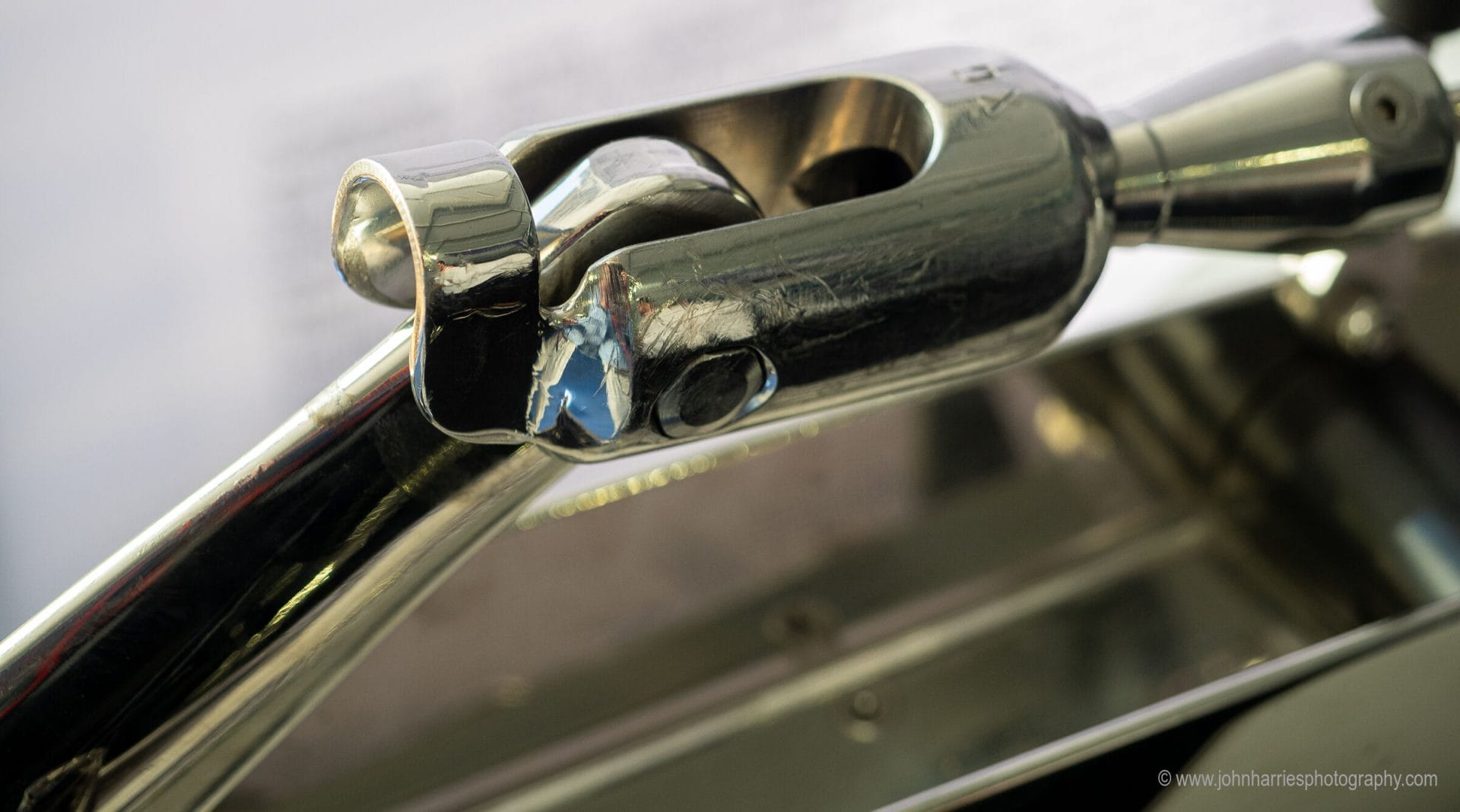
I have long recommended against anchor swivels, to the point that I also recommend against the Ultra anchor (even though I like a lot of other things about it) because it pretty much requires the use of Ultra’s swivel, or at least a shackle the wrong way around.
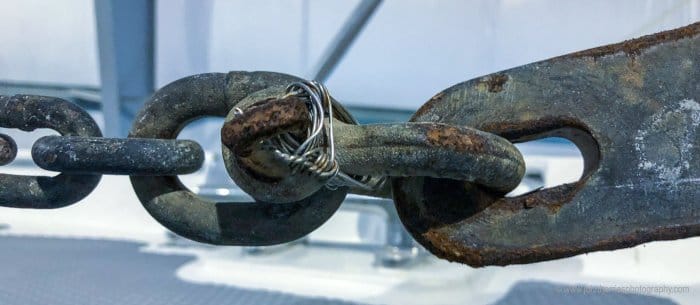
Swivels have never looked right to me, at least when they are connected directly to the anchor shank, the way most people use them, because any off-axis load will place huge pry loads on the fastening pin and the cheeks it’s through—see photo at top of Tip.
