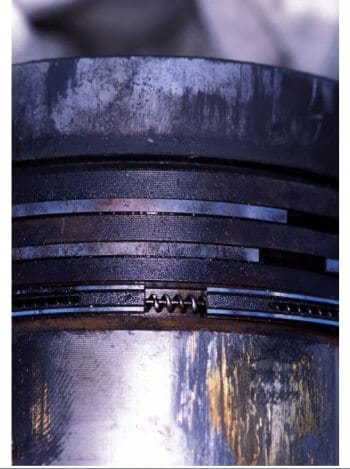
Did you know that many of us yachties are gradually, and sometimes not so gradually, wrecking our engines, as well as spending more on fuel and generating more carbon than we need to?
It’s true, so let’s look at the problem, and then the solution.
The Problem
Let’s define the problem: the single best thing we can do to keep our diesel engines happy—after regular oil changes and clean fuel—is to run them hard. What, I can hear you say?! Surely, if an engine is underloaded it will last forever (you are not alone, I used to believe this). Well no, the exact opposite is true.
In fact, what happens if you run your diesel engine at low power setting a lot is that the cylinder walls will glaze-up and then the rings won’t seat properly, power will drop, and your engine will start to suffer from the dreaded blow-by syndrome (as well as all kinds of other bad stuff), in which combustion gasses and unburnt fuel bypass the rings because they are no longer seating properly.
If you are seeing a slick on the water around your engine’s exhaust, and particularly if that slick remains after the engine is fully warmed up, you may have a glazed engine. Another tell-tale symptom is that the engine will no longer reach full throttle RPM, even though the boat hull is clean and the prop has not been changed.
If you catch this situation early enough, you may be able to correct it by running the engine hard for long periods—I have fixed a glazed engine myself this way—but if not, the only answer will be an expensive rebuild or a new engine.
Hi John,
While I agree with most of the observations and recommendations that you and Steve make, I believe that the recommendation you are making of 75% load is an oversimplification that is too conservative for most. What we are discussing at heart is how to make make engines last the longest before requiring rebuilding. Part of this is ensuring that we have good combustion and good oil life but there are also many other aspects such as ring wear. These different factors must be balanced for each specific engine design and application.
I agree completely with the recommendations to ensure proper operating temps. As stated, this isn’t simply a coolant temp measurement, oil temp and combustion temps are very important. Unfortunately, you can’t simply state a % operating load and get to safe temps. The reason for this is that there are a wide variety of engine designs with different characteristics. Even in a single base design, there can be many different configurations. For example, the Cummins 6BT came in configurations from ~120-400+hp continuous ratings and the Detroit 671 went from ~170-400+, the increase made by changing injectors, timing and turbos. These different versions need to operate at very different load ranges to get to the same oil and exhaust gas temps. I used to have a 6BT that would hit 600F EGT’s around 10-15% load, an ideal range of 750F or so around probably 30% load and by the time you got to 75% load, you were over 1100F, not a place I would want to operate most of the time. Getting into good temp ranges is important (and the ones Steve gives are very reasonable) but exceeding them is not constructive and it is easy to do that.
I think that it is important to look at the way most people use their engines and whether there are truly any issues. I suspect that it is a very small proportion of sailboat owners who actually run their engines at 75% load with any regularity. Many people run at 75% of max rpm but this is often more like 50% load depending on engine sizing and prop. There are indeed problems with light load running but they are not all that common and I suspect most people having problems are running at even lower loads than this. For example, many charter companies recommend charging at ~1500 rpm in neutral and these engines can get high hours at these low loads pretty quickly with surprisingly few problems. In the truck world, OTR trucks idle for days at a time with few problems although they do get blown out regularly. People with diesel pickups are often running at <10% load for extended periods of highway travel and while I know of some problems in these engines, they are again fairly limited.
On the flip side, there are aspects of running at higher loads that can shorten engine life even excluding damage from misuse. For example, ring wear is best approximated by a PV relationship where as cylinder pressure and piston velocity increase, the wear rate increases. In my experience, a decent rule of thumb is that an engine will burn a certain amount of fuel in its life and you can choose the compromise between power and hours provided you keep it reasonable. People occasionally try to cite fatigue as an issue but it is simply not an issue as engine parts subject to fatigue due to cylinder pressure need to be designed so that stress is always below the fatigue limit.
My recommendation would be to focus more on the transient states. Constant cold starting of an engine is hard on it, the lubrication is not great and there is a significant period of time before things warm up to normal operating temp. We should work to limit the time in this state by trying to limit cold starting through behavioral changes (I use this as an excuse to always sail on and off our mooring and the anchor) and putting an appropriate load on the engine as it is warming up. Synthetic oil is also interesting but not something I would switch to on an old engine. I think that the 75% rpm recommendation you often see is a decent starting point and that people should be on the lookout for any symptoms of issues with not being fully up to temp. Also, I agree completely with your recommendations on engine sizing and prop pitching.
Sorry for being so long winded.
Eric
Hi Eric,
Lot’s of interesting stuff, as always. I agree that the 75% recommendation is an over simplification, but in my defence I also say:
I will be significantly expanding on it in the next post, which is already written and while not as detailed as your comments, will go a long way, I think, to help people understand the issue and make better decisions about how they run their engines.
I will also cover the importance of achieving proper oil and combustion temperature.
The one place I might differ a bit with you is on how big the problem is. I’m seeing a lot of boats that are fitted with engines that are so overpowered for the hull form that many people are consistently running them at 20-30% power. And Steve D’ Antonio, who sees way more engines than I do, is seeing the same problem.
If you add consistent running at under say 40% load (not RPM) to frequent charging in neutral, as many sailboat owners do, I think the problem is actually quite common. As you say, you can get away with low loading for surprisingly long periods, but not if you never run at higher loads. A profile that fits a surprising number of recreational users.
Interestingly I had a fascinating conversation some years ago with the engineer on a super yacht with oversize generators. He was having a hell of a time with glazing because said generators ran 24×7, much of the time at 20% load or less. Finally he fixed it by installing a hydraulic take off on each and some kind of artificial adjustable hydraulic load (didn’t get the details on that). He found that using said gadget to load at 80% or so for 30 minutes every watch solved the problem.
I look forward to this next chapter, because I want to understand how PTOs and props (loads at either end of the drive train) can work in concert to get to the sweet spot where fuel efficiency crosses appropriate wear.
I also want to better understand, in light of your recent article on variable props, how prop pitching can be changed to load the engine properly.
Hi John,
I agree that designers are putting in engines which are too large which exacerbates the light load issues. As you suggest in the post, “overpropping” could really help in this situation to get better fuel economy and less light load issues without any sacrifice on usable power. Like everything, I believe in moderation in this and that going to any extreme is probably bad. When I was designing industrial air compressors, we always joked that we were really good at designing them for 50-75% speed and that we should just upsize everything. The fact was that we were trying to keep the displacement down so they were not very efficient at full speed.
On the topic of generators, this is a tricky one. Large yachts run them full time and size them for max load while they never run anywhere near there. I have seen exhaust brakes installed on them to get temps up just like adding an extra load, all of which is very wasteful. On smaller boats that don’t run the generator full time, I am a big fan of using solar or wind to get the last 20% of battery capacity which allows the generator to load up during the bulk phase and the renewable to do what it does best which is low power charging over long periods.
One thing that I should add on transients is that a turbocharged engine should not be shut down hot as the oil in the turbo will overheat.
Eric
Hi Eric,
Yes, I agree, over-propping can be great, but you need to know what you are doing and be careful not to over do it. I have 2500 words coming on just that and will really appreciate your input on it when we publish it in a couple of days.
