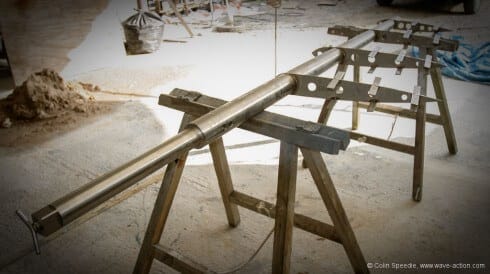
Some time ago I posted here with my views on the suitability of spade rudders for offshore cruising. Having lost a spade rudder that looked to be in A1 condition, naturally my thoughts at the time were coloured by that disaster. Despite the fact that I had up until that time owned three yachts that had spade rudders, had covered tens of thousands of miles aboard them, and but for a bad case of metal fatigue might never have had a concern about their use, my immediate reaction was to rule out having one on our next boat.
But I learned a lot at the time as we fabricated a new rudder from scratch; not least in terms of how difficult—and expensive—it can be to do it right. And since then I’ve put my habit of being an inveterate noser-around in boatyards to good use looking at examples of spade rudders both good and bad, to balance against the understandable antipathy caused by our loss. As a result of those examples and time for reflection I’ve altered my views in some regards—but not all.
Rudders Need Maintenance
One thing I have noticed is that very few owners include removal of a spade rudder within their maintenance schedule, which I think is fundamentally wrong, especially for any yacht intended to make extended voyages offshore. We removed our rudder every other year on our working boat, to examine and service it, usually as soon as we lifted the boat out, as it was impossible to do so with the boat in a cradle (otherwise we’d have had to dig a very deep hole), then replaced it at re-launch. Here’s why:
- It’s virtually impossible to stop water getting into a conventionally fabricated (stainless stock/GRP shell) spade rudder. Getting the water out isn’t easy either, and if left inside the shell over the winter may combine with other internal chemicals or pollutants in an anaerobic atmosphere and exacerbate internal corrosion. Our rudder was huge (and heavy!) and so took some handling, but we would turn it upside down, then tie it against a wall to allow the water to drain thoroughly over the winter. Another option I’ve seen employed is drilling and tapping the bottom of the shell to accept a nylon drain plug, capped with Sikaflex. This can then be removed in winter to allow the shell to drain.
- I’ve often seen owners ‘examine’ the state of the bearings and seals by just waggling the rudder around. However, it’s very difficult to ascertain the true amount of wear in the bearings in this way, especially with the steering system (rod or wire) attached. Detach everything from the quadrant and you may find a very different result.
- Most standard rudder bearings are made of a hard plastic material such as Ertalon or Polyacetal. These take a real pasting, and so will wear over time, and if the bearing wall is not thick enough can crack, especially if there is any corrosion present. Inspection is the only way to properly assess their condition and, if they’re OK, proper cleaning of them (they should be kept free from grease) will help prolong their life.
- Removal of the rudder also allows the bearing surfaces of the stock to be examined for corrosion. It will also allow for a thorough inspection of the shell from all angles, where any cracking or crazing can be assessed and appropriate remedial action taken.
- Whether your stock has a stuffing box or O-rings (both now fallen from favour) or simply employs a lip seal, sooner or later it will need servicing or replacing, especially if there is any play in the bearings. And it’s not uncommon to find that the lip seal installed is not suitable for marine use (with a mild steel spring) and so won’t last any time at all. As it’s virtually impossible to remove and replace these lip seals intact (they don’t cost much anyway) with the rudder in place, it makes sense to source the correct grade of seal in advance and replace it when you’ve got the rudder out (to achieve the best seal with lip seals a pair should be used). Or, if your rudder installation will allow it, consider fitting a specially designed gaiter. Worn or loose fitting lip seals or O-rings are a common source of leaks, especially in heavy weather, so it makes sense to replace them on a regular basis.
What’s The Best Form of Construction?
I prefer one piece/material construction, which offers the best chance of structural and watertight integrity. As Matt so eloquently explained, carbon construction is now becoming more cost effective and seems to me to be the way to go for the future with GRP boats and, equally, one piece aluminium or steel makes most sense for hulls in those materials.
