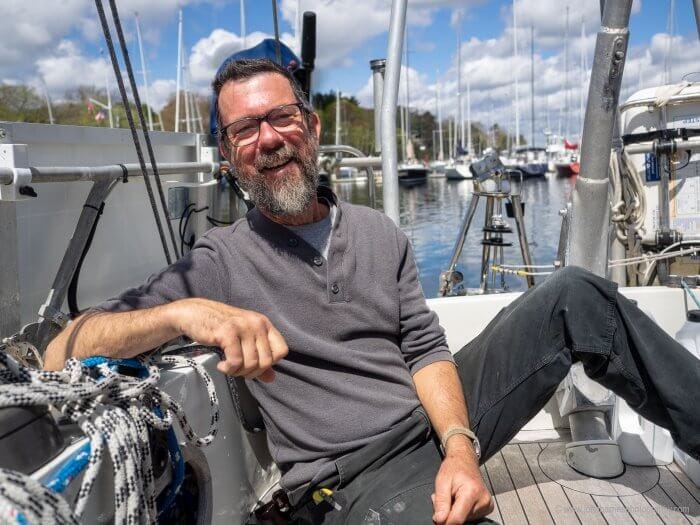
As you pretty much all know by now, I believe that the series drogue designed by Don Jordon is by far the best storm survival and anti-capsize gear available.
My belief is based on the solid science done by Don Jordan in cooperation with the US Coast Guard, much of it based on earlier work by the Wolfson Unit of Southampton University.
But, just as importantly, we have verified that science, and learned more, from some of the best and most experienced offshore sailers of our time, including Tony Gooch, Trevor Robertson, and Susanne Huber-Curphey, all of them with multiple successful series drogue deployments during Southern Ocean circumnavigations.
A few weeks ago, I spent a morning continuing that process with Randall Reeves of Figure 8 Voyage fame. Here’s what I learned:
Hi John and Randall
The video of the dyneema bridle whipping about is both instructive and disturbing. It is not something I had anticipated when considering a dyneema drogue.
I think the problem is two fold:
1. The light dyneema drogue needs considerably more weight at the end to keep it in tension as the vessel surges back on the back face of a wave, a point you both make. This is easily solved by making the anchor weight heavier (double?), but of course this has to be done before deploying the drogue. I will certainly do this and thank Randall for the warning.
2. The dyneema warp has far less inertia than a heavy, wet piece of 18mm nylon double braid so whips about much more readily. The video makes this really clear. The solution to this may be to make the bridle of nylon double braid and the rest of the warp of dyneema. The heavier nylon section should be much less lively than the light dyneema. It may even be necessary to make the part of the leader section of the warp (between the bridle and the first cone) of nylon but judging by the video, this should not be necessary.
3. Stein Varjord’s planned use of glass fibre battens is ingenious but adds another job to be done in the cockpit under difficult conditions. I would rather avoid it if possible.
Having seen Randall’s video, my thinking is that when/if I put together another Jordan-type series drogue, I will use a nylon bridle and all the rest in dyneema, and double the end weight from Don Jordan’s specification for a nylon warp.
Hi Trevor,
Thanks for your thoughts. As always, they make sense.
I hear you on the undesirability of adding complications. That said I’m still interested in Stein’s idea for a couple of reasons:
Also, I really do think that the battens could be installed before, or shortly after leaving port, so other than pulling in the lines attached to the bridles there would not be a lot of added complication during deployment.
Anyway, I plan to experiment with the idea, although it won’t be until next spring.
Hi John,
Great article summarizing the continual refinement of the SDDDJ. The video clip of the Dyneema bridle whipping around seems a perfect example of the law of unintended consequences, as I don’t recall anyone anticipating such increased flotation or motion. The proof of real world use and testing is invaluable!
Regarding the idea of the retrieval loops, although I appreciate the several descriptions that you and others have written on how the splices would be made and attach, I still can’t visualize them. Can anyone point the way to a diagram of how it would be done?
The evolution of Stein’s proposal for protecting vane gear is fascinating, and I hope that someone will put together a real world example before too long. I think the proposed block and control line at the outboard end is a good one. Of the several methods I can see used to attach blocks to the ends of backstay flickers, it would seem that lashing it in place best preserves the structure of the composite batten for the rigor of offshore use.
As for the attachment of the lightweight control line to the bridle, I wonder if chafe will be a concern at this location? I’m trying to imagine how much movement there will be between the bridle and line attachment as the batten flexes in the innumerable load cycles of a deployment.
Given that the bridle is such a critical part of the drogue, testing of the batten system in benign conditions is definitely needed, both for proving the hardware design as well as the modified deployment procedures. An additional question is whether it will tend to increase or cancel the whipping motion of a slack Dyneema bridle.
Lastly, can anyone comment on the use of special deployment bags such as the ones made by Ocean Brake?
Looking forward to the discussion!
I was also wondering about the deployment bags. If there is space on deck to fasten the bag stretched out it looks to me to be a good option. Could it even have lines to the bridle attachment points so that after putting the weight out the deployment bag is dropped off the stern and retrieved after full deployment?
Dave
Hi Dave,
I guess I’m confused as to why you would want to do that?
John,
I was making a few connections – which might have only been visible inside my head 🙂
The Ocean Brake deployment bag looks quite large when opened out into a mat for deployment. The Rival 38 cc we are currently buying doesn’t have much clear space on and around the aft cabin, a line snaking out has multiple things to snag on. The article mentioned a fear of being close to the line as it is released.
So I figured that hanging the deployment mat over the stern would keep any danger well out of the way and reduce deck space and potential for snags reduced.