Of course I got a lot of push back over the years from swivel lovers, and even the makers of the Ultra, and that’s fine, robust discussion is a lot of what makes AAC work.
In this case a lot of that disagreement was based on the advertised break loads of the Ultra Swivel. I get it. How could we not trust a really nice-looking piece of kit with a huge advertised break load; for example, the UFS16-100, at 53,200 lbf (2365 kN)?
But wait, that assumes a straight pull on the axis of the swivel. What about if the anchor can’t pivot to the load, due, for example, to being stuck in rocks or an obstruction? That’s the scenario I have always worried about in connection with swivels.
Well, now we have the answer:
Hi, John. Any thoughts on the Mantus anchor swivel?
https://www.mantusmarine.com/mantus-swivel/?srsltid=AfmBOoqJa3Qogz-1hzkLS5zmqM1gQPceSyzesHpXr-cGcGrhlKUcDscg
Hi John and all,
Part of my thinking about gear that I consider for Alchemy is whether there is a problem that needs solving: and will the gear facilitate solving that problem.
In what is certainly thousands of nights at anchor and many “lunch stops”, I have never encountered a problem that I wished (or thought could be) solved by a swivel. Never have I felt the chain needed un-twisting even in those anchorages where we circled the anchor every tidal change and stayed for long periods.* For sure, the anchor occasionally comes up “backwards” on the roller, but a push with a handy boathook sets it right.
So, no problem: no swivel.
My best, Dick Stevenson, s/v Alchemy
*Not sure a swivel really “swivels” if under pressure anyway: at least not the galvanized ones. And, if any twist occurs, I suspect it is easily absorbed by the snubber,
Hi Dick,
That’s been our experience, and conclusion too: https://www.morganscloud.com/2010/09/12/anchor-swivels/
Hi Francis,
Assuming that one wants a swivel at all (I don’t) I would much prefer that design since it can reorient to the load. Unfortunately, it would not be usable with the Ultra anchor since, like with a shackle attached the right way, a slot is required in the anchor stock.
I used the Ultra for over 2 years with the broken swivel pictured above. I think they made it almost mandatory to use the original swivel because every time I pulled it the anchor was facing the wrong way.
Hi Yigit,
That’s interesting.
Sorry I don’t see a photo. You can find the instructions for posting one here: https://www.morganscloud.com/2013/11/10/aac-comment-guide-lines/
Hi John, I’m sorry I wasn’t clear enough. I meant the picture of the broken swivel on the article. Even with this one the anchor never came on the right way, that’s why I thought if you choose Ultra as an anchor you have to have their swivel (which was very expensive for me).
Hi Yigit,
OK, thanks for the clarification. Actually, I think I was being a bit dense!
On the anchor, have you tried turning the chain 180 degrees in the wild cat. This can be a magic fix, although certainly not always.
Hi John,
As someone who designs AtoN buoy moorings I fully agree on the no need for a swivel sentiment, except in quite specific scenarios, and if you want to use one, put 3 links of chain between it and the anchor.
I disagree on the shackle being the wrong way round though, that’s how they are designed to be used, even though I accept it’s often not practical without an enlarged end link. I’d also advise the use of a bolt type shackle (with a safety split pin) which allows the pin to spin without loosening, which screw pin shackles do under load, making your mousing wire the critical component stopping your anchor falling off.
I found Dan’s comments interesting. An old sailor gave me the tip about putting 3 chain links between the swivel and the anchor which, I believe, does a lot to avoid off axis loads. I tried this tip using a 1/2″ galvanized swivel on my 3/8″ chain. With this combination in place my anchor would always orientate itself correctly as it came over the bow roller which I found to be a big plus. Before this I would sometimes need to lean over the bow and line up the anchor so that it came up over the bow roller correctly.
Hi Dan,
I totally agree on adding chain between the anchor and shackle if one must have a swivel. In fact I recommend that here: https://www.morganscloud.com/2010/09/12/anchor-swivels/
We will have to agree to disagree on that shackle orientation. I’m very comfortable with the idea that the body of the shackle should be through the anchor stock, and most anchor manufacturers agree given that they provide a slot. More on that with pictures showing the off axis modalities here: https://www.morganscloud.com/2019/11/11/some-thoughts-on-the-ultra-anchor-roll-bars-and-swivels/
The other problem with putting the shackle pin through the anchor, as you point out, is that then the shackle must be grossly undersized to get the body through the chain.
I’m also not big on bolt shackles, preferring standard pin shackles well wired (preferable monnel) and also treated with blue locktite. That said, I agree that there is an argument for bolt shackles.
