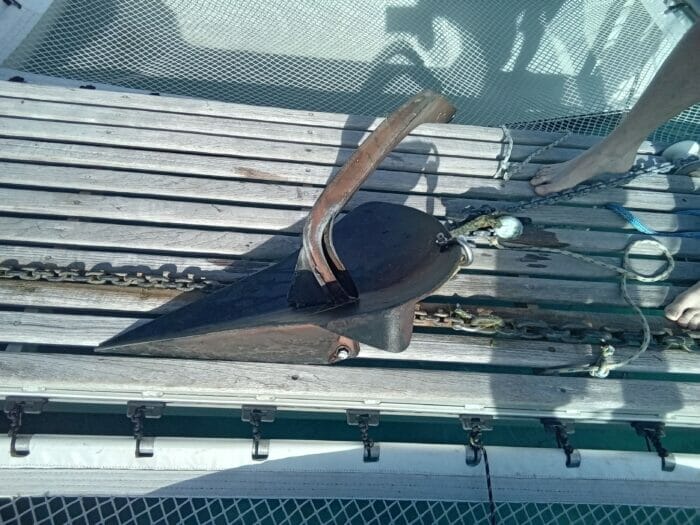
Member Gavin wants to get to the bottom of why his Spade anchor, that had served him well for six years, failed so catastrophically.
AAC contributor, engineer, and experienced sailor Eric Klem and I both got interested in:
- What the cause might have been.
- The lessons all of us can learn from this incident.
So we both followed up in the comment stream with some questions that Gavin answered promptly and well.
And then we both independently came up with some thoughts about what might have happened, which correlate well, although Eric’s include a deeper engineering understanding than mine.
A big thank you to Eric for much of what follows. That said, I have built on some of the things Eric told me and in so doing could have made errors. If so, they are all mine.
I’m also hoping that both Eric and Matt come up in the comments to this article, as they so often and so generously do, to correct any engineering mistakes I have made and/or postulate different theories.
Before we get going, this is a long article at over 3000 words, and then I plan to follow up with a second on the many lessons I learned from this incident. That said, it’s worth your time.
This is not just about one spectacular failure, but rather about things we can learn from this that can make us safer going forward.
Here’s Gavin’s original comment, lightly edited:
I am interested in opinions on my recent catastrophic failure of my SPADE anchor S160. I am particularly hoping to hear from John, and Steve Goodwin of SV Panope.
I have a 46 foot catamaran, 14 ton displacement. I have lived on my boat full-time since 2016. When I started out, I had a Spade S140. I upgraded to an S160 in 2017 in Cherbourg.
I have sailed this boat from Florida, to Newfoundland, and on to Greenland, Iceland, UK, the Baltic, the Med, the Caribbean, and across the Pacific and I am now in Fiji.
I have about 50,000 miles of ocean sailing miles logged and we anchor approximately 320 days per year.
I have been in my current anchorage now for 48 hours with lots of wind.
I am with 6 other boats. They are using Manson, Sarca, Excel, Rocna, and Delta anchors. I was using my Spade S160.
It is a very gusty anchorage with winds from different directions 10 knots gusting to 33 knots. I was anchored in sand, 3 meters depth water from sea bottom to sea surface at high tide on 20 meters (65 feet) chain, 7 meter (23 feet) nylon snubber bridle.
I had set the anchor as per my normal routine with 1800 rpm in reverse with two engines. I had checked the anchor by snorkelling and it was buried in sand.
In these sorts of conditions we have never dragged. But this time we did. My SPADE bent 90 deg where it meets the scoop (see photo above).
I snorkelled the anchorage again and confirmed there is nothing but sand. The damage occured while anchored, and not during retrieval.
Gavin French
I also recommend that we all read the whole thread since Gavin expands a lot on the above. (I have closed said thread to comments since it will be more useful if further discussion occurs on this article.)
Let’s take this step by step:
My first thought just looking at the picture was that it must have been caught by a rock, but I think it would be quite possible that a significant shock load at the right angle could bend the shank before overcoming the inertia of a fluke burried deeply in hard sand.
Hi Dan,
I wondered about whether or not the shank could bend in just sand, but given the rarity of this failure, concluded that it was not likely. Also my thinking is that the very stiff clay we have anchored in so many times here in Nova Scotia and other places would restrict pivoting more than sand.
I don’t see that as likely. The forces necessary to bend a shank like this, even if we assume a hidden weld defect at which the failure will initiate, are probably beyond what seabed sand can resist at any degree of packing. I can’t see a failure of this type happening without the fluke being wedged against rock in some way.
I am not an engineer, so the following comes from a certain level of blissful ignorance.
If manufacturing defect was indeed a contributor, the question for those of us who rely on Spade anchors is how often do they occur. Given the complexity of the shank design, it’s not surprising that a rare defect would slip through, but are they only rare?
Personally, I will continue to rely on my Spade, but I will be regularly inspecting my shank for any signs of water intrusion.
Hi Bob,
On your number three, the Spade shank is not watertight, it’s open at the end, so a pinhole would not make a difference to that.
I agree that the short scope would not generally be a problem, but in conjunction with a Dacron snubber and the other issues I detail and assuming the anchor was caught in a rock, I’m very confident that snubber issues made things worse.
And we have an opinion from a professional engineer (Eric) that any anchor could be bent in those conditions by that boat if the load was off axis. As I say in the article, based on my own experience of being anchored in katabatic winds I’m close to 100% sure Eric is right.
As to how often this occurs, I think the absence of reports speaks well to that. Not often. One thing I know after 20 years of publishing is that if I recommend a product, particularly an anchor, and there are failures or problems, I will hear about it! That’s how we found out about the Rocna drag modality.
Thoughtful writeup as usual John,
I too suspect the obvious off axis side load.
My experince has been only positive with now my 2nd Spade, previous like you was the galvinized S160 and now S220.
Thoughtful writeup as usual John,
I too suspect the obvious off axis side load.
My experince has been only positive with now my 2nd Spade, previous like you was the galvinized S160 and now S220.
Hi John,
I’m also no engineer, but have the highest qualifications obtainable from the know-it-all institute… 🙂
I agree with all points here, but there’s one issue that has been implicit , but as far as I’ve noticed, not discussed:
The SPADE shank is several times as stiff as almost any other anchor shank, which is a great benefit almost always. However, that very property can also be a vulnerability. That vulnerability would seem to be relevant in the case discussed here, with a short rode and a perhaps not very stretchy snubber.
My point is that the stiffness comes from shank geometry, the triangle cross section, not from a thick bar of steel. The walls of that triangle are relatively thin. They totally depend on being connected to each other. The moment a weakness in that connection is achieved, the shank consists of thin plates and the stiffness of the shank is a small fraction of its normal.
Stiffness means ability to withstand a high load without deflection, of course. That lack of deflection means significantly less shock absorption than with other softer shanks. In a situation when other shock absorption options are less available, like in this case, the lack of flexibility in the shank could be what makes the load too high for the welds. The dramatic bend in this case is to be expected. The moment this shank starts to fail, the resistance to further bending is minimal. It will be a bit like the ketchup bottle effect: Nothing, nothing, nothing, nothing, all of it!
The conclusion seems to be just the obvious: To achieve any complex goal with any product, choices / compromises must be made, always. The SPADE anchor has gotten needed shank stiffness while keeping a great balance by removing weight inside the shank and adding lead in the tip. Kinda similar to a monohull boat. This works really well. It’s a great anchor.
The potential weakness is less inbuilt shock absorption than anchors with a weaker shank. However, shock absorption isn’t really the job of the anchor, but rather the rode and snubber, of course. I’d much prefer a stiff shank and be aware that I need to pay attention to shock absorption in my system.
Hi Stein,
I agree, but I thought I had covered off the this issue of Spade shank geometry:
I also quoted Eric on the same subject.
And, as I say in the article, I intend to explore this further in the next article.
That said, while I agree, and say, that the Spade is more susceptible to a construction flaw or deterioration I’m not at all sure that stiffness, in and of itself, equates with vulnerability. This is a complex subject. For example for many years yachties (including me) pretty much all agreed that high stiffness chains like G70 were not a good idea, but when I asked the engineers at Peeless who make the stuff the answer was that’s a common misconception, but not true. In fact G70 is recommended for high impact use as binder chain on trucks.
Obviously this is a different situation since G70 gets it’s stiffness from heat treating and the Spade shank from geometry, but it does show that what is obvious to us lay people is sometimes very wrong.
Hi Again Stein,
Just found this very good explanation of the relationship between stiffness and strength: https://www.fictiv.com/articles/engineering-fundamentals-refresh-strength-vs-stiffness-vs-hardness#:~:text=These%20properties%20are%20related%2C%20but,it%20deforms%20permanently%20or%20fractures.
The way I read this is that stiffness can be a very good thing in anchor stocks because it means the stock can take far more load before it permanently deforms. I say this because we know from reports and testing by Steve Goodwin that once a stock has bent, even a little, the anchor gets unreliable.
So yes, a solid anchor shank may fail less catastrophically but once it’s bent, the anchor is useless anyway. So having a stock that’s twice as strong, and stiffer is, I think, generally a good thing, as long as it’s made right.
More in the next article.
Having followed the Rocna vs Spade discussion on the board from its beginning, and being an early Rocna adopter, I’ve had lots of time to peer at and ponder various Spade anchors on many bow rollers. My massive Rocna 25 is certainly an ugly duckling compared to the graceful Spade, but that hollow shank and bolt on connection to the fluke provoked nagging doubts about the Spade, and yes, now that you mention it, my Rocna roll bar, after 16 years of use, has just been perforated by rust inside the roll bar. The Spade pictured in this article looks quite rusty, which probably relates to the shank failure.
Having had some experience with box frame automotive chassis (Triumph sport cars), I learned that rust proofing measures applied to the exterior of hollow steel fabrication do not prevent invisible deterioration from occurring inside the hollow metal structure. That hollow triangular shank on the Spade looks cool, but seems vulnerable. I think I would stick with simple mass when it comes to anchors. Complexity of design and construction is not an advantage in the anchor department.
Hi Reed,
I disagree. The complexity of the shank construction confers big benefits (in exchange for some drawbacks) one of them being that the Spade does not exhibit the dangerous dragging modality of almost all roll bar anchors, particularly Rocna and Manson. It also does not have the stowing problems of the roll bar or the problem of bent roll bars that the Mantus M1 exhibits.
And given that we have way more reports of fast dragging with Rocna than we have bent stocks with Steel spades I think the balance of tradeoffs favours the Spade.
The point being that the Spade could not work as well as it does, particularly without a roll bar, without the fabricated stock.
More in the next article on trade offs with Spade.
Hi… I am “Gavin” who owns/owned the bent SPADE S160:)
First, let me say that divesting any attachment to my ego has been both the plan for, and result of, my ocean cruising. And so please take all comments here as analytical and without personal attachment and most certainly with no offence intended.
