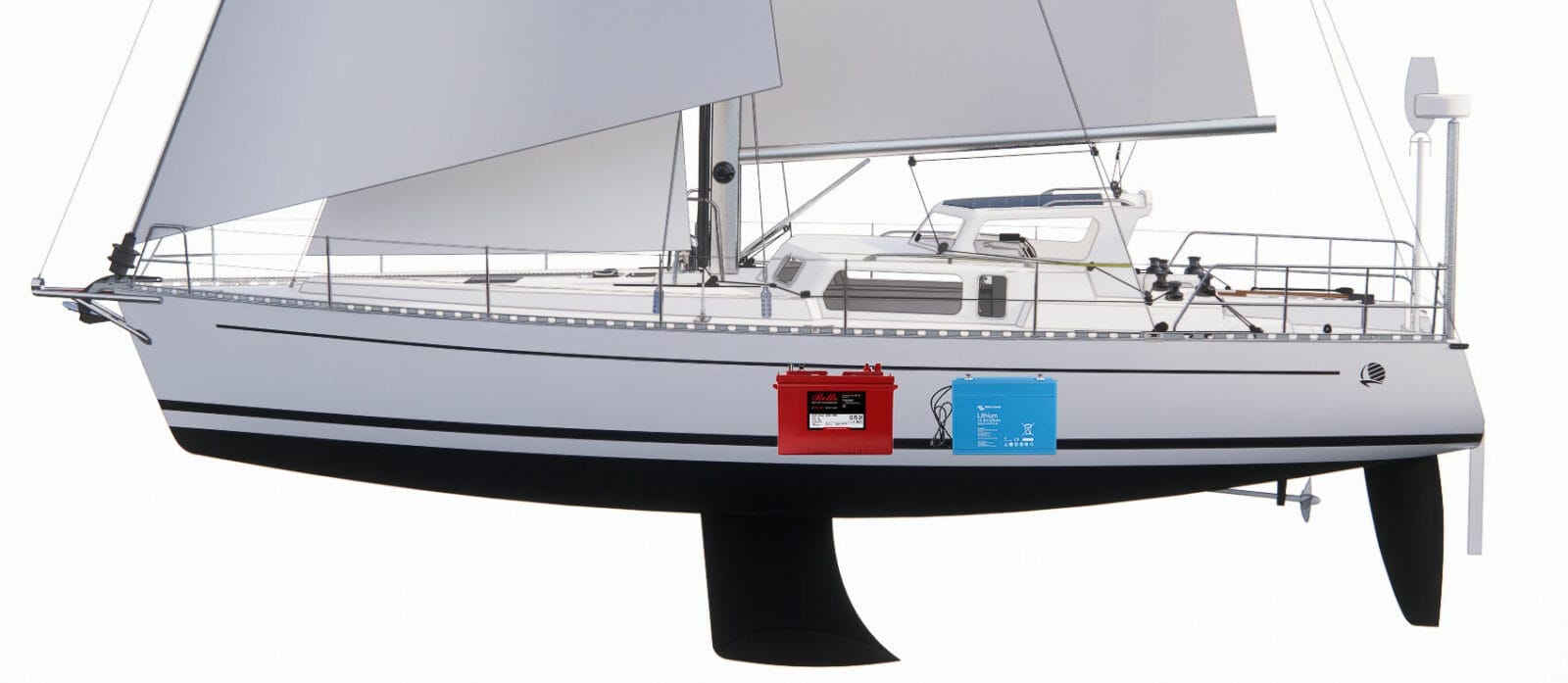
While Maxime is busy behind the scenes putting the Adventure 40 build project together in France, we can use the time to reveal our thinking on some of the systems, starting with electrical.
And even if you are not interested in buying an Adventure 40, this is still an interesting exercise in system design.
Governing Principles
Before we get going, a quick reminder of the core Adventure 40 principles that govern all systems:
- No options.
- But as easy as we can make it for owners to customize.
