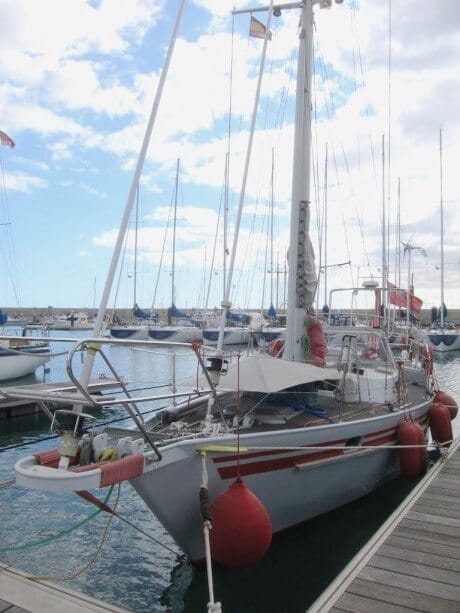
For a long time I dreamed of a steel yacht as the ideal ocean cruiser, so much so that I came very close to having one built and looked at many boats on the second-hand market. It was a dispiriting experience in many ways, as amongst the builders there seemed to be complete disagreement on how to keep the paint on and rust at bay, the Achilles heel of steel boats. This was in turn borne out by inspecting many used boats, where the theories proposed by the different builders all seemed to fall down. Every one of them had a rust problem.
Then a revelation
In 2003, my crew and I were sitting in the tiny harbour at Portrush in Northern Ireland, when a yacht appeared in the entrance and made its way to join us on the two-boat pontoon. We helped them alongside, and I found myself looking with increasing interest at this new arrival. Obviously steel, and beautifully built with a host of custom features, she was a beauty, and not a rust streak in sight.
I have sailed on steel boats in a professional capacity. Whilst sturdy, etc… they DO require a lot of maintenance. When you find that you have some time on your hands, there’s always some rust to chip away at.
Like teak decks, a good idea in principal, but not really ideal for the average couple out cruising.
That’s why we opted for a GRP boat. My only regret with that choice is that it will limit our high latitude cruising. However, my wife does not share this regret as she much prefers cruising in warmer climes.
Hi Wim
Well, it’s the same with aluminium – they definitely require more input from the owner.
What’s intriguing about this boat is that she isn’t new – any boat can look good when new – but that she wears the miles so well. And I’m sure that we’ll all learn a lot about how you can make that possible in this series.
Best wishes
Colin
Horses for courses, I suppose.
Whilst sailing on that steel ketch, we had an ample supply of officer cadets to chip away at the rust and to paint.
However, the maintenance would IMHO require quite a lot of self-dicipline from an averag cruising couple.
A love of sailing and cruising does not necesarily equate to an equal love of maintenance.
I bought a used steel boat a few years ago. If you want a used, relatively small, metal boat, the choices available in aluminum – especially in North America – are very limited. (huge understatement). The choices for steel are somewhat better, but – of course – very small relative to what’s available in plastic. It took me a year of searching before I found the boat I wanted.
The maintenance is a bit more but I personally find it easier and more pleasant to do than what is required for a glass boat. Rust shouldn’t be a big deal – you see it, you grind out the rust spots, you put Ospho or an alternative on, and then you paint. Pretty simple – usually – in practice.
Where rust isn’t the problem but the topsides or deck need a touch-up repainting, it couldn’t be easier. I’ve found it to be less time-consuming and less physical than waxing the topsides. Of course, untreated topsides on an aluminum hull would be even better – but barring something like a win at Lotto (unlikely, since I don’t play) it’s unlikely I’ll buy an aluminum boat. To buy ANY boat which is NEW – even a “Model T” – is beyond my financial means. But, no matter, my current boat works for me.
Hi Jerry
It’s the same in the UK – were it not for French builders there would be no aluminium boats at all.
