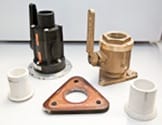
Installing a seacock properly is not a trivial project.
First you need to install a backer plate and then you need to figure out how you will bolt the flange of the seacock down.
Yes, I know that many, perhaps most, boats do not have their seacocks bolted, but that is, in our opinion, a very poor practice since any force coming in contact with the top of the seacock or the attached hose, such as a clumsy foot—a problem I’m famous for—can exert an incredible sheer force on the through hull threads. And if those threads strip, things are going to get very damp very quickly.
Add an aluminum hull and a seacock that is made of bronze, like most of those in Morgan’s Cloud, and you need to figure out a way to keep the two electrically isolated. (See the pictures at the bottom of the post for how the bronze seacocks on Morgan’s Cloud are installed.)
Oh yes, and you need to make sure the seacock that you are about to install really is bronze and not some form of brass. This is particularly a problem in Europe where valves are sold for marine use as “tonval bronze”, which is not bronze at all, but brass.
Brass is really bad news in salt water since the zinc leaches out of it leaving a spongy and weak potential boat-sinker behind. One more thing: if you tee something off the seacock you will use a nipple and all nipples except t hose made by Groco, at least as far as I know, are made of brass, not bronze, so watch out for that.
With all of the above metal seacock hassles, when we needed to install a new seacock for the drain required for our new separator exhaust system, we decided to give a Forespar seacock made from Marelon, a tough plastic, a try. An experience that can only be described as “out of the frying pan and into the fire”.
The installation manual said:
If it is desired to additionally fasten the king-nut to the backing block with screws, there is provision for such, but it is completely unnecessary.
Not only do we believe the above instruction to be just plain wrong, particularly with a plastic through hull, we don’t believe fastening with screws is adequate either. We through-bolt our flanges (king-nut) to the backing plate.
Wait, it gets worse: Despite the above assurance, there is no practical way to actually accomplish the above since one of the four holes provided is obstructed by the handle and the flange is so small in the way of two others that there is no way to get a screw head, never mind a washer, to bed in the space allowed. Despite this the manual states:
On the backside of the king-nut there are four (4) blind ¼” holes. These may be drilled through to the front side before installation to allow for round-headed screw fasteners.
I suspect that the non-functional holes and the associated text in the manual are only there to serve as a fig leaf—you were wondering how I was going to work that in, huh?—so that the company can say “Well, you could have bolted it down”.
This otherwise excellent product has been let down to save a few pennies by not providing a decent flange for proper fastening–a real pity. See the photos below for how we solved this problem.
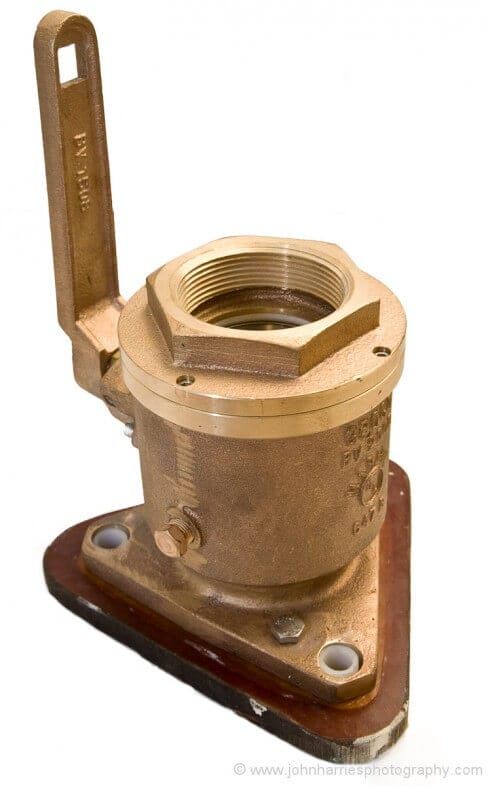
The mounting holes have been bored out oversize to take insulating sleeves. This reduces the “meat” around the hole, but we feel that the addition of large washers will make this safe.
