lateral “U” and break it.
By my rough working of the vectors, it will *usually* be best to attach the preventer as close as possible to the clew, regardless of where the mainsheet attaches to the boom. However, if your mainsheet is farther forward, you will either need to be very careful to not over-tension the preventer against the mainsheet (which risks bending the boom in the lateral plane), or else you will need to attach the preventer closer to at the mainsheet (and therefore accept both a lateral bending load on the boom, and worse angles on the preventer, at the instant when the preventer actually comes into play.) Once the preventer is in play, the preventer load and the sail clew load cancel each other instead of adding, and the mainsheet load drops to zero.
When I work out these forces and angles using a very low-stretch preventer line, attached to the boom end near the clew, and with very little preventer preload, the answers are quite satisfactory.
Hi Rob,
I’m afraid that article is in final edit, so too late to add that complication. Also, as editor I have tried to keep the calculator as simple as I can by not adding too many edge cases, since, if we try to cover every eventuality, we end up with a mess that’s difficult for anyone to understand. For example, at one point we had reefing and 2:1 preventers in the calculations, but even one mudded the waters, never mind two or three.
The best way to handle these things is the comments. Matt’s answer is very helpful and I’m guessing both Eric K and Kurt will chime in with thoughts in the comments.
And further, I will be fully editing and republishing my articles on the practicalities, so if good stuff arises from Kurt’s part 2 I can add that.
Hi Matt,
Good to hear that I might have been worrying unnecessarily.
However, there is another variable here, based on experience. What I call the sleepy dummy syndrome: Tired crew in the dark forgets preventer and starts cranking on the mainsheet. I have seen two booms that got broken this way, although in both cases they were using mid boom preventers with end boom mainsheets, but the theory is the same.
Also I’m thinking that the designer of a boat with a mainsheet attachment in the middle of the boom will have already up-specified the stiffness of said boom in the horizontal plane, or at least they should have. Therefore I still wonder if one third of the distance between clew and mainsheet, in from the clew, might not be a good rule of thumb for the preventer attachment point.
Eric Klem: I seem to remember that you were the first to bring up this issue on my first articles. Any thoughts?
Kurt: any wisdom?
The designer will almost always have specified the boom based on sailing loads. If it has mid-boom sheeting then they will have considered the lateral bending component that comes from mainsail clew vs. mainsheet bail at different distances from a pinned gooseneck. They won’t have considered your scenario of winching hard on the mainsheet against a tensioned preventer.
Whether you could bring the preventer attachment forward/inboard on the boom, closer to the mainsheet, by enough to make this lateral boom bending risk impossible given typical crew strength and winch ratios – without also creating poor preventer geometry that renders the preventer ineffective – is a fair question, and one to which there can be no universal answer. It’s always going to be specific to a particular design.
Hi Matt,
That makes total sense. I was about to say that it would always depend on the boom design and would be impossible to model without knowing the specs of each boom, but then stopped in the hope one of the engineers would say exactly that…and you did. 🙂
Anyway, I think we can say that in the case of centre boom sheeting:
I’m still kinda liking the 1/3 in rule of thumb, but will be interested to hear Kurt and Eric’s thoughts.
Anyway, once we get this sorted, as best we can, I will work it into part 3, even if it’s just a warning.
Hi All,
In the world of perfect humans and modern lines, with mid boom sheeting it is possible to run your preventer from the end of the boom. As Kurt points out, high modulus lines mean you can run very little preload and not have issues with large boom movements. However, I would not do this with even a polyester preventer as you need to preload it enough that now you are putting a significant bending moment on the boom. Even with high modulus lines it is not great as the boom is deflected 1 way when sailing and after the accidental gybe, its deflection flips allowing some dynamics which are not great.
