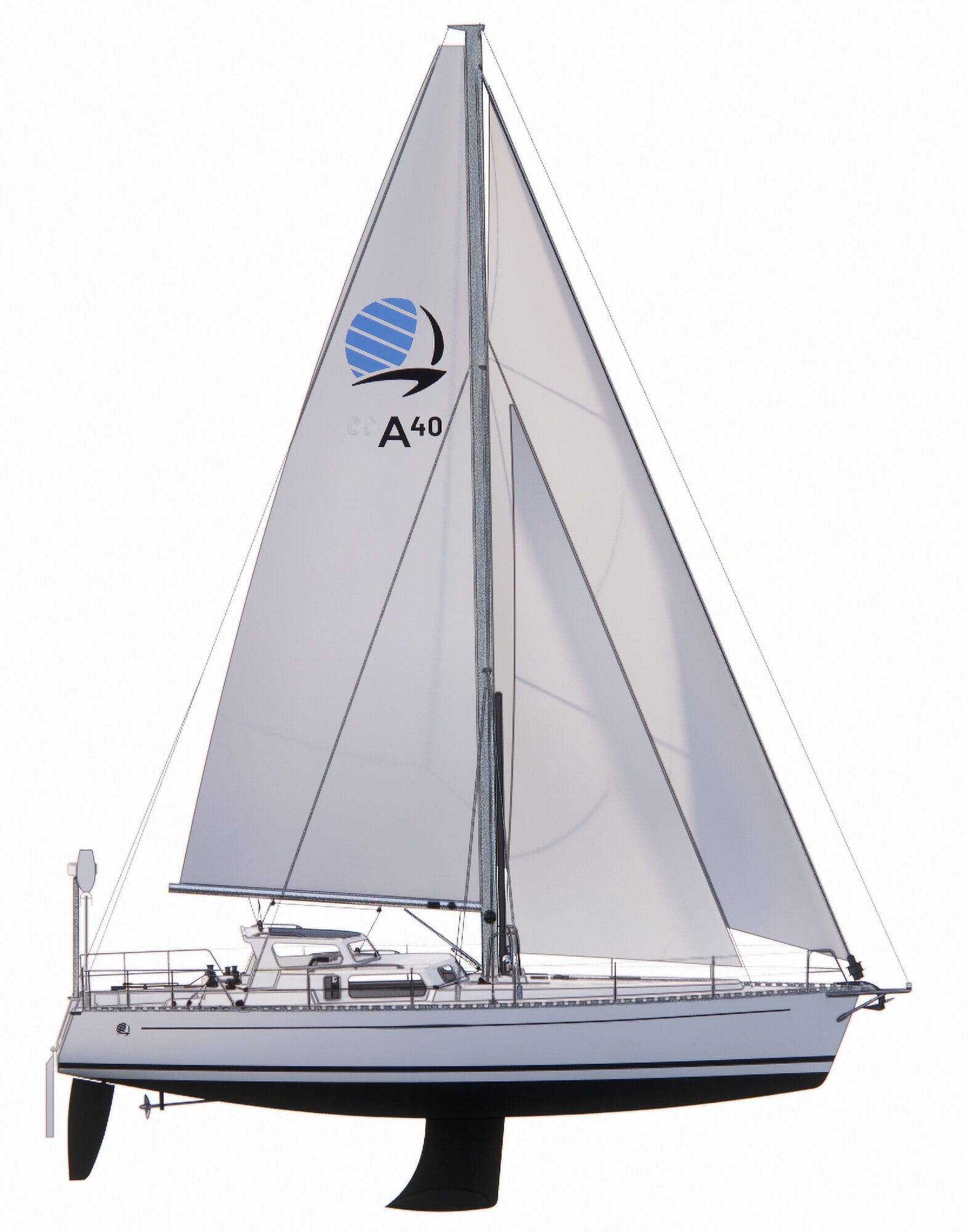
Rudder and Steering
In the last chapter we examined and discussed the Adventure 40 hull form. Now let’s dig into the rudder and steering gear.
Single Rudder
A single rudder is not negotiable for the Adventure 40 since twin rudders are more vulnerable to floating debris, expensive, and get us into needing a bow thruster, since we lose the power of prop wash. Twin rudders are a bug, not a feature.
Spade Rudder
The Adventure 40 will have a spade rudder with:
- A partially-balanced design for easy steering.
- Partial balancing is great since it reduces load on both autopilots and vane gears as well as making the boat easier to steer generally.
- Ease of steering is doubly important on a tiller boat where we can’t make up for an inefficient rudder by fitting a powerful wheel setup.
- A composite shaft and no metals inside so we don’t get the water ingress and corrosion problems that rudders with metal shafts in composite blades are always prone to.
- By the way, our new-to-us J/109 has exactly this kind of rudder with no metals, and that’s one of the reasons Phyllis and I selected the boat.
- Massive shaft and bearings to take the loads reliably.
What About Skeg Rudders?
What about a skeg-hung rudder, that much-loved alternative of traditionalists and forums?
I used to be a fan, and, like many, believed it was the only seamanlike alternative, but after years of thought and discussion, I’m now satisfied that the superiority of skeg over spade is a myth, not a fact.
Or, as some wag said, many skegs are held on by the rudder, not the other way around.
The point being that rudder reliability is far more about good engineering and construction quality than type.
The other two disadvantages with skeg-hung rudders are:
- Can only be slightly balanced.
- Generally far less efficient than spades, both when sailing and manoeuvring—our J/109 with a spade rudder steers in reverse as well as she does in forward; the McCurdy and Rhodes 56 with skeg rudder, not so much.
Why Not Transom-Hung Rudder?
While he gave a transom rudder serious consideration, Maxime has decided against it for the following reasons:
- A kick-up or cassette rudder adds complexity and many more potential failure points.
- The actual practicality of replacing a rudder blade at sea is suspect, and what if the pintles and gudgeons fail or get damaged?
- Having the rudder right on the stern makes it very vulnerable to accidents in harbours and anchorages.
- I can confirm this. Over our years of cruising we have been hit at least twice on the transom by other boats trying to dock behind us, and have also backed into unseen obstructions a couple of times.
- By moving away from transom hung, and because the boat has a tiller (more on that in a minute), it will be possible to allow very large rudder angles, which is a simple and effective way of substantially increasing the manoeuvrability—be great in the ever more congested marinas we are seeing these days, particularly for a boat with no bow thruster.
- While possible, it is difficult and more complicated to build a transom-hung rudder that is partially balanced—part of the area being forward of the pivot point.
- The stern is already a busy place on an offshore voyaging boat what with vane gears and maybe water generators. Adding those two to a transom-hung rudder would be a mess, and maybe not even doable.
- It’s difficult to install an underdeck autopilot on a boat with a transom-hung rudder, at least in a seamanlike way.
All that’s pretty convincing, but the deal breaker for transom-hung rudders is that they are much more vulnerable to stalling and cavitation, and that gets way worse as the boat heels.
What About Backup?
Any rudder can get damaged, and rudder loss is one of the most frequent reasons boats are abandoned at sea. I think that the best practical answer is a drogue as a steering backup, rather than any sort of backup rudder.
Tiller
The Adventure 40 will be steered with a tiller, not a wheel.
Tillers have fallen out of favour in recent years, mostly because many modern designs have too high steering loads as a result of designing for large interiors rather than good steering manners under sail. Think fat sterns to cram in big aft cabin(s). This is also the reason for the rise of twin rudders.
I also suspect that a big reason for the dominance of wheels these days is that standing behind one gives us guys a feeling of power—women seem to be immune from such silliness. I often joke these days that buying a J/109 with her huge and cool-looking wheel means that I now don’t have to buy a motorbike.