(The original seacocks, also from Groco, installed in 1984, had much wider flanges—just another way that cost cutting diminishes a good product.
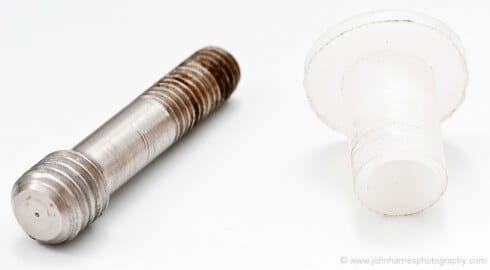
The plastic sleeves with shoulder flanges isolates the seacock from the hull.
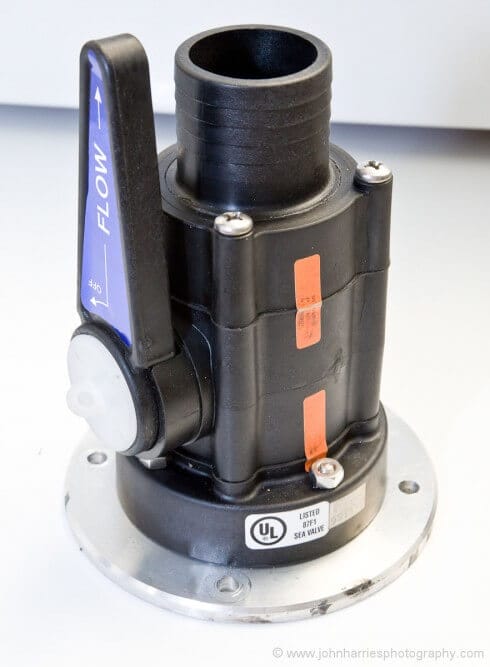
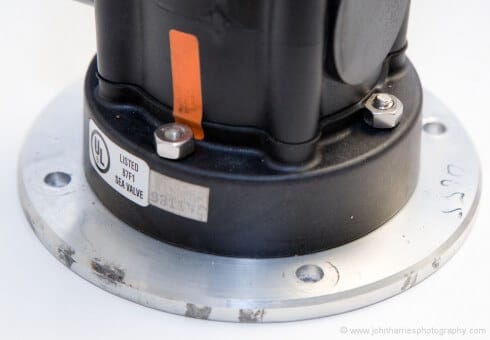
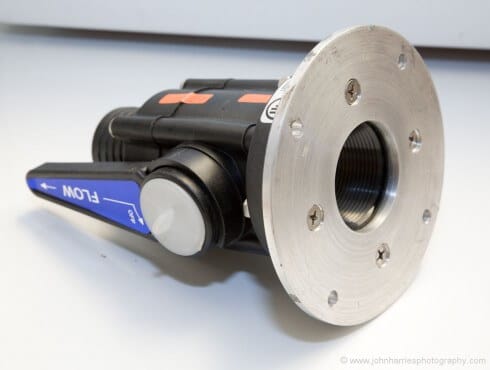
The four unused (in this picture) holes will take hex head bolts to fasten the plate down to holes that were bored and threaded into the backer plate before it was welded into the hull.
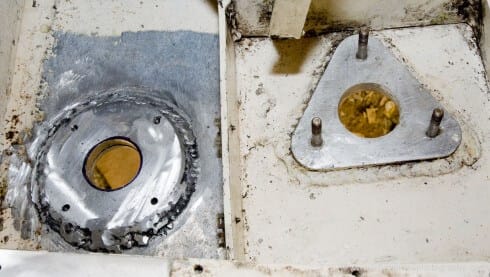
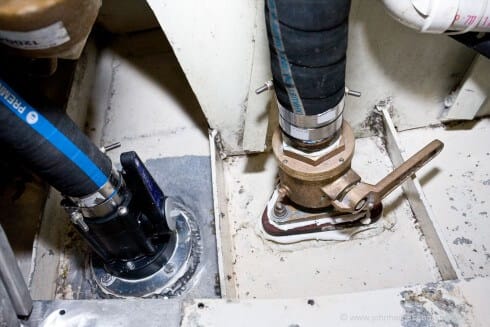
Here’s a good description and pictures of an install.
