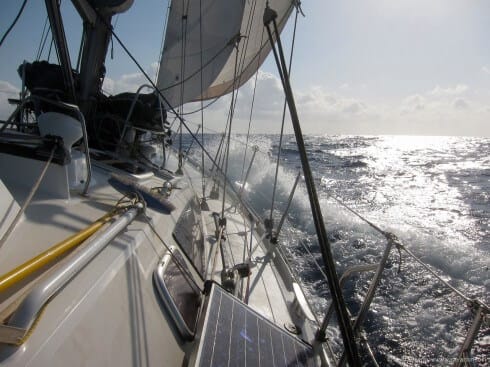
Turning to the single major cause identified in the insurer’s study, we find a staggeringly high percentage of losses caused by something we can all address—30% of sinkings are caused by water ingress through the topsides.
And it’s worth remembering that there will almost certainly be a corresponding spike in such accidents that don’t result in sinkings but that will still ruin your day through wrecking your electrical systems or simply soaking your bunk. Water—especially salt water—should be kept out even in small doses, especially if you have a modern, shallow-bilged yacht, where a little water will go a long, long way.
Start At The Very Beginning
As with watertight bulkheads, it helps if you are in the lucky position of starting from new, and are building in metal. From the planning stage consider how you can reduce any holes through the hull or deck, and replace with welding wherever possible.
Teak decks should be avoided at all costs, unless glued down, and even then I’d rather be without them.
Replacing drilled and tapped deck fittings such as grab rails with welded pipe might make the boat look more work-boat like, but they will never leak. Follow this concept through at all times and you’ll save yourself a great deal of maintenance and repair work down the line.
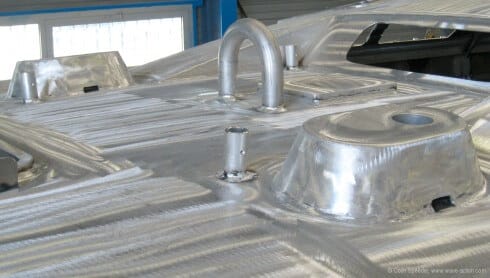
Don’t Forget The Anchor Locker
One perennial area for leaks is the anchor locker in the bow. Almost unbelievably, many builders still don’t install anything like adequate drain holes in the base of the locker, and anything smaller than an inch in diameter (x 2) is going to clog with debris sooner or later, usually when you’re bashing your way upwind in steep seas.
That extra few hundred pounds is not only going to do nothing for your windward ability, but the enclosed water will also find each and every weak spot in the locker, such as minimal amounts of tabbing on the bulkhead (on only one side!), power cables passed through the bulkhead with no watertight gland or even sealant, or the thin ply bulkhead abraded through by the chain and leaking badly—all of which I’ve witnessed.

It’s straightforward enough to address these issues, through enlarging the drain holes (subject to space and structural strength) and reinforcing the bulkhead and installing proper watertight cable glands for all wiring.
A useful option is to fit a false floor in the base of the locker that will act as a form of strainer, helping to keep the drain holes free from debris. I made such a floor out of an offcut of the type of GRP decking found in some marinas—cheap, tough, rot proof stuff that lends itself to many types of heavy-duty work of this kind.
Before any long passage we’ll throw a few exploratory buckets of water into the anchor locker and check that the water comes out through both drain holes unimpeded, which is usually enough to let you know if there’s a problem.
If we’re anchoring a lot (especially in rivers) we’ll regularly empty the locker, wash the chain and warp, lift the floor and clean out the base, where there will usually be a solid amount of silt, paint flakes and leaves. Assiduous washing of the chain during recovery will of course help, but even so it’s amazing how much crud can gather there.
Another common source of leaks in this area always used to be the hawse pipe on deck, although these have become less popular recently due to the almost universal adoption of power driven windlasses. In the old days (especially) on racing boats, we would commonly stow the anchor below to keep weight out of the ends, and drop the chain down through the hawse pipe, attached via a messenger line to a wooden plug that would then be driven into the hawse hole. These had a bad habit of coming out in rough weather, and more than one vessel I knew of ended up with a lot of water below as a result. These should ideally not only be plugged, but the plug clamped in some way, too, and with a waterproof cover that can be solidly lashed in place.
Solid Water Over the Decks
Anybody who has had to endure a long hard flog to windward will also know just how much solid water can make its way across the deck. Deck hatches, especially on the foredeck, are extremely vulnerable to really solid water forcing its way through hatch seals that are old or damaged, or even where the hatch lid itself is warped or becoming loose.
