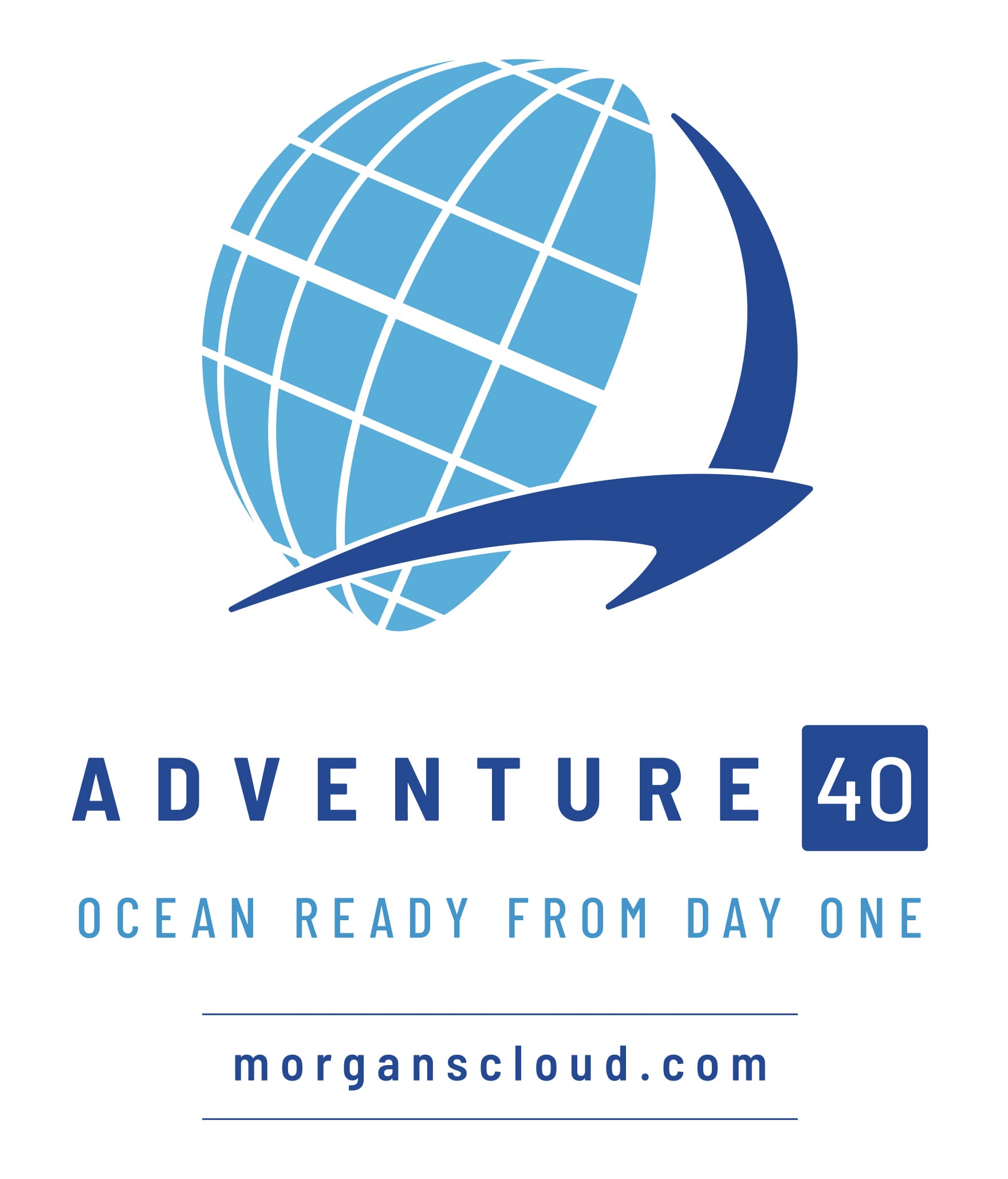
Reliability
There is a saying that “cruising is the process of working on your boat in exotic places” and it’s distressingly true. Even buying a brand new boat does not fix the problem, let alone fixing up an old one. But I don’t believe it must be that way. Let’s look at how the Adventure 40 will be better than that.
The Goal
Here is my reliability goal for the Adventure 40:
- You will be able to buy one for around US$250,000.
- The boat will come to you fully offshore-equipped, with a complete, professionally written and illustrated, assembly and commissioning manual.
- Any competent sailor with basic tool skills will be able to commission the boat in seven working days or less.
- You will only need to add a hand held GPS, linens, and dishes.
- After tuning (documented in the manual) and sailing the boat for a week, you will be able to sail the boat 30,000 miles around the world with only routine maintenance.
Impossible? I don’t think so. We just need to change some things about how the boat gets designed and built:
Designed For Task
Most sailboats built in the last 20 years were not designed to go offshore. Hell, a lot of them were not even designed to go sailing. No, they were designed to look good in a boat show with an interior to wow the dreamers who have never been outside protected waters.
In contrast the Adventure 40 is first, last, and all the time, designed to go offshore, and then those design decisions have been vetted and improved by the hundreds of offshore sailors that comment here at AAC.
Quality
There is a pervasive assumption about boats, reinforced by the current state of the industry, that less expensive boats like the Adventure 40 must be poorly built and equipped with junk gear.
That does not have to be so. By eschewing foo-foo features and going simple—for example, tiller steering instead of the twin wheels supplied on some boats of comparable price—huge amounts of money can be saved that, on the Adventure 40, will be invested in great construction and making sure that the gear that is included is the best.
In specifying the boat we will be guided by the basic principle of the lowest possible total ten year cost of ownership, not a sticker price. I still think that we can get the boat in under US$250,000, but if she ends up at say US$257,000 because she has a really good engine and robust drive train that will go ten years and 10,000 hours with nothing but oil changes, so be it.
Prototyping
It really is no wonder that many new boats are a nightmare of poor design and worse construction. Think about it. Often, a builder, who has hardly ever been to sea, gets together with a designer, who has not been to sea much, and the two of them listen with rapt attention to the marketing/sales guys. This triumvirate designs a boat, often without benefit of an engineer.
They then find some suckers to buy the first boats. Generally the first ten boats are crap. After which, the builder changes everything (if they have not gone bankrupt) based on the anguished screams and warranty claims of the first owners…and the whole cycle starts again.
There is a better way:
- A prototype Adventure 40 will be built.
- Experienced sailors test the boat hard.
- One or two families of four test the boat on coastal cruises including overnight sails.
- The boat returns to the yard to have problems and omissions fixed.
- Gear that has failed to perform is replaced with different gear.
- Repeat as necessary for at least three months.
- The specification, right down to the last screw, is documented and frozen.
- The first production boat is built to that specification.
- The first production boat is tested to make sure nothing went awry.
- Production commences.
Quality Control
Obviously I can’t enforce this, but I’m suggesting to the builder that every Adventure 40 be built under the watchful eye of a quality control inspector who makes absolutely sure that the boat conforms to the detailed and public specification derived from the prototype.
