Nigel Calder’s newest machine, that claims to revolutionize electrical systems on boats, has generated (ouch) a huge amount of excitement. For those of you who have not heard about it, a quick view of the above video will bring you up to speed.
So is this thing a good product that we should buy? Let’s dig in and find out.
Understanding The Problem
To do that, we need to understand two things that are fundamentally wrong with cruising boat systems, which Nigel is trying to fix:
Problem #1—12 Volts Is Dumb
I’m guessing that we ended up with 12 volts on boats because that’s what was used on cars. And that was fine back in the day before we put a bunch of stuff on our cruising boats that requires a bunch of power (measured in watts) to run.
We have two chapters (see Further Reading) that explain the relationship between watts, volts and amps, so I’m not going to do that all again here, but the key issue is that as volts get lower we must increase amps in order to deliver the same number of watts (power) to run a machine.
And as we increase amps the wires that carry them must get bigger. This is why we all have these huge expensive battery cables in our boats. And if that wasn’t bad enough, another problem with moving a bunch of amps around is that if there is even the slightest resistance in the circuit—a small wire, a slightly dirty contact, or the connections and relatively small wires inside an alternator—stuff gets hot.
And not only will that heat reduce the life of machines like alternators or, in extreme cases, even cause a fire, producing heat wastes energy that could otherwise be used to power our stuff.
Problem #2—Wasted Power From Diesel Engines
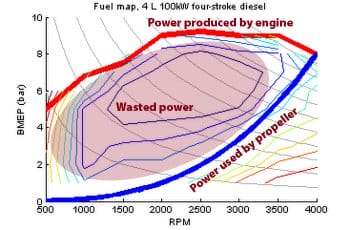
Again, we have in-depth chapters that explain this, but the quick overview is that the available power of a marine diesel engine is only fully used by a propeller at wide-open throttle. So at the typical speed that most of us cruise at, there is potential power not being used that Integrel harvests.
And, in addition, when we run in neutral to charge, most engines are capable of producing far more power than the typical cruising boat alternator can turn into electricity. So once again, Nigel’s goal is to grab more of that potential power.
Nigel’s Solution
OK, now that we understand the problems with present systems, let’s look at what Nigel and team have cooked up to fix them.
Voltage
First off, their Integrel (yes, that’s how they spell it) generator (that takes the place of an alternator) operates at 48 volts so that all the wires involved can be one-quarter the size of that required by a 12-volt system, or one-half that required by a 24-volt system.
Engine Loading
Integrel uses software in a black box to vary the output of his alternator replacement depending on the RPM of the engine and whether or not it’s in gear. This is how he harvests that unused power.
This is also great because Nigel’s machine will automatically back off its demands on the engine at times when we need all the power for propulsion, or the Integrel generator itself is getting too hot.
Efficiency
Integel is much more efficient compared to generating power from a normal alternator, both when underway and at anchor. More power to charge the batteries for less fuel.
Generator Replacement
And there’s one more benefit being claimed for this machine: No need for a separate generator.
By making their alternator replacement 48 volt and more efficient, Nigel can produce a heck of a lot more power (5-9 kW) than most any generally available DC alternator can (1-5 kW), and therefore pretty much any reasonable AC load can be run off this thing.
(We will have a deeper look at the generator replacement claim later, after we understand the basic system.)
Drawbacks
Well, that’s all pretty exciting. Let’s all buy one, shall we?
Wait…AAC is the home of rational thinking voyagers who dig deep into reality before we spend our hard-earned cruising money, not newest-thing-motivated-fanboys.
So what are the drawbacks with this machine? Three things worry me:
This is interesting, not only because I respect everyone involved (and have met the Shards several times), but because they so closely reflect the “what is cruising” mindsets. So I’m glad you brought up the “glass house” element.
We determined we did not want a inboard genset, even though with a steel full keeler, we have the room and no qualms about installing such a thing. We find it easier to just roll back the usage and lower the need for “mod cons”. But that’s us. Others clearly differ and that’s their right and privilege to address that as they see fit.
But the “no free lunch” maxim applies: We want a large-case, big ol’ alternator to charge a big ol’ battery bank, and to make water, when we are motoring. We are also about to install a fairly amp-hungry autopilot. The difference is that we also have wind and solar (and Honda 2200s!) and a wind vane. While the radar would be intermittant, the reefer will be more or less on constantly. So our “profile” is to charge big-time when charging is necessary…but to make that necessity limited (looks over at the 2019 Nautical Almanac…)
We are clearly in the minority, I suspect. Nigel Calder’s system, irrespective of the rather trenchant observations above, addresses the desires of the majority. A trip to a boat show with sailboats (if you can find such an event these days) confirms this.
It’s an interesting concept that I’d not heard of before reading this.
I like the idea of harnessing the wasted energy while motoring – and the fact that we’d now be loading the engine properly has to be good. I suspect however that fuel consumption will be affected – so it’s not exactly free?
I don’t personally agree with going to 48V – for the same reason the automotive industry largely dropped it. (From a fundamental level, breaking the current in a DC circuit requires dropping the arc voltage to below roughly 12V (minimum arc voltage). That can be done easily in a 12V circuit – as soon as a switch is opened and an air gap formed. In a 24V circuit, to reliably do it you need to have a double break contact. For 48V you’d need 4 contact pairs – or a very large air gap and very fast opening times. Switches have simply not been developed (far as I know) to reliably handle 48VDC.)
Regarding the belt driven side – I wouldn’t have an issue with that – our 5.5KW generator is driven by a serpentine belt and in 7 years I’ve not had to replace it.
I’d love to get rid of the space use by our generator, but I suspect that the DC/DC converters, additional inverters etc, might impinge on some of this gained space – though the waterline would surely pop up some!
Interested to hear and learn more about it…
Hi Bill,
That’s interesting about switching issues with 48 volts. A good point I had not thought of.
On your generator. What brand is it, how many hours do you have on it, and what has the reliability been like? I’m always interested in DC generator real world experience.