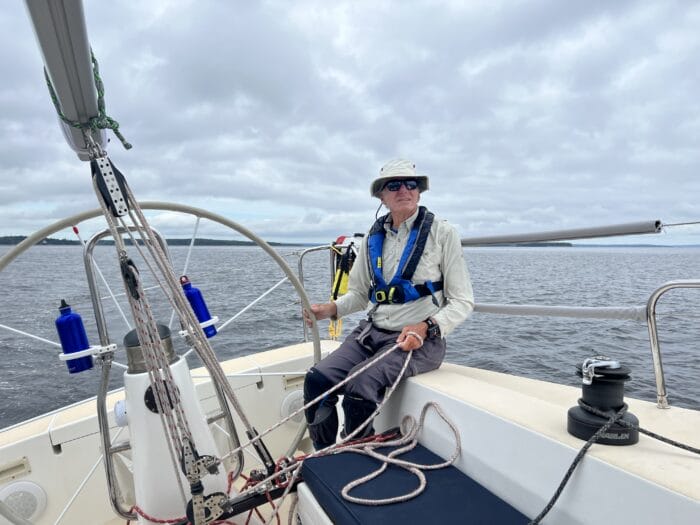
When we design a boat that’s all about sailing, particularly a fairly small one like the Adventure 40, tillers make the most sense.
Here are some of the reasons:
- Much less expensive. In fact, the savings over a wheel, of several thousand dollars, will more than cover the costs of, for example, up-strengthening the keel-to-hull joint and the rudder.
- Removes the problem of designing the cockpit so that a crew member can get around the wheel without the dangerous, and far too common, need to jump up on the seat (see photo below).
- This in turn allows the cockpit seats to be longer for a given cockpit length, since on a boat with a wheel the only right way to solve the above problem is to cut the seats away in the way of the wheel—as J/Boats have done (really well) on the 109, see photo above.
- Much easier and more efficient to use with a vane gear.
- If the tiller is hinged where it joins the rudder head, it can be lifted into a vertical position, thereby freeing the cockpit for entertaining or just generally moving around more easily.
- Much easier to design and install an emergency tiller.
- The fact is that most emergency tillers on boats with wheels are a joke that will never work in real life offshore, or at least not for long.
- Intrinsically more reliable than a wheel—far less to break.
- More effective and faster to move the rudder back and forth from lock to lock when manoeuvring in tight spaces.
- Frees up a huge amount of room in the aft end of the boat by removing the quadrant and associated cables.
- Removes the danger of a loose piece of gear fouling and jamming the steering gear, an all-too-common and dangerous problem.
- The underdeck parts of wheel steering gears should be completely boxed in to prevent this, but most are not.
- Much easier to reach the winches than from behind a wheel.
- Way more fun to steer a boat with than a wheel. You have to experience steering a well-balanced tiller boat to get this, but I promise you it’s true.
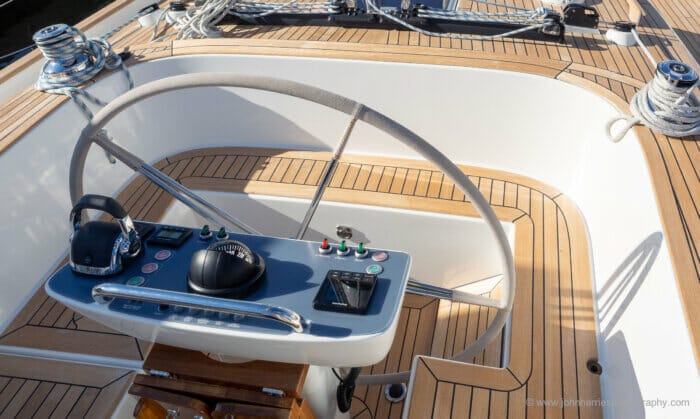
As you can see, I’m a huge fan of tillers, but, of course, like anything, there are downsides:
- No binnacle to mount a cockpit table or engine controls on.
- Mounting the controls intelligently high up on the coaming pretty much solves the latter problem.
- When underway, the sweep area for the tiller must be kept clear, which reduces the number of people who can sit in the cockpit comfortably.
- If steering with a powerful underdeck autopilot, we must be careful that the tiller does not pin someone to a seat or coaming. This one is probably the biggest tiller problem, and one we will need to think about.
- Perhaps we can solve this by allowing the tiller to hinge up to vertical and lock.
That’s all I can think of on the downside, so a clear win for a tiller.
Self Steering
Now let’s turn our attention to self steering.
The Adventure 40 will come standard with a vane gear installed. This is an unusual step these days, but in keeping with the mission of offshore cruising, and achieving that in the simplest way possible while spending money on construction quality not fancy gear.
That said, I know that there will be owners who will prefer to install an underdeck autopilot as well, so the Adventure 40 rudder shaft will be designed and built to take an autopilot tiller arm, with a strong point glassed in to take the other end of the autopilot ram.
It will also be important to make provision in the design for adding more batteries to the standard bank the boat comes with to support an autopilot.
Bottom line in all of this is that those thinking of an underdeck autopilot for their Adventure 40 should budget US$15,000 to US$20,000 for the pilot and electrical system upgrades to support it.
For the rest of us, who decide to keep that money in the cruising kitty, a simple tiller pilot will do when sailing inshore, when setting up the vane gear is too much of a pain, and when motoring (in or offshore), particularly now that there seems to be a quality option offered—if it were me buying an Adventure 40 that would be my preferred choice.
Further Reading
Comments
Let’s talk about it in the comments.
Sign Up As Interested In Buying an Adventure 40
And if you can see yourself at the tiller of an Adventure 40, please sign up below—the more names we get on this list, the sooner we get an Adventure 40 to sail.
Note that this is a different and additional list from our member mailing list.
On the tiller pilot… have you seen that Scanmar has acquired Pelagic autopilots and have solved the windvane/tiller pilot integration problem with an “off-the-shelf” solution? Though, with a tiller, this is less of a benefit. But, still cool nonetheless. https://pelagicautopilot.com/products/autopilot-for-windvane-self-steering
I’ve had very good experience with my Pelagic autopilot as replacement for an old Raymarine tiller pilot that I never really liked. I installed the Pelagic a couple of years ago on my J/92 to enable single-handed racing.
Mike Scheck (original developer) is still with the product at Scanmar and provides great support. He even updated firmware to allow adjustment of tacking angle after I suggested it following my first race:
https://vimeo.com/482216199
Correction: Brian Boschma is the original developer, and still supports the product for Scanmar. Mike is the Scanmar President; both have given me excellent support!
Yes, Mike and the folks at Scanmar provide exceptional service. I bought mine vane gear from the at the Annapolis Boat Show in 2014, and they have ALWAYS been super-responsive when called upon. Great company!
Hi Tom,
That’s very good to hear, particularly since a J/92, being a performance boat, will require a smart pilot, particularly when racing, and even better to hear that you are getting good support.
Hi Ken,
thank you, very interesting to know! The compactness seems to be a big plus. Of course whether an owner will want to fit this will depend on one’s strategy on redundancy. At first glance and from a personal point of view, the combination of no big underdeck pilot + Pelagic electronics + small actuator on windvane + actuator on (auxilliary) rudder seems attractive!
Hi Ken,
That is interesting to see, and might be of benefit in light air. That said, most vane gear manufacturers caution against using the vane gear this way to steer when motoring because of the damage that the turbulence from the prop causes to the bearings and linkages in the gear.
I’ve been a member for years and have been following the Adventure 40 since it’s initial concepts. I hope to buy one. This is my first post.
Awesome news on selecting a tiller over a wheel!
Thank you!!
Hi Marc,
thank you!!
How does sailing away from the coast into blue water render a normal tiller pilot inappropriate?
i.e.; needs to move under deck.
Normal tiller pilots – Raymarine for example – suffer from moisture. The Pelagic electronics are below deck, the ram is robust, and it is more strongly built than the others.
Hi PD,
Generally, in the past, tiller pilots have not been very reliable, particularly when called upon in big breeze and waves, but in those conditions a properly set up vane gear does great, so for ocean voyaging typically a tiller pilot is only used when motoring. The other benefit of this approach is that it reduces the demands on the electrical system by a huge amount. More on that coming.
The Pelagic has a separate sealed control head that can be mounted away from the arm, as well as an arm driver box connected to 12v and mounted below decks. I keep my control head in the cockpit on the bulkhead with buttons facing aft, but I suppose nothing prevents you from mounting it below deck as long as you can keep it away from metal/electrical items. The arm itself is all metal and very simple/robust. Scammer sells spares at a reasonable rate; for example a spare arm for my system is $275 (https://pelagicautopilot.com/collections/accessories-and-spare-parts/products/spare-actuator-without-fittings). If I were going on a passage I would certainly pick one up!
