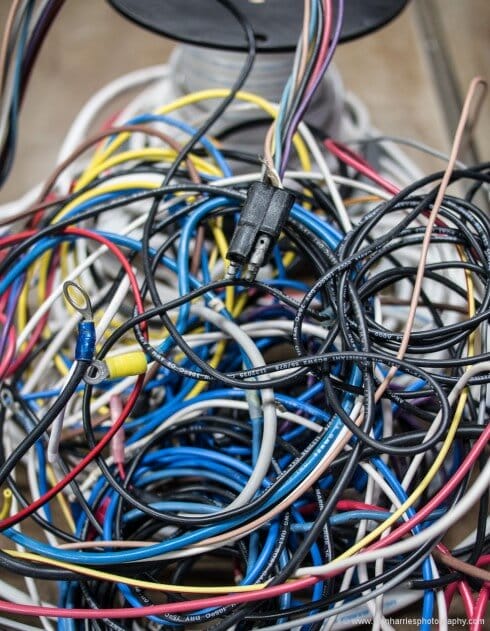
Modern yachts have a lot of wiring, as any owner who’s worked on one knows. Wiring harnesses are heavy, and they take a lot of time and effort to install. They represent a substantial material and labour cost to a builder and, on a production line, that expense can really add up.
A different approach to wiring, one that is rapidly gaining traction among builders, is a “distributed power” system. Distributed power is very different from the conventional approach, and while it does have many advantages, there are conditions that must be met—and that no system I’m aware of currently meets—before I would be comfortable recommending distributed power for a cruising boat.
A new systems architecture
Most readers are likely familiar with the electrical system architecture that’s found on most small to mid-size boats. You start with a battery bank. On one side are the charging systems—the alternator, wind turbine, water turbine or solar array. On the other side is a massive, heavy cable run to an enormous main breaker panel (or a handful of smaller panels) and bus bar. From the breaker panel and bus bar, a pair of wires are routed to each individual electrical consumer on the boat.
In a distributed system, there is no master breaker panel. Pairs of medium-gauge cables are routed from the main positive and negative buses near the battery to many small switching nodes, strategically placed throughout the boat. Each node controls a handful of circuits, with very short individual wiring runs, to power the equipment in its vicinity.
These nodes are remarkably capable devices. They communicate over a common data bus, to which command and monitoring devices are also connected. Over-current protection is electronic, and can be programmed independently for each individual branch circuit. Individual devices are controlled by sending digital commands on the data bus, which are received and acted upon by the appropriate node.
This leads to some very convenient new capabilities. For example, a single button marked “Sail – Night” will set the masthead light to red-green-white, turn off the cabin white lights, turn on the cabin and instrument red lights, and switch off the steaming light. Pressing the “Anchored – Away” button will shut off everything except for the bilge pumps, high-water alarm, dragging alarm, and white all-round light. Every circuit has its own ammeter and voltmeter, the readings from which can be used in automated power drain and time remaining calculations. It’s even possible for the controller to automatically shut off heavy loads such as water heaters and refrigerators when the generator, inverter or shore-power connection is at risk of being overloaded.
Less wire to pull = Happy builders
To help illustrate why distributed power is so appealing to builders, I’ll use the Starwind 860 trimaran that Katy and I are currently building as an example. The boat’s outriggers are each divided into three watertight storage compartments, each with its own bilge pump. We also have a courtesy light by the boarding gate, and a trolling motor on each transom for poking around in shallow areas where the main engine would be overkill. That makes a total of one ~40 amp and four light duty circuits in the outrigger.
In the “standard” configuration, there’s a switch/breaker panel at the helm, fed by a heavy cable from the batteries, and individual wiring runs to each pump and to the courtesy lights. The trolling motor’s high-current cables are run through breakers at the stern, directly to the battery bay. Its control harness is routed to the helm. We can map out these circuits and calculate the total amount of cable needed.
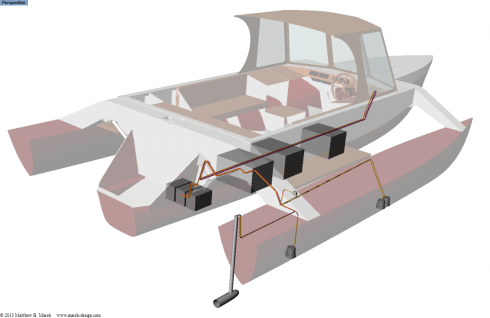
The total: 12.7 m of heavy cable (~4 AWG), 38 m of light cable (~10 AWG), and 7.8 m of control cable. And that’s with a wood-composite hull where we can easily share much of the negative wiring; a metal hull would call for a bit more cable because of the need to use double-pole breakers.
Now, we’ll calculate the cable lengths for the same devices connected to one distributed power node placed where the main bundle enters the outrigger.
