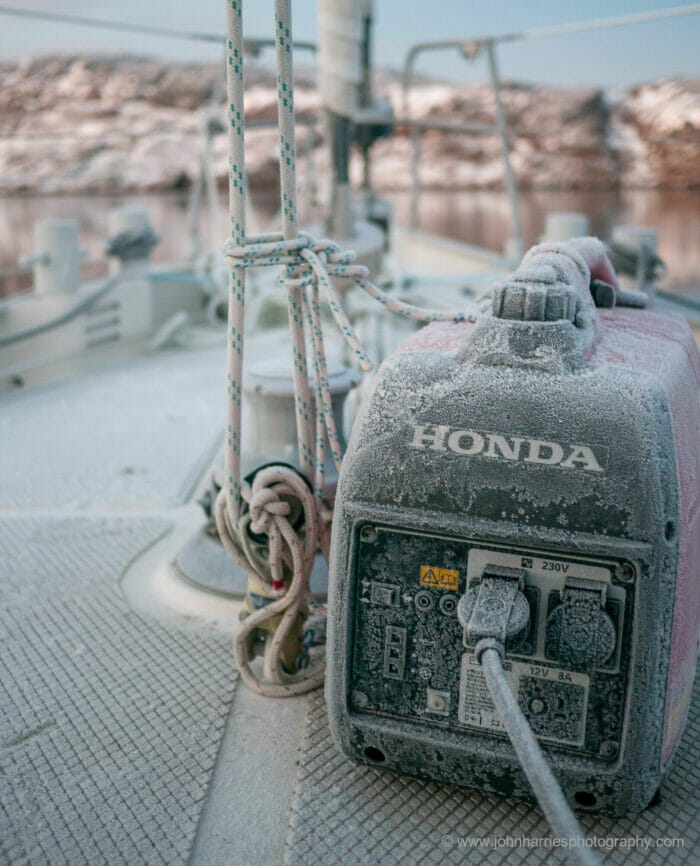
A few weeks ago we published an article on the dangerous issues I have found in the shore power system on our new-to-us J/109 and what I’m doing to fix them.
During the ensuing discussion a member asked whether or not supplying power to a cruising boat with a portable generator through the shore power cable was safe.
I have to confess that I had never really thought about it, and that Phyllis and I did just that while taking care of a friend’s boat one winter in Greenland.
And while I’m in the confessional I also have to admit that I was considering just that option (among several others) for our J/109.
But when I started really thinking about this, I was surprised how difficult I found it to quantify the dangers and understand the solutions (if any), despite having a good understanding of electricity from my time as a mainframe computer technician back in the day when the machines filled rooms.
The big issue here is where the neutral and ground wires are tied together as well as the earth itself. Getting this right is a fundamental requirement for shore power safety.
So first off let’s take a look at how things work when we are plugged into a marina shore power system, and then we will see how plugging into a generator is different.
Note: Everything that follows is applicable to North America only. There may be differences in other countries, but as we will see, I don’t need to get into that to reach my conclusion.
I am fairly certain that there will *never* be an ABYC or CE/ISO code for running a shipboard AC power system from a portable generator.
In addition to all the electrical ambiguities (is this generator floating- or bonded-neutral? what if the floating-neutral Honda craps out and someone plugs in a bonded-neutral Champion instead?), the CO issue, the gasoline issue, the question of safely restraining a 100 to 300 pound machine meant for stationary operation on a moving deck…… the generator itself would have to meet all the relevant product safety codes for mobile marine use, which are NOT equivalent to those for stationary on-shore use. By the time you’ve made the generator compliant with those rules, you’ve just built a standard marine generator of the kind we’ve been able to install, as permanent/fixed machines, for decades.
There’s just no consistent, reliably safe way to do it with a portable machine without inadvertently allowing *some* combination of legal parts that ends up being dangerous, so there will never be a code for it.
Hi Matt,
That works for me. As you say, by the time you fix this right, if that’s even possible, you might as well install a small diesel generator to code. And in doing that you get away from gasoline and have much less CO danger.
And good point about changing from bonded to non bonded generator without realizing what we have just done. Didn’t think of that one. Mind you I was tired after all the possible gotchas I did think of!
“is this generator floating” Probably, if it was sinking it’d stop working;-) Sorry.
Ouch!
After hurricane Florence in New Bern, NC, our dock was without electricity for almost nine months as extensive repairs were made in our marina. In January following the storm as we were preparing to depart for the Bahamas and for warmer weather, we used a Honda EU2200i Companion to supply 120V a/c to the boat via a shore power cord mostly for space and water heating.