And here is the most important point: The QC inspector, although paid from the purchase price of the boat, contractually works for and has fiduciary responsibility to the buyer.
Sure, this will add some cost to the boat, but not as much as you might think. Remember, the boat is standard and built to a detailed spec. Also, this is a mass production boat, so there will be economies of scale in the QC process too.
What About the Builder?
I can hear the more business oriented among you now: “What about the builder? Why on earth would he or she subject themselves to, let alone fund, this draconian plan?”
The answer is simple: Because there is a lot of money to be made according to the initial budgets we have done. I can tell you after a career in small business that the single biggest destroyer of profit, after lack of customers (we have that one cracked), is ambiguity. And what have we done with this plan? Removed most (you never get rid of all) of the ambiguity that bankrupts boat builders.
Examples:
- Warranty claim: Does the boat conform to the published and public specification? Yes: claim denied.
- Missing piece of gear from delivered boat: Did the QC inspector sign off on the packing list when the boat was shipped? Yes: claim denied, call the insurance company that covered the boat in shipping.
- No options and changes, the biggest killer of boat builders.
Comments
Do you have any suggestions to make this process even better? Please leave a comment, I’m all ears.
you should maybe try and get Apple to build this boat…
I think apple’s success after jobs’s return was to a very large extent caused by one thing: focus. I think I see a lot of that in what you describe about this project. If you are able to carry that through the boat will be insanely great 🙂
Hi Dan,
Thanks very much for the vote of confidence. Focus is something I have always had an abundance of. Trouble is I sometimes have trouble distinguishing between focus and bull-headed!
I continue to really like where this design is going, and the focus on it’s off shore purpose!
Hi Jeff,
Thanks very much for the encouragement. I try to sound supremely confident (OK verging on arrogant) about this, because that’s how you get things done, but I have plenty of moments when I start to think I’m wasting my own time and the readers. Comments like yours help to keep me enthused.
Keep in mind the RCD (Recreational Craft Directive).
All boats in Europe must comply with the RCD.
Hi Michael,
Thanks very much. A very good point. Many of the sign-ups are from Europe, so we need to get that right. Also, the boat might be built in Europe, nothing even slightly firm on that yet.
Now I love this site, and the Adventure 40′ all the more… I have been mesmerised and had my life fundamentally changed by getting involved with Apple since 1999. My pension went AAPL in 2006 and those same shares I hope will be funding my Adventure 40′ in a few short years…
As for building, you might ask if one of the emerging East European countries could be an opportunity.
Make this a class act guys! (It’s certainly starting off that way.)
Recommend reading “Six Frigates” by Ian Toll. It describes the design and building of the first ships for the U.S. Navy—including the Constellation. The intent was to build them identically in accordance with the original design. But President Washington insisted that the building of them be spread out to different shipyards in Boston, Philadelphia, Baltimore, Norfolk (and two other I don’t remember). Each shipyard master incorporated his own ideas, so no two were alike.
Hi Westbrook,
I read it this winter—great book. And it certainly shows the dangers of options!
Hi,
Love your website and email updates and very much like the idea of Adventure 40.
However, I would have thought the concept to be aluminum. Has there been a discussions on pro and cons GRP and aluminum? If I missed it, could you point me to the link?
I would have thought it would be hard to beat the longlivety of aluminum and together with now advanced techniques like numeric cutting, it should be financially feasible for the same costs as GRP.
You can put me down as interested, but would be even more interested if it were to be aluminum.
Thanks and keep up the good work,
Patrick
Hi Patrick,
On the aluminum issue. Please see Matt’s comment below. He is a real engineer and a smart guy and explains it better than I could.
Also, I can’t sign you up. We need you to do that yourself here.
Thanks very much for the encouragement.
This update on the Adventure 40 is quite instructive. It shows the driving forces have good heads on their shoulders and the right marine credentials. Even better, it shows solid business judgement. That bodes very well. I just love things like the “zero options” decision, the arch with messenger lines in the conduit, empty equipment area next to the engine, the sea-chest with spare spigots.
If I could get my hands on a boat today with only two thirds of the planned features in the same price range, I’ll camp on your doorstep until you give up and sell me one.
John
I have one thing to say: Get on with it!
Joking aside , I have signed up and I am convinced that this project really could change the sailing industry.
I am 100% on board with your philosophy and having a few thousand miles single-handed sailing under my belt, cant wait to get my hands on this boat.
Phillip
Hi Phillip,
Thanks very much. It’s that kind of encouragement that will make this boat float.
John
As a follow-up to my last, I also support the consideration of aluminium. IMHO the best offshore boat material. The insides of my 1973 built boat are still shiny aluminium and a recent ultrasonic showed zero diminution in plate thickness.
Phillip
Michael – Regarding the RCD, this is one area where economies of scale really come into play. A lot of the work that goes into RCD compliance is a per-design cost, not a per-hull cost. It is a substantial contribution to the cost of a boat when only five hulls are built; it could be quite small (although not negligible) when spread over two hundred hulls.
Patrick – Regarding aluminum. Alloy hulls *can* be very sturdy, long-lived, and low maintenance. If there are to be only a handful of boats, it’d probably be cheaper, too. We’re talking dozens or hundreds of hulls here, though, so the cost of good composite tooling will pay off. And a thick, solid fibreglass laminate can easily be made as tough and resilient as an aluminum hull if it is correctly designed. (We could easily specify the Adventure 40’s GRP hull to have puncture/grounding resistance an order of magnitude better than many current 40-footers, without compromising her sailing ability.)
John – I really like the idea of a cabinet of serious voyagers to evaluate the design and the prototype. Every time I go to a boat show, I get frustrated at how many builders are spec’ing out their systems based on who had the flashiest ad in ProBoat. They end up with things like a $20,000 furnace with a thousand-hour service interval. No, the spec review has to be done by people who have spent more than their fair share of time upside-down in an engine bay or hanging on for dear life in a force nine.
Hi Matt,
Thanks very much for the great comments, as always. It’s particularly comforting to know that I’m not off base on the QC inspector idea from someone who has real experience in the field. Of course its something that has been done in commercial vessel building for ever by the class agencies, but has fallen out of favor in yachts.
Hi Matt,
Hi John,
About the RCd you are absolultely right…
Seem reasoning is off course through for all fix costs.
About Alu versus GRP :
Of course you know we are fans of alu, of the material. So you may say we are partial. Yes we are…
Some other considerations of different nature :
– In the US the alu is not as highly regarded as it has been since long in Europe (see the articles of Colin Speedie)
– From a businness point of view : of course you are right if we speak of large numbers BUT you have to also consider the elements “needed investments” and risk management. The assumption to make to project liveable is a certain number of boats…. with alu that critical number of boats is much lower.
– John points out : it not only about making a affordable boat… and he is right. The day you buy a boat you must think about the day you will want to sell her…
In Europe all well built aluminium boats have a much higher second hand value… read : the spread between buying and selling is much lower.
