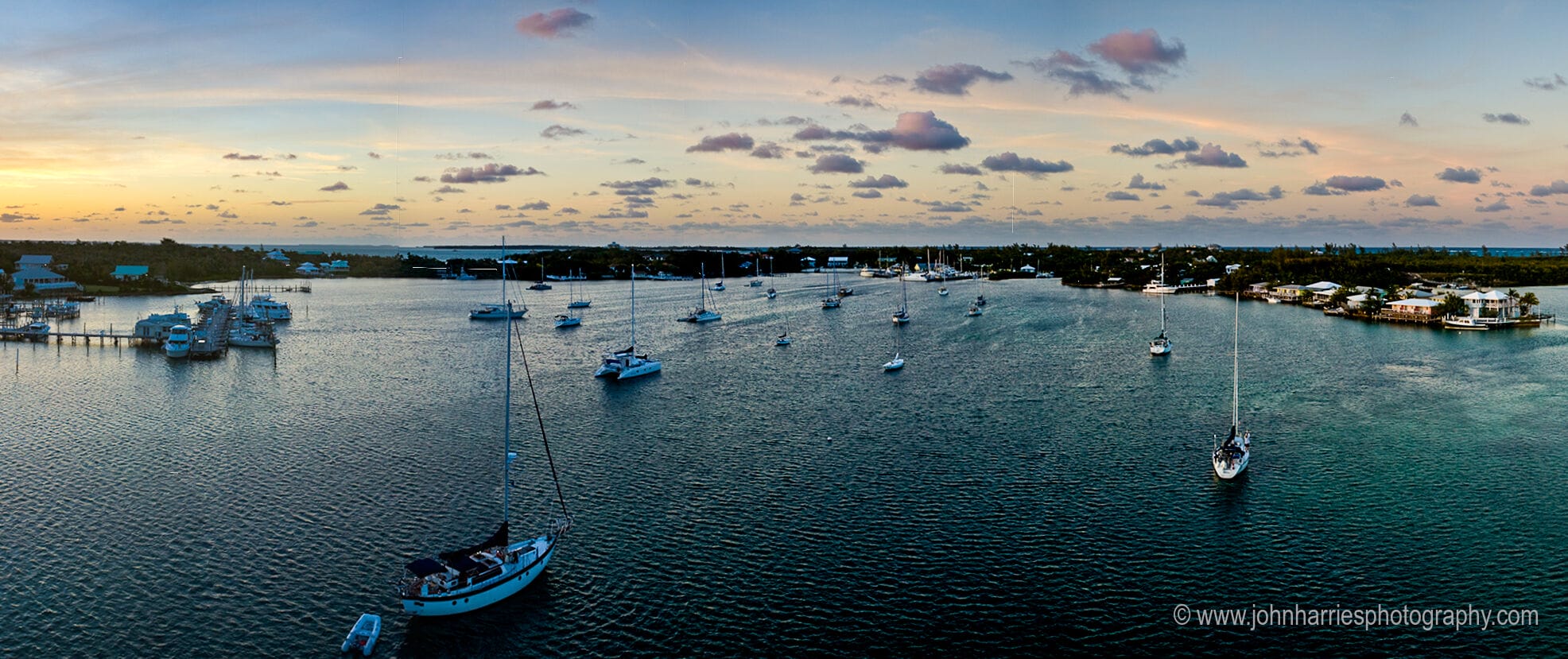
We have several chapters in this Online Book about the characteristics of the four generally available materials to build a boat out of: steel, aluminum, wood and fibreglass (see Further Reading below), but that still leaves the question: Which is best?
As usual, the answer is the oh so annoying: it depends on what we plan to do with the boat.
But what I can say, is that there are two materials that are pretty easy to drop from the hull materials prospect list. So let’s start with that, and then move on to the two left standing to pick a winner.
Hull Materials We Don’t Recommend
I strongly recommend not even looking at boats made of steel or wood—with the possible exception of a good wood epoxy saturation build.
Why neither of those two materials? Both are intrinsically unstable.
Or, to put it another way, no matter how well the boat is built, if left to their own devices, wood will rot and steel will turn into a pile of iron oxide.
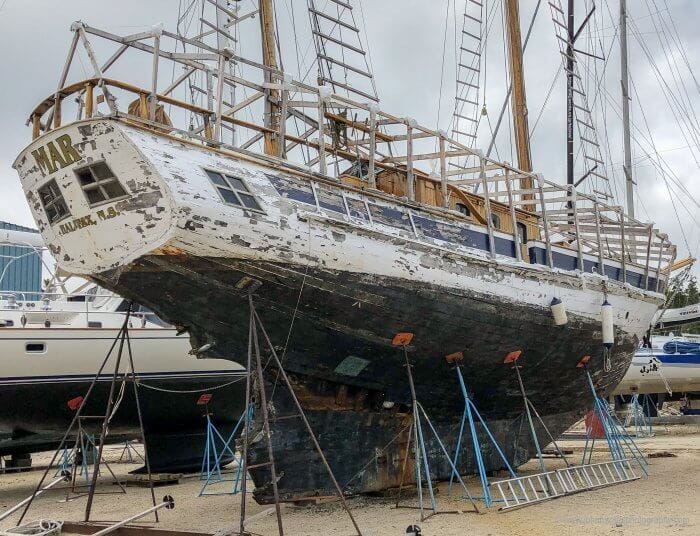
OK, before you take me to the woodshed in the comments, let me make clear that I understand that good boats can be built of both wood and steel.
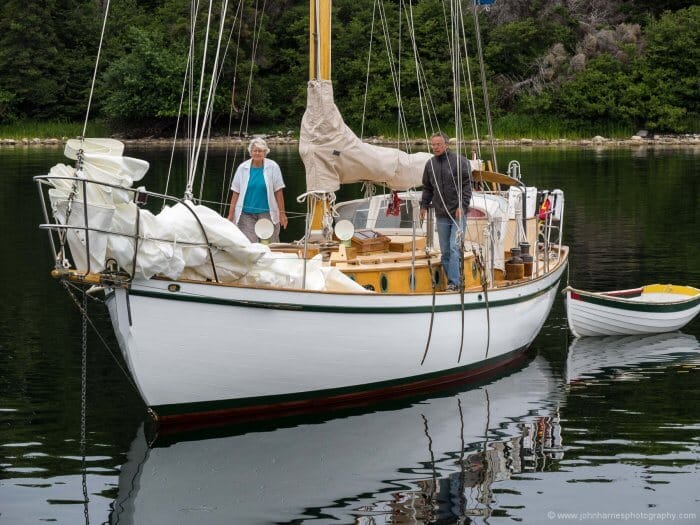
For example, one of my good friends has a wooden boat that has given great service (including a bunch of ocean crossings) for decades, and will continue to do so for many more. But he built her himself, has cared for her meticulously, and has incredible skills. But I’m not Wilson (that’s his name) and, in all likelihood, neither are you.
The same applies to steel. If you built the boat yourself, or supervised every step of the build, and then cared for her yourself, it can work.
The Uncertainty Problem
But we are talking about second-hand boats for most of us, so in that case steel and wood are out because it’s difficult to be even reasonably sure in a pre-purchase survey on either material that something horrible is not going on deep within the structure.
Something that, when discovered, can turn our new-to-us boat into a worthless pile of junk—we are talking the risk of serious wealth destruction here.
Difficulty of Repair
Still not convinced? Let’s dig deeper into what happens with these two materials when we find a problem.