1) Re Snubber. John, you asked me several questions by email and so I wonder why you didn’t clarify about my snubber before publishing and hanging a portion of the conclusions on this uncertainty? I can confirm, and I took the time to write the chandelry in Hiva Oa Marquesas where i bought it, that the snubber is “Aliphatic Polyamide”… Aka Nylon. I apologise for the Octoplait reference in my email and meant that (albeit with some ignorance:) simply to mean 8 strand nylon not 3 strand rather than a brand reference. It could certainly have been longer, and I have a second one which is 12m long which i typically use “in a blow”. It is slightly more work to rig given the angles and lines that suport my bowsprit so I more often use the simpler 7m one. I wonder what might have happened if i had been using that one, but I personally think a lengthy discussion of the snubber verges on pedantic.
2) Re geometry. John you describe the scope of 3m water, 20m chain, 7m snubber as “That is a seriously short rode, although probably just-adequate scope”. Whether to include the meter of height from water to bow cleat is unknown to me, but I do routinely as a habit in the interests of redundancy. So at 4 m (3 water plus 1m to cleat), 27m of rode calculates to 6.75:1. If ee exclude the height of the cleat the calculation is 9:1. Please explain your description of the rode to me as SPADE themselves have replied that they felt the scope and setup was “beyond that which we reccommend”. But I do also think focusing on scope also risks missing the point here.
3) In terms of the caternary effect of chain, and deep water versus shallow anchoring, I think that is clearly true. As above, I wonder what my longer snubber might have done. But to pull my head out of the pedantic locker… I very much believe that catastrophic anchor shank failure discussions should not hinge on 7 versus 12m of nylon snubber or even chain caternary.
4) Re was there a rock or not? I spent a lot of time snorkelling this anchorage after this event while meditating on the fact that somehow my boat suffered no damage:) And I believe (based on following the drag track, the clear water, and the precise gps coordinates of my anchor drop) that I excavated the actual hole the anchor pulled out of like a deranged pirate seeking his treasure chest. No rock or coral. But again, I wonder if this is missing the point as many an anchor will find itself next to a rock.
5) While “any anchor might bend in these conditions”, I would not put this in bold typeface attributing lots of merit. I truly mean no disrespect to Eric. But do we really believe that any anchor with a solid shank would bend catastrophically a full 90 degrees to the point of being completely useless as this one did? Bend perhaps, but fold up like wet origami as my SPADE did here… unlikely but who knows?
6) Perhaps relevant but undiscussed is the fact that, like Steve Goodwin in his videos, I typically drop my anchor using a clutch on the windlass so it ‘freefalls’ rather than motoring it down in reverse using the windlass. I have not videoed it, but it stands to reason that it could land with quite a clunk on rocks. And thus put the welded and relatively poorly galvanized SPADE shank at risk of minor defects leading to corrosion.
Gavin
Hi Gavin,
I’m glad to hear the snubber was nylon, not Dacron. Also note that I wrote that it might just have been that you were mistaken in your email.
I’m not going to get into arguing each of these points with you. You asked me for my opinion and now you have it, but you certainly don’t need to agree with it. I didn’t really expect you to, given how much emotion (understandably) you must be feeling from a very unpleasant experience.
I put a lot of time and effort into this analysis and I’m confident in it, at least unless we get further reports and/or Matt and/or Eric find an engineering mistake.
That said, a few clarifications:
In Part 2 I will be writing more about the effect of the above issues on Spade anchor selection, or not, as well as what we can learn for the incident that’s applicable to all anchors.
Hi John, i will happily revise any wording that generated any upset of any kind. None was intended:) And I feel I neither agreed nor disagreed but weighed in to explore further. Thanks again for your opinion.
Gavin,
I’n not sure what you are referring to. I never even implied that I was upset, and I’m not. After 20 years of doing this I have a very thick skin.
I agree Gavin, at least 6.5 to 1 scope, is by no means considered seriously short scope. Especially since you report wind gusts reached 33kts. That is hardly severe as it sounds like it’s being made out to be. Also, catamarans are known to not “sail around on anchor” as much as mono hulls which makes up most of the snatch loads. Your point #6 sounds much more plausible or even what Sjur “the welder” had said below about the importance of quality welds. A weak or cracked weld would significantly reduce the strength of the shank.
The SPADE is a great “design” and has many happy and dedicated owners. The “design” is not the issue which leads me to why I can’t buy a SPADE. They have known quality control issues and they don’t seem to care. There are other choices of similar “design” that, in my opinion, the SPADE is falling behind.
Other than the catastrophic loss of your anchor, I am happy that it wasn’t more serious.
Hi Peter,
I never said it was seriously short scope, what I wrote was that it’s seriously short rode, which 60-feet is. Two very different things.
And I agree, that Spade need to address their quality control problems and I have been beating on them for years about it.
However, given that we only have one report, I think it’s a mistake to extrapolate to the point of assuming this was caused by a QC problem. We just can’t know that.
As to others catching up with the Spade design, I agree, but it still had a lead in some areas.
More on all of that in Part 2.
Hi Gavin,
in 2) you wrote: “Whether you include the meter height from the water to the bow cleat is unknown to me, but I routinely do out of habit in the interest of redundancy.”
When calculating the ratio, the height of the bow roller above the water must of course also be taken into account.
In other words, the water depth alone is completely irrelevant, only the height of the bow roller above the anchor counts and determines the angle of the tensioned chain to the bottom.
Have you really measured the height of the bow cleat above the water? 1 m above the water on a 46-foot catamaran seems pretty low to me, I would rather estimate 2 m.
Hi Dieter,
I agree, although I don’t think that in this case this was a contributor to the anchor bending, but I could easily be wrong.
Gavin again…
7) I very much enjoy this site. But I must say that I have met very many experienced sailors who have never heard of Morgan’s Cloud, John Harries, or Attainable Adventure Cruising. So, again without aggression, I think the assumption that any and all reports of a SPADE failure would make it back to you are at the very least questionable. So how many events have happened really? We could ask SPADE, but I elect some grains of salt might be required there also?
Hi Gavin,
I never said that any and all reports of Spade failure would make their way to AAC.
What I said was that if there were a lot of failures it’s extremely unlikely that a bunch of them would not have been reported here. A very different statement. I stick by that.
And I agree, asking a vendor is probably not the best source of data.
My 2 cents as a welder and blacksmith (and a great deal of material science with iron/steel materials) this migth be down to fabricator error. Not preparing the weld grooves correctly and grinding the welds back to far. I seems to me that a fabrication error migth be to blame, watching the pictures of the split shank. Not to be offensive. But the spade shank is not its strongest point. It is a great way to save weight and still keep a great deal of strength. But twisting motion on a triangular section combined with bad weld penetration would be a recipe for disaster here. I still like the spade. And the spade consept.
But this could be down to freshman on the job. And this kind of mistake can be hard to spot with out xray or ultrasound. So if they inspect visualy. I think its a likely culprit. Weakening over time before it finaly gives. Kind regards Sjur
This seems likely.
I’m going to be *very* non-committal in my assessments of this one. I don’t see any clear flaws in Eric’s analysis, or in John’s. But some of the necessary evidence for a high-certainty verdict is buried under that sand, and the rest is in the microstructure of the failed seam, which needs a microscope — not a phone camera — to analyze.
It is always possible to break anything that humans have made. Always. No exceptions.
Was the Spade shank designed to withstand the torsion moment at the fluke/shank joint that is created when the pull is at 90°, the fluke is firmly wedged between rocks or corals, and the rode is loaded to near its breaking strength…. without yielding? Probably not.
The location and mode of the failure in the photos is exactly what I would expect from an anchor of this design when overloaded in that fashion, if we assume one slight imperfection in the shank seam welds — the kind of imperfection that would never show up without X-ray or LDD imaging.
Maybe, if the weld were perfect in every way, it might have held a little bit longer. But that’s not an assumption that we ever make in design, QC, or operations.
And, if I’m reading correctly, the failure led to a dragging situation, and the boat was not lost. Not a total breakaway with the boat being blown aground with no time to react. Is that correct? If so, then that is exactly what we want to happen when such a failure occurs.
Hi Matt,
Good analysis thanks. As you say, without very sophisticated analysis we are never going to know exactly what happened. And I agree that in all probability no Spade (or any other anchor) is made perfectly with welds that would satisfy say aviation level quality. Neither is anything else on out boats, as you know so well.
As to dragging, I gather that the boat did drag immediately after the anchor failed and quickly. To me this is definitely a negative trade off with the Spade design, but on the other hand, assuming that the Spade stock takes twice the force to bend that’s required to bend most anchors, as Mantus say, that’s also a benefit. I’m going to explore this more in Part 2.
Anyway, all this uncertainty, which is so common in the yachting world, is why we always tend to come back to experience, and the prevalence, or not, of antidotal reports, and there the Spade does well.
Given Gavin’s investigation of the burial plot with the result that he found no solid object, here is something for an engineer to calculate:
The lever arm of the shank, combined with the large fluke area fully buried in tightly packed sand, with the rode at perhaps 90 degrees off axis… is there a possible wind/wave/current combination shock loading that could induce a shank bend before the fluke could overcome the resistance of the medium, or the snubber could break, or the bow could give up its hardware?
Perhaps this failure could occur with or without a weld defect in the shank. After all, the superlative holding power of these sorts of anchors does reduce the shock load forgiveness that often prevents damage to older generations of ground tackle (even if that drag might be undesired for other reasons).
Perhaps an engineer would be willing to lay out the equations involved, so we can know what configurations (e.g.: the specific resistance of packed wet sand) would produce this result. Respectfully, I say this because I feel like we are speculating on the basis of anecdotes and truisms more than calculations and controlled trials.
Finally, has the possibility of a contrary countercurrent on the bottom been considered? Such might be demonstrated to add significantly to the resistance of the sand bottom. I imagine that it is much easier to bend a narrow profile shank into a strong countercurrent than it is to lift a large fluke area through sand that is being packed and pressed down by that same countercurrent; such a force -if such had been present, even momentarily- might possibly have been sufficient to counter the beneficial stretch of the snubber, thus allowing a shock load the ability to transfer to the anchor shank before the snubber could sufficiently absorb the force. But no doubt an engineer could sort that out.
Hi Steven,
Gavin’s sea bottom investigation, as can be seen in the videos, was surface only. As I say in the article it’s quite common to have a layer of sand over rock. Also, if you read up though the thread and the article, two engineers (Eric and Matt) have already opined that they don’t think an anchor would get bent like that in sand. And my long term experience out there would say the same.
As to older versions dragging instead of bending, I have seen several bent old style anchors. My thinking is that anchors get bent when they get stuck under or between rocks, so this is a situation where holding is not relevant.