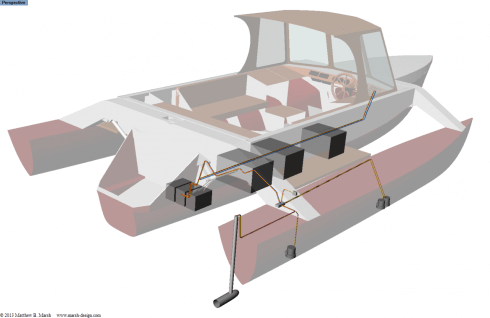
The total: 7.7 m of heavy cable (~4 AWG), 23 m of light cable (~10 AWG), and 14 m of control cable. By using distributed power in this application, we can get by with only 60% as much power cabling, and—even after adding the extra control harness—we’ve reduced the total amount of wiring to fish through the boat’s conduits by 13 m. Furthermore, we no longer have to buy individual breakers (at $25 to $50 each, they really add up) or find room for a gigantic panel to hold them.
Here’s another view of the two systems. The distributed version is on the left; the conventional on the right. The cable routing is roughly the same, but there’s twice as much wire in the bundle for the conventional system. The difference becomes more dramatic as you add more circuits: the distributed system can feed perhaps a dozen different circuits from a node that has only three cables going to it, while the conventional system’s bundle will grow thicker with every extra device.
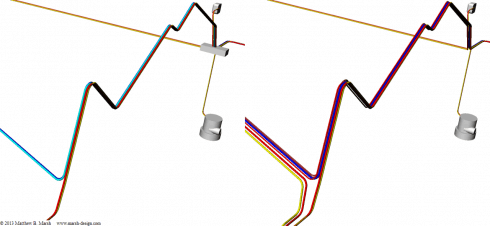
It should come as no surprise, then, that the aviation industry has been using distributed power for several decades. The ’60s-era Boeing 747 has over 217 km of wiring harnesses; hauling that kind of weight around brings measurable costs in fuel burn and performance.
There’s gotta be a catch…
Or, more accurately, several catches.
One is that, while distributed power is great when it works, and is very reliable when it’s new, the systems are harder to troubleshoot than a conventional system. When conventional wiring goes wonky, you grab a voltmeter and start working your way back from the load until you find power. That usually isolates the fault. With a distributed system, all the interesting stuff is packed into one little sealed computerized box. It can be hard to tell whether the problem is a node hardware fault, a command bus fault, a command panel fault, or an incorrect digital command.
Another is that the marine versions of these systems, being relatively new and relatively high-tech, are redesigned periodically. Spare parts may be easy to find now, but whether you’ll be able to find compatible nodes in fifteen or twenty years is a salient question.
Criteria to meet
Before I’d be willing to recommend a distributed power system for a cruising vessel, I’d want a few assurances:
Documentation
The owner and any technicians he/she hires must have open access to the complete specifications of the system. This includes the entire communications stack, from the physical and electrical details of the digital control bus to the data encoding protocol, the binary message format, detailed troubleshooting flowcharts, and the software needed to program the nodes. If any of this information is proprietary, dealer-only or pay-to-play, it’s a pretty safe bet that the system will be impossible to troubleshoot in an out-of-the-way location.
My first test when evaluating a distributed power system, then, is to go to the manufacturer’s website and try to download the support documentation. If it’s not readily available for download or freely emailed on request, that manufacturer loses the sale.
Spare parts
If I am going to recommend that a client invest thousands, or tens of thousands, of dollars in a single-vendor system, I want some assurance that replacement parts will be available down the road. I think it’s quite reasonable to require a 20 to 25 year commitment to provide replacement nodes, control modules and other single-supplier parts at a fair price. (This doesn’t necessarily mean a 25 year warranty, but rather a 25 year contractual obligation to make spare parts available, quickly and without obscene markups.)
Do any vendors pass?
Here’s what, in my opinion, is really hindering the adoption of distributed power: I’m not sure that any vendors in the marine sector are willing to meet both of those criteria.
I like the concept. The basis of the technology is sound and well-proven, and has proven to be reliable in the aerospace world. However, cruising boats live a long, hard life, and complete refits every five or ten years just aren’t acceptable. Without some hard assurances that I (or a technician in a remote area) will be able to troubleshoot, repair and re-program the system when things start to fail, I can’t recommend distributed power systems to anyone who’s going beyond reach of help.
If you are a vendor of such systems, or if you’re using one, please chime in below. I’m particularly interested in hearing from vendors who are willing to back their marketing departments’ promises of reliability with similar commitments from their intellectual property and logistics departments.
thanks for this fascinating glimpse into the future…was not aware of these developments till now…confirms my continuing view of the fine positive value of this site…christmas is closing in, and i have you on my list for an appropriate cash gift that you have already reciprocated…thanks again
I like the concept as well. One disadvantage might be that if a ‘feeder cable’ to one of the nodes fails, it will take down not one but several pieces of (critical) equipment on board.
Pre-installing a spare cable to overcome this ‘single point of failure’ risk might be fairly easy, but reduces the simplicity of the system a bit.
Don’t know if there are any failure statistics available of distributed systems already installed in a marine environment?
Failure statistics: No, and I doubt there will ever be any that would be statistically meaningful. Too many vendors, too many unique applications, no systematic way to report or track faults between different suppliers.
The feeder cables to the nodes aren’t much of a worry. They’re just standard two-conductor wire, fused at the bus bar near the battery. It’s pretty easy to tell if they’ve gone bad; just put a voltmeter across them at the node in question. It’s the node itself that would be hard to troubleshoot.
Yes, the feeder cables are easy to troubleshoot and not very prone to failure. But if it happens in heavy weather or during crossing a busy shipping lane and several critical systems on the same node go down together you might not have the option to repair on the spot. In a traditional system just a single system goes down, which seems to be an advantage. This is no indication of the overall safety of the distributed power system.
