
February 2022: This was one of the original articles defining the Adventure 40 concept. We are now in the process of further defining the boat by publishing the detailed specification prepared by the French team, who are going to make the Adventure 40 real. These articles will, over the next few months, supersede this one. In the meantime, we will keep this article available.
I have to admit, I have been procrastinating about writing posts about the Adventure 40 systems because this is the area where we will have to make some of the hardest and most unpopular decisions if we are going to produce a viable, reliable, fast, strong and comfortable offshore voyaging sailboat for less than US$200,000, ready to sail around the world. But, I procrastinate no longer, here goes.
Things to Keep in Mind
For those who may be wondering why I’m writing about the engine before discussing the interior it will need to fit into, I need to explain a fundamental Adventure 40 concept:
Unlike most production boats, where an interior that will sell at a boat show is designed first and the systems are then fitted into the space left over, the Adventure 40 design team will focus on the systems that make the boat a fun, safe and easy to maintain offshore sailboat first, and then fit a functional interior into the space that’s left. A radical concept, but a totally right one.
And, if you are wondering why I am putting so much effort into the engine for a boat that is primarily designed to sail, Colin does a great job of explaining here.
Engine
The engine will be about 35 HP, relatively low revving and high torque, based on an industrial block. A good choice would be the Beta 35 based on a Kubota block.
Yes, I know the horsepower sounds low, but I assure you it’s not. As I have written before, many, perhaps most, modern sailboats are ridiculously overpowered, which results in poor fuel economy and premature engine failure due to under loading—diesels, particularly industrial ones, like to work hard.
Also, keep in mind that the Adventure 40 will be a long waterline comparatively light hull form that will be much easier to drive through the water than most modern production boats, which need more power because their hull forms are fundamentally inefficient.
Finally, if I’m wrong about the engine size, always a possibility, we will That said, rest assured that the engine we end up with will be able to drive the boat to a speed to length ratio of 1.25 (about 7 knots) into 20 knots of wind and a 3 foot (1 meter) chop—when the wind and waves get higher than that, no amount of power will drive you any faster, or even that fast, without cracking off and putting some sail up.
Transmission
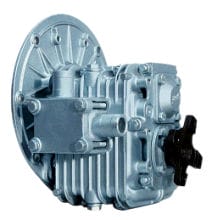
The transmission will be a mechanically activated unit such as the ZF/Hurth ZF15, because this will allow for locking the propeller shaft without use of a separate shaft lock.
The gear will be fitted with a heat exchanger oil cooler, which, along with oversizing the transmission, as I have done, is one of the best things you can do to guarantee that the Adventure 40 will not be plagued by the transmission problems so common on sailing yachts.
Running Gear
The propeller shaft will be of high quality stainless steel (Aquamet 22, or equivalent) that will be at least one size over standard practice for an engine this size. It’s amazing how often sailboat propeller shafts bend or break due to something fouling the propeller—an event that should be a minor irritation, not the start of a major repair job.
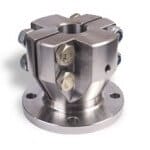
The shaft will be coupled to the engine with a clamp-on split-coupling, with set screws screwed into dimples in the shaft and then wired. The coupling will be faced on a lathe to insure accuracy after it is fitted to the shaft. A DriveSaver will be fitted between the transmission and coupling to act as a fuse in the event of a severe prop fouling event.
The boat will come standard with a two blade fixed propeller but the shaft will be machined to accept a MaxProp, for owners who wish to add one and keep the fixed prop as a spare.
There will be enough bare shaft between the front face of the propeller face and the aft face of the strut to accommodate an owner-fitted line-cutter device.
If there is any doubt about properly supporting the shaft run, two cutless bearings will be fitted, one in the stern tube and the other in the strut—many sailboats have inadequate shaft support.

The shaft will enter the boat via a PSS dripless shaft seal, rather than a stuffing box.
The shaft will be fitted with a clamped collar just forward of the shaft seal boss to insure that the shaft will not foul the rudder or exit the boat in the event of the coupling coming loose; and so that the boat won’t leak catastrophically in the event of the shaft seal rot0r coming loose.
Fuel System
The boat will be fitted with a single high quality aluminum tank with baffles and large inspection ports so that all parts of the tank can be reached for cleaning.
I am hoping that this tank will fit in the bilge, and given the hull form that I favour, I think this is likely. Fuel tank size can’t be specified until the boat is drawn, but I am aiming for minimum flat water range under power of 400 miles at six knots. Because of the extremely efficient hull and relatively small engine, I’m guessing that this will equate to about 50 US gallons (190 liters).
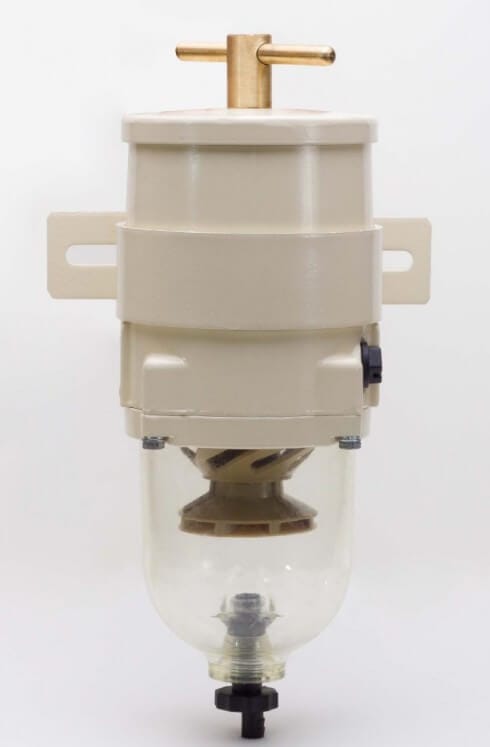
A Racor 500 primary off engine fuel filter will be fitted. This filter is huge overkill for such a small engine, but it is the smallest one I know of that does not have a spin-on element—an invention of the devil.
Alternator
The engine will be fitted with a single 80 amp alternator driven by a serpentine belt. The mounting points and belt system will be robust enough to take a 150 amp large case alternator for those owners that wish to fit one and keep the old alternator as a spare.
Instrumentation
The instrument panel will be supplied with oil pressure and water temperature gauges, not just indicator lights. Loud alarms that can be easily heard in the cockpit will be fitted for low oil pressure or high water temperature.
Oil Change
A permanently mounted oil change pump will be provided.
Exhaust
A standard water lift muffler will be used, but particular attention will be paid to insuring that water can’t back-flood the engine. Precautions may include:
- Center-line U-bend to deck height.
- Surge tube fitted to exhaust outlet.
- Telltale water flow into aft end of cockpit, rather than siphon break.
Access
In order to avoid the use of a V drive, it is likely that the front of the engine will protrude under the companionway steps. These steps will be completely removable.
Access to the side of the engine, transmission and drive train will be from the “utility cabin” on one side of the boat and from a large cockpit locker on the other side. This will result in 360 degree access without too much disassembly. Grubby engine jobs will be doable from the utility cabin with all tools, parts, and a small work bench to hand.
The decision of which side of the boat the utility cabin will be sited will be, at least partly, based on the location of the service points on the engine selected—an example of the ease of maintenance driven holistic design that will go into the boat.
Comment
If you have suggestions to improve this engine specification or questions about it, please leave a comment.
Well, we are both either very right, or very wrong. With a couple of exceptions for scale, and my favouring of an AquaDrive CV unit, even though I have a very different cruiser than the proposed Adventure 40, most of the design and servicing considerations are the same. I’ve got seven more holes to drill before final bolt-down and launch in four weeks.
May I suggest (because they are an option on the Beta lin), either a second PTO for bilge pump, engine compressor for a reefer or for a second alternator, plus a remotely mounted oil filter? Mounting an oil filter vertically oriented on a bulkhead is much cleaner than having it on the side of the block when it comes time to unscrew it or change it out. Cost is about $100.
I have searched the internet for a remote oil filter for my Yanmar and have been unable to find a suitable unit. Does anyone have any suggestions on brand and source?
Thanks
Milton
Thanks,
At one point I thought about machining one myself but that is a little too much work and probably more expensive in the long run sue to the time it would take to design and do the work.
Thanks again for the info.
Hi Marc,
A remote oil filter is a great idea, that is unless the standard one is in an easy to reach place. As to another PTO, I really don’t like cluttering up engines with such things. In my experience, there are better and less complicated ways to add the items you mention. Also, I don’t believe in having two alternators on an engine. I much prefer one large one, and a spare.
All this is based on our thinking that the main engine is a mission critical system that should not be cluttered up with a lot of add-on gear.
For example, engine driven refrigeration compressors are intrinsically unreliable due to the vibration they are subjected too—I know, I have had and removed two—and who needs to have to remove one before you can properly get to the engine for service—there are much better ways to do refrigeration.
John, I actually concur on the refrigeration/engine combo, but some people like ’em…As for the second PTO, my thinking is influenced by the ridiculous amount of access I have in my own boat, which facilitates an engine-driven emergency pump or a second alt dedicated to charging only the start and windlass batteries via an Echo Charger. You requirement for simplicity trumps such elaborations.