It’s a ‘NextGeneration’ – Kubota engine with Markon alternator… Has about 2500hours on it and all WAS fine until we got hit by lightning! Since then I’ve had to do all sorts of things – and have just replaced the alternator – which couldn’t (surprisingly) be rewound… This gets all the more complex when one finds out that Markon closed and the new choice needs new mountings, etc…
I’m now looking for years of trouble free use with a brand new alternator! (Heavy pounding on wood beside me!)
Just a side note, a move to 48V systems for the auto industry is happening now.
https://www.nytimes.com/2018/02/08/business/electric-cars-48-volts.html
Hi Doug,
Thanks for the link. Interesting that cars will also be faced with using dual systems because it’s not worth redesigning all the stuff that runs on 12 volts.
But it may be “worth it” to redesign all the peripheral equipment to run on 48V if the mega volume auto industry goes to 48V, right? I mean, where did most of this 12V equipment we use today come from?
Hi David,
Sure, but that has not happened yet. Right now the only yacht gear that uses 48 Volts is a few bow thrusters and a few inverters. So there are some usage profiles that 48 Volts works for, but not many: https://www.morganscloud.com/2020/12/17/should-your-boats-dc-electrical-system-be-12-or-24-volt-part-2/
Absolutely agree hasn’t happened yet. What I was saying is that I don’t personally think that the auto industry will be designing with dual voltages (to meet 12V needs on their 48V models) for long as their volumes are large enough to justify redesigning of the accessories to 48V if/when they get to a majority of cars operating on 48V systems.
Thats interesting. And since the automotive sector has a footprint indefinetely larger than the yachting industry we might see the advent of mass-produced 48V battery packs. For the integrel system this would mean one voltage transition spared, and for the battery bank no need for serial installation which would push the reliability issue.
However I wouldn’t expect this move within the next 5-10 years… Maybe my grandchildren will cruise in 48V-powered boats, then.
We have hybrid systems on yachts now in the form of hydraulic powered systems.
Maybe the future will be 48v for the heavy loads,12 or 24v for everything else.
Actually 48volts was not dropped. It is on the current roadmap for all mainstream car manufactures and component manufacturers. There ‘was’ an old 42v initiative that was dropped, years ago. Mainstream component manufacturers are all gearing up for 48volts – for the above obvious reasons. Further, newly invented and designed 48V to 12v DC-DC converters are now far cheaper with the advent of low cost transistors and high frequency inductor designs, needed to buck and boost the voltages, efficiently and cheaply. So with the car industry moving in this direction – it will continue to arrive – but because of the very heavy, quality-qualification related regulations in the Auto sector – it’ll take a few more years. All of Nigel’s premises are solid… and it’s happening steadily in the car world. Wait a few more years as this automotive sector’s initiative accelerates the transition to the marine world,… it’ll become common-place.
It is maybe a little sad, but I beleave your rather critical conclusion is correct. We all might hope the batteri charging could be more efficient. I have tried to put a big dynamo on my Yanmar 4J and an aggressive voltage regulator. It ruined the water pump and the chrankshaft. The Yanmar was contructed with a small dynamo and could not last with a bigger load. In my fishing boat with a Callesen engine I have made 130 000 hours with up to 6 KW dynamo. This demands good alignment (no rubber mounting of the engine as the dynamo must be sitting outside the engine), measurement of the load on the belts and double V-belts of a high quality. There are many types of V-belts and even the best ones of Kevlar are getting longer with use. So the stretching of the belt must be measured regularly.
I find it easier to have a small dynamo on the main engine and a small diesel generator in adittion as in your Morgans Cloud.
Hi Svein,
That’s interesting and sobering on the destruction of the 4J, thanks.
Hi John and Ernest, I will stress that the 4J is a very good engine. I have had several of them and they last more than 20 000 hours. I have a new one now only used 90 hours. The 4J is very light and can be overloaded as I did. I installed the big generator with a modern V-belt a bit smaller in width than the traditional B type, but not going to the bottom of the V of the pulley. I also used a larger pulley, then laser alignment of the hole system and so a belt tension meter to find the correct belt load and finally laser alignment again. This kind of installation I have learned from Callesen diesel. Callesen use belt driven Transmotor dynamo up to 12 KW. Such a big system will produce a lot of energy, it needs belt maintainence often and a cooling system. In my Callesen I have a Transmotor cooling maschine. It is big and heavey, but cools down the engine room and makes air pressure in engine room 0,2 bar above the pressure on deck. In a small yacht this system is an overkill in my opinion and I go for the solution aboard Morgans Cloud.
The 4JH’s cannot have a high side loading on the front pulley, Kubotas are somewhat more tolerant. In my 4JH4 installation as I had the space available we fitted a layshaft in front of the engine, shaft running between 2 bearings and a flexible coupling to the crank. Running a 140A alternator and fridge compressor both driven by double vee belts. All of this is carried on a mounting frame bolted along the block sides and an additional pair of rubber mounts at the front of the frame. A bit complex but works well.
Some years ago Yanmar were marketing an inverter generator option fitted between the engine and the gearbox on 4JH engines, which is a much better solution for the drive connection. Same as now being used in some cars. Not sure if it is still available but this would be a better solution, however it is not suited to retrofit installations.
Hi Alan,
Do you have a source or specification for your assertion “The 4JH’s cannot have a high side loading on the front pulley, Kubotas are somewhat more tolerant.”?
Solid numbers would be really useful for this discussion.
And the shaft sounds interesting, although as you say complex and probably beyond the DIY capabilities of most boat owners. Also, most boats will not have room for such a set up.
Hi John, unfortunately no hard numbers and this was a point of frustration when I was configuring my Yanmar installation. The local suppliers could not come up with any definitive numbers even after going back to Japan.
My statement re Yanmar vs Kubota should be qualified as “reputed to be”
There is some interesting discussion on alternator sizing and installations here
http://www.zrd.com/faq
Ref Eric’s query I believe the main problem is th shaft seal not being able to endure the high side loading, but Eric will be better informed from actual experience
Cheers
Alan
Hi Alan,
Thanks for the fill. I agree, frustrating that Yanmar and others are not more forthcoming with specs.
