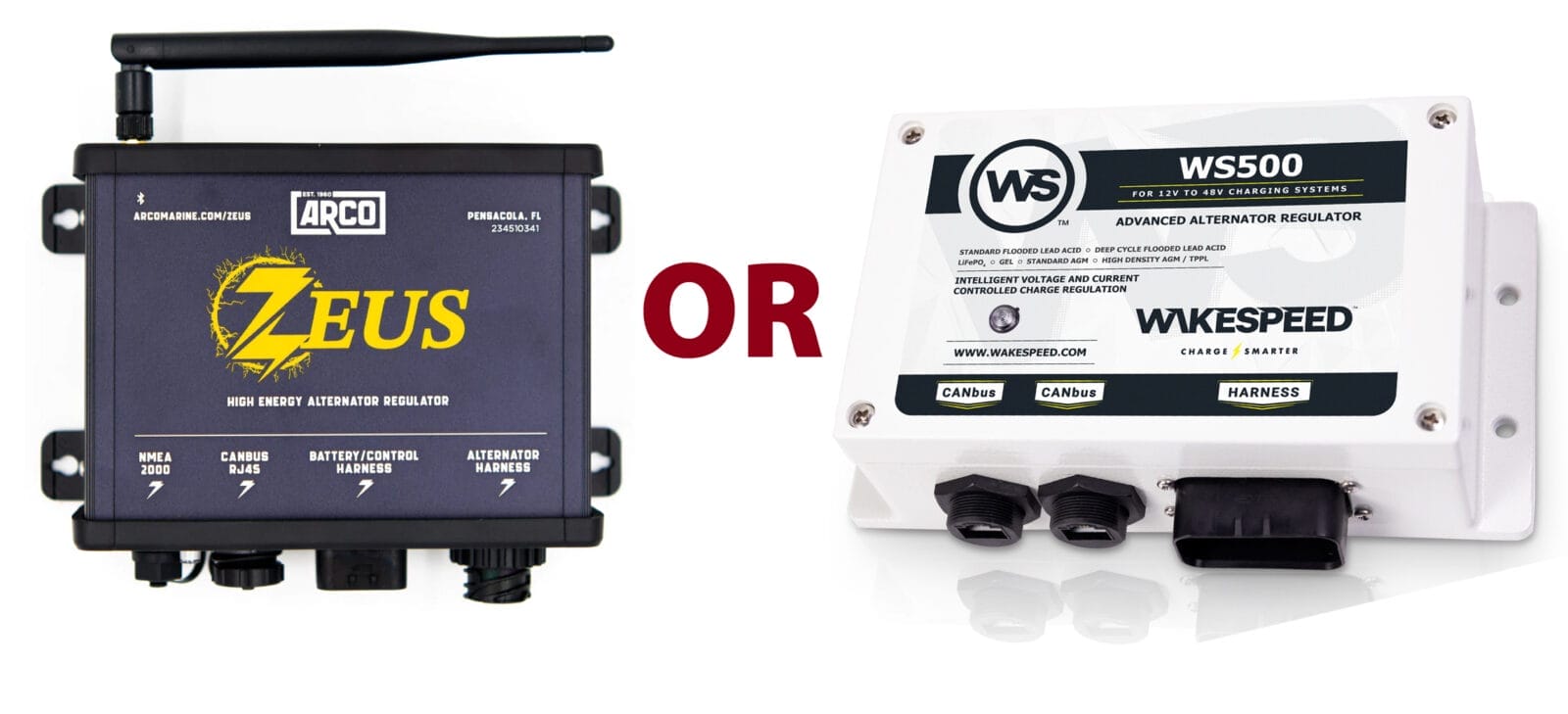
Given that so many influencers these days are being paid in various ways, let me be clear. AAC and I don’t get a penny if you buy a Wakespeed or a Zeus. Zip, nada, zilch. I work for our members. They are the only bosses I have.
That said, and for the sake of total disclosure, Wakespeed have given me two regulators for evaluation (soon to be three), but if you think I can be bought that cheap, you are mistaken.
The value of three regulators is trivial compared to the total that over 5000 members pay us each year. I know who butters my bread…and supplies the loaf.
Before we dig into which smart alternator regulator to buy, a note on my background:
This is not a quick review by some yachtie with a little technical experience. I founded and ran a tech company (computer-systems integrator) where our success was continually dependant on my ability to pick good high-tech products.
And, yes, I made mistakes…which taught me a lot, and which I have applied to evaluating these two products.