Would you consider as a piece of “safety gear” something like a spring or hydraulic starter, however? They are, like bringing a complete spare water pump, basically a swap-out/ bolt-on item that allows either service to be performed on the “usual” starter, or allows a way to start the engine in the absence of compression levers and decent…or any…voltage.
As electricity and (certainly salt) water don’t mix and since an engine driven high capacity (we are sinking) pump may be a life saver and hand starting is out, how about a spring starter fitted as standard ?
Wouldn’t something like this :
http://www.springstarter.com/
or this :
http://www.startwell.com/
kind of thing…
Because
“the main engine is a mission critical system ” and the starting battery can go dead, and probably will go dead, at the worst moment (said Murphy…)
Hi Emilios,
A very interesting idea, thank you. However, unless I’m missing something these spring starters are a replacement for a normal starter motor, so I suspect that people would be less than happy about having to wind one up every time they wanted to start the engine.
Having said that, for those that wish to, carrying a spring starter as a replacement spare for the starter motor might be a good plan. We on “Morgan’s Cloud” have always carried a spare starter motor and been very glad of it on at least one occasion.
Personally I think I would continue to carry a starter motor, rather than a spring starter, since in all the years I have been voyaging I have never been prevented from starting the engine by a flat battery. The secret is to keep the engine start battery isolated and separate from the house bank and this is the way the Adventure 40 should and will be wired.
Spring starters can indeed be replacements in situations (like a bulldozer left outside in the Arctic unstarted for a month) where electrical start may be compromised. The wind up aspect to my mind is trivial considering it would only be used in situations where the stock electrical starter needs a rebuild or when the circuits are fried, compromised or the banks are flat. A spring starter to my mind covers off more bases than a spare electrical starter. I say that having designed a battery bank layout that should see me never without at least two Group 27s (starter and windlass) at 100% charge due to (switched) echocharging off the main house bank and multiple (solar, Honda, wind) inputs beyond an alternator.
I’ve just finished a book, however, in which the owner of a steel boat has a near-miss lightning strike that fries every conduit aboard, leaving her unable to start her engine. So the potential is there, and I’d rather have a “diesel with no volts” option in a pinch. It’s possible I was influenced by the film “Flight of the Phoenix” which featured a jury-rigged plane rebuilt after a crash in the desert that needed a shotgun shell to start!
I think you can install both.
You don’t need a second PTO, you can have a longer shaft and rails for accessories. These are all standard from Beta. Some can be mounted directly n the engine. You can also have a second alternator or a mount for it.
Hi George,
That’s true, but on the other hand the more stuff we hang on the engine the more cluttered everything gets.
Trade-off, as always, isn’t it?
Hi John,
I agree with the horsepower … Our 49 foot Southerly has got just a 53hp but it is quite sufficient to drive us upwind well even in rough conditions. We have never felt we needed more in 12,000 miles so far. So many people think it sounds underpowered (as you say most boats are overpowered). Advantage is much improved fuel economy. With our autoprop we just sip fuel if we need to motor quietly in glassy conditions at say 6 knots.
Hi Paul,
Thanks for the backup on that.
Hi,
I like most of the reasoning, and support the idea of the remotely fitted oil filter. I fitted a fuel polishing system, and am very happy I did, at relatively low cost, also providing me with the option of running either one of two Racor 500 filters. Last, 50 gallons seems way too little, while sailing in remote areas, and would need to be increased if a generator/and or diesel heater would be installed.
Hi Willen,
This is not a high latitude remote area boat and 400 miles is a pretty good range for any voyaging boat of this size, particularly one that sails as well as this one will. In most of the general cruised areas of the planet diesel fuel is readily available. The point being, don’t focus on the number of gallons without taking into account the extreme efficiency of this boat under power and even more while motor sailing (estimate 650-700 mile range).
Or, to put it another way, you can’t compare this boat’s tankage on a gallon for gallon basis with her wide stern competitors that have completely the wrong prismatic coefficient for motoring at speed to length ratios between .8 and 1, where displacement hulls are most efficient.
Having said that, if we can get more fuel in, we will, but we won’t distort the hull to do it. Also, I’m really hoping that we can get the water tanks under the cabin sole too. The payoff of getting all the tanks into the bilge, is huge!
Further, I think adding a generator to this boat, although doable, would be a real mistake. A better job can be done on this simple boat with solar and wind. And a boat like this can be heated with a single bulkhead mounted drip feed stove that uses very little fuel.
“I’m really hoping that we can get the water tanks under the cabin sole too.” Don’t be shy about raising the sole. I’m 5’6″ and many boats are optimized for people whose eyes are much further from the floor than mine. Too often my view out the galley window is all sky. Still I suppose the A40 will have to accommodate tall people too.
Hi PD,
Headroom is an interesting parameter. Even though I’m 6′ 2″ I have never thought that being able to stand throughout the accommodation was that important, and, like you, I value being able to see out.
On the other hand, it seems, from my reading and comments here at AAC, that many people will actually reject an otherwise good design because they can’t stand up everywhere. I think that’s a mistake since it can result in making the boat boxy looking and losing out on a lot of other good things like below sole tanks.
Anyway, the early renderings are showing some interesting approaches to this trade off.
I have just installed a Beta 35. The oil filter is easily accessible, right in the front, and with patience and an oil diaper there is no mess after the sump is drained.
Hi Terence,
Good to hear.
John-
Do you expect that, when it comes time to plan system layout, it will be a goal/priority to ensure there’ll be room for owners to replace the single Racor 500 unit specified with a dual Racor 500 setup?
-J
Hi J Holt,
Absolutely. The whole idea of the Adventure 40 is that the boat comes with what you need, but is easy to customize. There will be plenty of room in the utility cabin to mount any sort of fuel system you might want including an all singing all dancing double filter system with polishing.
the simplest polishing gets by fine with one filter, especially if you also have a day tank which gets only filtered fuel. There is no need for another oil filter between day tank ans engine, except for the one that comes with the engine anyways.
Hi George,
Yes, day tanks are an option, but they take up a lot of room, as well as adding quite a bit of complication and expense, so probably not a good one for the A40. Here’s an analysis of a day tank installation done right: https://www.morganscloud.com/2009/12/18/diesel-fuel-day-tank/
We should have a conversation with Racor. For inboard application you will need to use a metal bowl. I discovered this on a survey about a year ago. The filter must also met the 2 minute 30 second fire resistance test. It is also unfortunate that they do not sell a smaller capacity cartridge type filter. I’m not sure that the vortex water removal of a 50 gph unit will be very effective at less than 1 gph.
Hi Myles,
The metal bowl requirement, is, I’m pretty sure, for gas engines, not diesel. Also, for coast guard rated commercial vessels. And Racor do not make a smaller drop in type filter. They used to (I have one) but discontinued it.
Good point on the vortex, but water will still separate via gravity due to the low flow volume. I have been using a 500 on our generator, which is much smaller than Beta 35, and it works fine and has done for years.
Consider locating the pre-filtering system away from the engine where it is accessible. This eliminates proximity to the heat source. Too often, too much ‘stuff’ is jammed into the engine space. Also, while we sailors are somewhat enamoured with the Racor filtering, I would suggest we listen a bit more to our power boat compatriots. Consider what is referred to as a mud canister filter followed by a fuel/fuel-water filter set-up canister. Racors are known to become clogged and if the fuel flow is not sufficient, it will not turn the turbo. Also, draining the crud out of a Racor is both messy and prone to fuel spills. Also consider a separate electric fuel pump — very handy for priming the injector pump as well as a back-up for the on-engine fuel pump.
Hi JoeC,
There will be plenty of room around the engine, plus a utility cabin right next to it, given over to systems, so you would easily be able to add that stuff to your A-40.
Hi John,
You won’t hear any objections from me about choosing a more reliable and lower maintenance drive system instead of a cheaper and somewhat quieter sail drive!
Regarding the choice of locating the cockpit locker port or stbd, for me there are more important considerations than ease of access to one side or other of the engine. When I go below on a boat with the galley on the stbd. side it just feels “wrong,” especially on a boat of this size. Galleys are traditionally on port for reasons having to do with right of way when hove to. However there are ergonomic reasons for a boat with a U or L shaped galley and sinks near centerline facing forward * to have the galley on port. For the majority who are right handed, this allows you to work at the sink or stove with your right hand while using your left to hold on or brace yourself in rough conditions. Stbd. galleys are at cross purposes for most people, and therefore the proper location for any deep cockpit locker is on port behind the galley.
*If we have a low/no bridge deck design for all the reasons discussed previously, the sinks cannot face aft for lack of room.
Richard
Hi Richard,
Very good points. Everything is a compromise! I have to say that emotionally I’m exactly the same. Starboard galley…what are you, some kind of weirdo? 🙂
While I had always felt, “over my dead body”, I ended up spending a few months evaluating Saildrives, because essential design goals couldn’t be solved with shaft drives.
i was extremely surprised to find out that saildrives are much, much better than their reputation. There used to be quirks in the early models, but that is taken care of. Most problems stem from omitted oil changes or neglected anodes.
do regular maintenance, carry essential spares, and it should be just fine. One boat has done the NWP with saildrives – no problem at all
the driveleg that Beta sells for the 35 and 38 is rated for 60 HL – a nice reserve.
