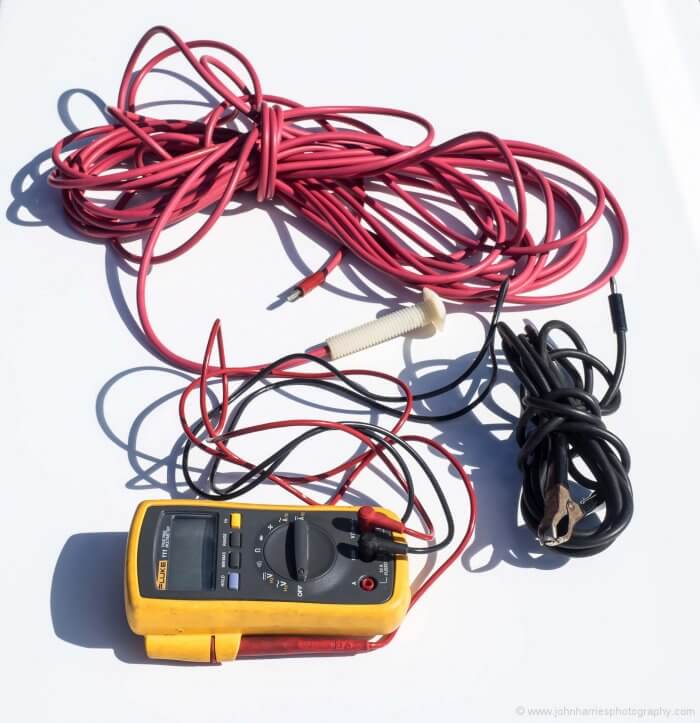
Morgan’s Cloud, our 56-foot aluminum cutter, turned 30 this year, and she and I are coming up on our twenty-sixth year together. One of the amazing things about the boat, and the material she is built of, is that, at least as far as I can see (I look pretty carefully and regularly), she is just as strong today as she was the day she was built with no appreciable wastage.
That said, boats built from aluminum do require care and attention to detail. To help with that, in this three-part chapter I’m going to provide practical tips.
And let me emphasize the word practical. I’m going to focus on what we actually do that has worked to keep our boat in good shape for a quarter of a century, rather than get into a lot of theory.
Here we go:
John,
Thank you for removing some of the mystery behind caring for aluminum boats. An Ovni is high on my list for future cruising, and over time I’ve heard horror stories about caring for them (and similar boats). So these articles are very helpful.
Hi Mike,
Glad it’s useful. As we shall see in part 2, caring for aluminium boats is really no bigger deal than any other material, just different.
That VDO gauge looks nice. Found it at two other French retailers as well. Have asked Summit Racing if they can order it (part YC310) from their VDO supplier. Will ask same of VDO directly and ping thread if responses are noteworthy.
Hi Brian,
Thanks, hope you have luck with your search. When I tried to source one in North America I couldn’t find anyone (including VDO) who would even admit that such a thing existed.
Another similar interesting divice from Philippi is the “hull isolation control STV iso” and relatively cheap.
Philippi is also selling an AC polarity tester named “shore connection unit LAR”
Great article , very timely , have just relaunched my 1989 Ovni after a 2 year refit and are in the process of sorting the electrical system . Could not source the VDO product so using a local Australian made product called Seabis . Can’t wait for part 2 !!!
Hi Ian,
Glad it is useful. I had a look at the Seabis, but have to admit that I was rather put off by the tone of their website and the fact that they make a lot of huge claims for it, but never explain what it does or what the installation issues are.
How was working with them on the installation?
Damn, John, inset zincs? It’s so obvious, but evidently not, as I’ve never seen it before. Aside from the obvious reduction of drag, do you find any other benefit? I have a steel boat and it’s probably not worth doing as “going faster” is a low priority, but I’m willing to listen to persuasion.
Hi Marc,
The only benefit of inset anodes, is, as you surmise, speed. That said, four anodes sitting proud of the hull would have quite a bit of drag so if I was faced with that I would at least try to find streamlined ones.
Thanks John, great info!
Just replaced my inset zincs with alloy anodes, as the boat spends most of the time in fresh water. The old zincs had turned brownish and was told its an indication they stopped working, but not much show of wastage. My isolation transformer gets quite hot (50″C?) is that normal, does the temp. go up and down with the amount of amps use.?
Certainly will try to obtain the VDO gauge you mentioned. Also like to know how often do you haul your boat? I understand yours is always in salt-water. Mine apparently will soon be due for a new barrier coat.
Thanks again.
Rene
Hi Rene,
The only way to know exactly what your anodes are doing is the meter I write about above, but the very fact that they were not showing much wastage may not be good news in that it can just be an indication that they are not working.
As to the isolation transformer, they all get warm and the more current (amps) being passed the warmer they get. That said, 50c sounds too warm to me, but that’s only a guess. I would strongly recommend contacting the transformer manufacturer and asking them if this is OK. Also check the rating on the transformer to make sure it’s big enough for your use.
Our steel vessel had an “Acme” branded isolation transformer aboard, which to my understanding was engineered for land-based construction purposes. It got way too hot for my liking just sitting there with no load. That and other factors spurred me to do an extensive electrical refit. I replaced the Acme with a Charles unit designed for the marine environment — night and day difference. The Charles runs cool, has a powder-coated case, and to the best of my recollection features epoxy potted or transformally-coated innards. I think the Acme transformer was widely used in the 80s as a cheap alternative to the marine units. I have seen photos online of its use on other boats. However, having witnessed the drastic effects of salt air on non-tinned wiring and connectors, the thought of keeping the Acme scared the hell out of me.
As for zincs, ours are teardrop shaped and I “reactivate” them by diving on them twice a year with a stainless steel wire brush to remove any scale and brighten them up.
Hi Brian,
Thanks for the fill on the transformer. We have a Charles too, and it’s 30 years old with no problems so far.