I take your points about keeping on top of the paint – I’ve had the brush out today – and would prefer an unpainted aluminium boat, but steel can look good like Caitlin, and that’s good too.
Steel has many things going for it – and if it works for you, then you’re by no means alone.
Best wishes
Colin
All steel boats are not created equal as the little sweetheart Caitlin proves! In the Pacific Northwest, a company named Amazon built a series of 38 & 44′ sailboats about 20 years ago in Vancouver BC, many of which still look like new. Over on Vancouver Island, Waterline Yachts builds superb boats, properly coated and insulated. Both are round bilge designs indistinguishable from glass. If you are from North America and looking for a steel boat I’d give careful consideration to one of these.
At the Seattle boat show two years ago there was a Waterline 48 about 5 years old sitting alongside the newly announced Oyster 54. If I were given the choice of one or the other til death do us part, I’d choose the 5 year old Waterline, even though the Oyster is twice as expensive. And that is no knock on the Oyster, especially now that they have corrected the little niggling annoyances that I hated on the earlier 53′ design.
Charlie and John
Treadmaster is great stuff – until you come to replace it. It has to be one of the worst jobs in the world. But it’s super grippy material, and has to be one of the safest non-slip materials there is. The only other drawback I recall from IOR racing days (it was a popular deck finish) was the dreaded ‘gunwale bum’ from sitting on it for hours on end as human ballast on the sidedeck – but that’s another story….
We have recently changed our antifouling from Trilux 33 to Seajet Emperor 034. We haven’t launched yet, so nothing to report so far, but once we’ve had a chance to evaluate it we’ll do so.
Best wishes
Colin
I will follow this series with interest. I have looked at steel boats on and off for years but could never get my head around the rust issues and related maintenance headache as well. Aluminum is also intriguing and I would prefer a metal boat for high latitude cruising. However, like Wim, my wife has ruled that out!
This has led us to focus on finding another glass boat and we just purchased her. We spent two years searching for the right one, which is about average for us. Coincidentally, our new (to us) boat is an Oyster 53….! As we are just figuring her out – and without getting too far off topic – I would be very interested to hear of the “hated annoyances” in the design that Richard mentioned.
Cheers.
Derek
O no, the dreaded foot in mouth disease!
Fortunately the little annoyances on the 53 are relatively easy to fix. The boat itself is a tank.
1- Start with a major hand hold upgrade throughout the boat. You should be able to move anywhere in the interior with one hand on a secure hand hold. Can your wife, or even you reach the one on the saloon ceiling? Are the companionway handholds properly placed? Getting thrown out of the galley and landing on the chart table is not pleasant. You’ll thank me when you cross the Gulf Stream….
2- Take out every little custom Oyster cabinet hook and throw it overboard. That way when you use the forward head while crossing the Gulf Stream you won’t have a bloody hole in your thigh where the protruding hook embeds itself.
I could go on, but you are already half there…..
Richard,
Great stuff! Many thanks for the insight and I will work on those improvements. The wife is “vertically challenged” so no way can she reach any of the ceiling handholds.
We are also in the PNW (Seattle).
Cheers.
Derek
Hi Derek,
I’m near Jackson Wyoming, but plan to be in the Seattle area sometime in the next 30 days. If you feel it would be useful I could conduct an offshore preparedness survey, describe my Oyster 53 recommendations. do a few napkin sketches etc.
Fair winds,
Richard
I was long attracted to the idea of a steel boat and did a lot of research on the subject. With modern paint systems, if a steel boat is properly prepped and painted when built, rust should be much less of a problem than it was in the past. In the end, however, what really dissuaded me from steel was its weight. I concluded that any boat smaller than 50 or 60 feet will be heavier than it should be if built from steel.
This doesn’t matter too much if you don’t mind a slow boat, but I like a boat that sails well.
In the end—after a long, long search—I found a used aluminum boat I could afford and have been very pleased with it.