- The simplest system that will get the job done.
- Good gear, not a lot of gear.
- This is an offshore voyaging sailboat, not a condominium with all the mod-cons.
- This is a relatively small boat, so we need to keep the weight down and not use up precious storage space with over-the-top battery banks.
With our framework defined, let’s look at some fundamentals we need to decide on:
Hi John,
One thought. When making battery trays, I would encourage you to see if you can make them fit GC2 batteries. My impression is that they are still the standard for people who are cost conscious and/or want the ability to replace just about anywhere. When we bought ours 10 years ago, we got Trojan T105’s which are on the higher end and they were $120 each from the local golf cart store for 6V 225Ah. Hearing some friends, it sounds like they can be had for $150 each these days from the golf cart store (or double from West Marine for a white label of a lesser brand), Defender sells the high end Rolls for $191. Part of the reason that I suggest this is that while group 24’s or 27’s will be fine for a year or two, I am not aware of any with real deep cycle construction (the Rolls battery in your link has no cycle life graph like their deep cycles) so I don’t think that they will be a great long term option for people wanting to stay with lead acid and they are small enough that there won’t be a good alternative that fits. A GC2 is 10.18L X 7.13W X 11.15H versus a group 24 which is 10.2L X 6.8W X 9.3H. Of course, if you support GC2’s end to end, you only need to widen the battery box 1″ and you can fit 2X 4D’s and then you would provide lots of options but end to end may not be the most space efficient.
I am not arguing with what batteries you are planning to supply as original equipment as your logic is sound on that, just to make the tray large enough that someone could upgrade the boxes on the tray and drop in GC2’s. To me that keeps with the A40 philosophy of being easy to upgrade for a very obvious upgrade while providing a reasonable setup to get you out there. I think part of my reaction is also that the proposed sizing kind of forces you to go lithium or add a generator for the intended offshore use. If you are counting on engine charging twice a day when underway, that seems like a lot of main engine use (assuming low charge acceptance due to bank size) which is also not fuel efficient for charging so your fuel capacity becomes really critical and it isn’t super nice to your engine. People who want to go the route of conservation and lots of renewables to do mainly renewable generation will also need to fit a deep cycle bank with significantly more capacity or forgo some major loads like the fridge.
GC2’s do have the same issue with lack of redundancy at 24V and the energy size bank you are talking about as they will all be in series. I have personally never had a cell failure on a GC2 despite abusing the heck out of them in electric cars and house banks for big boats with 20+ of them but I have failed cells in other less robust battery types. I used GC2’s here as I think that they fit the profile of widely used and available best but if there is something even better in that regard, then I would substitute that.
Eric
Hi Eric,
That’s an interesting idea and one that might be best.
I guess it really comes down to one thing: do we think that anyone will actually be going long term cruising and voyaging with lead acid in two years by the time the first boat splashes?
My bet is no and that’s why I went with the lightest and smallest lead acids that would give us 24 Volts and fault tolerance.
But if I’m wrong about that, then I like your idea better, although the lack of fault tolerance still bothers me. I know of two Dashew boats brought down by exactly that issue.
As to engine run frequency at sea, let’s leave that to part 2 when we get into charging. As you know there are a bunch of ways to solve that without adding more batteries, and once again the lead or lithium thing plays a big role that I want to get into more then.
Hi John,
Yes, the question of what chemistry everyone will be cruising with is definitely an interesting one. I tend to think that a significant percentage of lead house banks will still be around for a surprisingly long time despite lithium’s cost coming down and there being closer to turn key solutions. The reasons will vary and some will be legitimate and some not. I can think of several people who have looked at it and decided not to because of not knowing how to set it up right, worry about troubleshooting and repair in out of the way places, worries about parts in out of the way places, not feeling technically proficient to work with it, not wanting to spend the time, etc. A friend who is an EE and made his career at power electronics recently moved up his plans for long distance cruising and converted his boat back to lead from what I believe was a very well done homebrew lithium setup as he just didn’t feel like he could effectively troubleshoot and fix it under pressure with the boat bouncing around. Don’t get me wrong, I think lead will be in the minority soon for long distance but I also think the tail of the lithium adoption curve will be long.