The Honda generator was on the dock, and our boat was in its slip relatively undamaged amid the chaos the storm left behind. What I disliked most about the setup was the constant refueling of the generator because its small fuel tank. Repeatedly handling gasoline in a situation where prompt fire suppression was unlikely lead me to adapting (with bits from Amazon) our dinghy’s 3 gallon fuel tank to feed the generator. That was better, but still it was a MacGyver solution.
My second problem was the noise. Yes, the 2KW Honda’s are quiet. But, when run at full output to heat a boat, they are not quiet.
I did not feel too bad about the carbon monoxide risk with the generator running at a distance on the dock. We have a CO detector on the boat. But, to put the generator onboard… We have had our CO alarm sound from a generator running, air conditioned trawler anchored to windward of us. It gave us a pause. It did not take a lot of exhaust gas to trip the alarm.
You covered the electrical problems. I won’t.
All and all, the Honda is great for what it was intended to do, supply electricity in a remote location for short periods of time. I’ve used it for that, running electric saws and drills at “The Barn’ north of Roan Mountain on the Appalachian Trail. It is great for that, but for air conditioning or heat, you need to think carefully about what you are getting ready to do.
An alternative to the Mark Twain/Winston Churchill quote is to refer to the Dunning–Kruger effect https://en.wikipedia.org/wiki/Dunning%E2%80%93Kruger_effect
There are criticisms of it and concerns about how dependant on US culture the effect is. However, it seems relevant here.
Those who know very little about this are likely to overestimate their ability to recognise the dangers.
Hi Dave,
So true. I have made exactly that mistake many times, although as I get older I try to do better. The secret seems to be to get as comfortable as possible with saying “I don’t know”. Defiantly a work in progress for me!
Very good subject. You said: So what’s the stake driven into the ground for? Primarily to dissipate lightning strikes and static electricity, which do return to earth—that’s the other 5% missing from the above paragraph, but not relevant to this article.
This is not true. In Canada AC each high tension phase is carried on single conductor wire over steel pole (735k KV) and the ground is the returning path. There are 3 wires group, one for each phase. When arriving at the last transformer in your street, since you are residential you have only one phase (not exact, you have one and half to get 240 v) this one is GROUNDED to earth and the white neutral wire you receive connected to the meter and your home panel is in fact the EARTH. The electric code requires a home owner to have the white NEUTRAL and the EARTH reunited at the panel thus the spike in the ground + attachment point on the city water pipes which are grounded (of course they are in the soil).
So indeed the stake in the ground of course could be used for lighting strike on the local transformer…but its not its primary use. Primary use is to provide low resistance generation point for the 120 V in phase with the local transformer in the telephone pole close by. Since its an AC current it change direction 60 time per second so indeed its going into and out of the ground 60 times per second… and the earth is a low resistance conductor. Not the best… but a good one.
Now about the home generator. Lets gets simple, its only a sinuisodal wave generator of 120V … same wave could be found in your radio speakers and believe me people working on theater stage with 10 000 watts of speakers have the same concern of any electrician – not to get shocked. That wave need 2 wires to be propagated. Third wire is an alternate return in case one of the wire is broken. Neutral versus live, black or white are only convention. From a physic point of view, the electrons doesn’t know and doesn’t need to know. They just flow in and out 60 times per second.
The use of ANY AC generator (alternator indeed) requires careful planning of the switch over of the 2 wires (live and neutral) and the establishment of an alternative path (grounding) on a boat. That should be left to marine electrician. ABYC has very good directive about this and my preferred is to have a boat with an isolation transformer installed per ABYC and verified to have no live, neutral or AC ground wire touching the hull or any apparatus. (Difference between bonding and grounding…)
Then whatever the 120 volt source… If someone use whatever kind of AC source provided and whatever the floating or bonding ground system, if that source enter the boat through the dock connector it will have have to pass through the ELCI main switch and the GFCI outlet before it could be used. If the live/neutral are inversed the main switch will tell and the isolation transformer will convert it straight. And then its usage should only be directed only to the inverter/charger which has to charge the battery and regenerate the AC for all the outlets.
Of course it is forbidden to plug anything else into that generator…this would not be safe because then there is no alternate path for the current if the tool get shorted or bad luck of any kind. This is why its so marvelous these days to have only battery tools on board…
In that described situation, a portable AC source being it a portable inverter with LiPO or a gasoline alternator is safe to use on a boat.
disclaimer i’m not a high power electrical engineer but my brother is and he used to works for Hydro Quebec. I checked on him to provide this answer.