The solution is simple. Two shackles, rated above swl of chain. Bow to bow; one pin end to anchor slot, second pin end in chain. Mouse correctly, coat threads in pure lanolin. Avoids dodgy swivels. Less expensive. Easy to inspect. Easy to take apart. Cheap enough to replace often.
Hi Randall,
Sure, that’s one option, but not my preferred one since it adds a second possible fail point and putting the pin through the stock reduces the off axis strength by about half from rated, therefore the shackle will be a lot weaker than the chain. Therefore I prefer the bow through the a slot in the stock (as in the photo), which is the strongest solution with the least possible points of failure.
Thank you for the point about off axis reduction of the shackle if the pin end is through the anchor slot. However, when fitting a new Rocna 20kg anchor, I could not find a shackle that was both rated at or above the WLL of the G4 5/16″ chain AND would fit through the anchor slot. That was in NZ, with reasonably good chandleries and suppliers, ie full Crosby inventory. Am I missing something?
Hi Randall,
If memory serves, I use Crosby G-209-A shackles in the 3/8 inch size. The pin fits in my ACCO G4 5/16 inch chain and connects to a 77 lbs/35k Spade anchor
My best, Dick Stevenson, s/v Alchemy
Hi Randall,
As Dick points out, a Crosby G209A (make sure to get the “A”) will do the job and I’m sure one of the dealers would send you one by post without horrible cost. https://www.morganscloud.com/2007/09/01/which-anchor-shackles/
Jimmy Green in the UK also has shackles that will do the job and they are great at shipping overseas.
Re. shackle orientation.
Yes, some (NOT all) bow shackles that use a threaded or bolted pin can be installed with the bow through the chain and the pin through the shank. Because the pull can be up to 90° off axis in this case, the working load limit is reduced to 50% of the stated rating. (This is different from your AtoN case where the reduction due to off-axis load might be less.)
Others – particularly D-type shackles and those that rely solely on a cotter pin to retain the shackle pin – cannot be side loaded at all.
I generally tell people to put the bow through the anchor shank and the pin through the last chain link, because this will always allow the system to use the full strength of any type of shackle, and does not require an oversized last chain link.
Doing it the other way around is fine *IF* the shackle in question is designed for side loading *AND* the working load limit is adjusted according to the maximum off-axis pull angle. That’s too complicated for the average used boat salesman, but is perfectly fine if you know what you’re doing.
(I highly recommend Crosby’s training material for this subject, https://info.training.thecrosbygroup.com/resources-crosby-training-videos )
I will say that this is somewhat academic and I am a big hypocrite since my anchor shackle is exactly as Johns picture above, because a) the screw pin type was all I could get on the day I decided to change the shackle, and b) I don’t have chain with an oversize end link and the shackle body will not go through the chain (which I assume is why anchor manf’s put a slot).
Confession made, the issues that concern me are that firstly, the chain can slide to the edge of the shackle pin, putting a prying force on the joint – which is even worse if it’s a screw-pin type. And secondly the anchor hole against the shackle body is a point load due to the radius of the shackle body.
I may be wrong, but I have never seen any other scenario with a chain in either marine (ship anchors, port fenders, AtoN), or rigging/safety, where the body of a shackle goes through a flat plate – so being different from the norm makes me nervous, I kind of see it as a work around.
Hi Matt,
Thanks for the fill on that.
Thanks for posting this update, John.
Something else to note about this swivel is that it is loaded “off-axis” every time the anchor is recovered. If the anchor is stuck then it would be relatively easy to unintentionally break this swivel during recovery. I believe most windlasses suitable for this size of anchor would have more than sufficient capacity to exceed the breaking strength in this off-axis recovery scenario if the anchor were stuck.
Further, it is important to note that the force to “yield” or permanently deform the swivel arm is less than half the “ultimate” strength. If the swivel yields multiple times through repeated use, then the overall strength can be further reduced through work-hardening and fatigue (similar to breaking a paper clip through repeated bending).
The ultra-swivel is a very robust design with impressive pure-tension breaking strength, but I believe this hidden off-axis weakness makes it vulnerable. I know that they have many units in operation and I have not been able to find any reports of failure but I still have concerns about this design.
Hi Kurt,
Your comments make the common use of swivels even more worrying.
For others, Kurt’s spreadsheet calculates that the swivel will start yielding (bending) at just 1300 pounds and this for a swivel advertised to anchor an 80′ boat on!
Kurt: given that low yield strength and that said swivel is for use with anchors of over 200 lbs weight, I wonder if the action of flipping the anchor that is a supposed benefit of the swivel might exceed the yield, at least sometimes, given the leverage of the anchor stock as the swivel passes over the bow roller?
Yes. I think it may be possible to reach yield as the anchor rotates over the bow roller depending on the circumstances. I believe it is possible and even likely to reach yield during normal anchor recovery when the anchor is well set, deeply buried or possibly stuck. If the anchor is stuck, I believe the maximum pull capacity of most anchor windlasses would be sufficient to yield if not break the swivel arm.