A vender may give a quarter century promise, but,will they be in business?
Vendor commitment will be driven by economics, which is dependent on market acceptance. Enno’s post (below) suggests a vendor centric implementation scenario which I doubt will be sustainable in the long run. As with all emerging technologies, the early adopters will be those with the financial resources to take risks; after time specific products will emerge that prove robust and cost-effective enough for the mainstream. We’ve seen this pattern with things like electronic charting and related navigation systems. Give it 10 years, and distributed power will be relatively commonplace.
Matt,
Excellent article. I played with the idea but decided against it.
I can see the advantage for a B777, B747 or a space shuttle, I think a sailboat is too complex (maintenance costs vs operation) a machine for such a system. Keep it simple and generic is my ultimate goal. I’m crazy for everything technical, mechanical but I realize a sailboat has to stay technically friendly or otherwise it becomes evil in no time. I’m already the slave of the Engine God, the Battery God, the GPS God, etc. I don’t need another one.
Last spring I was playing with the idea to convert my Simrad NMEA 1083 to the Simnet system (NMEA 2000) replacing everything with new Autopilot, broadband RADAR, AIS, Compass, wifi; the whole thing. Simrad refused to answer my questions and wanted to charge me a consulting fee; I decided to stick to what I have and only add a wifi multiplexer for a tablet in the cockpit (I don’t have any gadget in the cockpit besides basic sailing instruments and paper charts).
Better to “own” the technology; I can get rid of it and it will not change anything in my life, if the technology is available it makes my life easier or funnier, that’s OK. But if I feel that missing my electronics, or my electric in a middle of an Atlantic passage is a catastrophe than I should rethink the whole approach.
My experience is that I should be able to fix everything on my vessel, everything should be accessible and replaceable. For the essentials, no “black box” is acceptable.
I enjoyed your article!
Matt, I have to agree with Patrice here that while this makes a lot of sense, the “robustness” of certain elements is not proven, and that it is the skipper, and not a head office tech, who is going to be tracing faults in some exotic locale.
In our refit, I like the idea of sub-panels/zones, where you run from the main panel in the center of the boat/near the batteries and engine (in our case, a pilothouse) to a smaller switched panel that will involve short, modest amperages and runs, like “galley” or “workshop”. This can aid in tracing faults or in isolating problems without shutting the entirety of the DC system down.
I find the distributed power concept attractive, nonetheless, but it’s a little in the same league as proprietary device integration (CANBUS, NMEA 2000, Seatalk). I prefer discrete devices that can optionally integrate to a PC-based “plotter”. Similarly to Patrice again, I have no desire for “convenience” that requires a consultant. Discussions with people stuck in foreign ports awaiting some module or overworked local tech to arrive have strongly influenced my thinking on this, as have the writings from “The Marine Installer’s Rant” and some other horror writings.
Mark, Patrice:
I tend to agree; the person ultimately responsible for fixing this stuff is either the skipper or a local tech he’s hired to help out. That’s why I would automatically reject any system for which I can’t freely obtain all the technical data and troubleshooting manuals. Flying in a manufacturer’s technician, when they’re in Europe and you’re in the Philippines, is just not cool.
If the interior layout permits it, I do prefer having several small panels instead of one gigantic one. They’re easier to figure out when you’re in a hurry. And this approach- like the distributed systems- can let you use a couple of 4-6 gauge cables for a run that, with a single big panel, would have a dozen or more 10-12 gauge cables.
Hi All,
If I were doing a boat from scratch, that is definitely how I would do it: Several subsidiary panels throughout the boat. Each would have a couple of spare breakers too.
Matt/John:
We are in agreement here, and Matt, your “semi-distributed” layout is how I’m doing things. John, your “couple of extra breakers” notion is already in play…when I put in an AIS and radar, the breakers are already there.
One of the upsides of having a custom-built steel boat is that one frequently has access “behind the scenes” that is denied (or not designed for) in production boats, where there seems to be a touch of denial about the eventual need to fish conduit without calling in a contortionist. Of course, the downside is that you end up with a 41 footer (in my case) with the internal “living space” of a 36-37 footer, but to us, that’s a small price to pay for the ease of use immediate and skipper-friendly access to critical systems provides.
Hello Matt, Mark, Patrice,
picking up on this earlier thread I’d be interested to know what would be a good way of organizing the subpanels. Would this be i.e. by area (forepeak, center cabin, engine room, …), or rather by function (lights, pumps, …), or another system?
Thanks, Phil
Hi Philippe,
The idea is to organize the sub panels by location, not function. So, for example, the forward cabin would have one heavy duel conductor run to it from the main panel that would be protected by a breaker on the main panel marked fore-cabin and sized for the full load of all fore-cabin circuits. Then in the fore-cabin there would be another smaller breaker panel feeding all the loads in the area with a properly sized breaker for each.
There are many benefits to this including easier trouble shooting, less wire, and ease of adding a load (as long as spare breakers are provided on the sub-panels). I have done some of this over the years on our boat, and if doing a boat from scratch I would go 100% this way.
Hello John, thank you for the clarification.
So would you run a one feed to the galley and then at the galley have a panel with control for Fridge, Gas sensor, Gas solenoid, Galley light ?