As to precise mathematical modelling, sure that would be nice but I don’t think it’s practical without a huge budget and I’m not sure it would tell as a lot more than the opinions of two well informed engineers that we already have.
Your faith in engineering math might be a bit misplaced.
We can do what you describe, but it’s not going to be with nice analytic equations that can be solved in minutes. Rather, it’ll be a long systematic series of finite-element structural analysis simulations coupled with several different soil mechanics codes, repeated over a broad range of load and seabed conditions. Think hundreds of hours of labour and of compute time, over a period of months.
Scenarios like this are why we use a safety factor (i.e. “factor of ignorance”) of something like 3.0 or more, rather than trying to accurately calculate every possible situation.
Hi Matt,
Thanks, I wanted to write something like that, but figured you or Eric would do way better. Your comment proves that.
Hi Sjur,
I agree, definitely a possibility, as I write in the above, I’m just not sure it’s the most likely given that we are not getting more reports and that any anchor, even one perfectly welded, could fail when jammed sideways.
Everyone is always looking for that magic bullet. Or shall a say that anchor that is bullet proof and will hold in all types of bottoms and all weather. Well NEWS FLASH there is no substitute for proper set proper scope and anticipation of conditions. There is no one anchor that will hold in all situations. Sometimes a second storm anchor is required or you may need to simply abandon that anchorage because the bottom just wont hold with your primary anchor combined with the type of bottom make up and wind and tide conditions and the predicted winds.
Just about any anchor design if sized correctly for the boat and set properly will work some designs better in different bottom types then others but strength wise if not undersized and inspected for corrosion and damage they should serve you fine.
ya shit happens BUT shit can be avoided a great anchorage in normal conditions may be a nightmare when things kick up maybe search your charts look for more sheltered anchorage based on the predicted winds.
I made the mistake once when I anchored up in my normal anchorage after a days sail set my anchor based on the current conditions and wind direction and tide level and didn’t check the wind forecast for the next few days or note that it was king tide that week end. (Mantus anchor one size larger then recommended all chain rode with nylon snubber.)
Got a call the next day when I was on my way to have dinner with friends that my boat was heading toward the main channel and moving fast. Well turned out the normal easterly wind was replaced by a storm front from the west at 30kts with 40kts gusts. Combine that with a king tide 3-4 ft above normal and the results were a lack of scope for the higher tide shock loads on my short snubber and deeper water just east of where I was anchored. The result was My anchor turned dragged into deeper water and couldnt reset until it hit the shallower water on the other side of the main channel.
In the end I was VERY LUCKY the only damage was I was late for my dinner date with friends because I had to jump on my dingy race out get on my boat bring up the anchor (that had set on the other side of the ICW channel) bring the boat around the leeward of a spoil island and tied up to a friends dock. (same friend who gave me a call)
since then I pay much more attention to NOT expect that because I have enough scope NOW based on current conditions and my anchor is set well for current bottom and tide conditions to expect that setup to hold without checking weather and tide forecasts for the next few days based on how long I will be there. If wind or tide or current predictions show a change in direction or wind speed I look how will that effect my situation. Does the bottom shallow or get deeper should I drag? should I pick another more sheltered anchorage. Should I put out extra scope or longer snubber to handle the shock loads.
simply put NO anchor is going to hold if you make a mistake and anchor in the wrong place for future conditions. Before the Rocna and Mantus and the spade was the CQR and the Bruce. And fisherman’s anchor and Danforth they all would hold and they all would drag. but many a sailor anchored reliably with all of them if they knew their ground tackle and its limitations sized it appropriately. And selected their anchorage carefully and with knowledge of conditions and expected future conditions.
Hi Michael,
I agree with most of that, but I don’t think it applies in this case.
The wind was offshore and there was no swell in the inlet that Gavin had selected.
That said, the whole scope thing is interesting in this case. Gavin’s scope was indeed correct for the water depth at about 6:1 when measured against generally accepted norms, but what I’m thinking is that maybe those norms are wrong in shallow water. More in Part 2.
Hi John and all,
It is my take that anchoring shallow demands greater scope than anchoring deep. I try to always, in overnight anchoring, anchor to be ok in a F7, Near Gale, at least in the gusts, if a squall rolls through. To that end, I habitually am up to 10-1 in shallows (8-12 feet) and feel fairly comfortable with 3-1 (or a bit more) in 80-100 feet. Part of this is my experience that the seabed is much more predictable and accommodating at deeper depths than it is in the shallows (no evidence for this, just my experience). Similarly, I often will anchor in 30-40 feet rather than sneak in to the shallower areas closer to shore. For one thing, the sun does not get to deeper depths and weeds are less of a problem.
Random Thoughts, Dick Stevenson, s/v Alchemy
Hi Dick,
I agree on all your points.
I’d like to see Spade weigh in on this. And have Gavin send the anchor for analysis.
Hi Robert,
Sure, that would be great, but I doubt it will happen. In my experience most manufactures just circle the wagons and stay quite after something like this.
I’m not a metallurgist or an engineer but I have TIG welded mountain bike frames and car parts out of 4130 chromoly and related but higher strength specialty steels. When we were designing joints and testing different welding rods and techniques, we made and destroyed a lot of tubular Ts, one tube mitered and welded to the side of the other. If the weld zone was properly prepared, and the tubes were back-purged, we were never able to break a weld. The tubes would always come apart somewhere else. Often this was near the weld, within the heat affected zone, but not always. What I learned from researching the metallurgy of welds and trying to select the right rods and techniques at that time, was that it’s extremely complex, there are a lot of variables, and a lot of very detailed quality control that needs to go into those welds. I would be very curious as to what standard their engineering and QC is held to in their manufacturing department.
Hi Matthew,
I agree that it would be great to know more about Spade’s process, but I’m pretty sure that’s never going to happen, even though I have often encouraged them to talk more about this stuff. The bottom line is that openness is just not common in the marine business. Sad, but reality. That said, Mantus are better in this regard than many, which does them credit.
Hi Gavin and All,
There seems to be some confusion about what I wrote about the length of Gavin’s rode:
After reflecting on this overnight I have changed it to:
Gavin — could you please provide a photograph of the other side of the stock? I would specifically like to see what it looks like at the junction with the lower portion of the anchor from the side toward which the stock twisted. Could you also please confirm whether or not you had ever had the anchor re-galvanized?
John — I have a S160 of the same vintage as Gavin’s that has been similarly used and which has also lost nearly all of its galvanizing. It has performed well to date. I’ve considered re-galvanizing it, but am also wondering if it is simply better to replace it. I already carry a spare S140 on my Boreal 47. Perhaps you will address this scenario in part 2 while thinking about the life span of a modern yacht anchor.
Jonathan, i have given all the photos and video to John. I am not sure the view you want is available? Maybe in one of the videos. I have no way to share more of them through these comments though due to their size. I had scheduled regalvanizing of the anchor at a metal shop in New Zealand which was due to happen about a month from now. So no, never regalvanized at the time of failure. I am cruising with a Boreal 47 and they were with me in the anchorage:)
Hi Jonathan,
Yes, will definitely dig into that in Part 2. Probably one of the most important things I learned from this.
Hi Jonathan,
Good question on whether the anchor had been re-galvanized. Definitely got me thinking.
While I don’t personally feel rode length was the primary issue here, I can offer a little more of my experience anchoring extensively in shallow water, in case it’s relevant to future articles or expert opinion. These are just my observations offered humbly.
1) It seems to me that the caternary effect in shallow water is less. Anchoring in deep water involves lots of chain being elevated off the bottom a significant height and the “lifting” begins early in boat movement. But in shallow water the boat moves to almost the full extent of the scope before coming tight enough to lift chain, and then the lift height is minimal. So
I experience less “caternary snubbing” in shallow water and I think nylon snubbing has been more important for me with shorter rode. With 100m of chain out in deep water the nylon seems less involved relatively.
2) When anchored in shallow water, especially in gusty anchorages, the boat moves with the wind quickly. And so when the rode is long in shallow water the boat has more time to accelerate from the gusts before reaching the full extent of the rode. And the consequent greater speed means more momentum, such that my boat experiences MORE sudden halting or jerking with long rode in shallow water. It has been my feeling that lengthening the snubber in shallow water is more helpful than lengthening the rode.
Hi Gavin,
I never said it was the primary issue either. I simply explored it as a possible contributor. I will be expanding on that in Part 2.
My experience with shock loads in relation to water depth has been the exact opposite to yours, but then we have very different boats.
That said, I agree that a good nylon snubber is most important in shallow water.
Hi John,
good job on staying neutral and fair.
going forward, how can we minimize the risk?
the reason I ask , we have a Krogen Express 52 on the way.
the original anchor spec is a 6o# Spade. I asked for a 100# instead and got a little pushback but it may happen. I would think that a bigger anchor would be stronger but if the parts are all proportionally larger then the failure mode may be the same. Bigger spade equals more torque to rotate. Thoughts? My thought was, bigger is better, could I be wrong?
thanks
Carl Linley
Hi Carl,
Thanks for the kind words. I sweated bullets over this one.
Part 2 will be about exactly that, minimizing risk going forward.
That said, I’m pretty sure bigger is better: https://www.morganscloud.com/2019/04/24/specifying-primary-anchor/
Sure more torque to rotate, but the bigger Spades are also stronger, so I think that cancels out. Anyway, I would not reverse upsizing, which has worked well for decades for us and our readers because of one incident.
Compare the scaling laws for stiffness in torsion and bending (which rely on the second moment of cross-sectional area, i.e. an L^4 proportionality) versus those for mass (L^3) and for bending moment applied by a given force (L^1).
Assuming that the 100lb is a perfect linear scale-up by mass of the 60lb, then:
All of its dimensions are 1.19x longer, wider, & thickerIt is 1.67x heavierIt is 1.98x stiffer against bending and twistingThe moments to which it will be subjected in a given situation (eg. wedged firmly in a rock crevasse with a 5 kN rode pull at 90° to the shank) are 1.19x higherThe ratio of stiffness to moments/forces is 1.67x higherPut another way, minus math: In a larger/heavier structure, not only is there more metal to resist the stresses, but those stresses are lower (for any given load) because the geometry is larger and more spread-out.
In other words, the kind of strength we care about here scales linearly with weight. A heavier anchor is ALWAYS better.
Thanks Matt, Great explanation.
I’m reminded of when I consulted an engineer on the thrust plate for my aqua drive that was flexing more that I liked. He did some math and came back saying that going to 1″ plate would solve it. I said, wait, it’s already 3/4″…and got a similar lecture. He was right too.
Update re Anchor Inspection:
I am now at the main yachting center in Fiji. I have just taken the anchor to two high volume metal shops here in Nadi. I cannot provide names, and neither are forensic or insurance-related, and no money changed hands. It was an examination from pure curiosity on both my pay and theirs. The staff have that classic look of men who work with metal all day and they were fascinated by my anchor. And both independantly agreed, for whatever that is worth.
