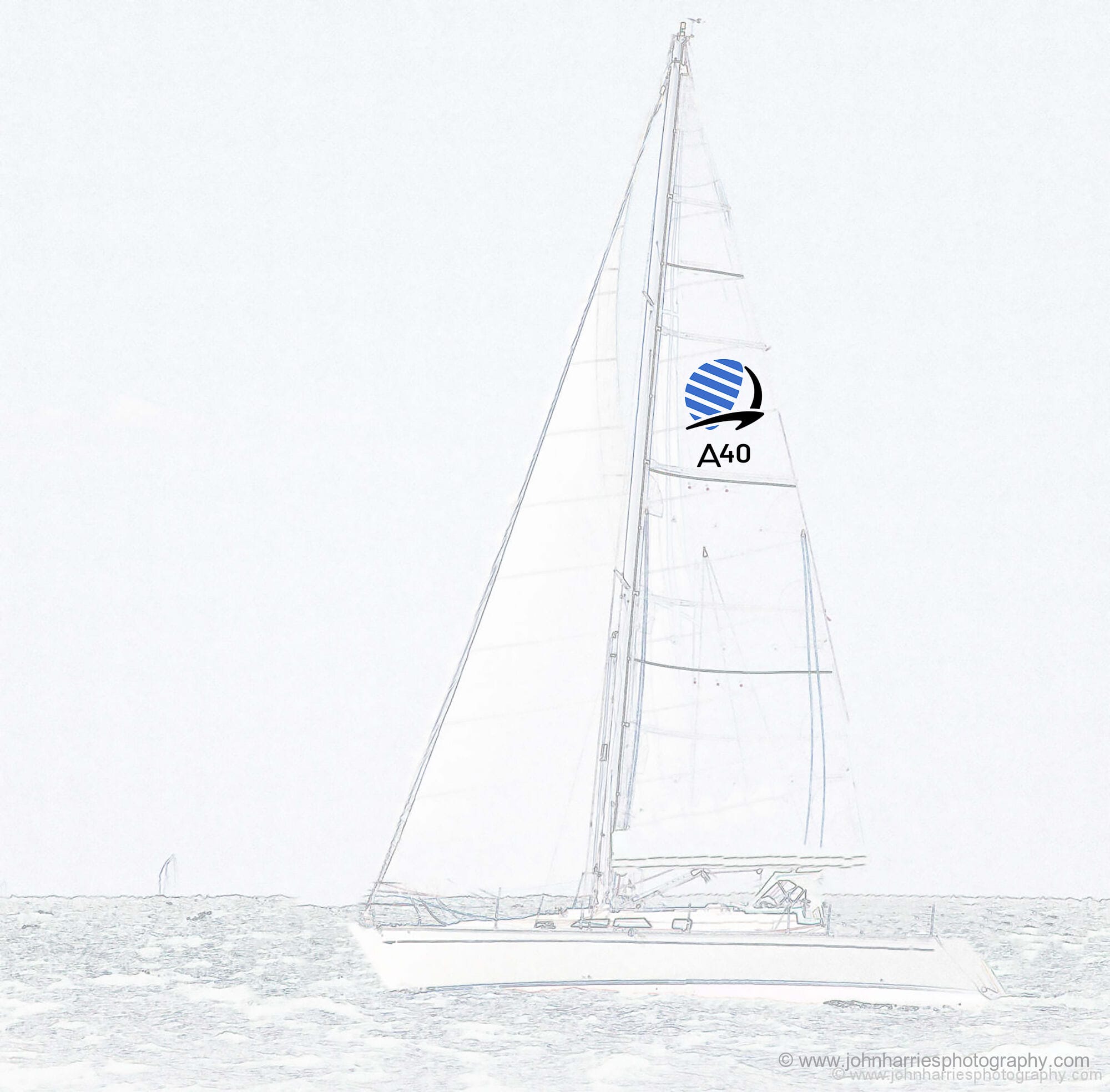
Hull
We are now ready to reveal and discuss the specification for the Adventure 40 prepared by Maxime and Pascal, the partners in France who are going to make the Adventure 40 real, and who are being advised by Vincent, the naval architect they chose for the project.
It’s been nine years since we thrashed out the Adventure 40 mission and core design concepts, so rather than just pasting in their specification I’m going to share each part and then relate it back to that earlier shared and deeply-discussed work, so we are all looking at this in the same context.
This approach will also help those of you who were not in on the idea in the beginning and are trying to figure out if the Adventure 40 is the boat for you.
This is important to get done now because the boat is targeted at a specific owner profile rather than trying to be a boat for all—an unattainable, but all too common, goal in boat design.
Or, to put it another way, part of my goal over the next few Adventure 40 articles is to provide enough information for some of you to decide that the boat is not for you—no shame in that, and better we all know what the real market is sooner rather than later.
This will then give the French team a clearer idea of how many people are committed to the boat, or at least deeply interested.
Let’s start with the dimension envelope that Vincent will design the boat to fit in:
- Light ship displacement: 7 to 8 metric tons (15,400 to 17,600 lbs)
- Load carrying capability: 2 to 3 metric tons (4400 to 6600 lbs)
- Length overall: 11.8 to 13 meters (38.71 to 42.65 feet)
- Draft: less than or equal to 2 meters (6.5 ft)
To put these numbers in context, the Adventure 40 is:
- About three-quarters the size of a Valiant 40
- About the same size as a Westsail 32
If that does not make sense, please take a moment to read this article.
Two-Person Boat
Or, to put it another way, the Adventure 40 is a couple’s live-aboard cruising boat.
If you are looking for a boat to take a larger family longterm live-aboard cruising, this is not the boat, at least unless you have a high tolerance for crowding. There won’t be room for more than one decent sleeping cabin, once Vincent draws in proper storage and machinery spaces, and not enough load carrying capacity.
One day I hope we will do an Adventure 48 to 52, displacing around 11.5 metric tons (~25,000 lbs), which would be a live-aboard boat for a family of four, for example.
Draft
The 2-meter (6.5-foot) draft was chosen based on Phyllis and my experience of cruising with just that draft for some 30 years, while finding it the optimal tradeoff between performance and access to ports and anchorages.
Also, the Adventure 40 will not have lifting appendages. More on why not here.
A Great Sailer
The good news is that, by using modern design and not being constrained by the all too common, but deeply ill advised, goal of building the biggest boat for a given length, the Adventure 40 will be way faster and more comfortable when underway than the Westsail 32, and a better sailer than either. Sorry, Valiant 40 and Westsail 32 owners, I know they are great boats, but design and build have come a long way in 50 years.
Room for a Great Interior Layout
Also, contrary to common opinion, Vincent can design a way more functional layout in a longer boat for the same displacement than a short fat one. Here’s why.
At a Great Price
More good news: the relatively small size of the Adventure 40, along with keeping her standard (no options) and simple, is a lot of why I’m confident that the boat can be sold ready to go for the target price of about US$250,000 and still be of far higher quality than even boats costing far more.
Hull Shape
That’s just the numbers, now let’s look at the sailing capabilities that make the Adventure 40 different from any production boat available today—the primary reason we are doing this:
- Sufficiently narrow and V-shaped forward sections to prevent pounding.
- But still with proper volume and flare in the ends of the boat to provide reserve buoyancy to reduce pitching and keep the deck relatively dry.
- Low moment of pitching inertia by keeping the heavy items (tanks, engine, chain) as close to the middle of the boat as possible, and by avoiding, wherever possible, weight in the bow and stern.
- Most modern production boats suck in this regard, due to the trend of pushing the accommodation right out to the ends of the boat and then cramming them full of heavy gear.
- Carefully shaped and matched bow and stern shapes so that the boat remains easily steered when heeled—no huge wide stern that will cause the boat to become hard to steer in a puff and drive the bow down into the next wave.
Bottom line, the Adventure 40 will be a fast, efficient sailboat designed to treat her crew kindly when the going gets tough, whether that be on a long coastal daysail against a rising sea breeze or a gnarly fall voyage to Bermuda.
Why does this matter more than the huge interiors we all see on boats designed to sell, not sail? More on that in a moment, but first let’s look at how the hull will be built.
Hull Construction
I’m excited to reveal that the French team have committed to building the hull from epoxy resin, not polyester as used in most production boats. The advantages are many:
- Better resistance to water intrusion.