Hi Traas,
Yes, that’s what I would do if doing a boat from scratch. That said, I would also make sure that all was compliant with ABYC and I have not checked this architecture against their requirements.
It can get even worse!
Hallberg-Rassy is selling their newer boats with an EmpirBus system. This system is password locked. Initially they claimed that the owner gets the password after the warranty period runs out. When I asked them after 2 years they had changed their policy and now the owner never gets access to the electrical distribution system. Essentially this prevents any upgrades or new installments of electrical equipment. Of course one can order changes in the configuration for a hefty fee ( a few mouse clicks work). The only way to get out of this horrible situation is to change all nodes which is about €1000 per node.
I can only recommend to stay away from both Hallberg-Rassy and EmpirBus.
A password locked electrical bus? Is someone trying to prevent repeat customers?
Enno,
You’re absolutely right. I think that any technology should be “owned” by the end user (especially when the end user paid for it). I heard the same about Hallberg-Rassy horror story; couldn’t turn on anything on the boat and no technician around . . . The once proud and arrogant new owner was very quiet . . . But again if you’re ready to pay 600,00 euros for a boat with plastic sole then you’re ready to accept anything.
Anyway I believe that such a system is pure madness and is reminiscent of our times; where there is always someone who believes that you should be monitored or/and controlled. Simrad’s policy (at least in Europe) is that technicians should install Simrad products and maintain them; not the owner. We’re far from the time when sailing meant freedom . . .
Great article, thanks Matt.
I would also be concerned about the potential of a lightening strike or other shoreside electrical spike taking out
Great article, thanks Matt.
I would also be concerned about the potential of a lightening strike or other shoreside electrical spike taking out the control system and thus cutting the juice
Lightning is a valid concern. I would, however, suspect that a strike that can take out the distribution nodes would also take out the engine controller, the instruments, the autopilot head, and just about anything else that has electronic components.
I figure if lightning hits, every electrical device on the boat will be dead, regardless of how it’s connected. And I would plan my emergency procedures around that assumption. Anything that survives would be a bonus.
Matt, Nice article. I have looked at these systems for over 10 years now and think they are brilliant in most respects. I believe at least one UK sailboat manufacturer is going this direction on his boats and has been for a couple years now. I think of this system as a 3 wire system, DC pos & neg and an information wire, but there are variations. It has so many elements that would make life easier and more efficient. I would use this system like a shot if I were to do a boat from scratch with the caveat that mission critical elements have conventionally wired back-ups which should not be a big deal design or execution-wise.
Thanks, Dick Stevenson, s/v Alchemy
PS. Didn’t Nigel Calder build one of his Malos to this electrical design?
Yes, Dick, I believe he did in both his “Nada” and “HYMAR” projects with his Malo 46.
It took thousands and ages and despite Calder’s skill and initial enthusiasms, I got the impression, insofar as I paid attention to the progress, that his results were a bit equivocal.
The solution could well be a standardised, open communications protocol that is widely used. Should a switch node from manufacturer X die and no longer be available, then one can be found from manufacturer Y. As the technology becomes old hat some enterprising electronics engineers will build the little boxes required to keep it all going, much as happened with NMEA 0183.
Incidentally, EmpirBus looks like a NMEA 2000 controlled breaker board. The DCM11, which module does the switching, has battery terminals and 16 12v outputs, which then go out to fused distribution blocks. So it does not actually look like a proper distributed power system in the way Matt describes.
I’m in the process of replacing a rat’s nest with circuit breakers, each attached to a DIN terminal paired with a ground DIN terminal, so the power and ground can be brought in still in their outer sleeve and tailed in together. Should help traceability and allow both ground and power to be easily lifted, from a given feed, if grounding problems present.
Jamie,
You’re right, a standardized protocol (NMEA2000) is the way to go. Even if the message syntax is different between vendors, it can be reverse-engineered (by passively monitoring the bus) if a 3rd party sees a market for interoperability products.
EmpirBus is a true distributed system, like I described here and like the aviation industry is using. DCM nodes have internal monitoring, overcurrent protection, etc., you can connect individual devices directly to them without fuse blocks. (I would suggest you should still fuse the feeder cable where it leaves the bus at the main battery.) It looks like their nodes can also serve as analog-to-N2K sensor interfaces measuring voltage, current or resistance.
I will ask EmpirBus if they would like to chime in here.
Am I the first to chime in with experience owning one of these systems?
Our Southerly 49 has an Empirbus system model CLC installed 4 years ago when the boat was built. The system is not “locked” and I have added numerous devices to the boat and modified the system many times. I like the ability to add items with very little wiring. When I added an anchor washdown pump it just needed a short wire run up forward and I programmed a switch on the main panel to turn it on/off. Then later I realized I should have put the switch at the helm. But this was just a 5 minute programming change and bingo the switch was installed. Modifications are using a PC to talk to it, but I think new systems come with a configuration panel built in.
I do agree it is a concern about parts in the future so will keep an eye on things and buy a few more spares in a year or two.
Fair Winds,
Paul Shard
SV Distant Shores II
Paul,
Thanks for sharing your real-world experience with the Empirbus system. User stories are a heck of a lot more helpful than marketing literature.
I note that the Empirbus NXT system has replaced their CLC system, but the parts and documentation for the latter are still available 11 years after its introduction. That is promising.