Getting back to the notion of a Model T offshore boat—I really think it should be built of unfinished aluminum, hard chine, with the simple systems described.
Hi Charlie
I’d generally agree with the weight point, but I’d suggest that many steel boats turn out way over weight (from what the designer intended) due to the philosophy of steel (bombproof) construction being extended to every area, including the interior. No boat of whatever construction can expected to make your pulse race a little in a good breeze that way.
Bryan and Dorothy factored this in from the outset, and took steps to ensure that the fit-out wasn’t overkill, bearing in mind, for example, that bulkheads etc are simply joinery on a steel boat, and so don’t need to be 2″thick!
As a result, this boat (at least) is no slouch. She weighs around 131/2 tons loaded, including 2 tons of fuel, water and anchor gear. As she has a longer LWL and a taller rig, the numbers are far better, and despite their philosophy of sailing conservatively she regularly knocks off 130-150 mile days with ease.
Best wishes
Colin
Hi Charlie,
Welcome here.
On your model T thoughts. I hear you and no one is a bigger fan of aluminum than I am. But for the Adventure 40 (Model-T) I worry that a boat built that way would be a stretch too far for the market we are aiming at. Also, my guess is (and it is only that), that once one gets past a build run of between 5 and 10 boats (Richard guesses 3), we would be able to deliver better value using a highly automated and quality controlled composite molding process.
Excellent points, Colin. A carefully built smaller steel boat can be relatively light; witness Tom Colvin’s original Gazelle (with no engine even), which as designed had a D/L ratio of around 220. Go into the brokerage market looking to buy such a boat, however, and you’ll find zero to few to choose from, I wager. Building one from scratch is another story.
I totally agree, Charlie. And that’s why I’m enjoying writing up this series.
Many people (e.g. yourself, myself, John) like aluminium boats – except perhaps the paintwork.
I’d like to like steel, too, but as you point out finding a good one isn’t easy. But in these times where new build heavy duty production cruisers for go anywhere cruising are also rare, then metal boats may become more the norm, as potential owners look more for boats that are ‘fit for purpose’.
And I hope that anyone out there thinking of building in steel will find inspiration from this boat – proof that steel can be a really good choice.
Kind regards
Colin
Right now I am working towards building a 36′ steel origami sailboat.
I think this is the model T of steel sailboats.
My first plan was to build a Gazelle until I came across a couple of origami web pages.
Having worked with steel all my life, I think building one of these hulls would not be to hard.
James
Hi James
That’s one of the beauties of steel – if you are used to working with it, and have the skills it’s a good home build material, and frameless fairing seems like a good way to go – Van de Stadt use something similar.
Hope you find the next two parts of this series provide some inspiration for your project.
Best wishes
Colin
Hi – just wondering if you can point me to the next two parts of the series ? I can’t find them when i search.
Thx Colin
Pete
Hi Pete,
This is part of one of our online books so there are links top and bottom that move your through the chapters.
More here: https://www.morganscloud.com/about-online-books-2/
Charlie,
My sentiments exactly.
Colin,
Meta, who produced Moisttessier’s Joshua and now my Rajah Laut, suggests both for steel and aluminium, to coat the freshly cleaned metal with zinc silicate. They have their own brand called Inversalu and a slightly different name for the steel version but it is essentially the same.
Zinc silicate is used on large tankers, bridges and even for anchors and chains as a replacement and improvement upon galvanization.
After two or three coats of the zinc silicate an epoxy paint can be put on top or leave raw as Charlie suggests. It is naturally a grey color and not too dissimilar to what aluminium looks like with a patina.
My two cents……
Hi Victor
Interesting point – we recently looked at Inversalu as an option, but were not quite ready for all the work stripping the hull etc where we are currently. But I’ve heard good things from French owners about it, the only reservation being the antifouling ability which doesn’t seem special.