Hi Kurt,
Thanks for the fill on that. The thought that even just repeatedly retrieving the anchor over the bow roller, coupled with getting it out of the bottom after a few hard sets could exceed yield on that swivel is disturbing indeed. I can confirm that on or M&R 56 there were frequently times where breaking out the 55 kg SPADE would near-stall our massive Ideal windlass with a pull rating of over 3000 lbs.
I installed a “Flip Link” between the anchor chain and my Sarca Excel. This simple piece of kit is an elongated, shaped, flat, chain link that orients the anchor as it passes over the ancho roller. Specifications (including working loads) and a picture at flip-links. Works great – no moving parts and inexpensive, especially relative to a swivel.
Sold by the Canadian distributer of Sarca Excel anchors, Ground Tackle Marine.
Hi Tim,
The Flip-Link that you referred to looks like it will get the anchor positioned correctly to enter the roller, and is pleasingly ingenious, but it fails my test of needing to solve a problem: perhaps I should have said, “a significant” problem.
To me, the anchor coming up backwards is an annoyance and does not enter the realm of a problem and is easily re-oriented in the ways previously described.
In addressing and solving this annoyance/problem, a piece of gear is introduced to one’s ground tackle system that includes a hunk of metal, an additional short piece of chain, 2 D shackles (if G4 or stronger chain is used, appropriate shackles such as Crosby’s must be sourced) needing mousing and hope that the accumulated length beyond the anchor’s shank works out with your windlass positioning.
Now, I recognize that skippers differ in their tolerance for stuff, but I tend not to add gear/complexity for annoyances.
My best, Dick Stevenson, s/v Alchemy
Hi Tim and Dick,
Like Dick, I would not want to add two more shackles if I could possible avoid it.
I did a cursory (not thorough line-by-line) cross-check of the two calculations linked. I believe they are generally correct, and are in agreement with Ultra’s published strength and resulting tensile stress in the properly loaded (pure tension) case.
I also built a rough CAD model of the swivel in question and am trying some FEA cases on it. I will not share it here because I cannot vouch for its accuracy, but I will say that it supports the contention that, in this type of ball-and-socket swivel, the tensile stress due to bending at the ball neck is likely the limiting factor, and is what you’d expect from Kurt’s calculations.
Swivels like the broken one in the article photo are far worse.
These things are designed for pure tension. Loading them off-axis creates very large, concentrated internal bending stresses.
Wait, it gets worse. (Yes John I’m stealing your catchphrase.) Many swivels have sharp inside corners, tool marks, gouges from rubbing on rocks or on the chain, cut/tapped threads…. these cause stress concentrations, which are great places for cracking to start. And, since they’re cyclically loaded….. metal fatigue, yay!
Wait, it gets worse. (Again?) You now have a component that can, in normal use, be loaded to approximately its yield point. This means that the component must be inspected after every high-load situation to see if it has yielded or developed cracks. This is a very different story versus something like a chainplate or shroud or turnbuckle, which is designed so that the yield point cannot be reached in any extreme of normal use.
Hi Matt,
Thanks for running through that. Although I totally trust Kurt, with a results this startling the more verification from qualified sources the better.
Also very good point about stress concentrations. Swivels lead a hard life and Kurt’s calculations assume no dings, so I wonder how much worse the numbers would get after a bit of wear and tear?
I know I, and others, were stunned that what looked like an inconsequential gouge on the the mast for our J/109, caused by the trucker, was shown be FEA to have reduced the strength by half, and required scrapping the mast.
Great work! It reminds me of the Spinlock Race tether clips that will hold 5,000 pounds … unless you cross load them somehow, in which case they won’t hold body weight due to a design flaw. Oops.
When I got the PDQ it had the same swivel you have in your last image. Before I owned the boat, it had become slightly bent. When changing to a different anchor (originally a 25-pound Delta) I would a small crack inside as well. It’s days were numbered. And that by a 25-pound anchor with limited holding capacity! The anchor shank was not bent and I believe it was the factory anchor, but who knows.
The shackle was connected dirrectly to the shank. Yup, that’s bad and so obviously dumb, yet it is constantly illustrated.
I never saw the need for a swivel. Once I learned to lift the anchor the last 10 feet while going aft (the anchor will align due to water flow) it always came up right-way-round.
Hi Drew,
Yes, very like the great work you did on the Gibb type clip. The sad thing is that thousands of those clips were sold and used even after the fatality. The way in which the sailing community can ignore bad design for decades never ceases to amaze me.