Moving out of the perfect human world and into the real world, as John mentions, the above method invites human error. Both the sheet and the preventer stand the chance of being ground on by a crewmember. The crewmember probably won’t notice much as the load will come on slowly as things deflect and they may well grind until forces are high enough that they break the boom. You can do this when the preventer is attached at the sheet attachment too but it takes much more inattention. So in my thinking, I like to keep the preventer at the same location as the sheet roughly. The boom should be designed for the full sail load with that reaction location already (sailing DDW in a big breeze). Some mid boom sheeting setups use multiple attachment points to avoid point loading the boom and this gets tricky as you may need to mimic it with the preventer. There are a few downsides including higher preventer loads and more geometries that leave the preventer fouled up with the shrouds.
Note: all of this is assuming “normal” cruising sails meaning bermudian and most of the force on the rig at the corners. Something like a gaff rig with distributed force along the gaff and boom needs to be treated differently (for example the best arrangement for the boom will usually be with sheet ~2/3-3/4 of the way to the clew).
Mid boom sheeting is one of those trade-offs but my thinking is that mimicking the sheet placement with the preventer placement is usually best. Maybe someone can convince me otherwise though.
Eric
Hi Eric,
Thanks, that makes sense to me. Also, after having slept on it something else struck me: As we reef the clew moves inboard so the problem of having the preventer further inboard than the clew diminishes with each reef. I’m now pretty firmly in your camp, but still open to hearing why I might be wrong.
Sorry for my tardiness on this, guys. Work-life caught-up to me late this week. There is a lot to unpack here, but I will try to outline my thoughts briefly. I may repeat a few of the points made above in the process.
There is no question in my mind that with a mid-sheeted boom, the preventer is still best attached at the boom’s end because that gives the best leverage and least bending post-gybe (more on pre-gybe momentarily). As the preventer is moved in-board, the geometry degrades very quickly as outlined in the article. Specifically, the preventer leverage decreases causing a corresponding increase in preventer load. Keep in mind that we are already fighting the load multipliers due to the angles. If the preventer needs to be moved inboard of the clew, then I would recommend limiting the separation distance to no more than a couple of feet. If any more separation were necessary, then I would recommend evaluating the specific bending loads for the given application.
To John’s point about reefing, I would agree that the clew moves inboard with reefing and I have in-fact studied this issue. My conclusion is that as the clew moves in-board (with reefing), the preventer should remain at the boom end. This is opposite of the condition described above and it comes back to leverage. As the clew moves in-board, its leverage decreases, while the preventer’s leverage remains constant. As a result the geometry improves lessening the forces. It does introduce some bending, but because the forces are reduced and the distances between the forces is fairly small initially, the bending loads should be small and manageable. As the clew moves further inboard (with heavy reefing), the sail area becomes small with much reduced leverage (resulting in a combined reduction). I will have to search, but I read an article some time ago, where Selden was quoted as recommending the same as above. I will try to find that, but not sure I will be successful. If I understand Rob’s original post, it sounds as though his boom has a strong-point at the boom-end. The article I mention above also has a similar strong-point. If Rob in fact has such a strong point, then it gives me further incentive to attach at the boom end.
One last point, is that with the preventer attached to the boom-end, we minimize the risk of the preventer interacting with the shrouds.
All of the above is related to post-gybe concerns. In my opinion this should be the primary concern for preventer configuration, because the preventer is heavily disadvantaged post-gybe so we need to be as kind to the system as possible in this post-gybe arrangement. That said, I agree that a mid-sheeted boom imparts a horizontal and vertical bending moment to the boom system. This will hopefully be by design (i.e. not an aftermarket change) and the boom will be reinforced in both directions to handle these bending loads. I agree that adding pre-load on the preventer will add to both of these bending moments, but also agree with Matt and Eric that so long as we are using high-modulus preventer, the preload should be small and shouldn’t contribute significantly to the overall bending imposed by the mid-sheet. That said, I also agree with John, that the operator of such a system will need to be aware of this issue and exercise greater caution to not excessively load the mainsheet. On the bright-side, the mid-boom sheet has a lower degree of leverage due to its mid-boom location. Unfortunately, the mid-boom sheet usually has increased mechanical advantage to counter this problem. Many end-boom sheets are 2:1, while their mid-boom cousins are commonly 4:1 or 6:1 to overcome the leverage disadvantage. I don’t know for sure, but I strongly suspect that properly designed mid-sheeted booms are substantially stronger than a comparable end-sheeted boom. My intuition is that these mid-sheeted booms are probably capable of taking a much greater degree of abuse.
