Question: I was wondering if you think the engine should be grounded to the hull or not [on an aluminum boat].
Answer: Definitely not, in our opinion, the engine chassis should be carefully insulated from the hull. Further, the propeller shaft should be insulated from the engine. (The easiest way to do the latter is with a DriveSaver).
What we are doing here is making sure that no metals that are more noble on the galvanic series are immersed in the same body of salt water and connected together.
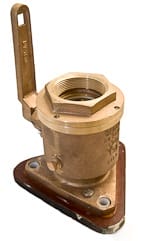
One of the above conditions is OK, but not both. For example, Morgan’s Cloud has bronze seacocks, but even after 24 years there is no sign of any corrosion around them. The secret is that they are very carefully insulated from the hull using plastic through hulls, a spacer plate and insulating sleeves around the mounting bolts, so that there is no completed circuit between the bronze and the aluminum.
However, if you ground the engine to the hull, an electrical current can then run from the hull though the seawater to the bronze and steel in the engine’s salt water cooling system and back to the hull through the connection. You have constructed a battery and the least noble metal, in this case aluminum, will be eroded.
Of course if the boat is protected by hull zincs, as it should be, they will go first since they are even less noble than aluminum.
Isolating the shaft from the engine is a “belt and suspenders” approach if the engine is isolated, but well worth it since if the shaft becomes connected to the hull, the damage is likely to be inside the shaft log, usually consisting of a piece of thick walled aluminum pipe welded into the hull, a very difficult and expensive thing to repair.
We are pretty comfortable with our position on this, as detailed above, particularly since it seems to have worked well on Morgan’s Cloud for over 20 years. However, it is a complex subject, so if anyone has anything to add, please leave a comment.
I’m curious how you’ll handle the alternator and starter on the repowered Morgan’s Cloud. Are you using true insulated-ground equipment for these tasks (thus electrically isolating them from the engine), or are you grounding the alternator in some other fashion?
Hello John,
I asked the original question. I had a follow up to your response which I’ll post here:
Front up, “Definitely not, in our opinion, the engine chassis should be carefully insulated from the hull.” is exactly what I figured too.
The trouble is, it’s very difficult to insulate the engine from the hull. My boat came with a solenoid to disconnect the ground which I now can do via a normal battery mains switch. However, even with both terminals disconnected, I ended up with the charging system providing an electrical path. If there is any path, it seems better to fully ground the engine to the hull and when not running the engine, close the (plastic in our case) seacock.
I’m interested if, when shutdown and in fully disconnected mode, you have tried to measure using an VOM meter whether your engine is anyway grounded to your hull?
What’s funny is, I’ve never found THE authoritative, scientific reference to the right answer. And you’d think there was one. I’ve asked aluminum workboat builders and they seem pretty unconcerned actually. Maybe someone will chime in on your website.
Thanks again,
Blake
Hi Matthew,
Yes, we are using an isolated ground starter motor and alternator. In fact the whole electrical system on “Morgan’s Cloud” is isolated and floating. Not easy to do or maintain (we check it every week) but well worth while on an aluminum boat.
Hi Blake,
There are really two different issues here: Isolating the engine from the hull and isolating the entire electrical system from the hull and the chassis of the engine. And yes, it is really hard to do, particularly as a retrofit.
However, I really believe that it is best to do both on an aluminum boat. On “Morgan’s Cloud” I just last week changed one of our four hull zincs for the first time in 20 years! (The other three are fine.) This shows how inactive the boat is with everything carefully isolated and the electrical system floating.
And yes, we do check both of the above with a simple LED light system that I built. We also check that our zincs are working correctly with a silver/silver anode and a meter.
You can get away with less, but at the very least you will go through more zincs and at the worst real damage can occur.
I know that the commercial guys are less concerned, but keep in mind that many commercial boats are considered to be at the end of their lives after 20 years. Also, commercial operators of both steel and aluminum boats seem to be perfectly happy to replace plate, regarding it as a part of general maintenance.
Hi John,
I can see the benefits of a floating DC system, although it seems to worry some electrics professionals, but isolating the engine chassis from DC negative would appear to be problematic if the engine has glow plugs for cold starting.