So even if you’re not interested in buying an alternator regulator, it’s worth your time to scan through this article and then read the conclusions, since it’s a graphic demonstration of how to cut through slick marketing, much of it fuelled by payments to influencers, to get to the right selection.
And lest you think that my background gives me all the answers, I learned a personal lesson while installing the Wakespeed—heeding it could save you a lot of aggravation.
Thank you, John, good information as usual. It is saving me from my overthinking self.
Please do continue with more information on Wakespeed and ZEUS.
Ross
I’d like to see the Part 2, thanks for writing this article.
Part 2 please 🙂
Channeling Vesa….
Part 2, please Sir. 🙂
Hi John,
To prove you right, yes I’d also like to read more about your thoughts on this, since I also tend to put myself in the expert seat, even when I shouldn’t. And I do think I’ll be getting a couple of these in the not too distant future.
These articles are very timely as I’m planning on an electrical system upgrade in the next couple years…we should have a lot of the esoteric stuff regarding Li batteries and charging controls disucssed. Transparency like this is invaluable and I’m glad to be one of your bread butterers!
Thanks John, I am waiting for part 2.
side question Can you have two shunts measuring in and out of the same circuit. How do you install this?
Hi Denis,
Why would you want to do that? Are you referring to the Zeus having both alternator and battery shunts. If so I will cover that in the next part.
Hi Denis,
I was concerned about this question and according to Arco, you have a Victron BMV shunt, the Zeus can use this shunt’s data directly (just add twisted pair wires.)
-evan
Oops. *if you have a Victron BMV…
Hi Evan (and Denis),
I’m pretty sure you were given bad information. Al and I talked about just this when I installed the new system on the J/109. The problem is that the Victron shunt, unless they have changed it, has no separate terminals for sense wires. So the only way to connect the sense wires is to piggy back them on the load wires, which Al says is a very bad idea.
The point here is that there will be some resistance in that piggy back configuration and with shunts where the voltage variance to a given change in current is tiny, that’s not good, particularly when we are controlling an alternator.
And to be clear this is not regulator specific, the same applies to both.
You can read about this in the Wakespeed FAQ (Page 3): https://www.wakespeed.com/wp-content/uploads/WS500-FAQ-Guide-V1-10.07.2022-1.pdf
Of course, if Victron are now putting sense wire screws on their shunts, all is good.
I was the boat we found the WS bug. Looks like Victron samples the shunt digitally. So does WS. If you use the same shunt for both, they drive noise and the WS sampling is all over the place. I told Zeus to watch out for this during development.
You can piggyback on the board attachment screws fine physically, its an RF/Electrical noise problem.
I solved it with a second shunt inline.
Hi Paul,
Based on my fundamental electronics training, I disagree that you can piggyback the screws.
And Wakespeed specifically caution against it: https://www.wakespeed.com/wp-content/uploads/WS500-FAQ-Guide-V1-10.07.2022-1.pdf
And if adding a shunt worked then I think noise was the problem in the first place. There is no way that the WS 500 could “sample digital” in that a it’s shunt sampling is analog. That said, if I remember correctly Victron have an analog to digital converter on shunt, but that’s not readable by the WS 500. That said, with CANBuss and the right BMS ( say Lynx) the WS 500 does not even need a shunt because all commands come from the BMS.
Thanks John for opening this comparison again; but, I think we will all look forward to your unpacking the real testing details… (that’s the place where the devil / Mr Murphy lives.)
I’ve been in the throes of looking at these two regulators for my system as the Balmar MC-612 is pretty limited in its configurability.
DVCC & Canbus integration with integration of shunt-derived state of charge monitoring seems to be the Holy Grail and represents a compelling goal to both Wakespeed & ARCO (if for no other reason than good marketing)?
In my own EPOCH LFP setup though, I am not convinced it’s necessary or all that desirable to go to DVCC, Cerbo GX control with its extra layers of complexity. Unlike lead acid, where internal resistance grows larger with higher SOC, necessitating higher voltages to optimize charging efficiency, and a real need to use real-time SOC data to regulate charging, the Epoch LFP’s take all the charging I throw at them and by the time the bank hits 13.9 VDC, the bank is at 99.9% SOC. It really is a lot simpler.
I would ideally want a smart regulator that is very good at tight control of charging voltages, maintains safe alternator loads by monitoring alternator temps and output and would be able to turn off charging in the event of a BMS shutdown. (load dump). Both the Wakespeed & Zeus can probably do these things well but I have yet to read of a proper testing comparison between the two.