Another interesting case that I have wanted to investigate but never have deeply:
The conventional wisdom is that the bow of the shackle goes in the shank. However, many of the earlier anchors (CQR, early Bruce, early Danforth, and all present day ship anchors) use a heavy shackle with the pin through a round hole. One advantage is that the shackle cannot jam at an odd angle, which sometimes happens. Another is that the strength reduction of shackles in this orientation is well understood (50%) and can simply be designed for; the shank will bend at much less than 50% of the chain strength, so the case is, in fact, mute. A shackle jammed at an odd angle may have a breaking strength reduction they do not understand.
Of course, since most modern anchors have a slot, the question seems mute. But is it? I posed this question to Fortress, which makes anchors designed both ways, and they explained to me that both are valid, and in fact, they provide a slot solely because the market expects one. Interesting.
Engineering design of lifting equipment never uses an anchor shackle in a slot. Either a hole is provided in the correct plain and a D-shackle is used, or an anchor shackle is used in a round hole and the side load reduction is factored in, along with a customary safety factor in both cases.
Personally, I would go with a large anchor shackle in a round hole if given the choice, connected to the chain with smaller shackles as needed.
A little something to analyze, remembering that this is what CQR did.
Hi Drew,
Good point and yes, I too remember the huge shackle on CQR. But, as you say, it does have to be double sized if the total system is going to match the strength of the chain and it does add another shackle. On the CQR, if I remember, the big shackle was welded closed and then galvanized, so I would feel better about that than I would just adding a shackle. Also, the CQR shank is thick and the hole perfectly matched to the pin so that the large shackle was well retained. In short the whole thing was designed and built at the factory for that set up.
The other issue is I’m not sure the hole in the Ultra is big enough to accommodate a large enough shackle to match the chain strength, or the shank thick enough to retain it from sliding back and forth.
Add it all up, while I agree the CQR set up is good, I prefer a slot and single shackle as a general recommendation since it’s simpler and more fool proof: match the shackle strength to the chain, and all is good. I’m guessing that’s why most anchor manufactures have gone over to it.
Hi Drew,
I don’t know all the reasons that shackles are installed that way in lifting applications but it could well be related to predictable loads and Hertzian stress. Good design practice for a highly loaded pin is to put it in a close fitting hole. This allows the part to move in a known motion. The close fit also means that Hertzian stresses are limited whereas they could be significant using an anchor shackle in a slot. For people not familiar with Hertzian stresses, they are stresses local to the contact area when 2 parts do not fit together well over a large area and their correlation to part failure is much less straightforward than something like a tensile stress.
I am not in love with how we do anchor shackles per John’s method but it does seem to work okay and our setup is the same as his as I don’t know of a better way with the available hardware. Another thing that bothers me is how we keep the shackles from undoing by overthreading them which isn’t great, it breaks all the rules of threaded joint design.
Eric
Hi Eric,
Thanks for bringing that up since I have often wondered about the stress caused by the point loading at the two edges of the slot, although I did not know what to call it until now.
Do you have any estimate, even a very rough one, on how much that would degrade the shackle break load? I guess that would be hard because it would depend on the damage caused to the shackle surface over time and the resulting stress concentrations? Also, over time the edges of the anchor slot round off, so there’s another impossible to quantify variable I’m thinking?
Also a good point about the way we over thread. In recent years I have gone a bit easier on that and instead relied on a combination of wire and blue locktite. In the past I have taken apart anchor shackles and been concerned to see how much the threads were degraded, probably at least partly from my over tightening them with a huge wrench in the mistaken belief that more is better. Live and learn.
Anyway, I find all of the above a lot less scary than subjecting shackles and swivels to loads trying to pry them apart. As you say, the lesser of two evils.
Hi John,
The actual stress values are highly sensitive to the exact nominal geometry, tolerances and properties of the material chosen (modulus being a big one). Most of the times when someone does a stress analysis, they don’t even look at Hertz stress as they follow good design practices so it is not a big factor. The place where I run into it with some regularity is on dry cams (wet cams are usually oil film limited) which have a thin line of contact between the cam and the roller follower. We have had cases where someone will replace a follower with a slightly different one and rapidly get a failure where there was great life before. The reason that cams are so sensitive to this is that not only is it line contact, they are sensitive to the failure mode which is surface level damage that looks like tiny pitting which starts to shed material that gets into the mating surfaces making it rapidly worse. You would see the same things in a cylindrical roller bearing if you removed the grease or you had high load and cyclic motion over a very small angle change (this is known as potholing a bearing). You can calculate these stresses by hand for simple geometries or using analysis tools for complex ones so in applications where it could be an issue, we just analyze and adjust the design if needed before prototyping.
Coming back to this application, it is not something that overly concerns me provided that the hole in the anchor shank has nice radii on it and high quality shackles with appropriate safety factor are used. The point loading here is on the inside of the bow on the shackle where the material is in compression and shouldn’t ever be in tension (if this were the pin side on a bolt type shackle, that would not be true). Areas in compression are much more forgiving, when you see failures you almost always see tensile failures. Also, these stresses are very localized so you might put a small dent in the surface but given the compression side location it is unlikely to cause a failure in normal use.
