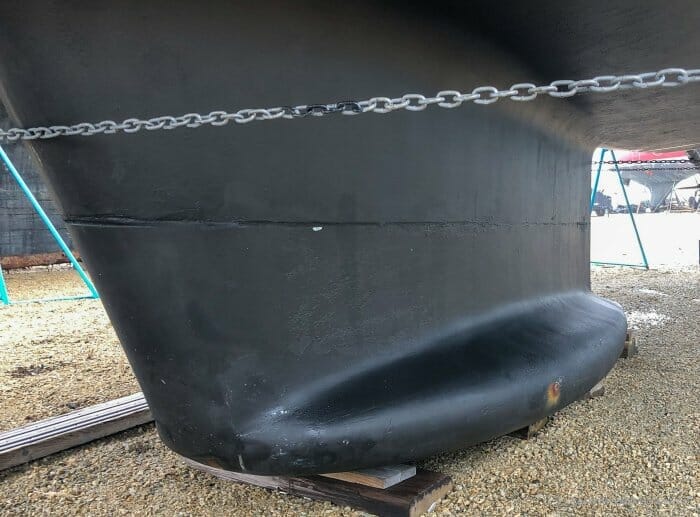
In this chapter in our Online Book on Buying a Cruising Boat I shared two keel types I would never want to own and two that are generally so reliable that if I had a boat with either, assuming she passed a good survey, I would forget the whole keel issue and move on.
Problem Bolts
But the problem is that the vast majority of used boats out there, which might be bought for a low enough price to make the total after refit attainable for many of us, have one of two keel types that can cause big-time trouble:
- Stainless steel bolts into lead.
- Mild steel bolts into cast iron.
By the way, I have written “keel bolts” throughout this series because that’s general usage, but in most cases what we are dealing with is studs that are either threaded into an iron keel or cast into a lead keel, with nuts and washers inside the boat.
How Big a Problem?
To learn about the reliability of keel bolts, I went to Bill Souter at Mars Metal, a Canadian Company that has probably built and repaired more sailboat keels than anyone on the planet, certainly in North America.
First off Bill and I talked about how common the problem of wasted stainless steel bolts is. The news is not good. He has seen bolts that have lost as much as 30% of their original diameter in less than five years.
On the bright side, Bill has also seen stainless bolts in perfect condition after 20 years.
The reason being that if stainless steel is exposed to salt water in a low oxygen environment, it goes active, which essentially means it is no longer stainless and so rusts.
And while Bill has less data on mild steel bolts (he has seen a few in his time at a boatyard before joining Mars), he (and I) can see no reason for the news to be much different.
That’s great to say, but the problem is that, based on an informal survey I did of about 50 older boats hauled out of the water, well over two thirds of them would fail Bill’s test.
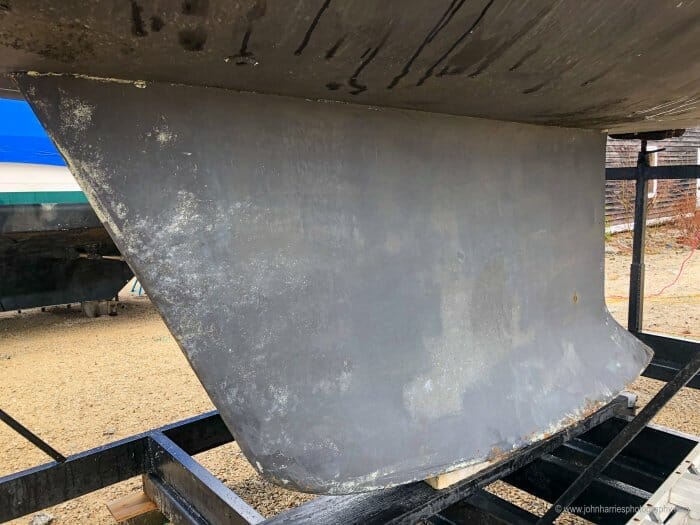
Not Good
I have long thought that the problem was worse than most of the industry is willing to admit, but Bill’s position takes things to a whole new level of expense and aggravation for any boat owner who really wants to feel secure about the state of their boat’s keel bolts.
This also presents a huge problem when buying a new boat, since no one on either side of the transaction is going to want to tackle taking the keel off.
Testing In Place
Given that, the next thing I dug into was the options for checking the state of the bolts without removing the keel:
I particularly look forward to advice with torquing, as it’s a bit of a dark art easy to overdo.