So – for me – the choice of the material is not so easy to decide on…
Jean-François
Hi Jean-François,
First off, thank you very much for participating in this project, which many people in your position would perceive as competition. I does you huge credit and having a real boat builder involved is of huge value to the process.
I too am very conflicted about the aluminum or GRP decision. Having lived with the material for 20 years I do believe that aluminum is the best boat building material in many ways.
It is very interesting what you say about the resale value of aluminum boats being higher in Europe. On this side of the Atlantic the opposite is true, although there is some change happening.
I guess it comes down, as you say, to the number of boats to be built. On that subject I only see this project going ahead if we can secure firm orders with deposits for at least ten boats, and twenty would be better. To me, the whole basis for this project is that at least 100 boats will get built in say three years and I hope for many more than that.
If that is not realistic, then I think we need to re-think the whole thing with a very different boat that could be in Aluminum. And at that point, we might as well forget it since the ideal boat already exists. (You will find several of them outside your office door 🙂 ). Perhaps then all that should happen would be for AAC to see if we can persuade (and help market) Boreal to do a 38-40 foot boat, very standard with no options, although maybe that is not worth it?
Dear John,
Thank you for your nice comments…
As Colin and you know we have always tried to make a clear distinction between contributing as good as we can in a logic of “open source” to what we think is a great and very inspiring site and our boats.
We share a common passion and vision. And we like to see people going out sailing and discovering the world… and try to help them when we can.
thanks again.
JF²
One further thought, John. You mentioned having a QC inspector accountable to the buyer.
I used to play that role in a major construction company (one of the first such companies in Canada to have a real QA program). We were a separate branch, reporting directly to the VP and not to the project team, so that we could intervene as needed. (QC reporting to PM is a disaster waiting to happen.) Having this person around will undoubtedly piss off some shop managers, but it’ll also save a lot of headaches and cut way back on unpredictable long-term costs (i.e. warranty claims).
The build process is interesting to me – especially as it relates to quality…
In order to make each boat the same (and therefore minimize/eliminate secondary fixes), the jigs and fixtures need to be very good and for 200 – 500 boats as has been talked of, they need to be long lasting. When building this many boats, you’d need to be able to build more than one at a time – so those jigs and fixtures need to either be duplicated, or designed in such a manner that they can be applied to part completed hulls etc. I guess the point of this ramble is that you might consider involving someone from a car company – who is skilled at the initial tooling up of a production system. Maybe a car company would be the right place to look for a builder? The car company might also be the right place to look for the prototype (with marine guidance) as they have the CAD/CAM and 3D modeling resources which would allow fast development of jigs and fixtures from the development of the prototype.
How about a Lotus Adventure 40!!!
Bill
Hi Bill,
You might want to study the history of now-bankrupt Aptera. A car designed by a boat designer with no successful boats to his credit, built by a computer company and marketed using tech industry concepts. It was particularly embarrassing when they showed up for the $10,000,000 X-prize competition with a tricked out transporter worth five times more than their competition and tried to run their car around the pylons at 45mph. It leaned over so far that it threatened to upset, and the driver’s door kept popping open—.
Hi again Bill,
If you are looking for automated production line boat building, don’t look at GM or Boeing. Beneteau and Bavaria have gone there and done that. And neither builds the kind of boat we are talking about. Got a spare 20 million dollars for tooling and automation and 200 prepaid orders with 50% deposits in hand? Didn’t think so. So you are not going to have a fully automated production of the Adventure 40 , unless of course you have Beneteau build it.
Wasn’t really advocating a car company build it – other than perhaps a small specialist company such as Lotus. More I was trying to offer the opinion that the tooling for the boat, to ensure each was the same in order to eliminate the costly time taken to fix mis-matches caused by poor tooling, would be an expensive part of the build and that it should therefore be considered in the overall business plan.
As a side note, the idea that the QC guy works for the buyer is nuts – if I were to order an A-40, and I had to hire someone to do the QC function, I sure wouldn’t think about hiring the company’s bloke with his presumed bias towards the company. On the other hand, if the QC guy worked for the company, I’d expect the function to be doing it’s job appropriately and designing quality into the boats – just as they operate in every other manufacturing company I am aware of… If buyers selected the QC guy it would be like home buyers ordering up a home inspection – the consistency and knowledge of whom are non-existent.
Hi Bill,
On the QC inspector. Perhaps I was not clear. He is not “the company’s bloke”. He (or she) works for the client and was chosen by the Cabinet.
And this model is actually better for the builder than having their own inspector. The reason being that in any sort of conflict there will be much less ambiguity: If a QC inspector who works for the client has signed off, a client claim will not waste the builders time and resources nearly as much as it would if the QC person worked for the builder. Done right, an independent QC person or company is a win/win.
By the way, here at AAC, we try not to denigrate other people’s ideas with attack words like “nuts”. Having said that, feel free to disagree with me, or anyone else. Diversity of opinion is important and useful.
Who pays the QC person’s salary/fee?
Hi Bill,
As I said in the post, the buyer pays the QC inspector although there is no option on this. Either the buyer hires the designated QC inspector or they don’t buy the boat.
There is no way the builder could do a good job or keep his or her sanity, if there were half a dozed QC inspectors of varying quality running around the plant.
Hi Bill,
I spent a month at Lotus Racing back in the day. They pulled 4o or 50 bodies for their customer race cars out of the molds in a green state and stacked them against the wall. Guess what— they all warped so much you had to torque them into place.
Kind of like the problem Boeing had with their Dreamliner fuselages on a much smaller scale!
The grass on the other side of the fence always seems greener!
So is the QC Cost outside of the cost of the boat? Doesn’t seem right…
I too was at Hethel an eon ago – don’t know of any warped bodies – but it doesn’t surprise me… I think a hull probably has a little more structural integrity to withstand warping during storage – sure hope so! 🙂
Hi Bill,
The QC cost will be part of the final sticker price. However that amount will be immediately segregated in escrow to pay the QC company. Keep in mind that you always pay for QC, or the lack thereof, this just makes it clear who the QC people owe fiduciary responsibility too.
Dear John:
Good to see the Adventure 40 moving ahead. Although I like aluminium, what Matt states in his reply is correct from a large production point of view. Sometime in the future someone may well build an aluminium Adventure 40 from the drawings but GRP is fine if built right.
I am just in the middle of reading about innovation, in particular disruptive innovation. The A-40 is definitely in the Incremental and Radical innovation bracket because it is an outcome of years of sailing experience but at the same time is radical in the building and end product result.
I have lost touch with yachts because all I was seeing were “tubs with toys”. Apart from some specialized and individual builders (Alubat for example) the rest were as far removed from ocean sailing as motor homes are from rallying.
This concept is innovative and very interesting!
I am happy to see the comments on customization, as one of my fears of the “no options” mantra was that this would not be a friendly boat for aftermarket applications.
In that vein, one request would be to make it friendly for an after-market wind-vane. This shouldn’t be difficult, especially since the A-40 will have tiller steering.
