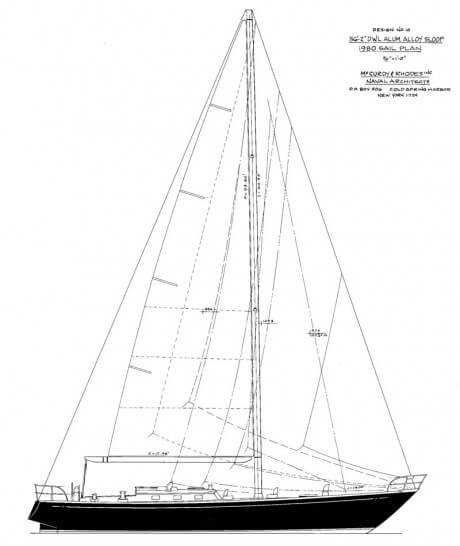
It is amazing how often people look surprised, and even mildly alarmed, when I tell them that we own an aluminum boat. The next tentative question(s) is almost always about electrolysis and the general longevity of the material.
For some reason there seems to be many stories of disaster, particularly on this side of the Atlantic, around aluminum as a boat building material. These stories normally go like this: “I have a friend, who knows a guy, who has a cousin, that bought an aluminum boat, and after a week in the marina the bottom fell out of her”.
The funny thing is that after 20 years of aluminum boat ownership and ten years of being a fairly high profile proponent of the material, I have yet to meet one of these mythical aluminum boat victims.
The fact is that as long as the boat is built out of the right aluminum alloys, and the right welding wire is used (all well documented), aluminum boats last longer and stay stronger and more stiff than boats built of any other material you can think of.
Which brings me to Carina, a McCurdy and Rhodes Custom 48—same designer as our own Morgan’s Cloud—that has just won the Newport Bermuda Race for the third time. Thing is, the first time Carina won, the leisure suit was in fashion…the year was 1970.
Carina won again in 2010, exactly forty years after her first win. And then again this year. And you know what Carina was doing between her second and third win? She sailed around the world clocking up 42,000 miles. And while she was at it, she did a few races…like The Trans-Atlantic, The Sydney Hobart and The Fastnet—not exactly known as walks in the park.
One tough old bird that aluminum boat…fast too.
I spoke with Rives Potts, who is not only Carina’s owner and skipper, but also runs Pilots Point Marine. Rives has been involved in building and repairing many aluminum boats over the years. He had this to say:
- If an aluminum boat is built of the right alloys and the right welding wire is used, she will last essentially forever.
- The great thing about aluminum is that what you see is what you get—if you have a problem, you can see it.
- He has not had to make any structural repairs to Carina. And she shows no significant corrosion.
- She is still incredibly stiff and strong after 43 years of hard voyaging and racing.
- And because Carina is stiff, she is still fast and it is much easier to keep the deck fittings and hatches watertight than it would be on a boat that flexes more.
- When he has seen corrosion damage on aluminum boats—usually the result of a wiring problem or an inaccessible area where debris has lain for years—it is confined to a small area and is easy to repair as good as new by cutting out the plate with a skill saw and welding in new plate. Just make sure you use the right alloy plate and the right welding rod.
- Repairs and modifications to an aluminum boat are easier [that means cheaper too] than they are on boats built of most other materials.
- The only real drawback of aluminum is keeping paint on it. But if the paint job is done right even that issue can be overcome.
So if you are looking for a boat to take you offshore safely and comfortably, don’t look past that old aluminum boat. She might have a few years and miles left in her…or a few decades and a few circumnavigations.
And if you are crazy enough to embark on a major refit, at least if you are restoring a well built aluminum boat, you will know that you are investing in a good hull, unlike poor stupid Bob.
Comments
We are cruising the south coast of Newfoundland, where internet availability is scarce, so it may be some time before we can respond to comments.
Further Reading
- Lots more about aluminum boats.
Very true. As a fellow 40-year old McC&R (Luke-built) aluminum sailboat owner, I couldn’t be happier. There is simply nothing as secure, quiet or comforting as racing through the ocean in a metal. No flex, no squeaks, no leaks, no oil canning…just pure power and smooth sea motion. Mine ws refit with a ‘wooden boat interior’ for the best of both worlds. Of course, most of this credit is due to her designer but there is no question that aluminum is a terrific material from which to craft a boat. Commom sense prevents all the rumors.
And yet… not for the Adventure 40?
Hi C. Dan,
If we could do aluminum at the price point, then maybe. However remember that the Adventure 40 is not going to be the ultimate offshore boat. Rather she will be the ultimate value in an offshore boat. Just painting the decks and bottom properly of an aluminum Adventure 40 would, I estimate, add US$10,000-15,000 to the price in comparison to a fiberglass version. And realistically, how many people in the mass market will buy an unpainted aluminum boat, particularly in North America? So add in painting the hull, and we are up over $20,000, just for painting.
Dear John,
I confirm your figure for deck and bottom for a Adventure 40 with a simple deck shape and if the welding job is done correctly so you don’t have layers and layers of filler to applicate.
But for a hull you would need to add much more than the additional 5000 you mention…. Mostly to the get the hull ready to paint.
I understand what you say about the willingness to have an unpainted hull but at the same time painting the hull would be – in my eyes – against the philospohy of the Adventure 40 and the idea of low maintenance
And the first scratch is a very expensive one…
Jean-François
Hi,
i have actually a question on that one, and more specificaly on painted decks, as i have to remove the many layers of different ugly paints and the antislip on good old “Moscatel”,
i will sandblast it first, and i’m actually considering leaving those decks blank, or at least where it does not need antislip,
what would be yr feelings abt that ?
next question is of course which antislip to apply after that …
The hull would remain as it is, as it was originaly faired by epoxi resins and painted, and repainted epoxi.
Hi Bruno,
If it were me, I would use Treadmaster. See this post for some tips.
Also, type “Treadmaster” into the site search box next to the menu for many more articles on this material and our experience with it.