John,
I appreciate the article is about looking inside through a keel to inspect the condition of studs embedded in the keel. Before this I would be inclined to dimensionally check the exposed parts of the keel bolts using thread gauges for the applicable thread standard; easily bought but quite expensive, £100 to £300, can be rented. The next thing would be dye penetrant or magnetic particle inspection to determine if there are any cracks. My thoughts are if the top of the studs could be determined as okay, then look at the methods you mention, any issues on the top part, then move straight to stud removal and replacement. A problem with ultra sonics in steel (don’t know about lead), is that the casting process can cause internal disassociations which may prevent any further penetration into the steel and to the bolts. A difficult issue inspecting keel bolts which can’t be removed, as you show. It almost suggests that dropping the keel and removing the studs could be considered mandatory, on older boats, even if it meant machining them out. Just my thoughts. Regards, Alastair
Hi Alastair,
Nothing at all wrong with that position. Bottom line, removing the keel is always the best bet if there is any doubt.
I’m totally with you on the idea that if the heads are not in good shape then the keel comes off. More in the next artcicle.
One thing, I’m not sure how much dye or MPI will tell us without removing the keel. Dave at Mars felt that those were only useful with the keel off.
Hi Again Alastair,
Just to clarify, this is not really about “condition of studs embedded in the keel” but more about looking for wastage and waisting at the keel to hull joint, which should show well on UST.
Hi John
note MPI does not work on Stainless Steels, unless they are the duplex grades.
From my experience using Ultrasonic to test welds, it might pick up significant reduction in bolt/stud sizing but it should not be regarded as a guarantee of that all is OK. The signal may have to pass and return thru several media (lead/iron, water, air) to reach the bolt and return, all of which can cause distortions in the signal.
regards Alan
Hi Alan,
Good point, going to cover MPI and dye in the next chapter.
And thanks for confirming on UT. That’s pretty much what my source said: he would find a really bad bolt, but no guarantees.
I’ll be looking forward to hearing what Bill recommends for if your bolts are stainless and require replacing.
I’m not too concerned about the process of dropping the keel, I’m more concerned with what the hell do I do in the event that the bolts need replacing?!
Hi Jordan,
Coming soon.
Without preempting your next article, can you give a frame of reference for how much it would likely cost to remove the keel for inspection on a 40ft boat?
Hi Bill,
That’s covered in the next but one article.
Thanks for this article. Relevant to me since my Sabre 362 broke from her mooring during a storm last fall and went aground enough to develop a crack there.
Can you clarify the difference between studs and bolts? Here you say to check both:
“the stud tops inside the boat must be absolutely flat and free from corrosion, so some careful work with a file will be required in most cases.
And, of course, we must have access to the bolt ends inside the boat,”
but earlier you seem to say they are variations of the same idea? I’m a little confused but that’s not new.
And I’m interested in how to know if water got to them, of course the tops of the bolts/studs are often sitting in bilge water so don’t they always have water, or is the environment inside the keel interface less o2 rich so therefore a problem?
Hi Michael,
As I say in the article:
“By the way, I have written “keel bolts” throughout this series because that’s general usage, but in most cases what we are dealing with is studs that are either threaded into an iron keel or cast into a lead keel, with nuts and washers inside the boat.”
So on modern boats you will almost always be dealing with a threaded stud penetrating the boat with a nut and washer on it. See the photo in part 1.
As to the condition of the stud heads and nuts in the bilge, I did not spend a lot of time on that since it’s generally fairly easy to inspect visually. That said UT should find issues there too, although if it’s really bad it’s going to be obvious when we try to clean up the heads of the studs and they start crumbling under the file.
I think I figured out the confusion: I read that section I quoted as “we need to check both the studs and the bolts”, when you were saying “of course we need to be able to see them“ the use of two different terms there made me assume I was clueless!
So, it sounds like you’re saying if there is hidden corrosion there should also be visible corrosion?
Hi Michael,
I agree it would be better if the entire industry used “keel studs”. Still, this is boats where most nomenclature is based on history, not common sense!
And no, I’m not saying that “if there is hidden corrosion there should also be visible corrosion”. In fact I’m saying the opposite. The studs inside the boat, and the attached nuts could be fine and yet the part between the hull and keel top be almost entirely eaten away. That’s the reason for using UT imaging.
You might want to read some of the articles I linked to in further reading in part one. As I said there, my plan is to cover the stuff that others have just punted on (because it’s hard) but leave the basics to the articles of others.
Thanks. I apparently let specious thoughts skew my reading.
