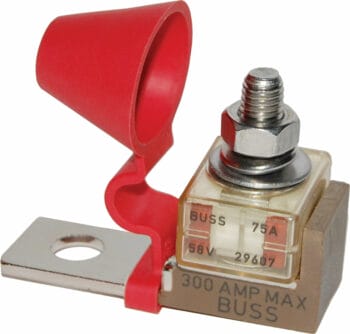
The great discussion on my recent article about proper battery fusing and particularly the potential danger of MRBF fuses failing closed, instead of opening the circuit in the event of a short circuit, reminded me about another big downside of these kinds of fuses that actually negates the supposed advantage of being able to install them on the battery terminal.
Take a look at the graphic above. As you can see, the fuse comes with a little rubber cap that I bet is there to satisfy the ABYC requirement to insulate all battery positive terminals from possible shorts.
First off, having used these fuses on the small lead-acid bank on our J/109, I can tell you that little cap is pretty useless. It refuses to stay in place and does not properly cover the exposed parts of the battery lug.
Wait, it gets worse: The other problem is how the heck can we insulate the metal part that bolts to the battery terminal?
Begs the question why doesn’t a manufacturer just offer a proper boot?
Hi Jesse,
I agree, Blue Sea should ship that mount with a custom made proper boot. The cap they ship it with is just plain stupid.
Last year I finally installed terminal fuses on all 5 of my batteries, after your warnings about dead shorts on the positives. But I missed the warning that these fuses can fail open. I may not have room in my battery locker for the T fuses, however. But I will try to figure out a way to follow your advice, as I regularly do. I certainly found the rubber covers difficult to use effectively. You might also look at these, which I have not personally measured for the job yet. https://shop.pkys.com/Blue-Sea-4018-Battery-Terminal-Insulator_p_2828.html?gad_source=1
https://www.go2marine.com/Sea-Dog-PVC-Battery-Terminal-Cover-Red-1-2-Each?gad_source=1
Thanks for never ceasing to learn yourself and then teaching the rest of us.
Hi Terrence,
Thanks for linking to that, I was not aware of that one and think it’s probably the one Jesse is referring to. Jesse?
That said, it still annoys the hell out of me that Blue Sea sell the MRBF mounts without a proper purpose designed way to cover them, and so we have to search around for some other product.
And thanks for the kind words, much appreciated.
Further, I now see the major problem is lithium, not my small, in comparison, Lead Acid batteries. Nonetheless, I will seek better boots. I have used zip ties on my terminal fuse covers, but never felt satisfied with the result.
Hi Terence,
Sure lithium is worse, but even a small group 31 lead acid can deliver enough amps when shorted to melt a metal tool, so you are right to improve things, as I will by properly covering the negatives.
“ even a small group 31 lead acid can deliver enough amps when shorted to melt a metal tool,”
When my raw water pump repair developed a syphon up through the Heat exchanger, I discovered the awesome power of a group 27 battery covered by salt water.
The images of my 2/0 battery cable connections just gone. The BlueSea fuses and connections a disfigured lumps of metal makes you a believer in the damage a short circuit can do.
I’ve use the battery terminal covers indicated by Terrence. I zip tie the covers to the wire, otherwise they can be knocked off the terminal. You can cut slits in the side to handle additional wires attached to the terminal and still leave the terminal covered. (No more than 3 connections to a terminal i.e. bilge pump) .
The issue of the MRBF lack of cover is still an issue to properly protect the terminal from accidental damage. The tolerance of the MRBF fuse to manage surge power mitigating incidental replacements is both a positive and a negative.
Hi John,
That must have been a nasty experience. Flooding is one of my worst boat related nightmares.
Looking at the Class-T rated 200Amp fuses on the BlueSea site, does it matter if they are not Ignition Protected. I note that the ANL and the MRBF fuses both say they are Ignition Protected and approved for Marnine Use. Is this just a case of not having the fuse tested or is this a factor?
Hi John,
If I remember the ABYC guide lines correctly, ignition protection is only required when installed in a compartment with a gasoline engine. The other issue to think about is that ANL and MRBF fuses would only remain safe from igniting vapours if the AIC was not exceeded. Anyway, Blue Sea specifically say that their class T fuses are ignition protected: https://www.bluesea.com/products/5502100/Class_T_Fuse_Block_with_Insulating_Cover_-_225_to_400A
Bit of motorcycle innertube cut to shape and cable tied.
Hi Abigail,
Good Option.
Coming back to this tip and the accompanying one on covering negative terminals.
As part of a DC distribution refit this winter I am using MRBF fuses on my 3 house AGM batteries with additional MRBFs being mounted on some downstream bus bars.
i purchased 2 pairs of boots to try out for coverage.
Ancor. Described as 260350 Wing Nut Battery Terminal Boots
Blue Sea. Described as Dual Post I/O CableCap
The Ancor boot is more flexible than the Blue Sea boot and seems to grip the fuse block. The cable access hole can be trimmed to accommodate larger cables easily and would certainly flex over 4/0 cable if required. My installation is using 2/0.
