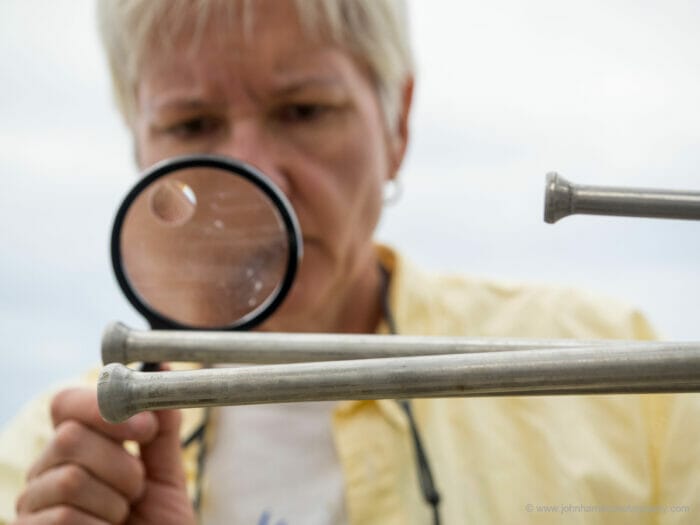
In Part 1 we got the mast out of the boat and worked for hours inspecting a bunch of stuff…and now we get to work some more.
Still, all this effort is worth it to prevent a gravity storm, so let’s carry on.
And, just so you don’t totally despair at the prospect of reading all this boring detail, don’t forget that this is leading to the much-requested rig-inspection checklist.
So grab a cup of highly caffeinated coffee and let’s do it right. Deferred gratification is good for mast karma.
Hi John,
A very nice series of articles.
A few thoughts:
There are (perhaps were at this time) rod rigging maintenance books that did not mention a dab of grease on the cold molded heads prior to re-assembly
My rigger, now retired, said rod should be replaced every 100,000nm, but he said it depended on the size of the rod. It has been a while, but I remember larger rod needed to be replaced sooner than the rod on smaller boats. I would be curious about whether that can be confirmed.
In Europe, I had a required periodic insurance survey which mentioned replacement of wire rigging every 8 years and rod at 10 years. I tried to challenge that and failed: in part as I was told all surveyors in the UK and EU adhered to that schedule. Mileage did not matter.
In a number of my overwintering yards, over the years, I have had to leave the mast up. I always pressured up the backstay adjuster a bit and firmed up the running backstays to keep the rig from movement. I am always surprised when 6 months later everything is as I left it. (Having pressure on the backstay adjuster also keeps the adjuster from “breathing” as the atmospheric pressure changes which saves wear on the seals- I never leave it completely slack even at anchor).
If it fails, there is a default position for my backstay adjuster that is basically full slack. I tried to tension the rig by bringing the turnbuckle to its most closed position and the backstay was not nearly tensioned enough when it was full slack. I had a pair of “tangs” made that were a few inches shorter than the default length of the adjuster. This allowed me to replace the whole adjuster with the tangs and get good tension on the backstay, albeit not adjustable. I was living aboard full-time and this was nice as well because I could continue to sail while the adjuster was off the boat for servicing, which often took a while if needing to be sent off.
I wanted to consider DIY Dyform rigging when I re-rigged in the UK, but was told that Dyform was the name of the wire made in the UK, but that the company had stopped making it as they could not compete with the compacted wire coming out of Asia. I attempted to explore the province of the compacted wire I could find, but that was too confusing. Riggers I consulted and were working with were wary, so I went with rod. This was 10+ years ago, so please check it out.
One rigger I know and some experienced sailors say that a rig that has been to sea in a hurricane should have the rigging made new. Same advice for a really hard grounding. In other words, some shock loading and abuse can be cause for re-rigging.
My best, Dick Stevenson, s/v Alchemy
Hi Dick,
All good information. The big take aways for me are that no one really knows what the right replacement periods are, and further we have to guard against those expressing opinions that are more about serving their own interests than based on any real facts. I know of one rigger that states on their site that all rod should be replaced every six years, clearly more about commercial gain than anything else.
As to getting longer than ten years out of Rod, I was offered that at 12 years in 2019 by Pantaenius UK as long as I had the heads NDT tested, so I think that is a valid option, although, as always, it depends on the underwriter you end up talking to.