Hi John,
I’m looking forward to the solutions/repair part of this, as keel bolts is one of the areas on boats that I see as an almost unsolvable problem, mostly due to my lack of knowledge, I assume. I think the vast majority of boaters and boat professionals are in the same uninformed situation as I am. That makes this issue a big problem.
As a multihull sailor, with no keel bolts and no safety issue from loosing keels, if at all possible, I also feel a bit of temptation to gloat, but I’ll do it discretely. 🙂 As mentioned in other articles, monohulls with internal ballast and a lifting relatively light keel blade can join in the gloating. Loosing the keel is then just a performance hit, not related to safety.
Hi Stein,
I agree that keel bolts are regarded as “almost unsolvable problem” by most owners. The result is that many, like with rudders, just stick their heads in the sand. My hope is that with this series we can help fix that by really digging in to the options and costs. Still, at the end of the day, it will be up to each owner to decide how far they want to go.
Hi Stein,
On multihulls, sure that’s a benefit, but on the other hand mono hull owners with bolt on keels don’t have to worry about cracking and deterioration of the very heavily loaded cross beam joints on multihulls, a problem that I’m pretty sure is just as big in the production multihull world as bolts are in the monohull world, and one that would be at least as difficult and expensive to fix on most multihulls as bolts in monohulls.
Bottom line, boat reliability is all about design and build quality and not much about design type.
I am familiar w/ portable X-ray equipment used in field applications. I used to be the Chief Engineer for a company that made such equipment. Two parts are needed, an X-ray source, and a recording device. They are common in the power-line inspection biz and very common in ambulatory veterinary practice (think farm visit). Lower power units are hand held, higher powered units are stand mounted. Not sure how much power would be needed to image thru lead keel to image the steel bolts inside (suspect it would be substantial), but could easily image portion of bolt embedded in keel stub. Do web search for ambulatory vet x-ray imaging equipment for examples.
Hi Jeff,
That’s good to hear, but it does seem that actually getting this done practically, even for the area not imbedded in the keel that we are primarily interested in, is not cost effective or easy. One of the big problem is that most owners won’t have detailed engineering drawings, but that’s exactly what most industrial imaging companies are used to working from.
I think this is one of those many areas around boats where theoretically and practically possible are a long way apart—I have never heard of anyone getting their keel bolts X-ray imaged. That said, as I say in the article, if you can get a company to commit at a reasonable price it’s worth pursuing.
Hi John. Back in the 80’s I had a 33′ wood sailboat with a bolt on cast iron keel. I found a surveyor who could X-ray the keel bolts on site. The images clearly showed the corrosion of the bolts at the keel/Hull joint. I managed to extract the bolts from inside using a locknut on the bolt head and had new bolts machined out of mild steel and reinstalled. A bit amateurish probably but back then one did what one could on a budget. Looking forward to your next article on replacing keel bolts.
Hi Viv,
Good to hear from you again, and that’s great news that you were successful in x-raying the keel bolts. And thanks for the reminder that I need to get back to that series. So many articles, so little time. And to think I once worried about running out of things to write about!
Hi John,
2 questions that I am curious whether you came across answers to in your work or are going to cover in a future article:
1) What about boats with wet bilges? Even if the joint looks perfectly externally, is corrosion of the portion sticking up into the boat a concern? It seems to me that very few boats actually have dry bilges. I saw your comment above but my concern is for the area where it passes through the hull. On some more heavily built boats, this can be quite thick so that if the hole is close fitting, you can’t actually do a good visual inspection.
2) Lets say you did ultrasonic testing on a joint that had a little weeping and determined that the bolts were fine, what then? Do you just reef out as much of the caulking as possible and jam more in and monitor it for watertight integrity? It seems difficult to properly stop ingress without a keel removal.
Thanks.
Eric
Hi Eric,
Good questions.
1). Yes, I think that’s a concern. The parts showing are easy to evaluate, but if water is seeping down the bolts from the bilge, what then? Still, the more I think about it the less likely I see a scenario where water is indeed getting down the bolts but is not showing outside, to at least some extent. So, as I think Casey suggests in one of the articles I linked to in Part 1, it might be a good idea to fill the bilge to cover the bolts with the boat out of the water and leave it for a week or so to see what happens.
That said, your point does make me think that UT is a good idea on older boats even if the hull to keel joint looks perfect.
