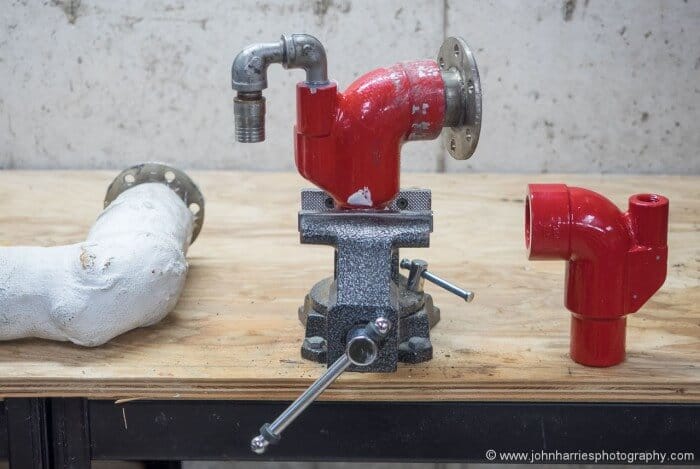
Most of us with recreational boats have exhaust systems with mixing elbows where the raw (salt) cooling water is injected into the exhaust line to cool the gasses so that they can exit the boat via rubber hose without causing a meltdown.
Let’s see, salt water and hot corrosive diesel exhaust:
Double, double, toil and trouble; fire burn and cauldron bubble.
The funny thing is that many, perhaps most, engine manuals don’t even mention the mixing elbow under regular maintenance. Maybe the engine manufacturers like selling new engines when all kinds of bad stuff happens due to increased exhaust back pressure caused by a partially blocked mixing elbow…or maybe it’s all a dark plot orchestrated by Henry Kissinger.
But enough with the conspiracy theories. Put removing your exhaust elbow and cleaning it out on your regular maintenance list. How often you ask? Well, that’s hard to say, because how quickly it gums up depends on a lot of variables, including exhaust length, design, exhaust temperature at the elbow and how completely the engine is burning fuel…and the astral sign of the boat owner.
Having said that, it seems to me that small engine exhaust systems gum up more quickly than those on larger engines and it seems that this is further exacerbated by the back pressure caused by long exhaust runs common on sailboats.
And talking of back pressure, many sailboat exhausts are marginal at best in this regard so any blockage in the elbow will be doing bad things.
Therefore, I would suggest initially pulling things apart and cleaning out the exhaust elbow at 500 hours. If you find it’s clean the first time, you can increase the interval, but on no account would I run an engine for more than 2000 hours without checking the exhaust mixing elbow.
Supporting the above, our generator exhaust becomes pretty nasty and partially blocked at 500 hours, but our main engine mixing elbow was pretty clean at 1500.
One more thing, as I said at the beginning, the atmosphere in a mixing elbow is probably the most corrosive that any part of your boat is subjected to, and therefore I strongly recommend carrying a spare elbow in your onboard spares kit and replacing the elbow whenever it looks the least bit dodgy.
Hi John,
There are many maintenance jobs that still make me anxious: where I think the likelihood of my doing damage while performing the requisite work exceeds a certain threshold. Rest assured, readers of John’s article, I considered the work on the exhaust elbow a no-brainer: ie. I believed I could not cause a problem and never did.
My way was to swap elbows every 2 years, taking the old one off and putting the spare on and then spending a quiet hour or so chipping away the accumulated carbon deposits and making sure there were no thin spots in the revealed metal.
I would suggest also having a couple of extra gaskets (much more than simple paper things). Mine were often re-usable (not sure what engine mechanics might say about this, but I never had a problem), but they also could stick and be ripped when removing the elbow. I also occasionally had to clean the faces of the connection.
In 2 years (probably 600 hours or so) the elbow on my Westerbeke 42B would be 10-20% compromised.
My best, Dick Stevenson, s/v Alchemy
Hi Dick,
Great tip on the gaskets, I should have mentioned that. We always keep two spare sets and a spare elbow.
Good to have the confirmation on timing too
Thanks for both.
Dick and John, of what material would a non-paper-gasket be made of and what thicknesses are we talking about? Tiring of what the Victor company wanted for their pressed cardboard graphite-infused gaskets for the Atomic 4 (although you need it for the head gasket), I started to make mine out of gasket paper in 1/32″ and 1/16″ thicknesses, which is fine for pumps and other bits and pieces, using the “tap with a ballpeen hammer” method. No problem. But an exhaust elbow is an intrinsically harsh environment, hence my query.