Can’t really see how the size of the rod would make a difference to required replacement time. I would think that would be more about the safety margins the designer had built into the rod sizing than anything else.
Hi John
Although it is only of interest to a minuscule number of AAC readers, you are correct in noting that wooden boats, or at least plank on frame ones, cannot stand having their rig set up so hard that the lee shrouds do not go slack when hard on the wind. The traditional structure is simply not rigid enough although a modern wood/epoxy composite boat may be. The resulting flapping around is no doubt hard on the gear, but not as destructive as over stressing the structure would be. I wonder about the rigidity of some fibreglass boats as well, having sailed aboard some that did a lot of creaking and groaning in rough weather.
Another “advantage” of a wooden boat with a wooden mast is that the mast needs varnish every year. This is infinitely easier to do when it is horizontal rather than vertical and a lot easier when all of the standing and running rigging is removed. So, I unstep the mast and strip the gear every year which forces a close inspection of everything.
I have always had the notion that bronze turnbuckles, toggles and related hardware are not as subject to fatigue failure as stainless, but perhaps that is incorrect.
Hi Wilson,
As you might of guessed, I put in that exception based on education from the horribly overpaid AAC wooden boat consultant…you.
Certainly makes sense since plank on frame wood will, in my limited experence, tend to permanently change shape over time if in any way over loaded. I’m thinking about wooden boats that hog over time, when I say that.
I wonder if this is a function of plank on frame not being a homogenous material, so that over loading changes the relationship between the planks and frames—slippage if you will.
And extrapolating from that maybe that’s why fibreglass boats, if properly constructed, are happy enough to have the lee shrouds tight without permanent damage.
A key point in all of this is that (counterintuitively) having the lee shrouds just firm when going to windward does not increase the maximum load on rig or hull when underway. Said load is governed by the maximum stability of the boat.
However, said no-slack tune, does increase the load on the hull when the boat is at rest, so I’m thinking that may be the problem.
A good discussion of that here: https://loosnaples.com/how-tos/tension-gauges/
And yes, as far as I know, bronze does not have the deterioration issues of stainless steel.
Hi John,
This all seems very reasonable. At the same time, it is very frustrating to me that we throw away huge amounts of rigging that is still in perfectly fine shape by coming up with a conservative time and miles based approach. In truth, conservatively sized rigging that has been well looked after and not damaged could go indefinitely. Unfortunately, I don’t know how you would practically implement this as conservatively sized would need to be quantified for each design and then you would need to make sure that it was always in good shape and never had any bad loading (forestays are subject to not nice loads so I would still replace them). And your engineer is spot on that little knicks on the surface are a really big deal in any highly loaded structure. So all in, I think your recommendation is about right.
One technique that I find very helpful when inspecting wire is to simply run your hand around it while it has a preload on it and make sure it is still round, if it feels lumpy at all, you have a problem. I do this around any areas that could be higher stress such as at the exits of fittings and around spreader tips. This is in no way a substitution for a more detailed check but it is something that you can check very quickly on a quick deck walk or whenever up the rig. I am going to have to try the trick of a phone for a magnifying glass, it will certainly be more stylish than the magnifying visor I use.
Regarding wire quality, it is definitely an issue and it is actually an issue with most materials now. The more reputable suppliers are likely to include a material cert and/or a certificate of conformance with each reel of wire without even being asked. Asking your rigger is not a bad idea although I suspect not all will be able to produce one even if they originally received it. I have gotten a copy with each set of wire that I have bought. One thing that I think is probably equally important is if you are having a rigger do a swage, ask for proof of calibration on the swaging machine. The dies in these wear and other things can get out and then you may have a swage that looks good but won’t hold well. I can think of 2 riggers who told me that they haven’t had any issues so they couldn’t see why it would be checked and on one of them, I looked at a terminal in their shop and could see it was no good but they were very busy making ends for people.
Eric
Hi Eric,
Great comment, full of great tips, thank you. I will include them in the final check list and then update these in depth articles with them.