Eric
Hi Eric,
Thanks, I always find these comments of yours where you delve into engineering that I have no clue about fascinating.
The big learning for me from this one, that now I think about it makes perfect sense, and will be useful to me in all kinds of situations, is that we have to worry about these kinds of stresses a lot less if they are on a surface under compression, rather tension.
I agree that side-loaded swivels are disastrously weak when installed directly on the anchor, and have seen a couple damaged like your picture.
Same weakness applies to non-swiveling devices to connect chain to anchor, like the Kong fixed connectors.
We chose a Kong fixed connector so that we could connect our 10mm medium strength chain to the anchor without having a weak point. The Kong has the 10mm chain one end, and four links of 12mm chain the other, which is shackled to the anchor with a shackle stronger than 10mm chain.
That way we solve the side load problem too (as others have mentioned)
Hi John,
I totally agree that swivels are items created by emissaries of the Devil, 🙂 of course, but to take the role of their advocate; the Ultra Anchor swivels are not made from normal stainless steel. They’re made from superduplex, if I remember correctly, but at least standard duplex. That’s more than twice the strength of normal 316 stainless and even less vulnerable to fatigue than high quality galvanised steel. I would certainly not use the swivels anyway, but do the calculations mentioned take this higher quality steel into account?
Hi Stein, I just checked on the Ultra site and they say the swivel is made of “316Ti”, not Duplex, and TI is, as far as I can determine, only about 25% stronger than 316 and 316L.
Also, I checked Kurt’s spreadsheet and it specifically uses Ti stainless.
Hi John,
Interesting. I’m sure I’ve read somewhere a statement from them saying that it’s made from some form of Duplex, but it’s a while ago, so it may have been changed. Saving costs is what companies do, once they got the engineers out of the room…
Hi John
Interesting article and analysis on the Ultra swivel. The question you don’t answer though is for those of us that have an Ultra anchor and swivel; should we remove it and use a shackle given the debate of using a shackle in a round hole?
Thanks
Julian
Hi Julian,
If it were me, I think I would remove the swivel and use a galvanized Crosby alloy high test shackle with a pin as close to the diameter of the hole as possible and then use another shackle to connect to the chain with it’s pin through the last link. I think I would also shim the pin on the shackle going through the stock with washers to insure that the stock stays in the centre of the pin.
That said, we need to be aware that so doing will reduce the safe working load or the shackle through the stock by at least 50% from rated in an off axis pull, so whether or not we will be able to match the SWL of the chain is dependant on the diameter of the hole in the stock of the Ultra.
Bottom line, while I think the above is way safer than the swivel I don’t think it’s as safe as a shackle in a slot.
Eric, Matt, Kurt, any thoughts on the above?
Hi John,
I agree with you, but wanted to mention that several chain manufacturers can supply the chain with a larger link at the end, that would let you put a quite big shackle trough it, like with an anchor with an elongated hole.
Also, the reason for doubts over shackle orientation might arise from not having looked properly at the geometry. It took me some pondering. So maybe others can be helped by my explanation? No matter where the pin is, the load will align with the shackle, right? Yes, but….
If the pin is in the chain, as recommended, and the chain is kept reliably at the mid point of the pin, (perhaps by sheaves) the shackle arc will orient itself well balanced in the anchor shank hole. The load through the shackle will be even on both ends of the pin and on both pin holes in the shackle arc. It won’t be perfect, of course, but close. The shackle should keep most of its strength almost always.
With the opposite orientation, the situation seems very similar, except that the anchor shank will be centred on the pin and the chain (or the second shackle) is moving in the shackle arc until it finds alignment. The chain should align itself on the shackle arc at least as well as the anchor stock did as described above. Pretty much the same thing, right?
Nope. Not at all the same type of alignment. The loads are just as well aligned on the chain and on the anchor, but not so on the shackle. If the chain pulls sideways on the anchor, the shackle arc doesn’t pull straight on the pin, not equal on both ends of the pin. The chain is trying to strip the pin threads and open the arc. Succeeding with that takes much less force than if the shackle was pulled straight with equal load on the arc legs and minimal load on the threads.
That’s the reason I will never buy an Ultra Anchor until they present a better way to attach the chain. A massively oversized shackle might be it, but a swivel certainly isn’t.
