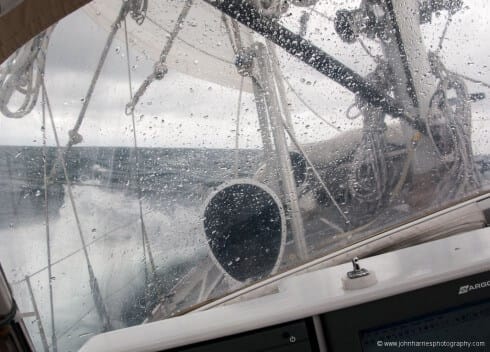
I really enjoy running this web site. In fact, more and more each month. And one of the things that I have enjoyed lately is the participation of trained engineers like Eric, Chris, John and AAC Technical Correspondent, Matt Marsh. (If I have missed anyone, please speak up.)
The cool thing about these engineers’ participation is that I am now understanding, as never before, many of the things I have observed in my 55 years of messing around in boats.
So I thought that it would be interesting to relate some of my own experience to Matt’s post on cycle loading, and then derive some tips for boat and gear buying from the result.
If you have not read Matt’s post, please do so now, otherwise this post won’t make a lot of sense to you. Don’t worry, I will wait right here while you do.
Back? Great. OK, let’s look at what we ocean voyagers can learn from Matt’s post.
Nice summary, John, and I generally concur with your recommendations. A few further thoughts, though:
“Avoid the Seventies”.
A valid point, but there were some good boats from that era and there’s plenty of equally bad (or worse) stuff from the ’80s, ’90s and even today. As scary as it is, David Pascoe’s famous rant Are they fibreglass boats anymore? is still very much valid: there are many cases where we do not have the slightest flippin’ clue what the hull is really made of.
Fatigue, particularly in aluminum.
When designing in metal, you’re limited in some cases by the yield strength of the metal (the stress at which it deforms without springing back) and the ultimate strength (the point where it breaks). (In many other cases, you’re limited by stiffness, not by strength- an important distinction, but not necessary for this discussion). If you repeatedly load and unload the metal to a significant fraction of its yield strength, those strengths will gradually decrease.
For steel, they eventually stop decreasing, at about 50% of their original values, after about a million to ten million cycles. This is the “fatigue limit” or “endurance limit”. For aluminum, they never stop decreasing, but the decline slows down dramatically and is pretty small beyond ten million cycles. With either metal, you can work around the problem by designing the part to be strong enough in the fatigued condition- i.e. by designing around the fatigue strength, not the original yield strength.
Aluminum’s big problem is that its composition and microstructure change quite dramatically in the region around a weld. A weld is already a stress concentration, and now we’re weakening the material in that area. That’s a recipe for rapid fatigue and, eventually, the formation of cracks. You can work around this problem, but it requires a co-ordinated, professional effort:
– The designer must thoroughly understand the load paths and be careful to avoid anything that would lead to a stress concentration, excess flexibility or vibration.
– The material supplier has to have strict QC to ensure that the individual components are of the correct composition and temper.
– The welders have to be really, really good at their jobs, following the proper weld sequence and being very careful to ensure good weld penetration without causing heat damage to the surrounding material.
There are a lot of aluminum boats that last darn near forever, and there are a lot that fail in their first few years- the difference usually boils down to fatigue, which can be prevented with proper design, well-trained labour and good QC.
Hi matt,
Thanks for the clarifications and corrections, particularly on fatigue limit, which I had a bit backward, although nothing that changes my conclusions.
Very interesting points about the issues with aluminium welding and the requirement that everyone involved really know what they are doing. I had a very interesting discussion last week with an experienced aluminium welder, who works at a local boatbuilder, on the practical aspects of getting a good weld. He went on and on about the importance of making sure that the surfaces are cleaned of all oxidation and are not contaminated with any other metals.
This will sound a little self serving, but your thoughts on aluminium fabrication made me wonder if when buying aluminum boats maybe concentrating on those with a good number of miles on them might be a good idea on the theory that if they don’t show any signs of fatigue failure or flexing after say 50,000 miles, that they are probably not going to. Either that, or buy from a company like Boreal with proven QC and boats out there. This might be particularly true since one of the good things about aluminium is that, as I understand it from a surveyor that specializes in the material, any fatigue failures are blindingly obvious (and difficult to hide) to anyone who knows what they are doing and where to look.