Hi Mal19,
That’s interesting. The Volvos, are, I think (not sure) Perkins engines painted green. If so, that’s a commercial block, so that might account for the robustness of the spec.
Hi Svein and Alan,
Out of curiosity, what is the failure mode on a 4J that has higher front end loading? Svein referenced a ruined crankshaft, what was wrong with it (bent, scored, etc?) and what was the root cause of it?
Thanks.
Eric
Hi Eric,
I have had several small Yanmars in fishing boats, taxi boats and sail boats. They are often different from each other and not always the same. Two big 4JH lasted 22 000 hours while a small one was finished after 3 000 hours. I have learned from several Yanmar engineers that the construction hours vary in this time span 3000 to 20 000 hours. The simple rule is: Much power, stronger engine. The first problem with 4JH above 45 HP is the fresh water pump. I normally have to change them after 5000 H. The Chrank shaft bearings will last 30 000 H, but the gasket in front of the main shaft only 10 000 H. When this happened the lube oil will fly out all over the front end. This is only a one dollar gasket. If you put a bigger load on the front end of the engine, this numbers will be smaller.
Mase of Italy has a small 220V 3KW generator based on a small Yanmar diesel. Yanmar engineers says this engine will last 3000 hours and can be overhauled for another 3000 h. Then the Mase generator is finished. This could be a good alternative to the bigger 5-8 KW generators many yachts use. As John says 5-6 KW is a bit big and when used only one hour a day, 3000 h is a lot.
My new 4JH57 is interesting and looks very good. It has almost the same torque on all engine speeds so I have put on a bigger propeller and can make the same speed on 1700 rpm as the old 4JH2 did on 2200 rpm. The cooling system is also much improved from the 4JH2 to the 4JH57, so it is tempting to use the extra power to install a much bigger generator like Nigel’s. But based on my experience i choose not to do so. I go for a small auxiliary generator around 3KW. I have ashore a new 3 cylinder Westerbeke diesel with a 6 KW 220 , but it is too big for my sail boat and will fit better in my fishing boat.
Hi,
Real world reality check- my 78hp Volvo is limited to 14.6hp maximum off the front pulleys. As stated above it is best to stay under that, way too much downside.
Hi Svein,
Thanks for the reply. I am still unclear on what the actual failure mode is but I am not sure we would get to the bottom of it.
Engine manufacturers end up in a slightly tricky spot with all of this. Crankshaft loads are torque based but the rpm is also important if you are worried about the oil film on bearings and giving a spec to the consumer in this way would simply confuse most people. My experience is that companies typically try to provide you a full solution that they don’t want you to change and if you decide to change it, you take the responsibility for issues as otherwise they would have an overwhelming spec list for them to manage and the consumer to understand.
Eric
Your engine destruction nightmare might have been based on using the wrong transmission belt system. Using a belt that relies on friction only, belt tension must be substantially higher than with synchronous (toothed) belts, which might have saved your engine.
Hi John
I thought that belt drive system looked familiar. I’ve seen it before with an almost identical belt size on a VW/Audi V6 that I’ve nursed for 250,000 miles. (you might gather that I don’t like to throw things away even if they are flawed!)
These engines produce from 180-250 hp, and run from 800 rpm to 7,000 rpm. The water pump, camshafts and 30 valve train are all driven from a single serpentine belt, and I wouldn’t be surprised if the loads are similar to those of Nigel’s steroid alternator. The one absolute requirement is that the belt be replaced every 100,00 miles as the engine is a interference design and will grenade itself spectacularly if the belt fails. The German engineers have been hard at work designing these cars, with the result that the entire front end of the car must be removed to change the belt. So you can drive it until it explodes, pay the dealer $1200 to change it out, or become proficient enough to do it yourself as I have.
I think I’d put a new belt on Nigel’s magic machine before I set off for a summer cruise to Antarctica—-. Not that I’d buy one at 1/3 the asking price.
I would expect that the belt driving the cam shafts will in fact be a synchronous (ie toothed) belt and not the sepentine type that relys on friction alone. If not, a loss of friction due to water, oil, etc would mean loss of the engine! This begs the question….why are toothed belts not being specified in the Integrel installation? These run at much lower tensions than the friction (serpentine/v) types and would go some way to alleviating worries about the side loads placed on the crank front bearing.
Hi Philip
Since the Audi recommended replacement interval for the (more durable) toothed belt is about the equivalent of 1600 operating hours, what does that say about the life expectancy of the belt type driving the Calder alternator-on-steroids?
When I re-read the latest edition of Nigel Calder’s Boatowner’s Electrical Manual last summer, and then when I watched his Integrel video several months ago, I kept wondering why everyone is so hell-bent on squeezing enormous amounts of electrical power into a battery in the shortest time possible. It’s not that I don’t understand why. When trying to exchange diesel fuel for electricity, given today’s technology, all solutions will tend to go that direction. It’s just that I’m wondering if that is the right problem to try and solve.
If I had a magic wand, I would get me a device that turns diesel into electrical power producing only maybe 10 amps at 12V while operating nearly noise free and designed to run 24/7 for years. If that would weigh no more than about 30kg/60lbs, I really wouldn’t know what else to ask for. 10A covers our at-sea consumption with autopilot, electronics, nav computer and refrigerator and either my wife or daughter (not both) watching a video on a laptop or tablet.
I wouldn’t have to change anything about my 12V system and could get rid of my Fischer Panda out-of-production very small 12V diesel generator weighing about 40kgs with external pumps, fuel filters and cabling.
When replacing my aging battery bank, I could stay away from lithium ion and continue with good quality standard lead acid, even down-size a little. And that bank would last phenomenally long as probably the deepest depth of discharge it would ever see is 95% SOC. I would continue to use a moderate amount of solar but probably not bother with wind or water generators.