This is interesting and the photos on the YBW link are a bit scary.
We have a ‘semi-marinised’ Isuzu C241 and have had virtually no build up at the exhaust over 2500 hours of running and I wonder why. Yes, there has been some soot on the walls but nothing significant.
I fabricated the elbow in thick wall stainless pipe with the raw water inlet pipe entering at an acute angle.
Semi-marinised? Well, the exhaust manifold is not cooled so the gases are pretty hot when they arrive at the elbow. I wonder if this has something to do with the lack of deposits? The hot exhaust manifold can get a bit much at times and it’s certainly not something I would recommend. Especially in the tropics when the engine compartment blower can only just keep the temperature down. I would prefer to clean the elbow every 500 hrs!
PS Exhaust gaskets are very easy to make and carrying a selection of gasket materials and a couple of hole punches on board can be useful.
My operational manual for Yanmar 4JH4-HTE states;
Every 250 hour: clean exhaust water mixing elbow
Every 500 hour: replace exhaust water mixing elbow
So…Yanmar is not a part of the secret conspiracy of diesel manufacturers….
Hi Jon,
Those specs sound like a conspiracy of a different nature: to get you to spend $$ on parts and labor. I think it quite likely that you can swap exhaust elbows every year or 2 and clean the old and put it back on again unless they make it of very thin material.
In any case, have you seen the degree of build up when your elbow is taken off? Do you have the standard very large exhaust hose that mitigates back pressure?
I have a new Yanmar 4jh5e which I am quite happy with, but I have a custom made exhaust elbow to meet some installation requirements.
Dick Stevenson, s/v Alchemy
Hi Dick and John,
As it happens we use a standard Yanmar exhaust elbow on our custom made (it’s a long story) generator exhaust. These are not robust elbows and our experience is they are all done at 500 hours. Once we tried to go longer and it started leaking at 700 hours.
I would do as Yanmar say and replace at 500 hours. Of course I’m sure Kissinger had a hand in the elbow design for Yanmar.
Hi Dick…
Maybe you are right about the other wayaround.conspiracy? Or making maintenance requirements so strikt that the hardy ever come in a position of responsability for any kind of failure!
i have not checked my mixing elbow for the last 300 hours….. Time to do so. :
Jon
I dont have any problem with mine as the steel is very thick and I often flush well with fresh water. however if I did, I would put a VHT flameproof coating on the inside. The same as on exhaust headers, this handles about 1000 celsius. You would have to bake the mixer in the oven a few times.
this would slow the process as the coating would need to be eaten off first before there was access to the metal.
Im sure then, your mixers would nearly last forever.
Due to most Exhaust elbows are made by “Cast Iron” they rust quickly and fail.
I replaced mine to a “Stainless steel” model,,,No rust, No maintenance. One item less to worry about! Can’t understand why it is NOT std on new engines for wet exhausts??
SS is not totally maintenance free, Conny, since carbon can still build up even if there is less corrosion. Most SS elbows are fabricated (as opposed to cast) and the welds tend to corrode from the inside out. They certainly do in SS mixers (muffler/waterlock) due to the acidic salt water/exhaust gas combination.
But I agree that SS is far better than cast iron and cast SS would probably be better than welded SS since it wouldn’t have all those little crevices on the inside of the welds. I made mine out of 4mm wall thickness pipe and it’s still good after 30 years. Can’t complain!
Why is it not standard on all new engines with wet exhausts? Ask Henry K.
Hi Pat,
I can confirm that SS is not a panacea. My friends at Billings Diesel had a hell of a time with weld failures on SS custom exhausts at one time. They then changed to a special alloy and welding wire, which solved most of the problem. Unfortunately I don’t know the details.
Further I have had two SS elbows fail at the welds on me over the years.
Having said that, I agree that a well made SS elbow is the best readily available alternative.
I believe my success was largely due to the welding procedure I followed.
First of all I used 316 SS (there are better alloys but this is relatively available).
I layered multiple TIG welds so that the almost inevitable cavities and crevices on the inside of the weld (where corrosion is most likely) were restricted to the first pass. I then continued layering metal until the welded area was about 50% thicker than the wall thickness. From memory that would have been 5 or 6 passes.