Wood
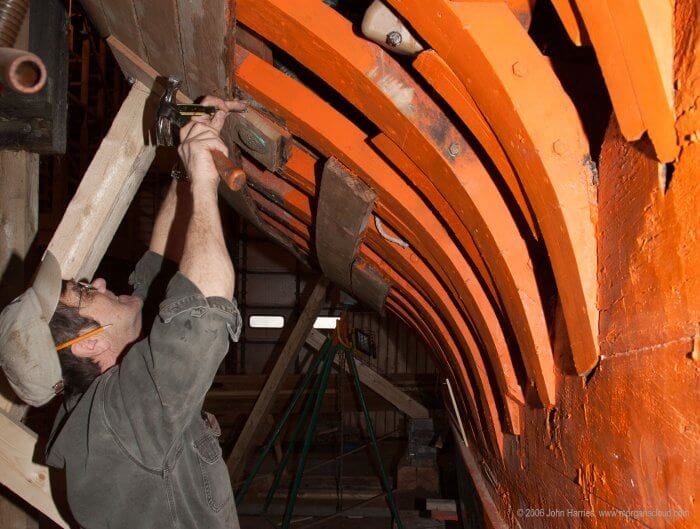
With wooden boats, if we find say a rotten stern post, or any other defective structural member, the skills and time to replace it are prodigious.
Heck, just replacing a single plank in a way that will actually be watertight takes great skill and perseverance. Way beyond practical DIY for most of us. And I have seen professional replacement of just a few rotten members in a wooden boat cost over US$100,000.
Steel
What about steel? Well, on the positive side, repairs require less skill than wood, but on the other hand the maintenance of a steel boat is brutal; and rust never sleeps so the work is also constant and endless.
So unless you have some perverted love of chipping rust and working with toxic chemicals, forget steel.
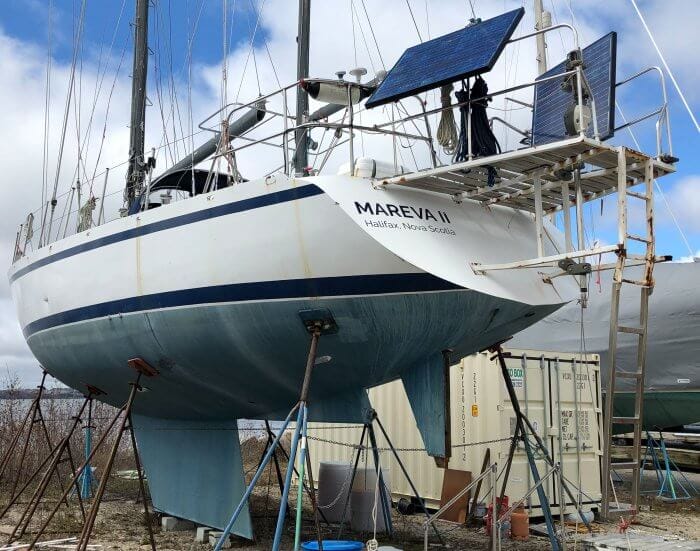
The bottom line is that I know a lot of people who own a steel boat, or have done so in the past, but I have never met anyone who has owned a second steel boat.
Recommended Hull Materials
So where does that leave us? Yup, with fibreglass and aluminum.
Both are intrinsically stable, assuming we don’t do something stupid, and, when built right, a hull of either does not deteriorate just because of the passage of time.
And both can be surveyed prior to purchase to make fairly sure (there is no certainty) that there is not something horrible lurking. Yes, I know there are many horror stories (I have one of my own) about fibreglass boats with hidden faults, but that’s a survey failure, not a material one.
So which is best, aluminum or fibreglass? That depends on what you want to do. Let’s look at each.
Aluminum
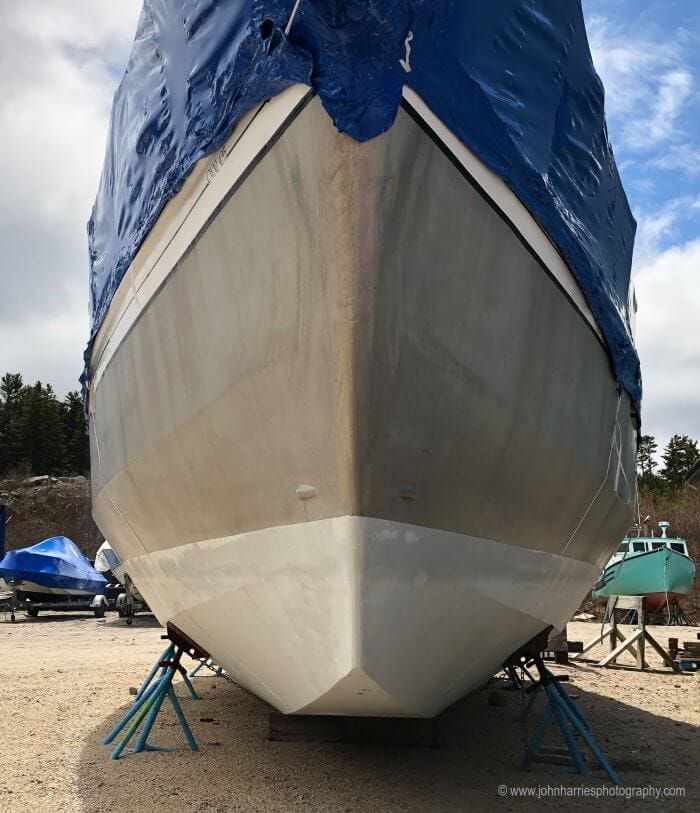
As a 30-year aluminum boat owner, I love the material. And if Phyllis and I were planning to go to seriously hazardous places (as we have in the past), aluminum would be our only choice.
There is simply no other material that can match the combination of strength-to-weight ratio, impact survivability, and stiffness, as well as keeping those characteristics for decades, all without the horrible maintenance load of steel.
But, on the other hand, aluminum is a nightmare to keep paint on, an expensive nightmare.
And don’t think for a moment that leaving the hull bare solves that. Prepping and painting the deck and cabin of an aluminum boat to the yacht standard that many owners want and want to maintain, will, if done right by professionals, cost as much or more than painting an entire fibreglass boat.
The point being that if you are considering aluminum, you need to do as I did: take your glasses off when you see the paint bubbling. Or, better yet, seriously embrace the industrial look and have no paint on deck or hull, other than non-skid.
Also, although there is no question that most of the horror stories you hear about aluminum are just that—stories—the material does require caring for, including closely supervising anyone who works on the boat.
Most boatyard professionals are dangerously ignorant about aluminum and many will make that worse by not appreciating their own ignorance.
Bottom line, if you are not willing to learn aluminum boat care (see Further Reading) and won’t be constantly present to rigorously enforce that knowledge on others, don’t buy an aluminum boat.
Fibreglass
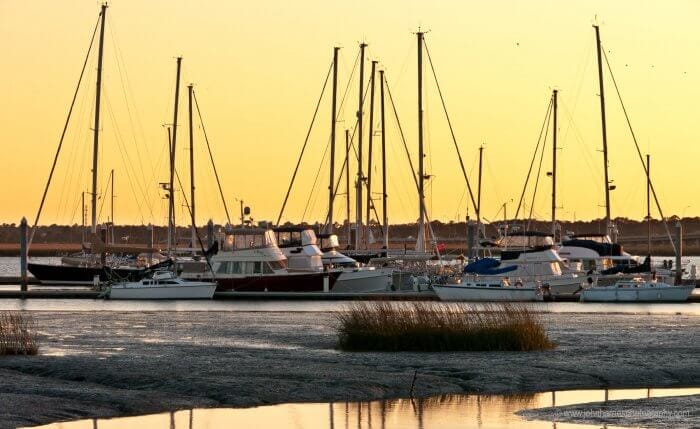
So that leaves good old fibreglass, the best material for most of us, and most usage profiles.