Many (perhaps most) of the boaters who don’t completely neglect their anodes tend to throw them away far too early. Probably more than three-quarters of the anodes I see in scrap bins still have most of their useful life in them.
What matters, for this purpose, is total exposed surface area. If the anodes look brown or gunked-up, just give them a quick scrub with a wire brush to expose some fresh metal. The bulk of the mass is just there so that they won’t waste away to nothing during the intervals when you aren’t checking them.
Re. the isolation transformer. AC power hardware designed for use on land really does not belong in this application. It’s usually not protected from corrosion in any way, and there’s a good chance it won’t be wired properly for marine use (where the ABYC standards are different from the Electrical Safety Authority codes, it’s for a good reason). And while transformers do get warm, the kinds found on boats do not get dangerously hot. If you burn your finger on the case, unplug it and call the vendor.
Hi John, Just remember though if a 2 bob piece finds its way to the bottom of the hull, you’ve had it. Seriously though, our solid fibreglass cruising hull will see us out. In our next lifetime though with even more resultant enlightenment an aluminium hull will be just the shot. Cheers Dave & Ruth.
Hi Dave,
There’s a lot to like about solid fiberglass, particularly that, as long as it was done right in the first place, its pretty hard to hurt it with neglect, so definitely a real advantage over most other materials in this regard. I will have some offsetting benefits of aluminium in the next post, but the bottom line is it’s all about tradeoffs, there is no best hull material.
HI John, this is a very important article if one has a aluminium boat or a boat with aluminium in the hull. I have an old oak icebreaker with a 2mm aluminium skin. This thin protection skin lasted 60 years. We followed your rules. If you do not, I know such a thin skin will vanish fast. To mix oak, steel, copper and aluminium in a hull is very dangeous. You can get a lot of corrosion. And the corrosion will start in the aluminium parts. But doing it your way even a 2 mm aluminium hull can last 60 years. If one can manage to protect such a thin aluminium skin, steel, iron and oak will also be in a perfect condition.
Hi Svein,
Well there’s another endorsement for the longevity of properly cared for aluminum!
Thank you John and Matt, and my comment re : the hot isolation transformer was overstated, normally it feels warm , but there have been times, maybe when the hot-water tank was heating up, it felt much warmer. Certainly will check it more frequently.
The reason we changed the zinc annodes, was advised alloy ones would work better in fresh water, and will try to keep them shiny as mentioned.
Time will tell.
Svein, like to know more on how your alloy skin was applied to your boat, maybe under a different heading.
Rene
Hi Rene! Your question is to me very interesting, but I think the editor will find it off the headline. So John, as an editor you must find another option to discuss this matter if you think it is important. I have studied ice skin of wooden boats fore a long time , but you must deside how to continue or not on this matter.
Hi John,
As to Sveins comment re: alloy skin, if you dont like to pursue it at this time and if your R&R
permit to do so, you may forward my e-address to Svein.
Many thanks,
Rene
Useful post, thanks John.
And yes Alu alloy anodes do seem counter intuitive dont they! Nonetheless our Allures 45 is factory fitted with 2 on the skeg and one on the centreboard and applicable for all waters. Interestingly, they are mounted on rubber isolation gaskets and their Alu fixing bolts are set in silicone sealant by way of protection. We have had very little wastage indeed over the last 3+ years.
The prop and bowthruster are also similarly protected.
Hi Neil,
Yikes, by isolating the anodes someone at Allures has made a very bad mistake. And the fact that they are not eroding is not good news, in fact probably the opposite. For anodes to protect the hull they must be electrically connected to the hull with no resistance.
More in the next chapter, but in the mean time I would recommend checking the hull voltage with a meter and silver chloride electrode sooner rather than later.
Hi Neil,
We recently had anodes mounted on our older Garcia at the Allures/Garcia yard so I know exactly what you are seeing. I think the rubber gasket is just between the anode and the hull but the mounting bolts pass through it. The bolt heads & nuts are covered with silicone. The idea, I believe, is to limit anode erosion to its working surface rather than on the back or around the mounting bolts, which might make it disintegrate or fall off.
Hi Phil,
Well that’s a relief! Thank you for the fill. That said, with only one anode mounted this way I would be very diligent about checking regularly with a meter and silver chloride electrode to make sure that the boat was still protected. All it would take was a bit of corrosion debris under the bolt heads to render the hull completely unprotected.
Hi John,
4 of my inset alloy anodes are about 8´ in diam and bolted down with one bolt in the center.
Should the hull have been scraped clean of all coatings before mounting anodes?
Am not sure if this was done.
Rene
Hi Rene,
More on this in Part 3, but the key point is that the anodes must be well connected to the hull to work. So on our boat, I keep the mating surfaces clean. That said, it’s not vital as long as you are checking with a meter and a silver chloride electrode since that will immediately warn you if the anodes have become disconnected.
Thanks again John for, what now appears to be a very important topic, confirmed by Svein and his 2mm alloy skin. Always knew the role of anodes, but never realized how vital role they play on alloy boats and looking forward to your Part 3.
Rene
This is a very timely article for me. I am the (relatively) new owner of a 12 year old Garcia and in the midst of anode replacement. The anode arrangement is much like described above for the Allures with a rubber gasket between the boat and anode. In my case, there is a stud welded into the hull and a nut that holds the anode on. Electrical contact is made from stud to nut to anode. The nut was completely covered in sealant. Additionally, the previous owner had coated both sides of the gasket with adhesive sealant. Needless to say, that made getting the old anode separated from the boat a real pain in the ***.
I don’t really see the point of making the back of the anode a 100% watertight connection and prefer not to reinstall with sealant behind the anode. I’m not even so sure sealant over the stud and nut is necessary. Can anybody else using this type of anode mounting system chime in as to exactly what you do and why?
As an aside, the anodes are aluminum, this seems pretty standard in France. They are evidently alloyed with indium and magnesium to both adjust the potential voltage and prevent the aluminum oxide layer from forming.