Hi Stein,
Yes, an oversized link is a good option in some cases: https://www.morganscloud.com/2013/09/25/which-anchor-chain-should-we-buy/
And yes, good point on shackle alignment. I cover that with pics here: https://www.morganscloud.com/2019/11/11/some-thoughts-on-the-ultra-anchor-roll-bars-and-swivels/
Wow…Thanks for this very interesting article John…
I do have the Ultra UA35 Ultra anchor with UFS 10-35 swivel for my Hallberg-Rassy 412. The anchor to date has been outstanding sailing the Gulf Islands around Vancouver Island. however your article raises concern on Ultra swivels. Ultra’s website advertises that their swivels are stronger than anchor chains, which may be true but they don’t mention off-axis lateral strength. Mud and sand bottoms will not be a problem, and if I knowingly plan to anchor in rocky bottoms, I will remove the swivel, to be safe.
Hi Keith,
I too thought mud and sand would not be an issue for the swivel, but Kurt pointed out how low the yield is on these swivels and also pointed out modalities that could exceed that load. See this thread: https://www.morganscloud.com/jhhtips/the-off-axis-weakness-of-anchor-swivels/
Assuming that Kurt’s calcs scale for your 10-35 swivel, that would mean that it will start to deform (yield) at just 460 lbs load at 90 degrees off axis. And I’m pretty sure that’s a load that can be seen in general operation in mud or sand, particularly on retrieval. Or possibly even in cases where the anchor is poorly oriented when the swivel crosses the roller since the weight of the fluke has a huge lever arm on the swivel in that case.
I totally agree with your reasoning John. Just yesterday I was walking down my pier to our boat. Out of interest I counted 15 vessels that had the swivel attached directly to the anchor. Ok, a bit dull and hardly scientific. Some looked a wee bit “tired” with my casual observation.
I use an Asano purse shackle. The pin has a recessed hex socket. 243 loctite on the thread and there is a spring clip in a recess. This also fits on my number 6 sarca excel to permit the swivel ability. Not cheap but seems like it is built for the job. Your thoughts on these would be appreciated.
Hi Michael,
My curiosity was triggered, so I looked it up. Found this: https://asano-metal.com/products/detail/228
They say it’s made of “special stainless”, and specify SUS316. I’m no metallurgist, but normal 316 is not a material I would want on my rode, due to its general weakness, vulnerability to fatigue and crevice pitting, especially in salt water above about 20 degrees C (68F). 316 can be modified, cold forging and more, to become a lot stronger, but it doesn’t seem like that is the case here.
I notice that the 13mm (1/2 inch) version has a working load of 600 kilo (1323 pounds) and the 16mm (6/8 inch) 1000 kilo (2205 pounds). I don’t remember what load ratings other same size shackles have, but to me this does seem low for fairly beefy shackles.
I do like that the shackles look smooth and have no protractions that can snag onto things, and that there is a locking method. Also that the rings are very compact. Maybe that’s the reason for the low working load? However, I’m not too confident about the type of locking ring. It seems to me that being banged around it could fall out too easily? I don’t really know, of course. Never even seen one IRL.
Mi Michael,
Yes, it still amazes me how many people are still using swivels attached directly to the anchor. But then there are still a huge number of yachties still using CQRs 30 years after modern anchors made the CQR utterly obsolete. I think a lot of it is that the majority of people with boats don’t actually anchor very often so they get away with these things for decades.
As to the Purse Shackle, certainly interesting but I still prefer a Crosby galvanized 209A because I can wire the pin, as well as locktite, which I think is more secure that that circlip that could be damaged or pulled off by the shackle being dragged along rocks, or even hard sand. Of course the same applies to wire, but if we use multiple strands and seize the bundle right a few broken strands don’t matter and also serve as an indicator of required replacement.
Also I was not able to find out which SS grade the Purse Shackle is made from, even on Asano’s site, which makes me guess that it’s 316 or 304 which means the shackle will not match the chain strength, which the Crosby will:https://www.morganscloud.com/2007/09/01/which-anchor-shackles/
Interesting discussion, especially since we have both an Ultra anchor and Ultra Swivel since a few years back. Did you ask the Ultra makers their opinion and allow/ask them to comment? Would be good to know the steel quality as mentioned in one comment.
Hi Ragnar,
The steel quality is not in doubt, it’s listed right on the page for the product that I linked to in the tip above.
And no, I have not asked the Ultra makers to comment, all that will produce is a storm of denials and accusations, as you can see on my original Ultra anchor review. So I really don’t see the point in going through all that agro given that two engineers came up with same results using different calculation strategies and a third (Matt) checked their numbers and applied FEA.
And do keep in mind I was kind to Ultra in the above because I used break load, the yield load is about a third of that, which is really disturbing. See Kurt’s comments.
And further we know that swivels attached directly to an anchor have a history of failure as Practical Sailor has agreed in a separate study. See my orginal article on swivels, linked to above.
That said, of course Ultra are welcome to comment on the article, just like anyone else.
Hi Ragnar,
I remember the discussions a few years back with an Ultra representative that John mentions. I can understand that they are proud of having made a very nice anchor, which it really is. However, I feel that the personality of that representative was not suitable for the public domain. He seemed to really try to discuss well, be informative, but just failing at keeping emotions out of a discussion that just MUST be kept to pure logic.