Summary
When buying a boat, good old frozen snot is the baseline and aluminum the ultimate, but with caveats. As for steel and wood, the great majority of us should not go there.
Comments
I’m guessing that many of you steel and wooden boat owners are now seething and reaching for your keyboards to tear me a new one. Feel free to disagree and tell us why steel or wood is great, but be realistic.
And please keep in mind that we have a lot of readers who do not have a lot of boat ownership experience. So if you blow sunshine about the issues with steel or wood boats, particularly old ones, you may make yourself feel better, but you may also tip someone into a life-altering decision with substantial negative consequences. Not something any of us need on our conscience.
Hi John,
here comes a “seething” steel boat owner, but only to state that you are probably right in most cases of steel boat ownerships. Just a few remarks:
1. You should have included Colin Speedie’s article from 2012 on this site “Thinking about a steel boat?” It explains very well how to avoid most if not all issues with the material.
2. The reason why you haven’t met “anyone who has owned a second steel boat” may be because a steel boat owner has absolutely no reason to look for any other boat because he or she is so satisfied with his or her first steel boat. That certainly is true for myself.
3. I don’t feel that I have any more maintenance burden than my fellow sailors with their fibreglass boats, but that is because my Snowball was built the right way in a reputable yard, now 45 years ago, and later my pre-owner replaced all the steel parts that normally give rust problems, like hatch coamings, life line stanchions, foot rails and many more with stainless steel. Furthermore the boat is spray foam insulated, no gaps, no condensation anywhere and is protected by a high quality 2-part paint system throughout which is very well maintained over the years.
Yes, there are some steel boat specials like the two galvanized standpipes which were worn (read rusted) thin and had to be replaced. On the other hand my engine is keel cooled, a huge advantage, nearly impossible with fibreglass or wood.
But of course, it is probably very hard to find a used steel boat of that standard and that confirms your statements in the article.
4. A personal thing that was sitting in the back of my mind ever since we met in Nuuk in 2011: I suspect you saw the brown discoloring on Snowball’s stern and it became even worse when we had arrived in England the following year, really terrible and I was ashamed of it. But a half hour of scrubbing removed the stuff. It was rust running down from a lesser grade “stainless steel” fitting that held the stern posts for the solar panel. Long since replaced and no issues any more.
Hi Hans,
Actually I thought about including a link to Colin’s series, but sadly I heard (not confirmed) that said boat ended up with some serious corrosion problems so I decided against it.
And I’m sure you are right that “Snowball” is a great boat that has served you well. But, as you say, she is probably the exception that proves the rule.
The other point for others to contemplate is suppose for a moment that “SnowBall” had been built of aluminium? She could have had all the features you love and have been a great deal lighter, even if she were built to the same strength—aluminium has a higher strength to weight ratio than steel. And if unpainted, she would have had a lower cost of ownership and might even have been less expensive to build. Properly coating steel in and out is very expensive.
I agree absolutely. Snowball is a Taranga, designed by Kurt Reinke. Tarangas are very rarely built these days, but if they are, aluminium is the material of choice, no question.
I’m shocked to hear that “Caitlin of Argyll” should have fallen into a sad state.
Hi Hans,
Me too, on “Caitlin of Argyll”. But it was just a rumour, so hopefully it’s not true.
Hi Hans,
Looks like she was being recoated in 2015 and sounds like there may, or may not, have been issues: http://islanddriftercanaryislands2015-16.blogspot.com/p/4.html
May have just been a repaint.
Hi John, i followed the link and found that they had had indeed a problem which was solved by cutting away a corroded piece of hull and welding in a new plate, which proves the easy repairability of steel hulls. But of course it also proves that one just can’t be sure even if it’s a boat as good as “Caitlin” (or Snowball ??)
Hans, I would like to have a conversation with you concerning paints and foams to use on my sailboat. Rick Dowe
Hello John,
I think you are correct about steel boats, except, there are boat owners I know who have owned more than one steel yacht. In the Netherlands many are build to very high standards, and there is a long tradition of doing so. Perhaps that is the difference, that there are more builders here that build with steel, service steel, and have done so for a long time. Many now also build aluminum.
My father has owned three: a 60ft steel traditional Tjalk that my parents lived on, then a 33ft Zeeschouw, and finally a 36ft Van der Stadt cruiser. They all rusted and required a lot of work. In the end he could not keep up, and the beautiful Van der Stadt was reduced to scrap metal. So indeed, even starting with a near perfect boat, it won’t stay that way unless you put in the work, as Hans is clearly doing with his Snowball.
There is an end of life, when it is no longer worth it to maintain an old boat. I have seen several smaller fiberglass yachts getting dismantled and chipped up, but there seems to be nothing that can be done with all that plastic. Steel, wood and aluminum can be recycled. Is there an other destination than landfill for fiberglass?
Hi Maurik,
Good points, particularly the great job the Dutch do on metal boats, generally the best in the world in my view. Also good point that in the end steel boats tend to die from rust no matter what we do.
I also agree that old fibreglass boats are a huge issue, but since I was mainly writing about buying second hand boats, I think that encouraging people toward fibreglass is kinda green, since they will take care of, and thereby extend the life of, whatever GRP boat they buy.
That said, there is no question in my mind that the greenest option is unpainted aluminium. Big carbon footprint to build because of smelting aluminium, but aluminium boats stay useable the longest because if built right they don’t corrode as steal does, or soften up, as glass does: Cases in point: https://www.morganscloud.com/2012/07/01/one-tough-old-aluminum-boat/ and https://www.morganscloud.com/category/boat-design-selection/morgans-cloud/
Seems odd >99% of ships are steel. Personally enjoy visiting the WW1 and 2 navy ships in my area.
Believe for the recreational sailor Fe makes no sense for a reason not mentioned. Weight. To TIG weld Al you need a certain thickness or you will burn through. So a minimal thick is spec’d. To MIG or TIG Fe thickness isn’t much of concern but with very thin sheet available for sacrifice. Weight also affects speed, available pay load and efficiency. So it makes little sense until you get to well over 60’.
With modern construction techniques and coatings corrosion and electrolysis aren’t the bugaboo you suggest. Add in impressed voltage stray current corrosion is also dealt with effectively. Fe has the highest puncture and abrasion resistance of available materials. In all modulus parameters is the strongest. The limitation isn’t what you suggest but rather it just doesn’t work for smaller vessels. Look at recreational boat/ship listings of large vessels. Fe hulls with Al top hampers predominate. Once hull becomes less of a percentage of total weight Fe is and remains a very viable choice. Hence new construction is those suitable sizes it continues to lead.
Hi Lee,
Sure steel has benefits, most things do, but I stick by my thinking that for the yachts AAC members own, the disadvantages far outweigh the advantages.
The popular view seems to be that aluminium boats are stronger than fibreglass. I wonder if a lot of that may be to do with their design and their marketing rather than the material used. I’m thinking about Ovni, Allures, Garcia etc. Pitched as ice hungry aluminium sea tanks.
As far as I understand it fiberglass is stronger than aluminium (for a given weight). Of course if a fiberglass boat and an aluminium boat have an equal hull thickness the aluminium hull will be stronger (everything else being equal) but if the fiberglass is laid up to say 1.5x the thickness of the aluminium, or whatever, until it is the same weight as the aluminium, it will be stronger. Or reduce the thickness slightly so it is equal in strength to the aluminium and save some weight. Either way fiberglass seems to be the better material choice to me. Plus no worries about galvanic corrosion.
Having said that fiberglass is a bit common and a bit ugly, aluminium is cool and exotic. But when was practical ever cool?
Strength, here, is more a matter of design philosophy. The kinds of buyers who want welded aluminum, and are willing to pay for it, tend to put a high priority on toughness and strength. Therefore, aluminum cruising yachts tend to be designed to be tough and strong, even if that adds some weight and costs more labour hours to make.