However, is it not true that with an engine isolated from the hull and a floating DC system, an engine ground to DC negative would only be current carrying when glow plugs were in use, and in the case of an engine-grounded starter, when the starter is powered up, i.e, only on engine starting? If so, this constitutes such a tiny proportion of a boat’s life that one would think it could be tolerated.
Alan
Hi Alan,
There is no reason that I know of that an isolated DC system should worry electrical professionals. An isolated AC system would be dangerous. However, on our boat the AC ground and neutral wires are tied together and grounded to the hull at a single point, as called for in ABYC specifications. This will not cause any corrosion problems as long as you have an isolation transformer, as we do, and all the AC/DC equipment on the boat, such as chargers and inverters, keep the DC and AC grounds separate, as they should, and normally, do.
You are right about the glow plugs. An isolated ground engine like our Perkins has neutral wire attached to the block interrupted by a normally open relay that is wired so that it pulls for as long as the glow plugs are energized.
In the case of a case-neutral stater motor, you could do the same thing, although the relay (sometimes known as a solenoid) and the wiring will need to be sized heavily enough to take the high current required by a starter motor.
Don’t confuse this system with one where all of the sensors on the engine are case-neutral and the relay is energized for the entire time the engine is running. In our opinion such a system, while better than no isolation, is not the answer for an aluminum boat.
Hi again John,
I should say that I am no expert on boat electrics. Most of what I know has been gleaned from Nigel Calder’s writings, and I may not have always understood.
The concept of making and breaking the engine block to battery negative connection according to the needs of the glow plugs seems very sensible.
Have the ABYC recommendations changed with respect to grounding? I ask because they used to suggest connecting the AC grounding wire and neutral at the boat side of the isolation transformer (essential) and then making a connection between that point and DC negative/ground at a single hull zinc. This also makes sense to me because as NC asks, without connecting the two grounds where does an AC leak into the DC system go (from a faulty charger, for example)? There is a risk that it will seek a path back to the isolation transformer through a crew member.
Like you, I have never fully understood why floating DC systems sometimes cause professionals to pale, but I suspect it is precisely because it suggests that the AC and DC grounds may not be connected.
Incidentally, NC makes a second case for connecting the two grounds based on the need to hold them at the same potential as part of a lightning damage control system. I am straying into, for me, a very arcane area here, but I assume that is the only reason to ground the AC system to the hull (as you do), and thus to the DC system if it is also not floating (not your situation). This begs the question – what purpose is served in Morgan’s Cloud by bonding the AC ground to the hull?
As others appear to be, I am rather surprised by the fact that it is difficult to obtain definitive answers to some of the questions that occur in this area. If you can offer some, I would be grateful for them.
All the above of course assumes an isolation transformer is part of the system, because, if you will pardon the pun, this changes the ground rules.
Alan
Like you, I’m not an electrical engineer, and so really can’t give you any definitive answers. Anyone wiring a boat, particularly the AC system, which can kill you, should buy and use the ABYC specifications, or equivalent. Having got that out of the way, here is what I think I know. Note that all of this assumes a metal hull and an isolation transformer.
1). Grounding the AC neutral and case grounds to a single common point on the metal hull is vital. This creates the path that will blow a breaker if the live wire touches case ground or the hull.
2). I can see Nigel’s point about the DC ground being attached at the same point since, without this step, it is possible that the DC system could carry an AC voltage if a charger or inverter failed. On the lightning issue, I don’t think keeping the AC and DC systems at the same potential matters so much on a metal boat since the lightning strike will be carried by the hull. In both of these issues, keep in mind that Nigel is not a metal boat owner.
3). As I have said before, grounding the DC system on an aluminum boat to the hull is, in my opinion, a bad idea that will, at the very least cause more zinc use, and could damage the hull. As far as I know, all of the good European metal boat builders install isolated ground DC systems as well as a system to warn you if this isolation becomes compromised. By the way, I think I’m correct in stating that the same hull short warning system would warn you in a case where a faulty charger or inverter had connected the AC live to the DC system. That is as long as the AC neutral was grounded to the hull.
Thanks John. It has been an interesting and useful discussion.
It is clear that insulated returns are essential on an alloy boat. And you make the case well for also isolating the engine block from the hull if at all possible.
What is less clear is the wisdom or otherwise of connecting the AC and DC grounding systems.
Perhaps Colin can tell us what Alubat do?
Alan
Hi Alan,
Perhaps I did not make myself clear.
