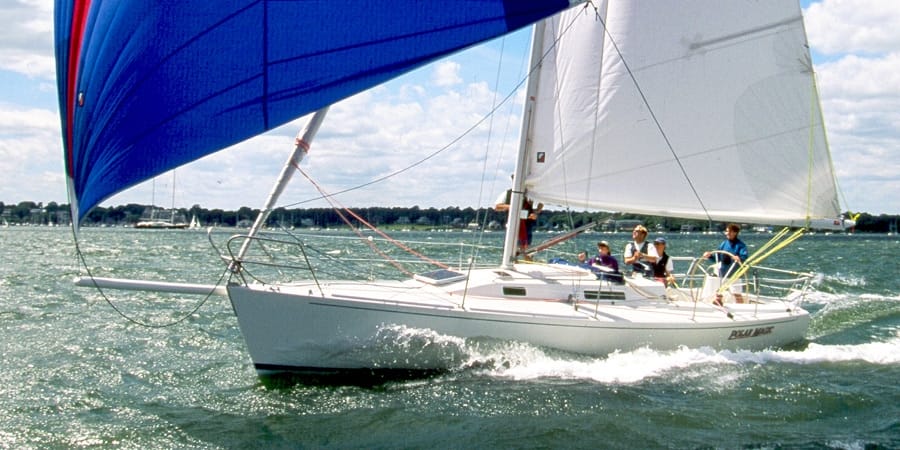
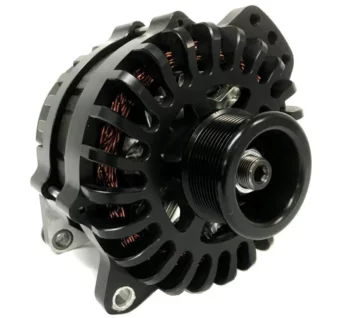
Scuttlebutt have an interesting two-part story about upgrading the electrical system in a J/105. Worth a read, even though this is a racing boat.
To me the takeaways are:
- How terrible the electrical systems are in production boats, to the point of useless, at least for offshore use. They were running the engine 8 hours a day to keep up with demand!
- Replacing the stock alternator driven by a single belt is job #1 in any electrical system rebuild.
- Replacing the standard internal regulator that ramps down charge current way before the batteries (lead or lithium) are even close to charged is part of job #1.
- Details like properly crimping battery cables are vital.
- In most cases the best bet with a production boat electrical system is to tear the whole battery and charging system out and start again.
- Read the manuals, several times.
- Most of what you see out there on YouTube about lithium is bogus.
- A dedicated and isolated start battery is the only way to go. Off/one/two/both switches are just silly.
- Seems like Electromaax has some good kit. I spent a little time on their web site and was impressed.
All useful, but the biggest takeaways are:
- Just getting the alternator and regulator right reduced charging from eight hours a day to one.
- They would have got the same benefit with an appropriately sized lead-acid bank, but it would have been bigger and heavier, so in this case lithium was a clear winner, but only for that reason.
- Without the alternator and regulator upgrades, upgrading to lithium would have been a total waste of time and money—getting charging right is the key to success.
Much more on electrical system upgrades:

One thing they didn’t mention was alternator cooling. I replaced the stock alternator on my Volvo D2-55 with a derated AC Delco unit. Even derated, it regularly bumps up against the temperature limiter in the small engine space typical of sailboats. Now to install a fan…
Hi Michael,
Good point, particularly in a tight engine space like on the J/105. No point in having a big alternator if the voltage regulator is forced to pull back because it gets hot.
Hi Michael,
Heat is definitely a good point, if you start with a high ambient, then you have less temperature rise that you can tolerate. The typical reaction to this is to install a blower which certainly helps, especially with small engines. On big engines, I have run into many instances of people being unhappy that the blower made almost no difference and it is because the engine is already a big blower so adding a small one can have a small incremental effect. Big engines (not your Volvo but something that is common on trawlers) require big blowers.
The alternative or more targeted blower approach is to duct cold air to the alternator. If you figure out the fan direction, this is pretty easy to set up. You don’t want to put the duct right on it as you will create hot and cold spots which can lead to overheating without realizing it.
Similarly, the engine is not being helped by ingesting warm (less dense) air so it can make sense to duct a cold air intake. However, in this case it is crucial to think about your overall engine room temp and blowers become crucial as some items often found in there simply can’t take the increased temp if you lose the main cooling source being the engine pumping air.
Eric
I made this upgrade, save the LiFePO4 back in 2018. I chose Electromaxx as well. John was very helpful. He and his team are a wealth of knowledge. We went with the Aquamaxx 140 amp alternator, the Emaxx Pro external regulator with sensors, and the serpentine belt kit. There have been many upgrades in their equipment since our purchase. Ours still functions perfectly.
Excess heat generated from the working alternator was an unexpected issue that came up after the installation. I noted that the regulator would reduce field output to 50% much too often for my liking. After some thought, I chose to install a 4″ fan to draw air from the interior of the boat through a couple of strategically located holes I made at the front of the engine compartment and expel it from a cowl that I cut into the transom. I located the 4″ tube behind the alternator to suck the excess heat away and out of the boat. In my opinion this is superior to pumping salty air from the exterior into the engine compartment. My method has not caused any additional rust to occur in the engine compartment in the 5-6 years it has been used. As an added benefit, the fan installation allows me to selectively cool the engine compartment after motoring for any period of time. Less heat in the cabin is a good thing, depending on your latitude. I have yet to switch from AGM to LiFePO4. That may be a project for another boat, or another year. I agree whole heartily that a proper installation will essentially require rewiring the charging system.
Our installation of the higher output alternator yielded results that made it very worthwhile. We have a single 105ah start and two 105ah house batteries wired in parallel. When needed, we will run the engine for an hour or two at the beginning of the day to put some charge back in the house bank and make some hot water. Our 350 watt solar array will take it from there.
Hi Michael,
Sounds like a very well thought out and installed system to me. I also think that you did this in the right order: get the charging really well sorted out and then, if necessary, change to lithium. In my view many cruisers spend way more than they need to and still have inefficient systems as a result of coming at the problem the other way around.
I also installed an Electromaxx 160 amp alternator, serpentine belt kit and external regulator last year on a Cal 44. Electromaxx was the only option I could find for a belt kit for the Westerbeke 64A engine. So far no issues. John at Electromaxx was great to deal with. Tech support was also great and quickly solved the one issue I had when I mistakenly installed the wrong software update on the regulator.
I had hoped to get one more season with the existing AGM bank but no such luck. So I made the switch to lithium. The boat is in Mexico so the options for batteries were limited. AGM were also very expensive here. After a lot of research on this site and on marinehowto.com, I did go with drop in smart (Bluetooth) lithium from amazon mexico. It has taken some thought to get all of the solar, ac charger and alternator charge controllers settings correct. The other controllers are all Victron, so next step will be to get Victron Venus OS running on an Raspberry Pi to act as a master controller. Until then I manually need to monitor charging sources.
But before that I also need to deal with engine/alternator ventilation. Engine is under the main cabin so options are limited. Also it will need to be a continuous duty blower not a inline bilge blower. Thanks to everyone for the info re ventilation.
Hi Jeff,
Thanks for the overview of what sounds like an interesting system. On the blower, we found these blowers work quite well: https://defender.com/en_us/shurflo-yellowtail-in-line-blower
They go about 2000 hours before replacement is required, so carry a spare.