Their opinion was:
1) With confidence they felt that there had been a failure IN the weld of 1 of the 3 seams PRIOR to the ultimate failure.
2) The metal plates of the shank were in good shape with minimal corrosion either internally or externally,
3) Several of the welds that had no evidence of failing had evidence of corrosion EXternally.
4) They were NOT confident in determining if the issue was due to deterioration from use versus a defect from the initial fabrication.
5) They did seem to think the overall fabrication was of high quality but they were not impressed with the galvanization.
Sorry, I forgot to add that they felt the general galvanization of the shank was in relatively good condition. It was only the tip and body of the anchor that showed significant rust.
Hi Gavin,
Thanks for going to all the trouble. Very interesting.
Could you expand on what mechanism or clues the welders used to determine that a weld had failed before the incident, not during?
Matt: if you read this, do you have any thoughts on what the signs would be of prior weld failure and the viability of experienced metal welders determining that by visual inspection?
Also, in a failure of this type on this triangular fabrication, would you expect the weld or the un-welded plate to fail first? As a lay person I would expect the weld would go first, but that’s a totally uninformed opinion.
(For others: Matt is a professional engineer and makes his living designing and supervising the building of very sophisticated laser guided welding machines.)
The Spade shank is a fabricated box-beam structure, with a triangular cross section. It is loaded in a mix of tension, bending, and torsion; the exact mix of loads being dependent on where in the shank you’re looking.
If fabricated perfectly, then neither the plate nor the weld would break. The whole structure would yield in some form of flexural-torsional buckling, resulting in an intact but twisted/crumpled shank pointing in the wrong direction. Further overloading, if the fluke doesn’t drag, would eventually lead to either a tensile failure of the rode, a tensile or shear failure of the shackle, or a tensile failure of the shank.
So, the fact that there is a rip in the metal means that it did not fail quite as designed. We then look at the surface of the torn metal to see what happened.
If the weld didn’t penetrate far enough in the first place, we’ll see failed weld bead (which has a hard-to-describe, but visually distinctive, texture and structure) up to some line, and then the original cut edge of the metal (which will have some mix of galvanization and corrosion) deeper than that.
If the weld penetrated far enough, and a small crack started, and that crack gradually progressed over time and over many load cycles, we’ll see these time steps along the fracture surface. They’ll look progressively older and more corroded as we move from the newest ones back to the original.
if the weld penetrated far enough, but cracked as it cooled, and that crack persisted for some months or years before becoming the initiation site of the major failure in a single overload event, we’ll see two distinct zones along the failure surface. One will be fresh, with the characteristic texture and structure of failed weld bead. The other will be the original crack, which will be somewhat uniformly aged.
Gavin’s description makes the third option sound likely.
There are also things you can discern from examining the microstructure at the failure point about whether a fracture came from a sudden high-strain-rate failure (eg. a truck crashed, therefore the steering linkage got ripped off) versus a failure due to fatigue or progressive crack development (eg. the steering linkage failed, therefore the truck crashed). These can be critical in the kind of forensics that separate “Pilot got confused and flew into mountain” from “Pilot did everything he could to save airplane after tailplane actuator shattered into pieces” and so they have been very well studied for many decades.
Any good, experienced fabricator or metalworker with a few Welding Board tickets in their resume would be able to get these initial assessments correct, most of the time, with a few minutes of visual examination.
Hi Matt,
That’s great, thanks so much. Just the sort of real expertise I was hoping for.
Perhaps this image demonstrates? it is much zoomed in and I do not have a fancy camera. And it felt very much like a beautiful sunset… to look at it was dramatic and impressive, but to photograph it seemed elusive. The area in view would be the top left of the shank (near the junction with the scoop) if it were viewed from deck while on a bow roller.
B) was the area felt to be fresh new damage with clean ‘healthy’ metal that looked pulled apart after the event began.
A) was the area I described with more chronic changes.
Note, in the bottom right of A you see a thin line of shiny clean metal on the surface. This area was what gave the impression that the chronic damage would not have been visible externally prior to the event. But this conclusion about potential visibility prior to the event was less certain.
The phone camera’s AI enhancement has destroyed all the relevant information. But your description and what your metalworkers told you matches perfectly with the failure mode as observed. “A” being a very old, long crack left over from initial fabrication, and “B” being that crack rapidly propagating through the weld when the shank’s side loading became too extreme.
In other words, it looks more like a QC issue than like a design issue.
Hi Gavin,
Thanks, but like Matt, I can’t see much from that. Could you please upload the original at full resolution to the same drop box we used before.
Also, although I know it’s a pain in the neck, given the amount of trouble you have gone to so far over this, I think it would be well worth while to see if you can get some better high resolution photos. Pretty much any digital camera made in the last 10 years will do. Perhaps a friend/fellow cruiser has one?
If so ask them to save the photos, if at all possible, in RAW, not Jpeg and then upload them at full resolution. I have the tools to read most any Raw format. I can then share them with Matt and publish them here in higher resolution than the comments support.
The other option, although not as good, would be an iPhone Pro 13 or later which actually has a pretty good macro mode. Again, we need the files at full resolution.
My motive for pushing you on this is that I don’t want to leave any wiggle room if, as I’m starting to think, this was an original manufacturing error. As long as we don’t have proper photos the whole thing becomes open to interpretation, for example questioning the credentials of the people who opined on it.
John,
The anchor generated a lot of interest and discussion at the metal shops, and I was asking lots of questions using Eric Klem’s original questions to me as a guide. And so my description below is framed by his original questions.
The incident occured almost exactly 1 month ago and the anchor was on my foredeck during that time.
Close examination of the weld seams by these guys showed quite different appearances. Some of the ripped open welds showed no corrosion, just very minimal surface, rust-coloured discolouration. This was presumed to be from exposure of the raw metal to the air for a month. And referencing the photos, these areas were visible and initially looked like shiny new bare metal. But one seam in one section close to the scoop and near the main bend of the shank looked very different… it had significantly more corrosion and some pitting into the metal edge of the plate and the exposed weld. The transition, once pointed out to me was clear even to my eyes and showed corrosion in an area that should have been within the weld itself. It was about 15cm long as a rough estimate. It had a much more chronic look to it. It appeared it would not have been visible from the outside by the naked eye, prior to the major deformation.
There was one area that was possibly a defect from hitting a rock, but could just have easily happened during the ‘big bend’, so that question remains unanswered.
And while the galvanizing of the plates was in good shape both internally and externally, it seemed that the galvanizing was less well stuck to the welds than to the metal plates themselves.
The galvanizing looked smooth they thought, not bumpy.
Gavin
Hi Gavin,
Great fill, thanks. Will definitely help me with Part 2. When you get a moment, could you please upload photos to my dropbox, as detailed as you can get, of the seam that seemed to have failed before as well as the one of the ones that failed after. Sorry for the trouble, but I think this is critical.
Hi Gavin, I have to commend you for a number of steps you took that are over and above what the average cruiser would take such as searching the anchor trail for rocks or bommies by snorkel after the failure. We have cruised Fiji for four seasons and the top end of the Yasawas is significantly more exposed to the SE trades than the southern portion. Your anchorage was on the Leeward (West side) of the group and the wind comes over the top and down the valleys leading to catabatic blasts – just the sort of conditions that you need to have full confidence in your ground tackle.
The Spade lovers have, in my humble opinion, been a bit too quick to explain your bent shaft by theorizing there was a buried rock. If I were the owner of Spade anchors I would pay you for a replacement anchor and pay the full cost of shipping your anchor back to them. This is a valuable real world learning opportunity for them that could possibly lead to a modification in design, construction techniques and/or welding quality control that would make future anchors even better. That opportunity will only be realized if they are open minded and not defensive.
Incidentally although you had nerely 7 : 1 scope a sudden lurch of the bow from a gust is quickly transmitted to the anchor. In shallow water situations such as the SE lagoon at Fulaga we typically go with a minimum of about 100 feet of 3/8 (10mm) chain. This is not from any text book but I believe helps lessen veering forces on the anchor. This is not meant as criticism but as a constructive suggestion since I know you Cats love getting closer to the beach than us poor monihulls could possibly consider.
Good Luck from Martin Minshall SV Katie M II
Hi Martin,
Spade did offer Gavin a new anchor, as I understand it quite early on in this saga. Not sure if they offered to pay the shipping. That’s not normal in a warranty situation.
Interesting discussion, especially for a metalworker. I’m very glad no one was injured and the boat stayed safe. We have a 2 year old spade S160 which I just this week painted with ZRC zinc rich coating in an effort to stave off the rusting on the tip. I have used this coating very successfully in the past in non-marine applications, both with and without a topcoat.
Allowing rust to completely engulf any piece of steelwork is an invitation for trouble.Pitting from corrosion can set up micro-fracture stress points from the tiny acute angles produced in the structure of the base metal or the weld. While I’m sure my coating of ZRC will be temporary, I know that it does have very high abrasion qualities, so am hopeful that a maintenance coat will only be required every 3 months or so (we cruise full time, so anchor 99% of the time). Another coating option recommended by Peter Smith on his KiwiRoa is inorganic zinc silicate. The prep work is more involved, but it has great potential as well. Time will tell how it holds up.
Brian on Helacious
Currently in the Chesapeake waiting for a weather window …
Hi Brian,
There have been a bunch of efforts to paint rusty anchors over the years, and unfortunately none of them seem to last long, at least around the tip that takes so much abrasion. I have simply never worried about the rust in that area. That said, I think you are right that bad rusting on the stock is a matter of concern because of the potential stress concentrations. The good news is that even quite old Spade anchors don’t seem to rust badly in that area.
Hi Brian,
I recently tried a solder repair to an area of missing galvanizing on our anchor. I am a hobby level metalworker and I have to say that I really found it challenging to do well and I never felt like I did a good job, I doubt that I have actually increased the anchor longevity. I learned about it from a video from Mantus (https://www.youtube.com/watch?v=2Kan2Pfj61k) and I have to say that their video didn’t look very inspiring but I figured I would try it and see if I could do better. For one, I don’t think you can get enough heat with the type of torch they used at least for a bigger anchor, I had to use a propane rosebud for the initial heating. Maybe someone like you with professional metalworking experience could do a better job. This wouldn’t be a fix for an inaccessible place but on anchors with no hollow areas, it may be an option for the right people.
Eric
Hi John,
Interesting, I had incorrectly thought Octoplait was nylon so had discounted the possibility of the bend happening due to boat forces alone as the reported conditions were not that strong. If a less stretchy snubber were indeed used in such a shallow anchorage and the anchor got held sideways, I suppose it would be possible to cause a failure in those conditions to an otherwise good anchor. Given Gavin’s comment that it was actually nylon, it seems that this as the sole cause is quite unlikely. I see some discussion of whether a stiff anchor shank would be more likely to cause problems in a few comments and my general feeling on that is that we should rely on the rode for shock mitigation and not the anchor, the anchor is not an efficient place to do that. The loads throughout the rode are pretty close to constant even in a dynamic situation as the only things that can change the load are mass effects (gravity and inertia) which are not big at the accelerations and loads we have so it isn’t super important where in the rode the spring is.