http://www.pbase.com/mainecruising/replacing_thruhulls
Here’s a link to his other projects
http://www.pbase.com/mainecruising/boat_projects
I appreciate your problems, I have used Marlon seacocks on our aluminium hull and welded a heavy wall (1/4″) 1 1/2″ threaded tube stub straight into the hull, keeping it very short so as to reduce the bending moment you rightly worry about. Then you fit the seacock with a backing nut so that you can position the handle in the correct orientation. You can weld a heavier disc of aluminium over in an over size hole if you wish to spread the load even more. This way you have none of the problems you are experiencing with isolating dissimilar metals, numerous holes for screws etc. and no possibility of leaks around the spreader/ backing plate. A Forespar seacock is able to be serviced as well. The cry that plastic seacocks melt in a fire are fine but, to be fair, if the fire is so intense that it melts a water filled seacock then you have a larger problem than the seacock failing. My personal solution was to have no seacock in the direct engine space.
On Aluminium and steel boats we have added gusssets between the pipe and hull along half the length of the pipe that brace the short length of Pipe to reduce the bending issue. We also use Schedule 80 PVC ball valves that are above the waterline on Aluminum hulls. if it melts it may put out the fire. Hooray! then we stop and worry about sinking!
Hi Andrew,
I like the idea of the welded tube stub.
However, I guess that, even with your very fine system, I would like to see the seacock bolted down, as ours are. The bolts are not a problem in that they are only into the backer plate, not through the hull.
By the way, we really have not had any “problems isolating dissimilar metals”. In fact, after our experience of dealing with the challenges of plastic, if I were doing it again, I would go back to bronze.
I think the ultimate system might be stand pipes bringing the seacock above the waterline, like on the Boreal.
Like you, I don’t worry about fire and plastic seacocks much. Even with metal seacocks, like most of those on MC, the hoses are going to burn through anyway. And it is likely that the seacock will be both open and inaccessible in a fire.
A few questions please? After your seacock installation on Morgan’s Cloud will you leave them open to the sea or will you fit an external strainer? I have an aluminum boat in the yard and feel that the strainer is not a good idea if we have the stand pipe fitted as we can rod the stand pipe clean. Why two different brands of sea cock, The Marelon and the Bronze? Steve Dashew has a lot to say on the subject on his new FPB.
Hi Peter,
The bronze was to replace an old seacock (24 years) of the same make that was worn where the handle engages the ball. We decided to try the Marelon for a new seacock required by our new exhaust system, as a supposedly easier installation option since no isolation would be required. However, due to the poor design of the flange, it was actually harder to install it properly than a bronze one would have been.
No we do not have strainers on the outside. Just another set of complications: how do you fasten them? What material? etc.
Occasionally we will get a lump of weed blocking an inlet, but not often. When this happens I just pull the hose off and poke it out and shut the valve quick. I also have a wood plug at hand, but have never had to use it. Sure, you get a bit wet, but it is a lot less dramatic than you would think. However, I would not try this with a seacock over say 1-1/4″.
Honestly the only way to go is seachests welded to the hull if possible coming up above the water line with access at the top so you can check and or clean you strainers then you can get all your raw water for engines, a/c ,saltwater wash down ,head ,gen,ect. Directly from the chests without worry.
Hi Arthur,
I agree, and if I were building from scratch I would certainly consider a sea chest.
Right you are Arther,
And then you add a blow-down port on top— air if you have a big compressor, or large volume water from your emergency bilge pump. Now you can blow the seaweed off your hull surface mounted pre-strainer without getting wet!