- Blistering is non-existent on an epoxy boat.
- Epoxy resin is used to seal boats built from polyester.
- Much better adhesion to the fibreglass cloth and core.
- Better impact resistance.
- Better resale value.
All that’s great. But by far the best reason for building a boat out of epoxy resin is that there will be no secondary bonding problems, that common curse of production fibreglass boats where the joints between assemblies like bulkheads, chainplate knees and, worst of all, keel reinforcing members, come away from the hull over time because of the inability of polyester resin to stick to itself once it’s dry.
Sure, builders will claim that they got all the members in and glassed while the hull was still tacky but, in fact, that often does not happen—ever heard of weekends…or happy hour at 5 pm?
You can read more about secondary bonding problems over at Steve D’Antonio’s site.
Bottom line, they suck, as I know all too well after having to rebuild my Fastnet 45 forty years ago, and getting a second dose of secondary-bonding headaches now:
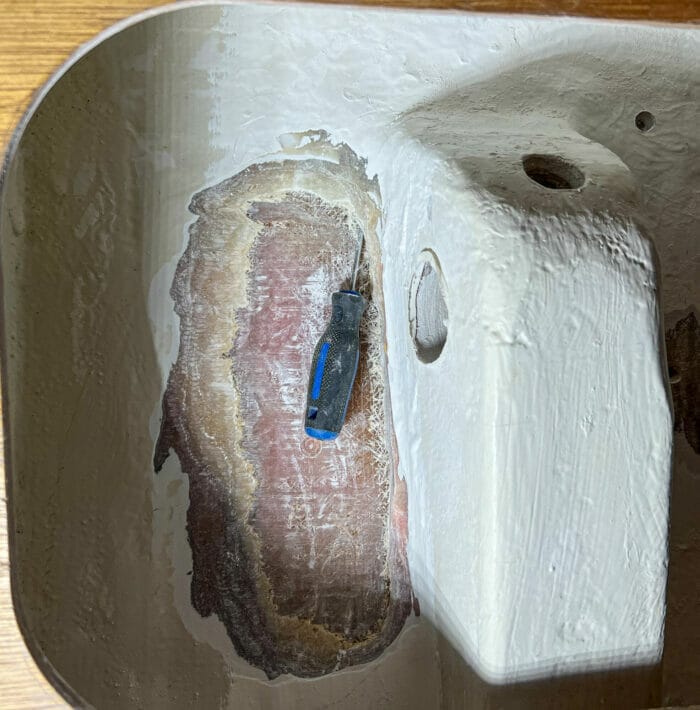
The deck, bulkheads and hull will all be cored with, of course, the core removed in the way of fittings and through hulls.
…I’m pausing for all the wailing and gnashing of teeth to die down…
And, yes, I had to think about this some, too, particularly since we originally specified that the hull be solid glass, but there are a bunch of benefits to going with a cored hull, most notably:
- Much higher strength- and stiffness-to-weight ratio.
- More volume for a given displacement.
- Better payload than a heavier boat.
- Weight we don’t put into the hull we can put inside the hull.
- Less pitching due to less weight in the ends.
- Able to withstand a tighter headstay without bending or damage.
- Makes a huge difference to windward ability.
- Much lower chance of deck leaks due to less flexing of the entire structure.
- It’s pretty much impossible to build a solid fibreglass hull that does not flex at sea, at least without turning the boat into a slug.
- A higher ballast-to-displacement ratio. Weight we don’t put in the hull can go in the keel.
- More sail carrying power.
- Less heeling.
- More easily driven.
- Better longevity over time: flexing begets more flexing, and on it goes.
Bottom line, stiffer lighter boats sail better than heavier boats, and can even have as good or better motion if the hull form is right.
And we can already see these advantages being applied by the French team in reducing the target displacement for the boat from the original 8 to 9 (18,000 to 20,000) to 7 to 8 metric tons (15,400 to 17,600 lbs) displacement.
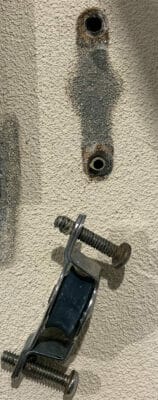
Of course, the big worry with core in the hull is water intrusion, but the use of epoxy and their plan to vacuum infuse will reduce that risk to a fraction of that of polyester boats with balsa cores, the method of construction that has generaly given cored boats a bad name.
Talking of which, although we have had to fix a few areas of wet balsa core on our J/109, we have found no large areas, despite some truly stupid fitting installation mistakes (both by the builder and after market) that had been letting water into the core for years. This seems to confirm that vacuum infusion limits problems.
Bottom line, I think a hull cored with epoxy is a good call. That said, I will be even happier if they use some sort of closed-cell core material that will further limit water migration issues.
Let’s Go To Bermuda On an Adventure 40
OK, now we have a modern, but moderate and wholesomely-designed hull built out of durable but light and stiff materials.
Cool, but what does that really mean when we get out there cruising on an Adventure 40?
To understand that, come along with me on a voyage to Bermuda. Why Bermuda? If your boat won’t get you to Bermuda, south across the Bay of Biscay, or across the Tasman to New Zealand, quickly, safely and comfortably, it’s not a boat you want to go voyaging in.
Yes, the following is a fantasy, but one based on my over 25 (lost count) transits of one of the tougher pieces of ocean on the frequently-traversed cruising routes.
Let’s say we are three-and-a-half days out of Newport. We left in company with some friends on a typical modern wide boat with a very wide stern.
So far, it has been a reach with the wind in the northwest to north, where it has been since the cold front came through the night before we left, so our large-tushed friend has stuck with us—just about any boat will sail halfway decently on a broad reach.
But now clouds are building and the wind has been veering all day and finally settles into the southeast, blowing 20-knots true, gusting higher, and quickly building a nasty sea, as the east-bound low-pressure area to our north drags a warm front over us.
Bermuda is now dead to windward and still 150 miles away. We strap the boat down, trim the vane gear, and shelter under the hard dodger, as Vincent’s hull form starts to show that this is exactly the conditions he was thinking about when he drew her and engineered her stiff and strong hull.
A few hours after the wind shift, our friends drop below the horizon behind us. Their boat is staggering and rounding up in every gust and being stopped dead and knocked off the wind by every wave.
They are barely making 2-knots good toward Bermuda as we romp on, pointing high, with a velocity made good (VMG) of better than double that, toward the St. Georges Dinghy Club bar.
We chat on the VHF and they tell us that their lightly-built boat is flexing badly and so every hatch and port is leaking, turning the interior into a sodden mess.
And, to further add to their misery, the erratic steering behaviour of the boat is making it impossible to use their vane gear or autopilot, so they are hand steering and getting soaked by every wave while doing it.
A little more than a day later, aided by a bit of tactical cunning playing the veer to the southwest as the cold front comes in, we beat through Town Cut just for the fun of it and tie up to the Bermuda Customs dock, four-and-a-half days out of Newport, and with a powerful thirst that only a Dark ‘n’ Stormy will satisfy.
Four days later our friends are towed in looking battered and bedraggled. Apparently, the slamming and flexing got so bad that they were forced to heave-to for a day, which let a secondary low that formed on the front catch them with its associated gale-force winds.
That resulted in two more days heaved-to before the wind finally veered into the northwest and let them make Bermuda. At least the wind didn’t die completely, as it often does after frontal passage, because the water that was getting into their boat sloshed out of the shallow bilges and flooded all the electrics, taking out the engine.
Just a day dream? Hang out at the Customs dock in Bermuda and you will see many realities that look just like the experience of our imaginary friends.
Not Just For Going To Bermuda
So is the Adventure 40 just an offshore boat? No, her capabilities, while perhaps not as vital for coastal cruising, will still make getting there way more fun.
For example, the Bras d’Or Lakes, here in our home province of Nova Scotia, is one of the most wonderful and unspoilt cruising grounds in the world, but it’s also, more times than not, an over 100-mile stone beat against the prevailing southwest winds, which often pick up in the afternoons to the mid-twenties, to get back to our home waters in Mahone Bay, and three times that distance to get back to Maine.
And year after year, when going back west, we have seen most other cruisers staggering toward home, motor sailing while pitching horribly or, worse still, trying to drive their overloaded marina queens directly into the wind under power alone—a futile business once the waves get over one meter.