Just as a reminder: the Efoy fuel cell produces 8 amps nearly noise free, pretty much indefinitely, and weighs 8kg/16lbs. The price is around EUR 5.000 and installation should be quite simple. I have not heard reports of poor reliability and it has been used on round-the-world race boats, so fas as I know.
The drawbacks are that the fuel is outrageously expensive per kWh and that the fuel will be extremely hard to get in some south pacific atoll (I am not sure about any safety hazard with storing large quantities of methanol on board).
Why don’t we (humanity) work to make the Efoy use diesel fuel rather than attaching a 30 kW generator to a 60hp diesel engine and making lithium batteries that can be charged at 10 C and to hell with cost and reliability?
As an aside: last spring I installed a bus-system with multiple Ah meters on the boat and I have started to use solar panels (flexible) for the first time. Our summer cruise was 6 1/2 weeks and we had very nice weather in Denmark, anchoring a good number of nights. When the boat was hauled in fall, these were the approximate readings of the total Ah count:
Shore charger: 3,300Ah
Solar panels: 1,100Ah
Engine alternator (high output): 1,050Ah
Fisher Panda DC diesel generator: 295Ah
Hi Henning,
I couldn’t agree more. If the fuel issues with the Efoy were solved I would install one in a heartbeat. That’s really the key point I’m making in the above article: we should be looking at conservation and better charging sources, not a monster machine producing 9kW.
Hi Henning,
A questions for you: How many hours have you got on your F-P DC generator, and how has reliability and service/support from F-P and their dealers worked out for you?
Hello John,
I will answer your questions but be aware that (a) my generator is probably 10 years out of production and (b) my experience is hardly representative.
The Fischer Panda AGT 2500 had been installed by a professional installer ca. in 2000 under order of the previous owner of our boat. The install was bad since the sea water seacock was hard to access under the aft cabin bunk and the generator was nearly completely blocking access to a cockpit locker in the cockpit sole. I corrected both problems (a lot of work a cost).
The generator was and is mounted on a massive stainless steel plate, over an inch thick, intended to reduce vibrations, weight maybe 40 lbs. I kept that when I moved the generator but am not sure about its effectiveness.
This model has external electric pumps from Johnson and Jabsco for sea- and fresh cooling water as well as an external electric fuel pump (which I replaced with a model common on trucks). I like the general idea of this design but I will probably want to move the electric sea water pump to a more remote location since this pump generates much of the noise of the generator that is perceived from the salon sofa. When I did the relocation, I followed advice from an installer and extended all cables and hoses (fuel back and forth, sea water, fresh water, exhaust) by several meters so that I can now remove the bolts holding it down and then lift the entire unit out of the locker and set it onto the cockpit floor where I have perfect access from all sides and where I can run it as long as I like if I don’t mind the noise.
Generally, this generator and setup is quite quiet. We generally run it in the morning after a night at anchor and when I am under the shower, I cannot tell if it is running or not.
When we had bought the boat it had 98 hours and when we slowly began to use the generator in earnest, a problem developed where it would shut down immediately after start up from lack of oil pressure. Since there was plenty of oil in it, I changed the pressure sender, then attached a manual pressure instrument to confirm that oil pressure really did drop sharply just seconds after it had jumped up after the first revolutions.
A local engine shop that I have great trust in believed it might have faulty crankshaft bearings and asked me to hand it over to them for the winter for a rebuild. They bought a used base engine from Kubota, as a crankshaft was no longer available, and put a new motor together from the best parts of both. However, even though it was a total rebuild, the problem persisted. One of the two proprietors of the shop must have liked me because he spent his evening hours of several weeks fiddling with it the way other people solve sudoku puzzles. At one time when putting things back together again, a small sieve which is used in lieu of an oil filter on this engine, fell off from the nut it was crimped on unnoticed. Suddenly the problem was gone.
It turns out that the oil (exactly the type specified in the manual, a special oil for lawnmowers) had too high density and the sieve would block the oil when it was still cold. He used a lower viscosity 10W40 oil and it ran fine even with the sieve.
A year or two later after another couple of hours of actual electricity generation, it wouldn’t start. We diagnosed no fuel whatever we did. Luckily, Kubota had a single injector pump left which solved the problem.
This was in 2013 just before our sabbatical and it has been running fine ever since (now at close to 400 hours).
The winter after last I asked a local Fischer Panda representative to look the rather low output of a maximum of 78 amps at 12V. We found that one of the phases was shorted to another phase where they connect to the diodes. We used half a roll of rescue tape (too hot there for anything else) and I have now seen a maximum output of 96 amps with which I am happy.
So there you have it. I certainly don’t recommend to do as I did. A lot of aggravation, time and money for precious few amp hours. An Efoy fuel cell would have to use liquid gold as fuel to even get into the same ballpark as my total cost per amp hour.
And it’s not that I can now expect decades of use of my big investment. The generator is obsolete in the truest meaning of the word. Even the slightest broken part will mean its certain death.
This generator is the smallest ever made as far as I know, only a little more than a foot high in its GRP and lead case, and if it were an inch higher, it would no longer fit in the locker under the cockpit (45ft boat). The only other place for a generator would be one of the two lockers under the cockpit benches and I am not prepared to completely give up one of these – so I know that I can never replace it with any other diesel generator.
While I did not make the initial purchase decision, I did throw a lot of good money after the bad money (a saying in Germany) and I massively overestimated the electricity I would need a generator to make. Less than 300 run time hours in 11 years with 2 1/2 years of full time living aboard and many long summer cruises such as around the Baltic.
If it breaks this season, I will replace with an Efoy and be confident that however high the fuel price per kWh is, it will be less than what I have paid in the past.
Hi Henning,
Wow, what a tale of woe! This seems to be the pattern with DC generators, it’s a great idea, but the actual units let their owners down and often bankrupt their manufacturers. A real pity since I think that for many usage profiles a 2kW DC generator is by far the best alternative, at least in theory.