And yes, I really like you point about using solar to top off batteries. In fact I’m looking at a installing a couple of panels on MC for just that purpose, if I can get over my total fixation on clear decks that is!
Sometimes I wonder how much damage is caused by “rules of thumb” in this field.
There’s such a huge variety of possible ways to set up and tune an engine that I have a hard time believing any general rule or guideline that looks too simple!
I agree with Eric that being aware of, and properly controlling, the transient states is critical. On engines large enough to justify the cost, I’m quite fond of oil pre-pressurization systems, for example, and I very much like to see electric block heaters on anything that’ll regularly be started below 0C. I’ve been running some interesting (although not very scientific) experiments on my cars lately, using OBD2-to-Bluetooth interfaces, and finding very dramatic changes in fuel consumption as various components warm up (notably, this process continues for several minutes after the coolant temperature stabilizes at nominal).
A major key, I think, is to get good numbers from the engine manufacturer for the specific model and rating you have. What’s the nominal-load EGT, the running-too-cold EGT, the nearly-overloaded EGT. What RPM range should it be reaching at full throttle. What are the tolerance bounds on the coolant temperature. How long should it be idled on start-up before being put under load (I’ve seen recommendations anywhere from 10 seconds to 15 minutes, depending on engine). What’s the recommended break-in sequence. Does it speak OBD2/CAN and if it does, what type of PID04 or PID43 LOAD readout is it going to give you (those are damned useful numbers if you can access them). Things like that.
The observation that “all members of a given engine family will burn about the same amount of fuel between overhauls, whether high power / low hours or low power / high hours” is one I’ve come across several times, and it does seem to be generally applicable (as long as you aren’t doing forced induction incorrectly).
Hi Matt,
I hear you on the drawbacks of rules of thumb, but on the other hand the big problem I have found is that marine engine manufacturers are very cagey with the specifications you mention. For example I had to badger the hell out of Perkins to get just two EGT readings, and I have more access there than the average boater because of my position here at AAC.
So given that the real numbers may not be readily available and that most boats don’t have an EGT I think that Steve S’Antonio’s rules of thumb, that I published this morning, are way better than nothing, particularly since he really does have very wide experience.
Having said that, you will notice that I do recommend an EGT for those planning to over-wheel by a lot.
Hi Matt (and John),
Since you brought it up….what is the practical difference between using PID04 and PID43? I understand one is calculated load and one is absolute load, but I have heard the way this is calculated varies by manufacturer.
How many of these metrics are useful for cruising operations vs diagnostics? I’ve found monitoring fuel flow to be useful as well as EGT. I also noticed John mentioned the difficulty in getting good numbers from the manufacturer.
Thanks,
Robert
Hi John,
Really enjoyed this article thanks, and Eric’s comment (Eric, I suspect you never need to apologise for being long winded on this site). By the way, I shared this article on my FB page since you have a “2 day, read for free” offer on. I will be interested to see what feedback I get from my sailing FB friends. One question is, should you make the follow-up article also free for 48 hours? My thought for what it’s worth – if sailors found value in the first article, they will sign up to read the second, at your very reasonable membership rates. Cheers,
Rob
Hi Rob,
I’m embarrassed to say that I made a mistake and it was not free until 10 minutes ago when I fixed it.
And yes, I agree, the second part will not be free. It’s only fair that if people want the whole story including specific information on what to do about the problem that they should become members, particularly since this kind of in depth how-to piece is takes a lot of time to research and write, and it’s the members that pay me to do that.
Hi.
Well, I just wanna add some thoughts on this subject.
Yes ,glazing cylinder liners is caused by Carbon build up (and will eventually end up in a scored and seized engine) mostly around piston rings and at piston top land which will polishing the liner and no oil will stuck and lubricate the polished surface. Poor quality of fuel, oil, or to cold combustion is the common reason to carbon build up in these areas as well as around the exhaust valves.
The clearance of piston and cylinder liner together with high combustion temp (full throttle) is also a factor to count on due to expansion of the piston which minimize the clearance.
Bottom line is to make sure to have high quality of fuel,oil and run on fully warm engine. The most fuel efficient is at Max torque according to the above shown “mapping-diagram”.
Regarding power for a displacement boat is a “rule of thumb” not to go less than 5hp/ton
(metric),,,,but the gear ratio have great impact of what size of an engine you should choose. It is quit a diff between, 2,15:1 than 1,66:1. On a given engine, a 2,15 can easily swing a 18″x14″ while 1,66 only can handle 17″x10″ prop. Normal operating rpm of a propeller is at 900-1300 rpm which will be the target.
Very interesting article/subject .
Thanx,,//Conny
Hi Conny,
Thanks for coming up with good engine information, as always.
I will be expanding on exactly those issues, particularly reduction ratios, in the next chapter in a few days.
One thing I would say though: I think that the old 5hp per ton rule generally yields engines that are more powerful than they should be, particularly for sailboats. In our case that rule yields 120HP, which is the size we had in the boat for nearly 20 years and in that time we established that it was without doubt more than we could use by about 50%! See this post for what we discovered: https://www.morganscloud.com/2010/04/27/selection-criteria-for-new-marine-diesel-engine/
Eric has also just done the drag calculations on the Adventure 40, and here again the 5Hp per ton rule would yield and engine that’s 30% too big.
The other problem I see with that rule is that it focuses people on top end HP, rather than usable power at cruise speed and torque, as you point out.
Hi John,
Great article and lots to ponder. I was wondering what your opinion is regarding the use of oil & fuel additives to improve oil performance and aid in reducing wear to injectors?
Love the website.
Fair Winds,
Ron Brown
Hi Ron,
Sorry, I simply don’t know anything about additives, other than that I believe there’s an awful lot of marketing BS surrounding them. The only additive I have used is Bio-Bore JF to limit microbial growth.
However Steve D’Antonio has a good piece on them here: http://stevedmarineconsulting.com/diesel-fuel-additives-part-i/
And thanks for the kind words on the site.
Thanks for a terrific article about an important topic, and thanks for long useful comments (Eric).
I think engines generally benefit great on a right running inn time. They will last longer, perform better and be in better shape. The most important hours in an engine’s life is when it is new. Many have the opinion that driving the engine neatly inn is good, because they think it will last longer. If an engine is run in under low heat the wear of the piston, cylinder and rings will be wrong in addition to the glazing problem. The day you will give full throttle then the pistons expand and the cylinders can pinch a little when the rings and cylinder wall has aligned themselves and been honed to each other, not okay to get the full potential of power.
My practice is when a new engine is warmed up and checked for any leaks I start up again and give it a lot of power, (not easy with road going vehicles). A turbo engine gets higher load on the piston rings and need fewer run-ins hours I guess. The hour amount is a little guesswork and some clear table I cannot come with. But if the engine is treated like it’s written about in on this site from its brand new it is good. I think I will lug on with a marine anchor soon from the stern, I have never tried this before since it will be my first new marine engine to run-in.
Regarding synthetic oil that is an interesting theme brought up. I do not know why the marine world do not use them much, is it the high price or the fact that we are changing oil often? But one thing is clear; I never use synthetic oil during a run-in period. That oil is so good that you have to use much more time to get the result you are after.
I’ve run inn many motorcycle engines hard with good experience. After warming up a new engine, then out on the racetrack with taut wire. Doing so my engines had less problems and was faster at the end of the season than most of the competitor´s engines that was nicely run in, -one of my secret trick at that time ☺
Hi Odd Arne,
I think that’s a really good point: Contrary to what many believe (including me up to a few years ago) a new engine will run in a great deal better for it’s entire life if it is not chronically underloaded when new. Having said that, it is important, I think, to follow the manufacturer’s guidelines on this.