Also, I am curious how you are thinking about green-lighting this project. Will the builder bear the cost of the prototyping/design, or will it be buyer-financed via deposits? This could be one of the largest Kickstarter projects on record!
(I am somewhat serious… there are several projects that have raised more than $2 million before any costs have been incurred, and one project that raised over $10 million: http://www.kickstarter.com/discover/most-funded)
Apologies – I hadn’t reread the original specs in a while, so forgot that a windvane was listed as “standard” (hopefully that’s still the case).
I’m curious what has caused the price to creep up to $200k from the original $175k? If the first round of buyers committed in a kickstarter-like fashion (with a substantial deposit), would that allow those early-adopters to get the price back down towards $175k (i.e. a 10-15% discount)?
Hi C. Dan,
Understand that the $175,000 price is a target simply arrived at by taking the price of the Beneteau 45 and backing out the cost of some features like twin wheels, the dealer margin, and expensive advertizing and marketing. It was never intended as a firm sticker price. I don’t think we will see that number until the boat is actually designed.
Having said that, I still have the target of keeping the number under $200,000. But, as I said in the post, I’m not willing to compromise the boat’s quality to do that. There is little point in building a boat to a number if the owner is then faced with expensive repairs in the first few years of ownership. It’s the 10 year cost of ownership that counts.
We should know more in a few weeks, in that one of our readers, who is a very smart professional engineer, has already done a scantling schedule and is assigning costs as I write.
I find the discussion of a design review “cabinet” and an adversarial on-site QC representative interesting for their idealism, and interesting as well because I have personally been squeezed between competing interests by exactly that situation.
First of all, if the boatbuilder has financial skin in the game as will undoubtedly be the case, he will rightfully demand to have some input into how the boat is to be built. And that is as it should be. If he is the right boatbuilder for the project he will know more about the pitfalls of running a boatbuilding business and building a quality product for a price, and have construction experience with much larger variety of boats than the sailors who have been out putting miles under the keel. Sailing 50,000 miles certainly teaches one volumes about the sea and its demands, but it can just as easily create narrow beliefs about what type of boat is best. (not surprisingly that is the same type of boat the sailor owns!) John Neal has 250,000 miles on board Halberg Rassey’s—– if he were to choose the features of a new design, guess what it would closely resemble! Not a criticism, just a statement about human nature. So, if there is to be a “cabinet” the builder should be a valuable addition to it.
Regarding the Owner’s Rep/QC guy, the owners certainly need and deserve to have somebody looking after their interests. And if the QC guy is adept enough to avoid getting locked out of all the toilets at the factory he should quit boatbuilding and go into politics!
Guess that calls for a boat yarn—. I was once hired as the project manager for a large build that had a full time owner’s rep on site. I soon realized my primary function was to absorb abuse from the mad Aussie that the boat owner had found on a bar stool in Shooters in Lauderdale so the company owner that I worked for wouldn’t have to put up with him. Finally reached the point where I told the Aussie that if he ever bad-mouthed me to the owner or the designers again I was going to take a fork lift and run the forks through his office trailer with him in it until it ended up in the river. Told my boss that I was taking a week vacation, and if the Aussie was still there I was quitting. Last I heard he was driving a cattle boat in Sydney harbor.
And finally about the Apple model, I can’t think of two products more different to manufacture and sell. The only common thread is that Apple and many boatbuilders think they have to go to a place where they can employ slave labor to build their product. Harsh? If Apple built their I-phones in California instead of at FoxCon it would cost approximately $20 per unit more and reduce their net profit margin to something like 40% instead of 50%. And after assembling a great crew to build a high-tech catamaran in Washington, some of whom who eventually built the giant Oracle trimaran, my investor wanted to move the business to a maquiladora south of Cancun and use $1 per hour labor to throw matt and roving at it. The China Syndrome model for failure in the boat building business—–.
Hi Richard,
I was not clear enough in the post. There is no intent to set up any sort of adversarial situation. I see no reason that the right professional QC person can’t be of benefit to both parties by arbitrating disputes and explaining complex issues and trade offs to clients. I can tell you that any QC inspector that poisoned the project with adversarial behavior would get his or her walking papers from the Cabinet in short order.
On the cabinet. Again, perhaps I was not clear. The cabinet is not designing or engineering the boat. Professional naval architects and engineers working for and responsible to the builder do that. The builder will have final say on how the boat will be built.
What the cabinet does do is make sure that the result is a good offshore boat by having final say on overall design decisions and by testing the prototype and identifying things that don’t work well.
Of course, in the final analysis the Cabinet has no contractual power, since the builder is paying. But they do have a potent ultimate sanction if they feel that the boat does not meet it’s goals: mass resignation.
In summary, success will depend on all parties behaving professionally, just as it always does in business.
Couldn’t agree more John. Sometimes I let my attempts at humor get the best of me! The owner’s rep who replaced the mad Aussie was a professional with the same goals as the company and owner, and was a valuable asset to the project and a pleasure to work with. A situation that is inherently adversarial need not be conflictual when both parties behave professionally.
Glad to see the A40 project moving forward. Like many others, I am partial to aluminum, also. However, I will be OK with GRP if the design can provide: 1) very high puncture and grounding resistance, 2) thorough blister prevention, 3) means to eliminate leakage through the deck and deck to hull joint and 4) a significantly lower cost than aluminum (say at least $30,000 less).
Otherwise, I am completely satisfied with the boat as specified thus far. If this can really be done for around $200,000, the prospective builder should have years of work ahead.
Dear John,
Great post and a good way to see things…
In late 40’s a Belgium family decide to settle down with a whole community in Patagonia. Gabriël, the founder, used to say : ” When my road is long and difficult, when people do not understand where I go to and why, I doesn’t mean I’m wrong…”
Might apply to you…
One personal remarks if you do allow me :
I like the way you propose to operate.
The idea of Cabinet is great.
BUT essential to me it is to find a naval architect who concentrate three essential experiences :
– off shore cruising experience and live aboard experience
– naval architecture and naval engineering
– having build boats/having been involved in the building process of boats…
At least in Europe – from what I see – a lot of naval architect have no clear view of who things have to produced afterwards. Production is quite often “not their problem” and/or do not live and sail on board of boats they have designed.
I know that at Boréal the fact we gather this three know-hows is one of our factors of success…
I believe such an arcitect will not be more expensive than an other…
As always : my personal view and critics/comments welcome
Jean-François
Hi Jean-François,
I agree that such a naval architect would be ideal. The trouble is that, aside from two guys named Jean-François, there are very few that have these qualifications. We will look though. Such a designer would relieve the Cabinet of many issues and generally make things a lot easier.
This is a great plan!
I was 16 years old when I realized that builders and designers have no time for cruising and therefore generally don`t know much about cruising offshore other than what they hear from their clients. I already had the plan to become a naval architect at that time and I cruised about 40,000 miles with my parents which was the foundation for my thinking.
I was very convinced of myself, didn`t know much about designing or engineering, but I had a boat in my head that needed to be drawn on paper. That happened and the design criteria were fairly similar to what you write in your article. Two years of sketching and dreaming further, I went to University and finished the design of “the maintenance free offshore/arctic boat” while studying.
