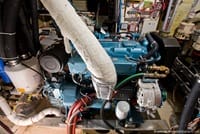
When we were crossing the US/Canada border heading for Maine to start the repower project on Morgan’s Cloud, a US Homeland Security officer asked the usual questions about what the purpose of our visit was.
After I explained that we were replacing the engine in our boat, he asked how long we would be in the US. My answer was greeted with a look of incredulity and “THREE MONTHS?”. Clearly the officer had never owned an offshore sailboat.
The way we came up with the three month estimate was to list everything that had to be done, assign reasonable times to each task, total them up, and then double the result—pretty accurate as it turned out.
Here is a photo essay on what we were doing all that time.
John,
Nice fix for the water tell tale, a dual purpose solution and one I would like to steal. Thank you.
Hopefully it should be a long time before you get oil or diesel in the bilge but do you have a separate engine room bilge and do you have an oil staining/ filter unit to “clean” the water?
You obviously have spent a great deal of time considering what you like to have and how to achieve it. A good job well done. ( I hope you remembered to fit the lowest nut to the aquadrive plate missing in the photo!)
Hi Andy,
Feel free to “steal” it. Actually I have to give credit to Greg Sanborn, service manager at Billings Diesel for suggesting it.
No, we don’t have a separate bilge for the engine room, although it is something I would do if building a boat from scratch. Nor do we have a filter on the bilge pump, although it is a good idea. My only worry would be restriction on the pump reducing flow in an emergency. But then again, one could install a bypass valve.
We are very careful not to get oil in the bilge, to the point that we have oil absorbing pads under the engine at all times. Not only to catch any leaks, but also so that we will see any small leak before it gets worse.
One of the big reasons that we took the Cummins out was the amount of raw fuel and oil that it was sending out the exhaust due to the cylinders being out of round.
John
Do you use an oil bypass filter with dryer and if so what brand?
Have you considered using an electric oil pump to pre lubricate the engine before starting? I think I read somewhere (Calder?) that most engine wear comes from the debris that the standard oil filter doesn’t filter and the first minute of running your engine when it is poorly lubricated.
Since I’m asking questions: Do you pre heat your engine block and fuel in Arctic conditions?
Hi Carter,
No we just have the standard Perkins oil filter installed.
We have considered a pre-lube pump, but did not install one. If the engine has not been used for more than a few days we pre-lube it by turning it over on the starter motor with the key off, so it does not start, for about 30 seconds until we see oil pressure on the mechanical gauge. This was a big reason for the starter button in the engine room and the mechanical gauges.
Note that you must be careful doing this if you have a water lift muffler since you are pumping water in to it with no exhaust flow to clear it—you can flood an engine that way. That is one of the reasons we have the drain valve on the lift.
I guess I would generally vote against adding a lot of after market stuff like bypass filters and pre-lube pumps since each is just another thing to go wrong. Also a big leak in all the additional piping could be catastrophic.
This is an industrial engine that Perkins specifies to go 10,000 hours and presumably they are assuming that life in the configuration they sell it. And 10,000 hours should see me out of the voyaging business!
John,
I’m glad to hear it all worked out in the end. You are very fortunate to have found such a meticulous team of technicians to put it all together.
As for the pre-lube stuff, I’ve never come across it on any engine I’ve personally encountered. I can see the possible benefit on a very large engine, but with modern oils (which tend to cling to rings, cams, etc. for a very long time) and a smaller motor (which will likely achieve OK oil pressure in the two or three seconds of cranking before it catches) it’s not something I’d worry about too much. Unless you have one of those Yanmars with the upside-down filter that drains every time you shut it off.
In most of the engines I use, we change the oil because of age or convenient timing long before the required intervals are reached. Sure, you end up spending an extra few dollars on oil and having to carry a bit more back to the recycling depot, but I suspect it’s still cheaper/simpler/has fewer failure modes than bypass filters and such, at least for smaller engines (say under 8 litres or so).
I’ve been complaining about cramped, badly installed sterndrive engines at the last few boat shows…it’s nice to see you showing off a setup that, although certainly not simple, is relatively organized, accessible, logical and soundly put together.
Hi Matt,
I think you are right that a pre-lube system might be worth it for a larger engine.
The Perkins has an upside-down filter too but it has a check valve in it that stops it draining when the engine is stopped. The result is that oil pressure comes up very fast, a matter of less than five seconds, even when just cranking with the starter motor.
On the flip side, the upside-down filter is messy to change, but not as bad as the side mount filter on our generator. Engine designers should be forced to do a few oil changes on their creations. On the bright side, Perkins provides an oil change pump as standard.