Hi Andre,
I was writing about what happens after the transformer (secondary). What happens before (primary) is way past my pay grade and not something I even looked at. Nor does it matter for the purposes of this post.
I do agree that regardless of any of this, an isolation transformer is the best bet. A drum I have beaten in at least half a dozen articles over the years. Most recently the one before this.
At the risk of getting a *little* bit off topic, there’s always confusion about the role of the grounding stake and where the electricity actually flows. I will try (and perhaps fail) to clarify.
From the generating station, across the high-voltage lines, to the substation, to the local lines, to the final transformer before we encounter it, electricity is distributed as 3-phase AC. There are three wires, each of which is carrying a 60 Hz (or 50 Hz) sine wave. They are out of phase with each other by 120°, or one-third of a cycle. If you measure the root-mean-square (RMS) voltage between any two of the three wires, you’ll get the nominal voltage of the transmission line.
That’s a great way to move electricity, but not a great way to use it. At the last transformer before it gets to you, the three wires are joined to the three corners of a transformer that is (schematically) triangular: a “delta”. On the other side of the transformer, there is a Y shape. In a typical light commercial setup, you will get 208 V between any two of the three tips of the Y, or 120 V between the midpoint of the Y and any one tip. The three tips are each 120° out of phase with the others, just like on the transmission line. They’ll be coded red, blue, and black, with white at the midpoint. A big, nicely balanced motor might use all 3 phases and omit the neutral; a computer or a fridge will use 1 of the phases and the neutral.
In a North American residential setup, the transformer will be wired so that one of the three phases drives a pair of coils with three taps, usually coded red, white, and black. The red and black are 180° out of phase, i.e. opposed, and the white is the midpoint between them. Thus, white to black is 120 V, white to red is 120 V (but offset by half a cycle), and red to black is 240 V. All three wires carry current. (The 2nd phase will drive an identical transformer for the next few houses up the street, and the 3rd phase for the next few houses after that, so the load of the whole neighbourhood is shared equally among the three phases.)
So far, the output side of either kind of transformer is floating. All the current is flowing through the wires — none is flowing through the ground. The voltage measurements are only meaningful from wire to wire. But if we are to use the electricity safely, all those voltages must be referenced to a ground. Otherwise, we could get 120 V between two wires, but with the wires being at 8,000 and 8,120 V relative to the dirt we’re standing on.
So, at the source of power where we switch from transmission lines to distribution wiring, that neutral (white) terminal must be referenced to earth / ground, literally the earth under our feet. This connection carries negligible current; its role is to tell the transformer exactly what “Zero Volts” means at this location. Those green box transformers you see on the roadside have 10-foot loops of copper buried deep under them for this purpose. Your home’s main panel has a copper stake buried in the ground nearby, as does the big main panel at the head of the pier.
The green ground wires at your individual loads all link back to that same ground. They tell your load devices “This is what zero volts is at this location, and if you try to release any fault current at any voltage other than zero, it’ll naturally return to the source via this wire instead of finding its own dangerous path.”
With that in mind, you can see the enormous risk of linking the neutral to the ground, again, at any point farther downstream from the source. You are now creating a second ground reference, and effectively telling the system “Ground is XX volts over there, but YY volts over here” and then linking those points directly together with a wire that’s carrying the full load current. Some of the current that *should* flow back to the source via the neutral wire will, instead, flow out your illegal grounding connection, through the water, through the dock pontoons, through the soil, and back up the source’s ground stake, to be reunited with the source’s neutral.
This is part of the beauty of isolation transformers. Current from the output side of an isolation transformer must, by the laws of electricity, return to that same transformer. With the transformer’s output side ground connected per ABYC / ISO standards, any fault currents are limited to just the small, well-protected setup on your own boat. They can’t get into the water, cross to the dock pontoons, and find their way back to the source by any other unsafe route. Galvanic currents can’t pass between your boat and the shore at all (they are DC, and are blocked by the purely magnetic connection across the transformer coils).
Well-said Matt. I would add, polarization transformers play a very similar safety role, with the exception of galvanic isolation, the only difference between those and isolation transformers is the manner in which they are wired. Either can be ABYC compliant. There is a subtle but important distinction between grounded (the neutral wire) and grounding (the safety ground wire) conductors. Grounding conductors are, as far as ABYC is concerned, and under normal conditions, not current carriers.