I started building this 50 foot beauty at the age of 22 (after having a “regular design 46′ Alu cruiser” built with and for my father) and about 4 years ago she was launched. The maiden trip went across the North sea in bad weather, followed by a winter cruise to Norway (I’m from Holland). Now, the boat has been across the Atlantic a couple of times and we sailed her about 25.000 miles in the Arctic.
The boat appears to be fairly maintenance free as it was designed to be, also the work that needs to be done is easily done. But all the “problems” I run into is that the equipment available on the market needs regular maintenance, as you say: oil changes, cleaning, winch servicing, sail repairs etc. It is unavoidable, but on a decent size boat, it takes up about 2 full weeks of work a year to catch up with maintaining everything properly (= as per manufacturers recommendations), even tough we applied the “art of leaving out” as main selection criteria for all equipment, you still end up with quite a lot of work on your hands.
Any way, if you like to have a chat about the boat, feel free to contact me.
The other comments mentioned that it is hard to find a member of the team with the proper qualifications; I have cruised over 100,000 miles, I am working as a naval architect (professionally) for 8 months a year and during the northern summer, you can find me and my boat in the Arctic. and I built 3 offshore yachts with my own hands, varying in size of 35 to 50 foot. I’m definitively interested to become involved in this project!
Hi Erik,
Thanks for all the great comments and input. I will definitely keep you in mind when the time comes to form the Cabinet. In the mean time, your thoughts in the comments will help a lot.
From a designer’s perspective, it wouldn’t hurt for her to be a head turner in any harbor. The boat should present an air of safety and competence that is immediately apparent to anyone who steps aboard. Traditional lines with moderate overhangs show a knowledge of and respect for the attributes that have made for safe passages for many decades. With low cost being such a factor, tooling will of necessity be quite simple. Therefore the few shapes that define the boat’s character must be very artfully drawn and proportioned.
Many, if not most members of the Cabinet will have more offshore experience than the designer. The rigors of producing the work and running the business, especially in this age where much detail is required from the design office, only allows so much free time to be out on the water. Most custom design projects are for very knowledgeable clients who cannot find what they are looking for on the current market – used or new. They know the parameters they are looking for and they rely on the designer’s expertise to achieve it.
A skilled designer who is a good listener, knows the extent of his job, and will allow the contributions of all the members of the Cabinet to influence the final outcome will serve you well.
I do agree that a good offshore boat is a head turner as you describe it, but there have been so many researches on hull shape vs boat behavior in bad weather that I think that a safe and comfortable boat has a higher priority than classic appearance.
Those design parameters are waterline serface, weight distribution, lateral surface, lead ratio, block coefficient, prismatic coeff. etc. etc. Those optimum parameters define your hull shape.
Second, easy access to every thing aboard demands more or less the volume of the hull, classic boats with lots of overhang do not have such space. I personally hate any kind of maintenance that needs to be done on the classic beauties, due to the lack of space around the equipment and no other place available to place the equipment.
The production price of a yacht is largely defined by length of hull, a classic has a long hull, but minimizes interior space. Therefore, the amount of boat you get for what you pay is not directly in favor of classical hull shape.
To make the boat a real head turner and to lower the cost, I think an offshore boat should look like an offshore boat. I mean that a lot of “ugly” equipment for the commercial vessels should be used on such a yacht, it is of a much higher quality, it is cheaper, it is very well tested and innovated, it requires less work to keep it operable.
We “tested” this theory on our current boat and it works, every one who passes our boat needs to take a closer look, practically no exceptions. An offshore boat should look tough, sturdy and no-nonsense, a boat that can take what ever nature decides to throw at her.
Personally, I think that a boat with good sea-keeping capabilities in combination with a rough look is easier to sell than the classics that have been around for decades. It should be something that does not exist yet, something that attracts they eye because it is different. At least: that’s my opinion, but as mentioned before, 10 sailors, 10 opinions.
I think “Seal” that you designed is a good example of what I mean with my comment above.
Hello Erik,
A hull with beautiful lines can have modest overhangs – just enough to keep the bow dry and the transom out of the water. She will be moderate in all her proportions, well-behaved, controllable and unlikely to pound in heavy conditions, while easily driven to make sure the engine stays off when the breeze lightens.
Nor does a beautiful boat need to be dainty in any way. The boat should both be rugged and obviously appear so to any observer.
Hi Ed and Erik,
I agree with you both on this completely. What we want here is a boat that “looks the business” to quote Skip Novak. But that does not mean that she can’t be lovely to look at. Our own “Morgan’s Cloud” designed by Jim McCurdy, is one of the best looking boats on the water that garners compliments wherever she goes, but she is also rugged looking with her white paint and Treadmaster decks. Ed’s design “Seal” is, as you say (Erik) another example of the skilful blending of form and function.
Hi Ed,
Welcome here! We really appreciate you taking the time to contribute. Also thank you for your open attitude to the Cabinet concept.
For those that don’t know him, Ed is a professional yacht designer with a large portfolio of successful and beautiful boats under his belt.
Ed,
It is great to “meet” you here…
Although the boats we design are very different from yours, we highly regard them as a REFERENCE.
I have personally spent a lot of time “inspecting” Seal in Ushuaia and discussing with Hamish (we were lying with our previous boat along side his for some time. They have two daughters. I have two sons about the same age and I always say to my boys, look at the girls with big boats).
We (both JF ) have a different view on the keel and the rudder and I hope one day we’ll the opportunity to discuss that live with you.
To all:
About Seal in this context : Seal is a (or THE) great professional expedition boat.
The context of a A40 is very different… : the concept, the sailing area, the way of building (Seal is a kind of “One off” and Hamish did a lot himself), the budget (budget/foot) is different
Ed, we do share your point of view of your last post about the design/hull shape/overhang… It is very well summarized.
Personnally we think that the idea “the production price of a boat is largely linked to length” is an idea which has to be expressed to readers who are not necessarily involved/close to boat building with more nuances, more carefully…
Jean-François
Jean-Francois (sorry, I don’t have the “French C” on my keyboard),
What I meant with “the production price of a boat is largely linked to the hull length” is that materials, equipment en building logistics are mainly selected on hull length, there are of course exceptions.
But think for example about the following:
– Hull length defines largely the amount of material used and is a large contributor to determine the scantling sizes.
– the amount of material required is a large indicator for hull weight, therefore ballast weight, rig size, deck equipment size, engine power, propeller and shaft sizes etc.
– building shed size depends on hull length, same for the lifting capacity and logistics on the yard as well as on the road to get the boat delivered.
Most of those costs can be roamed off a bit if the waterline is short(er), but my best estimate is that 80% of the price is determined by the hull length, given that we keep on thinking within the sketched concept of the Adventure 40.
Hi Ed,
Good to see you joining into the discussion. As I’ve said more than once, you are the Master of hard dodger design and styling!
What a great idea! I have been following this discussion and have now finally signed up.