Ok John, that exhaust system won’t work for me, with my totally dry system. Looks like a great system though.
On the boat I ran in Antarctica, the “tell tale” of water to the cockpit was led high enough to get a small bucket under it. Great for cold weather, when motoring we always had a nice warm bucket of salt water in the cockpit for warming hands, washing stuff with, or defrosting anything.
The cooling was always blocking with kelp in the Chilean channels so it was always reassuring to be able to look down – and see that stream of warm water.
It’s good to see the bolts wired on the drive, I had the Drive Saver bolts come out once when on a freind’s boat, we went astern, there was a bang…and then water started pouring into the boat! The still spinning shaft coupling had totally undone the stuffing box packing nut, easily fixed but…
So now I keep a close eye on them; maybe I should also wire them.
A very nice installation. I found your site as I am perseverating on the exhaust elbow in our 1975 Olympic Adventure 47, also a center cockpit.
Now that you have had the water separator for some time now, do you still prefer it to a wet exhaust system? The lower back pressure would be a very desirable feature at the expense of more complexity.
We replaced the stock elbow on our newly installed Beta Marine 60 with a much higher elbow (a good foot above the water line) but have met with disappointment as we have broken welds twice near the manifold. We are in the process of modifying the existing system to include a stainless, flange expansion joint or flexible coupling to absorb the motion of the engine. Your installation looks like vibration has been well addressed as well, something we may need to attend to in the future.
Hi Michael,
Yes, we are still very happy with the water separator exhaust system after 1500 hours of use.
And yes, preventing cracks in any ss parts of an exhaust system is a challenge. It seems that heat, ss, and vibration are a tough combo.
We used the standard Perkins ss mixing elbow, but added the riser between it and the manifold. So far, no problems with the riser. Having said that, we carry a spare mixing elbow.
Hi John,
I am fabricating a custom high rise exhaust elbow for my new engine.
It is a challenge to build and install substantial on-engine braces to support the weight of the exhaust elbow.
Would you be able to share any photos or ideas for supporting the exhaust elbow with on-engine brackets or braces?
Thanks so much John!
Kind Regards,
Kevin
Hi Keven,
You can see the one brace on our dry section in this photo https://etugri87v3i.exactdn.com/wp-content/uploads/2012/01/JHH5_102200.jpg.
So far (1800 hr) all is good.
Hi Kevin.
We fitted a new Yanmar 3JH5E 3 years ago with an optional high riser exhaust elbow, also from Yanmar. Not sure what the material is, quite light, some sort of alloy, defintely not stainless. It’s a very nice piece of work, with the exhaust gases passing through an inner sleeve for the first 3″ and the cooling water being injected into this “jacket” before mixing with the exhaust gases. It was expensive but worth the money. Maybe other engine manufacturers offer similar and it might end up cheaper than diy!
Two other diy mods I have, prompted by a trip across the Indian Ocean, are a drain for the muffler/waterlift, and a sort of Joker valve for the exhaust exit. Nothing more than a length of rubberised fabric clamped around the exhaust exit, open at the sides. Offers no back pressure and hangs down when engine is not running, effectively sealing the exhaust against wave strike. Not my invention! Most sizeable RIBs, and all inshore rescue RIBs have them.
Yours aye
Bill.
Hi Bill,
Two very good ideas, thanks. I like the second one particularly because it is so simple.
We have something similar to both, detailed in the above post.
John
You often talked about the engine being mission critical and you are against putting on things like 2nd alternator, water maker pump or a refrigerator pump.
What is your take on using the engine coolant for the water heater?
The reason is my water heater is about 15 years old. I have replaced the hoses for the engine coolant but if for some reason the joints at the water heater side were to leak, that would mean I have to cut the hose from the engine coolant outlet and route it back to the engine inlet.
Thanks.
regards
Eric
Hi Eric,
I think that’s fine, in fact I have been doing it for years. Having said that, I like to see (and have installed) valves on the hoses to the waterheater so that in the event of a leak the heater and it’s hoses can be isolated from the engine. Also, if the engine was properly plumbed for the water heater, you should not need to route the water heater hose back to the engine. All you should need to do is turn the valves off.
John,
My 44ft came with Yanmar 4JH-HTE which is a 66 hp turbo with intercooler. Since the engine is mounted below floor board amid ship, the raw water pump is forward at the bottom of the engine which is unfortunately below the galley sink.
Reaching the raw water pump require a cotortionist and half a monkey while lying on your belly. I have decided to remove the turbo (which has ceased anyway) and the intercooler to make this a naturally aspirated engine reducing power to about 45hp.