Hi Martin,
The key issue here is that the anode must be connected electrically to the hull, otherwise it is simply a decoration that does nothing except give the owner a false sense of security.
More in part 3, coming soon.
Hi Martin,
I have an older Garcia and recently had the Garcia/Allures yard add anodes to the hull. They have a rubber backing pad and sealant over the nuts; I don’t know if there is sealant on the backing pad.
My understanding is that there are two reasons for doing this. First you want to confine the anode erosion to the front surface and limit it on the back and around the mounting bolts because if it wastes away there it will fall off, or at least loose its secure electrical connection, before the end of its useful life. The second reason is that water trapped behind the anode becomes very caustic (high pH) and this causes paint damage. Using sealant as well as the backing pad may well be overkill but I think using the pad and sealing around the bolts is probably good practice.
Philip
Thanks Philip, that is useful info. I agree that sealant on the back is overkill but want to know if anybody has a reason why it is necessary. Ironically, the sealant on the back of the anode indirectly damaged my paint in that I accidentally dug through the paint trying to remove the sealant. I’ll put sealant over the nuts but not on the back when I put anodes back on.
Hi Martin and Philip,
I don’t think all of this really matters very much, as long as the anode is properly connected to the hull.
That said, our anodes have been bolted to bare aluminium for 30 years and there is no evidence of any pitting or other problems with that, so, if it were me, I would not bother with gaskets and the like.
More in part three.
Hi John,
Surely one of the key points here is that your aluminium hull is painted. This is the primary reason that your zinc anodes have so little corrosion – they are only protecting the hull in any spots where the paint is damaged and the Al exposed, which would be few given your obvious attention to detail. The primary corrosion protection on any vessel or marine structure should be a protective coating. These unpainted Aluminium boats are fine in theory, but as soon as you throw your steel anchor in you become one big anode.
Hi Dan,
Yes, good point, paint does protect parts of the boat, but the key point is “parts”. For example the inside of the shaft log won’t have any paint, so anodes are still required.
That said, having an unpainted hull above the water won’t make any difference one way or another. And I have never seen an aluminium boat that was not painted below the waterline.
Hi John,
I agree, there are always parts that are unpainted or hard to get to to repaint, and the anodes will/should protect them, but you will need your anode relatively close to the point to be protected, sea water still has a resistance of 0.2 Ohms/M which becomes significant over a boat length.
Not sure I agree 100% on whether having an unpainted hull above the waterline won’t make a difference. Yes, aluminium oxide is a good corrosion inhibitor in air and if you are permanently moored in a sheltered harbour that might be fine, but in use, boats have a tendency to be wet a lot of the time above the waterline, and thus you have an electrolytic path. For my money you’re better off painting as much of the vessel as possible and saving your anodes for the bits you can’t get to or the scratches you can’t see.
Hi Dan,
Proximity of the anode to the metal being protected is an interesting one. I’m not entirely sure, but I think that actually it does not matter since it’s the conductivity of the aluminium, not the sea water that matters. Or to put it another way, a single anode, if well connected and and large enough, will raise the hull to a safe voltage and there will be no significant potential differences anywhere on the hull.
That said, I still prefer having multiple anodes because it gives backup in case one becomes disconnected.
As to bare hulls being a problem, I just can’t see that being significant. Sure some current will flow through water splashing up on the hull, but very little. The bottom line is that aluminium is really not that vulnerable. The proof is the many bare aluminium boats that have been fine for decades.
Due to the difficulty & expense of replacing a shaft log I applied epoxy barrier coats inside mine. Easily done by pushing a paint saturated rag through. The coverage was not 100% each coat so multiple coats & drying periods were
required. Using different colors each coat allows you to see when it is fully covered. The initial aluminum preparation inside the shaft log was done with sandpaper attached to a slot cut in a 1/2″ diameter 5 foot long aluminum rod, spun by a hand held drill. This was followed by the chromate conversion. It took a couple of hours.
My Van de Stadt Samoa was built in Japan and the anodes are in flush/recessed pockets, bolted to an aluminum stud that is welded to the hull. They were not bedded in sealant, but do have the rubber pads and full barrier coat on the hull behind them. I had always wondered about that. The nut holding them on is never loose, and they always show just the slightest amout of activity to assure me that they are working.
Hi Stephen,
That’s interesting. I will be interested to hear how it holds up after a few years. Another approach I have heard of is to line the log with a G10 tube beaded in polysulphide. My worry with both of these approaches, perhaps unfounded, is that it will be difficult to determine if the barrier is 100% effective and if not crevice corrosion is going on at a point where it was breached.
Anyway, given that our boat’s shaft log is fine after 30 years, I guess I will stick with my current (ouch, bad pun) approach.
John, a very good piece on a poorly understood subject.
While I understand why you advocate isolation (it’s common among European builders), Grounding the hull to the AC safety ground, and DC negative, is a requirement for compliance with ABYC Standards.
The reason this arrangement often goes astray is because there should be only one connection between the hull and the vessel’s DC negative/AC safety ground system. If there are multiple point so contact, the hull can become a conductor.
If the hull is not grounded, particularly to the AC safety ground, it could become energized with 120 volts without tripping a circuit breaker. If a person then touches the hull and something that is referenced to the AC neutral/ground, a generator or engine block, or the chassis of other electrical gear for instance, an electrocution could be the result. Again for ABYC compliance, the DC negative and AC safety ground should be common.
On the other hand, from a corrosion perspective, if you do have a DC positive fault to a grounded hull, rest assured, the corrosion is unlikely to persist years, the boat would probably sink long before then, as stray current corrosion is among the most aggressive and fast acting, it will eat a hole in the hull in weeks if not days. The question is, what’s more important, electrocution prevention or corrosion prevention? Having wired a number of steel and alloy boats, good attention to detail and making certain those doing the wiring understand the importance of isolation, and chafe protection, can for the most prevent such faults.
Silver Silver-chloride reference electrodes are available from a wide range of sources, simply Google it. I’ve used on from Mercury Marine for 25 years.