I knew a guy who had two identical small trawlers built, one which was treated with a hot zinc coating, the other with a conventional paint system. After four years the difference even from a distance was amazing – the zinc treated boat still looked pretty new, the other looked like – an old trawler. Not by any means a scientific assessment, but it impressed me!
Best wishes
Colin
Colin,
Yes, you are right Inversalu is the right product but only from the get go. I will probably apply two coats on top of what is there now since I have had the epoxy sand blasted off and there is a good bite to the surface.
I have just tried Jotun Sea ALU for the bottom paint. It may be a Caribbean only product since I have not seen it elsewhere. It was the only product I could find around here with absolutely no cuperous oxide. I will let you all know how it holds up.
Charlie and John,
Steve Dashew doesn’t seem to have any problem selling his raw aluminium boats. They are hardly the Model T variety either.
Colin & Victor,
Painting or coating aluminum except for anti fouling is missing one of the really huge advantages of aluminum boats as Charlie suggests. Oxidized aluminum may not be the prettiest, but it is durable and self sealing when the proper alloys are used.
I’ve also found while looking at metal used metal boats in the US that you pretty much have to consider steel. I like the idea of an uncoated alu Model T, but wonder how cost would factor in in relation to a Model T for cruising.
Dave
Hi Dave
If I’m not mistaken the principle of the Inversalu process is that is not just a protective coating, but also performs the function of an anode and is also an antifoulant – as I’ve said, I have no personal experience of it, but have only heard good things from owners, although they have generally added that the antifouling properties are not necessarily the best.
But I’d agree wholeheartedly re painting – if I had my time again I’d avoid putting paint on aluminium at all, apart from maybe a few cosmetic areas.
And I missed out on my comment re the two trawlers – these were both steel, not alloy, and the hot zinc treatment certainly seemed to have worked there.
Now it’s back to touching up paint!
Colin
Hey Colin,
Nicole’s Esquilo was also initially treated with hot zinc when she was built (late 60’s) and she looked like a marvel for years. Before going to Patagonia in 2000 Nicole had the boat repainted and to my knowledge she never treated the hull again with zinc…
So never steel I would say I share your opinion…
I would be very curious about the feedback on Inversalu…
(Who am I) but I can not see/understand the advantages of it as antifouling…
JF
An excellent article to follow on from the “T” debate. I love to follow other peoples perspectives. Boats are a compromise full stop. My wife and I have been building our own 47 foot aluminium yacht for 6 years now from scratch to a Van de Stadt design called a Samoa. I have worked metal all my career so it is straight forward. Corrosion is about joint design and painting is chemistry. Both of these points are often missed in a boat yard where the bottom line is to stay in business. Some folks want a bare aluminium hull others myself included prefer the painted look so what? What is important is to enjoy the process and end result. What was evident from the great “T” debate was a lot of people criticizing from their armchair rather than from inside the bilge with dirty hands like John and Colin. There are very few sites like this where real world experience can be exchanged and shared. Lets keep supporting it to do that.
Hi Andy
How right you are – boats are a compromise, no matter how we imagine it when we start out. And it’s true that many faults are down to the yard when they are simply trying to turn out a boat in the shortest possible time. I’m sure we’ve all seen home built boats that are (at least) the equal of the best yards, where the owner/builder has the time, dedication and skills to do things to the letter. Personally, I’d prefer not to paint, but if you can make it work, then I’m sure we’d all like to hear about it. As with Caitlin of Argyll, I’m only too pleased to have my personal prejudices proved wrong!
The Samoa is a great boat (look at the record of Beth and Evans’ Hawk), and even in steel a powerful, fast boat, let alone in aluminium. Nearly ten years ago I was trying to fund raise for a new research yacht and the Tonga was our base design choice, and she had pretty much everything we wanted. So do keep posting here on your progress – I’m sure we’d all love to hear about it.
And thanks for the kind words re the site – we’ll keep trying to come up with interesting views to be knocked about by our great readership. And I still think the Model T will fly…..