An Adventure 40 will change that chore into a fun series of boisterous but satisfying day sails between the lovely harbours of the Nova Scotia Atlantic coast. There is nothing, but nothing, like settling in for cocktail hour bathed in the smug satisfaction that a smoothy-executed sail against tough conditions confers…and watching other boats straggle in hours later is kinda fun, too…wait, who wrote that?
And then, after a couple of days, when the wind finally goes around to the northwest as the next high comes in, blowing a gusty 18 to 30 knots—northwest winds are almost always gusty on this shore—the easily-driven hull form and directional stability of the Adventure 40 will let us sail a fast and fun broad reach with the vane gear doing the work, while other cruisers spend a day struggling with the helm, as the changes in heel angle with every gust mess with their boat’s asymmetric hull form.
Trade Winds?
And what about trade wind passages off the wind, the ones we all dream of? Surely a wide-sterned boat will be better? After all, race boats are designed that way.
Nope, that only works with a boat that planes, which is not something that happens on a heavily-loaded cruising boat.
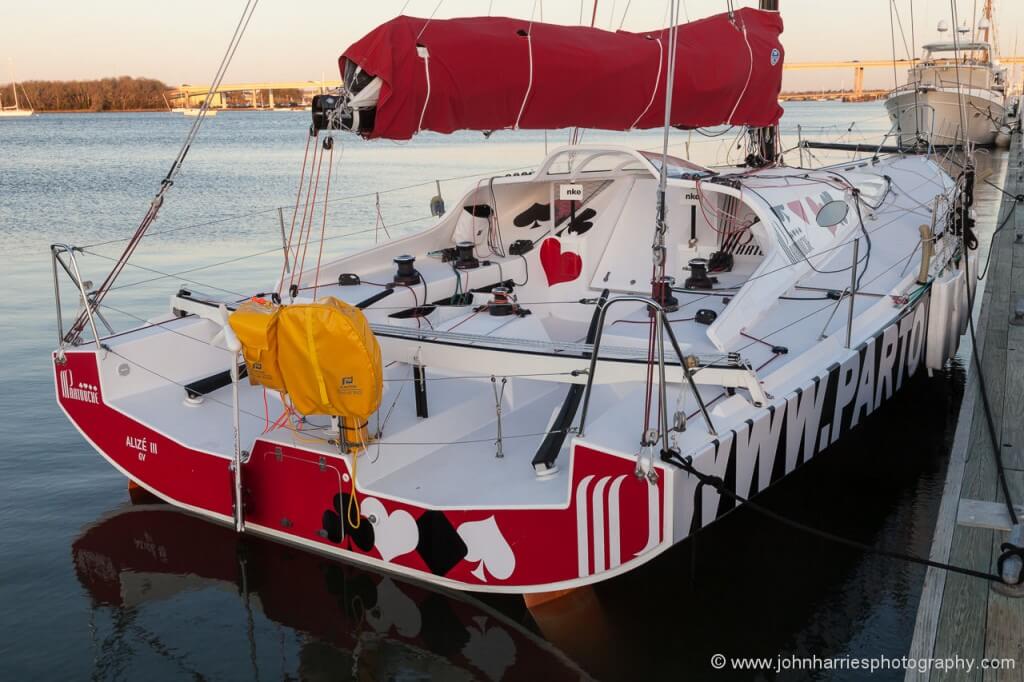
Summary
As I’m sure you have figured out by now, I’m excited about the way this is going. The French team are closely sticking to the base concepts of the Adventure 40, but bringing their own experience, modern developments, and innovation to the table.
Coming Next
Next, we have a fascinating paper from the team on the rudder, complete with an innovative idea for backup steering, and then we are on to the keel and how it will be made as resistant as possible to grounding damage, including another innovative solution.
And, somewhere in all of that, the French team want to get your views on the best way to finance the design process, so we will publish an article for discussion on the options they are considering.
Comments
So what do you think? Is an Adventure 40 the boat for you? Please leave a comment.
is there a cost advantage in staying under a 12m LOA? in terms of marina availability and cost etc
Hi Marcus,
Sure, there’s almost always a marina cost and availability benefit in making a boat shorter, although I know of no particular break point at 12 meters—we have discussed this a bunch of times before. In my experience, generally marinas jump their per foot or meter charge at 50 ft.
But, regardless of that, we certainly don’t want to constrain Vincent from coming up with the best boat he can by adding a limit driven by that criteria. The whole concept of the A40 is that her primary task is to sail well, fast and comfortable over long distances, and the more length we have for a given displacement (within reason) the better she will meet her primary mission. Also, more length makes it easier to design a functional layout below, as I explain in the linked post.
In summary, the best way to end up with a good boat design is to stay focused on the primary goal and not ham string the naval architect with a bunch of other limitations.
Hi John,
Sounds like these guys are the right team. I was already thinking that a vacuum infused and cored construction would be the right solution, and that epoxy would be great. Vinylester is a good alternative, almost as strong as epoxy, but epoxy is the real deal, as long at they use some proper heat cure process, at least 50 degrees C for at least 8 hours. Most epoxies cure fine at room temperature, typically taking about a week for a full cure at 23 degrees C, (“hard” is NOT cured!) but they all get both harder and stronger plus more flex tolerant from heat cure. The difference is really significant. The high end epoxy / carbon products use 120 degrees C cure cycles. Not for the faster cure, but for strength. That’s not realistic here, but 50 degrees C certainly is. This will be everlasting boats.
I also love the awareness about size. A boat length of perhaps up to 43 foot, giving the same boat “size” as a 32 foot boat is in my mind definitely the right way to go. So many advantages. The trend of squeezing in more interior volume isn’t based on actual thinking about advantages versus disadvantages. It’s just a gradual loss of grip on reality, a sickness. A 32 foot 40 footer is NOT cheaper than a 40 foot 40 footer, but it’s certainly an expensive, slow and uncomfortable 32 footer…
PS
In the beginning, Maxine should be Maxime, if I remember correctly?
Hi Stein,
I too wondered about heat curing, but I guess that will be up to the boatbuilder selected and Vincent to thrash out, when the final laminate is being specified.
As to overall length, it will be fascinating to see how Vincent uses the flexibility we are giving him. I bet he is one happy naval architect about that, since, as I understand it, most commissions include an overall length limit. One of the big reasons we get so many bad boats. Also, I think, a lot of the reason for the modern trend to plumb bows with all the attendant problems.
Thanks for the correction, fixed now.
Hi John,
Since they plan vacuum injection and epoxy, which are definitely ambitious choices, I’m pretty sure they are already planning a heat cure. It’s less challenge than the vacuum injection system itself. Also, if the mould is warm, the epoxy gets thinner and the injection process goes much better.
Hi Stein,
thank you for the kind words, and for the advice regarding curing!
As John correctly guessed, whether there will be heat cure or not is not known now, and will be only when the builder is selected.
I personally can’t wait for this to become reality. We’re a cruising couple, currently sailing a 36 footer in the Med, with cruising plans to take us around the globe. We’ve been looking at 38-42 foot (used) HR’s as our next boat, and the Adventure 40 is serious competition at this price point.
Hi Thomas,
I think that’s a smart comparison in that I’m pretty sure the A40 will be more boat for the money, than buying an older HR and refitting it. The other problem with many of the HRs, good boats though they are, is too little storage and very little deck accessible storage.
For me that is the comparison for sure. Buy a high-quality bluewater cruiser or an Adventure 40.
I like the A40 being new so its a known history and systems installation methods are known by me (not multiple previous owners). Don’t have to deal with rudder fixes, keel bolt unknowns, rigging inspection and decisions that are not mine, old wiring, etc. etc.
It might be less glamorous an interior than an HR or similar, but I prefer well-designed and built than looks. Also, if it has a simple Herreshoff style interior that would be perfect for me. 🙂
Whoops… meant to say “buy a high-quality USED bluewater cruiser or an Adventure 40” LOL
Hi Kevin,
I think that’s a really good way to look at it. Your comment definitely resonates with me right now as I struggle with fixing a bunch of that kind of stuff on our J/109! It the A40 had been available it would have been a no-brainer.