Apologies for lack of clarity.
Dave
Dave,
We only have 2m of transom width and plenty of things to catch onto. Putting the deployment bag overboard and letting the JSD run off totally out of harms way, would mitigate my one big remaining concern. I’ve no idea if there are any unintended consequences, but it’s surely worth a test.
Reading highly experienced people who have watched these things actually deploy is highly cautionary. The goal has to make the JSD idiot-proof, because it’s my sense that by the time a storm compels us to use our it, we’ve all been reduced by fatigue and anxiety pretty much to the level of idiots anyhow.
Having said that, these articles on the JSD have increased my confidence enormously, and has justified our AAC membership purely on their own.
Hi Dave,
Thanks for the fill, that makes sense and might be a good answer, although the details will take some thinking about. That said, if it were me, I think I would just use a simple bag as detailed in the article.
Hi Scott,
That all makes sense. That said, I don’t think chafe at the loops would be an issue, given that we are working with Dyneema here. I would worry more with Nylon though.
As to the Ocean Brake bag. Looks like a nice piece of kit. That said, as I write in the post, I have always found that just flaking into any old sailbag works just fine.
And finally, you may find it easier to visualize the loops if you read Trevor’s article that I link to at the end of the post.
Hey John, thank you for another in a long line of informative essays. I have been following and anxiously waiting for this recent addition. I am still going to try my jumars since this will make quick work of the retrieval. However in a sustained blow or if broaching becomes possible i would like to have some loops in my rode as a second option. I will be re-rigging my JSD with amsteel once i understand the process. Reading past discussions and this one I have remained fogging on the loops and their attachments. I’m hoping you could clarify. I am competent with brummal splices but i am unsure of the rest. Is your idea to create several 1 inch dyneema rings and then to attach them to the rode? (in lengths dependent on vessel length) and if so how would one do this? I am sure there is something I am misunderstanding…
Hi Alan,
Have a read of Trevor’s article that I link to at the post end and I think things will become more clear. If not maybe I will try my had at a diagram, although I suck as an artist.
Hi John and Randall
I have done a bit more experimenting with retrieval methods for drogue with dyneema warp and here is what I have found:
1. Andy Schell is entirely correct that a cut spice is unsuitable for making a loop in the warp to allow retrieval. I thought cut splice held in place with a shoemaker splice might work as the shoemaker splice relies more on the friction of being woven through the warp and less on the outer part of the splice being compressed. However experiment shows that a shoemaker splice does not have enough friction when lightly loaded to take any significant pull against the normal direction for loading the splice. Unless someone comes up with a splice for dyneema that does not depend on compressing its outer part, a cut splice is not going to work.
2. A soft shackle of smaller diameter dyneema threaded through the drogue warp works as an attachment for the retrieval line (at least in a fair weather cockpit simulation), but if permanently rove is more likely to foul something as it runs out than a brummel splice loop. I hope/believe it is possible to thread a soft shackle through the unloaded part of the drogue warp forward of the retaining line as the drogue is retrieved, but I have too little experience with using dyneema after it has been under tension to know whether it can be fluffed up enough to pass a fid through it easily. It needs to be easy to do as the cockpit of a small vessel in the aftermath of a major gale/storm is not a place for fiddly work with a fid.
3. The suggestions to use a climber’s ascender (Jumar) have considerable promise. I tried it on undersize dyneema (6mm), all that I had to hand, and it holds well. There was no tendency for the 6mm dyneema to slip through the ascender when it was winched as tight as I could manage using my sheet winches. Presumably 10 or 12mm dyneema would be even more secure. There was no discernable shredding of the dyneema line by the ascender jaws provided the load is entirely relieved before opening the ascender – but that has to be done regardless of the type of rope used. The dyneema was crushed nearly flat by the ascender jaws but could be fluffed up to its usual form when the load was relieved and seemed to have suffered no damage.
Conclusion:
I think it is worth pursuing a retrieval method that does not rely on permanently attached external loops because of the danger of these loops fouling when deploying the drogue. The speed and forces involved as the drogue runs out in force 10 is dramatic; Randall Reeves makes this point in the latest post, as I did in one of my earlier ones. If I put together a dyneema drogue I will initially try to retrieve it using Jumars. You need two Jumars of course, one on the running retrieval line to the bows and the other on a short retaining line aft to hold the drogue while the running line is reattached. If that does not work I will try using soft shackles inserted where required during the retrieval process and removed immediately they have done their job.
Of course I will trial the retrieval system in fair weather, but unfortunately that often misses a problem that only shows when using the gear in earnest.
Trevor, I believe I was the one who mentioned the use of a Jumar, it is a brand made in Sweden but readily available everywhere. The importance of that brand is the aggressiveness of its teeth. Actually the lack there of. Gibbs from England makes a version but it is much too aggressive for this application, high loads would run the risk of tearing the plait of the dyneema. There is no issue with any of these ascenders losing a grip on dyneema. Quite the opposite, they are very tenacious. While Jumars are hugely overbuilt for their intended use (6000lb breaking strength) they are only intended for 1000 lbs or less. Climbing rope breaks at 3000. I have seen a falling body shock load a Gibbs and shred a climbing rope. I don’t know what 10,000 pounds shock loaded would do to dyneema. It wouldn’t look pretty but I believe the dyneema would not fail. Either the jumar or a cleat or the winch would. But..we are talking about retrieval, when loads are much less..if it doesn’t break the winch it wont break the jumar. To be clear, the jumar would be placed in lieu of the loops John was suggesting. Pendants off the jumar could be run direct to a winch or to a block at the bow and back to the winch. You would need two jumars.