Empirbus uses NMEA2000, a variant of CAN, for which diagnostic and reverse-engineering tools are fairly easy to find. That increases the odds that a non-vendor technician will be able to see what the thing’s doing, as well as the odds that third parties will eventually be able to interoperate with it.
Matt, Absolutely agree about the breadth of damage in a lightning strike. And the need to anticipate this event. I believe many of the worries in this area diminish if it is true, as I understand it, that these systems have been used successfully in automotive areas and airlines for more than a decade now. That and having a conventional wire system for critical systems backup.
Dick
Hi Matt, this object is very interesting. As a hobby I have sailed recently new built motor ships from Holland to Norway. They have all been loaded with new, modern digital systems as you describe it. When they do not work in The English channel it is terrible. I have twice lost radar, VHF, compass, AIS, autopilot and main engine. Many modern engines are also controlled by computers to day. This is so stressing that I will never do it again. To reset such a system you need the original programs and they are not often easy to get. The Hallberg-Rassy story mentioned above here is bad, but I have had bigger problems when the Cummins main engine does not work because of computer problems. It can be very difficult to get the correct program.
I love new technology, but in a ship and especially in a expedition ship I will be very carefully and wait until the systems are more reliable and serviceable. In the car industry is seems like acceptable when the repair system is private, but in a ship out there somewhere it is totally useless. You need a backup or a traditional alternative. The old crude oil diesel pump will almost never fail. A modern one seems like an always wrong pump.
I have been involved with these decentralised distribution systems for a number of years. Sometimes they can be a great thing when a simple button push can control many functions, or interlocks can be used like turning off a freshwater pump when a grey tank becomes full.
Yes they do save time and weight during installation and can do clever tricks.
However if a node fails and drags down the CANbus then the complete system is dragged down. One particular system (Ok it is one of the older systems out there) seems to be prone to lightning. Not that the boats themselves are struck or any vessel near them struck just that an electrical storm in the vicinity takes out a node or two. I have bench tested some newer systems trying to destruct them with wrong polarity, wrong voltages, short circuits, etc and they seem pretty robust. I don’t have any experience of their durability to lightning though.
Planes, cars and coaches have used these systems for years and are reliable and safe. But the nodes tend to be built for a specific purpose, they are not general nodes which have to cover a wide range of use (abuse)
With my current knowledge, the next new build or restoration project I do may have a decentralised distribution system, but only if the boat was to stay local.
Thanks to everyone who’s chimed in, and by all means feel free to continue the discussion.
I think what we’re seeing here is not so much a rejection of new and potentially unfamiliar technology, but rather a well-justified insistence on being able to repair one’s own systems.
In a boat that sees serious use, things are going to break. It’s not a question of if a boat will need electrical upgrades or repairs; they always do, eventually. When that happens, a cruising skipper can’t be dependent on a vendor half a world away. The work has to be possible with on-board or local resources and expertise.
I suspect that the first distributed power vendor to embrace this reality and make their technician tools and manuals available to end users will come to dominate the sector. And there will likely always be some boats for which a conventional system remains an appealing option.
Matt, I think you’ve nailed it: It’s not the technology people dislike…there are clear advantages and potential savings in weight, wire and worry…but rather the service model.
It’s akin to that of Apple computers, the computers of which it has been said were made for those who didn’t really like computers. Most people prefer the aesthetic experience of the “Mac way” of doing things, along with the substantial thought that went into styling most Apple products. But they dislike the “bring it to an Apple wizard” requirement, and in some cases are dissuaded from purchasing Apple gear completely, due to the higher buy-in and the opacity of fixing even minor glitches (for some, not all). The “culture” of Windows, and more so, Linux, is still somewhat “tinkerer/hobbyist” oriented by contrast. This is akin to propreietary distributed power (Apple) versus plain old conventional wiring, which can be laborious at sea to trace and fix…but it can be fixed: A DC panel doesn’t require a password or a reboot or special signal-tracing devices. My latest meter, a Mastech clamp-on, cost about sixty dollars. That, a crimper, wire, a few spare breakers, heat shrink and a solder iron allow me to fix almost any electrical fault aboard, and when I get a FTZ battery cable crimper, I’ll hit 100%.
The promises of distributed power system vendors can’t touch that, and the “convenience” becomes a curse when the lights go out clawing off a reef in the Southwest Pacific on a dark and stormy night.
I heard that Hallberg Rassy bus system are unreliable: my HR40 still uses the old wiring method, no way I would buy an HR with the new bus system.
How I would love an open source approach, allowing other parties to develop soft and hardware that mixes into the system of a certain make.
It’s the same sh*t as with computers and software: the users used as beta testers: I like to be one step behind the curve.
Hi all, I work for a commercial boat builder and we have used Empirbus CLC and NXT on numerous projects. We have four 18 meter survey catamarans with ten NXT nodes, plus six NXT membrane switch panels each and four Royal Navy survey motor boats with four NXT nodes plus two NXT membrane panels each as well as two FW Murphy PV750 Powerview control panels. We have a 20 meter pilot boat in Kenya with NXT and Powerview and a number of other craft with NXT or CLC.
So far we have had a lot of success and only one question mark on an NXT node that was\suspect but returned no fault found by Empirbus. We ended up putting it down to a glitch during programming.