I was thinking a bit about fault tolerance. My first thought was that they make 12VDC to 24VDC converters so you could power the smaller loads from half a 24V bank. I think the biggest issue with this is that you won’t be able to use your engine to charge although things like solar may work if the right controllers are used. Not having things like the windlass would also not be great (technically the windlass can just be used slowly while watching temp on 12V as they are brushed DC). My other thought for a lead installation was that you could have an engine start bank that was something like 2X 12V group 24’s in parallel (assuming 12V starter). This would give you 2 versions of backup: you could substitute in one of the group 24’s for the battery(s) with the dead cell and put up with the uneven charging or you could rewire your engine bank into the house bank and then use your now 12V house bank as your start bank. Definitely not ideal and the capacity isn’t huge but for a low power boat, it is probably acceptable as a get to port solution. Of course, making any of this actually work requires good planning, carrying the wiring diagrams and having tried it to make sure that you have the right fittings. Unless the boat has built in redundancy, I think you basically have to carry some piece of gear to do it and it feels right to carry a battery as a fix for a dead cell but then you also need a way to keep it charged which is why I was thinking about paralleling the start battery although the weight and size bug me.
Eric
Hi Eric,
A well reasoned defence of lead acid, and I totally understand your friend’s change back to lead. The thought of trying to fix some home brewed lithium system at sea or in a remote place is something that only someone who has never been offshore to remote places would be comfortable with!
On the fault tolerance, I have wrestled through that one too, with much the same thinking and in the end I punted, but still thinking. Right now the solution I like the best for lead is the one above (small batteries) and I think that in the end that might be the best bet for lithium. That said the platform will need to be bigger, but that may change.
The other thought I had is to use my serial backup idea to also give us fault tolerance. More on that in the Part 2.
Lead-acid isn’t going away that soon. Yes, an increasing fraction (possibly a majority) of owners will go to LFP, but not all of them, and not on that schedule.
Designing and installing the main bus, panels, fuses, alternator, regulators, etc. to work with either lead or lithium, and then shipping it with a very basic set of lead batteries, is absolutely the right call.
Sizing the battery compartment to accommodate as many common sizes as possible, in both lead and lithium, is wise. No, you’ll never get all the possible formats, but it shouldn’t be too hard to cover most of the common ones that are within a few inches of fitting.
Surely you’re both right, no? LA batteries are not going away any time soon in existing boats, but in a brand-new, long-distance boat specifically designed for low loads with delivery several years in the future, I think John’s bet on assuming lithium conversion is wise.
Hi Nathan,
Yes, that’s pretty much my bet, but I could be quite wrong, predicting the future of technology, even two years out is very difficult.
Hi John
Your example roughly mirrors that of mine in a 40 foot, 8800 kg dry weight fin and skeg monohull. For a year now I have been running 370 watts of solar into 440 amps at 12 volts Victron Supercycle batteries. My sailing season is February to April, September to November. Cruising area is the Mediterranean where a windvane can be a liability and you are never far from shore power. I have two observations which may be of interest, one which applies to longer passages and the other to coastal cruising.
On passage I run the fridge, autopilot, nav instruments, lights, sockets for charging two Ipads (one for AIS, one for navigation and a considerable draw) and at night Radar (as I am alone). In high traffic areas the radar is on all the time at night. The meter at the chart table suggests this is a 6 amp + draw. Nights are long at this time of the year and by the time the solar kicks in 90 minutes after full dawn I am down 18 to 20% on the battery bank. Solar charging in the day brings two challenges. Firstly cloudy dull days and secondly shading from the sails when pointing into the sun. The best daily input I have achieved from the panels this spring, according to the Victron app, has been 1.33 kWh.