This DC genset seems to be ideal – low cost, can produce 50-55 amps continuous and lasts for about 1000 hours – although I see his price has shot up – it was about $1700 when I first looked – today as I look its $2500 – the dreaded inflation storm we are in today (August 2022)?
https://dcautogen.com/product/v5-autogen-48v-dc-generator-charger/
Hi Mark,
Looks interesting, but it runs on petrol (gas) so that would disqualify it for me. Also it’s 48 Volt and I’m not a fan of 48 volt systems on boats, at least not yet: https://www.morganscloud.com/2020/12/17/should-your-boats-dc-electrical-system-be-12-or-24-volt-part-2/
If I recall correctly, the old Whispergen stirling engine based gensets did almost exactly what you are asking for – converted diesel into 800w of continuous DC power (a lot more than 10 amps); while also offering up to 5kw of additional heating output; all relatively silently.
now… they were NOT 30kg, and they of course violated almost all of John’s simplicity and user serviceability requirements. They were on the order of the same cost as Nigel’s proposed system I believe. There were a good number made out of the New Zealand factory before the earthquake there destroyed it, and I believe there was a danish or german company who licensed the tech for a few years too – several thousand domestic units were made I thought.
seemed to me like a good option -stirling engines are darned efficient and super quiet. Not sure if this is on the horizon anywhere else now… any knowledge of these units?
bg
I fully agree with all your comments above except maybe for the mechanical issues which probably could be solved by proper dimensioning.
My real concern is heat! According to their information the Integr@l system could work continuously with full load (9 kw) for a long time in 25 degrees C, but how about a badly ventilated engine room at 80 degrees C or more? I cannot find any information about this issue. Certainly their controller will decrease the power but to what level? 9 kw with 80% efficiency means 1,8 kw heat produced inside the alternator! That is a lot of energy that must be removed, I guess only 4-5 kw is a possible output if you want this unit to last for long in a cramped engine room.
I also find it strange that they use lead acid batteries in their setup and most of all they say 1C is the normal recommended charge rate by battery manufacturer? Even if it could be possible to push 1C into a lead acid battery if it is enough discharged, it would not accept it for long. It will soon reach its absorption level and charge current will decrease rather rapidly. So what’s the point to use this complicated and expensive system if you mainly will use it for charging your batteries, the time saving will not be that big compared to a properly designed “normal” system.
I’m looking forward to part 2 of this article, will this system work as a generator replacement!
If you use litium (LFP) batteries it’s possible to take advantage of the high output but as already mentioned, we don’t know how high this output is in real life. Maybe there is a reason for why they don’t use LFP batteries in their own set up…?
Hi Anders,
Good observations, you are bang on right with all of them. I will be covering practical battery bank sizes for various usage scenarios in part 2. Spoiler: the base battery size is not going to cut it, or even close.
The only reason for not installing LiPo batteries is $cost. All the other technicals reasons are only positive. I can’t think of a single technical reason for not installing LiPo + a dual layer BMS. (Std install)
Hi Peter,
I agree that cost is the big issue, but there is also complexity and fragility to deal with too: https://www.morganscloud.com/2018/05/05/battery-options-part-1-lithium/
John,
You said $18,000 for DIY installation but I think you meant to say $1,800, which is what you used in the subsequent addition.
Philip
Hi Phil,
No, I meant 18,000, being the total with DIY installation of $2000 added to the hardware cost of $16,000.
That said, I can probably make it more clear with a slight change, thanks.
I have recently ordered a new boat with delivery in May. When I read about the Integrel system I was very excited and put the 8kva Panda on hold pending further investigation. Very briefly, the cost was going to be double and the weight quadruple the genset. The Panda is back on order! Hope this somewhat untechnical view helps.
Hi Julian,
Glad you did the math. Mine is comming in part 2. We are on the same page, although there are some interesting variables that I will expand on.
Energy conservation is always cheaper than power generation….if you want all the comforts of home, stay at home!
Hi John,
I finally got around to watching the full video on this and I came to a similar conclusion as you.
This got me thinking once again that you would get much of the benefit without the complexity if you simply had a regulator for a normal 12V alternator that backed off the output at high rpm just like this system does. You would have the benefit of either having a smaller engine or more available thrust for the same engine and you would operate in a slightly more efficient part of the fuel island plot. I am unaware of anyone making a regulator that does this but it would not be hard and I would happily install one.
I don’t quite get this system with a lead acid battery bank as the bank would have to be enormous to actually take advantage of the output potential. Going to some form of lithium, it makes a lot more sense to me to have these sorts of outputs but the other issues still stand.
To Bill’s point about 48V and the problems of arcing, I was a little surprised not to see a contactor with magnetic blowout in series with the line to the battery switch although there could be one that I just can’t see. I am pretty out of date on this stuff so it may no longer be applicable but back when I was building electric cars for fun, the placement of these was a big deal.
The belt system is a bit hard to judge without more information. That is certainly a fair amount of power to move through a flat belt and I suspect that they didn’t want to add a second belt so couldn’t use a synchronous one as these are not typically used in serpentine applications. Just like power versus torque, a high speed belt requires less tension although there are limits to what is reasonable for belt speed. I don’t know whether the pulley on the end of the crank is stock or not but if you get its diameter up, then you can keep tension reasonable. Cranks and their bearings are typically robust as they have to deal with the loads from the connecting rods which are quite high but this does need to be checked at the design stage. Other accessories are a different story and you may find that waterpumps and such are not designed for the loads if you increase tension, an L10 calculation would be in order here. One good thing in all of this is that with a belt tensioner, you don’t have the issues related to people who overtighten belts. With good engineering, I don’t see a reason why the arrangement won’t work but it would certainly be possible to do a poor implementation which was problematic.
Eric
Hi Eric,
Thanks for coming up on the belt issue. I was waiting to hear your reading on that, so good to hear that it might not be as bad as I feared.
As to the batteries, that was exactly my conclusion, more coming in Part 2.