Some modern boats are equipped with very flimsy hatches for such a vulnerable site, and the lid and seal can easily become damaged if closed on a stray piece of rope or some other object. We always check carefully that no such object is there before closing one of our hatches, especially the forward sail locker hatch.
What Can You Do?
Fit Lewmar Oceanstyle range or the Goiot Tradition range (especially the latter). These have stronger welded or cast frames and lids, better seals and thicker lenses than their cheaper brothers, and so will last longer and be less leak-prone. If you’ve got an older boat and have to replace hatches, then if your existing aperture will match with a model from one of the above ranges (or similar) then these hatches are well worth considering as replacements.
Maritime and Coastguard Agency rules for all coded small commercial vessels in the UK insist that all foredeck hatches be reversed, so that the hinges are at the leading edge, which certainly helps reduce the chances of leaks, but at the expense of spoiling the air flow when at anchor, which is more than a nuisance in tropical areas.
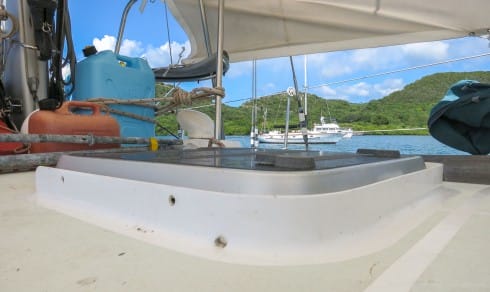
An alternative for a non-coded boat is to install wave-breaks around the hatches that will stop solid water getting to the seals. The first time I ever saw these employed was on a 60s wooden racer, where they had been made in beautifully chamfered teak, which didn’t only reduce the chance of leaks but looked good, too. Ours are made in simple vertical aluminium plate, and while they look a little agricultural, they work really well.
I even sailed on one boat where they had made them in 4mm neoprene glued to the leading edge of the hatches (which were also reversed), as she was a bit of a ‘sub’, prone to burying her bow going downwind—what the die hard IOR era Whitbread racers called ‘sailing in the green room’. Looked hideous, but it did stop the leaks!
We pressure test our hatches with a hose and check their seals every year, and clean the seals with warm soapy water regularly—even small amounts of accumulated crud can cause minor leaks. And it pays to check the integrity of the joints on some of the hatches that use a split extrusion, as the internal bar that they rely on to secure the joint has a habit of failing. Lewmar make a repair kit for their offshore range that can easily cure that problem.
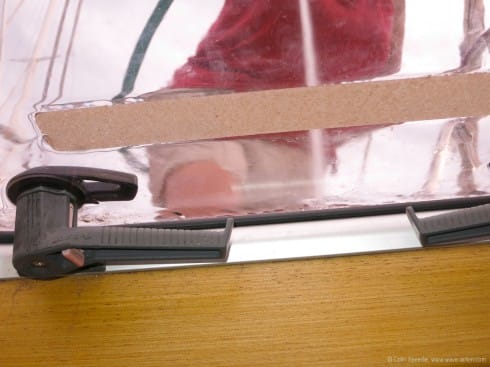
Another place where a wave break will work well is ahead of the companionway hatch garage, which will elbow aside any serious water from the cockpit area.
This has the additional benefit of moving the soft dodger attachment up off the deck, which protects the vulnerable canvas material from damage (to some degree) and reduces leaks around the companionway and instrument console.
There is always the potential for water ingress around the companionway or instrument console, with the potential to not only wreck all of your expensive electrickery, but also to find its way below via the wiring conduits within, so it’s essential to make sure that any joints have been really well sealed.
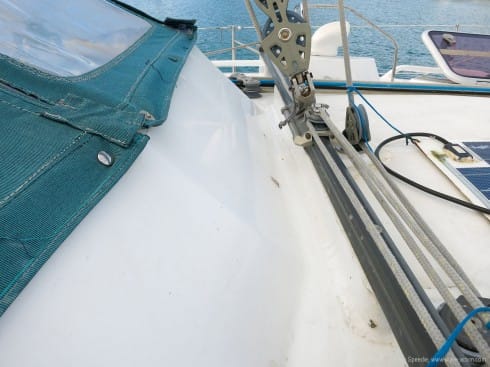
Close the hatches!
This may seem to be stating the flippin’ obvious, but it should be etched on every skipper’s brain. During last year’s transatlantic we went for six and a half days on the wind after crossing the equator with all hatches closed due to the amount of water flying around.