At anchor (and coastal cruising which is bound to have some engine usage) the solar panels rule. By midday the batteries are at 97% and the batteries are on float. Now one could run a watermaker, a 12 volt water heater and all the power tools one man could use at one time and still not make much of a dent.
So, at sea I don’t have enough solar – and perhaps not enough batteries- and at anchor not enough batteries.
When I get into the real world I am hoping a Windvane will deal with the biggest villain in the power draw equation. And I’ll be hoping for sunny days.
Hi Mark,
Thanks for the real world numbers, very useful, and I think the problem at sea is typical, and best solved with a wind vane, but with the caveats you mention.
The other thing to keep in mind about the at sea problem is that most of us are not at sea overnight that often. So running the main engine to charge, assuming we have a good alternator and regulator, is not the end of the world. Point being that we can end up with way too much solar and having spent way too much money if we try and design for an edge case that does not happen often.
Eric does a good job of quantifying this: https://www.morganscloud.com/2023/01/24/balancing-battery-bank-and-solar-array-size/
Lead acid cells are rectangular in plan. On a healing boat it seems better to mount the batteries sideways with each cell’s long-side fore & aft rather than side-to-side, to minimise sloshing. Just another factor to consider when locating and designing a lead-acid battery box adaptable to lithium. (I don’t know if lithium batteries are sensitive to orientation.)
Hi PD,
Good point. On lithium, like AGM and Gell, orientation is not critical, In fact most can be installed on their sides.
Hi PD and John,
You both know this, but many don’t:
As you mention, most relevant battery types can be placed both longships or awarthships, but flooded cells absolutely not. They must be oriented with the cells parallel to the centre line. The battery long side must be 90 degrees to the centre line. The Trojan T 105 6V batteries discussed above (great stuff) is one example of this. The wrong orientation makes the top corners of the plates dry out.
Hi Stein,
Actually I did not know that. Or maybe I had forgotten it since I have not used liquid filled in 30 years. I found this at Rod’s site. As usual around this stuff their are some added complexity to this issue which Rod explains well: https://marinehowto.com/installation-orientation-of-flooded-batteries-on-boats/#:~:text=Cells%20running%20port%20to%20starboard,vessel%20to%20minimize%20plates%20uncovering.
Also, according to Trojan there batteries are good to 22 degrees, and I think generally the A40 will sail at about 20 to 25 and the liquid will slop around keeping the plates wet in any sort of a seaway so maybe not a huge issue.
That said, makes sense to get the added safe angle by thinking about this, thanks.
Since instruments are capable of running off either 12 or 24, some nav lights definitely are as well.
If you lost 1/2 of a 24v bank would it not still be possible to sail on with critical systems running at 12v?
There might be some fiddling with cables in the battery, not ideal but some resilience.
We did get a bad cell in a Trojan T105. The bank was about 7 years old and well used. It didn’t stop us replacing like for like. We had 4 so made use of the redundancy.
Hi Dan,
Sure, you could do that, but a lot of other important stuff would be down, like the windlass. And also the alternator would be down. That said, I agree this is not that common. Still, if we can end up with fault tolerance without making too many sacrifices, I would like to see that.
Hi John.
I’m aware that you’re dead-set against drop-in LFP batteries, and you have valid reasons for that (though not everyone agrees with your conclusion, of course). However, I think you’re letting your anti drop-in position carry you a little too far when you say that they’re “uninsurable” because they’re not ABYC compliant.
First, I’d guess that 90% of cruising boats out there are non-ABYC-compliant in some way or another (through-hulls, for example), but that doesn’t make them uninsurable by any stretch of the imagination. And second, when we’re re-shopped our insurance two years ago, the number of insurers/brokers who asked what type of batteries we have was precisely… zero. They didn’t ask, didn’t care. I know that’s contrary to what some folks are repeating on the internet, and I don’t doubt that some insurers do care. But it’s a big stretch from there to “ uninsurable”.
Jeff
Hi Jeff,
I agree most boats are not fully ABYC compliant.