Hi George,
I now have a boat with a saildrive and based on that, would far prefer one with a direct drive. More on the drawbacks with saildrives that make them inappropriate for the A40, a boat where we want to minimize maintenance complications: https://www.morganscloud.com/2019/07/03/why-are-saildrives-even-a-thing/
thanks for the link; will need to read that carefully. Based on a quick read, the key issues won’t apply for us – we will have to watch anodes carefully anyways, considering that we have an aluminium hull, and we use keel cooling and a dry exhaus.
I would like to ask why you do not install something like a Brunson Autoprop as initial equipment? I re-engined by Fisher Freeward 30 with a Beta 35, larger than I needed but more economical than a 25 when producing 20-25 horsepower, the figure that was needed. I installed a ‘Deep Sea Seal, very effective but allowed water in after changing from reverse to neutral in a very cold Hamburg, fortunately I spotted this before leaving the boat. I find the Autoprop very effective, adding about one knot to my sailing speed and eliminating the need to lock the shaft when sailing. It also maximises the use of whatever the current power setting is on the engine.
Denis
Hi Denis,
I’m sure the Brunson is a great product and I personal would never own a sailboat with a fixed prop, but if we are going to hit the price point we must concentrate on needs, not wants. Also, different owners will want different prop options, so let’s let them make up their own minds, rather than charging them a bunch of money for a prop they may not like.
And, after all, any voyaging boat should carry a spare prop, so the two blade fixed prop is not lost money.
Not sure what happened with your “Deep Sea Seal’ but I have been using a the dripless seal specified above for 20 years and thousands of hours of engine time without it ever causing a problem or letting a drop of water into the boat.
John,
I think the rubber mounting attached to the prop shaft became stiff when very cold and the change from reverse to neutral allowed the shaft to move forward a few millimeters. The cold rubber did not have its normal ‘spring’ and therefore did not apply enough pressure to the seal face. I did a few changes from forward to reverse and the seal started working again and has continued to behave itself. I will be examining it as soon as I get the opportunity.
Denis
Hi Dennis a bit late but can i ask you what size prop you have installed for your engine…i got a similar boat…thanks Ed
Hi Ed,
The propeller is an H5-442mm diameter Bruntons three bladed Autoprop. This is approximately 17.5”. My Fisher Freeward 30 cruises at six knots at 2,000 rpm. She will go faster but this is the most comfortable speed.
Further to the Deep Sea Seal comments: When the Beta 35 Engine was installed I was not happy that it was fitted at the highest adjustment of the mounts. I had made a number of complaints to the installers who had proved to be pretty incompetent, I was fed up and impatient to be off and decided to rectify the situation later by fitting blocks under the mounts. Following the Hamburg leak incident, during our return from Norway and subjected to quite severe rolling I noticed, I could not help but notice, vibration and noise at the extremes of the roll. Freewind went into a boatyard for a refit including the installation of the blocks. The boatyard called me to inform me that the engine was basically loose, fully floating and only held in place by the coupling! The longitudinal engine bearers had parted company with the transverse webs which were, fortunately, still glassed in and the rubber in all the mountings had been torn away from the metal. This engine movement had obviously flexed the propshaft causing the seal to distort and damaging the sealing faces, hence the Hamburg leak. The engine is going back in onto new flexible mounts on a stainless steel engine bed properly bolted to the webs. A new propshaft and new PSS seal will be installed.
I am sure I do not have to spell out the two morals of this story, but I will: Do it now and do it right!
Denis
Wow thank you so much for your reply…so helpful…like you i have had the engine installed and noticed they are high on the mounts at present…i was worried about this and told about this and they prepared some blocks for me but didn’t yet get round to installing them…my engine bed is not ssteel but metal coated in plent of primer…i think that should not be a prob becaues they used the holes of the previos engine which were through bolted …
Dennis might i ask do you know the pitch of your propeller? …i am installing a three blade fixed so i can compare ? is your reduction 2:1?
Cheers
Ed
Hi Ed,
The Autoprop is self pitching, it adjusts in response to the combination of power input and boat speed through the water. Their website has a pretty good demo video illustrating the propeller function.
Following my experience, even though I was aware of the inadequacy of the installation the actual loads that must have been developed surprised me, I would not delay in putting things right!
I have some photos of the propeller if you would like me to send them to your e-mail address?
Denis
Thank you very much Dennis…noted in fact i havent’t used it much after installation and that i didn’t run into any issues but in fact it when it was running it looked as though one fine day it could just snap as the vibration is amplified at that high level..infact the operations manual mentions this…at least the mechanics agreed to correct it but i was going to start getting complacence about it until i read your experience.
..don’t worry about pics ill look up the website to find out more but will probably be going for a fixed type in my case as i got quite some expenses to do on other things..thanks Ed
A Brunton that size can be had for a couple thousand £$€, and you make that back in fuel savings fast, especially at today’s prices.
Hi George,
That’s true, and will certainly be an option for those who want to fit one. That said, the big drawback with the Bruntons is that it requires a shaft lock, so more money and complication. On the other hand, if the engine has a mechanically activated gear it may be possible to get away without the shaft lock but that would depend on the gear manufacturer being happy about the spin stopping loads on said gear.
Anyway, $2000 is a big chunk to add to the price for a prop that some users may not want, particularly since the fuel savings won’t be that big on the A40 because the engine is right-sized: https://www.morganscloud.com/2015/06/02/understanding-an-engine-fuel-map/
There have also been issues with reliability on the Brunton props so we would have to be very sure that was fixed before selecting it as standard.
Hi John,
Yes, painfully aware of the shaft lock issue. On the planned engine size for the A40, you can have a mechanical clutch gearbox, so you won’t need the shaft lock.
Depending on engine use, the cost may be recovered quite quickly and if you have a feathering prop anyways as to not to impinge sailing performance, it’s pretty much a wash.
To my knowledge, the reliability issues are a thing of the past. I’ll find out ;-( …
It all looks good! Inevitably, one keeps on thinking of more useful stuff, so I salute your courage in starting this whole thing off! Here’s my two pennyworth of grief: exhaust overheat alarm device, coupled with the Speedseal run-dry modifications to the raw-water pump, plus even the run-dry impellers from the same people as the DriveSaver. Speedseal alone is a brilliant little idea, and not expensive: run-dry impeller would be the icing on the cake.
I know the idea of the tell-tale water-flow onto your feet in the cockpit is much more reliable than syphon-breakers (ugh) and it ought in theory to give you some warning of a blockage, but familiarity breeds inattention (at least in my life…) and nothing beats a sudden squawking alarm, at the cost of some more (cheap, pottable) electronics.
Hi Nick,
You could certainly add all that to your Adventure 40, without any problems. We have to keep the standard boat simple though, if we are going to hit the price point.
My latest engine is a Beta 50 driving my 40′ overloaded liveaboard (as distinct from cruiser:-) It is a very nice simple engine with full instrumentation and alarms, accessible oil pumpout, remote oil filter etc.and I think it would great for your project in any suitable horsepower. In general what you describe sounds perfect but…..
I wonder about your choice of an aluminum fuel tank. In my experience an aluminum tank has a limited lifespan. Admittedly it may be 10 years or more but at some point they all seem to develop corrosion pinholes from the inside or outside. I would think this would be aggravated by locating it in the bilge. I think a properly constructed “free standing” fiberglass tank gelcoated on the inside and made of modern resins would be a much better and longer lasting solution. I do not know the cost comparison but I do know that tank problems can be a major pain in the……butt.
While the bilge is an attractive location it makes a drainable tank sump problematic and I have always thought they made a lot of sense.
I am anxious to hear your comments.
Ed
Hi Ed,
Most aluminium tanks that fail are the result of using the wrong (brass) pickup tube fittings, or poor welding in the first place. Also, many are made too thin and therefor oil-can, which causes fatigue cracks in the welds. Properly done, with aluminium pickup tube fittings (available for aircraft) aluminium tanks last pretty much indefinitely.
I have heard bad things about seepage and smells from fiberglass diesel tanks, but have no personal experience. Richard (RDE), and thoughts?
I don’t like sump drains and would certainly not move the tank up to get one and lose all the space benefits of bilge tanks. Having said that, you make a good point about the importance of being able to drain contaminates from the tank.
Let’s just add a separate pick up tube to the lowest point in the tank with a valve and hose fitting on it. Just connect a hand pump, turn on the valve and pump out. Also could be used for a fuel polish pickup for those that wish to add such a system.
Given the choice, I will almost always specify cross-linked polyethylene for fuel tanks in a fibreglass or wood hull. Good XPLE tanks are virtually indestructible, cannot corrode, and are immune to just about anything you can imagine spilling in a bilge.
Aluminum is quite adequate if done properly. The trouble is, it takes a lot of skill and planning to do them properly, and many builders cut corners here.