Hi John.
I think most of the manufacturers are very conservative regarding load in the first hour of a engines life, and that is why most of us is in the belief that it is right to do so. Of course if a moving part has a small fault it will be broken faster under high load and I think they want to delay that to happen. Hopefully (to them) as long as possible, to the warranty time is out. The engines we get are tested and run for a little time before we get them, so they are not completely raw. Another issue is that it was necessary in the childhood of the Otto engine to run-in safe, and maybe that advice have followed into modern manufacturing.
Dave
Hi John
Thanks for the timely article. I have one of those light weight high revving modern engines.
I did not fall for the bigger HP is better syndrome. I am considering adjusting my Max Prop for two degrees more pitch. Steve Dashew recommend this years ago with the caveat “do not tell your mechanic “. Nigel Calder wrote a excellent article in Professional Boat Builder last year questioning the math behind the accepted practice of setting prop pitch to achieve WOT. His thoughts were that this was designing for non real world conditions and doing so screws up the fuel / power curve. Less RPM, less fuel, less noise would be welcome. Any thoughts?
Hi Dave,
I will be publishing 2500 words on exactly that…tomorrow.
Afternoon John:
Ouch. Guilty! What a well written and well researched article.
I know that our 4JH4-HTE Yanmar is rated for 110hp at 3300 rpm max but honestly, I mostly run at 2300 to 2400 rpm which pushes us to near hull speed under most conditions (with our self pitching AutoProp). You are motivating me to push her up to 3300 more frequently to let her breathe. The displacement waves are liquid Himalayas at that RPM but I am now a believer (after this article).
Pete & Kareen Worrell
S/V PATIENCE
Hi Pete,
Actually, not as guilty as you might think because you have an Autoprop, which is the only propeller, other than controllable pitch ones, that changes its pitch dependant on load to better match the prop to the output power of the engine. So, while it might be a good idea to run a little harder occasionally, you are way better off than most.
And thanks for the kind words, makes it all worth while.
Hi John,
Thanks for this timely topic, as my Volvos may have a glazing problem.
They are 9.5 ltr with an output of 155HP each with about 5000hrs.
They start fine, but since it is a 60 ft alloy displacement boat, it has been running at approx 8 knots for most of the time, but also many hours at around 6kn. As such I am interested in a larger prop or increase the prop pitch. Did I understand you correctly, that the blades can be twisted (with some heat I take it) I like to install some pyros and oil temps gauges.
They are 6 cyl inline non turbo and lugging within reason should not be too much of a problem as it can be with V8. Lately have been running them WOT (2000rpm) for about 1/2 hr or so, no problems.
Thanks again for your research, great reading.
Hi Rene,
I seem to remember from a previous comment of yours that your boat has a very low drag hull form and therefore I’m guessing that you have only been using a very small part of the 310 hp you have available, so yes, I think glazing is a real possibility, depending on how often you have run the engines at high load. But the fact that you have run them at WOT without issues, would seem to bode well.
Either way, with that profile I’m guessing that you would benefit from over-propping by quite a lot. And while I think that a good prop shop can change the pitch a bit, I fear that to really make a difference to your fuel burn you will need new props with higher pitch, more diameter (if you have room) and maybe more blades.
Also, given the amount you may have to over-prop I’m thinking that an EGT on both engines, as you say, would be a good idea too.
All of this is going to cost a lot, but I would guess that the payback period from fuel saved would be quite short, particularly at European fuel prices.
Hi Rene
It sounds like you have a very low power rating for the displacement which means that your engines will tend to run cool. Not knowing your boat or your engine setup, can you motor on 1 engine? Doing this is kind of like having a 2 speed gearbox. When you only use a single engine, it gets loaded much more heavily. You can have a slow “gear” where you run a single engine and then you can run both when it gets rough or you want max speed.
Besides steering balance, the big issue with running a single engine is often locking the other shaft. If you have a gearbox that allows you to lock it, that is easy but if you don’t, you would have to fit a shaft brake to do this.
Eric
Thank you John for your comment.
However, we cruise in the Seattle area, but the boat was made in Holland and it has a round underwater hull shape, and low drag.
New 4 bladed props instead of 3 bladed ones nodoubt will come with a nice price ticket, but as you mentioned, cheap compared to new engines.
Will also keep a closer eye on oil temps as they may have been too low at times and is that the major cause of glazing and/or in-complete combustion aswell?
If glazing is a problem, will higher temps at WOT be able to solve this in your opinion?
I know it is a loaded question.
Many thanks
Hi Rene,
Sorry, I was, for some reason, under the impression that you were in Europe. Out of interest, what is your water line length, beam, and displacement?
As to cleaning up glazing, I simply don’t know, other than we were able to do so by running hard. I have heard that it’s quite common in the commercial world to run an engine hard while the boat is tied to dock to clean it up, but I have never actually seen it done, and the thought of a warp breaking is really scary.
Having said that, I think you said in an earlier comment that you still reach rated RPM at WOT, and if that’s so, and you are not seeing a lot of slick on the water near the exhausts, then things are may not be bad.
(Eric Klem, any thoughts?)
Hi Rene and John,
If the engine is not underpropped and you can still reach max rpm, that is a good sign as it means your efficiency has not dropped off significantly. Getting to know the look of an engine’s exhaust is very important in my opinion as you then get to know the changes. If the exhaust cleans up nicely once the engine is up to speed, that is again a good sign. For someone who has owned an engine for much of its life, you can get an idea of how it is wearing by watching the exhaust when cold.
I have occasionally run engines both at a dock and at a mooring under load (and I did once break a 1.5″ spring line which was really dangerous). In general, I find the practice of doing this regularly kind of wasteful and usually pointless. If the goal is to get an engine up to temp, you might as well go out and cover some ground and if you can’t load the engine heavily enough doing this, you are severely underpropped (ignoring tugs).
Eric
Thank you Eric, and agree with your low power rating.
It may take relative few HP to cruise at 3-4 kn.
Infact, have used one engine without any issues, thanks to its large rudders.
I can’t block the other shaft, but am not sure if the gearbox will be damaged by freewheeling. On my dad’s yawl, with a B&W transmission and 3 blade prop it was okay to freewheel. Some apparently are ok to freewheel, and some maybe are not?
On this boat apparently the previous owners have used the PS one, because it drives the hydraulics, without blocking the other. I should ask Volvo and/or the transmission manufacturer.
Hi Rene,
I was actually thinking of cruising at your normal cruising speed but on a single engine. That engine would need to output twice the power but unless you are operating very close to hull speed, 1 engine can usually do that easily. Your prop size and associated slip would determine how much increase in rpm you would need on a single engine to run at your normal cruise speed.
Eric
Hi John and Eric,
No problem as for my where-abouts, boat in Seattle, Dutch boat and living on the Canadian prairies, gets confusing at times
The WLL is 51′, beam 17′, draft 5.6′ , displ. +/- 50 ton
When starting, usually right away, but try to always preheat both with block heaters, there is a bit of a film on the water, but am not too worried about it. Collecting vintage English cars am used to that, and proves you have oil in the sump:). The marina doesn’t approve of
running engines in gear, but its a good way to heat up your engines in a very short time. Will be on the look-out for places where it can be done, at least you can concentrate on the engines without worrying about wake and other traffic. The manual states the prop can freewheel for up to 24 hours, which has never been the case while I have had the boat, and then start it up to lubricate things. Have enough space for a larger 3 blade prop and prefer to go that direction, but first will gather some facts on both engines and take it from there.