Hi Trevor & Alan
On an earlier discussion about this issue I suggested that a modification of a line clutch that was actually designed to hold high loads on Dynema might be the ultimate solution. The problem with using Jumar jammers is that they are not really designed for that type of line or the loads that will be encountered.
John correctly pointed out that no manufacturer would bother to build such a device for such a small market. However that was not exactly what I had in mind. With CNC milling so common, it seems feasible to design a hinged side plate that would allow side access to a well proven and reliable standard clutch. If done properly it would be faster and more reliable to release and could be attached at any point along the drogue line.
Just as a matter of mountaineering trivia, Jumars where made in Switzerland by Jümar Pangit. I still have a pair of the 78s. I suppose they could have moved production to Sweden.
I’ve broken several name brand accenders used in test rigs; you are at VERY high risk of ruining them over ~ 1200 pounds. Rope damamge is also very likely, or I should say, probable. So make sure there is a load-limiting mechanism. Anything over 600 pounds is abuse.
There are belaying devices better suited for this, but nothing is designed for use with Dyneema, and they are optimized for specific rope types and diameters.
Although not specified in this way, most single climbing ropes have a breaking strength between 58– and 6500 pounds. They will break at lower stress if knotted or drop-tested (sudden load) but that is not a standard breaking strength for any rope.
Great video. There is a lot of food for thought in that. The “obvious” suggestion is nylon, but with that much surge it will fatigue. The best answer is to keep the slack out, perhaps by adding weight, but perhaps also by setting some jib, but a jib sheeted tight is actually the wrong shape; you really want something that does not exist, like a tiny V-shaped riding sail a the bow. This would provide forward tension.
Maybe polyester is the best material, with just a little natural stretch and better fatigue properties. Wouldn’t you love to see them tested side-by-side… but that’s not realistic. I’m bettering, though, that a clever engineer could run a simulation based on that video and would tell you that X5 stretch along the entire drogue (not just the bridle) would solve the problem.
Yeah, I’m thinking Dyneema may be the wrong material from a purely engineering perspective. I don’t like it on travelers, for example, where I would rather have some give. I’ve made that mistake. Dyneema is a great material, and I use it for many things, but I am unconvinced it is best for a JSD. Maybe. But maybe not. Maybe polyester instead of nylon. Better fatigue resistance than nylon, virtually the same abrasion resistance as Amsteel (side-to-side this is probably true–Amsteel brags about end-to-end, which only matters on pulleys), and perhaps just enough stretch. But it’s bigger and more expensive.
(And obviously I meant 5800-6500 pounds, above. I’ve pull tested quite a few samples.)
Hi Drew,
Nylon has a good track record over many sets, so it may just be best to stick with that. More coming.
Hi again Drew,
Trevor has, if memory serves, used a small jib forward to good effect.
I wonder how big of a deal the slack is from a loads perspective, while it looks impressive I am not convinced that there is actually much shock loading (it is a big deal from the perspective of vane gear damage obviously and less slack should give a nicer ride). The steady state load on the drogue is limited by the drogue’s resistance in the water so if there is no slack, then there is no need for shock absorption assuming that the system is designed appropriately.
Once you introduce slack into the system, the impact loads are a function of the mass impacting, the speed, and how much give there is in the system. In the case of a drogue made of dyneema, the mass is going to be low and the speeds are not all that high. The only negative is that the give is pretty low too so even dissipating a moderate amount of energy will have a high impact load. Doing the most basic calculation, 100′ of 1/2″ amsteel (6.4 lbs, 2.9kg) which is more than appears to go slack with an impacting speed difference of 5 knots (2.6 m/s) will have an energy of only 0.5*2.9kg*2.6m/s*2.6m/s = 10 joules which is not a lot of energy. The actual energy will be higher as the bridle is not perfectly in line and that has a more than linear effect but this should still get it in the ballpark. If the first 50′ stretch 0.05% (this is the stretch at 1% of BL), then the force is only 1260 newtons or just under 300 lbs average from this impact which would have a peak of around 600 lbs. It isn’t even completely additive to the static load as the impact will be over before the cones are fully loaded up.
If we take the extremely conservative view that the whole drogue stopped and now needs to be accelerated all at the same instant and it is in a straight line, the numbers look more like 0.5*25kg*2.6m/s*2.6m/s=85 J. Still dissipated over 50′, the stretch will now be more like 0.1% which is more like 2.5% of BL, leaving a load of 4450 N or 1000 lbs average and 2000 lbs peak on a line that is rated to 34000 lbs. Given that this represents only 1/17 of the breaking strength of the line and I believe is a very conservative way to look at it, this doesn’t overly concern me. Don’t get me wrong, I don’t like the slack but also don’t think that it necessarily means that dyneema is not a suitable material. If anyone thinks that this is not a good way to look at it, please let me know.
Eric
Hi Eric and Drew,
Your conversation on snatch loads is way above my pay grade, so I’m staying out of it.
That said, I’m reading your thoughts carefully and learning a lot. Thank you very much for your time and expertise.
The only thing I can add is that, as I understand it, toward the end of his life Don Jordan stated that he saw no problems with the use of Dyneema and in fact seemed to like the idea because the lower stretch would result in the surfing-preventing load coming on more quickly.
Hi Drew,
Both Trevor and I have come to the same conclusion, but without your experience. So, good to have that specialized knowledge.
There is SO much about JSDs we don’t know, but I do have a few thoughts.
