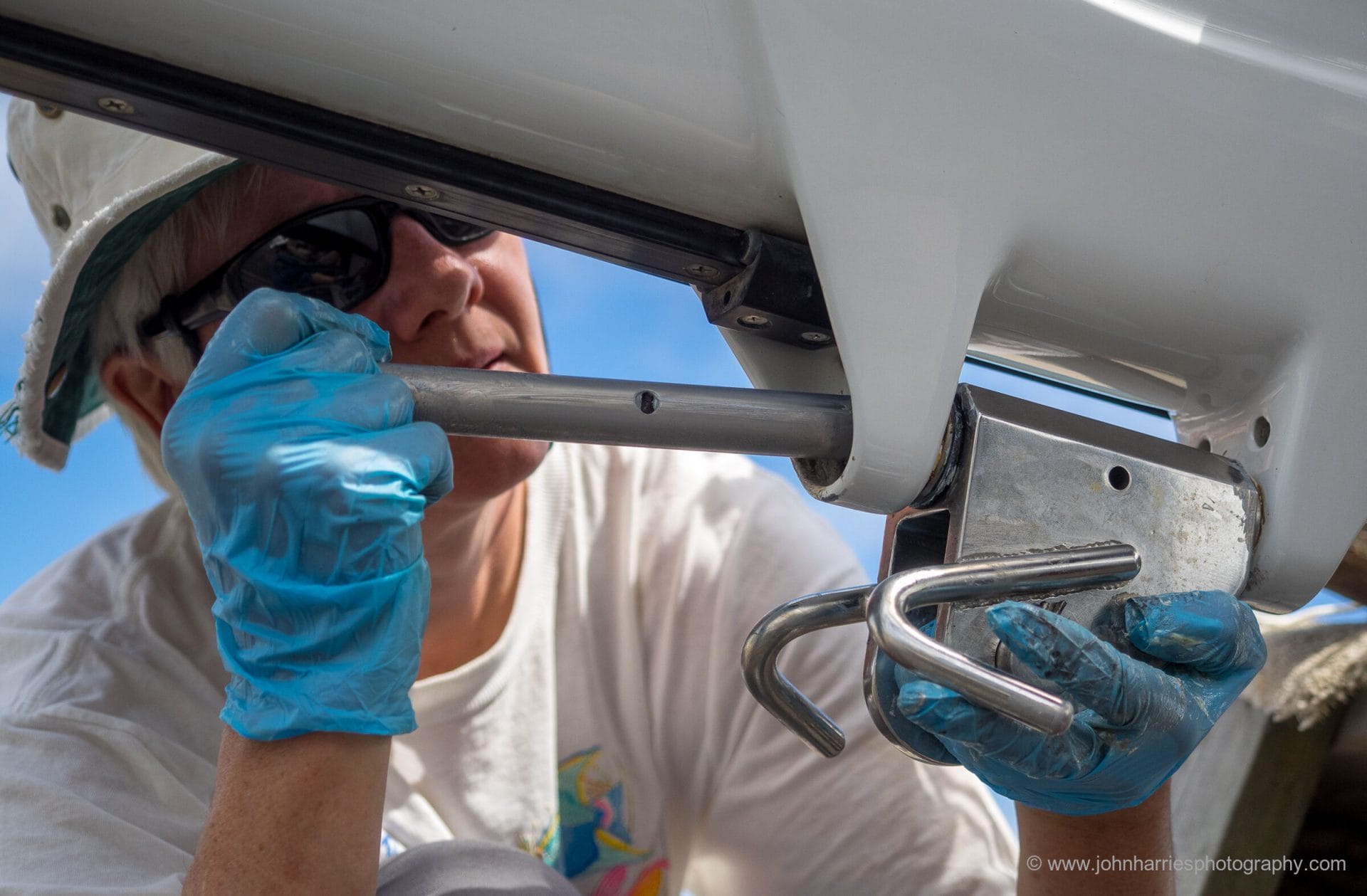
This is the first of five chapters on rig maintenance and inspection ending with a downloadable check list.
Interval
The absolutely longest interval between unstepped inspections is five years, and three is way better. And boats that do a lot of mileage should unstep every 30,000 miles—equivalent to a circumnavigation.
Yeah, I know, many owners don’t do it that often and some never do.
But, as I have written often enough to make you readers want to puke:
Seamanship is the fine art of actually doing what is a pain in the ass to do.
So let’s get those masts horizontal, before a gravity storm does it for us, and dig in:
Timing on this is perfect. I’ve got the mast down on my new to me 1981 Tartan 37 and working on pulling and replacing the original chainplates and the rest of the standing rigging. Can’t wait for the rest of the series.