Hi Thomas,
thank you for the message. I personally can’t wait for meeting the people and projects the A40 intends to serve – I hope the timeline will be right!
Two things: are they planning on taping the hull/deck joint? We did that in all the boats I’ve built, and find it crazy that it’s rare with production boats.
Also, bagging a cored boat is an environmental nightmare. Unless things have changed, it would be two giant bags/peel ply/breather or flow medium/hoses/dumdum/etc in the dumpster for the hull, two for the deck, per boat. Every time a crew of people threw one away I’d dream of kicking sheets of uni on a counter and building the damn boat like it was wood.
Or just wet layup and living with some extra weight since it’s production.
Hi Michael,
I agree that bolting hull and deck together is a very poor solution. Structurally weak and inevitably leads to future leaks. Joining the two parts with fiberglass tape and epoxy is the right method. If the core goes to the joint, that needs to be done both on the inside and the outside. The latter leaves a 10cm strip in need of a nice surface. Perhaps an extra cost, or maybe it can be covered by rubber?
I also feel bad about the large areas of release films, breather, vacuum membrane, hoses and sealant tape that goes into the dumpster with normal vacuum bagging. However, with vacuum injection, it can sometimes be done in one go, depending on what system they choose. That cuts the waste in half. Also, no breather cloth is used, and sometimes no peelply or release film, just the membrane. Probably they will have to use some of that here, though.
It’s now possible to make multi use membranes. They’re normally made from silicone rubber, roughly shaped to the mould and attached to a frame. When the fibre and core is ready, just put the frame on top of the mould, clamp it onto the rubber seam, adjust the membrane as it seats and watch the resin fill in. Super easy to use. Such membranes are expensive to make, but the massive reduction in waste materials, plus big time savings and a much more predictable good vacuum makes it totally worth it, unless only a couple of boats are to be made.
All these elements reduce the waste to not too bad. I think it might compare favourably. Especially if we remember that wet layup non vacuum methods lead to a lot of wasted application materials, a much higher resin consumption and a much less durable boat.
Products that last very long are environment friendly, because they don’t force us to buy more stuff all the time. Consumerism is one of the main problems we have. We’re tricked into buying garbage. I’m convinced that this boat will be strongly established on the opposite end of that trend.
Vacuum infusion generally saves more material than it wastes. Yes, you have a large *volume* of bag, peel ply, etc. to discard. The bag, at least, should be recyclable. But the *mass* of that stuff (and its compressed volume, after a trip through the hydraulic trash masher) is pretty small compared to the mass of resin that is saved versus a hand-built wet layup. And, as Stein has pointed out, reusable vacuum membranes are now becoming common.
The total environmental impact of building a boat is as much about longevity and durability as it is about shipyard practices. A hull that will last for 80 years has a vastly lower total impact than one that must be scrapped after 40, even if its manufacturing process were to produce somewhat more waste.
Cored construction with hand layup, balsa sheet, and polyester resin is a manufacturing (and longevity, and repair) nightmare.
With vacuum-infused epoxy and a good closed-cell foam like Corecell M, though? And with the foam segments being precisely CNC-cut, leaving solid material at the fitting and bolt locations? No concerns here. None at all. That’s a very good way to build.
And another benefit…. a one inch cored hull has an R value of about 7, versus <1 for solid fibreglass of the same weight. Now you don’t have to insulate inside the hull if you’re visiting cold climates. That saves money, time, space, and mildew.
Hi Matt,
Good point on the insulation properties of cores. There are few things more uncivilized that a solid glass boat on a damp cold day with condensation running off every inside surface.
Hi Stein and Matt,
you clearly are more competent on this than we are!
Regarding the environmental equation, yes, exactly, our very first objective is to make the boats as long-lived, and as likely to be used intensively, and to be intensly useful, as possible. Of course, this argument shouldn’t be taken as a whishful-thinking excuse for doing nothing else – but it remains the primary objective.
The point about one-use infusion materials versus the quantity of boat material they save is well-taken!
We had only heard of the existence of silicone multi-use membranes, but have not dived into the equation yet. I think I’ve heard that, even if not using them for the very first builds, it’s worth making sure that the molds’ flanges are compatible. Anyway, one of the many points to be discussed with the prospective builders!
Hi Michael,
if by taping you mean no bolts, yes, sure! However, the specifics of bonding the hull and deck (and bulkheads) haven’t been devised yet. They will be discussed with Vincent and the builder.
So glad the boat is not getting bigger. Under 12M’s would be perfect for me. In my opinion, soooo many new boats are just being built too big.
A smaller boat without all the extra cabins would have the space for the necessary storage and access to systems. Maybe the saloon area can accommodate guests or extra crew but for a limited time only. Sounds perfect to me.
Also, a bit off-topic but I hope you continue to include a well-thought-out plan for dinghy storage. If I recall the original articles mentioned the use of an arch for dinghy storage while inshore and locker space to stow it when deflated while offshore. Seems like a good practical solution. I am surprised how often new boats are designed without really thinking of where to put a dinghy. Heck, a Bristol Channel Cutter 28 (BCC 28) has two spaces to stow a hard dinghy but modern boats not so much…
Fit for a particular purpose with well-designed solutions would be a breath of fresh air.
Hi Kevin,
all duly noted, thank you for the input!
I continue to be excited about this project, and would love to find that it is the right boat for me. Please keep writing John!
While we’re on the subject of external criteria that shouldn’t be applied to a boat: the ICW air draft is 20 meters (I think?) which would be nice to stay under. Probably not a real concern?
The ICW air draft is nominally 65 feet (19.8 m) and staying below that is indeed a very important criterion for any boat that’ll be sold to Americans on the East Coast.
Mast height also has a very significant impact on cost. It would be very difficult to build a mast much higher than 60 feet while staying within the Adventure 40’s cost targets.
Hi Nathan,
With this displacement and probable righting moment, I can’t see the mast being even close to over the 65 foot waterway limit.
That said, at 6.5″ meter draft she won’t be a waterway boat per se, but should be fine for the deeper parts like inside Cape Hatteras. Probably won’t work for some parts of Georgia and none of the New Jersey waterway. But, given that’s she is primarily an offshore boat, she will be great for going outside and missing those parts.
Hi Nathan,
yes, we will be far from the ICW air draft limit.
As Matt says, there are big drawbacks to too high a mast. And we’re not competing in the tallest-mast-in-the-marina contest!
Hi John,
This all makes sense. There is one thing that I really hate about epoxy that I haven’t seen discussed and that is the need to have a painted hull rather than gelcoat. When you talk about cost of ownership and such, this kind of dooms the owner to a $20k? repaint every 10-20 years depending on a bunch of factors whereas good gelcoat can last a heck of a lot longer. I am not expert enough in composites to have a firm opinion but if there were a way to do the boat with gelcoat by using something like vinylester and being careful with the order of operations on the build, that would be nice.
The cored deck thing is an interesting question and I grapple with parallel questions all the time at work. As we push for more performance in things, that forces us to accept designs with harder or more expensive construction and service methods and it is hard to look at this holistically, we typically look at a single example at a time. An example where it has been really successful is with electronics where the chips have gotten so good, huge amounts of analog circuits have been replaced so while the chips are super hard to make, the overall design is better although it does become unserviceable but an equivalent analog version would be super hard to service anyways. An example of where this is better due to trade-offs is modern car unibody construction methods where you get a stiffer car that is much safer in a crash but at the cost of it being much more expensive to repair and somewhat tougher to build. An example of something where I really struggle with is how everything has become power operated in cars, even retracting door handles which are cool and do decrease drag a bit but will likely be a nightmare later in the cars life especially as it isn’t just door handles, it is also doors, seats, mirrors, etc. To me, building the hull as cored is similar to the unibody car example, you get higher performance but with added complexity in build and service. Assuming that they can hit the cost targets with the build, the issues in terms of service are with a grounding and owner modifications. Groundings and collisions that compromise the hull skin are not super common and require major repairs anyways so don’t bother me a ton. Clueless owners and yards compromising the core are a big deal as a repair can get scary large, hopefully mitigated somewhat by vacuum infusing, and I don’t know how to prevent this. One thing for sure during build would be that checking that all thru hull fittings have no core showing would be an excellent in-process inspection to have. I hope the team plans to have a quality inspector on-site during all builds and part of the build plans are specific, measurable inspections intended to catch the big problems.