Have always preferred the simplicity of CPP, but even Dashew told me they are not very efficient. At one time they were very popular in the Scandinavian countries, and may well be still the case?
Thank you all for your very valuable experience and sharing it with so many other boaters.
Was also quite surprised to read that some boaters find it now to expensive to pay the membership fee, and it is just those few who would benefit most of being a member.
If it wasn’t for the Canadian and USA soldiers brave efforts some 70 years ago to liberate my home country, I may not have been here. So to show my gratitude (in a small way) , I’m quite prepared to pay for those who would like to, but can’t. Just let me know.
Many thanks.
Hi Rene,
I think you are right that a little sheen on the water at start when the engines are cold is inevitable, at least with older engines that were built before the present stringent environmental regulations, and as long as it goes away when warm, you don’t have a problem.
Even our newer M92B, which is a tier 2 engine produces a little sheen on the water when cold.
Thanks for the specs on your boat. She sounds very interesting and very much the kind boat I like.
I note that at a speed to length ratio of 1 she will be doing 7.1 knots and that 8 knots is a ratio of just 1.12, so I think that you are right to be concerned about under-loading, given the size of the engines. Extrapolating from our experience with MC, and assuming an efficient prismatic coefficient, I would make a wild-assed guess that your engines are only being loaded at 50 HP each (load factor of 33%) or less at 7.5 knots.
If you do decide to increase the props I would be really interested in hearing how it works out.
And thank you so much for the kind words and offer on the site.
Thank you John and yes, the underwater ship is very much like that of a sailboat without the keel, but a somewhat wider beam. It always amazes me how little the boat moves, compared to my neighbors planing hull when larger waves enter the marina.
Funny, that you came to 33% at 7- 8 kn by calculating it and I came to a very similar percentage by looking at its (small) wake.
Thank you Eric, re ; comment apr.25 1310hrs
Will try that experiment and see the difference in Exhaust, oil and other temps.
Would like to do it with the SB engine too, but the hydraulics are powered from the PS one.
The exhaust itself are nice and clean, due to the water cooling, but unlike most diesels, the oils in both engines don’t turn black, at least not for quite a few hours.
This is a drum I beat regularly, and the resistance to it is both interesting and curious. Sailing vessels, with over-powered trawlers a close second, are among the worst offenders. I inspect these vessels regularly and have torn down many an engine, the evidence exists. While I wouldn’t call it an epidemic, it does happen, and I believe it’s easily avoidable.
The 75% load aspect is also an area readers often understandably fixate on. It’s difficult to calculate this number without a load instrument, and most small diesels don’t have one. In that case, WOT less 200-400 rpm (depending on the engines WOT rpm) will attain the goal, which is simply maximum safe operating temperature for oil and exhaust. Ultimately, if oil temp is at or over 180F and exhaust temp is at or over about 450F you are likely appropriately loaded.
When folks use the over the road truck analogy, pointing out how much they idle and they seem to be OK, it’s not exactly accurate because for much of their lives those engines are worked extremely hard, think climbing the Rockies, or carrying full load at 70 mph for 8 hrs, offsetting much of idling issues, and that sort of idling is becoming less and less common, many States restrict it now. The same is true for diesel pick ups (I have one, and a diesel VW Beetle too), they may run lightly loaded much of the time, but they are heavily loaded at every acceleration cycle.
Large yacht gensets are often equipped with a water cooled load bank, the very essence of inefficiency to be sure, which is essentially a large resistor that presents a healthy resistive load on the genset, which is then cooled with seawater.
Finally, cylinder glazing refers to the appearance, which is smooth, and shiny, ice-like, however, a coating or “filler” of sorts does form. The actual process is somewhat complex, and it’s broken down into two sub-groups, glazing and polishing. In the former, combustion byproducts, as well and oil and fuel, combine and oxidize to fill in the valleys or grooves in the cross hatch pattern, creating the smooth finish. The effect is usually uniform and it sometimes has a yellowish appearance.
In the latter, polishing, carbon deposits on the rings and piston ring lands prevent the rings from floating, and self-adjusting during piston movement, as well as inhibiting expansion and contraction during heating cycles. This leads to excessive and uneven pressure being placed against the cylinder wall by the seized ring, which leads to wear (as opposed to the deposits in the case of glazing). The effect is often localized vertically on one region of the cylinder wall.
The terms are often used interchangeably, and I confess I’m guilty of this, strictly speaking, however, they are different. The cause, and effect is the same, as is the corrective action, cylinder head removal and cylinder wall honing.
Hi Steve,
Thanks for the really useful additions and clarifications, much appreciated.
The other thing that interests me, and I suspect you may have come across, is the almost universal ignorance about this problem exhibited by professional mechanics in boat yards. In fact, in my experience, many of them will aggressively write-off an owners’ concerns about under-loading, and call him or her a fool for suggesting even moderate over-propping.
Hi John and Eric,
Have done a few tests with driving with one engine instead of where we normally use both.
At 1800 rpm on the PS engine, 7.1kn, EGT 480’C, oil 95’C, gearbox 70’C
WOT reached 2300rpm, 9.0kn, EGT +-700’C??, oil 115’C, gearbox 72’C
SB at 1800rpm, 7.0kn, EGT 350’C, oil 85’C, gearbox 65’C
WOT 2250rpm, 9.0kn, EGT 650″C, oil 100’C, gear 82’C
The EGTs are approx. as not sure how accurate these laser units are to read and where you point it makes quite a difference. Pointing at each cyl. head exhaust gave only +-100’C. The oil temps are also approx. as at WOT I only did it for 15 minutes or so.
I was happy with the rpm and from now on will use one engine when the speed is restricted. There was no difference in steering performance and the temps were at a good range, and feel the 3 bladed props are a good match.
With both engines at WOT gives approx. 10.6kn.
Thank you for your advice which worked out well.
Hi Rene,
Great to hear that things worked out and the articles were useful. As you say, I don’t think that a IR temp gauge is that accurate for EGT. Having said that 700C seems very high. The other thing that jumped out at me was how hot the transmissions are running. I’m no expert, but 70C does seem high. In my, admittedly limited experience, if a transmission has an oil cooler, and I think it should, then the running temperature should not be much more than that of the sea water.
When you change the transmission oil, has it gone black? If so, that would indicate that the gears are running hot. Anyway, might be worth checking with the hear manufacturer to see if 70C is ok.
Does anyone one else have any insight into proper temps for the gears?
70C, or 158F, is typical and actually exactly what I’d expect to see for a SWC hydraulic transmission (jacket water cooled transmissions, used with dry exhaust engines, operate at near coolant temp).
700C, or 1300F is high for exhaust temp, although it may be within this engine manufacturer’s acceptable range, I rarely see anything over 800-900F, and that’s with an EGT probe in the gas stream. If you are able, measure EGT at the outlet of the exhaust manifold.
Oil temp, at 115C, or 240F, is slightly above what I’m accustomed to seeing, 225F is usually the max. Oil temp should be measured on the middle side of the oil pan.
I’d check the calibration on your IR gun, measure a dark-colored mug of slushy ice water, it should be near 32F, and the same for boiling water, which should be close to 212F.
IR guns can be confused by reflective surfaces such as chrome or polished stainless steel. Dark, mat-colored surfaces are best for use with an IR gun.
Hi Steve,
Thanks very much for fielding that.
To add to what Steve says, it is hard to get a really reliable temperature from an IR gun. To get an accurate reading, you need to know the emissivity of the surface you are aiming at and this can range widely. I find them to be remarkably accurate but I still do not fully trust them and use something like a thermistor if I need an accurate value.