I can see no need to be fearful of using a distributed system if the hardware is well made. The CLC product was fine and quite economical the input and output cards could be changed cheaply, but they are not water proof and can feel a little fragile (you have to be careful assembling them). NXT is more expensive but very robust, waterproof and very powerful. I like it very much.
I understand some of the concerns about reparability etc, but I don’t think peoples concerns are right. You have to think about products like NXT in a different way to traditional wiring and weigh up the pros and cons to suit the application. Most boat owners don’t like electrics and really don’t understand them. A switch, fuse and wire might seam the simple approach and it is to a point. But when you start to construct more complex systems and monitoring for example, you need to start adding other components including relays, timers, diodes, resistors and so on. This results in more connections, more design, more points of failure. One NXT node can do everything the above can do and more without all the connections, wire and components. This reduces not increases complexity. Ok you could have the most basic of electrical systems without monitoring or controls, that’s fine if that’s your cup of tea. But if you want a system that self checks it self and connected devices your going to need more. I think if I was at sea with a complex wiring system it’s going to be easier to fault find with a distributed system than getting my head in the back of a switch panel somewhere, only to find a component had failed, maybe a relay and I have no spares. One NXT node can be changed in a few minuets with one spanner for the battery terminals and a screwdriver for the screws holding it in place. It is highly unlikely a node would fail anyway, but if it did it’s a synch to change. Oh and no programming required, just set the node address and it takes its logic from the system. What could be simpler.
Good example of how something like NXT can be a benefit to a boat owner as follows: If you fit a normally open bilge switch which closes when you have flood and it fails, because the switch fails or a connection fails you don’t know about it, how is it going to alarm? All good control and monitoring systems are fail safe. So you fit a bilge switch which is normally closed. Now in a simple circuit this wont work as that lamp and buzzer will always be on till you have a flood. So you have to introduce components to reverse the normally closed switch circuit so the alarm sounds when the switch opens. This will require some electronics or a relay circuit, the relay will always be on, consuming power and when it fails or switch opens the alarm will sound. On NXT input is set to normally closed and in logic you can set it to alarm when it opens, simple. Next you put your bilge pump on and you cant hear it as it’s windy, how do you know it’s not failed? With NXT you can set up an alarm if no current flows or if the output has tripped etc. This has to be better. Less wiring and complex circuits, more intelligence and safety.
This is the way your car went many years ago and this is the way all machines will go.
Simple traditional systems are fine, but if you want to start adding any form of sophistication go for something like NXT.
Hi Simon,
Again, just to clarify, Matt’s post in no way denigrates distributed power systems. In fact he went to a lot of trouble to explain the benefits of said. The point of his post was to highlight the danger of committing your entire boats system to a set of components from one manafacturer who has not made a credible commitment to supporting said components for a reasonable system life. It can be the greatest system in the world, but if the manufacturer stops supporting it after say five years (a long product life these days) tearing the whole thing out and starting again is going to fantastically expensive.
Hi
I do not think that bus systems are generally unreliable. The problem is that one makes himself entirely dependent on the manufacturer. Especially EmpirBus and Hallberg-Rassy use this system to blackmail their customers. EmpirBus is even using a PIN/PUK system like mobile phones to prevent customers to use the system in the intended way and to charge for some mousclicks. (I’m really upset about this you see)
I think Frans has a good point in whishing an open source approach. Open standards are the only way to ensure interoperability. In an ideal world it should be possible to replace a defective module with one from another manufacturer. The only way to achieve this is a common, open hardware platform which can be produced by several independent manufacturers. This would also lessen the risk if one manufacturer disappears or stops supporting the system.
In a world where every manufacturer is trying to create a “vendor lock in”, through incompatible and proprietary protocols, this is unlikely to happen.
An example of this is NMEA2000 which is proprietary and closed. Now we have Simnet, Navnet3D, SeatalkNG and so on. All of those are almost but not entirely NMEA2000 compatible. This is just not good enough for a critical application.
Hi Enno,
You are absolutely right. Until these systems are open source and there is a standard I would not dream of putting myself in a position where a single manufacturer could blackmail me. As an ex mainframe computer technical I remember the bad old days where manufacturers used proprietary systems to manipulate their customer to their own ends far too well.
Hi John, Enno, and all,
I understand your points about being locked into a particular manufactures product but there are some bits in this conversation that might not be quite as they may seem on the surface.
Firstly I have used both CLC and NXT Empirbus products in quite large numbers and I am not aware of any unlocking of features at all. When you buy the hardware it has the full capability as sold. But if a boat builder wants to offer you more functionality i.e. add ability to synchronize wind screen wipers in a NXT system, they can if the node supports it, but it is only then an adjustment in software to enable it and possibly some rewiring between node and wiper motors. There is no unlocking or fee paid to Empirbus. But if you buy a boat with no wipers and fit them later and want synchronizing you will most likely have to buy an NXT node that supports wiper synchronization and also be prepared to spend more money for that node and also use three channels per wiper. In a CLC system it’s similar but you only need a wiper card to fit in a spare CLC slot. In a similar way you might want to input a 4-20mA sensor, maybe a pressure transmitter and set it up to sound an alarm if pressure is low. You can do this in NXT but only if the node supports it. If the node dose not support it then the node needs replacing with one that does or you need to add another. But if the node supports it and your boat builder wants to charge you for the feature there is no unlock or fee, but they can charge you to set up the function in the software.