In this respect, ie communication of impending load dump, Canbus communication has real value but the actual charging protocol is pretty simple. (eg Victron IP22 protocol of 13.9 VDC Bulk/ with very short absorption time & 13.45 VDC Float has my bank well topped up & balanced.)
Unfortunately, in my setup, the Epoch BMS’s do not, at present, have a way to communicate an impending MOSFET shutdown despite their Victron Canbus integration. This means that, until I can protect against a load dump, I will stick with my Dumb Balmar regulator to feed the AGM start & thruster banks & use Orion XS DCDC chargers for the alternator to charge the LFP’s.
Hi Evan,
None of that has any bearing on which alternator controller to choose. If you don’t want to use CANBus just use “wiggle wire”. Both regulators can do that, so there is no real benefit for either in that case. Given that I would still default to the WS 500 because it’s the proven solution with tens of thousands in the field.
That said, one point though that I think you are missing. If a BMS, for example Victron Lynx, has CanBuss then it’s simpler, not harder, to use it with the WS 500. Heck, you only have to hook up five wires and don’t even need a shunt, never mind two.
And add Victron monitoring and you will have full read out from the WS 500 with no added wires or issues. What could be simpler. And then if you decide in the future you want DVCC the WS 500 is ready for that too, with no added wires. What could be simpler than that? In my view CANBus is the way of the future.
Also, in my view you have the need for current control backward when comparing lead acid and lithium. Lithium needs current measurement far more than lead acid because its charge current is not self limiting by increasing internal resistance. So, for example, it’s perfectly possible to overcharge and damage a lithium battery at voltages as low at 13.5 volts, if it’s held there for long enough.
I would suggest you have a read though the excellent article over at Nordkyn, and particularly the part about the requirement to measure charge current, not just voltage, to charge lithium batteries without shortening their lives: https://www.morganscloud.com/jhhtips/great-source-how-lithium-batteries-charge/
I found this a great resource and learned a lot. Highly recommended.
Hi John.
I’m not suggesting for a moment that one does not want accurate SOC or current monitoring with LFP.
I’m simply saying that, unlike lead acid battery banks where one needs more prolonged absorption times to achieve a full SOC and ideally using smart chargers & regulators that monitor and control charging according to SOC goals, LFP is a much simpler protocol.
Yes. I’ve read that article thanks.
Hi Evan,
I guess we will have to agree to disagree that LFP is simpler than lead acid.
John,
Only 5000 subscribers? That blows me away. I consider my membership essential and can’t think of another site with so much common sense and experience based advice. Your articles help me make important decisions during our refit and so cut down on the agonizing, slab reef at the mast and PC based navigation come to mind as big ones but there are others. Thank you for that.
May I suggest to any member reading this that you go out and find just one new subscriber to support AAC?
I’m looking forward to part two of this series and hoping for as much detail as possible. Maybe part three could be an in-depth look at the Whitespace concept and how to best implement it. My engine and Wakespeeds will thank you. We will be running two 24V, 140 Amp Balmars on a Beta 60.
Hi Torsten
Thanks for the kind words.
Yup, and the other issue is that about half of those are on legacy prices at 19.99 and 24 a year.
I think this is the penalty for telling people what they need to know, not what they want to hear.
On the other hand we have remained relevant for over 20 years while many of the “tell ’em what they want to hear” types have come and gone.
I have written about this: https://www.morganscloud.com/why-we-need-your-help/
And I love you idea of members going looking for more members. Thanks
As far as programming for white space, that’s reasonably easy if you just want to make sure you have enough power when you need it for maneuvering…I think.
However I think (again) that if you want max efficiency it probably gets harder and is likely past my pay grade, at least without a huge amount of research. Maybe I can persuade Eric Klem to write a how to…Eric?
Anyway, the good news is that the good folks over at Ocean Planet will do it for you, so that’s what I would recommend. https://oceanplanetenergy.com/high-output-alternators/
Hi Torsten and John,
I am not familiar with the term whitespace in this context. Are you discussing taking advantage of the mismatch of the prop curve and engine power curve to allow for high output and potentially efficient charging at mid-range engine speeds?
Eric
Hi Eric,
Yes, you are right. I think the term was coined by Al over at Wakespeed when he added the feature to the WS 500. If you download the Wakespeed app (free) you can see how he has it implemented.