The cruise temps look fine but I agree with Steve and John that the WOT temps look high if they are accurate. 700C is definitely in the range of melting pistons on certain engines if you stay there for long. Some engines have fuel maps that will allow this is you overprop by a lot (lower rpm for the same power output means higher EGT’s). Also, the oil temps look high. Oil starts to break down rapidly at high temps as well as losing viscosity. When I designed air compressors, it was very hard to keep the oil feeds on some bushings we had cool enough due to low flow and proximity to the cylinder and if I remember right, the oil expert pushed us hard to stay below 220F for the Mobile1 oil we were using and said to never exceed 240F. Like all things, there is an optimal oil temperature which is neither too hot nor too cool.
Eric
Thank you all for your comments.
The EGT temps measured were high, but the spot between the manifold and water injection is shiny SS, that’s why I put a ??? behind it and the readings were not a constant number, varied wildly.
Will take more readings, and take these over a few hours each as these were all taken within an hour. The gear oil looks like new and has its own cooler.
The header tank, with its 3 thermostats build in stayed at 95’C
Was pleased to reach the max rpm with both engines, 1984 Volvo MD 100B, 9.5 ltr, 155HP, non turbo with approx. 5700hours each.
Thanks again.
John— Good morning sir. Your wife sent me this link to post my question here since I could not find an article to address my question.
I am looking at flushing my coolant system with something to clean out anything inside of it that should not be (recently took ownership of someone else’s problems)… I have a Perkins 4-108 Diesel, with a brand new Bowman Heat Exchanger that is barely over a year old installed…. I cannot seem to find recommendations using the search bar on your website… Looking for the Step-by-step + product recommendations to clean out system of gunk, and start with fresh Coolant (Peak FINAL CHARGE GLOBAL)…
Thank you in advance!
Skipper T
S/Y Explorar Conmigo
Hi T,
You can take Steve’s answer as fact, he’s the real deal and knows way more about engine maintenance than I do.
I’m sure John will have a recommendation. In the meantime here’s mine.
Usually, for large engines a quart of Cascade LIQUID dish washing detergent does a good job when mixed with fresh water after draining the antifreeze. The engine needs to get hot enough to open the thermostat so it may require running under a load. Probably, other similar brands would work, too, but Cascade does very well cleaning up petroleum contamination, loose rust and dirt. It is not a good de-scaler, other products do that, TracEcological is one supplier.
This works on generators and main and auxiliary engines, you only need a cup for the smaller ones unless it’s 4.5 liter or larger.
Usually, one good hot run followed by two fresh water rinses will leave the system clean without compromising circulating pump seals or rubber parts in the cooling system.
Refill with pre-mix coolant rated for diesel applications, what ever the engine manufacturer recommends, (I use coolant meeting ASTM-D6210 ) and if mixing be sure to use distilled water.
I was just discussing elsewhere why Dawn liquid dishsoap is the favourite of sailors and animal rehabbers (it gets oil spills off feathers, evidently; my wife is a wildlife rehabber). Now I have to bring liquid Cascade on a boat with a teenaged dishwasher? What an interesting lifestyle this is!
Thanks Steve & Marc!
Hi Steve,
Thanks very much for fielding that one. The only stuff I have ever used (on the recommendation of my friends at Billings Deisel) is the Cummins proprietary cooling system cleaner, which seemed to work fine. That said, I wonder if the Cummins stuff might not be a bit harsh for normal use, so I like your recommendation a lot. We are coming up for a coolant change and I will use your recommendation.
Diluted muriatic acid is another option, but I’d be concerned about a spill or a leak on a metal boat like we both have.
Hi Marc,
I’m no expert, but there is no way in the world I would pour hydrochloric (muriatic) acid into my engine cooling system, no matter how diluted.
Let’s think about this for a moment: you are not comfortable with the stuff around your metal boat, but you are willing to put it in your engine?
No, I wouldn’t, but it’s been used to flush out Atomic 4s engine passages (which is raw water cooled, not closed) in diluted form with some success. So, less “in” than “through”.
Hi John, I have a question on condensation in half full diesel fuel tanks in sail boats but not sure where to post the question. The comment is closed for “Biofuels Can Cause Contamination In Diesel Tanks On Boats”. Can you point me in the correct direction? Thanks,
Hi Rob,
Not sure why comments were closed on that post. Anyway, I just fixed it.
I will be “breaking in” a new Volvo D2-30. The owners manual is of no help, and contradicts the overall advice of the thread encouraging high power settings for both break in and cruising to avoid glazing. Now, to add to the confusion, an article from seaboard marine endorsing cruising at 50% or less of rated horsepower. https://www.sbmar.com/articles/low-speed-running-break-in-of-marine-diesels/
Ok, I think I am sufficiently unsure as to not want to start the engine at all! What’s the best power for breakin and and general cruising?
Hi Jeff,
I read through the article and although I can see how it appears to conflict with what I wrote above, the details are actually closer than they first appear. For example:
And:
So for example he is recommending 70-80% power, that’s a lot higher setting than most yachties use.
That said, the writer makes one big error and that is saying we should monitor cooling temp to tell us if we are chronically under-loading. That’s quite wrong because due to the action of thermostat the cooling water will reach correct temperature pretty much regardless of load. To check for under-loading we must use oil temperature, or best of all, exhaust temperature.
I would also recommend reading Steve D’Antonio’s article in further reading about the dangers of under-loading as well as reading right through this online book to really understand the issues:https://www.morganscloud.com/category/mechanical/mechanical-online-book-engines/
Bottom line, unless Volvo tells you otherwise, I would be careful not to chronically under-load you new engine, particularly during run in.
Jeff:
I agree entirely with John, SBM’s advice appears to be in keeping with our recommendations.
I also agree with John’s comments regarding coolant temp monitoring, unless a diesel is idling at the dock, the thermostat will ensure the coolant reaches the set temp almost regardless of load. I’m a bit surprised at Tony Athens for saying this, he’s one of the more knowledgeable diesel folks out there.
Oil and exhaust temp are the best indicators of load, with the former being very easy to monitor using an IR pyrometer, and shooting the middle side of the oil pan or oil filter.
A dilemma; I have a Whitby 42 (approx 24,000 lbs), which has the factory-original Ford Lehman 80hp engine. I believe this engine was installed as a deal was made with between the two manufacturers, rather than a necessity for 80 hp. I have only found two people who have repowered these vessels, with smaller engines (one a 55hp and the other a 60hp) but have not received responses as to whether or not they’re satisfied with the change. The ample freeboard on the Whitby, and the not-so-hydrodynamic hull form, makes me ponder whether or not there would there be a notable loss in performance by striking off 20 or 25hp? Present fuel consumption on the older engine is approx .75/hr at 1650 rpm; not working the engine to its detriment, of course. I have to admit there are some hesitations to invest so much money and time in a less-powerful unit, and at what performance cost (if any). Do you have any experience ?or do your readers have any experience in a similar situation?
Hi Robert,
Our experience in which we installed an 87 hp in place of a 110 hp in our 50,000lb boat (twice the size of a W42) says you should be fine with 55hp as long as it is a M1 or M2 engine that can run at high power settings continuously. Beta Marine are good in this regard.
https://www.morganscloud.com/2010/10/23/perkins-m92b-review/
Read the entire online book for more: https://www.morganscloud.com/category/mechanical/mechanical-online-book-engines/
Thank you, John; I was looking at both Beta and Volvo engines.