To that end, three follow up questions:
Hi John,
Regarding feeling the wire to see if it is out of round, it just feels a tiny bit lumpy to me. If you take a 50′ long shroud, each individual strand is significantly longer, like maybe 60′. Winding around each other is what makes the end product only 50′. If you have a broken strand, the rest of the strands are trying to make a straighter line which is a lower energy state so they will pull in and force the loose strand out a bit as it is no longer held in by tension. It is subtle but you can feel it. I have felt it a few times including on a boat I was about to deliver, my parents daysailor and some club boats at a club my wife used to belong to so we could sail weeknights too. In all cases that I can remember, the broken strand had broken just inside the swage fitting so a visual inspection would not have caught it right away and we really had to look and sometimes cut to find it. I don’t know the incidence rate of breaking just inside the fitting versus just outside and it may be that there are many more failures outside but those are more easily caught. Regardless, if a strand is fully broken and there is tension on the wire, it will feel out of round in that area.
I am not totally sure what the calibration process is for these machines but I am aware of a few things that are done to check or calibrate. There are a series of MIL standards (MS51844E for example) for this stuff that I believe most people will use but there may be other standards I am not aware of. The most basic check is measuring the OD of a swaged fitting which can be done with a micrometer or calipers. This is actually something that can be done on every fitting and given how quick it is, may make sense as a customer. You can find charts of the acceptable range pretty easily, here is an example from Hayn: https://hayn.com/swage-specifications/
I would hope at the very least that any rigger has a go/no-go gauge and is checking the fittings but I am not confident that actually happens. You can also do a pull test of a few samples. There are many calibration services out there that handle all sorts of different tools and machinery and it is very common for people with equipment to have a calibration contract with them. There are generally 2 types of services, one where they actually perform a calibration and adjust or replace components as needed or one where they simply provide a measurement of where you are in your calibration range and then it is your responsibility to get service if needed. In truth, a lot of the calibration checks can be done yourself but you don’t get to claim that a professional calibration service did it so it depends on what you need. The real question is what you do if you measure and find you are out of calibration. Typically, that would mean you would need to check all samples since the last calibration that passed which is part of the reason why you try to make sure to never fail by doing preventative maintenance and regular calibration checks. Having said all this, it may be that you should either plan to measure and visually inspect the fittings upon receipt or you should be certain that your rigger is using a go/no-go (that is isn’t worn, these actually typically get calibration checked too) or measuring.
What you will see for poor swages depends a bit on the machine used, I think that by far the most common will be roller but there is some rotary going on in the marine world too. As Colin mentioned, some fittings can come out of straight. I don’t actually know at what point a fitting would fail but if I could visually see this, I wouldn’t want it unless the fitting manufacturer had a spec for acceptable that it was within. In the case that I could see, the fittings were noticeably not round either due to the dies being too worn or the shafts being out of parallel but I don’t think any number of passes (2 is usually the recommended and the max is like 3-4) would have fixed it. I also strongly suspect that a basic caliper measurement would show that the fittings had not been fully compressed but I didn’t need to go that far to know to walk away.
Eric
Hi Eric.
That’s great, thanks. As soon as you pointed out that a lump would appear to indicate a broken strand inside a swage, I got it. I will definitely add that to the check list and the above.
Also, thanks for the fill on checking swages, I will add that too.
Eric.
What are your thought on checking the head diameters with a mic or caliper ( don’t like these as much, not as accurate) when the mast is out? Would there be apossibility of wear or deformation of the heads on older rigging?
I had a surveyor tell me that the rig was too tight on
The CS 30 that I bought last year. I am wondering if this constitutes the abuse that John mentioned?
Thank you.
Colin Post
CS 30 Top Hat
Hi Colin,
These are not measurements that should change over time, they tell you if the original swaging job was done properly. The outside diameters of swage fittings are not subject to wear and if there has been plastic deformation, that is a problem and you want to know it and condemn the fitting. Good calipers are fine for this, the tolerance band is reasonably wide but using a mic certainly doesn’t hurt and can help if you are right on the edge of the band.
How did your surveyor determine that the rig was overtensioned? Did they use a gauge? Did you sail the boat in 20 knots of wind and look at lee shrouds? Was the mast step deformed? Very few people will just be able to pull on the rig at the dock and do the mental calculation of the wire diameter, the span, etc and make an accurate determination. My limited experience with surveyors unfortunately suggests that you should be suspicious of statements like this from them. Still, it suggests you should carefully go through everything much like John has had to do with his new boat.
Eric
Hi Colin,
I would agree with Eric’s concerns about the surveyor’s assessment since it’s difficult for me to understand how he arrived at it in any sort of reliable way. It’s actually pretty difficult to over tension the rig on most production boats as the boat will bend long before the safety margins on the wire is exceeded.