The impact is more than 10 joules, because you have accelerate both the mass of the materials AND the water contained within the cones. This is huge factor on parachutes and should not be ignored here. Not a huge number, but probably more than 50 kg, not 2.9 kg even in the first case. The entire drogue contains more than 100 kg of water. I know this from experience.
The other nasty thing about slack is it’s effect on fatigue. Depending on the fiber, fatigue life is 3-5 times greater if just a little residual tension remains on a rope, rather than going completely slack. It has to do with fibers moving in the bundles and also how the crystals and molecules coil and uncoil. You can Google this. It’s a big deal for nylon, but I’m uncertain about polyester or Dyneema. It is even true of metal rigging, explaining why higher pretension is better than slack rigging. It also sets the maximum length for many bridles where yawing is present; you want to avoid a slack leg (although that is not immediately relevant here, since both legs went slack).
If we are curious about the magnitude of that sort of shock load, that could be measured by load cells in fair weather by gathering some slack and hitting it under power. I doubt it is a big number, but the effect of cyclical slack on fatigue and chafe is what I would investigate.
So complicated and testing is so impractical. This is why sharing experiences is so important.
Hi Drew,
I had made the assumption that any forces from the water were included in the base load that Jordan calculated but you have me rethinking that now. Since water is dense and incompressible, there must be some amount of water that would need to be accelerated. It would be interesting to know the max acceleration Jordan calculated for just as a function of a wave strike and what it would be. As an aside, prior to good FEA software for impact calculation, we generally found that hand calculations were significantly conservative due to the assumptions that all forces would align, all of the worst loadings would occur simultaneously and that we had failed at the point of plasticity but you did need to get your boundary conditions right in the first place.
While theoretically possible to build a dynamic model to look at this, you would have so many important assumptions about your boundary conditions in the model that you would be forced to validate the model with testing to get any reliability from it.
As to other materials, I agree with you that I don’t like nylon due to loss of strength when wet and poor fatigue characteristics. Dacron does seem like a reasonable material if trying to avoid dyneema.
Thanks for the response.
Eric
Hi Trevor,
Great, thank for trying the Jumar under load. That was going to be my next task, but you have saved me the effort.
I’m less worried about the loops fouling on the way out. But then I have a larger boat with a clear aft deck and a sheltered place where we lash down the deployment bag prior to leaving port. From the bag mouth to the aft rail is also pretty clear on my boat. Also, I only need three loops due to my retrieval method. Point being that the snag worry depends a lot on configuration.
That said, I agree that if Jumars work, it would be great to get rid of the loops, however, I would worry about the Jumar failing when used in anger particularly on bigger boats, so I think I will have the loops added, when I get a new first section made. (We have the old cones.)
Hi John
Re connecting a brummel splice loop to the main rode on a 12 strand dyneema JDS.
First an apology for being verbose, but without diagrams describing the options takes many words.
I have tried and failed to find a reliable way to attach a retrieval loop to the main rode that does not require the main rode to be cut and spliced at each attachment point.
The loop is easy: its tail (with or without a brummel lock) is safely buried in its own standing part, which is under tension and thus compressed when the retrieval line is attached – so far so good.
BUT I cannot find a way of connecting the loop to the main warp that puts the outer covering of the stressed part (the loop) under tension. The warp is has to go inside the loop’s tail. I can see no way of inserting the main warp into the loop’s tail without cutting the warp.
A conventional brummel-and-bury is useless, as is a shoemaker splice – the wrong part (the stressed part) is buried and there is nothing to compress the outer and hold things in place.
A shoemaker splice that was also sewn and seized held when winched hard but it felt unreliable, and those feeling are correct often enough to take notice of them. I don’t trust seizings on something as slippery as dyneema.
Linked or cow hitched eye splices at each point in the main warp that the retrieval line is to be attached would work and not require an external loop. Although I do not like the idea of cutting and splicing the main warp more often than necessary, this is the only option I have come up with so far that works. As there are already at least eight eye splices in the bridle and drogue, all functionally critical and most highly stressed, I suppose a few more make little or no difference to the reliability of the whole. Perhaps it is the way to go.
It is annoying that I have spent so long on such a trivial problem and still not found an elegant solution. Doubtless somewhere in the discussion there is something important that I have missed. I sit holding fid, needle and palm, hoping for enlightenment.
Addenda: for completeness of my previous comment, the testing I did on climber’s ascenders used Petzl Ascension gear, French made and rated for 8 to 13mm lines. The line was unsheathed 12 strand 6mm Dyneema.
Hi Trevor,
Hum, I’m a self confessed splicing dunce so let me work through what I think I got from Andy:
Now I think about it, I see the problem you are referring to: As the loop line loads the whippings will load and the main line will not compress enough to keep splice integrity since the rest of the main line going to the boat will be loose.
I think you are right, this may be a dead idea, at least without cutting the main line.
One thought: How about passing the main line inside the loop line before cones are added or each section is spliced. Not elegant, and will require bigger cones to slip over the combined loop and main line…yuk. Might work for me, since I only need a three loops on the inboard end of the main line to get it to my big winch, but not so much for single handers.
I think we are left with the ascender, which will need more testing.
The only other option I can think of is to use Dyneema line with a Dacron sheath. Thoughts on that? Not sure it’s a good plan because the Dyneema may slip inside and the sheath bunch, I think.
Anyway, I’m going to update the article to reflect this issue.
By the way feel free to send me a photo or diagram as we try and sort this out.
For retrieval anyone tested something as simple as a short piece of webbing through the dyneema and knotted vaguely similar to the cone connections to give a prussic something to bite onto?