Just noticed that this thread had revived…I repowered with a Beta 60 on a full keeler in steel about 7,000 pounds heavier than a Whitby 42 and couldn’t make full RPM until I flattened the 19-inch four-bladed prop’s pitch from 15 to 13 inches in forward. I left it at 15 in reverse for stopping authority. The revs went up and I am well-pleased with the results and my fuel “map”. I would think going to a 55 or a 60 HP Beta would give you similar results, save you might wish to rethink if your prop will still be correct with the new engine. There’s savings in weight and noise, too, and the Beta runs cleaner than the Westerbeke it replaced.
Hi Robert,
Is your current Lehman still running well? If so, I would do nothing. They are very good engines and the fuel burn rate you give will be very hard to beat. You can measure temperatures and see how you are doing on loading the engine but also I assume you have a lot of hours and would know by now whether you are having issues or not just by looking at your exhaust.
However, if the time has come to replace the engine for whatever reason, then it is a much harder question. Based on your fuel burn number, you are likely using less than 20hp to motor around normally. Then the question becomes what is the most power you have ever needed from your current engine? If you know the max speed, the rpm you were running and the max rpm you can reach, you can get a rough idea and you can also get a rough idea just knowing the boat’s speed and then making some assumptions. The other thing to do is to play with one of the online prop calculators and see how sensitive your boat is to power. I suspect that you will find that it is perfectly fine to put something less powerful in. FYI, a lot of people feel that for your size boat, 2hp/1000lbs of displacement is appropriate, it isn’t very scientific but it gets you in the ballpark of what is appropriate.
Eric
Thank you for the response, Eric. The engine runs fine, but, if taking her to Europe, was informed that there might be emissions issues; otherwise, I have been researching a complete rebuild for her. She works well, and the only issues I’ve had with her have been from the fuel supply line (so many connections, so many places to look for an air leak!). A complete rebuild is more than half the cost of a new engine…something to keep in the back pocket (no pun intended)
Robert
Hi Robert,
I strongly advise against a rebuild. Theoretically it should be fine, but the track record of recreational engine rebuilds is abysmal.
Sadly, I agree, the skills required for a successful rebuild are difficult to find in the US today, a function of economics, easily available new engines and no organized, nationwide vocational training programs. The result is hit or miss, I’ve had engines rebuilt well, and others not. If it’s a shop the does rebuilds routinely on this brand of engine, fine, but those are as rare as the proverbial hen’s teeth.
Why no mention of Yanmar as a replacement?
The whole emissions issues is another concern, John you brought this up. I recently had a client’s purchase in Europe fall through because the vessel had been re-powered in Portugal with a non-EU emissions certified engine. However, I’ve never heard of a recreational vessel being refused entry into the EU because its engine wasn’t compliant, has anyone else?
(Lecturing at IBEX)
Hi Steve,
The reason I don’t like the Yanmars is that they are, as far as I know, all M4-M5. The result is in a displacement sailboat is that for warranty purposes the prop must be set to allow them to reach WOT, but on the other hand, if memory serves, the engine is not to be run at more than about 60% power for longer than half an hour or so. The result is we end up with a bigger engine than the boat needs or can really use.
(Steve Dashew used to get around this by over-wheeling the hell out of them, but that’s not ideal.)
On the other hand the Beta’s are M1-M2 and they are happy to run at 80% power 100% of the time. (I have that direct from the CEO’s mouth.)
This was the same reason I changed from an M2 cummins 115hp to a M4 Perkins 87HP, which has worked very well and resulted in a big fuel saving since we are now operating in a better part of the power curve at cruise.
That said, I believe Yanmar does make M4 engines, but my understanding was that they were not available in small sizes?
Hi John,
I am not convinced that an M4 engine is quite so evil, I would be interested to hear your and Steve’s take on it too. If we are realistic about most people’s usage, they end up using the engine at a rating that is probably the equivalent of M4. On many of these boats they actually have more power than they could ever put down and going to a smaller engine would make sense but I still think that you would find that very few boats every operate at an M3 rating (load factor <50% and full power <4/12 hours).
The good news about going to an engine like this is that your underloading concerns are less big of a deal. The same engine is often offered in different ratings and they do this by changing cylinder pressure and speed (more on that later, I have some issues with this). The effect of increasing the max cylinder pressure is to increase the max temperatures as well which is one reason that life is effected. But if you don't use this extra cylinder pressure that is available, you don't hurt the life of the engine and in a pinch when you need it, you have it. If you match a prop to an M1 rated engine and then throttle back much at all, you run a risk of underloading. However, if you buy that M4 engine, you will have a smaller displacement engine where the temps will be higher at the same throttled back position. Obviously this is all a balancing act and it is possible to overdo it but if you stay within the engine's ratings, then I don't see a problem with it.
The issue that I have is when you get an engine where they govern at too high an rpm. Because you are well past your maximum efficiency point, it takes a lot of extra rpm to get a little extra power (classic example is Beta 35 vs 38, 9% increase in power and 29% increase in rpm). Because the power curve is concave down, you end up been poorly matched on the propeller at normal operating points unless you overprop.
I happen to have gone through one of these examples recently with helping someone select a Deere so I have the spec sheets handy so figure an example might be interesting. Lets say you want 230 hp max but typically cruise around at 75% rpm which corresponds to 100hp (I cherry picked this operating point a bit so that there were good engine models to compare but I think that it is valid). Looking at similar engines in terms of intercooling, etc, this would have us looking at either the 4045AFM85 in an M4 rating at 2600 rpm or the 6068AFM85 in an M1 rating at 2300 rpm, basically the same engine just in 4 or 6 cylinders. At our 100hp operating point, the engines are at 43% load so we are slightly out of the 40% rating on the 4 cylinder engine but we are way under the 100% rating on the 6 cylinder. Now if we look at power/displacement, we see that at 100hp we are seeing 22.2 hp/L versus 16.7 hp/L, obviously the 4 cylinder is going to run warmer. Because EGT's are also a function of speed (not exactly linear though), we can then go and get energy/combustion event/L and we find that the 4 cylinder engine is still 19% higher meaning it will still be hotter and less likely to have issues with underloading.
One interesting question that I would love to ask an engine designer (I know the answer for the compressors that I used to design which are basically 2 stroke diesels without fuel systems) is why they rate the time at maximum operating point in hours/hours as opposed to percentage. At even 1 hour, you should easily be at steady state on everything so why would you need to back off? I would think that this would be more of a measure of engine life shortening and if this happens at steady state, it doesn't matter if it happens today or tomorrow.
I guess that this is the long way of saying that if you want to buy an M1 or M2 engine, you don't want to size the engine for peaking capability, you should be running at a high percentage of rated power at normal cruise. If you are someone who wants that peaking power for whatever reason, then an M1 or M2 engine is going to be lightly loaded during normal use and may have issues that would be better served by a smaller M4 rated engine assuming they are otherwise equivalent. I know that I like to have some peaking capability for maneuvering, anchor setting and rough weather that would probably make my ideal operating point about 50% of peak.
Eric
Hi Eric and Steve
That all makes sense, as always. I was not trying to say that M4-M5 is evil—great for a planing boat that needs a burst to get up on the plane. And yes, I get that if you want a big boost in power for a short time an M4 might make sense. But from my own experience with a biggish boat, the theoretical power we could get from our 115HP Cummins 6 2800 WOT was useless because the prop was not capable of putting into the water. I think this is very common with sailboats: more power than the prop can absorb.
So we changed to an 87 HP Perkins 4 M2. I have noticed no difference in motoring into a sea and wind or maneuvering. And the good thing is that we now cruise at 1800 to 2100 RPM (depending on wind, sea state) with 2400 WOT. I think I’m right in saying that 2000 would be too much (50 HP) if M4 and 40% load limited, as is typical with M4, for cruise. So if the same Perkins was M4 we would be limited to about 1800 for periods longer than an hour, which would be a drag since if the sea is up we need that extra.