Not all insurers are adamant about replacement of rigging at 8 or 10 years, so it’s worth asking them. As our rig was in perfectly good condition at ten years I asked our insurer if they would accept a rig inspection by a professional. They did, he did an excellent and through job and they extended our cover for two years.
I’m in total agreement that rigging is not an area to skimp at all. Eric’s comment about bad quality swages due to worn and/or deformed swages is absolutely right. I’ve seen new swages that were bent or creased on a number of occasions and that’s just asking for trouble.
Hi Colin,
That’s good to hear. I remember you getting that done here in Nova Scotia. I will add that too.
Hi John,
Interesting discussion.
My take on the considerable rig on Tanielle is to use SAF 2205 duplex stainless steel in rod form. I will machine end fittings from the same material and weld them to the rod. This ss is the same strength as Nitronic 50 but has far superior fatigue properties. My caps would require 26mm 316 but only 20mm 2205 rod saving weight and windage. So far the majority of mast manufacturers end communication once this is suggested so I imagine it will be impossible to insure the rig.
I would see this rig lasting a very long time and probably never needing to be replaced.
Of course it would still need inspecting and there will be galvanic issues with aluminium, eg foils and masts.
An australian company Arcus Wire has the Hamma range of 2205 wire which I suspect is Indian.
My next step will be to ask AE Smith the NZ rig engineer who did all the rig and mast calculations for Hoek design on Tanielle, to look at the 2205 issues and benefits.
Hi William,
Your suggestions seem interesting. I’m not very competent on metals, but have noticed the benefits of duplex stainless. My question here wound be the welds. Wouldn’t they disrupt the uniform strength of the rod? The superior strength and corrosion resistance of duplex is usually explained by its tighter bidirectional crystalline structure. The welding process would leave a transition zone where the cold formed rod material goes from welded to not welded. I’d assume the crystalline structure would be left not homogenous, which would seem to be a weak spot? Even if this isn’t the case, I’d be wary of the transition from the thin rod to the larger terminal. Just the change in dimensions might make a focus point for loads…?
All this is just questions, curiosity, not my opinions.
Since you seem positive to exotic materials and performance, a carbon mast would solve the corrosion problem, while simultaneously saving a lot of weight and being far stronger. While I’m at it: Using Dyneema for the standing rigging will also save a lot of weight, and money, and is easy to inspect and replace, which on the other hand must be done far more often. It will also be thicker than rod, but about the same as ordinary wire, so more drag in the air than rod. In my opinion, Dyneema is the only smart solution for a cruising multihull, due to the wide platform and rig configurations, while on a cruising monohull, I don’t think so. The high end racers use high modulus carbon rod these days. I’d never suggest that for a cruiser, but it does give minimum drag and max stiffness.
Hi Stein,
This is way past my pay grade, but your question about welding jumped into my mind too.
Hi William,
That’s interesting. That said, although I’m in no way qualified to evaluate your idea, my general recommendation for cruisers is to stay away from pioneering new technologies: https://www.morganscloud.com/2013/10/25/want-to-get-out-cruising-dont-be-a-pioneer/
Hi William,
Apologies if this is all obvious to you, I am not sure what you have studied in this regard. The old rule of thumb is that the higher strength an alloy is, the harder it is to attach to it. I have experience with Duplex 2205 but never with welding it and I would share some concerns voiced here about that unless there was a lot of tightly controlled post processing. Not only does welding affect the crystal structure, it leaves a prestress and leaves geometries that have stress concentrations if not processed right.
Most techniques of attachment like cut threads remove material and creates stress concentrations which decrease strength which is not good. There are some forming techniques such as used in heading rod, rolling threads, etc that build up material but these create geometric stress concentrations unless spread over an enormous area so that all changes are incredibly gradual.
There are some cool tricks that you can play to deal with a lot of this but I think applying them to rigging would get quite exotic and you should be looking to carbon or PBO or whatever first. For example, in fatigue applications engineers will sometimes spec things like shot peening, laser peening, cryogenic treating, etc but these all require process development and would require you to put a lot of different vendors together. I have spec’ed all the processes I listed at some point but they were always highly specialized applications where there would be lots of testing and we were willing to pay a lot for the performance needed.