We can achieve similar results with fibreglass if we want to. But we can also use fiberglass’s strength to cut back on material quantities and reduce the amount of high-touch labour needed, therefore reducing weight and cost. That’s how most production builders prefer to go.
It’s not terribly difficult to design a fibreglass hull that’s as tough as a welded aluminum Ovni; there just isn’t much demand for it and it’s a harder thing for the marketing guys to make hay of. Especially when the CFO is asking for cuts to the Raw Materials budget.
Hi Pete,
Sure, if you make the boat thicker it will be stronger, and if you don’t care about performance that’s fine. But I’m pretty sure I’m right is saying that aluminium has a much higher strength to weight ratio than fibreglass, which makes it work great if one wants strength and performance. Also aluminium is far more ductile and so less likely to get holed. And sure, with GRP we don’t need to worry about galvanic corrosion, but with aluminium we don’t need to worry about water getting into the laminate. Aluminium is also way easier to repair to original strength.
That said, as I wrote in the article, I agree that for many, perhaps most cruisers, fibreglass is the best choice.
Hi Pete, Matt and John,
I can’t say anything you haven’t already mentioned, to some extent, and most points I’ll make are kinda obvious, but anyway, different words may contribute?
When the material itself has lower density, is lighter, we can build the hull thicker for the same total weight. An aluminium plate that is the same weight but much thicker than a steel plate, is dramatically stiffer than the steel plate. However, the steel surface remains much harder, more resistant to scraping rocks or penetrating sharp items. The exact same, with a bigger step, is true when comparing FRP (Fiber Reinforced Plastics) to aluminium.
If we want a hull that is just as robust to any type of abuse as possible, steel wins hands down, while also often being the cheapest to build, but it will usually be quite a lot heavier than the same boat in the two other mentioned materials, and vulnerable to decay.
If we want a boat that is very robust to abuse, albeit not as much as steel, while being almost as light and stiff as FRP, aluminium is the clear winner, but it costs significantly more than standard FRP builds.
If we want a boat that is light and stiff, and where a vulnerable surface is acceptable, FRP is the clear winner, especially because it’s the cheapest (excluding exotic materials and methods).
Summing it up.
Steel: Max robust and fairly cheap, but heavy, and not durable.
Aluminium: Quite rubust, fairly light and durable, but expensive.
FRP = Light, durable and cheapest, but not robust.
So what’s the best boat hull material? Obviously, as John often says:
It depends.
If we build a very thick FRP laminate, it will be tremendously stiff and strong, (and probably not cheapest anymore), but the surface will remain soft and vulnerable. Lying on a beach with some small rocks in the sand in waves, could be survivable for a strongly built boat. Still, even an excessively thick FRP hull will wear through faster than a much thinner aluminium hull, which again will wear through faster than an even thinner steel hull. The surface hardness of the hull material is essential in that situation.
However, in a boats life, hopefully that’s never. 🙂
Hi Stein,
I agree with most of that, except expense. If aluminium is left unpainted it’s generally less expensive than steel because the cost of labour and materials to adequately coat steel is avoided. And even without that, aluminium is far easier and quicker to work with than steel—as Frank Luke said to me once, aluminium is just kinda-hard wood—so there are big savings there.
Also, if building a custom, or even short run production boat, aluminium is most often less expensive than GRP because no mould or expensive tooling is required. This is particularly true these days when the designer can develop a cut file much more easily that in past times, and every part can be cut out ahead of time by a specialty company.
Having built many different things in both steel and aluminum, including a 44′ aluminum sailboat, I think that aluminum is much faster to fabricate and weld than steel. This more than offsets the material cost difference. Plus, achieving properly finished and blended welds on aluminum is easy compared to steel.
Hi All,
It is interesting to compare material properties here although this assumes that all the materials are perfectly processed and they are suitable for the application (it is possible to do the layup or get the welding torch in where it needs to go).
Looking purely at yield strength, fiberglass is by far the strongest. Note that yield strength is per area of material and not weight. E glass is around 1800 MPa (there is much more variability here than the other materials and it has to do with fiber orientation and quality of layup, most production boats are probably way lower). 5083 aluminum plate is around 230 MPa. A36 steel plate is around 250 MPa.
Looking at density, fiberglass and aluminum are similar, steel is about 3X more. Fiberglass is around 2.5g/cm^3. Aluminum is 2.7 g/cm^3. Steel is 7.9 g/cm^3.
So if we want strength to weight or strength for area in a purely tensile member, fiberglass wins. Comparing aluminum and steel, if we want strength for area, there is really no difference but if we want strength to weight, then the aluminum wins by about 3X.
However, all of the above is for pure tension and very few things in the real world use pure tension. In general, we find that a lot of applications put materials in bending. When you are in bending, your thickness becomes hugely important for strength. For example, strength is proportional to the square of the thickness for a beam in bending. If we keep thickness constant such as in an area where you are space constrained, the relative strengths are proportional to the yield strengths so the order is fiberglass then aluminum and steel tied. However, it gets much more interesting if you compare by the same weight. The fiberglass and aluminum will have about the same thickness so the result is the same as when you hold the thickness the same. However, due to steel’s density, you end up with 1/3 the thickness which when you consider cross sectional moment of inertia, it becomes much less strong, like often an order of magnitude less. This means that the steel boat either becomes very heavy or is forced into a geometry with less bending in the members such as by using closely spaced framing.
Fiberglass has another trick up its sleeve which is coring. Since most of the material towards the centerplane when there is bending is under very light load, it can be replaced with a less dense material that has adequate shear strength and have very little impact on overall bending strength. Essentially you can think of it as a way to lower the density while not impacting bending strength. When this is done, fiberglass is way stronger than anything else on a constant weight basis.
So from a pure yield strength and weight standpoint, there is a clear winner but that is not everything. Looking at something like toughness, the shape of the curve beyond the yield point is really critical and ductile materials far outperform here as they keep absorbing energy and not breaking. Abrasion resistance is another consideration which goes steel, aluminum, fiberglass. On puncture resistance, you really need to watch out for the cored fiberglass as the thin skin does not like point loading. Another thing to watch is whether the material can be used to make the optimal shapes in a cost effective way, fiberglass and metal behave very differently here.
I take away from all of this that both fiberglass and aluminum give properties that if properly designed, analyzed and optimized into a design can yield good boats. I have come to appreciate fiberglass a lot for the majority of use cases although some of the specifics around preventing deck leaks, rudder construction, etc. are preferable with aluminum.
Eric
Hi Eric,
Great overview, thanks. The big learning for me was the point about stiffness and thickness. I knew this went up by the square of thickness, but I had not really related that to this discussion, and so doing makes things a lot more clear for me, particularly why steel does not work as well as boats get smaller. Add that to Matt’s point about the rapid weakening from corrosion of thinner steel plates and I’m even more comfortable with my recommendation to stay away from steel as a yacht materiel.
Another thought arising from your comment, is if one is really supper worried about bending and puncture I’m thinking the best all around solution is aluminium Strongall in which very thick aluminium plate is used with almost no structural members: https://meta-yachts.com/en/
It’s also interesting to note that the yard that builds Srongall is the same one that build Joshua in steel, but they are no longer using steel.
Hi John,
Strongall looks great from a puncture perspective, nothing like a thick material to do that.
From a pure bending standpoint such as the loading when you fall off a wave and land flat at the bottom, the more efficient structure (strength to weight) in the elastic region (meaning no permanent deformation) is going to be a framed construction.
I don’t have a good sense of whether yacht designers are designing around bending or point loading. I kind of suspect that most fiberglass cruising boats have the limiting design parameter being bending as cored construction has pretty poor puncture resistance. The calculus could change for expedition yachts venturing into ice regions but I am not sure.