In summary, my opinion is to leave the preventer attached to the boom-end for maximum benefit and minimum loading post gybe. When the preventer is loaded-up post-gybe, we are essentially staring down the barrel of a loaded gun. We want to make sure we don’t have a failure in that moment when the crew and ship are in a vulnerable state. For those with mid-boom sheeting, be sure to use a high-modulus preventer and go easy on the preventer preloading. As mentioned previously, higher preloading with these high-modulus lines provides very little incremental benefit. Caution crew about the dangers that John outlines with respect to over-loading the mainsheet. This caution applies to all sorts of other systems on our boats and this is no different.
Hi John, Matt and Eric,
First off, may I say that your collective care and wisdom taken in the comments provides insights from both sailing and engineering viewpoints that make this site so valuable for me – just superb guys. And typically thorough explanations and common sense on this issue, thanks.
Which made me ponder overnight on our particular case, and realise that with our in-boom furling we have a mandrill running through the boom to furl / reef the sail. This distributes the sail leech and foot loads to the two designed strongpoints; the gooseneck and the end-boom fitting. The multi-part mainsheet has blocks spreading the load about 40% to 50% from the boom end, but even this distributed attachment does little to mitigate the potential risks, especially the one John describes from sleepy crew.
I think I need to contact the boom manufacturers and ask their view on the “least worst” position for connecting the preventer. I suspect the answer will be leave it at the boom end, but they may suggest otherwise.
The good news is that we have tested our rig in typical trade wind sailing conditions about 10 times (usually at night), both with full mainsail up and when well reefed, sailing from NZ to Tonga in 2017. This was thanks to carbon dust buildup in the electric pump motor for the hydraulic self-steering. Each time our end-boom rigged preventer did its job and recovery became a finely tuned process, including percussive maintenance on the motor housing with a winch handle.
I may ask further questions or comment on the few rigging tweaks we learned from this experience in Part 2, if not otherwise covered.
Many thanks guys.
Thanks Rob. If you get any feedback from the spar manufacturer, please circle back with us on their recommendations.
Thanks Kurt, great answers – will do. Have emailed the supplier.
I’m curious what the sparmaker will say. A boom with an internal furler is inherently much more vulnerable to lateral buckling than one with a closed cross section. Depending on the exact cross section shape, it might be safe to apply loads at bolted-on fittings on the *bottom* of the boom at partial length – but the best case for the preventer will almost certainly be end-boom. And anything applying a lateral load on the boom *above* its mid plane would be very bad indeed.
Hi All,
Just for curiosity, I added a mid boom sheet and a mid boom preventer to Kurt’s picture of sailing deep. As can be seen, in this case the preventer has almost as good an angle (51°) as the sheet (55°) at this point of sail. In the horizontal plane, the load on the preventer will only be about 5% greater than the sheet when comparing the same perpendicular wind load. However, there are 2 key assumptions here that I can think of:
Ignoring the apparent wind argument above, a boom that can survive the normal mid-boom sheet load should be able to survive a mid-boom preventer load with many boats geometries (I did this years ago with our boat and found it slightly more favorable than the Kaufman 47 example here). Structurally, I think the big downside of a mid boom preventer in the scenario above is that the preventer itself including the turning point at the bow needs to be upsized. The payoff for this is more tolerance of user error.
I am curious if there are any other thoughts on this.