As Matt mentions above, to get a truly definitive answer requires a knowledgeable eye on a microscope but I think the recent comments about a potential flaw in the weld are going down a likely path. If the anchor were a part of a formal investigation, they would use special cutting tools which don’t destroy the evidence to take sample cross sections for microscope analysis of the weld region and to determine what alloys were actually used.
It strikes me that this shank design has a couple of things specific to it from a design side to be considered. The first is simply that there are very long welds. I assume that they have to do some form of skip welding on it while fixtured to keep the shanks straight which means lots of starting and stopping and room for flaws. Given the volume of anchors sold, I would guess that this is being manually welded which becomes very operator dependent, not everyone can be a good welder and Matt has covered some likely failure modes. Also, welding is tricky to inspect, I would expect/hope that they do some form of x-ray inspection of which there are standards to use but this is typically only done on a statistical sampling basis so most parts are not inspected and even the ones that are may be allowed to pass with some defects (I don’t think any cracks are allowed in any standards). For anyone curious about welding standards and inspection, I know that at least AWS D1.1 is available for free online and I suspect some others may be too.
Once the weld is complete, you then have a backside of the weld that is inaccessible for mechanical prep for galvanizing and depending on the penetration, it may be a very uneven surface. Welds definitely have more potential for corrosion than just galvanized plate and a small pin-hole can be a big deal over time. I was struggling to figure out exactly what the cause was before the most recent exchanges in the comments and I had been thinking that some form of corrosion into the weld seemed the most likely followed by a manufacturing issue although I now think that is flipped.
I am certainly not anti-welding, I just think that there are trade-offs that must be weighed. All of us rely on welds on a daily basis in cars, in buildings, etc. and thanks to welder certifications, inspection standards, design rules, good equipment and a few other things, welds generally work well. Whether weldments make sense are a function of application, for example the stuff that I design is much more suited to processes like machining, casting (struggling with 1 green sand casting that keeps cracking on core knockout right now), forgings, etc.
Eric
Hi Eric,
Thanks for a well balanced analysis, as usual, that will be very helpful to me as I write part 2.
Greetings, everyone.
A few thoughts that may or may not have relevance to Gavin’s anchor failure:
1) As has already been said here, predicting the strength of the Spade shank is extremely difficult, especially given the variability of the welds. Another factor that needs to be considered, is to extent does the welding process DESTROY the heat treatment (strength) of the parent metal.
2) I have always had a strong feeling that the prediction made by Mantus, that the Spade shank is “2X stronger” was being, ahem, a little generous.
3) Regarding the high relative stiffness of the Spade shank: I once attempted to straighten a 45lb Rocna shank (that had been mis-aligned by the factory). Toward the end of my failed efforts, a “cheater bar” that was over 20 feet long was been used. The shank was deflecting several inches, but the damn thing would not yield. It was behaving just like a leaf spring on a car. I believe that (side loaded) “springiness” of a shank provides the same sort of benefit that a snubber (or catenary) provides: It lowers the peak load of a dynamic event.
3) During my crazy, high speed reset testing, I have bent the shanks of deeply buried ALUMINUM and STAINLESS STEEL anchors (never galvanized) that were NOT contacting anything but sandy mud. In these cases, the anchors rotated or released from the seabed, but apparently they did not rotate fast enough to prevent the shank bend. I feel that there is at least some possibility that Gavin’s anchor was NOT contacting rock or some other immobile object.
Steve
Hi Steve,
Thanks for coming up on this, always great to get your view on these things.
Hi Steve,
I was thinking of that great video of you with the Rocna anchor shank when reading John’s article yesterday. It did a great job of showing just how strong they actually are. While they can be bent, it takes strong storm conditions assuming a good rode and it takes an anchor stuck at the wrong angle.
It is definitely possible that Mantus’ FEA model of the Spade shank isn’t super accurate. FEA is a tool that is very easy to get pretty pictures out of but takes skill to get really actionable results out of and not everyone has that skill, I don’t know whether the team at Mantus do or not for a weldment. The pictures make it look like they are using Solidworks Simulation which is fine but not one of the really high end FEA packages (this is a comparatively simple linear analysis so you don’t need one of those). One of the tricks with it is that the auto mesh generator gives a very poor mesh for high aspect ratio cross sections such as weldments and if they didn’t use a good rule of thumb or convergence analysis, the results might be way off for stress. One thing that I note is that they appear to have a fixed boundary condition at the bottom of the shank which on the Spade is not fair, you have a shank in a slot which has point loading. I assume they just were not worried about the stress around the attachment area and since the failure for Gavin was not in that area, it isn’t a huge deal right now but that area of the model should not be considered accurate. Also, it is possible that they simply treated the shank as a simple single piece of metal that was magically made, handling weld areas is trickier and takes a lot more skill/time that they probably didn’t want to put in. Even with all of these potential issues (they may have had the skill and time to mitigate them I don’t know), I suspect that a well manufactured Spade shank is still very strong and probably stronger than most or all others.
I don’t know if you or anyone else knows whether Spade does any post welding heat treating? That certainly would have a big impact on the material properties. I also suspect that they would struggle to keep the shanks straight during it without a lot of process control. Heat treatment of welds is a whole subject in itself with lots to digest and not always intuitive trade-offs.
Eric
Hi Eric,
I agree that the Mantus study is far from definitive:
Anyway, good to have your thoughts that the Spade stock is strong, and probably stronger than most, as designed, I think that’s all that really matters for our purposes here, and is also about as good as it gets with most boat gear.
Steve,
Firstly, I am in awe of your work! Thank you so much.
Second, if you would consider it, I would love to contact you outside this comment stream. Please feel free to message me at my email, but I understand completely if you prefer not to.
Hi all,
First, this quality of this type of discussion can only be found here. Thanks John and Phyllis for making this possible!
I find all comments here interesting and well thought out. I agree that the “weld cracked during production, promoting weld corrosion while in use” theory seems credible. I don’t think a hard object was necessary. I also agree that the SPADE reliance on weld quality and durability is not ideal. Then comes the stiffness / non springiness issue that Steve explained better than my try earlier.
The SPADE thus, has a construction that is very strong, but
– More vulnerable to misaligned shock loads, because of potential weld weaknesses.
– While the same stiffness means exactly the misaligned shock loads will be much harder than with springy shanks.
While I’m convinced the SPADE shank is indeed able to take much higher static loads, in any direction, than any other anchor I know of, this combination does seem to reduce its strength advantage.
Still, “the proof is in the pudding.” The SPADE actually doesn’t fail this way often enough to matter. It did matter seriously to Gavin when it happened to him, of course, but I still feel that an oversize SPADE is my favourite anchor, for its overall predictability and the absence of a roll bar. (I have no solid reason, but roll bars just seem wrong to me.)
My current anchor is a Delta, came with the boat, which sets ok but holds about as well as a rubber duck. Plows are for, well, plowing, not staying put. Thus, no confirmation bias. A new anchor is in my near future. I don’t yet know which one, but my bet is the mentioned oversize SPADE, combined with some situational awareness gained here.
Hi Stein,
You just wrote part 2 for me! …OK, I will add a bit more:
I just now remembered (and located) an email conversation that I had with Rex Francis (the man behind the Anchor Right anchors) that we had several years ago. Here is an excerpt of one of Rex’s messages:
“As to the spade anchor, and they are excellent, the other real thing to watch re your comment on rust, is when re galvanizing, throw away the old shank and replace it with a new one, we twisted two of the spade base when we were doing holding power comparisons years ago, problem with a hollow gal shank it rusts inside like you would not believe, you can regal them but it will not take to the rust and shale that the acid simply cannot remove, the spade anchors we were using looked fine until they collapsed under the large loads we were applying, the inside of the shanks in some places were like eggshell, quite amazing they actually took the loads we were applying without folding –twisting . Keeping in mind these test anchors were second hand.”
Hi Steve
Interesting, but I’m always sceptical when it’s one anchor manufacturer talking about another anchor, particularly when they use dramatic language like “rusts like crazy” and “eggshell”.
Let’s not lose sight of the fact that this is the first stock bend report on a steel Spade (other than a small bend under huge load) that we have ever had on anchor that has been around for over twenty years. In my view the real world trumps accusations from other vendors.
Also, Gavin and the welders both said that there was little rust on shank, inside or outside, and this on an Spade that has been used for 6 years over 300 days a year.
Hi John,
For sure, the Spade’s track record is fantastic. I don’t mean to steer people away from the anchor.
And yes, severe corrosion is not an issue with Gavin’s anchor.
I probably should not have brought that up in this discussion.
Steve
I notice that in the BoatUS photo of the Danforth T-4000 being pulled from its normal shank attachment point while at the same time being restrained only at its fluke tips, the shank bends with the shank turning to the side. Could it be that the Spade anchor shank also bends to the side giving the mistake impression that fluke was restrained from rotation and the shank was subjected to a side load?
https://www.boatus.org/findings/05/
Hi William,
If you look at the straight section of anchor shank on most anchors, they are strongest in the direction of pull in line with the shank but in the 2 directions perpendicular to that, vertical is significantly stronger than horizontal. It gets a bit more complicated when you consider that there is a section of shank that bends down to connect to the fluke but most anchor manufactures vary the cross section to keep the relationship true. I suspect that a major reason you see shanks that are taller than they are wide is simply that it increases the anchors performance as the shank doesn’t prevent burying as much when constructed like this even though it may not be the best strength to weight option. I am not totally sure what the ratio of side loading to max vertical loading during breakout is but since strength is proportional to the square of the dimensions, I am confident that the loads are not different enough to justify the cross sections (it also ignores loading in other directions that could twist up the shank).
When you get a section that is tall and thin and you load it in bending with a vertical load, it is very likely to twist up as you see in those pictures. It would take a really perfectly aligned test setup to keep it failing straight, once stuff is yielding and the loads are not quite perfectly aligned, one side will yield a bit more and then the process will accelerate as it comes out of straight.
So yes, you could get a failure that leaves a twisted shank from a vertical load on the anchor. However, the final shape of the shank would likely point up much more than the photos show. Also, I think it is unlikely to be loaded in this way in the conditions Gavin describes. I have thought a bunch about whether there could be prior damage due to breaking a stuck anchor out in the type of loading you are asking about. I have concluded that it is unlikely to be the case as getting damage that would cause as large a crack as the latest pictures show but doesn’t deform the shank enough to be very obvious is quite unlikely, it would really be perfect loading.
Eric
A big thank you to all those involved in this article and its discussion!