Hi Craig,
I have not tried it, but I’m pretty sure that loading it to the levels we are dealing with here will do a lot of damage to the lay of the rope.
Well, with some 12mm D12 max onboard which will be the bridle and having worked extensively with it, some squashing wouldn’t worry me in the slightest. That stuff is near bulletproof, just watch the bend radius, especially on a splice. Much less a worry than the risk of any loops fouling. What sort of loads did Randell et all experience on retrieval? Enough to be a worry for the rope would have me more worried about a winch if it was round one.
Hi Craig,
Needs to take about 3000 lbs working on my boat, surge maybe double that. Less on Randals boat. Winches have proved adequate for retrieval on many boats.
Only way to know is try it with those kinds of loads. If you do, please send me photos of it under load, immediately afterward, and then after deformation is milked out.
Inserting webbing (suggested below) might be hard on the rope, but what about inserting tapered line inside (a short section of core) to make fat spots? It should not weaken the rope and would be quite easy to do. A few stitches would lock it in place. You would have to test the holding power of a prusic, but it may be one of the very few ways to grab Dyneema 12-plait without damamge. It would be smooth and not damamge the rope.
Just spit balling.
Hi Drew,
That’s certainly an interesting idea. New article on the subject coming tomorrow.
“but what about inserting tapered line inside (a short section of core) to make fat spots?”
Just been thinking exactly the same thing. In the case of 12mm d12 it wouldn’t even need to be tapered that much with so much spare capacity. A loop sticking out of the dyneema snagging in those conditions really is scary!
Back home on the boat next week so will have a play. Only have a 500Kg lever hoist (so it says but cheap from a market in china) so double reeved could prob get up to 3/4T. Some 5mm d12 max onboard which might be OK for a test then hunt down the USB microscope.
12mm D12 is over 20T MBL, seriously doubt if tonne and a half on a prusik would bother it much. I’d be much more wary to be trying to use a jumar or shunt, something might well go bang with them.
I’ll see if I can break something 🙂
Are those loads measured or theoretical? I used to be able to guess vaguely close up to about 500Kg playing with load cells but above that it’s just crazy tight.
Hi Craig,
Yes, theoretical based on known loads on our jib sheets and known power ratio on the winch, so reasonably accurate. Most I could see being ot is 25%. 3000 lbs sounds like a lot until you get on a 56′ boat with a #65 three spped winch. Remember loads on a 56 foot boat are over double those on a the average 45 footer.
Think a single cone at the outboard end of each bridle leg might help a bit to keep tension on the legs?
Hi Craig,
That’s an interesting idea, but given the amount of slack I’m not sure it would do the job reliably. The problem is that the only way to test these ideas is to go out in a Force 9, and then if they don’t work it’s going to suck. Given that’ I think I will stick with Stein’s idea because it is at least somewhat tested, albeit in a different function.
hi John
I was wondering if a small winch drum would deploy and retrieve a jsd similar to the net drums trawlers use to bring there nets in after the boards come up may be a silly question I have no experience with drogues only nets
Hi Darrin,
Interesting idea, but the loads are really too high for any sort of drum that could be installed on a sailboat.
John,
You talk about the catastrophic effect of open throat wire thimbles; the pictures are quite clear, and it has been identified elsewhere. I assume that the solution is simply closed throat thimbles, but the solution isn’t discussed. Is this the recommendation? If so, do you have any suggestions of a source of supply; they don’t seem to be easily available?
Hi Nigel,
See the article at Practical Sailor that I linked to for advice on correct thimbles for each use. Drew has done great work on that, so no point in duplicating it here. He is also way better at that type of work than I am.
John, obviously I suck at finding your links – could you point me in the right direction?
Thx, Ernest
Hi Ernest,
Near the top of the article.
Oh. I could swear I did a search for “Practical” on the page.
Thanks *sheepishgrin*
” The problem is that the only way to test these ideas is to go out in a Force 9, and then if they don’t work it’s going to suck. ”
🙂
Think that’s an issue for all the issues coming to light with the JSD, such small sample size of boats actually out there in really nasty stuff so things like the thimbles & catching the windvane don’t make themselves known until you’re there. Still, you’re allowed to do more than one thing – cone on each leg might help. Maybe some fishing floats might help as well, stop the legs sinking under the paddle if it’s out and some weight to stop the legs jumping up over a vane. Anyway, the likes of Randell who have been there would most likely know better than us mere mortals what might help.
I really like the idea of a flotating device together with some weight to keep the bridle at water level – not below and not above. Maybe something like this might work:
https://i.imgur.com/7BUVos6.png?1
As the bridles should not be compromised, IMHO, the fenders should only be tied to it with some ribbon loop, but this might move along the leg, so I thought a “safety line” from the boat attachment point to the first fender, and from there to the next, might be of value. Not a lot of load to be expected here.
The lead weights should be attached to the fender.
What would you think?
Another thought: what if you would add some weight not only at the drogue end but also at the leader section, directly where the bridle legs are attached? Wouldn’t this increase the effectiveness of the drogue? This came to my mind when looking at Randalls video where it seems that the first section of the drogue is close to the surface. Might even help to preserve some leading cones.
Hard to guess what would work without being too involved out there. Might be to keep the bridle clear of a wind vane a couple of short lengths of bamboo lashed to the bridle from the chain plate with a fishing float at the aft end would work as well as anything. Dunno……
Hi Ernest,
I think the big problem with all of these ideas of attaching stuff to the bridles is going to be the potential for snagging during the deployment. And further I can’t see any advantage over Stein’s idea. Also the thought of those weights and fenders whipping around as the drogue loads and unloads does not appeal to me.