As a light aircraft pilot who uses checklists every time I go flying, my inner pedant is screaming that this article is a guide, not a checklist. A checklist is a list of bullet points, designed to be read by someone who is already very familiar with the process, to ensure that they haven’t forgotten anything critical. A checklist looks like this:
https://studylib.net/doc/8358531/cessna-172-skyhawk-checklist-mentone-flying-club–inc
Hi Alistair,
You are right, and that’s exactly what I have written at least three times, twice in the above and once, in more depth, in the introduction.
Hi Again Alister,
To avoid this misunderstanding I have changed the title to inspection. The key point is that we have to, as you say, understand the process in depth before a check list is even remotely useful.
That said, you definitely need to read the introduction to this series: https://www.morganscloud.com/2022/01/16/cruising-sailboat-rig-inspection-checklist-part-1/
Thanks, I did read the introduction when you first published it. I guess I had slightly unrealistic expectations that the second article on this topic would jump straight into the checklist.
Hi Alistair,
The good news is the check list is in progress and looks good, but then again, pretty much useless without the articles to back it up in the same way that flight training and the aircraft’s manuals backup a flying check list. Point being, the articles need to come first.
Great, thank you. Sorry for being such a pedant!
Hi John,
I see nothing to disagreee with, but I’d like to emphasise what you say about using monel rivets when fixing cracks in an aluminium tube.
The first half of my racing we only used alu masts. A lot of them came down, as they were made to be as light as possible. (Never lost a carbon mast, when that became more available, even thought some were on the same boats and typically less than half the weight…)
The issue is that the insert and/or external plates critically need to be pulled very tight to the mast tube. There must be no gap and no slack. That means that the rivet must have a high enough pulling power to shape the alu pieces and force them together.
We had number of small hooks that fit through the hole for the rivet, with a nut so it could be tightened to start getting it into place. Got them from an aircraft tech. Then we’d put some rivets at the leading edge of the mast to pull the inlay into the hardest bend. The first rivets would be drilled out and replaced as the following ones pulled it closer. You can feel when a rivet hits a dead end. You can also see in the neighbouring still empty rivet holes that the crack between the mast and inlay disappears.
We also used a bit of epoxy with silica filler to further help removing all gaps when the shape was difficult, but I don’t think it helped much, when all else was done right.
The reason for obsessing with tightness is that all the strength comes from the metal sheets being held together with absolutely zero space for movement. The rivets need a lot of tension. Monel rivets do that. Aluminium rivets just don’t.
Hi Stein,
Thanks for a great fill on the challenges of sleeving and doing it right. Invaluable information.
Hi John,
This is very timely, as I have stripped all of the gear off of the mast of our, new to us, Cambria 46, and am working on sanding down to repaint. I got your memo on welding just in time. There are a number of old fastener holes, as well as a couple of elongated holes from my inelegant removal of very frozen screws, that I had planned on having fill welded. The plan now is to use Belzona 1111 to fill holes and to redrill/tap where needed, unless you have a better suggestion. I also plan to tap and screw the hardware that previously had rivets, as I have plenty of experience in the former and none in the latter. Do you see a problem with that?
On a separate note, thank you for the wealth of information you provide on the AAC site. It has been, and continues to be, the go-to resource for me during the process of searching for, purchasing and refitting our vessel for extended offshore cruising. The wealth of knowledge presented by you and this community is indispensable!
Hi David,
I have just a limited amount of experience with screws tapped (threaded) straight into the aluminium, but I don’t like it. Every single time I’ve unscrewed one, it might seem to hold fine, but the thread in the alu is just dust. It seems to be dissimilar metal corrosion, which could perhaps be prevented by using the right protection, but still I cannot bring myself to trust it. Alu is just way too brittle and weak to take significant loads on such a small amount of material.
You can also use a nut and washer on the inside of the mast. usually easier than it seems, even in the middle of the mast tube. You use long battens, tape and a flashlight. That side of the tube must face down, look into the hole until the nut in the wrench is right.
Anyway, if possible, use rivets… Monel rivets are much stronger than threads in alu, and perhaps even when compared to nuts, partly because you would typically use more rivets, meaning you spread the load far better. They’re very easy and fast to use.
Thanks Stein.
Cracks tend to happen in the parts of the spar that are most highly stressed in bending and/or tension. Let’s assume your mast is 6063-T6 alloy. Tensile yield strength is 214 MPa @ 24°C. You find a crack, you “fix” the crack with a TIG torch, and you put it all back together. Now you have a small region of 6063-O aluminum (tensile yield strength 48 MPa) in a spot that has already proven to be too highly stressed for 6063-T6. Obviously the crack is going to return, with a vengeance, once that rig has been loaded up a few times.