I’m an advocate of aluminum anodes, they are truly a free lunch. Aluminum is amphoteric, however, which means it, a hull, is susceptible to attack from alkaline solutions, which, as you note, are in turn produced by using too much cathodic protection, i.e. too many zincs. It will cause paint failure and it can indeed attack the aluminum, I’ve seen it on several occasions. I’m also a strong advocate of isolation transformers, and consider them a prerequisite on any metal boat. More on these here
http://stevedmarineconsulting.com/wp-content/uploads/2014/03/OV_transformers.pdf
And while I agree that an isolation transformer virtually eliminates the issue of outside corrosion sources, there’s no such thing as a “hot dock” because corrosion is primarily a DC phenomenon, and docks are energized with AC. While possible, AC corrosion is very rare, and requires especially high current. When you plug into a dock, even if your power isn’t on, without isolation from a transformer or galvanic isolator, you are instantly connected to every other boat in the marina, and their associated (DC) electrical/corrosion problems. Blaming the docks, therefore, is laying blame in the wrong place.
Transformers can be wired in such a way that they may not provide isolation and still be correctly wired, these are referred to as polarization transformers, the only difference is the manner in which they are wired. They still offer in water electrocution and other protection, just not isolation, some believe these to be safer from an onboard electrocution hazard perspective. They must be used in conjunction with a galvanic isolator. For metal boats, transformers should be wired in isolation mode.
Your guidance regarding ABYC compliance (which is voluntary for diesel recreational vessels btw in the US) is welcomed and excellent. When I was in college I worked part time for an electrician, all of his vans had a bumper sticker that said, “Wiring is not a hobby, call a professional”. Canada (Transport Canada), Australia/NZ (AS/NZS 3000:2007) and the EU (Recreational Craft Directive and ISO) have mandatory marine electrical standards (Australia’s/NZ’s is among the most stringent I’ve encountered). As an ABYC Certified Electrician and Master Technician, I’m in the position of identifying faults on a near daily basis, either in person or on line, many the result of incompetent professionals or unwitting do it yourselfers. It keeps me up at night.
Charles was one of the few manufacturers making a transformer designed specifically for the marine market, it is UL Marine approved (different than just UL approved) and ABYC compliant. They stopped offering boosting transformers and now only offer a straight transformer. Since then a few others have become available, Atlas, Asea, and Wards, and others, with varying features and cost. The only drawback to a non-boosting transformer is when plugging into 208 (or less), you get 208 and 104 (or less) on the secondary, with the latter being hard on refrigeration and other AC motors. This is a real problem for 120/240 VAC vessels.
Hi Steve,
Lots of good points, but one I need to clarify. I never advocated for isolating the AC from the hull. In fact our AC system neutral and ground are connected to the hull at a single point (on the boat side of the transformer) in compliance with ABYC spec. And further it’s perfectly possible to have the AC system grounded and the DC system floating as we do and be in compliance with ABYC, as we are. (I rewired the AC side to ABYC immediately after I bought the boat.)
The only time I had problems maintaining this was with an inverter-charger where the manufacturer had connected the DC negative and the the AC ground to the case. When I pointed this out they admitted it was a design error and took the unit back for full refund.
All the other equipment that I have installed over the years that has both AC and DC in the same unit (chargers and inverters) keep the DC side floating and not connected to case ground.
As to a hot dock, I’m not sure that’s true. I’m not an electrical engineer, but I’m pretty sure that it’s quite common to have a few volts of DC on the ground or neutral wire. Maybe caused by inductance, although I’m way out of my depth on that one. And of course if the dock has say steel pilings connected them to the hull via the ground wire will cause problems, as will (as you point out) other boats. Anyway, what ever the case, installing an isolation transformer makes all of these issues that many attribute to a “hot dock” go away, and that was my point.
John:
OK, thanks for the clarification, and I see what you are doing.
ABYC, if you choose to comply, does actually mandate a connection between AC safety ground and DC negative. And ABYC E-2, 2.5.10 says, “A metal hull shall be connected directly to the engine negative terminal” i.e. DC ground. This is a stray current prevention requirement. Then add the AC to DC connection requirement and you have a AC/DC bonded hull. Again, you can choose not to do this, it isn’t mandatory, none of ABYC material is, just pointing out the Standards as they are written.
I’m not a ABYC Standards adherent for the sake of compliance. There are some standards with which I disagree, this just doesn’t happen to be one of them. When it comes to electrocution potential I can’t advise others to take chances.
Having said that, and not to belabor this but it is important for any boat owner to understand, metal or FRP hull, there is a good reason for tying the AC and DC grounds together. Any system that is “floating” if energized with 120 VAC, has the potential for electrocution if it is touched along with something that is referenced to the AC ground. This is why ABYC guidelines effectively prohibit floating systems. If an AC fault develops to the DC wiring system (think of AC and DC wires melting together, this isn’t uncommon, it was the source of Kevin Ritz electric shock drowning case), and the two do not share a common ground, it’s possible for you to touch a component in the DC system, which is now energized with AC, and complete the path to the AC source when touching the hull or something connected to it.
I think the risk of corrosion is low if the vessel is wired properly, and is equipped with an isolation transformer. Add a permanent reference electrode/meter and you have full-time monitoring and the risk lowered even further.
It is true, steel bulkheads and pilings, provided they are connected to the shore power ground system, it must be part of a circuit, just being nearby has no effect (bulkheads perhaps, pilings probably not), adjacent to a vessel that’s plugged in to shore power, can create a galvanic corrosion potential. I’ve had experience with this on aluminum stern drives located near steel bulkheads. This is why Mercury Marine, manufacturer of many aluminum stern-drives, was a pioneer in corrosion prevention, introducing one of the early galvanic isolators and impressed current systems.
An iso xfmr would negate the issue of interaction between steel bulkheads/pilings and hull, as would a galvanic isolator. Again, every metal-hull vessel should be equipped with an iso xfmr.