Best wishes
Colin
My opinion re painting aluminum: don’t unless you have to. Which means painting the bottom, of course, and the deck, where you want some non-skid and a light color to reflect sunlight and keep the boat a little cooler. Everything else is best left unpainted. The topsides on my boat are unfinished, except for a protective coating of a useful substance called Nyalic, developed for spacecraft, that keeps things from getting too grotty.
The big challenge is anti-fouling paint. Still haven’t worked out what’s best there.
Hi Charlie,
Having lived with a painted aluminum boat for 20 years, I could not agree more about not painting. In fact if I was doing an aluminum boat from scratch, she would not even have any paint on deck. Instead I would use Treadmaster, as we have on “Morgan’s Cloud”.
On painting the bottom, we are using E-Paint, which is working well for us.
Hi John: Re Treadmaster, I was strongly advised not to try gluing it to aluminum when I redid my deck. As much as I love the stuff (I had it on an earlier boat), I decided to take the advice. The consequences of a botched job seemed too high.
Re bottom paint: I tried E-Paint, but didn’t like it. Tried Vivid Free, which was so-so. Now I’m trying something with Econea, or whatever it’s called. I’m also trying out an Ultrasonic Antifouling system, to help the paint.
Hi Charlie,
I think you can get Treadmaster to stick well to aluminum, but it takes some diligence.
On E-paint, we had mixed results too until we got the mix of products and the application right as detailed in the link in my first comment. Now we are pretty happy, although the stuff must have gold powder in it!
I will look forward to hearing the results of your paint test on your blog—always looking for a better way.
John, Colin, & Charlie
I’d love to hear and learn more about suitable bottom paint for an alu boat. One of my main job responsibilities is the care of a 28′ aluminum research vessel. It is moored in fresh water, but slime and light weed growth can be a problem. The boat has Imron topsides and Trilux 33 on the bottom. Topside paint is not my choice but something I inherited with the boat, kind of mirroring Colin’s comments.
I’ve really been enjoying all the discussions on the blog. It’s the first one I usually check.
Dave
Hi David
I have formed some views on the use of suitable antifoulants for aluminium over the last few years, and I hope to be able to report on how the Seajet Emperor performs before I share them. Fresh water and aluminium boats is a whole new area in itself, so when I do put up my thoughts, I very much hope you’ll be able to bring your experiences to the table – we’ve all got a story to tell here.
Best wishes
Colin
I bought my plate pre-shotblasted and primed with carbo weld, a similar product to the french zinc primers. She has never been sand blasted. I painted her , a 31 ft origami steel twin keeler, with 30 gallons of epoxy tar, inside and out, then a alkyd topcoat. She is 27 years old now , but her maintenance is still an hour or two a year. I found that chipped paint off outside corners is most of your maintenance, trim them with stainless and you reduce your maintenance by 80%
Avoiding any wood on steel outside , is very important, wood on steel is like wet blotting paper on steel, regardless of how well you bed it down.
Any time any steel boat has a serious maintenance problem, you are definitely doing something wrong.
I’ve built three dozen steel origami boats for others, a couple hundred of my designs have been built by others around the world. They are some of the most well proven, and most affordable small steel boats out there.
Any boat lived aboard full time is going to be heavy. I saw one 36 footer emptied out , come up 6 inches in the water, at 1150 lbs per inch.
Hi Brent
Thanks for the interesting – I hope you’ll stick around for the next two instalments, when I’ll be covering other aspects of Caitlin, many of which may well chime with your own experiences.
And, yes, no boat can be expected to perform if overloaded, whatever she’s built of. Lou and I have a constant battle to keep from overloading our own Ovni.
Best wishes
Colin
We have used POR 15 on our steel and aluminum tanks with great success. Can’t imagine it wouldn’t work on the exterior of a yacht. They used to make coatings that had no UV protection but now they do in various colors. The local welder who made our tanks swears by it.