Hey Bruno,
It seems like you have a Romanée…
One thing : You don’t know what you will discover under your paint. There might quite some filler… If you sandblast you have to remove everything.
On our first boat, we sandblast the deck to remove everyhting. It took us much more time and sand than we tought. At some place we had several cm of filler…
As the paint was ugly but ok when we had removed the 20 year old treadmaster, we would have been better of with just a new layer of paint and new Treadmaster or a (Sicomin) anti slip paint…
After sanding we did ourselves a complete cycle of paint on some part of the saloon (and the hull) because of ethetics. 12 years later the paint is still perfect.
Hi Jean-François,
Great to have your confirmation and correction of my cost guess, thank you.
If it were my boat I would not even paint the deck, just Treadmaster. But can the Adventure 40 be like that and sell enough hulls? I fear not, although I don’t know for sure.
I note that you made the decision to paint the decks and cabin of your Boreal boats. Was that driven by marketing and sales or another reason?
I think that this may be the crux of the hull material decision: if we have to paint even just the deck, then that is probably a killer for aluminum, if not…
Hi John,
There are different answers to your question. Some elements which contributed to our choice :
– esthetics : general look of the boat. We did not want an all “grey” boat.
(But note that at the same time, we did not want any paint on the hull. This has determined the way we build the hull)
– esthetics : we wanted the look of the deck and the saloon to be tight and tidy. Said in another : we wanted way to hide the imperfections of the boilerwork. Therefor we wanted filler, therefor we have paint…
– antislip : we do not discuss the effectiveness and the qualities of Treadmastesr, but esthetics is another question. Moreover the day you have to remove it, it is a very very hard hard job (Bruno will confirm). You can also say that walking barefoot on it is not very pleasant. We use as anti-slip paint made by Sicomin Deck Line (bi component). The constitution of the paint makes it is “elastic”. It is either sprayed or applied with a roller. The way you apply it will determine its final aspect.
So under the antislip we apply the whole cycle of paint all over deck and deckhouse.
Note that the traditional paints are mechanilly bonded on the aluminium.
Now there are paints coming up which are bonding chemically tothe aluminium. This does make the process “lighter” because the surface oxide is not a problem.
There is a Swedish boatyard which is doing some tests with it. It is (at least here in Europe) pretty new and there is no feedback yet.
I hope this helps…
Hi,
many thks for yr feedback on antislip and deckpaint, and yes, the good old Romanée needs some efficient cosmetics, foreseen for next winter, you are both right, and a choice will have to be made, after blasting,
i’m also really convinced by antislip paints, as i use them since 25 years on my (job) oceangoing steelships, we just mix antislip slints during our epoxi-polyurethane cyclus, and this work great and easy, nice surfaces, good holding,
But as you say, the chemical bonding is usually a bit of a problem on aluminum, and i hate to re-do things too fast …
I have now no choice but to sandblast, i’m quite confident on the surface condition, as she is a 1979 (they started to build them in 1973), and hopefully used less filler 6 years later (i might check with builder G.Fillon), some even sandblasted the hull after years and left it blank,
After that, i’ll have to make a (fast) choice, as for so many (good) things in life …
thanks again !
Great post and reassuring comments from you experts for greenhorn Alu owners like us. We acquired a 23 year old alu Koopmans 48 last year and so far have nothing to complain about. Amazed at the speed considering her weight. We carry 8 tons of lead due to the lifting keel having no ballast so she weighs twice as much as the tupperware equivalent. Hull lines look fairly similar to the Carina
Cheers
Abel
hello Abel,
it appears that we sail very similar vessels. might be both fun and useful to connect. I see that you plan to enjoy Norway – and my Koopmans is one of two currently based there. Feel free to reach me at
rgds, Petter
Not only a great material, but a great looking boat too – lovely sheerline.
A boat to gladden the heart of any owner – no wonder he’s hung on to her!
Best wishes
Colin
What is the correct aluminum alloy and rod?
Hull plating is usually done in strain hardened alloys 5083 or 5086 (also common are 5456 and the slightly weaker 5054).
Framing could be 5000-series but is more commonly of 6061-T6.
I’ve never seen anyone stick-weld aluminum; it is usually welded by MIG (with a 5000-series electrode) or TIG techniques, with an argon or helium/argon shielding gas.
Aluminum is tricky to weld correctly and is very prone to fatigue around bad welds. When you combine a knowledgeable designer and a skilled welder, you can end up with aluminum hulls that will last almost indefinitely. If you give incorrect detail drawings to someone who isn’t quite so good with a MIG torch, you’ll get stress risers, poor returns and poor penetration, and you’ll find yourself wondering why the boat’s full of fatigue cracks in her second season. If you want to use aluminum, it’s really important that everyone involved takes the time to learn how to use it correctly- this means a lot of reading, and a lot of practice on bits of scrap.
Hi Matt,
All good information, thank you. Also, thanks for the correction on stick welding. When I said “rod” I was speaking generically, but, of course, it is wire that is used.
Great info, this is the first I have seen this list of aluminum types, Is there a way to find which aluminum types were/are used by the companies that build aluminum sailboats?
Hi Matt,
Absolutely perfect information. I’m happy I had not to answer this one as you express things in a much clearer way than I can do.
Note that theoretically all alumiunium with the same denomination (5083 or 5086) should be exactly the same.
According to our insurance they have on regular base claims from non conform aluminium coming from some countries.
In our contract we commint our Aluminium is coming from Norway, Holland or France.
Each plate is marked and you can track the origin…
Bill : the constructor should mention in his technical description which aluminium he uses for what. During the construction you should be able to see it on the plates…
The preferred electrode/filler wire grade for MIG and TIG is 5356: this *can* be used to weld 6061 as well as the 50xx alloys for the plating.
(Incidentally, it *should* be used for 6061 for any weldment which will be anodised.)
Opinions differ on whether there’s any electrochemical issues when combining 6061 framing or welded thru-hulls etc vs 50xx plating
If there are problems, it seems likely they’re either very subtle, or only arise under highly unusual circumstances.