Eric
Hi Stein, John and Eric,
Welding duplex gives 100% strength.
Tanielle is a 24m ketch built entirely from duplex.
We got welding tips from the duplex supplier then did our own destructive tests It took 3 attempts with a 100 ton brake press to break a 30mm x 6mm piece joined by welding.
The break was in the HAZ zone.
The 2 welders were then certified by Lloyds as was the steel and welding wire. The yacht welds were also xrayed.
In welding the rodto the forks I would drill a hole in the fork , then cut slots so the welds are in shear. The weld around the top would only be for appearance and to avoid a crevice. The fork would be machined from a solid bar. 2205 comes in differrent flavours and granular structures and my flavour is SAF 2205 which has a much finer granular structure and increased strength even before heat treatment. All up we used 38 kilometers of welding wire so can probably claim a little experience. One of the welders was a retired welding teacher.
http://www.tanielle.com.au
Hi William,
That’s one impressive boat!!!
It also seems like you have, to put it mildly, done your due diligence on this material, and on a lot of other relevant topics. My only gripe is that it seems a pity to hide that material behind paint. I know it’s not realistic or smart to have a polished stainless steel hull, but what a vision that would have been! Thanks for sharing and congratulations with the boat!
Hi William,
Interesting, I will have to look into welding duplex more at some point. You have quite the impressive project there, I think you must have posted a picture or a link in the past as I have a vague recollection of this. I can now see more of what your thinking is. It would be interesting to look at different options and see the best way to reduce weight aloft such as going to a carbon fiber mast or synthetic rigging or duplex rigging or whatever else there may be.
Ignoring weld strength for a minute, if I understand what you are proposing, you still are introducing a pretty significant stress due to geometry. Do you have a plan for how to deal with this? Any change in diameter or shape is a stress concentration including a change to a larger diameter and in this case it means tension in the surface of the material which is the worst if you want to discuss fatigue. The concentration is due to the stiffness of the bigger diameter being greater and being at a greater radius so if you draw your stress lines, they really concentrate around the step as they try to transfer load out. Rod fittings are a decent example of about as practical a mitigation to this as is reasonable, the shape of the end is designed to give a nice large fillet and the mating fitting puts compressive stress on it that also helps but still it is the site where you will have issues.
I am guessing that the rod doesn’t have good enough tolerances and is too difficult to post machine to allow you to do a shrink fit to it? The advantage of that is you can make a very gradually tapered socket to shrink fit on so the stress concentration is much less pronounced. I have never seen a shrunk fit fitting on rigging but most rigging is small enough in diameter that you would need very tight tolerances and a large temperature differential for it to work whereas yours is big enough that it starts to work a lot better although I suspect the tolerances are still prohibitive.
Eric
Hi Eric,
Thanks for your kind words.
I had in mind discontinuous V1 so the lower could heavier and allow for welding a custom fork tapered to the top.
Alternatively the rod itself could be threaded.
Each of the higher segments would also be oversize although reducing in diameter as we went higher.
Of course this all needs designing and finite element analysis.
I once had a rudder that was a shrink fit and Tanielle has 4 taper locks to connect the quadrant and ram arms to its 110mm stock. I don`t think I would be comfortable with either method on rigging. Perhaps a shrink fit combined with a swage press could work and could be worth experimenting with to determine breaking load and repeat consistency.
While I take your point on fatigue and stress concentrations the safe option is simply to overbuild. The existing rig design (see website) has the V1 as 115 Nitronic 22.2mm 48t UTS , V2 as 01 Nitronic 19.5MM 36.5 UTS V3 19mm Dyform.
I woud up the V1 to 25.4mm Duplex V2 to 20mm Duplex and the Dyform to Duplex wire.
My intention here is to elicit the wisdom of the group and get the sort of feedback you have so kindly provided
Hi John,
Do you believe your rule of “no loose lee shrouds …/… ” should be applied as well for catamarans?
My assumption is that catamarans have more structural “flexibility” on the lateral axis, compared to the lateral “stiffness” of single hulls, due to the structure holding the two hulls together, and hence may justify tuning with loose lee shrouds in heavy wind, without correlatively flapping lose during winter periods.
Thank you in advance.