Not all parts of a spar are like that. I would have no qualms about fill welding (with TIG or laser, using minimal heat input) to repair old fastener holes in lightly loaded areas that are primarily in shear or compression, and where the repair is small relative to the total section area, eg. in the sides of the boom. I would not do that in areas subject to bending or tensile stresses, particularly if those stresses are cyclical, or near areas of highly concentrated loads (such as the vang bracket, gooseneck, spreader bases, or tangs). Of course, this statement presupposes the ability to *correctly* discern the type and magnitude of the stresses on a part, which is not particularly intuitive, at least not without significant training in structural mechanics.
Hi Matt,
Thanks for the fill on that, very informative and pretty much exactly what the engineer who advised me on my damaged J/109 mast told me.
One thought, although I can see welding up screw holes, perhaps not if one intends to drill them out again and use machine screws. I’m thinking that the welded material is not going to have the thread holding strength that the old did?
Anyway, given, as you say, that actually accessing where welding will cause a stress riser and where it will not clearly requires an engineer, I think I’m comfortable with just saying no welding, at least without that professional input.
Hi David,
I think I’m probably with Stein on this one. And if the mast designer used rivets, then I would definitely do the same.
That said, screws can work, but the aluminium must be at least 1.5 fastening diameters thick to achieve proper strength, any less than that I would use monel rivets.Also, I would not be comfortable with the thread holding into a material like Belzona, so if it were me I would over-drill to get to good aluminium before fastening. Of course that means over-drilling the fitting too and that can be a problem if you don’t end up with enough material around the fastening to prevent pull through.
Another option, is, as Stein suggests, a nut and washer, although that can be a problem on a curved surface.
By the way, the Cambria is a great boat.
And thanks for the kind words.
Thanks John!
Hello John,
I am wondering what your advice would be for a really good rivet gun using monel rivets on aluminum mast.
Yianni Michaels
S/V Artemon
Sun Légende 42
Hi Yianni,
Sorry, I don’t have a recommendation. For the last 30 years I have had a bigger boat where all the fittings on the mast were attached with machine screws, so I have not had occasion to use a rivet gun in years.
Can anyone else help?
Hi John and John, 🙂
I can’t recommend a specific tool, but a couple of general guide lines:
Monel rivets are very hard, so to pop them you need a lot of power. For the bigger rivets, (which we should use), you will need a fairly hefty tool.
The weak point on all of them is the teeth gripping onto the nail of the rivet. They need to be made of extremely hard metal. When they get dull, the tool is useless.
If you got an expensive tool, you can replace the teeth but they alone cost more than a complete cheaper tool. The pro tools definitely last far longer, but most amateurs will be fine with a simpler version. If you treat it well, you will perhaps never use it enough to wear it out. If you do, you can perhaps buy another 5 or 6 of them and still come out cheaper…
If you make sure to never get dirt into the tool, keep it meticulously lubed and use it smartly, it lasts far longer. Poor lubing gives a lot of friction at critical spots inside the tool, which means you add force to do the job. That added force translates into way more wear everywhere in the already heavily loaded tool.
I’m not sure what to recommend for “really good” rivet guns.
I have one of the Princess Auto 13″ compound-lever ones (
https://www.princessauto.com/en/13-in-heavy-duty-hand-riveter/product/PA0008420937 ) and have found it to be totally satisfactory. The next significant step up from a tool like that is a $200-$400 pneumatic rivet gun, which is overkill for one job but worth it if you’re running a commercial shop.
Do note that, in general, small right-angle hand riveters do not have enough pull force for mast & rig work; they’re meant for light sheet metal stuff like eavestrough and HVAC. You need the symmetrical compound-action type in order to get enough tension on a big rivet for it to hold in mast & rig work.
Hi Matt and all,
The other area where rivet guns can be a must is the connections on foil pieces for some roller furling designs. I have one, used once under supervision of a rigger, and put away in deep storage. It was fairly easy on the pull, so I suspect it is much lighter weight than is needed for spar work.
My best, Dick Stevenson, s/v Alchemy
I have a right-angled one and agree with Matt’s assessment of suitability to purpose. I have used it on the boom for jackline eye straps, and on the spreader for flag halyard block straps, but use tapped holes and machine screws for the mast itself, for instance on mast steps custom made for my alarmingly sized feet.
My foil pieces on my furler seem to be all 3 mm Allen-type hex screws, so no worries there.