Just one suggestion: John writes that the owner will receive the boat on a truck. But would it not be better if the owner took over the boat at the builders yard? Then he/she/they could do the commissioning there or in the vicinity. Any issues could be sorted out with the builder there and then – quicker, easier and cheaper for both parts. The buier could be given say, seven days to do this and make any claims. Any dispute could be resolved by a referee, for example a member of the cabinet.
Apart from it being nice for builders and buyers to meet, it is incredibly instructive for the buyer to have the builder explain things and potential misunderstandings can be resolved before conflict arises.
It would be cheaper for the owner to go to the yard than transport the boat to him, less risk for both builder and owner and since the whole point of the exercise is to go sailing why not just get on with it right from the builders yard?
Besides, buyers will be spread all across the world and at least some of them will go to take over the boat at the yard anyway. I will do so myself if this materializes. Will have a nice launch with naming ceremony and champis all round.
Finally, this way it will be easier to give a clear final price. Ownership passes from builder to buyer at the yard, at this price, no extras, no transport, this is what you pay and that’s it. If the buyer wants to put the boat on a truck or whatever after that, that is of course entirely up to him and no longer any of the builders concern.
Hi Sverre,
Interesting idea, and maybe the way to go. One thing that would worry me would be the potential time sink for the builder in all of this. For this to work, the builder is going to need to be very focused on actually building the boats. While building a relationship with each owner might be nice, it could also be incredibly distracting.
As to disputes, I agree completely that they should be solved by some type of arbitration that is clearly defined in the contract. However, I’m not sure that the members of the cabinet would want to get drawn into that—I know that I would not. Maybe it should be a professional arbitrator.
I am along time “lurker” who is actually in the process of looking for a vessel that conforms to what is being suggested (used ovnis’s, etc).
I like the innovative organization approaches described ( I study organizational processes) and I wonder also about equally innovative financial structures ( e.g. Crowd sourced initial capital, etc.)
In any case, love the discussion and would love to have the type of vessel descibed to live on with my wife and young daughter!
Hi Anthony,
Thanks for the enthusiasm about the Adventure 40. Crowd sourcing the capital is an interesting idea as long as it could be done in such a way that it did not compromise the authority of those managing the design and build. People who have made a substantial up-front contribution might feel, justifiably, that they should have input into the product development, and we don’t want to get too many cooks spoiling the broth, or the boat.
As long time lurker let me add my 0.02$…
Have a look at the Varianta 44. A ready to sail 44 footer that is being sold for about 100000 euro, VAT included…
Not an example of what is attempted here, but it could offer some inspiration…
Hi Krist,
Thanks for the tip. As you say, the Varianta is no Adventure 40, but the fact that they can sell the boat at that price is very encouraging and helps to prove out the concept.
I also found the concept of selling the boat through a sailing school that would teach the buyer to sail her very interesting.
John,
We’d be happy to donate time to develop sailplan ideas. We’ve been working with a lot of cruisers with a focus on simplification and ease of use. I’d be looking at something along the line of this for base inventory.
Dacron main with top batten full, 3 longer than standard partials, 2 deeper than standard reefs. Lazy Bag (aka xxx-Pack) with integrated retractactable lazy jacks.
Non-overlapping furling headsail on Facnor LX furler.
Basic specs for Dacron sails would be our Offshore Plus Spec:
Cloth – Challenge High Modulus with optional upgrade to Marblehead/Fiber 104 HA.
3 rows triple step for broadseams with black thread recommended to make spotting future problems easier
Oversize radial patches
Overhead synthetic leech and foot lines. No plastic/nylon hardware due to UV considerations. Cleats to have cloth covers with velcro to protect them and line from impact damage/UV.
Doubled Tapes
Reef connectors
Double layer spreader patches
Adequate anti-chafe
(yada yada, yes quite bulletproof and designed for 40,000 miles service)
Cruising Code Zero – we call this our CLASS or cruisers light air sail solution as we refer to it. This can be flown on any point of sail from close reach to downwind. It’s most efficient at a beam reach and above. While you cannot point as high as you can with a jib, the sail has sufficient power that you get better VMG in very light air than you ever could accomplish even with a 155% Dacron genoa. This sail would be flown from a Facnor FX-2500 or equivalent.
Downwind Sail – We take the classic concept of twin downwind sails and modernize it. This consists of two light inexpensive nylon sails joined together to form a common luff. This sail is flown from the same furler that we use for the code zero. Alternatively a smaller Facnor furler could be used with it if a customer preferred a dedicated furler for each sail. We can probably use the FX-1500 since the loads are a lot less than the Code Zero. Poles recommended but they can be left in place while sail is furled. Very easy to manage, stress free, downwind sailing and fast.
Storm Sails – Some options here:
Tradewinds Option – No trysail. Use the reefed main (consider a 3 reef main at this stage). ATN Gale Sail for storm jib.
High Latitude Option – Trysail in International Orange. Removable spectra or dyneema stay and running backs also of dyneema or spectra. Storm jib in International Orange flown from removable stay.
Basic Repair Kit – Each owner to receive kit with basic repair materials, tools, and instructions. Discounts made available on appropriate onboard sewing machine
Training – Potential to create DVD/web video explaining use of sailplan
$$$’s – Less than you might imagine, especially if 5 or more sets made at once. Would just need I,J,P, and E to quote.
Hi Dave,
That’s great. Thank you. I will definitely take into account this comment as I put together what is fast becoming the Adventure 40 MkII specification. Also, thanks for your offer to help, I’m sure we will call on you for input.
John
re A40. I have been following in PRO Boat the building of the 8 USCG Academy’s Leadership 44 s. The infused hulls to a MILSPEC being done at Morris are a very interesting example of top quality built for max durability and service life on a replicable basis fitted with simple, durable systems. It might be worth keeping track of these boats as they go in to service. They are using a QC type oversight service reponsible to the Academy and the funders.
I believe they are being funded with donations from Academy Alumni
Hi Pedr,
Thanks for the heads up. Seeing the Navy 44s racing outside Annapolis last fall was one of the experiences that triggered the Adventure-40 idea in my head in the first place. They are great boats and will, as you say, provide a helpful template for the Adventure-40 project. Great to hear that the used a QC model very like what we are planning for the Adventure-40.
I read the article in Pro Boatbuilder as well. Very impressive construction but cost per hull rather staggering.
It was a military project…
I just spent a happy half hour reading Practical Sailor’s take on the boat. A lot to learn here for the Adventure 40.
Note: You have to be a PC subscriber to read the article, but that’s no bad thing.
I am wondering if you have followed the crowd designed “Cruising Anarchy 36”?
Perry designed the Flying Tiger 10 using a similar concept. By using the web to gather the best ideas they were able to keep costs down, while doing an interesting and innovative design.
Hi Tom,
Yes I have, off and on. I have always been a fan of Bob Perry’s, and in fact in the original Adventure 40 post I mentioned him as a possible designer.
I think the boat that Bob came up with as a result of the discussions on Sailing Anarchy looks close, although she is not quite the Adventure 40.