Patrick
Full rule: “This is why all boats, with the possible exception of wooden ones, should be tuned so that the lee shrouds are not loose when hard on the wind and fully loaded—applies to wire standing rigging, too”
Hi Patrick,
As I have many decades of multihull experience, including professional racing in the Formula classes, plus designing and building boats, I can say; no, that rule does not entirely apply to multihulls. I’m fairly certain that John also agrees about this and just forgot to mention it.
Most (not all) multihulls are indeed far more flexible, meaning that it’s often not possible to remove all slack. In most cases it’s just the leeward top shroud that is slack, and it’s not on a spreader. (Diamond stays should never be slack.) The much wider base means that the shroud angle is far better, meaning that the mast doesn’t get too much play, even with a lot of slack under load. I prefer to tension it as much as possible. At least make sure it’s never slack when not sailing. If tightening hard, be sure to know the structure of that specific boat.
The trouble with Lagoon 45 that has become very public lately, via Parlay Revival on YouTube, is a good example of too tight for a poorly made structure. Lagoon is by no means the only manufacturer with this build method and weaknesses. Most “budget” production boats, also monos, have the same problems to some extent. Wood is beautiful, strong and cheap, but it rots in water. For some “strange” reason wood inside boat structures tends to get wet. Why builders can’t grasp this and why they keep using wood for structural pieces is a mystery to me… (Nope. That’s just irony. Google “planned obsolence” or “The light bulb conspiracy.”)
The performance will not suffer much from this slack, since the fore and aft rig tension is what matters and that should indeed be properly tight. If you have a cat with no backstay or such, it’s a good idea to set the main halyard aft when not sailing. Tension it well to keep the headstay and the rest tight. I also usually put ropes across the head stay or wound in a spiral around the sail, to reduce oscillation in strong wind.
Even though wooden boats and multihulls often need the shrouds and perhaps more to not be entirely tight all the time, that doesn’t mean they have less of the problems other boats have when a slack rig piece is vibrating. It just means that we need to be more vigilant in our maintenance.
Hi Patrick,
I would go along with Stein’s answer, particularly since he has way more experience with multihulls than I do.
I would also change the rule around: if we have a boat on which we can’t keep the lee shrouds firm, then we should not fit said boat with rod rigging.
Hi John,
You mention disassembly of compression cone terminals. I tried to do that on 2 occasions. The first was when I wanted to replace a bent segment of my roller furling profile and the second when I replaced the cap shrouds. In all cases it turned out to be impossible, at least to me, to disassemble the terminal with any hope of reusing the wire it was attached to. Of course no problem with the cap shrouds, they had to go anyway, but annoying in the case of the headstay inside the furling extrusion: The only way to disassemble the terminal, (pushing the terminal’s body away from the wedged up wire) was to cut the wire one or two inches from the terminal, and hammering down on the protruding wire with brute force. That did the trick finally. Not even fixating the wire in a vise and hammering on the lower end of the terminal – with a wooden block for protection – was enough to make the terminal body budge. Not to mention that the vise probably did the wire no good. Of course it’s possible to unscrew the eye or fork, is that what you mean by disassembly ?
My conclusion is: never fiddle with a Norseman terminal unless you want to replace (or shorten) the wire. Besides, it seems impossible to get hold of new cones as Norsemans are no longer made. But there are other brands of course.
Do you or anybody else know a way to disassemble a Norseman without destroying part of the wire ?
Hi Hans,
I have taken a Stayloc apart successfully, but it was on flexible wire (steering cable) not 1×19, so not the same thing at all, and probably not as highly loaded, and that was a struggle, so I think you are right and will make a note of that in the above when I edit it to add everyone’s wisdom.
Hi John,
I just found mention of the “disassembly for inspection” here:
https://www.practical-sailor.com/sails-rigging-deckgear/hidden-causes-of-rig-failure
and that makes it clear to me that by disassembly really is meant to unscrew eye or fork or whatever fitting there is from the terminal’s body and have a good look at the dead end of the wire. It could be called “opening” rather than disassembly. And of course it makes sense as the bad stuff seems to be happening where you can see it after having the terminal opened. But the threads have to be locked anew.
As an aside: Tylaska makes the cones for the Norseman fittings. They seem to have all sizes in stock. I needed new ones mainly for the expensive backstay isolators. As I have 2 independent backstays I decided to live with the old isolators although I replaced the wire.