Eric
Regarding the painted hull: I think it’s more maintainable in the long run, even if you have to re-do it now and then. No coating is going to stay perfect (UV, dings and scratches…), and gelcoat is a lot harder to repair than just re-painting a small spot.
As for the cored hull, I think they got a bad rep from low-quality boatyards not treating them with the care they need. I’ve got one on my new-to-me, 42-year-old boat and the survey didn’t reveal any problems with it. I think this has a lot to do with the quality of initial construction (it’s a C&C), and it has had some very careful owners who took good care of it.
Now that I think of it, I think the cored construction might be why the boat doesn’t “creak” under sail like so many do.
Hi Emile,
Good point on why the boat does not “creak”, despite her age. Pretty much any solid laminate boat of that age is pretty soft and bends a lot, at least if she has been sailed a lot.
Hi Emile,
In my opinion, maintaining a gelcoat hull is far easier than a painted one for a boat intended to go far and likely without perfect cosmetic maintenance. As Stein points out, the gelcoat is much more durable in the first place and it is also much more forgiving around things like deck fittings. I also find it not that hard to repair although getting an exact color match is definitely tricky if you are really particular about it.
I think part of our difference of opinion may be around what the cosmetic standards are of a potential A40 owner. If they are trying to win awards at the boat show year after year, then I would recommend painted too but that use case comes with a ridiculous amount of hull and deck maintenance however you do it. If I understand the A40 buyer right, they are buying it for the core principles of the design including low cost of ownership and being able to go places. For ongoing cost of ownership, there is no question in my mind that if you don’t demand cosmetic perfection, it is possible to maintain a gelcoat hull for less than a painted hull although you will need to look past a few dings that are too deep to polish out or a few small repairs with imperfect color match. For reference, our gelcoat is almost 40 years old and has <5 scratches that are too deep to polish and none can be seen from further than 5′ away and our previous boat was quite similar. Our only gelcoat repairs have been on deck and including both the deck and hull, we have maybe 4 hours a year on cleaning, polishing and waxing. And for those who are not satisfied with it being a 5′ look, they can always paint over the gelcoat. It is certainly possible to paint yourself but by the time you pull every fitting and do all the prep, paint, and reinstall all the fittings, it is an absolutely enormous project whose opportunity cost must be considered.
I agree with your thoughts on cored hulls and done right, I prefer them for a performance oriented boat but if you were trying to do an updated Westsail 32, then I wouldn’t see the point (and would have no interest in buying the boat in general). Done wrong from the factory or messed up later, repairing a cored hull or deck can quickly get into many thousands and even tens of thousands of dollars. For this boat, I lean on the side of it being worth it but it isn’t a slam dunk to me and I think we need to be aware of the trade-off that is being made.
Eric
Hi Eric,
Definitely agree on gel coat being way, way, easer and less expensive to maintain than paint, and I have had both for long periods. I also agree we need to factor this into maintenance tasks.
That said, having just done a few repairs to a cored boat, although not personally (I delegated) I really don’t think it’s that much more difficult than fixing a hole in a solid boat, or that much more expensive for that matter. West System have a bunch of videos and instructions on fixing an old J/Boat that are useful.
Of course I’m referring here to a relatively low tech composite boat. Which brings up another point, kind of in agreement with yours, being that we don’t want to go so crazy high tech that it takes an oven and specialized skills to repair the boat to original strength.
i was under the impression that nowadays epoxy paints are superior to gelcoat and way easier to repair than the latter. some manufacturers are developing rolling additives so that you can roll without tipping and get a spray like finish. the maintenance of said paints are the same as the gelcoat, ideally one would would apply a protective compound twice per season, buff and polish accordingly
Hi Pedro,
The paints you think of are probably things like Awlgrip, Alexseal and DoubleCoat. They do have some pretty great properties, but they’re not epoxy based. Mostly they are some variation on polyurethane. They can indeed give a finish by just rolling (no tipping needed) that can compete with a pro spray job. I’ve tried the DoubleCoat and seen others use Alexseal. Impressive.
The surface of these paints are better than gelcoat when it comes to keeping the colour and shine, and they don’t really need polish. The weakness is that they build a much thinner layer, so it takes less to get a visible scratch, especially if the foundation is a different colour. I like these paint solutions a lot, but gelcoat is far more robust.
Hi Stein
i stand corrected about the paints. i was indeed refering to polyurethanes, not epoxy (but got confused because their primers are epoxy based) im actually going to paint my topsides with Alexseal in the coming weeks, using that new additive. can only hope it goes to plan!
Hi Pedro,
I think you’ll be happy with it, but make sure you have the right conditions. It’s as sensitive as spray paint, of course. Andy at the YouTube channel “Boatworks Today” is sponsored by Alexseal and has done some tests with the new additive perhaps a year ago or so. I haven’t got time to look for it now, but it contains some very useful detail advice about how to do it.
PS
Maybe it’s this one: https://youtu.be/jFLsOR9riM0
There are more videos about this on that channel…
Hi Stein
I know Andy, he is the one responsible for me going with Alexseal!!
After i saw one of his episodes painting a dinghy with a roller, i said :thats it, this is what im doing. Great guy and channel.
i am waiting for it to warm up a bit more but im also constrained due to typhoon season which starts from April onwards, and anyway then it becomes insanely hot in this place.
So far its been good even if ive applied the fairing compound 3ºC lower than the minimum recommended temperature of 15C, so ive waited 4 full days before any sanding was done , and im quite happy on how it turned out.
Hi Eric,
Good point on the painting downside of using epoxy. I should have put that in to the article. I wonder if this could be fixed, as you suggest by using a layer of vinylester between the gel coat and epoxy? I’m guessing not, if the boat will be cooked off in in an oven, but I really have no idea. The other thought is to build the entire boat with vinylester, given that it is in fact an epoxy based compound but is compatible with gel coat.
Anyway, I suspect that these things may indeed change a bit when the builder gets involved.
One thing I’m pretty sure of is that if the core is a closed cell type and the boat is vacuum bagged and infused she should be pretty much proof against water intrusion into the core. As I write above our J/109 has been surprisingly resistant even though she is balsa cored, and my old Fastnet 45’s decks were cored with Airex and yet had no core water intrusion problems at all despite none of the fitting fastenings being potted and literally scores of them having leaked for years when I got the boat.
Hi John,
I am not knowledgeable enough on composite construction to know how to allow gelcoat but it does seem that vinylester might be part of the solution.
It is good to hear your J109 has done well with its core. I have dealt with various deck core issues over the years although none truly major and have looked on in horror at some of the projects that I have watched being done at the local yards. I have also heard plenty of claims that it is fine to have a mushy core, I wonder why those people think there was a core in the first place?
Eric
Hi,
regarding water infusion:
our boat is about 40 years old, self built, hand laid in polyester.
The deck has a balsa core, and the hull sides have an Airex core. Bottom is solid glass.
Having pulled a couple of deck fittings, it seems that the balsa has suffered pretty much anywhere where there is a bolt through the deck – where as when cutting a hole through the part with Airex, it was dry as paper, and trying to separate the Airex from the laminate seemed next to impossible.
(Same goes for the solid glass bottom, where drilling a hole for a depth sounder showed that with good gelcoat, the solid hull has kept dry.)
These experiences – particularly with the part with Airex in it – seems to suggest that a closed cell core material might be a very important factor on its own in terms of ensuring no water intrusion, even with no vacuuming.
I don’t know which is a bigger factor in terms of building cost between vacuuming, choosing epoxy, or using a closed vs. open cell core material, but I would imagine that if the price difference between closed and open cell is not big, closed cell would be an obvious choice.
Hi Vesa,
Thanks for the real world confirmation on that. Bottom line, I can’t see a good reason for balsa, other than cost and maybe being a bit lighter, but the latter not enough to make sense for this boat. And one of the core A40 values is longevity of the basic structure will always trump cost, even if we have to break the budget number to get it.
Hi John,
I agree that balsa is probably not ideal. The core itself is actually about 130 kilo per cubic metre, while the foams normally used for hulls are typically 80 kilo per cubic metre. (Water is 1000 kilo per cubic metre.) Still, balsa can make a lighter completed sandwich laminate. The fibers go from skin to skin, giving a much stronger resistance to compression. That makes it possible to use thinner and lighter skins with less fibre while keeping it “strong enough”.