I can’t weld aluminum- heck, I have a hard enough time with flux-core on mild steel. I have a lot of respect for anyone who can do good clean work with a MIG or TIG torch.
Flaws in aluminum construction are, I think, likely to reveal themselves within the first year or two of hard service. You do occasionally hear about more insidious vibration and fatigue issues in big multihulls that turn up later, but those are becoming less and less common. And any surveyor who knows aluminum shouldn’t have too much trouble recognizing the early stages of failure, provided she can actually get to the components in question. (This latter bit is, of course, often more than a little tricky.)
Hi Matt,
I just followed your link to Pascoe’s site. Now that is some scary reading. And to think I was worried about boats built in the 70s!
Actually, while, as you say, there are some good boats built in the seventies, there were also some real horrors. And even some of the big reputable builders, who had built good boats before the oil embargo, secumed to the temptation to preserve their profit margins by cutting back on the thickness of the laminate. I personally saw several of these very light boats with substantial structural problems that developed within a few months of their launch in the early seventies.
Of course, as you say, there are some pretty distressing examples of that today too. Colin, the other day, told me of two horror stories of brand new boats that had to be written off due to structural problems, both from big name manufacturers that have a reputation for quality, in just the last two years.
I could tell you very similar horror stories involving freshwater mid-30s sized yachts from 2008 and 2011 respectively. Big boat-show brands both. Both had defects that put them out of the running, even for farting around in Lake Ontario, for a friend of mine who has both the desire to own a nearly new boat, and the experience to tell when they are insufficiently well-built.
I used to dislike most production boats of the last 20 years in a vague way. Lately, I can get appallingly specific on why so many of them are eggshells held together with snot.
I’m about to run out of my $10 for 24 hrs WiFi, so I’ll keep this short. When it comes to sizing gear, remember it has to function “en suite.” A properly sized block, needs a properly sized bail, needs a properly sized bolt, needs a properly sized backing plate, etc.
We see a lot of folks who have up-sized their gear and just moved the failure point to a new location. One glaring example last month was a boat that had gone from a Lofrans Windlass to a Lighthouse and they had just bored new holes in the old backing plate because they didn’t want to mount the windlass where there was adequate structure to transfer the loads to the hull. Quote “It would have been a tripper.”
Hi Chris,
A very good point, everything in a particularly system must be sized to have roughly the same strength.
Leading on from that, it is also really good to know what the weakest link is—the circuit breaker, as my friend Ian McCurdy calls it—and to try and make sure that that item in the system is the one that will do the least damage when it breaks if the system’s design load is exceeded.
An example would be to make sure that a sheet will break before the winch it is attached to rips out of the deck.
My Dad was an engineer. His intuition was far more valuable than his education. He was a mechanical (refrigeration) engineer and became a systems integrator on Gemini, Apollo, Apollo-Soyuz, Skylab, and Shuttle. He could intuit when designs were inadequate. Much of that came from breaking things. He used to tell me that nothing was quite so instructive as testing something to destruction — a lesson learned in WWII.
In our area of endeavor, testing to destruction might happen with anchors and such, but the big ticket items don’t get that treatment — it’s just too expensive. He once told me early adopters of any technology must be willing to lose everything because time to market pressures always resulted in often deeply buried, possibly fatal flaws. The history of engineering is chocka-block with examples.
Hi Chris,
Now there’s another really good point: don’t be a pioneer. Back in the day, when I was a mainframe computer technician, we used to say: “Q:how can you tell who the pioneers are? A:They’re the guys with the arrows sticking out of their chests.” Not politically correct, but a good point, nonetheless.
Indeed!
In design meetings, I used to chuckle-laugh-snort when someone said a field item had been rugged-ized, I asked them why had they created something that needed to be. The answer was usually blather.
John, A very interesting article. And I very much agree with you in appreciating the flock of participants who contribute so greatly to AAC. The above makes one have second thoughts about the light weight boats being turned out nowadays. I have thought, in the higher end boats, that light weight and longevity could be accomplished through good engineering and design. Now I am not so sure. I wonder what the hull life is on some of the cored hulls which must flex some, even in the best designed boats. This is certainly an area that I have never seen addressed in any publication.