The other advantage of Stein’s idea is that if there was some unintended consequence one would just need to cut the line going out to the end of the batten to put things back to simple and proven.
With all the problems with Dynema, why wouldn’t you just stick with what has worked for decades? It seems to me that all this fiddling around the edges is breaking John’s cardinal rules of gear selection. People I know and trust have gotten big boats out of horrific, life threatening conditions with the original JSD setup and safely and easily retrieved and redeployed for the next bout. I get the urge to tweak things with the latest and greatest tech but it seems to me that the drawbacks of Dynema are outweighing the potential benefits in this case.
Hi Brent,
Good question.
That said, I’m not sure why you would say “with all the problems with Dyneema”. As far as I know there is only one problem: the problem of fouling a vane gear and I’m pretty sure Stein’s idea solves that. Also a lot of boats don’t even have vane gears.
On the other hand Dyneema is much lighter, stronger, and more chafe resistant than Nylon.
Hi Brent,
Not sure what the heck I was thinking when I wrote the above. Must have been under caffeinated! Of course the other problem is retrieval and that just got a lot worse. See Trevor’s comment. So you may easily be right, at least for the moment.
LOL. I was shaking my head as I read your first comment. Thanks!
Hi John and all,
Just a wonderful discussion: all contributors should feel proud and great to have put together an operating manual for the JSD that is likely to make a big difference in many cruiser’s lives.
A couple of thoughts: many of us have cleats aft where the JSD needs to run out when deployed. I remember boats having wooden blocks (like shoe trees) that shock corded onto cleats that made it impossible (or far less likely) to snag flailing sheets. I would consider making my aft cleat snag-proof by making one of these.
Also, I owned a JSD with an OB deployment bag. Very handy for storage (rolled everything up like a big sausage). The JSD was zig-zagged back and forth: the ends being held down (not secured) with elastic. I think it likely would have allowed the deployment of the JSD to emerge without a problem, but I had planned for decanting (flaking) the JSD into a storage bag before deployment as I have never had a line run out and get snagged when stored in that manner.
Finally, someone asked: Why dyneema? For my 40 foot boat, the wet nylon JSD was just a bear to handle and move around. I felt lucky to have not had to do so except in port.
My best, Dick Stevenson, s/v Alchemy
Hi Dick,
Thanks for the confirmation on simple bag deployment. No one over believes me on how well it works until they try it.
And yes, the cleat “shoe trees” would work great I think.
Hi John,
many thanks for pursuing so tenaciously the quest for the perfect JSD setup! All this will greatly increase my degree of confidence when I’ll go on a transoceanic passage for the first time.
A question regarding the conditions met by Randall Reeves in the presumed Gulf stream eddy: how worse was the worst point, compared to the video?
Hi Maxime,
Sorry, I don’t know.
All this seems utterly complicated to me! I bought a dyneema JSD and had a bow roller machined especially with a large throat to be able to test the Hal Roth retrieval method. I won’t have the whipping problem because I’ve welded 1/2×3 inch stainless bar directly on the inside of the scoop at about 1 feet over water level… Test to be done in summer 2020 en route to Bermuda!
Hi Andre,
I assure you that if Trevor Robertson is pursuing these “utter complications” there’s very good reasons for doing so. He has probably sailed more heavy air miles than all of the rest of us put together. Also note that Hal never tried his method, whereas Trevor has used his about 10 times, if memory serves.
That said, if you use the Hal Roth method successfully at sea and in real conditions, we will be all ears and grateful to learn.
We are going to have to fit the solid “chainplates” to our Rival 38, fitting them closer to the waterline seems like a good idea. With our stern design that moves them much further from anything they might catch on.
The Hal Roth method along sounds attractive to me (assuming we upgrade to an electric windlass).
A key factor for us (without much offshore experience) will be lots and tests and practice starting in fairly light conditions to make sure we know and trust the setup and process.
Hi Dave,
With the chainplates closer to the waterline, how much narrower will their width apart be? As I understand it, the bridle exerts a steering force on the stern to help keep the hull in line with the drogue, and this force depends in part on the distance between the chainplates.
Scott, really good points. Going to try with a bridle on its own to see where might be a good location. The Rival is quite a narrow wine shaped reverse counter. Still there is a huge amount of clutter we plan to remove (although probably going to need to add a wind generator pole as ketch makes radar arch style solar impractical).
Dave
Hi Dave,
Not sure how you could use the Roth method if your chain plates were low down since it requires releasing the bridles from the chain plates. By the way, that’s one of my concerns about the Roth method since leaning over to unscrew the two bridle shackles in a nasty left over sea is going to be no fun and potentially dangerous.
John,
Yeah, been thinking more and looking at photos. Your point and the one about how our stern narrows (wine glass shape) mean I think I should fit more like yours.
The Rival has a “Bulwark” hull/deck joint. I’m now thinking that fitting full size plates on the inside of this to through bolt the chainplates will be best. It is all easy to inspect as an additional plus. I’m thinking I’d drill oversize holes and fill them with epoxy, then drill the epoxy for the bolts.
Getting a clean route for the line to a cockpit winch is going to be a challenge which is another reason to like the Hal Roth idea.
I’m thinking that they deployment mat could be sized to clip vertically to the outside of the pushpit, provides a way to visually check it should run out ok. Just recognising that a bag with JSD flaked in might need to be moved around for stowage and so is hard to check.