At 2,600 rpm sweet spot (est. 33hp) , I can still do 7.0 to 7.5 kn/hr without any difference in performance.
I have 3 questions for you John.
1. You have installed the water separator for the main engine. Did you do the same for the genset ?
2. I am considering reducing the number thru-hull below water-line. Your water separator will require a big hole like 1 1/2″ and probably located amid-ship near the engine or did you route the outlet to the transom just below the water line. How is the flow rate when the boat is pumping hard on a choppy sea?
3. Your exhaust anti-surge is 90 deg rather than Centek 45 deg. Would a 90 deg induce a back pressure for the exhaust?
4. I will be installing the water flow sensor – Aqualarm to the engine raw water before the mixer. Do you have experience with this unit?
Thanks.
Hi Eric,
Here you go:
1. No, our generator exhaust exits close to the generator itself, so no need for a water separator to reduce back pressure.
2. Yes, we had to add a through hull. Water separators require a through hull right below the separator to work properly. (Moving it aft would not work.) Flow rate is fine, no problems. Like you, I did not like adding another through hull, but you can’t make an omelet without…
3. I’m sure the 90 degree turn adds some back pressure, but it’s not an issue since we are so much lower than the Perkin’s spec on this parameter. (Back pressure is almost never a problem with a water separator exhaust. One of the biggest reasons for using one.) And the using a 45 degree would reduce some of the surge protection effect.
4. We have the high temp alarm from Halyard installed in the exhaust system: http://pdf.nauticexpo.com/pdf/halyard/brochure-exhaust-alert-system/25336-7100.html
Interesting that you removed the intercooler and turbo. Did you have the injection pump recalibrate?
One other thought, with the engine that low, I would consider a dry riser. Always a good precaution against flooding, although a bit of a pain to do.
I also moved your comment. You may find the post above useful.
John
Thank you for your speedy reply.
After removing the turbo and intercooler, I did not re calibrate the injectors but they were replaced. Consumption remains at 3.3 liter/hr or 0.9 gal/hr at 2,600 rpm. I did not notice any difference before/after because at that cruising speed of 7.0 kn/hr the turbo never kicked in or it was ceased anyway.
Hi Eric,
I may be wrong, but I’m pretty sure that the injector pump will need work too. If it were me, I would check with a good mechanic on this to make sure that removing the turbo without recalibrating the fuel system won’t cause problems down the road.
Anyone else know? Matt, Eric Klem?
Hi Eric,
John is right that simply removing the turbo can lead to some less than ideal circumstances. This doesn’t mean that the engine won’t work but you will end up with less than ideal performance.
The first thing that comes to mind is that the prop pitch needs to change. For a given rpm, the prop will determine engine load. If you significantly decrease engine output, then the load can exceed the available output which results in a reduction in rpm until the max output again exceeds the load.
I am pretty sure that the compression ratio on your engine will be lower than on a naturally aspirated version. The engine will run fine like this but it will not be as efficient. They do this to limit the maximum cylinder pressure which is greater with a turbo. There are different ways that this is done but quite often it is simply a different thickness of headgasket. I don’t know how it is done on this engine.
The fuel system is another place to look. With the exception of possibly being able to overfuel the engine, this will slightly decrease your efficiency but I would not expect them to cause any further problems. I think that the max speed on this engine is the same whether it is NA or turbocharged but it is still very possible that the timing is set differently between these versions. The injectors may or may not be different, oversize injectors will be less efficient but otherwise fine. Most injection pumps have a combination of a fuel plate and some form of air fuel control (AFC). Normally, the fuel plate sets the limit of how much fuel can be delivered for a given rpm. The AFC is really there to limit overfueling in certain circumstances. I suspect that the fuel plate is different for the NA version and running the turbo one will likely result in relying more heavily on the AFC for limiting. This is really only a big deal if you have an overpitched prop.
Hopefully this is helpful.
Eric
John & Eric Klem
Thank you for the clarification.
4JH-HTE compression is 15.9 torque 66/3,600 while 4JHE is 17.8 torque 44/3,600 for one hour rating output. Continuous rating is 60/3,500 and 40/3,500.
You are spot on with the much lower power than the NA as the compression for my unit still remain at 15.9 . My consumption is based on actual consumption over 60 hours averaged at 3.3 litre/hour or 0.9 gal/hr @ 2,400 to 2,600 rpm.
I have not change the props and will take photos when the boat is out of water. Will be installing Aqualarm for raw water flow alarm.