Eric
Hi Eric,
Yes, I think this stuff is far more complicated than most yachties realize, and an engineer of your experience saying “I am not sure” makes that point well. Anyway, I have always been intrigued by Strongall, but I suspect you are right that for most use framed is the best compromise—it certainly did well by me for years.
The article should have this title “Hull material which is best or 20 meters or less boats” because otherwise 99.999 % of the worldwide commercial and millitary fleet of boat sand drilling platforms (and submarine) at sea are steel and everybody get along with that. There exist much documented process to protect steel against corrosion its one of the most studied material.
Why nobody make aluminum barge ? You see tons of them aging in port still doing their work.
I Have yet to see a large scale aluminum hulled icebreaker ?
Large scale aluminum boats are rare (some commercial fast catamaran and corvette yes but rare) and small sailboat in aluminum not high number production but if you can wait you’ll have one.
Large scale steel boat are common and you would like to convince us that any small sailboat in steel would not be desirable ? I don’t understand the logic with the primary cause being the material.
The primary cause is the money. Aluminum is much more costly material, and aluminum welding a more complicated process with helium gas and water cooled mig guns that require “ferblanterie” expertise – hammering the weld after welding to anneal the aluminum otherwise the heat affected zone is bringing back the alloy to basic aluminum stiffness around 15 kpsi.
Aluminum is a top product. Really it is, 5083 is a miracle alloy for sea water usage. But everybody owning the 99.999 % of the world marine fleet had to make a business choice and we also have to as sailors and boat owners.
Don’t get me wrong i love metallic boats. I have a friend who has a sistership of my Chatam 43 built in aluminum, it floats about 2 inch higher that the only thing that can distinguish them. Paint doesn’t stick well to the hull or deck, he has more paint chips than i have, and they don’t rust. My boat have paint chips on the hull and they don’t rust as weel but on the steel hull they do. but apart that we can’t distinguish one or the other and we have compared our maintenance its about the same. The deck of a sailboat required much more maintenance than the hull.
what is the difference then ? His boat is 50 % more costly than mine. Both boats are about 13 years old and have cruised extensively north and south and we’ve been in the carribean together in 2021-2023
When i planned to build in 2008, commercial quotes from yard to build a 43 feet aluminum sailboat (only the hull, deck, opening with hatches …what we call a closed hull for later finishing) was 150 000 canadian.
I build my hull with stainless steel deck and superstructre for 60 000 $ including paint and including 1000 hours of my work valued at 25 $ per hour. Steel was 0.60 $ per pound and stainless 2.00$ per pound at that time.
Can’t paste the picture but go look at the evolution of pricing of aluminum. I predict in 5-10 years nobody will build aluminum boat it will be too costly.
https://tradingeconomics.com/commodity/aluminum
Current aluminum 2618 $ per ton
Current steel 721 $ per ton
Again money… for the money i saved, i spend it on high quality sails and Furuno electronics, cat 1 ocean hatches and prime mahogany finition inside. Will the boat last 50 years ? Yes and probably 100. I won’t see the end of this boat. there was approximately 1 square inch total of chipped paint on the topside and top railing… took me 2 hours total. This is all i got for 2 years in the carribean.
On a small boat as you mention it all depend on the building process and quality because at the end, no real steel boat exist its only steel hulls covered with epoxy and plastic about 20 mils thick. If it stays there, then the metal is protected as long as the plastic is there.
Disclaimer1 i have owned an aluminum boat also… had to rebuild a patch of the hull under the engine because water was dripping inside through invisible small holes in the 1/4 thick hull… galvanic corrosion which is 10 time more treacherous than rust.
Rust never sleep, but rust shows. The steel cries for attention when needed. Aluminum if you are lucky and very attentive you will see. Most often you won’t.
Disclaimer 2 i have GTAW and GMAW all position welding certification for aluminum, steel and stainless 304, 308, 309, 316 and training in destructive welding testing abilities.
Resume:
-Rusty steel boats do exist in large quantity, good steel boat exist in very small quantity.
-Aluminum is probably the best material but exotic and elite.
-Corrosion impervious aluminum boats do exist in reasonable quantity.
-Aluminum, Steel and Stainless steel can corrode given the right oxidant but sea water is not an oxydant for 5083 aluminum alloy
Aluminum and aluminum alloy are anodic to steel in seawater and will corrode very fast and silently to stray current or galvanic corrosion.
There are no, perfect, maintenance free, fool proof hull material valid for any working combination. You pick what make sense for your usage based on your competencies and understanding. When competency doesn’t match the material you get problems.
The problem with steel is that corrosion rates are similar for boats of all sizes, but smaller boats have thinner plating and framing.
1 mm of corrosion to a 25 mm thick plate is negligible. The same 1 mm of corrosion to a 4 mm thick plate will bring it down to 75% of its original tensile strength and half of its original stiffness. Stress concentrations at the rust pits will reduce that further.
So, steel – while it is excellent in most ways for large vessels – gets really problematic, lifespan wise, when you go to smaller hulls and therefore thinner plates. Rust that is just superficial on a freighter would, at the same thickness, be lethally structural on a small boat.
Hi Andre,
That’s all very interesting about boats over 20 meters, but it’s not relevant to our members, so the title you suggest would not really work.
Also, I already said in the article that steel can work if you build the boat from scratch yourself, so we agree on that.
As to relative cost, you are comparing apples to oranges when you compare having a hull built out of aluminium to home building out of steel. Also, if you look at resale value many people would be way better off buying the aluminium hull and finishing it themselves.
And you assertion that galvanic corrosion is 10 times more treacherous than rust is just not bourn out by experience or the number of old aluminium boats that are still in good shape after 50 years compared to steel boats of the same age. It’s also wrong to say you can’t see corrosion on aluminium. In fact a white powder shows long before any really bad damage is done.
So yes, steel worked for you, and that’s great, but most people are not going to spend years building a boat themselves from steel and coating it as carefully as you did so I don’t think any of your comment changes anything for most readers, particularly since I already pointed out that if you want to own an aluminium boat you need to know how to take care of it.
All that said, I totally agree with your last paragraph. In fact I wrote pretty much that in the article.
the aluminium in our hull of 15 m is about 6 to 7 tons.
so that about 13k more for material
generally the cost of the hull is somewhere at a quarter of total cost, hence a few percent up or down due to the material, still no issue compared to the fortune typically sunk into a boat.
the build is likely cheaper because it is much easier to work and bend, and an automated MIG welder covers steel or alu the same. Fronius, the top brand is about 15k a unit amortised over 10 years -who cares about the cost. For Alu/MIg, they use an Argon-Helium mixture, which at the quantities they buy is a bit more. And my shop rate for the welder is the same. i also I have a one phase Fronius TIG welder, so I can make small changes myself 6K – also irrelevant in the context of overall cost. Only needs Argon.
the savings on paint is a multiple of that; ours has only the underwater paint, everything else is sandblasted (course on the deck and giving great traction.
galvanic corrosion you have to watch, no question and keeping up with Anodes and making sure a proper electrical installation a.must. But being sunk by a galvanic corrosion hole will require serious inattention of your bilge pumps.
i would set the limit more like at 30 m: at some point it makes more sense to deal with the paint system.
in summary, I’d consider a very good depreciated wooden boat long before a steel one, but that’s my choice for the aforementioned reasons.
Hi George,
Good to have an actual cost number on the material difference. Amazingly small, particularly when considered against the cost of a boat or the cost of coating steel properly.
Hi John,
thank you for another great article.
After 16 years of owning a laminate yacht, now I am looking for a used aluminum yacht. I realize that there is no perfect material, but aluminum looks best to me.