For myself, I feel happy that through this forum (and other means) I have “gotten to the bottom of things”. Each of us can conclude as we wish. For me, the bottom line is that a weld defect in the shank coupled with dramatic shock loads at a 90 deg angle resulted in catastrophic failure under circumstances where a galvanized SPADE withOUT weld defect should/would possibly not have. I also feel, based on my up close examination with the metal shop guys, that visual inspection of the anchor would not have identified the issue. And I translate that into likely future inability for a layperson to visually inspect their anchor for issues of this nature. Whether this represents manufacture defect versus consequence of previous use/damage is beyond my pay grade.
I love Practical Sailor magazine/website, and so I disclose that in advance.
I found these two articles from 10 years ago, the content of which I am certain will be of interest to anyone reading this comment stream. (Possibly especially Eric and Matt who have the highest chance of fully understanding them;)
https://www.practical-sailor.com/sails-rigging-deckgear/anchor-tests-bending-more-shanks
https://www.practical-sailor.com/sails-rigging-deckgear/anchoring-mooring/bends-and-breaks-anchor-shank-strength
In the figures of one article is the discussion of warranty and the author states: “Fortress and SPADE both indicated that they replace shanks, but they have not replaced many. The alloy and stainless Spade have higher replacement numbers than the galvanized steel model”. Obviously, the circumstances are unknown and the type of damage unknown, but remember that this article was written 10 yrs ago. It seems mine is not the first damaged Spade shank, even of the galvanized steel model. Again, the details of other damaged galvanized spade shanks are clearly unknown, but certainly not unheard of even 10 years ago. And seemingly confirmed by SPADE themselves.
Matt Marsh has stated here in this comment stream that: “Any good, experienced fabricator or metalworker with a few Welding Board tickets in their resume would be able to get these initial assessments correct, most of the time, with a few minutes of visual examination.”
I have taken the anchor to two metal shops who had zero interests in the outcome, one of which maintains a fleet of steel supply ships. Both came to the same conclusion and quickly… a weld defect demonstrating chronic corrosion within. I feel this in-person examination is both impartial and exceeds what could be further concluded by an elsewhere expert via photos, no matter the photo quality. Also, my past days as a general surgeon in the USA and Canada leave me inclined to avoid litigation or conflict. And so in spite of John’s request for quality images (which I admit to having in my possession) , I feel personally inclined not to share further images.
I have also not disclosed details of my discussions with SPADE USA, SPADE UK, or Seatech and Fun as I feel these are private and would require their permission. But each have weighed in early in this process I can assure readers. And interestingly, each with quite different opinions.
SPADE Seatech and Fun have sent me a copy of their warranty document. Two of the points of note are: that galvanizing must be kept in good condition, and that damage by deformation or bending are not covered. See attached screenshot of the warranty. Take that as you will in terms of what it means.
In terms of my love for Practical Sailor, one of my favorite sections was “Credit where credit is due”. Some of you may know of it, but for those who don’t, it’s the section where manufacturers behave on a way of exemplary honour/integrity.
In light of that, I do feel it is ok and fair to share that Seatech and Fun have offered to replace the anchor. The replacement offer came immediately upon hearing from me and without request on my part.
Anchors are chunks of metal, but we forge a relationship with them that feels more like religion or marriage. And faith in one’s anchor has a big part to play in this relationship. And indeed in our sleep and contentment to leave an anchored boat.
If your wife were to dance a little closely with the neighbor then that’s one thing. But this catastrophic failure is more ‘analogically akin’ to a full weekend affair. Perhaps you could convince yourself it was a solitary incident in 20 years because you had heard of no others. And quite reasonably it could be the right thing to hold steady on vows and carry on.
But for others it might be time for a change.
And that’s a very personal decision.
Hi Gavin
I can see no logical reason that you are refusing to share those high resolution images.
Unfortunate, since that will always raise the question: Why is Gavin not sharing the photos?….
John,
I have explained my reasons for not sharing further photos in my comment: 1) I feel Matt’s comments make it clear that an impartial assessment by the metal workers here is trustworthy, 2) I feel their in-person assessment can arguably be better than someone using photos. 3) I have been advised by legal counsel that it might be best to keep them to myself, 4) My intention was to get to the bottom of things and convincing anyone who thus far is not, as never my intention.
If you find that illogical I respect your opinon. If anyone chooses to question my honesty or integrity, I can assure you I will lose no sleep.
Hi Gavin,
All I know is that at first you were all over sending me videos and photos, I have a large file. Now suddenly you won’t share the ones that really matter. You reasons make no sense to me.
As to the opinions of the welders. Please advise the names and town of the two companies they work for.
John,
I remain attentive for your thoughts on the remainder of my summary comment.
Hi Gavin,
Your refusal to share the photos makes the rest of your comment irrelevant in my view.
Hi Gavin,
One thing I will add is that I’m disappointed in you for withholding the fact that Spade had offered you a new anchor at no charge. That was important information that we should all have known up front. The fact you chose not to tell us something that put Spade anchor in a positive light makes the whole thing feel to me like a vendetta, not a rational attempt to get to the bottom of what happened. It also makes me wonder what else you did not tell us.
Gavin, I haven’t logged into this Web site in some time so I’m just seeing this discussion on your bent anchor. If you do feel a need to examine the cause of the anchor failing I’d be happy to help. I’m a forensic metallurgist with a long history working in this field.
Given the length of time between when the event happened, where the anchor has been and the subsequent examinations that have taken place, if you are looking at legal recourse (you mention in a comment you were advised not to share photos for legal reasons) you may have a difficult time achieving a satisfactory result.
In any case, if you are interested some other opinions on your anchor failure I would be happy to help.
dj
Hi David,
I would love to see a report from you on that anchor. We might even be able to organize a gofundme campaign to finance the shipping and your time. Of course I would need to independently verify your credentials so we could put that on the gofundme page so people know what they are paying for. I would kick that off with a contribution.
That said, I sincerely hope Gavin is not going take legal action against Spade. This is a company with a great track record over nearly a quarter of a century, not some mendacious, faceless corporation, so doing that to them over one failure where they offered to replace the anchor on warrantee would be, I think, unreasonable. If we start that, we will be taking legal action again just about every company in the marine business and there is only one group of people who win when that starts. And the rest of us will be paying for it in increased liability insurance costs incorporated into the price of marine gear.
Also, although I have no legal expertise I would have thought that Spade’s liability would be limited to replacing the anchor, which they already offered to do, particularly since no one was hurt and the boat not damaged.
I don’t know the sea state or motion of the boat, or the history of the anchor, but there are a few things I can extrapolate from testing.
Force. Gusting to 33 knots, the maximum straight line tension would be about 900 pounds with a good snubber. This varies a lot, because it depends on whether the gust hits exactly when the rode starts to tighten. But based on a lot of time with a load cell, that is the probable max over a period of hours. With a poor snubber (polyester–yup, tested that) this is probably closer to 1400 pounds. It’s a big boat with a lot of windage.
Yawing. Hard to say much without direct measurements, but in similar conditions, the load is typically 1.4 to 1.8 times greater. Again, it depends on when the gust hits. Let’s say 2100 pounds.
PS test bent a 22-pound Rocna an got 500 pounds. I have no knowledge of how strong the Spade shank is in comparison, but strength typically scales with about 1.2x weight with anchors. A guess would be about 2200 pounds for the Spade 160. Pretty close to the predicted maximum side force, so it took a while before just the right combination occurred.
Could sand alone do this? Pivoting fluke anchors have been bent in firm bottoms but I’ve never heard of a Spade or other modern anchor bending that way unless it caught on something or they hit a dock (perhaps the most common cause of bent anchors!). They slowly turn. I’ve set anchors to their holding limit and then veered them 90 degrees. The only one I bent was a Fortress. In it’s defense, it was batting way out of its weight class and is for a different purpose.
Additionally, if the anchor were deep enough to hold that sort of force in sand, there would be 3-5 meters of chain buried with the anchor, which would prevent the anchor from feeling the side tug immediately, such as yawing.
Finally, for the anchor to be set deep enough that the sand or mud could hold it against turning, it would need to have been set with several times that force in a straight line first. He didn’t have the engines for that and the wind had not been that strong. In other words, the anchor had not been over-set and was just holding the peak force. It had been wiggled a lot. It would have turned first.
I’ve seen a few twisted Spades, but no more or less frequent in proportion to use than any other good anchor.
Hi Drew,
Great to have you view and particularly your estimates of the loads involved. Thank you.
I missed the photos the first time I commented. Based on the thin line of clean metal, and following the reasonable comments from the welders and Matt, I have changed my thoughts. Yes, it may have failed without catching on a rock. What is needed, as noted many times, is high resolution photos, taken systematically within a day of the failure. I can’t see much, but as Matt said, it looks more like a weld process error than deterioration alone. That is a challenge with a design that is so dependent on quality welds.
Hi Drew,
Thanks for the full, timely too, given that I’m publishing more on this tomorrow.
Hi John and all,
The recent discussion on the bending of a Spade anchor is, to my way of thinking, another argument for a big anchor on the bow. Manufacturing defects aside, strength has to scale with size and, from my observation, too many skippers shy away from a little extra weight in the bow or from expense (see below)
There was a question a week or two ago with regard to sizing an anchor to which I responded: and then I could not find the original question in order to post my response in the correct place. Hopefully, it will be found here and it also fits this discussion.
Hi ???
I have a 77-pound Spade on a 40-foot boat (fairly heavy displacement), an upgrade from my 66-pound Spade which is in pieces in the bilge as my spare anchor and taking the place of an 80-pound Luke. Part of the decision is dependent on your cruising grounds: remote, deep, no help, problematic bottoms, anchor a lot: all call to me for a heavier anchor. And I believe that 10-20 pounds additional weight put in the anchor pays impressive dividends in keeping the anchor in the seabed. Most of us cruisers will hardly notice the difference in boat motion and/or sailing characteristics (and most of us can shed a few pounds forward to compensate).
As for manufacturers and their anchor choices/suggestions, my observation is that most of them put toy anchors on the bow of their boats: as seen when I visit boat shows. I believe there to be an unwritten proclivity to not put anything on a new boat that might make you think cruising was in any way dangerous: hence toy anchors, no high-water alarms or auditory alarms when a bilge pump is activated, no fire alarms, few handholds, inadequate sea berths, etc.
My best, Dick Stevenson, s/v Alchemy
Hi Dick,
I agree on the benefits of upsizing the anchor and have written at length on that: https://www.morganscloud.com/2019/04/24/specifying-primary-anchor/
For the purposes of this thread it should be remembered that Gavin had indeed upsized his anchor.