Hi Tom,
Thanks for the real world first hand information on that, always the best kind.
Hi all,
just a few words in addition to the article, to emphasize once more why a spade rather than transom-hung rudder: since we want some stern overhang, the choice of rudder type has substantial consequences on where the rudder is or can be. A transom-hung rudder would be very far aft, and thus very hard to keep underwater in all conditions (think heel + waves) without messing with the hull shape.
And another small advantage that we had forgotten to mention: taking the rudder and propeller weight closer to the center of the boat is a slight plus for soft pitching movements at sea.
Hi Maxime,
Good point on the overhang. Sorry, missed taking that from your white paper. I will add it to the part starting “All that’s pretty convincing, but the deal breaker for transom-hung rudders is that they are much more vulnerable to stalling and cavitation, and that gets way worse as the boat heels.”
Very exciting. Thrilled with the rudder choice, and tiller. Hoping that the design team finds an ergonomic solution for a helmsman to reach tiller and engine controls while maintaining good visibility. The ability to hinge up and lock the tiller while under way using wind vane or autopilot would be very appealing. Happy for standard equipment wind vane, I would add an autopilot, either below deck, or a robust tiller pilot as suggested; design and build to accommodate either addition (perhaps a specific model) would be appreciated.
Hi Michael,
thank you for the input! I agree with all your points, all these are things we plan to do!
I don’t get an email trying to sign up for adventure 40 info, and yes I checked my junk
Hi Richard,
We have had a bit of trouble with this. I will go ahead and subscribe you by hand.
Fold-up tillers are great. They’re easy to design, make, and fix.
Re. Spade vs. skeg. Intuition and engineering often yield different results here. A spade rudder is a simple two-support cantilever; so easy to analyze and design that its core structure is a standard exam problem for second-year undergrads. A skeg rudder is a a parallel pair of point-coupled cantilevers with differing support constraints; proper and complete analysis of that requires significant expertise in finite-element modelling. It is much easier to make a good spade rudder than a good skeg rudder.
Re. Engine controls. By far my favourite way to do this is to put the rotary shift/speed handle from a modern mid-size outboard engine on the tiller tip. The control cables from that are easily linked to conventional teleflex cables at the rudder post joint. That leaves one hand free to work the spring line on a jib sheet winch while steering AND shifting with the other.
Re. Rudder construction. As I’ve said a few times before, all-composite construction with a composite shaft is vastly superior to mixed metal/composite for this purpose, and will have a practically infinite service life if well-made.
Great idea for engine controls on the tiller end like an outboard. I haven’t seen that done before.
Hi Matt and Kevin,
While I see the utility of having the controls on the tiller, as a sailor, (first and last) I would hate the clutter and complications on the tiller, particularly since I can see the engine controls interfering with a good tiller extension and and it’s stowage when not in use. Also I get nasty visions of what happens when I steer with the tiller between my legs, as is very useful on a tiller boat when using both hands for other things—we used to do this in 505s when hoisting the spinnaker.
So, to me anyway, the added utility of having the engine controls on the tiller, is not worth the downsides and complications.
Tiller-mounted engine controls are complexity creep, to be sure.
An interesting option that I’ve never seen on a sailboat, but that worked very well on a few powerboats I’ve seen, was to have the control head for a standard single-lever shift/throttle module hooked up to a foot pedal. One had stay-where-you-leave-it friction, like normal boat controls and unlike a car’s gas pedal, and had the same shift/throttle behaviour as a normal hand-mounted control. Another version (on a *very* fast jetboat) would come back to idle by spring, like a car throttle.
That might be worth a quick concept sketch or cardboard mockup, if a good place for a coaming- or binnacle-mounted control can’t be found.
Hi Matt,
Good point on the design complications of skegs. Having walked around boat yards looking at them, I would bet good money that on many, perhaps most, production boats the skeg had no real engineering done on it, and often it was just stuck on any old how, so in fact the rudder shaft is taking most all the load.
Hi All,
I agree that a spade rudder is easier to analyze but one on a skeg should not be too difficult unless 3 bearings are utilized in which case stiffness of the components starts to matter a lot. Also, it is not an either or choice, there are also partial skeg setups and these can be quite effective as the skeg no longer represents a highly cantilevered protrusion from the hull and you can put some balance into the rudder blade. They have their trade-offs too but can be a good option for certain boats. Our current boat happens to have one and it handles well including in reverse, has a reasonably good helm feel and the structure looks substantial and triangulated to me although I have done no analysis.
I think a much harder design task is to make a breakaway lower section of the rudder. Analysis of structures below the yield point is relatively straightforward but once plasticity is involved, it gets a whole lot harder and the number of engineers qualified to do it shrinks a ton. In other words, it is easy for an engineer to predict at what point some permanent damage will have occurred but much harder to predict how much of the seam between the breakaway and permanent sections will actually break in a given impact. I think the goal is to have it break completely away while limiting loads in the rest of the structure to below their yield limit. This is complicated by the fact that rudders use composites that have directional fibers and often involve imprecise layup techniques so the strength of any part could easily vary by ±50%. You can make this easier by really overdesigning everything else so that the breakaway value is not close to the yield value of everything else but by that time you have lost a lot of your benefit. Our boat actually has a breakaway rudder and when owners post pictures of it happening, most do not break the way you would like, it happens at different points, it often doesn’t fully detach which makes steering hard and since it is not fully detached, it often continues to delaminate the rest of the rudder by pulling on it unevenly. I am not saying you shouldn’t explore a breakaway feature I actually think that a well executed one is a great idea, just that it is hard to implement well and that you have to figure out how to prevent subsequent owner repairs from ruining this feature.
Eric
Hi Eric,
many thanks for this – very useful to have in mind!
One essential problem with a spade rudder is that, through collision or grounding, a metal shaft is likely to bend, with the rudder then getting jammed at an angle under the hull. This happened to me on a daysailer and it was impossible to motor or sail; even towing was very difficult. At sea the only recourse would have been to drop it out the bottom.
Now, presumably a composite shaft won’t bend : if the blade doesn’t break off then the shaft is likely to fracture, probably making it difficult or impossible to drive out of the bearings. Now what do you do?
Hi James and all,
It is my take, in casual observation over the years, that, statistically, if you lose rudder control at sea (and especially if pinned to one side), you lose your boat. And yes, there have been those who dragged a drogue or 2 and made it back to port, but I believe that there are far more who have given up, accepted a ride from a passing ship, and abandoned or scuttled an otherwise perfectly good sailboat.
That being my take, I would wish rudder integrity to be high priority, and that a functional auxiliary rudder be considered: probably one that works with the wind vane. I believe that Monitor wind vanes already have a design for one and that it is an option. I do not know whether it has a history of use or if there are other alternatives.
My best, Dick Stevenson, s/v Alchemy
That is addressed in this way.
“A sacrificial lower part that will break off without damaging the shaft, bearings, or hull in the event of a grounding or collision with debris.”
If at sea I wouldn’t want to drop my rudder. Then you have a big hole in the bottom of the boat.
Hi James,
That’s true about damage to the shaft, but the same applies with skegs since in most cases in a good impact the lower bearing, or the skeg itself fails so the shaft still bends.
As far as a composite shaft breaking off, surely that’s a better situation than a metal shaft bending, since at least the whole thing is gone leaving us to figure a jury rig or use the contemplated spare rudders? And as long as the bearing and bearing housing are engineered stronger than the rudder so they don’t tear out of the boat, the boat should still be watertight with the shaft still in place and the rudder gone.
We just had the rudder out of our J/109 and I’m pretty sure that it would shear off clean at the bottom of the metal bearing sleeve glassed to it.
Of course, all of the above presupposes that the sacrificial lower part does not work as planned.
Dick, Edward and John: you all make sense to me! Plus there’s a good chance that a really sturdy transom- hung rudder might take the transom with it in an accident. In several boats I’ve had bad examples of both, but the worst was transom- hung. Another thumbs up for tillers, they’re so much nicer to steer with.
“It bent just below the bearing” comes from using a uniform-section metal rudder stock that’s too weak at the bearing and too strong lower down.