Some builders hedge their bets by preferring to avoid this combination below (heeled) waterlines for thru-hulls, or in the bilge-water zone for interior framing.
I’ve seen an experienced boat builder making a Philippe Harlé boat, and he explained to me that the secret of fabrication is 1) the welding equipment that MIG has to be water cooled for better precision and 2) the hammering process after welding to rebuild the strenght loss in the HAZ (Heat Affected Zone) where aluminum alloys loose all their mechanical and structural properties. If someone doesn’t hammer correctly the hull, it will not be possible to have it without paint as all the defects will appear. So not easy for an amateur to do a first time boat in aluminum.
Thanks for the reassurance on aluminum! (UK spelling now!) I really think it is the best material to date for ocean sailing.
Hi Viv,
Just wanted to show that I’m bi-lingual. 🙂
arguments on the same line !
http://www.kastenmarine.com/aluminum.htm
definitely what i think, but good to share the same feelings on our old sweet lines strong and light hulls …
i would say the same, especially for Europe, whay not the A40 …,
had a look at those : atlanticyachts.nl ?
Dear John,
All very true.
One additional reality at least in Europe – it might not be true in the US – is that the second value of an aluminum boat stays longer high.
Most probably, we would all be amazed to hear what Abel has paid for his 23 old year boat… And I believe that, correctly maintained, she will keep her nominal value through the years…
Best regards,
Jean-François
Jean-Francois,
You’re spot on, after insurance survey it is insured for EUR 2ooK and the surveyor said that if properly maintained, it will not depreciate. Lets see ;-))
I personally would be happy with a bare hull/deck in aluminum. Functionality is to me the essence of the Adventure 40 but As you said yourself John, maybe North America is not ready for the sight of a naked hull! In Europe going topless is the norm so a hull without topside paint is not considered garish at all.
I like the purposefulness that an unpainted aluminum hull presents, like driving a Land Rover Defender instead of a Range Rover, one is to do and the other is to show. The point of the Adventure 40 is to get people into sailing that is more than marina hopping but is a build-up to ocean sailing and world travel. I can see that a composite hull at an attractive price would maybe attract more people to the way of life, but would it not just become another plastic boat? There are many really good boats out there and a lot of floating condos as well, all in plastic. By being different, cutting edge and innovative, then the Adventure 40 could be a winner.
I understand that lots of us writing on this great site have a fair amount of sailing under our belts and maybe we are not the market for the A40. So, personally I would go for aluminum, but is that good for the A40 concept – that I don’t know.
Hi Viv,
What a great comment, thank you. Sums up the conflict that I feel too on this point exactly.
I agree with Viv about the ‘purposefulness of an unpainted aluminum hull’. I see the A40 as being a no-nonsense, functional and purpose-built boat. When I signed-up to express an interest in purchasing one, I misunderstood and had assumed that it would be a metal boat. If it’s just going to be another plastic boat, albeit a well-designed one, I’m not so sure there would be enough difference to set it apart from all the other ones out there. I know it’s impossible to design by committee, but, maybe a poll of your potential buyers would provide valuable feedback on the aluminum painted/unpainted question?
Ann
Hi Ann,
I think that at some point a poll of sign-ups on this and other design decisions might be a very good idea.
However, I can’t agree that just because the hull material ends up being composite, rather than aluminum, that this would make the Adventure 40 “just another plastic boat”.
Whatever material the boat is built from, the Adventure-40 will be stronger, faster, more comfortable at sea, more reliable and significantly less expensive to buy and own than anything else on the market. That is anything but a “me too boat”.
John, Viv and Mireille I agree completely.
Your analysis is spot on. Some cleverly expressed idea’s and philosophy’s. (personally I loved my old series three landie)
I think the 1st A40 should be grp given the target market. That target market needs only to dockside walk to hear all those “horror” stories about electrolysis!
Perhaps a model II (grp OR aluminium high lat. version) could be slated for future production depending on buyer interest.
I would prefer the ali boat myself but your target market won’t as they r either new to voyaging or not into the specialised high latitude voyaging yet..
Give them time to voyage. Some will be happy on the trade wind/low latitude route and they have the perfect tool for it.
But some will retain the philosophy that sent them to sea in the first place.. the desire to seek new experiences.
These will be your repeat customers and some will want a new tool for the job of high latitude sailing.
As I understand it the initial brief was for a seagoing VW beetle ie. a low cost entry level tool that does it’s intended task very well. A great design through a well engineered (strong AND eficient to build) great sailing easy to maintain product.
Hi Nelson,
Thanks for the great and very clear comment. Much as I am a big fan of aluminum, I think you are probably correct in your reasoning.
exactly …
kind of a light(er) Peter Smith’s “Kiwi Roa” ???
http://www.petersmith.net.nz/about/kiwiroa.php
Bruno,
Peter Smith did the fitting out interior and exterior of my boat but the hull is from Meta in Tarare, FRANCE. Built in Stongall. Big job to all the paint off that Peter put on. He did a good job, too good in my opinion. Now it is time to leave raw.
My 40-year old aluminum deck was painted and covered with Treadmaster before I bought her. The epoxy holding the Treadmaster to the deck is a tight a bond. Fantastic grip. Very acceptable aesthetic. The decks will need to be redone within the next few years and I do debate how best to address this. Bare aluminum would be fine if the boat were new but I wonder how it will look after all these years of minor corrosion, faring, dents and dings. No question, if you remove paint from the equation, aluminum has few complaints.
Michael,
I have rolls and rolls of Treadmaster which I will NOT be putting on my aluminum deck once all the paint is removed. I will sell at a very fair price. I am presently in the Seattle area. I have both textures in light beige color. Interested?
Hi Victor,
I may have a repair job coming up that will require Treadmaster. Keep me in mind and contact me through John if you haven’t sold it in a week or so.
Congratulations on your long delivery up from Panama, and welcome back to the land of cool rain!