And I agree on the voltage regulator. What I would like to see is one that takes into account engine RPM, as you suggest, and also uses a shunt to determine net current going into the battery so that it can keep the voltage at acceptance until the battery is truly fully charged. The old Link 2000R used to do the latter 20 years ago, and it’s beyond me why no one has fixed these two issues since.
I suggested to Nigel that he use his technology to produce a really good 12 or 24 volt 2kW alternator/regulator solution along these lines, but he has no interest and seems totally fixated on the Integel, which is, to me, a great pity.
Hi John,
That’s a shame that Calder is not interested in the much simpler and broader application solution. Both items on your wish list would not be hard to implement (says the mechanical engineer not an electrical one). Hopefully someone picks it up.
Just to put it in perspective, I took the fuel island plot for the 60 HP engine used in the Hymar tests and looked at what difference it would make if you had a 160A alternator that you regulated down to 10A at max rpm. Since you could increase prop pitch and load the engine harder, I found that at 2200 rpm (3000 rpm governed) you would bump your engine efficiency from 260 g/kwh to 250 or about a 4% increase so not a ton but not nothing. With the Integrel, you would run the same prop pitch but during periods of hard charging, you would see even slightly better efficiency but I suspect it doesn’t run that hard for long or you would have some major power hogs. It is worth noting that with this engine, its absolute highest efficiency is 230 g/kwh so even with a perfect CVT, you could only bump the efficiency by 13% over a normal matched prop configuration. The other interesting thing about this plot is that things get less efficient pretty quickly if you underprop.
Eric
Hi Eric,
That’s interesting, particularly the hit from underpropping, which seems surprisingly common in the cruising community. Anyway, the thing that really jumps out at me in all of this is that someone buying a Integrel is spending a huge amount of money for a pretty marginal gain in efficiency, particularly since, as you say, it will only be operating at it’s efficient point for a very short time with most battery banks. Way more economical, and greener too, to just focus on reducing the load side and/or, getting prop pitch right.
Hi Eric, John,
As I understand the “benefit of either having a smaller engine or more available thrust for the same engine” enables owners like us with smaller sized engines (we have a naturally aspirated 55Hp for our 14.5 metre yacht) to maximise power generation by having a larger than recommended alternator with a regulator that un-loads the engine to protect it or provides more power to the prop when needed, all done automatically.
But say we were motor sailing with our engine at “high rpm” and the engine is under-loaded, this would be an ideal time to harvest power wouldn’t it, not back-off charging? Then if we started bashing into a strong wind against tide chop and the prop was loading up the engine to the point the rpm was dropping, we would want the regulator to slug down the alternator output to minimum or nil wouldn’t we?
If a smart regulator could do this it would be very cool I agree – currently our MasterVolt alternator CAN be slugged (we have a soft switch in the MasterVolt controller system to do this) but only ON or OFF and the activation is manual, plus it requires a trip to the nav station.
I have probably misunderstood something Eric, but why would you want the smart regulator to back off at high rpm? Wouldn’t we need the regulator to sense rpm and throttle setting for our model engine and power map, to make the best decision for any given situation?
And then if we have a new oversized alternator enabled by smart “electrickery”, wouldn’t this lead us back to a risk of it failing at a crucial time (given Murphy’s Law Squared applies in marine applications) and to John’s maxim of “don’t pimp up your engine”? Actually I was a little surprised this wasn’t John’s point #1, haha.
Cheers, Rob
Hi Rob,
You are correct in what you say, I had jumped a bit into implementation. Sensing engine load would be the ideal but can also be a bit tricky to actually do as you have to deal with mechanical and electrical engines and a wide variety of manufacturers and models. I think that you could get most of the benefit by simply doing it based on rpm which would be very easy to implement. You could run a calibration or have a method for the user to input the pulley ratio. Interestingly, this is the path that Integrel have chosen to use as well and it should be more important to them based on their higher potential outputs.
Eric
Hi Marek.
My sentiments exactly.
Except that your statement holds true for homes as well.
Twenty years ago I toured the 5,000 sq ft. Rocky Mountain Institute demonstration house in Snowmass Colorado. In a climate zone where below zero F temperatures are normal the house had gone 10 days without any heating and the room temperature never fallen below 65 degrees. It’s build cost was similar to other high end homes in the area. During the (present) 30 year life span of the home the energy savings alone have nearly paid for it.
I’ve been designing and building homes off and on in the mountains for the ensuing 20 years and have never once encountered an owner who was willing to incorporate the lessons available. And I suspect there isn’t one in a thousand buyers of a new $500,000 to 20 million dollar yacht who won’t follow the path of trying to create “all the comforts of home” in his floating dream.
As someone who has installed this kind of system, not Nigels but similar: Big alternator 360a (american power hpi360 derated to 300a on my 57hp 4jh), Solar 1150W capable of 90ah at peak, 1200aH of lithium arranged as 2 independent 600A banks (batteries are lithronics, UL rated) and victron dual inverter/chargers for same reason. I think the system could generate 2 x 120A + 90A + 300A or about 630A of charging if everything was on.
Why did I do this…
I did it first of all to have multiple days sailing with normal power on and to be able to run the boat primarily on solar. I have about 1000ah available which is enough for about 3 days sailing (2 fridges and normal plotter + autopilot). I think I have enough solar to keep the boat going most of the time without the engine especially at anchor and most especially in the tropics. Even if I lost a bank I still have 500AH usable which is 250% more than I had stock on the boat (440AH AGM). It has separate load/charge buses etc and is installed with a very paranoid safety view. I was looking at using cheaper stuff that isn’t as safe and I’m happy I didn’t.
My house bank charges the bowthrusters and engine battery continuously using a mastervolt smart 12V – 12V battery charger so they are charged always, not just when the engine is on.
Second, yes I wanted to be comfortable. Yes, I can run an AC unit from it for an hour a day if I want but that’s a side benefit not my purpose in doing it.
I’m a software engineer and I wanted power for laptops/cooking etc. I wanted redundancy, hence two banks with two inverter/chargers AND each solar panel has it’s own controller so lots of redundancy there. 350W of the panels are bonded to the deck, rest are on the bimini. So, 30A of solar power peak if I lost the bimini.