The way you solve that is to make the composite rudder stock and blade progressively weaker as you move from the bearing to the tip, in proportion to the bending load expected at each point on the rudder in normal use. That results in good structural efficiency, minimal waste of raw materials, and a structure that – if abused, eg. by impact – will fail progressively, from tip upward, leaving the higher sections intact.
Hi Matt,
very true, of course! Thank you for underlining that.
After 2 years with a tiller on my Wauquiez Gladiateur, I’m a huge fan. With the tiller raised, I have a cockpit as big or bigger than much larger boats. Also, with a tiller extension, it’s easy to steer from almost any position in the cockpit or seated up on the coaming…tiller is a winner in my book!
The pinning someone with the tiller on autopilot issue can be solved by merely making a hinge in the tiller just forward of the AP mount- the tiller then folds back upon itself, clearing the cockpit when under AP. A quick flip and you’re back in control. This is in addition to the traditional hinge on the rudder head,
Hi Rob,
That would certainly help, that said the stub from the rudder shaft to the hinge could still, I suppose, hurt someone, at least when being driven by an under deck pilot. But then again, people can, and have, got hurt by an under-deck pilot turning a wheel so we might just want to use your idea and just tell people not to get aft of the hinge. After all, this issue is a lot less dangerous than getting close to a mainsheet traveler and not paying attention.
Huge fan of tillers. Especially for solo sailing. It’s funny when I read the article I immediately was thinking “great to have a tiller but what about the tiller pilot issue on a boat this size?” Only to keep reading and see that you are already working on a solution.
For me anyway it’s this kind of attention to detail (big and small) that will set this boat apart. Designed by people who actually sail. Keep these nuggets for an FAQ or design detail walk through of the boat (bow to stern with detailed explanations or links to articles here).
Hi Kevin,
Thanks for the support, and the plan going forward is just as you say.
Huge fan of tillers and vane gears here also. I once had a setup where the rudder swung through 360 degrees as the rudder stock angle was lined up with the hull. Very slick to back out through a mooring field as I could sing the rudder 180 degrees and motor along at speed just fine without that tiller “backing problem” of the tiller smashing your legs when you are in reverse. Just thought I’d throw that idea to the designers.
Oh, and big strong standard bearings from a company that will be around in 20 years would really be helpful when the time comes to replace the bearings.
Would the vane double as a boarding ladder?
Hurry up and take my money!!!
Hi Whitall,
We use our Monitor windvane as a boarding ladder from our dinghy quite frequently. It is especially handy when it is blowing and choppy, but tucked under the transom is much calmer.
However, it alone as a swimming ladder, does not work. Even moderately athletic, I could not come close to using it as a boarding ladder in clothes and I think I also failed in a bathing suit. This concerned us as it meant no access to the boat if you were alone and fell overboard, even at anchor.
It was that first step that was impossible: so I made a “stirrup” that hangs from the transom rails with light tape and is easily reached from the water. Easily pulled down, it rips the tape and falls into the water where it provides that first step onto the Monitor and all else is easy.
My best, Dick Stevenson, s/v Alchemy
Hi Dick
I fell off my Monitor last year while using it as a passarelle when Med moored. Fuelled by embarrassment and aged 66 I managed to scramble back aboard but I wouldn’t want to try it in a seaway. I was surprised by both my sudden surge of strength and by my stupidity. I hope nobody noticed.
Over the years I have had two Monitors, two Aries, one Hydrovane and one Haslar type self steering gears. Of them all I liked the Hydrovane the least and the Aries the most.
One drawback with the Monitor is the percentage of real estate it occupies on the stern of most boats. It leaves little or no room for a stern ladder or a water generator. It does, as you say, make a useful step when boarding from a dinghy.
The boat with the Monitor is for sale. The new boat doesn’t yet have a windvane. I am inclining towards following Colin’s choice of a Pacific. I wonder if he, also, was annoyed by the amount of space the Monitor took up.
Best
Mark
Hi Mark,
I am impressed you were able to get up and out: good on you. That is why I made the stirrup mentioned in the previous post which shifts returning to the deck away from an athletic event.
And Aries: my friends who were early circumnavigators spoke of Aries with reverence and would exchange hints on where to find parts etc. to keep them going.
And yes, the Monitor adds real estate: this is a concern the more you are in marinas and the like and not at all sailing and anchoring.
My best, Dick
Hi Whitall,
But where would you stand to steer with the tiller all the way around? I guess right aft. Anyway, I’m guessing the hull form would preclude that.
If the hinge at the rudder stock is fully articulating you just flip it over. There’s no stop, so don’t loose focus and drop the stick to the cockpit deck. I do this (not the dropping) all the time in my Ontario Yachts – Viking 34.
As to taking your money, I’m sure the French team would love to. More on that coming soon.. And I agree on bearings JefFa have been around a while so might be a good option. Just bought one for my 17 year old J/109 and it fit perfectly. The joys of production boats.
Hi Whitall,
wow, this 360° rudder swing is something I’ve often dreamt of! That said, the auxilliary tiller for windvane lines, and the clutter aft of the rudder shaft, will likely preclude this on the A40…
Assuming the hull shape can accommodate it, you can do a 360° rudder arc by making a hinged tiller that’s able to flip all the way over the top instead of just forward & up/clear. The hard part is underwater, making sure the rudder can spin that far without hitting the hull.
Hi Matt,
thank you for the tip! Hadn’t thought of that. That leaves the issue of the auxilliary tiller and its windvane lines. Plus of course, if there’s an underdeck pilot, we cannot do this. And underwater, there’s also the issue of propeller clearance.
Anyway, such a setup would have to be used very carefully… and I hope you will forgive me if I don’t see engine controls in the middle of this!
Hi Maxime,
I’m with you on worrying about the creeping complexity of adding too many features to the tiller set up. As in many things on boat, each feature we think about seems attractive alone, but then when we combine them we more often than not end up with a horrible mess. Aim for as simple as possible, I say.
The finest implementation of a tiller and autopilot I have seen is in the Breehorn 37.
The rudder head incorporates a short extra “tiller” for the autohelm to work on, under the main tiller. When on autohelm or in port, the tiller folds back up against the backsty and can be hooked there, leaving a clear cockpit but still functioning pilot on its micro-tiller. This seems better than a hinge part way along. Picture attached (but not very clear). But why not ask Breehorn for details? They are lovely people.
Also, their tiller is long enough to steer from well forward under the spray hood in poor weather, but sit to the side for good vis when you want. Because it hinges completely away, it is no annoyance.
Hi Richard,
That does indeed look like an interesting implementation, and the small tiller could even be made removable for those who opt for an under-deck autopilot.
Hi Richard,
sure, this is the kind of setup we have in mind! And tiller pilot or not, we’ll likely need some sort of auxilliary tiller somewhere for the windvane lines.
I saw a very neat solution to attach windvane lines.
Similar to Richards post above except the additional tiller arm faced aft.
The windvane lines attached to this behind the tiller, completely out of the way.
The tiller can fold up out of the way as normal.
It does of course require enough space behind the rudder shaft, so doesn’t work for every layout.
Hi Dan,
yes, we have this in mind: the auxiliary tiller can look both ways!
Here is an extract from Nordkyn Design on Rudders.
What has always impressed me is the fact that should the stock become bent it can be lowered to ensure that the rudder top does not jam on the hull. Also if you go to the site you will see how the tiller can be raised and disconnected at the press of a button whilst also being connected to an autopilot
It really is a very very worthwhile read written by an exceptionally talented engineer and sailor.
Nordkyn uses a single spade rudder. It is a concession made to resilience to damage because twin rudders would be more efficient. A single spade rudder is effectively protected by the largest and strongest skeg a yacht can have: the deeper ballast keel in front of it. Rudder skegs are detrimental to flow, rudder balance, and steering performance. In addition to this, they tend to come with much smaller rudder stocks and the strongest argument is not always that clear-cut.
Here, the rudder blade was balanced to allow using a tiller for steering, even when the foil loads up.
Should Nordkyn’s massive rudder stock ever get bent and jam the rudder blade, provisions were made to allow dropping it down a short distance from within the boat to restore hull clearance until repairs can be carried out.