Tank replacement after 20 years would be tolerable if you could do it without ripping up the whole interior. If you’re using metal tanks, the cabin sole should be designed so it can be lifted, and the tanks replaced, without tearing all the furniture apart. It’s rare to see a boat where that is the case, though.
Hi Matt,
Sounds like a good option. I have no experience with such tanks. My only worry would be that if there was any flex in the tank walls they might fatigue and crack over time? Anyway, bottom line, I’m not married to aluminium tanks if there is a better and offshore-proven alternative.
One thing I will say though. I know well done aluminium tanks work. If we change from that, we must be absolutely sure the alternative will last. Until you have experienced 50 gallons of diesel in the bilge due to a ruptured tank half way to Bermuda, as I have, it is hard to comprehend how horrible it can be.
I agree entirely on the access issue. All tanks must be removable without breaking the boat up.
Plastic is not very rigid and must be adequately supported. But that’s true for most materials in the thicknesses used for tank walls. As for fatigue, well, try to break a Ram-X canoe sometime- they’re made of the same stuff, and you can wrap one around a rock, kick it back into shape, and keep going.
I’ve seen and heard about far too many fuel system issues that traced back to tank corrosion and welding flaws. Why plan for a 20-year design life when you can get 50 years of service for the same price?
The potential of corner cutting during construction is obviated by purchasing them from a reputable supplier who is exclusively in the marine tank business.
Agree on the use of fibreglass fuel tanks. If you go that route they should be finished with vinylester. Also the tank should be designed with a low end and equipped with a way of draining water contamination — a tap. Siphoning is is laborious, can not reach areas blocked by the baffle. As for fuel polishing, that is happening when the engine is running, but unfortunately does not reach the crud and water at the bottom of the tank.
As a postscript my 1975 Gulfstar has gelcoated FG tanks isolated from the hull and still going strong with no noticable seepage. I have seen serious seepage problems with built in tanks. The Alden Challengers are a prime example with diesel fuel coming right through the bottom paint.
Tankage seems very reasonable. I recall conversations on the dock before crossing from Mexico to the Marquesas. Lots of people were comparing fuel capacities and motoring range. My comment “you can’t carry enough fuel to motor the whole way folks. Sooner or later you’re going to have to SAIL”
Some surveyors don’t like the plastic bowl Racors but I do think it’s only a requirement on commercial vessels.
Hi Evan,
Nicely said.
Hei Evan
I just love that comment.
Hope you don’t mind if i bowwor it?
all i can offer are a few cost-effective ideas for consideration:
a) an alternate engine coolant intake line that taps the bilge seems to be a worthwhile expedient to better cope with heavy flooding…would need periodic exercising to stay in good operating condition (occasionally stick the line in a nice size bucket after switching it on maybe ?)
b) maybe have hand crank capability in case of starter failure ?
c) maybe have an run-hours meter to facilitate good maint intervals ?
then here are a few non-engine considerations while i have them on my mind:
some mast steps maybe ?
presume there will be life raft storage ?
cockpit locker seals well engineered for effectiveness
cheers
richard in tampa bay, s/v lakota
d)
Hi Richard,
Sadly, hand crank engines are almost unheard of these days. One of the problems is probably liability. Hand cranking an old Lister was, if you did it wrong, extremely hazardous to your wrists.
Yes, hours meter will be fitted and RPM too, I just forgot them. Thanks for reminder.
See the rig post for the other stuff.
I think too much emphasis is placed on horsepower, whereas Brake Mean Effective Pressure (BMEP) and torque at given revs and the shape of the curve is more an indicator as to what an engine can do, in combination with the correct gear ratio and prop. I think one should design from the point of view as to what cruising speed is optimal and in what conditions, in comparison to achieving hull speed at say peak torque. Backing off a knot or so from hull speed would give far better fuel consumption if operating around the sweet spot of the engine. I doubt you would want to punch into weather at hull speed. I’m also curious about the locked prop and if this is a function of the gearbox design? The fuel filter/s and oil pump solution are great and pracatical must haves. I wonder about making sure a good marine alternator and regulator are fitted, to ensure as optimal battery charging as possible – a major consideration. Why run an engine if you don’t have to.
Hi John,
I could not agree with you more about torque. That’s why the Beta Marine. I have written at length on this site about the benefits of torque (use search box) and the importance of being on the right place on the curve at cruise RPM.
As to hybrids. A fundamental of the A-40 is reliability, therefore there will be no leading (bleeding) edge technology on the boat.
Locking the shaft has also been dealt with at length on other posts. Point being the ZF/ hurth will let you do either. Also, you must lock the shaft to get some types of feathering props (Autoprop) to feather.
Regulator will be discussed later under electrical. Rest assured it will be good.
Autoprop feathers without locking the shaft, at least mine does.
Thoughful reply. Thanks. Totally agree Torque is King!
Hi both Johns
An often unnoticed problem with new build engines (or replacements) is that any interference with the alternator will invalidate the engine warranty. And as most alternators supplied OEM are machine sensed, that’s less than ideal.
Which was the case with our Volvo, which has a 115 amp Hitachi, but being machine sensed you don’t get that kind of output for long. Nor, I have always been told is there much point in fitting a ‘smart’ regulator with a machine sensed alternator. Which is why later this year we’ll be installing a Balmar alternator of comparable output (or maybe slightly more) with a matching smart regulator.
We’ll keep all of the old wiring connections intact so that the Hitachi can be used as a spare.
Best wishes
Colin
Hi Colin,
Good point. One of the things I like about Beta marine is that they are flexible about custom alternator options on new engines. I’m pretty sure the builder will be able to come to a deal with them to supply an externally sensed alternator, and large enough hardware for up to 150 amp replacement, from the factory, with a full warranty.
Hi John
Well chalk up another big plus for Beta marine – great to hear about a firm that puts the interest of the customer first!
Best wishes
Colin
Like Colin I agree that is excellent. As you know i’m not an electronics engineer, however this guy raises some good points about alternators/regulators. http://www.smartgauge.co.uk/controllers.html In addition to those points I’d be interested to hear what charger you will run, how many and what type of batteries and if you intend to carry any kind of generator be it towed, hand portable or installed. I believe you will have some solar and wind?
Some of us on the west coast are faced with some long stretches of motoring on the return from Mexico. We typically face adverse winds, seas, and current on what’s often referred to as the “Baja Bash.” Those more adventurous will go from California up to the Northwest. Our principal cruising grounds are Mexico and the Pacific Northwest. Those with luxury of time and ability to be out of touch for extended periods and sail from Mexico to Hawaii and then north from Mexico and around the Pacific High for the return to California or points as far north as Alaska. Our boat is “overpowered” per se, but the reality of the matter is, that we can maximize weather windows in our favor thanks to generous tankage and a turbocharged Yanmar that can keep us moving at over 6 knots in conditions where other boats are lucky to make 3 knots.
I think the design targets are perfectly adequate for the east coast buyers but it would be nice to see an option for slightly more power and fuel capacity. We do have some fuel stops along the Baja, namely Magdalena Bay which is time consuming, and Turtle Bay which is convenient but also known for watery fuel and overcharges. The only honest fuel vendor Turtle bay just passed away recently.
For me personally, I’d like to see enough fuel capacity to make it from Cabo to Ensenada, but I realize that may not be possible in a boat as small as 40′.
Hi Dave,
I hear you on the benefits of lots of fuel and a powerful engine. After all I own a boat that carries 290 gallons and has a 87 hp high torque engine.
But that’s not the Adventure 40. The Adventure 40 owner will, in the situation you postulate, hunker down, put her on the wind and sail, just like we used to do. This will be more palatable than you might think because she will be much closer winded than your boat or mine.
I have friends that do the whole area you mention in a Cal 40, with even less fuel and an even smaller engine, and they do fine.
And, just as a reminder: no options, none zero zip. Options will ruin the reliability of the boat.
Hi John,
I’m kind of with Dave on this one—. Spent 7 years cruising Puget Sound on a boat that was definitely underpowered, and I will say that when you are dealing with the tidal currents and summer weather patterns between here and Alaska you don’t have the option of “putting her to weather and just sailing”. You’d definitely be happier with a 3 blade prop (preferably feathering) and another ten horsepower. And on my delivery passages down the coast and to Panama we always seemed to have light or no wind behind us (Mexico south) or no wind or 30+knots (Pacific Northwest offshore)
So motoring capability is important. (As an aside, my Kiwi friends told a story about towing Lin and Larry Pardey through a pass in the Tuamotos. Seems even the most experienced advocates of pure sailing had problems with tidal currents that they couldn’t overcome with only 1 personpower and an oar for propulsion.)
37 hp and a fixed 2 blade prop may still be the best choice for the A-40, but it won’t be optimal for the West Coast.
re glass tanks: I’ve built them and coated them with multiple layers of epoxy resin inside, but never had the customer come back with either a baseball bat or a bottle of fine wine in hand, so I’ll withhold comment for lack of direct experience or feedback.
The one substantial advantage of molded fiberglass tanks vs. polyethylene when they are intended for the bilge is that they can be molded to the actual shape of the cavity, thus eliminating the need for side support and gaining fuel capacity while still making them removable.