2). In that case, I think the keel needs to come off, although maybe not immediately, and Mars Metals agree. I have never had any luck stopping water penetrating any sort of joint without pulling the whole thing apart. The point being that even if the bolts are fine now, they will be deteriorating quickly in the future if water has got to them, at least if stainless or mild steel. Also a crack at the keel often indicates that the builder used 5200 as a void filler, distressing common according to Mars, and therefore the joint will be flexing so no repair will last and also the bolts are being repeatedly stressed in bad ways—Mars talked a lot about the dangers inappropriate bolt stressing, that you would know way more about than me. More in the next but one part.
Hi John,
Thanks for the reply. With regards to applying sealant, it seems that a boat that is hauled each winter might get away temporarily with an external application of sealant assuming that the joint does not have movement and that the patch is carefully inspected each year until the keel is pulled and properly rebedded. Not ideal but it might work if you discover a problem when the boat is not in a place with the facilities to drop the keel. However, if the joint is not what I term “stable”, then it is an all-around bad situation and you are correct that non-stable joints have fatigue issues. 5200 or any other sealant directly in the load path would definitely lead to a non-stable joint.
I realized that there is 1 more part to the question of bilge water which is how much difference fresh versus salt water makes. In our case, our current boat had lived its whole life on the great lakes before we bought it and while it was not a perfectly dry bilge boat, I suspect that helped as the bolts do look good when I remove the washers and nuts.
Eric
Hi Eric,
That brings up an interesting point. When putting the keel back, assuming that the joint has been made right and all voids filled with thickened epoxy, would you limit the area that sealant is spread to immediately around the bolts, or spread sealant throughout the joint?
I think I vote for the later, on the bases that the sealant will be fairly thin and even and therefore distribute loads well. But I’m interested in an engineering take on that since I’m currently writing about putting the keel back.
Hi John,
Definitely an interesting question. I very rarely use sealant in any of my design work so I am not sure that I can properly answer the question. I tend to design expensive capital equipment that is mostly metal so our go-to sealing methods are o-rings for static joints and rotary seals and rod seals for stuff that moves but there are occasionally other options we have to pursue as well. A few random things that I have learned and other thoughts:
-In general, I try to really make sure that I know where the load is transmitted on a joint. In metal parts, you can often get away with just holding tight flatness on both faces but in many other materials and even often in metal, it makes more sense to have a very shallow relief over a lot of the area. In the example of a keel, you can put in the effort to make the surface mate well over large areas. It gets weird to try to do known smaller areas as that will be a lot of load on the parts and you want that seam fair so it raises questions of where you would relieve. If they mate over a large area, you will end up with very little sealant if you torque up the fasteners enough prior to it curing.
-I have wondered whether it would make any sense to not seal around the bolts at all and to have a separate sealing groove nearby? The advantage is that you could not get a failure that would lead to a hidden part of the bolt getting wet and staying that way and you could see the whole bolt down to the keel.
–
Sealing dissimilar materials is always tricky.
-Anytime water and freezing temps are involved, you really have to be careful. Ideally you would have a very good seal near the outer edge and have a dry bilge so that water was basically not present. The trouble is that you can’t vent in between any of the sealing so as the water expands and contracts from freeze/thaw cycles you will get a slow progressive failure over time.
-Sealants have thickness ranges they work over and this is really important. Given the differing CLE’s on the materials and the expected temperature swings, thicker material with high elongation is better and that may mean putting in a specific sealant groove to allow that thickness.
-When torquing fasteners onto a joint with a viscous fluid on it, you have to torque multiple times over a few minutes as the surface area is so large that it takes a while to squeeze the excess sealant out. If you want some real dry reading, look up thin film theory.
-Joint stability is critical. When loads can be easily calculated, I like to have the preload be a minimum of double the separation force (note, you need to look at moments for a keel to get the separation force) to account for imperfect calculations, k factor variation, etc. In certain designs, I have run as low as 1.3 but that is a much more engineered application. Ideally, this preload provides enough clamping load that things cannot slide, if not it either needs to be increased or some other means to prevent movement is required such as dowel pins.
-Materials that creep can be a real pain in the neck for maintaining appropriate preload. Sometimes getting bolt length right can do this, other times you need to put disc washers on there, regularly retorque, or use some other trick to lower the spring constant.
If I had to do it tomorrow and didn’t have the advantage of resources to consult here is what I would be tempted to do (obviously all the prep work like cleaning would need to be done but I am skipping that here). I am sure that this could be improved upon too though.
1) Use the keel as a form and set the boat down on it with a mixture of thickened resin on the bottom of the stub to ensure the fit is good.
2) Chamfer the edges of all bolt holes through the stub for sealing.