Now there’s a great idea!
Hi John,
Not my great idea! I just had the benefit of working on a project where the owner always hired three or four different designers to solve every problem he could conceive of—.
I remain a strong believer in standpipes such as I had on my aluminum hulled Nomad. All discharges went down one standpipe, each with a valve and vented loop. The various intakes were also in a standpipe with dip legs below the water level. I had vented loops in all discharges and intakes. I had no problems with poor engine cooling or other sea water uses, but this could be a factor in other situations. With the standpipes near the centerline, I had no worry about hose breakages or back siphoning at any angle of heel. The standpipes were anchored to the aluminum hull framing, so there could be no high torques.
Ed
I have found an interesting seacock / valve solution in my aluminum boat. Short aluminum tubes (7 to 10 cm) are welded to the hull, somehow PVC fitting and GF ball valves are attached to this tube. I have not dismantled the valves yet as the boat is still in the water and I just bought it half year ago. But this configuration lasted 30 years and is still tight and dry.
Hello all,
this Winter I will need to replace all thru hulls and seacocks on my 45′ Jeanneau from 1998 (solid grp hull). My current thru hulls and seacocks are all 316 stainless and I installed them myself in 2006/2007, replacing the original brass. This was when I still believed 316 stainless would not corrode and, again, long before I learned about this site as well as Rod Collins’ excellent instructions, such as this one: http://www.pbase.com/mainecruising/backing_blocks
That replacement was in a mild panic after, on the hard, I wanted to change a hose for the refrigerator intake, removed the hose clip and pulled on it with one hand. Whoops, I had the hose, the seacock and half of the thru hull in my hand and I could see the floor of the shed through the remains of the thru hull. See here for a serious case of osteoporosis:
https://td2ec2in4mv1euwest.teamdrive.net/primespace/public/67443/TZBZ50Z00P91U0056VXCAHM190K9VMS6/20160718_073153.jpg
I discussed with the yard manager if I should use bronze or stainless (I wasn’t aware of plastic at the time) and he told me “with stainless you may have problems, with anything else you will have problems”.
5 years later I discovered quite severe crevice corrosion in the threads between thru hull and seacock in two cases and now, after 10 years, more than half of the total of 16 have more or less serious corrosion problems as can be seen here:
https://td2ec2in4mv1euwest.teamdrive.net/primespace/public/67443/QMX8GX000P91U0056VXC9DBE50K9VMRN/20160708_155919.jpg
https://td2ec2in4mv1euwest.teamdrive.net/primespace/public/67443/9K1C4M800P91U0056VXC9ES0R0K9VMS1/20160708_155933.jpg
https://td2ec2in4mv1euwest.teamdrive.net/primespace/public/67443/87FACQG00P91U0056VXC9DRHP0K9VMRQ/20160708_160015.jpg
https://td2ec2in4mv1euwest.teamdrive.net/primespace/public/67443/4B0AVDZ00P91U0056VXC9E7SA0K9VMRU/20160708_160100.jpg
I turns out that using hemp hair and mastic, like plumbers do, is worse than using polyurethane sealant on the threads as the hemp saturates with (salt-) water in order to work and that’s your salty and oxygen-starved area right there.
Also, all but two of my seacocks are in an area with significant hull curvature and that makes for a really bad connection between the mushroom flange outside and between the backing nut and washer inside and the hull. With such a flimsy assembly, it’s hard to correctly position the valve handle, too. You really have to thread the ball valve onto the thru hull while its still loose and then fix everything with the thru hull’s backing nut – not easy.
Even back then I thought “this is bad” and “there must be a better way” but I carried on, believing this was the only way to do it. 10 years wiser now, in a similar situation, I would just stop and rethink and, also, I would have replaced only a few and waited a couple of years to find out how it’s working.
As for replacement, it seems that these are my options and I’m not really happy with any of them.