Having said that, there is no business plan attached to the Bob’s Boat and therefore, as Bob says “But no, unfortunately you can’t run out and buy a CA 36. The object was just an exercise in exploring design ideas and looking for the elusive perfect boat”.
With the Adventure 40 we have a plan to make the boat a reality. More coming soon…
The CA36 looks like Shannon or an old Morris 36. I like it although I’m surprised a hard dodger didn’t make it into the plans. I’m always confused about the lack of a hard dodger in sailing boats. I’m also surprised to see swept spreaders considering most “cruising couples” are sailing downwind. I think something just a bit better would be something slightly longer with a forepeak and dedicated shower (and hard dodger, not a raised salon where you can’t get a sense of the weather while on watch). I do like that the halyards are at the mast, where they should be.
Hi David,
Wow, you nailed why the CA36 is not the Adventure 40. Thank you.
I’d also want solar panels on the hard dodger like New Morning because I wouldn’t want the added maintenance/noise of a generator:
http://www.newmorning.info/page12/page36/page49/files/102408BTSN-7738.html
I also love that boat’s cockpit layout (except for the sugar scoop stern. Not a fan of that). I’d also want it to be center cockpit (for the better motion… or at least has the front of the dodger be at the center of motion) but those designs don’t work/look well, imho, on boats below 45′.
Hi David,
You really don’t want solar panels on top of the dodger. I know you see it done a lot, but the drawbacks are that you lose one of the big benefits of a hard dodger: being able to stand on it to reef and furl the main or for a better height of eye. Also, it’s a very inefficient place to put panels because of shading and the difficulty of tilting the panel. The Adventure 40 will have an arch, which is a much better place for panels.
And you are right, there is no way to do a good center cockpit boat under 45′ and 50′ is better. Don’t worry too much about motion comfort. That’s much more about hull form and weight distribution than cockpit location. Also, the thing you want at the center of motion is the sea berth, not the cockpit.
The panels on the boat I showed were flexible panels that can be stood on. Arches are great too.
Unless the technology has changed dramatically, I doubt you’d be able to get sufficient output from flexible panels mounted on the dodger. Price of those is still pretty high. Standard 140w panels are down to around $300. Two of those on a stern pole and perhaps a good wind gen would probably suffice for basic needs.
We have our passarelle stored amidships where it can be swung down. Due to freeboard there would be no way to reach someone in the water though without getting on the ladder yourself. I still like the benefits of some sort of swim platform which go far beyond MOB recovery. I’ve seen people go overboard on other boats in situations where the swim platform would have been ideal for getting them back on board.
From reading that boat’s blog. They generate all of their power from those panels & the wind generator and occasional motoring and they seem to run a lot of electronics and gear. It’s a 56 footer without a generator and they claim they once didn’t need power for a week at anchor. Granted it was the tropics. They probably are expensive though.
40′ is pretty small for a center cockpit design unless you’re willing to not have a pass-thru between the main and aft cabin. On our boat the engine compartment is under the cockpit and there’s a narrow and rather short pass-thru to the aft cabin. We’re about 46′ though. We have solid stainless rail around the boat and our solar panel are rail mounted. I like to be able to step on the dodger so I don’t have them there. The best place for the panels in my opinion would be on a stern pole where they could be kept in the sun. Another problem with dodger mounted panels is they are often shaded.
Some type of swim step or platform makes dinghy boarding easier as well as MOB recovery. Some boats have a simple flip down platform which I like.
I definitely agree. I think CCs look funny below 50′.
I don’t like a platform on the stern for MOB. It works well in calm conditions but when do MOBs happen in calm conditions? Too much heaving back and forth. Too much concern in getting smacked on the head by the stern and platform. I prefer a boarding ladder at the beam (where you can mount a platform on the ladder for dinghy boarding).
I was thinking what would be on my list for “my” perfect boat:
*Preferably a center cockpit (depends on LOA)
*Longer & Narrower > Wider & shorter
*Moderate overhangs & Narrow ends.
*Easily singlehanded
*Hard Dodger with solar panels on top
*Partial Skeg Rudder with oversized shaft & ability to have the unprotected portion to be cleanly sheared off and keep the top part. So the lower section is weaker than the holding power of the shaft & rudder bearings. It should still be able (in cripled form) to provide enough steerage for downwind and motoring.
*Wind vane
*Fin or modified fin keel (maybe bulbed but definitely not a wing)
*Straight Spreaders
*4 reefs in the main (4th is same area as a trysail)
*Dutchman reefing system
*Cutter Rig
*Running backstays
*Manual furling forward jib (can be lead to a winch)
*Manual furling cutter stay (can be lead to a winch)
*2 line reefing
*Removable storm jib stay that doesn’t furl.
*Aluminum construction painted white. I don’t like bare aluminum.
*Teak caprails varnished with Signature Finish Honey Teak (lasts two years in the tropics). I just have to have SOME teak.
*Watertight bulkeads at forepeak, engine room, rudder shaft area. All thru-hulls in watertight bulkhead areas)
*Integrated water/fuel tanks under main cabin (effectively giving one a double hull in the largest area)
*Large galvanized Rocna/Spade Anchor using the Dashew method: Whatever is recommended, double it and add 20%. I like to sleep without worry.
*300′ of G7 chain
*2nd anchor always ready for deployment with 100′ of chain in the recommended size. Probably an aluminum Spade for weight.
*2 Oversized windlasses
*Large Luke & Fortress Anchors (w/ mud palms) stored within the boat.
*Feathering prop
*No bow thruster
*No generator
*Maybe a watermaker
*Foot pump for tank water & seawater in kitchen along with pressure water.
*Water filter under kitchen sink.
*Keel cooled refrigerator
*1 bathroom
*1 separate shower next to the companionway so that it’s also a wet locker
*Nav Station situated so that the helmsman and navigator can hear each other
*Mute button on music radio somewhere in the cockpit (probably under the dodger)
*LED lighting
*Kitchen sink at center of boat (drains on both tacks)
*1000 miles of diesel tankage (assuming diesel required for heater is included)
*Non-turbocharged diesel with 2hp/1000#
*200 gallons of water
*3″ of insulation (it’s good in the tropics too)
*No microwave.
*Furuno FA150 AIS, GP32 GPS, NX300 Navtex, & Radar for reliability and low power operation without a chartplotter.
*Weather fax at helm station (connected to laptop)
*VHF & SSB at nav station, VHF remote mic under dodger)
*Depth/Speed/Wind/Multifunction instruments above companionway
*Laptop chart plotter at nav table
*No chartplotter at the helm. You should be steering not playing with a toy. Only autopilot repeater & multifunction repeater at the helm.
*Small faraday cage somewhere with handheld radio, second epirb, handheld gps, and extra batteries
*Diesel water heater/cabin heater
*No A/C. It’s only usuable at the dock and who wants to be at a dock?