In production boats stainless steel stocks are generally being replaced by aluminium, which, if properly designed and fabricated, and most importantly properly isolated against electrolysis, offers many advantages in terms of weight and cost. But I’ve seen plenty of cases of corrosion of these stocks, including internally, and believe that there’s even more reason to remove and inspect them regularly as a result.
I’ll bet that most of us have heard of at least one sail drive being eaten by electrolysis in recent years—I’ve seen quite a few—but no-one seems to consider that if the sail drive has been eaten, what’s happening to the rudder stock? Regular inspection of the exposed shaft at the hull/stock position should be a must—oh, and don’t antifoul the stock with a conventional copper based antifoulant…
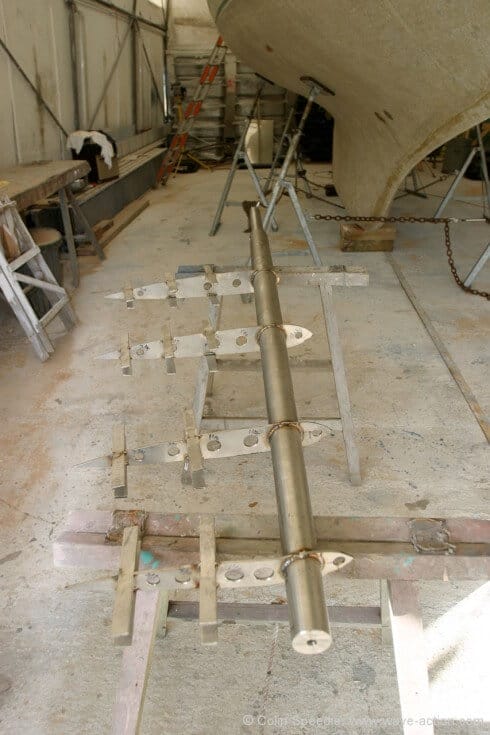
The machining and the tapering of the stock took a week, with the shaping of the profiles and welding several days more. Welding the external tangs didn’t only help to form the shape, but also would help support the shell.
Thanks to Seaweld at Mylor, all of this was carried out to the most exacting standards, and the resulting structure was far stronger than the original.

With the welded tangs in place the first side of the shell could be bonded more effectively to the structure by laying up mat over the tangs before the foam was applied.
With the second side of the shell attached, a solid layup to bond the two sides could be applied to make for a really strong shell—much more so than with a conventional production rudder.
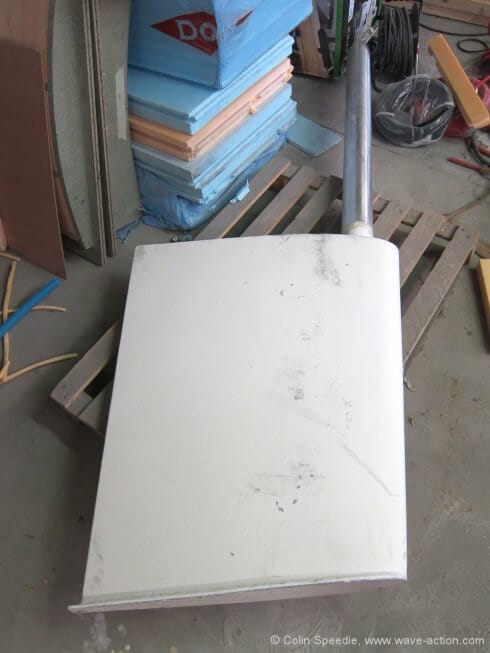
Massive stock and all welded one-piece construction on the Boreal 44. An end plate is used to improve hydro-dynamic efficiency and reduce tip losses, and also to protect the shell when drying out, as the boat is designed to do.