Hi Richard,
Now there is a good point. Could make a signification difference to the range. Just when I thought we had that one all figured out!
Hi John,
When one is managing the construction of a complicated project, the planner must organize his materials and labor flow around the constraints of necessary process sequences. It just won’t do to try to put the roof of the house on before you’ve built the walls! Project management software is designed with links and critical path chains to facilitate this decision process.
Good design actually needs to proceed in the same way.
In the case of fuel tank material the correct decision can’t really be made until the hull form and interior design are known—(unless in fact there is only one satisfactory material.) Tankage size, location, and optimal materials may look quite different in a boat with a deck salon and two-level floor vs a low trunk cabin or flush deck.
Once the available space is defined, cost vs budget, tank capacity vs ease of construction, durability vs cost, and in-house build vs subcontracting can be analyzed in a priority tree and a final decision made.
Hi Richard,
I agree entirely.
Going up to the 43 or 50 wouldn’t cost so much more if you can stomach the weight
Hi George,
Yes, but that would actually be a negative, not a positive since the A40 would not be able to use the added power so fitting a bigger engine would increase fuel use and worse still the engine would glaze up due to under-loading. We have a full online book on optimizing engine size that you may find useful: https://www.latitude38.com/lectronic/whitall-stokes-departs-solo-circumnavigation/
Close winded ability doesn’t mean all that much when the seas are large and steep, and winds 20-30 knots or more. You end up having to crack off a fair amount due to sea conditions. Question is will the potential buyers of an A40 have the same mindset of your friends with the Cal 40? The west coast is possibly not that large a market for the A40 so it could be a moot point.
Cruisers from the east coast or Europe rarely experience our coast. Most will pass through the canal and continue to the South Pacific. It’s a dramatically different set of cruising grounds than anything they’re used to. The payoff is we have places like the Sea of Cortez and Puget Sound. It’s just a lot of work to get north unless you have the time and inclination to sail from Mexico to the Northwest via Hawaii in which case the trip is somewhat tolerable. The approach embraced by many of us is a strong diesel and adequate tankage. We can be back in a matter of weeks as opposed to months.
As RDE stated, the 37hp will work, but won’t be optimal for the west coast.
Hi Dave,
Yes, all true. I have always had admiration for you West Coast sailors—a much tougher cruising ground than the East Coast of the Continent.
Having said that, I really can’t see how a big engine helps you going to windward once the true (not apparent) wind gets over about 25 with a steep sea offshore.
“Morgan’s Cloud”, even with her old 120 hp engine would only be able to make about 4-5 knots into that steaming and it would be brutally uncomfortable with a huge fuel burn. And this is a 25 ton 56 foot boat with very fine ends that motors better than most motor boats.
Our strategy in those conditions is to hoist the main and staysail, unroll a little jib-top and motor sail. Speed goes up to 7.5-8 with a very close tacking angle and it is much more comfortable. Fuel burn goes to less than a gallon an hour.
Beat all the way back from Svalbard to Norway across the Barrents Sea (600 miles), with the wind never less than 25 knots and as nasty a sea as you will get anywhere, like that and it worked great.
Point being that no matter how much power we put in the Adventure 40 she is not going to motor up wind successfully into 30 knots and a big sea.
But what she will do brilliantly, due to her easily driven hull, is motor sail in the same conditions, very comfortably, and burning less than half a gallon an hour, so range, even with 50 gallons, will be huge.
I think effective motorsailing is like heaving-to: a process where every boat going has its own little peculiarities, and which people don’t necessary have in their armoury of techniques, although I suspect that is less the case in this venue.
I don’t see a lot of motorsailing. I see a lot of sailing and TOO MUCH motoring. I use motorsailing on both my boats because I prefer the motion and I am realistic about our steel boat actually falling in the hull form and displacement class for motorsailers. But it requires certain (and on my boats, differing) tweaks of mainsail and course to get both a comfortable ride, no chafe or slatting and enough draw from the sails to both reduce fuel burn and to get a couple of free knots SOG due to sail trim.
Another rarely discussed topic of motorsailing is how ballast allocation can make a difference both fore and aft and high-side/low-side. I have cross-transfer pumps as part of my new watertank layout as I think 20-25 days on one tack in certain places (although probably not in great wind the whole way) make such considerations worthwhile.
Perhaps your motorsailing tips (when to do it and how to do it for max. comfort and SOG) could make for a post, if it isn’t already in there?
Hi Marc,
Good idea, I will put it on the post list.
I agree on a second PTO – it is highly recommended. As far as fuel and lube – I’d find room for two identical Gulf Coast Filters, one plumbed as the primary diesel fuel/water filter/separator and the other as a bypass oil filter (plumbing is what makes them an O-1 and a F-1, otherwise the metal canisters are the same beast) Both use a paper towel roll (i.e. Bounty) as the paper element which means no more expensive or hard to find canisters or proprietary elements. While I understand the mounting size and position limitations I think the steel canister and bullet proof design and operation benefits are superior and on a world cruising boat you would be crazy to use anything else.
Note: smaller GCF o-1 JR and GCF F-1 JR may be available on special order so please call the factory for the latest details. You will be glad you did. No association, just a satisfied customer.
Kubota – been using one aboard as a genset since 2002 – just keeps going strong… with a diesel and a bypass lube oil through GCFs. No need to say more – the secret is clean fuel and oil and it will out run you… so easy to service – unscrew top, lift out into 5 gal bucket, remove element, drop a new element onto the spindle and re-insert, fill with fluids, tighten down lid. Round trip service takes just minutes. And you can see the element – so now you know what is going on inside your fuel tank and engine lube. Try to see inside with the expensive metal canister filters.
Hi Douglas,
The Racor 500 does not use metal canister filters. It uses paper so you can see contaminates. Good as they are, two GCF are going to take up a lot of space on this boat and are, I think, overkill. Still, just the kind of customization the A-40 is designed to support.
Glad to hear that the Kubots have done well by you.
Sounds like you might be trying to fit all of this into a tight space… even though you say otherwise… the Racor 500 is not approved on inspected boats because the bowl can break – a metal guard is required… and might I add that the heat in a tight engine space is another potential problem… its 94F today in Panama – get those batteries etc out of the engine room heat… remember this is going to be a world cruiser and heat is going to become a number one enemy sooner than later… I’d even plan on running dedicated dryer aluminum flex venting (3-4″ dia) with bilge blowers or muffin fans to the back of each alternator for improved ventilation resulting in increased output (over 30% has been my experience with Balmar external regulators showing a 25F reduction with blowers) and easily doubling the alternator life. Heat kills. That said – I’d find room for the GCFs too. Contact me offline for more specific recommendations.
The dedicated blower setup is a good idea if it is in the form of drawing cooler air from the bilges into the engine spaces and blowing engine “room” air out of the boat. Some people I know have converted bus heater blocks (or for some reason, heater blocks from Cadillacs and Lincolns…) which are diverted from heat exchangers plumbed into hot water heaters into wet locker heaters to provide “gentle heat” to dry foulies and boots.
The more robust sort of muffin fans (4″ or so) are very useful aboard for proper air circulation. It’s perhaps beyond the range of this current discussion (as was my “moderated” post), but it does acknowledge that even modest power plants like the Beta 35 produce a great deal of waste heat that can be utilized safely and productively.
John,
I think that you are continuing to do an excellent job of trying to strike the balance that the A40 is. Here are a couple of thoughts.
I think that 35 hp is reasonable. If you asked me to pick one before this post, I would have said 40 so not that different. We have a bar crossing to do every time we leave the mooring so I definitely appreciate having a decent amount of power but having a hull that moves through the water, especially rough water, well makes a much bigger difference.
Have you looked at the Campbell Sailor prop http://www.westbynorth.com/ ? I know of very few 2 bladed props that really bite well when it gets rough and the issue becomes the prop, not your engine’s power rating. These props have relatively low drag under sail, excellent motoring characteristics, excellent reliability and a cost comparable to other fixed props.
You mention having two support bearings on the propeller shaft as a possibility, has anyone checked the specifications for a drive saver? It is generally considered bad practice to put 3 bearings on a shaft without a coupling that can flex radially (and potentially axially depending on how the bearings are constrained). The only real exceptions to this are for really flexible shafts or when 1 bearing does not constrain radially. Marine transmissions have a bearing on the output so if the coupler is rigid, then a single shaft support bearing on the other end would define it. The reason that we don’t like to over constrain them is that it really hurts your driveline efficiency and wears out bearings quickly.
I think that the spec looks great.
Eric
I have use the 3 blade Campbell Sailor prop for two years. It replaced a 3 blade fathering prop that finally wore out. I don’t notice much different in the prop drag and I notice a HUGE difference in thrust and power. The Campbell is much better. I can rev the engine (Volvo D1-30) to 3100 RPM (3200 is max) and get 6 knots with a 16000 pound boat at 2100 RPM. Prop is 15×9 and looks tiny compared to the old JFProp. The Campbell blades are cupped. The only downside is I need a lot more revs in reverse to get good stopping power.