Well, apart that is from ten minutes when some idiot decided that the sea had gone down enough to open one of the leeward hatches over the galley a little (mea culpa…) with a predictable result.
Or the time on my last boat when we were tramping along upwind in really strong conditions, when she just dropped her nose as we went over one wave and ploughed straight through the next. One minute we had a dodger, the next we didn’t. And if I’d closed the companionway hatch and put the washboards in before hand, we’d have saved ourselves an awful lot of mopping up. Oh, well—you live and learn. Hopefully?
Good advice.
Re: “30% of sinkings are caused by water ingress through the topsides.” – what is the source of this statistic? In the earlier post, this was cited in comments without attribution.
Skepticism reigns,
Gybe
s/v Ferrity
Hi Gybe
I didn’t notice that the comment didn’t include an attribution, but I’ll try and track it down, albeit when I can get a decent signal – we’re at anchor in Bequia at the moment.
Glad you found it useful.
Best wishes
Colin
Electrickery! You should take out a patent on that word!
Hi Richard
It’s an oldie but a goodie – we used to use it as term for the birds nest of wiring found on an old British motorcycle, usually fifteenth hand by the time we got to own it!
Best wishes
Colin
Forgot that it had already been invented by Lucas!
Hi Richard
Not invented by them, but certainly inspired by them.
We used to call Lucas electrics ‘Prince of darkness’, and if you ever rode an old Trumpet or Beezer at night you’ll know why!
Best wishes
Colin
Enlightening! Keep’em coming!
Hi Richard
I’ll try – and thanks for the kind words.
Best wishes
Colin
Well done Colin! Another great article. Rajah Laut has huge wave breaks around each hatch. Sometimes it is a pain when your toe finds one. Since each hatch also has a four inch air vent, when conditions dictate, we have large neoprene boots and stainless steel bands surrounding the vents to prevent any chance of water ingress.
We are fortunate too in that RL for some reason does not like to drop the bow so the front office is usually quite dry.
Where are you now?
Hi Victor
Yes, it’s a real pain (literally!) when you kick one – metal boats are so unforgiving.
Sounds like Rajah Laut is really well prepped, and that’s a neat idea for those vents – thanks very much for the thought.
Chines and/or some flare at the bow really help to keep the decks dry, and I’m constantly surprised (and pleased) at how little water comes across the decks of Pelerin – As I’m sure your boat is similar (from memory) then I’m sure she’s the same – good thing, too, eh?
From sunny Bequia!
Colin
Bequia—Sweet
I enjoyed reading this and usually shake my head when – more often than not – I see metal boats with deck hardware that is bolted, rather than welded down. I imagine this is an easier execution for the builder who gives less priority to the owners’ increased maintenance down the road.
A very minor point no doubt, but when I use the term “topsides” – as used in the title of the post – I am referring the the part of a ship’s sides above the waterline or outer surface of a hull above the water – as opposed to the deck, which is the area being discussed here. I wonder if it was those darn “Sperry” brand shoes that started the common mixing of terms here…
Hi Matt
I’d agree – it’s just so much easier to buy in an OEM type component, and on any metal boat through bolting is going to cause trouble sooner or later. Which is why it’s necessary to work with a builder who shares your vision, and is prepared to make the most of metal through fabricating and welding everything. Planning is everything, sorting out all of those minor details in advance and getting agreement on how they’re to be carried out.
You could be right about topsides, but I suspect it’s as much to do with the difference between US and UK English – what is it they say? ‘Two nations separated by a common language’!
Best wishes
Colin
Colin,
A very nice article. I believe that water leakage through or around the deck, deck fittings, deck to hull joint, etc. is one of the best arguments for not re-furbishing an old boat (and for shying away from many new boats). A boat that weeps/leaks in these areas is just a misery and most older boats do just that (and, sad to say, some brand new vessels) after being off shore in boisterous weather for a couple of days. Re-furbishing rarely addresses this as spraying water, even pressurized water will not reveal these leaks. It takes the torquing of everyday life at sea make these problems apparent. The amount of work to address this issue on an already completed boat is astounding.
Dick Stevenson, s/v Alchemy
Hi Dick
Excellent point, and I’m right with you on that one.
The worst is potentially dealing with the hull/deck joint. After a few years of circuits and bumps on the marina circuit there are inevitably leaks at the toerail joint where the bonding paste has been damaged or dislodged, and these never show up until a hard slog to windward when the rail is going under, do they?