3) (Optional) Route a small circular groove around each bolt hole in the stub as a primary sealing groove. This obviously only works on some boats due to stub thickness and bolt placement.
4) Put sealant over the entire connection.
5) Place the boat on the keel and torque the nuts several times over the space of a few minutes until no difference is found.
6) Give it a retorque after a season of sailing.
Eric
Hi Eric,
That’s great thank you. I can see clearly from your comment that we are never going to get a really perfect watertight joint. That said, it seems to me that the most efficacious thing we can do is get the joint really trued up so that the sealant is not trying to act as a gap filler and the keel is stable. I also like the idea chamfering the holes a lot. The idea of a groove is interesting too.
There’s no such thing as a dry keel bolt on any boat that isn’t fresh from the factory. Even if the bilges are bone-dry and the joint looks perfect from the outside, there will always be a segment of keel bolt, below the plates/washers where it passes through the hull, that is perpetually soaked in last year’s bilge water.
I think the only really permanent solution is to select the correct metallurgy in the first place. If you’re stuck with non-ideal metals on an existing boat, I might be inclined to look for appropriate corrosion inhibitors, rather than at ways to keep them perfectly dry. Or, in other words, try to control the chemistry of the liquid touching them, rather than prevent liquid from touching them.
Hi Matt,
I think you are right, the core of the problem was going away from bronze bolts in the first place. Everything else we are talking about is trying to palliate that original problem.
And that’s an interesting idea of coating the bolts. I have had great results with CRC and wonder if giving the bolts a regular spray might not be a good idea.
Spraying the tops of them probably won’t do much. But if we remove the nuts (one at a time), vacuum out the water and crud, inspect the bolt, then spray some inhibitor down there before reinstalling the nut…. that might do the trick. And, hey, we get to inspect for deterioration at the same time. The question is which inhibitor to use. CRC No. 06026 seems like a good candidate, but I ought to ask their chemists before making any recommendations.
Chemicals exist that make it possible for a cast-iron engine block to survive for 40 years in direct contact with hot cooling water, so it certainly seems plausible that an inhibitor exists that’ll work for stainless steel immersed in cold bilge water.
Using SS instead of bronze here seems like it was a false economy. 1″ threaded rod is $100 a foot in silicon bronze, or $42 a foot in SS-316…. and that’s small-quantity retail pricing; wholesale should be substantially better. Saving $300-$500 in materials on a $250,000 boat, but adding a maintenance point that will cost $500-$1000 to inspect every 10 years, is appealing enough to a production accountant but doesn’t make sense to me as an engineer or as a boat buyer.
Hi Matt,
Really interesting comments as usual. Two questions if I may:
1) Silicon bronze bolts would seem a logical choice when dealing with lead keels, but what about cast iron keels? I understood one of the principles in limiting corrosion is selecting metals that are “similar” (degree to which they are more or less noble)? So in this regard (putting aside crevice corrosion negatives of stainless), would stainless steel bolts or studs be a more logical match than bronze for use with a cast iron keel, if we are trying to limit overall corrosion within the keel structure?
2) And, on the basis of eliminating water, could pure silicone sealer be a better corrosion inhibitor and insulator than “chemicals” that might loose their effectiveness in two to five years, and need replacing to remain effective (as with engine coolant water additives)?
Thanks. Rob
Hi Rob,
You are right, all the reading I have done indicates that bronze will not work into cast iron since the two are too far apart on the activity scale.
For cast iron I think the best bet is good quality galvanized steel bolts. More on that in a future part.
As for silicone as sealant, as far as I know silicone is not recommended by any expert I have ever talked to, or read, for underwater use. On the other hand properly applied Polysulphide has a 60 year track record of lasting for decades under water. The point being that in most cases on keels, as far as I can see from all the observation and reading I have been doing, failure of sealant is a lot more about poor engineering and installation—most notably using the sealer, often 5200, at a gap filler, which it is not intended for—than failure of the sealant itself.
Hi Matt,
Good idea on removing the nuts and spraying, I think. I will look forward to hearing what CRC have to say.
And I did the same calculation on bronze bolts and was equally distressed that builders took this step for so little savings. But then again we are talking of the same builders who saved less than $50 a boat by using mild steel plates in rudders.