I will make strong backing plates from GRP board (sourced or laminated myself) this time around, fitted to the hull curvature and epoxied in place, so that will make even a non-flanged thru hull seat better.
1. Forespar 93 series (“OEM”) Marelon plastic
The Forespar managers at METS 2014 strongly favored this line (“You will get the OEM line, will you?”) but I did notice the flimsy flange and the fact that one hole is blocked by the handle. My feeling is that with a backing plate nearly an inch thick, I could cut a metal thread into the GRP of the plate (as Rod Collins suggests) and use allen-head bolts inserted top-down (unlike what Rod suggests – they would have to be cut to the precise length). And can you not disassemble the whole ball valve and thereby get at the blocked hole?
2. Forespar MF849 (non-OEM) Marelon plastic with large flange
These have a beautifully large flange but they can’t be disassembled and were not recommended to me at METS. Also they are not available in 1” size, which I would need for the sink and washbasin drains and the engine and generator intake.
3. Trudesign with “load bearing collar”
I agree that these are higher-precision, better tooled than Forespar and there is a complete line of accessory fittings. That was also what their staff told me at METS in response to my question “Why should I buy yours and not Forespar?” But they moaned and rolled their eyes when I asked “What models do you have with a flange?”. They don’t and claim that the load bearing collar gives equal or higher strength to shearing loads while being easier to install.
On their display, I noticed a small clearing between the collar and the hull and between the collar and the seacock. Given the reduced strength of plastic vs. metal, I would think that the whole assembly, if loaded heavily sideways on the hose, would flex by as much as 10°. I don’t think that would cause the thru hull to break or the threads to strip but it would be pretty close.
Also the plastic thrugh hull with backing nut will make an even more fragile bond to the hull (because the plastic mushroom flange and plastic backing nut will flex more in response to the point-loading caused by the hull curve than metal would), but I would partially address this by using a backing plate.
But really, what I want is for the actual thru hull fitting to be optional to the integrity of the hull – just threaded in at the very end for good looks.
4. Groco bronze ball valves
I have no experience with bronze but I don’t think they will be as corrosion-free as plastic.
They seem to have completely solved all issues like separating the flange from the ball valve, separating parallel threads from concical (NPT or BSP) and bronze hose nipples.
They are not common in Europe and there is no similarly complete maker here, so I would have to special order from the US.
I really have to trust your advice on the longevity of bronze but please understand that I *really do* want this to be the last EUR-3000-and-50-hours-of-labor-replacement of seacocks that I do in this life.
5. Blakes
Available off the shelf here but, as far as I can see, really only suited for wooden hulls.
With all options except for Groco, I would have to fit a strainer to the outside of the hull for the intakes of engine, generator and refrigerator as a separate part with self tapping screws into the hull lamiate which I would hate to do.
So what to do?
Hi Henning,
Wow, what a hell of a road you have been down with this. Having read through your whole excellent analysis of the options, and given that you only want to do this once more, I would recommend going with Groco. Simply the best option. As long as you don’t have any trouble with stray current corrosion, the Groco bronze seacocks will outlast both of us, and, as you point out, they have the whole thing thought out, right down to the backing plates. If it were me, I think I would use their backing plates attached to the hull with epoxy. You could thicken the epoxy with a high density filler to fill any gaps caused be hull curve. Done this way, you don’t have to drill holes in the hull for the flange bolts.
As to the longevity of bronze. I have bronze seacocks in Morgan’s Cloud that are 30 years old and show no signs of corrosion. The only reason that I have replaced a few is because of wear between the ball and the actuating handle, and Groco have improved that in their new offerings, so you will be able to put these seacocks in your will.
Hmm, excellent (if expensive-sounding) analysis, Henning. Thank you for sharing it.
John, how do you separate the bronze seacocks from the aluminum hull? I have bronze seacocks (they look like Groco, but I haven’t confirmed this) on steel threaded pipe for my two sink exits and bronze cocks off teed off the standpipe and while there’s no sign of issues, I am considering taking everything off in the winter for a thorough inspection prior to salt-water. Any thoughts or comments on the separation of church and state are welcome from the real world.