Richard
Hello Richard
Thank you. You have been on my call list for a while and I will do so when back in Jackson (assuming I get there.) As you may have gathered I have started the refit here in Port Townsend with Carol Hasse and Brion Toss as my primary support team for sails and rigging respectively. I hope to also have a removable hard dodger welded up. I have a nice naval architect from Portland helping me with the design.
If you decide you want the Treadmaster I could bring it back to Wyoming or ship to wherever it is needed. I have both textures and would have inventory how much of each but certainly enough for a 45-50 foot boat.
I have decided to paint on what the local alloy fishing trawlers use here. It is easy to touch up abused areas rather than matching up sections of Treadmaster. It won’t ever look as nice but my boat will never look nice so why bother? I am more concerned with the esthetics of function rather than the esthetics of lookin pretty.
Hope to catch up with soon. I have Steve Strand coming down from Canada to look at Rajah Laut this Sunday. He sold Ocean Watch their steel boat a few years back. He is also doing a big aluminum project in the Philippines.
Anyhow more later..
Cheers
Hi Victor,
what do the local alu trawlers use then ?
usual epoxi paints with antislip slints ?
Rgds
Bruno
Cheers John,
Although the a40’s not my next yacht I’ll keep following the development as I feel you have something here.
Anyone know if a cruising yacht has ever gone through this sort of development.. I would think not which indicates you have something unique.
On a different note and speaking as a parsimonious cruising sailor even I would be happy to send AAC some of our well hoarded funds for the value of ideas, experience and content contained herein.
Keep it up as AAC is appreciated and has real value..
Listen guys , I am going to order my new Garcia 55 exploration under Jimmy Cornell´s supervision and collaboration. I guess will be one of the best blue cruisiers actually in the world.
Hi Willy,
Note that the boat Jimmy Cornell is having built is 45 not 55. I also have some severe reservations about the boat, particularly the twin rudders which are, in my opinion, not a good idea, particularly around ice.
Before you pull the trigger on that boat, I would suggest you at least look at the Boreal and talk to the people at Boreal for a different view.
Disclosure: Boreal is a corporate member and supporter of this site.
any idea of the price tag for the exploration 45 ?
i could not find much tech details so far,
just read that Boreal has a two years full order book, seems they found their market ! great ! and this without counting all the ones dreaming of it …
I found a selling price info on a copy of a Yachting World report.
According to this report, October 2013 price tag should be 425k€ + VAT.
Looking at all Allure/Garcia/Outremer/Alumarine current production, Garcia Exploration 45 seems to have some similarities with Allure-Yachting Allure 45 (same: length, architects, workshops etc…).
I wonder if a ruggerised Allure 45 might not be not very different from a Garcia Exploration 45 with a lower price tag….
Great piece, thank you for sharing it.
We just purchased a an aluminum Rumba 41 which has two areas of the hull that are corroded because of the failure of the resin encapsulating the steel ballast. We are receiving conflicting advice on the preferred repair method. Some argue for drilling our each small crater (there are many) welding in a small backer and filling the hole with weld from the outside. The other camp suggests simply cutting out the two sections and welding in new plate (each about 12″x 42″). Can you lend any insight or thoughts about these options?
Thank you,
Hi Steve,
Hum, this is a tricky repair. The problem is welding aluminium in the presence of the ballast without contaminating the welds and also heat conduction by the ballast making for cold welds. If it were me, I think I would simply weld a patch over the existing area without cutting anything out, and then fair it in with epoxy putty.
Make sure you get a top grade welder to do this, because getting the heat right is going to be tricky.
By the way, anyone who tells you to fill a hole with weld bead is not a competent person to work on an aluminum boat and should be ignored. There is no way to get a proper and reliable repair with this wrong, but all too popular, approach.
One other thing. I’m concerned about steel ballast in an aluminium boat. I have never seen that before. I would want to investigate what exactly the situation is and be very sure that no water can get into the weld cavity.
Hi Steve,
I do share John’s vision.
I just want to overstress the importance of getting rid of the cause of the problem.
How is the ballast insulated from the hull ? You know ?
Don’t take the risk to melt that insulation…
Why would you cut out the plate ?
Note that it is always very very difficult to judge a situation and give advice without having seen the reality.
Hi Steve, nice boat !
isn’t it a swinging keel or a fixed keel ?
anyhow, this is a well known problem on those early aluminium designs, with leaking encapsulation,
Harlé got the same on some of our Romanée (fix keel) where the resin seal in the bilges was cracking after a few years by her lack of elasticity. and bilge water leaking through to the lead, making a great battery of the keel, with corrosion as a consequence,
Most owners of the affected boat keels have indeed cut the bad plates and made a new insert taking care of inserting another aluminium flat bar behing the new weld in order to avoid a smelting lead contamination of the new weld, it worked well !
If your ballast is steel, you might not have that problem of melting ballast, unless the ballast itself has been encapsulated in some resin which might melt as well !.
but indeed as Jean-François underlined, the main thing is to solve the original problem first, which usually is a leak in bilges well to the keel, or water the keel in the keel in some way,
so after cutting this bad area which was usually juster under the bilge, they inserted and welded an horizontal plate in the keel to seal the bilge well hermeticaly instead of the resin.
The other solution of drilling and filling by welding the craters from outside is indeed bad on a lead ballast because the lead will melt when welding and in the welding seem …
What others also did, is drill the craters and just fill them with modern epoxi resins !! it works also … but you then first have to find a way to drain the liquid which is still inside and dry, or you’ll get more holes later on !
To solve the bilge problem on healthy boats (like mine) where the water did not reach the ballast yet, most of us poured modern “flexible” epoxi resins on the bottom of the bilge well, like International Watertite, e.g.
Good luck and fair winds !
PS : i did not hear of any of those surty boat loosing their keel for that reason !
Hi Steve,
You have got some great advice here from people who really know: Jean-François is a boat builder and Bruno clearly knows your boat.
The key take away, as far as I can see, it to be careful of weld contamination and make sure you get the the bottom of what caused the problem in the first place and make sure that the keel cavity is dry and watertight after the repair.