And here’s the key point, the prop is at the same settings as it was with the Cummins, albeit with a slightly higher reduction.
And we are loading the Perkins properly too, even at 1800, as proved by exhaust temps. We never loaded the Cummins properly.
I think another key point is that sailboats pitch when motoring into any sea so added HP, even if the prop can transmit it, just does not work past a certain point.
So, yes, I was too simplistic by just blaming rating, that said I stand by saying that most sailboats are overpowered and that we can generally get a better result by lowering HP and rating together.
Bottom line, we cruisers spend most of our motoring time at cruise and I have found that we can optimize for that without losing much, if any, real usable peak power.
Hi John,
Sorry for the late reply, just getting back to this. I agree completely that most sailboats are not capable of putting down the power that their engines have.
It sounds to me like you went from a lightly loaded M1 engine (the Cummins 6B) to an engine that is 3/4 of the displacement putting your loading in a more reasonable range. Until you are full throttle on your new engine, you will never feel a difference from the old one as you are still limiting by the requested output not the possible output.
2 other factors to consider are cruising speed and size. Lots of cruisers that are 40’+ motor around at 5-6 knots to save fuel either for financial reasons or range reasons. These people are excellent candidates for a somewhat smaller displacement engine with an ~M4 rating so that they can cruise slowly but have the power for the very occasional time when the going gets tough. The issue with this of course is that ideally they would also have a variable ratio transmission as it is very hard to run the engine efficiently in this application although the hull drag curve trumps engine efficiency. Size is important, larger boats can keep plowing into bad weather with less power to weight and in nice weather, drag is not linear with displacement. I have run boats in the 100′ range that do fine with 2/3 hp/1000 lbs while a similar 30′ boat would do better with 2 hp/1000lbs. I have also run boats in that size that have much more power and many of these have owners with very deep pockets that are willing to spend a lot more on fuel for very small speed increases, not a trade-off I like.
I just noticed that the numbers in my post above with the 2 Deere engines looked off and realized that I made a brain fart and used 6L as the displacement of the 6 cylinder version instead of 6.8L. The difference in power/displacement is even greater than I stated as a result.
Eric
Hi Eric,
One correction. The Cummins was M3-4. The engine is (was) made M1 but it’s a special order and drops the WOT to 2200 if memory serves.
I guess it comes down to the trade off between cruise efficiency and peak power. In my experience with my present boat and her predecessor (45′ 25,000lb, 45hp) I prefer a smaller M1 or M2 so I can cruise continuously in a more efficient part of the fuel map (closer to WOT) and also load the engine properly.
The first benefit has extended our range and reduced our costs far more than I thought it would.
And the second benefit, is, I think, more important than people realize in that both my M4 engines tended to glaze up. The result was I had to run them hard regularly and very inefficiently (too high speed to length ratio) just to keep them clean.
Talking of which, I did some research on Yanmars, and while they still won’t share what the rating is, their new manuals call for running at WOT regularly to prevent glaze up. But when I talk to boat owners out there, most of them don’t even know what the top RPM for their engine is, and still believe that running at WOT is bad for the engine.
On peak power. Most owners I talk to think they want a lot, but then have never used it. And I think there are good reasons for that:
For example, I’m aggressive with the throttle when docking, but have never used more than 2200 on the Perkins or Cummins (2400 and 2800 WOT respectively) even when docking in tight conditions in gale force winds.
The other time one might want a lot of power is getting off a lee shore. But in this case sailboats lose all forward motion regardless of power due to the pitching moment, much of it due to the mast. And this is even true with MC and her carbon mast. So again, the amount of power actually usable, particularly with a folding or flat blade feathering prop, is far less than most people think it is.
Of course none of the above changes the fact that the basic problem is, as you say, engines that are too big for the boat, regardless of rating. Still, once we have the engine sized right, my experience leads me to believe that an M1-M2 is a better bet for most of us.
Of course if we had practical variable speed transmissions or controllable pitch props, all that might change, but since we don’t I base my recommendations to others on what is actually available at a reasonable price.
Hi Robert,
Unfortunately I have to agree with both John and Steve that I would not pay to have someone do a rebuild, you are taking too big of a chance with too much money on the line.
I do think that for the rare person who has the knowledge and experience to do it themselves, it can make sense but this is a very small proportion of the sailing population. The issue that I have with this approach beyond the skills is parts availability, if you rebuild an engine at 30 or 40 years of age, is it reasonable to think that parts will be available for another 20 or 30 years? Probably not for most engines.
Then there is a risk benefit calculation to do. How much longer do you plan to own the boat? How big of a deal would it be to have to replace the engine in Europe as opposed to wherever you are currently based?
Again for the person with the right skills, if the engine is running well it might be perfectly reasonable to keep it and not rebuild it assuming Steve is right on the emissions thing. You could make sure your oil pressure is good, check compression and get an oil analysis done to get the state of health on the internals. If those came out good, then you could go through and systematically replace all wear items such as hoses, accessory bearings, easily serviceable seals (waterpump, etc), brushes, etc, have the injectors rebuilt and adjust the valves. This isn’t for everyone as you need the right skills and you run a slightly higher risk of needing to do an engine swap in an inconvenient place but the risk would be tolerably low for many, myself included.
Eric
John:
It would be great if you confirmed that M rating for Yanmars, when I have a chance I will.
“The result is in a displacement sailboat is that for warranty purposes the prop must be set to allow them to reach WOT…” Unless I’m misunderstanding, pretty sure all engine manufacturers require their engines make WOT at commissioning.
I have no dog in the fight, however, I see Yanmar’s being used by a number of launch operators. If you’ve watched launches run, you know most are operated by teenagers, and it is a true torture test, usually full fwd, full reverse all day long.
What I find with these engines is the actual block isn’t the issue, it’s all the added on bits that tend to fail, brackets, heat exchangers, exhaust elbows etc, often from vibration.
Ultimately, I think there’s no better test for a small diesel than a yacht club launch or water taxi.
(Lecturing at IBEX)
Hi Steve,
As I understand it Yanmar are cagy with their ratings for recreational engines. That said about five years ago Billings wanted to put a Yanmar in a small lobster boat and they were told in no uncertain terms by Yanmar that such heavy use would void the warranty and that the engines were not designed for commercial use.
That said, despite trolling through Yanmars site and the manuals for 20 minutes (I got interested) I was not able to find anything on ratings or limitations on cruise load. So, just don’t know. Still I was always of the impression that the Yanmars sold for recreation were light duty.
I will be interested to hear what you learn.
Hi Robert,
Probably too late to be of help (unless like me you spent years pondering a repower), but might be useful to others. Drawing on advice from here, I repowered our Reinke 13m with a Beta 50hp, 18 months ago. This is a 12t aluminium yacht, with twin keels and 11.4m waterline. The previous Isuzu 68hp engine had lots of issues, including glazing and extreme noise levels.
The new Beta is a dream. Runs well in cruise at 2000rpm / 6knots. Or if in a hurry can do 2500rpm / 7.5knots (at double the fuel consumption per nm).
I installed an EGT gauge, which helped confirm everything turned out as planned. It is interesting to watch the engine load — at the same RPM the EGT temperature changes notably in response to conditions (e.g. increases 40 degrees C if conditions go from calm to a moderate headwind)
A few times I’ve wondered whether I might have been better off with a larger engine. If money were no object, I think I might have chosen the Beta 60, which I think is the same block. However it’s actually only 56hp, and it was about $3k more. I also didn’t get any insight from Beta Marine as to why the ISO 8665 power curve is almost the same for the Beta 50 and 60 (i.e. ISO 8665 power at max RPM is a smaller % of the max power at max RMP for the Beta 60 than Beta 50).