Or inadequately reinforced teak grab rails on deck, bolted straight through the balsa core – it’s amazing how far water can wick through balsa…
And even the best quality sealants don’t last for ever, so one day you’ll be taking it all off to re-bed and re-seal. And as you point out, new boats aren’t immune – from the paltry amounts of Sikaflex I’ve seen used on the deck fittings of some European boats you’d think the stuff was solid gold!
Best wishes
Colin
thanks for the info. A great article on bedding deck hardware can be found at: http://www.pbase.com/mainecruising/rebedding_hardware
In fact, his website has a number of great “how to ” articles that I have found very helpful.
Another trick I have yet to try is to close all hatches etc, leaving just one hatch open into which a decent size fan can be directed (will need some sort of seal wrapped around) the purpose of which is to INCREASE the air pressure inside the boat. Turn the fan on and walk around on deck painting soapy water at all suspect locations eg hatch seals etc. If it bubbles…..you found a leak!
Pretty much that exact test is now standard procedure for high-efficiency buildings on shore. Close everything up, pressurize the interior with a powerful blower, and look for leaks. I’ve done it a few times with a fog machine in the suspect room, which produces nice little jets of fog coming out at any likely water ingress points. In the Canadian climate, another popular version is to wait for a cool, calm winter night, pressurize the interior, and walk around tthe exterior with an infrared camera; leaks show up as bright flares on the IR image.
Those kind of tests could probably be carried over to a boat scenario, but I think a pressure hose from the outside is likely a better test. At sea, deck openings have to be sealed against waves coming over the deck, i.e. fast-moving water under pressure. That can often cause a seal to fail even if the seal was fine under static conditions.
Hi Steven, Matt
good, thought provoking stuff, and thanks for the nicely illustrated link, Steven. Just shows what can and should be done with a little care.
And surely it ought to be possible to use the sort of techniques you outline, Matt, in a major yacht production facility? Does anyone know whether one or other of the majors does so?
Best wishes
Colin
Hi Steven and Matt,
There are both good ideas for leak finding and well worth doing. However, neither solve the fundamental problem with older boats, particularly those built in GRP, that you can do all the dockside leak chasing you like but even so the boat may, or most probably will, leak like sieve through the decks as soon as she subjected to the flexing induced by offshore swells.
It took Poor Stupid Bob some eight years to get his boat really dry below when offshore, even though she did not leak a drop when sailing inshore or tested with a hose. In the end what worked was to remove every single fitting, port, and hatch and re-bed them and at the same time fix the inadequate mounting flanges and backer plates provided by the builder—it would have been easier to build a new boat!
Great article Colin,
Production boats are not built with the idea that sooner or later you’ll developed leaks. Very few manufacturers use proper bedding techniques that ensure that the core material is protected and will force any leak outside for an easy visual and tactil inspection. Most of the boats I have seen are finished like a house with no proper access for visual inspection. By the time you can see the water the repair is structural. Rubber butyl, neoprene sheets, and epoxy are the best tools to keep a dry GRP boat. Of course metal boats are definetely at an advantage here; less holes, dryer the boat!
Hi Patrice
absolutely right, and it’s just as true when you come to make good structural repairs, e.g. after a collision or similar. Inner mouldings have many advantages, but they do make it very difficult indeed to get adequate access visually and physically to the place under repair. And as far as leaks are concerned, they’re a bit like the roof of a house – the leak may be many metres away from where you can observe it, the moulding has simply channeled it to somewhere else, which makes tracking down the source of the leak almost impossible.
Best wishes
Colin
“Maritime and Coastguard Agency rules for all coded small commercial vessels in the UK insist that all foredeck hatches be reversed, so that the hinges are at the leading edge, which certainly helps reduce the chances of leaks, but at the expense of spoiling the air flow when at anchor, which is more than a nuisance in tropical areas.”
I read in a book by L.Francis Herreshoff that the natural flow of air in a boat facing into the wind, as at anchor, was into the companionway and out the forward deck hatch. I experimented by having someone light a wooden match at the companionway while I put my nose near the forward hatch. Sure enough. Try it on your boat.
Fine article.
Steve Guy.
Hi Steve
that’s true, and I’ve seen the drawings, but I think it really mainly applies in light airs. When you’re in the tropics, the best way to get air through the boat is to have forward opening hatches that can be adjusted to divert the breeze through the boat. When at anchor so the boat is (generally) lying to the wind, this works really well. If your hatches are aft opening, then windscoops or similar are the answer, but they’re more work, and more prone to damage in squalls. With the arrangement we have (3 forward opening hatches on the foredeck and coachroof) we never bother with our Windscoop, unless we’re alongside and the wind is on the beam.