Hi Mike
I just looked up POR 15 on the web, and it looks like a really good option. There’s no doubt that in recent years some really exciting developments have occurred in the protection of steel (and other metals) , many of them from the field of oil and gas production.
Thanks for the heads-up on this.
Colin
I’ve been quite happy using POR 15 for maintenance painting on the three steel sailboats I’ve owned. Sandblasting followed by epoxy paint is better (or at least very well-proven), but if you can’t sandblast (typical when painting scratches or alterations), then POR 15 seems to be the next-best thing.
As POR 15 is unlike any other coating I’ve used, it is absolutely necessary to read all the instructions.
The only downsides I see are that it is pricy (especially in the small cans that you want for maintenance work—you want to avoid much re-opening of a can of POR 15 to avoid getting moisture in it), and difficult to find outside of the US (though I notice they now have a few non-US dealers listed on their website).
We bought a second hand (actually a fourth hand) but very well maintained 30 yr old steel boat 4 years ago. Having also prepped her myself for our Atlantic circumnavigation, I now have some idea of the pros and cons of a steel boat. Sturdy, very safe feeling, very comfortable smooth movements. These are definite pros when living aboard and going long distance. Also, steel doesn’t necessarily mean slow. On our crossing from the Cape Verdes to Martinique we took approx. 12 hrs longer than a 53 ft Beneteau, leaving at the same time and with just a slightly different route.
Is maintenance and painting a problem? Yes. But not on the outside. With good preparation and current paint systems there is relatively little rust, it is easy to see when it appears and easily touched up. The biggest problem I ran into is inside. Keeping control of the rust is possible. However, to get to the rust usually means having to move a hose, a few cables, or one or other piece of equipment. And this is when maintenance becomes time (and energy-) consuming. And if you ever have to take apart some fixed structure to get to the rust, that is the moment when the real costs kick in. Welding in itself is fairly cheap. It is the preparatory work to allow for the welding that create the costs in a steel boat. This is a very important point to keep in mind when building or buying a steel boat IMHO.
I am still convinced that a well thought out steel construction can be an economically interesting option. But more than with other materials you need to keep things simple, especially inside.
Hi Philippe
Looks like a well thought out and very capable boat. I’ve seen a few Joe Adams designs, but not in steel, and they look good.
It’s a fact that most problems with steel occur from the inside, often in hard to get-to spots in the bilges and in and around the engine. It seems critical that whoever builds or conceives the boat has to take this into account, in order to allow (at the very least) regular inspection of all areas that might be likely spots for water to gather and rust to gain hold.
The same is true of being able to dismantle interior joinery in order to repair damage or corrosion – if you can inspect it and then access it to make good, that seems like a reasonable trade off to me. As the joinery in a steel boat only needs to be just that, it should be easily possible with a little forethought to design in ease of access to allow for essential maintenance. Equally true for aluminium….
Best wishes
Colin
I’m no expert and having only just bought a plastic boat – an Elizabethan 33 – upgrading from a clinker Folkboat – I will not be buying any other sort of boat any time soon. However, I have come across two excellent accounts of the use of steel sailing boats. Sadly Bernard Moitessier is no longer with us but he goes into some detail on the design and construction of steel boats as well as the benefits. Check out his books ‘The Long Way’ and ‘A Sea Vagabond’s Life’. They’re a great read anyway. Also, unless the Antartic ice has done for him recently, Trevor Robertson has got to be the most experienced person on the planet when it comes to building a modern (in terms of construction techniques)steel sailing boat and sailing one into the most extreme high latititude environments. See his blog at http://iron-bark.blogspot.com/.
Tom
Hi Tom
Two great sailors, and two great boats. You’ve got to take your hat off to Trevor Robertson for his remarkable feat in Antarctica, let alone his others.