I can also revert to using the fwd bow thruster AGMs (2 x 110ah) to power the boat worst case, I have all the cables/regulator ready to go and can reprogram the solar stuff to charge it.
The heat issue on the HO alternator was “engineered” around by improving the engine air cooling, replaced the stock one with a bigger one and added a second one. I’m hoping I don’t run the engine much for charging but we’ll see.
From a cost POV, it’s really expensive, no question, you’re going to spend about 80-90K for what I have, professionally installed, especially when I just doubled up on stuff for redundancy which didn’t make it any cheaper. If this for everyone, nope, the cost will likely stop most people from doing it.
I actually wonder if the market will be more for weekend type comfort coastal cruising. Often this market wants AC power and air conditioning while anchored, all the comforts. But doesn’t require continuous heavy duty genset use and likely wouldn’t get close to 10000 hours. I’ve chartered a boat with a noisy buzzy FP genset that was louder in the cabin than the main volvo propulsion engine, so we used the engine to charge the batteries instead (don’t need AC in the tropics with breeze). I bet the manufacturer would love to offer on the hook AC power and airconditioning without added space, cost, complexity of a separate genset.
As for me, our boat came with a lazarette mounted NextGen 5.5. Barely hear in the cabin compared to main engine. So for AC, charging, watermaking (future) I’d rather have the separate device just for sound reduction. But I’d gain a lot of storage in the stern if I didn’t have the genset.
Agree completely about reliability- I wouldn’t want to be on the bleeding edge and with my new Beta I would be really nervous about chewing up bearings etc.
Hi Mike,
I will get more into this tradeoff in Part 2.
I think you would need a good sized battery bank to absorb 9kw of charge without heating up. I have a 1000ah 24volt setup of lifeline AGM batteries and they heat up on half this charge rate. It may work in theory and in an air conditioned lab but not in my bilge in the tropics.
Hi Nigel,
Good point. Ad I write in Part 2, the only practical way to get the benefits touted for Integrel is a huge bank of lithium. https://www.morganscloud.com/2019/02/18/nigel-calders-generator-replacement-machine-part-2-is-it-really-better-than-a-generator/
Hi Eric Klem,
I agree with your conclution to day that it is difficult to understand why different front loads can ruin a Diesel engine. In my experience with 4HJ it is the fresh water pump that brakes down first. But this pump is a closed unit so I do not know what is wrong inside the pump. I have to buy a new one. In all Europeen country’s Yanmar parts are very expensive. The last pump costed 10 000 NOK. A Yanmar engineer working in an oil service company in Europe told me he serviced 800 small Yanmars. He used a lot of spare parts and bought them cheap in China. His advice was to be prepared and buy the spare parts in advance in China. Then a water pump is easy to change. So that is probably as far as we can come on this question : what extra front load can a fast running light weight diesel accept?
very interesting reading . I just met an all electric boat norwegian self built with a 96 volt system 400 ah for the propulsion good for 40 miles ; and 12 V for the rest .
Personally on Rih Malti we use li ion as main bank 3*180 Ah 24 V of Victron. ( serial nrs 1 -2 and 3 ). one issue which may apply here is that when loading by engine alternator of 75 amp 28 V we only are able to tdo 6,5 knots . When the BMS closes the loading i suddenly go 8 knots . For difficult situations ( port entry etc ) i am placing a switch to switch off the alternator via the oil pressure valve . ( A yanmar method documented in the manual) . Maybe something to apply in this setup too ?
Hi Patrick,
The control unit on the Integrel does exactly that (cuts back it’s requirements as the engine gets closer to WOT) but fully automatically. See above article.
If it hasn’t been asked already, what are the side loads going to be on the crank with a generator trying to pull 15-20hp from the crank? or is this sufficiently dealt with by virtue of using a serpentine belt. I’d love to see the data on the bearing loading at that HP demand
Hi Pierre,
That is indeed an important question. I have detailed what we know in the article and you will find some interesting discussion further up in the comments. We don’t have any further information.
Hi Pierre,
Without knowing a lot of actual design numbers, you can’t get a belt tension. That said, with some educated guesses you could get an idea of the load.
Belt systems should be considered torque sensitive not power sensitive. Within certain speed limitations, a belt can handle up to a certain torque for a given set of pulleys. The obvious way to transmit more power through that belt is to crank up the speed either by changing the input shaft speed or by changing the pulley sizing. For the most part, engine accessories tend to load in this way too, at low rpm stuff like your waterpump requires less power than it does at high rpm. With the way the Integrel is programmed, it is putting out max power at much lower speeds meaning that it has higher torque than a peak to peak system as a result which is critical to the calculations. Also, larger pulleys are good in that they lower belt tension up to the point that their speed limits are reached.
I first like to calculate the tension simply to turn the pulley, the actual load will be higher than this but it allows you to gut check the rest of your numbers to make sure you don’t have an error. For this, you need to know the torque on the pulley and the radius. For example, if we assume the engine is running 1400 rpm, the pulley ratio is 3:1 (generator at 4200 rpm), 10 kW (13.5 hp) which is 203 in lbs at this speed and the pulley radius is 1″, you end up with a tension of 203 lbs. What this number actually is is the difference in tension between the portions of belt that are before and after the pulley and since you know tension can’t go negative, you know it is the minimum tension. Note that this tells you nothing about whether the belt will slip on the pulleys or not, that is why there may be additional tension. Also, the angle between the incoming and outgoing sections of belts is important in what the load on the pulley is.