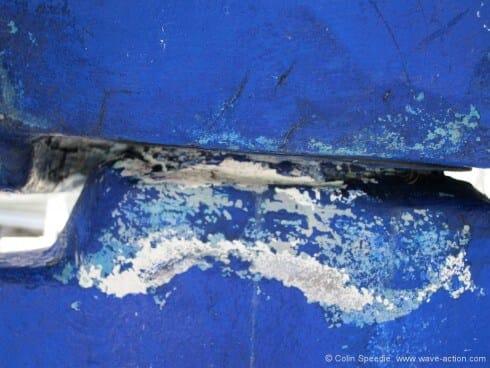
And in this case something was obviously suffering, as there were deep cracks visible on both sides. GRP stock, too, with visible repairs on the rudder shell, effected with epoxy filler, before setting off—for the Atlantic…
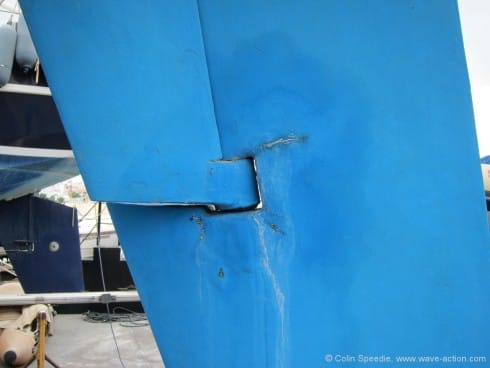
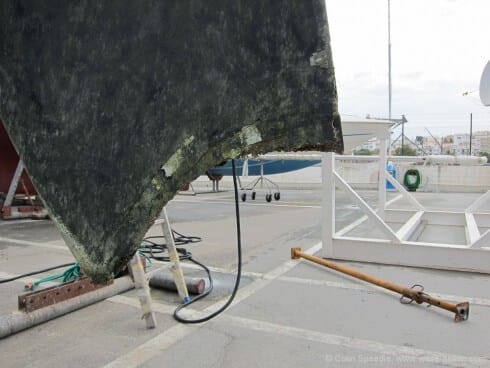
In this case, on a big Swan lifted out for inspection, the damage wasn’t recent and the skipper had no idea it had occurred.
It looked to me like the sort of thing that could happen when berthed stern to against a quay, where there is often rubble or debris on the bottom. But it had worked—and the boat had kept going.
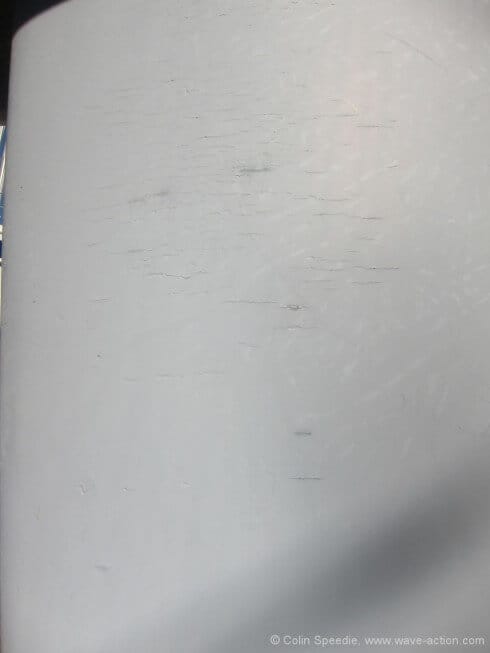
What’s alarming here is that the cracking caused through stress is so close to the top of the rudder where (in theory) the structure should be at its stiffest—so what’s happening inside?
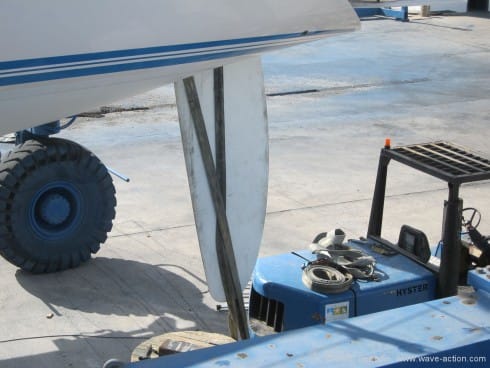
The rudder on this boat hadn’t been removed for some years and had seized in place, necessitating some inventive thinking to remove it.
These strops were attached to the forklift while the boat was lifted by the travel hoist, but they still failed to budge the rudder. The moral of this story? Remove and service regularly.