Twin rudder options were not progressed due to their very real exposure to damage:
Hi James,
I would agree with most all of that, except maybe that twins are more efficient, a lot of variables here including wetted surface and added weight, so I think the relative efficiency would be one of those, it depends, things. Anyway, safety from debris closes the deal for single.
Hi James,
thank you – “provisions were made to allow dropping it down a short distance” intrigues me a lot, but I didn’t find the webpage where to learn more?
https://nordkyndesign.com/nordkyn/development/
Thank you!
The site is https://nordkyndesign.com/
If you go to Design etc., you will have a very informative few hours of reading. The speed in light air is excellent and downwind fantastic. Many other good ideas/suggestions too
Another benefit of a tiller is to control speed when coming into a slip, picking up a mooring or slowing down to anchor under sail. In case the engine is inoperable, it’s important to be able to handle you boat under sail. A tiller makes close quarter handling much easier and safer.
Coming into our slip under sail with too much speed (+4 knots or so on beam reach with prevailing westerlies) it’s comforting to be able, with a sharp turn into the wind with a tiller, to slow down to 1.5 knots, get back on course and glide into the slip up wind under control. Love tillers!
Hi James,
You are so right, a few fast course alterations can bleed a bunch of speed. On the other hand, if we run out of speed in a light air approach a tiller boat can be sculled in as well, another win, win.
this just keeps getting better. I am stoked that it’ll have a tiller. I changed my 65′ Pearson back to a tiller after someone had put a Edson wheel set up in it for same reasons you listed.
Any word on what the vane gear will be or is that coming in future articles? Hydrovane is great for an emergency rudder and is so effective at steering that my boat is slower to handle with the rudder attached to it. (I think my ships rudder is under sized and the boat is a full keel and skeg hung rudder.) The only downside I’ve found with hydrovane is attaching and removing the rudder. The capehorn wind vanes I’ve seen have a flip up rudder. The Hydrovane is a super clean install with no lines or cables running to forward. completely
My little Raymarine tiller pilot handles my full keel boat fine so I would imagine that something like it for this more nimble design would be great.
Thanks for the up date John!
Hi William,
I know the French team have done some preliminary work on the vane gear, but I’m betting no final call will be made on which brand until after the design is pretty much completed. Also, even after one is chosen, it will, I think, need to perform well on the prototype to keep its selection. Bottom line, I don’t think any gear selection calls will be cast in stone until after the prototype phase. That would certainly be my recommendation.
Hi William,
I totally confirm what John just wrote.
In addition:
I get the pluses of the Hydrovane. However, having made provisions for an efficient and powerful rudder, we would like to fit a windvane that acts on this rudder. Of course we will have to devise a clean installation for the lines.
Hi Maxime,
thank you for showing us how innovative a “not-bleeding edge” boat can be!
Here is a thought to back up your choice of wind vane system: The A40 will have a steering system with a tiller acting on a well engineered composite rudder with a sacrificial part.The only way I could see this fail is by hitting hard something big (rock, log, whale) and doing so partially from the side, or the keel would take the hit. A wind vane rudder, which is fairly close to the main rudder and much weaker, is likely to be impacted as well and unable to serve as emergency steering, so one downside less for choosing a wind vane acting on the main rudder. Moreover the system you have in mind is the simpler system with one component less that can fail.
Hi Nicolas,
thank you for the kind words, and for the additionnal argument!
I’m also a tiller fan, especially after I heeded the advice of Mike Pyzel (Santa Barbara) and converted my Islander 36 from wheel (back) to tiller. That was part of preparation for the 2012 single-handed transpac and I’m glad I did it because in most ways it makes single-handing, and wind vane sailing, easier. Some thoughts relevant to this article:
– being able to quickly push the tiller into any angle between horizontal and vertical, and have it stay there, is very handy, and safer when the below-deck autopilot is operating (tiller vertical). For this capability, I rely on friction by tightening the bolt securing the tiller to the top of the rudder post until the tiller stays in place, but is still movable. Flats welded to the top of the rudder post where the tiller bracket clamps are very helpful.
– an adjustable-length tiller extension handle is a must have as it allows flexibility in where you stand or sit while steering and trimming. I’ve been very happy with a Spinlock one, but there are others.
– I don’t recall where I got the idea, but a track on the tiller, with a car on it that terminates the vane control lines (I use jam cleats), allows the ‘gain’ of the wind vane to be easily adjusted, and thus optimize steering efficiency (minimize the S in your wake). The optimum position of the car depends on the course, sea state and wind. Roughly, in most cases, I’ve found sailing closer to the wind requires less gain (car aft), and sailing off the wind is better with more gain (car forward).
– I have two tillers, a short one and a long one. When I sail alone, I use the long one which allows me to steer and trim in the lee of the dodger. When I sail with others, I use the short tiller as it makes the cockpit more habitable.
Hi Steve,
many thanks for all this – all useful, especially the heads-up on being able to adjust “windvane gain”!
Hi Maxime,
Thanks for the reply, and you’re welcome! One thing that might be a (perhaps minor) consideration in selecting a wind vane is how easy it is to attach a small autopilot motor so that the vane gear can be as a backup to the below deck drive when motoring (ie, no wind). The old ATOMS wind vane made it very easy as you can see in the following brief video of the ATOMS steering in light NE Pacific trade winds. The small motor is not attached but you can see its ball joint off the vertical linkage where it snaps into place when needed about 10 seconds in. The tiller track is briefly seen (below the tiller extension handle which is resting on the car that the control lines are cleated to) at about 22 seconds:
https://photos.app.goo.gl/eEkxaUWWZ5a855W1A
The A40 developments are very exciting!
Steve
Hi Steve,
yes, this will be one of the (many) selection criteria!
Hi Steve and Maxime,
I totally agree on being able to vary the wind vane gain. When struggling to get our Sailormat (not recommended) to steer our McCurdy and Rhodes 56 (a big boat for a vane) well, varying the gain was a lot of our eventual success. We had to do this by messing with the gear itself which was a real pain, so doing this quickly and easily with the aux tiller, makes total sense.
Yes on the breakaway tip:
When I purchased our Outbound 46 in 2016 I was concerned about the possibility of the balanced spade rudder (through collision or grounding) becoming jammed at an angle under the hull. The solution was a breakaway tip which I created using a router to score a narrow ‘stress riser’ 40% of the thickness of the glass 12” from the tip and beneath the SS internal flange. I left the trailing edge (1” strip) intact thinking it may allow me to recover the tip and filled the gap with epoxy and barrier coat to assure no risk of water entry. It was invisible when complete.
While it has never been tested it gave me peace of mind that the 4.0” dia SS shaft would survive most collisions.
Hi Scott,
Sounds like a good modification to a great boat.
John,
Would a telescoping and up-folding tiller handle work?
Hi Peter,
That’s an interesting idea. I have actually seen exactly that fitted to the Hutting 52 Phyllis and I took care of over one Christmas in Greenland.
Here’s a photo:
Hi, while at this, why not go the last mile and get rid of that unsightly and expensive wind vane contraption?
It’s on the way when boarding from stern on marina, when boarding from dinghy, or when getting aboard from water, it’s on the way when releasing or retrieving the JSD.
Wind vane functionality can be integrated to boat. Air vane can be raised to eg. radar arc, and hydrovane can be replaced with trim tab on rudder trailing edge. Hollow shaft and two teleflex type cables through it.
While at it, also put the JSD to drum at stern. Deploying and retrieving becomes a breeze. Personally, I love hydraulics, but others necessarily don’t. Industrial 0,33hp 12V motor costs a couple of hundred.
You get my drift? If not for this, why not for “Adventure 41”.
Cheers, PF
btw. Thanks Matt for that idea of using outboard handle on tiller. I have been on impression that typical Yanmar/Volvo/Kubota gas and clutch are too stiff for a handle. I suggested a handle for Oceanvolt fellas, but they didn’t go ahead with it.
Hi Petri,
The use of simple and robust equipment like a vane gear is fundamental to the design philosophy of the A40, also it’s the only way we can truly be “Ocean Ready on Day One” at the target price point given that a really functional offshore autopilot including all the gear to feed it is at least three times the cost of a vane gear, and not nearly as fault tolerant.
More in an upcoming article on the true cost of autopilots.