If you want to go further into what the actual tension is, you then need to look at what the preload is required to keep the belt from slipping on the pulleys. I realized that I used a colloquialism in my comment above which may be misleading to some. Serpentine belts which I often refer to as a flat are usually actually a series of small V’s stacked up in parallel. You can go through the calculations for how much contact length you have and at what torque to see what pretension is needed. The calculations are not hard but would be too detailed and take this comment stream a bit off track, if you want to know, Gates has a decent design guide document or you can use their Design Flex software which is free. When I am doing a first pass sizing and before I do the real calculations, I typically use a 2X on the load for the pretension and this seems to work reasonably well when I come back and actually calculate it but if you have limited contact area, this may be low as I suspect it is in this case. In the engine picture in the post, you can see that the belt is a Gates MicroV so I plugged in 1400 rpm, 3:1 ratio and 10 kW to Design Flex Pro and the smallest recommended configuration has a 9″ crank pulley feeding a 3″ pulley on the Integrel, the smaller pulley versions are all in the not recommended category. If we were to crank up the speed a bunch, then the pulleys could be much smaller.
Without the actual design and a bunch of time, we can’t actually evaluate whether the implementation is reasonable or not. I believe that it is possible to design a reliable system for this type of power but there are many factors that need to be checked especially in designs like this. Regardless, the other issues John has highlighted all still stand.
Eric
Hi Eric,
Thanks for the fill on that. It took me a couple or read throughs, but now I think my understanding of the load issue is much improved.
Nigel’s system is elegant and brilliant, but I share John’s reservations on the probable unreliability of any novel system built in small quantities, regardless of the brilliance of the designers. (I am an engineer, and have designed a number of one-off systems. I am all too familiar with Murphy’s law.)
In practice, for each boat Integrel will be a one-off custom installation, due to the variety of engines and structures around them.
On Milvina (15 metre monohull) we are happy without a generator. Complexity and space required put us off.
We have a off-engine 160A 12 volt alternator for house systems, and put up with the extra work aligning the shaft, and replacing bearings every few years. Also a KISS windmill and a 150w solar panel. We feel we are comfortable, but we do NOT have all home comforts. No AC,. A fridge/freezer that works but is not as good as a domestic one.
I enjoy camping in a two-person tent in the Scottish hills in winter, or Canada in winter, so I feel that Milvina is luxury with our modest electrical system, but that is personal choice.
Hi,
I’ve seen at least one example of hybrid marine diesel by Beta. Although, I am not sure if it produces 48V when in generating regime.
Have you been able to look at such engines as a comparison?
Regards,
Hi Ignat,
No, I have not looked at the Beta hybrid, but as a general rule I’m not in favour of this level of complexity, particularly since for most usage profiles hybrids or both types are less efficient than straight diesels. See this post: https://www.morganscloud.com/2013/04/23/electric-or-diesel-electric-drives-for-voyaging-boats/
If you want to figure our whether or not any of these options work for your usage profile, we have a spreadsheet to help you do that: https://www.morganscloud.com/2014/04/13/real-numbers-for-electric-and-diesel-electric-drives/
Thanks John!
Just to clear up a common misconception. You say that “most engines are producing far more power, even at low RPM, than the typical cruising boat alternator can turn into electricity. So once again, Nigel’s goal is to grab more, or even all, of that wasted power.”
That is incorrect. The engine is producing exactly the power that is being consumed by the combination of alternator, prop, and other loads that are applied to it. If it were making more than the power that is being consumed, the engine would accelerate (increase its speed). What you’re trying to say is that the engine *is capable of* making more power at this speed.
But this power is not wasted, it’s not being produced. If you ask the engine to go from 3 kW to 9 kW, it will require roughly 3x the fuel rate. Yes the engine may be more efficient, but reasonable efficiency improvements may take that fuel rate multiple from 3x to 2.6x or so. (These numbers are relevant for generating in neutral but the same principles are in effect if the propeller is also taking some power.) The heat and cylinder pressure loads on the engine also increase. Sometimes, and to some magnitude, the heat load increase may be welcome and beneficial, but running an engine consistently at say 90 or 100% load instead of 10 or 20% load will almost surely have a negative impact on durability.
Thanks for your excellent website and articles!
Hi David,
I guess Nigel and I will have to agree to disagree with you, although I do see the way you are looking at it. But another way to look at it is Controllable pitch propellers are most assuredly more fuel efficient at speeds lower than WOT: https://www.morganscloud.com/2016/04/03/controllable-pitch-propellers-cpps/
Same applies to high load alternators.
Hi John,
I am curious what you disagree with that David says? It all sounds correct to me.
And I don’t think that it conflicts with your point about a CPP moving to an efficient point on the fuel island plot. The integral can move you to the most efficient point along a constant rpm line but it still requires extra power (and fuel) to run, just with good efficiency for an internal combustion engine. The difference between an Integral and a CPP is that the Integral moves you along lines of constant rpm whereas a properly tuned CPP moves you along lines of constant power and in both cases you only get to max efficiency for that variable, it takes changing boat speed to get to the true max efficiency on a fuel island plot unless you are already at it.
Eric
Hi Eric,
I guess it’s semantics, and that’s why I ended by saying I could see his point. So yes, I get that what this is really about is fuel, not power, but both I and Nigel are in the business of making things as easy to understand for yachties as possible, so the idea of wasted power being harvested by the alternator seems to work well.
Anyway, I agree, you are both right that wasted power, or “free power”, at least at the engine, is fundamentally incorrect.
You will note that in my more recent writing I have referred to “near-free-power” when talking of alternators being run at high loads when the engine is at cruise RPM, which, while probably not perfect, this does get the point across in the same way that Nigel talks about Integral.
Hi David,
Matt March, AAC engineering correspondent here at AAC, explains all this well in a series of articles here: https://www.morganscloud.com/category/mechanical/mechanical-online-book-engines/
Not bad, clear and mostly well written engine stuff there. Appropriately leaned towards the naturally-aspirated diesels that are most common on board sailboats. Though I will brag a little and note that I helped develop a 30 bar BMEP marine (see the relevance?) diesel engine all the way back in the early 2000’s. Of course his article is a bit dated but 20 bar BMEP is kind of the entry point these days. But that’s all about turbocharged engines; NA engines that we’re talking are pretty much hard-limited in the 9 bar BMEP area (as Matt correctly noted) by simple air/fuel ratio limitations.