But the ABYC language is quite clear that drop ins that don’t communicate are not compliant: https://www.morganscloud.com/jhhtips/most-drop-in-lithium-batteries-not-abyc-compliant/
And I did not say the boat was uninsurable, what I said was the batteries are not insurable. Whether or not that would result in an insurance being denied, or worse a claim denied is hard to say. That said, insurance companies are twitchy about lithium (right or wrong) so putting batteries in the A40 that are clearly not compliant would be a big mistake and expose the builder to liability.
All that said, I agree my language was harsh. I will soften it a bit.
Very interesting discussion on a number of levels.
From the perspective of redundancy and fault tolerance in a nominal 24V system I believe that it may be appropriate to allocate space for a 2s2p install of 100Ah lithium batteries for a nominal bank of 400Ah. This would satisfy passage and extended cloudy days storage with a nominal 400w solar supply with alternator recovery as needed.
So four smaller batteries. Yes some more wiring is involved, perhaps not significant, and might well satisfy the identified concerns.
Alternately use of 24V lithium batteries (100 or 200Ah) in a 2p arrangement is also an option.
The space allocated for a lithium install then becomes available for FLA batteries if that is indeed the choice made when built.
From my recent experience I found that 2x200Ah lithium batteries installed Port to Starboard took up the exact same space as 4 GC2 225Ah batteries installed fore and aft. Thank you Beneteau for the space allocation 🤔. And yes the sub-floor installed over the battery space was designed with taller lithium battery height in mind as it provided some ventilation to the original FLA bank.
Engine start battery installed separately.
Hi Steve,
I think 400 Ah at 24 volts is excessive for a boat of this size. That’s 10 kWh. To put that in perspective and in terms we are all familiar with, it’s roughly equivalent of a 2000 Ah lead acid bank at 12 volts!
I don’t think anyone would ever dream of adding that much to a 40 foot boat. My point is that I think it’s better to take advantage of lithiums better energy density to save weight and space, not fill all the space that is left by lead acid.
As I say in the article, even 200 Ah at 24 volts in lithium is more usable capacity than we had on a 56′ 50,000 lbs boat, over three times bigger than the A40
Or to look at another way. The big reason we can get away with a small as-shipped lead acid bank is because we have the lithium option.
It’s a lot, yes, but let’s be fair John – the M&R 56 was always a little under-endowed in battery capacity, and you put a fair bit of effort into working around that limitation.
I have, on occasion, specified 19 kWh (nameplate) lead-acid banks on boats whose daily usage on passage was on the order of 6 kWh/day. A thousand pounds is a lot of weight (which can be ok, if the boat is designed to carry it low and central). But if you start asking the client “what on your usage list will you give up in order to reduce this weight” sometimes the answer is “actually I’ll accept the weight, and build her with one less freshwater tank but run the desalinator more often.”
Today, I would not hesitate to specify a system of similar or higher usable capacity in LFP. The cost and weight of the extra LFP cells if you want to upgrade from an 8 kWh pack to a 16 kWh pack is just so miniscule in comparison to the cost and installation labour for the BMS, fuses, contactors, chargers, regulators, controls, monitoring, etc. which are pretty much the same either way. But being able to use the autopilot while the fridge stays cold as you take an extra day to repair a troublesome engine? To many people, that’s worth something.
Hi Matt,
I disagree. For years we were under on batteries but managed fine at 500 Ah at 12 volts. However about ten years ago we went up to 800 Ah and had all we needed and then some. And that was without solar. And a lithium upgraded A40 will have even more than that in just the space of four small lead acid, and with space left over.
And I would never cut water supply on the A40 to accommodate a bank that is, at least in my eyes, excessive. This is an ocean going boat and therefore must have enough water aboard to complete the voyage if the watermaker—one of the most failure prone pieces of gear on the boat—quits. That and a big enough fuel tank is challenging enough to fit in on a boat this size, without making the battery bank excessive.