Don’t even complete on the purchase til next month so plenty of planning time, plus replacing the engine seacock and other jobs will also be a higher priority 😉
Thanks
Dave
Mine are at 128 inch apart (3,25m) and they are so strong you could lift the whole boat with just one 🙂
Just a thought on using thimbles with dyneema. On a forum that has an extensive discussion running ( with some experienced among them) on how to rig Dyneema JSD with Dyneema bridle, there is the concern about the throat of the dyneema eye on the thimble tearing under high loads. This is aside from the thimble causing chafe or the eye rotating around the thimble. The angle of the two legs needs to be very narrow to avoid this tearing force on the dyneema as it “exits” the thimble, i.e. A smaller angle than thimbles provide.
Hampidjan have enclosed thimbles with welded gusset that they say are suitable for dyneema, and the edges are well rounded, but does anyone have any knowledge/ experience with dyneema on thimbles tearing at the throat?
Aside from thimbled eyes on our bridle attached to our drogue chainplates with a beefy Crosby G209A shackle, I’m not sure how else to attach the bridle to our cat.
Any suggestions would be most welcome.
Hi Rob,
I think you are right to be concerned about that. Our two Dyneema shore fast lines are equipped with the Hamipidjan type thimbles and that has worked well. We were advised to use these by the company that provided them who specialize in providing Dyneema lines with splices and thimbles for very high load industrial applications. Also see the work done by Drew at Practical Sailor that I linked to above.
Yes, but the Hamidijan thimbles still present this issue of the dyneema tearing at the throat exit point of the thimble under high loads such as during a JSD deployment. At least it is postulated as an issue by some experienced using in dyneema in thimbles. I’m trying to find data or hear of experience that confirms there is some cause for concern before I commit to it.
I’m thinking of giving a test sample to a load test facility. One end has Stainless Hampidijan thimble with locked Acera 14mm eye, the other end is a non locked Brummel eye that is stitched (with bury in excess of 72 times diameter ie over a meter bury) with long legs to give very narrow throat angle. Pull it apart and see what end breaks and where. I know one thing, when it breaks it will be a serious bang!
Hi Rob,
That would be a great test. If you do it please try cow hitching the soft eye around a shackle pin. I’m beginning to think that no thimble at all may be the best bet. Also some photos of the set up and what breaks would be great. I would be happy to publish the results.
Hi John,
Arghhh, I just found out my contact that used to do break testing for us, is no longer available to do that, so I’ll be searching for another. I’ll certainly let you know the results if I get it all organised. It might be awhile as we’re flat out with this cat build and systems installation, but I think it’s a valuable thing to do if there is no available data on this thimble + dyneema issue.
I would expect the Hampidjan gusseted thimble to be massively strong, so the dyneema throat tearing would be the weak point,…… I think.
Hi Rob,
Bummer! Still, thanks for persevering, it will be a very useful test.
We are using soft shackles to attach the bridles to the the chainplates. The soft shackles are made from the same diameter UHMWPE as the bridles (12mm in our case) and are the high strength design using a button knot. The bridle eyes are 1.5m long and covered with a Dyneema chafe sleeve. The soft shackles are also covered with a Dyneema chafe sleeve (over the entire shackle except the securing loop and throat) – the reason for the long eyes in the bridle is to provide better chafe protection for potential boat contact (our chain plates are about 1m forward and on the outside of the hulls of our sugar scoop sterns).
Thank you for that info Tomasz. My question is how to attach the soft shackle to the chainplate?
Our chainplates are full carbon and bonded inside the boat, so we have a removeable 16mm stainless pin through the chainplate running horizontally, with 2x 10 mm (wide) vertical cutouts into the carbon chainplate that rigging screw tangs could fit into, and then we slide in the 16mm pin and secure it with 2 retaining clips.
The 10mm cutouts are not wide enough for a 3/4″ shackle body, so we are planning to have a custom stainless fitting to fit in the chainplate, and that is what we could put the soft shackle onto. But the bend radius of whatever goes into the chainplate has to be fairly large for the soft shackle, ideally.
How do you attach your soft shackles to your chainplates? Aren’t there 90 degree edges that your soft shackle bend around?
Hi Tomasz,
I’m not a fan of using soft shackles on a JSD. Yes, I know they are pretty secure, and I could be wrong, but having experimented a bit with several types I’m not convinced of their security, particularly when the line is loading and unloading.
Good question. We use a similar soft shackle to attach our anchor bridle legs to the anchor chain and haven’t had any issues letting go there. There’s no differential pull on the soft shackle so no reason for the noose to open. As you say, testing is not easy.
Just thinking about retrieval again.
Rather than going straight to a winch and needing more power on the winch how about putting the tail of a block and tackle on the winch? You would need to repeatedly nip the end of the block and tackle to the JSD but you could have the block and tackle use most of the boat length with some care to avoid snagging.
I’m also thinking this might help with getting a fair route to the winch as you line the block and tackle with the pull and can use turning blocks to the winch.
If you can get a good lead to the winch then when you have pulled enough in to reduce the load you can switch to using the winch directly.
Of course this does require a lot more moving about the boat 🙁
Dave
Hi Dave,
Sure you could do that, but it does add a lot of complication and fiddling about. From our own testing and talking to others it seems that the standard sheet winch on most any boat is powerful enough to do the job, so I’m not sure we need to add anything to that.
The problem tends to be more exhaustion of the person grinding the winch and a drill motor works well to solve that issue. It’s true a tackle would reduce the load on the grinder, but they would be grinding a lot longer.