Hi John,
I have 2 rivet tools that will handle 1/4″ pop rivets. The one I mainly use is, I believe this one: https://www.grainger.com/product/MARSON-Rivet-Tool-4Y128 . It appears to have gotten even more expensive but it does work very well and has no problem with 1/4″ rivets of any material. I really like the long handles and that only 1 handle moves because it allows me to get the rivet really straight as it starts to pull in.
The other tool is a no-name brand that looks similar to this: https://www.amazon.com/Dorman-743-100-Rivet-Gun/dp/B0049E4VJO . I got it for working in a confined area and I have also used it while aloft. It works fine but I find that it is much harder to keep the rivet from wobbling as I start to actuate the handles.
Eric
Newbie question: Last spring Kelly and I partially rebuilt a newly purchased rig that had been sitting horizontal in New England weather for 15 years. The spreader ends were badly pitted under rotted leather covers. I removed, cleaned, treated, repainted, replaced and gooped ends with tefgel. With renewed spreaders now re-attached to welded bases, I ran the new rigging wire and tied as tightly as I could to each spreader end with stainless seizing wire to hold the proper angle. However, after transporting and stepping the mast, I could see that the shrouds and spreaders had slipped to cause the angles to be grossly out of position. I saw your comment about setting the spreader angle while holding the shroud ends to the mast base, but would you please recommend the optimal method for holding shrouds tightly to the spreader ends where clamps aren’t provided by the manufacturer? The rig is down again this winter for more work, so I’d like to try again! (Photo is original corroded assembly). Thanks for all the great info here!
Hi Chris,
Yes, this is a bit of a challenge. That said, if you use a good flexible wire it’s possible to seize the stays on tight enough that they won’t move under normal use.
A few tricks:
It may take you a couple of attempts, but you should be able to get the wire tight enough that the spreader will be impossible to move using say the force from one arm.
Then, once the mast is up and dock tuned (but not full sailing tuned), you may need to go up in a bosun’s chair and adjust the dihedral with a few taps with a rubber mallet on the spreader immediately inboard of the end, while someone on the ground well away from the boat to have a good angle, calls it to you.
Just a thought, but if you discover compression at the internal mast step (and even at deck level) it’s a good idea to examine the external area directly below the step. Not only will you often find the ‘grinning’ keel gap, but with older boats with encapsulated keels fine scale longitudinal cracking from too much compression or movement up and down… Repairing one area usually means repairing others in the equation.
Hi Colin,
A very good point. I will add that in.
After never hearing of Duralac myself, I came across an article in Practical Sailor (Anti-seize Goops, PS July 2018), by odd coincidence shortly after reading this AAC post, that may explain why it is hard to source: “A barium chromate primer that functions like a gasket, Duralac physically prevents electrical contact, in doing so fights corrosion. This product is popular among some riggers, but it is restricted for sale in some areas since barium chromate is a suspected carcinogen.”
Hi Jamie,
Yes, I have heard that before. Bottom line, I think, is that we should be careful about using gloves with this stuff. But then again, half the stuff we use on boats is hazardous to our health, at least if we don’t take the proper precautions.
After reading Colin’s article on corrosion a few years ago, I acquired some Duralac. You can get it from Fisheries Supply in Seattle.
Well, now I realize I may have spoken too soon. Duralac comes, or used to come, in two types: green and yellow. Somehow I acquired the green, which was the “best” for some reason But it looks as if Fisheries sells the yellow. Colin may know of the difference.
Hi Terence,
I googled around a bit and it seems like Duralac Green is “cromate free” so maybe a new product developed in reaction to the concerns about the toxicity of the yellow. The only other thing I know is that Hall Spars always used the yellow, but that might have been because the green was not available then.
Hi John,
I wrote the following for the Great Lakes Cruising Club, but thought it might be an addition here, especially for those boats that are new.. or new to the owner.
Hi all,
I notice that there is a recent offering of a seminar for Great Lake boats sailing toward salt and I submit this to augment that course. This is a suggestion I wrote for a new boat owner launching in a salt water environment, but applies just as much for those Great Lake’s vessels going into salt water.
There are a few areas where a boat manufacturer could save the owner a world of work and likely problems and expense down the line, all to save a minimal amount (in comparison) of expense if done during the manufacturing process.* A big area is the installation of stainless steel fittings into and onto aluminum: most often seen on mast hardware, but also seen on toe rails, radar masts, wind generating vanes, solar fixtures and the like and where there is provided no protection for dis-similar metals being in contact.