And keep in mind the boat comes standard with a vane gear and solar so can be sailed to port safely even if the main bank craps out completely. More on how in part 2.
So in summary, in my view, anyone who needs to use 6kWh or more a day net over and above solar charging needs to buy a bigger boat. The A40 is not for them.
Also, quiet time at sea on a passage is more about charging capability than bank size. All that adding more bank does, past a certain point, is increase the time between charging cycles, but the amount of time with the engine running to charge remains the same. So the best bet for someone who loves to sail and does not want to use the engine at sea, is a hydro generator: https://www.morganscloud.com/2023/08/09/watt-sea-hydrogenerator-buyers-guide-cost-performance/
Following with interest.
I am currently prepping my 47′ steel center cockpit cutter for an exploration voyage to points well north this summer (certainly northern Labrador, and hopefully Baffin if the ice gods allow). I was planning on replacing my 10 year old T-105 bank (4x = roughly 420Ah@12v) bank prior to departing, and as luck would have it one of the cells went bad this winter in storage and took down half the bank anyway (2 isolated banks plus separate engine start).
We’ve managed several 4-6 week long cruises on this meagre bank over the years, with only 200w of solar and only 100a (nominal) alternator charging… and it was doable- but barely; and yes – we motored a lot more than I would have otherwise. No vane gear- only electro/hyd autopilot, 12v and engine drive reefer; usual electronics suite, drip diesel heat (so no blower draw).
I’m in the process of adding hydronic diesel heat, fwd looking sonar, upgraded (electric) windlass and Starlink; so draws will go up a lot. We’ve upgraded to a 150a alt, added another 200w of solar, and I have just purchased 6, GC-2 new batts from Rolls (Surette Battery Co – a great Nova Scotian company in Springhill, NS).
building a new box for the extra 2 batts right now (from 3/4″ and 1/2″ HDPE).
I dearly would have loved to flip the boat to 24V – but as a retrofit that would have been a monster project and not likely worth the effort. I briefly considered the lithium option… but on a 42,000lb boat it seemed to be not a big deal on the weight side (I think i have about 150 lbs of old chain in a keel tank I can jettison to help reduce the impact of the new batts), and the re-jigging of the charging system was yet another thing I will put off until the tech is more mature. I have lived with FLA for my whole sailing life, and I know and trust it’s behaviour… which is comforting when so much else will be new to me on this trip.
I’m not saying I’ve made all the right choices – but I’m comfortable with the trade-offs for now. Time will tell!
Hi Ben,
I think you are making the right choices. There is no way I would take on a voyage to Baffin Island with a lithium system given today’s “state of the art”. Just way too complicated, difficult to repair, and poor fault tolerance with many single points of failure that would be impossible to bypass in a remote place. The other aspect is that a voyage to Baffin is incredible taxing on the skipper (I have cruised there twice) and so the last thing you need is any unfamiliar technology on the boat. Way too distracting.
Hi John, this comment is based on what I would like to see as a buyer, based on my owning and cruising a 40 ft ovni. A lithium based 12 volt system with one manufacturer providing as much of the equipment as possible. Why? While I understand there are savings, not sure how much? On cabling going 24 volt, it introduces more complexity.
To get a system for a small boat that will work well for coastal and offshore, lithium is a no brainer. Why one manufacturer, again simplicity when you have a problem there is one place to go. If the boat is going to be built for a purpose it should have a spec that can fulfill that purpose. Also in two years lithium will be cheaper and more of a standard expectation. I always enjoy reading the blog, thanks Richard
Hi Richard,
I agree that buying from all one vendor for lithium is the right way to go and have been strongly recommending that for some years. I like both Victron and Mastervolt, but that could change.
As to shipping the boat with lithium, I would not call that a no-brainer now, but it might be in two years. But on the other side, see Eric’s thoughts, which are well reasoned.