Hi Mark,
Please read the post above.
Whoops, OK, thank you, John. I’m already into the McMaster-Carr catalogue for bushing or “sleeves” as the Brits call them.
Hi Henning.
I have replaced most of my seacocks as follows:
Blakes for heads in- and Outlets. This was an unnecessary expense as the original Blakes were in perfect condition after 15 years and and a circumnavigation. A friend was delighted to be given them. My previous boat also had Blakes and they were perfect after 15 years. Both boats were/are grp so not sure why you believe they are only suitable for wooden boats.
TruDesign for most others. I think that to call them “plastic” may be unfair. They are glass-filled Nylon. They are also tested with the equivalent of a man standing with his Weight at right angles to the shaft. I suppose it depends on where your seacocks are installed, but Mine are all in places where it would be nigh impossible to stand on them. The mechanical efficiency/strength of their fastenings is also difficult to fault. Strong, corrosion free, not Prone to seizing, they certainly have my vote.
Yours aye
Bill
To add to Bill’s helpful comment:
We have a GRP Beneteau 473 – when we bought her the surveyor advised we replace two bronze-fittings immediately before re-floating as they had gone to soft copper. Having had this “wake-up”, I replaced all the through-hulls two years ago using Trudesign fittings throughout – no metal. I used the models with the external flange rather then the recessed type. Many of them were installed on the curve of the hull-side, some on the flat bottom. I found the units to be very robust when tightening, and though none are in a position where someone could put their full weight on them, but I would be confident they would stand up to such treatment. The key for me was to bed all fittings in with a self-curing silicon adhesive which filled any slight crevices and created a very solid but still slightly flexible joint. I used the 3M 5200 product – the only problem being it stuck to absolutely everything so you need to be diligent (I got through half a box of surgical gloves)!
Also, the fittings received the subsequent new anti-foul undercoat extremely well, outside and in, with no sign of peeling or erosion of the paint two years on, and the valves are all working as smoothly as when new. So they get my vote too Bill.
Hope this helps.
Rob
Hi Rob,
Just to clarify so that bronze does not get a bad reputation, the original fittings in your Beneteau were almost certainly not bronze but brass. The use of true bronze in new boats, particularly in Europe, has been for some years now pretty rare. Of course that doesn’t stop the manufacturers from calling brass by fake names, see the post above.
If the seacocks really were bronze you would not have had to replace them.
Also, while I am being pedantic, 5200 is not silicon based, it’s a polyurethane. I bring this up, because as far as I know, silicon based products should not be used under the waterline. Also silicon based products can’t be painted.
I am pretty sure that the through hulls were bronze John, as I went looking for replacements in the chandlers and found identical ones in bronze locally. But they were all coupled to stainless seacocks (how dumb), hence I believe their various degrees of breakdown. Had they been coupled to bronze or TruDesign seacocks I believe your statement would have been correct. Going through the same process as Henning two years ago, I just decided to get rid of as much metal under waterline as possible, and having a GRP boat meant that having nylon reinforced plastic/glass fittings didn’t seem out of place (especially as the TruDesign fittings have Bureau Veritas and EU certification).
You are of course correct on the 3M 5200 product which is designed for marine applications above and below the waterline and is as you say Polyurethane based – my error.
Cheers
Hi Rob,
You may be right that they were bronze, but it’s worth knowing that just because the bin at the chandlers says “bronze” does not make it so. For example tonval bronze, often sold as bronze is actually brass.
Hi All,
I agree that composite seacocks are compelling (I have two). I just wish that a manufacturer would come up with a quality composite seacock that has a proper flange for easy bolting, like the Groco. I just can’t see that if it was never considered safe to install a bronze seacock and through hull without bolting that it is now suddenly OK to do the same with a composite seacock and through hull, particularly since I’m pretty sure the composite through hull and threads will not be as strong as the same in bronze.