Eric
Hi Eric,
That makes sense and it’s good to hear that the preventer load would not be a lot more than the sheet load.
I have to say I’m really conflicted on this one, and perplexed about how to cover it in Part 3.
On balance, I’m more comfortable with attaching at the main sheet because, like you, from observation I know how easy it is to break a boom with the preventer and mainsheet separated.
That said, one thing that did strike me is that if we break a boom by over-tensioning the preventer or mainsheet it’s unlikely that anyone will get hurt, except maybe in getting the situation under control, because the broken parts will be being blown away from the cockpit. But if the boom breaks when caught aback the pieces will be heading toward the cockpit and so the risk of injury is higher, I think.
Anyone have any good idea on how to resolve this, or anything that has not been brought up yet? Matt, Kurt?
What about a compromise where we attach the preventer half way between the mainsheet and the clew? Surely this reduces the chances of both scenarios above, and as we reef the clew moves closer to the preventer. Also reduces the load on the preventer. Right now this is my preferred solution for part 3 but I’m far from sure, and all ears as to why I might be very wrong.
Hi John,
I am afraid that this is a case where I also don’t really know what to say. If it were a single boat, it would be reasonable to run a bunch of analysis and convince yourself of what the safety factors are and how likely a use error could lead to breakage but boat designs are all over the place and I don’t know how to generalize to that degree. Things like boom strength, gooseneck strength, mast resistance to side force at the gooseneck, preventer geometry, sheet geometry, etc. are all different. I suppose one thing that people could do with their own boat is compare preventer angle to the boom to the sheet angle to the boom and make sure they are similar if consider a mid boom preventer although this doesn’t solve for the issue of the higher wind force with the preventer.
Putting the preventer between the points is certainly a compromise solution that can try to balance things. Done with high modulus line and a light preload, it should be fine. And it is more resistant than end-boom to someone cranking on too much preload as the lever arm for the bending moment is much lower. As you point out with the clew moving during reefing, all booms have to be designed to take some bending moment, it is just that mid-boom sheeting ones must take a whole lot more but that is simply a design input that gets designed to. The trick with this for the average user is probably that the math for sizing gear will not be as straightforward. Depending on how Kurt has laid at part 2, this may or may not be easy for them to size the gear.
Our boat has mid boom sheeting with 3 blocks along the bottom of the boom. For our preventer, we attach to the attachment eyes of the after 2 blocks with a short bridle that load equalizes. Once we have the boom <70° or so out, we generally do not run a preventer. I can think of 1 time we did and I ran it from an eye I put on the end of the boom as otherwise the preventer messed with the shrouds too much (our boat is small enough that it is relatively easy to get the boom in and add this line without any heroics). On maybe 2 or 3 occasions we have had the boom at maybe 30-40° and been in super sloppy seas so we stabilized the boom with the sheet, topping lift and a mid-boom tackle to the toe rail but I do not consider this a preventer although to be honest the geometry is not terrible (looks like a sheet with a decent vertical component so needs to be strong but otherwise fine) whereas it would be unworkable with end boom. When it is rolly we do occasionally pull more twist out of the sail than is strictly optimal to keep things from moving too much and I know some people will try to use a preventer here but I don’t think that actually solves the root issue which causes wear on components. Actually one of the nice parts about mid boom sheeting is that our traveler covers about ±40° of boom travel so we often use that instead of the vang and sheet. I am comfortable with our setup for the reasons that our current usage is coastal cruising and we don’t push the boat hard downwind especially in terms of mainsail size. I am looking forward to reading Kurt’s second part and your third to see what we can further improve.
I am curious to hear what others think.
Eric
Hi Eric,
That’s great, thanks. With this comment, this thread gives me enough information to explain the issues that must be thought about when deciding on where to attach the preventer, which I think is a better approach than trying to come up with a calculator that covers every eventuality or a one size fits all recommendation. Bottom line, whatever we do it’s a trade off between possible boom damage scenarios, and only the skipper of each boat can make that call, just as we do every day while cruising.