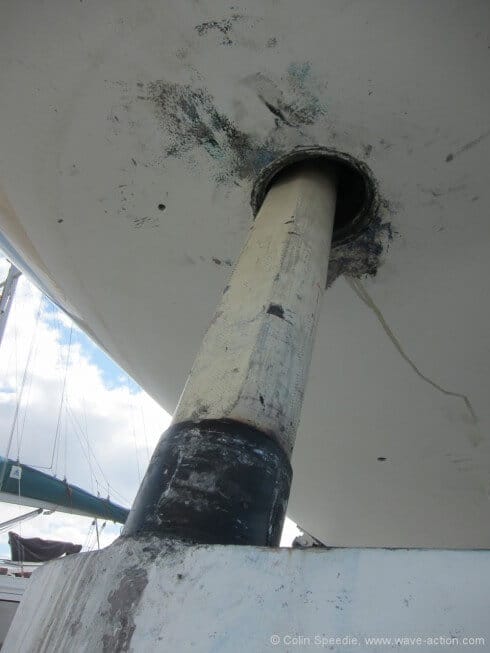
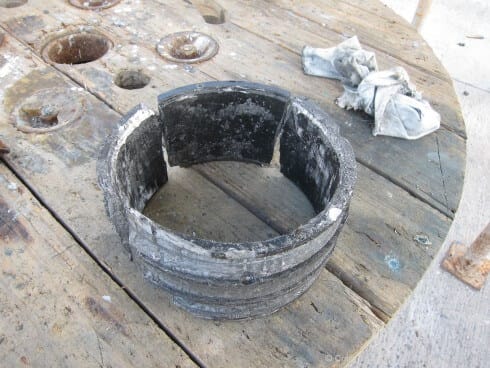
Replacement of the bearing proved difficult as the original manufacturer had long since gone out of business.
Fortunately, the excellent Jefa Rudder Systems was able to come up with a replacement.
And So…
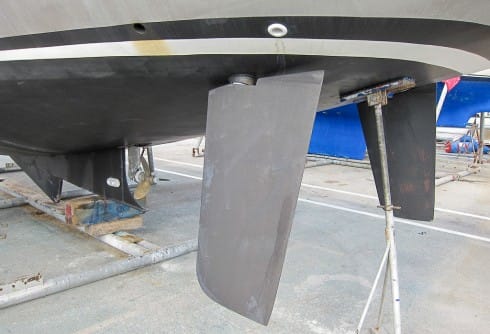
Whilst I still prefer the strength and security that a skeg offers, I accept that a properly designed and constructed spade rudder can be a viable choice, but it must have some form of protection ahead of it in the form of a keel or prop skeg to reduce the risk of collision damage. One of the reasons I am not a fan of twin rudders is that this is virtually impossible to achieve with this configuration.
But however a spade rudder is mounted, it is not a ‘fit and forget’ item, and needs to be checked and maintained religiously—however good the designer and builder.
Excellent article, Colin.
And I think you’ve just made my argument for a transom hung, tiller steered rudder design for the A-40 in ten easy pictures!
* Rudder built entirely from glass and foam, with no encased stainless steel to experience crevice corrosion or aluminum electrolysis.
* No thru-hull penetration to leak or cause corrosion at the interface.
* Low friction bearings mounted to transom above the water line. Easy to service and replace.
* Tiller attached directly to the top of the rudder. No quadrant, cables, gears, and wheel to buy and break.
* Autopilot ram attached directly to rudder on secondary tiller.
* Removable pie shaped cut-out in sugar scoop to enable rudder replacement and repair in the water.
* Option of cassette style kick up rudder sealed to bottom of sugar scoop by flexible “wings” attached to rudder and removable/replaceable.
Hi Richard,
I too like the idea of a transom hung rudder, for all the reasons you state. The only problem is that I just can’t come up with an elegant way for said rudder and a pendulum-servo self steering gear—the most powerful and easiest to use type—to coexist.
Hi John
The vane gear can usually be mounted outboard of the rudder, and if the rudder is mounted in a cut-out as Richard suggests shouldn’t be too far outboard or inelegant. Make the mountings simple and/or quick release a la Windpilot, and it’s not going to be too vulnerable in harbour either.
Best wishes
Colin
Hi Colin,
That makes sense, although I think the gear would be a more vulnerable to harbour damage, ditto the outboard hung rudder. But then having spent years in industrial and fishing harbours where the other users are not too worried about a “bit of a bump”, I’m probably being paranoid.