More on transformer here https://stevedmarineconsulting.com/wp-content/uploads/2019/12/ShorePowerTransformers181-04.pdf
Hi Steve,
I just read through your article linked in your comment. Excellent, and an article that any boat owner thinking about a transformer should read.
Hi Matt,
Thanks for the fill on that. I was pretty sure that the earth stake was not current carrying, but not confident enough in my knowledge of three phase and what goes on on the primary side of the transformer to get into it.
Anyway, the key point is that the neutral and ground must be tied together (ground referenced) in one place on the secondary side of any transformer, but only in one place. Once we understand that, and why, isolation transformers and how they must be wired becomes much easier to understand.
A critically important subject John, and one well worth discussing.
I sit on the ABYC Hull Piping, Engine and Powertrain, and Electrical Project Technical Committees, which are tasked with writing and amending ABYC Standards. When the AC Gensets committee met in 2019 the subject of portable gensets came up and was discussed at length. These committees are a classic case of sausage making, it often isn’t pretty, with competing interests lobbying their cases, often vigorously, along with a healthy dose of devil’s advocacy, which is in fact useful. You might think, who could lobby for a portable genset? It came as news to me but some pontoon boat manufacturers actually make accommodations for portable gensets, and their use on these open vessels is very popular.
Surprisingly, the least concern is electrical. Most small portable gensets, like the one pictured, use a non-conductive case, so it touching a wet dock, stanchion etc., isn’t really an issue. Some portable gensets have a ground lug, so the internal metallic chassis can be grounded to something, earth, or the vessel’s bonding system if there wasn’t already a neutral to ground connection within the genset. ABYC Standards are clear on this, the grounded neutral and grounding safety wires must be connected at any source of power, which includes gensets, when (and only when) they are the source of power. And, many portable gensets already include their own GFCI protection.
This passage from OSHA clarifies several of these issues, the underline is mine…
“Grounding Requirements for Portable and Vehicle-mounted Generators Under the following conditions, OSHA directs (29 CFR 1926.404(f)(3)(i)) that the frame of a portable generator need not be grounded (connected to earth) and that the frame may serve as the ground (in place of the earth): • The generator supplies only equipment mounted on the generator and/or cord and plug-connected equipment through receptacles mounted on the generator, § 1926.404(f)(3)(i)(A), and • The noncurrent-carrying metal parts of equipment (such as the fuel tank, the internal combustion engine, and the generator’s housing) are bonded to the generator frame, and the equipment grounding conductor terminals (of the power receptacles that are a part of [mounted on] the generator) are bonded to the generator frame, § 1926.404(f)(3)(i)(B).
Thus, rather than connect to a grounding electrode system, such as a driven ground rod, the generator’s frame replaces the grounding electrode. If these conditions do not exist, then a grounding electrode, such as a ground rod, is required. If the portable generator is providing electric power to a structure by connection via a transfer switch to a structure (home, office, shop, trailer, or similar) it must be connected to a grounding electrode system, such as a driven ground rod. The transfer switch must be approved for the use and installed in accordance with the manufacturer’s installation instructions by a qualified electrician.” https://www.osha.gov/sites/default/files/publications/grounding_port_generator.pdf
Honda’s website says, “Do not use the generator in wet conditions, such as rain or snow, or near a pool or sprinkler system.” This pretty much rules out use afloat…
While there is an electrocution risk, I believe the greatest risk is from CO poisoning and fire/explosion from handling of gasoline.
Bottom line for the ABYC Committee, we agreed to make the standard applicable only to permanently-installed gensets, thereby, in a left-handed manner, excluding portable gensets from the ability to comply with ABYC Standards. Since they were not prohibited per se, those manufacturers could still use them, albeit without being able to say they were ABYC compliant.
” This standard applies to the design, construction, and installation of alternating current (AC) generator sets intended for permanent installation and operation on boats.”
To be clear, regardless of ABYC Standards compliance, I am adamantly opposed to the use for portable gensets for all the reasons detailed, including the potential electrical, fire and CO poisoning hazards.
Hi Steve,
Works for me. Lot’s of different issues here, but on the electrical side I do think the dangers are higher than many realize, but then I could be wrong too. That’s kind of my whole point. And I can certainly see why the process gets messy at ABYC because there’s a lot of stuff here to be wrong about and a lot of ambiguity. For example, Matt’s point is a good example: that the owner might change from a generator with the neutral and ground not connected to one with them connected and a metal case. Most yachties would have no idea about the implications of such a change.