Appreciate the detailed explanation.
Hi Eric,
Thanks very much for fielding this, it was way beyond my diesel engine pay grade.
Hi John: in a couple of weeks we will start with replacing the old Perkins 4.236 engine for a new M92B on our aluminium Van de Stadt Samoa. Question: the installation manual recommends to bond the engine to a Zinc anode via the special stud on the engine (to reduce or eliminate electrolytic corrosion within the engine cooling system and transmission). The engine is 24V insulated and then nonetheless connecting it to the hull sounds strange to me. I have a couple of big round Anodes in the hull but not sure how I could connect the engine to them from the inside of the hull and whether at all this is a good thing to do on an aluminium boat. What did you do when you installed your engine? Regards, Mark
Or do they mean just connecting it to an anode which you install somewhere in the engine room??
Hi Mark,
You definitely do not want to connect the engine to the hull or hull zincs. That said, you do need to protect the heat exchangers from galvanic action. The best way to do this is a zinc threaded into a piece of metal pipe that you insert into the salt water line and then connect said pipe to the engine block with a wire. That’s what we did.
Hey John,
Could you comment quickly on the installation of the mechanical gauges How did you install the second temperture sensor and tube to the oil pressure? Oil I guess is relatively easy because you can use a t-fitting and attach both electrical and mechanical sensors to it, but the temperture sensor is designed to be in the flow of the coolant, so you can not have them both on a tee fitting because air will trap and there will not be flow over the sensor?
Thank you in advance. We have a perkins 4.236 and want a similar setup.
Best, Conor
Hi Conor,
I built the temp sensor into the fresh water cooling circuit to the water heater, just at the point where the water leaves the block. Just used a threaded T. Seems to work well and the temp on the mechanical gauge is always pretty close to that on the electronic gauge.
John, you wrote,
“I’m going to email the URL of this post to the Homeland Security officer.”
Did you end up doing this? Seriously, so doing could help someone in the future. Three months just flies by when working on a boat…
Hi Kit,
No, never did, I would not even know where to send such an email.
I can begin to tell you guys how much I enjoy reading your postings. I am so glad i signed up for 3 years. I have so much to learn and so little time to do it that I feel blessed to have found your sailing blog. Keep up the great work. It’s so valuable to those of us who don’t know what we don’t know and don’t have 40 years to catch up!
vern aden
Hi Vern,
Thanks so much for your very kind comment, makes it all worth while.
I have a specific question for anyone with strong diesel engine experience. I’m installing a new exhaust on my elderly 3QM30 Yanmar; new pipe, a bigger 5L waterlock and a proper inverted U riser at the manifold that lifts 450mm over WLL. The top of the engine is just at WLL and most of the layout is sorted.
However I do have one component I cannot make up my mind about; I also have a Vetus LGS 50 water separator to install. There are two possible locations I can put it in, both nicely within a metre horizontal radius of the waterlock and close to the vessel centreline.
The first puts the top of the separator at 1300mm above the bottom of the waterlock, but the bottom of the separator would only be 120mm over WLL. Now this just fits into Vetus recommendations, but part of me is concerned that the waterlock is a bit low and could let seawater back up the drain line. This is made somewhat worse by the location of the existing through-hull I plan to use for the drain line that exits around 300mm below WLL, well below the recommended 75mm. (It was used for black water waste but is now redundant because we went to a composting head.)
The other location would place the top of the separator 2000mm over the waterlock (Vetus recommend a max of 1500mm) but the drain would now be a healthy 900mm over WLL. However because the lift is now 2000mm the engine backpressure has been increased.
The best number I could find for the engine’s maximum backpressure was from a 3YM30 installation manual which recommends a max of 1500mmAq. The principle contributor to this would be the height of the lift and the amount of liquid water in that line. If it was 100% liquid then a 2000mm lift would obviously be 500mm too much … BUT the line is clearly not 100% liquid. The best number I can find is around 25%; therefore 2000/4 = roughly 500mmAq backpressure, plus a bit for the line roughness and the waterlock. Using this logic I’m likely to be well under the engine’s 1500mmAq limit. Is this reasoning correct?
Or should I stick with the lower install position that just fits within Vetus’ generic specs for the separator, and add a one way valve in the drain line to mitigate the risk of seawater backing up in the wrong direction?
Hi Philip,
Sorry, way beyond my pay grade to answer. You might want to consider sourcing a system and design help from Halyard Marine in the UK. That’s what I did and the result was excellent. They ship world wide too.
These guys do this stuff all day and guarantee their work.
https://www.halyard.eu.com