Hi Hans,
That’s a good point. That said, I was under the impression, but could easily be wrong, that once we back off the thread on the eye, we are supposed to replace the cone before putting it back together. If that’s true, we will be starting again, and almost certainly cutting the wire.
I googled around a bit, but could not find a definitive answer on that. Does anyone know for sure?
Hi John,
I just replaced my lower shrouds and the backstays with new wire. The backstays had (and have) Norsemans on their lower ends and there are these isolators with 2 each Norsemans. So I gained some experience with this type of compression cone fittings.
I see no reason to replace the cone if the terminal is just opened (unscrewed) for inspection as the cone is not affected by this operation. Getting the threads cleaned enough for a proper redo of the loctite treatment could be a problem though. I didn’t have this problem as I replaced the wire anyway and so had good access to the threads.
I found a good way to get the terminal off the wire in the process: cut the wire directly at the terminal and back out the cone with the wedged up wire out of the terminal’s body with a suitable punch, that way losing only an Inch or so of wire. This short length can in many cases be compensated for with the turnbuckle. Also I wondered at first why the cone has to be replaced at all, but once you have the wedged up wire in hand it becomes very clear that the cone is compressed on the wire’s core so much that you’re just not going to get if off undamaged.
Bottom line: if not sure about the terminal then the best way is to check if the turnbuckle allows for some shortening of the wire and if so, cut and disassemble the terminal and redo with a new cone. One could also add a toggle to make up for the lost length if necessary, although not quite so elegant.
Hi Hans,
A good analysis that makes very good sense to me. Thank you. Also, thanks for the tip on getting the cone off with minimum wire loss.
I do still wonder if there is some reason that the cone should be replaced after just unscrewing the fitting for inspection, but I have to admit I can’t put a logical reason together to support that. What I should do is call say StayLoc and ask them, but right now I’m so busy with stuff I have promised that I’m scared to add something else to the list!
I watched one rig come down. Fortunately, it was inshore and was a rotating mast, so it lifted off the socket and the mast was undamaged. We helped them collect the pieces and towed them in. No one was hurt.
The cause? A bent toggle fractured. I had two of those crack on my Stiletto 2 (both in what you marked as the “danger area”) but I caught both during one of my regular walk-arounds (not the spring inspection–they were fine then). Ever since, I make a point of looking at them every few months.
Thanks, John! You say above “…because we discovered that she had been stored over at least one winter, and probably two, with the mast in—never a good idea, in my view…” I winter my boat in Rhode Island, and it seems 95%+ of owners leave the mast up. I’ve been taking mine down each winter, and storing it indoors. But I feel like the oddball. Would you please elaborate on this.
Thanks!
Anthony
Hi Anthony,
Good on you. You are not an “oddball”. https://www.morganscloud.com/2014/11/01/the-dangers-of-storing-with-the-mast-stepped/
Added to the reasons I list in the above article, leaving the mast in add significantly to the wear and tear on all components of the rig due to constant vibration over the winters.
Hi Anthony and John,
That said, and I agree, but most of the mast damage I have seen over the years has been on the unstepping and stepping of the mast and its storage (and wallet damage). I suspect the breaking point is closer to taking the mast out, but may be dependent on the skipper being present when the work is done: for example, I have watched turnbuckles dragged in the gravel/dirt on masts when no owner was present, but the crew was far more careful when I was there lending a hand and being involved.
My best, Dick Stevenson, s/v Alchemy
Hi Dick,
I agree on being there when the mast is unstepped, or stepped. Some tips on that here: https://www.morganscloud.com/2014/12/06/9-tips-to-make-unstepping-your-mast-easier/
Hi. What to use for lubrication of the turnbuckles? A Google search yields so many contradicting recommendations. I have used Lewmar winch grease (which is a calcium grease, and which is supposed to be VERY good), but Selden makes a rigging OIL that they recommend using (twice a year). Other say to use a molybdenum grease, and I even see some recommend Mc Lube SailKote.
Thanks, Arne.
Hi Arne, I hav used anhydrous lanolin for decades and been very happy. Lasts for a whole season or longer. I will be interested in what others use.
My best, Dick Stevenson, sv Alchemy
Hi Arne,
I use my favourite Lubriplate, as I do for most everything on the boat. 130 AA https://www.lubriplate.com/Products/Grease/Multi-Purpose-Greases/130-Series/NO-130-AA