Thanks for your site I too have been on the lol out for the mythical elecrosis boat:…… I have a 35 year old koopmans it has some corrosion on stanching bases not same type al and a bit where toenail is bolted on basically I am certain that I could let it go 35 more years and it would not be a problem I am baffled by the volume of cynics who have zero experience in short al is in my limited exp the toughest inch to inch most maintenance free easy to repeat material I have seen it’s really easy to put on a sloppy mig weld with argon shield then tug to clean up id desired also grinds out way easier than steel
Thank you for very interesting info on aluminum boats.
Recently purchased a dutch built 60ft aluminum motorboat in seattle.
The teak deck is fastened with self tappers thru the alu deck and after 30 years, it may be time to look for something else. Have been told to cover the teak with the kiwi product, but don’t like the looks of it. another; just put the tread-master over the teak deck?? I prefer a low maintenance ( alu) deck and if need be with a tread-master finish.
Look forward to any suggestions.
Hi Rene,
I’m afraid there is only one right way to do this: remove the old teak deck, plug the holes and then coat deck with non-skid paint or Treadmaster. This issue is one of the biggest, maybe the biggest, drawbacks of old aluminium boats. If you cover the teak you are sealing in water and since the screws are probably stainless steel, creating a big corrosion problem.
Within this job, the biggest challenge is how to plug the holes. Welding is an option, but is usually not practical because the boat is probably insulated with foam, which will burn. Probably the best option is to drill the holes out, tap them, and thread in an aluminium flat head countersunk machine screw to seal it. Some, maybe many, of the screw holes will probably be severally corroded through dissimilar metal corrosion, so you may need quite large machine screws.
Hello Rene,
Maybe I could add 5 cents of experience to your issue.
I also own a Dutch build aluminium vessel (Koopmans welded by Folmer with swing keel) that was equipped with a teak deck. Luckily it was only glued. However, after 15 years of use some of the glue had started to loosen and there was water ingression under the teak. Being based in Norway where water freezes in the winter, the water became ice and every seasons forced more of the teak deck loose.
In the end I felled compelled to act as I was afraid the stagnant water under the teak would cause corrosion, and last summer the teak deck was removed fully. Quite a bit of an effort and even more to clean up the mess.
Another aluminium vessel which I have encountered the teak deck was screwed. As far as I can recollect, the solution used on that vessel was to fully remove the deck and the old stainless screws and then fill the old holes with new aluminium treaded rods that were welded in place. This created a new water and corrosion proof structure. However, not a quick fix as there were more than 2.000 screws in the deck.
Now my decision was what to put back. I discarded teak for reasons of cost and also maintenance, as the vessel will see the tropics in the reasonable future. I considered Treadmaster and TBS (more comfortable to walk on). Both options are not cheap. Secondly, it involves covering the aluminium surface, and hence hiding any future problems of water ingression or corrosion for view. The decision was in the end to pain with two component paint and add non-skid to the last coat – an economical, easy and functional solution I am so far happy with. When any damage to the coating arises, I may fix it myself.
Use high gloss paint for non-skid: When I discussed painting with the painter he advised me to use high gloss paint. I was initially afraid it would be very slippery, but he assured me it would work, with it does. The potential problem with painted non-skid is that dirt and grime is collected on deck and the coarseness of the surface makes is difficult to remove. However, on high-gloss, the dirt has a hard time sticking and it is easily removed with brush and water.
Hope some of this hard earned knowledge may be of use.
Hard-earned, indeed. SS screws through teak and into aluminum is a nightmare scenario to me. I have a steel deck painted with high-gloss two-part with an elderly product called “Decolay”. I’m thinking it’s time for a change. What did you use for the non-skid, please?
Hi Petter,
Great information, thank you. Two things I would add.
When fixing screw holes it is quicker and easier to use countersunk aluminium machine screws and just set them in Plexus adhesive, rather than welding.
On using gloss paint. As we found out the hard way, all is good until it snows. At that point, no matter how aggressive the sand in the paint, things get lethal. What seems to happen is that the snow packs under your foot and the interface between that and the gloss paint is as slippery as a skating rink.
For this reason and others, we now recommend either Treadmaster or one of the new paints with hard rubber fragments imbedded, particularly if there is any chance you will be moving around on deck.
There is also an additive for Awlgrip that knocks the gloss off, but I have no experience with that.
John,
I appreciate your comment about the lack of compatability between non-skid and snow, but I do no like the idea. Have not tested this, and is no looking forward to it either. Current plan is to venture into winter fjords to try some “uphill skiing” from shore to summit. Then I will have full opportunity to validate your experience.
-p
Thank you John for your advice.
By sending an email to your website, I hoped to learn of any new short-cut on the market. You confirmed there is none, at least none that keeps the boat seaworthy longterm. First thought of covering the old deck and holes with a new alu plate, but the insulation prevents welding. I see maintenance as part of the hobby, so no problem.
Thanks again.
What would cause the plating of an aluminum boat to get thinner ? Is it electrolysis ? What can be done to prevent it?
I know a boat for sale that had plates replaced due to thinning. Would like to know why it happened and how to prevent it from happening again.
Thinning happened in bow area and under the engine area.
Hi Ren,
There is no intrinsic reason that aluminium plate should thin over time. Or to put it another way, there is something wrong with that boat that caused the problem. Look for: no isolation transformer; non-floating DC system, or one that is supposed to be, but isn’t; wrong paint (copper content) copper or iron salts dripping off fittings, or the engine, that were left for very long periods; dissimilar metals that are supposed to be isolated from the hull, but aren’t; not enough zincs, or poor quality ones.
Water in lead-filled aluminium keel: fill voids with oil after repairs?
Hope there is life in this thread still? It has been very useful in the ongoing repairs of our aluminium Koopmans 39 built in the Netherlands 1995 – 1996.
Last year we discovered a faulty (missing) weld in the bottom of the keel, water slowly dripping from the keel when hauled. The boat has spent the winter in a shed for surgery on the keel. On pressure testing the keel we discovered 3 faulty welds in the bilge – just as expected from information gleamed from this thread!