Hi John,
That is a reasonable way to look at it. I tend to think of these things from a cut and dry numbers standpoint but that isn’t very practical here.
Just for completeness, I took Kurt’s worst case scenario and added the preventer for mid boom. As can be seen, the preventer angle has decreased from 51 to 35° which means loads in the horizontal go up by ~35% in relation to the best scenario due to the change in boom angle. Also, the preventer is now likely interfering with the lower shrouds.
I also added a second line showing if the preventer were not run all the way to the bow showing that the angle can increase from 35 to 43°. Purely from a loads standpoint, this is probably a good thing as that gets the loads back closer to the 51° example of running deep and while it increases the vertical loads, that is what booms are strongest and there is still plenty of angle there. In fact, you could get to 90° horizontal in this example but then the preventer will look like the mainsheet when close hauled meaning loads will be quite high and boom swing will be high so I don’t think it is a good idea to go that far. From a more practical standpoint, I don’t know that moving the preventer makes a whole lot of sense as not many boats will have sufficiently strong attachment points spread along the boat and it means that you need to think about moving the preventer every time you sheet in or out. We have rigged a stabilizing line to our toe rail when sheeted in reasonably far occasionally but it is not sized as a preventer and I don’t think our toe rail could take real preventer loads.
Eric
Hi Eric,
Thanks for doing the added calculation and exploring moving the attachment point aft to reduce horizontal angle. I had wondered about that too, although I’m loath to encourage any point but the bow because of the risk that people will interpret it as an OK to use a mid boom tackle, and as you point out there is the difficulty of adequate attachment points.
I haven’t seen any mention of whether the mainsail is loose footed, or attached to the boom via slides or a bolt rope along its foot.
Does it matter? Can the mainsail load on the boom always be modeled as a point load at the clew?
Hi Steven,
Kurt’s model assumes a loose footed main, which has become pretty standard today. I can also say as an ex-sailmaker that slides on the boom don’t take much load, at least on sails made in the last 20 years, so while they might make a small difference to bending moment on the boom, and possibly optimal preventer position (more in part 3), but as long as we have decent safety margins, I don’t think we need worry about that too much.
Hi Steven,
As John says, I would not be worried for most modern mains. Where it gets really different is with non-bermudian sails. Sails such as gaff sails tend to put a lot more load distributed along the boom but more importantly, their sail area is distributed much further away from the mast. What this means is that the sheet and preventer carry more of the load and the mast less with a perpendicular wind force to the sail. This is somewhat mitigated by most of these sails lacking effective twist control so they struggle to present all their sail area perpendicular but I wouldn’t want to count on that especially if there is a vang involved.
Eric
Sounds like the intention is to eliminate the flying-boom risk by transferring the forces to the hull instantly and completely. And a boom brake can’t achieve this due too poor angles, stretch, and bending.
Perhaps good in a stable heavy cruiser but lighter boats and/or really big conditions could see the boat broach violently and end up being firmly held broadside and vulnerable to being rolled.
If a boom brake is seen as a device to control rather than prevent boom movement then maybe the angles, stretch, and bending don’t matter.
Is there a case for building a fuse into the preventer that passes control too a boom brake when the forces become sufficient to imperil the entire boat. This would reduce the violence of the broach, perhaps even prevent it. It would also result in the boat sailing on on the new gybe rather than being held stalled and broadside. Yes the boom moves tho leeward, but not suddenly at great speed.
HI PD,
Even if the book brake is perfectly adjusted, and letting the boom across slowly, the forces on it are only very slightly less than they would be if it jammed and did not move at all. Bottom line: boom brakes put unacceptable forces on the boom, themselves and the fittings they attach to because of the unfavourable angles.