Good to know. Was this welding with SS wire, or rod (if there’s SS rod, I haven’t heard of it, but then I’m a novice welder)?
Yes, Marc, one uses a filler wire/rod specifically alloyed to end up after welding with “identical” characteristics to the parent metal.
Hi Pat,
That makes sense, thanks. I think I’m right in saying that when they were having trouble with the welds corroding out, they were welding MIG not TIG and that changing to TIG was a lot of what solved the problem. Does that make sense? Since I know very little about welding I may be talking rubbish.
You may well be right, John.
TIG is far slower and more controllable than manual MIG. For pipe welding TIG is preferable since it’s very difficult to maintain the correct angles when working round tight circumferences and/or awkward shapes at the speed needed when welding with MIG. If you don’t maintain the correct angles you risk defects in the subsequent weld due to lack of protection from the Inert Gas (the IG component of TIG and MIG).
Hi Pat,
Thanks, makes sense.
Hi John,
Your article made me think how we could be more preventative still. I have used a NZ concentrate product Salt Away with their mixer, to flush our outboard engine, tender, trailers, fishing gear, wet-suits and our main hull and decks, using a garden hose. Could it be used on our inboard engine? https://www.salt-attack.nz/products/marine-boat-motors
Better still, they suggest making your own frozen “shots” using 100ml Salt Away concentrate (which I always carry on board) and 100ml fresh water in a small snap-lock bag or container – put in the freezer to set.
At the end of your trip, pop the mushy frozen shot into your strainer box (not the bag obviously), run the engine for 30-40 seconds or until foam appears from the exhaust outlet. Leave the Salt Away to do its work removing salt, calcium and carbon deposits and providing a protective layer on everything against salt corrosion. I have certainly seen good results with my outboards.
If you can’t get Salt Away, I believe Salt X has a similar formulation. I checked with Volvo – they supply their own product intended for larger launch engines complete with an expensive injection system. The Volvo service manager I checked with thought Salt Away would work just fine and would help protect the impellers and seals even. Anyone know of a reason why this won’t work long term, other than cost?
I have my first batch in the freezer!
Rob
In the mid ’80s my wife and I were motoring in to pick up sailing guests, when the engine noise changed and black smoke started to seep from the engine compartment cover. I felt the cover, and it was no warmer than usual. I had Janet slow the engine, and I pulled the cover free.
At the back of the engine a solid jet of water was spraying against the rear bulkhead — the raw water discharge jet had drilled through the exhaust elbow and was now firing water and exhaust gases every where but out of the boat. I cut a strap out of a coffee can. I wrapped the elbow with oiled shop towel, and wrapped the towel with the strap and then applied four hose clamps (otherwise reserved for 6 inch vent hose).
The replacement elbow had to be ordered from Sweden, so we sailed this way for the seven weeks it took for it to arrive in Annapolis. When I replaced the elbow, the extemporaneous repair was stained but otherwise unaffected. However, when I sawed the exhaust elbow in half, there was an interesting metallurgical story.
From the hole created by the jet outward, there were three distinct bands of destruction. Within a cm of the jagged hole was bright metal with an almost polished appearance. the next band a few mm wide was corrosion with no polish. the next band about a cm wide was scaled metal with very little corrosion, beyond that was healthy iron.
When I discussed this with the gods of Volvo they had little to add. When I showed it to a steam engine friend of mine. He concluded the hole was a combination of heat, corrosion, and shot-blasting from particulates in the water. This connected well with the seven impellers digested by suspended sand (had to replace on three day cycle) during an ICW delivery trip from Destin Florida to Wash DC.
He also observed the design was flawed in that the water jet should have run in an elbow in the elbow so that the water jet flowed parallel to the exhaust gas flow, not across it to impinge on the elbow wall. He said this would cut down on scaling and corrosion as it kept the water from flashing on contact with the hot wall. Such a surface flash to steam deposition was the major element in scaling. Whereas a gaseous flash to steam just creates a brine.
This is very good to understand. Thank you.
If fabricating an elbow it’s simple to introduce the water via a tube entering at an acute angle so that the water flow is already close to parallel to that of the exhaust gas. Extend it to about the centre of the outlet and cut it at an angle approximating right angles to the axis of the exhaust. No need to attempt an elbow within an elbow.