Anyway, as you say, and I say in the article, there are a bunch of good reasons not to use gas generators around boats and water, including CO. And I agree, CO is the probably the most likely thing to get you, closely followed by gas fed fire.
Being in south Florida I just wanted some cold A/C.? Thought I believe All is just way to unsafe for me to sleep that cozy. Sea breeze?
I know this will probably freak you out, but…when I crossed the Atlantic in 2010 on my way to the Med from the US, I had to acquire a step down transformer in the Azores (Horta) to convert the Euro 220 VAC to 110 VAC to run my boat systems. At the time they were selling big yellow watertight 4000 KVA split phase transformers designed for European construction sites that needed 110 VAC to use American power tools. The split phase transformer divides the 110 VAC between the hot and neutral wires supplying 55 VAC to each, the rational being that splitting the 110 VAC reduces shock hazard and potential electromagnetic interference.
During the time I’ve been using this arrangement, one disadvantage was having to remember that switching off a circuit with the circuit breaker doesn’t cut off the 55 VAC neutral connection, so working on things like the hot water heater could produce some unexpected sparks. The other disadvantage is that the transformer itself consumes amp hours when plugged into a metered shore power connection, which, over the course of a winter layover can add costs to the electric bill. Otherwise, no problem with electrolysis (perhaps because it’s an isolation transformer?)
My only 110 VAC needs are for house receptacles (power tools, electric heaters, small appliances), and the house bank battery charger. Everything else is 12 V, for which I cobbled together a 7hp Kubota single cylinder diesel with a 140 amp alternator to keep the house bank charged. The whole arrangement has worked well, the only major drawback being the added weight of genset and transformer.
Hi Reed,
I have no opinion on that one since it would take me a bunch of time and drawing out to get my head around it.
That said, if it were me, I would fit an isolation transformer since most of them these days include step up and down. This is how we managed when we cruised Europe and it worked well with the added benefit that it was ABYC compliant: https://www.morganscloud.com/2021/08/10/check-your-boat-shore-power-system/
I like the sound of your DC generator. Over the years I considered doing the same thing, but our AC generator was so reliable and in place, so it never got to the top of the list.
That’s horrifying. If I were to take such a transformer to the local Intertek or UL lab, I suspect they would file a formal disciplinary complaint against the engineer who signed off on manufacturing it, and probably call for a safety audit of the whole company.
The 240V mains to 110V center tapped to earth yellow plastic boxed transformers were common items on the two construction sites in the UK where I worked between 1990 and 1994. They were inspected/tested by the site electricians weekly and marked with dated and initialed tags. Only 110V tools were used with the transformers. See http://www.carroll-meynell.com/110v-electrical-supply-systems and others that “110V CTE” in Google will reveal.
Tools intended for use in the United States (and boats with electrical systems intended for use in the United States) can use the yellow plastic boxed transformers to supply 110V after replacing their plugs, but at some peril as neither of the power leads in a 110V CTE system is a grounded conductor as Reed’s above note states. The 110V CTE plug is a yellow affair with three round pins, and is nothing like a NEMA 125V plug.
Hi Matt,
I too, like William, remember those transformers. As I understand it they were specifically developed in England so that construction crews would not have to use 220 Volt hand tools, so not in and of themselves a safety risk, in fact the opposite. I’m also guessing this was back in the day when power tools had metal cases, making 220 volts doubly dangerous.
That said, I agree that using them to power a boat is problematic, at least unless we fully understand how they are wired and ground referenced (I don’t).
Update, This is wrong, see comment below: I guess, at least in theory, if we did have said understanding and the boat side green wire was isolated from the shore side, they could act as an isolation transformer, but that would require ground referencing on the boat, which would then be dangerous when the transformer was not present.
That’s a long way of saying “don’t do that”.
Hi Matt and William,
Correction: I just noticed Williams link and followed it, and can now see clearly that these can’t be used as isolation transformers because the centre green wire is connected to the center tap and that in turn connects to the earth and the supply ground.
All interesting new knowledge for me that gives me the theory to reinforce “don’t do that”.
My young and stupid self once used a portable generator to run an electric pump to empty my hull after it’d holed when the mooring failed. As I was wading round in the water I kept feeling shocks in my legs. Didn’t like it but the water got pumped out.