Hi Steve,
I need to look again at the ABYC specs (AAC is a member) when I rewired the boat there was no such requirement (If memory serves) as long as there was an isolation transformer in place. The key is that the AC system (after the transformer) ground and neutral must be grounded to the hull at a single point, and ours are.
Either way, I just can’t see any danger in keeping the DC side floating. In fact, as I think about it could be argued that it would be safer since if you touched a live AC line and say the DC buss (either pos or neg) no current would flow.
And in your example of AC getting into the DC circuits (A concern I share) then the DC system, in effect, becomes an extension of the AC system by definition, so the breaker will blow in cases where it would normally, ditto ground fault interrupters.
Also, as a 26 year aluminium boat owner I have to disagree with you on the level of desirability of an isolated DC system. Several times we have had the isolation compromised and immediately experienced alarmingly fast anode deterioration. And, as I say in the post if it’s a high resistance short this can go on for years on a boat with the DC system grounded to the hull with no way to detect it.
Also, by connecting the engine to the hull, we set up a battery that will be eating away at the anodes 24×7.
To me, if you want to keep an aluminium boat pretty near corrosion free for 26 years, as I have, an isolated system is vital.
As to the steel pilings, that’s what I wrote, the isolation transformer solves the problem.
Can anyone recommend engine mounts that isolate the engine electrically? I checked with the maker of the mounts on my aluminum boat, and they say that the mounts are not designed to do that. The boat is now on the hard and it’s time to replace those mounts and add a flexible shaft coupling, too.
I had an electrician on my boat a couple days ago and he wants to REATTACH everything I have disconnected from the hull back to the hull. He doesn’t like the isolation switch on my engine at all. All of his advice runs counter to everything I want to do to eliminate electrolytic corrosion, but I’m ignorant. I don’t know how to proceed — not that I have much choice because finding techs to work on the boat is nigh impossible (severe shortage of labor here in Vancouver, it seems).
Hi Paul,
The people who make the Aquadrive also sell flexible mounts that will isolate. I don’t know the brand, but that’s where we got them when we re-powered.
And yes, I hear you on the difficulty of finding anyone who understands aluminium boat electrical systems, particularly in North America.
Probably the best way to advance it to let the tech, assuming he is qualified, make sure that the entire AC system is properly installed to ABYC specification and then make sure that the DC system is isolated, as detailed in these posts.
Thanks John. Exactly. I heard from the electrician again and he insists on bonding for ABYC safety standards. This is a guy who crows about building aluminum boats. But he thinks it’s normal to replace zincs ever six months. Good for makers of zincs.
I’m planning to add the flexible shaft coupling, although I worry a tiny bit that it might shift potential electrolysis from shaft to hull. I don’t think I can isolate everything, but my objective is to get there. A tiny worry is that I’ll make things worse; there are no signs of corrosion on my boat, so one is tempted to do nothing. But I got a Seabis and that scares the crap out of me.
Hi Paul,
When you say “bonding” that covers a huge area, so don’t fixate too much on that. The actuality is quite simple: assuming an isolation transformer, the AC system neutral and ground must be connected to the hull at a single point, as per ABYC.
That’s a separate issue from isolation of things like the shaft and keeping the DC system floating.
At this point I would suggest re-reading all three parts of this series since all of this is covered, including why isolating the shaft won’t be a problem.
The point being that if we look at this as one overall problem, it can be very hard to get our arms around, but if we break each part down it get’s a lot easier.
Alas, Aquadrive doesn’t have a dealer in Canada and the Canada yard I’m using says they cannot get these mounts. Does anyone reading this know of an alternative — engine mounts that isolate electrically? Many thanks for any help!
I got my AquaDrive, adapter plates and soft mounts from Mermaid Marine. They are very popular on fishing boats and the “soft” mounts and the CV unit itself have been great at reducing noise and vibration (and, of course, concerns about alignment) on our steel sailboat. I hope this helps.
Thanks again John. Just to be clear, the electrician here (from a very fancy-pants company) wants to violate your Rule 1: “All aluminum boats should have their DC (battery-based) electrical systems isolated from the hull.” He wants the DC system grounded to the hull. After some back and forth he has said he’s willing to not do this, but he doesn’t like it. A lesson for everyone is not to assume that electricians with lots of experience on (commercial) aluminum boats will know how to do it right.
Also, this guy kept saying “galvanic corrosion” for every kind of corrosion. That’s normal among laypersons, but it made me wonder how knowledgeable he is of electrolysis.
Hi Paul,
Yes, you are right to worry. Just because someone can wire a boat, does not mean that they have any understanding of corrosion. I have run into some truly breathtaking ignorance about the subject among marine electricians.
Anyway, in his defence, it is very common in the commercial world to ground the DC system to the hull and live with the resulting anode burn. See #1 in the post above.
If, at the end of this, you just can’t end up with an isolated DC ground system, there is a way to manage with a system grounded to the hull and still catch stray current leaks. It ain’t pretty, but it will work. So if that’s the end game for you, get back to me here and I will share it.
Paul:
The number of professionals in the marine industry who truly understand corrosion, its causes and prevention, and can explain to you what’s occurring, is very small indeed. As my corrosion training prof. used to say, “show me the path the electrons are taking”. If a pro can’t do that, he or she is simply guessing.
You can increase the likelihood of getting someone who knows what he or she is talking about by using only an ABYC Certified Corrosion Technician. You can find them, and confirm those who say they are, on ABYC’s website, http://www.abycinc.org
Among corrosion professionals, and within ABYC circles, the word “electrolysis” is frowned upon (whenever a claimed corrosion pro uses it, it immediately catches my attention, because most corrosion training programs and respected texts discourage its use), as it does not accurately describe the corrosion process. Here’s what ABYC has to say about on the subject, “Electrolysis – The breakdown of an electrolyte resulting from current flowing in an electrochemical cell that includes that electrolyte. Example: the breakdown of water into hydrogen and oxygen gases in a supplied-current electrochemical cell. ‘Electrolysis’ is often used loosely to describe corrosion in general, or the operation of supplied-current cells in particular. Its use in this respect is often confusing, and should be discouraged.” Corrosion specialists jokingly say “Electrolysis has more to do with hair removal than corrosion”
Connecting the hull to the DC negative, and AC safety ground is mandated for those wishing to comply with ABYC Standards, so it’s not surprising that the electrician insisted on this. While there are other schools of thought that John has detailed, according to these widely-accepted ABYC guidelines, all be they voluntary, that is the “right” way to do it.