Grabbing followup comment link.
Addenda
Scotty (I kid you not), the steam engineer, also recommended a thermistor on the dry side of the exhaust elbow and one in the exhaust water overboard outflow (maybe in the muffler) and either two temp gauges or a delta-T gauge as an early warning of the need for a maintenance look see. (His stuff was more inclined to blow up than ours. His gauges were also very much prettier.)
Good day,
My Volvo auxiliary, an MD 30, has only 1700 hours. Unfortunately, the two pieces making the exhaust elbow need to be replaced. The upstream part could be fixed by a metal shop but the downstream part is fairly rusty where the two parts joint. Volvo dealer says they have no replacement parts for that engine anymore.
Would you know who produced that same engine in the early 1980s and painted in green to make her called Volvo MD 30?
Thanks
Mag
Hi Mag,
Wow Volvo really are terrible at this stuff! I think I’m right in thinking that the MD 30 is a relabeled Perkins, but I’m not sure. Anyone else know for sure and where Mag can get parts?
Hi Mag
I’m not sure who made the engine block for this motor.
The parts you’re interested in however would have been fitted by Volvo during their marinisation of whatever motor they were using (both Perkins and Volvo have sourced motors from a variety of manufacturers over the years including Peugeot and the Ishikawajima Shibaura Machinery Company).
The exhaust elbow can almost certainly be fabricated by any reasonably skilled metal worker and I would suggest having it made in stainless steel (see comments above). If you send photos to me at pat(at)boatstasmania.com.au I may be able to offer more constructive comment.
Hi Pat,
Thanks for fielding that with a great answer.
Hi John,
Thanks for your reply.
I will see just how hard it is to convert to the 2nd heat exchanger and will knock up an anode holder if too hard.
The stainless steel to be used in fabrication is 316 L which stands for low carbon. Lasts much longer.
Of course the TIG rods need to be this material as well.
Also after welding you need to pickle the welds which brings the Cr (chromium) back to the surface where the welding temperature depleted it.
Hi Marc,
I have always had a spare gasket that was provided by the manufacturer, so I have not had to improvise. That said, I have gasket material that I keep for spare that was promoted as acceptable for exhaust elbows. My notes indicate it was Remflex, exhaust gasket raw board, 6.5 x 11 inches. This product may be a bit thicker than necessary (or that you might need) for most applications as my genset exhaust elbow connection was not designed well and needed a thicker gasket, but they have lots to choose from.
My best, Dick
Remflex…thank you, Dick. As with most things on boats, I find having the right “Plan B” obviates its ever needing to be called upon.
Here’s the link to Remflex for those who are interested: http://catalog.remflex.com/category_s/190.htm
Hi Marc, You are welcome, and, yes, like carrying an umbrella. Dick
Hi John and everyone, any recommendation (make, model?) for a good wire reinforced wet exhaust hose? My exhaust muffler is located 2 foot below the engine lowest point sitting wedge in the grey water bilge. The boat came with it in that location. Thinking aloud, I am not sure if it is it is an ideal location as it requires more work to push the water from the muffler to the exhaust exit (about 1.2m above the muffler). I would have thought that a higher location at the level of the engine would be ideal. Any comments on this theory?
Hi Ee Kiat,
Exhaust systems can be quite complex, so I caution against trying to crowd source a design since there are a lot of variables here and a mistake can result in a wrecked engine either from flooding or too much back pressure. What you need to do here is get hold of a copy of the engine installation manual and follow that to the letter.
All that said, I would caution against moving the muffler up since that can be a quick route to a flooded engine.
As to whether or not the exit is too high, the manual will tell you that.
Hi Again,
As to the hose, I have never found much difference between brands, but then again I have not done any sort of study either. You might check Practical Sailor to see if they have done a report.
Thanks John!
Hi John, my current exhaust exits at the waterline. As I will be hauling the boat up, I am wondering if i should raise the exhaust exit to above the waterline to avoid water siphoning back to the engine. Would you recommend that?
Hi Ee Kiat,
Raising the outlet won’t necessarily make things any better, and may in fact make them worse by reducing the distance to the high point. An exhaust system is just that, a system, so it needs to be designed as a whole by referencing the engine installation manual. Asking me, or anyone else, for recommendations on a single part of it may easily result in wrecking the engine.