The keel section is filled with lead. We have no details about how this is placed in the keel. We have now made access holes to the keel so we can see top of what we believe is the lead, but cannot really see whether the lead is moulded in place or set as ingots in epoxy or resin. Ultrasound measurement of the keel shows no areas with less than 6 mm (the plate thickness), although this is of course no guarantee against there being pin-hole electrolysis. None is visible from outside, and bottom 1’of keel was sand blasted before the repairs.
We have spent a lot of effort in repairing the keel and searching out and repairing the leaks in the bilge area. We plan to treat the bilge with epoxy. Although the keel now is presumably dry after several weeks of vacuum applied, there is bound to be some salt in the voids between aluminium and lead. As pointed out above this could constitute a potent battery, and we are told we should fill the keel cavity with oil to neutralize this effect. I understand this will make later welding repairs difficult, but our welder states that with the new access holes any oil can later be rinsed out before any further welding.
Does anyone have any suggestion on what kind of oil would be best to use for this purpose? Some suggest vegetable oil, some suggest diesel, some old engine oil, or could we use anti-freeze made for aluminum engines? The oil/liquid needs to be thin to creep into the presumably small voids. Epoxy does not seem to be an option as there is no way to prep the surface for adhesion.
Any thoughts/suggestions much appreciated!
Hi Hans,
Sorry, I don’t know anything about the oil idea, although it sounds credible.
Two things that may help:
First off, I would definitely not “treat the bilge with epoxy”. In my experience it is just about impossible to get epoxy to bond properly to aluminium in the kind of conditions prevalent in the bilge, no matter how much prep work you do. So by doing this you are, I think, more likely to mask future problems than prevent them.
Second, this whole problem of salt in the keel cavity may not be as bad as you fear. Both our boat and her sister ship have had keel breaches resulting in salt water getting into the keel cavity due to hard groundings—the previous owner of our boat ran her on a rock at 7 knots the day we closed on buying her!
In both cases the water was drained out and the hole repaired with an external patch. In both cases the lead is in contact with the aluminium for the simple reason that it was poured into the cavity when the boat was built. Nether boat has had any problems. In the case of our boat the breach was 23 years ago and our sister ship over 30 years.
If there was anything really bad going on in those keel cavities we would have seen evidence of bubbling in the epoxy putty covering the keel years ago.
The bottom line is that lead and aluminium are not that far apart on the activity series and therefore it seems that the reaction is pretty limited. I’m also going to guess that any reaction that does occur gets stopped pretty quickly by the build up of aluminium corrosion byproduct (self anodizing) (the white stuff you see when aluminium corrodes).
There are hundreds of aluminium boats that were built with lead poured into the keel. Many are decades old and I doubt that the keel cavity in many of them is free from salt. But even so, I have never seen, or heard of, a bad problem in this area.
In summary, the oil idea may be a good one, and probably can’t hurt, but I think that the dire predictions, that some people have probably disrupted your sleep with, are right up there with “drop a penny in the bilge and it will sink your boat in a week” myths.
Hello Hans Jacob,
I am pleasantly surprised to see that there is another Koopmans vessel in “my neck of the woods” – or maybe rather my pond of water – so to speak.
The issue with aluminium, internal ballast and water is regretfully not new to Koopmans vessels. In Iris, the bulk of the ballast is located closed to the centreboard. As far as I know it consists of lead ingots that was fixed in place with molten lead. The ballast is enclosed in an aluminium box that was welded shut and pressure tested. In principle a fully closed structure. Eureka! Not so fast……. When she was on the hard the last time, it was proposed to drill some holes in the hull from the outside, under the ballast and close to the bottom of the vessel. The thought of drilling holes in a fully closed and intact hull pained my heart, but after a bit of deliberation I conceded. And what flows out – yes water. Horror!
Tasting it, it was pure and fresh. It turns out that after 15 seasons in the water with temperature changes, there has been condensation accumulating in the ballast section. We drilled some more holes, and luckily found only pure and fresh aluminium in all places. After drying out the ballast area with air for an extended period, the holes were plugged with aluminium treaded rods, welded shut and primed. From the top side of the ballast the “tank” was now pressure tested and found intact. The last task was to fill the area with oil and reseal. According to the advice from a reputable yard making aluminium sailing vessels, the oil should deter any future condensation. According to them, they also use this method and for the same reason fill oil in among other things the rudders of the vessels they make.
Hope this may be of use and feel free to get in touch directly, should you so desire.
Hi Petter,
That is really great information. Thank you.
Do you know what type of oil the yard uses?
I’m thinking that even though I have not had any problems I might just fill our keel cavity with oil, now that we are seeing some real world experience here.
Hi Petter,
There seems to be something missing from this picture. H2O can’t just materialize in a closed and totally sealed container. If the source of your water was condensation it had to come from the water vapor present in the air at the time the compartment was sealed. Since the purpose of sealing the ballast compartment was to isolate the ballast from the rest of the boat I’d assume that the area remaining outside of the lead would be quite small— certainly not enough to contain the quantity of water (vapor) you describe. And once the airborn water vapor had condensed out into H2O there would be no further liquid production even after decades had passed.
There are only two possible sources of water in your ballast compartment: Chemical reaction between the metals present— ruled out by the atomic structure of the two metals—– and leakage into the compartment from an external source.
As a matter of fact, a sistership to one I built about 30 years ago developed a similar problem, only in that case it was a bolt on keel with the upper half isolated as a fuel tank.
Hi Richard,
That’s a good point. My guess would be a leak from the water tank. If Petter’s boat is anything like ours, the water tanks are integral to the hull above the ballast compartment.
Thanks for engaging, RDE.
You got me thinking; I go along with you, and would like to add another data point. The water that came out was totally pure, clean and fresh. Volume I would guess was 2 ltrs. Ballast compartment holds approx 500 ltrs of lead. Secondly, after having emptied the ballast compartment it was pressure tested for leaks. It held pressure, and I then presume there were no leaks. Right? Any suggestions how this might happen?