To me this is just another example of the continuing reduction in quality of boats and in many cases the standards that govern them. For example, I understand that the common practice in Europe now is to allow builders to use brass (tonval bronze) and then regulate that said fittings should be replaced every five years—outrageous in my view.
Maybe I’m old fashioned, but I still recommend bolting, as detailed in the post above, and still feel that the Groco line is the ultimate in seacocks and through hulls.
Thank you John, Bill, Rob,
I think a good thru-hull and seacock install should have these attributes:
a. everything is solidly mounted, not just strong enough but 10 times stronger than it needs to be
b. minimal chances for corrosion
c. the seacock handles can be positioned exactly as needed
d. available options to fit any installation requirement, e.g. a 90° turn between thru-hull and seacock, all required sizes and outside strainers that don’t require screws tapped into the laminate
e. thread types must match (parallel to parallel, conical to conical)
f. the installation can be done straightforward and relaxed, with no luck involved or high-stress, alone or with minimum help
g. all parts can be disassembled without destruction and even (theoretically) reassembled a second time
h. the seacocks can be serviced and have a drain for winterizing while afloat
i. any “goo” used should be used sparingly and for sealing purposes only, not to achieve mechanical strength. The seacock should be bolted on, not glued on.
My existing install is a complete failure on all points except d.
The thru-hulls and backing nuts don’t sit evenly on the curved hull in many cases. There is some flexing and point loading. I have mismatched threads. I have severe corrosion. During the install I was bathed in sweat many times, stressed, disgusted and cursing. The outcome is far below my standards.
So this time I’m not willing to compromise. If it’s not coming out right, I’ll pull it out again or stop and if spring comes around and I’m not done, then the boat will spend the season in the shed (I think they give summers away).
The seacocks will be bolted to backing plates epoxied to the hull. The handle position will be exactly as I want it. The thru-hull will go in last, after the hose is on. I will use minimal sealant, between the mushroom collar of the thru-hull and the outside of the hull only, not on the threads. If there’s any part I don’t like, I will take it apart again (everything will come apart easily) until I’m happy.
While I would trust fibreglass reinforced plactic enough and also feel that a plastic boat and plastic seacocks are a good match, from my perspective this means that I can’t use TruDesign for lack of a flange and the Forespar MF849 (not “OEM”) as this fails on points d. and f.
I don’t like to drill holes for bolts through the GRP hull so I’m crossing Blakes off my list, too. That leaves me with Forespar 93 series (“OEM”) and Groco Bronze.
Forespar has problems with points a. and d.
Groco has a possible problem with b. (e.g. in case of galvanic currents) and excels everywhere else. And it’s recommended by John.
In my professional life as an IT consultant I frequently wonder why clients pay me to consult, then don’t follow my advice. So in my private life, I guess I’ll do as John says. After all, I’m paying an AAC membership fee 😉
Hi Henning,
Don’t feel bad, I used to do IT consulting to and they never listened to me either, that is until they had a disaster. That in turn led to our unofficial company motto: we don’t do business with virgins. I digress.
Glad that we were able to help on sea cocks, although I hope that my fixation on bolting them does not lead you to lose a sailing season.
Anyway, good luck with the project. When you are done it would be great to get a report here.
Hello John and all,
I am a recent new member and have been enjoying all of your wealth of information. My wife and I are at the contemplation and education stage of moving up to a larger (power) boat which we would have done in aluminum for sure (currently have fiberglass). To that end I have read many books and web articles on the topic of aluminum boat construction in the last couple of years and, with that as my sole reference, I very humbly would point out that the picture of your newly installed (welded in) backing plate jumped out at me.
Assuming what I have read is correct the preferred way to install any increase in thickness in an aluminum hull is to weld in a single plate in the area which is the desired overall thickness required and to have a taper of at least 3 to 1 down to the thinner surrounding that you are welding to. The reason is to avoid crevice corrosion between the plates and spread the stress load(s) out in the transition.