Hi P D,
That’s just about on par with some of the stupid stuff I have done. Amazing that I have made it to 70.
Thanks John, that’s a subject I’ve covered in print many times, but that version is the most exhaustive, it’s the culmination of 20+ years of experience with marine transformers. It’s worth noting, polarization transformers offer all the safety benefits of isolation transformers, with one difference, they do not offer isolation from shore ground, which is only a corrosion, and not a safety issue. A polarization transformer still behaves as a source, to which fault current will travel, rather than through the water. Most shore power transformers can be wired for either isolation or polarization. If wired for polarization, they also need a galvanic isolator for protection from galvanic current.
Having said all that, just any off the shelf industrial transformer that happens to provide the right secondary voltage probably isn’t appropriate for use aboard, as it may lack, among other things, the necessary shield between primary and secondary coil, and not all meet UL1561 requirements.
I am an advocate for
From ABYC E-11
11.7.1 Shore Power Transformers
11.7.1.1 ISOLATION TRANSFORMERS – Devices used as isolation transformers shall be either encapsulated, dry type or high frequency/switch mode.
11.7.1.1.1 Encapsulated, dry type transformers shall meet the requirements of UL 1561, Dry Type General Purpose and Power Transformer (see E-11.18, DIAGRAM 6, and DIAGRAM 7).
11.7.1.1.1.1 Encapsulated, dry type transformers shall have a metallic shield located between the primary and secondary winding and be electrically insulated from all other portions of the transformer. It shall be designed to withstand, without breakdown, a high potential test of 4000 VAC, 60 Hz, for one minute, applied between the shield and all other components such as windings, core, and outside the enclosure.
NOTE: Breakdown is considered to have occurred when the current which flows as a result of the application of the test voltage rapidly increases in an uncontrolled manner.
11.7.1.1.1.2 Encapsulated, dry type transformers shall have a separate, insulated wire lead or terminal identified as the shield connection that shall be solidly connected only to the shield, and brought out for external connection and shall be equal to or greater than the aggregate circular mil area of the largest transformer phase conductor(s).
11.7.1.1.1.3 The shield and its connection shall be of sufficient ampacity to provide a sustained fault current path for either the primary or secondary windings to ensure operation of the main shore power disconnect circuit breaker when subjected to a fault current level in accordance with TABLE 3A.
11.7.1.1.2 Isolation transformer cases shall be metallic with a grounding terminal provided.
11.7.1.1.3 Isolation transformers shall be tested and labeled by an independent laboratory.
11.7.1.1.4 High frequency/switch mode transformers shall:
11.7.1.1.4.1 meet the safety requirements of IEC/UL 62368, Audio/video, information and communication technology equipment, and
11.7.1.1.4.2 the environmental requirements of IEC 60945, Maritime Navigation and Radio Communication Equipment and Systems: Methods of Testing and Required Results.
11.7.1.2 POLARIZATION TRANSFORMERS – Devices used as a polarization transformer shall be of the encapsulated type and meet the requirements of UL 1561, Dry Type General Purpose and Power Transformers.
Hi John.
Excellent article, and good advice.
One small suggestion, though:
You said
”By the way, an important aside here. One of the most persistent myths around electricity is that it returns to the earth. That’s 95% wrong. In fact, electrical current returns to its source, in this case the main panel—actually the step-down transformer — and eventually the power station, but let’s not get persnickety here.”
Actually, it does not return to the power plant.
Simply because the step down transformer does what an isolation transformer does: galvanically isolates the primary and secondary windings. Thereby, the ’source’ of the current is the transformer – not the power plant (strictly speaking).
The help understand why, think of an electrical circuit as an ”electric drive-belt”. It really does not consist of two wires (electrically speaking) but just one – forming a loop.
One loop between the power plant and the step down transformer’s primary winding, and another loop between the secondary winding and any device you plug in.
Electrical current never leaves either loop (unless there’s a fault, in which case a new loop forms between live wire and ground, instead of between live and neutral). Electrical energy does, via induction. Electromagnetism connects the loops – much like you can connect two drive-belts with an axis or a transmission box.
The belts remain separate, though.
Energy is transferred from power plant to your device one way only.
This of course changes nothing regarding the safety aspects of the system – just a side note.
Here is an excellent series of articles for those interested in more details:
http://amasci.com/elect/elefaq1.html#aa
It should help grasping many of the concepts discussed here.
Hi Vesa,
I see what you mean. I will remove that sentence, particularly since it’s not relevant to the issue anyway.