The two primary (but not only) types of corrosion we encounter in the boat small boat marine industry are galvanic and stray current. The former occurs between dissimilar metals, the latter is the result of a current “leak”, most often DC, into bilge water or the water in which the vessel floats, or both. Aluminum is also susceptible to poultice corrosion. If he was referring to the type of corrosion that is mitigated with anodes, then that is galvanic. Either can be affected by the various hull grounding/isolation techniques. Don’t get me wrong, I’m not defending this tech, I have no idea if he knew what he was talking about, I’m simply defining the terminology and practices.
I recently wrote this article http://stevedmarineconsulting.com/wp-content/uploads/2014/03/Corrosion-CRWHS18_HOS4_FINAL.pdf in an attempt to concisely explain these two common types of corrosion, and in the hope of dispelling many of the myths and urban legends swirling around them. And this one to explain aluminum corrosion scenarios specifically http://stevedmarineconsulting.com/wp-content/uploads/2014/03/Aluminum-Corrosion-Cruising-World-May-2017.pdf
If someone puts forth a theory about a corrosion scenario aboard your vessel, ask him or her to draw you a picture, literally, tracing the electron path. If that person cannot do this, then yes, you should be suspect.
Hi Steve,
Thanks for shining a light on all of that. I really liked your last sentence, and totally agree. The first thing I do whenever I’m thinking about anything electrical is draw out the current flow. If I can’t come up with a sensible simple diagram I know I have more work to do before I understand what’s going on.
As to connecting the DC system negative to the hull, while I agree that an aluminium boat can be so wired, as I explain in the post above, doing so makes it impossible to easily catch low current leaks that don’t trip a breaker, so I prefer a floating DC (not AC) system. As to which approach is always right, I do need to point out that a floating DC system, with some sort of short-to-hull measuring device, is pretty much standard in Europe, where there are far more aluminium boats built than in North America.
Also, back in the day when more aluminium boats were being built in North America (70s-80s) a floating DC system was also the standard. (I have an old paper in my files from Jim McCurdy on the subject.)
Just to be clear to others, nothing in the above should be misunderstood as advocating for a floating AC system. All AC systems should be wired to applicable standards (ABYC does a great job of defining them) including being properly grounded to the hull.
John:
Understood on all counts, and you’ve made your reasoning for a floating DC ground clear. As an aside, as a young mechanic/electrician, I used to regularly work on Jim McCurdy’s boat in Oyster Bay. It had two battery switches, one for positive and one for negative…
Also, on the subject of compliance, your clarification is appreciated, however, for the AC system to be ABYC compliant, its safety ground must be common with the DC negative, and hence the hull, so for those who don’t wish to do this, direction to professionals is necessary. I’m not debating the floating ground issue with you, I understand your reasoning and you’ve made its advantages clear, just pointing out how the Standards approach this issue.
It would be helpful for those taking the floating ground approach you advocate, if you wrote a brief summary on how and why this is done, one that could be shared with electricians carrying out work aboard these vessels.
Hi Steve,
Yes, it’s a complicated issue and I can certainly see and appreciate your position: just comply with the standards and be done with it. A much easier approach than mine.
As to writing a spec on how to have a floating ground boat, I would be the first to admit that’s beyond my capabilities since I would, in effect, be setting myself up as a standards institute of some type. Way beyond my pay grade.
What I will try and find time to do is have a detailed look at ABYC (AAC is a member) and see if I can find out what the Europeans have to say on the subject since so many European boats are floating DC ground.
I guess my base concern is this. Since so few aluminium boats are now built in North America, I really wonder if the powers that be at ABYC have given this issue any real thought or analysis. Maybe it’s just an attempt at a one size fits all solution. And if that were true, and given that floating DC ground is pretty standard among European aluminium boat builders, that calls the whole thing into question.
Hi John & Steve,
I have read your comments on floating or Isolated DC system with lots of interest.
Maybe a silly thought but in order not to compromise on safety, why not connecting the DC ground via a galvanic isolator to the vessel’s AC safety ground? In that way it’s blocking up to 1.4V DC but allows AC fault current directly to the AC’s safety ground wich is also connected with the hull.
Regards,
Kors
Hi Kors,
Interesting idea, but galvanic isolators are just that, they only work at the currents induced by dissimilar metals in salt water. They do not stop stray current corrosion, which is the reason for isolating the DC system. That said, maybe in combination with a stray current indicator. Hum, I would have to think about it and ultimately test it in real life to know.
The electrician I got really wants to ground DC to hull. Takeaway: follow John’s advice to be wary of electricians.
Does anyone know if the VDO device John recommends is essentially doing the same thing as the “Seabis” device? I’m guessing that the latter is just a fancier version of the former (and more frightening, with lots of colored lights labelled “critical” and so forth).
Thanks John.
Do you know if the VDO device you recommend is doing more or less the same as “Seabis”?
Hi Paul,
Yes, pretty much exactly.
It looks like the VDO leak tester is no longer available. Is there any alternative, other than SeaBis?
Hi Ann,
That’s bad news. I just spent half an hour searching for an alternative, but no luck. So I guess it’s the SeaBis. I have written to TyBoat to see if they know of a replacement and will revert if I get an answer.
Hi Anne,
Just heard back from TYBoat and they confirm that the gauge is no longer available.
Another option to SeaBis is to make your own out of a couple of small LED bulbs, as I used to do before the VDO gauge was available. See if you can get ones that draw about 20 milliamps.