My best to all, Dick Stevenson, s/v Alchemy
Hi Dick,
I think you can build a lightweight composite cruising boat that will last, but it takes three ingredients: great engineering, huge realworld experience, and plenty of money. For the owner with the latter, my old friend from 505 racing days Mark Lindsay at Boston Boatworks can supply the first two. Mark built the hull for Newbold Smith’s “Reindeer”, a lovely boat, because Morris Yachts, fine boatbuilders though they are, did not want to try to build the boat as light as Smith wanted it.
Good post John.
Reading your comment : “you must, as Matt so clearly explains, engineer it to be at least twice that strong if it is going to survive the ravages of cycle loading for a good long time” makes me laugh a little! Not that I don’t agree, believe me I do! But I am an engineer as well, and it use to be “at least three times as strong” as a safety factor. That is what the American auto industry was doing (as an example) until the Japanese got onto their turf. Then, to be competitive, they started calculating more precisely what safety factors were required, and it became much smaller with the years, and “finite element analysis” became the preferred tool to reach that goal (since empirical experimentation is too expensive)!
So that “finite element analysis” is what is done for your car, and you’re driving it! But you are driving it in the conditions it was designed for, respecting the rules of the road, and not overloading it! So maybe the boat designers are actually doing a good job, for the average Jo who buys his Jeanneau to sail the local lake. It is the wakos like you (and me, and many others reading these posts) that are demanding too much of our boat maybe! Going out at sea in a storm !? What are you thinking !
Oh yeah, that’s true, they have the “oceanic” models, one would think it means more than “salt water tolerant” 😉
In short, what Matt is saying, is that after all this hard work studying to become an engineer he recommends a safety factor of 2 !? Glad to see that some young engineers still have some common sense, but that will be hard to sell to boat manufacturers !
And be careful with tip #7, “avoid the seventies” as a lot of your readers would not like to be avoided
Thanks for chiming in, Jacques. I certainly agree with your point about FEA- as we gain a better understanding of the forces involved, it’s possible to make more efficient use of material. (And if I’m going to experience a car crash, I’d much rather be in my FEAed-to-the-max Hyundai than in a ’70s vehicle of comparable weight and size.)
Just to be clear, I am emphatically not recommending that 2.0 is the correct safety factor to use.
My point was that if a part is intended to survive extensive cycle loading, the design calculations should be based on the fatigued strength of the material after 10^6 to 10^7 cycles, which for many common boatbuilding materials is roughly half of their new-condition strength.
The “safety factor” (I hate that term, really… “factor of ignorance” would be more apt) is supposed to account for all the unknowable factors. Things like overloading in an emergency situation, a few inches of sub-par welding, unexpected shock loads, etc. I’ve seen this figure vary from 0.9 (some mining operations) to nearly 10 (propeller shafts on heavy displacement motoryachts), depending mainly on how well the various forces are understood. But I don’t think it’s appropriate to include fatigue in the standard factor of ignorance, as fatigue is well understood and quantifiable.
It would be interesting to hear comments about the use of epoxy to construct ‘grp boats’. I know a couple of builders (power and sail) have gone this route. Cost aside, how does epoxy cycling and fatigue limit compare to other building materials?
Hi Joe,
I’m certainly no expert, or even close, on high tech laminates, but my understanding from hanging around a bit with those that are, is that you get much better and longer lasting laminates, particularly if a core is used, with epoxy resin than polyester, because epoxy adheres (sticks) much better than polyester. However—there’s always a “however” in boats—epoxy can be much more difficult to work with and generally requires more skill.
I know that there are 505s around, built from epoxy resin skins over kelegcell core by my friend Mark Lindsay, over 20 years ago, that are still stiff, light and competitive.
Nothing like a new can of worms. The whole discussion on hull materials and the changes though time and technology. I don’t know what to research first and why? Why study up? A boat change and likely to embrace more speed. I’ve lately herd “speed is safety” I get that argument.
How do we know what we got and what’s enough? I sail a pre Frers Hallberg Rassy 1988. It’s heavier and slower than the new hulls. HR is known for a tough hull, pioneers of GRP? Right? It seems HR brought in more of what I want, better up wind, faster but at what cost? Is it tougher? Stiffer? Hull thinness? As a home builder, I can build a house from the same material with two different “attentions to details” and get two different houses. So I’ll build my own home but I’m not ready to build or watch the building of my next boat. How do I know? Lyman Morse…….$$$
When is tough enough. I don’t want to be the Winston Churchill. I’ve heard it “fell” off a 45 foot breaking wave and landed on its side in the green water. Imagine that! I want a fast, comfortable, fun boat to sail that can take that kind or event and then never let it happen. So what materials fit that demand?