Of course systems like CLC or NXT were never intended to be configured by the end user as the software is not end user friendly unless your very comfortable working computers and very basic tools. You really need training and a days training is not enough to teach you all the features and possibilities. The other thing is that as a manufacture or a supplier it would be a nightmare if you were getting hundreds of support calls from end users. Can you imagine it if your cars ecu was end user configurable from the box!
Another point is that in case of NXT it is NMEA 2000 compatible and will work with other NMEA 2000 electrical products from other sources, i.e. Offshore Systems have relay output and input modules, Maretron has similar and it is possible to mix and match, but again the software needed to do this is not designed for the end user.
In time more and mare marine electricians and electronics technicians will become proficient with configuring, modifying and replacing parts of systems and I am sure enterprising hobbyists will get access to the tools they need.
When you look at NXT it’s a much bigger product than just another module. It’s capabilities in one module is massive. Any channel (model dependent) can be either an Input or Output, dimming via PWM, 0-10V, 4-20mA, many switches (4) to one input, wiper sync, etc, etc. In other systems you might need multi modules interconnected via more wire and not waterproof. Thus yes you might be putting a lot of eggs in one basket but I still think this approach has its benefits.
But I really do appreciate the other side of the argument.
But it’s not a lot different to the difference between those who like fixing there cars and dislike common rail diesel engines and ECUs. But like them and as the product matures I am sure people will come round.
NMEA 2000 has actually opened up the possibilities to mix and match more than any other protocol in the marine sector I believe.
Hi Simon,
That just confirms my thinking that these systems are not ready for use on offshore voyaging sailboats. The idea that I would need a trained professional with special proprietary software to make even simple changes to my electric system is scary indeed, as well as totally impractical in most of the world’s cruising designations.
Hi Simon
I have to disagree on some of your statements.
My boat is equipped with CLS modules. These modules definitely do have a locking mechanism. All of my modules on my boat are locked with a 4 digit PIN code. If you try the wrong pincode several times the module will not accept any more configuration attempts. In this case you need a 6 digit PUK code. The software provided of Empirebus is quit easy to use and almost self-explanatory. You definitely do not need several days of training to understand this. I have only standard CLC modules without wiper modules. These modules are really simple. There are digital inputs and digital outputs and programmable circuit breakers. That’s about it. The most sophisticated function is PWM dimming. There are no analog inputs so one cannot connect for example fuel gauges.
On my boat some circuit breakers were not set to the correct voltage. It is really easy to download the configuration from the modules, change the setting and then upload the configuration to the bus. Unfortunately you need the PIN to upload. I was aware of the problem when I bought the boat and asked Hallberg-Rassy if the owner gets access to the bus. The answer was that one gets the PIN at the end of guarantee period which I could understand. Unfortunately, after two years they had changed their mind and wanted a lot of money for any changes in the configuration file and denied me the PIN code. I tried to upload my new configuration file several times with different PINs which caused the whole system to lock down. You now need a 6 digit PUK to reset the system before it will accept new configuration attempts. Here we talk about the virtual equivalent of changing a fuse. Do you really think the owner should not be allowed to do that? The alternatives for me are now to either pay ransom to HR or buy three new modules (1000€ each). I do not feel very well about scraping perfectly sound hardware just because someone denies me a 4 digit number.
Furthermore I do not think that the comparison to car electronics is valid. The bus on a car controls almost everything from ignition timing to mileage. The CLS modules on my boat do nothing else than switching power. Besides on a boat in the middle of an ocean you cannot just stop and ring the nearest mechanic to fix a problem. You need to be able to fix everything yourself. To deliberately build obstacles into an offshore sailboat to prevent repair is entirely unacceptable to me.
I investigated also into the open source option. Open hardware microcontrollers do exist (Arduino) and the basic functionality is already there. There is a CANbus module and interfaces to possible I/O cards. All this is hardware in the 20€ range. Making a quality controlled module out of this is definitely beyond my abilities and requires a skilled electronics engineer (preferably with background in the automotive or aviation industy).
Generally I believe that this is reliable and relatively simple technology. Distributed power systems have been used both in the automotive- and aviation industry for years. If its reliable enough for an airliner it should be good enough for a sailboat. At least we do not fall out of the sky if something goes wrong. The problem lies not in the technology itself but in the way manufacturers use it. EmpirBus is build to fit the requirements of luxury boat builders rather than offshore sailors (EmpirBus/Trigenic and HR are almost neighbors).
Hi all again 🙂
Will keep this short as typing on phone and waiting for dentist.
John I agree again to a point but if we are talking about reliability being able to modify is another thing. I think we could argue in a similar way about navigation equipment. Once set up by manufacture it’s not intended to be modified. If we look at CLS or NXT spare outputs can be set up for adding future equipment and essential simple on off equipment like a VHF can be kept off completely as there is no practical benefit having it on there. Where it’s more useful is for controlling lighting or monitoring bilges etc or other stuff that benifits from a bit of intelligence. I agree on both sides of the argument but think that the pros out weigh the cons as long as it’s use is sensible.