When I envision the mechanical logistics of your new backing plate (as best as I can see in the pictures) it appears the crevice corrosion problem would be exasperated by the upward pressure on the recessed screw heads whereby the backing plate is being pulled away from native hull plate when under load from the nuts (albeit at a microscopic level) – and – the void created by the screw heads themselves provides a larger area for moisture and oxygen to collect between the plates. So if a thicker homogeneous plate had been welded in and tapped and threaded for the studs this would have avoided that potential problem.
I only comment in case it helps anyone out or at least gives food for thought. I would certainly want to discuss this with an experienced metal boat builder for a second opinion before judging. The idea of ‘bomb proof’ aluminum boats seems so appealing but the devil is always in the details as they say.
Thanks again for the great site.
Respectfully,
Jason.
Hi Jason,
You might be right, and I did fuss a bit about the void between the two plates. That said, after 7 years there’s no sign of any issues. (I check that kind of stuff yearly when I clean the bilge.
Also, I think I’m right in saying that crevice corrosion is actually a problem with steel, not so much aluminium. And after all the entire boat is welded, so why would those welds be any more susceptible than any other?
One thing I have learned in 25 years on aluminium boat ownership is that the stuff is way more robust and corrosion resistant than most people think it is, as long as you don’t allow stray currents to flow.
As to cutting a big hole and welding a thicker plate in, I don’t really like that much, particularly without a safety overlap. Old aluminium plate is actually quite difficult to weld to and get a perfectly watertight weld.
With the way we did it, we did not breach the watertight integrity of the original plate.
All that said, I guess if I were doing it again today I might not weld at all, but instead glue the seacock plate down with Plexus:
https://www.morganscloud.com/2008/02/01/plexus/
Thank you John and the rest of the commenters. As an American, about to replace the seacocks on a hopefully-new-to-me 47 foot fiberglass sloop, this is quite timely. I feel lucky that Groco is what is typically used in my part of the world. Having overseen multiple refits on motor yachts that I have run or crewed on, this is not a topic that I have really given much thought to before recently. It has always been “trust the boatyard while looking over their shoulder” and I’ve rarely seen much to warrant further investigation. Although, there was a boat I ran recently that had a grate-type bronze intake grate screwed into the solid glass keel with wood screws (!!) that backed out and gave me a pinhole ingress into the hull. That was fun! I whittled a bung from a pallet and it held for a week while we waited for our haul out. Yikes. The new grate was properly through bolted, but I’m still a bit leery toward extra holes in the hull.
Hi Taylor,
Thanks for the thanks, much appreciated. I agree with being leery about holes in the boat, additional or not, the stupid stuff I found on our new to us J/109 was sobering indeed.
I just had the handle of a 3/4” Marelon seacock shear off in my hand with not much force. I’m switching my remaining couple of Marelons to Groco bronze. I’m planning to epoxy their mounting plates with insert nuts to the hull, does anyone have any positive or negative experience with them?
Hi Matthew,
Bummer. I have had good luck with Marlon but I agree the handles on the 3/4″ are a bit flimsy. I have two on the J/109 and so will order a spare, so thanks for the warning.
As to Groco, I’m a huge fan. They lasted over 30 years on the M&R 56 and the new ones are even better engineered (I replaced two). Simply the best, by far.
John,
It’s not clear from the photos if — for the bronze peacocks — you also use a bronze through hull fitting that screws into the valve itself from outside the hull? Eg, these from Groco: https://www.groco.net/products/fittings/thru-hull-fittings/th-series
If you do use such a through hull fitting, how do you ensure separation of different metals? Just a generous amount of marine sealant? Or something more specific?
Alex
Hi Alexander,
We make sure that all of the fittings under the water are either plastic or bronze, to the point that in one case I had to have a couple of nipples machined in bronze. That said, most of what we used were from Groco. Great company.