Best wishes
Colin
I disagree when you say that at teak deck should be avoided at all costs. A traditional teak deck more than 50 mm thick is normally nice and water tight. Alu decks are also water tight, but ugly and has no charm. The problem is that many boat builders have tried to minimize the thickness of the traditional teak deck and to use teak as a decoration. My favorite deck is a 3 inch thick Oregon pine wood deck: Very beautiful, not slippery to walk on and easy to keep water tight. In the arctic, alu is not only ugly, it is slippery and cold while orgeone pine is nice and safe to walk on. To me sailing and walking on a traditional Oregon pine deck is a pleasure. I have sailed many ships with steel decks, but that has been commercial ships. The steel decks did not leak, but they where ugly. I prefer a wood deck on a yacht. In my opinion Johns statement that there should be no wood on a yacht is a rather strange opinion. Wood is not an enemy, it is around us always and rather natural. Of course you need to learn how to use it in a ship and how to maintain the wood. One of the strongest ice going boats ever built, “Fram” was made of oak and sailed to 85 N a long time ago. No alu boat has ever been close to that latitude.
Hi Svein
perhaps I should have been clearer – what I was talking about was a modern teak deck, which is little more than a veneer, either screwed or glued on to a GRP/alu/steel deck, and I’m afraid I’d stick by my opinion that these are troublesome, especially if they are screwed down on any of the above materials, sooner or later.
A solid teak deck is different, and if correctly installed by skilled staff with top quality teak is a thing of beauty and practicality. But when did you last see one, and where would you find the wood?
And many years ago I worked on an old sailing trawler with pine decks, and whilst they were lovely, they were old, and leaked copiously unless kept damp – we had to hose them down twice a day – in Scotland! Beautiful, though.
And as I’ve posted before, I love wooden boats, like the lovely pilot cutters built by my friend Luke Powell, but sadly, there aren’t many of them.
Alu and steel decks aren’t lovely, but they can have a certain workmanlike charm if prepared and painted properly, and if done right they will be virtually maintenance free – and I know which I’d prefer.
Best wishes
Colin
Hei Svein
You are certainly right that Fram is a beautiful, and really strong ship. But even tough she is no match for Fram regarding beauty, you should take a look at Tara.
http://en.wikipedia.org/wiki/Tara_expedition
Sadly, the english articel doesn’t state much regarding her drift path, but the german one does.
Tara got withing 160km of the North Pole, and was therfore closer than even Fram. The accomplishment certainly isn’t the same, but she still did it. One of her skippers once told me that prepared for the drift she was no fun to sail in the Bretagne, because even in Spring she got to hot for comfort inside.
Regards
Simon
Excellent article with good comments. I am one of those poor fools who took on the rebuild of a boat (Rustler 36) “just back from circumnavigation and ready to go again”. Almost finished, and I have a new boat which I know inside out, and which is better than new. I have moved from using exclusively mastic (Pantera, Sika and family) to using butyl rubber strip for all sealing where mechanical fastenings are in place. It is somewhat more fiddly and time-consuming, but much cleaner and more efficient, eg each bolt/machine screw can also be individually sealed. And it has the benefit that it will not harden over time, and can easily be applied to a leak. I have become a real fan of the stuff. (See also the website quoted by Steven above). Most people have GRP boats and have to accept myriad holes through the deck. I have drilled out every one and plugged with epoxy, and only sealed above deck. Every through deck hole is visible from below, so that the inevitable leaks are visible. It does mean that the deckhead looks somewhat workboat, but that´s a small price to pay. Looking forward to the next chapter.
Bill
Hi Bill
it sounds like you’ve done a major job there, but I’m sure your hard work will pay off, and at the end of it the boat will be better than new. And the Rustler 36 is a great boat.
Butyl rubber is good stuff, and I’d agree with your comments re its properties, to which I’m gradually becoming converted. In the past I’ve always used the correct grade of sealant (we carry two grades of Sika and also silicone sealant), but it’s not always easy to come by. Where we’ve used butyl rubber it has been far cleaner and neater to use than Sika (which gets everywhere), and has, so far, worked flawlessly. Lesson learned!
Best wishes
Colin
Great article Colin,
Your idea of putting wave breaks around the front and sides of our forward hatches was brilliant. When green water does rarely come over the bow of our Boreal 44 it is a wonder to see how the wave breaks relieve the pressure on the hatches. We have learned over the 40 years of sailing to trust no hatch no matter who makes them.