Much cheaper core with less materials in the skins is a quite tempting idea for builders. Especially because this is also strong, until water comes in… “Planned obsolence” is a well established thing. I think many boat builders use balsa for the mentioned money saving, but perhaps just as much to make sure their boats don’t stay on the market forever…
It’s possible to do it better. If a balsa sandwich laminate is made with vacuum infusion, the durability is very much better, as the gaps between the balsa pieces gets saturated, which stops water from spreading. I’ve done some testing with this a lot of years ago. It gets really strong, but I’d still not choose it.
The extra cost of epoxy or a fancy foam is significant. It can be twice or three times as much. However, looking at the total price for a cruising boat, those cost differences typically end up below 5% or max 10% of the finished boat cost. In my mind, very good materials and building methods is the very best place to “waste” money. Nothing else we do on a boat, except for top notch design work, can get anywhere close to this cost / benefit ratio.
Stein,
basically what you are saying is that with a price difference an equivivalent of, say, a couple of MFD’s both renewed once in a lifetime of a typical boat, you can have a hull that lasts virtually forever – as opposed to potential water intrusion, a squiky boat, and a hull that has half the useful life?
Balsa is great for model airplanes – but for boats it is always suspect since the cell structure is ’designed’ to suck water from the roots up to the leaves, which it does very well. It is also biodegradable – which it also does very well.
Paying that extra for epoxy and good quality closed cell foam, amortizing the cost over 40 years, or being able to resell the boat saying no osmosis, not wet core, solid grp in all the right places for mounting stuff from the get go, are starting to sound like a real bargain!
Hi Vesa,
Of course I can’t quantify the price difference precisely, but in essence yes, that’s the type of conclusion I draw too. This is valuable for owners, and some special interest builders, like this, but not to companies serving “the general market”…
When balsa is used in sandwich constructions one should only use it as end grain pieces. The wood is cut in very short pieces and laid up next to each other, usually on a scrim. One must never do as is normal in model planes, where the wood is the actual strength and the fibers run parallel to the surface. The advantage of fiber direction must be aligned with the primary loads. The main jobs of a sandwich core is to hold the skins at a fixed distance from each other. Almost all other loads on the panel are carried by the very thin skins. The main exception is point loads that can penetrate the skin. This is where balsa really shines, because its end grain is way harder than any realistic foam.
As a very rough guideline, I’ve found during builds that when the hull and deck have been made and it all starts to look like a boat, it feels like it’s just the finishing touches before it sails. In reality, at least (!) 90% of the work and expenses are still ahead of us… That’s why massive cost differences in that part of the build won’t influence the end cost anywhere near as much as one would feel. However, if “only the best is good enough” is the attitude through a whole build, there’s plenty of ways to make every stage get far more expensive in both materials and build complexity. That way the end price will certainly suffer much more.
The obvious solution is to make the right choices in the right places…. Duh! 🙂 I really think this project is extremely well equipped to do just that.
Hi Stein,
I agree, the danger to the project in this thinking is not limiting the added money spending to things that really matter, like the hull. Still, I think that as long as we don’t stray from the core values and start putting a lot of fancy and expensive gear on the boat, it should be possible to get the balance right. This is one of the reasons I’m so dead set against anything that does not contribute to the basic mission for the boat, like bow thrusters, or even the provision for them.
Hi Vesa,
Your comparison to a couple of MFDs really brings this into focus. I suspect I will steal that for a future article!
Hi Stein,
I totally agree with your last sentence. This kind of thinking is fundamental to making the A40 different and better, and without doing that, why bother? The world does not need another disposable boat.
If the weight difference between balsa and any of the foams is more than a rounding error in the 3rd significant digit of your weight budget, then none of those materials are viable candidates to begin with. At that point you’re already well into the rabbit hole of Nomex honeycomb and carbon prepreg laminates.
Balsa core was the least bad option available 40 years ago. I’m hard pressed to think of any reason to use it anywhere on a boat today, not when Corecell M and Airex T92 exist.
Hi Matt,
Here’s another reason to stay away from balsa, and that’s weight. I’m reasonably reliably informed that when TPI went over to vacuum infusion mid production on one or two of the J/Boat designs, the boats got significantly heavier than the boats than had been built with the resin applied by hand and rolled in. The reason being that the vacuum process sucked a lot of resin into the kerfs in the balsa sheets. And while that added resin was good for preventing water migration, it did not add any useful strength.
I also remember that Richard Elder confirmed that the lightest and strongest balsa boats are hand rolled out, although a lot depends on the diligence of the applicators, so probably not something we want to do on a production boat.
This should not be a problem with closed cell foams, I’m thinking.
Hi All,
More than 15 years ago the Hanse Boat Builder launched a range of epoxy vacuum built sailing boat from 37 to 63 foot length. The external coating was gelcoat.
They were racer-cruiser type and the design was from Jüdel and Vrolik, German naval architect.
Having a circumnavigation project in mind, and after all the same considerations John developed with the Adventure 40 project, I made the choice of the 43″ model. She was launched in Jul 2007, and after a serious preparations we set sail, my wife and me, in July 2008 for a 8 years voyage. We were back in 2016 after some 50000 NM.
This type of building, epoxy, close cell, vacuum bag, had given to us a strong and safe boat, with a very good isolation we tested under the snow in Patagonia.
Of course, as a production boat, we have had to cope with the fancy double steering wheel, a ridiculous chart table but the internal layout was pretty good after the addition of handholds…anyway!
We are still sailing Uhambo, and she is in French Brittany at now, and the gelcoat is stil in good conditions!
Bonjour Alain,
thank you for the feedback! It’s good to learn that the build type made your decision even though some other features were not ideal for your mission. Long live Uhambo!
Hi Eric and all,
thank you Eric for starting the discussion of paint vs gelcoat. It’s true that paint is a likely drawback of going with epoxy. The only advantage I can think of, with no gelcoat, is the ability to better control the result of the infusion process.
The ways to avoid paint would be, as you mention, to “downgrade” to vinylester (but this would require a super-solid proof that we’re not significantly downgrading the long-run durability of the boat), or to combine epoxy with a gelcoat – but we haven’t heard this is easy to do.
So, we’ll discuss all this in detail with the prospective builders (I know, my answers must sound quite predictable!). And to date, the most likely outcome is that we end up with paint.
Just putting this into the mix; instead of a bonded-in finish, or painted finish consider Vinyl Wraps. They have come of age and are very quick to apply by experts with good robustness and durability that are now acceptable to builders. Matters such as colour fast, repairability and ease of replacement have all been addressed in premium wraps. A 45′ boat with 1.35m freeboard, a tad over $4000, according to some USA suppliers. A UK supplier sales brochure (I have no association with this company) https://yachtwrapsuk.co.uk/wp-content/uploads/2021/01/Yacht-Wraps-Brochure-2020-21-3.pdf
Hi Alastair,
sure, this is to keep in mind, thank you for the addition!
Hi Alastair,
Yes, wraps are an interesting idea. There’s a guy locally here who swears by them, and I have seen a couple that look pretty good. I do wonder, through, what happens when the wrap is finally done and needs replacing. How do you get the old stuff off? Looks to me like it could be a nightmare. the other problem is that I can’t see wraps doing the deck area, particularly the non skid, and that’s the bulk of the cost of painting, and particularly repainting, a boat, not the hull.
Hi Alastair and John,
to go into more detail: even when focussing on the hull sides, I don’t see how the wrap would avoid the first layer(s) of paint – although we’ve not looked at this in detail. But this doesn’t rule a wrap out.
Hi Maxime,
Your response may be predictable but I think it is wise. These trade-offs are often much harder than are made out in casual conversation. Because different resins allow different layups to be used if you want to go to higher end glass, you get interesting trade-offs of initial cost, weight, secondary bonding issues and longer term maintenance and the answer will be somewhat dependent on who the contract manufacturer is and what their capabilities are. Theoretically this could be done in a highly analytical fashion against a set of analytical requirements but I doubt that makes sense here and it is probably better to do it as a qualitative assessment informed by a few quantitative things like relative cost of resin, cost of repainting, etc. In my line of design, one of the things that sets apart the good designers and design teams is knowing when and how to lock certain aspects of the design down. People tend to either try to make too many decisions early which means they have to compromise other parts of the design or they never nail anything down and they never finish. I am hopeful that your team can navigate this well and I agree that you want to have your manufacturer selected for this type of decision to be finalized even if it means going contrary to the literal interpretation of John’s post that epoxy is a done deal. If only there were not the painting problem, then I think this would be an easy decision for all the reasons mentioned in the post and the comments.