John
Keep up the good work. At least on this boat, we will all KNOW about the compromises made, rather than funding out after purchase.
To support Matt’s comments on XLknked HDPE, I have sold five hundred gallon tanks to hold high specific gravity liquids like alum for treatment plants. They are TOUGH. Seen videos dropping large tanks full of sand from top of forklifts. They can be repaired with a heat gun and a melt stick.
What are your thoughts in Webasto forced air heat?
Remember tall people when we get to the cabin.
Go, John, Go!
Hi Ray,
Thanks for the encouragement and for the great information on HDPE tanks.
One thought I did have about such tanks: Is it possible to fit them with large clean out ports that are both reliably leak proof and relatively easy to remove? I know how to do that in aluminium, but I have not seen it done in plastic. Also, is it possible to fit such a tank with baffles?
Hi John
To see just how good these tanks can be, have a look at Tek Tanks (www.tek-tanks.com), another excellent UK based company. I’ve recently had the opportunity to look at some of the work they’ve done for Boreal, which was first class.
Good to see we can still do some things right in the UK (ditto Beta Marine)
Best wishes
Colin
Hi Colin,
Thanks very much. Well that pretty much answers all my questions, thanks. I really like their implementation of clean out hatches. Very like what we have on MC.
Looks like we go with plastic tanks.
Thanks, Ray.
Can I add another thumbs up for Beta – and in addition to great engines a plus is that their sales and after sales support is first rate.
John,
Thank you for the fun and informative web site. The Adventure 40 development is intriguing to me as I consider other boats besides my old Islander 36.
Have you considered a diesel-electric power pack? In principle it should be the most efficient and compact solution (and most quiet). For example a 5 to 10 kW diesel generator charging batteries that drive a 5 to 10 kW electric motor….
Steve
Hi Steve,
We have discussed diesel-electric and hybrid at length in the comments to other posts in this series.
The short answer is no, I’m not considering diesel-electric for the A-40: too expensive, too complicated, and doubtful if such packages are materially more efficient than a modern diesel with a auto-pitching prop.
The last opinion came from Greg, service manager at Billings, one of the most experienced diesel guys anywhere.
To add to John’s comments, hybrids are very hard to justify in sailboats in my opinion as they lack any real advantages and have plenty of disadvantages. It is important to distinguish between the two types of hybrids, series and parallel. What you are describing with a power pack that has no mechanical connection to the propeller is a series hybrid. A parallel hybrid would have both the electric motor and the engine attached to the driveshaft.
Series hybrids tend to have poor efficiency due to the number of energy conversions. Energy starts in chemical form (fuel), gets turned into rotational kinetic energy (engine), gets turned into electrical energy (alternator), and then gets turned back into rotational kinetic energy (motor). At every step, you loose efficiency and the steps are compounding. There are a few applications where these do make sense. One is big locomotives and other applications where immense torque is required at zero rpm because we have not yet figure out a way to design a good torque converter to do this. Another is in an application where peaking is required but the nominal load is quite low, in this application the system basically runs the engine at maximum efficiency at all times and then a bank of batteries provides a few seconds of boost when it needs it. The final application that I can think of where it makes sense is where an engine won’t physically fit and it needs to be mounted remotely.
Parallel hybrids don’t suffer from the series efficiency losses but they still don’t make sense in most cruising boats. At steady state motoring along normally, all the electric motor/generator does is provide extra parasitic loss (things like bearing friction) as it is neither generating nor powering. If you were to use the motor to add power to the shaft, then you would be drawing down your batteries so at some point you would need to reverse the process and draw power out of the system and recharge the same amount of energy. The problem with this is that you would loose energy through energy conversions on every step so you would be making the system less efficient than simply using the diesel engine. On a boat, there really is no such thing as regenerative braking during normal use unless you actively use your propeller as a generator when sailing so you don’t get a benefit there.
The major exception to my arguments against both series and parallel hybrids would be if you had an alternative way of charging the batteries and you had an enormous battery bank. Assuming that you would use an average of 15 kW on a 40′ boat when motoring, an 8 hour day of motoring would be 120 kWHrs. For reference, a single 8D battery typically has around 2.5 kWHrs of capacity so the bank would need to be enormous. Alternatively you could try to generate the power as you went but this is impractical as well as most solar panels that you see are 0.1-0.2 kW, only a maximum of 1/75th the power needed even at maximum solar efficiency. The one place where you could store enough energy and recharge fast enough is on a boat that doesn’t motor much such as a daysailor with a big battery bank and has a grid connection at night meaning that it is kept on a dock with shore power.
Hybrid cars are somewhat popular but they have a very different load profile than on a boat. The prius is an example of a parallel hybrid and it benefits from the fact that cars spend a lot of their time at conditions other than steady state. It can have a smaller engine and still get decent acceleration thanks to the electric motor that takes care of peaking and it can also capture some of the energy that would otherwise go into heat when braking. The volt is an example of a series hybrid and its real strength is that you can plug it in. The volt would never make sense for someone who drives long distances regularly but makes sense for commuters who could almost always charge off the grid. Both cars benefit a lot from improved aerodynamics, rolling resistance and low weight, the actual drivetrains are not as efficient as many think as the rest of the car accounts for a lot of the efficiency increases.
I hope that this is not too far off topic.
Eric
John/Eric/Steve/Edmund von der Burg,
Firstly I think Eric’s comments are misleading and to some extent inaccurate in terms of efficiency and only tell part of a story. Understandable in terms of the original thread. Rather than go into the reasons which are outside the scope of this thread I wish to state matters this way. It is all about a given person’s criteria and what they want to achieve. In that sense there is a place for all the technologies, John and Eric mention. It is worth bearing in mind electric propulsion was here before the diesel and in the last 15 years developements in both technologies and the combinations of them has increased choice both through improvements in the technolgies and their associated costs. John’s choice, to my mind as a marine engineer (albeit originally steam!) is the right one for the Adventure 40. It could be put thus. KISS. Keep it simple stupid. Whilst a given sailor’s choices come down to how and what want to achieve with the propulsion – and in this day and age the power generations systems which are also important, along with the design of the boat which dicatates or guides what and which systems can be fitted. Again and in that sense – the way John is going about designing his systems, I think is perfect. In my case and for what I want to achieve and bearing in mind my boat is a cutaway keel, 26ft, double ender – then my pure electric non geared electric propulsion is far more efficient than any diesel engine, as are the calculated running costs. Not to mention simplicity. Also, by adding in a small portable petrol generator it gives the option of a serial hybrid configuration I still achieve savings all round in terms of simplicity, weight, space and cost per mile BUT of course there are compromises and that all comes down to what you want and how you want to sail. That is what I want to learn and how to do that better, so any motor is an inconvenience – if a worthwhile safety feature. Like Eric suggests we could go off topic here and possibly cover old ground, yet we cannot ignore developments in technologies. But if we stick with what John’s criteria are then it would be a more marketable boat if put into production. Going out on an apparent technological limb is for folks like me. I never did like being mainstream 😉
I guess the main questions that have been discussed here about auxiliary propulsion of sailing yachts come from the (quick?…) application of the normal way of deciding needed power for motor-boat, to sailing boat, and of the specificities of diesel engines.
For a motor boat, you must first calculate efficient cruise parameters and then check if the corresponding engine & propeller fulfill all the other propulsion constrains (max. power needs…).
– To decide efficient cruise parameter, you must first calculate or test hull efficiency at different speeds in normal weather & sea conditions. It gives you the normal (efficient…) cruise speed for the boat. Then you must calculate the most efficient propeller to obtain that speed in those conditions and the most efficient diesel engine + gearbox to obtain the needed propeller power and RPM. This way you get the max efficiency of engine and propeller at the efficient hull cruising speed that has been chosed at the first step.
– Then you must check if this engine & propeller fulfill the other constrains you have, wich might be, depending on the type of motor-boat, max speed in normal weather & sea conditions (motor-yachts…) or capability to tow large boats (tugs…). If the engine and propeller that have been proposed for efficient cruise fulfill those constains, which is often the case, you can conclude. If not, you will generally have to use a slightly bigger engine and a more compromised propeller & gearbox, wich means that engine & propeller will not work at their peak efficiency in your normal efficient-cruise mode. Point is that for most motor-boat (excluding tugs and yachts with very different cruise-speed & top-speed….), you will not need to compromise very much the “best” engine & propeller you first choose looking only at efficient-cruise mode.
For sailing yachts, efficient cruise should be pushing an efficient long hull at about 6 knots in flat sea and no wind, and “other constrains” should be the capability to go upwind and up-current with motor only in a force 9 gale with short sea, for instance to be able to change anchor in a gale. Depending on rigging, doghouse, solar-panels etc, it might be between 2 to 10 time the max-power level you normally get from a diesel engine whose most-efficient power level is the right one for your calculated “efficient-cruise” mode.