But I’m sure both of them would agree that protecting and conserving steel has come a long way in the ensuing years, often as a by-product of developments in the field of oil and gas exploration. New finishes for metals of all kinds that they would have used themselves if they’d been available when they built their boats, no doubt.
Best of luck with the new boat
Colin
Many thanks Colin. It’s an age thing. 1997 when Trevor built Iron Bark seems like yesterday not 15 years ago! As you say much must have changed. Hope that includes insulation. Trevor’s account and photos of thick frost and ice on the inside of Iron Bark are not for the feint hearted. Look forward to hearing more on the latest advances.
Tom
This is a very interesting article. I choose steel for my 47 sailboat just launched and to make it maintenance free… i built the deck in SS 304 so everything above the hull is stainless steel. 3 coats of epoxy primer inside topped by 4 inch of polyurethane soya based isolation and it will be trouble free to last me. Topside there is not much plane to maintain and under water it is very rare to find rust because there is less oxygen than on the deck were crawly places are impossible to maintain.
My parents owned a 35′ steel cruiser built in 1989. It is sold to a friend of ours and it is still with it’s original coat of paint and no rust anywhere. Amount of time spend to keep it in that state is not more than a couple of hours a year.
our new built Arctic expedition boat (50′) is also made of steel, that was for the ease of building. Now, 40,000 miles and 4 years further, there were some rust spots where the paint was not applied properly, but that has been fixed. I do not expect any paint work in the next 5-10 years.
I enjoyed this article and it is very helpful as I am considering a steel boat for long distance cruising. The Migrant 36 has quite a wide transom which allows it to have a generous sized aft cabin. This goes against the advice in John’s article “Motorsailers not recommended”. I am not insulting Caitlin of Argyll by calling her a motorsailer but I would be interested to hear thoughts on her hull shape.
Hi Billion
I wouldn’t class the Migrant 36 as a motorsailer, although it’s true that in the standard format she is a heavyweight cruiser. The underwater lines are less full than what I’d call a motorsailer, the two feet added to the stern (of Caitlin) extend the lines nicely, and she has a considerably taller rig than the standard design. As a result her sail area to displacement ratio is far better, and she sails well.
Best wishes
Colin
Interested reading, Im looking for a yacht over the next 2-4 years and steel is looking very interesting. Please keep me uptodate. Im based in the UK. Many Thanks
Very interesting, thanks.
I am currently considering an Alan Pape design in steel. Will read part ii.
Regards
James
Hello I enjoy watching your videos very much. Especially your cooking in the gallery. If you have time to answer this question, I would really like to know the name of the stove top oven that you use to bake your breads. I wanted to purchase one for my boat. Hope to hear from you.
We have a 57ft Steel Cruiser which was built to Australian survey specs. one of the best ways we have found to prevent rust on the inside is to allow any possible areas for water to sit (stringers, ribs, bulkheads, lips, nooks & cranny’s) to drain to the bilge. Ideally the bilge should always be dry and 99.9% of the time it is however there is always the odd occasion that condensation, or some other thing creates a puddle and if that puddle is allowed to sit its a sure fire way to kill the steel in that spot. When we repair/replace any part connected to the hull on our boat we notch the corners (hull side) so they create a natural drain. This also means that any unwanted moisture in the boat goes to the lowest and most visible part of the bilge, rather than staying trapped behind (insert any part of the boat that isn’t immediately visible). The other thing we have found which was mentioned in the article is the use of stainless as a wear surface. Its the easiest way to prevent issues and if/when paint chips off as it does its really not an issue and can stay uncoated as long as needed without any side effects (the parts must be designed in such a way that the weld between mild and stainless is not able to be chipped or is very difficult to chip)
The Asperida: A Copper-Nickel Sailboat after More than Thirty Years in Seawater
https://www.copper.org/applications/marine/cuni/applications/hulls/asperida_boat_hull.html
Hi Doug,
Interesting. Aluminium, properly cared for, has exhibited the same longevity.