Hi John,
Regarding Stein’s idea for vane gear protection during JSD use and the attachment of the glass wands to the boat/bridle, wouldn’t it make sense to attach one end of the wand to the vane gear stanchion rather than the boat? It is the vane gear we want to protect after all. It seems it could all be pre-loaded in the calm of the anchorage – one end to the vane gear and the other end attached on the bridle at a pre-determined position with the bridle pre-set on the stern stanchions/lifeline, as you do before you head offshore. That way, all that is left to do is deploy the JSD and let the pre-set wand rig do its job of taming the whip of the bridle legs.
Hi Paul,
Sure you could do that, although I’m not sure if it would make that much difference because the battens will toe in a bit from the hull curve. Probably worth trying both ways and seeing which looks best on each boat.
Hi John,
Just catching up on all this so apologies if I missed anything.
I agree with your discussion with Trevor above, I just don’t see how you would keep the cover tight on a splice as it won’t be under load.
Looking at the bridle attachment, I am far from in love with it. I keep coming back to 2 stacked strop bends (finally learned the name). A few minutes of playing around with some string seems to confirm some of my worries on the separate cow hitches and I can’t see a problem with the strop bends. I realize that we discussed this in the comments to another post and I hope that someone can do some actual testing of this.
Eric
Hi Eric,
You are right, no way a splice is going to work. Trevor and I (mostly Trevor) having been working on this offline, including many experiments. We also have a substitute solution that I have tested successfully and Trevor approves of. More coming in a few days.
Regarding a mushroom anchor as an end weight, and considering how crucial the weight is to keeping the cones in the water, are there any “single point of failure” concerns with the mushroom anchor vs. chain, which can have more than one attachment point to the towline? (I.e. bight of chain with both ends secured to the towline.)
Chuck
Hi Chuck, I wouldn’t think any more likely to fail than chain, but why use an anchor? As I understand it, the idea of the chain is to sink the drogue cones in the water column, so they act as far as possible in still water. The mushroom might act as a large end cone and add to the overall resistance, so tending to make the drogue rise into more broken water for the same weight? Also a mushroom anchor, unless completely true, could end up twisting the JSD making retrieval more complex?
I have run our 10mm chain through heavy gauge 2 inch “lie flat” poly hose seized in place, which mitigates against boat damage when deploying or retrieving the drogue. This then doubles as our dinghy anchor chain when in coastal mode, protecting the tubes when retrieving over the side, so chain gets my vote.
Rob
Hi Rob and Chuck,
Now I think about it I would stick with chain, but just make really sure there is enough of it.
Apologies if I posted this elsewhere. I use 10 x 3lb SCUBA lead dive weights threaded onto a heavy webbing with loops on each end. These are shackled to an eye at the trailing end of the JSD. It is a cheap, compact and simple end weight. The dive weights can be found for around $5 each.
See http://svbeatrix.com/images/JSD_End_Weight.jpg for a photo. The rust stains in the picture are from a previous galv steel shackle.
Hi Jeffrey,
That sounds like a great solution, definitely more compact than chain.
Hi Mal19,
For my thoughts on that see: https://www.morganscloud.com/2018/12/02/which-old-salts-should-we-listen-to-10-ways-to-decide-part-2/
#10
Hi Mal19,
My thoughts on why using a series drogue is a good idea:
https://www.morganscloud.com/2018/09/16/there-are-no-rogue-waves/
https://www.morganscloud.com/2018/10/13/just-get-a-series-drogue-designed-by-don-jordan-dammit/
Hi John,
I have 130 cones that I have bought, imported from the USA and unused as the previous owner retired from sailing and sold his boat. I intend to make up a series drogue for my boat which is a 40ft. trimaran with a loaded weight of approximately 7,000 kg. and quite low superstructure as compared to a catamaran. I have 200 metres of 16mm 8 strand nylon (new). My question is this, is 8 strand suitable for the JSD and if not why not? I have read on the Ace web sight that 3 strand is not suitable because of a tendency to unravel under higher loads, I can understand this. Also to note, the beam aft is 26 ft. which makes the bridle at 2.5 time beam 65ft. which provides a lot of extra stretch. My area of sailing is the East coast of Australia from Sydney North and hopefully into the Coral Sea and Pacific Islands so none of that high latitude stuff for me.
Any thoughts or comments very much appreciated.
Best regards
John
Hi John,
I really don’t know on the 8 strand, but my guess is that it would not be a problem as long the platt was not so loose that the cone ribbons tended to pull out. That said my thinking is that a JSD is the last line of defence so I’m always loath to recommend anything that has not been proven in anger, lest the law of unintended consequences manifest, as it did with Dyneema.
As to number of comes etc, just make sure you are within Don Jordan’s specification.
I am rereading this as I contemplate going offshore again, My stern is fairly narrow, as well, and has a Monitor hanging off of it. I think I understand Trevor’s batten idea EXCEPT how to attach the battens to the boat. Can someone walk through that for me SLOWLY and in more detail? Thanks.
Hi Terence,
First off the idea was Stein’s not Trevor’s. As to attaching it to the boat, I don’t think anyone has actually done yet, but it should not be that difficult. What’s wrong with my idea in the post?
nothing wrong with it. I just can’t quite visualize it. Sorry to be dense.
Hi Terence,
Not being dense at all. I just reread it and some expansion is definitely needed. How about this:
Great explanation. I can now see how to make it work on my vessel.
John: In the above article you refer to the problem of securing a retrieval line to dyneema. In a pink box labelled “February 2020 Update” you indicate that this problem is solved but I am not sure where the solution is described. Can you please point me?
Please disregard above question … not sure why I did not find it before … its pretty clearly identified in the index.
Hi Andrew,
I updated that article to better link to the solutions to the problems Randall identified. Thanks for the heads up.