I have read all your articles on how to care for an aluminum yacht. However, how to look for serious problems on a used (25 years old) aluminum yacht?
I know that I can check the electrical installation with a meter, but can I find any alarming signs of electrolysis in a yacht that is in the water? Are there any other areas on a used aluminum yacht that I should pay attention to? My question concerns hull corrosion and the resulting lower strength of the hull.
If any of you have experience with finding problems on an aluminum yacht, I would be very grateful if you share it.
In 3 weeks I’m going to see the boat and check it. If I don’t find any major problems, I’ll probably buy it.
Thank you in advance for any opinion.
Hi Michal
I started to answer, but it got long, so I am writing a Q&A tip. Look for it in the next week or so (unfortunately I’m traveling for a few days)
Thank you John. I appreciate it very much.
Hi Michal,
I got a moment to finish it: https://www.morganscloud.com/jhhtips/qa-inspecting-an-aluminium-boat-hull/
The great thing about steel is that it really only has one failure mode – and it always makes itself obvious to the observant. The problem is that many steelies were built decades ago and where either not built or maintained correctly. Or the paint system they used has long been superseded by the far better systems now routinely used by all large commercial vessels.
There are really only three things you need to get right.
Keep the bilges clear of all plumbing and wiring, hose them out with detergent and fresh water once a year or so, and keep them clean. Foam up areas between any tanks and the bilges – as these are inaccessible.
Avoid dissimilar metals, insulate or paint over the junctions. Eliminate wet timber in contact with the steel – better yet replace with a modern composite like Coosa board. Never drill a hole when welding or gluing could be done.
Learn a good commercial paint system – like Jotun – and stick with it. First of all degrease and chemically clean the area thoroughly, eliminate all residual salt. Get a salt tester kit. Use modern carbide rasping tools to clean up small areas, passivate with phosphoric acid, then paint to a measured thickness of at least 200u. This will take at least 5 coats using brush or roller.
Follow these rules and a steelie will be no more maintenance than any other. Sadly though the task of getting a steel boat that has been allowed to deteriorate is bolting the stable door after the horse has left and it should probably be scrapped – and this is what you see too many examples of.
And for some reason I don’t understand – failed steel boats seem more common in North America than anywhere else. Right now I can walk down my finger here in Australia and point to three absolutely excellent steel boats in the 40 – 50ft range and no-one thinks them unusual. In fact two of them are routinely mistaken for fiberglass hulls.
Hi Philip,
While I agree with much of what you write.
I can’t agree that a “Follow these rules and a steelie will be no more maintenance than any other”.
Even a steel boat perfectly coated and and lovingly taken care of will need re-coating at some point, and that is way more expensive and difficult to do well than a fibreglass boat, and an unpainted aluminium boat never needs paining or re-coating at all.
Case in point: https://www.morganscloud.com/2024/10/06/hull-materials-which-is-best/#comment-311953
And even a painted aluminium boat only needs the outside recoated, and only if we care about cosmetics. Ditto fibreglass where gelcoat will last for decades with a quick buffing, not to speak of being, I would guess, an order of magnitude less expensive to apply in the first place.
And finally, neither GRP or aluminium boats need any coating or re-coating inside the hull.
Bottom line, keeping a steel boat from rusting is very expensive and time consuming up front, ditto over time.
Nothing steel boat fans can say changes the fundamental that steel is an intrinsically unstable material as against aluminium and fibreglass that are intrinsically stable. Stable is always going to be easier, less expensive, and more forgiving.
Cost of recoating, yes and no.
there was beautifully painted aluminium boat in the yard the other day, about 13 m and the owner said he repainted it himself. I asked him, how long did it take you. He said he sandblasted the top layer and applied two new coats over the original paint. Time spent less than two weeks. He rent a paint booth for the work.
if the paint system doesn’t have to be taken down to the steel, it might not be such a big deal,
Hi George,
We had the same experience when we repainted our aluminium boat hull. That said there are almost always dings on the deck that need full primer treatment and from what I see out there the same is true with steel after a while.
I do agree that steel is inherently unstable, but not catastrophically so. As George L mentions – repainting the exteriors is not an unreasonable task and with a modicum of care a modern epoxy/polyurethane system should last at least 20 years – if not more. When I purchased ours, we sandblasted from the waterline down to white metal, and repainted with Jotomastic 90 (with an alloy flake) to 300u and six years later it remains as good as the day it was done. Done at a commercial yard, total cost was under A$6k at the time.
(They were doing a massive trawler right next to us at the same time, we were pretty much just ‘overspray’ to them – as the foreman said. All done in less than a week.)
The key element is to keep the interior from rusting – which is why most of what I mentioned above is directed to that concern. Once these surfaces are compromised beyond easy repair – then I agree it’s probably too far gone as it essentially involves a major refit to perform correctly.
Overall I would only ever choose a metal boat because they are so strong, rigid and done properly they never leak. Aluminum is the other excellent choice – as long as it has been welded by someone who knows what they’re doing. Good welders are not as common as people might like to think, nor can it be done on the cheap. And when good examples come available around here, they are usually well outside my price range.
In that sense I’m comfortable with steel as I’ve learned how to live with it, and it suits my budget. If I was to buy another one – I would happily make an offer on one of the three aforementioned boats tied up nearby.
And while I fully accept steel is not for everyone – I’m kind of glad for this. It reduces the competition in the market. 🙂
Hi Philip,
Sure, if we are just painting the outside, and particularly the hull, all is good and relatively inexpensive. But, as I understand it, most steel boat die from the inside out because it’s extremely difficult to adequately coat every tiny corner. And then, even if you can when new, when the inside coating needs repair that often necessitates taking some or even the entire interior out of the boat, and then reinstalling it.
Contrast that to aluminium where we don’t even want to coat the inside of the boat.
There are now a lot of 50 year old aluminium yachts around, with many more years of life in them while most 50 year old steel yachts are in the corner of some boat yard having broken someone’s heart.
So we come back to my original recommendation: while a new steel boat properly supervises in build can work, buying a second hand one is generally not a good idea. Are there exceptions? There are always exceptions, but that does not make hoping to be lucky a good strategy.
For me with steel it’s the inside the hull issue that gives me pause (also weight and performance). Over time how do you get to all areas inside the hull to inspect or re-coat? Maybe with a boat designed to be able to do that but even after that it seems like a lot of work and expense vs the other hull material options. I might consider steel if I had a very specific trip in mind (eg short term to arctic and then sell the boat afterward) vs long term cruising (eg years aboard).
Hi Keve n,
Yup, that’s the biggest issue, getting the coating absolutely perfect on the inside and keeping it that way. Sure it’s possible, but as you point out, why bother when there are other materials that don’t have that fundamental problem.
Also, as far as the high latitudes are concerned, most voyagers with experience in that area have selected or switched to aluminium in recent years. Sure steel has a higher puncture resistance but in the real world the benefit is not that much because aluminium plate can be specified thicker without an undue weight penalty.
And if one is really worried about this issue, there is always Strongall: https://meta-yachts.com/en/
Re: the difficulty of painting aluminum. I used the Pettit primer system both below the waterline and on the decks of our Dix cutter. The underwater part has been perfect for 8 years, no complaints. The Kiwigrip deck anti-skid I applied in ideal conditions with proper 2 step priming and low humidity began failing after 4 years. It is continuing to deteriorate We’ve done 3 winters in the tropics, with summers mostly in the north above 50˚. I believe the detachment of the coating is due to the thermal expansion of the aluminum. The Kiwi grip is an acrylic polymer and is very hard. Different Coefficients of expansion.
I wonder what others have used as deck anti-skid on their aluminum boats?
I went with the bare look on the cabin sides and topsides, and am very happy with the decision. They have a nice patina now after 8 years, not everyone’s aesthetic for sure, but certainly easy to maintain.