Hope you make it to Martinique soon.
Hi Steve
thanks for the kind comments, and I’m delighted they’ve worked so well on RC Louise.
I wish I could claim that I’d dreamt up the brilliant idea of these simple devices, but as I said in the article, I first saw them back in the seventies on an old ocean racer, and I’ll bet they weren’t a new idea then – and, boy, those boats were wet on deck, so they were really needed!
Leaving Bequia this morning, so we’re on our way North via St Vincent and St Lucia.
Best wishes
Colin
We have first hand experience to support John’s (and other’s) suggestion that water dams are required and effective around foredeck hatches. We have the Goiot Tradition hatches that John recommends, and still found that beating into weather, when it was coming green over the bow, the hatches leaked.
Any engineering analysis shows that gasket on a hatch held down by two handles and a hinge must be fairly soft if it is to seal. Problem is that the water pressure to distort this soft gasket is not very high, so it is bound to leak in a heavy horizontal water flow. The 2″ or so high dams prevent the direct blast. We have beaten into 45 knots for 28 hours with lots of green water and no leaks, since adding the dams. Before that we had dribbles in such conditions. (BTW, even on a foam insulated aluminium boat, you can weld the dams on. We did)
Bedding trick
We bed hardware with Sikaflex, using generous amounts, and have never had a leak. The yards are often stingy with the bedding compound, not to save cost of the goop, but to eliminate clean-up labour.
We found an easy way. First bolt the fitting in place, to check that all is well, then smear the fitting and surrounding deck with Vaseline or cooking fat.
Remove fitting, cover with Sikaflex, and bolt it down tight. When Sikaflex is quite cured (usually next day) run a knife around the edge and the excess Sikaflex pulls off easily. Scrub with soapy water to degrease.
Vaseline is the most effective, but takes more soap and hot water to remove.
The grease is much faster and more precise than masking tape. More importantly the Sikaflex does not get under it
The idea of countersinking bolt holes makes sense to me too, but we have never done it.
We fill bolt holes with Sikaflex, and also Sikaflex the backing plate. Same Vaseline trick to reduce clean-up work to a few minutes.
Hi Neil
sorry for the delay in replying – we’ve been anchored in a remote bay on St Vincent. You’re absolutely right about the water dams – we came across from St Vincent to St Lucia with 30 knots + at times through the confused conditions off the North of St Vincent with some solid chunks of water coming over the decks at times, and not a drop got below.
And thanks for the great tip on vaseline and Sikaflex – I’ll definitely give it a try, as cleaning up after Sika is a pain in the neck.
Best wishes
Colin
Bonjour
Cet article me concerne particulierement, j ai une fuite sur mon HANSE 400
introuvable pour l instant dans l attente d une expertise ( voir article fuite sur mon blog site Web) avec des amis navigateurs nous avons essaye de la localiser comme defini dans l article Morgan ? …..
Ce sujet d article est important et confirme le professionalisme de votre forum
Bien cordialement ULYSSE
Hi Daniel
bon chance avec la fuite – c’est toujours une problème de les trouver avec des bateaux modernes en GRP.
Et merci pour les comments généreux!
Cordialement
Colin
I am struck by the contrast between these hatches set in substantial wave breaks and the propensity to install flush hatches on many new “sold as” blue-water vessels.
Do flush hatches offer the benefits of avoiding solid water hitting the seals and possibly prising open the hatch lid? Or are the rather insubstantial looking draining channels around the hatch simply not going to cope with the volume of water or get blocked thus putting the seal under standing water?
I would welcome Colins views.
Hi Philip,
Colin may not see your question. See Comment Guide Lines (#3): https://www.morganscloud.com/2013/11/10/aac-comment-guide-lines/
As to flush hatches. I have no personal experience, but the idea of protecting the seals from direct wave strikes seems like a good one, however done. That said, in my experience, and I have tried to sleep under a lot of leaking hatches in my ocean race days, what really counts is the quality and rigidity of the hatch and the size and quality of the seals. Also, if the structure abound the hatch flexes, as it does on many lightly built boats, no hatch, no matter how well built with stay watertight for long.
Bottom line, many, (most?) production boat hatches are not up to the job once offshore.
Returning to flush hatches, I don’t think that the fact that the seals will be, in effect, underwater while the drains work is an intrinsic problem, since an inadequate hatch is going to leak and time water comes aboard, anyway.