Eric
Hi Eric,
That makes sense to me. I’m also perfectly willing (not that it’s my final decision) to be open minded about a change to the base specification that goes against something I have already written, as long as it makes sense within the core values of the boat.
The point being that I tend to write as if things are a done deal and locked down, simply because too many qualifications gets boring and stifles progress, but that does not mean that once I write it, it can’t be changed or is a done deal, even in my mind.
The biggest reason for this process, other than getting people interested in the boat, is to get input from a lot of people. Your point that epoxy needs paint and the resulting discussion is a good example of that.
I can, and am willing, to write about why we made a change, as long as I believe that said change will make the boat better. For example, maybe a change to vinyl ester and gel coat will make sense, but, as you say, we won’t know that until a lot further into the process.
Hi Eric,
Thank you for the kind words and advice. Yes, we’ve found that we have a trade-off to make between locking too many parameters and leaving everything open, just as you say. And the decision on epoxy is a good example. Obviously, when we’ll go to the builders, some of them will say “hey, you’re taking this too far, vinylester is ok” – and this will be the start of interesting discussions, even if we end up staying with epoxy.
I don’t know if there is a way to bond new epoxy to gelcoat inside a mold, coating the female mold with gelcoat, and the laminating with epoxy over it.
The other way around seems quite possible – as long as the epoxy has cured and amines have been cleaned off:
Boatworks Today tested by glueing two pieces of plywood, one laminated with polyester & glass, another with different West Systems epoxies & glass together with gelcoat.
The results were surprising:
in two of the tests with West 206 & 207 hardeners, the glass and poly pulled out of the ply before the gelcoat came off the other piece of ply & epoxy.
So, it is certainly possible to get gelcoat to stick to epoxy.
https://www.youtube.com/watch?v=kHAbyglpp3M
West System’s manual also states that gelcoat on cured epoxy is not a problem.
I guess that leaves the problem of getting wet epoxy to cure in a way so as to not have the amine blush mess with the epoxy bonding with gelcoat in the mold.
Perhaps a layer of vinylester or some kind of a primer on the gelcoat prior to epoxy?
Epoxy should tack onto a cured ester, if not the other way around. Perhaps that would be a way of getting a gelcoat finish on an epoxy boat.
To get straight to your question, yes I think the A40 is the boat for me. We can all armchair the design night and day, but all boats are a compromise. Given the parameters, I’m in.
Hi Blair,
That’s great to hear!
Hi Blair,
thank you – I do hope the future articles will confirm this!
I like the idea of the cored construction for the reasons stated in the article. I presume the fabricator will have Quality Control/Quality Assurance processes in place covering all aspects of the hull fabrication from material quality and storage through the vacuum infusion process to curing. Based on my personal experience with the fabrication (as owners “project manager”) on a large scale cored FRP “Wind Fairing” installed down both sides of the length of a very large suspension bridge, and on multiple steel welded orthotropic roadway deck fabrications for very large suspension bridges, I would recommend: (1) consider implementing a Destructive and Non-destructive test program on a pre-production prototype (using all the production means and methods including curing and post cure edge trimming & hole cutting) to determine if there are any quality issues (low/lack of resin areas, debonding/delamination etc) with the proposed detailed method of fabrication, and to show it can reliably mass produce product without issues; (2) be wary of using high pressure water-jet cutting equipment for hole cutting and edge trimming particularly if the hole cut or trim line is initiated by an initial piercing jet, as the water jet can cause interlaminar delamination at the initial piercing and along the line of the cut in low resin/weak areas; (3) use the Destructive Test results to calibrate Non Destructive Test methods that you plan to use during production…on the FRP fabrication I was involved with in 2003 Laser Shearography (spelling ?) was used with difficulty and limited success…presumably methods have advanced since then. If minor issues are documented, use the opportunity to develop acceptable production repair methods; (4) consider random sampling for Destructive testing during production runs if production quantity gets high ( every 50th hull ?)….you could be surprised what you would find. On a separate note, would it be possible to build in accommodation (areas of Non cored hull) for possible owner later installation of items such as a retractable bow thruster, forward looking sonar fittings etc ? …. or is this even a concern ?
Hi Carl,
Interesting, although far past my pay grade to really understand. Anyway, good QC has always been a core A40 aim: https://www.morganscloud.com/2012/05/19/adventure-40-reliability-quality/
Also, I think it likely that the French team will award the build contract to an established builder with a good track record, so they will already have experience and have been through the learning and R&D phase on other boats. I’m also guessing that Vincent will engineer the boat with higher safety margins than something like a bridge fairing where weight is (I’m guessing) super critical, which will make the whole process a lot more forgiving of small manufacturing inconsistencies.
As to areas with no core, yes, that’s planned as we will see in a future article. That said, I would fight tooth and nail to prevent any provision for a bow thruster, or at least a retractable one. I have been ship mates with the latter and can say the damned things are an abomination looking for a chance to fail. I also know of at least one boat sunk by a retractable bow thruster.
The key point here is there really is no reason that a boat as small and easily maneuvered (more on that coming) in tight spaces needs a bow thruster.
Hi John,
I totally agree that a bow thruster is misplaced on a boat like this. It would very rarely contribute meaningfully and would certainly cost a lot and have other significant disadvantages. Since these conclusions are kinda obvious once we just try manoeuvring, I have wondered why so many boaters have so strong emotions about needing one. I think it’s mainly fear of being a fool in some harbour next to a beer drinking place.
The thruster seems similar to a crutch for someone who can walk, but isn’t sure about that. This gut feeling of insecurity seems to be very normal among even reasonably skilled skippers. That means that thruster or not will influence the second hand sales price noticeably, perhaps more than the price of the installation. I would guess this is an increasing trend. I don’t like it, but I think it might be worth a strategic consideration.
Perhaps one method could be to just put in a tunnel in the boat, but closed off. It’s just there so it’s very easy to install a thruster if someone would want to. Just cut open the holes in the hull and install the thruster. That tunnel might console the nervous buyer and would cost very little extra in production.
Hi Stein,
The idea of putting a tunnel in and closing it off is interesting, but I’m guessing that so doing may constrain Vincent as he designs the bow shape to get in the thruster and keep it immersed. If that’s so, then I would be dead set against it, because it violates a core A40 value: sailing comes first.
The other thing is it will add weight in just the wrong place. And quite a lot since the structure must be strong to support any sort of useful thruster.
I hear you on the resale thing, but then again, if we get this right, we are going to create not just a boat, but a whole group of sailors around that who understand what really matters and who actually go to sea.
Almost a cult, if you will. So maybe we actively want to boast about not needing a bow thruster with this boat: “are you a good enough seaman for an A40”. “the more you know, the less you need”. Or we can get really politically incorrect: “a real woman (or man) with a tiller and an A40 don’t need no bow thruster”.
And another thought is that the A40 is never going to appeal to the marina-boat crowd anyway, so do we want to make even a slight compromise to appease them? I say no. Stay pure. Putting a bow thruster on an A40 would be like putting a Blackberry keyboard on an iPhone.
As a person new to boating, but enthusiastic about becoming a long term cruiser, plus being an engineer, and a likely single handed sailer most of the time, to alleviate the often mentioned concerns about docking in difficult conditions, the ability to add some front end lateral trust when needed seemed like a good thing. But that said, I have no problem deferring to expect sailor advise that “better sailors don’t need no thruster” and make do without it…hopefully it will lead to some good tall tales for the bar.
Hi Carl,
Your comment makes a good point in that clearly there are benefits to a bow thruster and those benefits, as Stein wrote, tend to appeal, justifiably, to those new to offshore sailing, a big segment of the people we are hoping to attract. This is why so many new boats, even small ones down to 30 feet have thrusters.