When we first got Halcyon, we had a big jibe in about 25 -30 knts of wind (note: I was not at the helm). The preventer pulled the leak damaged pad eye through the deck. We had our first failure leaving a 2×2 hole in the deck at the start of a nasty passage. I don’t blame the boat or the minor water infiltration. It’s my fault. Maybe I couldn’t stop the jibe, not being at the helm but I certainly could have reduced the loads that resulted. The truth is I was lazy. The wind changed and I was going to finish up eating and then reef.
I guess my point is to failure. As the steward of our vessel, we have choice in the loads especially when it’s bad. Don’t get me wrong, I’m a tough boat guy but you can cut a hardboiled egg with a sheet of paper. Technique is everything. For me, let the hull material research begin. I’m still working on “Heavy weather avoidance” lol
Hi Dan,
Yes, you are right, and that was a lot of my point in the post: it’s a minefield out there with a lot of boats, probably the majority, that are not safe to go to sea in. Not a state I’m at all happy about but, as I said in the post, we boat owners and buyers will generally be a lot happier and safer if we deal with the world as it is, not as we would like it to be, or as some salesman will try and tell us it is.
These issues are a lot of what inspired me to come up with the Adventure 40.
Talking of flaws in aluminium construction reminds me of a relatively lightly plated 60′ ocean racer I inspected during construction back in the ’80s. The general workmanship was excellent and I was full of admiration for the fine consistent welds and lack of distortion despite the 4mm topsides plating at the bow and stern. I noticed an empty welding wire box and was surprised to see that the builder was using a different filler wire than I was used to using.
He told me it was “much better” as the welds are “stronger”. As an aluminium boatbuilder myself (at the time) I had to learn more and so called my suppliers and talked with their metallurgist. He explained that the boatbuilder was right – to an extent – but that he hadn’t mentioned that the welds have little ductility. Not good.
This is not something that would show up in any normal survey inspection and I often wonder what happened to the boat in question. This was back in the early ’80s and I would be surprised if this kind of error was being made these days.
Our 40′ aluminium cruising yacht is now 28 years old and – so far, so good. No failures, no cracks, no significant corrosion. I’ve replaced the hull anodes once in that time (they’re about due to be replaced again!).
Hi Pat,
Yikes, that story really brings home the point about only buying an aluminium boat from a reputable manufacturer with a proven track record.
However, assuming that the welds were wrong, it seems to me that a good surveyor would be able to detect the resulting cracks pretty easily after the boat had been sailed a while. Of course, sadly, that does not help the original buyer.
John, I was rafted off Reindeer many years ago in an attempt to do one of those circular anchored boat things (forget the name) that YCs are fond of and make glorious pictures from above. Newbold was kind enough to give a tour of his lovely boat, but we never got around to construction details. It sounds like there are not too many long lasting cored hulls produced from the criterion you describe. Dick
Hi Dick,
I’m envious, in that I have never been aboard Reindeer.
I think that’s the whole point, isn’t it. Great boats can and are built with these high tech materials including high tech core materials, but you had better get the engineering and execution perfect if you want the boat to last. The other problem is that is is so difficult for a surveyor, even at the time of build, to determine whether everything was done right.
John,
Good post with some very wise real world takeaways. I thought that I would throw in a couple more thoughts in about fatigue.
Fatigue in most materials starts to be a problem due to excess tensile stress. Compressive stress can break things but it is unlikely to start fatigue on a part as the little cracks that form don’t try to flex open. Most fatigue starts at the surface of the part and works its way inwards. Typically, the highest stresses in a part will be at the surface. If you think of a solid beam with a force pushing down on the middle, the bottom of the beam will be in tension and the top will be in compression with both forces acting along the beam. The middle of the beam will have basically no stress which is the reason why we have developed I beams which have a more uniform stress distribution throughout. In addition to the transmitted forces being highest at the surface, the stress tends to be even higher due to imperfections. The cracks that form in a fatigue situation and eventually lead to failure will generally form at these tiny imperfections as they lead to higher stress.