As to a JSD, there will be a provision for it built into the boat, but again, a mechanized drum would have to be massive and very powerful to work for retrieval, so just not in keeping with the elegant simplicity core A40 principle.
We also have to think about weight. With a boat this size every pound counts.
Thanks. It seems that Andy’s suggestion about Cape Horn vanes could check all four boxes at once.
It’s off-the-shelf, it can be neatly integrated, it’s not on the way, and there seems to be a promise that when integrating a good tiller drive unit to it, like Pelagic, mucho AP power is saved and the whole thing stays robust.
I’m surprised nobody commented on the factory-installed vane gear. This is by far the most interesting aspect to me. Will you choose an off the shelf model? Will they design a new A-40 specific model? What about prospective owners who have a love-affair with their own vane gear but can’t choose? I for one LOVE the robust simplicity and good looks of the Cape Horn integrated units. Had one on ARCTURUS that sailed us to Sweden and have another in my shed for installation on our Norlin 34 SPICA for the day I finally attempt my solo trans-at 😉 Very curious to hear how this develops.
Also count me as a convert to spade rudder steering. Plus, how many abandonments are from RUDDER failure versus some other kind of STEERING failure?
Hi Andy,
thank you for your comment!
The idea is: off-the-shelf model (we have enough things to design and troubleshoot!), but very carefully integrated to the wider design.
For sure CapeHorn is a contender – in my mind, the two top contenders are CapeHorn and WindPilot. But I’m afraid that an owner who dislikes the final choice will have to devise his own solution…
Count my vote for the Cape Horn. It’s the only vane I know of that can truly be integrated into the boat’s steering robustfully and elegantly while enhancing rather than detracting from the boat’s lines.
The Cap Horn can serve as a mounting point for an emergency rudder: http://caphorn.com/en/emergency-rudder/
I think that would solve a lot of issues in one go.
Hi Emile,
true, but not all CapeHorn installations have the tower located aft of the pendulum, and I suspect that the more we make it fully-integrated, the more likely it is that the tower moves forward. Anyway, we’ll see!
Hi Andy,
Very good point on rudder fail against steering fail. I have wondered about that myself. As you and I both know, generally, the simpler we make something the less likely it is to break, and tillers are way simpler than wheels.
Hi All,
I support the notion that loss of steering is very often a result of something other than damaged rudder.
Ie. steering linkages breaking, quadrants being blocked, quadrants coming loose from the shaft etc.
I experienced loss of steering on a 3weeks out of factory boat because the quadrant had not been clamped properly onto the rudder shaft. It slipped down and the key fell out of its groove. Problem was remedied within 15 minutes with an 8mm Allen key and some swearing. We were very fortunate on two things;
1. The key was 10 cm away from sliding underneath the fuel tank and being lost “forever”. We would then have been left with an inoperable steering as the emergency tiller was, as often is the case, completely useless in any form of seaway.
2. We were 20 minutes away from a narrow and complicated landfall with several undersea rocks. Had we lost steering during that landfall I am unsure if we would have been unable to stay off the rocks.
Torbjørn
Hi Torbjørn,
A sobering story indeed. I bet the factory did not use any threadlock fluid, and/or did not use a properly set torque wrench on the fastening. It never ceases to amaze me how the “pros” bypass these essential steps, both in the factory and in boat yards.
On the topic of an emergency rudder (or rudders), the intended use I assume is a “get home” rudder that ends ones journey, but allows one to make it back to port.
One solution is a drogue & bridle arrangement, but I don’t know if it would be sufficient for only one or two aboard as steering control is exhausting. Perhaps it depends on the keel length and transom width to know how tenable this solution is. I can attest that steering with winches is pretty ugly.
Another solution would consist of strong attachment areas for a cassette and spare blade (or two). Downsides of this are cost & complexity, risks in deployment as the boat must be moving forward when the blade goes into the cassette. (Don’t ask me how I know.), and finally storage space for the e-rudder system. The solution to getting the boat moving forward is to use a drogue anyway to control the stern and achieve forward motion before deployment of the blade.
No firm answers here, but if a system with a drogue and bridle can be adequately designed and tested, it would be the simplest path. Though perhaps not the “optimal” when used in anger.
On my boat I have an outboard cassette e-rudder as well as a drogue, and even provision for a tiller pilot.
Hi Whitall,
The drogue steering system has already been tested extensively : https://cruisingclub.org/article/guide-steering-without-rudder
That was what I was alluding to in the article above and has long been my preferred option in that I equipped our old boat for it and soon as I saw Michael Keyworth’s excellent video.
That said, as I said in the article above, the French team are looking at providing reinforced areas in the transoms for those who wish to add an emergency rudder.
Personally, I would equip with the drogue, but giving people the basic structure for other options and letting them choose is totally the A40 way.
Excellent progress here, obvious support for tiller steering. I am glad there has been mention of a trim tab as an alternative to the wind vane. Simple strong solutions seem to be the style of the A40, a trim tab fits this criteria. Reducing clutter on the transom, reducing weight aft, reducing cost are all attractions of the trim tab. Eliminating control lines to the tiller furter reduces clutter. A hollow composite ruder stock provides the perfect opportunity to control the tab via a shaft within the rudder stock.. Of course like many good ideas it’s not new, Nick Skeates has proved the trim tab works with several circumnavigations on Wylo II. After damaging his Aires with his series drouge I believe Trevor Robertson revisited the trim tab concept. The trim tab also radically reduces the power requirements for the auto pilot. These are simple well proven solutions not theories.
I was hoping to see at the very least some discussion on the merits of aft dagger boards such as used on the Boreal, these seem a great idea for tuning the balance of the yacht to further reduce loads on autopilot and wind powered self steering. I have only ever seen these on French yachts, again not a new idea, but one that seems simple, cheap and easy to maintain. I would favor this over twin auxiliary rudders which just seem to add weight complication, clutter and cost. I have sailed many thousands of miles with an Aires and I am a huge fan of steering the boat with wind power. I also have a powerful below decks autopilot. One of these sy
Hi Peter,
Not sure I would be in favour of adding the complications of a trim tab to a high performance spade rudder as planned for the A40, although I can certainly see the utility on a boat like the Wylo with a full keel and the rudder attached to it.
As to dagger boards aft, they work well on shallow draft boats with small rudders, like the Boreals, but I don’t think the A40 will need them or in fact derive much, if any, benefit since will be a relatively deep keel boat with a high performance and good sized rudder, and so will track and steer fine without the. complications and non trivial expense of aft dagger boards.
The point being that aft dagger boards on a boat like the Boreal make up for an inadequately sized rudder that’s not efficient due to draft constraints, but there is nothing stopping Vincent from giving the A40 all the rudder area and depth he needs to make her perform well.
Talking of which, I would certainly encourage Vincent to give the A40 a bigger rudder than might be optimal on a race boat to make her more easily steered, particularly off the wind in bid seas. As Bob Perry is often want to say, “no one has ever said that any of the rudders he has designed were too big”.
That said an owner who wishes to experiment with aft dagger boards would be able to do so using the proposed reinforced areas on the transoms for attachment.
Thanks for your reply John. Firstly don’t worry about a trim tab compromising the performance of a high performance rudder, trim tabs have been used for a long time on aircraft, the reason being to make the controls lighter, the concept is power steering just as a servo pendulum windvane does, just with vastly fewer moving parts less cost and weight. Trim tabs work even better with balanced rudders.
Secondly dagger boards although useful on shallow draft yachts their primary purpose is for adjusting the CLR to balance the yacht, assisting course keeping and lowering steering loads.
The other way to do this is by adjusting sail plan fore and aft, which unless you are you putting up larger headsails generally means reefing the main off the wind to maintain balance. Sailing a dinghy such a Lazer is great for teaching the concept of using the underwater appendages to help steer the boat. Increasing the size of the rudder does not solve the fundamental problem. An increase in rudder size must match an increase in keel size to maintain a CLR which will give slight weather helm, this is vital. For these reasons dagger boards have been put to good use on deep draft yachts wanting to maximize speed and course keeping while minimising crew input and keeping sail changes to a minimum. Imoca 60 is a good example. Now the autopilot can steer what would otherwise be an imbalanced boat.