Anchors are a compromise, balancing maximum holding and strength against minimum weight while being robust enough to retain these characteristics through years of rough usage. I believe the SPADE anchor’s compromise is fundamentally flawed. It is superb when new but is lacking when it comes to long-term robustness. Maximum tip weight with minimum overall weight requires a relatively thin-walled, hollow shank and lead ballast in the tip. The hollow shank is extremely strong as manufactured but has little margin for corrosion, and corrosion is a serious problem. That hollow shank also has twice the exposed area to corrode and is subject to electrolysis from the lead ballast, which is not encapsulated. The result is that the SPADE has a reduced life, especially in in warm water.
This is not entirely idle speculation. I bought a SPADE anchor in June 2007 and used it as my primary anchor on Iron Bark II for two years in conditions similar to Gavin – the boat continuously in commission and lying to its own gear largely in tropical water with excursions to the high latitudes. Within two years corrosion/electrolysis had weakened the SPADE to the extent that I condemned it.
When the anchor was new the various components appeared to be more than adequately strong, but the corrosion that occurred once the galvanising was worn away by abrasive bottoms, compounded by electrolysis caused by the exposed lead ballast, reduced the thin plate to unsafe dimensions. After two years the winglets (the ‘ears’ in the sides of the fluke) were entirely corroded away and the main fluke plate was noticeably thinned by corrosion. I could see no corrosion on the shank, but of course could not inspect the inside hollow. I decided the whole thing was suspect and discarded the SPADE as untrustworthy.
I replaced it with a Manson Supreme. To get the same tip weight and fluke area I had to go up a size, but regarded that as a small price to pay for having an anchor that was not dependent on galvanising for its integrity. The Supreme is has a solid steel shank of generous proportions and has no lead ballast to cause electrolysis. This compromise reduces its tip weight the fluke area compared to the SPADE, hence the larger size of the Manson Supreme. I used that Manson Supreme for 12 years in a variety of conditions, latitudes, climates and bottom types, from Antarctica to Greenland and the tropics, and had it re-galvanised once. There was a bit of corrosion in the hollow roll bar which I ignored. Unlike a shank failure, if the roll bar collapsed the result was not going to be catastrophic – it will merely make it difficult to set the anchor until you weld it up.
I have since changed boats and changed anchors, the new boat being an Alajuela 38 for which I bought a 33kg Rocna Vulcan. This anchor has also performed reliably in both tropical and polar waters. Again, a SPADE anchor one size smaller would have similar setting ability (tip weight) and holding power (fluke area), but, again, regarded that as insufficient reason to take a risk with an anchor that has little margin for thinning of its components due to corrosion/electrolysis.
Both my solid steel scoop anchors, the Manson Supreme and the Vulcan, have been used on abrasive, tidal bottoms which quickly removed most of the galvanising. The resultant corrosion is unsightly but of little importance -it takes a lot of rusting to significantly weaken their large, thick components. The fact that neither has lead ballast so are not subject to electrolysis, helps too. Both anchors are robust and do not get significantly less so with age and use. These anchors have been subjected to quite extreme abuse without any apparent damage, such as repeatedly overrunning the anchor at full throttle hard enough to stretch the chain in order to tear the anchor free from an obstruction in water too deep or cold for diving.
In summary, I think all anchors are a compromise but the SPADE’s compromises as unacceptable for the sort of voyaging that I do. The SPADE’s shortcomings probably do not matter on a vessel that is only in commission for part of the year and/or confined to cooler waters. For such a vessel, the SPADE’s superior holding is attractive.
By increasing the anchor size a little I have achieved the same level of performance with a more robust anchor that I can inspect and cure any problems before a catastrophic failure occurs.
Hi Trevor,
How great to hear from you again after all this time. Phyllis and I were talking of you just the other day and wondering how you were getting on.
On the Spade, that’s interesting, and obviosly disturbing and also very different from my own experience where, when we sold the McCurdy and Rhodes, we had much, much, more than two years: ten on one and 22 on the other. Sure, they were a bit rusty, but nothing like you describe. I’m at a loss to explain the difference.
We might not have anchored as much as you in a given year, but over the years I’m sure the days at anchor added up to a much larger total, although perhaps not as many in the tropics.
As to trade offs, I do need to point out that testing has shown that the Manson can exhibit the same rapid dragging modality after a 180 degree shift as the Rocna. There is no perfect anchor, as you say.
Good to year that the Vulcan has done well by you. I’m not a roll bar fan, so it’s good have another non roll bar anchor as an option.
Hi John
There are undoubtedly multiple causes for the difference in the corrosion rates of our respective SPADE anchors. Two obvious ones are
A common complaint of the SPADE anchor is that its galvanising is poor. It may be that the rapid corrosion of these anchors is due to rampant electrolysis from the exposed lead ballast in the tip overwhelming the galvanising then getting to work on the main body of the anchor, rather than that the galvanising is of poor quality. Addressing this issue is a matter too complex to be dealt with in a comment , but may be worth further consideration.
Re the failure of the roll bar anchors to reset after a 180° windshift: I have never experienced this problem and wonder how serious it really is. My data set is limited. I set and lay to the roll-bar Manson thousands of times in a wide variety of conditions over an extended period (good, wide data), but in one boat only, using one anchor only (very limited data). Extrapolating from such a narrow data base would be dangerous, but so perhaps is extrapolation from a small sample of artificial tests.
I arrived in New Zealand last week from Europe via the Panama Canal. This is my first excursion into the low latitudes for some years and there have been changes in anchoring techniques amongst the longer-distance temperate and tropical cruising community. Roll bar anchors are by far the most common anchors, and most are properly sized for the vessel. I saw or heard of very few failures to reset after a windshift, which provides an anecdotal-only extension of my data base. Bottom line is that adequately-sized roll bar anchors seem to be fit for purpose.
Hi John,
I am wondering whether it is time to start thinking about buying a new shank and whether Spade will consider some sort of “at cost” (or better) to do this. They were good to me when they gave me a new anchor (10+ years ago) for my quite rusted one and even let me bump up the size with me just paying the difference.
It might be premature for my Spade as this anchor has been in UK waters or north since I got it (and now fresh).
My best, Dick Stevenson, s/v Alchemy
Hi Dick,
Unfortunately, that’s not an option. Spade flukes and shanks are matching and even have serial numbers. More on my thinking on replacement in Part 2
Hi Trevor
I remain a big fan of roll bar anchors, having been one of the first to adopt the Rocna in the UK in the early 2000’s. As a commercial sailor much of the time in the Hebrides I was delighted to at last have an anchor that really performed!
When Louise and I had our Ovni 435 built we specified a Rocna 33 as the bower and our old 25 was kept as the Kedge. We used the 33 for thousands of nights and never had a problem until we dragged badly in severe thunderstorms in the Ilha Grande region of Brazil, on both occasions with 50 knot + gusts from 180 degree shifts at times.
On both occasions we had maximum scope out (all chain), were on deck and got control of the situation, although we got very close (to other boats) at the time.
So, I’m afraid it can happen. After that we took extra care in conditions that might generate such shifts and apart from picking a boulder in the roll bar once, never had a problem again. Apart from those three occasions I never had an issue with the anchor and remain of the opinion that it is an excellent anchor – with that one reservation.
We chose a Spade S100 for our new boat, and, so far so good, are well pleased with it. I have some reservations over the short scope performance, having heard credible reports that it isn’t their best area, but again, will bear that in mind and we have a new second anchor that will be tested and revealed next year.
I think that all of the anchors mentioned have excellent performance ( I also liked the Sarca Excel), After years and years of relative uncertainty with fishermen, Bruce’s and CQR’s etc. I can only say bravo to all of the ‘new generation’ anchors and the people that designed them.
As a Scot I am something of a fatalist and believe that nothing is perfect. What I take away from all of this is the need to make regular inspections of our Spade and take care to touch up the galvanising.
Best wishes
Colin
Hi Colin,
Very good analysis, as always. Particularly good point that no anchor is perfect, but all the modern ones are so much better than those we put up with before.
Hi Trevor,
Good ideas on the difference between our two experiences on Spade.
That said, we spent quite a bit of time anchored in warm water over the years.
On the electrolysis theory, I can see it contributing to rusting at the tip, but have a hard time visulizing current circuits that could affect the stock. Also Spade was sold some years ago, and one of the first things the new owners did, so I understand, is start isolating the lead with epoxy. That said I have no solid data on how effective that has been, also they may only be doing it on the aluminium anchors. I will check on my two new ones.
On the reset failure, it’s pretty well documented. We used to recommend the Rocna, and then after about a year the first report came in from Nick Kats in Ireland. One report? I discounted it. Then it happened to Colin twice, and we started getting more reports, to the point I could bo longer ignore it. And finally Steve over at S/V Panope, developed a video camera technique that clearly shows what happens. It’s a low frequency, but high consequence event.
I heard, although do not know, that even Peter Smith has acknowledge the problem and my guess is that’s a lot of what drove the new Rocna II. I’m hopeful he has fixed it.
More here, including the video: https://www.morganscloud.com/2021/03/22/when-electric-drive-works-for-a-cruising-sailboat/
Hi All,
Lots of interesting thoughts on trade-offs.
Tip weight is an interesting subject that gets a lot of weight by some and is completely discounted by others. I think the reason for this is that tip weight is only part of the equation in getting the tip embedded and I almost never see the other parameters being discussed (okay, I occasionally see discussion of how sharp they are). It would seem that the angle that it is trying to bury at is super important. Not only is this the angle down but the presentation angle of the centerline of the fluke to the angle of pull. If you watch the anchor set and the anchor has a lot of sideways angle and then movement to the direction of pull before digging in, it appears to me that this must be less optimal for setting. I have noted that the ballasted scoop type anchors like Spade, Rocan Vulcan, Mantus M2, etc. tend to have very tall shanks that are not super long and this means that the pull point on the anchor is putting a significant sideways pull on the fluke when it is in the setting position and not just forward. Contrast that with an anchor like the Mantus M1 which has a low but very long shank and the anchor is much more in line with the chain pull. I don’t think you can just define an angle based on shank geometry for this as it also depends on the drag in the fluke but I suspect that it is mainly driven by the shank. The downside of the geometry of something like the Mantus M1 is that ultimate holding power will be a little lower for the fluke area as its buried angle is a little lower but that assumes good bottoms, the strength of an anchor like this is its ability to get a good set in marginal bottoms.
If you want to see the difference in geometry typical of these 2 anchor types, look at the Mantus Dimensions tab which has great side on pictures for these 2 anchors:
https://www.mantusmarine.com/mantus-anchors/
https://www.mantusmarine.com/m2-anchor/
You can see an example of both the Rocna Vulcan and Mantus M2 being pulled fairly sideways before setting here: https://www.youtube.com/watch?v=r4R2r5C_oP8. I know that I have seen this happen in Steve’s videos as well, it is just a bit more nuanced. If you contrast that video with this one where all 3 anchors have the shank design more typical of a roll bar anchor you can see that they are being pulled ahead much more and not sideways although there is obviously still some sideways pull: https://www.youtube.com/watch?v=wdURE1-X0j8. I wonder if someone like Steve or Drew has ever tried to measure this angle and chart it against setting ability?