Hi Ann,
Just heard back from TYBOAT. They have an alternative that looks good to me: https://www.tyboat.com/achat/P-6396-dolphin_testeur-de-fuite-electronique-octopus-leakage-bargraph-pf3-leak-pour-bateau-metallique-12-24v.html
Thanks so much! I have ordered one…
Hi Ann,
Great, please let us know how it works out.
Has anyone tried the corrosion reference electrode from boatzincs.com (http://www.boatzincs.com/corrosion-reference-electrode-specs.html)?
Yes, I bought one about a year ago. I have not compared it to another reference anode but it does give readings about as expected. Parts of the booklet it comes with are also useful.
John:
I’d chat with the folks at ABYC before you jump to the conclusion regarding their take on, and experience with, metal boats. Some very savvy folks sit on the Electrical Standards Project Technical Committee. In fact, I’d suggest you speak with Capt. Dave Rifkin, I can put you in touch with him if you like.
Have you been to Seattle/Pacific Northwest lately, alloy boats everywhere, and there are several manufacturers in the US building small aluminum craft for military, police, Coast Guard etc. Of those I inspect, and I inspected one last week that belongs to NOAA, most at least claim ABYC compliance, i.e. a common ground.
Again, you have a system that works, and it’s embraced by some alloy boat builders, more in EU than NA. It’s worth pointing out that the EU approach is taken with FRP as well as alloy vessels, so it’s not specific to metal boats.
Bottom line, ABYC mandates a common ground primarily for electrocution prevention, if everything is at the same potential, it makes it difficult for a person to complete the path.
Hi Steve,
I’m certainly not suggesting that the folks at ABYC are anything other than extremely smart, nor am I jumping to concussions. All I’m suggesting is there just might be other ways to do things on aluminium boats. And perhaps ABYC has not put a huge amount of resource into thinking about that. Not an unreasonable position given that floating DC seems to be pretty standard in Europe and I’m sure ABYC has a ton of stuff on their plates at any given time.
As to the number of aluminium boats out west, yes, I’m aware of that (just got back from BC) but, as you say, most are commercial and therefore in some way classed or at least subject to regulation, and therefore are going to be required, or at least strongly encouraged, to go 100% ABYC, so I don’t think that proves much.
Anyway, I’m certainly not qualified to in any way adjudicate between European ways of doing things and ABYC, so I won’t be going down that road.
Enough of that.
I think it would be more useful for you and I to explore the actual dangers of a floating DC system, rather than argue about whether or not going the ABYC or the European way is best.
To that end, let me start of by saying that I’m perfectly willing to believe that there may be dangers in the European way (floating DC) that I have not thought of—I’m a long way from infallible!
So in thinking about it, assuming that the AC system is properly grounded as per ABYC, and assuming an isolation transformer, I think I’m right in saying that the only thing we need to worry about is places where AC and DC intermingle, mostly battery chargers.
Given that, let’s assume that some how the hot AC gets attached to positive side of the DC system.
Thinks and doodles on piece of paper…with a grounded DC system, there’s going to be a hell of a bang, and maybe some flames, when a bunch of low resistance DC loads (including the secondary windings in the charger) pass all that AC current to ground, and then the AC breaker feeding the charger blows as long as the DC loads don’t fry first. All good, and a win for grounding the DC side, except maybe fire risk.
Let’s see…If the DC System is not grounded then I think—here’s I’m not as sure as above, more variables and I’m no expert on transformers—the secondary winding in the charger still tries to pass all the AC and fries, and/or the AC breaker goes (same result).
Now let’s assume that I’m wrong about that (because I’m not at all sure of myself on that one) and the secondly winding does not pass a lot of current and trip the breaker.
Then we have a dangerous problem, because the entire DC system is energized and anyone who touches it and the hull is in big trouble.
OK, given all that, I think we can provide the same safety as grounding the DC, simply by making sure we have capacitors connected between the DC negative and the boat hull, as most all floating ground boats have, since said capacitor will either blow with a hell of a bang, or pass enough current to blow the breaker feeding the charger.
Assuming I have all this right then it would seem that what we need to do is make sure that all floating ground DC systems include a capacitor of the right size to pass enough AC current to ground to blow the largest AC breaker on the boat—the best of both worlds.
Thoughts?
Assuming I have not goofed on this, I might write a post on this idea and see what the engineers that comment here have to say. And, if they don’t blow me out of the water, I will then modify the tips in these chapters to highlight the dangers and what to do about them: either comply with ABYC or install a capacitor as above.
John:
It’s a worthy topic to be sure.
The small aluminum boats to which I referred are not classed per se, however, many of the agencies ordering them do mandate ABYC compliance. Not all end up fully compliant, however.
I’m currently working on an inspection project in Australia, however, once I have free time I’ll review in detail the material in your post.
John:
I have a wx delay here so some time to respond to this.
Simply put the crux of the floating DC ground approach means if AC hot comes into contact with a chassis that is only bonded to DC ground, and not the hull, an engine or genset block for instance, it’s energized, you touch it and the hull and you complete the path to the source, and get shocked, and maybe killed if no GFCI is present. This is why ABYC guidelines call for a common ground system, electrocution prevention.
Also, you must think about the required B/C grounding requirements (both AC and DC grounds connected to case of metallic chargers, failing to do this means the chassis can be come energized and not trip a fuse or breaker). This is in fact the way many boats unintentionally or unknowingly comply with the AC-DC grounding requirement.
You and others can choose not to do this for corrosion prevention reasons, I’m not debating that, I’m simply saying it’s not without risk.
Hi Steve,
Thanks for coming up on that. I hear you on the situation if the AC hot connects to any part of the DC system or an isolated metal object like the engine. And that’s why I’m putting considerable time and effort into this. After all there are 1000s of boats out there with both AC and floating DC systems, so it seems worth my time. That said, I think that just saying “wire to ABYC” is not actually going to solve anything. People will just shrug and go about their business without a clear to a lay person explanation of the dangers and a relatively easy suggestion to ameliorate them.