See Kurt’s answer for physics at work: https://www.morganscloud.com/2024/09/02/building-a-safe-boom-preventer-part-1-forces-and-angles/#comment-311548
We also covered getting pinned and fuses in this thread: https://www.morganscloud.com/2024/09/02/building-a-safe-boom-preventer-part-1-forces-and-angles/#comment-311539
If the sail is attached to the boom all along the foot, then isn’t the sail wind load a distributed load along the boom? Most of your points hold regardless. The only main difference is that while the end-of-boom preventer attachment point still gives the greatest leverage (and hence, the lowest preventer load), it is actually not the best from a boom bending perspective. I believe the leverage argument far outweighs the boom bending argument but just trying to check my thoughts here.
Hi David,
Yes, it does make a small difference, but not much. See detailed discussion further up the thread and on Part 2.
We have been using the good recommendations for our preventer system. The angle of the preventer is clearly the most essentiel as stated.
I have just had a Big discussion with a fellow sailor who uses the boom brake. He says a rigger had told him that the Wind backwinding on the main is more critical towards the rig than the boom breaking. I dont understand the argument and can’t see anyone here bring that point to the table. Could it be there is a difference between straight spreders and backswept spreaders? Is a backswept rig able to sustain a backwinding as good as a top rigged straight spreader mast? All in all the argument from the fellow sailor being that the forces on the rig are better when the sail is let across than keep the pressure on the back side of the main. Does any of this make anysense?
Hi Martin,
I’m no rigger and no engineer, but have about 50 years of sailing behind me, including lots of racing on extreme racers, often with experimental rigs, or far to light rigs, meaning I’ve experienced masts falling more than ten times, maybe twenty, and many times more of other types of failures. I can’t always pinpoint the reason for the failure, but I’ve developed a feel for what is strong enough and what isn’t, and have noticed what events cause problems, and what doesn’t.
The discussion you had doesn’t have a simple answer, since the forces and situations vary much, but some statements can be made. The reason rigs fall is close to never a static load, like a backwinded sail in strong winds. It comes down when dynamic loads occur, like a boom crashing across the boat at speed or with a flogging mainsail. This type of load often becomes many times higher than the static loads present. The dynamic loads also tend to be unbalanced, focussed on a smaller area, like fist hitting a body, while static loads usually spread out more evenly on the structure, as it has time to do that.
Boom brakes have the appealing property that, if they work as intended, they slow down the motion of the boom, thereby dramatically reducing dynamic loads. Great! I was at one point tempted by one. However, they need constant attention and competent adjustment to do that well. I’ve never seen one that doesn’t, and also not one that has decent force angles. Rather, they multiply the forces acting on them. That means boom brakes are a vulnerability more than a solution. When it doesn’t work as intended, it creates a more dangerous event.
Maybe there are better ones out there? I don’t think so, but as an inspiration for what might be needed: On racing multihulls there’s a long curved mainsail track, and the main sheet is always properly tight, so they can never have a crash gybe. The boom always moves across by means of the traveller control lines. Also, these boats also move so fast that the whole situation is different. A gybe is more like a tack.
If a mainsail on a preventer is fully backwinded, that could present some unbalanced forces that could bring the mast down. However, the forces are dramatically lower everywhere in the rig than what a crash gybe will give. I really don’t think any competently built cruising rig should have even the slightest problem with handling the relatively static loads of a backwinded main, as long as it doesn’t flog.
Thanks Stein. Well reasoned arguments!
Hi Martin,
I can’t think of anything much I would add to Stein’s excellent thoughts. Here are the maths on boom brakes which are pretty damming. https://www.morganscloud.com/2024/11/12/why-we-dont-recommend-boom-brakes/
Given those numbers, like Stein, I would have a hard time seeing the mast failing before the boom:
Thanks John for the valuable information. You have always been the source i listen most closely to sailing wise. Fair winds.
Hi Martin,
Thanks for the kind words, makes all the work worthwhile.