If you connect the DC neutral to the AC neutral and AC case ground at a common point, as you would on a fiberglass boat, you will no longer have a floating DC system since the AC MUST, for safety, be grounded to the hull at that single point. Sure you could float the entire AC system, but then if either leg comes in contact with the hull no breaker would trip and you would have a trap just waiting to kill.
Note that I’m not saying that this is what ABYC or Nigel, or anyone else, defines as good practice. I’m just pointing out an inescapable fact: You can’t have the AC and DC grounds connected AND have a floating DC system.
What you could do, at least in theory, is use a large capacitor that will pass AC, but not DC, to ground the AC system. However, I would not recommend this since if the capacitor ever goes open circuit you would have a potentially lethal situation. Also, the capacitor would need to be very carefully sized to make sure that it would pass enough current to trip the largest breaker on the boat.
To take this any further I think we need a professional electrical engineer with knowledge of marine standards. Anyone out there?
Gentlemen
you need to correct your terminology as the writings above can be mis-understood.
A DC system has a POSITIVE and a NEGATIVE, it does not have a neutral or a live or a ground.
An AC system has an EARTH/GROUND, a LIVE and a NEUTRAL.
Radio and navigation systems may have a “RF Ground” which should be via a grounding plate.
Please do not confuse negatives, neutrals and grounds as being the same, they are not.
Aluminium boats, in the UK, are wired as follows.
AC system
EARTH/GROUND connected to hull for electrical safety.
Live and Neutral are both isolated from EARTH, unlike in a UK domestic house environment where Neutral is connected to Earth.
LIVE and NEUTRAL circuit protection must be via double pole circuit breakers as the Neutral will still have potential if only the live is isolated.
Shore supply must be via Isolation transformer.
DC System should be fully insulated from the Hull.
Negative must not be connected in anyway to the hull or AC Earth/Ground.
Insulation monitors are available and we tend to install both AC and DC monitors on Aluminium workboats now.
regards
Kevin
http://www.yachtbits.com
marine electrical and electronic systems
UK
Kevin,
Can you explain why you advocate not connecting the AC neutral and earth on the boat side of the isolation transformer and then jointly grounding to the hull?
Concerning monitors do you have any recommendations?
Alan
Alan
On the whole issue of earth or ground (depends on which side of the Atlantic) it is vital that you, as we have on “Morgan’s Cloud”, follow a recognized standard such as ABYC when installing an AC system. Electricity at 110 volts or worse still 220 is dangerous stuff around salt water and you don’t want to be messing with it using information that you get from this comment stream.
Some of the information in this comment stream on this subject is correct, but some is not.
This post was about DC systems and isolation, not AC systems.
John,
Do people always use double pole breakers on a floating DC 24 volt system, on the branch circuits.? If so Why? I understand they are now two ungrounded conductors , but the return path to the batteries is the same. I am trying not to double the size of my DC panels. I am interested in your ideas. Any good technical books you can recomend. This is for a steel boat.
Hi Charls,
Interesting question. The answer is a bit long for a comment. I will answer it in a post. Look for it in the next few weeks.
Hi All,
I just removed a long and involved comment on the subject of AC grounding. Once again, I need to make clear that I will not allow the comments to this post to go down that road. This post is about DC isolation, not AC grounding. Getting the former wrong can cause damage to your boat. Getting the latter wrong can kill you.
The only place you should get information about AC grounding is from a recognized standard such as ABYC. I have wired our boat to ABYC and I am totally happy that their standards are the best and safest way to do the job. I will not allow a debate of that on this site. Not with people’s lives at stake.
One thing I will say, is that anyone suggesting floating an AC system on a boat is, in my fairly well informed opinion, wrong since, in the event of either current carrying conductor touching the hull, a breaker will not blow.
I am closing the comments on this post.
After the above comment I received two emails from the person that left the comment I deleted. He was upset, perhaps justifiably. This is what I wrote back:
“I really don’t want to get into a debate about this. Heck, you may even be right, I’m not infallible, or even close.
Having said that. We have many readers who have no electrical understanding and I don’t want them to think of this site as a source of information on the proper installation of gear carrying lethal voltages. The bottom line is that all such installations should be done by a qualified technician to ABYC (or comparable) specifications.
Having thought about it, I probably could have handled the situation better than I did. My apologies for that.”