Point is that strength of the engine to help in a worst-case situation is a good selling argument, so, you need to remember that you will pay for it twice : first when buying the big engine and then when “efficient-cruising” real efficiency will be half or less, the theorical engine + propeller efficiency you might get, so it might be a good point to double-check the power you do really need in that worst-case situation and to optimise the aux. prop. system correctly after that. I guess that John’s experience as expressed in this blog mainly relates to those 2 points. But an other issue is that diesel engines and classic propellers are not good at satisfying max power constrains of, for example 50hp, and efficient power level of 10hp. A technically correct way of adressing such a wide gap is to use 2 or more diesel engines, advanced power electronics (smart inverter…), advanced gearless electric motor and electronically controlled variable pitch propeller. Another solution often used in military boats is to have classic diesel engine & gearbox optimised for top speed, plus variable pitch propellers and special garboxes accepting serial electric transmission from secondary much smaller efficient-cruise diesel engines….
For the A40, I guess that a set of 2 or more diesel engines/generators + smart inverters + VPP + advanced electric gearless engine(s) +… is out of the 2013 scope, but it could provide very good, or best, efficiency in normal cruise conditions and fulfill any aux. prop. constrain. I guess that today, a technically-qualified skipper who accepts to pay some premium for the pleasure of having a really optimised (“greener”…) solution might install that in his boat, but I don’t think it might be realistic today in an affordable blue-water sailing-yacht.
Laurent
Running Gear. I use the same R&D Marine coupling. I tapped the hole M8 for the same security reasons you mention. A better or further option with hindsight for fore and aft security of the coupling and therefore propshaft fallout prevention in my case, is I suggest this. My gearbox (in my case electric motor shaft) has been stepped on the diameter. You can then machine the shaft face square with the recessed face of the coupling and tap and wire an axial M8 hole, secured with a bolt and penny washer to prevent any axial movement. Likewise on the prop shaft side. I note you use a different coupling to the R & D flexible coupling option between the half couplings. I use the R & D with their small electrical continuity mettalised rubber insert for a bonding path to the anode. I also use the PSS seal as you propose. I would use a further locking ring to prevent any axial movement which could ‘burp’ the seal and flood the boat. In my case and as my electric drive motor is so small and light I adjust the fore and aft position of my motor on the R & D flexible mounts so the PSS shaft collar is face to face in its compressed position with the R & D split coupling, thereby preventing any axial movement, other than the tiny amount from the felxible drive coupling.
PS John. I like your further collar suggestion to stop the propshaft falling out and fouling the rudder. Hence my comment about axial M8 tapped holes in the gearbox shaft and propshaft which is my only option due to axial fore and aft space. So in the event of a flexible coupling failure, the prop shaft can now only move the distance of the fitted compressed state of the PSS rubber bellows to its fully compressed state, which is insufficient length to foul and potentially jam my rudder. Also if you scroll to the bottom of this page http://www.pbase.com/mainecruising/pss_shaft_seal you will see the Ruland collar as further security to stop the PSS collar moving if the grib screws fail. As i said I use my split coupling to the same effect. I know a guy with a Moody 33 whose boat flooded when the PSS collar moved and burped the seal.
Have you given any thought to using an electric motor to drive the propellor using electricity generated by the alternator? Perhaps the technology is not sufficiently proven yet, but the ability to install the engine in a location that does not need to take the driveshaft into consideration may be advantageous, and reduce the build costs. It might also be possible to install the electric motor in a sealed compartment, reducing the potential damage from a failed shaft seal.
Probably not the right solution for the A40, but I’d be interested in comments.
Hi Edmund, See my comment above.
Diesel in Bilges. John mentioned that. Horrid. Whilst in the Royal Navy, the strong backs blew off our diesel tanks which were located beneath our messdeck which slept around 30 folks, when I was an apprentice. 2 inches of diesel on the deck of our sleeping quarters! It took 3 months to get rid of the smell. I often slept on the flight deck on a camp bed under the stars in preference, whilst in the Med. Yup – diesel makes one hell of a mess. I am just glad it wan’t FFO!! (Fuel Furnace Oil)
John,
Kubota based Beta 35 has a fine reputation with only one maybe minor but annoying issue: as you can see from the picture in order to change the belt you have to disconnect the raw water pipe.
Thanks for providing us with a wealth of information
Hi Nicolas,
In my experience, those serpentine belts go a good 2000 hours between replacements, even with a big alternator. So just replace the belt every time you have the water pump off for rebuild, which will be, or at least should be, again in my experience, about every 2000 hours.
Very interesting, Thanks. I am just going through exactly the same process with my new aluminium 40 footer (about 9-10 tonnes loaded 33 foot LWL narrow stern), and pretty much have decided on the beta 35 independently for all the same reasons plus the fact that it will fit in the same space as the old bukh 20DV.
I am now looking at gearboxes and reduction ratios, it seems hard to get much good info on gearbox reliability. I am keen to avoid a gearbox cooler unless it’s needed as I have seen a few cases of the tubes leaking. Having none eliminates this risk. Any input on the best options here would be much appreciated.
The only other thing I would love for reliability (if the keel tank is going to need an auxiliary fuel pump due to a head of more than 0.25m) is a small inline diesel header tank for when the fuel pump fails or the primary filter clogs. If it holds 10 litres or so that should give you a few hours of running to sort out the problem or get someplace safe.
My fallback is a Jerry can in the cockpit with a bit of fuel hose and a outboard style bulb to get the siphon happening. But an inline tank would stop the engine shutting down in the event of a failure. A low level alarm on the header tank would warn you of any fuel issues long before the engine starves and stop the need for bleeding. If the overflow drains back to the main tank it will act as a fuel polisher recirculating the extra fuel supplied from the aux fuel pump.
The header tank can also be used to run the diesel cabin heater if needed, and makes bleeding the engine and filters a breeze. It also gives you a reserve if the main tank is running low, sometimes it’s nice to know you definitely have ten liters of clean fuel.
It adds some complexity but may also avoid some, such as only needing one pre filter and no separate supply for a diesel heater. I have heard gravity header tanks can occasionally leak past a worn injector pump and injector and fill up a piston. causing a hydraulic lock. Is this possible?
One other thing I am considering is a prelube reservoir for the engine oil. Sounds good but is it just another complication?
Hi Ben,
Welcome back!
Gear Box: I strongly recommend a cooler. Yes, they can fail, but a spare is not that expensive. Without one, the gearbox will run hot and the life of the oil and gearbox will be significantly shortened. I have a friend who went through three Hurth boxes without a cooler and has not had a problem since fitting one. I also had a small motor boat with this size engine and no cooler. It was not a big problem because I used her to commute from an island, and the run was only 15 minutes. Even so, the gear oil needed changing every 50 hours and it was always black. With a cooler I get 250 hours and the oil looks brand new and tests that way too.
Not cooling the gear box is the single biggest cause of transmission failure.
Prelube Reservoir and pump: Not worth the aggravation and potential failure. Any time you have not used the engine for over a week, just give it a few turns on the starter motor to move the oil around prior to energizing the run solenoid.
Day Tank: A hard one, potential benefits against more complication. On balance, I think I would not bother, but it’s a close run thing.
John, glad to see you have moved away from a saildrive. You might consider the Yanmar 3JH5 as an alternative engine, same hp as the Beta. An advantage in my view is that it is direct injected which means no pause to start and if the batteries are down you might still be able to get it away whereas with the Beta’s glow plugs you would have no chance. There has not been any mention of reduction gearing – the proposed ZF is 1.9:1, whereas if you went with a PRM 120 (a more robust box and does not need a troublesome oil cooler) you have an option of a 2.9:1 reduction, allowing a larger prop (ideally a 3 blade Flexofold or Varifold owner installed) producing more thrust which is like an additional 5-10hp, just what you need those fast flowing reef passes. I would certainly support the use of a fibreglass fuel tank, fabricated from the correct vinyl ester resins these are way superior to aluminium. Many power boat builders now use them, and most underground fuel storage tanks are same.
Yes, I have just been looking at the PRM120, only thing is at 35rpm it is only rated to pleasure duty. I would prefer light commercial at least… One Plus for the PRM is being able to use the normal engine oil. See page 5
http://prm-marine.com/media/Owners%20Handbook.pdf
The Twindisc MG360 looks to be contiguously rated for this HP
The TMC60 just about scrapes into the continuous category with a 2:1 box . Page 2 here http://www.twindisc.it/technodrive/italy/invertitore-marino/pdf/TMC_60P.pdf
So on the whole I am pretty confused by the info, compared to what you see the yachtie engine companies fitting as standard to their range often looks pretty lightweight?
Hi Ben,
The advice I got from Greg at Billings (see the post) is simply make sure the box you choose is rated commercial continuous at at least the HP of the engine, and make sure it is water cooled. Do those two things and any of the main stream brands will serve you well. It is also good, although not vital, if it has an oil filter, which most recreational transmissions do not.
And you are right, most production sailboats have transmissions that are simply too small, which is why you hear of so many failures in yachty world and so few in the commercial.
Hi John, thanks for the info on gearboxes, as I said I have just been procastating about putting in an order and to paying my money so this post couldn’t have come at a better time. Looks like I can get a cooler for the TMC60. Just need to decide on the Ratio.