Right now I’m looking at using a capacitor that will pass enough AC current to blow the breaker, but still maintain the DC isolation. Preliminary work says 1000 micrfarads should do it, but I need an engineer to verify that since I was trained to fix electronics not design electrical circuits. My other thought is what might be done with GFIs. And I’m also thinking about the corrosion implications of going fully grounded as well.
Once I get all this sorted out in my head, I will post about it.
On chargers and inverters I have always been able (with one exception, see below), and always have, connected their cases to the hull (common ground) without compromising the floating DC side. Point being that in all the cases I have come across (ouch, bad pun) the chassis of these devices are not connected to the DC negative.
That said, I did come across one inverter unit some years ago where the DC neg was connected to the AC ground. When I checked with the company (Xantrex) their engineering people admitted this was a design fault and took the unit back for a full refund.
Point being, there is no need to float the case of most inverters or chargers to maintain a floating DC system.
Hi John,
I found a handy online calculator for capacitators (https://www.elektronik-labor.de/OnlineRechner/Kapazitaet.html albeit german, scroll down to “Kapazität berechnen”). 1000 µF would allow for 2.4(4.8)A to pass at 120(240)V, and I doubt that a breaker would trip at this amperage. If my calculations (read input into said online calculator) are somehow correct you would need 2080µF for 240V (4160µF for 120V) to allow currents up to 10A.
I found Elcos from Jianghai up to 1000µF, so you could put them in parallel to allow for sufficient current in case of an AC to DC leak.
What I am wondering however is how would the DC wires react to such a shortage – they most probably would not be sized for this power.
Hi Ernest,
That’s interesting but the problem is choosing the input variables. For example, the ones you have used would be correct if we wwre trying to get rid of 50hz ripple. But that’s not typically a problem, assuming that we have a good quality charger and inverter which will both have capacitors and coils inside them to do just that.
For our purposes as discussed in the post above we are going to be much more interested in frequencies in the khz and mhz range reing radiated by things like SSB radios and digital electronics as well as switching transients.
So that leaves the question of using a capacitor to pass enough current to blow a breaker in the event of a leak from the AC side to the DC, but as you say, a capacitor to do that would have to be huge. Also given that CE ISO standards are perfectly happy to have the DC side floating I really wonder if we even need to worry about this. Don’t know for sure.
As far as I am concerned (and I’m by no means a professional electrician) my main concern for the above mentioned scenario – AC hot faulty connects to DC positive on a non-floating DC system) would be the power that would tranverse the DC cables until the shortage gets abandoned by the breaker. These wires would by no means be sized to carry that wattage so I believe danger of fire would be eminent.
Hi Ernest,
Actually DC cables tend to be heavier than their AC counterparts because they carry a larger number of amps for a given number of watts so I can’t see that being a problem.
I’m in BC now and right in the middle of having electrical work done on my boat. I’m getting massive blowback from electricians about wanting to isolate DC and the engine. It’s not just about safety/ABYC standards; they insist that doing this will actually increasing damage from electrolysis/stray current. I’m going completely insane. I’m really starting to doubt the wisdom of all the advice to isolate, and I’m worried that I’m actually making my boat more likely to suffer corrosion. I just don’t know what to do and whatever I do has to be done now now now while the boat is on the hard.
Hi Paul,
I’m actually in the process of revisiting the whole issue, see my comment thread with Steve D. I’m a long way from having this figured out, but there is no question that there are some dangers to isolating the DC system. That said, let’s not forget that isolated systems are pretty much the standard on aluminium boats in Europe.
One thing I am sure of is that the idea that an isolated DC system would increase corrosion is wrong. What we are guarding against by isolating is stray current corrosion and if the system is truly isolated then by definition no current can flow. If anyone tells you different, challenge them, as Steve D suggests, to draw you a diagram showing how the current will flow from the battery, through the hull and water, and back to the battery. (One of the biggest mythes in electricity is that current flows to ground, it doesn’t, for electricity to flow their must be a circuit back to the source, in this case the battery.)
Also, we have had an isolated ground system on our boat for thirty years and have no evidence of stray current corrosion.
All that said, as I said in a previous comment, going fully grounded is a viable option, and maybe that’s the best bet for you given the situation. If you do go that way, make sure to buy and use a good meter and silver chloride anode as detailed in this series, and pay particular attention to the state of your anodes.
Hi John,
Keep up the great articles. They are helping us enormously with the build of our aluminium catamaran. With some difficulties we managed to secure a VDO leakage test instrument through Kent Marine but no instructions were supplied as to exactly where to fit it. Could you perhaps please shed some light on this?
Hi Euan,
I have emailed you the instructions I have.
So a question about the Ovni rudder anodes. The previous owner of the boat has installed the round rudder anodes on a length of stainless threaded rod through a hole in the rudder – one on each side. The anodes sit on top of the primer and antifoul. Can anyone tell me if this is how Ovni rudder anodes should be fitted? Seems to me they should make contact with the metal of the rudder by scraping back the antifoul and primer to bare metal where the anode sits. Can anyone with an Ovni shed any light on this and how it should be done?
Thanks
Hi Charles,
I agree with Steve.
And further, see tips #4, #17, #22 in the series starting with the chapter above.
The brand of the vessel aside, no anode works if it does not have a very (no more than one ohm) resistance connection to the object it’s protecting, the cathode, the rudder in this case. You can check this with an ohm meter, while hauled out. If the anode and rod are installed over a painted surface, that’s problematic. Typically, in the case of a metal boat, the stud to which an anode is attached is either welded (for steel) or fastened (for aluminum) to the hull. Again, the connection must be very low resistance. If anything, the rod should make good electrical contact with the rudder, or the surface over which the anode is placed must be clean, free of paint and bright metal when the anode is installed. Never use a wire brush, even if it’s stainless steel, to clean anode connection surfaces, always use non-metallic abrasives such as ScotchBrite pads.
Thanks guys much appreciated