Eric
Hi Eric,
I agree shank geometry is complex and vital. One thing I do know is that in the early days Alain Poiraud, Spade designer, tried twice to design a cheaper anchor that did not require lead in the tip or a hollow shank. He failed both times and came to the conclusion that he just could not get the reliability he wanted without using those two features. (I was in email touch with Alain at that time).
I also know for sure that a Spade with zinc in the tip instead of lead does not work—I was there when a friend who tried that dragged several times. The lead is that critical.
So I do think there is something good about the combination of the lighter hollow stock and the lead. I think it might be that a very slight upward pressure on the chain tips the Spade into a stable aggressive setting position. More on that in the next post.
It’s also interesting that Mantus says that the M1 is better at resetting than the M2: https://www.fisheriessupply.com/product-resources/mantus-anchors/mantus-m1-vs-m2-anchors-which-is-better-pdf#:~:text=The%20M2%20anchor%20is%20less,anchor%20housings%20and%20bow%20sprits.
On the other hand the large roll bar on the M2 is vulnerable to bending as Steve’s videos have shown, but that large bar seems to be required to avoid the dangerous dragging modality of the other roll bar anchors
The bottom line for me is this stuff is so complex that I just fall back on my experience with Spade over 23 years: never dragged once set, and failed to set less than 20 times—very challenging bottom types in each case. Also, never bent, despite the way we brutalized it on several occasions.
So I guess at this point the big question for me is: is the Vulcan as reliable as the Spade? If I could be sure that the answer was yes, I would be all over it. Testing would say yes, but testing, while useful is not conclusive. Also, it’s interesting that Peter Smith has seen fit to design a new roll bar anchor, when he already has the Vulcan.
Bottom line, I don’t know anything for sure, or even close, other than the Spade has been good to me.
Hi John,
Yes, the anchor geometry is more complex than it can first seem and full of tradeoffs. It seems that all of the modern anchors are designed to sit on 3 points when setting and be roll stable to getting there. The anchors without roll bars can get stuck in a different 3 point position where they are mostly upside down so the designers are forced to make the shank taller and use ballast to make it less stable there. I also think that if they extend the length of the shank, they are going to have issues as that will move 1 point of contact significantly while moving the center of mass a lot less and it will want to roll on its back much more. So it is back to trade offs.
I am looking forward to Steve’s testing of the new Rocna with both ballast and a roll bar. I worry that it will have fouling issues again though, they dealt with some of the original issues (upturned fluke) but it appears not all (sharp bend in middle of fluke, relatively small roll bar that can clog easily).
Eric
Hi Eric,
I think you are right about the potential of anchors without roll bars to get stuck upside-down. This is my primary reason for still thinking that the Spade may still be special since I know of no reset failures with it. And of course we know that smaller roll bar anchors like the Rocna and Manson exhibit the fast drag modality because they can foul and then get stuck upside down.
So I think a good way to think about this is balancing the Mantus M1’s good reset track record requiring it’s huge and vulnerable roll bar , and the Spade’s good reset record requiring a hollow stock and lead weight. If that’s right, and I think the preponderance of evidence says it is, then each of us have to pick our preferred benefit against the drawbacks that come along with it.
I’m writing about this at the moment, and this thread. has really helped me clarify my thinking. Thanks
Sorry to hear that you think the new Rocna may not fix the problem. I had high hopes for it, particularly given Peter’s experience both out there and designing anchors.
Hi John,
I’d like to add a little wrinkle to the Mantus M1’s reset track record. Simplifying a bit, I have spent ~6 months on anchor this year and ~2.5 months last year. 44 ft boat, 16 tons, 85 pounds Mantus M1. Most all of the anchoring was on sand and sandy mud bottoms, with more than a fair share of posidonia grass.
From this limited experience, I have learned that I very much prefer to be onboard and awake any time a near 180 degree wind shift happens. 5 times I had experienced the anchor disengaging when the boat sailed over the anchor. 4 out of 5 times, the anchor reset by itself within about 15-30 meters. The remaining one time, I had to retrieve the anchor and go somewhere else before getting to know my neighbor too closely, so I don’t know if it would have reset. 3 occasions were associated with thunderstorms and 1 with katabatic winds.
I like my anchor and I’m not going to replace it for a while. However, I’d prefer if it stayed buried on wind shifts and turned in place, so that I don’t have to jump out of bed to the sound of anchor alarm from time to time.
Hi Alex,
Thanks for the field report: which I always appreciate.
What you describe would make me quite nervous.
15-30 meters is a long distance in many anchorages: there is land that might be close at hand and other boats. And even if you re-set, your geometry with other boats around you will be different. Additionally, it is my take that any distance an anchor drags, even with the initial set, increases the opportunity of it picking up a log or debris that will further interfere with re-setting.
One of my enjoyments in many anchorages is hiking: sometimes being gone from breakfast till nightfall. I would worry, especially in unsettled weather, about leaving a boat on an anchor that might not re-set.
My best, Dick Stevenson, s/v Alchemy
Hi Alex,
Oh my, that is disturbing since I thought that the Mantus M1 was the only roll bar anchor that did not suffer from this problem at all, because of the large size of the roll bar. Thanks for coming up on this, particularly since I’m in the middle of an article on anchor trade offs. Your report will make me do some edits. Thanks!
I’m trying not to read too much into this limited dataset. Maybe it’s the grass that didn’t let it reset in couple anchor lengths, who knows. It’ll probably take me another season and a few more wake-ups by anchor alarm before I decide to give another anchor a try. Because when it holds, it holds well, and it sets perfectly nearly every time. Also, even quite violent ~90-120 degree wind shifts didn’t move it even once.
Hi Alex,
Absolutely, agree that we should not read too much into this. But on the other hand four occasions is concerning, even though the anchor reset in three of those, but after a relatively long drag. And yes, none of the roll bar anchors seem to have problems with veering, even to 120 degrees, it’s the 180 degree rapid shift in load that makes them flip on their backs and then refuse to set again because of the weight of fouling from the first set. Steve’s video shows the modality well: https://www.morganscloud.com/2019/05/24/anchors-resetting-failures-with-rocna-and-some-thoughts-on-vulcan2/
All that said, sure, forewarned is forearmed.
Hi Alex,
Interesting and the report is definitely appreciated even if it is not good news. I figured that there would be failures out there but you have a surprisingly high failure rate. Thankfully we remain at 0 failures with our M1 that is probably at 600-700 nights at this point but I figure if we use it enough, we are likely to find a weakness at some point.
In the cases where you dragged, do you happen to know the bottom type? And the time that you had to move, did you get a look at the anchor and could you see why it wouldn’t reset?
One thing this discussion got me thinking about that I hadn’t previously thought of is that the shank geometry of these anchors which really helps in setting means that there is a larger torque on the fluke from any change in direction. I can imagine where this could cause more abrupt motion potentially including a breakout when another anchor may take more time to swivel but I would need to see testing to really support that hypothesis. On the flip side, the really tall shanks on the ballasted scoop anchors could try to roll them out in an abrupt shift of ~90°.
Eric
Hi Eric,
Every time that I dragged, the bottom was mud/sand mix. It’s the kind of substrate that makes me appreciate the deck wash pump I installed as per John’s advice on this website. About half of the time, the fluke comes up packed with some mud that I need to wash off.
The one time I had to move, I know there was quite thick cover of posidonia grass on the bottom. All boats at that anchorage had to aim precisely at the sand patches with anchors or make countless attempts before getting a set. So, I was not very much surprised that, once out of its sand patch, my anchor had trouble getting buried again. However, by the time I raised the anchor, the fluke was almost entirely clean, as I recall. I did not need to use the pump before re-anchoring, nor was there any large debris fouling the rollbar. Also, it was dark o’clock, so I may have missed some details.
Hi Alex,
Thanks for the fill. Sounds like the same modality that Steve Goodwin proved out on the Rocna where the weight of mud stuck to the fluke keeps the anchor on it’s back. In the last case, when it was sand and weed, said weight probably fell off as you raised the anchor.
Hi Alex,
Thanks for the additional details. We do get some amount of mud clinging to our anchor fluke right around the shank attachment but it is never very much. With the previous Rocna we had, we would have times where most of the fluke had many inches packed into it. My hypothesis has always been that the anchor has such high tip weight and good setting geometry plus relatively low tendency to clog that it is tolerant of clogging although it seems you have proven that balance can be upset. I think that all scoop anchors will foul with some amount of bottom but the degree is very variable and important. Steve’s testing of drilling holes in the fluke of his Manson Supreme was fascinating and I do wonder whether the anchors like the Viking, Sarca Excel, etc. that do this are onto something.
The only failures to set we have experienced beyond a single time with a guest on the windlass in a really grassy anchorage who dragged the anchor at quite short scope for a while have been 2X where the chain fouled one of the roll bar bolt heads pulling the anchor along backwards. Contributing factors might be that we have 5/16″ chain with a 65lb anchor so the chain is small enough to catch and we usually sail onto the anchor which makes for less than perfect drops. Anyways, while I find it highly unlikely as a failure mode, I do worry slightly about the chain going under the back of a not fully buried fluke and fouling so if there might be a wind shift, we try to set hard enough to get a full bury to keep the chain from catching under the fluke.
Eric
My Spade, bought in the UK 2 years ago and used continuously since, has encapsulated lead-at least that’s what it looks like to me.This must be a newer feature that addresses an important issue.
Hi Brian,
Good to hear. I will photograph my new one and add that to Part 2
Since the conversation has veered a bit, I decided I could ask my Spade questions. 1. How often, if at all, do others replace the stainless bolt that holds the thing together? Since it is not in the classic dangerous anaerobic conditions, perhaps never? 2.On galvanizing: after many years, the only area that looks as if it has failed is the shank INSIDE the fluke. This article led me to check it. I think I may sand off the surface rust and either paint it with Rustoleum or use their galvanizing spray AND monitor it more regularly. Does that make sense? Thanks.
Hi Terence,
I will be getting into anchor inspection and maintenance in an article in the next few weeks.
That said, if the shank has seriously deteriorated with measurable less of metal where it mates to the fluke I would be considering replacement of the anchor since that’s a very high load area. How old is the anchor?
And no, I have never replaced the bolt, given that it’s not load bearing, but I would inspect it.
The anchor is maybe 15 years old, but it has seen limited use–except for one year long cruise. I do not think I have lost any metal, but I am going to take it apart to look. I look forward to your next article. Thanks.
Hi Terence,
A good idea to pull it apart and take a look. The key will be if there is any appreciable thickness loss, or pitting. As I understand it, the later can cause stress concentrations, so a bad thing, particularly at the high load area where the stock and fluke come together and I think less of a worry as you get deeper into the socket. I will write more about this stuff, and hope that the engineers around her will fill and/or correct what I write.