Hi John
I’m afraid I didn’t explain my thoughts very well. What I’m suggesting is that the Windpilot can be very quickly removed from the transom (with a little bit of forward planning), so that it is safe from damage in harbour. Ours takes 10 minutes max to remove or re-install, and we now do so whenever were at rest in a position where the gear is vulnerable (and against theft in boatyards!).
Best wishes
Colin
Hi Colin,
Good point. We do the same thing with our Sailormat, although it is not as easy to remove as yours, more like an hour by the time we get it all stowed away.
Another thought: The mounting bracket for the gear could, perhaps, act as a guard for an outboard hung rudder.
Colin, our Voyager windvane is mounted outboard of the transom-hung rudder in this fashion:
http://i169.photobucket.com/albums/u212/rhysdarkstar/102_0610.jpg
or see http://alchemy2009.blogspot.ca/2008/05/vaneous-transfusion.html
It can be removed easily in 20 minutes or so. Those mounts are quite substantial. The man in the photos is Peter Tietz, who fabricated the vane.
Hi John, as an alternative have you considered a trim tab type self steering system? This would work well with an outboard rudder, using a hollow rudder stock for the trim tab’s shaft. Whilst this system is not as powerful as a pendulum servo, given the AA40 is going to have a reasonably well balance hull shape, this lesser power should not be a problem
Hi Alan,
Yes, I did give some thought to a trim tab system, but in the end decided against it, for just the reason you mention: lower steering power. Keep in mind that I conceived the Adventure 40 as a buy-and-go boat for those new to offshore voyaging and I’m pretty sure I’m right in saying that it is way easier to get a good quality pendulum-servo gear to steer a boat well than a trim tab gear.
While I concede your very well argued points, Colin, I tend to agree with RDE in this case. Yes, a transom-hung, skeg-mounted rudder is problematic in terms of performance and drag, but we *are* speaking of cruisers, right? Five point five versus six knots SOG seems trivial when you consider “one less hole below the waterline” and the ability to repair or even replace a transom-hung rudder without a haulout.
I own a spade-rudder boat, but offshore, I would worry less with a transom-hung rudder with a sturdy tiller head should the ram pack it in OR should I wish to bypass the wheel steering in favour of a vane.
Even if my current diet succeeds in every respect, I will never enjoy nor fit particularly well in the space where most quadrants dwell. I much prefer the open air!
Hi Marc
Actually, I’m very much in the same camp as yourself and Richard.
Up to about forty feet, so do I, and there clearly benefits in terms of cost and simplicity. As long as the rudder is properly balanced, personally I’d prefer tiller steering up that size in any case, as I seldom take the wheel and leave the Windpilot to do the hard work. More room in the cockpit, simpler to hook up an autopilot or self-steering gear, too.
But above that size it’s less of an option, in my view, and then it’s a question of whether the designer and builder did their job right, and whether they used the best materials to ensure structural integrity and reliability.
Best wishes
Colin
I concur to a somewhat scary degree. Originally, for reasons of speed and stowage, I wanted a 45 footer in steel for offshore work. But the mechanical forces involved exceeded what I could reasonably expect my fit but height-challenged wife to handle in any kind of blow. And although I’m nearly a foot taller and stronger, the tiller on the 40-footer is seven feet long and is indeed a handful if I’m hand-steering in 25 knots (a “worst-case” scenario in which the AP, the vane and the hydraulics have failed).
So I agree that the desirable simplicity and sturdiness of the transom-hung rudder and (optional/emergency/windvane-driven) tiller does produce countering arguments at the 40 foot level. It’s easier to pack smarter than it is to buy a boat you can’t operate because it’s beyond one’s physical abilities. That’s why I look a little askance at the 70-year-old retirees heading south in high-sided, flattish bottomed Catalina 47s and even bigger Beneteaus: in my view, the desire to replicate shore accomodations is trumping the ability to safely operate the boat should most of the mechanical aids fail…and you’ve failed to discover whether your deluxe fast cruiser can safely heave to! Clearly, there are older sailors who can cope with this, but those veterans tend to stop at a Pacific Seacraft 37 or so, with the exception of course of John and Phyllis, who know what they’ve gotten into!
Because we rarely have to hand-steer doesn’t mean we should forget that it’s a job for the larger sort of Viking, and can be a challenge and even a danger under truly adverse conditions.