Hi Brian,
Sorry to hear about the issues with Kiwigrip. I had high hopes for that stuff for aluminium boats. For deck covering we used treadmaster stuck down with west system epoxy and had good service, but it’s a lot of work. The other option might be to coat the deck with thickened west (after acid wash etc) first and then put the kiwi on top, but that’s only a guess. Put Treadmaster into the search box on the menu and you will get a lot more information.
I have a few areas of diamond Treadmaster – around the windlass at the bow and on our companionway steps. It has held up pretty well. I’m going to look at their softer ‘wavy’ pattern this winter while in London. I talked to a Canadian in Vancouver at the Metal Boat Society meet a number of years ago who had stuck TM down with Sikaflex (291?). Iy was an alloy Brewer design…lost touch so don’t know how it worked out. It seems a flexible adhesive might work better than an epoxy? In any scenario it’s a pile of work.
When we were looking for a 40-50 foot boat in the 1990’s we consulted Philippe Harlé, one of the top and most prolific French naval architects. He has designed ocean voyagers, and weekend boats in all materials for many builders, and had no vested interest in any material.
He commented that one great advantage in aluminium over steel and fibreglass is that the amount of work to rupture an aluminium hull is more than the others. You could call it “toughness”
Thank you John and Phyllis for a topic most if not all boaters have or were forced to think about. Also a big Thank You for all the very interesting comments from your membership.
Born below sea level (Holland) just after WW2 there was little money, let alone for boats. We all spent our first days surrounded by water and no doubt all were worried about the material that kept the water in. Now a few years later we boaters worry about the material that keeps the water out.
My grand-dad’s boat, a wooden Fries Jacht, named Frisia, now a world wide classic, built well over a century ago, in 1876, Google it, is still around, but it took some hard guilders to keep her afloat. I, as a pre-teen grandson still remember how my Dad at the helm, dared to take a jibe with quite a breeze and looking up, saw the un-staged mast bending like a straw, hoping for the best, but overtaking 2 or 3 by doing so.
My Dad’s first boats were ofcourse wood aswell, but his last one was steel, commissioned in 1964 and still going strong, but it has spent some years on the hard indoors:). Now pretty well all the boats in my family are/have been aluminum. My “small 60ft Feadship”, built in 1984 in Holland, has now spent the last 30 years or so on our US/Cnd west coast. One of my brothers aluminum motorcruiser was built here in Cnd by Kanter, but he used it on the European waters. Another brother has had Flyer II for almost 30 years, with first owner ofcourse the well known Connie van Rietschoten, the only sailor having won the Round the World Whitbread Race TWICE. My first serious sailing journey was in 1968 from Holland to Iceland in a 33ft Avenir sail boat also built by Royal Huisman as were Flyer 1 and 2. Grand-dad Huisman started building wooden sailboats, and later his grandson Wolter started using steel, but it didnt take him long when he discovered the advantages of aluminum and fascinating to see how it became one of the worlds finest mega yachtbuilders. and I think their subsidiary mast making company Rondall, made the tallest mast on Bayesian, whose tragic and mysterious end came just a few weeks ago. Even more so to know that both owners of the company died within a day of each-other, one went down with his yacht, while his biz partner died a day earlier, a thousand miles away in the UK during his morning jog by a Hit and Run driver. Coincident ??
I know from my days in the merchant navy that painting ,as is the case with the Eiffel Tower is a never ending process. So your comments on steelies came across a little hard, as the bulk of boats in Holland were Steelies, but I should state most of those were used on fresh water. A friend is doing a circumnavigation at this moment on his 60 year old, Dutch build, 65 ftr motorcruzer, named Monara.com, presently in Japanese/ Russian waters. Capt Jan ofcourse was complaining about rust, but we learned early in life that it is all part of the boating life-style.
My plan is to one day have my boat sandblasted down to the bare metal, a job still too expensive and the Awlgrip still too good to have it done presently, but also not knowing how much Bondo will show up under that Awlgrip. I have noticed Americans have some kind of fear for the metal, much less so in Cnd, while in Europe, if you can afford it, pretty well a favorite. Maybe the reason we see quite a few 50 year old aluminum hulls, totally gutted ,only to start a brand new life.
I often wished the builder had used a thicker hull plate so that fewer lead bars for ballast were needed. Steve and Linda Dashew with their FPB’s also have left quite a legacy for bare aluminum yachts !
However, I have to agree with you, it is one of the best materials for boats, but it will be interesting what technology comes up with in the field of graphene, epoxies, carbon, kevlar etc.
A number of years ago I came across this comment, that ships are designed for 15 tons of pressure per mtr/sq. Damage will show at 30 tons/mtr/sq, while falling of a freak wave creates 100tons per mtr/sq.
To you and Phyllis, Happy Thanks Giving !
Hi John,
I will have to agree with you on a steel boat. After selling my Morgan 382 we looked and tried to purchase several other boats but were always outbid. In 2021 we went down to Grenada and looked at and eventually bought a steel boat. We went down the following year and sailed it back to Maine. After having the hull UT I had to rip out the forward birth and I am now replacing metal. Not something I was looking forward to in my retirement. I had to take a course in MiG welding because no one wanted to work on it and eventually I had it moved to my house so I could have freedom to make steel dust and not contaminate other hulls.
It’s hard to sell a boat when it is torn apart so I will continue.
Hans, I would love to hear from you on your paint recommendations. I have a pretty good idea on what to do but love to get your personal opinion.
Hi Richard,
I’m really sorry to hear that, that’s a terrible task for retirement. I hope you get it sorted out without too much agro. And thanks for being open about the drawbacks of steel. Overcoming confirmation bias is hard, but we do a real service to others when we talk about the drawbacks of whatever decisions we have made.
Hi John and readers,
I bought a used Aluminum boat. Its a Garcia. Boy did I get far more then I asked for in work!!
My boat was built in France in 1987 – beautifully built and strong as strong can be – but the boat turned out to have some serious corrosion issues completely and totally missed on pre buy inspection.
I have had to extensively replate the boat in 5083. This replating is from both corrosion and damage – I am convinced that boats in this class that can be beached with a retractable keel will have lots of bumps in the bottom plates of the hull – mine does and I am not replating those as its just cosmetic – all the serious stuff was replated.
My aluminum welder is a freak of nature – his welding is the best I have ever seen and anyone who looks at the work we have done comments on the welds – how good they are or something like “I have never seen TIG welding as tight at that”. So my welder is a craftsman and has built a number of Aluminum boats – so 100% the right guy for this restoration work.
So where was the corrosion and what caused it ? As my welder-boat builder said to me – in his entire career he has never once seen an Aluminum boat corrode from the outside – its always always from the inside out. In this hull, the water tanks had SERIOUS corrosion – when we sand blasted the hull we blew holes through the hull in 3 places – all 3 places had fluids resting on the bare aluminum. I never knew this but I do now – municipal water in your aluminum tanks WILL corrode your aluminum tanks and if one were to sterilize the water with “Milton” or “JIK” or some other type of water sterilizer, you WILL have serious corrosion on the Aluminum plate that comes in contact with that sterilized water.
So we had to rebuild both Port and Starboard water tanks. I learnt a valuable lesson – dont ever EVER underestimate the amount of time it will take to rebuild a tank – plus the time to make new tank inspection hatches in the rebuilt tanks!
Then there was the engine bay…… two holes caused by sandblasting (lucky we found it at this stage of work though) of the water side of the engine bay area of the hull, had to be replated in the engine bay. This was due to leaking wet exhaust that no one ever noticed over many years….it was very easy to see where the drips where hitting the Aluminum plate. We had to cut that part of the engine bay floor out and replate.