Enno, ok yes agree on CLS there is a pin code that a supplier can choose to use. This is a HR thing I do not pin protect systems. When I was refereeing to training I was really talking more about NXT as the abilities are huge. But I’m not saying no one can get a grip with either it just depends on what level and what your looking to to do.
Note that NXT is not replacing CLS just yet the hard running in parallel.
Simon
Hello all,
Interesting discussion about the distributed power system and the kind-of negative spin-off it is getting in the comments. But the world is larger than EmpirBus, there is CZone, Maretron, Paneltronics, OctoPlex by Carlingtech, Digital Switching Systems, Phillipi, Capi2, etc. Two mayor players in the marine electrical field, Mastervolt and Victron, also offer distributed power systems. They must have good reasons for that. Some of these systems have been around for a while and despite all the above comments have proven that there are a significant amount of advantages for a distributed power system. Some research on the internet can provide a lot of information on these distributed power systems.
For me, one of the most important advantages is the simplicity a distributed power systems has. Despite the seemingly higher level of technology, it seems hard to believe at first, but as explained by Simon in detail, a system set up with only one cable run to each node and all local equipment connected with short cables to the node and all switches replaced by a button on a touch screen, immensely simplifies the system and makes troubleshooting much easier.
I am currently in the process of outfitting a 55 ft bare hull motoryacht and will use the CZone system. As most of these systems use the NMEA2000 protocol to do the actual switching, you can integrate any NMEA2000 device into the system. In my case I will use a Simrad NSS screen that has the software integrated to operate the distributed switches. As backup I have a PC with the CZone software and a USB-connection to the NMEA2000 switches. The Victron inverter/charger can be easily connected with the VE.bus to NMEA2000 converter and all charging/electrical information can be displayed either on my PC or any NMEA2000 capable screen. To go to a full NMEA2000 system all equipment (AIS, GPS, autopilot.) and sensors (depth, rudder, weather, tank levels, amps, voltage, etc) will be NMEA2000. I will use 3 databuses. The first one will be to monitor tank levels, battery charging, voltage 24 hrs/day (we will be living aboard). The second will be used when on-our-way, to switch on all 24 V (a few 12 V only) equipment. And to more or less prevent interference and for redundancy reasons, the actual NMEA2000 data information that will be exchanged between the navigation systems is exchanged over a third databus.
As many have contributed, it seems hard to believe that a reputable manufacturer as HR puts a lock on the distributed power system that they build standard into their yeachts to generate additional income, but in general I believe most manufacturers do not use this commercial trick. I am reluctant to admit that the philosophy used by some of the contributors (keep it simple, stick to what you know), I have applied when I choose my engine. Not the fancy VW V8 completely computer controlled for which I would need a sophisticated engineer for the fault finding, but the Doosan L086TIH which I believe to be able to maintain myself. I will however connect a Seagauge analog gateway interface to the engine, to display the engine data anywhere that I like in the digital system. For the electronics and navigation I feel confident that with the set-up of CZone in combination with the Simrad, the Victron and the NMEA2000 instruments, I will be able to trace any fault well supported by some additional software and NMEA2000 test equipment. As a last resort the CZone node has the capability of of by-passing the digital stuff by inserting a simple fuse and bring any off-line piece of equipment back to life. This summer I will start installing part of the system, you can follow it on my blog http://www.xanthiona.com (it has a google translate button).
Great article and thread Matt. As a long term live aboard and owner of a 30 ton Lagoon catamaran with a Scheiber electronic system I can say from my experience that when everything works well it is great, but I would never choose it for a serious cruising boat that does not have a Scheiber factory technician also living aboard! The big problems with this system lies as many worry about, in the area of reliability and service and troubleshooting in a marine environment. The boat manufacturer treats their customer like a mushroom ie keeps them in the dark assuming they are only capable mucking things up – I am sure sometimes it is correct but the choices and more importantly systems information in a free world should be given to or easily available to the paying customer. An added complexity with these integrated node systems is when they fault INTERMITTENTLY with no obvious pattern or predisposing conditions, which I am having problems with at present. Override switches attached to keelsen boxes that house multiple breakers, switch groups of functions eg. In an intermittent Scheiber malfunction while cruising underway, by using an override switch say to turn a navigation light on, it also turns a deck light on, thus making night navigation unsafe due to far too much light on the boat. Guess what, Scheiber is not supported in Australia where we are based. When it come to marine electronics I am a great believer in the KISS principal even at the cost of more wiring. In particular a single failure should affect other functions as little as possible. Michael.
Any chance of doing an update on this article? Seems like the market stabilized a bit, the technology advanced, and reliability may have improved. Also, the current systems all seem to offer easy overrides in case of problem.
Thanks
Hi Scott,
I have just reread the article and I guess I can’t really see what Matt would update. The article as it stands explains distributed power systems well and gives readers a complete criteria to evaluate the options being offered by vendors with particular attention to problems that should be avoided.
Sounds to me like you are more looking for a review of the competing systems and that’s not something we do here at AAC. The reason being that a real review of systems like that would take months and tens of thousands of dollars, so as to be really useful and not just a gee-wiz list of features culled from manufacturer hand outs, as you so often see masquerading as a review in magazines.
I guess what I would say, is that if I were doing an offshore boat’s wiring from scratch I would use several small breaker panels, one in each part of the boat, rather than one of these complex electronic control based systems.