Greetings,
Petter 😉
Hans,
My favorite “oil” is automatic transmission fluid and its viscosity should be right for your application. I ‘ve been told it is a very pure “oil” and even use it on the leather seats in my vintage cars. Once asked an 80+ year old horse saddle maker, what he is using for the leather and his answer was transmission fluid. Have use it on all color leather and it soaks right in.
Since a tranny is often a combination of different metals, I can’t see any problems.
John, Rene,
Thank you for taking the time to respond. We take great comfort in hearing about the “disasters” of other boats, boats that have later completed ambitious cruises. I think for the time being we will just keep an eye on things. No oil, no epoxy, and definitely no more sleepless nights!
Hi Hans,
Glad to help. It’s a lot easier to be objective when it’s not your boat! I know I would have been losing sleep, and we can’t have the Norwegian Cruising Guide’s chief correspondent overtired.
I’m sorry to have to say this but lead can corrode aluminium quite dramatically in salt water and the build up of aluminium oxide doesn’t seem to stop it.
Lead is closer to copper than aluminium on the galvanic series and is not passive. The table I use differs slightly from the one John refers to: http://www.engineeringtoolbox.com/metals-galvanic-series-seawater-d_1495.html
Sorry to have to bring this up but the whole point of a forum like this is about sharing our experiences – good and bad.
My boat has internal ballast in the form of lead ingots located in deep compartments in the bilge. After 20 years I decided to open these up to check and found that one of them had some water in it and that the aluminium had corroded seriously here. Luckily the sides of the compartment (hull plating) had been well coated with high-build epoxy / dynel which had been applied when building the boat and this wasn’t affected. I had also placed neoprene sheeting between the lead and the hull to protect the surface coating from damage. Unfortunately I hadn’t been so careful with the transverse end plates. Here there was serious corrosion. There was even a spot where the 8mm plate had perforated. There was lots of white sludge. It was a mess. I do not know how long this had been going on since the boat was 20 years old when I decided to have a look but I’m glad I did.
If I were you I would want to ensure that there was no salt water remaining inside my keel despite John’s good experience so far.
I would suggest using emulsifying oil (“cutting oil”). It would have the advantage of mixing with any residual water that may be in the keel rather than simply floating on the surface. I would fill the keel, leave it for a year and then drain it out to check whether the oil has emulsified with any residual water. If not it can re-used. It wouldn’t be difficult to locate a small reservoir of this oil above the waterline to create a slightly pressurised system. Any drop in level in the ‘header tank’ would indicate a leak in the keel (temperature changes taken into account).
You’re right that this may make future welding more difficult since oils eventually seem to penetrate quite deeply into aluminium and cannot simply be wiped off the surface with acetone. Even after grinding and acetone wiping repeatedly oil-soaked aluminium is difficult to weld.
Hi Pat,
I would agree that it’s important to get all the water out and try to keep it out. We have certainly done that with our boat and our sister ship did the same. And, as I understand it, Hans has been very carefully drying his keel out all winter (he is a personal friend and I have had off-line communication with him).
However, once the area is dry, I’m pretty sure the corrosion potential is not that bad. If it was, then all aluminium boats with internal poured lead keels would be in big trouble, and that’s simply not the case.
I’m really not sure why that is. Perhaps a poured keel self insulates via the corrosion byproducts being wedged tightly between the lead and aluminium.
The other though is that with a poured keel the two metals are not separated by an electrolyte, which is required for galvanic action.
Anyway, while I’m not sure of the reasons, I’m fairly sure of the conclusion.
One thing I would say is that I’m highly sceptical of the corrosion amelioration benefits of coating the aluminium with epoxy. I just can’t see any way to get a good long term bond in that environment.
As to the efficacy of the oil, as I said in my first comment, I really don’t know, but I can’t see how it could hurt, other than the future welding issues. And I like the cutting oil (emulsifying) idea a lot.
Thank you Pat for sharing your experience and I too have quite a number of lead ingots in the alu bilge and will checked it asap. Luckily its slip is in fresh water. Thanks again.
I have lead ingots for trim ballast I propose to move to beneath the engine (there’s a retired keel tank there I would like to fill) on my steel boat. Is there any support for coating the ingots themselves to isolate them from other metals? It strikes me as easier to do a better job than trying to spray or coat areas that are difficult to reach completely and are hard to dry in a measured fashion. Basically, I’m talking about two-part epoxy encapsulation.
I would suggest using Dynel cloth in the epoxy you use to coat the lead.
It ensures you get a good thick even coating of epoxy and resists abrasion really well. It’s also fairly easy to get it to conform to difficult shapes.
Freshly abraded lead seems to bond well with epoxy.
Thanks for the useful suggestion.
Pat and John,
Instead of applying epoxy, what about using some kind of physical barrier preventing the lead coming in contact with the alu hull and will also allow ventilation. Was thinking of the HD open web plastic flooring on the sides and some thicker plastic at the bottom to carry the weight?
I don’t know what I’ve been doing wrong all these years but I’ve had no problem getting epoxy to bond with aluminium and stay there long term.
The best surface seems to freshly ‘sand’ blasted and wiped over with acetone (make sure to use an abrasive that doesn’t contain potentially problematic minerals). I’ve also had success with freshly disc abraded (60 grit). I use solvent free epoxy for the first coat and stipple it on (rather than laying it on with a brush) to ensure that it makes good contact rather than ‘bridging’ the microscopic surface irregularites which increase the surface area.
The Gougeons would suggest using ‘wet and dry’ paper using the resin as the ‘wet’ which I’m sure is good advice but I’ve never bothered.
I’ve also had good success applying a light ‘primer’ coat of hi-build epoxy paint (diluted with about 30% thinners) using airless spray direct to freshly blasted & cleaned aluminium followed up with an undiluted coat as soon as the thinners have flashed off. Followed by at least 3 generous coats on top of this at appropriate intervals. 30 years below the waterline with no loss of paint (except where I’ve grounded on rocks!).