Hi John,
Wanting to check at least one of our 11 keel bolts when we are on the hardstand for our annual scrub down (no winter lay-up here). From the reading thus far, I am thinking if I draw out one bolt, and if it is in good shape, it would then provide a solid datum point to ultra-sound the rest (accepting that it may not tell the whole story). I see re-sealing again as the critical issue (using polysulphide, thanks), as when we replace the bolt (it’s not a stud) the hull/keel join will wipe the new sealant off, and if we force too much sealant into the tapped cast iron keel (which is likely to be less than perfectly clean), we may never get the bolt home properly, due to trapped hydraulic/air pressure. Might we be better to use say an insulating lanolin grease, or with one of Matt’s chemical “inhibitors”? Eric’s idea to have a chamfered hole is good, but we are not planning to drop our 17 yrs old keel, as we have no gaps or weeping at the hull/keel join and no rust showing.
SO, I am really looking forward to the coming article on keel bolts / studs and learning more, especially on torque settings and suggestions for maintenance/inspection cycles.
And by the way, we don’t have a “project boat” and we are lucky enough to own our dream boat, so we won’t be looking again either. But I am finding this article series fascinating reading. Far from “sticking to what we know” as someone rather strangely suggested earlier, please don’t – rather keep challenging our thinking on this and the status quo. This is really great work from you and Colin. It’s then up to us to decide what we apply, and what is or isn’t attainable.
Thanks, Rob
Hi Rob,
Hum, on drawing a bolt, I think that’s a good idea, assuming you can get it out without it wringing off. And if it does wring off, although that would be heartbreaking, at least the question is answered. More coming on what to do if that happened.
On what to do about putting it back, it’s a hard one and I would not pretend to have any definitive answer. I guess if the bolt is in really good shape after 17 years maybe we could say that the question matters less, since clearly the environment is not bad for corrosion. I think, if it were me, I would give it a thin coating of polysulphide. I have just had amazingly good luck with the stuff. Worst case, if won’t go back properly with the goop on you can always pull it again and wipe some off.
I guess the other path I might consider, given that the joint looks good, would be to get two new bolts from Beneteau, put a cut in one and then have a UT technician check the bolts with the two new ones as a base line. The guy I talked to thought that would be quite accurate.
You could also torque the bolts after that for added comfort. Hopefully Beneteau will have the right values still. That said, in your case with bolts not studs, torquing will be much less precise because the threads in the keel are probably pretty corroded after 17 years and you have no way to clean them, other than drawing the bolts. But even so, if the bolts and threads can withstand the process that’s another indicator that they are not too badly wasted.
And finally, thanks very much for the kind words. This series, particularly the part on keels is really difficult to research and write since there is so much ambiguity, so your encouragement is doubly appreciated.
Hi Matt,
Unfortunately I feel you are right that it is hard to actually guarantee that any bolt is dry with the way most connections are constructed.
I too would be interested to hear more on corrosion inhibitors if you find anything out. Crevice corrosion is something that I simply don’t know enough about to comment on the effectiveness. In other applications, I have had pretty good luck with this sort of thing. Heck, I almost never install a bolt dry these days in any application, I have learned that lesson the hard way enough times.
Eric
I’ve done a lot of ultrasonic testing in refineries (API licensed inspector). The short version is that ultrasound will only tell you if the bolt is SEVERELY compromised, like far less than 1/2 remaining or seriously cracked. I would do it for a boat I was considering, only because I have the gear and would be testing other things that ultra sound is good for anyway (base of mast, tanks, locations of embedded backing plates), but I would put very, very little faith in the results. If I determined a bolt was bad, I would believe that, but if it seemed they were all good, I would know that they might still be pretty ugly, particularly if I did not have a matching bolt for calibration. I would put more faith in the condition of the nuts and the condition of the hull/keel seam.
Hi Drew,
That’s pretty much what the technician I consulted said, so thanks for the confirmation. That said he was a bit more optimistic saying that if he saw little variation between the bolts that would be good news. That said, I agree, no guarantees. But then again when were there certainties in any of this? So my thinking is still that UT can play a role in some situation as a risk evaluation tool, but not in and of itself any sort of guarantee. More in the next chapter.
Many fine wooden boats had bolted on keels, often of iron. My dad’s boat, built in 1950, had a massive iron shoe running all along the bottom of the full keel. Cement was poured over that, denying access to the bolts, which were surely galvanized. The subsequent owner circumnavigated for 11 years before she was lost in a hurricane, 42 years after her keel was laid. No one ever worried about the bolts, as far as I know. I guess we should have been concerned, unless wooden construction techniques were different and better than GRP.
Hi Terence,
Yes, they probably should have been concerned, but then again with a configuration like that the bolts would probably have been very lightly loaded in comparison to a modern fin keel design.