Because so many of the problems start at the surface, there are many things that we can do to improve fatigue performance. For one, we can try to get rid of as many stress concentrations on the surface as possible. In the extreme, many people actually polish the surface although this likely does not work in corrosive environments. What it does mean is that if you inadvertently damage the surface of a highly stressed part, you need to fix it and make it smooth again, a sharp cornered hacksaw groove through the middle of a part can really be a problem. With welds, grinding and heat treating can make a big difference as Matt discussed above. Heat treating can be used for several purposes including eliminating the inherent stress from welding and even making non welded parts more fatigue resistant through case hardening and through hardening. On shafts and some other parts where a discontinuity such as a change in diameter is required, proper fillets are crucial and even they often lead to a stress concentration on the order of 3X. Another technology which is very cool and is used extensively in things like engines is shot peening (they even have laser peening now) where a compressive stress is intentionally put into the surface of a part to make the magnitude of any tensile stresses lower so that cracks don’t form or at least do so more slowly.
As you point out, this is all stuff that the designer needs to figure out, the builder needs to properly follow the spec and the owner must maintain.
Eric
Hi Eric,
Thanks for the interesting comment. I have been reading a bit about stress risers and the takeaway for me, aside from the obvious of avoiding them, is that it is just one more indication of the very high safety margins we need on offshore boats because things are going to get dinged and they need enough margin to absorb that without failing.
Hi John, one more engineer amongst the fine crew here, Mechanical Engineer, went thru Auckland Uni in early 80’s with most of the guys who form the technical backbone of NZ’s successive AC challenges. 30 yrs in the resources industry round the world. Involved in all sorts of interesting jobs including a few prototype “bleeding edge” projects where design was in some cases not much better than best guess. Also partner in a welding training and repair company.
Talking about aluminium boats most common failures in welds seem to simply be a lack of sufficient weld length, which allows flex in the plate eventually fracturing the welds. Very common in smaller fast power boats. Also need to have the right ratio of framing for the plate thickness, ie limiting the size of the unsupported panel. When aluminium was popular for race yachts there were alot of failures because designers were chasing weight savings, plate too thin and not enough frames and stringers. If you want to see examples of aluminium construction to a high standard, visit Steve Dashew’s site – there are alot of good photos of work in progress. The fact that those boats are unpainted also means the weld process has to be more carefully managed to avoid heat related distortion.
Hi Alan,
A very good point that the secret to good aluminium construction is execution. I have been following Steve’s project in NZ, and talking to him about it, for quite some time and with great admiration.
I also really like your point that specifying an unpainted hull forces the builder to be more careful since there is no way to hide any mistakes—another benefit of aluminium.
Hi John,
I just wanted to clear up an apparent misconception about steel initially losing strength.
….Benefits of Steel
“What this means is that if you build a structure out of steel it will initially lose strength from cycle loading until it reaches its fatigue limit, and after that, it will stay at the same strength no matter how many times you cycle load it……”
Matt wrote a good article on cycle loading and the mechanism by which the fatigue cracks grow and the Wikipedia article further explains the phenomenon. The inference that ” steel initially loses strength… is simply not correct.
Before I continue, a bit of revision, remember Stress = Force / Area.
Simplistically speaking, for Ferrous materials, provided the cyclic stress is below the fatigue limit then fatigue cracking does not occur. It’s not a matter of the material initially losing strength and then miraculously becoming stable.
However, where the cyclic stress is greater then the fatigue limit, fatigue cracking occurs. This is the case for both ferrous and non-ferrous materials; It’s the mechanism by which steel crankshafts fail and aluminium masts develop cracks.
Think of it as being a bit pregnant. Although the crack may start at the microscopic level, with each cycle, it progressively gets a little bit bigger. The propagation is usually only measured in parts of microns uM, but over millions of cycles, this adds up.
The point is, with each cycle the crack gets a little bit bigger, the cross-sectional area of the remaining structure gets smaller and the structure gets progressively weaker. (No initial weakness and then stability.)
At some point, the cyclic load, i.e. “The force” divided by the remaining cross-sectional area, exceeds the ultimate tensile or yield stress of the material. When this occurs, the structure fails catastrophically, without warning (if you don’t count the fatigue crack which is the early warning sign, albeit one that is not normally visible to the naked eye. ) and is usually accompanied by a very, very loud bang.
With Aluminium Yachts, I agree with your conclusions; built it massively enough and fatigue cracking will be so slow that for all practical purposes it will not be a problem during the lifetime of the yacht.
PS love the online books – a fantastic resource.
Pat
Hi Pat,
Thanks for catching that. I have fixed it. And thanks for the kind words.