Then there was the heads where some years ago someone added an aluminum water box to the floor of the heads to collect shower water but the design was such that they used one wall of the bilge next to it as a wall of the water box – they painted it with a primer (which was still there to some extent) and then an epoxy which was apparently very hard – it had cracked and water had got under the epoxy and was able to just sit there for who knows how long – it had corroded away a pit hole that was less then 1mm before it was through to water – we blew threw it when sand blasting.
Apart from the bumps in the hull here and there, the rest of the hull is solid and in good shape.
The lesson is clear – DO NOT LET FLUIDS come into contact with the Aluminum plate on the inside.
@John. I have many photos/videos of the process as we went. I have many photos of the corrosion before we touched it and many photos of the repair process step by step. If you want access to these photos in the cloud, let me know and I will give you a link so you can access them.
Hi Mark,
Sorry to hear you have had such a time with the Garcia. Sounds like the surveyor really let you down since checking inside the tanks is basic with aluminium boats.
The dents in the bottom are one of the reasons I like the Boreal with it’s keel box, but if said dents are not too bad, I think you are right, they are not a problem.
On the tanks, you are right that chlorine attacks aluminium. We always ran dock water through a filter to take the chlorine out.
And yes, I can see that exhaust water would cause a problem since it’s highly corrosive. And we strongly caution against coating aluminium inside with epoxy because, as you found, water always gets under it and causes issues.
That said, my experience does not support the idea that any water inside the boat on the plate will cause issues. When we were in cold water (most of the time) as you would expect the bilges in our M&R 56 were constantly wet from condensation and that never caused issues. I also discovered standing water under the generator, when we took it out to replace the mounts, that had been there for years, again, no issues.
One thing I would say, is that I strongly suspect some of these issues were at least contributed to by stray current corrosion so you will want to check over your electrical system and make sure it’s isolated.
More here: https://www.morganscloud.com/category/aluminum-boats/
I would like to pitch in being a steel boat owner.
I agree about the pitfalls of steel. We spend a fair amount of time keeping the inside of the hull spotless. And yes there may be somewhere i dont know whats going on. Oh the anxiety. But in my opinion you missed talking about the upsides to steel. Its the strongest and cheapest material. Dont buy a steel boat that has not been properly surveyed and be critical. Dont buy a rusty steel boat unless you want many hours of fun.
One Big upside is us poor sailors can actually get a good boat in steel that we could not afford in GRP or Aluminium. The maintenance may be a little higher on a steel boat, but only if the boat is lacking maintenance.
When i win the lottery I will upgrade to an aluminium boat. But for now my steel boat gives me so much safety and comfort at sea i dont see the negatives as hard as described in the article.
GRPs on the other hand have so many structural issues when sailed hard and especially the production boats twist and wobble after a couple of hard ocean crossings. In my opinion it is not always that simple. If you choose GRP and want to do serious sailing it needs to be high quality GRP work to meet my standards.
Hi Martin,
Good on you for acknowledging the anxiety of wondering where unseen rust might be gnawing away.
And agree that second hand steel boats are often the cheapest option to buy. But there are also reasons for that that are less attractive. The key one is cost of ownership taking into account maintenance and the delta between the buy price and the sell. This last can be particularly bad since many older steel boat can’t be sold for any price, or at least for so little it’s more of a gift than a sale, and this after costing far more to maintain than GRP or aluminium over the time we own the boat. Add that up and often steel is by far the most expensive material.
The other issue, is opportunity cost. If we buy a second hand steel boat and then have perform major repairs that takes months or even years of “prison work” as Colin calls such tasks, as so often happens, was that the least expensive option? No, not really. Think about the cruising time we lost, if nothing else.
As to steel being strongest, again, that’s too general a statement. Eric Klem explains why here: https://www.morganscloud.com/2024/10/06/hull-materials-which-is-best/#comment-311996
And yes, I agree that many GRP boats are poorly built and so soften up with age. But that’s a QC problem, not a problem with the material. We only have to look around at the number of older well built GRP boats still out there cruising, many approaching a half century old, ditto aluminium, to see that both materials can have great longevity. And when did anyone last see a 50 year old steel yacht out there cruising, at least one that has not been totally rebuilt?
Its not that i dont agree on your points. But just to take our own situation as an example. To make our dream of cruising attainble it was either through an old smaller GRP or a bigger and Well maintained steel boat. I have also heard all the horror stories of steel and can also easily see how they happen without diligence. But i would never recommend anyone buying a second hand boat that was not in a good overall structural condition.
Was I lucky with our boat. Maybe partly. Just like so many other boat buyers. We surveyed it and spent a long time reaching the conclusion this steel boat was the right one. We spend alot of money on the boat, but not because of rust work or paint maintaince. The downsize to steel is it is so heavy it brings the cost of engines, Blocks and sails etc up compared to Aluminium and GRP. That is actually my main argument for considering other materials.
We could never afford a 50 foot aluminium or a Well built GRP.
So to sum it up. I would also rank it 1. Alu 2. Well built GRP 3. Steel. But i will always rank the attainable adventure higher than sitting at Home dreaming of doing what the old boomers are doing with all their savings (sarcasme may occur)
One last comment. Lets say we agree sailing is better than dreaming of the unattainble sailboat. So searching for a second hand boat has to take up front price into account for some of us.
When we searched the boat market 3 years ago i almost never saw an older built aluminium boat i wished to own. Since you owned an older aluminium you may have an other perspective. But looking at the market for aluminium boats fra 80-90 is a slim chance of finding anything really good. In my honest opinion the quality of aluminium sailboats first really went up end 90’s when the new consensus of electrolysis was changed and the aluminium market grew.
Hi Martin,
I agree that there is a slim chance of finding a really good boat from the 80-90s, but then I would argue that applies to all hull materials. Bottom line, most 30-40 year old boats are going to require a lot of work, but on the other hand with aluminium and GRP if the hull was built right in the first place, the chances or really big problems are much lower because nether material degrades just from the passage of time, as steel does.
Hi Martin,
I would certainly agree that if a boat gets you out there sooner, that’s the most important criteria. So yes, if you can find a inexpensive second hand steel boat that does not end up needing a huge amount of repairing before getting out there, that’s a valid option. The problem is that from what I have seen, that’s also quite rare.
And i forgot to say that I love the work you do here. We spent years preparing for our sailing adventure and I love the simplicity and directness in the advice and knowledge on this site. Alot of this knowledge I put into practice everyday. For that I am thankful.
We found a very Well built steel boat. The only one we seriously considered. It is welded and constructed to Lloyds certificate, with a stainless steel deck. But nonetheless when the GRP boys polish we paint and grind the small rust spots. Part of being a steeler.
Hi Martin,
I think that’s a good summary to leave it on. Key point, you went to a huge amount of trouble to get a good boat, and that trumps all.
One point regarding alloys that may be obvious to most commenters here, but not so to all readers: Welding any alloy is very hot. Thus all nearby interior accoutrements – furniture, bulkheads, trim work, fabrics, insulation – must be removed when repairing. And any significant area of welding may well distort shapes such that interior parts won’t fit back into place.
One key advantage of composites is repair at ambient shop temperatures. Yes, there is the effort to cloak and cover everything, use lots of fans and blowers, and vacuums when grinding to a clean bonding surface. But these are all tools and skills readily achievable to most hands-on DIY boat owners.
Adding or remodeling interiors presents the opportunity to bond cabinetry panels to the hull and/or deck, increasing stiffness and decreasing flex (give your fly rod a shake).
In sum: GRP may not be the toughest material, but it is the easiest to repair and modify, while its limitations can be mitigated with good design, even on old boats.
Hi Randall,
While we have welded on our aluminium boat without removing everything, including welding on new toe rails, I think that’s a generally good point.