Bottom line, you need to either find the engine installation manual and follow it, or find someone who really understands exhausts to design a complete system for your boat.
Hi John, ok, noted the complexity. Trouble is that there are no real expert in this area for sailboats or small pleasure crafts especially one of 30 years old without any manufacturer’s manuals to refer to. Singapore is the world busiest port, so it is very equipped for big container/cargo ships! the engine manual does not touch on installation, just engine data, maintenance etc. no worries, I will keep looking and meanwhile keeping the mantra “if it aint broke, dont fix it until you have consulted an expert”.
Hi Ee Kiat,
Most engines have a separate installation manual, so might be worth hunting down one of those. What kind of engine is it?
Another option would be to get a company that manufactures exhaust components to design a system for you. I had good luck with Halyard Marine in the UK, and their system, that I installed in 2010, has been great. https://www.halyard.eu.com
Sorry, I should have thought of that option before.
Hi John, my engine is a Perkins 4.236. Thanks for the link. I will look into exhaust system later as I can live with the current system for the moment.
My engine, a Yanmar 4JH4E, is mounted below the water line, and has this custom stainless steel mixing box after the elbow. It leads back to a water lock box before doing an above water loop to a transom exit. I’m wondering if this steel box is needed, or if there is a better solution than this box?
Hi John,
Exhaust design is a really complex subject, so not one that me, or anyone else, can add a lot of value to from afar.
That said, that system does sound a bit funky. Also a SS box like that is prone to failure since the material does not like diesel fumes mixed with salt water. And in this case the exhaust is already cooled by sea water so using SS here instead of composite does not seem to make a lot of sense.
The only thing I can say is that having installed one on our McCurdy and Rhodes I’m a big fan of water separation systems. You might want to talk to Halyard Marine: https://www.halyard.eu.com
They designed a system for us and it has been flawless. https://www.morganscloud.com/2010/07/16/engine-installation-details/
Thank you. I’ll look into it. We’ve already had to fix corrosion in this box. Not the best design at all.
Late related comment. I know of two Beta 43 exhaust elbows that failed in the first 100 hours of operation . Not stainless. My old Perkins 4-108 has the same elbow as when I purchased the boat in 1997. It remains clean as a whistle. I have no explanation.
Hi Terence,
Sounds like a defective batch of elbows from whatever company Beta uses to make them. Probably the wrong welding rod used. These things do happen to most all engine manufactures, so the key point is how did the Beta handle the situation?
For another example, Perkins had a bad batch of starter motors some years ago, and I had an exhaust elbow show pin holes on my Perkins at about 300 hours.
Also, it’s worth knowing that stainless steel is generally not the optimal materiel for exhaust elbows since the gases attack the welds. That said, with the right alloy and rod stainless has become more common in recent years.
Hi John,
Our exhaust elbow is relatively new (~ 300 hours) and will come off at the end of our NZ season for inspection. But wondering about maintenance for the rest of the exhaust system on our Volvo D2 55 (Perkins painted green).
Can anyone please advise a sensible replacement interval for our moulded plastic combo plastic Vetus muffler / waterlock? External inspection – looks in good condition and no sign of heat deformation from exhaust gasses. Good raw water flow through the strainer and exhaust outlet. Can’t find anything on the Vetus support pages.
AND also please, the replacment interval for the wire reinforced rubber exhaust hoses that connect it to the exhaust elbow and on the other end, to the exhaust outlet? Hose feels uniform and still flexible right along its run.
See black hose in photo which leads aft from the Vetus unit, up to deck level and back down to the above-the-water exhaust outlet, in the back quarter of our aft cockpit sloop.
When these reinforced heavy duty exhaust hoses fail, do they tend to give way badly, or do they develop tell-tale pinholes or slits? I ask because we carry self-amalgamating heat proof tape, but not spare exhaust hose.
Thanks.
Hi Rob,
As far as I know those plastic waterlifts last for a very long time as long as they are not chafed or abused so I’m not sure there is a replacement interval, but I’m no plastics expert. Drew, and thoughts?
On wire reinforced hose my rule has always been to inspect carefully and replace at any sign of surface cracking. This seems to occur first at bends and well before any failure.
I would check on this over at Practical Sailor since drew, who is a chemical engineer writes on these kinds of issues there.
Thanks John, that’s very good advice.