The high performance composite spade rudder sounds great, however the deeper it goes the bigger the diameter the rudder stock will need to be, loosing efficiency and creating drag on the way. Meanwhile a dagger board on the lee side can be much thinner, orientated at the correct angle and allowing for the heel of the boat. If the built in redundancy of being able to use the same board on either side is given away, asymmetric board can be used to maximize lift. Deeply emersed and more efficient because it’s not getting jacked out of the water like the centre line rudder which is loosing endplate effect and grip because it is at the wrong place and angle, surely it’s worth a look? I am dead against twin rudders for all the reasons you have pointed out but I can see the the advantages for speed and control of appendages off the centre line.
Hi Peter,
Good points and ones I’m very comfortable with as a long time 505 and some time Laser sailor.
We could discuss if there are any benefits to a trim tabs or boards all day long, but the bottom line for me is that I just can’t see the utility of adding the complications and expense of a trim tab or dagger boards to the Adventure 40.
One of the great truths about offshore boats that I subscribe to above most everything else is “if you don’t have it it can’t break”. So, for example, adding a trim tab to the rudder would also add a whole bunch of failure prone linkages in difficult to access places, as well as making the shaft far more complex to design, and expensive to build, and all for a benefit that is, at least to me, marginal, (and arguable) at best.
Hi Peter,
replacing the windvane pendulum with a trim tab is a very attractive idea indeed – but just as John, I just don’t see how this can be done, on a spade rudder, in a reliable way that stays reliable in the long run. Right now the only idea I have is that there could be a maintenance well through the hull above the rudder’s trailing edge, but of course it doesn’t solve the main issues. So if you have detailed ideas for the mechanism, I’m all ears!
Hi Peter,
You have good points and I agree with most of what you say, but still I lean towards (I always try to not lock into an opinion) the opposite conclusions.
As mentioned before I don’t know enough about trim tabs on rudders to contribute well. My guess is that the actuation would have to be by a push/pull axle inside the rudder stock, with a small vertical quadrant inside the rudder blade, to another push/pull rod mostly inside the rudder, to a lever on the trim tab. Alternatively the vertical rod inside the rudder stock could be a rotating axle, making a bit fewer parts, but probably harder to fit inside. The rudder stock should anyway be really big, so there’s space. A big rudder stock does not create noticeable extra drag when using composite. It’s only the few top centimeters that need to be wide, which will make a nice fair transition to the hull bottom. It’s not a big tube that must fit inside the blade. The fibers spread out into the blade when leaving the hull. I actually think a huge composite stock will reduce total drag, if well done.
It’s easy to make a trim tab system both strong and reliable. My gripe is that it’s still extra stuff attached to the most important tool on the boat. With a separate servo pendulum steering the rudder via ropes, the systems are completely separated. Problems with one cannot foul the other. I think it’s worth while to still keep an eye on the trim tab option, though. Perhaps it can be designed in a way that does remove drawbacks?
When it comes to aft daggerboards, however, I think the data quite clearly ends up not in favour. They will certainly be two instances of quite significant extra building cost, they will add weight and potential failure points. They can certainly give advantages too. I’m a balance fanatic, 🙂 but if the rest of the boat is designed well, which I’m certain it will be, the benefits of extra daggers will certainly not be worth the disadvantages.
If the rudder is made bigger, the CLR (centre of lateral resistance) doesn’t formally move noticeably. The rudder should ideally not carry a significant portion of the lift, as that creates more induced drag, tip vortex and more, than carrying it all on one foil, the keel. In real life we do sail with a weather helm, and a bigger well balanced rudder will make us able to take more of the lateral force on the rudder without detrimental effects, but not enough to significantly alter the CLR or keel configuration.
The IMOCA 60 racers don’t use aft daggers. The older generation of them have daggerboards near the keel and mast. They’re not for adjusting balance, but because the canting keel is near horizontal to windward, so it gives zero lateral resistance. Since they’re limited to max 5 underwater appendages, the new generation (and the updated ones) have 1 canting keel, two rudders and two lifting foils. No daggers anymore. These boats are impressive awesome machines, but they’re actually quite a messy concept, a mashup of adapting to changing limitations. I’ve actually sailed one in the late nineties, not racing. It’s good to look at them for ideas on detail solutions in the rig and more, but as concepts they’re no good inspiration for cruising boats, not even very fast ones.
going with a tiller is a no brainer to me.
about the rudder type: if you are willing to spend money on a 4 knot collision engineering solution for the keel, why not apply the same ethos to the skeg rudder? you have the chance of really making a difference and build something great. i dont think that the downsides listed outweight a properly designed and built skeg rudder. its not that i dont like efficiency, i do like it, i just place sturdiness (when correctly done), thus safety and peace of mind above it.
cheers!
Hi Pedro,
I’m certainly all for engineering the rudder to be much stronger that is standard these days, that said, as engineer and boat designer Matt Marsh points out there is nothing about adding a skeg that makes that easier to do, in fact adding a skeg makes the engineering involved more complex and the results less predictable.
https://www.morganscloud.com/2022/03/11/adventure-40-rudder-and-steering-gear/#comment-301971
And, by the way, theFrench team are hoping to engineer the keel to withstand a substantially higher grounding speed than four knots. More on that in another article.
All that said making an articulating fin like a rudder, skeg or spade, as strong as a keel would be very difficult to do and result in a bunch of weight in just the wrong place, hence the provision of a sacrificial lower part of the the rudder.
Hi all,
This is certainly an interesting discussion on an interesting topic! Reading here I get many thoughts. Most of them are agreeing to the statements. FWIW, a collection of my thoughts on this, probably forgetting much:
I’m a fanatic fanboy of tiller steering. It’s perhaps the best illustration of the KISS (keep it stupid simple) principle on a sailboat. I say nothing new, but my confirming points are that it indisputably gives:
– A vastly better rudder feel.
– A vasty better reliability and serviceability.
– Much better manoeuvrability.
– More space in the cockpit.
– Significant cost savings.
– Noticeable weight savings.
– A big smile on any true sailors face.
The only down sides of tiller steering I can think of now are:
– Heavier work if the boat is poorly balanced, which in reality is good, because it tells us that we have to wake up and balance the boat.
– We often can’t let it go for a moment, to do another job. There are several simple and cheap solutions to that, like two ropes and a cleat.
Many say that it’s too tiring to steer with a tiller on long watches. I can see what they mean, but again, if the tiller is hard work, the boat needs to be trimmed better. I find it much easier to get to a comfy protected position with a tiller and an extension. Also, on long watches or anytime when cruising, how much of the time do we hand steer? 1% of the time? Certainly only when we do it for the enjoyment or because we really need to steer well in tight quarters or especially heavy weather. In either case a tiller is a far superior tool for the task.
As Andy mentioned, when boats are lost or abandoned due to a rudder related issue, it’s probably close to always the steering that is the issue, rarely the actual rudder. I’ve looked into a notable number of cases. When “rudder problem” or similar was given, in every case I looked at, except for one, (a cat sailed fast across a big whale with the daggerboards up and lost both rudders), the steering was what had failed, not the rudder.
I also strongly prefer balanced spade rudders. Stern hung rudders can work really well, if done right, but often they just don’t and tend to have issues. I have really disliked all skeg rudder solutions I’ve seen and tried, both for sabotaging the rudder function and for questionable strength. If done really well, it can probably be fairly decent, but a balanced spade done right will always be far better, cheaper and a big composite stock can make it at least as strong too.
A composite rudder stock with a fat rudder top (to make the big stock meet the blade smoothly) and a very large diameter lower bearing can be ridiculously strong. Enough to not break almost no matter what hits it. The stock cannot be bent, of course. It either breaks completely or stays straight. I’d actually build the stock and blade from standard modulus carbon fibre. It sounds more exotic and expensive than it is. The perfect match for this location. If the hull has excessive strength in the rudder area, the steering of this boat will NOT be a vulnerability! 🙂
I’d argue that the backup for this rudder and tiller system is this very rudder and tiller. It’s such a bulletproof solution. If say the lower 70% of the blade is lost, (normal would probably be much less lost) the steering would still work as normal, just with far less power. In an emergency we can easily live with much less steering power. We just have to balance the boat better. I think this setup is kinda unbeatable… Since the steering is so essential, it’s still nice to have more options, like a drogue, but I can’t see how that would ever be used.