Hi Marc
I’d agree – I reckon 40ft is the limit, given the limitations of crew strength and endurance for the average couple.
On our old ‘working’ boat we had a big wheel, way oversized winches and everything scaled up. The reason being that we had very mixed crews of all ages and strength capabilities and we wanted to ensure that all could join in and sail the boat – one of the reasons she was (and is) such a well loved boat.
It’s a vastly overlooked area – production boats tend to be scaled down, winch and gear wise, which rules out smaller/older/lighter weight crew members from getting the most out of our favourite pastime, and as you rightly point out, it can be a recipe for disaster.
Best wishes
Colin
Colin, A very nice article. A mini-course and excellent informative pictures. It is ever educative when walking around boatyards to speculate on what little anomalies one notices mean.
One design feature my old boat (LeComte Northeast 38, a later version) had was a huge spade rudder. It handled impeccably, light touch when sailing, turned on a dime and backed up accurately. The rudders top edge went along the arc of the hull staying fractions of an inch away. Wonderful for holding onto the water flow, I imagine, but offshore, I could not escape the nagging anxiety of wondering how much force it would take, hitting the bottom of the rudder, to drive the trailing edge of the rudder the short distance needed to jam the rudder into the hull rendering it useless. I have not heard of the happening, but there is a lot of debris out there and it did not seem unlikely to have a log or something slide along the keel and smack the rudder. It would take very little angular movement in the rudder to jam that trailing edge upwards. After many offshore passages, we notice dings or missing paint on the leading edge from debris we have hit, some we have heard, most we have not had a clue about. We are happier with our skeg hung rudder.
Thanks, Dick
Hi Dick
glad you liked the article.
Spade rudders give excellent feel and control. So much so that I’ve often observed that boats thus equipped back up better than they go ahead – as long as you hold on to the tiller or wheel good and tight!
But they can be vulnerable, and there can be little doubt that a skeg gives added protection to a rudder. But equally it seems to me that most problems with spade rudders tend to be caused by structural failure of some kind than impact damage.
I’ve looked at some really hefty spade rudders recently, and as long as they have been designed internally as well as they appear to have been externally believe that they should cope all but really severe impacts. With a keel or prop skeg ahead of them it should be the case that they will get some protection from them, in any case.
Best wishes
Colin
A couple of details:
* In my design suggestion the rudder form is a balanced spade.
* There is no skeg. The bearing points are far enough apart already.
* It is protected aft by a substantial sugar scoop/swim step.
* This platform provides an ideal base for a wind vane.
* If desired a cassette style fused breakaway rudder is easy to accomplish. In this case you will use one of the wind vanes that allow offset mounting.
* The A-40 concept is budget driven. The price of a wheel (or two) a heavily built skeg and an onboard rudder will pay for the cost of a lot of gear—.
re size limitations: Note that almost all Open 60’s are tiller steered. And this is with huge sail area and power several magnitudes greater than any cruising boat.
Colin & John,
Yes, rather the wind vane steering bracket take a shot rather than a stern hung rudder. It is easy to carry spare support tubes. My Monitor has taken good blows from 2 poorly handled boats and one stone wharf when my bow anchor was lifted by a neighbor. Substantial dings and indents, but cosmetic only so I was lucky, but if the vane was not there, my stern would have taken a beating.
On another note, I have seen some transom hung rudders that, when hard over at dock, lay right against the hull, tiller pointing straight up with a fender placed over it, about as protected as could be. I suspect that would need designing in from the onset.
Dick Stevenson, s/v Alchemy
hi Dick,
In order to do have it fold all the way you either need to eliminate the swim step and end plate sealing or use a rudder shaft in which case you are back to the problem of stainless steel rotting away inside fiberglass.
I like the idea of gudgeons and pittles built from glass or carbon, fabricated as part of the rudder that pivots around a nice SS shaft above the water on the transom. Cheap and bulletproof.
Henri Amel correctly determined that there was no way you could ever keep a rudder dry long term so he created a “wet rudder” where water simply flows through and there’s a zinc to protect it. Thus you rarely hear an Amel owner crying the blues about a rudder. In fact I’ve never heard of an Amel suffering a complete loss of steering ability.