Hi Alan,
I have to say I’m not big on the Yanmars, I’m hearing too many stories of short life. OK in a weekend use boat that will put on say 50-100 hours a year. But in an voyaging boat where the engine may be called upon to run for several days, I prefer an engine that is based on an industrial block that is designed to run continuously.
As to the glow plugs, my Perkins has them too, but I have never had to use them, and it always starts on the first compression. I wouldn’t worry about it.
Reduction gear: You can get that ZF with just about any reduction you want. The actual reduction will be set after the boat is designed, but I would guess that it will be around 2.5:1. And yes, we will look at the PRM, although the boat will have an oil cooler. Again, this is a difference between light recreational use and commercial continuous. I have had water cooled transmissions for 20 years and about 10,000 hours of use and have never had a failure of the cooler…or the box.
just to clarify a some points
1. The Yanmar 3JH5 has exactly the same background as Kubotas – it is an industrial block from Yanmar’s TNV series engines (I believe built in Holland) used in tractors, skid steer loaders, generators, pumps and other industrial applications. Interestingly if you compare the weights of the respective source industrial blocks the Kubota is 110kg and the Yanmar 145kg – the Kubota appears to be the highest output motor of its range whilst the Yanmar is the lowest output in its range. The Kubota is an engine designed to run at 3600 rpm (derated to 2800 rpm by Beta) whilst the Yanmar runs to a max of 3000rpm. In summary all I am saying is I do not think you should write off the Yanmar option.
2. There is a major difference in glowplug applications – the Kubota is an indirect injection engine with a “pre-combustion chamber”. The glow plugs, one for each cylinder are inside the chambers and must be used to start the engine from a cold start irrespective of ambient temperature (and often if it is more than 1 hour since the engine has run). Your Perkins is a direct injection engine, its single glow plug is located in the air inlet manifold and is only expected to be needed when you are starting in sub-zero temperatures. Quite different applications.
3. I would expect your engines have had hydraulic gearboxes, which must have an oil cooler becuase of the heat generated internally by the oil pressure being used to clamp the hydraulic clutches. A mechanical box does not have this need, the oil is only providing lubrication – as in cars where you rarely (if ever) see an oil cooler for a manual shift gear box. I take the view that any component that can be eliminated, especially in contact with salt water, has to be a bonus. I have had gearbox oil coolers in the past and they were yet another maintenance item.
Hi Alan,
Great information, thank you. You obviously know of what you speak.
One place I do differ with you. I still think that it is important to water cool mechanically activated transmissions. The transmissions I spoke of that failed and produced black oil after short periods were, in fact, mechanically activated, not hydraulic.
You will note that the ZF/Hurth mechanically activated transmissions offer water cooling as an option. In fact the one in the photo in the post is fitted with one. I’m sure ZF have a reason for offering that option.
The nice thing about water cooling on a mechanically activated transmission is that it uses a heat exchange that is simply bolted to the transmission case that cools by conduction, so even if the exchange leaks, there will be no contamination of the transmission oil. Surely the best of both worlds.
Hi John,
the black oil you encountered in that mechanical gearbox was obviously not normal and suggests some form of burning. Was the fault ever diagnosed (my curiosity as an engineer)? All I can think of is that the clutch packs were incorrectly adjusted and slipping, or there was a catastrophic bearing failure (which would be clearly audible). Gear box oil should never change colour in normal operation because, unlike engine oil, it is not exposed to any combustion contaminants
Hi Alan,
I think we are getting mired in the detail here. I have seen several Hurths exhibit this problem, not just one.
Bottom line, ZF/Hurth offer a cooler for a reason and several very experienced mechanics have told me that a cooler is always a good idea. The Adventure 40 will have a transmission oil cooler unless Greg, (see post above) tells me it should not.
Just a brief reference to the many Fuel Tank options and ideas discussed above – I’d like to offer an opinion on the relative priorities of features mentioned (excluding size):
priority one: No leaks (more holes/ports down low, more chance of a leak)
priority two: Ability to access the tank interior for cleaning, including all the corners where crud may hide
priority three: Durability
priority four: Removability
Removability is always going to be a tough one. If I had to choose, I would take a cleanable tank over a removable tank any day. If I’m 2000 miles from civilization and my engine stops due to dirt in the tank, I want to clean it, not remove it. But you never know, with cunning and luck maybe we can get them all.
Hi Martin,
I agree entirely with your priority list, well put. And your trade off. Rest assured that you will be able to reach every corner of the tank from the ports for cleaning. It’s a nasty job, but there is just no substitute for giving the tank a good clean if you have fuel problems.
Nicolas,
Try threading a few belts when you do the belt change and secure the spare ones well out of the way. That way spare belts will be ready at hand and the old can be cut away without removing the raw water pipe.
Dick Stevenson, s/v Alchemy
Dear John,
I was not going to comment until some remarks about Yanmar engines caught my attention. I have been moving toward repowering for the last couple of years and have been collecting info from cruisers who range widely, albeit most of us have smaller boats than yours. The choices, for boats in the 40 foot area, came down to Beta or Yanmar from my point of view.
My research says most cruisers who have Yanmars have been very happy. The same for Betas. Most also had some complaints. In my admittedly haphazard collection of data, most Betas were more locally based and cruised: east coast of the US and in UK area. Being able to get the Kubota based parts should be possible most everywhere in the world, but there are a lot of Beta sourced or produced parts, just like all the marinized engines: Nanni, Westerbeke etc. I believe Beta does the best job of those type engines, but I would contend that, in my experience, those who think that FedEx (DYI UPS etc.) can get parts anywhere are deluding themselves. Many times it is easier, faster and cheaper to fly to the part, put it in your luggage and fly back. And certainly less aggravation by a long shot. (We have been quite happy with our Westerbeke, by and large, but with almost 5000 hrs, I can think of few parts, large and small, for which there is not a spare for at this point.)
My dealings with Yanmar as a company has been terrible. Getting info was almost impossible. In the end, with Yanmars, you deal with the dealer and they deal with the company. A good dealer has many great ideas and says “yes” to bigger alternators & external regulators, remote oil filters and drain pumps, relocating the fuel filter etc., all without compromising the warranty. Beta as a company, on the other hand, was a delight to deal with in both the US and UK.
I was sure that Yanmar was not on my radar screen until my legwork was in. Now, we are likely to go for the Yanmar 4JH which is a 3000 rpm engine with a good track record. I am no expert at reading those curves, but the torque/power etc. curves did not seem all that remarkably different from the Beta. The Beta is certainly more like your Perkins Sabre and has a great deal to offer, but it is a good deal heavier than the Yanmar. Were we to only be UK based or the east coast of the US, we would go with Beta, but Yanmar’s extensive dealer network tipped the scales to the Yanmar for us. As to your hearing about Yanmar’s having a short life, that was not a complaint I came across. I did only focus on naturally aspirated models, especially the JH series.
I chose to write this as there were disparaging comments about Yanmar, and I think it more realistic and fair to say that it is quite likely that either of these engines, well installed and cared for, will make their owners quite happy. I found some horror stories and difficulties with every engine I researched. Yanmar will have many more of these stories because they sell many many more engines (and models). To my thinking, Yanmar,s do not on paper have the “robustness” of the Beta, but I found so many who, like me, are in the 300-500 hours a year usage and have Yanmars and would go that route again, that I was impressed.
My best to all,
Dick Stevenson, s/v Alchemy
Hi Dick,
Yes, the Yanmar naturally aspirated four cylinder is a good engine, in fact, I used to own one. It’s when they take the same block and wring nearly 100 hp out of it with a turbo and intercooler that I get nervous.
Having said that, it is a recreational light duty block, and, all other things being equal, I prefer engines that are based on commercial duty blocks, like the Kubota and Perkins.
As I understand it, the Yanmars are designed with a sub 5000 hour service life in mind. In fact, I have heard from pretty reliable sources that the design service life is more like 2000-3000 and that in light duty recreational rating.
The most worrying fact about the Yanmars is they will not even allow their dealers to install engines from their recreational line in a commercial vessel.
I contrast to that my Perkins that has “design service life 10,000 hours” stamped right on it. And that is assuming commercial-continuous use! I will probably get far more.
So assuming your 300-500 hours a year (much like my use) I want to see the Adventure 40 with an engine that will go 15-20 years, at least, rather than 10 or so at best.
Also, see my comment below.
Hi All,
I need to clarify one thing here. I have never said that the Adventure 40 will have a Beta 35 or a ZF 15. What I wrote was that these items were representative of the gear that will be chosen for the Adventure 40.
I quote from the introduction to the first specification post:
“To give you an idea of the attention to detail that will go into this boat, I have been very specific in this article. But we will be looking for, and I’m sure finding, better ways to do things, right up until the prototype phase is finished.”
Since there is a big talk about engines can I ask if anyone heard of a succesful installation of a Deutz air cooled diesel engine on a metal sailboat?
Not Deutz in particular, no, but I can’t see why someone wouldn’t have done it at some point. A dry stack is common (if loud) on metal workboats/trawlers and a metal sailboat would be particularly well-suited to the requirements of keel cooling.