The general idea from the representative seemed to be something along: “The swivels are so excessively strong that there’s no need to worry about any type of load.” Not a quote, just my impression. Such a notion is just flat out wrong. That’s obvious to anyone looking at it, and confirmed by the calculations here.
I wonder why Ultra Anchors wouldn’t just change the hole to an elongated hole. There seems to be zero downside to that. Then we can use a single shackle, as recommended here. (I’d probably buy one then). Or still use a swivel straight on, for whoever wants to live in that illusion.
RANT
I seriously struggle with seeing how the swivel straight on the anchor shank can still be a discussion at all. The physics are obvious. Any object available to bending loads is dramatically weaker than the same object if only tension is possible. That’s all we need to know. Avoid bending loads. End of discussion.
There’s only one possible conclusion in this context: We just NEVER put a swivel directly on the anchor shank. I also think swivels are pointless no matter what we do with them, but if we insist on having one, it must be completely free to align fully to pulls in ANY direction, just as a pure chain would.
Even though these statements are facts of physics, not my opinions, a few people will still “disagree”. Whatever… We just have to accept that some people, like the mentioned rep, can’t get past their emotions, so facts must be ignored. I take a deep breath and think; it’s their loss, not mine.
End of rant, (for now). 😀
Regarding any of the stainless anchor swivels, I haven’t seen any discussions about crevice corrosion. I’m shy of using any stainless underwater.
Hi Larry,
Generally, I agree. You will find multiple references to that concern in our Anchoring Online book: https://www.morganscloud.com/category/anchoring-mooring/online-book-anchoring/
Hi. I have always been worried by the lateral loads on these devices and am disappointed when professionals install them like this. The excellent “Complete book of anchoring and mooring” by Earl Heinz has a photo of an 83 footer washed ashore due to such a failure.
As an aside I was taught at sea school to place the shackle pin through the anchor to ensure that the two flat surfaces had the maximum contact rather than the way you have shown it?
Fair winds – Charles
Hi Charles,
Yes, there is debate about that, but if we put the pin through the anchor we have the same off axis pry loads on the shackle as with a swival, and also the shackle will have to be grossly undersized to get through the chain. Also see Eric Klem’s analysis further up the thread.
It might be fun and educational for someone here who has an Ultra anchor and swivel to tie their boat well to the dock, wedge the anchor in the dock (piling, cleat, joist or whatever) ahead of the boat with the anchor shank at right angles to the chain, and give the anchor and swivel a good pull with the boat’s windlass to see what bends or breaks. After all it should be no worse than an unfair windlass pull on the anchor lodged in a rock or wreck on the bottom. If it fails, the owner would be fortunate to have the failure occur alongside the dock in good weather. It it does not fail he would be more confident in his gear.
Hi William,
Testing the real items to breaking is indeed very interesting, of course. Especially if it’s not my own stuff that breaks… 🙂 If I did have the mentioned setup, I think I’d probably be hesitant. It’s expensive stuff.
The other problem is that it can also be dangerous. Loading things up until they break means there will always be flex, in several elements. That can wreak havoc in surprising ways. The chain might become a brutal whip. That can be contained, but good thinking must be done.
Hi William,
Interesting thought, but I’m not sure it would tell us anything we don’t already know given that two engineers calculated the break and yield loads independently using different methods and came up with the same answer (Kurt and his bother), and then a third (Matt), checked their work and used a third method to verify it.
Point being that while this stuff seems complicated and hard to credit to us lay people, figuring it out is pretty simple for an engineer and not open to a lot of doubt.
There is another example of a bow shackle fastened with its pin in a round hole and loaded off axis so as to pry the stainless shackle open in the photo at https://etugri87v3i.exactdn.com/wp-content/uploads/2014/02/JHH5II-16137.jpg?strip=all&lossy=1&w=2560&ssl=1.
Hi William,
Absolutely, poor design.
But the good news is that mainsheets are very low load (comparatively) when reaching and running, and when beating, where the load starts approaching that the spar designer planned for, the load is on axis. Also with shackles the loss of strength for 90 Degree off axis is 50% so probably not a problem, given that the load gets MUCH lower as the angle gets worse. So a different situation than anchors.
Actually, I was thinking about the case of the sleepy crew tightening the mainsheet against the preventer while sailing downwind both prying the stainless bow shackle open and breaking the tang-to-boom weld with the increased lever arm.
Would a stainless quick link be a better option?
Hi William,
Good point, it would definitely be a better design with an attachment point that would pivot to the load.
A quick link is an interesting idea, although I’m not sure it would match the strength of the shackle because it might have to be smaller to get through the hole depending on the relationship between gauge and space to get it on. Would take some experimentation and checking of specs.