Since this boat will not have a bow thruster, the tiller and balanced spade rudder are even more important features. I’d make sure the rudder can be turned a bit past 90 degrees to either side. Then the boat does have a fully operational stern thruster, via the prop wash. Way better than any bow thruster. Most sailors are not used to this idea. Since I think this is an important point, I’ll elaborate on my experience with it.
I work as a skipper on tourist boats on the canals of Amsterdam. The longest one I do frequently is 20 meters (65 feet) and carries 80 passengers. It’s a “salon boat” which means it is about 100 years old, very elegant, white with varnished teak superstructure, full glass walls and crystal chandeliers inside. Even a slight touch on the canal sides with any part of the boat gets very expensive. Still, on a normal full day, the boat has to go through about 70 times a 90 degree turn and about 15 times a 180 degrees rotation. The latter is because the boat entrance is on starboard side while the usual dock is on port side of a one way channel. The available space at either end of the boat during turns is a bit under 1 meter (3 feet).
This sounds like the perfect setup for a nervous breakdown. 80 people looking at you while you make embarrassing and expensive crashing, scraping or falling glass sounds. However, it’s actually quite easy. This boat, the Rose, and most of the others, do have bow thrusters now, but they are almost only used for holding a stable position while waiting for a docking space. When turning we only use the main propeller and the rudder. The rudder goes to almost 90 degrees, so when giving thrust, the boat almost only rotates. Barly any forward motion. I can easily adjust the distance to the canal sides by a bit of reverse or by straightening the rudder a bit while in fwd. This capability is far better than any bow thruster. All the big canal boats do this. It looks like they have rotating prop drives, but none of them do.
So would this work on the Adventure 40? I have no doubt whatsoever that it would. There are some special features on the rudders of some of the canal boats that make this even more powerful. Those features are not suitable on a sailing boat, but it’s also not really needed. The important issues are that the rudder is reasonably close to the propeller and that the rudder is balanced. If the tiller can be turned a bit past 90 degrees to either side, it would be very beneficial. Then we can precision control the rotation of the boat, both directions, by turning the tiller only about 20 degrees, rather than having to turn it 180 degrees to the other side.
One of the mentioned special features on the rudder of some canal boats is indeed a trim tab on the aft end. This is a separate winglet aft of the rudder itself. It has a lever linked to the hull of the boat that makes the trim tab align with the rudder when centred and makes it rotate more than the rudder to either side. This gives extra steering power to shallow inland boats, and extra effect to the prop wash manoeuvring described above, but neither are needed on the A40. The reason I mention it is that some mention trim tabs on the rudder as an ingredient to self steering, if so, maybe this is a slight extra benefit? I haven’t considered the issue well enough to be sure of what I think, but I’m sceptical.
The rudder and stock in one composite piece with a tiller is such a beautifully simple perfect solution that any messing with it feels like a no go. I also have too little experience with wind steering to make up my mind, but in line with the love of simplicity, I like as few and basic components as possible: A wind vane of the pendulum type, using the power of a servo pendulum in the water, to steer the main rudder via ropes. The only mechanical parts then are the connection between the wind vane and the rotational angle of the servo pendulum in the water. Those mechanics have low loads, and if made well, it should all be very durable.
For the same reason (don’t mess with a perfect system) I’m sceptical to a below deck autopilot ram. I feel anything attached to the steering system must be physically disconnected when not in active use. A connected but not engaged ram, electric or hydraulic, will definitely be felt on the tiller. That’s enough to make me invent new words. 😀
Hi Stein,
Lots of good points. I, like you, would lean to keeping the tiller and rudder super simple and just connect the vane gear and maybe a tiller pilot directly to the tiller on deck, rather than adding the quadrant that a Cape Horn gear connected below requires. My thinking is that it’s just better to have the few blocks and control lines on deck where we can see and get to them easily. I also don’t like the complications of the gear required to disconnect the Cape Horn from a below deck quadrant, and particularly the holes in the deck to bring those lines out, that that set up requires.
Hi John,
I completely agree on the issue of hidden control lines and holes in the deck. In fact my thinking is that if we go with a CapeHorn, the lines should be kept on the wet side of the deck.
Hi Stein,
thank you for all this! We’re totally on the same page on having very wide rudder angles, and a short distance between rudder and propeller, above all else.
https://windpilot.com/n/wind/en/prod/sosr//
Could this be an interesting setup? Alternatively the Pacific Plus which has an integrated auxiliary rudder?
Hi John,
Engine controls and a compass are interesting problems on a tiller steered boat. I have seen several boats that still have a binnacle but this further clutters up the cockpit so not ideal. I have also seen a few with a binnacle mounted on a cockpit coaming which is reasonable for the engine controls but not ideal for a compass unless you have one on each side. The hard dodger also seems like it might offer some interesting options such as being mounted to the side inside of it where you can just reach forward and grab it but it isn’t in the way and won’t get snagged by sheets. Of course if the rudder post is far enough forward in the cockpit, you can have seating aft of it but these inverted layouts are weird. One thing that I don’t like is putting the engine controls where they have to be foot operated or you have to bend way over. If I remember right Bestavaer have offered quite a few different options for how to solve this and they have hard dodgers and tillers typically so they may be worth a look even though they are bigger. In any event, this seems like something that will end up being worked out initially in CAD and if the answer is not clear, then a mockup or 2 will solve it. This is one of those areas that I would expect a lot of adjusting needed in CAD so I find it hard to have an opinion on what is right or wrong, I think there are many ways that it can be solved and the implementation needs to just be reasonable.
One idea with regards to pinning people with the tiller while on autopilot is to mitigate it with software (yes a hardware guy just said that but I don’t think it is too high of a risk so it is not unreasonable). It is pretty easy to set travel limits in an autopilot or even design for a specific one and be limited by the max stroke. This combined with a folding or telescoping tiller could make it very reasonable. An important part of all of this would be the modeling of the cockpit area and making sure that the tiller height, cockpit width, seat height, etc all work well together. If you want to go to an extreme on mitigation, you could argue that with a below decks autopilot and an autopilot tiller in the cockpit, you could make the tiller completely removable and it would be installed for hand steering and close quarters work only. I don’t personally like this solution as removing the tiller could be a pain and it is hard to get a low backlash connection there but it is interesting to think about.
Eric
Hi Eric,
As you say, I think all of this is solvable, and that extensive modelling in 3D, followed by real world experimentation on the prototype should provide good solutions without a lot of added complexity. The good news is that Vincent is an expert in 3D modelling and even has a virtual reality set up to be better able to experiment, and he also has a bunch of experience with tiller boats.
Hi Eric,
thank you – in fact, what you’re saying with the engine controls on the inside side of the dodger is the first thing we plan to try!
Hi all,
I am relatively new to sailing, and am leaving my first comment here.
Regarding the engine control, I saw on Sirius ds310 that they used a winch handle sitting on the side. When not in use one simply remove the handle.
Think it’s made by spinlock.
Found that a interesting solution, keen to hear your opinion on this.
Best regards
Kresten
link to video of engine control on Sirius ds 310
https://www.sirius-yachts.com/yachts/310ds/
Hi Kresten,
That does indeed look like a nice solution since it would let us put the controls in a place that would normally be a fouling hazard for sheets, assuming that works out as the most ergonomic alternative.
Hi John
Not sure that tiller steering precludes a binnacle. I converted my Rustler from wheel to tiller steering – for all the reasons you outlined – and added a binnacle forward of the mainsheet track for the compass and cockpit table. Works really well, and is a very handy support in rough weather. However, I made the binnacle myself, and I suspect that finding one off the shelf might not be easy. Not a difficult project, happy to provide details to anyone interested.
Yours aye,
Bill
Hi Bill,
Thank’s an interesting idea. Do you have a photo? Our comments software now support photo upload.
I’d be interested in photos. I have a tiller – steered Yamaha 33. Would be nice to have the compass a bit closer.
Hi John, Maxime,
Great progress!
You mention a white paper by the French team. Is that available to read for the rest of us as well?
Also on the keel and grounding strength?
Kind regards
Torbjørn
Hi Torbjørn,
I will be pulling all that together in the next article.
Great. I’ll keep hitting that refresh button.