On balance, my guess, and it is just that, is that an inexpensive, but well thought out for upgrade, lead-acid system will still be the best bet in two years. Again guessing: I’m thinking that there will still be too many complications in lithium, and too much owner support—remember a lot of A40 buyers will be first time cruising boat owners—to make lithium a good idea.
This is in keeping with A40 fundamentals, in that we have always said that it will come with the fundamentals for task. In my view lead acid qualifies on that criteria. No. it’s not what most people want, but people have been crossing oceans for decades with small lead acid banks.
Also I don’t see how going 24 Volt makes the cabling more complex? Engine systems should always be separate anyway, so all I can see is adding a 24/12 power supply for NMEA 2000, which is pretty trivial. And going to 24 also fits into A40 fundamentals because it is a difficult upgrade but easy to do for the builder.
Hi John,
Very good summary; we came to similar conclusions when working out the electric system for a 48ft yacht, but I would go for 24 V even for 35 and up.
Here some observations:
On none of the gear we bought (and it is quite a list), whether winches, windlass, lights, etc. was there any difference in price, except that getting the engines to 24V would have been drastic. Some electronics still need 12 V, but a 24 to 12 V transformer will do the trick.
We decided not to touch the electrics of the engines; they run on their own 12 V circuits. That way, the engine manufacturer won’t complain. For house power, there is a completely separate generator head – we got them inline off the PTO, but a couple of belts or a serpentine belt should work ok if they are not too big.
We also start with temporary lead-acids, just so that we can move the boat and will go to Lithium Iron when the sailing gets serious. The boxes and wiring are put in place right away.
The capacity calculation seems reasonable, you don’t “need” all that capacity once you change to Lithium, but it is very convenient and gives more leeway when charging etc.
Hi George,
Good to hear that you did not have to pay extra to go 24 Volt. Thanks. As I agree that keeping the engine 12 volt is the way to go, although that may change I think.
I assume by lead acid you would go for AGM, not a liquid cell lead acid. Less maintenance, less chance of anything going wrong, and without the venting requirements of liquid cells. I personally would not put liquid cell LA’s on a boat these days. I removed them from my last boat and put AGMs in. No need to mess around with ‘topping up’ with distilled water etc.
Hi Michael,
Although I have used AGM in recent years I would not necessarily reject liquid filled. This article is a bit out of date, but still relevant to that call:https://www.morganscloud.com/2018/05/11/battery-options-part-2-lead-acid/
How the project is going? Seems ot have not had any updates since April (sorry if I missed)
Hi Ignat,
I’m waiting on hearing from Maxime. I will rattle his cage.
Thank you!
Did I miss Electrical System—Part 2? or it is still to come?
Hi Ignat,
Still waiting for Maxim. Not a lot of point in publishing more detail before we find out what’s going on with the builder.
‘Provide separate load and charge busses‘
John this is one of the comments for the electrical wish list for the Adventure 40.
I hope l’ve read that correctly.
I’ve tried searches of AAC to see if this topic as been discussed but l’ve had no luck.
My loads and charging sources are on the same buss!!
I know of the Victron Lynx buss system where they sell two versions, input and distribution
If you could point me in the direction of information of using two separate busses it would help me to design my next electrical improvement.
Many thanks.
Hi John,
We have recommendations on that subject, and pretty much everything else you will need to think about as you design the system, in our Online Book on electrical systems. Table of contents here: https://www.morganscloud.com/category/electrical/online-book-electrical-systems/
Probably best to start off with a quick read through to get all the context, rather than focusing on one chapter.
Thanks John, l will work my way through the 49!! Articles.
I have read some of them already.
This one caught my attention first,
‘Building a Seamanlike Lithium Battery System’ which takes me in another research direction that sailing friends ask me about.
I keep telling them to join AAC to save them time and money and they get to learn something valuable…..knowledge.
Hi John,
Good plan, although you will be able to skim or skip at least half of them since we also cover lead acid and other issues that won’t apply. Still I think it’s worth your time since it’s important with these things to think about an overall system, before getting too far into the details.