Hi John,
Thanks, I downloaded the app and took a look. I am so glad that someone is finally allowing this level of control.
I put an article on how to optimize this on my list, it is certainly worth thinking about also as we are starting to see some really powerful alternators on relatively small engines. It is also related to 2 articles I was already thinking of on drivetrain efficiency related to propellers and with big alternators, including how to deal with the alternator output when propping really makes a difference.
Eric
Hi Eric and all,
For years, I have had a field wire disconnect switch which takes my alternator off line. Early on I had a smaller engine which occasionally had to work hard to get out of rivers when wind was vs river stream and I wanted all power to be able to get to the prop, especially with the alt working hard and taking hp after a few days at anchor.
I am almost embarrassed to admit that the more compelling reason was the occasional wish to use the microwave when motoring: I did not like hammering the alternator, the belt etc. when the current draw of the microwave kicked in. So, take the alt reg off line and use the microwave and when the microwaving is done, bring the alt reg back on line: it ramps up and gently replaces the amperage used and no hammering of the alt, the belt etc.
I never did need to use the disconnect to get full power to the prop, but it was there if necessary.
My best, Dick Stevenson, s/v Alchemy
Hi Eric,
That’s great news, thank you! And a nice follow on from your upcoming articles on torque too.
Looking forward to part 2
Hi John. Thank you so much. I was about to lay down my $800 US for a Zeus. I liked the idea of NOT needing to select a positive or negative harness as one needs to do with the Wakespeed. I have very old instruments on my CS 30, soon to be replaced. So the CANBUS is now in the picture. Having the electronics able to communicate plus having good battery monitoring appeals to me. I absolutely need a system that just works. Full stop. Again, thank you for the clear no B.S. assessment. I too wouldvery much like to see part 2.
Colin Post
John, very good, as usual, and I’m interested in part 2.
I enjoyed the article, John, especially since one of my next projects is to upgrade one of my alternators and install an external regulator for it. I’m looking forward to Part 2. Many thanks!
Part 2. Yes please. I’m considering changing my alternator regulator at the end of the season, so Part 2 will be extremely useful to me. Thanks
I run a WS500 and APS 56v alt on a cat, and there are some unresolved issues with the product. On a cat the regulator must be near either the battery or the engine room, cant be both. That means extending the loom. The loom is very noise sensitive, and extending either the batt shunt or alt temp sensor gives problems unless you shield well. Thats undocumented.
The temp control on my and others boats can oscillate wildly. The damping applied is not adjustable and oversensitive. You need to faff around with sensor location to get smooth temp control for steady output.
In both cases above the sampling and actions happen too fast to show up in the debug output, so you dont really know whats driving the switching.
The rotor field is fully powered when the engine is stopped. Heat. It could ramp back, but it doesn’t. I ran mine though a relay with the oil pressure sensor.
N2K documentation for BMS integration is terrible. You can’t determine what parameters the BMS is controlling and what the WS is controlling. Who is in charge of what and when? The answer is both, sometimes.
Programming, well, you know that interface.
WS is a fascinating product, but has very large gaps and the aquistion hasnt helped.
They have / had amazing support, really nice guys, but the product has long term large gaps.
Hi Paul,
Thanks for the report, always useful.
The risk of noise on the lines is intrinsic to the method of using a shunt to measure current, regardless of the regulator brand, because the voltage variations in relation to current are so small. A couple of things to check: Did you twist the wire you added to the shunt sense lines? Also, did you by any chance use a shunt that does not have separate sense wire attachment screws. Both problems are covered here: https://www.wakespeed.com/wp-content/uploads/WS500-FAQ-Guide-V1-10.07.2022-1.pdf
Not sure either of those are your issue, but I’m pretty sure something is wrong in said lines. Also, I have not seen any issues on alternator temp sense so perhaps you have a bad sensor.
If rotor field is fully power with the engine stopped, again, I think this is intrinsic because unless we use RPM the regulator has no way to know if the engine is actually running once the ignition switch is on. (Unless using the RPM option in the regulator). That said, the field should go to zero as soon as you turn off the ignition, that’s what the brown wire is for, which should be connected to the terminal on the ignition switch that energizes when turned on, so if it doesn’t there’s an installation issue.
And I agree, the documentation is not great and very techie.
That said, why are you digging into which is controlling what. Why not just use the app to select a standard configuration, or at least start from there, as I learned the hard way to do?
48v boat w 30kwhr batt and 9kw alternator. No profile for that setup.