But what that misses is that bow thrusters have huge disadvantages too. Most notable weight in exactly the wrong place, and the drag of the tunnel that I have seen credibly estimated at 10% of total hull drag. They are also very expensive when we take into account modifications to the hull and the electrical system required to support them.
So what we need to do is reframe the question as: “yes, we hear you want a bow thruster, but are you willing to drag a bucket behind the boat at all times when underway, and have a boat that pitches more into a sea, as well as spending 10-20K, to get it, particularly since a couple of hours reading this online book and a day or so of practice will make it so you don’t need a bow thruster.” https://www.morganscloud.com/category/docking-tying-up/online-book-docking/
Or to put it another way, for some reason that escapes me, even quite experienced yachties never bother to learn how to bring their boats alongside even though it’s actually an easily learned skill, and that unwillingness to learn is the core reason for bow thrusters, even though they have a truly terrible cost benefit trade off.
I would suggest that the design of the hull, keel and rudder, would not limit handling under power such that a bow thruster was desirable. Having sailed many different fin keel and spade rudder designs of yachts, many LOAs, all handle well under power, are predictable and easy to start, turn and stop, even in limited spaces and with folding propellors. From what I have read about the A40, I see no reason why this generalisation would not hold true and in fact, is a positive attribute of the style of design being developed, ease of handling under power.
Hi Alastair,
Quite right. In fact the team have specifically targeted close quarters maneuvering. I will be sharing that in the rudder article.
Hi all,
Alastair, as John already confirmed you’re right that the general configuration of the boat makes for relative ease of handling under power. Our task here is only to make sure that all small decisions add to this attribute.
As to having a bow thruster versus learning close-quarters maneuvering, let’s add that going out with twin rudders hence no prop wash, or with a folding propeller with poor thrust in backward (two more things often done), are arguably each more difficult than no bow thruster.
Put a drone 100′ above the boat and film it doing some manoeuvres, getting off the dock in an onshore wind, etc.
People think they need thrusters when they’ve never seen boat handling done properly without one. It’s not a hard mindset to break out of, given video evidence.
Hi Matt,
Yes, I have long thought about using a drone to show some of the techniques I have written about in our Online Book on close quarters boat handling. And, in fact, that book already includes a couple of illustrative videos
That said, I think that text and drawings, as we have used extensively, are a better way to actually teach the core techniques since the key to success is understanding the forces as work, which video is poor at.
For example, many of the how-to videos on YouTube promote a monkey see, monkey do, mind set without imparting the real understanding that produces a boat handler who can handle most any eventuality.
And don’t get me started on the monkey see, monkey do videos that proport to teach how to install a lithium battery system.
I’m not thinking how-to videos (you’re absolutely correct that the format you’ve used in the articles is better for teaching).
Rather, I’m thinking of video proof that this particular boat can in fact be handled precisely and professionally without needing a thruster.
Hi Matt,
Yes, I agree. In fact we already did one to show just that and it has proved popular over the long term: https://www.youtube.com/watch?v=oD_WgCveuro
That said, I think you are right, a drone’s eye view, preferably including cuts to action on the boat and wharf, would be the ultimate in proving that this can be done without thrusters. Might want to do that with the A40 prototype.
Hi Carl,
thank you for the input on quality control. In addition, let’s recall that most possible builders are relatively small businesses, with a strong interest for long-term reputation. That doesn’t make formal quality processes non-relevant. But pride and skin in the game by someone who is there on a daily basis can be another important factor too, all the more that here we already have an owner’s forum where no weakness will go unnoticed.
So the challenge might be to find arrangments that best combine all these possible processes and incentives – another issue that only in-depth discussions with prospective builders will clarify.
Epoxy costs are very sensitive to oil prices and pressure on oil prices will likely remain high for medium term. Most forecasts today are already above the pre covid future forecasts. Epoxy being more expensive than other resins, this may have a noticeable impact on the final price (I have read by up to 3 times more than polyester resin). We shall see. Regarding the environmental foot print of vacuum bagging or the waste stream, Epoxy releases almost no VOCs unlike Polyester, so there are greener positives with Epoxy, plus it doesn’t burn like polyester does.
Hi Alastair,
Thanks for three very good points on epoxy. One thought on the cost is that I think I’m right in saying that hull materials are usually less than 10% of the total cost of a boat, and if that’s right, (Matt, Stein?) and we assume that the resin is say 25% of that, then it would seem that the increment for epoxy resin would be less than $7,000. Not trivial, but I think a saleable cost/benefit ratio to the market.
Hull materials being about 10% is approximately right. Labour, probably double the cost of materials. Once you’ve got a complete hull, keel, structure, deck, etc. all put together, you’re *at best* 30% of the way to a finished boat. Sometimes less, if it’s a fancy boat.
Epoxy resin is $2500 to $5000 per tonne, in 1+ tonne quantities. Polyester is $1000 to $2500 per tonne. Corecell M80 25mm is $100/m2 retail and probably half that in full container loads.
An 8 tonne boat is about 3 tonnes of lead, 3 tonnes of hull/deck/structure, 2 tonnes of everything else, and has maybe 150 m2 of laminate.
Back of the envelope, I’d guess you’re looking at maybe a $10k premium to build the $250k boat with top-quality foam and epoxy resin, instead of whatever generic stuff happens to be cheapest on Alibaba this week. Owners ought to make that premium back fivefold on depreciation to 15-year resale.
Hi Matt,
Thanks for doing the numbers on that. Certainly worth 10K in my view. Unless we come up with something else, I think that then leaves Eric’s point about gel coat instead of paint as the most important criteria for this decision.
I remain very interested in this boat and love the open discussion of design decisions. Robust sailing performance is increasingly important as climate change throws old patterns out the window.
Is the “And if she is:” box the regular newsletter sign-up or a specific answer to the call for the level of interest at this point?
Hi Damon,
That sign us is specifically for those interested in the A40 and is a different list than the one we use for member notifications. As of today we are up to 587 people interested in the A40!
Hey John, this question may be way off topic in that you probably crossed this bridge a long time ago – but particularly with the “French Connection”, the vast experience this architect and the European community have with aluminum, the collective admiration on this site for the Boreal oeuvre – why was chine built aluminum dismissed for the A40? Could be cost competitive by dispensing with moulds, all panels laser cut to high precision from CAD files? Simple curvature conic sections easily wrapped into a water-friendly form? All the advantages you are familiar with of high local strength, integrated components like tanks chainplates, etc.? And thinking of the green concerns in the preceding comments, ultimately recyclable.
Hi Rich,
That’s come up several times, but the bottom line is that aluminium, while I love the material, is better suited to shorter run boats, rather than a mass production run like the A40. More here: https://www.morganscloud.com/2013/01/07/adventure-40-faqthe-boat/
I recall reading elsewhere in this wonderful website that stability and resistance to rollover follows the cube of displacement. Once the decision to build with a core was made, was the idea of building the boat a little larger to keep the origional target displacement considered instead of making it lighter?
Hi P D,
good question. No, the trade-off in size is governed by being large enough to fit the payload and the accomodation required by the mission, without cheating with the hull shapes, and no larger than this, to keep things as affordable as possible. So lighter goes to lighter. The heavy weather strategy is to carry a Jordan Series Drogue, the necessity of which won’t be much diminished even by adding a few tons.
(also, when we say “this follows the cube of displacement”, we should ask “what else being kept equal” – there is more than one way of adding displacement. I’ve not given precise thought to this, but I wouldn’t be surprised if the relationship isn’t as overwhelming as it sounds at first)
In addition to removing the core “in the way of fittings and through hulls” would it be possible to work out the ideal place(s) for ultrasonic antifouling transducer(s), and remove the core there?
https://nordkyndesign.com/ultrasonic-antifouling-system-part-2-fighting-algae-growth/
https://www.morganscloud.com/2020/04/03/ultrasonic-anti-fouling/
Hi PD,
Interesting idea, but I don’t think we want to get into adding that kind of edge case to what is already a complicated specification given that very few people will actually install such a system given that there’s a lot of differing reports on whether or not these systems are actually useful.
Point being once we start to try and accommodate edge cases like this, there will be no end to it—we have to keep the boat as simple as we can since every add to the spec adds money.
That said, removing the small amount of core required to install a system like this is not a big deal for an owner.
We will be providing hard pads for added transducers and added seacocks.