A Beta 70T or 75 would also have fitted (physically, but not financially!), however with a prop matched at full speed, I would not have put any reasonable load on one of these engines. They can produce 40HP at 1200 RPM, which is my max speed power requirement! Going any faster just uses exponentially more diesel for very limited speed gains.
Also worth noting, if your propeller is worth keeping there are a range of gearbox ratios to choose from. I measured the shaft RPM with a laser tachometer, to get a RPM/speed relationship. I combined that with my best estimate of our old engine’s remaining power/RPM relationship and calculations of power produced by our prop at different RPMs to obtain a RPM/power relationship. This put me in the right ball-park for the gear ratio (say +/- 10%), accurate enough to determine the most appropriate gear ratio. In my case it fell between the available 2.29 and 2.47 gear ratios. I ended up going with the 2.29 as given the max diameter of my prop 2.47 starts becoming quite limiting for any future prop replacements. This has worked out well and provides a match that I’m very happy with which requires no fine tuning of the prop.
This was the aspect that left me the most nervous about the repower as our SS folding prop is still in near new condition (20 years later!), and a similar new folding prop (if I needed to change pitch) would have been $4000AUD!
Hi Klaas,
Sounds like a very well managed repower to me. People would have better outcomes, as well as saving a lot of fuel and carbon, if they took such an analytical approach, rather than just jamming over large engines in the boat as seems so common these days.
You and us must be two of the few yachties with an EGT, but, as you say, this gauge can tell us a huge amount.
I said “these engines” meaning all small diesels…
Hi John
You may be right that engine rebuilds almost never work, but I have difficulty understanding the problem. I have rebuilt a wide variety of engines, from Ferrari v12’s and a 300SL Gullwing Mercedes to 4 cylinder racing engines and marine diesels but I don’t think I have ever worked on the same class of engine twice. The lack of individual type experience certainly disqualifies me as a professional engine builder. Never had an engine failure, even with the 185 hp 8,000 rpm SV engines based upon the crude Type 4 VW block that I used to race. The little 4 cyl marine diesels that we use in sailboats are so simple that it would seem difficult to screw one up.
I once bought a nearly new BUHK for $500 that had overheated in a Swan who’s owner threw in a new engine so he could motor out the start line of the weekend regatta. Definitely a candidate for the garbage heap, right? Took the cylinder head to a specialty shop that welded it in an inert oven after heating it to a nice red glow. Cost about $300 including new valve seats and valve guides. It ran for years until the boat was sold to a new owner who decided it was too small. It has since gone through two new turbo Yanmars.
Hi Richard,
See Steve and Eric’s comments for the problem. As I said, rebuilds are great…in theory. The practicality is that of the some 15-20 rebuilds of small sailboat engines I know of, half have ended in a new engine within a year or two.
Hi John,
I have read a study done for DOD which goes against conventional and AAC wisdom. This research specifically focuses on military diesel generators but I can’t see why it would not apply to a marine diesel. What do you think?
“There is a common belief among users of DoD diesel driven (DED) generators that extended operation of diesel engines at rated speeds and light loads (high idle) results in deterioration of performance and engine damage.”
“Information developed indicates that the ill effect of high idle on most military diesel engines is limited to the nuisance of carbon buildup in the exhaust system and discharge of unburned fuel (wet stacking or slobbering) in the engine vicinity when operating at low temperatures.”
E.J. Kates (12) reaches the same conclusion in his standard text, “Diesel and High Compression Gas Engines”, with the statement “no serious harm follows underloading, but it is uneconomical … overloading causes combustion problems and overheating.”
I’ve uploaded a copy here:
http://kp44.org/engine/ftp/Effect_of_Long_Term_High_Idle_on_Diesel_Engines.pdf
Jeff
s/v Beatrix (KP44 1980)
Hi Jeffrey,
That has not been my experience in that I have glazed up two engines through chronic under-loading and fixed one by running it hard. One thing I do know is that most engines can put up with a lot of chronic under loading as long as they are run hard for a comparatively short period regularly. That might be what this study is referring to and is different than the typical cruiser destructive profile which is chronic under-loading combined with never running at high loads.
Hi Jeffrey.
The Yanmar engine manuals stipulate that the engine should be run for 5 minutes WOT after any period of low rev/low load running.
Regards
Bill
Hi John and Jeffrey,
When working up in northern Alberta and BC many years ago, it was normal for diesel trucks to sit there at high idle all night long. Often wondered if any unburned diesel would get passed the rings and dilute the lube oil ??
Once back on the road, these diesels were working hard enough to clean-out any carbon built-up. The old time mechanics, inorder to get rid-off any carbon in gas or diesel engines, would spray a fine mist of warm water into the inlet manifold, not enough ofcourse to create an hydraulic lock !
You may have read that many farmers are going back to the older tractors, as apparently the newer big machines, for many, become to expensive to keep going and the farmers dont have the expensive tools and/or knowledge required and to get the tractors back to the dealers often cost a lot of money in transportation as many are much wider than the legal limit.
Are the new hi-teck computerized diesels back-firing?……….pun intended!
Any thoughts on a Yanmar 40 hp 3JH40 common rail diesel vs a Beta Marine 38 for a Cape George 36 displacement sailboat? Thanks
Scott Johnson
Hi Scott,
I really like the Beta however, get the 35 not the 38. It’s the same block, but the 35 with a top end of 2800 RPM will be in a good place in the power curve at cruise on the the Cape George. You will never use the added three HP of the 38, but having it will force you into the wrong pitch settings on your prop since to get that small amount of added power they take max RPM to 3600.
Yanmar make good engines but these modern ones are awfully complicated. Also, Beta will put what ever alternator you want on at the factory and preserve the warranty. If you buy the yanmar you will have all the hassle and expense of changing the alternator and in so doing you void the warranty.
Hello John:
This question is not directly related to this post but I could find no posts where you specfically address fuels or fuel additives. Since you sail the “north” as we also do I thought you might know the correct answer to this question.
Question: Is it alright to use the commonly available “fuel oil” (often used to heat homes) as fuel for our boat’s diesel engine?? I have been told it is the same product but I wish to be sure. The reason I ask is the in many ports (especially outports) “fuel oil” is all that is available.
Thank you
Hi Philip,
We have used fuel oil for many fills over the years without issues. That said the injectors in our Cummins did require more frequent service than I would have generally expected, so that might have been the reason. I have heard that it’s a good idea to use an additive that raises cetane and lubrication when forced to use fuel oil, but we never did that.
All that said, in recent years the quality of fuel seems to have got better in the North with many places able to supply diesel.
Thank you John.
That is what we suspected. We have also been using fuel oil for years due to limited access to regular diesel in many places.
However, in later years we developed some problems with our old Perkins 4-108 and we wanted to rule out the fuel as a problem.
In retrospect (especially after reading your chapters) I believe all the problems were caused by my efforts to “baby” the engine to make it last longer. I did exactly what you say not to do and suffered the consequences.
I guess that is part of the learning process. But I thank you for helping others avoid these hard knocks.
I was not sure where to post this question, but will try here. I have asked BetaUK if I should use a cetane and lubricity enhancer in my new engine. Thus far, no response. I used to use one for my old Perkins. I have read various opinions, as one might expect. Perhaps the crew on this site can weigh in. Thanks.