The Blue Sea boot covers the MRBF with cabling going through a U shaped channel. It could be trimmed for larger 4/0 cable with a bit of work. There is a groove to seat a zip tie to secure it, which would be required as the boot just sits on top of the MRBF with no grip. This boot is a more rigid material than the Ancor
Both boots would protect the complete MRBF assembly from something being dropped from above, and the majority of the sides. Both boots do not sit flush to the top surface of the battery case and sit up maybe 2mm above it. So something being pushed sideways against the boot could possibly contact the flat bar that connects to the battery screw terminal.
After handling and placing both boots in position, I am going to order more of the Ancor product to complete the install. Will most likely zip tie them in for more security.
Further on protective covers, Blue Sea makes a top cover for their 4 stud (3/8”) bus bar which I will have 3. I also have one 8 stud (3/8”) bus bar. There is no cover available for that. I’ll bend up a plexiglass top cover for that one. I considered cutting and fusing together 2 pcs of the 4 stud cover, but that will get messy and have to much flex (guess that answers the why)
Hi Bill,
Thanks for the great tips. I wondered about the Ancor covers, but good to have confirmed that they work: https://www.morganscloud.com/jhhtips/cover-the-negative-terminal-on-batteries/
I’m redoing my whole system with lithium (2x300Ah). I naively started with MRBF fuses, which is a mistake because of the circuit breaking capacity being too low, but I also noticed an interesting phenomenon : the wire connected to the fuse is very hot (which is not the case for the negative wire connected to the other terminal). I used a thermal camera and could confirm that the base of the fuse holder was way holder than it should be (40°C under only 100Amps, with a fuse holder rated for 300Amps continuous)
Not sure whether I did something wrong when installing them, but anyway that’s one less thing to worry about with class T fuses
Hi Brann,
Wow, that’s disturbing. But when I think about the quite small conductor contact area on those fuses, I don’t think you did anything wrong, rather I think this might be intrinsic to the fuse. What was the fuse rating?
Anyway, I think you are right, no worries with a class T.
Hi Brann,
Heat can be generated and spread to the whole terminal area connections if a stainless-steel washer is inserted along the electricity path. This is not an uncommon discovery when Steve D’Antonio conducts surveys and gives him something to write about (https://stevedmarineconsulting.com/battery-terminals/) in his excellent articles where I become aware of the myriad ways that us amateurs can make seemingly innocuous choices that can have unintended consequences.
My best, Dick Stevenson, s/v Alchemy
No washer there in my case. I’ll double check on the boat tomorrow, but I’m pretty sure there’s nothing between the holder and the fuse.
There’s a washer on top of everything along with a spring washer and a bolt of course, but these are not directly between the holder, the fuse and the lug.
the fuse rating was 300Amps. Here is a shot with a thermal camera. One can clearly see that the base of the fuse holder is extremely hot. The screw of the terminal was also very hot which got me quite worried. It seems heat finds weird ways to dissipate when it encounters dissimilar metals …
Hi Brann,
Thanks for the fill on that and the interesting pic. I just can’t see anything you did wrong although I suppose it’s possible that it’s a bad crimp and that’s where the heat is coming from, but the shot does not seem to support that.
Might be interesting to use a good meter to measure the voltage drop from:
Hi Brann,
That certainly seems concerning. Another possibility to check for is if the heat is actually coming from the battery terminal. Some of the lithium batteries have different internal connections to the positive and negative terminals and it is possible that could be the source of the heat. It is also a possible manufacturing defect. Since you already ordered the class T fuses, re-measuring post fuse change should tell you if this is the case. We use the MRBF fuses in a few spots so I am definitely interested to know what you find.
In my view, a lot of our DC systems live with legacy issues as each new generation of thing to come out tries to keep as much backwards compatibility with the other things. The biggest one is obviously the voltage, 12V was high at one point in time but it is nothing these days. Some of the battery connections I have seem look awfully small to me, when the copper leaving it is many times the terminal size, it makes you wonder. The idea of pulling a continuous 200A+ was nuts until very recently. Heck, our battery bank has probably never seen over 20A continuous load ever.
About 25 years ago I built a few electric cars for fun. The only practical choice for batteries was golf cart batteries. One of the cars ran 24X Trojan T145’s which are a little taller than a GC2 but otherwise the same hooked up in series. If we were competing in a hill climb, we could pull 600A+ continuous until you would hear a horrible sizzling noise and lose all power. The failure mode was the battery terminal melting which would compromise the battery case too. We learned that something like 15-20s doing this was the absolute limit. On another very similar vehicle we ran T105’s and I don’t think we ever melted any of those battery terminals, probably because those batteries ran the same terminals but couldn’t throw quite the same current. The controllers in golf carts are rated for much lower so there was no design need to support these currents when developing the batteries. Of course this is an I^2R loss so you can’t linearly extrapolate to other currents but it shows just how hot things will get as we were doing it in <20s which is nowhere near continuous.
Eric
Hi Eric,
I too have noticed that a lot of gear just does not seem to be keeping up with the power draw required my modern boats and systems, particularly at 12 volts. Like you, we use MRBF fuses on the J/109 but the max current they ever see is 75 amps charge.