I am comfortable with a spade rudder if the engineering is solid. A balanced rudder would be a plus. Love the idea of a tiller.
Hi Dave
Good old Henri Amel – a real lateral thinker. His boats abounded with simple, practical ways around complex problems that other builders simply chose to ignore – to owners detriment. I wonder what he makes of the latest generation of boats to bear the Amel name?
Best wishes
Colin
Colin,
There’s some major differences with the 55 and 64 compared to the Amel/Carteau designs. Hard to say what Henri would think but the order book is full. The new boats sail better because they abandoned the integral water tank in the keel stub, which makes that section narrower. Obviously there were many other changes as well. I have not seen one in person but there will be one at the Annapolis show. They are still center cockpit ketches at least. The complexity is a bit much for me. I like my old school Maramu but she is getting long in the tooth.
Colin,
Great article as usual.
What are your thoughts on self aligning aluminium ball bearings for spade rudders?
Hi Nicolas
I have no personal experience of aluminium ball bearings in such a system, but I can’t see any reason why they would have any advantage over some of the well-proven plastic materials such as Delrin (polyacetal) which have now been in use for some time.
Buit I’m convinced that roller bearings are the way to go with spade rudders, especially for high performance boats where the loadings are very high.
Best wishes
Colin
Laminated rudderstocks generally must be wider than metal stocks in order to resist the transverse loads imposed on them. This means the rudder blade must also be wider, which tends to degrade the rudder’s hydrodynamic form. One way around this is to flatten the sides of the stock into a trapezoid shape. This not only creates a narrower cross-section, but also presents a much larger surface area for bonding the stock to the skin of the rudder blade. Note, however, that a trapezoid stock needs bearing rounds installed where the stock passes through its rudder bearings in order for the rudder to turn properly.
Hi Marcella
Thanks for the useful explanation. Yet another good reason for going for a composite rudder in my view.
An example of the bearing surface on a composite rudder can be seen in the penultimate slide of the slide show, and it’s probably worth mentioning that these bearings need just as much attention as the bearing surfaces of the stock on a conventional construction spade rudder. Fortunately in the instance in the slide show, the bearing surface was undamaged, despite the corrosion that had seized the outer bearing cage, probably because the rollers themselves were Delrin.
Best wishes
Colin
Hi Colin,
Did you consider a hollow shaft for your rudder construction?
When you use a thickwalled pipe as shaft, you can reduce the shafts weight by as much as 35% while only 2% of torsional or bending strength is removed from the shaft. When you increase the diameter by just an inch or so, you can reduce more than 60% of the weight of the stock.
I designed quite a few rudder over the years, including icebreaker rudders, and I’m really fond of playing with diameters and wall thickness if I get the freedom to do so.
For sea keeping capabilities of a boat, I consider it important to reduce weight in the ends of sailing vessels. The rudder is usually one of the heaviest pieces of equipment on the stern of a vessel, but also very often overlooked to achieve weight saving, which can be done without loosing strength or reliability of the rudder.
Best Regards,
Erik
Hi Erik
We were determined to follow the original Frers design plan to the letter, something that the original builders hadn’t done. They had sleeved 3″ OD round bar into 4” OD thick wall tubing just inside the upper section of the shell (where we couldn’t inspect it), and it was at this welded ‘hard spot’ that the shaft failed. So we wanted no welds in the shaft, and allow the taper to keep the rudder narrow and efficient.
We also found that the builders had ignored the plan in more ways than one, What was left of the stock had no profile (where one should have existed), instead 1” round bar had been welded to the shaft and a mess of chopped strand mat had been slapped around it. If this had been replicated all the way down the shaft the weight gain would have been considerable over the light, strong profiles.
In the end we felt that there was little or no difference in the weight of the two rudders, although I’d concede that the new one could have been lighter, although that would have required considerable investment in other ways.
Best wishes
Colin
Hi Colin,
Thanks for your quick response.
A sleeved construction is indeed far from acceptable on an offshore boat. All torsional loads are transferred via welds, and you can wait for the moment that these will give way.
Not being able to taper the stock is indeed a disadvantage of a thick walled tube construction. The only thing you could do, is reduce wall thickness on a lathe.
Following the design of a smart and well known designer is usually not a bad thing to do, good choice.
Thanks,
Erik