Aluminum has many obvious attributes as a construction material—high strength to weight, durability, lack of maintenance—but there are other, subtler benefits that aluminum can offer, especially if starting from scratch. Careful thought at the planning stage to take advantage of that potential is time well spent.
It is an easy material to work in. Louise has just returned from France where she has inspected our boat at the completion of welding. From start to finish it has taken around six weeks from a pile of plate to a finished hull and deck. She was also able to view the completed joinery waiting to be dropped into place. This is, in effect, “furniture”, and not structural, a benefit in terms of its long term integrity, as well as ease of access for periodic inspection of the hull or in the event of any structural damage that might necessitate welding. It also demonstrates how an aluminum yacht in the hands of the right builder need not end up being colossally expensive.
Aluminum lends itself to one-off design internally too. In a GRP yacht the position of bulkheads is still to some degree dictated by their structural role, making the interior layout far less flexible. With aluminum, bulkheads, heads units and so forth can in theory be wherever you like. The only limiting factor for us is the factory philosophy of limited modification at sensible cost—but if we had wanted a custom built interior, we’d have to be prepared to pay for it, so we’re very happy with what we’re getting.
The OVNI has a number of features that make good use of the potential of aluminum construction. All tanks (fuel and water) are integral and welded into the hull, and have removable plates to enable cleaning and internal inspection. All of the lead ballast (3.5 Tonnes) is encapsulated in plastic and then plated in to the bilges. In the event of the hull being pierced in any of these areas, only a tank or a ballast chamber will be breached, hopefully averting a potential loss. At our request the builders extended the forward bulkhead behind the anchor locker to full depth, welded and watertight, giving us a crash bulkhead against collision with any floating objects—that ought to help us sleep easier!
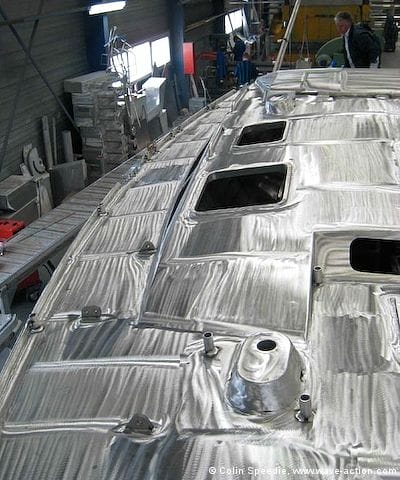
Where we have really tried to exploit the benefits of alloy construction is on deck. Our motto is, “if it can move—weld it”. Not just from the point of view of structural integrity, but also to avoid leaks and corrosion caused by dissimilar metals where fittings have been screwed or bolted on. So all grab rails (and we have plenty), dorade vents and tangs for deck gear are welded. We have also had fitted welded breakwaters around both forward hatches to protect the seals from deck sweeping seas, as well as a solid breakwater where the cockpit dodger will be mounted. All have been easy and cheap to achieve at this stage of the build—the watertight bulkhead, complete with inspection hatch cost around $300, for example. An additional anchor stern roller in line with a sheet winch was easily incorporated, a simple custom boat hook holder mounted on the stern arch, tangs for webbing davits—simple things, but worthwhile we feel, all adding in their own way to a functional, sturdy, and (hopefully!) leak proof home.
Colin,
We have retired with thoughts of changing our Westerly Ocean 33 bilge keeled for an Ovni and cruising further afield.
Your post regarding repainting has really begun to put us off aluminium. What are your thoughts about the merits of yours verses GRP yachts now?
Nigel
Hi Nigel
I think that painting is the worst aspect of aluminium boat ownership, without a doubt. But, if you are prepared to put in the time and effort and do it with the appropriate level of care then it becomes just another aspect of keeping your boat in good condition. I’d prefer an unpainted boat if I did it again, though.
Where aluminium really scores is in terms of strength and custom features. With an aluminium boat you can build in many valuable cruising features to make the boat suitable for high latitudes or other wild places where durability may be an issue. And because the strength/weight ratio is good it’s still possible to have a boat that performs well, despite a heavy-duty build. These points (expanded above) are why we chose aluminium ourselves.
But if we wanted a boat for home waters cruising, we’d have made a different choice, probably opting for a second-hand GRP boat – as we had before. It’s all about what you want to do with your boat, we feel.
Best wishes
Colin
First time for a question! First, love the site, you guys are pros, many thanks!
The question: Any pics showing your custom ideas regards building an aluminum boat? See quoted text from above chapter –
“We have also had fitted welded breakwaters around both forward hatches to protect the seals from deck sweeping seas, as well as a solid breakwater where the cockpit dodger will be mounted. All have been easy and cheap to achieve at this stage of the build—the watertight bulkhead, complete with inspection hatch cost around $300, for example. An additional anchor stern roller in line with a sheet winch was easily incorporated, a simple custom boat hook holder mounted on the stern arch, tangs for webbing davits—simple things, but worthwhile we feel, all adding in their own way to a functional, sturdy, and (hopefully!) leak proof home.”