When this is the case, within a very short period, splashes with salt water and living in a humid salty environment will cause the screw/bolt/fitting etc. to corrode and eventually make their removal very hard, perhaps impossible without damage. This annealing of dis-similar metals usually goes un-noticed until the piece of hardware needs removal or the mast needs painting. It will likely then demand much careful work and, likely, an impact hammer or worse to get the fasteners out with the chance of actually doing damage (stripped out hole).
The remedy for the new boat owner is to remove every piece of gear where there are dis-similar metals, cut a thin plastic pad to separate the gear from the surface, and to coat the threads of the fasteners with TefGel or Duralac or the like. This is (hopefully) easier than expected, and can be done a few pieces of gear at a time and will give the pleasure of knowing that you are taking good care of your boat.
These anti-seize compounds will allow the hardware to be easily removed in the future, even well into the future.
BTW, I believe this is a good idea for boats, even if staying in fresh water.
My best, Dick Stevenson, s/v Alchemy
· If owners asked whether these simple things were done upon manufacture, the manufacturers would get the message that we want boats where the future maintenance is considered.
Hi Dick,
Absolutely, I advocated for that in part one.
Hi Dick, John,
A note of caution from a non-engineer. For fittings that are loaded in sheer, my understanding is that a significant portion of the strength of attachment comes from friction between the tightly mating surfaces, not just the sheer strength of the fastenings themselves. If you reduce friction by putting a piece of plastic between the surfaces you may need to recalibrate the fastening size.
Wilson
Hi Wilson,
Agree completely and will be interested in an engineer’s response. My take, such as it is, is that this concern is critical in highly loaded items like chainplates. Correct torque is an important step in re-doing one’s chainplates for just that reason.
The fittings on the mast have seemed to me to more likely to depend on shear strength as they are far more lightly loaded generally, and the fitting is seated on a smooth surface that may not provide much “grip” (and often bedded with a non-adhesive bedding), and, my eyeball at least, the machine screws seem like they are quite robust enough to meet the challenge.
In any case, I have removed fittings added the thin plastic “pad”, TefGel’d the fasteners, and returned to service for decades without a problem. And when I remove the fitting, I am not pulling off a section of paint stuck to the fitting and cleaning the area of corrosion (a painted aluminum mast and boom).
Good thought, though, and stuff like that is always good to keep in mind and assess.
My best, Dick Stevenson, s/v Alchemy
Hi Wilson,
That’s a very good point, and one I had not thought of until a few years ago when I added some JSD chainplates and isolated from the hull with Delrin strips. How bad an idea this was was pointed out to me by a mutual friend of ours who is a professional engineer.
He also explained the point you just made. I then removed the Delrin and just isolated with polysulphide after which our mutual friend was happy, although he did also make me upsize the bolts.
Hi Wilson,
There are a few ways to design a joint but you are right that the preferred method in most cases is to have the friction generated by clamping the pieces together handle the load. This creates a nice, zero backlash joint where the bolts are not subject to fatigue if properly done. As you say, you need to watch out for putting a low friction element in there as it takes a lot more clamping load to make it work.
You can also make a joint where bolts are in shear. Done well, these will actually handle more load for a given bolt size but they tend to have issues with load sharing and wear. For people hand-drilling holes, you probably can’t hit the tolerances needed unless match drilling. Even then, you need to make sure that the things being attached are relatively stiff or there will be other issues with load sharing. Also, you want to be careful that the load direction is constant or you get wear which messes everything up. Shear connections certainly have their place and are found in a lot of big building structures but have their limitations. A lot of companies have policies specifically discouraging or even prohibiting them in bolted joint design. Then again, we all live with shear joints regularly such as with cotter pins in rigging but that is a good application as it is a single pin with a relatively constant direction load.
Eric
Hi Eric,
Thanks for the fill on that.
In this whole set of articles on rigs/spars/lines and the bits and bobs that make the sailing happen I see no mention of the service schedule or recommended sundries for winches. I found your suggestions for a water-based degreaser, but no suggestions for the grease (And there’s sooo many, and they all claim to be the best. Ugh). With 10 winches on the to-do list for spring, does anyone have a tried and true winch grease?
Hi Courtney,
I suppose one could save a few pennies and find grease that does the job for less, but I just go with Lewmar grease as they made my winches. A tube lasts quite a while and then Three in One light machine oil for the pawls.
I use lamp oil (paraffin) for cleaning: no smell, easy on the hands and inexpensive enough so I just use a lot to make the job go faster with some old tooth brushes.
My best, Dick Stevenson, s/v Alchemy
Hi Courtney,
Good point, I think I have mentioned winch service intervals, but never written anything specific.
I will whip up a tip.
Here you go:https://www.morganscloud.com/jhhtips/qa-winch-service-intervals-grease/