The warning in the manual came from us working w Al to track it down a bit over 2 yrs ago.
They are very noise sensitive in most respects. Engine room is about 5m from batts, so loom has to be long one way or the other.
When integrating Victron, REC and WS, also whilst guineapigging the Wifi router thing from their partner, CAN was very very problematic.
Ended up following TopSecret and keeping discrete control. Much more reliable.
Hi Paul,
Ah, I remember the WiFi gadget. That was early days and the problems end users had with it was a lot of why it got dropped. The firmware has been upgraded many times since then, so if it were me, I would still look for a standard configuration in the app and try that as a starting point. I would also make sure my WS 500 firmware was right up to date. Also, 5 Meters to an analog shunt is quite a way so I would still be looking for any place in the installation where noise can creep in. The other fix might be to go all CANbus, and then you don’t even need a shunt with the WS 500, but that depends on BMS and batteries, of course.
Looking forward to part 2. I have a WS500 controlled Balmar, charging a 24v Victron SmartBattery bank through a Lynx BMS. Lacking a shunt for the alternator, not sure I have it optimally configured. However, the system has exceeded expectations for the past year and a half, cruising full tome.
Jay
I’d like to join the chorus asking for Part Duex. Yes, please.
Great piece John.
I am excited to have finally brought up our WS500 under the long awaited new 2.5.2 firmware which supports full integration with the Victron Cerbo / Smart BMS integrated DVCC multisource charging control and the elegant Whitespace rpm driven charge programming. I have a screen shot of the first run to share.
I highly recommend Off Grid and Marine Energy Systems for their elegant Wakespeed Software Configuration Tool. The Pro version is worth every penny. It does real time graphing and data logging. Tab to Configure and it parses and geo-annotates the png parameters and allows editing back to the WS500. And the Wakespeed dashboard is glassbridge sexy and super helpful.
3 Cheers to Al, Victron, and OGM!
Bill Bowers
SV ConverJence
Hi Bill,
Good to hear it’s working well. I was not aware of that configuration tool, and will take a look. Thanks
Hi, I’m a new subscriber. I’m installing LiFePo4 on my boat. I’ll have a knowledgeable electrician helping but still interested in understanding the following: I’m considering the Wakespeed to replace my Mastervolt Alpha Pro regulator, which is attached to my 80v Mastervolt alternator. It has limited settings abilities. However, I’m also adding a Victron Orion Smart Isolated DC to DC converter. The Victron manual shows a direct connection from the alternator to the DC to DC. Does a regulator provide benefits not provided by the DC to DC? Or does it become redundant? I went over my existing set up for my AGMs with the battery distributor and he felt that I could use my existing setup (mostly Mastervolt) but to switch out the solar controller and add the DC to DC. Thanks, and perhaps this has been answered elsewhere.
Hi Tom,
The key here is for an optimal system all charging sources should feed to the lithium house bank. However that does require the BMS to control said charging sources. Some systems do connect charging sources to the lead acid engine start battery, but that’s sub-optimal with efficiency losses.
To understand why, and how to design an optimal system you need to read through this Online Book. Some chapters you can skim, but most you will need to read carefully to make sure you have the base understanding so you can get the best system for your money: https://www.morganscloud.com/category/electrical/online-book-electrical-systems/
Pay particular attention to the chapters on battery bank separation and cross charging, starting here: https://www.morganscloud.com/2022/09/04/battery-bank-separation-and-cross-charging-best-practices/
And our lithium chapters starting here: https://www.morganscloud.com/2022/09/04/battery-bank-separation-and-cross-charging-best-practices/
After you have that base understanding, I suggest you ask Ocean Planet Energy to put a system together for you since there are a lot of people out there claiming to understand lithium battery systems who don’t.
I wish Wakespeed offered direct customer support. I have found the vendor they reference useful and have paid them for custom settings, but they were not able to schedule a phone call, and would not enable any DVCC features nor discuss them.
I suppose I can call and say I have an RV with twin yanmars 🙂 Sad as the company seems run by boaters, but we must be too big a PIA!
update – just had a great call with Wakespeed – they certainly do support us, may have been a moment in time for what I was asking etc.
Hi Matthew,
Good to hear that it came out alright in the end. That said, your thread does illustrate how complex all of this is getting, to the point there are going to be frustrating issues that the support techs just won’t know the answers to. And of course Victron exited end user support years ago. This is why I generally advise buying a complete system from an expert like Ocean Planet Energy.