Hi Pat,
I agree. In fact most of my boat is covered with epoxy in one way or another. And I have not had a lot of trouble keeping it stuck on. I use the same techniques you mention. I have also had great experience with the West system two part acid wash treatment and the wet sanding with epoxy trick you mention.
However, we were discussing the bilge area of older boats (Hans and Marc’s). In this case the area has almost certainly been subjected to years of oil and grease contamination. You, yourself, pointed out the difficulty of getting aluminium that has been exposed to such contaminates really clean for welding, ditto for bonding. Add to that the access difficulties in a bilge and all the nooks and crannies you may not even be able to see, let alone clean properly, and I think it unlikely that a good and uniform bond is achievable.
In this case I would argue that coating with epoxy will at best give a false sense of security and at worst allow salt water to penetrate between the epoxy and the metal where it can do damage that will be difficult or impossible to monitor.
Incidentally, although it is not appropriate for this task, in areas like the bilge I have found Plexis a much better bet than epoxy.
By the way, I like Marc’s idea of coating the ballast and your idea of adding cloth makes that even better.
Thanks for the tip about Plexis, John. It sound like useful stuff.
Of course, you’re right about the difficulties that may be encountered in prepping some bilge areas – especially if there has been long term oil contamination (my motor compartment is isolated from the rest of the bilge area and so there has been no oil elsewhere). It all comes down to access, the presence of complications like stringers and so on.
I would certainly agree that not coating is far better than coating onto a poorly prepared surface.
hi,
got the same known problem for the bilges in the Romanee, with the original synthetic keel-bilge sealing starting to crack after 30’years ..
i cleaned it thouroughly and repeated degreasing treatment with all kinds of solvants,… and then poured International Watertite epoxi sealing in the bilges bottom and sides.
it has been a great solution so far and since 3 years no further problems nor cracks
Hi John,
I spotted your site recently following a search on aluminum sailing yachts. I joined shortly afterwards.
I am in the hunt for a used yacht to take my family world cruising for several years. My wish list is as follows:
> Aluminum
> Pilot House
> 55+ feet
> Swing or lift keel (to go into shallower moorings)
> Dutch Build
> Enclosed engine room and forward/rear sealed bulkheads
I have been watching the market for years to be aware of what brands/models/pricing etc. Now, the timing is right for me AND it appears a yacht meeting those requirements has shown up on Yachtworld, but it is a bit old…from 1985 and the manufacturer is no longer in existence. But it was constructed by well know and highly qualified Dutch contractors.
What concerns would you have of purchasing an aluminum yacht this old??? Is there anything specifically you would watch for when viewing/surveying a yacht like this.
Thanks for your thoughts.
– Andy
Hi Andy,
There’s no intrinsic reason that this should not be a good boat. After all look at the post above and our own “Morgan’s Cloud” was launched in 1986.
That said you will need a really good surveyor who will get into seldom seen areas.
Specifically, with a boat this old I would want to know the last time the propeller shaft was removed and the the shaft tube inspected from the inside. Ditto the the centre board case.
After that the issues are the same as for any boat this age and boil down to whether or not she has been maintained and her gear regularly upgraded. If not, sorting that out could literally double the cost of the boat.
For example, those teak decks could be hiding huge problems that, alone, could set you back $100,000 to fix.
Given the age and price of this boat I would strongly suggest hiring Colin to take a look. I know of at least one occasion where he saved one of his clients a fortune, and endless heartache, by identifying the real costs of bringing an older aluminium boat up to scratch:
https://www.morganscloud.com/consulting/
I would also compare the cost of this boat with any upgrades to that of buying a new Boreal. You might be surprised to find that in the end the Boreal will cost you less because the resale price will be much higher.
Disclosure: Boreal are a long term corporate member and supporter of this site and Colin writes for AAC and in a close personal friend.
Hi John,
The aluminum boat hunt is closing in on a target. I am attempting to reach out to Colin Speedie based on your recommendation but, I think my efforts to use his “contact” page are not working (my Mac doesn’t seem to cooperate with his robot/spider filter). Do you have another way I can reach him? Update: I found a sister-yacht of the one I sent to you that appears to be in much better condition and may have a lower sale price! However, it is located in Antigua as opposed to southern Spain. Would you still choose Colin Speedie with the target yacht now being in Antigua??? Thank you, Andy
Hi Andy,
I would choose Colin if the yacht was…on the moon!
I will send you his email address.
Hi John – I have read a number of times in this thread (and elsewhere) of acetone being used as an effective degreasing agent for aluminum – according to the pros at Lincoln Electric where I went for my MIG/TIG training – acetone is a poor degreaser – “just smears stuff around” – at the time they recommended Dechlorinated Brake Parts Cleaner as the degreaser of choice – available at any auto parts store – HOWEVER – if one accidentally uses regular Brake Cleaner (chlorinated) instead – one of the by-products of the welding process will be phosgene gas which is fatal if inhaled in even the smallest of quantities – not worth the risk in my books – instead I have since used a number of commercial degreasers – also widely available – (Canadian Tire carries a couple of different kinds) without any issues aside from drying out my skin immediately- gloves are highly recommended – many are also marketed as being environmentally friendly for what that is worth – another point that my instructors went on about was the importance of degreasing before abrading – apparently oil is very hard to remove once the surface has been scratched – Francis
Hi Francis and Andre,
Thanks for the good advice. All sounds good to me. On the prep side, I have had very good luck with the two part acid etch kits from West System.
Hello from my experience at welding aluminum, the best way to remove grease is with paint thinner – stuff sold in harware store. Thinner leaves nothing… One can use TSP or other degreaser but they will leave some residues. I always use a stainless steel brush to remove some of the oxyde before welding tough. Dilution of phosphoric acid is used prior to painting to make sure the oxyde is dissolved…but beware, in 30 minutes the oxyde is back.
I always carry some paint thinner on my boat in case i need to clean up something. Beware of acetone for its property to enter skin and also play nasty trick with some plastics – discoloration and modification of surface.