*Aft berth with 2 bunks
*Sette table and opposite bench can turn into two sea berths
*Island double in foward berth for at anchor sleeping (makes the Admiral really happy)
*Large forepeak for storing gear (spares, extra line, halyards, dock lines, fenders, fortress anchor, trysail, storm jib, asym, deflated dinghy, outboards, inflatable kayak for rowing ashore)
*Large medical kit under nav table
*Large Hypalon dinghy with wood floor
*2 hp outboard for most trips.
*15 hp outboard for longer trips.
*Ability to charge with 110/220/50hz/60hz shorepower
*Halon fire system in engine room
*Super large emergency pumps in each hull section
*Lifesling in rigid container on the stern rail.
*Gas inflated MOB device with inflatable 6′ rod, horse shoe, and blinking led light on the stern rail.
* Inflatable PFD with integrated harness, emergency light, & personal AIS device for each person.
Your perfect boat will likely need to be larger than 40′. Keep in mind John is trying to produce a sailaway 40′ that is $200K. I don’t know if you’re throwing out ideas for John’s $200K cruiser or just what your dream boat would have.
Painting aluminum sets up a maintenance cycle. There’s a reason you see a lot of smart people with unpainted aluminum boats. I’d vote for an unpainted hull and someone who wants paint and maintenance can have the hull painted themselves.
A lot of your ideas are valid but add weight. More weight means you need a larger rig, more sail area, bigger winches, etc. The Dashew approach to ground tackle works wonderfully on their boats but few of their recent designs are under 70′ or so. I’m a fan of Dashew ketches but Steve would likely acknowledge that his philosophy would not transfer well to a 40 footer that is going to sell for less than a comparably sized Catalina and be set up for real world cruising. Most of the used Deerfoot/Sundeer/Dashew boats will sell for much closer to a million than $200K.
Interesting that you specify no chartplotter in view of the helm. This flies in the face of logic. When you need it most, you don’t want to be downstairs at the chart table.
4 reefs in the main is impractical and unnecessary. Every reef point adds extra weight along the leech. You would be setting yourself up for a lot of issues with leech flutter. If I were designing your main, I’d end up reducing the roach to help but it still wouldn’t be pretty. We design and supply mainsails all the time with a deep third reef that roughly corresponds to the area you’d have with a trysail.
Dutchman is quite expensive and the sail has to be built around their system requirements. It’s actually less expensive to go with a lazy bag (stack-pack, mack pack, etc) and you get a sail cover to boot. Plus you don’t have to carry spares for the system.
Teak is lovely to look at. A lot of us prefer it on other people’s boats. A teak caprail will need to be removed and rebedded periodically. Adding a bunch of holes you don’t need seems impractical. After all this is supposed to be a low cost go anywhere cruising boat, not a dock condo or something to park at the yacht club.
If I read your comment correctly, you want three forestays. Seems like a lot and you will have a lot of sail repairs from tacking and jibing. At most, I’d want to see a removable synthetic inner stay. Using a modern approach, it’s possible to have the ability to fly a staysail without even rigging a stay. Check out the various foil-less furlers from companies like Facnor and Karver.
Just out of curiosity, what boat do you have now and where has most of your cruising been?
I agree. Think VW Van — something simple and inexpensive — not a Mercedes Sprinter. The latter is definitely a nicer car, but it’s a lot more complicated and a lot more expensive.
Having said that, a good investment is to do some good, early systems design. A lot of the expense and complexity of a boat comes from having to go out in the market, looking for best of breed equipment, then scratching your head figuring out how to put it all together.
For example, installing a radar. The normal process is that you select a unit, then look for a mount that will fit it. Then you look for a pole to fit the mount. Then you have to find a place on the boat to put the pole. The perfect spot would be in starboard quarter, but dang! that’s where the autopilot is. Why didn’t I think of that earlier? So, you settle for the port quarter and give up a little storage space in the locker it will go through. You install the radome, then discover that the cable isn’t long enough to make it to the nav station. So, you buy a longer cable. And so on — I’m sure this story is familiar to anyone who has kitted out a boat.
While the A40 certainly should not come with a radar, its installation should be anticipated and a place reserved for it. For example, the arch could be predrilled, with a conduit nearby, ready to receive a certain brand of radome. It is known that the cable on this brand is long enough to make it from the arch to the nav station, where a place has also been reserved for it. There is an extra blank in the electrical panel where its breaker will go.
While this approach limits choices for the owner, in the long run it can result in tremendous total cost of ownership savings for the buyer.
-tk
Hi Dave,
Very well and clearly put. I would agree with just about all your points. In fact I think that putting together a really great and functional offshore boat is a lot more about decided what can be left off and how to simplify what is installed, rather than deciding what to add on. I hate so say this, as a Canadian resident, but kind of like the difference between a Blackberry and an iPhone.
Definitely would vote for the A40 to be unpainted, despite my preference for a painted hull. It’s just so pretty. Boats are all about compromise. I love the way you put it about teak: we all like it on other people’s boats. Very well put. Teak and painted hulls definitely have no place on the A40.
I currently sail a Catalina 36 with a dutchman out of Annapolis. It’s definitely no offshore boat. I have a small chartplotter under my soft dodger but it can be removed and taken down to the settee where I can better plan with paper charts laid out on the table. I’ve seen too many idiots at the helm fiddling with their chartplotter instead of actually steering, oblivious to other traffic. Plus, on long passages especially at night, I want the plotter to be under the dodger where its warmer.
Yes, the 3rd forestay in my mythical boat would be removable and synthetic so that you don’t need to remove the staysail to put on the storm jib.
I also like the other ideas I’ve seen here with a non-overlapping genoa on a furling stay, a stayless code-0, and a synthetic removable stay that uses a hanked on staysail and storm jib.
My boat has two reefs and I have a separate try sail which I don’t like having to setup when the wind howls. A 3rd deep reef sounds like a great idea. Thanks for the info on the reefs and leech problems.
David,
Agree with your analysis and especially the comment about lack of a hard dodger. That should be standard on any cruising boat. We have an old Amel that has been an immensely practical and reliable platform. I appreciate the Dashew boats which were also designed by someone who actually logged many sea miles. Most designs I see are more a reflection of the marketing department’s demands than something actually designed and built for offshore service. I have tremendous respect and admiration for the work of Mr. Perry but I’ve experienced some hazardous components of his designs, for instance tall and steep companionway ladders. I don’t fault him, as he’s been commissioned by a client to produce what they view as marketable. There’s a marked difference between boats built to sell as many units as possible and those reflecting a naval architect’s vision of a true cruising boat based on his own real world cruising experiences.
I sense the Adventure 40 will be based on what actually works in the real world of cruising.
I think the point is the power of crowd sourcing, not the details of the CA36 design.
Even if you don’t like what Mr. Perry has done, we can learn something from him about using the web to field innovative design elements.
Agreed Sean. I think the FT10m was an excellent example of a collaborative development environment. And to be clear, there is a lot I like about Mr. Perry’s work, particularly some of his custom designs. A friend of mine captains a 72′ custom Perry and we are really impressed with that boat. It bears no resemblance to the production boat designs that I’ve been critical of.